模具结构(模具设计材料)
两板模基本结构模具设计材料

目录
• 两板模基本结构 • 模具设计 • 材料选择 • 模具材料 • 模具制造工艺
01
CATALOGUE
两板模基本结构
定义与特点
定义
两板模是一种模具结构,主要由 上模板、下模板和模架组成。
特点
两板模设计简单,制造成本低, 适用于中小型塑件的大批量生产 。
结构组成
01
04
CATALOGUE
模具材料
钢材
钢材是两板模模具设计中常用的 材料之一,具有高强度、耐磨性
和耐腐蚀性等优点。
钢材可以通过热处理和表面处理 等工艺进一步提高其性能,如提 高硬度、增强耐磨性和防腐性能
等。
钢材的缺点是密度较大,较重, 且成本相对较高。
铝材
铝材是一种轻便、耐腐蚀的材料,也常用于两板 模模具设计。
02
03
上模板
上模板是两板模的上半部 分,主要作用是安装模具 的凸模和顶出机构。
下模板
下模板是两板模的下半部 分,主要作用是安装模具 的凹模和定位机构。
模架
模架是两板模的支撑结构 ,用于固定上模板和下模 板,确保模具的稳定性和 精度。
结构分类
按用途分类
根据模具用途不同,两板模可分为热塑性塑料模具和热固性塑料模具。
明确模具设计的要求和目标, 收集相行详细的结构 设计,确定零部件的形状、尺 寸、材料等。
出图与整理技术文件
完成设计后,按照标准或规范 要求绘制图纸,整理相关技术 文件。
设计软件
CAD软件
CAM软件
用于进行二维或三维的模具结构设计 。
用于生成加工代码,实现模具的数控 加工。
05
CATALOGUE
塑料模具结构
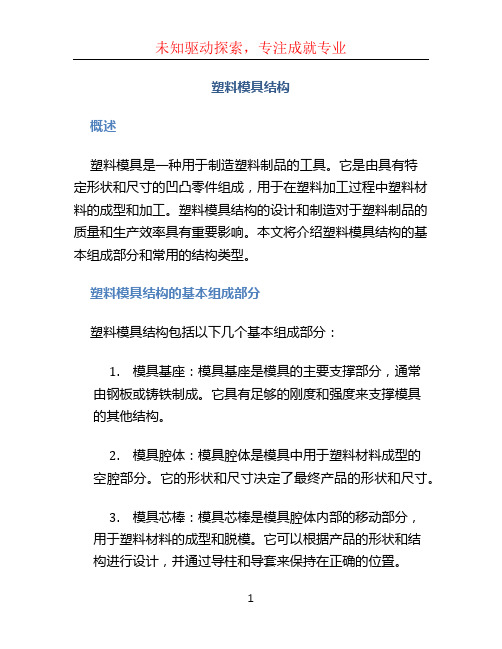
塑料模具结构概述塑料模具是一种用于制造塑料制品的工具。
它是由具有特定形状和尺寸的凹凸零件组成,用于在塑料加工过程中塑料材料的成型和加工。
塑料模具结构的设计和制造对于塑料制品的质量和生产效率具有重要影响。
本文将介绍塑料模具结构的基本组成部分和常用的结构类型。
塑料模具结构的基本组成部分塑料模具结构包括以下几个基本组成部分:1.模具基座:模具基座是模具的主要支撑部分,通常由钢板或铸铁制成。
它具有足够的刚度和强度来支撑模具的其他结构。
2.模具腔体:模具腔体是模具中用于塑料材料成型的空腔部分。
它的形状和尺寸决定了最终产品的形状和尺寸。
3.模具芯棒:模具芯棒是模具腔体内部的移动部分,用于塑料材料的成型和脱模。
它可以根据产品的形状和结构进行设计,并通过导柱和导套来保持在正确的位置。
4.模具导向系统:模具导向系统用于确保模具腔体和芯棒的准确定位和运动。
它通常包括导柱、导套和导向销等部件。
5.冷却系统:冷却系统用于控制模具温度,以确保塑料材料的快速凝固和脱模。
它通常包括冷却水管道和冷却孔等部件。
6.开关系统:开关系统用于控制模具的开合动作。
它通常包括压缩弹簧、推杆和开关机构等部件。
7.引导系统:引导系统用于模具的分离和组装。
它通常包括固定螺栓、螺母和定位销等部件。
塑料模具结构的常用类型根据不同的塑料制品和加工要求,塑料模具结构可以分为以下几种常用类型:1.单腔模具:单腔模具是一种最简单的模具结构,只有一个塑料材料成型腔体。
它适用于小批量生产和简单形状的塑料制品。
2.多腔模具:多腔模具是一种具有多个塑料材料成型腔体的模具结构。
它可以生产多个相同或不同形状的塑料制品,提高生产效率。
3.热流道模具:热流道模具是一种通过加热系统来控制塑料材料的流动和成型的模具结构。
它可以避免塑料制品中的缺陷和熔融料的浪费。
4.双色模具:双色模具是一种能够在同一模具中成型两种不同颜色的塑料制品的模具结构。
它可以实现多彩和多功能的塑料制品。
塑件材料分析与模具结构设计

塑件材料分析与模具结构设计塑件材料分析与模具结构设计塑料零件在今天的工业中扮演着越来越重要的角色,我们在生活中随处可见使用塑料制成的产品。
塑料具有高强度、轻量化、不易变形、成本较低等优点,因此广受欢迎。
而制造合格的塑件则需要对材料进行深入地分析,并设计合适的模具结构。
首先,我们需要对塑料材料进行细致的分析。
塑料材料分为热塑性塑料和热固性塑料两种。
热塑性塑料可以被加热成为液体,并且再冷却时可以重新固化,具有较好的可塑性和可加工性。
热固性塑料一旦被加工成形,在加热后也不会回到液态,同时具有很好的耐热性和刚性。
在选择塑料材料时,需要结合产品的使用要求和制造成本进行综合考虑。
常见的塑料材料有聚氯乙烯、聚丙烯、聚苯乙烯等。
其次,我们需要进行模具结构设计。
模具结构的设计需要考虑到产品的形状和材料特性。
首先,我们需要根据产品的形状进行相应的模具结构设计。
模具分为单模和复模两种,单模一般适用于产品形状简单的情况,而复模适用于形状复杂的产品制造。
其次,针对材料特性,我们需要考虑到模具的冷却系统设计。
在模具制造过程中,需要通过模具充填时优化材料流动性,以防止出现缩孔、裂纹等问题。
此外,还需要考虑模具的表面处理,以防止模具表面出现磨损、腐蚀等不良情况。
最后,我们需要进行模具结构的试制和测试。
试制过程中,需要注重材料的选用和模具结构的合理性,以尽量避免不良的产品质量。
同时,需要根据生产时间和生产效率的要求,不断对模具进行优化和改进,以提高生产效率,减少生产成本。
总之,塑件材料分析与模具结构设计是制造高品质塑料产品的关键要素之一。
在进行塑料制品加工生产时,我们需要深度研究材料性质,针对不同的产品需求设计合适的模具结构,并对模具进行不断地改进和优化,以最大化产品的性能和质量。
模具的基本结构组成

模具的基本结构组成一、引言模具是制造工业产品的重要工具,它能够将原材料加工成所需形状和尺寸的零件。
模具的基本结构组成是模具设计与制造的基础,本文将从以下几个方面介绍模具的基本结构组成。
二、模具的基本组成1. 上模板:上模板是模具的上部分,也是模具的主体部分,它承受着模具的大部分工作压力。
上模板通常由钢材制成,具有足够的强度和硬度来抵抗模具在工作过程中的应力和磨损。
2. 下模板:下模板是模具的下部分,它通常与上模板配合使用,用于支撑和定位工件。
下模板也由钢材制成,其硬度和强度要求较上模板低一些,但仍需具备足够的刚性和耐磨性。
3. 滑块:滑块是模具的一个重要组成部分,用于实现模具的开合动作。
滑块通常由滑块板和导柱组成,通过导柱的引导,滑块能够在模具的开合过程中平稳移动。
滑块的设计和制造直接影响模具的工作效率和精度。
4. 塑料模具芯:塑料模具芯是模具中的一个重要部件,它用于成型工件的内部形状。
模具芯通常由钢材或铝材制成,具有良好的刚性和导热性能,能够有效地支撑和冷却工件。
5. 模具座:模具座是模具的支撑部分,它提供了模具的安装位置和固定方式。
模具座通常由铸铁或钢材制成,具有足够的强度和稳定性,能够确保模具在工作过程中的稳定性和精度。
6. 导向机构:导向机构是模具中的一个重要组成部分,它用于确保模具在工作过程中的准确位置和运动轨迹。
导向机构通常由导向销、导向套和导向板等部件组成,通过它们的配合运动,能够实现模具的精确定位和稳定运动。
7. 顶针:顶针是模具中的一个常用部件,它用于实现模具的顶出动作。
顶针通常由钢材制成,具有良好的弹性和耐磨性,能够承受较大的顶出力,并保持工作精度。
8. 弹簧:弹簧是模具中的一个重要辅助部件,它用于实现模具的复位和顶出动作。
弹簧通常由弹簧钢制成,具有一定的弹性和耐久性,能够确保模具在工作过程中的正常运动和复位。
9. 冷却系统:冷却系统是模具中的一个重要组成部分,它用于控制模具的温度和工作环境。
常见的压铸模具结构及设计
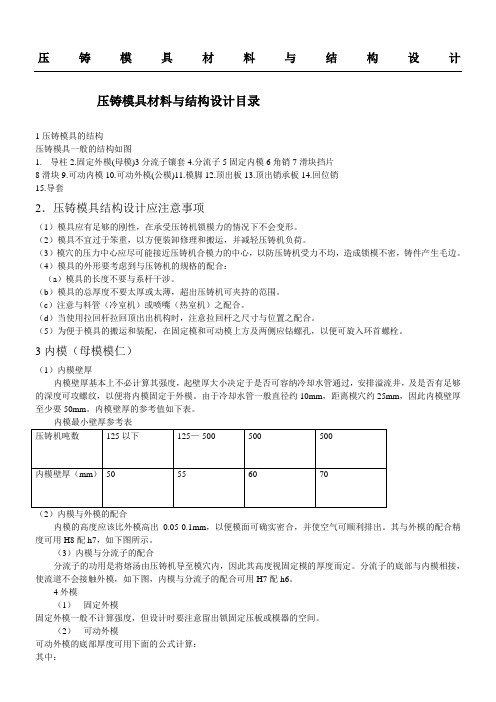
压铸模具材料与结构设计压铸模具材料与结构设计目录1压铸模具的结构压铸模具一般的结构如图1.导柱2.固定外模(母模)3分流子镶套4.分流子5固定内模6角销7滑块挡片8滑块9.可动内模10.可动外模(公模)11.模脚12.顶出板13.顶出销承板14.回位销15.导套2.压铸模具结构设计应注意事项(1)模具应有足够的刚性,在承受压铸机锁模力的情况下不会变形。
(2)模具不宜过于笨重,以方便装卸修理和搬运,并减轻压铸机负荷。
(3)模穴的压力中心应尽可能接近压铸机合模力的中心,以防压铸机受力不均,造成锁模不密,铸件产生毛边。
(4)模具的外形要考虑到与压铸机的规格的配合:(a)模具的长度不要与系杆干涉。
(b)模具的总厚度不要太厚或太薄,超出压铸机可夹持的范围。
(c)注意与料管(冷室机)或喷嘴(热室机)之配合。
(d)当使用拉回杆拉回顶出出机构时,注意拉回杆之尺寸与位置之配合。
(5)为便于模具的搬运和装配,在固定模和可动模上方及两侧应钻螺孔,以便可旋入环首螺栓。
3内模(母模模仁)(1)内模壁厚内模壁厚基本上不必计算其强度,起壁厚大小决定于是否可容纳冷却水管通过,安排溢流井,及是否有足够的深度可攻螺纹,以便将内模固定于外模。
由于冷却水管一般直径约10mm,距离模穴约25mm,因此内模壁厚至少要50mm。
内模壁厚的参考值如下表。
内模最小壁厚参考表(2)内模与外模的配合内模的高度应该比外模高出0.05-0.1mm,以便模面可确实密合,并使空气可顺利排出。
其与外模的配合精度可用H8配h7,如下图所示。
(3)内模与分流子的配合分流子的功用是将熔汤由压铸机导至模穴内,因此其高度视固定模的厚度而定。
分流子的底部与内模相接,使流道不会接触外模,如下图,内模与分流子的配合可用H7配h6。
4外模(1)固定外模固定外模一般不计算强度,但设计时要注意留出锁固定压板或模器的空间。
(2)可动外模可动外模的底部厚度可用下面的公式计算:其中:h:外模底部之厚度(mm)p:铸造压力(kg/cm2)L:模脚之间距(mm)a:成品之长度(mm)b:成品之宽度(mm)B:外模之宽度(mm)E:钢的杨氏模数=2.1×106kg/cm2d:外模在开模方向的最大变形量(mm),一般取d≤0.05mm.例:某铸件长300mm,宽250mm,铸造压力选定280(kg/cm2),外模之宽度560(mm),模脚之间距360(mm),最大变形量取0.05(mm)。
模具的基本结构

模具的基本結構1、雙板模(2板模)A.典型操作條件1)塑料型腔壓力從1000至12000ps(典型值為5000ps)(1)注嘴衬套——有锥度的插入注塑模中,让塑料从注喙流入分浇道。
(2)定位环——常用来精确校准模具在机器模板上的正确位置。
(3)阴模板——包含模具型腔的半付模具。
(4)阳模板——另半付模具,模芯常装在可移动的模具上使注塑件容易脱模。
(5)推杆(顶销)——使注塑件和浇道脱出模具的移动杆。
(6)浇道拉料杆——设计成当模具开模时从注嘴衬套中拉出塑料注道残料。
(7)支承板——使模具提高抗挠度的支承板后面。
(8)支承柱——放在抗挠度的支承板后面。
(9)推杆回定板——固定推杆和拉料杆的头部。
(10)导柱——用作精确位上下两片模上彼此相关的位置。
(11)夹模板(装模板)——夹持或用螺栓固定于机器模板上的底板。
(12)冷却通道——在支承板或阴模板和阳模板中,常被用来分散注塑件的热量。
(13)加热元件——对热固性塑料模具,热固元件用来帮助塑料固化。
注塑模具基础1.二板模与三板模的区别是什么?请画出二种类模具简图,并描述三板模的开合模顺序?✧二板模与三板模的区别是:三板模在定模部分多一次取出流道与产品分离。
三板模一般采用点浇口二板模浇口可根据产品及要求灵活选用。
✧二板模结构(2plate mold)✧前模压板(top damp plate)✧母模板(A plate)✧活动板(或推板strpper plate, 在推板顶出时选用);✧公模板(B plate)✧承板(supplrt plate)✧间隔板(spaoer block)✧顶针固定板(ejector retainer plate)✧顶针板(ejector plate)✧公模固定板(bottom damp plate)在AMP模具有Ejectorhousing,实际上是为了防止产品异物掉落顶出机构,而用封闭的间隔板✧三板模结构(3 plate mold)在二板模的前模板与母模板中加一块水口脱料板(runner strpper plate);模具一般有四支导柱(guide pin)和四支拉杆(support pin);另外也有只用四支长导柱,导柱兼拉杆用。
模具结构设计方案

模具结构设计方案模具是工业生产中常用的工具之一,广泛应用于塑料、金属、陶瓷等制品的生产过程中。
模具的结构设计对产品的成型质量、生产效率以及模具寿命等都有着重要的影响。
下面将以塑料模具为例,详细介绍模具结构设计的几个方面。
首先是模具的整体结构设计。
模具一般由上、下两部分组成,上模和下模之间通过模具螺栓连接。
上模通常由进料口、固定板、移动板、顶针等部分组成,下模则由底板、定位销、导向板等部分组成。
在整体结构设计中,需要注意上、下模的对位准确、顶出机构的稳定性以及模具的可拆卸性等。
其次是注塑模具中的流道系统设计。
流道系统是塑料模具中最关键的部分,直接影响产品的成型质量。
在流道系统的设计中,需要考虑塑料的充填速度、压力和温度等因素,合理选择流道的截面形状和尺寸。
同时,还需要设计出合适的喷嘴和冷却系统,以确保塑料在流道中充分流动和冷却。
第三是模具的冷却系统设计。
冷却系统对于模具寿命和产品质量有着重要的影响。
在冷却系统的设计中,需要合理设置冷却通道,并确保冷却通道与模具表面的距离足够近,以提高冷却效果。
同时,还需要注意冷却通道的位置和布局,以保证整个模具受热均匀,避免产生应力集中和变形等问题。
另外还需要考虑模具的顶出机构设计。
顶出机构主要用于将成型的产品从模具中弹出,避免产品粘模。
在顶出机构的设计中,需要确保顶出机构的稳定性和可靠性,同时考虑到产品的形状、材料和尺寸等因素,设计合适的顶出机构形式和数量。
最后是模具材料的选择。
模具材料的选择直接影响到模具的使用寿命和成本。
一般而言,模具材料要求具有较高的硬度、强度和耐磨性,同时还需具备一定的耐腐蚀性和导热性等特点。
在选择模具材料时,需要根据具体的生产需求和经济因素综合考虑,选择合适的模具材料。
综上所述,模具结构设计是一个复杂的工作,需要考虑多个方面的因素。
合理的模具结构设计可以提高产品的成型质量和生产效率,延长模具的使用寿命,减少生产成本。
因此,在进行模具结构设计时,需要充分考虑以上几个方面的原则和要点,以保证模具的性能和质量。
模具中的常用材料

Si 0.85~1.15
铸1.2333(锻 1.2358)
0.57~0. 61
铸1.2370(YBD-3) 0.9~1.0
(锻1.2363)
5
Cr12MoV锻
1.451. 70
铸1.2382(锻 1.2379)
1.5-1.6
0.25~0.45 0.20~0.40 ≤0.4
0.5-0.8
Mn 0.65~1.05 0.70~0.90 0.40~0.70 ≤0.35
表面淬火 HRC56以上 整体,表面 感应HRC58-
62
《模具中的常用材料及设计中应注意的一些加工问题》
材料
税前价 格/ 公斤
Cr12Mo1V1( 类 似于SKD11) 德国牌号1.2379 (相应铸态牌
号1.2382)
SKD11 :59.83
Cr12MoV
14.96
DC53
70
7CrSiMnMoV (相应铸态牌
1.2333
铸态材料对照表
热处理
用途
底板、压料板、压料圈基体、驱 动块、带导板的CAM滑块
退火硬度
FH/IH 50-54 IH 54-58
拉延凸模、压料圈
驱动块、不带导板的CAM滑块\单 薄底板、压料板
耐磨损的拉延凸模、压料圈、凹 模
FH/IH 50-54 IH/H 58-62 FH/IH 54-56 IH 56-60
单薄压料板
滑块等
整形大凸模、凹模
料厚超过1.5或翻边高度超过25的 翻边凹模,拉延模镶块
供货状态 硬度(HBS)
灰铸铁
HT250 /HT300
球墨铸铁
QT400(不常用, 可用
QT500代 替)
模具的基本结构及相关概念
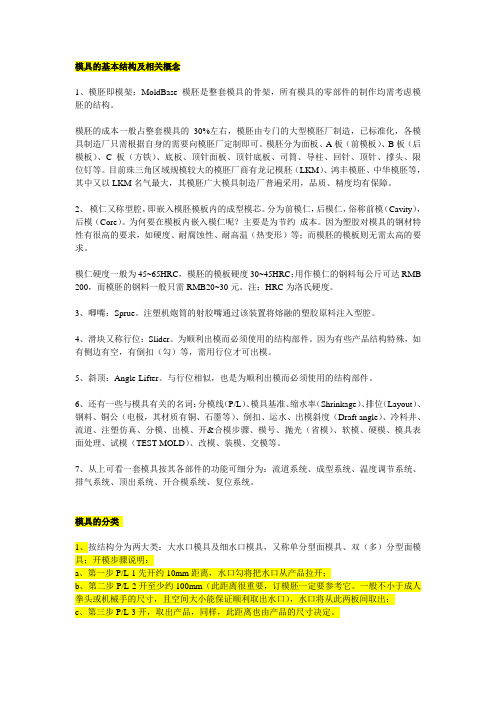
模具的基本结构及相关概念1、模胚即模架:MoldBase 模胚是整套模具的骨架,所有模具的零部件的制作均需考虑模胚的结构。
模胚的成本一般占整套模具的30%左右,模胚由专门的大型模胚厂制造,已标准化,各模具制造厂只需根据自身的需要向模胚厂定制即可。
模胚分为面板、A板(前模板)、B板(后模板)、C 板(方铁)、底板、顶针面板、顶针底板、司筒、导柱、回针、顶针、撑头、限位钉等。
目前珠三角区域规模较大的模胚厂商有龙记模胚(LKM)、鸿丰模胚、中华模胚等,其中又以LKM名气最大,其模胚广大模具制造厂普遍采用,品质、精度均有保障。
2、模仁又称型腔,即嵌入模胚模板内的成型模芯。
分为前模仁,后模仁,俗称前模(Cavity),后模(Core)。
为何要在模板内嵌入模仁呢?主要是为节约成本。
因为塑胶对模具的钢材特性有很高的要求,如硬度、耐腐蚀性、耐高温(热变形)等;而模胚的模板则无需太高的要求。
模仁硬度一般为45~65HRC,模胚的模板硬度30~45HRC;用作模仁的钢料每公斤可达RMB 200,而模胚的钢料一般只需RMB20~30元。
注:HRC为洛氏硬度。
3、唧嘴:Sprue。
注塑机炮筒的射胶嘴通过该装置将熔融的塑胶原料注入型腔。
4、滑块又称行位:Slider。
为顺利出模而必须使用的结构部件。
因为有些产品结构特殊,如有侧边有空,有倒扣(勾)等,需用行位才可出模。
5、斜顶:Angle-Lifter。
与行位相似,也是为顺利出模而必须使用的结构部件。
6、还有一些与模具有关的名词:分模线(P/L)、模具基准、缩水率(Shrinkage)、排位(Layout)、钢料、铜公(电极,其材质有铜、石墨等)、倒扣、运水、出模斜度(Draft angle)、冷料井、流道、注塑仿真、分模、出模、开&合模步骤、模号、抛光(省模)、软模、硬模、模具表面处理、试模(TEST MOLD)、改模、装模、交模等。
7、从上可看一套模具按其各部件的功能可细分为:流道系统、成型系统、温度调节系统、排气系统、顶出系统、开合模系统、复位系统。
塑胶模具结构设计

塑胶模具结构设计塑胶模具结构设计是制造业中至关重要的环节,它直接关系到产品的质量、生产效率和成本。
本文将围绕塑胶模具结构设计的基本原则、设计流程及注意事项进行详细阐述。
一、塑胶模具结构设计的基本原则1. 确保产品精度在设计塑胶模具时,要保证产品的尺寸精度和形状精度。
这要求设计师充分了解塑胶材料的收缩率、流动性等特性,并在模具设计中予以充分考虑。
2. 易于加工与装配模具结构应尽量简单,便于加工和装配。
复杂的设计不仅会增加制造成本,还可能影响模具的可靠性。
在设计过程中,要充分考虑模具零件的加工工艺性和装配顺序。
3. 高效生产塑胶模具结构设计应考虑生产效率,尽量减少生产过程中的辅助时间。
例如,通过优化流道设计、缩短冷却时间等措施,提高生产效率。
4. 安全可靠5. 维护方便模具在使用过程中难免会出现磨损、损坏等问题,设计时应考虑模具的维修便捷性,降低维护成本。
二、塑胶模具结构设计流程1. 分析产品结构在设计模具前,要对产品结构进行分析,了解产品的尺寸、形状、技术要求等,为模具设计提供依据。
2. 确定模具类型根据产品结构特点和生产要求,选择合适的模具类型,如单腔模具、多腔模具、热流道模具等。
3. 设计分型面分型面是模具闭合时,分离塑胶制品和浇注系统的界面。
设计分型面时要考虑产品的脱模斜度、外观质量等因素。
4. 设计浇注系统浇注系统包括主流道、分流道、浇口等部分,其设计直接影响到塑胶制品的质量。
设计时应关注流道截面积、长度、浇口位置等因素。
5. 设计冷却系统冷却系统对塑胶制品的质量和生产效率具有重要影响。
设计时要考虑冷却水路的布局、冷却水流量、冷却水温度等因素。
6. 设计顶出系统顶出系统的作用是在模具开模时,将制品从模具中顺利取出。
设计时要确保顶出力均匀、可靠,避免产品变形或损坏。
7. 绘制模具零件图及装配图三、塑胶模具结构设计注意事项1. 充分考虑塑胶材料的特性,如收缩率、流动性、热稳定性等。
2. 优化模具结构,提高生产效率,降低生产成本。
塑胶模具结构详解
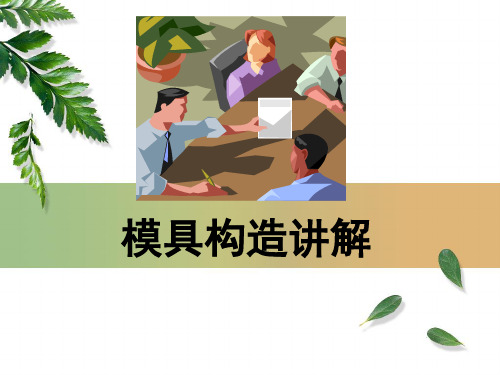
PA66 SPVC TPU PMMA PBT
1.0~2.5 1.5~2.5(2.0)* 1.2~2.0(1.6)* 0.5~0.7(0.5)* 1.3~2.2(1.6)*
ABS
1: ABS俗称超不碎胶,是一种高强度改性 PS 。
2:三元结构的ABS兼具各组分的多种固有特 性:丙烯 腈能使制品有较高的强度和表面 硬度,提高耐化学腐蚀性和耐热性;丁二 烯使聚合物有一定的柔顺性,使制件在低 温下具有一定的韧性和弹性、较高的冲击 强度而不易脆折;苯乙烯使分子链保持刚 性,使材质坚硬、带光泽,保留了良好的 电性能和热流动性,易于加工成型和染色。
(5)免胶料流动出现“跑道”效应、使胶件产生困 气、熔接痕现象:止口位胶片潜入浇口、避免表面 气烘胶片、胶柱入浇口,表面易产生气烘外表面 有气烘。
(7)避免浇口处产生气烘、蛇纹等现象。
(8)胶料流入方向、应使其流入型腔时、能沿着型腔 平行方向均匀地流入、避免胶料入浇口在长度方 向均匀地流入、避免变形成品为透明胶片成品不 直接入浇、避免表面气烘、蛇纹流动各向异性、 使胶件产生翘曲变形、应力开裂现象。
四:模具的内部结构设计
1:模具的胶位设计 胶件壁厚应均匀一致,避免突变和截面厚 薄悬殊的设计,否则会引起收缩不均, 使胶件表面产生缺陷。
2:胶件壁厚一般在1~6mm范围内,最常用 壁厚值为1.8~3mm,这都随胶件类型及 胶件大小而定。
2:模具骨位的设计、
(1) 胶件骨位其作用有增加强度、固定底面壳、 支撑架、按键导向等。 由于骨位与胶件壳体连 接处易产生外观收缩凹陷;所以、要求骨位厚 度应小于等于0.5t(t为胶件壁厚) 、一般骨位厚 度在0.8~1.2mm范围。
模具构造讲解
目录
一:模具的分类 二:模具的结构 三:常用注塑材质 四:模具的内部结构设计
图解说明塑胶模具的结构组成完整版

图解说明塑胶模具的结构组成HEN system office room 【HEN16H-HENS2AHENS8Q8-HENH1688】模具采购必备基础知识之二:塑胶模具的结构组成图解说明:模具注塑成型是批量生产某些形状复杂部件时用到的一种加工方法。
具体原理指:将受热融化的塑胶原材料由注塑机螺杆推进高压射入塑胶模具的模腔,经冷却固化后,得到塑胶成形产品。
塑胶模具由动模和定模两部分组成,动模安装在注射成型机的移动模板上,定模安装在注射成型机的固定模板上。
在注射成型时动模与定模闭合构成浇注系统和型腔,开模时动模和定模分离以便取出塑料制品。
塑胶模具的结构虽然由于塑胶品种和性能、塑胶制品的形状和结构以及注射机的类型等不同而可能千变万化,但是基本结构是一致的。
一、塑胶模具结构按功能分,主要由:浇注系统、调温系统、成型零件系统、排气系统、导向系统、顶出系统等组成。
其中浇注系统和成型零件是与塑料直接接触部分,并随塑料和制品而变化,是塑模中最复杂,变化最大,要求加工光洁度和精度最高的部分。
1.浇注系统:是指塑料从射嘴进入型腔前的流道部分,包括主流道、冷料穴、分流道和浇口等。
2.成型零件系统:是指构成制品形状的各种零件组合,包括动模、定模和型腔(凹模)、型芯(凸模)、成型杆等组成。
型芯形成制品的内表面,型腔(凹模)形成制品的外表面形状。
合模后型芯和型腔便构成了模具的型腔。
按工艺和制造要求,有时型芯和凹模由若干拼块组合而成,有时做成整体,仅在易损坏、难加工的部位采用镶件。
3.调温系统:为了满足注射工艺对模具温度的要求,需要有调温系统对模具的温度进行调节。
对于热塑性塑料用注塑模,主要是设计冷却系统使模具冷却(也可对模具进行加热)。
模具冷却的常用办法是在模具内开设冷却水通道,利用循环流动的冷却水带走模具的热量;模具的加热除可利用冷却水通热水或热油外,还可在模具内部和周围安装电加热元件。
4.排气系统:是为了将注射成型过程中型腔内的空气及塑胶融化所产生的气体排除到模具外而设立,排气不畅时制品表面会形成气痕(气纹)、烧焦等不良;塑胶模具的排气系统通常是在模具中开设的一种槽形出气口,用以排出原有型腔空气的及熔料带入的气体。
模具结构设计
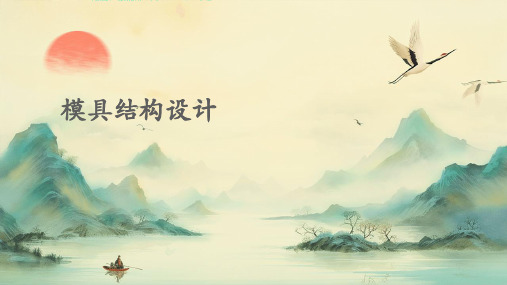
VS
详细描述
锻造模具结构设计需要考虑锻造工艺参数 、锻造材料特性、模具寿命和制造成本等 因素。在设计中,应注重优化模膛设计、 导向装置、顶出装置等部分,以确保锻造 生产的顺利进行和产品质量。
05
模具结构设计软件与应用
CAD/CAE/CAM技术在模具结构设计中的应用
01
CAD(计算机辅助 设计)
利用CAD软件进行模具的三维建 模,实现模具零件的精确设计和 定位。
低热膨胀系数
模具材料的热膨胀系数应尽可能小,以减小 温度变化对模具尺寸的影响。
04
模具结构设计实例分析
注塑模具结构设计实例
总结词
注塑模具结构设计是模具设计中的重要一环,需要考虑多方面因素,如塑考虑塑料的收缩率、流动性、结晶性等特性,以及模具的强度、刚度、寿命等因素。同时, 还需要考虑注塑机参数,如注射量、注射压力、模具安装尺寸等。在设计中,应注重优化浇注系统、冷却系统、 顶出系统等部分,以提高生产效率和产品质量。
浇注系统设计
浇注系统是模具的重要组成部分,其 设计的好坏直接影响到制品的质量和 生产效率。
浇注系统的结构形式有多种,应根据 制品的大小、形状和材料特性选择合 适的结构形式。
浇注系统的设计应遵循“快速、等高 、等流量”的原则,确保金属液能够 均匀地充满型腔。
浇注系统的尺寸和位置对制品的尺寸 精度和模具的加工制造也有很大影响, 需要仔细考虑。
02
CAE(计算机辅助 工程)
通过CAE技术对模具结构进行有 限元分析,预测模具的应力分布、 变形和寿命等性能。
03
CAM(计算机辅助 制造)
将模具设计数据导入CAM软件, 生成数控加工代码,控制机床完 成模具的加工制造。
常用模具结构设计软件介绍
模具基本结构简介之三板模

模具基本結構簡介之三板模1. 介绍在模具制造中,使用三板模是非常常见的一种模具形式。
三板模是由上模板、下模板和侧模板组成的,其中上模板和下模板通常用于形成模具内部的空腔,而侧模板则用于固定和定位上下模板。
本文将详细介绍三板模的基本结构和工作原理。
2. 上模板上模板是三板模中的一个关键部分,其主要作用是形成模具内部的空腔。
上模板通常由高强度的金属材料制成,如钢材。
在制造上模板时,通常需要经历下列工序:•材料选择:选择适合的金属材料,常用的有P20、H13等;•加工:根据设计要求,进行铣削、镟削、磨削等加工工艺;•加工表面:通过研磨等方法使上模板表面光滑度更高;•热处理:采用淬火、回火等热处理工艺提高材料的硬度和强度;•组装:将上模板与其他模具部件组装在一起。
上模板的设计需要考虑产品形状、尺寸和生产工艺等因素,以满足模具的使用要求。
3. 下模板下模板是三板模中另一个重要组成部分,其主要作用是提供模具内部空腔的下半部分。
下模板与上模板紧密配合,共同形成模具的工作空间。
下模板通常也是由高强度金属材料制成,制造工艺与上模板类似。
下模板与上模板、侧模板和模具座等部件一起组成了一个完整的模具系统。
下模板的设计需要考虑模具的定位槽、导柱、导套等结构,以确保模具的定位精度和稳定性。
侧模板是三板模中的一个重要组成部分,其主要作用是固定和定位上模板和下模板。
侧模板通常由金属材料制成,具有较高的刚性和稳定性。
在制造侧模板时,需要考虑到以下方面:•加工精度:侧模板的加工精度需要保证模具的定位精度,以便正确装配上下模板;•耐磨性:侧模板需要具备一定的耐磨性,以应对模具长时间使用时的摩擦和磨损;•安装便捷性:侧模板的安装需要方便快捷,以提高模具的装配效率。
侧模板与上模板和下模板之间通常通过螺栓、导柱等连接方式进行固定。
使用三板模进行模具工作时,需要按照以下步骤进行:1.安装侧模板:先将侧模板固定在适当的位置,确保与上模板和下模板的配合精度。
模具结构介绍范文
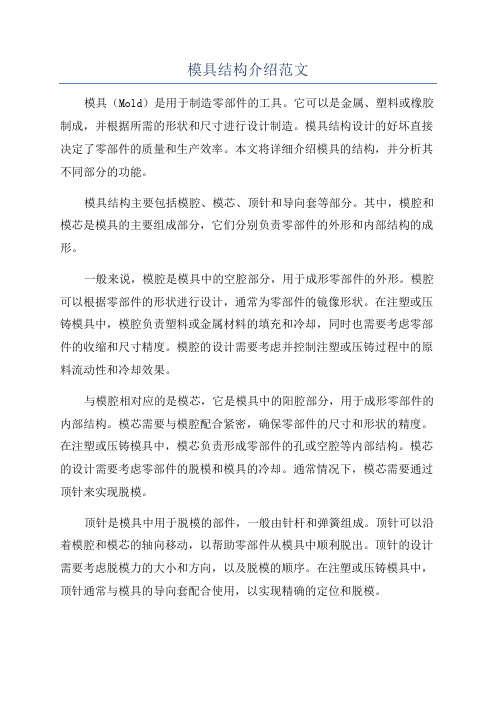
模具结构介绍范文模具(Mold)是用于制造零部件的工具。
它可以是金属、塑料或橡胶制成,并根据所需的形状和尺寸进行设计制造。
模具结构设计的好坏直接决定了零部件的质量和生产效率。
本文将详细介绍模具的结构,并分析其不同部分的功能。
模具结构主要包括模腔、模芯、顶针和导向套等部分。
其中,模腔和模芯是模具的主要组成部分,它们分别负责零部件的外形和内部结构的成形。
一般来说,模腔是模具中的空腔部分,用于成形零部件的外形。
模腔可以根据零部件的形状进行设计,通常为零部件的镜像形状。
在注塑或压铸模具中,模腔负责塑料或金属材料的填充和冷却,同时也需要考虑零部件的收缩和尺寸精度。
模腔的设计需要考虑并控制注塑或压铸过程中的原料流动性和冷却效果。
与模腔相对应的是模芯,它是模具中的阳腔部分,用于成形零部件的内部结构。
模芯需要与模腔配合紧密,确保零部件的尺寸和形状的精度。
在注塑或压铸模具中,模芯负责形成零部件的孔或空腔等内部结构。
模芯的设计需要考虑零部件的脱模和模具的冷却。
通常情况下,模芯需要通过顶针来实现脱模。
顶针是模具中用于脱模的部件,一般由针杆和弹簧组成。
顶针可以沿着模腔和模芯的轴向移动,以帮助零部件从模具中顺利脱出。
顶针的设计需要考虑脱模力的大小和方向,以及脱模的顺序。
在注塑或压铸模具中,顶针通常与模具的导向套配合使用,以实现精确的定位和脱模。
导向套是模具中的定位部件,用于确保模腔、模芯和顶针的正确定位。
导向套通常由导向柱和导向套轴承组成。
导向柱安装在模具的固定板上,导向套轴承则安装在模具的动态板或顶板上。
通过导向套的定位,模腔、模芯和顶针可以在注塑或压铸过程中正确移动和定位。
导向套的设计需要考虑导向的精度和防止卡死的措施。
除了上述主要组成部分外,模具结构还会涉及其他辅助部件,如冷却系统、排气系统和喷嘴等。
冷却系统用于控制模具的温度,以确保注塑或压铸过程中零部件的质量和尺寸的稳定性。
排气系统用于排除气泡或气体,以防止零部件出现气孔或热缩痕。
注塑模具结构最清晰讲解--图文含动画

模具结构概览
7
上固定板(S55C)
母模板(S55C)
母模仁 (P20\NAK80\420\S136 \SKD61\S13) 上定位块(SKD61) 塑胶制品 顶针(SKD61) 回位销(SUJ2) 导套(SUJ2) 斜顶(SKD61) 引导块(SKD61) 斜顶座(SKD61\SK3) 耐磨块(SKD61\SK3\PDS) 模脚(S55C) 下固定板(S55C)
编写目的,则是为了让年轻产品工程师更好认识注塑模具,了解模具包含哪些结构,模具结构的动作怎么进行,模具工件怎么 加工出来等;当遇到新项目设计时,能大致评估零件注塑的可行性和难度系数;当遇到零件变更或改善时,能大致评估改动的 模具工件以及调整费用。知其然并知所以然。
主讲人:
IVU
Ye
注塑模具结构讲解
01 产品分模/流道系统 02 模具结构概览 03 斜顶机构原理 04 滑块机构原理 05 冷却系统 06 产品顶出 07 典型模具零件加工及设备
2
IVU
Ye
产品分模
3
正面
背面 产品3D图
正面
背面 分模图
分模线,公母模仁结合面。 本产品的背面槽穴非常多,因此把 背面定为公模,顶针将从公模向外 顶出,易于脱模。
IVU
Ye
产品顶出
21
母模
复位弹簧
锁死合模状态(正面)
公模 锁死合模状态(侧面)
公模后退
开模过程:母模不动,公模后退一段距离不动,此时注塑机的推杆带动推板使得顶针一起向前,拉料杆保持不 动(倒钩结构可将产品向下拉扯),从而顺利将产品顶出。 合模过程:产品掉落后,注塑机推杆收回,推板在复位弹簧作用下回缩,公模向母模前进,进入下一个循环。
前模芯,与后模共同形成产品特征。 后模芯,与前模共同形成产品特征。
模具结构简介

10.顶针板导柱(EJECTOR GUIDE PIN)
11.顶针板导套(EJECTOR GUIDE BUSH)
12.定位销(CENTER SLEEVE) 13.垃圾钉(STOP DISC)
14.INTERLOCK
15. LIMIT SWITCH
模具基本结构简介之三板模
Wireless Business Unit
Wireless Business Unit
模具结构基本 简介
前言
Wireless Business Unit
模具基本结构一般分为两 板模﹐三板模和热流道三种。 模具的结构一般由客户或者依 据产品来决定的。
模具基本结构简介之两板模
Wireless Business Unit
两板模基本零件简介
Wireless Business Unit
三板模的运动过程
Wireless Business Unit
合模过程:当顶出板上有拉回机构时,在合模前,顶出板被注塑机強制 拉回。
(1)在注塑机地推动下,动模向定模运动,若頂出板沒有被预先拉 回,复位杆最先接触定模板,在反作用力下,顶出板在复位杆的带动下 回位.
(2)动模板压向定模板和弹料板,最后完全合紧,注塑机上的喷嘴 与模具上的浇口套密合,开始注塑. 这样就完成塑胶模具的整个运动周期.
2.浇口套(SPRUE BUSH)
材料CALMAX
3.支撑柱(SUPPORT PILLAR) 材料709
4.吊模块(TIE BAR)
材料S50C
5.限位块(STOPPER)
材料709
6.导柱(GUIDE PIN)
7.导套(GUIDE BUSH)
8.弹簧(SPRING)
9.复位杆(RETURN PIN)
模具基本结构及分类
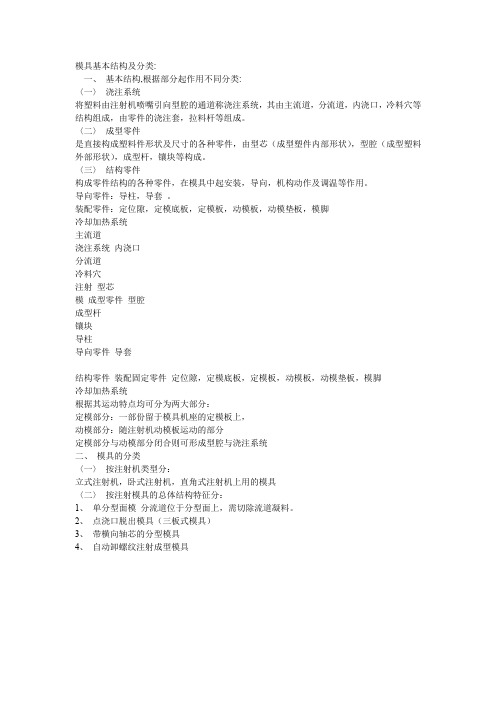
它是指构成模具结构的各种零件,包括:导向、脱模、抽芯以及分型的各种零件。如前后夹板、前后扣模板、承压板、承压柱、导向柱、脱模板、脱模杆及回程杆等。
1.导向部件
为了确保动模和定模在合模时能准确对中,在模具中必须设置导向部件。在注塑模中通常采用四组导柱与导套来组成导向不见,有时还需在动模和定模上分别设置互相吻合的内、外锥面来辅助定位。
D、便于制品与流道系统分离。浇口形状、尺寸和位置的设计取决于塑料的性质、制品的大小和结构。一般浇口的截面形状为矩形或圆形,截面积宜小而长度宜短,这不仅基于上述作用,还因为小浇口变大较容易,而大浇口缩小则很困难。浇口位置一般应选在制品最厚而又不影响外观的地方。浇口尺寸的设计应考虑到塑料熔体的性质。型腔它是模具中成型塑料制品的空间。用作构成型腔的组件统称为成型零件。各个成型零件常有专用名称。构成制品外形的成型零件称为凹模(又称阴模),构成制品内部形状(如孔、槽等)的称为型芯或凸模(又称阳模)。设计成型零件时首先要根据塑料的性能、制品的几何形状、尺寸公差和使用要求来确定型腔的总体结构。其次是根据确定的结构选择分型面、浇口和排气孔的位置以及脱模方式。最后则按控制品尺寸进行各零件的设计及确定各零件之间的组合方式。塑料熔体进入型腔时具有很高的压力,故成型零件要进行合理地选材及强度和刚度的校核。为保证塑料制品表面的光洁美观和容易脱模,凡与塑料接触的表面,其粗糙度Ra>0.32um,而且要耐腐蚀。成型零件一般都通过热处理来提高硬度,并选用耐腐蚀的钢材制造。
模具基本结构及分类:
一、基本结构,根据部分起作用不同分类:
〈一〉浇注系统
将塑料由注射机喷嘴引向型腔的通道称浇注系统,其由主流道,分流道,内浇口,冷料穴等结构组成,由零件的浇注套,拉料杆等组成。
- 1、下载文档前请自行甄别文档内容的完整性,平台不提供额外的编辑、内容补充、找答案等附加服务。
- 2、"仅部分预览"的文档,不可在线预览部分如存在完整性等问题,可反馈申请退款(可完整预览的文档不适用该条件!)。
- 3、如文档侵犯您的权益,请联系客服反馈,我们会尽快为您处理(人工客服工作时间:9:00-18:30)。
模具結構(塑模)功能解說﹕1.定位環﹕將模具正確的定位在射出機板上﹐同時使模具堅澆道對准射出機的噴嘴。
2.注口襯套﹕塑膠進入模具內部的通道。
3.上固定板﹕使母模部分可以固定在成型機上。
4.母模板﹕在模具的固定側。
5.母模仁﹕為便于塑件成型而鑲配于母模板內的模仁。
6.定位塊上﹕裝在母模板上﹐以利用母模板與公模板定位裝置﹐與定位塊下配合使用。
7.拔塊﹕拔動滑塊退位及強制壓迫滑面裝置。
8.壓板﹕組成滑塊槽的裝置。
9.導柱﹕公母模板導向及定位裝置。
10.滑塊﹕為處理成品之倒勾而設立的滑動裝置。
11.成品﹕母模仁與公模仁合模而產生的塑件。
12.回定銷﹕用于頂出板定位之用。
13.定位塊下﹕裝在公模板上﹐以利于母模板與公模板定位裝置﹐與定位塊上配合使用。
14.斜槽﹕使成品形成倒勾﹐易脫離。
15.模腳﹕用來控制頂針與斜銷的行程。
16.下固定板﹕使公模部分可以固定在成型機上。
17.公模仁﹕為便于塑件成型的鑲配于公模板內的模仁。
18.公模板﹕模具的可動側﹐通常設計成使產品容易頂出。
19.上頂出板﹕對頂什及堅澆道控制起回位作用。
20.下頂出板﹕對頂針及澆道拉料起定位作用。
21.支撐柱﹕位于承板之后﹐作為補強承板﹐防止變形用。
塑模成型<<模具結構原理及維修保養簡介>>講義一﹑模具結松﹕1.定位環﹕架模時使模具引料接頭與機台噴嘴對正之工具。
2.機器噴嘴與模具主流道相連接之零件。
3.母模板﹕承載母模心之板塊。
4.母模輔助板﹕輔助母模心之板塊。
5.導柱﹕與母模配合定位之零件。
6.導套﹕與公模導朮相配﹐使公母模對正之零件。
7.公模板﹕承載公模心之板塊。
8.公模輔助板﹕輔助公模固定公模心之板塊。
9.公模支承板﹕支承公模板與底板﹐使兩者之間有空間讓頂出板活動。
10.公模底板﹕使公模固在機台上﹐與公模形成整體之板塊。
11.頂針﹕使產品脫模之零件。
12.公母模心﹕成形面之零件。
13.頂出定位鎖﹕項出析后移動歸位銷。
14.彈簧﹕使頂出板或模板復位。
15.頂出板﹕分上下頂出板﹑固定頂針﹑受力時推動頂針前進。
引料接頭二﹑模具分類﹕1.按結松分類﹕1.1.三板模﹕由公模﹑母模及脫料板三部分組成。
1.2.兩板模﹕由公模﹑母模兩部分組成。
2.按產品系列分類(以本公司成型模具為例)﹐目前生產之模具有十大系列﹕2.1.ZIF﹕BASE﹑COVER﹑CAM.2.2.R/A SLOT1﹕COVER.SBC.Housing.2.3.R/M﹕DAUL Housing DAUL Pin BridgeFOLDABLE BASE ARMA ARMB FASTECK AASLO CKCELERON W/PIN RETERTION MOOULE R/M PIN.2.4.SLOT1:2.5.FSS﹕STANDOFF A/B SUPPORT A/B2.6.HSS﹕BASE TOPBAR2.7. SOJ﹕2.8.BTB:1.0﹑0.8﹑0.635﹑0.62.9.CARD BUS:2.10.PCMCIA﹕三﹑模具組立﹕維修與保養1.模具組立﹕(以兩板模為例)1.1.新模組立前備齊模具組立圖﹐檢驗每件模具零件是否齊全﹐尺寸﹑外觀是否符合要求。
1.2.清理桌面﹐模具零件﹐按件號擺放整齊﹐歸類。
1.3.將倒角﹐去毛刺模仁加工全符合要求﹐配好下模仁﹐從模心開始組配。
注意配合間隙﹐導柱導套組立入公模模板中。
1.4.塞水孔﹐注意螺絲長短適度﹐緊固力度控制﹕3mm螺絲扭力2kg﹐4mm螺絲扭力4kg﹐5mm螺絲扭力8kg﹐6mm螺絲扭力10kg。
1.5.公模板與公模輔助板組立﹐注意O形環裝妥﹐螺絲緊固。
1.6.將模心定位于公模板內﹐緊好砌塊﹐螺絲緊固﹐公模平放桌面﹐成品面向下。
1.7.裝頂出板彈簧﹑定位鎖﹐將上頂出板置于公模上﹐緊固限位螺絲。
1.8.插入頂什﹐注意頂針倒角﹑修配﹐在頂針孔內滑動自如。
1.9.蓋上下頂出板﹐注意墊圈位置﹐緊固螺絲﹐導套放放置。
1.10.檢查頂出板頂出狀況﹐蓋上公模底板﹐支承板﹑緊固螺絲﹑裝進出水管接頭﹐檢查通水狀況。
1.11.組立母模與公模配合﹐注意模面是否有間隙﹐組立完畢。
1.12.試模﹑樣品與藍圖對照。
2.模具維修﹕2.1.修模前確認產品不良部位﹐不良部位模仁件號。
2.2.確定修模方式﹐換新件或換舊件加工﹐換新軟件需確認備品。
2.3.下模具主修模區﹐用天車將模具吊至桌面。
2.4.分開公母模﹐在不良部位用色筆作上記號。
2.5.模仁拆卸﹐取出損壞模仁﹐確定是否能回收使用。
2.6.領用新件﹐將倒角拋光部分加工到位。
2.7.模仁組立﹐注意配合狀況﹐對照產品或組立圖﹐有無裝錯。
2.8.模具組立﹐裝模心﹑裝頂針﹑頂出板﹑底板注意其方向。
2.9.檢查模面﹐再次確認有無裝錯模仁﹑頂針。
2.10.確認修模后﹐產品是否OK﹐填寫模修記錄。
3.模具保養﹕3.1.周期性保養﹕模具連續生產﹐達到保養周期時定期下模清理﹐除去油污﹑料屑﹐更換磨損模仁零件﹐上油﹑拋光﹐清理排氣孔﹐作細部清理后上機生產﹐確認保養效果。
3.2.生產量到周期﹕模具生產量到后確認有無到達保養周期﹐已到保養周期則作周期性保養﹔未到則作上回前模具保養﹐作模面防鏽﹐除鏽﹐項出部分之潤滑﹐防鏽﹐循環水路清理﹐模具外表防鏽處理后上架待產。
3.3.填寫保養記錄。
現代塑模成型塑料有兩種﹐主要的加工方法﹕注射成型及墊壓。
其總重量的大約 32%是用注射成型的﹐36&是用熱壓成型的。
一﹑塑件加工的主要作業﹕(三個)1.將塑料加熱到壓力下能夠流動時的溫度。
通常同時加熱并軟化固體顆粒﹐直到成為高溫而又具有均勻溫度和粘度的熔體為止。
目前﹐這個過程是在裝有往復式螺杆的注塑機的料筒里進行的。
螺杆提供了材料加熱攪拌所要求的機械作用。
這個全過程稱作材料的塑化(增塑)。
2.使塑料在由注射機保持其閉合的模具中固化。
從注塑機的注射缸里射出的熔化的塑料液體﹐通過各種流道送入模具的型腔中﹐最終在模腔的限制下形成所需的工件。
由于驅動射料杆的液壓回限制及模具內充填和冷卻作用的復雜流程﹐使這一看來簡單的作業變得復雜了。
3.對熱性塑料﹐停止加熱(加熱是使料熔化)﹐使塑件固化﹐保壓冷卻定形成為所需的制品后﹐開啟模具取出塑件。
二﹑注塑成形系統的基本元件是﹕1.混合器2.干燥器3.料斗4.計量儀5.塑化器6.注射器7.冷卻器 8.頂出裝置注塑機注塑機﹕是將粉未﹐粒料成回用原材料轉化﹐處理并成為所需形狀的機器。
注塑過程是加熱塑料材料為主﹐其熔化﹐然后迫使該熔體注入模具中﹐并在模具中冷卻和固化。
一﹑合模系統朮語﹕1.合模系統朮語﹕注塑機的一部份﹐在該部位固定模具并提打開和閉合模具的運作和力﹐以及在注射期間保持模具閉合的力。
當模具在水平方向閉合時﹐合模機構就秒作垂直鎖模。
這個裝置也可提供塑模塑作業中﹐必需的其他有效功能。
2.動模板或模板﹕即向定分移動的模機構的一部分。
用螺栓磁針動模固定在動模板上。
通常﹐動模上帶有頂杜孔和安裝模具的螺栓孔或”T”型槽。
3.定模板或模板﹕用螺栓將是模固定位的鎖模裝置的固定部分。
定模板通常帶有安裝模具的螺栓孔或”T”型槽。
此外﹐是模板通包括有將模具在模板上定武鋼和使的注道襯套與注射機構的注料嘴對准的設施。
4.拉杆﹑條佚﹑梁﹕當模具閉合時﹐這些合模機構中的受拉零件推動驅動機構。
安們也用作動模板的導向零件。
5.頂杆﹕在鎖模裝置中﹐驅動模具中一個機構頂出模塑件的構件。
頂出作用力可由一個或功敗垂成個固定在動模板上的由液壓或氣體動的缸體提供﹐或由動模板的開模行程機械提供。
6.合液壓式鎖模裝置﹕由直接連接到動模板上的液壓缸驅動的鎖緊裝置。
液壓通常直接用手打開或關閉模具﹐并提供鎖模力﹐以保持模具在注塑期間的閉合。
7.肘杆或鎖模裝置(液壓驅動﹑機械驅動)﹕帶有直接連接動模板上肘杆機構的鎖模裝置。
一個液壓缸或某個機構驅勸裝置連接到肘杆系統中﹐以發出開模和閉模力﹐并保持注射期間的合模力。
在注射期間保持模具閉合的鎖模力是由肘杆的機械效益提供的。
8.慢速開模﹕注射機中一個裝置﹐是為模具初始打開期間使模板慢速移動一段可調整的距離而設計的。
9.慢速閉模﹕注射機中一個裝置﹐是為兩個模面接觸之前﹐在可調距離內慢速移動模板而設計的。
10.慢速敞開﹕注射楓葉的一個裝置﹐是為鎖模裝置到達其最大開啟位置之前﹐慢速移動一段可調整的距離而設計的。
這個程序經常用于在機械頂出條件下減小沖擊作用﹐它有時作頂出或開模緩沖。
11.合模行程間斷﹕閉模行程完全停止﹐以允許閉模行程完成之前的輔助作業。
12.開模行程間斷﹕合模打開行程完全停止﹐以允許啟模行程完成之前的輔助作業。
13.合模前置閉合﹕機器電路中的一個元件﹐以允計合模完全打開﹐然合閉合至預定位置。
常用于使頂杆機構退回﹐以便能夠將鑲件放入模具中。
14.低壓閉模﹕機器中的一個裝置﹐降低合模周期中的合模力。
較低的合模力使模面之間因零件卡住所引起的模具損壞的危險達到最小。
當模具有障礙物時﹐該元件也保証分模處的間隔。
二﹑注射系統朮語﹕1.注射塑化裝置﹕注射機的一個部件﹐該部件將固態的塑料原料通過加熱轉化成均勻的液態。
該裝置使材料保持設定的溫度﹐并迫使材料通過注射裝置的注嘴流入模具。
2.射料杆部件﹕注射和塑化裝置的組合﹐在該部件中﹐加熱筒固定在射料杆和模具之間﹐該筒用熱傳遞加熱塑料。
在每一次進程中﹐射料杆將未熔化的塑料原料推入筒中﹐這繼而又迫使機筒前端的熔融塑料通過注嘴。
3.雙級射料機構﹕注射和塑化裝置﹐在該裝置的一個獨立機構中完成塑化。
后者是由機筒組成提﹐以通過熱偉導加熱塑料原料﹐并用射料杆推動未熔化塑料進入要筒﹐再進入第二級注射裝置。
該注射裝置具有保壓﹑計量和注射機筒的綜合作用。
在注射周期中﹐射料杆迫使塑料熔體從注身中通過注嘴射出。
4.雙料螺杆部件﹕注射和塑化裝置﹕注射和塑化裝置﹐在該裝置的一個獨立機構中完成塑化﹐該獨立機構是由螺杆擠出器件組成的﹐以便材料塑化并迫使其進入第二級注射裝置。
該注射裝置其有保壓﹑計量和注射機筒的綜合作用。
在注射周期中﹐射料杆迫使塑料熔體從注射機筒通過注嘴流出。
5.往復式螺杆﹕注射和塑化裝置的組合﹐該裝置中帶有往復式螺杆的擠出器件﹐常常用于塑化材料。
材料注射到模具中可以直接擠入模睦的方式﹐或用往復式螺杆徐為射料杆或兩者結。
當螺杆成為射料杆時﹐該裝置具有保壓﹑計量和注射機筒的作用。
6.可調注射速度﹕在最大和最小注射速率間無級控制調整﹐注射速率的能力。
7.預裝﹕預裝也稱為”填允”﹐是萬事俱備助射料杆的多次行程﹐通過預裝置或允填額處的材料到加熱筒﹐用于增加注射杆每次輸出容量的方法(僅適用于注射杆裝置類型的注射機)。
8.射料杆前置位置﹕通過限位開關﹐也就是通過壓力開關來控制的射料杆位置。
因此﹐注射期間總的生程縮短了﹐射料縮短整個周期(僅適于射料杆裝置類型的注塑機)。