制氧分子筛的使用
医用分子筛中心制氧设备操作说明书
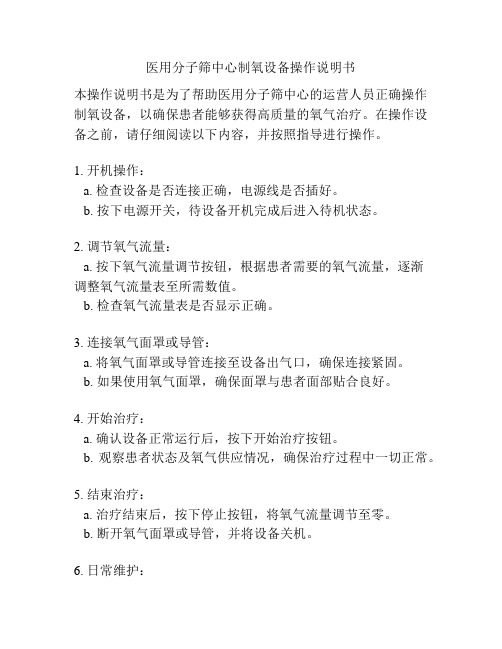
医用分子筛中心制氧设备操作说明书
本操作说明书是为了帮助医用分子筛中心的运营人员正确操作制氧设备,以确保患者能够获得高质量的氧气治疗。
在操作设备之前,请仔细阅读以下内容,并按照指导进行操作。
1. 开机操作:
a. 检查设备是否连接正确,电源线是否插好。
b. 按下电源开关,待设备开机完成后进入待机状态。
2. 调节氧气流量:
a. 按下氧气流量调节按钮,根据患者需要的氧气流量,逐渐
调整氧气流量表至所需数值。
b. 检查氧气流量表是否显示正确。
3. 连接氧气面罩或导管:
a. 将氧气面罩或导管连接至设备出气口,确保连接紧固。
b. 如果使用氧气面罩,确保面罩与患者面部贴合良好。
4. 开始治疗:
a. 确认设备正常运行后,按下开始治疗按钮。
b. 观察患者状态及氧气供应情况,确保治疗过程中一切正常。
5. 结束治疗:
a. 治疗结束后,按下停止按钮,将氧气流量调节至零。
b. 断开氧气面罩或导管,并将设备关机。
6. 日常维护:
a. 每天使用后,清洁设备表面,并定期清洁出气口及氧气面罩。
b. 每周检查设备内部是否有异物或污垢,并进行必要的清洁
和维护。
请注意,本操作说明书仅供参考,具体操作时请结合设备说明书进行操作。
如有任何疑问或意外情况,请立即停止使用设备,并联系相关专业人员进行检修或处理。
感谢您的配合与使用。
医用分子筛制氧机使用说明书
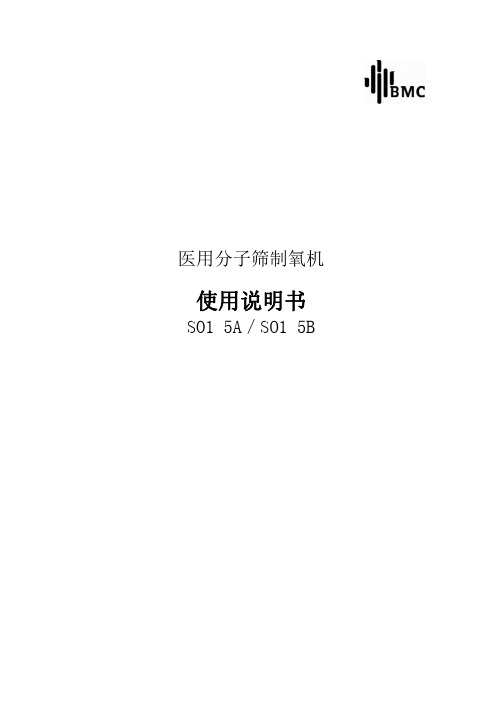
医用分子筛制氧机使用说明书SO15A/SO15B概述本说明书提供SO1医用分子筛制氧机(以下简称制氧机)的安装、使用及日常维护等方面的指导。
患者或操作者在使用本制氧机之前应详细阅读本说明书,严格按本说明书中的说明和提示操作,以确保安全有效。
本使用说明书版权归本公司所有,包括内容摘要,任何复制行为,只有在经过本公司书面同意后方可进行。
任何侵权行为,本公司有权根据国家版权法之规定,通过法律途径维护本公司的合法权益。
本说明书中的所有说明并不能替代医生的治疗方案。
请将此说明书放在制氧机附近,以便快速查阅。
本说明书中的“危险”“警告”“注意”和“小心”等词均涉及使用本设备时的“安全性”和“有效性”,具体含义如下:危险:紧急安全信息可能会引起伤害或死亡。
警告:如有违背,对患者或操作者有可能造成伤害。
注意:如有违背,有可能对设备造成损坏或发生故障。
小心:一般涉及操作上的提示,如有违背,有可能影响制氧机工作的有效性或使用上的方便性。
注册证编号:津械注准20222080363技术要求编号:津械注准20222080363生产许可证编号:津药监械生产许20140444号注册人/生产企业名称:天津怡和嘉业医疗科技有限公司注册人/生产企业住所:天津市武清开发区新兴路1号4-3生产地址:1.天津市武清开发区新兴路1号4-2北侧和中段2.天津市武清开发区新兴路1号4-33.武清开发区创业总部基地C20号楼售后服务:天津怡和嘉业医疗科技有限公司全国售后服务部电话:4008004235邮政编码:301700电话:************传真:************转810目录重要安全信息 (1)1.预期用途与禁忌症 (3)1.1预期用途 (3)1.2预期使用环境 (4)1.3禁忌症 (4)1.4工作原理 (4)1.4.1工作原理 (4)1.4.2制氧机电路连接示意图: (4)1.4.3气路连接示意图简介 (5)2.简介 (5)2.1开箱清单 (5)2.2产品结构及功能 (6)2.3产品结构图 (6)2.3.1SO15A型产品结构图 (6)2.3.2SO15A型产品显示内容示意图 (8)2.3.3SO15B型产品结构图 (9)2.3.4SO15B型产品显示内容示意图 (11)2.4标识说明 (12)2.5不同型号的产品描述 (13)3.操作说明 (14)3.1拆箱检查 (14)3.2放置制氧机 (14)3.3开机前的准备 (14)3.3.1松解压缩机捆绑带 (14)3.3.2安装湿化杯 (15)3.3.3连接鼻氧管 (16)3.4开机 (16)3.4.1SO15A型制氧机开机 (16)3.4.2SO15B型制氧机开机 (17)3.5雾化操作 (19)3.6遥控功能(适用于SO15B型) (19)3.7定时时间设定(适用于SO15B型) (20)3.8关机 (20)3.9报警 (20)3.9.1报警分级和说明 (21)3.9.2视觉报警 (21)3.9.3听觉报警 (21)3.9.4报警信息及其描述 (22)4.清洁和保养 (24)4.1清洗外壳 (25)4.2清洁湿化杯 (25)4.3清洁过滤网棉 (25)4.4更换进气过滤器 (26)4.5清洗一次性使用雾化吸入器 (26)4.6消毒 (26)5.维修细则 (27)5.1免责声明 (27)5.2保修时间与条件 (27)6.技术说明 (28)6.1技术支持 (28)6.2出口标称压力为0时 (28)6.3不同气压条件下 (28)7.废弃处置 (29)8.故障排除 (29)9.性能指标 (32)9.1主要技术指标 (32)9.2其他参数 (33)9.3正常工作环境 (33)9.4运输及存储环境 (34)10.电磁兼容性信息 (34)重要安全信息危险信息危险严禁在使用或靠近本产品时吸烟!请勿把火柴、燃着的香烟及任何引燃源放置在制氧机所在的房间内。
分子筛制氧机工作原理

分子筛制氧机工作原理
分子筛制氧机是一种通过分子筛技术来制取高纯度氧气的设备。
它主要由分子
筛吸附系统、脱附系统、压缩系统和控制系统等部分组成。
其工作原理是利用分子筛对氮气和氧气的吸附性能不同,通过循环吸附和脱附过程来实现氧气的制取。
首先,空气经过预处理系统去除其中的水分和杂质,然后进入分子筛吸附系统。
在这个系统中,空气通过分子筛床,分子筛对其中的氮气进行吸附,而氧气则通过分子筛床,进入下一个阶段。
这样,氮气被分离出来,而富含氧气的气体被送入脱附系统。
在脱附系统中,通过降低分子筛床的压力和加热的方式,促使已经吸附了氮气
的分子筛释放出吸附的氮气,实现氮气的脱附。
这样,分子筛床重新恢复到吸附状态,同时产生高纯度的氧气。
随后,经过压缩系统的处理,高纯度的氧气被压缩成为气体或液体状态,以满
足不同领域的使用需求。
控制系统则负责监控和调节整个制氧过程,确保设备的稳定运行和高效制氧。
分子筛制氧机工作原理简单清晰,通过分子筛对氮气和氧气的选择性吸附和脱
附过程,实现了氧气的高效制取。
相比于传统的制氧方法,分子筛制氧机具有能耗低、操作简单、制氧效率高等优点,因此在医疗、生活、工业等领域有着广泛的应用前景。
总的来说,分子筛制氧机是一种通过分子筛技术来制取高纯度氧气的设备,其
工作原理是利用分子筛对氮气和氧气的吸附性能不同,通过循环吸附和脱附过程来实现氧气的制取。
这种制氧方法具有能耗低、操作简单、制氧效率高等优点,因此在医疗、生活、工业等领域有着广泛的应用前景。
制氧机工作原理及使用方法

制氧机工作原理及使用方法制氧机是一种能够将空气中的氧气浓缩提供给患有呼吸系统疾病或缺氧症状的患者使用的医疗设备。
它的工作原理是通过物理方法将空气中的氧气与其他气体分离,从而获得高浓度的氧气供给患者使用。
制氧机主要由压缩机、分子筛、冷凝器、过滤器和控制系统等组成。
当制氧机开始工作时,首先由压缩机将空气压缩并送入分子筛中。
分子筛是一种具有特殊结构的材料,可以通过吸附和解吸的方式将氮气等其他气体分离出去,只保留氧气。
经过分子筛分离后,氧气会进入冷凝器进一步冷却,以提高氧气的纯度。
然后,通过过滤器去除空气中的杂质,最后经过控制系统控制氧气的流量和浓度,供给患者使用。
使用制氧机时,首先需要将机器连接到电源,并确保电源稳定。
然后,打开制氧机的电源开关,待机器启动后,根据医生的建议调整好所需的氧气流量和浓度。
一般来说,医生会根据患者的具体情况和需要来确定合适的氧气流量和浓度。
接下来,将导氧管连接到制氧机的出气口,并将另一端连接到患者的鼻子或口罩上。
使用过程中,患者应始终保持正常呼吸,并保持机器的通风口畅通,以确保氧气供应的顺畅和稳定。
制氧机的使用方法需要根据具体的机型和说明书来进行操作。
在使用过程中,患者应定期清洗和更换导氧管、过滤器等附件,以保持机器的卫生和正常运行。
此外,制氧机的使用应遵循医生的指导和建议,并定期进行体检和复查,以确保治疗效果和患者的健康状况。
制氧机通过物理分离的方式将空气中的氧气提纯后供给患者使用,是一种常用的医疗设备。
它的工作原理简单明了,使用方法也相对简单。
对于患有呼吸系统疾病或缺氧症状的患者来说,制氧机能够有效地提供所需的高浓度氧气,帮助他们改善呼吸功能,促进康复。
因此,制氧机在医疗领域中具有重要的作用,并广泛应用于临床治疗和家庭护理中。
psa制氧机 分子筛容量及产氧量计算

psa制氧机分子筛容量及产氧量计算以PSA制氧机分子筛容量及产氧量计算为主题,本文将介绍PSA 制氧机的工作原理、分子筛的作用、分子筛容量及产氧量的计算方法。
PSA制氧机是一种通过压力摄取吸附(Pressure Swing Adsorption,简称PSA)技术制取高纯度氧气的设备。
其工作原理是利用分子筛对气体的吸附选择性,将空气中的氮气、水蒸气等杂质分离,从而得到高纯度的氧气。
分子筛是PSA制氧机中的核心部件,它是一种由微孔和中孔组成的多孔性材料。
分子筛的微孔大小可以选择性地吸附不同大小分子的气体,例如,氮气的分子比氧气大,因此分子筛可以选择性吸附氮气,从而实现氮气和氧气的分离。
分子筛容量是指分子筛单位体积所能吸附的气体量。
通常用单位重量的吸附剂所能吸附的气体量来表示,单位为毫升/克。
分子筛容量的大小与分子筛的孔径大小、材料性质以及工作温度等因素有关。
一般来说,分子筛的孔径越小,吸附能力越强,分子筛容量也就越大。
产氧量是指PSA制氧机每小时所能产生的氧气量。
产氧量的计算与分子筛容量以及设备的工作效率有关。
一般来说,产氧量等于分子筛的吸附容量乘以设备的工作效率。
设备的工作效率可以用氮气浓度和氧气流量之比来表示。
例如,设备的工作效率为0.8,氮气浓度为2%,氧气流量为1000升/小时,则产氧量为0.8乘以分子筛的吸附容量乘以氮气流量的百分比,即0.8乘以1000乘以2%等于16升/小时。
在实际应用中,PSA制氧机的分子筛容量和产氧量需要根据具体需求进行计算和选择。
一般来说,分子筛容量越大,产氧量也就越大,但同时也会增加设备的体积和成本。
因此,在选择PSA制氧机时,需要综合考虑氧气的纯度要求、产氧量需求以及设备的尺寸和成本等因素。
PSA制氧机的分子筛容量和产氧量是实现高纯度氧气生产的关键参数。
通过合理计算和选择,可以满足不同应用场景对氧气的需求,并实现高效、可靠的氧气供应。
液氧与分子筛制氧

液氧与分子筛制氧摘要:一、液氧与分子筛制氧的定义与原理二、液氧与分子筛制氧的纯度差异三、液氧与分子筛制氧的应用领域四、液氧与分子筛制氧的优缺点比较五、结论正文:一、液氧与分子筛制氧的定义与原理液氧,顾名思义,是指氧气在低温下被压缩成液态的形式。
液氧的制作过程相对简单,通常通过深冷技术将氧气压缩并冷却至零下183 摄氏度左右,使其变为液态。
在医疗领域,液氧被广泛应用于呼吸机、氧气瓶等设备中,以满足病人对氧气的需求。
分子筛制氧,则是利用分子筛的吸附- 解析原理来制取氧气。
分子筛是一种具有微孔结构的晶态物质,其微孔能够吸附气体分子。
在制氧过程中,分子筛将空气中的氧气与其他气体分子分离出来,从而制得纯度较高的氧气。
二、液氧与分子筛制氧的纯度差异液氧的纯度通常较高,可以达到99.5% 以上,甚至可以达到99.9%。
这是因为在深冷技术下,氧气被压缩并冷却,几乎不含有任何杂质。
而分子筛制氧的纯度受分子筛吸附选择性的影响,一般不会太高,通常在90% 左右。
尽管如此,分子筛制氧的纯度仍能满足许多应用场景的需求。
三、液氧与分子筛制氧的应用领域液氧在医疗领域的应用十分广泛,如前所述,其主要用于呼吸机、氧气瓶等设备。
此外,液氧还被用于工业生产、科学研究、航空航天等领域。
分子筛制氧在医疗领域的应用也越来越广泛,特别是在急诊室、手术室等对氧气需求量较大的场所。
此外,分子筛制氧还被广泛应用于工业生产、农业种植、水产养殖等领域。
四、液氧与分子筛制氧的优缺点比较液氧的优点在于纯度高,稳定性好,能够满足医疗领域对高纯度氧气的需求。
然而,液氧的缺点在于其运输和储存需要特殊的设备和条件,且成本较高。
分子筛制氧的优点在于生产成本较低,纯度可以满足一般应用场景的需求,且便于运输和储存。
然而,分子筛制氧的纯度相对较低,在医疗领域可能无法满足一些高要求的应用。
五、结论总的来说,液氧与分子筛制氧各有优缺点,二者在纯度、应用领域等方面存在差异。
分子筛制氧器的原理
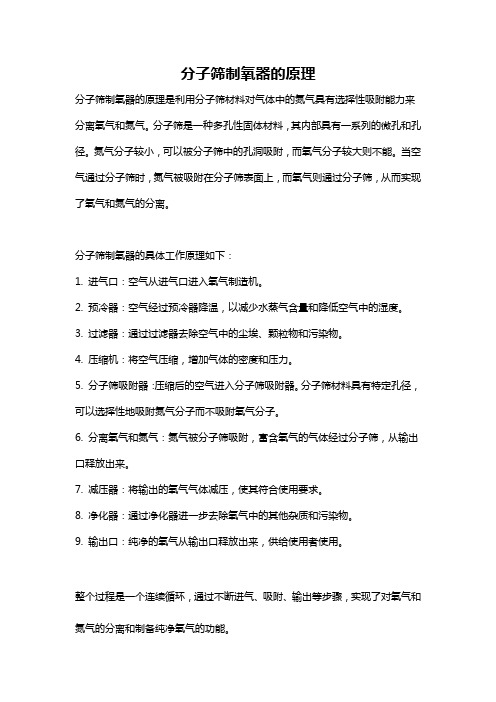
分子筛制氧器的原理
分子筛制氧器的原理是利用分子筛材料对气体中的氮气具有选择性吸附能力来分离氧气和氮气。
分子筛是一种多孔性固体材料,其内部具有一系列的微孔和孔径。
氮气分子较小,可以被分子筛中的孔洞吸附,而氧气分子较大则不能。
当空气通过分子筛时,氮气被吸附在分子筛表面上,而氧气则通过分子筛,从而实现了氧气和氮气的分离。
分子筛制氧器的具体工作原理如下:
1. 进气口:空气从进气口进入氧气制造机。
2. 预冷器:空气经过预冷器降温,以减少水蒸气含量和降低空气中的湿度。
3. 过滤器:通过过滤器去除空气中的尘埃、颗粒物和污染物。
4. 压缩机:将空气压缩,增加气体的密度和压力。
5. 分子筛吸附器:压缩后的空气进入分子筛吸附器。
分子筛材料具有特定孔径,可以选择性地吸附氮气分子而不吸附氧气分子。
6. 分离氧气和氮气:氮气被分子筛吸附,富含氧气的气体经过分子筛,从输出口释放出来。
7. 减压器:将输出的氧气气体减压,使其符合使用要求。
8. 净化器:通过净化器进一步去除氧气中的其他杂质和污染物。
9. 输出口:纯净的氧气从输出口释放出来,供给使用者使用。
整个过程是一个连续循环,通过不断进气、吸附、输出等步骤,实现了对氧气和氮气的分离和制备纯净氧气的功能。
分子筛制氧原理
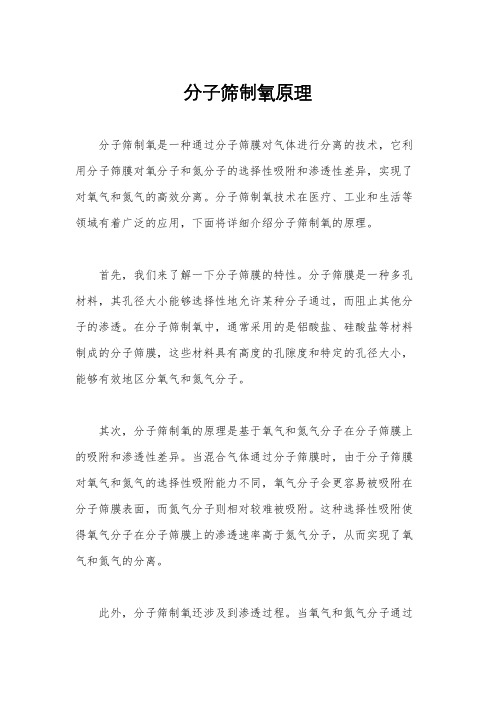
分子筛制氧原理
分子筛制氧是一种通过分子筛膜对气体进行分离的技术,它利用分子筛膜对氧分子和氮分子的选择性吸附和渗透性差异,实现了对氧气和氮气的高效分离。
分子筛制氧技术在医疗、工业和生活等领域有着广泛的应用,下面将详细介绍分子筛制氧的原理。
首先,我们来了解一下分子筛膜的特性。
分子筛膜是一种多孔材料,其孔径大小能够选择性地允许某种分子通过,而阻止其他分子的渗透。
在分子筛制氧中,通常采用的是铝酸盐、硅酸盐等材料制成的分子筛膜,这些材料具有高度的孔隙度和特定的孔径大小,能够有效地区分氧气和氮气分子。
其次,分子筛制氧的原理是基于氧气和氮气分子在分子筛膜上的吸附和渗透性差异。
当混合气体通过分子筛膜时,由于分子筛膜对氧气和氮气的选择性吸附能力不同,氧气分子会更容易被吸附在分子筛膜表面,而氮气分子则相对较难被吸附。
这种选择性吸附使得氧气分子在分子筛膜上的渗透速率高于氮气分子,从而实现了氧气和氮气的分离。
此外,分子筛制氧还涉及到渗透过程。
当氧气和氮气分子通过
分子筛膜时,由于氧气分子在分子筛膜上的渗透速率较快,而氮气
分子的渗透速率较慢,因此在一定时间内,氧气和氮气分子会分别
通过分子筛膜,实现了氧气和氮气的有效分离。
总的来说,分子筛制氧的原理是基于分子筛膜对氧气和氮气的
选择性吸附和渗透性差异,通过这种原理,可以实现对氧气和氮气
的高效分离。
分子筛制氧技术在医疗领域可以用于制取高纯度氧气,用于医疗氧疗;在工业领域可以用于氧气分离和制取;在生活领域
可以用于制取氧气气源等。
分子筛制氧技术的应用将会为人们的生
活和生产带来更多便利和效益。
医用分子筛制氧机工作流程

医用分子筛制氧机工作流程下载提示:该文档是本店铺精心编制而成的,希望大家下载后,能够帮助大家解决实际问题。
文档下载后可定制修改,请根据实际需要进行调整和使用,谢谢!本店铺为大家提供各种类型的实用资料,如教育随笔、日记赏析、句子摘抄、古诗大全、经典美文、话题作文、工作总结、词语解析、文案摘录、其他资料等等,想了解不同资料格式和写法,敬请关注!Download tips: This document is carefully compiled by this editor. I hope that after you download it, it can help you solve practical problems. The document can be customized and modified after downloading, please adjust and use it according to actual needs, thank you! In addition, this shop provides you with various types of practical materials, such as educational essays, diary appreciation, sentence excerpts, ancient poems, classic articles, topic composition, work summary, word parsing, copy excerpts, other materials and so on, want to know different data formats and writing methods, please pay attention!医用分子筛制氧机工作流程随着现代医疗技术的不断发展,医用分子筛制氧机作为一种重要的医疗设备,被广泛应用于临床医疗中。
分子筛制氧机原理

分子筛制氧机原理
分子筛制氧机利用分子筛技术来提纯空气中的氧气。
它的工作原理基于气体分子的大小和亲和力的不同。
首先,空气被引入分子筛制氧机的进气口。
然后,通过一个过滤器,空气中的灰尘、杂质和污染物颗粒被去除,只有纯净的气体通过。
接下来,纯净的气体进入分子筛器。
分子筛器中包含许多小孔和通道,这些孔径只允许较小的气体分子(如氧气)通过,而较大的气体分子(如氮气和水蒸汽)被阻挡。
分子筛器中的分子筛材料通常是一种特殊的沸石,具有高度规则的晶格结构。
这种结构可以选择性地吸附氮气和水蒸汽,而不吸附氧气。
当气体通过分子筛器时,氮气和水蒸汽会被吸附在分子筛材料的表面上,而氧气则通过孔径较大的通道流出。
最后,通过一个排气口,纯净的氧气被释放出来供人们使用。
分子筛制氧机可以根据气体的分子大小和亲和力的差异实现对氧气的分离和纯化,从而提供给用户纯净的氧气。
这种技术广泛应用于医疗领域,以满足患者需要额外氧气的需求。
分子筛 制氧

分子筛制氧是一种利用分子筛材料将空气中的氧气分离出来的方法。
分子筛是一种具有微孔结构的材料,其孔径大小可以通过控制合成条件来调节。
当分子筛材料吸附了空气中的氮气等杂质后,氧气就可以通过分子筛材料的微孔进入到另一个容器中,从而实现氧气的分离。
分子筛制氧的具体步骤如下:
1.空气压缩:将压缩机压缩的空气送入分子筛制氧装置中。
2.分子筛吸附:将分子筛材料装入分子筛制氧装置中,通过分子筛材料的微孔将空气中的氮气等杂质吸附在分子筛材料表面。
3.氧气分离:将经过分子筛材料吸附的空气送入氧气分离室中,氧气通过分子筛材料的微孔进入另一个容器中,而氮气等杂质则留在分子筛材料中。
4.再生:当分子筛材料吸附的杂质达到一定程度时,需要对分子筛材料进行再生,将吸附的杂质通过加热等方法释放出来,以保证分子筛材料的吸附效果。
分子筛制氧具有分离效率高、操作简单、能耗低等优点,广泛应用于医疗、工业、科研等领域。
医用分子筛制氧设备使用管理制度

医用分子筛制氧设备使用管理制度一、引言随着现代社会的不断发展和生活水平的提高,人们对医疗保健的需求越来越高。
而在医疗机构中,制氧设备成为了重要的治疗手段,能够为需要氧疗的患者提供所需氧气。
因此,对于医用分子筛制氧设备的使用及管理,需制定一整套制度,以确保安全性、稳定性和有效性。
二、设备分析医用分子筛制氧设备主要由压缩空气系统、分子筛吸附系统、冷却脱湿系统、调压缩氧系统、控制系统等部分组成。
上述每个系统对于氧生成及制备过程具有不可替代的作用。
为了保证设备的稳定性和长期持续性,应制定具体的使用管理制度。
三、使用控制为使设备使用更加稳定和有效,需制定如下使用管理制度。
1.设备安装:设备安装中需选择技术水平高、经验丰富的技术人员,并由专业部门进行验收确认合格后,方可进行开机启动。
2.日常检查:设备在运行中需定期进行检查和保养,定期检查应包括设备部件的情况,如气体流量、气压稳定性、机器温度、设备运行最佳氧的浓度等信息。
3.运行时间:设备在运行状态下最好不要超过30分钟,否则需要进行充分的休息,减少设备的磨损和消耗。
同时,设备需要进行定期清理和消毒,并及时更换消耗品,如分子筛和过滤器等。
4.运输存储:设备在运输过程中应注意防止碰撞和损坏,运用到不同地区时,应做好高温、低温、潮湿等环境的保护,同时在存储过程中也需要定期对设备进行保护,并加强消毒处理。
四、应急处置针对突发情况下的应急处置,应制定如下应急管理制度。
1.突发故障:设备在运行中如出现故障,我们应该及时排查故障,及时处理问题。
如故障无法自行排除,则需要寻求技术服务商提供帮助或及时更换部件。
2.突发事故:如设备出现突发性故障,可能对旁侧环境造成一定的影响和伤害。
在此时,应迅速切断电源、阀门,保护好患者,同时调用专业救援队伍及时开展处理工作。
五、总结针对医用分子筛制氧设备的使用管理,本文根据实际情况制定了一系列的管理制度。
为保证设备的安全性、稳定性和有效性,需要不断加强对设备的检查和保养,并加强对应急处置措施的推广和落实。
分子筛制氧原理

分子筛制氧原理
分子筛是一种具有微孔结构的固体物质,它可以根据分子的大小和极性选择性地吸附分离气体分子。
分子筛制氧就是利用这种特性来分离空气中的氧气。
那么,分子筛制氧的原理是什么呢?
首先,我们需要了解分子筛的结构。
分子筛通常是由硅铝酸盐或硅酸盐组成的晶体结构,具有均匀的微孔大小。
这些微孔可以让小分子通过,而大分子则无法通过。
这就为分子筛选择性吸附气体分子提供了基础。
在分子筛制氧的过程中,空气首先被压缩成液态,然后通过加热蒸发成气态。
接下来,气态的空气会通过装有分子筛的吸附塔。
在吸附塔中,分子筛会选择性地吸附氮气和其他杂质气体,而将氧气通过。
这样,就实现了氧气的分离。
分子筛选择性吸附气体的原理是基于气体分子的大小和极性。
由于氮气分子比氧气分子稍大,分子筛可以更容易地吸附氮气分子,而将较小的氧气分子通过。
这就实现了氧气的纯度提高。
分子筛制氧的原理简单而高效,因此被广泛应用于工业生产和医疗设备中。
通过这种方法,可以获得高纯度的氧气,满足不同领域的需求。
总的来说,分子筛制氧的原理是利用分子筛的微孔结构和选择性吸附特性,将氮气和其他杂质气体吸附下来,而将纯净的氧气通过。
这种方法简单高效,可以获得高纯度的氧气,具有广泛的应用前景。
分子筛制氧机的使用说明

分子筛制氧机的使用说明
分子筛制氧机是一种用于制取高纯度氧气的设备,通常用于医疗、制造和其他工业领域。
以下是该设备的使用说明:
1. 设备准备,首先确保分子筛制氧机处于水平稳定的位置,并
且通风良好。
接着检查设备的电源线和氧气输出管路是否连接牢固,无泄漏。
2. 启动操作,接通电源,并按照设备说明书上的指示打开主电
源开关。
待设备启动完成后,观察氧气输出压力表,确保压力稳定
在正常范围内。
3. 设置参数,根据需要调节设备上的流量调节阀,以设定所需
的氧气流量。
通常,医用氧气流量为每分钟2-10升,而工业用途可
能需要更大的流量。
4. 使用氧气,将氧气导管连接至需要供氧的设备或人体,确保
连接牢固。
然后打开氧气输出阀门,开始供氧。
在使用过程中,要
时刻观察氧气压力表和流量表,确保氧气供应正常。
5. 关机操作,使用完毕后,先关闭氧气输出阀门,然后关闭主
电源开关,断开电源。
最后关闭氧气输入阀门,排空管路中的氧气,以确保安全。
此外,使用分子筛制氧机时,还需注意以下事项:
定期清洁设备,保持设备清洁卫生,以确保氧气的纯度和安全。
注意设备的维护保养,定期检查滤网、分子筛等部件,确保设
备正常运行。
在使用过程中,如发现设备有异常噪音、漏氧等情况,应及时
停止使用,并联系专业维修人员进行检修。
以上是分子筛制氧机的基本使用说明,希望对你有所帮助。
如
果有其他问题,欢迎继续咨询。
分子筛制氧机原理

分子筛制氧机原理分子筛制氧机是一种利用分子筛技术来分离氧气和空气中其他成分的设备,它能够将空气中的氧气浓缩至更高的纯度,以满足特定场合对高纯度氧气的需求。
那么,分子筛制氧机是如何实现这一功能的呢?接下来,我们将从原理方面进行介绍。
首先,我们需要了解分子筛的基本原理。
分子筛是一种多孔性材料,其内部的孔道尺寸非常精确,只有特定大小的分子才能通过。
这种特性使得分子筛能够对气体混合物进行分离,将其中的某种特定分子分离出来。
在分子筛制氧机中,空气首先被吸入设备内部,经过预处理后进入分子筛模块。
在分子筛模块中,通过一系列的物理和化学过程,分子筛材料能够选择性地将氧气分子从空气中分离出来,而将其他气体分子留在外部。
这样,经过分子筛处理后的气体中,氧气的浓度得到了显著提高。
分子筛制氧机的原理基于分子筛对气体分子的选择性吸附和排斥作用。
当空气通过分子筛时,由于分子筛的孔径大小适合氧气分子,因此氧气分子能够被吸附到分子筛内部,而其他气体分子则无法通过分子筛的筛选作用,从而被排斥出去。
这样,分子筛制氧机就能够实现对氧气的高效分离和浓缩。
除了分子筛的选择性吸附和排斥作用外,分子筛制氧机还利用了压力摩尔分数效应来实现氧气的分离。
在分子筛模块内,通过控制气体的压力和温度,可以使得氧气分子在分子筛内部被吸附和释放的速度不同,从而实现对氧气的分离和纯化。
总的来说,分子筛制氧机通过分子筛的选择性吸附和排斥作用,以及压力摩尔分数效应,实现了对空气中氧气的高效分离和浓缩。
这种原理使得分子筛制氧机成为一种重要的氧气生产设备,广泛应用于医疗、工业、环保等领域,为人们提供了高纯度的氧气资源。
制氧分子筛使用温度

制氧分子筛使用温度制氧分子筛是一种用于制取高纯度氧气的重要技术装置,其使用温度是影响其性能和效果的重要因素之一。
本文将就制氧分子筛的使用温度进行详细介绍,包括其影响因素、适宜温度范围、温度调节方法以及对分子筛性能的影响等方面进行探讨。
首先,制氧分子筛的使用温度受到多种因素的影响。
其中,分子筛的种类是决定其使用温度的重要因素之一。
不同种类的分子筛具有不同的热稳定性,因此其适宜使用的温度范围也会有所不同。
此外,制氧分子筛所处的工作环境、应用场景以及制氧过程中的气体流速等因素也会对其使用温度产生一定的影响。
其次,制氧分子筛的适宜使用温度范围通常在200-600摄氏度之间。
在这个温度范围内,分子筛能够保持较好的吸附性能和分离效果。
当温度超过600摄氏度时,分子筛的结构可能会发生破坏,从而影响其吸附和分离性能。
因此,在实际应用中,需要根据具体的分子筛种类和工作环境来确定最佳的使用温度。
为了调节制氧分子筛的使用温度,可以采取多种方法。
一种常用的方法是通过控制加热源的温度来实现温度调节。
例如,可以通过加热炉、电热丝等设备对制氧分子筛进行加热,以达到所需的使用温度。
此外,还可以通过调节气体流速、控制冷却系统等手段来实现温度的调节和控制。
制氧分子筛的使用温度对其性能和效果有着重要的影响。
首先,适宜的使用温度可以确保分子筛的吸附性能和分离效果。
在适宜的温度范围内,分子筛能够充分吸附气体中的杂质,从而提高制氧的纯度和效率。
另外,合理的使用温度还可以延长分子筛的使用寿命,减少维护和更换成本。
然而,如果分子筛的使用温度过高或过低,都会对其性能产生负面影响。
当温度过高时,分子筛的结构可能发生变形、破坏,导致其吸附和分离性能下降。
当温度过低时,分子筛的吸附速度和分离效果也会受到限制。
因此,在使用制氧分子筛时,应该根据具体情况合理选择使用温度,以确保其性能和效果的最佳表现。
综上所述,制氧分子筛的使用温度是影响其性能和效果的重要因素之一。
制氧分子筛的使用

制氧分⼦筛的使⽤锂低硅制氧分⼦筛的应⽤摘要:⾼效锂低硅制氧分⼦筛的应⽤为⼤型制氧装置的发展提供了条件。
在利⽤⾼效锂低硅分⼦筛进⾏装置设计时应注意温度、吸附速率、吸附压⼒的选择,通过实验,选择合适的修正系数,可以充分的发挥锂低硅制氧分⼦筛的⾼吸附容量、⾼分离系数的特性。
关键词:⾼效锂低硅制氧分⼦筛,吸附速率,吸附温度,吸附压⼒⼀、综述近年来,由于制氧分⼦筛吸附剂的开发利⽤和⼯艺流程的不断改进,使创始于20世纪60年代的变压吸附空分制氧技术得到快速发展,与深冷空分装置相⽐,变压吸附空分制氧过程具有启动时间短和开停车⽅便、能耗较⼩和运⾏成本低、⾃动化程度⾼和维护简单、占地⾯积⼩和⼟建费⽤低等特点,因⽽,变压吸附制氧占据越来越多的市场份额,尤其是在节能降耗的富氧燃烧领域内应⽤越来越⼴。
变压吸附⽓体分离技术的关键是吸附剂的选择,吸附剂的性能直接影响最终分离效果,甚⾄影响⼯艺步骤的选择和变压吸附的⽣命⼒。
通常变压吸附空分制氧使⽤A型和X型分⼦筛,但因其分离选择性较低,对氮⽓吸附量⼩,束缚了PSA制氧技术的发展。
基于这种情况,国内外许多公司都在积极进⾏新型富氧吸附剂的研究开发和推⼴。
锂低硅系列制氧分⼦筛就是⽬前国内外许多公司都在积极开发和推⼴新⼀代制氧分⼦筛。
洛阳建龙化⼯有限公司对LiLSX分⼦筛的研发始于2005,历经6年,经过⼤量的实验,采⽤多层移动床固相交换法进⾏Li+交换,交换率⼤于99%,Li+的利⽤率100%,同时⾃⾏研发设计的特殊结构的焙烧炉试机成功并应⽤于⼯业化⽣产,解决了LiLSX分⼦筛焙烧结构极易被破坏的难题,⽣产出的吸附剂不仅保持了⾼的氮吸附性能,同时具有良好的机械强度和极低⽔含量。
2010年,JLOX系列制氧分⼦筛从新建的⽣产线上很快的⾛向国内并进⼊国际市场。
2011年1⽉,JLOX-100制氧分⼦筛在湖南冷⽔江闪星锑业有限公司制氧站的改造项⽬中被采⽤,这个改造项⽬是⼀次意义⾮同寻常的改造。
- 1、下载文档前请自行甄别文档内容的完整性,平台不提供额外的编辑、内容补充、找答案等附加服务。
- 2、"仅部分预览"的文档,不可在线预览部分如存在完整性等问题,可反馈申请退款(可完整预览的文档不适用该条件!)。
- 3、如文档侵犯您的权益,请联系客服反馈,我们会尽快为您处理(人工客服工作时间:9:00-18:30)。
锂低硅制氧分子筛的应用
摘要:高效锂低硅制氧分子筛的应用为大型制氧装置的发展提供了条件。
在利用高效锂低硅分子筛进行装置设计时应注意温度、吸附速率、吸附压力的选择,通过实验,选择合适的修正系数,可以充分的发挥锂低硅制氧分子筛的高吸附容量、高分离系数的特性。
关键词:高效锂低硅制氧分子筛,吸附速率,吸附温度,吸附压力
一、综述
近年来,由于制氧分子筛吸附剂的开发利用和工艺流程的不断改进,使创始于20世纪60年代的变压吸附空分制氧技术得到快速发展,与深冷空分装置相比,变压吸附空分制氧过程具有启动时间短和开停车方便、能耗较小和运行成本低、自动化程度高和维护简单、占地面积小和土建费用低等特点,因而,变压吸附制氧占据越来越多的市场份额,尤其是在节能降耗的富氧燃烧领域内应用越来越广。
变压吸附气体分离技术的关键是吸附剂的选择,吸附剂的性能直接影响最终分离效果,甚至影响工艺步骤的选择和变压吸附的生命力。
通常变压吸附空分制氧使用A型和X型分子筛,但因其分离选择性较低,对氮气吸附量小,束缚了PSA制氧技术的发展。
基于这种情况,国内外许多公司都在积极进行新型富氧吸附剂的研究开发和推广。
锂低硅系列制氧分子筛就是目前国内外许多公司都在积极开发和推广新一代制氧分子筛。
洛阳建龙化工有限公司对LiLSX分子筛的研发始于2005,历经6年,经过大量的实验,采用多层移动床固相交换法进行Li+交换,交换率大于99%,Li+的利用率100%,同时自行研发设计的特殊结构的焙烧炉试机成功并应用于工业化生产,解决了LiLSX分子筛焙烧结构极易被破坏的难题,生产出的吸附剂不仅保持了高的氮吸附性能,同时具有良好的机械强度和极低水含量。
2010年,JLOX系列制氧分子筛从新建的生产线上很快的走向国内并进入国际市场。
2011年1月,JLOX-100制氧分子筛在湖南冷水江闪星锑业有限公司制氧站的改造项目中被采用,这个改造项目是一次意义非同寻常的改造。
湖南闪星锑业公司在原矿冶炼炉上采用富氧燃烧技术,运行效果显著,决定扩大应用范围,然而,2008年制作的VPSA制氧装置产氧量却制约着富氧燃烧应用范围的扩大。
2010年12月13日闪星锑业公司发出了制氧站改造招标书,12月19日与承标方签订了对制氧装置进行提高产能的改造的协议,产能由原
1200Nm3/h(100%O
2)改为1500Nm3/h(100%O
2
)。
改造要求:一是制氧装置不改动,或者是少
动;二是设备不增加,即动力负荷不改变;三是只给15天的时间,原因是已在运行的富氧燃烧冶炼炉不能停,只能在年终停产检修的时间内改造完。
改造方案经甲方和乙方充分评估,决定采用我公司制造的锂低硅制氧分子筛,把原填装的47吨Ca5A分子筛换为20吨LiLSX分子筛。
2011年1月7日改造更换分子筛完毕,1月8日,十分顺利的启动了改造后的制氧装置,氧气流量达到了1500Nm3/h(100%O
2
)以上,所有冶炼炉并入富氧燃烧工艺流程,氧气站输出的氧气完全满足了富氧燃烧的要求,超出了改造设计要求。
使冶炼炉日处理矿石量比给改造前提高了20%以上。
这个改造令人鼓舞,闪星锑业公司对我公司锂低硅制氧分子筛给予高度的评价。
这个改造使人们认识到技术进步的意义——LiLSX制氧分子筛在节能降耗上的的作用!
大家知道,变压吸附制氧的基础是分子筛。
高效锂低硅制氧分子筛的平衡吸附容量和分离系数是传统的富氧吸附剂2倍以上(见表1),吸附速率也远高于传统富氧吸附剂,这就为高效制氧设备的发展提供了良好的基础,为制氧装置大型化的发展提供了技术支持。
随着制氧装置大型化工艺流程和操作条件的进步,我国大型变压吸附空分制氧技术接近国际先进水平,目前,国内制造的变压吸附制氧吸附塔直径已高达6米,单套装置的最大产氧能力已大于10000Nm3/h。
大型制氧装置,对稳定和提高制氧装置的经济技术指标提出了更高的要求。
众所周知,变压吸附制氧的核心是分子筛,了解和掌握不同的厂家的锂低硅分子筛的特性对提高变压吸附制氧装置的效率,降低能耗是值得关注的事情。
二、LiLSX分子筛在PSA装置上的应用
以下结合本公司JLOX 系列LiLSX 制氧分子筛以及同行业内其他公司LiLSX 分子筛的性能比较,从吸附速率、吸附压力和温度三个方面阐述在PSA 制氧装置设计过程中对吸附剂的选择和使用,以及PSA 工艺流程参数的确定。
变压吸附的基本参数是吸附压力、解析压力、传质速率,吸附压力影响着传质速率,传质速率影响着传质区的大小,传质区的大小又决定着吸附床的吸附剂是否被有效的利用,因而,吸附剂的传质速率决定着变压吸附制氧装置的效率与产率。
1、传质速率与产率
q
q
q e
c e
c
c a
a 吸附负荷曲线
b
流出曲线
图1
通过对分子筛的测试,可以得到图1所示曲线, 即吸附前沿曲线和流出曲线,这是每 一个变压吸附设计者熟悉和关心的图形,根据曲线可以了解吸附剂的性能。
我们希望得 到的曲线波幅小一些,波幅愈小,吸附床内吸附剂有效利用率就愈高。
上图W 是吸附饱和区,V +U 是传质区,V 是传质区已吸附区,U 传质区未吸附区,g 点是穿透点,Z 是吸附床总高。
从图中可以看到传质区愈大,流出曲线波幅愈大,反之,传质区愈小,流出曲线的波幅也愈小。
在极端理想的情况下,即吸附速度无限大的时候,吸附曲线和流出曲线成垂线,床内吸附剂都被有效利用。
很显然,我们希望传质区短,不仅吸附剂最大限度的有效利用,而且整个装置切换周期短,产率得到最大值,这样可以使单位能耗更加理想。
传质区的长度为:)
1)((00
k t t t Z
Z A -+=
其中k 是传质区未饱和分率,k=U/(U +V ),
从上式可以看出,吸附速率是关系到传质区大小的关键因素。
吸附过程的吸附速率由内扩散的扩散速率决定,而内扩散的过程是分子扩散过程,就变压吸附制氧系统来讲,氮气分子扩散到沸石分子筛中的过程是Knudsen型扩散,显然与孔隙率有关。
孔隙率是影响吸附速率的重要因素之一。
采用相同的N2吸附容量、相同的LiLSX原粉,以不同的成型工艺,得到不同堆集密度(反映不同孔隙率)的相同尺寸的分子筛球,在同一台动态评价装上测得结果如下表:
表2
反映孔隙率不同的堆比重相差0.05(g/ml),产率却相差31.84%。
数据清楚地显示了孔隙率对产率的影响,从所测试得到的流出曲线图上看,波幅增长,说明吸附速率随堆比重的增加而下降。
解决办法就是提高孔隙率。
作为制氧装置设计者,在分子筛吸附容量、颗粒直径相同的条件下,要注意对孔隙率的选择。
2、吸附压力与产率
吸附压力是影响传质速度的一个重要因素。
吸附压力高,虽然可以增加分子筛吸附速度,但是由于解吸是吸热过程,因相对压力高,解吸过程会造成解吸塔床层“冷冻”现象,解吸塔温度降低,反过来影响吸附动力学,吸附平衡将会变得非常慢,致使传质速度慢,这样只能使吸附前沿曲线波幅加长,吸附剂利用率大幅下降。
因而,吸附压力不能过高,吸附压力与解吸压力差尽可能的低一些。
经测试,JLOX锂低硅制氧分子筛低分压条件下吸附性能十分良好(见表3),这就有可能采用高真空度解吸、低吸附压力工艺来降低压差,降低传质层的高度,提高吸附剂的利用率,提高产率。
国内某公司在大型锂分子筛制氧装置上采用-70KPa的解吸压力、40KPa的吸附压力操作工艺,吸附剂的利用率非常高,能耗可控制在0.35Nm3/KW·h。
表3
3、温度与产率
我公司JLOX-103制氧分子筛在美国麦克仪器公司制造的GEMINI Ⅶ2390型全自动比表面积及孔隙度分析仪上进行不同温度下的N2平衡吸附量测试,与国外产品在相同的设备上以相同的测试条件测得数据比较,如下表:
表4
由上表可以看出,不同的工艺生产的锂低硅分子筛吸附剂对温度的敏感性不一样,锂低硅制氧分子筛随着吸附温度的增高,吸附容量下降。
气体分子的扩散速率与温度的平方根成正比,因而温度升高,吸附速率和解吸速率升高,但是,吸附容量却随着温度的升高而减小,如果吸附周期不变,则吸附床层的吸附质流速一
定,势必将在吸附周期内出现吸附质穿透的现象,从而产品纯度降低。
当吸附温度在一定的范围内降低时,吸附速率减小,吸附容量虽然增加,但是在吸附床的吸附质流速一定的条件下,会导致氮气还未被充分吸附就流到床层的出口,也使得产品纯度下降。
同时解吸速度因温度降低而变慢,解吸不充分,这样产率与纯度自然下降。
这两种情况都会严重的影响产率,因而,在设计制氧装置时,应选择对温度敏感性小一点的分子筛,在计算时,必须考虑温度的影响,根据吸附容量修正吸附质流速、吸附压力等诸因素。
三、结论:
1、锂低硅制氧分子筛促进了变压吸附制氧的快速发展,对提高制氧产率、降低能耗具有重要意义。
2、锂低硅制氧分子筛在使用时应考虑吸附速率、压力和温度的影响,通过实验,选择合适的修正系数,可以充分的发挥锂低硅制氧分子筛的高吸附容量、高分离系数的特性,大幅度的提高变压吸附制氧的产率,降低能耗。
3、洛阳市建龙化工有限公司生产的锂低硅制氧分子筛具有吸附性能好,分离系数高,产品的综合性能达到国际先进水平。