关键控制点控制程序标准版本
ISO22000:2018关键控制点确定控制程序
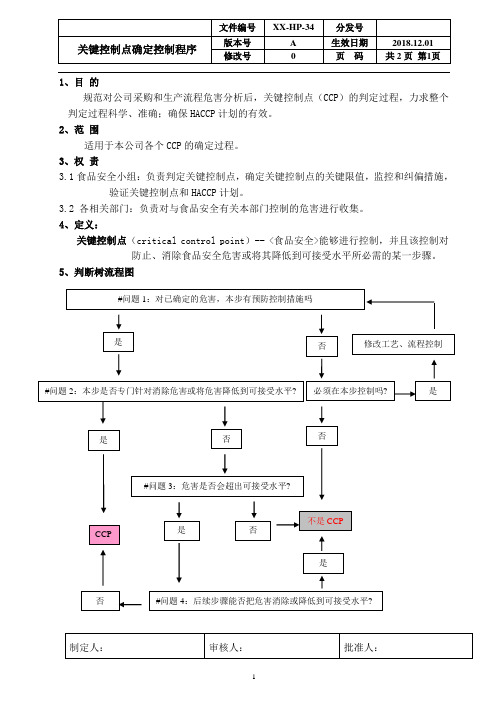
11、目 的规范对公司采购和生产流程危害分析后,关键控制点(CCP )的判定过程,力求整个判定过程科学、准确;确保HACCP 计划的有效。
2、范 围适用于本公司各个CCP 的确定过程。
3、权 责3.1食品安全小组:负责判定关键控制点,确定关键控制点的关键限值,监控和纠偏措施,验证关键控制点和HACCP 计划。
3.2 各相关部门:负责对与食品安全有关本部门控制的危害进行收集。
4、定义:关键控制点(critical control point )-- <食品安全>能够进行控制,并且该控制对防止、消除食品安全危害或将其降低到可接受水平所必需的某一步骤。
5、判断树流程图判断树(Decision tree)是四个连续问题组成:a)问题1.在加工过程中存在的确定的显著危害,是否在这步或后部的工序中有预防措施?如果回答,有,回答问题2。
如果回答无,则回答是否有必要在这步控制点食品安全危害。
如果回答"NO",则不是CCP。
如果回答"YES",则说明加工工艺,原料或原因不能控制保证必要的食品安全,应重新改进产品等设计,包括预防措施。
另外,只有显著危害,而又没有预防止措施,则不是CCP,则需改进。
在有些情况,的确没有合适的预防措施。
在这种情况进一步说明HACCP不能保证100%的食品安全。
b)问题2.这一加工步骤是否能消除可能发生的显著危害或降低到一定水平(可接受水平)?如果回答"YES"。
还应考虑一下,这步是否最佳,如果是,则是CCP。
如果回答"NO",则回答问题3。
c)问题3.是否已确定的危害能影响判定产品可接受水平,或者这些危害会增到使产品不可接受水平?如果回答"NO",则不是"CCP"。
主要考虑危害的污染或界入,即是否存在或是否要发生或是否要增加? 如果"YES" ,回答问题4。
关键控制点控制程序
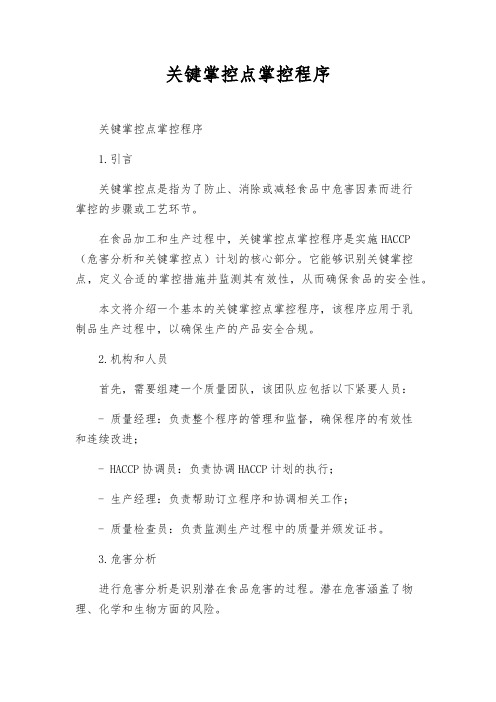
关键掌控点掌控程序关键掌控点掌控程序1.引言关键掌控点是指为了防止、消除或减轻食品中危害因素而进行掌控的步骤或工艺环节。
在食品加工和生产过程中,关键掌控点掌控程序是实施HACCP (危害分析和关键掌控点)计划的核心部分。
它能够识别关键掌控点,定义合适的掌控措施并监测其有效性,从而确保食品的安全性。
本文将介绍一个基本的关键掌控点掌控程序,该程序应用于乳制品生产过程中,以确保生产的产品安全合规。
2.机构和人员首先,需要组建一个质量团队,该团队应包括以下紧要人员:- 质量经理:负责整个程序的管理和监督,确保程序的有效性和连续改进;- HACCP协调员:负责协调HACCP计划的执行;- 生产经理:负责帮助订立程序和协调相关工作;- 质量检查员:负责监测生产过程中的质量并颁发证书。
3.危害分析进行危害分析是识别潜在食品危害的过程。
潜在危害涵盖了物理、化学和生物方面的风险。
在乳制品生产中,潜在危害包括但不限于以下几个方面:- 微生物:包括细菌、霉菌和病毒等,重要来自原材料、工装和人员;- 化学污染:包括严重的污染、污染物过量和不正常的添加;- 物理污染:包括异物、金属碎片和刀片等。
4.确定关键掌控点基于危害分析,可以确定至少一个或多个关键掌控点。
通常,一个关键掌控点是指在一个阶段或一系列步骤中能够有效地防止、除去或减轻危害的工艺步骤。
在乳制品生产中,可能需要确定以下关键掌控点:- 原材料接收:确保原材料符合产品要求;- 加工程序:包括搅拌、加热和冷却等过程;- 包装:确保产品不受到污染,和适当的保存和包装;- 清洗和消毒程序:确保设备和场地清洁、卫生并除去污染。
5.订立监测程序对于每个关键掌控点,需要订立相应的监测程序。
监测程序应涵盖以下几个方面:- 监测频率:应依据关键掌控点的紧要性和潜在危害的等级确定监测频率;- 抽样计划:抽样量、抽样地点、分析标准和方法;- 监测记录:记录应按规定的程序记录,并应包括样品编号、监测日期、监测员和结果。
关键工序质量控制点控制程序

中铁十一局集团桥梁有限公司咸安制梁场关键质量控制点控制程序《关键质量控制点控制程序》主要包括下列内容:1、目的2、适用范围 03、主要引用标准 04、箱梁预制关键质量控制点 04.1箱梁预制的关键质量点 04。
2关键质量控制要点 04.2.1 钢筋闪光对焊施工质量控制点 04.2。
2预应力孔道及保护层厚度控制 (1)4.2.2.1预应力孔道控制 (1)4.2.2。
2保护层厚度控制 (1)4。
2.3混凝土施工质量控制点 (2)4.2。
3。
1原材料控制 (2)4.2。
3.2计量控制 (2)4。
2。
3。
3浇筑检查 (2)4.2。
3。
4取样检查 (2)4。
2.3.5混凝土入模温度控制 (3)4。
2.3.6混凝土浇筑控制 (3)4.2.3.7混凝土养护检查 (3)4.2.3。
8混凝土养护控制 (4)4.2。
3。
9模板检验控制程序 (4)4.2.4张拉质量控制要点控制程序 (4)4。
2.4。
1钢绞线及相关附件 (4)4.2。
4。
2钢绞线数目 (5)4。
2。
4。
3油压千斤顶与油表校正报告 (5)4。
2.4.4后张法预应力施张检查 (5)4.2.4。
5梁体变形检查 (5)4.2.5管道压浆施工质量控制要点控制程序 (5)4。
2.5.1原材料控制 (5)4.2.5。
2计量控制 (5)4.2。
5.3施工检查 (6)4。
2.5。
4取样检查 (6)关键质量控制点控制程序1、目的通过本程序和相关文件的控制旨在对箱梁预制施工各关键质量控制点的施工进行有效的控制、管理和改进,以确保产品符合设计要求,达到预期的质量目标,满足工程质量总目标的要求。
2、适用范围本程序适用于中铁十一局集团桥梁有限公司咸安制梁场箱梁预制施工全过程。
3、主要引用标准TB10210-2001《铁路混凝土与砌体工程施工规范》JGJ18-2003《钢筋焊接及验收规程》TB10415—2007《铁路桥涵工程施工质量验收标准》TB10424—2007《铁路混凝土与砌体工程施工质量验收标准》科技基[2005]101号《客运专线高性能混凝土暂行技术条件》客运专线预应力混凝土预制梁暂行技术条件企业内控标准4、箱梁预制关键工序及质量控制点4.1 箱梁预制的关键工序箱梁预制施工的关键工序有:钢筋闪光对焊;预应力孔道及保护层;混凝土配制、拌和、浇筑、养护、强度;张拉;管道压浆.以上工序只能依据依时间、仪器、仪表、试验报告等判定并由具有合格资质的人员进行作业。
关键控制点控制程序标准范本
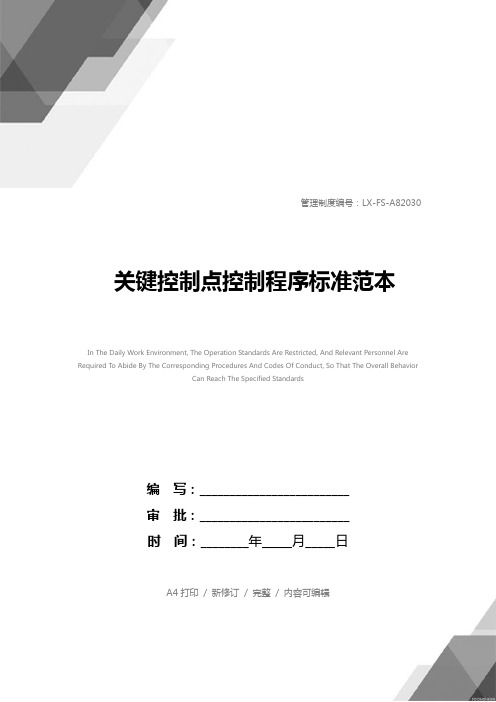
管理制度编号:LX-FS-A82030 关键控制点控制程序标准范本In The Daily Work Environment, The Operation Standards Are Restricted, And Relevant Personnel Are Required To Abide By The Corresponding Procedures And Codes Of Conduct, So That The Overall BehaviorCan Reach The Specified Standards编写:_________________________审批:_________________________时间:________年_____月_____日A4打印/ 新修订/ 完整/ 内容可编辑关键控制点控制程序标准范本使用说明:本管理制度资料适用于日常工作环境中对既定操作标准、规范进行约束,并要求相关人员共同遵守对应的办事规程与行动准则,使整体行为或活动达到或超越规定的标准。
资料内容可按真实状况进行条款调整,套用时请仔细阅读。
关键控制点控制程序1 概述根据食品质量安全要求设置关键质量控制点,实行强化管理,使其处于受控状态,确保达到规定的质量要求。
2 职责2.1 生产部负责工序质量控制和管理。
2.2 技术部负责工序质量检验。
2.3 生产工人负责严格执行操作控制程序或作业指导书。
3 关键质量控制点的确定3.1 关键质量控制点按以下原则确定:(1)属于关键特性或导致致命缺陷的项目和部位;(2)工艺上有特殊要求或对后续工序有显著影响的部位;(3)质量信息反馈中问题严重的项目或部位。
3.2 关键质量控制点由生产部确定。
生产部分析工序能力,找出影响质量特性的主要因素,编制关键质量控制点明细表,在工艺流程图上标出关键质量控制点,报总经理批准。
3.3 为保证产品质量的稳定,为防止食品添加剂超大超范围和超量使用,残留物质超标,微生物超标等质量安全问题。
IEC 62304关键控制点控制程序及全套表格记录
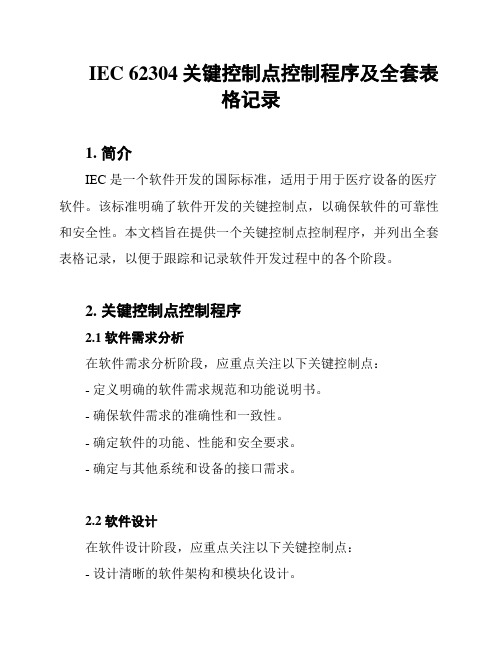
IEC 62304关键控制点控制程序及全套表格记录1. 简介IEC 是一个软件开发的国际标准,适用于用于医疗设备的医疗软件。
该标准明确了软件开发的关键控制点,以确保软件的可靠性和安全性。
本文档旨在提供一个关键控制点控制程序,并列出全套表格记录,以便于跟踪和记录软件开发过程中的各个阶段。
2. 关键控制点控制程序2.1 软件需求分析在软件需求分析阶段,应重点关注以下关键控制点:- 定义明确的软件需求规范和功能说明书。
- 确保软件需求的准确性和一致性。
- 确定软件的功能、性能和安全要求。
- 确定与其他系统和设备的接口需求。
2.2 软件设计在软件设计阶段,应重点关注以下关键控制点:- 设计清晰的软件架构和模块化设计。
- 确保软件设计满足软件需求规范。
- 考虑软件的可维护性和可测试性。
- 确定软件的界面设计和用户体验要求。
2.3 软件开发在软件开发阶段,应重点关注以下关键控制点:- 使用合适的软件开发方法和工具。
- 实施严格的软件编码和测试标准。
- 确保软件的可重复性和可审计性。
- 建立有效的软件配置管理和版本控制。
2.4 软件验证和验证在软件验证和验证阶段,应重点关注以下关键控制点:- 开展全面的软件验证和验证活动。
- 执行合适的软件测试策略和方法。
- 确保软件满足规定的验证和验证标准。
- 记录和跟踪验证和验证结果。
2.5 软件维护在软件维护阶段,应重点关注以下关键控制点:- 建立有效的软件维护过程和流程。
- 确保软件的缺陷修复和改进。
- 管理软件的版本更新和发布。
- 监控软件的性能和稳定性。
3. 全套表格记录在软件开发过程中,应使用以下表格记录各个阶段的相关信息:- 软件需求规范表- 软件功能说明书- 软件架构设计表- 软件模块设计表- 软件编码和测试记录- 软件验证和验证报告- 软件维护记录- 软件版本更新记录以上表格记录将有助于跟踪和记录软件开发过程中的各个阶段,以便于确保软件的质量和合规性。
4. 总结IEC 的关键控制点控制程序和全套表格记录对于医疗软件的开发至关重要。
关键控制点CCP验证控制程序
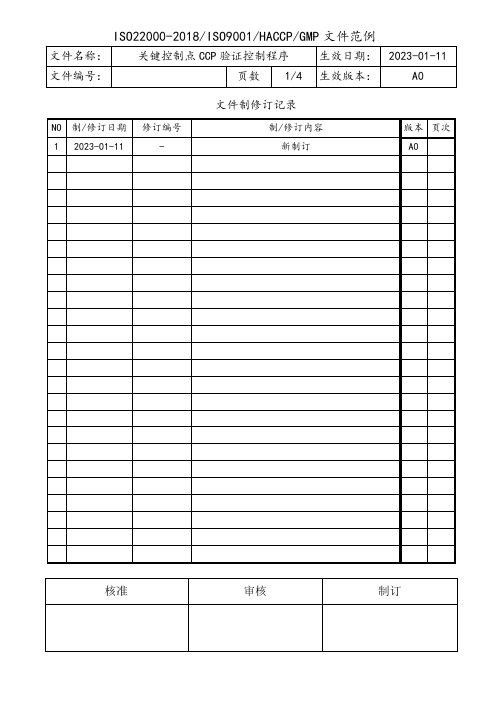
文件制修订记录1目的1.1确认HACCP计划建立和改进有效性的证据、确保HACCP计划有效实施,有效控制识别的安全危害;1.2证实关键控制点处于受控状态。
2范围适用于本公司质量和HACCP体系覆盖所有产品。
3职责3.1指定的HACCP组员负责对各关键控制点(CCP)进行验证。
3.2HACCP小组组长负责组织对HACCP计划的确认。
4工作程序4.1对HACCP计划的确认4.1.1当新的HACCP计划启用前,必须经过HACCP小组的确认。
每年至少一次,由HACCP小组组长组织对各已经实施的HACCP计划进行确认;验证HACCP计划的所有要素对于显著危害是否充分和有效。
发生以下情况时需要对HACCP计划进行重新确认原料、工艺、设备、销售或其它发生较大变化时(1)产品重复出现不合格时(2)出现新的危害或新的控制方法时(3)在生产过程中观察发现了新的问题(4)产生新的销售和消费者处理方式(5)其它可能对HACCP的有效性产生影响的情况。
4.2对关键控制点(CCP)的验证4.2.1关键控制点(CCP)确定的依据关键控制点(CCP)的确定必须由有资格的人员基于客观证据得出,客观证据可来源于以下信息资料公开发表的文献资料/技术参数、专家的建议、试验数据、法规标准、数学模拟等。
当以下情况发生时,应对关键控制点(CCP)进行重新验证(1)原材料改变(2)生产工艺流程改变(3)设备改变(4)重复出现不合格(5)其它可能对关键控制点(CCP)的准确性产生影响的情况4.2.2关键控制点(CCP)计量器具的验证在各关键控制点(CCP)配备适宜的计量器具。
严格按照《监测与测量仪器控制程序》对各关键控制点(CCP)的量器具进行管理,定期校准。
4.2.3关键控制点(CCP)实施符合性的验证HACCP小组组长授权专人负责在两个工作日内对各关键控制点(CCP)的监控记录和纠偏行动记录进行审核。
生产主管人员负责每天一次对各关键控制点(CCP)的实施情况进行督查。
关键质量控制点的操作控制程序
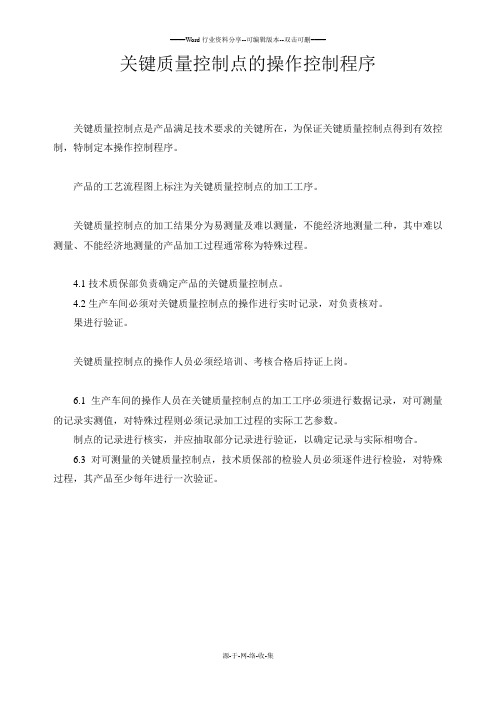
====Word行业资料分享--可编辑版本--双击可删====
关键质量控制点的操作控制程序
关键质量控制点是产品满足技术要求的关键所在,为保证关键质量控制点得到有效控制,特制定本操作控制程序。
产品的工艺流程图上标注为关键质量控制点的加工工序。
关键质量控制点的加工结果分为易测量及难以测量,不能经济地测量二种,其中难以测量、不能经济地测量的产品加工过程通常称为特殊过程。
4.1技术质保部负责确定产品的关键质量控制点。
4.2生产车间必须对关键质量控制点的操作进行实时记录,对负责核对。
果进行验证。
关键质量控制点的操作人员必须经培训、考核合格后持证上岗。
6.1生产车间的操作人员在关键质量控制点的加工工序必须进行数据记录,对可测量的记录实测值,对特殊过程则必须记录加工过程的实际工艺参数。
制点的记录进行核实,并应抽取部分记录进行验证,以确定记录与实际相吻合。
6.3对可测量的关键质量控制点,技术质保部的检验人员必须逐件进行检验,对特殊过程,其产品至少每年进行一次验证。
源-于-网-络-收-集。
关键控制点控制程序
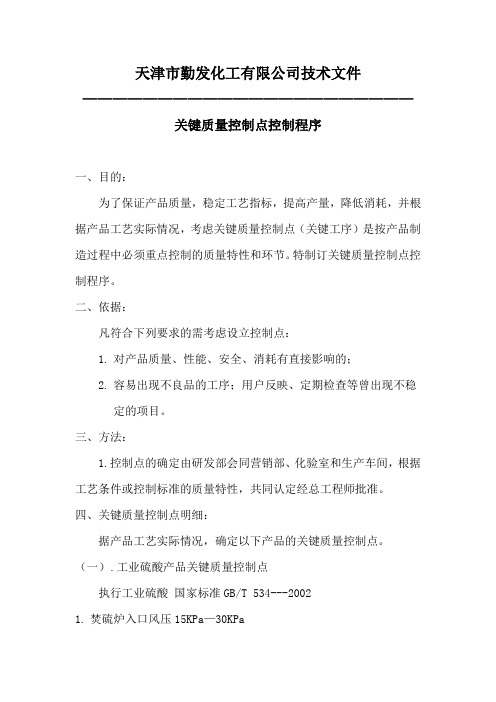
天津市勤发化工有限公司技术文件——————————————————————关键质量控制点控制程序一、目的:为了保证产品质量,稳定工艺指标,提高产量,降低消耗,并根据产品工艺实际情况,考虑关键质量控制点(关键工序)是按产品制造过程中必须重点控制的质量特性和环节。
特制订关键质量控制点控制程序。
二、依据:凡符合下列要求的需考虑设立控制点:1.对产品质量、性能、安全、消耗有直接影响的;2.容易出现不良品的工序;用户反映、定期检查等曾出现不稳定的项目。
三、方法:1.控制点的确定由研发部会同营销部、化验室和生产车间,根据工艺条件或控制标准的质量特性,共同认定经总工程师批准。
四、关键质量控制点明细:据产品工艺实际情况,确定以下产品的关键质量控制点。
(一).工业硫酸产品关键质量控制点执行工业硫酸国家标准GB/T 534---20021.焚硫炉入口风压15KPa—30KPa2.焚硫炉出口温度950—1050℃3.一段转化器入口温度420—440℃4.干燥循环槽硫酸含量(中控)92.5±1%5.吸收循环槽硫酸含量(中控)98±1%(二).液体二氧化硫产品关键质量控制点执行液体二氧化硫国家标准GB/T 3637---19931.解析塔顶温度85—95℃2.压缩机出口压力0.7—0,8MPa3.冷凝器出口温度<45℃4.吸收循环液中硫酸根含量(中控)<100g/L(三).工业氯磺酸产品关键质量控制点执行工业氯磺酸国家标准GB/T 13549---20081.干燥氯化氢气体压力250—350mmH2O2.盐酸流量1.4—2.0m³/h3.一级反应器温度140—180℃4.二级反应器温度70—100℃5.冷凝器温度≤35℃五、控制:1.工序质量由生产设备部和研发部负责按人、设备、材料、方法和环境五要素展开的内容严格管理。
2.在研发部的组织下,工序质量的检验由公司化验室进行,必须做到原料、中间过程、成品批批化验,合格的放行使用或对外销售,并进行不良品的分析与处置。
GMP关键控制点控制程序及全套表格记录
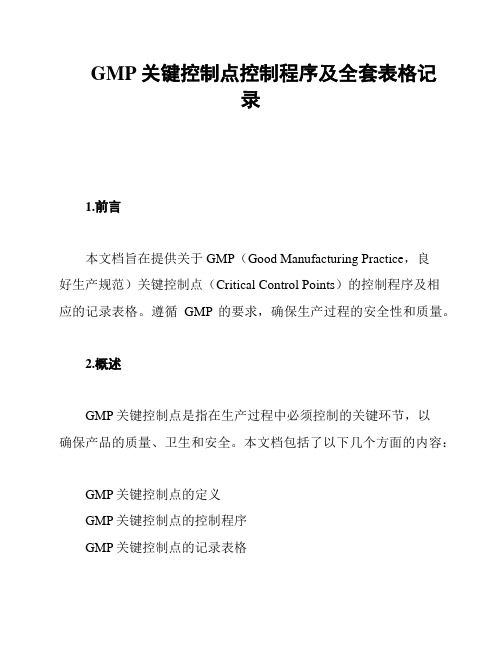
GMP关键控制点控制程序及全套表格记录1.前言本文档旨在提供关于GMP(Good Manufacturing Practice,良好生产规范)关键控制点(Critical Control Points)的控制程序及相应的记录表格。
遵循GMP的要求,确保生产过程的安全性和质量。
2.概述GMP关键控制点是指在生产过程中必须控制的关键环节,以确保产品的质量、卫生和安全。
本文档包括了以下几个方面的内容:GMP关键控制点的定义GMP关键控制点的控制程序GMP关键控制点的记录表格3.GMP关键控制点的定义根据产品的特性和生产过程的具体情况,确定GMP关键控制点。
这些点在生产过程中需要进行监控和控制,确保产品的质量和安全符合指定的标准和要求。
4.GMP关键控制点的控制程序为了控制GMP关键控制点,制定相应的控制程序。
控制程序应包括以下几个方面的内容:目标:明确GMP关键控制点的控制目标和要求。
负责人:指定负责GMP关键控制点控制的责任人员。
监控方法:确定监控GMP关键控制点的方法和频率。
控制措施:制定针对GMP关键控制点的控制措施,确保其在指定范围内。
紧急处理措施:制定应对GMP关键控制点失控情况的紧急处理措施。
记录要求:明确对GMP关键控制点进行记录的要求,保留相关记录。
5.GMP关键控制点的记录表格针对每个GMP关键控制点,制定相应的记录表格。
记录表格应包括以下几个方面的内容:日期和时间:记录监控GMP关键控制点的日期和时间。
监测结果:记录监控结果,包括各项指标的数值和是否符合要求。
异常处理:记录针对异常情况的处理措施和结果。
负责人:记录负责监控和记录GMP关键控制点的责任人员。
6.结论通过制定GMP关键控制点的控制程序及相应的记录表格,能够有效确保生产过程中关键环节的控制和监测,保障产品的质量和安全。
请按照此文档的内容进行相应的操作和记录,以符合GMP的要求。
以上是GMP关键控制点控制程序及全套表格记录的文档内容。
关键工序质量控制点控制程序
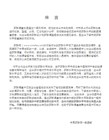
关键工序质量控制点控制程序一、隧道关键工序质量控制1、隧道开挖线放样⑴隧道掘进前放开挖轮廓线,要求按设计进行放开挖线,报现场工程师和测量监理工程师一起检查,合格后进行布制钻孔眼,孔眼间距,进行钻孔作业。
⑵隧道每开挖完一次进行检查,协作队伍检查开挖断面是否符合设计要求,欠挖部位进行凿除处理,合格后报现场工程师和监理工程师一起检查,合格后进行下道工序施工。
2、锚杆施工锚杆孔钻好后先自检,合格后报现场工程师、质检员和现场监理工程师一起检查,检查断面锚杆孔深、锚杆数量、锚杆孔环向间距及纵向间距、锚杆孔的角度和锚杆规格尺寸是否符合设计,合格后进行锚杆孔注浆、锚杆安装和挂钢筋网等相关后续作业,且所有锚杆必须安装垫板。
3、超前小导管施工超前小导管孔钻好后先自检,合格后报现场工程师、质检员和现场监理工程师一起检查,检查断面超前小导管孔深、超前小导管数量、超前小导管环向间距及纵向间距、超前小导管孔的角度和超前小导管规格长度是否符合设计,合格后进行超前小导管安装、注浆等相关后续作业。
4、钢筋网片加工制作及安装施工⑴钢筋网片加工必须有标准模具,控制好钢筋间距及焊接质量并符合设计要求,施工队伍先自检合格后报现场工程师检查,合格后由现场工师通知现场监理工程师一起检查。
⑵钢筋网片安装完成后,施工队伍先自检合格后报现场工程师检查,合格后由现场工师通知质检员及现场监理工程师一起检查;检查内容:钢筋网片搭接长度、钢筋网眼间距、钢筋网片保护层、钢筋网片层数是否符合设计要求。
5、钢拱架加工制作及安装施工⑴钢拱架加工必须有冷弯机等机具,控制好工字钢弯曲弧度及尺寸、钢板尺寸及孔径、焊接质量并符合设计要求,施工队伍先自检合格后报现场工程师检查,合格后由现场工师通知现场监理工程师一起检查。
⑵钢拱架安装完成后,施工队伍先自检合格后报现场工程师检查,合格后由现场工师通知质检员及现场监理工程师一起检查;检查内容:钢拱架位移偏差(包括横向和纵向)是否符合设计要求、钢拱架间距、钢拱架保护层、钢拱架搭接是否符合设计要求。
关键控制点控制程序
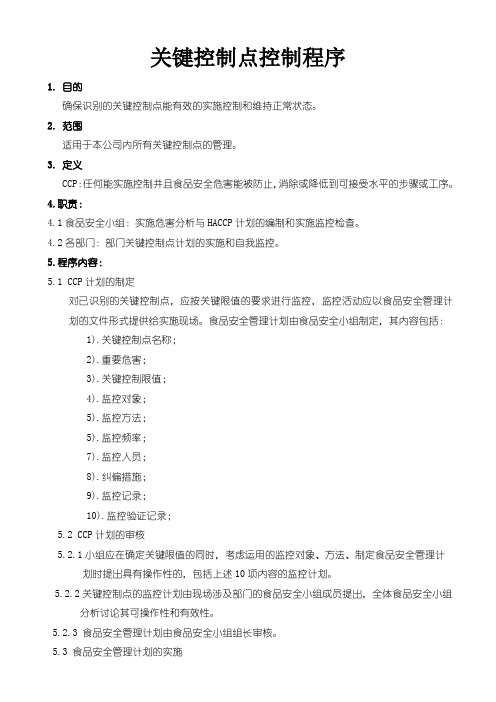
关键控制点控制程序1.目的确保识别的关键控制点能有效的实施控制和维持正常状态。
2.范围适用于本公司内所有关键控制点的管理。
3.定义CCP:任何能实施控制并且食品安全危害能被防止,消除或降低到可接受水平的步骤或工序。
4.职责:4.1食品安全小组:实施危害分析与HACCP计划的编制和实施监控检查。
4.2各部门:部门关键控制点计划的实施和自我监控。
5.程序内容:5.1 CCP计划的制定对已识别的关键控制点,应按关键限值的要求进行监控,监控活动应以食品安全管理计划的文件形式提供给实施现场。
食品安全管理计划由食品安全小组制定,其内容包括:1).关键控制点名称;2).重要危害;3).关键控制限值;4).监控对象;5).监控方法;5).监控频率;7).监控人员;8).纠偏措施;9).监控记录;10).监控验证记录;5.2 CCP计划的审核5.2.1小组应在确定关键限值的同时,考虑运用的监控对象、方法、制定食品安全管理计划时提出具有操作性的,包括上述10项内容的监控计划。
5.2.2关键控制点的监控计划由现场涉及部门的食品安全小组成员提出,全体食品安全小组分析讨论其可操作性和有效性。
5.2.3 食品安全管理计划由食品安全小组组长审核。
5.3 食品安全管理计划的实施5.3.1实施培训为了使每一个食品安全管理计划相关人员明白食品安全管理体系的重要性和操作要求,在实施之前应对各部门人员进行食品安全管理计划中相关控制点的培训。
5.3.2现场操作实施现场要保证效果,应提供必要的资源(如合格原料、测试仪器、SOP、记录)以体现工作内容是符合食品安全管理计划要求的,并且现场人员的工作应按食品安全管理计划的要求展开,并将工作中的控制活动作好记录。
5.4 食品安全管理体系的实施检查为保证食品安全管理体系的持续有效,食品安全小组应按计划要求进行监控检查,根据其类型分为两类;5.4.1日常持续性检查食品安全小组成员根据各部门的管理区域,按食品安全管理计划中的规定频率进行现场执行状况的内部检查,按《检验控制程序》文件要求进行巡查并填写各类巡查记录表。
关键控制点控制程序范本

关键控制点控制程序范本1. 引言控制程序是计算机系统中的重要组成部分,用于管理和调度计算机资源、执行应用程序,并确保系统正常运行。
关键控制点是控制程序中的关键步骤或决策点,可以直接影响系统的安全性、性能和可靠性。
本文将介绍关键控制点控制程序的设计和实现。
2. 控制点识别与分析在设计控制程序时,首先需要确定系统中的关键控制点。
关键控制点可以是用户控制输入、系统状态变化、资源分配、错误处理等。
对于每个关键控制点,需要进行详细的分析和评估,确定其对系统运行的影响程度和可能出现的问题。
3. 控制策略制定根据关键控制点的分析结果,制定相应的控制策略。
控制策略可以包括以下几个方面:- 输入验证:对用户输入进行校验和过滤,确保输入的合法性和安全性。
- 权限控制:对不同用户或角色进行权限管理,确保只有授权用户可以执行特定操作。
- 事务处理:将一系列操作作为一个事务进行处理,确保数据的一致性和完整性。
- 错误处理:对可能出现的错误进行处理,包括错误提示、日志记录和错误恢复等。
- 并发控制:对多个并发操作进行控制和调度,防止冲突和竞争条件的发生。
4. 控制程序设计与实现基于控制策略,进行控制程序的设计与实现。
控制程序可以分为以下几个模块:- 输入模块:负责接收用户输入,并进行验证和过滤。
- 权限模块:管理用户权限,控制用户对系统资源的访问和操作。
- 事务模块:提供事务处理功能,确保一系列操作的原子性和一致性。
- 错误处理模块:处理可能出现的错误情况,包括错误提示、故障恢复等。
- 并发控制模块:控制和调度多个并发操作,避免竞争条件和冲突。
5. 系统测试与优化完成控制程序的设计与实现后,需要进行系统测试和性能优化。
系统测试可以包括功能测试、安全测试、性能测试等,以确保控制程序的正确性和稳定性。
性能优化可以针对关键控制点进行,采用合适的算法和数据结构,提高系统的响应速度和吞吐量。
6. 结论关键控制点控制程序是计算机系统中的重要组成部分,对系统的安全性、性能和可靠性起到关键作用。
QP08 确定关键控制点控制程序
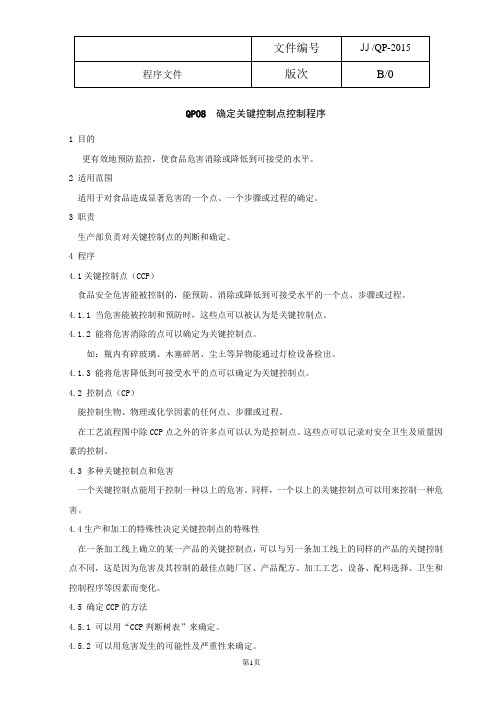
QP08 确定关键控制点控制程序1 目的更有效地预防监控,使食品危害消除或降低到可接受的水平。
2 适用范围适用于对食品造成显著危害的一个点、一个步骤或过程的确定。
3 职责生产部负责对关键控制点的判断和确定。
4 程序4.1关键控制点(CCP)食品安全危害能被控制的,能预防、消除或降低到可接受水平的一个点、步骤或过程。
4.1.1 当危害能被控制和预防时,这些点可以被认为是关键控制点。
4.1.2 能将危害消除的点可以确定为关键控制点。
如:瓶内有碎玻璃、木塞碎屑、尘土等异物能通过灯检设备检出。
4.1.3 能将危害降低到可接受水平的点可以确定为关键控制点。
4.2 控制点(CP)能控制生物、物理或化学因素的任何点、步骤或过程。
在工艺流程图中除CCP点之外的许多点可以认为是控制点。
这些点可以记录对安全卫生及质量因素的控制。
4.3 多种关键控制点和危害一个关键控制点能用于控制一种以上的危害。
同样,一个以上的关键控制点可以用来控制一种危害。
4.4生产和加工的特殊性决定关键控制点的特殊性在一条加工线上确立的某一产品的关键控制点,可以与另一条加工线上的同样的产品的关键控制点不同,这是因为危害及其控制的最佳点随厂区、产品配方、加工工艺、设备、配料选择、卫生和控制程序等因素而变化。
4.5 确定CCP的方法4.5.1 可以用“CCP判断树表”来确定。
4.5.2 可以用危害发生的可能性及严重性来确定。
如果经危害分析认为是危害,应对这种危害在加工工艺过程中产生的可能性及严重性进行分析;而且经分析危害可能产生,一旦产生就具有严重性,则此种危害就必须设置为CCP点来控制。
5 相关文件及记录5.1 《HACCP计划表》。
食品安全SC生产许可质量安全管理文件-3.5.2.3关键控制点控制程序
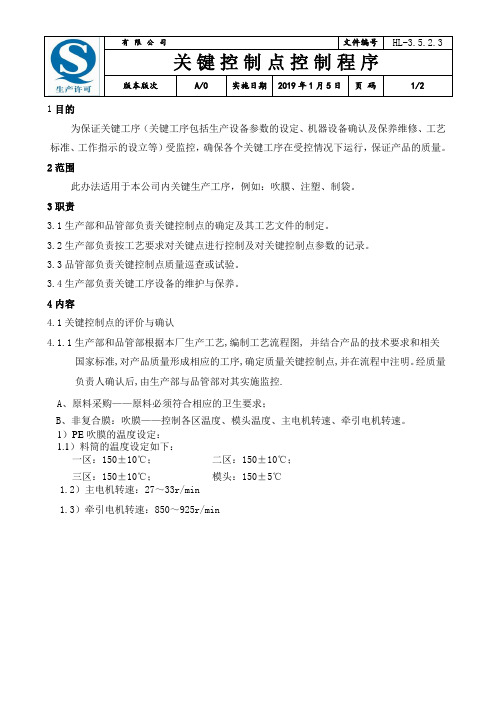
1目的
为保证关键工序(关键工序包括生产设备参数的设定、机器设备确认及保养维修、工艺标准、工作指示的设立等)受监控,确保各个关键工序在受控情况下运行,保证产品的质量。
2范围
此办法适用于本公司内关键生产工序,例如:吹膜、注塑、制袋。
3职责
3.1生产部和品管部负责关键控制点的确定及其工艺文件的制定。
3.2生产部负责按工艺要求对关键点进行控制及对关键控制点参数的记录。
3.3品管部负责关键控制点质量巡查或试验。
3.4生产部负责关键工序设备的维护与保养。
4内容
4.1关键控制点的评价与确认
4.1.1生产部和品管部根据本厂生产工艺,编制工艺流程图, 并结合产品的技术要求和相关
国家标准,对产品质量形成相应的工序,确定质量关键控制点,并在流程中注明。
经质量负责人确认后,由生产部与品管部对其实施监控.
A、原料采购——原料必须符合相应的卫生要求;
B、非复合膜:吹膜——控制各区温度、模头温度、主电机转速、牵引电机转速。
1)PE吹膜的温度设定:
1.1)料筒的温度设定如下:
一区:150±10℃;二区:150±10℃;
三区:150±10℃;模头:150±5℃
1.2)主电机转速:27~33r/min
1.3)牵引电机转速:850~925r/min。
- 1、下载文档前请自行甄别文档内容的完整性,平台不提供额外的编辑、内容补充、找答案等附加服务。
- 2、"仅部分预览"的文档,不可在线预览部分如存在完整性等问题,可反馈申请退款(可完整预览的文档不适用该条件!)。
- 3、如文档侵犯您的权益,请联系客服反馈,我们会尽快为您处理(人工客服工作时间:9:00-18:30)。
文件编号:RHD-QB-K3798 (管理制度范本系列)
编辑:XXXXXX
查核:XXXXXX
时间:XXXXXX
关键控制点控制程序标
准版本
关键控制点控制程序标准版本
操作指导:该管理制度文件为日常单位或公司为保证的工作、生产能够安全稳定地有效运转而制定的,并由相关人员在办理业务或操作时必须遵循的程序或步骤。
,其中条款可根据自己现实基础上调整,请仔细浏览后进行编辑与保存。
关键控制点控制程序
1 概述
根据食品质量安全要求设置关键质量控制点,实行强化管理,使其处于受控状态,确保达到规定的质量要求。
2 职责
2.1 生产部负责工序质量控制和管理。
2.2 技术部负责工序质量检验。
2.3 生产工人负责严格执行操作控制程序或作业指导书。
3 关键质量控制点的确定
3.1 关键质量控制点按以下原则确定:
(1)属于关键特性或导致致命缺陷的项目和部位;
(2)工艺上有特殊要求或对后续工序有显著影响的部位;
(3)质量信息反馈中问题严重的项目或部位。
3.2 关键质量控制点由生产部确定。
生产部分析工序能力,找出影响质量特性的主要因素,编制关键质量控制点明细表,在工艺流程图上标出关键质量控制点,报总经理批准。
3.3 为保证产品质量的稳定,为防止食品添加剂超大超范围和超量使用,残留物质超标,微生物超标等质量安全问题。
3.3.1 根据《糕点生产许可证审查细则》、《饼干生产许可证审查细则》和本公司生产的实际,将糕
点和饼干产品的:
⑴裱花蛋糕:配料、烘烤、裱花等工序确定为关键控制环节。
⑵面包:配料、醒发等工序确定为关键控制环节。
⑶饼干:配料、烘烤等工序确定为关键控制环节。
另外,把设备工装容器使用前后的消毒工序和操作人员的卫生管理,及车间环境卫生环节的控制确定为需要加强的工作环节,对工作程序、参数进行严格控制。
4 关键质量控制点的管理
4.1 生产部根据所生产不同类别的产品,制定关键质量控制点的操作控制程序或作业指导书,报总经理批准。
4.2 生产车间按关键质量控制点操作控制程序或作业指导书进行质量控制,并做好记录。
4.3 技术部对关键质量控制点实施质量检验,并做好记录。
4.4 关键质量控制点:
见《产品工艺流程图》。
5 记录
《配料表》
《配料记录》
《配料关键工序记录》
《烘烤关键工序记录》
《醒发关键工序记录》
《裱花关键工序记录》
这里写地址或者组织名称
Write Your Company Address Or Phone Number Here。