生产工艺操作程序关键控制点
重要工序质量控制及关键工序控制点
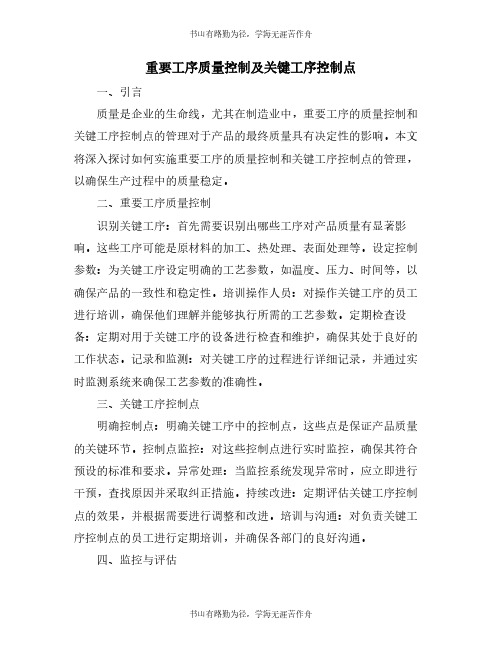
重要工序质量控制及关键工序控制点一、引言质量是企业的生命线,尤其在制造业中,重要工序的质量控制和关键工序控制点的管理对于产品的最终质量具有决定性的影响。
本文将深入探讨如何实施重要工序的质量控制和关键工序控制点的管理,以确保生产过程中的质量稳定。
二、重要工序质量控制识别关键工序:首先需要识别出哪些工序对产品质量有显著影响。
这些工序可能是原材料的加工、热处理、表面处理等。
设定控制参数:为关键工序设定明确的工艺参数,如温度、压力、时间等,以确保产品的一致性和稳定性。
培训操作人员:对操作关键工序的员工进行培训,确保他们理解并能够执行所需的工艺参数。
定期检查设备:定期对用于关键工序的设备进行检查和维护,确保其处于良好的工作状态。
记录和监测:对关键工序的过程进行详细记录,并通过实时监测系统来确保工艺参数的准确性。
三、关键工序控制点明确控制点:明确关键工序中的控制点,这些点是保证产品质量的关键环节。
控制点监控:对这些控制点进行实时监控,确保其符合预设的标准和要求。
异常处理:当监控系统发现异常时,应立即进行干预,查找原因并采取纠正措施。
持续改进:定期评估关键工序控制点的效果,并根据需要进行调整和改进。
培训与沟通:对负责关键工序控制点的员工进行定期培训,并确保各部门的良好沟通。
四、监控与评估监控计划:制定详细的监控计划,明确监控的频率、方法和技术要求。
数据收集与分析:收集关键工序和关键控制点的相关数据,对其进行分析,以评估其性能和效果。
定期评估:定期对整个生产过程进行全面评估,确保所有工序都符合质量要求。
反馈机制:建立有效的反馈机制,使管理层能及时了解生产过程中的问题,并采取相应的措施。
持续改进:根据监控和评估的结果,持续优化生产过程,提高产品质量和生产效率。
五、质量管理体系建设质量方针与目标:制定明确的质量方针和目标,为整个质量管理工作提供指导。
组织结构与职责:建立完善的组织结构,明确各部门和人员的职责和工作关系。
2生产工艺操作程序关键控制点
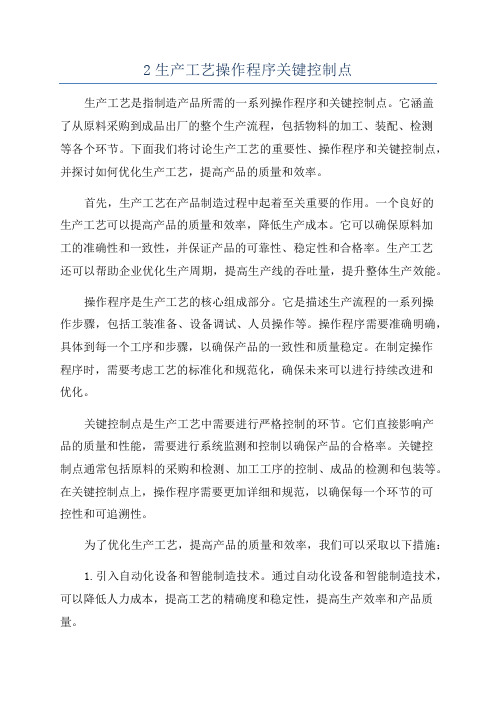
2生产工艺操作程序关键控制点生产工艺是指制造产品所需的一系列操作程序和关键控制点。
它涵盖了从原料采购到成品出厂的整个生产流程,包括物料的加工、装配、检测等各个环节。
下面我们将讨论生产工艺的重要性、操作程序和关键控制点,并探讨如何优化生产工艺,提高产品的质量和效率。
首先,生产工艺在产品制造过程中起着至关重要的作用。
一个良好的生产工艺可以提高产品的质量和效率,降低生产成本。
它可以确保原料加工的准确性和一致性,并保证产品的可靠性、稳定性和合格率。
生产工艺还可以帮助企业优化生产周期,提高生产线的吞吐量,提升整体生产效能。
操作程序是生产工艺的核心组成部分。
它是描述生产流程的一系列操作步骤,包括工装准备、设备调试、人员操作等。
操作程序需要准确明确,具体到每一个工序和步骤,以确保产品的一致性和质量稳定。
在制定操作程序时,需要考虑工艺的标准化和规范化,确保未来可以进行持续改进和优化。
关键控制点是生产工艺中需要进行严格控制的环节。
它们直接影响产品的质量和性能,需要进行系统监测和控制以确保产品的合格率。
关键控制点通常包括原料的采购和检测、加工工序的控制、成品的检测和包装等。
在关键控制点上,操作程序需要更加详细和规范,以确保每一个环节的可控性和可追溯性。
为了优化生产工艺,提高产品的质量和效率,我们可以采取以下措施:1.引入自动化设备和智能制造技术。
通过自动化设备和智能制造技术,可以降低人力成本,提高工艺的精确度和稳定性,提高生产效率和产品质量。
2.强化质量控制和质量保证体系。
建立完善的质量控制和质量保证体系,包括质量管理体系、质检标准和流程等,确保产品满足客户的要求和标准。
3.进行全面的数据分析和过程监测。
通过全面的数据分析和过程监测,可以及时发现生产中的异常和问题,及时采取措施进行调整和改进,提高生产工艺的稳定性和一致性。
4.实施员工培训和技能提升计划。
通过培训和技能提升计划,提高员工的专业素质和操作技能,确保他们熟练掌握操作程序和操作技巧,提高工艺的可控性和可靠性。
酱香型白酒生产工艺流程图及关键控制点

制曲关键控制点
原料质量
选用优质的小麦、大麦、豌豆等原料,保证 原料无霉变、无杂质。
粉碎粒度
控制好原料的粉碎粒度,不宜过细或过粗,以 保证曲块的透气性和发酵效果。
润料水分
润料时加入适量的水,使原料充分吸水膨胀,水 分含量要控制在合适范围内。
踩曲成型
踩曲时要用力均匀,保证曲块平整紧实,无裂缝。
培养条件
提高生产效率与品质
通过明确生产工艺流程,可以更加系统地管理和 优化生产环节,从而提高生产效率和产品品质。
3
适应市场需求与发展
随着消费者对白酒品质要求的提高,酱香型白酒 生产工艺需要不断改进和创新,以适应市场需求 和行业发展趋势。
酱香型白酒生产工艺概述
原料选择与处理
选用优质高粱、小麦等为主要原料,经过 粉碎、润料等预处理工序。
包装过程管理
包装前准备
确保包装车间环境整洁,定期对设备进行清洗和消毒。检 查包装材料是否符合要求,有无破损或污染现象。
包装操作规范
严格按照包装工艺流程进行操作,确保每一步骤的准确性 和规范性。特别注意瓶口、瓶盖的清洁和密封效果,以及 标签的粘贴位置和平整度。
包装质量检查
在包装过程中和结束后,进行多次质量抽查,检查包装是 否严密、标签是否清晰、产品是否破损等。对不合格品进 行及时处理,确保出厂产品的合格率。
酱香型白酒生产工艺 流程图及关键控制点
汇报人:XX 2024-01-22
目录
• 引言 • 原料选择与处理 • 制曲工艺 • 发酵工艺 • 蒸馏工艺 • 陈酿与勾兑工艺 • 包装与储存工艺 • 质量检测与评估体系建立
01
引言
目的和背景
1 2
传承与弘扬传统工艺
关键控制点的确定原则

关键控制点的确定原则一、前言关键控制点的确定是食品安全管理中的重要环节,其目的在于识别并控制食品生产过程中可能对食品安全造成影响的关键因素。
本文将从食品安全管理的角度出发,结合实际案例,探讨关键控制点的确定原则。
二、什么是关键控制点关键控制点(HACCP)是指在食品生产过程中,可能对产品质量或安全产生显著影响的生产环节。
这些环节必须得到严格监测和控制,以确保产品质量和安全。
三、关键控制点的确定原则1. 原料选择和采购原料选择和采购是影响产品质量和安全的重要因素。
在选择原料时,应优先考虑其来源、品质和历史记录。
同时,在采购过程中应严格遵守相关法律法规,并确保供应商具有合法资格。
2. 生产工艺流程设计生产工艺流程设计是关键控制点的核心内容。
在设计过程中,应明确每个环节对产品质量和安全的影响,并采取相应措施进行监测和控制。
同时,在设计过程中应充分考虑环保、节能等方面的因素。
3. 设备和设施管理设备和设施管理是确保生产过程顺利进行的重要保障。
在设备采购、安装、维护和保养等方面,应严格遵守相关规定,并进行定期检查和维护。
同时,应对设备进行分类管理,确保其完好无损。
4. 人员管理人员管理是关键控制点的重要组成部分。
在人员招聘、培训、考核等方面,应注重岗位适配性和技能水平。
同时,在生产过程中应实行严格的作业规范,并加强对员工的监督和管理。
5. 环境卫生控制环境卫生控制是确保产品质量和安全的基础。
在生产过程中,应加强对厂房、车间等环境卫生的监测和控制,并采取相应措施进行清洁消毒。
6. 检测与分析检测与分析是关键控制点的重要环节。
在生产过程中,应对原料、半成品和成品进行定期检测,并建立相应检测记录。
同时,在出现问题时,应及时进行分析并采取相应措施进行改进。
四、结语关键控制点的确定是食品安全管理中的重要环节。
通过严格监测和控制生产过程中可能对食品安全造成影响的关键因素,可以有效提高产品质量和安全性。
在确定关键控制点时,应充分考虑生产工艺流程、设备和设施管理、人员管理、环境卫生控制以及检测与分析等方面的因素,并采取相应措施进行监测和控制。
关键控制点及控制程序

关键控制点及控制程序1、原料清理1.1必须经过筛选、除杂等工序,保证原种的合格率。
关键控制点是筛选。
1.2条件是均匀进料,不搞突击生产,以达生产工艺要求。
2、预制毛油2.1轧胚、压胚时调节好辊子间距,既不能把料压碎,更不能整料进入下道工序。
关键控制好辊子间距。
2.2蒸炒,掌握好温度,把胚料炒到最佳出油状态。
关键控制好立式蒸炒锅的温度,一般控制在200℃,时间不少于40分钟。
2.3榨油,熟料进入样机时通过间接蒸汽控制好温度,力争保证油品品质及出油率,副产品残油10%,水分3%。
2.4沉淀过滤,利用物理原理清除毛油中的各种杂质。
关键是要控制好时间,不仅能分离悬浮的杂质,还能进一步除去油内的胶体杂质。
3、精炼3.1水化,根据毛油品质定量加入催化剂,使油中的酸价降至标准,同时分离、沉淀,以达半成品。
关键要掌握好水化锅的温度,水化温度80-85%。
3.2水洗,利用水、温度、盐自由调节,使油品中的皂粒,微量杂质与油彻底分离。
3.3碱炼又称脱酸,使碱金属盐怀与油脂分离,关键要掌握好碱炼锅离心机的操作工艺。
3.4脱水,利用真空负压原理,使油品中的水份与油分离,从而使油品质量达到国家标准。
3.5脱臭,经过此道工序后可使油品质量再上一个台阶,成为高级烹调油或色拉油。
关键要掌握好脱臭器的真空压力。
4、运输4.1容器,凡需要容器装的原料,其容器必须是符合仪器卫生要求,无毒、耐腐蚀,易清洗,结构坚固的容器,并能经常清洗,结构坚固并要经常清洗消毒。
4.2运输工具应保持清洁干净,便于清洗消毒,并具有防污染等措施。
4.3搬运时应轻装轻卸,不得与有毒、有害物混装混用。
面包生产工艺流程和关键控制点作业指导书
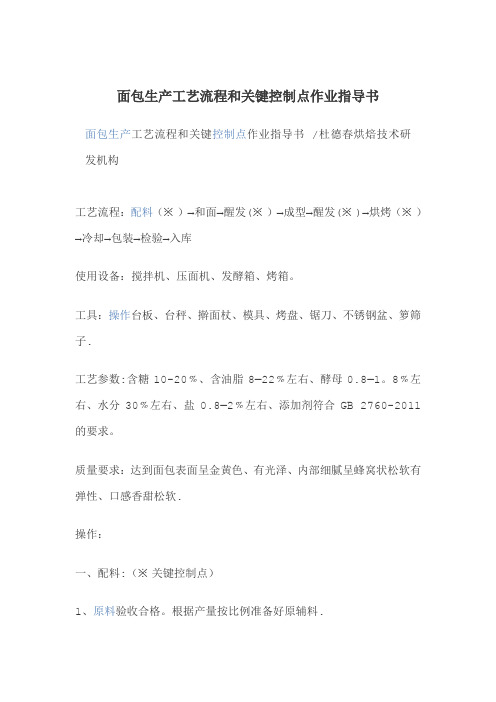
面包生产工艺流程和关键控制点作业指导书面包生产工艺流程和关键控制点作业指导书 /杜德春烘焙技术研发机构工艺流程:配料(※)→和面→醒发(※)→成型→醒发(※)→烘烤(※)→冷却→包装→检验→入库使用设备:搅拌机、压面机、发酵箱、烤箱。
工具:操作台板、台秤、擀面杖、模具、烤盘、锯刀、不锈钢盆、箩筛子.工艺参数:含糖10-20﹪、含油脂8—22﹪左右、酵母0.8—1。
8﹪左右、水分30﹪左右、盐0.8—2﹪左右、添加剂符合GB 2760-2011的要求。
质量要求:达到面包表面呈金黄色、有光泽、内部细腻呈蜂窝状松软有弹性、口感香甜松软.操作:一、配料:(※关键控制点)1、原料验收合格。
根据产量按比例准备好原辅料.2、将生产所需物料运到配料室,先把鸡蛋打好放入不锈钢盆内,再用箩筛把面粉在操作台上过筛,糖、油、脂、水、酵母、盐、添加剂称好备用.原料称量的顺序:根据产品标准由小到大进行称量,500g以内物料用天平称量,5kg以内物料用案秤称量,5kg以上用台秤称量。
3、配料过程工作人员要填写好工作记录。
二、和面:1、把以上原料放入搅拌机搅拌,搅拌15分钟左右,面团光滑为止。
三、醒发:(※关键控制点温度38℃左右发酵时间60分钟左右)1、搅拌好的面团放入醒发箱,温度控制在38℃左右,湿度控制在75—80﹪左右,醒发大约60分钟左右。
四、成型:1、醒发好后,把面团放在操作台上分割,分别制作所生产的形状成型。
五、醒发:(※温度38℃左右发酵时间60分钟左右)1、再放入醒发箱60分钟左右,温度控制在38℃左右就好。
六、烘烤:(※关键控制点烘烤温度上火190℃,下火200℃烘烤时间12分钟左右)1、成型醒发好后放入烤箱,烤箱温度上火190℃,下火200℃,烤至大约12分钟,表面呈金黄色即可。
2、烘烤过程要有专人负责。
烘烤过程要填写好生产记录。
七、冷却:1、烤好后的面包移至冷却间,冷却大约在5小时左右,使产品达到质量要求。
重要工序质量控制及关键工序控制点

重要工序质量控制及关键工序控制点一、引言重要工序质量控制及关键工序控制点是指在生产过程中对关键工序进行质量控制的方法和控制点。
通过对重要工序的质量控制,可以确保产品的质量稳定和合格率的提高,从而提高生产效率和降低成本。
二、重要工序质量控制方法1. 流程控制在重要工序中,应建立完善的流程控制措施,包括工艺流程、操作规程、工艺参数等。
通过控制每一个环节的操作流程,确保产品在每一个工序中都符合质量要求。
2. 设备控制重要工序中的设备对产品质量有直接影响。
应对设备进行定期维护和保养,确保设备的正常运行。
同时,还应建立设备操作规程,培训操作人员,提高设备的操作技能。
3. 材料控制材料是产品的基础,对于重要工序来说尤其重要。
应对材料进行严格的入库检验,并建立合格供应商的名录。
在使用材料时,要严格按照工艺要求进行配料,并对每批材料进行记录和追溯。
4. 检验控制重要工序中的检验控制是确保产品质量的重要环节。
应建立完善的检验方法和检验标准,并对检验人员进行培训。
对于不合格品,要及时进行处理和追溯,并采取纠正措施,防止类似问题再次发生。
三、关键工序控制点1. 工艺参数控制在重要工序中,工艺参数的控制是确保产品质量稳定的关键。
应建立工艺参数的标准范围,并对每一个工序进行监控和记录。
对于超出标准范围的工艺参数,要及时调整,并进行原因分析,以防止类似问题再次发生。
2. 操作规程控制操作规程是重要工序中操作人员的指导手册。
应建立完善的操作规程,并对操作人员进行培训。
在操作过程中,要严格按照操作规程进行操作,确保每一个操作环节的准确性和一致性。
3. 检测设备控制在重要工序中,检测设备的准确性和可靠性对产品质量有直接影响。
应定期对检测设备进行校准和维护,并建立检测设备的使用记录。
对于不合格的检测设备,要及时更换或者修理,以保证检测结果的准确性。
4. 质量记录控制质量记录是重要工序中质量控制的重要依据。
应建立完善的质量记录系统,并对每一个工序进行记录和归档。
重要工序质量控制及关键工序控制点

重要工序质量控制及关键工序控制点在生产过程中,重要工序质量控制及关键工序控制点是确保产品质量的关键因素。
通过严格控制关键工序,可以有效地避免产品质量问题,提高生产效率,降低生产成本,满足客户需求。
本文将从重要工序质量控制的概念和意义入手,详细介绍重要工序质量控制及关键工序控制点的相关内容。
一、重要工序质量控制的概念和意义1.1 重要工序质量控制的概念重要工序质量控制是指在生产过程中,对于影响产品质量的关键工序进行严格控制,确保产品在每个关键工序都符合质量标准。
1.2 重要工序质量控制的意义- 保证产品质量稳定性:通过对重要工序进行质量控制,可以确保产品在整个生产过程中的质量稳定性,降低产品质量波动性。
- 提高生产效率:通过对关键工序进行控制,可以及时发现问题并进行调整,提高生产效率,减少不良品率。
- 降低生产成本:通过控制关键工序,可以减少废品率,降低生产成本,提高企业竞争力。
二、关键工序控制点的确定方法2.1 重要性评估法根据工序对产品质量的影响程度,确定关键工序,进而确定关键工序的控制点。
2.2 统计分析法通过统计分析历史数据,找出影响产品质量的主要因素,确定关键工序控制点。
2.3 专家经验法借助专家经验,结合工艺流程和产品特性,确定关键工序控制点,确保产品质量稳定。
三、关键工序控制点的具体控制方法3.1 制定详细的工艺流程在关键工序中制定详细的工艺流程,明确每个步骤的操作要求和质量标准。
3.2 引入自动化设备引入自动化设备可以减少人为因素对产品质量的影响,提高生产效率,降低不良率。
3.3 实施严格的质量检验在关键工序中实施严格的质量检验,及时发现问题并进行处理,确保产品质量符合标准。
四、关键工序控制点的监控和改进4.1 建立监控体系建立关键工序控制点的监控体系,定期对关键参数进行监测和分析,及时发现问题并进行改进。
4.2 持续改进定期评估关键工序控制点的效果,根据实际情况进行调整和改进,不断提高产品质量和生产效率。
- 1、下载文档前请自行甄别文档内容的完整性,平台不提供额外的编辑、内容补充、找答案等附加服务。
- 2、"仅部分预览"的文档,不可在线预览部分如存在完整性等问题,可反馈申请退款(可完整预览的文档不适用该条件!)。
- 3、如文档侵犯您的权益,请联系客服反馈,我们会尽快为您处理(人工客服工作时间:9:00-18:30)。
生产作业控制制度一、销售部依据市场需求及客户要求,下达《生产制造单》至生产车间。
二、技术部负责编制《产品工艺流程图》、《作业指导书》,各工序操作员严格依据《产品工艺流程图》、《作业指导书》进行作业。
当因相关因素的改变而需更改《作业指导书》时,则依据《文件和资料控制制度》进行相应的更改。
三、设备质量的控制依据《生产设备控制制度》执行。
四、品管部负责跟进每一工序工艺执行情况,当发现有违反工艺操作或不规范操作时,应予以纠正。
五、品管部负责对每一质量控制点的工序产品进行检验和试验,并负责对工序产品的放行。
六、对有技能培训要求的工序,应组织此类工序人员的培训、考核。
只有经培训及考核合格的人员才能上岗操作,定员定岗,品管部负责本工序人员质量的管理和控制,当发现人员质量不合格时,应立即停止其作业,并提出人员培训申请,实施培训事宜。
当因相关因素的改变而需更新岗位技能时,则对人员进行重新培训。
七、对特殊过程的控制应由具备资格的操作者完成,且定员定岗。
八、附相关文件:《作业指导书》《产品工艺流程图》《批生产指令》《批生产记录(生产前)》《批生产记录(生产中)》《工艺流程图》《配料操作规程》《灌装/包装操作规程》洗发液生产作业指导书(操作过程控制)一、生产前的准备:1、清洗加热搅拌机,搅拌机干净后,才可生产。
2、清洗生产用具、桶、铲、冲洗干净后,才可使用。
3、检查校正磅秤、衡器,正确无误。
4、测试纯水PH值应在之间,方可使用。
5、测试纯水电导率应在8以下,达标后才可使用。
6、检查原材料是否满足生产用量,才可生产。
7、检查电源、各种仪表应正常。
二、秤料规程:1、纯水:按百分比计算,不得误差1%按配方比例加入。
2、原料:按百分比计算,按配方比例不得有任何误差。
三、生产操作:1、将原材料加入搅拌机,搅拌15---20分钟,彻底均匀后,方可加入其它添加剂。
2、去离子水,按配方比例加入,在每分钟50---60转良好的搅拌下,使原料与纯水搅拌,边搅拌、边加热、加热75℃,然后关闭加热管。
3、在良好的搅拌下,恒温搅拌30分钟、化、杀菌。
4、将恒温后,开始降温,边搅拌、边降温。
5、冷至40℃后,加入防腐剂、香精、添加剂、搅拌30---50分钟均匀后,才送化验室检验,合格后才出料。
进入静置室。
四、质量检验:1、半成品未出料前检验PH值在6---7之间,才合格。
2、半成品离心,30分钟/2000转,,无油水分离现象,才合格。
3、泡沫测试在50以上,才合格。
4、粘度测试在7000以上,才合格。
5、耐热±40℃、24h,恢复室温后应正常,才合格。
6、耐寒—15℃、24h,恢复室温后,应正常。
7、细菌检验,培养48 n±37℃,应达到国家标准,才合格。
8、经检验合格后,才通知生产部分装车间灌装。
五、分装成品:1、塑料瓶用乙醇消毒后,才可装成品。
2、塑料瓶应喷生产日期、保质期二年。
3、对不合格塑料瓶,一律不得装成品。
4、塑料瓶说明书、字迹不清楚一律不得装成品。
5、分装成品时,应凭化验室放得单,才可分装。
6、洗发液分装,瓶瓶过秤200ml,每甁秤量不得少于202g、只准多,不准少。
六、包装车间:1、分装车间过好秤的成品,应盖好瓶盖,检验瓶外观应整洁。
2、大纸箱应检查与洗发液是否相符。
3、质检员检验包装应达到企业内控标准,才在合格证上签字放行。
4、包装完后,经质检员全部检验合格后,才可入库。
洗发液工艺流程图说明:关键控制点A、原材料纯水加热75℃,恒温搅拌30分钟,才降温。
B、降温至40℃加入香精、防腐剂。
注意事顶:A、恒温乳化30分钟杀菌、乳化,不得少于1分钟。
B、香精、防腐剂40℃以下加入,不得在40℃以上加入。
C、香精、防腐剂加入后,要搅拌30分钟均匀后,才可出料。
D、原料、去离子水一定要过秤,不得误差1%。
洗发液关键控制点开料员:工程师:护发素生产作业指导书(操作过程控制)一、生产前的准备:1、清洗真空乳化机、油相桶、水相桶,应清洗干净。
2、清洗生产用具、桶、铲,才可生产。
3、检查油相、水相加热油应达到标准。
4、检查各种仪表、仪器、线路、开关应正常。
5、检查各种秤、衡器应正常。
6、测试纯水PH值:6~7之间,方可使用。
7、测试纯水电导率在3~8之间,应达标才可使用。
二、秤原料操作规程:1、原料按油相、水相秤好后,按油相、水相分开加热,原料、油质,不得有任何误差。
2、纯水不得误差1%,然后加入水相加热。
三、生产操作程序:1、油相加热85℃--90℃。
2、水相加热85℃--90℃(水包油体系)。
3、将水相先抽入乳化锅,然后再把油相抽入乳化锅。
4、均质2800转/分钟、均质5~7分钟,然后恒温搅拌30分钟乳化、杀菌。
在良好搅拌下降温。
5、降温至45℃加入添加剂、香精,在良好的搅拌下,继续降至40℃后,送化验室检验合格后,出料放入静置室。
四、质量检验:1、半成品出料前进行抽查,合格后,才通知生产车间出料。
2、PH值测试:6~7之间,才合格。
3、离心检验:3000转/30分钟、无油水分离才合格。
4、耐热±40℃、24h恢复室温后应正常。
5、耐寒-15℃、24h恢复室温后应正常。
6、细菌检验:培养±37℃、48n ,应符QB/T7916国家标准。
7、经检验合格后,才通知生产部分装车间分装。
五、分装成品:1、包装玻璃瓶、塑料小盒,用乙醇进行消毒、杀菌后,才可装成品。
2、应检查玻璃瓶、塑料盒应打印生产日期、保质期限。
3、凡不合格的玻璃瓶、塑料盒一律不得装成品。
4、分装半成品时,应凭化验室合格放行单,才可分装。
5、各种产品分装时,不得少1ml、不得多3ml。
六、包装车间:1、包装车间包装已经分装好的成品。
其盖、内垫也应用乙醇消毒后才可使用。
2、外用纸箱,应检查与成品是否相符、字迹是否清楚、图案、商标应正确、无误才可使用。
3、质检员检验合格后,每箱应放合格证、合格证有质检员签字、生产日期、批号。
4、经检验合格后,成品方可入库。
护发素工艺流程图说明:关键控制点:A、油、水相混合后、均质5—7分钟。
B、恒温搅拌30分钟乳化、杀菌。
注意事项:A、油相、水相加热不得低于85℃,不得高于90℃。
B、均质时间不得少于5分钟,为保证质量。
C、恒温杀菌乳化30分钟,不得少于一分钟时间。
D、45℃加香精,不得在45℃以上加入香精。
护发素关键控制点开料员:工程师:护肤乳液生产作业指导书(操作过程控制)一、生产前的准备:1、清洗真空乳化机、油相桶、水相桶,应清洗干净。
2、清洗生产用具、桶、铲,才可生产。
3、检查油相、水相加热油应达到标准。
4、检查各种仪表、仪器、线路、开关应正常。
5、检查各种秤、衡器应正常。
6、测试纯水PH值:6---7之间,方可使用。
7、测试纯水电导率在8以下,应达标才可使用。
二、秤原料操作规程:1、原料按油相、水相秤好后,按油相、水相分开加热,原料、油质,不得有任何误差。
2、水不得误差1%,然后加入水相加热。
三、生产操作程序:1、油相加热85℃--90℃。
2、水相加热85℃--90℃(水包油体系)。
3、将水相先抽入乳化锅,然后再把油相抽入乳化锅。
4、均质2800转/分钟、均质5—7分钟,然后恒温搅拌30分钟乳化、杀菌。
在良好搅拌下降温。
5、降温至45℃加入添加剂、香精,在良好的搅拌下,继续降至40℃后,送化验室检验合格后,出料放入静置室。
四、质量检验:1、半成品出料前进抽查,合格后,才通知生产车间出料。
2、PH值测试:6---7之间,才合格。
3、离心检验:3000转/30分钟、无油水分离才合格。
4、耐热±40℃、24h恢复室温后应正常。
5、耐寒—15℃、24h恢复室温后应正常。
6、细菌检验:培养±37℃、48h,应符QB/T7916国家标准。
7、经检验合格后,才通知生产部分装车间分装。
五、分装成品:1、包装玻璃瓶、塑料小盒,用乙醇直行消毒、杀菌后,才可装成品。
2、应检查玻璃瓶、塑料盒应打印生产日期、保质期限。
3、凡不合格的玻璃瓶、塑料盒一律不得装成品。
4、分装半成品时,应凭化验室合格放行单,才可分装。
5、各种产品分装时,不得少1g、不得多3g。
六、包装车间:1、包装车间包装已经分装好的成品。
其盖、内垫也应用乙醇消毒后,才可使用。
2、外用纸箱,应检查与成品是否相符、字迹是否清楚、图案、商标应正确、无误才可使用。
3、质检员检验合格的,每箱应放合格证、合格证有质检员签字、生产日期、批号。
4、经检验合格后,成品方可入库。
护肤乳液工艺流程图说明:关键控制点A、油相、水相混合后、均质5分钟。
B、恒温搅拌30分钟乳化、杀菌。
注意事顶:A、油相、水相加热不得低于85℃,不得高于90℃。
B、均质时间不得少于5分钟,为保证质量。
C、恒温杀菌乳化30分钟,不得少于一分钟时间。
D、45℃加入香精,不得在45℃以上加入香精。
护肤乳液关键控制点开料员:工程师:护肤啫喱生产作业指导书(操作过程控制)一、生产前的准备:1、清洗搅拌机、生产用具、桶、铲等用具。
2、检查各种秤、衡具是否正常。
3、纯水PH值测试,应达到6—7之间。
4、纯水电导率,应控制在3---8之间。
二、秤料的操作规程:1、纯水按配方比例秤好加入,误差不得超过1% 。
2、胶浆和添加剂,按配方比例秤好加入。
3、在良好的搅拌下分散,胶浆与水分散均匀,然后加入乙醇和保湿剂,彻底搅拌均匀。
4、最后加入水溶香精和防腐剂,混合后为透明液体,最后送化验室检验合格。
5、过滤出料,放入静置室。
三、质量检验:1、PH值控制6---7之间,为合格。
2、检查透明度,应符合本企业内控标准。
3、喷雾试验,应符合本企业内控标准。
4、经检验合格后,通知分装车间灌装,并开合格放行条。
四、分装车间:1、成品凭化验室合格放行条,方可灌装。
2、灌装应检查塑料瓶是否用乙醇消毒,凡来经消毒的瓶,一律不得灌装。
3、灌装时每瓶应过秤,不得少于1ml,但也不得超过3ml,应符合标准。
4、塑料瓶,不合格或字迹不清楚的一律不得灌装。
五、包装车间:1、灌装好的成品,喷头应拧紧,防止漏液。
2、质检员应每瓶过检验,凡有沉淀物、不透明液体,应退回生产车间,重新返工。
3、纸箱装箱之前,应检查纸箱与成品、规格、数量应相符,方可装箱。
4、经质检员检验合格后,应签合格证,每箱应放合格证。
5、包装合格后,质检员应开合格检验单后,成品方可入库。
护肤啫喱工艺流程图说明:关键控制点:胶浆彻底分散和过滤。
护肤啫喱关键控制点开料员:工程师:化妆水生产作业指导书(操作过程控制)一、生产前的准备:1.清洗加热搅拌机,搅拌机干净后,才可生产。
2.清洗生产用具、桶、铲、冲洗干净后,才可使用。
3.检查校正磅秤、衡器,正确无误。
4.测试纯水PH值应在之间,方可使用。
5.纯水电导率应在8以下,达标后才可使用。