底喷流化床
药用负压底喷式流化床包衣机创新性与应用性浅析
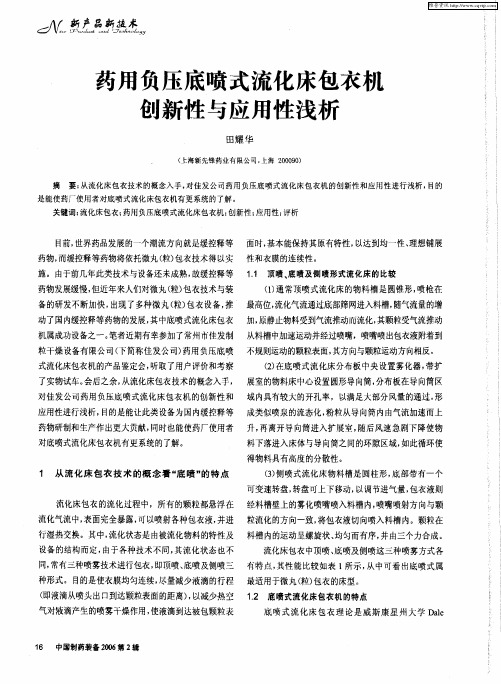
3 佳 发公 司药 用 负压 底喷 式 流 化床 包 衣 机创 新 性 浅析
31 药 用负压底 喷式流化床包 衣机关键技 术创新性 .
浅 析
顶喷 底喷 侧喷
大 中 小
中 高 低
随机 规则 规则
高 低 低
快 中 低
大 中
制粒 包衣
低 包衣、 制粒 ( 丸)
流化气流中, 表面完全暴露, 喷射各种包衣液, 可以 并进 粒流化的方向一致, 将包衣液切 向喷入料槽内。颗粒在
行湿热交换。其 中, 流化状态是 由被流化物料 的特 性及 料槽内的运动呈螺旋状、 均匀而有序, 并由三个力合成。 设备的结构而定, 由于各种 技术 不 同, 其流化状态 也不
基本原 理 负压技术是整机的关键之首, 其负压的创新性体现 在其系统的优化设置, 从而使包衣的整个工艺过程处于 工作时, 将物料按规格不低于 8% 0 的投料量投入流 密闭与负压状态, 达到了以下效果: 化床室, 通过气缸升压将各筒体密封, 开启引风机和加 ( 系统负压工艺流程可有效地避免包衣材料中有 1 )
气对液滴产生的喷雾干燥作用 , 使液滴 到达被包颗粒表 底喷 式流 化 床包 衣 理论 是 威斯 康 星 州大 学 D l a e
1 中国制药装备 2 0 2辑 6 06第
维普资讯
曼 :
表 1 i 种 喷 雾 方 式 性 能对 比
床型 风量 … 适用
流化床包衣中顶喷、 底喷及侧喷这三种喷雾方式各
同, 常有三种喷雾技术进行包衣, 即顶喷、 底喷及侧喷三 有特 点 , 能 比较如表 l 其性 所示 , 中可看 出底喷式属 从
种形式 。目的是使衣膜均匀连续, 尽量减少液滴的行程 最适用于微丸 ( 包衣 的床型。 粒)
流化床工作原理

流化床工作原理流化床是一种重要的化工设备,它在化工、冶金、环保等领域有着广泛的应用。
流化床工作原理是指在一定的条件下,固体颗粒物料在气体流动的作用下呈现出流态化的状态,这种状态下颗粒物料表现出液体的特性,具有较高的传热、传质性能。
下面我们来详细介绍一下流化床的工作原理。
首先,流化床的工作原理是基于气体流动的作用。
当气体通过床体底部喷嘴喷入时,床内的颗粒物料受到气体流动的冲击,开始呈现出流态化的状态。
在这种状态下,颗粒物料之间的空隙增大,表面积增加,使得颗粒物料表现出液态的特性,可以充分混合、传热、传质。
其次,流化床的工作原理还与颗粒物料的密度和粒径有关。
通常情况下,当颗粒物料的密度较大、粒径较小时,流化床的流态化效果会更好。
因此,在实际应用中,需要根据颗粒物料的性质和工艺要求来选择合适的颗粒物料。
另外,流化床的工作原理还与气体流速和流化剂的选择有关。
气体流速的大小会直接影响床内颗粒物料的流态化状态,通常情况下,流速越大,颗粒物料的流态化效果越好。
而流化剂的选择也会对流化床的工作原理产生影响,不同的流化剂对颗粒物料的流态化特性有着不同的影响。
此外,流化床的工作原理还与床内物料的混合、传热、传质等过程密切相关。
在流化床中,气固两相之间的充分混合使得床内物料的传热、传质效果得到了显著提高,这对于一些需要进行反应、干燥、吸附等工艺过程具有重要的意义。
综上所述,流化床的工作原理是基于气体流动的作用,通过控制气体流速、选择合适的颗粒物料和流化剂,实现颗粒物料的流态化状态,从而达到充分混合、传热、传质的效果。
流化床在化工生产中具有重要的应用价值,了解其工作原理对于提高流化床的工艺效果具有重要的意义。
希望本文能够帮助大家更深入地了解流化床的工作原理,为相关领域的工程技术人员提供参考。
流化床使用的10项基本原则
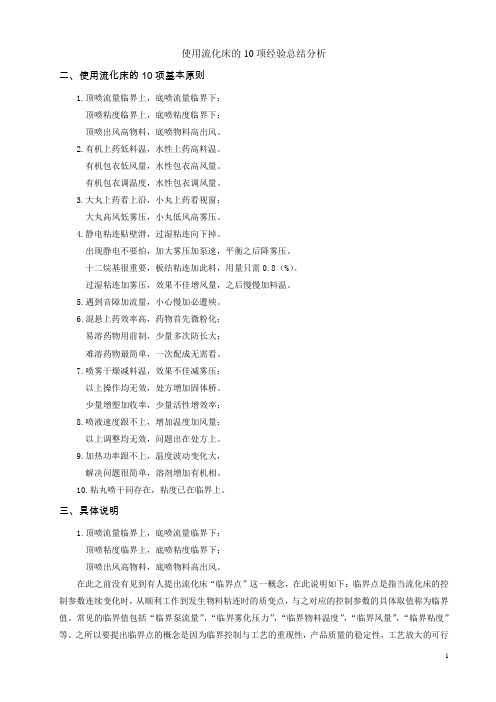
使用流化床的10项经验总结分析二、使用流化床的10项基本原则1.顶喷流量临界上,底喷流量临界下;顶喷粘度临界上,底喷粘度临界下;顶喷出风高物料,底喷物料高出风。
2.有机上药低料温,水性上药高料温。
有机包衣低风量,水性包衣高风量。
有机包衣调温度,水性包衣调风量。
3.大丸上药看上沿,小丸上药看视窗;大丸高风低雾压,小丸低风高雾压。
4.静电粘连贴壁滑,过湿粘连向下掉。
出现静电不要怕,加大雾压加泵速,平衡之后降雾压。
十二烷基很重要,板结粘连加此料,用量只需0.8(%)。
过湿粘连加雾压,效果不佳增风量,之后慢慢加料温。
5.遇到音障加流量,小心慢加必遭殃。
6.混悬上药效率高,药物首先微粉化;易溶药物用前制,少量多次防长大;难溶药物最简单,一次配成无需看。
7.喷雾干燥减料温,效果不佳减雾压;以上操作均无效,处方增加固体桥。
少量增塑加收率,少量活性增效率;8.喷液速度跟不上,增加温度加风量;以上调整均无效,问题出在处方上。
9.加热功率跟不上,温度波动变化大,解决问题很简单,溶剂增加有机相。
10.粘丸喷干同存在,粘度已在临界上。
三、具体说明1.顶喷流量临界上,底喷流量临界下;顶喷粘度临界上,底喷粘度临界下;顶喷出风高物料,底喷物料高出风。
在此之前没有见到有人提出流化床“临界点”这一概念,在此说明如下:临界点是指当流化床的控制参数连续变化时,从顺利工作到发生物料粘连时的质变点,与之对应的控制参数的具体取值称为临界值。
常见的临界值包括“临界泵流量”,“临界雾化压力”,“临界物料温度”,“临界风量”,“临界粘度”等。
之所以要提出临界点的概念是因为临界控制与工艺的重现性,产品质量的稳定性,工艺放大的可行性密切相关,直接关系到研发的成败。
“顶喷流量临界上,底喷流量临界下”说的是在顶喷造粒时应当将泵流量控制高于流量临界点以上,使得喷出的粘合剂多于临界泵流量时的粘合剂量,这时的粘合剂能在细粉粒子之间形成液体桥,逐步干燥过程形成固体桥,干燥后形成稳定的颗粒。
流化床制粒技术介绍
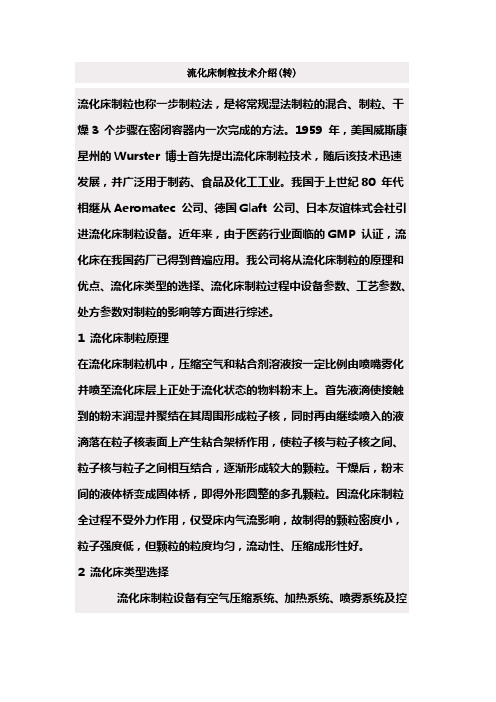
流化床制粒技术介绍(转)流化床制粒也称一步制粒法,是将常规湿法制粒的混合、制粒、干燥3 个步骤在密闭容器内一次完成的方法。
1959 年,美国威斯康星州的Wurster 博士首先提出流化床制粒技术,随后该技术迅速发展,并广泛用于制药、食品及化工工业。
我国于上世纪80 年代相继从Aeromatec 公司、德国Glaft 公司、日本友谊株式会社引进流化床制粒设备。
近年来,由于医药行业面临的GMP 认证,流化床在我国药厂已得到普遍应用。
我公司将从流化床制粒的原理和优点、流化床类型的选择、流化床制粒过程中设备参数、工艺参数、处方参数对制粒的影响等方面进行综述。
1 流化床制粒原理在流化床制粒机中,压缩空气和粘合剂溶液按一定比例由喷嘴雾化并喷至流化床层上正处于流化状态的物料粉末上。
首先液滴使接触到的粉末润湿并聚结在其周围形成粒子核,同时再由继续喷入的液滴落在粒子核表面上产生粘合架桥作用,使粒子核与粒子核之间、粒子核与粒子之间相互结合,逐渐形成较大的颗粒。
干燥后,粉末间的液体桥变成固体桥,即得外形圆整的多孔颗粒。
因流化床制粒全过程不受外力作用,仅受床内气流影响,故制得的颗粒密度小,粒子强度低,但颗粒的粒度均匀,流动性、压缩成形性好。
2 流化床类型选择流化床制粒设备有空气压缩系统、加热系统、喷雾系统及控制系统等组成。
主要结构由容器、空气分流板、喷嘴、过滤袋、空气进出口、物料排出口等组成。
按其喷液方式的不同分为3 类:顶喷流化床、转动切喷流化床、底喷流化床。
流化床制粒一般选择顶喷流化床。
近年来,为了发挥流化床制粒的优势,亦出现了一系列以流化床为母体的多功能复合型制粒设备。
如我公司新推出的多功能流化床、搅拌流化制粒机、转动流化制粒机、搅拌转动流化制粒机等。
现我们仅就流化床制粒进行探讨。
3 流化床制粒的优点尽管流化床制粒受到诸多因素影响,但与其他制粒方式相比,该技术仍具有很多优点。
a .物料的干混、湿混、搅拌、颗粒成型、干燥都在同一台流化床设备内完成,减少了大量的操作环节,节约了生产时间。
实验室多功能流化床包衣设备(制粒、微丸、干燥)

实验室多功能流化床包衣设备(制粒、微丸、干燥)概述:实验型多功能流化床是专为科研机构,各高校量身定制的功能强大的研发型设备,其设计兼顾了灵活性与适用性,可在一台设备中完成干燥、制粒、包衣、制备微丸等功能。
实验型多功能流化床是在消化吸收国外同类设备基础上推出的具有多种用途的流化床工艺设备,其设计目的是为了在同一设备中可进行干燥、制粒、制丸、包衣及包裹敷层。
根据不同工艺目的,可采取三种工艺(“顶喷”、“底喷”、“切线喷”)途径实现。
通过更换不同的流化床装置,即可进行三种工艺操作,而其他功能系统则可共用(空气处理系统,机身组件,供液系统,送风系统,控制系统)。
不同的流化床结构是最为核心的技。
三种工艺具有不同的能力,其实质区别仅在于物料的流化和液体的喷入方式不同。
实验室多功能流化床包衣设备(制粒、微丸、干燥)工作原理:在流化床上进行喷雾团聚造粒是一种可以增强粉末性质的成型方法。
通过在流化床系统中进行喷雾,我们可以将粉状、非流动性、溶解度普遍较差的颗粒转化成具有优异溶解度的自由流动的大颗粒。
该方法特别适用于制备片剂以及制造清洁剂、饮用粉末、速溶产品。
流化床喷雾团聚造粒可以移动流化床上极小的粉末颗粒,并对其喷以粘合溶液或悬浮液,产生液桥,使颗粒形成团聚体。
继续喷雾,直到团聚体达到所需大小。
当毛细管以及表面上的残余水分蒸发后,颗粒中形成中空的空间,而硬化的粘合剂也使新结构彻底凝固。
流化床中缺乏动能,会造成极为多孔的结构,其内部存在大量的毛细管。
团聚体的通常尺寸范围为100微米至3毫米,而起始材料可以是超微细的。
流化床干燥—颗粒受控干燥的高效解决方案(FLP1.5多功能流化床包衣机)流化床干燥是对湿润粉末进行受控、柔和、均匀的干燥的最佳方法。
流化床产品剧烈的热量/质量交换使这种方法变得特别有效、省时。
该技术还适用于残余水分极低的喷塑产品和挤塑产品的后干燥。
流化床干燥可用于整个粉末加工业。
在制药行业,这种创新的方法早已取代耗时的托盘干燥:使用流化床干燥的干燥工艺可以将干燥炉中的干燥时间减少约20倍。
综述-流化床微丸包衣影响因素探讨
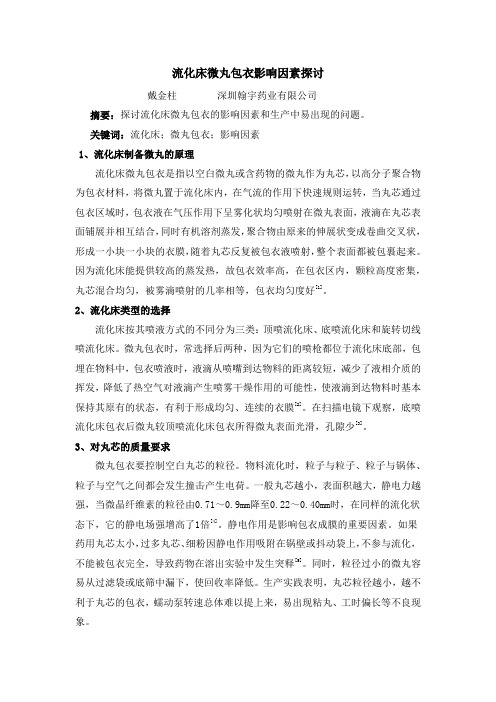
流化床微丸包衣影响因素探讨戴金柱深圳翰宇药业有限公司摘要:探讨流化床微丸包衣的影响因素和生产中易出现的问题。
关键词:流化床;微丸包衣;影响因素1、流化床制备微丸的原理流化床微丸包衣是指以空白微丸或含药物的微丸作为丸芯,以高分子聚合物为包衣材料,将微丸置于流化床内,在气流的作用下快速规则运转,当丸芯通过包衣区域时,包衣液在气压作用下呈雾化状均匀喷射在微丸表面,液滴在丸芯表面铺展并相互结合,同时有机溶剂蒸发,聚合物由原来的伸展状变成卷曲交叉状,形成一小块一小块的衣膜,随着丸芯反复被包衣液喷射,整个表面都被包裹起来。
因为流化床能提供较高的蒸发热,故包衣效率高,在包衣区内,颗粒高度密集,丸芯混合均匀,被雾滴喷射的几率相等,包衣均匀度好[1]。
2、流化床类型的选择流化床按其喷液方式的不同分为三类:顶喷流化床、底喷流化床和旋转切线喷流化床。
微丸包衣时,常选择后两种,因为它们的喷枪都位于流化床底部,包埋在物料中,包衣喷液时,液滴从喷嘴到达物料的距离较短,减少了液相介质的挥发,降低了热空气对液滴产生喷雾干燥作用的可能性,使液滴到达物料时基本保持其原有的状态,有利于形成均匀、连续的衣膜[2]。
在扫描电镜下观察,底喷流化床包衣后微丸较顶喷流化床包衣所得微丸表面光滑,孔隙少[3]。
3、对丸芯的质量要求微丸包衣要控制空白丸芯的粒径。
物料流化时,粒子与粒子、粒子与锅体、粒子与空气之间都会发生撞击产生电荷。
一般丸芯越小,表面积越大,静电力越强,当微晶纤维素的粒径由0.71~0.9mm降至0.22~0.40mm时,在同样的流化状态下,它的静电场强增高了1倍[4]。
静电作用是影响包衣成膜的重要因素。
如果药用丸芯太小,过多丸芯、细粉因静电作用吸附在锅壁或抖动袋上,不参与流化,不能被包衣完全,导致药物在溶出实验中发生突释[5]。
同时,粒径过小的微丸容易从过滤袋或底筛中漏下,使回收率降低。
生产实践表明,丸芯粒径越小,越不利于丸芯的包衣,蠕动泵转速总体难以提上来,易出现粘丸、工时偏长等不良现象。
底喷流化床(Wurster)包衣的操作要点 !

GSP认证及经营许可证办理交流区
ISO17025实验室管理交流区
欧盟CE认证交流区
FDA 美国食品和药物管理交流区
标准资料下载区
标准资讯快递
国外国际标准讨论下载发布区
[ ISO国际标准化组织标准]
[ IEC 国际电工委员会 ]
[ AOAC国际官方分析化学家协会标准 ]
[ BS 英国标准 ]
[ ASTM 美国材料试验协会标准 ]
[ DIN 德国标准 ]
[ JIS 日本标准 ]
[ EN标准 ]
[ NF标准 ]
[ ANSI 标准 ]
[ AATCC标准 ]
[ ETSI标准 ]
[ IS标准 ]
[ 美国标准 ]
国家标准发布下载区
医药行业标准发布下载区
此外,调节间距还可小幅度调节颗粒流化状态。比如遇到导流管外侧颗粒滞留不动时,增加间距,可促使滞留颗粒启动。因为增加间距,也就增加了导流管下面颗粒层的厚度,增大了阻力,逼使空气流向周边小孔。
底喷流化床包衣过程中常见的问题
静电
颗粒在流化床内不停运动,相互摩擦,有静电产生,导致颗粒相互吸引,也被筒壁吸附,颗粒不能正常流化。静电的出现反映颗粒己经比较干燥。用有机溶液包衣,或在干燥季节包衣更容易产生静电。提高进风相
GMT+8, 2009-11-1 01:20. Powered by Discuz! 7.0.0
© 2001-2009 Comsenz Inc.
药物检测分析讨论区
消毒灭菌讨论版块
中药讨论区
药品说明书
[抗病原微生物药]
世界顶尖流化床品牌-Glatt实验室流化床

包衣
具有和底喷系统几乎同样的包衣优点,
因此可以包出高质量的衣膜
粉末上药工艺
优 点: 同一设备中完成上药、干燥、 包衣工艺 生产效率高,生产周期短 适用于各种溶解度性质的药物 制备载药量大的微丸,适合大 剂量药物(增重400~500%) 局限性: 对工艺参数的控制要求较高 药物须微粉化,并加入助流剂
• 防潮及抗氧化 •缓释 特点:
工艺周期短
An Example...
顶喷热熔融包衣
MAIN MENU
未包衣颗粒
30% 包衣增重 Compritol 888
制粒工艺
湿法制粒 – 摇摆式制粒 – 流化床制粒 – 高速混合制粒 干法制粒 熔融制粒
流化床底喷技术
底喷装置也成为Wurster系统, 由Dale Wuster教授研制,是
流化床技术简介
70 年代以来,流化床技术和喷枪技术相结合,应用上有
很大的突破,广泛应用于制粒、包衣、微丸制备等工艺,
主要用于制药、食品、化工、陶瓷等行业。
流化床类型
MAIN MENU
顶喷 制粒
底喷 包衣
切线喷 制微丸
流化床技术简介
设备发展趋势
规格齐全:批处理能力从 2.5g 到大于 1 吨
处方研究设备
Mini-Glatt
工作容积: 200 - 750ml 批 量: 30 - 300 g • 制粒 • 包衣
MAIN MENU
• 干燥
Mini-Glatt 对压缩空气的要求
Compressed air utility:
MAIN MENU
Working pressure: 6 bar flow pressure
流化床制粒工艺开发及优化探讨

流化床制粒工艺开发及优化探讨摘要:流化床制粒作为改善粉体不良性质的主要制粒方法,由于其工艺环节少,颗粒均匀、可压性好等特点,近年来在制药工业中备受关注。
本文就流化床技术的特点、基本理论和工艺优化等方面进行了较为详细的阐述。
关键词:流化床制粒;基本理论;工艺优化;前言流化床制粒也叫一步制粒,主要是将常规湿法制粒的混合、制粒、干燥三个步骤在密闭容器内一次完成的方法。
我国于上世纪80年代引进流化床制粒设备,近年来在我国已得到普遍应用[1]。
根据喷液方向与物料运动方向的不同,可将流化床分为三类:顶喷流化床、底喷流化床、切线喷流化床。
三种流化床构造的不同使它们具有不同的工艺用途。
其中顶喷流化床制粒广泛用于粉体的制粒工艺,本文将对其基本原理、变量控制和优化等方面进行介绍。
1 流化制粒基本理论流化床制粒首先通过吹入热空气将物料在流化状态下混合,对其再喷入制粒所用的粘合剂溶液,直到达到符合要求的润湿量或颗粒大小,然后对湿颗粒进行干燥到预定的温度或干燥失重。
下面将详细介绍粒子在流化床内流化、聚集成长的过程和理论。
1.1 粒子流化理论流化床操作过程是由热空气向上通过装载固体物料的床体。
空气影响流化状态的机理已经被很多研究者讨论过[2]。
在低气体流速下,粒子床是一个固体床,压力差与表观速度成正比。
随着气体流速的增加,达到粒子床从固定粒子到流化粒子转变的临界点。
当气体流速增大,通过床的压力差也增大,直到在特定流速时粒子的摩擦力等于床体的有效重量。
当气体流速逐渐增加,粒子床开始膨胀,高度逐渐增加,而压力差只有轻微的增大。
在一定的流化速度下,粒子被气体携带,这种现象称为“夹带”。
当进风速度足够大时,粒子床上表面界限逐渐模糊,夹带更为显著,粒子被气流带离流化床。
影响流化状态的因素包括:①进风速度;②空气分配板孔径和直径;③粒子的大小和密度;④物料含湿量;⑤流化床直径/高度比。
其中,进风速度是影响流化状态的最主要因素。
1.2 粒子聚集理论聚集是粒子长大的过程。
流化床工艺的三种类型PK

流化床工艺目前主要有三种类型:顶喷、底喷、旋转切线喷。
由于设备构造不同,物料流化状态也不相同。
采用不同工艺,包衣质量和制剂释放特性可能有所区别。
原则上为了使衣膜均匀连续,每种工艺都应尽量减少包衣液滴的行程,即液滴从喷枪出口到底物表面的距离,以减少热空气对液滴产生的喷雾干燥作用,使包衣液到达底物表面时,基本保持其原有的特性,浓度和粘度没有明显增加,以保证在底物表面理想的铺展成膜特性,形成均匀、连续的衣膜。
1、底喷工艺又称为Wurster系统,是流化床包衣的主要应用形式,已广泛应用于微丸、颗粒,甚至粒径小于50μm粉末的包衣。
底喷装置的物料槽中央有一个隔圈,底部有一块开有很多圆形小孔的空气分配盘,由于隔圈内/外对应部分的底盘开孔率不同,因此形成隔圈内/外的不同进风气流强度,使颗粒形成在隔圈内外有规则的循环运动。
喷枪安装在隔圈内部,喷液方向与物料的运动方向相同,因此隔圈内是主要包衣区域,隔圈外则是主要干燥区域。
颗粒每隔几秒种通过一次包衣区域,完成一次包衣-干燥循环。
所有颗粒经过包衣区域的几率相似,因此形成的衣膜均匀致密。
实验和中试型设备(空气分配底盘直径大至18英寸)使用一个隔圈和喷枪,形成一个包衣区域。
大生产设备(空气分配底盘直径大至46英寸)增加隔圈和喷枪数量,扩大包衣区域以提高生产效率。
Wurster HS是底喷工艺的一项新技术,对传统Wurster喷枪系统进行了一些改进,使颗粒避免接触到喷嘴局部还未充分雾化的包衣液滴,和喷嘴局部由于雾化压力产生的负压区域,因此颗粒产生粘结的几率大大降低。
与传统Wurster系统相比,Wurster HS系统中:•喷液速率提高3-4倍,每个喷枪可达500-600g/min,因而充分利用了流化床的干燥效率,缩短生产周期;•喷枪可以使用较高的雾化压力,以形成非常小的雾化液滴,满足对小于100μm 颗粒的包衣需求;•颗粒避免接触喷嘴局部的压缩空气高速区域,减少包衣初期的表面磨损,有利于保持恒定的比表面积。
流化床操作流程
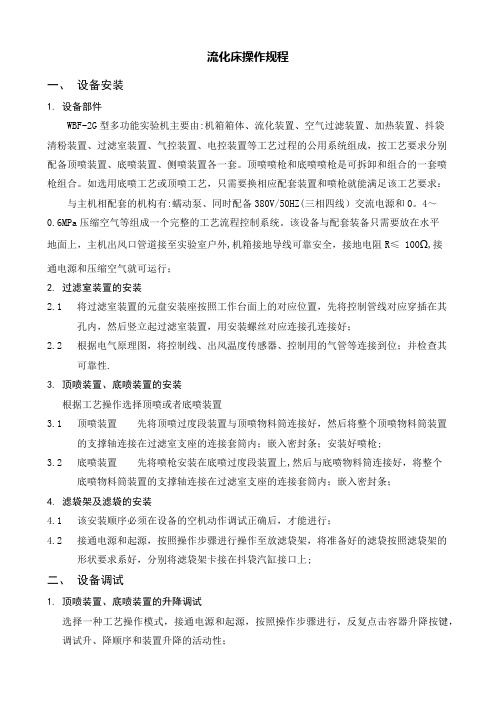
流化床操作规程一、设备安装1.设备部件WBF-2G型多功能实验机主要由:机箱箱体、流化装置、空气过滤装置、加热装置、抖袋清粉装置、过滤室装置、气控装置、电控装置等工艺过程的公用系统组成,按工艺要求分别配备顶喷装置、底喷装置、侧喷装置各一套。
顶喷喷枪和底喷喷枪是可拆卸和组合的一套喷枪组合。
如选用底喷工艺或顶喷工艺,只需要换相应配套装置和喷枪就能满足该工艺要求:与主机相配套的机构有:蠕动泵、同时配备380V/50HZ(三相四线)交流电源和0。
4~0.6MPa压缩空气等组成一个完整的工艺流程控制系统。
该设备与配套装备只需要放在水平地面上,主机出风口管道接至实验室户外,机箱接地导线可靠安全,接地电阻R≤ 100Ω,接通电源和压缩空气就可运行;2.过滤室装置的安装2.1将过滤室装置的元盘安装座按照工作台面上的对应位置,先将控制管线对应穿插在其孔内,然后竖立起过滤室装置,用安装螺丝对应连接孔连接好;2.2根据电气原理图,将控制线、出风温度传感器、控制用的气管等连接到位;并检查其可靠性.3.顶喷装置、底喷装置的安装根据工艺操作选择顶喷或者底喷装置3.1顶喷装置先将顶喷过度段装置与顶喷物料筒连接好,然后将整个顶喷物料筒装置的支撑轴连接在过滤室支座的连接套筒内;嵌入密封条;安装好喷枪;3.2底喷装置先将喷枪安装在底喷过度段装置上,然后与底喷物料筒连接好,将整个底喷物料筒装置的支撑轴连接在过滤室支座的连接套筒内;嵌入密封条;4. 滤袋架及滤袋的安装4.1该安装顺序必须在设备的空机动作调试正确后,才能进行;4.2接通电源和起源,按照操作步骤进行操作至放滤袋架,将准备好的滤袋按照滤袋架的形状要求系好,分别将滤袋架卡接在抖袋汽缸接口上;二、设备调试1.顶喷装置、底喷装置的升降调试选择一种工艺操作模式,接通电源和起源,按照操作步骤进行,反复点击容器升降按键,调试升、降顺序和装置升降的活动性;2.喷枪雾化效果的调试将压缩空气接入喷枪,启动系统至喷雾运行状态,调节供液频率和雾化压力可改变雾化效果;颗粒成型原理:雾滴大小与液体流量成正比,与雾化压力成反比雾化角度(微调)可通过雾化压力和调试喷枪头的空气帽来完成。
一步制粒机干燥方式与干燥设备的选型问题
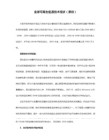
应用:⑴制粒:提高崩解、改善可压性、增加密度、圆化颗粒表面;⑵制丸:增加密度、制球形颗粒、高效能药丸、使颗粒表面光滑;⑶包裹敷层:溶液、混悬液包裹敷层、粉末包裹敷层、高效能药丸、粒径范围分布集中、增加密度;⑷包衣:薄膜衣、肠溶衣、缓释包衣、热熔融包衣。
(4)下筒体的顶升托架采用套缸式,用双大口径气缸实现升降,从而使三个筒体能完全密封。筒体的法兰之间采用法兰线与硅橡胶密封垫密封,无泄漏,可靠性高。并且在下筒体与托架的套缸型式中,装有下充气密封圈,保证活动的套缸能完全密封不泄漏。
(5)过滤加热器,采用不锈钢制作,箱体外包镜面或花纹不锈钢,过滤器为亚高效过滤器。
1.侧喷流化床处理过பைடு நூலகம்离心流化床与常规流化床主要区别在于一个速度可调的旋转盘,转盘与床体具备一窄缝。物料投入床内,并受到三个力的作用:离心力、空气的举力及本身重力作用,呈螺旋的绳股状运动。就单个粉粒而言,其轨迹基本恒定。雾化器设置在床壁,并顺着旋转方向同向喷入。
2.制丸离心床内物料所产生的物料自转、公转运动及相互摩擦作用,能生产出真球度高、表面光滑的药丸。影响药丸真球度的因素有喷液流量、风量大小、转子转速、雾粒大小及供粉速度。就某种药丸而言,必须匹配好这些参数,方能得到重复性良好的工艺。
一、沸腾制粒
许多制粒设备都兼有干燥的功能,所以制粒设备也多以干燥设备厂制造。为用户选型的方便,在此书中对制粒设备也有一些简单介绍。流化床技术在制药界广泛运用于粉粒干燥、造粒、冷却。无论是基础理论,还是工程运用,均已为人们熟知。已将流化床技术作为粉粒包衣、制丸,并开发了气动旋转流化床,喷动连续作业流化床等先进技术。目前国内已开发底喷流化床制粒包衣及侧喷离心流化床制丸包衣,至今已在多家制药厂得到运用。在中、西药片剂生产中,混合与制粒是压片前的重要工序,颗粒的质量是决定药片质量的关键。
【小白说】连载:吐血干货——流化床工艺放大
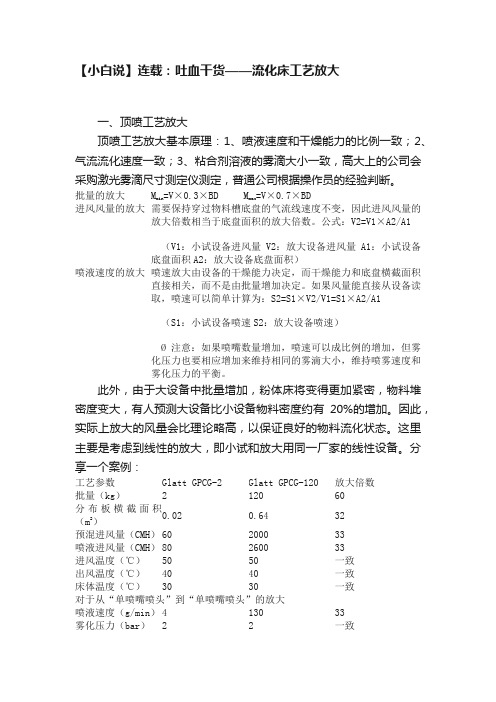
【小白说】连载:吐血干货——流化床工艺放大一、顶喷工艺放大顶喷工艺放大基本原理:1、喷液速度和干燥能力的比例一致;2、气流流化速度一致;3、粘合剂溶液的雾滴大小一致,高大上的公司会采购激光雾滴尺寸测定仪测定,普通公司根据操作员的经验判断。
批量的放大Mmin =V×0.3×BD Mmax=V×0.7×BD进风风量的放大需要保持穿过物料槽底盘的气流线速度不变,因此进风风量的放大倍数相当于底盘面积的放大倍数。
公式:V2=V1×A2/A1(V1:小试设备进风量V2:放大设备进风量A1:小试设备底盘面积A2:放大设备底盘面积)喷液速度的放大喷速放大由设备的干燥能力决定,而干燥能力和底盘横截面积直接相关,而不是由批量增加决定。
如果风量能直接从设备读取,喷速可以简单计算为:S2=S1×V2/V1=S1×A2/A1(S1:小试设备喷速S2:放大设备喷速)Ø注意:如果喷嘴数量增加,喷速可以成比例的增加,但雾化压力也要相应增加来维持相同的雾滴大小,维持喷雾速度和雾化压力的平衡。
此外,由于大设备中批量增加,粉体床将变得更加紧密,物料堆密度变大,有人预测大设备比小设备物料密度约有20%的增加。
因此,实际上放大的风量会比理论略高,以保证良好的物料流化状态。
这里主要是考虑到线性的放大,即小试和放大用同一厂家的线性设备。
分享一个案例:工艺参数Glatt GPCG-2 Glatt GPCG-120 放大倍数批量(kg) 2 120 60分布板横截面积(m2)0.02 0.64 32预混进风量(CMH)60 2000 33喷液进风量(CMH)80 2600 33进风温度(℃)50 50 一致出风温度(℃)40 40 一致床体温度(℃)30 30 一致对于从“单喷嘴喷头”到“单喷嘴喷头”的放大喷液速度(g/min)4 130 33雾化压力(bar) 2 2 一致对于从“单喷嘴喷头”到“三喷嘴喷头”的放大喷嘴个数 1 3 3喷液速度(g/min)4 390 33*3雾化压力(bar) 2 6 3干燥风量(CMH)100 3200 32*CMH 即cube meter hour(m/h),意为立方米/小时,但是CMH一般只用于表示风系统中的风量。
底喷流化床包衣工作原理
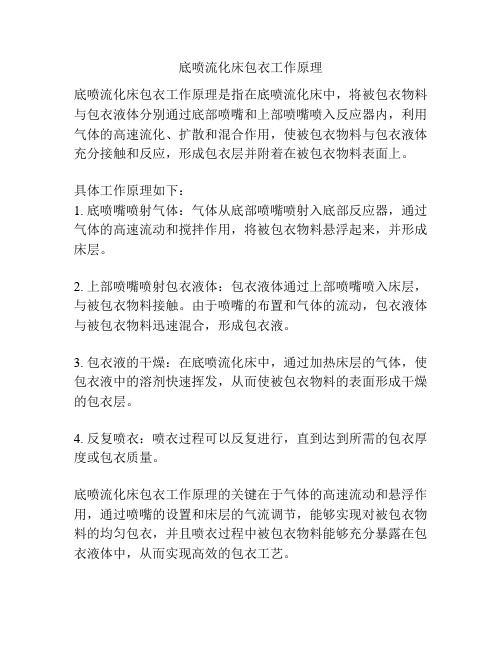
底喷流化床包衣工作原理
底喷流化床包衣工作原理是指在底喷流化床中,将被包衣物料与包衣液体分别通过底部喷嘴和上部喷嘴喷入反应器内,利用气体的高速流化、扩散和混合作用,使被包衣物料与包衣液体充分接触和反应,形成包衣层并附着在被包衣物料表面上。
具体工作原理如下:
1. 底喷嘴喷射气体:气体从底部喷嘴喷射入底部反应器,通过气体的高速流动和搅拌作用,将被包衣物料悬浮起来,并形成床层。
2. 上部喷嘴喷射包衣液体:包衣液体通过上部喷嘴喷入床层,与被包衣物料接触。
由于喷嘴的布置和气体的流动,包衣液体与被包衣物料迅速混合,形成包衣液。
3. 包衣液的干燥:在底喷流化床中,通过加热床层的气体,使包衣液中的溶剂快速挥发,从而使被包衣物料的表面形成干燥的包衣层。
4. 反复喷衣:喷衣过程可以反复进行,直到达到所需的包衣厚度或包衣质量。
底喷流化床包衣工作原理的关键在于气体的高速流动和悬浮作用,通过喷嘴的设置和床层的气流调节,能够实现对被包衣物料的均匀包衣,并且喷衣过程中被包衣物料能够充分暴露在包衣液体中,从而实现高效的包衣工艺。
药物制粒技术及流化床制粒影响因素的探讨概要

流化 床制粒的优点
• (1)集混合一制粒一干燥于一体,混合的时 间、产品水分含量、 干燥后制粒质量和均 匀性等满足相应要求;(2)制粒成品颗粒较 松,粒度在 20〜80目,且成品外观近似球 形,流动性好;(3)生产效率高、劳动强度 低; (4)混合、制粒、干燥过程均应在全封 闭负压状态下,以防止粉尘污染和飞扬, 受外界污染低。
喷雾制粒技术现状
• 流化喷雾制粒亦称“一步制粒法”是将粉末置流 化床内保持“动的悬浮”, 以黏合剂为媒介粉 末相互凝集成粒的制料方法,此法的优点是制成 的颗粒均匀, 尤适于亲水性和吸湿性小的物料 制粒。但此法一般用于大生产。小量制粒可用喷 雾干燥制粒法。
• 喷雾干燥制粒系将含药液(含水量可达70%〜 80%以上)经雾化后直接干 燥成颗粒(或粉末) 的制粒方法,已作为一项较先进的干燥技术应用 于药剂制 备。制品不仅外观和内在质量好,而 且适用于热敏性物料。中药提取浓缩至能均 匀 流动时,即能用此法直接雾化成粉或颗粒。但此 法对含挥发性成分或贵重药的药液不适用。
2连续流化床制粒机
• 连续流化床制粒机在传统沸腾干流技术中 融入喷雾和气流分级的技术,它是 流化床 设备的衍生产品。其特点:(1)采用流化冷 却(干燥)方式,质热传递 快;(2)喷雾 方式制粒,产品强度可控;(3)气源系统分 级,成品粒度范围极 小;(4)连续式制粒 作业,生产效率高。主要用于医药、食品、 化工等行业的粉 末物料混合、干燥、制粒、 颗粒“喷涂”、放大、熔融液冷却造粒等 作业。
• 湿法制粒在固体制剂中常适用于需要添加黏合剂 (如乙醇、糊精)进行混合 才能成粒的药品。 其同时适用于:(1)压片时需加入黏合剂可增强 粉末的可压缩 性和黏着性;(2)胶囊充填或压片 对流动性要求较高时可用此法;(3)对低剂量 药 物分布均匀、色彩良好,也可用此法解决;(4) 固体制剂中也可用此法,使用 适当的溶剂和黏 合剂增加药物溶出速率。
世界顶尖流化床品牌-Glatt实验室流化床
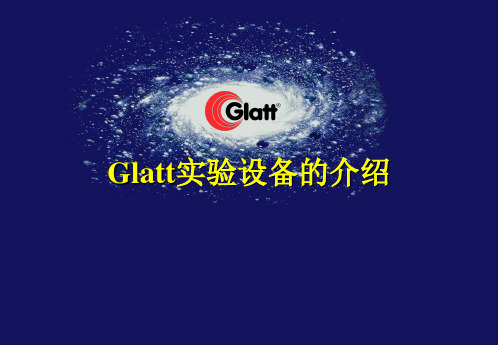
流化床顶喷技术的应用 1
一步制粒:
MAIN MENU
• 适用于大多数处方, 微晶纤维素和乳糖是比较好的 颗粒成型辅料, 原辅料粒径尽量小
• 粘合剂: HPMC或PVP溶液 • 低剂量药物( 如小于1 mg ) • 中药制粒(片剂、颗粒剂)
流化床顶喷技术的应用 2
热熔融包衣
MAIN MENU
•掩味
20 µ m, 防静电
GPCG1.1流化床的其他特点
MAIN MENU
工艺装置更换方便
便捷的进、出料
GPCG1.1流化床的其他特点
MAIN MENU
取样方便
蠕动泵
GPCG 2 流化床的主要特点
1. 防爆设计,符合欧洲ATEX安全规范 2. 可以增加进风除湿功能 3. 过滤袋和进/出风过滤器更换更加方便 4. 可以采用高效过滤器 5. 可以采用底部密闭出料 6. 不同容量的物料槽可供选择
4 冷却
MAIN MENU
跳转点 物料温度
出风温度
物料温度 出风温度
物料温度 出风温度
物料温度 出风温度
时间
时间
时间
时间
EcoView 控制系统特性
1. 操作安全 错误操作时有详细报警说明,并提供操作指导
MAIN MENU
2. 进风温度、风量、雾化压力等由PI(D) 精确控制
3. 工艺参数可设定允许波动的最小和最大值范围, 超出范围警报提示 4. 可设定四级密码:参观,操作,主管,维修
Glatt实验设备的介绍
实验设备介绍
流化床
MAIN MENU
高速混合制粒机
高速整粒机
高效包衣锅
流化床技术简介
流化床喷雾技术及应用

流化床喷雾技术及应用邹龙贵(常州市佳发制粒干燥设备厂,常州 213116)摘要:从流态化机理分析了粉粒物料在气相介质的运行轨迹,阐述了顶喷流化床制粒、底喷流化床包衣、旋转流化制丸及旋流流化床技术,并就相应的工艺进行分析,介绍其在医药、化工、食品中的应用实例。
关键词:流化床;顶喷;底喷;侧喷;包衣;制粒喷雾流态化具有气固两相大面积对流、传热传质快、效率高的特点,在工业上被广泛用于制粒、制丸及包衣。
1 顶置喷雾流化床1.1 顶置式喷雾流化床流程系统示意图(图1)图1 顶置式喷雾流化床流程系统空气经过滤、加热后进入流化床,促使物料流化;粘合剂经雾化器雾化成细小雾粒,喷射至流化的粉料上,物料得以润湿,相互间聚集架桥,水分经干燥后形成固体颗粒。
传统的制粒工艺:粉体干混粘合剂湿材挤压成条状颗粒干燥运用流化床顶喷法制粒,将混合—制粒—干燥多道工序纳入一台设备内完成。
与传统工艺相比:(1)缩短3/4以上操作时间,降低了操作强度;(2)成粒为近似球形,流动性好,利于压模成型和包装计量;(3)制粒时完成干燥,成粒为多孔性,利于速溶。
1952年瑞士AEROMATIC公司首次研究成功流动床干燥机,并将流态化与喷雾技术有机结合,开发了医药、食品、化工行业的流化床制粒设备。
我国80年代相继从AEROMATIC公司、德国GLATT公司,日本友谊株式会社引进该设备;近年来,医药行业面临的GMP认证,流化床在我国药厂已得到普遍应用。
1.2 顶喷流化床包衣的特点(1) 逆向喷雾喷雾方向与物料运动方向相反,液滴到达物料需运行一段距离,其间会蒸发掉部分湿份,从而降低粘性,铺展范围降低,衣膜成形慢。
(2)不规则流态化顶喷流化床内物料运行是随机的、杂乱无章的,每个粉粒接触液滴机会并不一致,因而包衣并不是均匀的。
(3)衣膜特性由于物料流化态的不规则性,衣膜不可能连续,厚薄不匀,会伴随产生孔隙等缺陷。
(4)顶置喷雾对喷雾范围不必加以约束,因而容易进行工业化放大,德国GLATT公司已生产2000kg/批机型,国内已生产300kg/批投料的包衣机型;但会有少量颗粒出现粘连现象。
世界顶尖流化床品牌-Glatt实验室流化床

2020年5月24日星期日
•实验设备介绍
流化床 高速混合制粒机 高速整粒机 高效包衣锅
•流化床技术简介
流化床技术是 50 年代发展起来的,最初设计只是用作 干燥设备,以提高干燥效率。
•德国Glatt公司1959年制造的 •全世界第一台用于制药工业的流化床
120kg
•
• 安丘市鲁安药业有限责任公司
• 扑热息痛一步制粒工艺
• 1 kg
1000 kg
•: •Glatt 实验型流化床的部分客户
•上海兴康医药开发有限公司 •上海强生制药有限公司 •上海爱的发制药有限公司 •上海复旦大学药学院 •上海医药工业研究院 •北京四环药厂 •北京军事医学科学院毒物药物研究所 •北京天衡药物研究院 •中美天津史克制药有限公司 •天津药业集团药物研究所 •深圳海王生物工程股份有限公司 •珠海丽珠集团制药总厂 •中国药科大学 •南京正大天晴制药有限公司 •哈药集团制药总厂 •华西医科大学药学院靶向给药实验室
•流化床技术的基本特征:
•
比较高的干燥效率
•流化床技术简介
70 年代以来,流化床技术和喷枪技术相结合,应用上有 很大的突破,广泛应用于制粒、包衣、微丸制备等工艺, 主要用于制药、食品、化工、陶瓷等行业。
• 流化床类型
•顶 喷 •制 粒
•底 喷 •包 衣
•切线喷 •制微丸
•流化床技术简介
设备发展趋势
微丸包衣
丸芯上药(溶液 / 混悬液) 胃溶 / 肠溶 / 缓释包衣
颗粒 / 药物结晶包衣
粉末包衣(50 - 200 µm)
掩盖苦味(口崩片/分散片/颗粒剂) 提高稳定性 缓释混悬剂
片剂包衣 ( 3 - 10mm )
- 1、下载文档前请自行甄别文档内容的完整性,平台不提供额外的编辑、内容补充、找答案等附加服务。
- 2、"仅部分预览"的文档,不可在线预览部分如存在完整性等问题,可反馈申请退款(可完整预览的文档不适用该条件!)。
- 3、如文档侵犯您的权益,请联系客服反馈,我们会尽快为您处理(人工客服工作时间:9:00-18:30)。
1.流化床包衣技术的基本概念
1.1 流化现象的概念
在一个设备中,将颗粒物料堆放在分布板上,当气体由设备下部通入床层,随气流速度加大到某种程度,固体颗粒在床层上产沸腾状态,这状态称流态化,而这床层也称流化床。
采用这样方法辅于其它技术可完成物料的干燥、制粒、混合、包衣和粉碎等功能。
由于固体颗粒物料的不同特性,以及床层和气流速度等因素不同,床层可存在三种形态:(1)、第一阶段,当流体速度较低时,在床层中固体颗粒虽与流体相接触,但固体颗粒的相应位置不发生变化,这时固定颗粒的状态为固定床;
(2)、第二阶段,当固定床阶段的流体流速逐渐增加到某一点时,固体颗粒就会产生相互间的位置移动,若再增加流体速度,而床层的压力损失保持不变,固体颗粒再床层就会产生不规则的运动,这时的床层就处于流态化;
(3)、第三阶段,当流体流速大于固体颗粒的沉降速度时,这时固体颗粒就不能继续停留再容器内,而被气流带出容器。
对制药工业应用来说,干燥、制粒、混合、包衣等是利用第二阶段运行的。
1.2 流化床包衣技术的概念
流化床包衣是在流化过程中,所有的颗粒都悬浮在流化气流中,表面完全暴露,可以喷射各种包衣液,并进行湿热交换。
其中,流化状态是由被流化物料的特性及设备的结构而定,由于每种技术不同,其流化状态不同,常有三种喷雾技术进行包衣,即顶喷、底喷及测喷三种形式。
为了使衣膜均匀连续,尽量做到减少液滴的行程(即液滴从喷头出口到达颗粒表面的距离),以减少热空气对液滴产生的喷雾干燥作用,使得液滴到被包颗粒表面时,基本能保持其原有特性,以达到均一性、理想铺展性和衣膜的连续性。
2.从三种流化床包衣技术的比较看“底喷”流化床包衣的特点
流化床包衣技术的三种型式分别为顶喷、底喷及侧喷,下面用表格形式对三种形式的流化床包衣技术作比较(见表1)。
从表1可以看到:三种流化床包衣形式是各有特点,然而综合各项与微粒(丸)包衣要求现也可看到底喷式属其中最适用于微丸(粒)包衣的床型。
底喷式流化床包衣是威斯康星洲大学Dale Wurster博士于1959年创立,其把喷动流态化与喷雾相结合,形成喷泉状态,使工业化包衣变得现实,其工艺的广泛运用至今尚无其它形式所能相比。
在流化床包衣设备分布板中央设置雾化器,即底喷流化床(也称Wurster系统),其中带扩展室的物料床中心设置圆形导向筒,分布板在导向筒区域内具有较大的开孔率,以满足大部分风量通过,形成类喷泉式的流态化,粉粒从导向筒之间的环隙区域,如此的循环。
使物料具有高度的分散性,因而底喷包衣工艺具有人们所期望的工艺重复性。
3.从微丸(粒)包衣工艺要求角度看“负压底喷规则流”流化床包衣的要点
3.1 微丸(粒)包衣工艺与规模生产要求
微丸(粒)包衣应适用于:≥50μm的粉末包衣、粒、丸(≤6mm)掩味、着色、热熔、防潮、抗氧化包衣、粒丸肠溶衣、环释包衣、悬浮液、溶液涂层放大等。
微丸(粒)包衣的要求:
(1)、物料能高度分散并伴随衣膜的喷涂而不产生粘连;
(2)、雾粒到达物料的距离应很短,湿分而不致于快速蒸发掉,与物料产生良好的附着,并具有极强的铺展性,使得衣膜牢固、连续;
(3)、物料与雾粒接触机会应均等,包衣均匀;
(4)、耗用包衣材料较少,且衣膜均匀。
微丸(粒)包衣规模生产时要求:高效、可靠、环保、安全等。
3.2 从微丸(粒)包衣工艺要求看“负压底喷”流化床包衣的要点
要达到上述包衣工艺与规模生产要求时,光有底喷流化床包衣技术是不能完美的,基于制药工业的特殊性,其生产设备力求高效性、可靠性、环保性、安全性和批量化,这就要把负压、底喷和规则流技术整合于一体。
负压技术是整机的关键之首,其负压的创新性是以系统优化设置,使包衣的整个工艺过程处于密封与负压状态,从而达到以下效果:
(1)系统负压工艺流程可有效地避免包衣材料中有机溶媒在气化时的气体外溢,消除易燃易爆事故隐患,减少环境污染;
(2)有利于突发性事故的泄爆,当系统内由于颗粒挤压摩擦、粉尘积累及有机溶媒气化膨胀所产生的压力升高至0.05Mpa时,泄爆装置即会自动打开,并会自动关闭电源,防止事故的发生;
(3)有利于流态化气流量的调节,保持物料流态化的稳定。
规则流型的流态化,喷泉式流态化能使设备中物料具有重现性良好的运行轨迹,这一点是严格包衣操作所不可缺少的,其目的是让物料与雾粒接触机会均等,包衣才会均匀。
同时,物料本身形成自转,其表面任一角度与雾粒接触机会均等。
因而,对于缓释、控释而言,底喷工艺形成的衣膜连续均匀。
生产设计了导向筒装置解决了这一难点。
这种特殊装置能使大部分气流量由中心区域的导向筒内通过,物料呈喷泉状的气流输送(亦称气流输送流化床),而导向筒外侧与塔体壁之间形成的流化床称为标准流化床。
此时,大部分气流量由导向筒下方的分风板进入,在流化床中央形成一粉粒物料柱,当其上升并离开导向筒时,由于风速急剧下降,颗粒将跌落在导向筒与床体间的流化区,再次向导向筒汇集上扬,如此反复循环,形成流化-气流输送-沉降-流化的过程,从而实现了规则流态化。
在结构上,一是导向筒高度可调,随着物料粒径变大,其高度会有所改变;二是流化分布板是随物料性质变化的,其开孔率及其分布采取更换方式调节;三是导向筒高度的合适设计,根据“死床”高度设计太高,碰撞加剧,会产生“衣层”脱落,高度设置太低会影响物料由流化区飞向包衣区迁移,从而引起产生包衣不均。
底喷的雾化不是随意就能达到有效雾化要求的,气流分布板要能使大部分气流量在分布板中心区域通过,分布板的中心区域位于导向筒的正下方,分布板的开孔率达70%以上,从而实现物料以气流输送状态上升,为喷泉流流态化创造必备的条件。
在导向筒与流化床壁环圆区域内,分布板的开孔率则为3%,使物料跌落在此区域内能形成标准的流化状态,有利于物料通过分布板与导向筒间的间隙向导向筒汇集。
这样起到每一滴雾粒能保持与颗粒附着前具有良好润湿性的作用,提高了附着率。
也由于雾化到达粉粒的距离短,不会被过早干燥,故颗粒在附着时其在物料表面具有良好的铺展性。
同时,能扩大衣膜面积,成膜厚薄均匀,润湿性又为衣膜附着牢固提供决定性的条件,最终达到包衣材料的目的。
4.结语
本文从流化床包衣技术概念着手,从三种流化床包衣的比较中看“底喷”流化床包衣的特点,也从微丸(粒)的包衣包衣工艺要求角度阐述“负压底喷规则流”流化床包衣的要点。
目前我公司产品产量从150g/批至200Kg/批。
应用于从粉体包衣至微丸的缓控释产品。
随着微丸制剂与缓控释包衣这一新型制药工艺的兴起,微丸制剂及缓控释包衣以掩味、着色、防潮、抗氧化、遮光、胃溶、隔热、肠溶、缓释及控释的特点决定了相应设备的市场。
文章链接:中国制药机械设备网/Tech_news/Detail/11004.html。