流化床技术及国内的应用
2023年流化床技术行业市场调研报告

2023年流化床技术行业市场调研报告流化床技术是一种应用广泛、广泛使用的化工工艺技术,其主要功能是对粉状物质进行粉碎、混合、干燥、反应等工艺操作。
该技术具有操作简单、设备投资低、生产效率高等优点,因此在其应用领域中得到了广泛的应用。
1. 流化床技术的应用领域(1)医药制造业在医药制造业中,流化床技术是一种应用广泛的干燥技术。
与传统的干燥方法相比,流化床干燥具有操作简单、更快速、干燥质量更佳的优点,因此得到了较为广泛的应用。
(2)化工工业在化工工业中,流化床技术主要通过反应床的方式实现反应过程。
该技术所需要的设备投资低、操作简单、反应效率高、实现精细化程度高,因此得到了广泛的应用。
(3)食品工业流化床技术在食品工业中主要应用于粉状食品材料的混合、干燥等工艺操作。
流化床技术实现了大规模、高效率的粉状食品生产,为食品工业提供了很大的支持。
2. 流化床技术的发展趋势(1)趋势一:智能化程度的提高随着人工智能技术的普及,流化床技术的智能化程度将会得到提高。
传感器技术、控制系统技术、数据分析技术等一系列技术的应用,将使得流化床设备操作更加便捷、智能、高效。
(2)趋势二:提高节能减排在环保政策方面,流化床技术需要不断提升的是其节能减排能力。
目前,国家环境保护政策不断升级,环保压力日益加大,流化床技术需要提高节能减排能力以应对环保的需要。
(3)趋势三:整合化和综合化随着全球化的蔓延和产业竞争的加剧,流化床技术需要变得更加整合化和综合化。
如何将流化床技术与其他相关技术(如传感器、数据分析等技术)进行整合,将是未来技术的一个重要发展趋势。
3. 流化床技术市场规模分析目前,流化床技术在医药制造、化工工业、食品工业等行业中的市场需求较大。
随着技术的不断发展和市场需求的不断增加,流化床技术市场规模也在不断扩大。
根据市场研究数据显示,2019年全球流化床技术市场规模已经超过100亿美元。
其中,医药制造、化工工业、食品工业是流化床技术需求最大的行业领域。
循环流化床锅炉技术的现状及发展前景

循环流化床锅炉技术的现状及发展前景循环流化床锅炉技术是一种利用高效循环流化床燃烧技术实现煤炭、石油焦等固体燃料的洁净、高效燃烧的技术。
其主要特点是燃料与气相、固相平衡流化,燃烧效率高、燃烧温度可控、污染物排放少。
1. 技术成熟:循环流化床锅炉技术已经经过多年的研究和发展,在我国已经建成的循环流化床锅炉装机容量已达数千兆瓦,形成了一定的产业化规模。
2. 功能完善:循环流化床锅炉技术的自动化程度逐渐提高,监控系统成熟,操作方便,运行稳定可靠。
循环流化床锅炉还具备灵活燃烧、硫捕集、脱硝、脱电除尘等多种功能。
3. 效果显著:循环流化床锅炉技术在煤炭、石油焦等固体燃料的燃烧效率上有明显改善,已实现了燃烧效率高于传统锅炉的目标。
循环流化床锅炉对污染物的排放也有明显改善,特别是对于二氧化硫和氮氧化物的排放效果显著。
4. 排放达标:循环流化床锅炉技术采用先进的脱硫、脱硝、脱电除尘等技术手段,可以有效控制燃烧过程中的污染物排放,达到甚至超过国家标准的排放要求。
1. 燃料多元化:循环流化床锅炉技术适应性强,可以适应各种固体燃料的燃烧,包括煤炭、石油焦、生物质等,未来可以实现更多种类燃料的利用,提高资源利用率。
2. 清洁化发展:循环流化床锅炉技术可以通过改进燃烧方式和燃烧设备,进一步降低污染物排放,实现更清洁的能源转换。
3. 高效节能:循环流化床锅炉技术具备灵活燃烧、高效热交换等优点,未来可以进一步提高能源的利用效率,减少能源消耗。
4. 大型化发展:循环流化床锅炉技术在我国已初步形成一定的规模,未来可以进一步发展为大型化设备,满足国家能源需求。
循环流化床锅炉技术在煤炭、石油焦等固体燃料的洁净、高效燃烧方面具有显著的优势,并且具备广阔的发展前景。
随着对环境保护要求的提高和能源利用效率的追求,循环流化床锅炉技术将在未来得到更广泛的应用和推广。
聚乙烯生产装置中流化床技术及应用分析
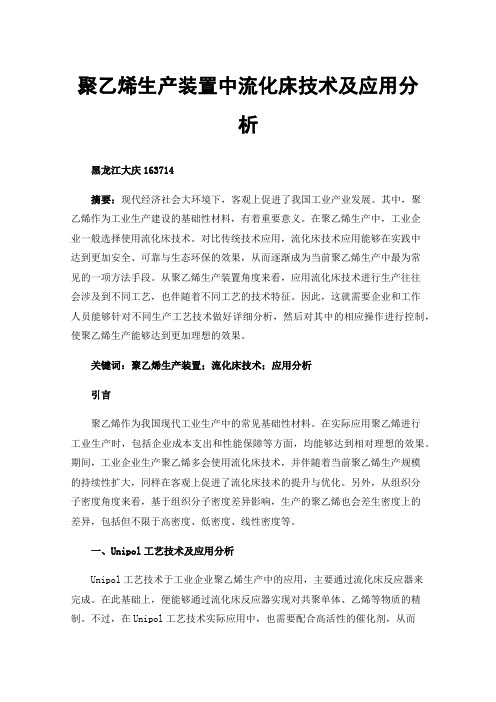
聚乙烯生产装置中流化床技术及应用分析黑龙江大庆163714摘要:现代经济社会大环境下,客观上促进了我国工业产业发展。
其中,聚乙烯作为工业生产建设的基础性材料,有着重要意义。
在聚乙烯生产中,工业企业一般选择使用流化床技术。
对比传统技术应用,流化床技术应用能够在实践中达到更加安全、可靠与生态环保的效果,从而逐渐成为当前聚乙烯生产中最为常见的一项方法手段。
从聚乙烯生产装置角度来看,应用流化床技术进行生产往往会涉及到不同工艺,也伴随着不同工艺的技术特征。
因此,这就需要企业和工作人员能够针对不同生产工艺技术做好详细分析,然后对其中的相应操作进行控制,使聚乙烯生产能够达到更加理想的效果。
关键词:聚乙烯生产装置;流化床技术;应用分析引言聚乙烯作为我国现代工业生产中的常见基础性材料。
在实际应用聚乙烯进行工业生产时,包括企业成本支出和性能保障等方面,均能够达到相对理想的效果。
期间,工业企业生产聚乙烯多会使用流化床技术,并伴随着当前聚乙烯生产规模的持续性扩大,同样在客观上促进了流化床技术的提升与优化。
另外,从组织分子密度角度来看,基于组织分子密度差异影响,生产的聚乙烯也会差生密度上的差异,包括但不限于高密度、低密度、线性密度等。
一、Unipol工艺技术及应用分析Unipol工艺技术于工业企业聚乙烯生产中的应用,主要通过流化床反应器来完成。
在此基础上,便能够通过流化床反应器实现对共聚单体、乙烯等物质的精制。
不过,在Unipol工艺技术实际应用中,也需要配合高活性的催化剂,从而构建起更适合的反应环境。
近些年来,伴随着我国工业领域的不断发展完善,有关聚乙烯的生产工艺技术也在不断创新完善,并同时也提升了催化剂的效益。
如此一来,即便是在相同反应器中,同样能够实现多种不同牌号,不同密度聚乙烯产生的生产。
从Unipol工艺技术应用流程来看,工作人员需先行运行聚乙烯装置,然后准备好聚乙烯粉料,之后将聚乙烯粉料统一投放至反应器内,在循环气压机的作用下,实现种子床的硫化。
流化床干燥工艺

流化床干燥工艺是一种常用的干燥技术,它通过使物料在流动状态下进行干燥,以达到均匀干燥和高效传热的目的。
下面将详细介绍流化床干燥工艺的原理、优点、缺点、操作过程、影响因素以及应用领域。
一、原理流化床干燥的基本原理是热传导和蒸发。
通过加热床层中的物料,使其温度升高,从而加速水分蒸发和热量传导。
同时,物料在流化状态下,不断与床层和热源进行接触,使其均匀分布和传递,达到高效干燥的目的。
二、优点1. 均匀干燥:流化床干燥过程中,物料在流化床中均匀分布,避免了局部过热或干燥不均匀的现象,提高了干燥效率和质量。
2. 适用范围广:流化床干燥适用于多种物料,如颗粒状、纤维状和膏状物料。
同时,流化床可以适应不同的工艺要求,如单方向流动、双向流动、气固分离等。
3. 环保节能:流化床干燥过程中,热量和物料之间的传热效率较高,能耗较低。
同时,流化床产生的废气较少,易于处理,符合环保要求。
三、缺点1. 设备投资较大:流化床干燥设备通常比较复杂,结构紧凑,因此设备投资较大。
2. 操作难度较高:流化床干燥操作过程中,需要控制流速、温度、湿度等因素,操作难度较高。
3. 物料破碎:对于一些易碎的物料,流化床干燥过程中可能会发生破碎现象。
四、操作过程1. 准备阶段:将物料加入流化床干燥机中,调整流化风速和物料流速到合适的值。
2. 启动阶段:逐渐提高温度和风量,观察物料状态和水分变化。
3. 稳定运行阶段:当物料达到稳定状态时,调整风量和温度以控制水分蒸发速率。
4. 结束阶段:当物料达到预定含水量时,逐渐降低风量和温度,直至完全停止设备。
五、影响因素1. 物料特性:物料的粒度、形状、表面性质等都会影响干燥速率和效果。
2. 操作参数:温度、风速、湿度、物料停留时间等都会影响干燥效果。
3. 环境因素:电源供应、设备维护、操作人员技能等也会影响干燥过程。
六、应用领域流化床干燥工艺广泛应用于化工、制药、食品、农产品加工等领域。
例如,在化工行业中,流化床干燥可用于干燥各种化学原料和产品;在制药行业中,流化床干燥可用于干燥药物原料和辅料;在食品行业中,流化床干燥可用于干燥糖果、巧克力、谷物等食品;在农产品加工领域,流化床干燥可用于干燥果蔬、种子等农产品。
循环流化床锅炉技术的现状及发展前景

循环流化床锅炉技术的现状及发展前景循环流化床锅炉技术是一种先进的锅炉燃烧技术,具有节能、环保、高效、安全等特点,被广泛应用于发电、热水供应等领域。
本文将介绍循环流化床锅炉技术的现状以及未来发展前景。
1、技术特点循环流化床锅炉技术以煤炭、煤屑、废热、废料等非化石能源为主要燃料,通过高速风流使燃料在炉内均匀分布,从而使燃料的燃烧充分、热效率高。
该技术具有以下特点:(1)熄火、剧烈爆炸等现象很少发生,能够保证燃料的可靠燃烧,从而减少污染排放。
(2)燃料颗粒大小范围较广,可处理不同种类的燃料。
(3)含硫、含氯等有害成分的排放量明显降低,可以达到环保排放标准。
(4)炉内温度均匀,使用寿命长,可靠性高。
(5)锅炉采用循环式加料,自动控制,操作简便。
(6)应用范围广泛,可以用于发电、热水供应、工业锅炉、化工等领域。
2、技术应用循环流化床锅炉技术已经被广泛应用于国内外的发电和热水供应等领域。
在中国,国内已有一些大型发电厂采用循环流化床锅炉技术。
例如,湖南金山电厂、山西黄陵发电厂以及华能大兴发电厂等发电厂都采用了循环流化床锅炉技术。
3、技术进展随着技术的不断进步,循环流化床锅炉技术也在不断完善。
近年来,循环流化床锅炉技术的主要进展包括以下方面:(1)热效率提高:目前循环流化床锅炉技术的热效率已经达到了 85%以上,在很大程度上节约了能源。
(2)技术可靠性提高:现代循环流化床锅炉技术采用先进的控制系统,可以实现全自动化控制,使得技术可靠性大大提高。
(3)减少污染排放:近年来,循环流化床锅炉技术在减少污染排放方面也取得了重大进展。
例如,采用低氮燃烧技术和脱硝技术等措施可以大幅减少氮氧化物的排放量。
循环流化床锅炉技术应用范围十分广泛,可以应用于电力、冶金、化工、建材、纺织、食品等多个行业。
随着技术的不断发展,循环流化床锅炉技术将会在更多行业中得到应用。
2、技术创新推动行业进步循环流化床锅炉技术的不断创新和发展将推动整个燃热行业的进步。
循环流化床技术在能源领域应用的研究

循环流化床技术在能源领域应用的研究近年来,随着环保意识的提高和节能减排的要求,循环流化床技术在能源领域中得到了广泛应用。
循环流化床技术是一种通过高速气流将固体颗粒悬浮在气流中使之高度混合和物理化学变化的技术。
在能源领域中,循环流化床技术主要应用在以下几个方面。
一、煤炭气化煤炭气化是将煤炭等燃料在高温高压下加氢,通过化学反应将其转化为合成气的一种技术。
循环流化床技术在煤炭气化中具有快速气固两相混合、高效传热传质、自动控制等优点,能够有效提高反应效率和气化产物质量,降低气化成本。
目前,循环流化床煤气化技术已经成为我国煤气化产业发展的主流技术之一,应用于煤制氢、合成气、一次甲醇、合成二甲醚、合成石墨烯等领域。
同时,也可以利用煤气作为发电、燃气锅炉和燃气轮机的燃料,实现高效清洁的能源利用。
二、制备微米颗粒材料微米颗粒材料具有广泛的应用前景,如触媒、光学材料、磁性材料、生物医学材料等。
利用循环流化床技术可以制备出高品质、高纯度、高活性的微米颗粒材料。
根据不同的要求,可以采用不同的循环流化床反应器,如气固鼓泡床、气固旋转反应器、气固超声波反应器等。
通过控制反应条件,可以获得不同形态、大小和分布的微米颗粒,从而满足不同领域的需求。
三、焦化废气处理焦化是一种将煤炭加热至高温,使其中的可燃物质分解的工艺。
焦化的过程中会产生大量的废气,其中含有大量的有毒有害物质,对环境和人健康造成极大威胁。
循环流化床技术可以处理焦化废气中的有机物、硫氧化物和氮氧化物等有害物质,将其转化为无害的氮、二氧化碳和水等物质。
在焦化废气处理中,循环流化床技术具有高效率、低能耗、适应性好等优点。
目前,已经有多家企业应用此技术进行焦化废气处理,取得了良好的经济和环保效益。
总之,循环流化床技术在能源领域中有着广泛的应用前景。
技术的不断完善和创新,将有助于提高能源利用效率、保护环境和促进可持续发展。
循环流化床锅炉技术的现状及发展前景

循环流化床锅炉技术的现状及发展前景1. 引言1.1 循环流化床锅炉技术简介循环流化床锅炉技术是一种先进的燃烧技术,属于流化床锅炉的一种。
它利用气体与固体颗粒之间的强烈对流使固体颗粒床具有流态化特性,从而实现了燃料的高效燃烧和热能的高效传递。
循环流化床锅炉技术将燃烧过程和热能转换过程完全结合在一起,具有高效、清洁、灵活、稳定的特点。
循环流化床锅炉技术通过循环往复的方法,将固体颗粒不断循环送回炉膛内,实现了固体颗粒的再生利用,充分提高了燃料利用率。
循环流化床锅炉技术还具有一定的自脱硫、自脱硝功能,可以有效减少燃煤过程中排放的氧化物和二氧化硫等有害物质,保护环境。
循环流化床锅炉技术的出现为能源领域带来了新的发展机遇,得到了广泛的应用和推广。
随着科技的不断进步和对环保要求的提高,循环流化床锅炉技术将在未来的能源转型中发挥越来越重要的作用。
1.2 循环流化床锅炉技术的重要性循环流化床锅炉技术可以有效节约能源资源。
这种技术能够提高燃料的利用率,减少能源的浪费,从而降低能源成本并减少对能源的依赖。
循环流化床锅炉技术可以降低污染排放。
与传统的燃煤锅炉相比,循环流化床锅炉利用气固分离技术,减少了废气中的灰尘和有害物质排放,对环境的影响更小。
循环流化床锅炉技术具有较高的安全性和稳定性。
通过控制燃烧过程中的温度、压力等参数,可以有效避免锅炉爆炸等安全事故的发生,保障设备和人员的安全。
循环流化床锅炉技术在能源利用、环境保护和安全生产等方面都具有重要意义。
在未来的发展中,这种技术有望成为能源领域的重要方向,为推动能源转型和可持续发展做出积极贡献。
2. 正文2.1 循环流化床锅炉技术的工作原理循环流化床锅炉技术是一种高效、节能、环保的锅炉技术,其工作原理主要包括以下几个步骤:燃料在锅炉内燃烧产生热能,然后通过燃烧产生的高温气体将热能传递给循环流化床床层内的流化质料,使其快速升温。
接着,流化质料受到热量影响而变得流动起来,形成一层类似沸腾水的状态,称为流化床。
2024年流化床技术市场规模分析
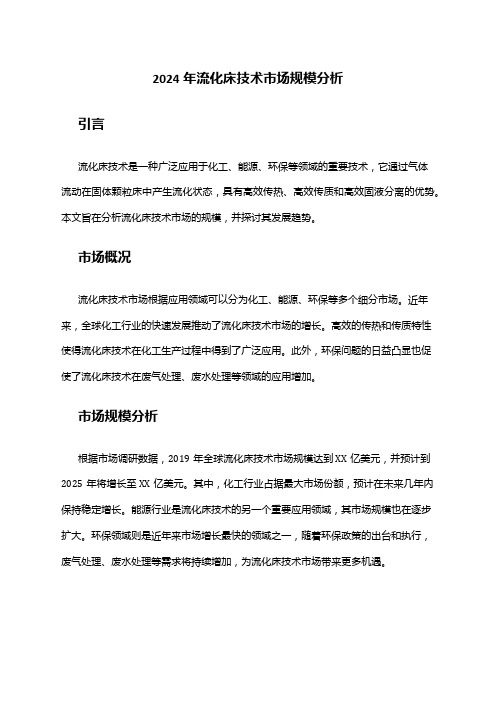
2024年流化床技术市场规模分析引言流化床技术是一种广泛应用于化工、能源、环保等领域的重要技术,它通过气体流动在固体颗粒床中产生流化状态,具有高效传热、高效传质和高效固液分离的优势。
本文旨在分析流化床技术市场的规模,并探讨其发展趋势。
市场概况流化床技术市场根据应用领域可以分为化工、能源、环保等多个细分市场。
近年来,全球化工行业的快速发展推动了流化床技术市场的增长。
高效的传热和传质特性使得流化床技术在化工生产过程中得到了广泛应用。
此外,环保问题的日益凸显也促使了流化床技术在废气处理、废水处理等领域的应用增加。
市场规模分析根据市场调研数据,2019年全球流化床技术市场规模达到XX亿美元,并预计到2025年将增长至XX亿美元。
其中,化工行业占据最大市场份额,预计在未来几年内保持稳定增长。
能源行业是流化床技术的另一个重要应用领域,其市场规模也在逐步扩大。
环保领域则是近年来市场增长最快的领域之一,随着环保政策的出台和执行,废气处理、废水处理等需求将持续增加,为流化床技术市场带来更多机遇。
市场驱动因素1.化工行业发展:全球化工行业的快速发展推动了流化床技术市场的增长,化工生产过程中需求高效的传热和传质特性。
2.环境法规:环保问题的日益凸显促使了流化床技术在废气处理、废水处理等领域的应用增加,市场需求不断增长。
3.能源需求:能源行业对于高效能源转化和清洁能源的需求推动了流化床技术市场的发展,其在燃煤电厂、生物质能源等领域具有广阔应用前景。
市场挑战1.技术壁垒:流化床技术作为一项复杂的工艺,需要具备丰富的技术经验和高水平的工程能力,技术门槛较高。
2.市场竞争:流化床技术市场存在较多的竞争对手,技术更新迭代较快,企业需持续创新才能保持竞争力。
3.成本压力:流化床技术的投资和运营成本较高,对企业的财务实力和运营效率提出了要求。
发展趋势1.清洁能源:清洁能源的发展将进一步推动流化床技术在能源领域的应用,尤其是生物质能源和燃煤电厂领域。
循环流化床锅炉技术的现状及发展前景

循环流化床锅炉技术的现状及发展前景循环流化床锅炉是一种先进的燃烧技术,通过将燃烧材料与一定量的酸性氧化剂(如石灰石或石膏)一起注入锅炉中,形成循环流化床,在高温下进行燃烧过程。
这种技术具有高效、清洁、灵活等特点,广泛应用于电力、热力、化工等行业。
循环流化床锅炉技术在我国的发展非常迅速。
自20世纪80年代初引进以来,经过不断改进和技术升级,我国的循环流化床锅炉技术已经取得了很大的进展。
目前,我国在循环流化床锅炉技术领域已经具备了一定的自主研发能力,并且形成了一批具有自主知识产权的核心技术和装备。
我国的循环流化床锅炉技术已经能够满足各个领域对于高效、清洁能源的需求。
循环流化床锅炉技术的发展前景非常广阔。
循环流化床锅炉技术是一种清洁燃烧技术,采用这种技术可以有效减少燃烧产生的大气污染物排放,符合环保要求。
循环流化床锅炉技术具有高燃烧效率和灵活性,适用于各种不同的燃料,包括煤炭、生物质能源和废弃物等,可以实现能源多元化。
循环流化床锅炉技术还可以实现废弃物资源化利用,降低了废弃物处理成本,具有较大的经济效益。
随着我国不断加强对可再生能源的开发和利用,循环流化床锅炉技术在生物质能源领域的应用前景也非常广阔。
循环流化床锅炉技术在能源领域的广泛应用,也为我国实现能源清洁化、高效化和可持续发展提供了重要支持。
虽然循环流化床锅炉技术发展迅猛,但仍面临一些挑战。
技术成本较高,需要进一步降低设备的制造和运行成本。
循环流化床锅炉技术在高温、高压、高腐蚀等条件下工作,对材料和设备的要求较高,需要进一步提高技术水平。
循环流化床锅炉技术在大规模应用时还面临一些技术和管理问题,需要加强技术创新和管理能力。
循环流化床锅炉技术在我国的发展前景非常广阔。
随着我国能源需求的增长和环境保护的要求,循环流化床锅炉技术将逐渐替代传统的燃煤锅炉技术,成为未来能源领域的主力军。
随着技术的不断创新和完善,循环流化床锅炉技术将继续为我国实现能源清洁化、高效化和可持续发展做出重要贡献。
2024年流化床技术市场前景分析
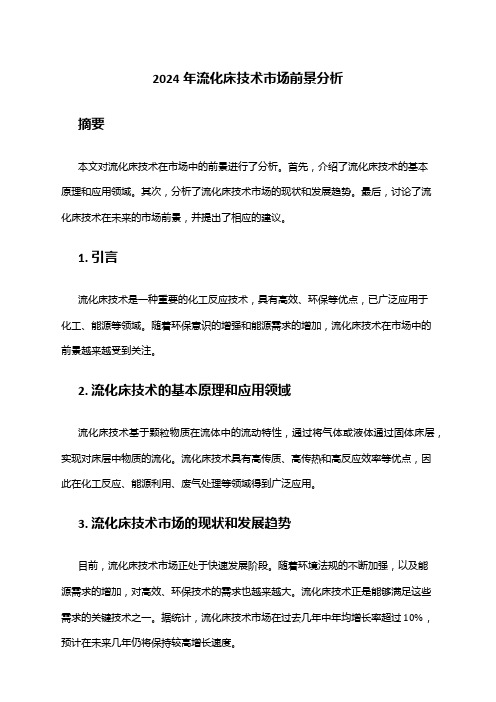
2024年流化床技术市场前景分析摘要本文对流化床技术在市场中的前景进行了分析。
首先,介绍了流化床技术的基本原理和应用领域。
其次,分析了流化床技术市场的现状和发展趋势。
最后,讨论了流化床技术在未来的市场前景,并提出了相应的建议。
1. 引言流化床技术是一种重要的化工反应技术,具有高效、环保等优点,已广泛应用于化工、能源等领域。
随着环保意识的增强和能源需求的增加,流化床技术在市场中的前景越来越受到关注。
2. 流化床技术的基本原理和应用领域流化床技术基于颗粒物质在流体中的流动特性,通过将气体或液体通过固体床层,实现对床层中物质的流化。
流化床技术具有高传质、高传热和高反应效率等优点,因此在化工反应、能源利用、废气处理等领域得到广泛应用。
3. 流化床技术市场的现状和发展趋势目前,流化床技术市场正处于快速发展阶段。
随着环境法规的不断加强,以及能源需求的增加,对高效、环保技术的需求也越来越大。
流化床技术正是能够满足这些需求的关键技术之一。
据统计,流化床技术市场在过去几年中年均增长率超过10%,预计在未来几年仍将保持较高增长速度。
不仅如此,随着科技的不断进步和创新,流化床技术也在不断完善和改进。
新型材料的应用、先进的控制技术的引入以及模型仿真等工具的发展,将进一步提高流化床技术的效率和经济性。
这些技术进步将为流化床技术在更广泛的应用领域中打开新的市场机会。
4. 流化床技术在未来的市场前景从目前的市场发展趋势来看,流化床技术在未来具有广阔的市场前景。
首先,随着环保法规对工业污染要求的提高,对废气处理和固体废物处理技术的需求不断增加,而流化床技术正是一种有效的处理技术,能够高效降解有害物质。
其次,能源是人类社会发展的基石,随着能源需求的增加和传统能源资源的日益枯竭,人们对新能源的需求也越来越大。
流化床技术在生物质燃烧、煤气化等领域的应用,将为新能源的开发和利用提供可靠的技术支撑。
最后,流化床技术在化工领域的应用前景也非常广阔。
流化床气化技术在我国的应用现状及发展前景

Ab s t r a c t : F r o m t h e i f r s t i n d u s t r i a l l f u i d i z e d b e d h a s b e e n p u t i n t o o p e r a t i o n i n 1 9 5 4 , t h e c i r c u l a t i n g l f u i d i z e d b e d h a d a w i d e r a n g e o f a p p l i c a t i o n s a n d r a p i d d e v e l o p me n t . I n r e c e n t y e a s, r t h e u s e o f a c i r c u l a t i n g lu f i d i z e d b e d
g a s i i f e s t e c h n o l o g y h a s b e e n d e v e l o p i n g r a p i d l y , t h e c o mb u s t i o n e f f i c i e n c y , c a r b o n c o n v e si r o n r a t e h a s b e e n s i g n i f i — c a n d y i mp r o v e d .R e v i e w s e v e r a l l f u i d i z e d b e d g a s i i f c a t i o n t e c h n o l o g i e s , a n a l y z e s i t s c h ra a c t e r i s t i c s a n d t h e o p e r a , t i o n o f t h e c o n d i t i o n s , e t c . F i n a l l y , t h e a i r f l o w b e d l a t e r d e v e l o p me n t p u t s f o r wa r d r e l a t e d S u g g e s t i o n s . Ke y wo r d s : g a s i i f c a t i o n t e c h n o l o g y; a i r - b e d g a s i i f c a t i o n; i n d u s t r y
生物质流化床气化技术应用研究现状

生物质流化床气化技术应用研究现状随着能源危机的不断加剧和环保意识的增强,生物质成为可再生能源的重要来源之一。
而生物质流化床气化技术作为一种高效利用生物质的能源转化技术,在国内外得到了广泛的应用和研究。
本文就生物质流化床气化技术的应用研究现状进行探讨。
一、生物质流化床气化技术概述生物质流化床气化技术是利用流化床反应器对生物质进行气化反应,使其转化为气体燃料的一种技术。
在流化床内,生物质颗粒被高速气流悬浮并与气体直接接触,因此可以在较低的反应温度下实现生物质的完全气化。
同时,流化床内部的湍流和固体与气体之间的热和质量传递可以进一步提高反应效率。
生物质流化床气化技术具有以下优点:1、资源丰富、可持续。
生物质是可再生资源,来源广泛,包括木材、农作物秸秆、林木剩余物、木薯渣等等。
2、环保效益好。
与传统能源相比,生物质气化产生的二氧化碳排放量低,可以减少对环境的污染。
3、经济效益明显。
生物质气化技术可以实现生物质的高效利用,产生的气体燃料可以替代传统的能源,对于推动节能减排、环境友好的经济模式具有积极的意义。
二、生物质流化床气化技术的应用研究现状1、研究进展在国内外,生物质流化床气化技术得到了广泛应用和研究。
研究人员通过实验室试验和大规模试验,对生物质气化反应的反应温度、反应压力、流化床粒径、生物质种类等参数展开了研究。
在反应温度方面,过高或过低的温度都会导致反应效率的降低。
研究表明,适宜的反应温度一般在800℃-900℃之间。
在生物质种类方面,各种不同的生物质具有不同的物理和化学性质,因此生物质流化床气化反应的效率受到生物质种类的影响。
研究表明,木材和秸秆等较为常见的生物质可以被有效气化。
2、应用场景生物质流化床气化技术在电力、燃气、化工等多个行业中得到了应用。
其中,电力是生物质流化床气化技术的主要应用领域。
在电力领域,生物质流化床气化技术已经得到了广泛的应用。
利用生物质气化产生的气体燃料发电可以替代传统的化石燃料发电,具有环保节能的优势。
中药流化床制粒技术的应用与发展
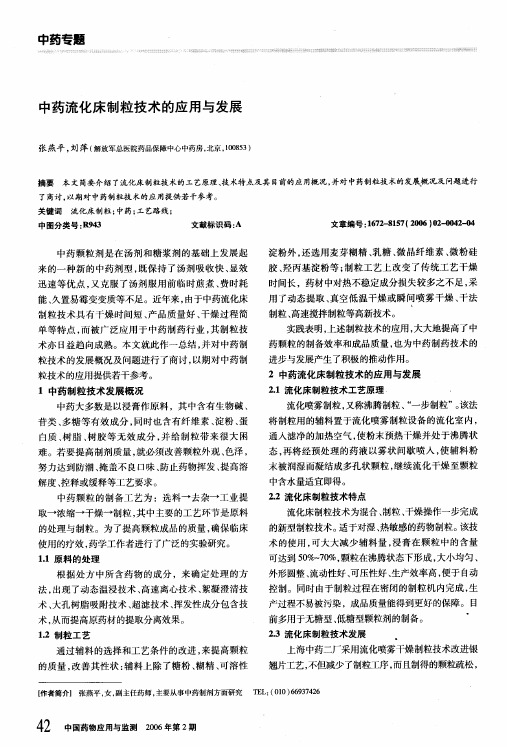
锅内 滚动吹干, 并用W号树脂PEG 乙 醇溶液进行包
衣, 可很好解决颗粒的吸湿问题U sl0
4 讨论 上述介绍为目 前常见的中药流化床制粒工艺的应
的浓缩浸膏喷雾, 使其在母核上附聚、 干燥成粒。可用 于作母核的辅料常选用 120 目 蔗糖粉、 一 p 环糊精、 磷
酸氢钙粉 、 滑石粉 、 微球硅胶 、 甘露醇、 、 一 乳糖 a 淀粉
而粗, 但CRH值低, 不利于长期保存, 需要好的 包装材
料160 11 对于无糖型颗粒的包装材料需特别强调, 一般的
分, 提高了成品的稳定性, 效果良 好。在花针感冒颗粒 剂的离心浓缩液中加人 巧 %的白糊精, 80℃ 在 将其溶 解, PGL- l0A 型喷雾干燥机即可消除粘壁现象, 用 得
到合格的干燥颗粒。 尽量降低干浸膏粉的粘滞性和引湿性, 严格控制
粘合剂雾化液滴过大, 或喷雾频率过高等;工艺设计
不合理}习 , 。
3.1.2 防止 “ 塌床” 的方法
对于不同的处方、 不同的中 药成分, 在操作中 可以 根 实际情况, 采取措施来预防和解决 “ 塌床” 现
象。
中 药 应 与 测 :0 6年 2期 43 国物 用 监 0 第
中药专题
我们将吸附澄清— 高速离心沉降这两种提取分 离技术结合起来, 用于颗粒剂的煮提制备工艺中, 该
【 作者简介] 张燕平, 副主任药师, 女, 主要从事中药制剂 面研究
上海中 药二厂采用流化喷雾干燥制粒技术改进银 翘片 工艺, 不但减少了 制粒工序, 而且制得的 颗粒疏松,
TEL: ( 010 )66937426
42 中 药 应 与 测 2 0 年 2期 国 物 用 监 0 “第
中药专题
呈多孔状, 压片后硬度高, 崩解快, 提高了片剂质量 0 加人适量的甜蜜素和糊精作为辅料, 运用喷雾干 燥法制备,制得脑心康无糖颗粒剂,经 TLC 定性 、
流化床技术在食品工业中的运用

流化床技术在食品工业中的运用前言流态化技术适用于大规模生产的高效气固、液固或气液固三相操作过程,广泛应用于化工、能源、材料、生化、环保、食品和制药等领域[1]。
在实际应用中传统流化床也存在着一些亟待解决的问题:气泡现象使流化不均匀,相间接触效率不高且工程放大较困难;一般只能处理松散的粉状和粒状物料,对于初始湿含量大的物料,须经过预干燥之后才能用普通流化床干燥器进行干燥;动力消耗大等[2]。
1食品干燥的发展及制约条件随着环境的变化经济的发展科技的提高以及人们认识的深化,以绿色、方便、保健为特征的新食品工业得到了迅速发展,人们对食品的需求呈现出以下趋势:(1)副食比重继续加大,且趋向更多样;(2)盛行保健食品,强化铁钙锌碘等,或低盐低糖;(3)无污染的绿色食品越来越多的受到人们的重视;(4)侧重感官品质的方便食品成为新宠,要求口感轻柔味道天然浓郁清淡鲜香等。
目前市场所售食品除一小部分为新鲜食品外,大部分都是保鲜食品,食品的冷藏处理量日趋增长,使分销系统复杂易污染,从而使干燥食品具有广阔的前景。
干燥食品,利用干燥技术加工而成的食品,不需冷藏,更易保存且长时间保鲜,并且有重量轻、食用方便等优点[3]。
由于食品物料的特殊性,其干燥方法和干燥条件也与普通物料干燥不同。
对于食品物料来说,在干燥过程中不仅需要除去水分,更重要的是在除去水分时能够保证食品的营养元素不被破坏,或者是尽可能少的破坏,同时在食品加工中还需要考虑到加工之后的色泽、口感等一系列的技术指标。
普通的流化床难以满足以上严格的技术指标要求,为了解决这些问题出现了各种流化床。
2 流化床在食品加工中的研究与应用2.1 脉动流化床干燥脉动干燥是指按一定的规律交替变化干燥工艺参数的干燥技术;脉动流化床干燥则是改变传统流化床的恒定送风为周期性送风,通过调节气流的脉动频率或脉动气流导通率,使通过孔板的气体流量或流化区发生周期性变化,对物料进行干燥。
脉动流化床用于不易流化的物料和有特殊要求的物料。
循环流化床锅炉技术的现状及发展前景
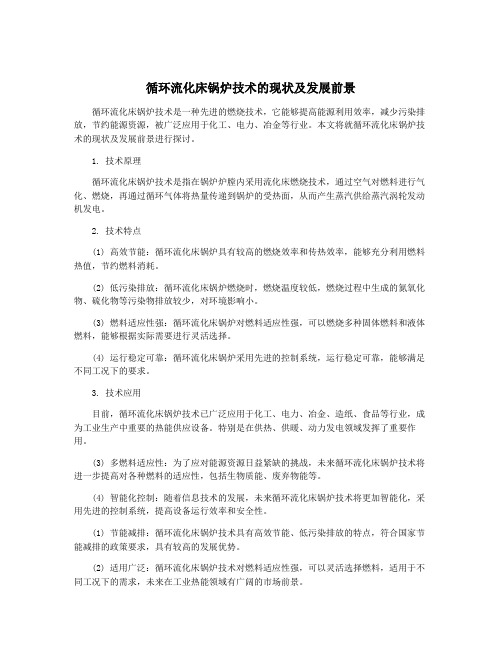
循环流化床锅炉技术的现状及发展前景循环流化床锅炉技术是一种先进的燃烧技术,它能够提高能源利用效率,减少污染排放,节约能源资源,被广泛应用于化工、电力、冶金等行业。
本文将就循环流化床锅炉技术的现状及发展前景进行探讨。
1. 技术原理循环流化床锅炉技术是指在锅炉炉膛内采用流化床燃烧技术,通过空气对燃料进行气化、燃烧,再通过循环气体将热量传递到锅炉的受热面,从而产生蒸汽供给蒸汽涡轮发动机发电。
2. 技术特点(1) 高效节能:循环流化床锅炉具有较高的燃烧效率和传热效率,能够充分利用燃料热值,节约燃料消耗。
(2) 低污染排放:循环流化床锅炉燃烧时,燃烧温度较低,燃烧过程中生成的氮氧化物、硫化物等污染物排放较少,对环境影响小。
(3) 燃料适应性强:循环流化床锅炉对燃料适应性强,可以燃烧多种固体燃料和液体燃料,能够根据实际需要进行灵活选择。
(4) 运行稳定可靠:循环流化床锅炉采用先进的控制系统,运行稳定可靠,能够满足不同工况下的要求。
3. 技术应用目前,循环流化床锅炉技术已广泛应用于化工、电力、冶金、造纸、食品等行业,成为工业生产中重要的热能供应设备。
特别是在供热、供暖、动力发电领域发挥了重要作用。
(3) 多燃料适应性:为了应对能源资源日益紧缺的挑战,未来循环流化床锅炉技术将进一步提高对各种燃料的适应性,包括生物质能、废弃物能等。
(4) 智能化控制:随着信息技术的发展,未来循环流化床锅炉技术将更加智能化,采用先进的控制系统,提高设备运行效率和安全性。
(1) 节能减排:循环流化床锅炉技术具有高效节能、低污染排放的特点,符合国家节能减排的政策要求,具有较高的发展优势。
(2) 适用广泛:循环流化床锅炉技术对燃料适应性强,可以灵活选择燃料,适用于不同工况下的需求,未来在工业热能领域有广阔的市场前景。
(3) 环保理念:随着社会环保意识的提高,循环流化床锅炉技术将受到更多政府和企业的支持,有望成为未来工业热能设备的主流选择。
2024年流化床技术市场分析现状

2024年流化床技术市场分析现状1. 引言流化床技术是一种重要的化工工艺,在化工、能源等领域具有广泛的应用。
本文将对流化床技术市场进行分析,包括市场规模、市场发展趋势、竞争格局等方面。
2. 市场规模目前,全球流化床技术市场规模不断扩大。
根据统计数据显示,2019年全球流化床技术市场规模达到了XX亿美元,并且预计在未来几年内将保持平稳增长。
这主要得益于流化床技术在环保、能源等领域的广泛应用。
3. 市场发展趋势3.1 清洁能源需求随着全球对清洁能源的需求不断增加,流化床技术在煤炭、石油等传统能源领域的应用逐渐增多。
流化床技术能够有效提高能源利用效率,减少污染物排放,使其成为人们重要的选择。
3.2 工艺改进与创新随着技术的不断发展,流化床技术在工艺改进方面取得了重要突破。
通过改良反应器结构、优化流体化剂及催化剂等,使流化床技术更加高效、稳定和环保,满足了不同行业对工艺的需求。
3.3 产业升级推动市场增长许多国家积极推动产业升级,加大对新技术的研发和应用。
流化床技术作为一种前沿技术,得到了广泛关注和支持。
政府在政策、资金等方面给予支持,促使流化床技术市场持续发展。
4. 竞争格局目前,全球流化床技术市场竞争激烈,主要厂商包括A公司、B公司、C公司等。
这些厂商在技术研发、产品质量和市场推广方面进行积极竞争。
各家厂商都在不断提高产品性能和技术含量,以满足市场的需求。
此外,亚洲地区在流化床技术市场中具有一定的竞争优势。
中国、印度等国家在流化床技术领域拥有丰富的资源和技术经验,成为全球市场的重要参与者。
5. 市场前景未来几年,预计全球流化床技术市场将继续保持稳定增长。
市场需求的不断增加、技术的不断创新以及政策的支持都将促进市场的发展。
此外,新兴市场的开发和产业升级将为流化床技术提供更多的机遇和挑战。
6. 结论流化床技术市场在全球范围内呈现出良好的发展态势。
随着清洁能源需求的增加、工艺改进与创新的推动,以及产业升级的推动,流化床技术市场将继续保持稳定增长。
内热流化床干燥技术的发展现状及应用前景

缩
述
ቤተ መጻሕፍቲ ባይዱ
Ch i n a Ch e mi c a l Tr a d e
。
磊 月
内热 流化 床 干燥 技 术 的发展 现 状 及应 用 前景
任 伟 何燕彬 z 董贺群 s
0 5 0 0 31 ) ( 石 家 庄 工 大 化 工 设 备 有 限 公 司 。河 北 石 家 庄
关 键 词 :流 化 床
流化 床干 燥技 术是 流态 化技 术和 传热 传质 技术 的成 功结 合 ,现代 流化 床干燥 技 术领 域 中 ,振 动 流化床 干燥 技术 、旋 转 闪蒸 流化床 干燥 技 术 、沸 腾流 化床 干燥 技术 等 已成 功广泛 应 用于各 化工 行 业 。但 流化 床 干燥技 术在 某些 领域 的不 足 也 1 3 显突 出 ,如 针对 热敏 性 物料 或密 度 较小 物料 干燥 时 , 由于 风温 低 ,空塔 风速 小 ,风 量和床 面积 都要 大 幅 提 高 ,导致 流化床 干燥装 置庞大 ,除尘 系统负荷 加重 ,装机 容量 加大 。 当最 终产 品含 水 率接近 或低 于 平衡含 水 率时 ,流化 床干 燥 的排 气温 度
摘
要 : 内热流化床 干燥技 术是 继单室流化床 、沸腾 流化床 干燥技 术基础研发 出来的一种新型 节能 型干燥技 术。在 分析我 国流化床干燥技 术现
内热 流化 床 换 热 器
状 的基 础 上 ,指 出 内热 流化 床 干燥 技 术 的 发 展 方 向 ,并提 出 内热 流 化 床 干 燥技 术 研发 应 用 重 点研 究借 决的 几 个 技 术 关 键 。
比例较 小 ,而换 热器 对床 层 的传 热对 干燥器 的 工作 指标 高低 起 到至 关 重要 的作用 ,是 内热 流化 床干 燥 面研 究和 设计 的重 点 。 内热 流化 床 中
流化床的原理和应用
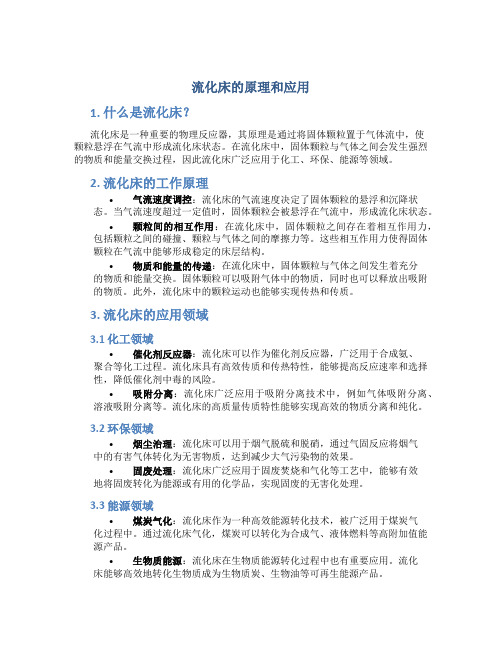
流化床的原理和应用1. 什么是流化床?流化床是一种重要的物理反应器,其原理是通过将固体颗粒置于气体流中,使颗粒悬浮在气流中形成流化床状态。
在流化床中,固体颗粒与气体之间会发生强烈的物质和能量交换过程,因此流化床广泛应用于化工、环保、能源等领域。
2. 流化床的工作原理•气流速度调控:流化床的气流速度决定了固体颗粒的悬浮和沉降状态。
当气流速度超过一定值时,固体颗粒会被悬浮在气流中,形成流化床状态。
•颗粒间的相互作用:在流化床中,固体颗粒之间存在着相互作用力,包括颗粒之间的碰撞、颗粒与气体之间的摩擦力等。
这些相互作用力使得固体颗粒在气流中能够形成稳定的床层结构。
•物质和能量的传递:在流化床中,固体颗粒与气体之间发生着充分的物质和能量交换。
固体颗粒可以吸附气体中的物质,同时也可以释放出吸附的物质。
此外,流化床中的颗粒运动也能够实现传热和传质。
3. 流化床的应用领域3.1 化工领域•催化剂反应器:流化床可以作为催化剂反应器,广泛用于合成氨、聚合等化工过程。
流化床具有高效传质和传热特性,能够提高反应速率和选择性,降低催化剂中毒的风险。
•吸附分离:流化床广泛应用于吸附分离技术中,例如气体吸附分离、溶液吸附分离等。
流化床的高质量传质特性能够实现高效的物质分离和纯化。
3.2 环保领域•烟尘治理:流化床可以用于烟气脱硫和脱硝,通过气固反应将烟气中的有害气体转化为无害物质,达到减少大气污染物的效果。
•固废处理:流化床广泛应用于固废焚烧和气化等工艺中,能够有效地将固废转化为能源或有用的化学品,实现固废的无害化处理。
3.3 能源领域•煤炭气化:流化床作为一种高效能源转化技术,被广泛用于煤炭气化过程中。
通过流化床气化,煤炭可以转化为合成气、液体燃料等高附加值能源产品。
•生物质能源:流化床在生物质能源转化过程中也有重要应用。
流化床能够高效地转化生物质成为生物质炭、生物油等可再生能源产品。
4. 流化床的优势和发展前景•高效传质和传热:流化床具有很强的传质和传热能力,能够大大提高反应速率和产物选择性,提高反应效率。
流化床燃烧技术特点与应用
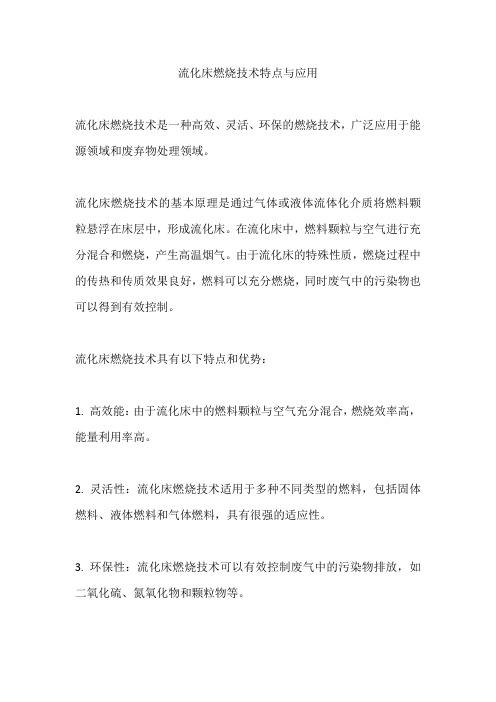
流化床燃烧技术特点与应用
流化床燃烧技术是一种高效、灵活、环保的燃烧技术,广泛应用于能源领域和废弃物处理领域。
流化床燃烧技术的基本原理是通过气体或液体流体化介质将燃料颗粒悬浮在床层中,形成流化床。
在流化床中,燃料颗粒与空气进行充分混合和燃烧,产生高温烟气。
由于流化床的特殊性质,燃烧过程中的传热和传质效果良好,燃料可以充分燃烧,同时废气中的污染物也可以得到有效控制。
流化床燃烧技术具有以下特点和优势:
1. 高效能:由于流化床中的燃料颗粒与空气充分混合,燃烧效率高,能量利用率高。
2. 灵活性:流化床燃烧技术适用于多种不同类型的燃料,包括固体燃料、液体燃料和气体燃料,具有很强的适应性。
3. 环保性:流化床燃烧技术可以有效控制废气中的污染物排放,如二氧化硫、氮氧化物和颗粒物等。
4. 应用广泛:流化床燃烧技术广泛应用于电力、热力、化工、冶金等行业,用于发电、供热、工业生产过程中的废气处理等。
5. 废弃物处理:流化床燃烧技术可以将废弃物转化为能源,如生物质、废纸、废塑料等可以作为燃料进行燃烧,实现资源化利用和减少废弃物的排放。
总之,流化床燃烧技术是一种高效、灵活、环保的燃烧技术,具有广泛的应用前景。
在能源领域和废弃物处理领域,流化床燃烧技术可以发挥重要作用,实现能源的有效利用和废弃物的资源化处理。
污水处理中的流化床技术

维护管理难度大
对水质变化的适应性差
流化床技术对水质变化的适应性较差 ,可能需要针对不同水质进行优化调 整。
流化床内部结构复杂,维护管理难度 较大,需要专业人员进行操作。
03
流化床技术在污水处理中的研究进展
新型流化床技术的研发
悬浮载体流化床技术
利用悬浮载体作为生物膜载体,提高生物膜的挂膜速度和稳定性,降低投资和 运行成本。
在污水处理领域,流化床技术常用于 生物反应器中,利用微生物与固体颗 粒的结合,实现高效、低能耗的污水 处理。
流化床技术的原理
流化床技术的原理是利用流体的动力作用,使固体颗粒在床内不断翻滚、悬浮, 形成一种类似沸腾的状态。
在这种状态下,固体颗粒与流体之间形成高效的传质和传热过程,同时微生物在 固体颗粒表面生长繁殖,形成生物膜,实现对污水中有机物的降解。
移动床生物膜反应器技术
通过在反应器内设置移动床生物膜载体,提高传质效率和生物膜活性,减少污 泥产量。
流化床技术与其他污水处理技术的结合
流化床技术与活性污泥法 的结合
通过将流化床技术与活性污泥法相结合,实 现生物脱氮除磷,提高污水处理效果。
流化床技术与厌氧消化技 术的结合
利用流化床技术处理高浓度有机废水,提高 厌氧消化效率,实现有机废水的资源化利用
污水处理中流化床技术的优势
处理效率高
流化床技术具有较高的处理效率 ,能够快速去除污水中的污染物
。
占地面积小
流化床反应器结构紧凑,占地面积 小,适合在城市等空间有限的地方 使用。
节能环保
流化床技术采用低能耗的搅拌方式 ,运行成本较低,且对环境友好。
污水处理中流化床技术的挑战
悬浮物堵塞
随着悬浮物的积累,流化床可能会出 现堵塞现象,影响正常运行。
- 1、下载文档前请自行甄别文档内容的完整性,平台不提供额外的编辑、内容补充、找答案等附加服务。
- 2、"仅部分预览"的文档,不可在线预览部分如存在完整性等问题,可反馈申请退款(可完整预览的文档不适用该条件!)。
- 3、如文档侵犯您的权益,请联系客服反馈,我们会尽快为您处理(人工客服工作时间:9:00-18:30)。
流化床技术及国内的应用
从流化床在国内制药工业应用的情况出发,分析了流化床在干燥、制粒、制丸、包衣方面的各自特点,同时也阐明了流化床技术发展方向。
流化床技术的应用较为广泛,其中最为广泛的应用技术为流化床干燥,流化床干燥又称沸腾干燥,使颗粒等物料呈沸腾状态,并在动态下进行热交换。
流化床技术因气—固两相大面积接触,其快速传热传质、温度梯度小的特性而被广泛运用于工业生产。
然而,制药工业运用流化床技术进行粉(粒)状物料干燥已有数十年的历史,20世纪末,由德国、日本、瑞士引进的流化床一步制粒机为我国固体制剂生产作出了革命性贡献。
近年来,流化床技术已溶入至干燥、制粒、药物包衣等领域。
1.流化床干燥机
1.1间隙式流化床
随着制药厂GMP改造工作的开展,带搅拌的流化床干燥机得到广泛的运用。
其特点:(1)床内设置搅拌,避免了死角及“沟流”现象;(2)设备结构简单,成本低,得以快速推广。
缺点:间隙式操作,批处理能力低。
同时,对粉尘含量高的干燥操作,过滤器阻力损失大,不能连续操作。
1.2连续式流化床干燥
GMP改造促进了间隙式搅拌流化床的运用,但也在相当程度上将连续式流化床带入了误区,将其定位在清洗死角和交叉污染上,而几乎被遗忘。
连续式流化床却具有间隙式流化床无法比拟的优点:(1)连续进出料,适合大规模生产操作,同使用多台间隙式流化床相比,其无需移动料车,布局面积小;(2)动态下进料,避免了加料引起的压实、结块死角。
(3)易于与制粒机、振荡筛、整粒机构成连续生产线,实现封闭操作的物流系统。
随着GMP的深入,连续式设备会得以发展,但需要制药厂、药机工程设计人员向如下方向去深入研究:
(1)湿粒加料,现行的压板加料伴随密封不严的现象,而星形加料未解决对粒的挤压、变形甚至粘连的问题。
由此看来,开发密闭性良好的分散加料装置势在必行;
(2)清洗死角的问题,传统的过滤角以圆弧过度,舌形多孔板代替直孔板,不积料视窗应得以贯彻;
(3)CIP方面,在设备可扩展分离室,流化床进风系统设置CIP清洗,避免交叉污染。
2.流化床制粒机
2.1顶喷式流化床制粒机
顶喷式流化床制粒机是目前运用最为广泛的机型,由于它集粉体混合—制粒—干燥于一体,俗称一步制粒机,其工艺已经成熟。
2.1.1目前顶喷式流化床制粒机的差距
但与国外先进技术相比,目前顶喷式流化床制粒机尚存很大的差距,主
要表现在几个方面:
(1)应用推广的偏差。
在我国误以为“一步机”就是好,由于欧美药厂所生产的品种单一,生产量大,品种互不交叉,这是我们无法相比的。
而国内生产的一步制粒机仅为国外一、二种机型而已,未形成按工艺设计的非标状态。
其主要原因是缺乏“中试”手段和对“流态化”技术未从根本上消化吸收,大部分厂商至今尚处于形状模仿状态。
(2)GMP概念。
现在一提起一步制粒机的圆形结构就符合GMP,这是药机厂普遍宣传的概念,从某种意义是不完善的。
以德国Glatt WSG120同类产品为例,其设备内壁连接平整,分布板快卸清洗,升降圈气密封,国内大部分设备设计制作远未达到。
2.1.2顶喷流化床制粒机研究方向
笔者认为,顶喷流化床制粒机应从如下角度去与国际先进技术接轨:
(1)介质的处理上,室外采风带来的湿度问题必须考虑,中药制剂、泡腾片等对空气介质相对湿度要求严格,进风必须除湿处理。
(2)介质的过滤,目前国内大多流化床制粒机的终端过滤均安放在换热器前,难以确保设计所需的空气洁净度要求,必须选用耐高温的高效或亚高效过滤器,同时应确保进风无短路,并要求加装压差仪监测积尘状态,并应按可拆装式密闭设计。
(3)安全操作:1)静电处理,设备过滤布袋处于高粉尘浓度区域,应选择嵌有导静电纤维丝,并不能因清灰操作折断。
同时,各个部件应有效的接地,绝缘零部件必须设置导静电针;2)“跑粉”的拦截,设备中布袋过滤器是易损件,工作时破裂将导致药品被风机抽走,造成损失并污染环境,设置捕集装置,一般可在主机出风口至风机段设置旋风分离器或二级布袋除尘器;3)参数的可追溯性,可重演的工艺参数是cGMP的基本特点,流化床制粒机应考虑:a进风湿度的监测,并可记录打印;b过滤器压差监测,并可记录打印;c进风温度——供液的反馈;d物料温度监测;e布袋过滤器压差——清灰频率的反馈。
2.2连续式造粒设备
德国Glatt公司的Continuous Fluid-bed AT、AG两种机型的连续式造粒设备,均已是成熟的连续流态化设备,并广泛运用于生化制药等行列。
根据国外先进经验和国情,常州佳发制粒干燥设备有限公司首推的LFL 机型是连续进出料造粒机。
其特点:(1)连续喷雾,成粒以喷涂方式长大,少粘连,产品为球形;(2)细粉连续返料;(3)出料口设有风选装置,成粒率≥90%。
3.流化床包衣机
3.1顶喷流化床包衣机
用顶喷流化床来进行包衣是流态化工作者梦寐以求的事,这是由于喷雾方式不必约束,容易放大的特点决定的。
国内有选用该方式,但技术均不成熟。
其包衣时,耗用包材量大,成本高,膜层厚薄不均匀,粘连严重。
笔者就顶喷包衣技术作过一定的研究工作,并成功地设计了1000kg/h 顶喷包衣装置,在用户生产中得到成功运用,其基本要求有:(1)非平衡流态化,标准流态化亦称全混式流化,物料随机运动,不宜用于精确包衣(肠溶、缓控释)。
而采用截面非等速流化,促使物料形成规则动态,是顶喷包衣的关键;(2)在喷雾区形成快速运动,衣材雾粒以喷涂方式接触物料而不产生架桥粘连;(3)雾粒在极短的行程喷射至颗粒表面而不产生喷雾干燥。
3.2底喷流化床包衣机
1959年美国Dale. Wurster博士发明底喷包衣机是流态化技术的重大突破,并得名于Wurster系统(如图7所示),与顶喷一步制粒机相比,国内流化床包衣技术尚属起步阶段,尽管国内亦有近十家制造厂推向市场,但却忽略了包衣精确的工艺重复性和低成本要求,仅定义为“包住”是包衣所不能接受的。
常州市佳发制粒干燥设备有限公司1999年首推底喷包衣机,并获得专利授权,至今已形成150g~1500kg/批的实际运用经验。
包衣产品覆盖中药颗粒剂薄膜掩味、防潮、西药胃溶、肠溶、缓控释粒丸、氨基酸类、活性酶及复合肥等,并具备膜材配制、辅料选配初步技能。
Wurster系统所形成的“喷泉”式流态化,使物料具有可述的运行轨迹,雾粒接触每个粒子机会均等,同时粒子表面任一部位亦保证有均等机会与雾粒相遇,所以,物料包衣均匀、衣膜厚度均、包衣增重比低,是目前最为理想的包衣工艺。
喷泉流是由正对较大开孔率的导向筒来形成,但其同时也约束了雾化,单喷嘴工业化放大受到限制,目前要将其放大尚需从以下角度去深入研究:(1)多喷泉流,在同一块分布板上设置多个喷泉,并确保其“包衣柱”一致性;(2)进风均布,流化床空气分布板截面风速严格一致,克服紊流所造成的分布不均;
(3)安全问题,高分子聚合物包衣材料多选用有机溶媒作为介质,操作不安全,设备防爆是一个不容忽视的课题;(4)低成本,薄膜化、低增重比是评价包衣设备的主要指标,同时,由于有机溶剂的使用也大大增加了操作费用,设计尾气溶剂的回收亦是科技工作者所应面对的课题。
3.3侧喷流化床包衣机
侧喷流化床包衣机是将流化床的分布板演变为一个旋转的转盘(如图8所示),并与床体形成一狭小的环隙,热风由此通过。
物料在转盘上由于受离心力、自身重力和热空气的重力作用形成环周的螺旋转运动,从而实现可述的流化状态,因而,侧喷流化床是一种良好的精确包衣设备。
较Wurster系统而言,侧喷流化床的运用受到相当的局限,原因如下:(1)物料物料高度密集区,对微粒包衣时会伴随粘连;(2)通过狭缝的热风量少,因而,喷雾速度较慢,包衣时间较长;(3)因旋转结构的原因,工业化放大困难;
尽管有以上问题,但侧喷流化床它却以如下原因表现出其优越之处:(1)对高剂量药物包衣可采用撒粉放大方式,快速;(2)扩大机型,只需在床体上增加喷嘴的设置,十分便捷。
4.流化床制丸
4.1底喷流化床制丸
底喷制丸流化床表现与Wurster相似,但其设计机理主要依据喷动流态化模型。
其特点:(1)物料形成快速运动,喷涂时不易产生粘连;(2)喷雾不必加于约束,喷液速度快;(3)大风量对流干燥对高剂量药物并要求以溶液、悬浮液喷涂放大制丸操作,具有快速高效。
底喷制丸流化床制丸要点是底喷喷涂放大制丸的技术,关键在于:(1)母粒,以30~40目的蔗糖结晶体或颗粒作为母粒是形成均匀制丸的关键;(2)粘结剂,粘结剂的作用是确保雾粒与母丸接触时良好的铺展、附着,粘度太高会导致母丸粘连,粘连低则出现膜层脱落。
4.2旋转流化床制丸
旋转流化床用于粉体撒粉放大、制丸与包衣工艺一致。