电气 自动化 外文翻译 外文文献 英文文献
电气工程与自动化毕业论文中英文资料外文翻译

电气工程与自动化毕业论文中英文资料外文翻译The Transformer on load ﹠Introduction to DC MachinesIt has been shown that a primary input voltage 1V can be transformed to any desired open-circuit secondary voltage 2E by a suitable choice of turns ratio. 2E is available for circulating a load current impedance. For the moment, a lagging power factor will be considered. The secondary current and the resulting ampere-turns 22N I will change the flux, tending to demagnetize the core, reduce m Φ and with it 1E . Because the primary leakage impedance drop is so low, a small alteration to 1Ewill cause an appreciable increase of primary current from 0I to a new value of 1Iequal to ()()i jX R E V ++111/. The extra primary current and ampere-turns nearly cancel the whole of the secondary ampere-turns. This being so , the mutual flux suffers only a slight modification and requires practically the same net ampere-turns 10N I as on no load. The total primary ampere-turns are increased by an amount 22N I necessary to neutralize the same amount of secondary ampere-turns. In thevector equation , 102211N I N I N I =+; alternatively, 221011N I N I N I -=. At full load,the current 0I is only about 5% of the full-load current and so 1I is nearly equalto 122/N N I . Because in mind that 2121/N N E E =, the input kV A which is approximately 11I E is also approximately equal to the output kV A, 22I E .The physical current has increased, and with in the primary leakage flux towhich it is proportional. The total flux linking the primary ,111Φ=Φ+Φ=Φm p , isshown unchanged because the total back e.m.f.,(dt d N E /111Φ-)is still equal and opposite to 1V . However, there has been a redistribution of flux and the mutual component has fallen due to the increase of 1Φ with 1I . Although the change is small, the secondary demand could not be met without a mutual flux and e.m.f.alteration to permit primary current to change. The net flux s Φlinking thesecondary winding has been further reduced by the establishment of secondaryleakage flux due to 2I , and this opposes m Φ. Although m Φ and 2Φ are indicatedseparately , they combine to one resultant in the core which will be downwards at theinstant shown. Thus the secondary terminal voltage is reduced to dt d N V S /22Φ-=which can be considered in two components, i.e. dt d N dt d N V m //2222Φ-Φ-=orvectorially 2222I jX E V -=. As for the primary, 2Φ is responsible for a substantiallyconstant secondary leakage inductance222222/Λ=ΦN i N . It will be noticed that the primary leakage flux is responsible for part of the change in the secondary terminal voltage due to its effects on the mutual flux. The two leakage fluxes are closely related; 2Φ, for example, by its demagnetizing action on m Φ has caused the changes on the primary side which led to the establishment of primary leakage flux.If a low enough leading power factor is considered, the total secondary flux and the mutual flux are increased causing the secondary terminal voltage to rise with load. p Φ is unchanged in magnitude from the no load condition since, neglecting resistance, it still has to provide a total back e.m.f. equal to 1V . It is virtually the same as 11Φ, though now produced by the combined effect of primary and secondary ampere-turns. The mutual flux must still change with load to give a change of 1E and permit more primary current to flow. 1E has increased this time but due to the vector combination with 1V there is still an increase of primary current.Two more points should be made about the figures. Firstly, a unity turns ratio has been assumed for convenience so that '21E E =. Secondly, the physical picture is drawn for a different instant of time from the vector diagrams which show 0=Φm , if the horizontal axis is taken as usual, to be the zero time reference. There are instants in the cycle when primary leakage flux is zero, when the secondary leakage flux is zero, and when primary and secondary leakage flux is zero, and when primary and secondary leakage fluxes are in the same sense.The equivalent circuit already derived for the transformer with the secondary terminals open, can easily be extended to cover the loaded secondary by the addition of the secondary resistance and leakage reactance.Practically all transformers have a turns ratio different from unity although such an arrangement is sometimes employed for the purposes of electrically isolating one circuit from another operating at the same voltage. To explain the case where 21N N ≠ the reaction of the secondary will be viewed from the primary winding. The reaction is experienced only in terms of the magnetizing force due to the secondary ampere-turns. There is no way of detecting from the primary side whether 2I is large and 2N small or vice versa, it is the product of current and turns which causesthe reaction. Consequently, a secondary winding can be replaced by any number of different equivalent windings and load circuits which will give rise to an identical reaction on the primary .It is clearly convenient to change the secondary winding to an equivalent winding having the same number of turns 1N as the primary.With 2N changes to 1N , since the e.m.f.s are proportional to turns, 2212)/('E N N E = which is the same as 1E .For current, since the reaction ampere turns must be unchanged 1222'''N I N I = must be equal to 22N I .i.e. 2122)/(I N N I =.For impedance , since any secondary voltage V becomes V N N )/(21, and secondary current I becomes I N N )/(12, then any secondary impedance, including load impedance, must becomeI V N N I V /)/('/'221=. Consequently,22212)/('R N N R = and 22212)/('X N N X = . If the primary turns are taken as reference turns, the process is called referring to the primary side.There are a few checks which can be made to see if the procedure outlined is valid.For example, the copper loss in the referred secondary winding must be the same as in the original secondary otherwise the primary would have to supply a differentloss power. ''222R I must be equal to 222R I . )222122122/()/(N N R N N I •• does infact reduce to 222R I .Similarly the stored magnetic energy in the leakage field)2/1(2LI which is proportional to 22'X I will be found to check as ''22X I . The referred secondary 2212221222)/()/(''I E N N I N N E I E kVA =•==.The argument is sound, though at first it may have seemed suspect. In fact, if the actual secondary winding was removed physically from the core and replaced by the equivalent winding and load circuit designed to give the parameters 1N ,'2R ,'2X and '2I , measurements from the primary terminals would be unable to detect any difference in secondary ampere-turns, kVA demand or copper loss, under normal power frequency operation.There is no point in choosing any basis other than equal turns on primary andreferred secondary, but it is sometimes convenient to refer the primary to the secondary winding. In this case, if all the subscript 1’s are interchanged for the subscript 2’s, the necessary referring constants are easily found; e.g. 2'1R R ≈,21'X X ≈; similarly 1'2R R ≈ and 12'X X ≈.The equivalent circuit for the general case where 21N N ≠ except that m r hasbeen added to allow for iron loss and an ideal lossless transformation has been included before the secondary terminals to return '2V to 2V .All calculations of internal voltage and power losses are made before this ideal transformation is applied. The behaviour of a transformer as detected at both sets of terminals is the same as the behaviour detected at the corresponding terminals of this circuit when the appropriate parameters are inserted. The slightly different representation showing the coils 1N and 2N side by side with a core in between is only used for convenience. On the transformer itself, the coils are , of course , wound round the same core.Very little error is introduced if the magnetising branch is transferred to the primary terminals, but a few anomalies will arise. For example ,the current shown flowing through the primary impedance is no longer the whole of the primary current.The error is quite small since 0I is usually such a small fraction of 1I . Slightlydifferent answers may be obtained to a particular problem depending on whether or not allowance is made for this error. With this simplified circuit, the primary and referred secondary impedances can be added to give:221211)/(Re N N R R += and 221211)/(N N X X Xe +=It should be pointed out that the equivalent circuit as derived here is only valid for normal operation at power frequencies; capacitance effects must be taken into account whenever the rate of change of voltage would give rise to appreciablecapacitance currents, dt CdV I c /=. They are important at high voltages and atfrequencies much beyond 100 cycles/sec. A further point is not the only possible equivalent circuit even for power frequencies .An alternative , treating the transformer as a three-or four-terminal network, gives rise to a representation which is just as accurate and has some advantages for the circuit engineer who treats all devices as circuit elements with certain transfer properties. The circuit on this basiswould have a turns ratio having a phase shift as well as a magnitude change, and the impedances would not be the same as those of the windings. The circuit would not explain the phenomena within the device like the effects of saturation, so for an understanding of internal behaviour .There are two ways of looking at the equivalent circuit:(a) viewed from the primary as a sink but the referred load impedance connected across '2V ,or(b) viewed from the secondary as a source of constant voltage 1V with internal drops due to 1Re and 1Xe . The magnetizing branch is sometimes omitted in this representation and so the circuit reduces to a generator producing a constant voltage 1E (actually equal to 1V ) and having an internal impedance jX R + (actually equal to 11Re jXe +).In either case, the parameters could be referred to the secondary winding and this may save calculation time .The resistances and reactances can be obtained from two simple light load tests. Introduction to DC MachinesDC machines are characterized by their versatility. By means of various combination of shunt, series, and separately excited field windings they can be designed to display a wide variety of volt-ampere or speed-torque characteristics for both dynamic and steadystate operation. Because of the ease with which they can be controlled , systems of DC machines are often used in applications requiring a wide range of motor speeds or precise control of motor output.The essential features of a DC machine are shown schematically. The stator has salient poles and is excited by one or more field coils. The air-gap flux distribution created by the field winding is symmetrical about the centerline of the field poles. This axis is called the field axis or direct axis.As we know , the AC voltage generated in each rotating armature coil is converted to DC in the external armature terminals by means of a rotating commutator and stationary brushes to which the armature leads are connected. The commutator-brush combination forms a mechanical rectifier, resulting in a DCarmature voltage as well as an armature m.m.f. wave which is fixed in space. The brushes are located so that commutation occurs when the coil sides are in the neutral zone , midway between the field poles. The axis of the armature m.m.f. wave then in 90 electrical degrees from the axis of the field poles, i.e., in the quadrature axis. In the schematic representation the brushes are shown in quarature axis because this is the position of the coils to which they are connected. The armature m.m.f. wave then is along the brush axis as shown.. (The geometrical position of the brushes in an actual machine is approximately 90 electrical degrees from their position in the schematic diagram because of the shape of the end connections to the commutator.)The magnetic torque and the speed voltage appearing at the brushes are independent of the spatial waveform of the flux distribution; for convenience we shall continue to assume a sinusoidal flux-density wave in the air gap. The torque can then be found from the magnetic field viewpoint.The torque can be expressed in terms of the interaction of the direct-axis air-gapflux per pole d Φ and the space-fundamental component 1a F of the armature m.m.f.wave . With the brushes in the quadrature axis, the angle between these fields is 90 electrical degrees, and its sine equals unity. For a P pole machine 12)2(2a d F P T ϕπ=In which the minus sign has been dropped because the positive direction of thetorque can be determined from physical reasoning. The space fundamental 1a F ofthe sawtooth armature m.m.f. wave is 8/2π times its peak. Substitution in above equation then givesa d a a d a i K i m PC T ϕϕπ==2 Where a i =current in external armature circuit;a C =total number of conductors in armature winding;m =number of parallel paths through winding;Andm PC K aa π2=Is a constant fixed by the design of the winding.The rectified voltage generated in the armature has already been discussedbefore for an elementary single-coil armature. The effect of distributing the winding in several slots is shown in figure ,in which each of the rectified sine waves is the voltage generated in one of the coils, commutation taking place at the moment when the coil sides are in the neutral zone. The generated voltage as observed from the brushes is the sum of the rectified voltages of all the coils in series between brushesand is shown by the rippling line labeled a e in figure. With a dozen or socommutator segments per pole, the ripple becomes very small and the average generated voltage observed from the brushes equals the sum of the average values ofthe rectified coil voltages. The rectified voltage a e between brushes, known also asthe speed voltage, ism d a m d a a W K W m PC e ϕϕπ==2 Where a K is the design constant. The rectified voltage of a distributed winding has the same average value as that of a concentrated coil. The difference is that the ripple is greatly reduced.From the above equations, with all variable expressed in SI units:m a a Tw i e =This equation simply says that the instantaneous electric power associated with the speed voltage equals the instantaneous mechanical power associated with the magnetic torque , the direction of power flow being determined by whether the machine is acting as a motor or generator.The direct-axis air-gap flux is produced by the combined m.m.f. f f i N ∑ of the field windings, the flux-m.m.f. characteristic being the magnetization curve for the particular iron geometry of the machine. In the magnetization curve, it is assumed that the armature m.m.f. wave is perpendicular to the field axis. It will be necessary to reexamine this assumption later in this chapter, where the effects of saturation are investigated more thoroughly. Because the armature e.m.f. is proportional to flux times speed, it is usually more convenient to express the magnetization curve in termsof the armature e.m.f. 0a e at a constant speed 0m w . The voltage a e for a given fluxat any other speed m w is proportional to the speed,i.e. 00a m m a e w w e =Figure shows the magnetization curve with only one field winding excited. This curve can easily be obtained by test methods, no knowledge of any design details being required.Over a fairly wide range of excitation the reluctance of the iron is negligible compared with that of the air gap. In this region the flux is linearly proportional to the total m.m.f. of the field windings, the constant of proportionality being the direct-axis air-gap permeance.The outstanding advantages of DC machines arise from the wide variety of operating characteristics which can be obtained by selection of the method of excitation of the field windings. The field windings may be separately excited from an external DC source, or they may be self-excited; i.e., the machine may supply its own excitation. The method of excitation profoundly influences not only the steady-state characteristics, but also the dynamic behavior of the machine in control systems.The connection diagram of a separately excited generator is given. The required field current is a very small fraction of the rated armature current. A small amount of power in the field circuit may control a relatively large amount of power in the armature circuit; i.e., the generator is a power amplifier. Separately excited generators are often used in feedback control systems when control of the armature voltage over a wide range is required. The field windings of self-excited generators may be supplied in three different ways. The field may be connected in series with the armature, resulting in a shunt generator, or the field may be in two sections, one of which is connected in series and the other in shunt with the armature, resulting in a compound generator. With self-excited generators residual magnetism must be present in the machine iron to get the self-excitation process started.In the typical steady-state volt-ampere characteristics, constant-speed primemovers being assumed. The relation between the steady-state generated e.m.f. a Eand the terminal voltage t V isa a a t R I E V -=Where a I is the armature current output and a R is the armature circuitresistance. In a generator, a E is large than t V ; and the electromagnetic torque T is acountertorque opposing rotation.The terminal voltage of a separately excited generator decreases slightly with increase in the load current, principally because of the voltage drop in the armature resistance. The field current of a series generator is the same as the load current, so that the air-gap flux and hence the voltage vary widely with load. As a consequence, series generators are not often used. The voltage of shunt generators drops off somewhat with load. Compound generators are normally connected so that the m.m.f. of the series winding aids that of the shunt winding. The advantage is that through the action of the series winding the flux per pole can increase with load, resulting in a voltage output which is nearly constant. Usually, shunt winding contains many turns of comparatively heavy conductor because it must carry the full armature current of the machine. The voltage of both shunt and compound generators can be controlled over reasonable limits by means of rheostats in the shunt field. Any of the methods of excitation used for generators can also be used for motors. In the typical steady-state speed-torque characteristics, it is assumed that the motor terminals are supplied froma constant-voltage source. In a motor the relation between the e.m.f. a E generated inthe armature and the terminal voltage t V isa a a t R I E V +=Where a I is now the armature current input. The generated e.m.f. a E is nowsmaller than the terminal voltage t V , the armature current is in the oppositedirection to that in a motor, and the electromagnetic torque is in the direction to sustain rotation of the armature.In shunt and separately excited motors the field flux is nearly constant. Consequently, increased torque must be accompanied by a very nearly proportional increase in armature current and hence by a small decrease in counter e.m.f. to allow this increased current through the small armature resistance. Since counter e.m.f. is determined by flux and speed, the speed must drop slightly. Like the squirrel-cage induction motor ,the shunt motor is substantially a constant-speed motor having about 5 percent drop in speed from no load to full load. Starting torque and maximum torque are limited by the armature current that can be commutatedsuccessfully.An outstanding advantage of the shunt motor is ease of speed control. With a rheostat in the shunt-field circuit, the field current and flux per pole can be varied at will, and variation of flux causes the inverse variation of speed to maintain counter e.m.f. approximately equal to the impressed terminal voltage. A maximum speed range of about 4 or 5 to 1 can be obtained by this method, the limitation again being commutating conditions. By variation of the impressed armature voltage, very wide speed ranges can be obtained.In the series motor, increase in load is accompanied by increase in the armature current and m.m.f. and the stator field flux (provided the iron is not completely saturated). Because flux increases with load, speed must drop in order to maintain the balance between impressed voltage and counter e.m.f.; moreover, the increase in armature current caused by increased torque is smaller than in the shunt motor because of the increased flux. The series motor is therefore a varying-speed motor with a markedly drooping speed-load characteristic. For applications requiring heavy torque overloads, this characteristic is particularly advantageous because the corresponding power overloads are held to more reasonable values by the associated speed drops. Very favorable starting characteristics also result from the increase in flux with increased armature current.In the compound motor the series field may be connected either cumulatively, so that its.m.m.f.adds to that of the shunt field, or differentially, so that it opposes. The differential connection is very rarely used. A cumulatively compounded motor has speed-load characteristic intermediate between those of a shunt and a series motor, the drop of speed with load depending on the relative number of ampere-turns in the shunt and series fields. It does not have the disadvantage of very high light-load speed associated with a series motor, but it retains to a considerable degree the advantages of series excitation.The application advantages of DC machines lie in the variety of performance characteristics offered by the possibilities of shunt, series, and compound excitation. Some of these characteristics have been touched upon briefly in this article. Stillgreater possibilities exist if additional sets of brushes are added so that other voltages can be obtained from the commutator. Thus the versatility of DC machine systems and their adaptability to control, both manual and automatic, are their outstanding features.中文翻译负载运行的变压器及直流电机导论通过选择合适的匝数比,一次侧输入电压1V 可任意转换成所希望的二次侧开路电压2E 。
电气工程及其自动化专业 外文文献 英文文献 外文翻译 plc方面
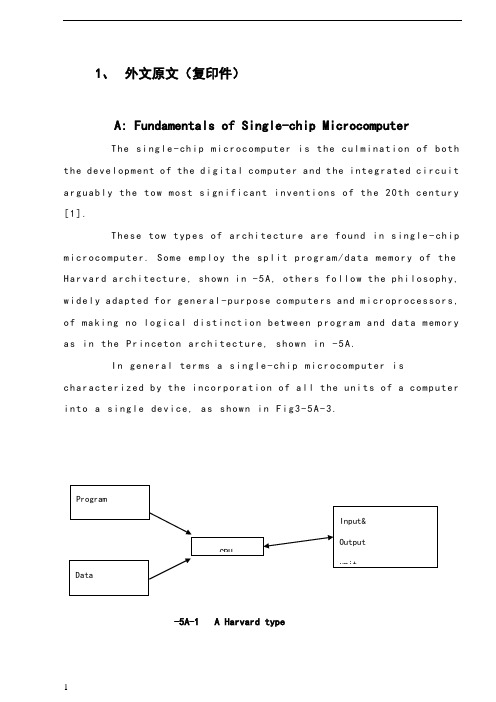
1、外文原文(复印件)A: Fundamentals of Single-chip MicrocomputerTh e si ng le-ch i p mi cr oc om pu ter is t he c ul mi nat i on o f bo th t h e d ev el op me nt o f th e d ig it al com p ut er an d t he int e gr at ed ci rc ui ta r gu ab ly th e t ow m os t s i gn if ic ant i nv en ti on s o f t h e 20t h c en tu ry[1].Th es e to w typ e s of a rc hi te ctu r e ar e fo un d i n s in gl e-ch ip m i cr oc om pu te r. So m e em pl oy t he sp l it p ro gr am/d ata me mo ry o f th e H a rv ar d ar ch it ect u re, sh ow n i n -5A, ot he rs fo ll ow th e ph i lo so ph y, w i de ly a da pt ed fo r g en er al-p ur pos e c om pu te rs an d m i cr op ro ce ss or s, o f m a ki ng no lo gi c al di st in ct io n b e tw ee n p ro gr am a n d da t a m em ory a s i n th e Pr in cet o n ar ch it ec tu re,sh ow n in-5A.In g en er al te r ms a s in gl e-chi p m ic ro co mp ut er i sc h ar ac te ri zed b y the i nc or po ra tio n of al l t he uni t s o f a co mp ut er i n to a s in gl e dev i ce, as s ho wn in Fi g3-5A-3.-5A-1 A Harvard type-5A. A conventional Princeton computerFig3-5A-3. Principal features of a microcomputerRead only memory (ROM).R OM i s u su al ly f or th e p er ma ne nt, n o n-vo la ti le s tor a ge o f an a pp lic a ti on s pr og ra m .M an ym i cr oc om pu te rs an d mi cr oc on tr ol le r s a re in t en de d fo r h ig h-v ol ume a p pl ic at io ns a nd h en ce t he e co nom i ca l ma nu fa ct ure of t he d ev ic es r e qu ir es t ha t the co nt en ts o f the pr og ra m me mo ry b e co mm it te dp e rm an en tl y d ur in g th e m an uf ac tu re o f c hi ps . Cl ear l y, th is im pl ie sa ri g or ou s a pp roa c h t o R OM co de d e ve lo pm en t s in ce c ha ng es ca nn otb e m ad e af te r man u fa ct ur e .T hi s d e ve lo pm en t pr oce s s ma y in vo lv e e m ul at io n us in g a s op hi st ic at ed deve lo pm en t sy st em w i th a ha rd wa re e m ul at io n ca pa bil i ty a s we ll a s th e u se of po we rf ul so ft wa re t oo ls.So me m an uf act u re rs p ro vi de ad d it io na l RO M opt i on s byi n cl ud in g i n th ei r ra ng e de vi ce s wi th (or i nt en de d fo r us e wi th) u s er pr og ra mm ab le m em or y. Th e s im p le st of th es e i s us ua ll y d ev ice w h ic h ca n op er ate in a m ic ro pr oce s so r mo de b y usi n g so me o f th e i n pu t/ou tp ut li ne s as a n ad dr es s an d da ta b us f or acc e ss in g e xt er na l m e mo ry. T hi s t ype o f d ev ic e c an b e ha ve fu nc ti on al l y a s t he si ng le c h ip mi cr oc om pu te r fr om wh ic h i t i s de ri ve d a lb eit w it h r es tr ic ted I/O an d a mo di fie d e xt er na l ci rcu i t. T he u se o f t h es e RO Ml es sd e vi ce s is c om mo n e ve n in p ro du ct io n c ir cu it s wh er e t he v ol um e do es n o t ju st if y th e d e ve lo pm en t co sts of c us to m on-ch i p RO M[2];t he re c a n st il l b e a si g ni fi ca nt s a vi ng in I/O a nd ot he r c hi ps co mp ar ed t o a c on ve nt io nal mi cr op ro ce ss or b as ed c ir cu it. M o re e xa ctr e pl ac em en t fo r RO M d ev ic es c an b e o bt ai ne d in t he f o rm o f va ri an ts w i th 'pi gg y-ba ck'EP RO M(Er as ab le p ro gr am ma bl e ROM)s oc ke ts o rd e vi ce s w it h EP ROM i ns te ad o f R OM 。
电气工程及其自动化专业外文文献英文文献外文翻译方面

1、 外文原文(复印件)A: Fundamentals of Single-chip MicrocomputerT h e sin gle -ch ip mi c ro co m p u t e r is t h e cu lm in at io n of b ot h t h e d e ve lo p me nt of t h e d ig ita l co m p u t e r a n d t h e i nte g rated c ircu it a rgu ab l y t h e to w mo st s ign if i cant i nve nt i o n s of t h e 20t h c e nt u ry [1].T h ese to w t yp e s of arch ite ct u re are fo u n d in s in gle -ch ip m i cro co m p u te r. S o m e e mp l oy t h e sp l it p ro gra m /d at a m e m o r y of t h e H a r va rd arch ite ct u re , s h o wn in -5A , ot h e rs fo l lo w t h e p h i lo so p hy, wid e l y ad a p ted fo r ge n e ral -p u rp o se co m p u te rs an d m i cro p ro ce ss o rs , of m a kin g n o l o g i ca l d i st in ct i o n b et we e n p ro gra m an d d ata m e m o r y as in t h e P rin c eto n a rch ite ct u re , sh o wn in -5A.In ge n e ra l te r m s a s in g le -ch ip m ic ro co m p u t e r is ch a ra cte r ized b y t h e in co r p o rat io n of all t h e u n its of a co mp u te r into a s in gle d e vi ce , as s h o w n in F i g3-5A-3.-5A-1A Harvard type-5A. A conventional Princeton computerProgrammemory Datamemory CPU Input& Output unitmemoryCPU Input& Output unitResetInterruptsPowerFig3-5A-3. Principal features of a microcomputerRead only memory (ROM).RO M is u su a l l y fo r t h e p e r m an e nt , n o n -vo lat i le sto rage of an ap p l i cat io n s p ro g ram .M a ny m i c ro co m p u te rs a n d m i cro co nt ro l le rs are inte n d ed fo r h i gh -vo lu m e ap p l i cat io n s a n d h e n ce t h e e co n o m i cal man u fa c t u re of t h e d e vi ces re q u ires t h at t h e co nt e nts of t h e p ro gra m me mo r y b e co mm i ed p e r m a n e nt l y d u r in g t h e m a n u fa ct u re of c h ip s . C lea rl y, t h i s imp l ies a r i go ro u s ap p ro a ch to ROM co d e d e ve lo p m e nt s in ce ch an ges can n o t b e mad e af te r m an u fa ct u re .T h i s d e ve l o p m e nt p ro ces s m ay i nvo l ve e mu l at i o n u sin g a so p h ist icated d e ve lo p m e nt syste m wit h a h ard wa re e mu l at i o n capab i l it y as we ll as t h e u s e of p o we rf u l sof t war e to o l s.So m e m an u fa ct u re rs p ro vi d e ad d it i o n a l ROM o p t io n s b y in clu d in g in t h e i r ran ge d e v ic es w it h (o r inte n d ed fo r u s e wit h ) u se r p ro g ram m a b le m e mo r y. T h e s im p lest of t h e se i s u su a l l y d e v i ce wh i ch can o p e rat e in a m i cro p ro ce s so r mo d e b y u s in g s o m e of t h e in p u t /o u t p u t l in es as an ad d res s a n d d ata b u s fo r a cc es sin g exte rn a l m e m o r y. T h is t yp e o f d e vi ce can b e h ave f u n ct i o n al l y as t h e s in gle ch ip m i cro co m p u t e r f ro m wh i ch it i s d e ri ved a lb e it wit h re st r icted I/O an d a m o d if ied exte rn a l c ircu it. T h e u s e of t h e se RO M le ss d e vi ces i s co mmo n e ve n in p ro d u ct io n circu i ts wh e re t h e vo lu m e d o e s n ot ju st if y t h e d e ve lo p m e nt co sts of cu sto m o n -ch ip ROM [2];t h e re ca n st i ll b e a si gn if i cant sav in g in I/O an d o t h e r ch ip s co m pared to a External Timing components System clock Timer/ Counter Serial I/O Prarallel I/O RAM ROMCPUco nve nt io n al m i c ro p ro ces so r b ased circ u it. M o re exa ct re p l a ce m e nt fo rRO M d e v ice s can b e o b tain ed in t h e fo rm of va ria nts w it h 'p i g g y-b a c k'E P ROM(E rasab le p ro gramm ab le ROM )s o cket s o r d e v ice s w it h E P ROMin stead of ROM 。
电气工程的外文文献(及翻译)

电气工程的外文文献(及翻译)文献一:Electric power consumption prediction model based on grey theory optimized by genetic algorithms本文介绍了一种基于混合灰色理论与遗传算法优化的电力消耗预测模型。
该模型使用时间序列数据来建立模型,并使用灰色理论来解决数据的不确定性问题。
通过遗传算法的优化,模型能够更好地预测电力消耗,并取得了优异的预测结果。
此模型可以在大规模电力网络中使用,并具有较高的可行性和可靠性。
文献二:Intelligent control for energy-efficient operation of electric motors本文研究了一种智能控制方法,用于电动机的节能运行。
该方法提供了一种更高效的控制策略,使电动机能够在不同负载条件下以较低的功率运行。
该智能控制使用模糊逻辑方法来确定最佳的控制参数,并使用遗传算法来优化参数。
实验结果表明,该智能控制方法可以显著降低电动机的能耗,节省电能。
文献三:Fault diagnosis system for power transformers based on dissolved gas analysis本文介绍了一种基于溶解气体分析的电力变压器故障诊断系统。
通过对变压器油中的气体样品进行分析,可以检测和诊断变压器内部存在的故障类型。
该系统使用人工神经网络模型来对气体分析数据进行处理和分类。
实验结果表明,该系统可以准确地检测和诊断变压器的故障,并有助于实现有效的维护和管理。
文献四:Power quality improvement using series active filter based on iterative learning control technique本文研究了一种基于迭代研究控制技术的串联有源滤波器用于电能质量改善的方法。
电力系统自动化毕业论文中英文资料外文翻译

毕业设计(论文)外文资料翻译专业名称:电力系统自动化英文资料:INDUCTION MOTOR STARTING METHODSAbstract -Many methods can be used to start large AC induction motors. Choices such as full voltage, reduced voltage either by autotransformer or Wyes - Delta, a soft starter, or usage of an adjustable speed drive can all have potential advantages and trade offs. Reduced voltage starting can lower the starting torque and help prevent damage to the load. Additionally, power factor correction capacitors can be used to reduce the current, but care must be taken to size them properly. Usage of the wrong capacitors can lead to significant damage. Choosing the proper starting method for a motor will include an analysis of the power system as well as the starting load to ensure that the motor is designed to deliver the needed performance while minimizing its cost. This paper will examine the most common starting methods and their recommended applications.I. INTRODUCTIONThere are several general methods of starting induction motors: full voltage, reduced voltage, wyes-delta, and part winding types. The reduced voltage type can include solid state starters, adjustable frequency drives, and autotransformers. These, along with the full voltage, or across the line starting, give the purchaser a large variety of automotives when it comes to specifying the motor to be used in a given application. Each method has its own benefits, as well as performance trade offs. Proper selection will involve a thorough investigation of any power system constraints, the load to be accelerated and the overall cost of the equipment.In order for the load to be accelerated, the motor must generate greater torque than the load requirement. In general there are three points of interest on the motor's speed-torque curve. The first is locked-rotor torque (LRT) which is the minimum torque which the motor will develop at rest for all angular positions of the rotor. The second is pull-up torque (PUT) which is defined as the minimum torque developed by the motor during the period of acceleration from rest to the speed at which breakdown torque occurs. The last is the breakdown torque (BDT) which is defined as the maximum torque which the motor will develop. If any of these points are below the required load curve, then the motor will not start.The time it takes for the motor to accelerate the load is dependent on the inertia of the load and the margin between the torque of the motor and the load curve, sometimes called accelerating torque. In general, the longer the time it takes for the motor to accelerate the load, the more heat that will be generated in the rotor bars, shorting ring and the stator winding. This heat leads to additional stresses in these parts and can have an impaction motor life.II. FULL VOLTAGEThe full voltage starting method, also known as across the line starting, is the easiest method to employ, has the lowest equipment costs, and is the most reliable. This method utilizes a control to close a contactor and apply full line voltage to the motor terminals. This method will allow the motor to generate its highest starting torque and provide the shortest acceleration times.This method also puts the highest strain on the power system due to the high starting currents that can be typically six to seven times the normal full load current of the motor. If the motor is on a weak power system, the sudden high power draw can cause a temporary voltage drop, not only at the motor terminals, but the entire power bus feeding the starting motor. This voltage drop will cause a drop in the starting torque of the motor, and a drop in the torque of any other motor running on the power bus. The torque developed by an induction motor varies roughly as the square of the applied voltage. Therefore, depending on the amount of voltage drop, motors running on this weak power bus could stall. In addition, many control systems monitor under voltage conditions, a second potential problem that could take a running motor offline during a full voltage start. Besides electrical variation of the power bus, a potential physical disadvantage of an across the line starting is the sudden loading seen by the driven equipment. This shock loading due to transient torques which can exceed 600% of the locked rotor torque can increase the wear on the equipment, or even cause a catastrophic failure if the load can not handle the torques generated by the motor during staring.A. Capacitors and StartingInduction motors typically have very low power factor during starting and as a result have very large reactive power draw. See Fig. 2. This effect on the system can be reduced by adding capacitors to the motor during starting.The large reactive currents required by the motor lag the applied voltage by 90 electrical degrees. This reactive power doesn't create any measurable output, but is rather the energy required for the motor to function. The product of the applied system voltage and this reactive power component can be measured in V ARS (volt-ampere reactive). The capacitors act to supply a current that leads the applied voltage by 90 electrical degrees. The leading currents supplied by the capacitors cancel the laggingcurrent demanded by the motor, reducing the amount of reactive power required to be drawn from the power system.To avoid over voltage and motor damage, great care should be used to make sure that the capacitors are removed as the motor reaches rated speed, or in the event of a loss of power so that the motor will not go into a generator mode with the magnetizing currents provided from the capacitors. This will be expanded on in the next section and in the appendix.B. Power Factor CorrectionCapacitors can also be left permanently connected to raise the full load power factor. When used in this manner they are called power factor correction capacitors. The capacitors should never be sized larger than the magnetizing current of the motor unless they can be disconnected from the motor in the event of a power loss.The addition of capacitors will change the effective open circuit time constant of the motor. The time constant indicates the time required for remaining voltage in the motor to decay to 36.8% of rated voltage after the loss of power. This is typically one to three seconds without capacitors.With capacitors connected to the leads of the motor, the capacitors can continue to supply magnetizing current after the power to the motor has been disconnected. This is indicated by a longer time constant for the system. If the motor is driving a high inertia load, the motor can change over to generator action with the magnetizingCurrent from the capacitors and the shaft driven by the load. This can result in the voltage at the motor terminals actually rising to nearly 50% of rated voltage in some cases. If the power is reconnected before this voltage decays severe transients can be created which can cause significant switching currents and torques that can severely damage the motor and the driven equipment. An example of this phenomenon is outlined in the appendix.Ⅲ. REDUCED VOLTAGEEach of the reduced voltage methods are intended to reduce the impact of motor starting current on the power system by controlling the voltage that the motor sees atthe terminals. It is very important to know the characteristics of the load to be started when considering any form of reduced voltage starting. The motor manufacturer will need to have the speed torque curve and the inertia of the driven equipment when they validate their design. The curve can be built from an initial, or break away torque, as few as four other data points through the speed range, and the full speed torque for the starting condition. A centrifugal or square curve can be assumed in many cases, but there are some applications where this would be problematic. An example would be screw compressors which have a much higher torque requirement at lower speeds than the more common centrifugal or fan load. See Fig. 3. By understanding the details of the load to be started the manufacturer can make sure that the motor will be able to generate sufficient torque to start the load, with the starting method that is chosen.A. AutotransformerThe motor leads are connected to the lower voltage side of the transformer. The most common taps that are used are 80%, 65%, and 50%. At 50% voltage the current on the primary is 25% of the full voltage locked rotor amps. The motor is started with this reduced voltage, and then after a pre-set condition is reached the connection is switched to line voltage. This condition could be a preset time, current level, bus volts, or motor speed. The change over can be done in either a closed circuit transition, or an open circuit transition method. In the open circuit method the connection to the voltage is severed as it is changed from the reduced voltage to the line level. Care should be used to make sure that there will not be problems from transients due to the switching. This potential problem can be eliminated by using the closed circuit transition. With the closed circuit method there is a continuousVoltage applied to the motor. Another benefit with the autotransformer starting is in possible lower vibration and noise levels during starting.Since the torque generated by the motor will vary as the square of the applied voltage, great care should be taken to make sure that there will be sufficient accelerating torque available from the motor. A speed torque curve for the driven equipment along with the inertia should be used to verify the design of the motor. A good rule of thumb is to have a minimum of 10% of the rated full load torque of the motor as a margin at all points of the curve.Additionally, the acceleration time should be evaluated to make sure that the motor has sufficient thermal capacity to handle the heat generated due to the longeracceleration time.B. Solid State or Soft StartingThese devices utilize silicon controlled rectifiers or Scars. By controlling the firing angle of the SCR the voltage that the device produces can be controlled during the starting of the motor by limiting the flow of power for only part of the duration of the sine wave.The most widely used type of soft starter is the current limiting type. A current limit of 175% to 500% of full load current is programmed in to the device. It then will ramp up the voltage applied to the motor until it reaches the limit value, and will then hold that current as the motor accelerates.Tachometers can be used with solid state starters to control acceleration time. Voltage output is adjusted as required by the starter controller to provide a constant rate of acceleration.The same precautions in regards to starting torque should be followed for the soft starters as with the other reduced voltage starting methods. Another problem due to the firing angle of the SCR is that the motor could experience harmonic oscillating torques. Depending on the driven equipment, this could lead to exciting the natural frequency of the system.C. Adjustable Frequency DrivesThis type of device gives the greatest overall control and flexibility in starting induction motors giving the most torque for an amount of current. It is also the most costly.The drive varies not only the voltage level, but also the frequency, to allow the motor to operate on a constant volt per hertz level. This allows the motor to generate full load torque throughout a large speed range, up to 10:1. During starting, 150% of rated current is typical.This allows a significant reduction in the power required to start a load and reduces the heat generated in the motor, all of which add up to greater efficiency. Usage of the AFD also can allow a smaller motor to be applied due to the significant increase of torque available lower in the speed range. The motor should still be sizedlarger than the required horsepower of the load to be driven. The AFD allows a great degree of control in the acceleration of the load that is not as readily available with the other types of reduced voltage starting methods.The greatest drawback of the AFD is in the cost relative to the other methods. Drives are the most costly to employ and may also require specific motor designs to be used. Based on the output signal of the drive, filtered or unfiltered, the motor could require additional construction features. These construction features include insulated bearings, shaft grounding brushes, and insulated couplings due to potential shaft current from common mode voltage. Without these features, shaft currents, which circulate through the shaft to the bearing, through the motor frame and back, create arcing in the bearings that lead to premature bearing failure, this potential for arcing needs to be considered when applying a motor/drive package in a hazardous environment, Division2/Zone2.An additional construction feature of a motor used on an AFD may require is an upgraded insulation system on the motor windings. An unfiltered output signal from a drive can create harmonic voltage spikes in the motor, stressing the insulation of the motor windings.It is important to note that the features described pertain to motors which will be started and run on an AFD. If the drive is only used for starting the motor, these features may not be necessary. Consult with the motor manufacturer for application specific requirements.D. Primary Resistor or Reactor StartingThis method uses either a series resistor or reactor bank to be placed in the circuit with the motor. Resistor starting is more frequently used for smaller motors.When the motor is started, the resistor bank limits the flow of inrush current and provides for a voltage drop at the motor terminals. The resistors can be selected to provide voltage reductions up to 50%. As the motor comes up to speed, it develops a counter EMF (electro-magnetic field) that opposes the voltage applied to the motor. This further limits the inrush currents. As the inrush current diminishes, so does t>e voltage drop across the resistor bank allowing the torque generated by the motor to increase. At a predetermined time a device will short across the resistors and open the starting contactor effectively removing the resistor bank from the circuit. This provides for a closed transition and eliminates the concerns due to switchingtransients.Reactors will tend to oppose any sudden changes in current and therefore act to limit the current during starting. They will remain shorted after starting and provide a closed transition to line voltage.E .Star delta StartingThis approach started with the induction motor, the structure of each phase of the terminal are placed in the motor terminal box. This allows the motor star connection in the initial startup, and then re-connected into a triangle run. The initial start time when the voltage is reduced to the original star connection, the starting current and starting torque by 2 / 3. Depending on the application, the motor switch to the triangle in the rotational speed of between 50% and the maximum speed. Must be noted that the same problems, including the previously mentioned switch method, if the open circuit method, the transition may be a transient problem. This method is often used in less than 600V motor, the rated voltage 2.3kV and higher are not suitable for star delta motor start method.Ⅴ. INCREMENT TYPEThe first starting types that we have discussed have deal with the way the energy is applied to the motor. The next type deals with different ways the motor can be physically changed to deal with starting issues.Part WindingWith this method the stator of the motor is designed in such a way that it is made up of two separate windings. The most common method is known as the half winding method. As the name suggests, the stator is made up of two identical balanced windings. A special starter is configured so that full voltage can be applied to one half of the winding, and then after a short delay, to the second half. This method can reduce the starting current by 50 to 60%, but also the starting torque. One drawback to this method is that the motor heating on the first step of the operation is greater than that normally encountered on across-the-line start. Therefore the elapsed time on the first step of the part winding start should be minimized. This method also increases the magnetic noise of the motor during the first step.IV .ConclusionThere are many ways asynchronous motor starting, according to the constraints of power systems, equipment costs, load the boot device to select the best method. From the device point of view, was the first full-pressure launch the cheapest way, but it may increase the cost efficiency in the use of, or the power supply system in the region can not meet their needs. Effective way to alleviate the buck starts the power supply system, but at the expense of the cost of starting torque.These methods may also lead to increased motor sizes have led to produce the required load torque. Inverter can be eliminated by the above two shortcomings, but requires an additional increase in equipment costs. Understand the limitations of the application, and drives the starting torque and speed, allowing you for your application to determine the best overall configuration.英文资料翻译:异步电动机起动的方法摘要:大容量的交流异步电动机有多种启动方法。
自动化专业中英文对照外文翻译文献
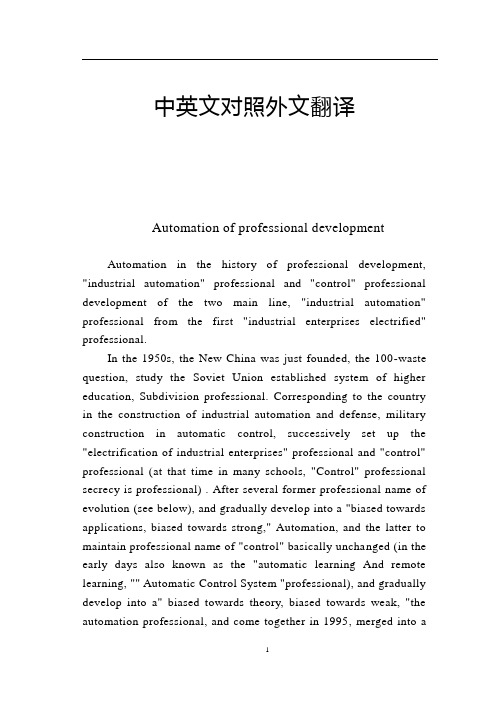
中英文对照外文翻译Automation of professional developmentAutomation in the history of professional development, "industrial automation" professional and "control" professional development of the two main line, "industrial automation" professional from the first "industrial enterprises electrified" professional.In the 1950s, the New China was just founded, the 100-waste question, study the Soviet Union established system of higher education, Subdivision professional. Corresponding to the country in the construction of industrial automation and defense, military construction in automatic control, successively set up the "electrification of industrial enterprises" professional and "control" professional (at that time in many schools, "Control" professional secrecy is professional) . After several former professional name of evolution (see below), and gradually develop into a "biased towards applications, biased towards strong," Automation, and the latter to maintain professional name of "control" basically unchanged (in the early days also known as the "automatic learning And remote learning, "" Automatic Control System "professional), and gradually develop into a" biased towards theory, biased towards weak, "the automation professional, and come together in 1995, merged into aunified" automatic "professional . In 1998, according to the Ministry of Education announced the latest professional undergraduate colleges and universities directory, adjusted, the merger of the new "automated" professional include not only the original "automatic" professional (including "industrial automation" professional and "control" professional ), Also increased the "hydraulic transmission and control of" professional (part), "electrical technology" professional (part) and "aircraft guidance and control of" professional (part).Clearly, one of China's automation professional history of the development of China's higher education actually is a new development of the cause of a microcosm of the history, but also the history of New China industrial development of a miniature. Below "industrial automation" professional development of the main line of this example, a detailed review of its development process in the many professional name change (in real terms in the professional content changes) and its industrial building at the time of the close relationship.First a brief look at the world and China's professional division history. We know that now use the professional division is largely from the 19th century to the beginning of the second half of the first half of the 20th century stereotypes of the engineering, is basically industry (products) for the objects to the division, they have been the image of people Known as the "industry professionals" or "trade associations." At present the international education system in two categories, with Britain and the United States as the representative of the education system not yet out of "industry professionals" system, but has taken the "generalist" the road of education and the former Soviet Union for Europe (close to the Soviet Union) as the representative The education system, at the beginning of theimplementation of "professionals" education, professional-very small, although reforms repeatedly, but to the current "industry professionals" are still very obvious characteristics.In the 1950s, just after the founding of New China, a comprehensive study and the Soviet Union and sub-professional very small; Since reform and opening up, only to Britain and the United States to gradually as the representative of the education system to move closer, and gradually reduce the professional, the implementation of "generalist" education through a number of professional Restructuring and merger (the total number of professionals from the maximum of 1,343 kinds of gradually reducing the current 249 kinds), although not out of "industry professionals" and "Mei Ming," but many of the colleges and universities, mostly only one of a Professional, rather than the past more than a professional.Before that, China's first professional automation from the National University in 1952 when the first major readjustment of the establishment of professional - electrified professional industrial enterprises. At that time, the Soviet Union assistance to the construction of China's 156 large industrial enterprises, automation of much-needed electrical engineering and technical personnel, and such professional and technical personnel training, and then was very consistent with China's industrial construction. By the 1960s, professional name changed to "industrial electric and automation," the late 1970s when to resume enrollment "Electric Industrial Automation" professional. This is not only professional name changes, but has its profound meaning, it reflects China's industries from "electrified" step by step to the "automatic" into the real history and that part of the development trend of China's automation professional reflects how urgent countries Urgent for the country'seconomic construction services that period of history and development of real direction.1993, after four years of the third revision of the undergraduate professional directories, the State Education Commission issued a call "system integrity, more scientific and reasonable, the harmonization of norms," the "ordinary professional directory of undergraduate colleges and universities." "Electric Industrial Automation" and "production process automation" merger of the two professional electrician to set up a kind of "industrial automation" professional, by the then Ministry of Industry Machinery centralized management colleges and universities to set up industrial automation teaching guide at the Commission, responsible for the "Industrial Automation "professional teaching and guiding work at the same time," Control "was attributable to the professional category of electronic information, the then Ministry of Industry of electronic centralized management control to set up colleges and universities teaching guide at the Commission, responsible for the" control " Professional teaching guide our work. After the professional adjustment, further defined the "industrial automation" professional and "control" professional "- both strong and weak, hardware and software into consideration and control theory and practical system integration, and the movement control, process control and other targets of control "The common characteristics with the training objectives, but also the basic set of" industrial automation "biased towards strong, professional, biased towards applications," Control "professional biased towards weak, biased towards the theory of professional characteristics and pattern of division of labor. 1995, the State Education Commission promulgated the "(University) undergraduate engineering leading professional directory", the electrical category "industrialautomation" professional and the original electronic information such as "control" of professional electronic information into a new category of "automatic" professional . As this is the leading professional directory, are not enforced, coupled with general "industrial automation" strong or weak, both professional "into" a weak professional category of electronic information is not conducive to professional development and thus many Schools remain "industrial automation" professional and "control" the situation of professional co-exist. Since 1996 more, again commissioned by the Ministry of National Education Ministry of Industry and electronic machinery industries of other parts of the establishment of the new session (second session) centralized management guidance at the University Teaching Commission, making the leading professionals have not been effective Implemented.1998, to meet the country's economic construction of Kuan Koujing personnel training needs, further consolidation of professional and international "generalist" education track by the Ministry of Education announced a fourth revision of the latest "Universities Undergraduate Catalog." So far in the use of the directory, the total number of professionals from the third amendments to the 504 kinds of substantially reduced to 249 species, the original directory is strong, professional electrician and a weak professional category such as electronics and information into categories Electric power, the unity of Information, a former electrician at the same time kind of "industrial automation" professional and the type of electronic information "control" professional formal merger, together with the "hydraulic transmission and control of" professional (part) , "Electric technology" professional (part) and "aircraft guidance and controlof" professional (part), the composition of the new (enforcement) are electrical information such as "automatic" professional. According to statistics, so far the country has more than 200 colleges and universities set up this kind of "automatic" professional. If the name of automation as part of their professional expertise (such as "electrical engineering and automation," "mechanical design and manufacturing automation," "agricultural mechanization and automation" and other professionals) included Automation has undoubtedly is the largest in China A professional.Of the characteristics of China's automation professional:Recalling China's professional history of the development of automation, combined with the corresponding period of the construction of China's national economy to the demand for automation and automated the development of the cause, it is not difficult to sum up following professional characteristics:(1) China's automation professional is not only a relatively long history (since 1952 have been more than 50 years), and from the first day of the establishment of professional automation, has been a professional one of the countries in urgent need, therefore the number of students has also been The largest and most employers welcome the allocation of the professional one.(2) China's automation is accompanied by a professional from the electrification of China's industrial automation step by step to the development of stable development, professional direction and the main content from the first prominent electrified "the electrification of industrial enterprises" step by step for the development of both the electric and automation " Industrial electric and automation ", highlighting the electrical automation" Electric Industrial Automation "and prominent automation" industrial automation ", then the merger of professional education reform in1995 and" control "of professional content into a broader" automated " Professional. From which we can see that China's automation professional Although the initial study in the Soviet education system established under the general environment, but in their development and the Soviet Union or the United States and Britain did not copy the mode, but with China's national conditions (to meet national needs for The main goal) from the innovation and development of "cross-industry professionals," features the professional.自动化专业的发展自动化专业的发展历史中,有“工业自动化”专业与“自动控制”专业两条发展主线,其中“工业自动化”专业最早源于“工业企业电气化”专业。
电气工程及其自动化 外文翻译 外文文献 英文文献 电力系统的简介
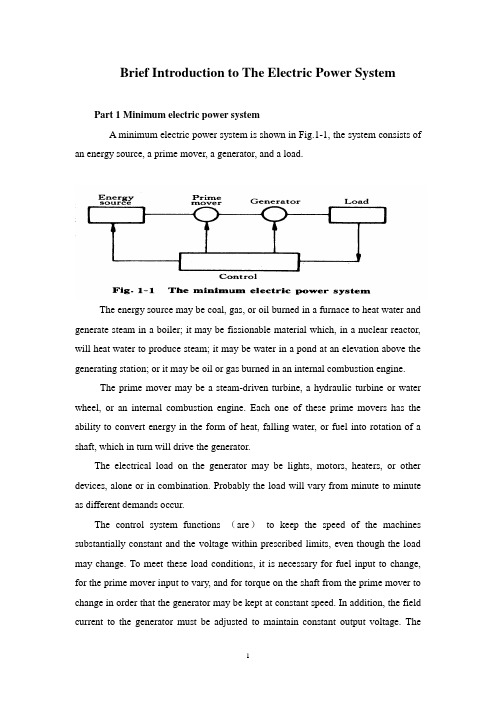
Brief Introduction to The Electric Power SystemPart 1 Minimum electric power systemA minimum electric power system is shown in Fig.1-1, the system consists of an energy source, a prime mover, a generator, and a load.The energy source may be coal, gas, or oil burned in a furnace to heat water and generate steam in a boiler; it may be fissionable material which, in a nuclear reactor, will heat water to produce steam; it may be water in a pond at an elevation above the generating station; or it may be oil or gas burned in an internal combustion engine.The prime mover may be a steam-driven turbine, a hydraulic turbine or water wheel, or an internal combustion engine. Each one of these prime movers has the ability to convert energy in the form of heat, falling water, or fuel into rotation of a shaft, which in turn will drive the generator.The electrical load on the generator may be lights, motors, heaters, or other devices, alone or in combination. Probably the load will vary from minute to minute as different demands occur.The control system functions (are)to keep the speed of the machines substantially constant and the voltage within prescribed limits, even though the load may change. To meet these load conditions, it is necessary for fuel input to change, for the prime mover input to vary, and for torque on the shaft from the prime mover to change in order that the generator may be kept at constant speed. In addition, the field current to the generator must be adjusted to maintain constant output voltage. Thecontrol system may include a man stationed in the power plant who watches a set of meters on the generator output terminals and makes the necessary adjustments manually. In a modern station, the control system is a servomechanism that senses generator-output conditions and automatically makes the necessary changes in energy input and field current to hold the electrical output within certain specifications..Part 2 More Complicated SystemsIn most situations the load is not directly connected to the generator terminals. More commonly the load is some distance from the generator, requiring a power line connecting them. It is desirable to keep the electric power supply at the load within specifications. However, the controls are near the generator, which may be in another building, perhaps several miles away.If the distance from the generator to the load is considerable, it may be desirable to install transformers at the generator and at the load end, and to transmit the power over a high-voltage line (Fig.1-2). For the same power, the higher-voltage line carries less current, has lower losses for the same wire size, and provides more stable voltage.In some cases an overhead line may be unacceptable. Instead it may be advantageous to use an underground cable. With the power systems talked above, the power supply to the load must be interrupted if, for any reason, any component of the system must be moved from service for maintenance or repair. Additional system load may require more power than the generator can supply. Another generator with its associated transformers and high-voltage line might be added.It can be shown that there are some advantages in making ties between the generators (1) and at the end of the high-voltage lines (2 and 3), as shown in Fig.1-3. This system will operate satisfactorily as long as no trouble develops or no equipmentneeds to be taken out of service.The above system may be vastly improved by the introduction of circuit breakers, which may be opened and closed as needed. Circuit breakers added to the system, Fig.1-4, permit selected piece of equipment to switch out of service without disturbing the remainder of system. With this arrangement any element of the system may be deenergized for maintenance or repair by operation of circuit breakers.Of course, if any piece of equipment is taken out of service, then the total load must be carried by the remaining equipment. Attention must be given to avoid overloads during such circumstances. If possible, outages of equipment are scheduled at times when load requirements are below normal.Fig.1-5 shows a system in which three generators and three loads are tied together by three transmission lines. No circuit breakers are shown in this diagram, although many would be required in such a system.Part 3 Typical System LayoutThe generators, lines, and other equipment which form an electric system are arranged depending on the manner in which load grows in the area and may be rearranged from time to time.However, there are certain plans into which a particular system design may be classified. Three types are illustrated: the radial system, the loop system, and the network system. All of these are shown without the necessary circuit breakers. In each of these systems, a single generator serves four loads.The radial system is shown in Fig.1-6. Here the lines form a “tree” spreading out from the generator. Opening any line results in interruption of power to one or more of the loads.The loop system is illustrated in Fig.1-7. With this arrangement all loads may be served even though one line section is removed from service. In some instances during normal operation, the loop may be open at some point, such as A. In case a line section is to be taken out, the loop is first closed at A and then the line section removed. In this manner no service interruptions occur.Fig.1-8 shows the same loads being served by a network. With this arrangement each load has two or more circuits over which it is fed.Distribution circuits are commonly designed so that they may be classified as radial or loop circuits. The high-voltage transmission lines of most power systems are arranged as network. The interconnection of major power system results in networks made up by many line sections.Part 4 Auxiliary EquipmentCircuit breakers are necessary to deenergize equipment either for normal operation or on the occurrence of short circuits. Circuit breakers must be designed to carry normal-load currents continuously, to withstand the extremely high currents that occur during faults, and to separate contacts and clear a circuit in the presence of fault. Circuit breakers are rated in terms of these duties.When a circuit breaker opens to deenergize a piece of equipment, one side of the circuit breaker usually remains energized, as it is connected to operating equipment. Since it is sometimes necessary to work on the circuit breaker itself, it is also necessary to have means by which the circuit breaker may be completely disconnected from other energized equipment. For this purpose disconnect switches are placed in series with the circuit breakers. By opening these disconnectors, thecircuit breaker may be completely deenergized, permitting work to be carried on in safety.Various instruments are necessary to monitor the operation of the electric power system. Usually each generator, each transformer bank, and each line has its own set of instruments, frequently consisting of voltmeters, ammeters, wattmeters, and varmeters.When a fault occurs on a system, conditions on the system undergo a sudden change. V oltages usually drop and currents increase. These changes are most noticeable in the immediate vicinity of fault. On-line analog computers, commonly called relays, monitor these changes of conditions, make a determination of which breaker should be opened to clear the fault, and energize the trip circuits of those appropriate breakers. With modern equipment, the relay action and breaker opening causes removal of fault within three or four cycles after its initiation.The instruments that show circuit conditions and the relays that protect the circuits are not mounted directly on the power lines but are placed on switchboards in a control house. Instrument transformers are installed on the high-voltage equipment, by means of which it is possible to pass on to the meters and relays representative samples of the conditions on the operating equipment. The primary of a potential transformer is connected directly to the high-voltage equipment. The secondary provides for the instruments and relays a voltage which is a constant fraction of voltage on the operating equipment and is in phase with it;similarly, a current transformer is connected with its primary in the high-current circuit. The secondary winding provides a current that is a known fraction of the power-equipment current and is in phase with it.Bushing potential devices and capacitor potential devices serve the same purpose as potential transformers but usually with less accuracy in regard to ratio and phase angle.中文翻译:电力系统的简介第一部分:最小电力系统一个最小电力系统如图1-1所示,系统包含动力源,原动机,发电机和负载。
电气工程及其自动化专业毕业论文外文翻译

本科毕业设计(论文)中英文对照翻译院(系部)工程学院专业名称电气工程及其自动化年级班级 11级2班学生姓名蔡李良指导老师赵波Infrared Remote Control SystemAbstractRed outside data correspondence the technique be currently within the scope of world drive extensive usage of a kind of wireless conjunction technique, drive numerous hardware and software platform support。
Red outside the transceiver product have cost low,small scaled turn, the baud rate be quick,point to point SSL, be free from electromagnetism thousand Raos etc. characteristics,can realization information at dissimilarity of the product fast,convenience,safely exchange and transmission, at short distance wireless deliver aspect to own very obvious of advantage。
Along with red outside the data deliver a technique more and more mature, the cost descend, red outside the transceiver necessarily will get at the short distance communication realm more extensive of application.The purpose that design this s ystem is transmit customer’s operation information with infrared rays for transmit media, then demodulate original signal with receive circuit。
毕业设计毕业论文电气工程及其自动化外文翻译中英文对照
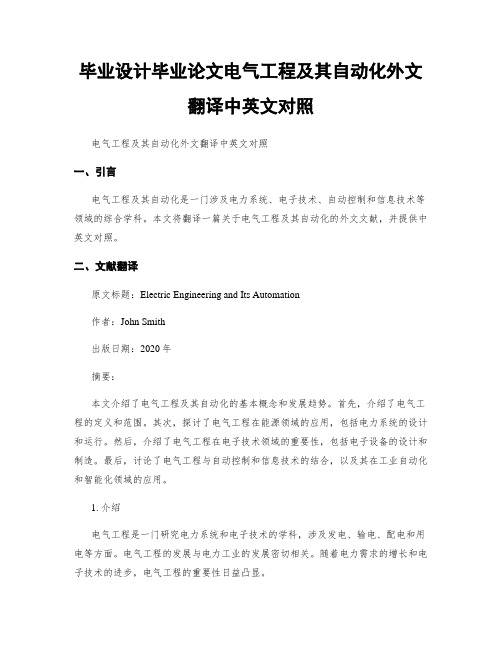
毕业设计毕业论文电气工程及其自动化外文翻译中英文对照电气工程及其自动化外文翻译中英文对照一、引言电气工程及其自动化是一门涉及电力系统、电子技术、自动控制和信息技术等领域的综合学科。
本文将翻译一篇关于电气工程及其自动化的外文文献,并提供中英文对照。
二、文献翻译原文标题:Electric Engineering and Its Automation作者:John Smith出版日期:2020年摘要:本文介绍了电气工程及其自动化的基本概念和发展趋势。
首先,介绍了电气工程的定义和范围。
其次,探讨了电气工程在能源领域的应用,包括电力系统的设计和运行。
然后,介绍了电气工程在电子技术领域的重要性,包括电子设备的设计和制造。
最后,讨论了电气工程与自动控制和信息技术的结合,以及其在工业自动化和智能化领域的应用。
1. 介绍电气工程是一门研究电力系统和电子技术的学科,涉及发电、输电、配电和用电等方面。
电气工程的发展与电力工业的发展密切相关。
随着电力需求的增长和电子技术的进步,电气工程的重要性日益凸显。
2. 电气工程在能源领域的应用电气工程在能源领域的应用主要包括电力系统的设计和运行。
电力系统是由发电厂、输电线路、变电站和配电网络等组成的。
电气工程师负责设计和维护这些设施,以确保电力的可靠供应。
3. 电气工程在电子技术领域的重要性电气工程在电子技术领域的重要性体现在电子设备的设计和制造上。
电子设备包括电脑、手机、电视等消费电子产品,以及工业自动化设备等。
电气工程师需要掌握电子电路设计和数字信号处理等技术,以开发出高性能的电子设备。
4. 电气工程与自动控制和信息技术的结合电气工程与自动控制和信息技术的结合是电气工程及其自动化的核心内容。
自动控制技术可以应用于电力系统的运行和电子设备的控制,以提高系统的稳定性和效率。
信息技术则可以用于数据采集、处理和传输,实现对电力系统和电子设备的远程监控和管理。
5. 电气工程在工业自动化和智能化领域的应用电气工程在工业自动化和智能化领域的应用越来越广泛。
电气自动化英文文献
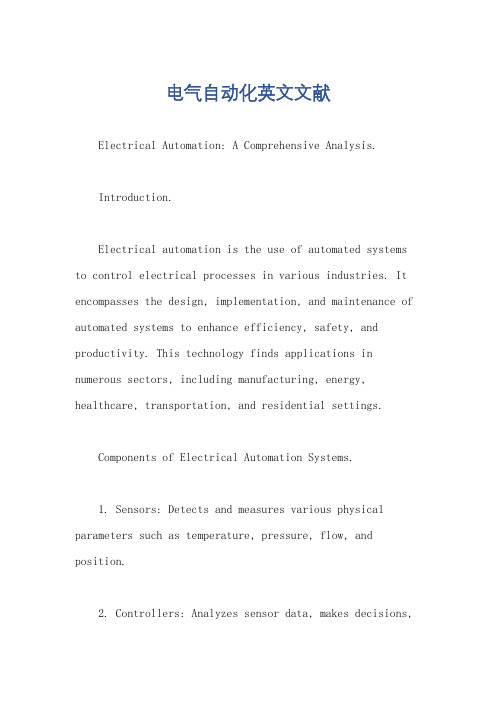
电气自动化英文文献Electrical Automation: A Comprehensive Analysis.Introduction.Electrical automation is the use of automated systems to control electrical processes in various industries. It encompasses the design, implementation, and maintenance of automated systems to enhance efficiency, safety, and productivity. This technology finds applications in numerous sectors, including manufacturing, energy, healthcare, transportation, and residential settings.Components of Electrical Automation Systems.1. Sensors: Detects and measures various physical parameters such as temperature, pressure, flow, and position.2. Controllers: Analyzes sensor data, makes decisions,and activates actuators based on programmed instructions.3. Actuators: Physical devices that perform actions in response to controller commands, such as opening valves, starting motors, or moving conveyors.4. Communication Network: Connects sensors, controllers, and actuators, enabling data exchange and coordination.5. Human-Machine Interface (HMI): Provides an interface for operators to interact with the automated system and monitor its performance.Benefits of Electrical Automation.1. Increased Efficiency: Automates repetitive tasks, reducing human errors and improving productivity.2. Enhanced Safety: Eliminates the need for manual intervention in hazardous environments, reducing the riskof accidents.3. Improved Quality: Ensures consistent and accurate control of processes, leading to higher quality products.4. Reduced Costs: Optimizes energy usage, reduces maintenance expenses, and eliminates labor costs associated with manual operations.5. Increased Flexibility: Allows for rapid reconfiguration of automated systems to adapt to changing requirements or product specifications.Applications of Electrical Automation.1. Manufacturing: Automated assembly lines, robotic workstations, and inventory management systems.2. Energy: Smart grids, renewable energy systems, and energy efficiency management.3. Healthcare: Automated medical devices, patient monitoring systems, and hospital automation.4. Transportation: Vehicle control systems, traffic management systems, and automated logistics.5. Residential Settings: Home automation systems for lighting, temperature control, and security.Challenges in Electrical Automation.1. Complexity: Designing and integrating complex automated systems requires advanced engineering skills and specialized software.2. Cybersecurity: Automated systems can be vulnerable to cyberattacks, requiring robust security measures.3. Maintenance and Troubleshooting: Regular maintenance and skilled technicians are crucial to ensure thereliability and uptime of automated systems.4. Initial Investment: Implementing electrical automation systems can involve significant upfront costs, requiring careful planning and justification of theinvestment.5. Displacement of Workforce: Automation can lead to job displacement, necessitating training and upskilling programs for displaced workers.Future Trends in Electrical Automation.1. Artificial Intelligence (AI) and Machine Learning: Enabling predictive analytics, self-optimization, and autonomous decision-making.2. Internet of Things (IoT): Connecting automated systems to the internet for remote monitoring, data analytics, and cloud-based services.3. Digital Twins: Creating virtual models of automated systems for simulation, testing, and real-time monitoring.4. Edge Computing: Processing data on-site to reduce latency and improve system responsiveness.5. Increased Adoption in Emerging Industries: Expanding applications in sectors such as agriculture, mining, and construction.Conclusion.Electrical automation is a transformative technology that has revolutionized various industries, driving efficiency, safety, quality, and cost savings. As technology continues to advance, the applications and possibilities of electrical automation are bound to grow exponentially, contributing to further innovation and progress across numerous sectors.。
电气自动化 单片机 外文文献 英文文献 外文翻译 中英对照

Single-chip1.The definition of a single-chipSingle-chip is an integrated on a single chip a complete computer system .Even though most of his features in a small chip,but it has a need to complete the majority of computer components:CPU,memory,internal and external bus system,most will have the Core.At the same time,such as integrated communication interfaces,timers,real-time clock and other peripheral equipment.And now the most powerful single-chip microcomputer system can even voice ,image,networking,input and output complex system integration on a single chip.Also known as single-chip MCU(Microcontroller),because it was first used in the field of industrial control.Only by the single-chip CPU chip developed from the dedicated processor. The design concept is the first by a large numberof peripherals and CPU in a single chip,the computer system so that smaller,more easily integrated into the complex and demanding on the volume control devices.INTEL the Z80 is one of the first design in accordance with the idea of the processor,From then on,the MCU and the development of a dedicated processor parted ways.Early single-chip 8-bit or all the four.One of the most successful is INTELs 8031,because the performance of a simple and reliable access to a lot of good praise.Since then in 8031to develop a single-chip microcomputer system MCS51 series.based on single-chip microcomputer system of the system is still widely used until now.As the field of industrial control requirements increase in the beginning of a 16-bit single-chip,but not ideal because the price has not been very widely used.After the90s with the big consumer electronics product development,single-chip technology is a huge improvement.INTEL i960 series with subsequent ARM in particular ,a broad range of application,quickly replaced by 32-bit single-chip 16-bit single-chip performance has been the rapid increase in processing power compared to the 80s to raise a few hundred times.At present,the high-end 32-bit single-chip frequency over 300MHz,the performance of the mid-90s close on the heels of a special processor,while the ordinary price of the model dropped to one U.S dollars,the most high-end models,only 10 U.S dollars.Contemporary single-chip microcomputer system is no longer only the bare-metal environment in the development and use of a large number of dedicated embedded operating system is widely used in the full range of single-chip microcomputer.In PDAs and cellphones as the coreprocessing of high-end single-chip or even a dedicated direct access to Windows and Linux operating systems.More than a dedicated single-chip processor suitable for embedded systems,so it was up to the application.In fact the number of single-chip is the worlds largest computer.Modern human life used in almost every piece of electronic and mechanical products will have a single-chip integration.Phone,telephone,calculator,home applicances,electronic toys,handheld computers and computer accessories such as a mouse in the Department are equipped with 1-2 single chip.And personal computers also have a large number of single-chip microcomputer in the workplace.Vehicles equipped with more than 40 Department of the general single-chip ,complex industrial control systems and even single-chip may have hundreds of work at the same time!SCM is not only far exceeds the number of PC and other integrated computing,even more than the number of human beings.2.single-chip introducedSingle-chip,also known as single-chip microcontroller,it is not the completion of a logic function of the chip,but a computer system integrated into a chip.Speaking in general terms: a single chip has become a computer .Its small size,light weight,cheap,for the learning,application and development of facilities provided .At the same time,learning to use the principle of single-chip computer to understand and structure the best choice.Single-chip and computer use is also similar to the module,such as CPU,memory,parallel bus, as well as the role and the same hard memory,is it different from the performance of these components are relatively weak in our home computer a lot,but the price is low ,there is generally no more than 10yuan,,can use it to make some control for a class of electrical work is not very complex is sufficient.We are using automatic drum washing machines, smoke hood,VCD and so on inside the home appliances can see its shadow! It is mainly as part of the core components of the control.It is an online real-time control computer,control-line is at the scene,we need to have a stronger anti-interference ability,low cost,and this is off-line computer(such as home PC)The main difference.By single-chip process,and can be amended.Through different procedures to achieve different functions,in particular the special unique features,this is the need to charge other devices can do a great effort,some of it is also difficult to make great efforts to do so .A function is not very complicated fi the United States the development of the 50s series of 74 or 60 during the CD4000series to get these pure hardware,the circuit must be a big PCB board !However,if the United States if the successful 70s seriesof single-chip market ,the result will be different!Simply because the adoption of single-chip preparation process you can achieve high intelligence,high efficiency and high reliability!Because of cost of single-chip is sensitive,so the dominant software or the lowest level assembly language,which is in addition to the lowest level for more than binary machine code of the language ,since such a low-level so why should we use ?Many of the seniors language has reached a level of visual programming why is it not in use ?The reason is simple ,that is,single-chip computer as there is no home of CPU,also not as hard as the mass storage device.A visualization of small high-level language program,even if there is only one button which will reach the size of dozens of K! For the home PCs hard drive is nothing,but in terms of the single-chip microcomputer is unacceptable.Single-chip in the utilization of hardware resources have to do very high ,so the compilation of the original while still in heavy use .The same token ,if the computer giants operating system and appplications run up to get the home PC,homePCcan not afford to sustain the same.It can be said that the twentieth century across the three “power”of the times,that is ,the electrical era,the electronic age and has now entered the computer age. However ,such a computer,usually refers to a personal computer,or PC.It consisits of the host ,keyboards,displays .And other components.There is also a type of computer,not how most people are familiar with . This computer is smart to give a variety of mechanical single-chip(also known as micro-controller).As the name suggests,these computer systems use only the minimum of an integrated circuit to make a simple calculation and control. Because of its small size,are usually charged with possession of machine in the “belly”in. It in the device,like the human mind plays a role, it is wrong,the entire device was paralyzed .Now,this single chip has a very wide field of use,such as smart meters,real-time industrial control,communications equipment,navigation systems,and household appliances. Once a variety of products with the use of the single-chip ,will be able to play so that the effectiveness of product upgrading,product names often adjective before the word “intelligent”,such as was hing machines and so intelligent.At present,some technical personnel of factories or other amateur electrtonics developers from engaging in certain products ,not the circuit is too complex ,that is functional and easy to be too simple imitation.The reason may be the product not on the cards or the use of single-chip programmable logic device on the other.3.single-chip historysingle-chip 70 was born in the late 20th century,experienced a SCM,MCU,SOC three stages.Single-chip micro-computer 1.SCM that(Single Chip Microcomputer)stage,is mainly a single from to find the best of the best embedded systems architecture.”Innovation model”to be successful,lay the SCM with the general-purpose computers,a completely different path of development . In embedded systems to create an independent development path,Intel Corporation credit.That is 2.MCU microcontroller(Micro Controller Unit)stage,the main direction of technology development: expanding to meet the embedded applications,the target system requirements for the various peripheral circuits and interface circuits,to highlingt the target of intelligent control.It covers all areas related with the objectSystem,therefore,the development of MCU inevitably fall on the heavy electrical,electronics manufacturers. From this point of view ,Intels development gradually MCU has its objective factors.MCU in the development ,the most famous manufacturers when the number of Philips Corporation.Philips in embedded applications for its enormous advantages,the MCS-51 from the rapid deveploment of single-chip micro-computer to the microcontroller.Therefore,when we look back at the path of development of embedded systems,Intel and Philips do not forget the historical merits.3.Single-chip is an independent embedded systems development,to the MCU an important factor in the development stage,is seeking applications to maximize the natural trend .With the mico-electronics technology,IC design,EDA tools development,based on the single-chip SOC design application systems will have greater development. Therefore,the understanding of single-chip micro-computer from a single ,monolithic single-chip microcontroller extends to applications.4.Single-chip applicationsAt present,single-chip microcomputer to infiltrate all areas of our lives,which is very difficult to find the area of almost no traces of single-chip microcomputer.Missile navigation equipment,aircraft control on a variety of instruments,compuer network communications and data transmission,industrial automation,real-time process control and data processing ,are widely used in a variety of smart IC card,limousine civilian security systems,video recorders,cameras,the control of automatic washing machines,as well as program-controllde toys,electronic pet,etc,which are inseparable from the single-chip microcomputer.Not to mention the field of robot automation ,intelligent instrumentation,medical equipment has been. Therefore,the single- chip learning ,development and application to a large number of computer applications and intelligent control of scientists,engineers.Single-chip widely used in instruments and meters,household appliances,medical equipment ,acrospace,specialized equipment and the intellingent management in areas such as process control,generally can be divided into the following areas:1.In the smart application of instrumentationSingle-chip with small size,low power consumption,control,and expansion flexibility , miniaturization and ease of sensors,can be realized,suchvoltage,power,frequency,humidity,temperature,flow,speed,thickness,angle,length,hardness,elemen t,measurement of physical pressure. SCM makes use of digital instrumentation,intelligence,miniaturization and functional than the use of electronic or digital circuitry even stronger.For example,precision measurement equipment(power meter,oscilloscope,and analyzer).2.In the industrial controlMCU can constitute a variety of control systems,data acquisition system.Such as factory assembly line of intelligent management ,intelligent control of the lift ,all kinds of alarm systems ,and computer networks constitute a secondary control system.3.In the applicationof household appliancesIt can be said that almost all home appliances are using the single-chip control,electric rice from favorable,washing machines,refrigerators,air conditioners,color TV and other audio video equipment,and then to the electronic weighing equipment,all kinds ,everywhere.4.On computer networks and communication applications in the field ofGenerally with the modern single-chip communication interface,can be easily carried out with computer carried out with computer data communications,computer networks and in inter-application communications equipment to provide an excellent material conditions,the communications equipment to provide an excellent material condition,from the mobile phone ,telephone , mini-program-controlled switchboards,buiding automated communications system call,the train wireless communications,and then you can see day-to-day work of mobile phones,Mobile communications,such as radios.5.Single-chip in the field of medical equipment applicationsSingle-chip microcomputer in medical devices have a wide range of purpose,such as medical ventilator,various analyzers,monitors,ultrasonic diagnostic equipment and hospital call systems.6.In a variety of large-scale electrical applications of modularSome special single-chip design to achieve a specific function to carry out a variety of modular circuitapplications,without requiring users to understand its internal structure.Integrated single-chip microcomputer such as music ,which seems to be simpleFunctions,a miniature electronic chip in a pure(as distinct from the principle of tape machine),would require a complex similar to the principle of the computer. Such as :music signal to digital form stored in memory(similar to ROM),read out by the microcontroller into analog music signal(similar to the sound card).In large circuits,modular applications that greatly reduces the size ,simplifying the circuit and reduce the damage,error rate ,but also to facilitate the replacement.In addition,single-chip microcomputer in the industrial,commercial,financial,scientific research ,education,defense aerospace and other fields have a wide range of uses.单片机1.单片机定义单片机是一种集成在电路芯片上的完整计算机系统。
电气 自动化 外文翻译 外文文献 英文文献

外文出处:Farhadi, A. (2008). Modeling, simulation, and reduction of conducted electromagnetic interference due to a pwm buck type switching power supply. Harmonics and Quality of Power, 2008. ICHQP 2008. 13th International Conference on, 1 - 6.Modeling, Simulation, and Reduction of Conducted Electromagnetic Interference Due to a PWM Buck Type Switching Power Supply IA. FarhadiAbstract:Undesired generation of radiated or conducted energy in electrical systems is called Electromagnetic Interference (EMI). High speed switching frequency in power electronics converters especially in switching power supplies improves efficiency but leads to EMI. Different kind of conducted interference, EMI regulations and conducted EMI measurement are introduced in this paper. Compliancy with national or international regulation is called Electromagnetic Compatibility (EMC). Power electronic systems producers must regard EMC. Modeling and simulation is the first step of EMC evaluation. EMI simulation results due to a PWM Buck type switching power supply are presented in this paper. To improve EMC, some techniques are introduced and their effectiveness proved by simulation.Index Terms:Conducted, EMC, EMI, LISN, Switching SupplyI. INTRODUCTIONFAST semiconductors make it possible to have high speed and high frequency switching in power electronics []1. High speed switching causes weight and volume reduction of equipment, but some unwanted effects such as radio frequency interference appeared []2. Compliance with electromagnetic compatibility (EMC) regulations is necessary for producers to present their products to the markets. It is important to take EMC aspects already in design phase []3. Modeling and simulation is the most effective tool to analyze EMC consideration before developing the products. A lot of the previous studies concerned the low frequency analysis of power electronics components []4[]5. Different types of power electronics converters are capable to be considered as source of EMI. They could propagate the EMI in both radiated and conducted forms. Line Impedance Stabilization Network (LISN) is required for measurement and calculation of conducted interference level []6. Interference spectrum at the output of LISN is introduced as the EMC evaluation criterion []7[]8. National or international regulations are the references forthe evaluation of equipment in point of view of EMC []7[]8.II. SOURCE, PATH AND VICTIM OF EMIUndesired voltage or current is called interference and their cause is called interference source. In this paper a high-speed switching power supply is the source of interference.Interference propagated by radiation in area around of an interference source or by conduction through common cabling or wiring connections. In this study conducted emission is considered only. Equipment such as computers, receivers, amplifiers, industrial controllers, etc that are exposed to interference corruption are called victims. The common connections of elements, source lines and cabling provide paths for conducted noise or interference. Electromagnetic conducted interference has two components as differential mode and common mode []9.A. Differential mode conducted interferenceThis mode is related to the noise that is imposed between different lines of a test circuit by a noise source. Related current path is shown in Fig. 1 []9. The interference source, path impedances, differential mode current and load impedance are also shown in Fig. 1.B. Common mode conducted interferenceCommon mode noise or interference could appear and impose between the lines, cables or connections and common ground. Any leakage current between load and common ground couldbe modeled by interference voltage source.Fig. 2 demonstrates the common mode interference source, common mode currents Iandcm1 and the related current paths[]9.The power electronics converters perform as noise source Icm2between lines of the supply network. In this study differential mode of conducted interference is particularly important and discussion will be continued considering this mode only.III. ELECTROMAGNETIC COMPATIBILITY REGULATIONS Application of electrical equipment especially static power electronic converters in different equipment is increasing more and more. As mentioned before, power electronics converters are considered as an important source of electromagnetic interference and have corrupting effects on the electric networks []2. High level of pollution resulting from various disturbances reduces the quality of power in electric networks. On the other side some residential, commercial and especially medical consumers are so sensitive to power system disturbances including voltage and frequency variations. The best solution to reduce corruption and improve power quality is complying national or international EMC regulations. CISPR, IEC, FCC and VDE are among the most famous organizations from Europe, USA and Germany who are responsible for determining and publishing the most important EMC regulations. IEC and VDE requirement and limitations on conducted emission are shown in Fig. 3 and Fig. 4 []7[]9.For different groups of consumers different classes of regulations could be complied. Class Afor common consumers and class B with more hard limitations for special consumers are separated in Fig. 3 and Fig. 4. Frequency range of limitation is different for IEC and VDE that are 150 kHz up to 30 MHz and 10 kHz up to 30 MHz respectively. Compliance of regulations is evaluated by comparison of measured or calculated conducted interference level in the mentioned frequency range with the stated requirements in regulations. In united European community compliance of regulation is mandatory and products must have certified label to show covering of requirements []8.IV. ELECTROMAGNETIC CONDUCTED INTERFERENCE MEASUREMENTA. Line Impedance Stabilization Network (LISN)1-Providing a low impedance path to transfer power from source to power electronics converter and load.2-Providing a low impedance path from interference source, here power electronics converter, to measurement port.Variation of LISN impedance versus frequency with the mentioned topology is presented inFig. 7. LISN has stabilized impedance in the range of conducted EMI measurement []7.Variation of level of signal at the output of LISN versus frequency is the spectrum of interference. The electromagnetic compatibility of a system can be evaluated by comparison of its interference spectrum with the standard limitations. The level of signal at the output of LISN in frequency range 10 kHz up to 30 MHz or 150 kHz up to 30 MHz is criterion of compatibility and should be under the standard limitations. In practical situations, the LISN output is connected to a spectrum analyzer and interference measurement is carried out. But for modeling and simulation purposes, the LISN output spectrum is calculated using appropriate software.基于压降型PWM开关电源的建模、仿真和减少传导性电磁干扰摘要:电子设备之中杂乱的辐射或者能量叫做电磁干扰(EMI)。
电气自动化 中英文对照 外文翻译 毕业论文

外文翻译Linear Matrix Inequality-Based Fuzzy Control for Interior Permanent Magnet Synchronous Motor with integral sliding mode controlFaGuang Wang, Seung Kyu Park, Ho Kyun Ahn Department of Electrical Engineering, Changwon National University, Korea Abstract--Recently, interior permanent magnet synchronous motor (IPMSM) is widely used in various applications, such as electric vehicles and compressors. It has a high requirement in wide load variations, high speed condition, stability, providing a fast response and most important thing is that it can be applied easily and efficiently. However, the control of IPMSM is more difficult than surface permanent magnet synchronous motor (SPMSM) because its nonlinearity due to the non-zero daxis current which can be zero in SPSM but not IPMSM. In this paper, the IPMSM is controlled very efficient algorithm by using the combination of linear control and fuzzy control with linear models depending on certain operating points. The H linear matrix inequality (LMI) based integral sliding mode control is also used to ensure the robustness. The membership functions of this paper are easy to be determined and implemented easily. Index Terms--Fuzzy control, H control, integral sliding mode control, interior permanent magnet synchronous motor (IPMSM), linear matrix inequality.I. INTRODUCTIONFrom 1980s’, with the development of semiconductor, IPMSM supplied by converter source has been widely studied [1] [2]. The development of microcomputer made the vector control system of IPMSM well controlled by single chip. IPMSM possesses special features for adjustable-speed drives which distinguish it from otherclasses of ac machines, especially surface permanent magnet synchronous motor. The main criteria of high performance drives are fast and accurate speed response, quick recovery of speed from any disturbances and insensitivity to parameter variations [3]. In order to achieve high performances, the vector control of IPMSM drive is employed [4]-[6]. Control techniques become complicated due to the nonlinearities of the developed torque for non-zero value of d-axis current. Many researchers have focused their attention on forcing the daxis current equals to zero in the vector control of IPMSM drive, which essentially makes the motor model linear [4],[7]. However, in real-time the electromagnetic torque is non-linear in nature. In order to incorporate the nonlinearity in a practical IPMSM drive, acontrol technique known as maximum torque per ampere (MTPA) is devised which provides maximum torque with minimum stator current [3]. This MTPA strategy is very important from the limitation of IPMSM and inverter rating points of view, which optimizes the drive efficiency. The problem associated MTPA control technique is that its implementation in real time becomes complicated because there existsa complex relationship between d-axis and q-axis currents. Thus, oneof the main objectives of this paper is to make a new efficientcontrol method for IPMSM and its calculation easy and efficient. The LMI fuzzy H control has been applied and solved the nonlinearity of the IPMSM model to a set of linear model. To increase the robustness for disturbances, an ISMC technique is added to the H controller. By ISMC, the proposed controller gives performances of the H control system without disturbances which satisfy the matching condition. It has a good compatible with linear controllers. T-S fuzzy control [8]is based on the mathematical model which is the combination of local linear models depending on the operating points. Linear controllers are designed for each linear model and they are combined as a controller and make it possible to use linear control theories for nonlinear systems. Linear controls via parallel distributed compensation (PDC) and linear matrix inequality (LMI) is a most popular method considering the stability of the system with PDC [9].H LMI T-S fuzzy controller is considered as a practicalH controller which eliminates the effects of external disturbance below a prescribed level, so that a desired H control performancecan be guaranteed [10-12]. In this paper, the robustness of SMC [13]is added to the H LMI T-S fuzzy controller for the control of IPMSM. We can divide the disturbances in the IPMSM into two parts. Firstpart is that SMC can deal with and other part is dealt by H LMIfuzzy controller. By using ISMC, the robustness of SMC andH performance can be combined. Integral sliding mode control (ISMC) is a kind of SMC which has sliding mode dynamics with the same orderof the controlled system and can have the properties of the other control method.II. H T-S FUZZY CONTROL AND ISMCA. H T-S fuzzy controlConsider a nonlinear system as follows.x(t)=f (x)+g(x)u(t)+w(t) (1)where ||w(t)||≤Wb and Wb is the boundary of disturbance. Dependingon the operating points, the nonlinear system can be expressed as follows.The i-th model is that in the case z1(t) is Mi1 and …and z p(t) isMip ,(2)And H T-S fuzzy feedback controller is ui= -kiX(t) (3)where i=1,2, … ,r and Mij is the fuzzy set and r is the number of model rulesGiven a pair of (x(t),u(t)), the fuzzy systems are inferred as follows:where and μi(z(t)) is themembership for every fuzzy rule.From (1) we get(7)Take (6) into (7), we can get the closed loop systemequations.If we set A present the error boundary of every ruleand satisfy the following condition:In the same way we get:(9)Based on these, the approximation error can bebounded by matrix Ap and Bp . H control performance is:(10)where is the prescribed H norm. If we get theminimized for(10) we can make the effect of w(t) of (1) on x(t) is minimized.If consider the initial condition, the H norm (10) canbe modified as the following form:where P is some symmetric positive definite weighting matrix.The following result is given in [14]:Theorem 1: If system (1) is controlled by T-S fuzzy controller (6), and there is a positive definite matrix P such that(12)then the closed loop system is uniformly ultimately bounded (UUB) and H control performance (11) is guaranteed.It is not easy to obtain P and, fortunately, after small change of (12), it can be solved by LMI toolbox. So we need to do some changes.Assume Utilize the Schur complements for (12), we can get:(13)whereNow the problem changes to find the positive definite matrix L and F to satisfy the condition (13) and we can obtain k j at last. The (13) can be solved by LMI toolbox on computer easily.B. Sliding mode controlThe system (1) with input signal noise or disturbance d(t) is:(14)In the system (14), it can be considered that the disturbance is the summation of two different kinds of disturbancesw(t)=w1(t)+w2(t) (15)where w1(t) satisfies the following matching condition:(16)For the disturbance w1(t) , ISMC gives the desired response of the following system:(17)where x0 represents the state trajectory of the system with the disturbance w2(t) only under H T-S fuzzy control uo . Assume thatw(t) is bounded and that an upper bound can be found as(18)where wmax is a known positive scalar.For system (14), first redesign the control law to beu(t)=u0(t)+u1(t) (19)where is the ideal control defined in (6) and is designed to reject the perturbation term w1(t) .A sliding manifold is defined ass=s0 (x)+z(x) (20)where s,s0 (x), , which consists of two parts: the first part s0(x)is designed as a linear combination of the system states; the second part z introduces the integral term and will be determined below.(21)where initial condition z(0) is determined based on the requirements(0)=0. Different from the conventional design approach, the order of the motion equation in ISMC is equal to the order of the original system, rather than reduced by the dimension of the control input. As a result, robustness of the system can be guaranteed starting from the initial time instance.III. COMBINATION H T-S FUZZY CONTROL ANDINTEGRAL SMCThe mathematic model of an IPMSM in the d-q synchronously rotating reference frame for assumed sinusoidal stator excitation is given as [3]:(22)where p is the differential operator.The overall scheme of the H LMI T-S fuzzy control system is as follows.H LMI T-S fuzzy based ISMC controller designed as following steps. Step.1. utilize the equilibrium point to calculate the error system. System (22) can be presented by state form as:(23)where x1(t) =iq , x2(t) =id , x3(t) =wr ,u10(t) =vq andu20(t) =vd .Based on (23), a reference system can be given as:(24)where f means the required value.Then the following error dynamic system is derived.(25)where e(t)=x(t)-xf (t)Step.2. determine for membership function.For x1 minimum case:For x1 maximum case:For x2 minimum case:For x2 maximum case:The fuzzy rules are as the follows:Rule.1 x1 is minimal and x2 is minimal:M1(t) =E1(t)G1(t) (26)Rule.2 x1 is minimal and x2 is maximal:M2(t) =E1(t)G2(t) (27)Rule.3 x1 is maximal and x2 is minimal:M3(t) =E2(t)G1(t) (28)Rule.4 x1 is maximal and x2 is maximal:M4(t) =E2(t)G2(t) (29)Step.3. obtain the matrixes A and B.Equation (25) can be of the following form:and the value of ( x1lim , x2lim )is based on the rule1 to rule 4, it gets to be x1min,x1max,x2min and x2max .Step.4. calculate controller parameters K using LMI toolbox based on Theorem 1.By LMI, the error systemcontrol input is defined by (6) as(31)where k j is a 1by 3 matrix. Use inequality (13) and Matlab LMI toolbox to calculate out the parameters k j . So that, H T-S fuzzycontroller of the system is where u1 f and u2 fare reference inputs.Step.5. Design ISMC for system.Based on the SMC matching condition the system with disturbance is asfollows: (32)where d(t) is the noise or disturbance.The sliding surface is defined as:(33)x1r and x2r are required output values, x1n and x2n are states of nominalsystem: (34)Assume u1(t)=u10(t)+u1s(t) and u2(t)=u20(t)+u2s(t) .Derivate of slidingsurfaces are:(35)where e1n(t)=x1(t)x1n(t) , e2n(t)=x2(t)x2n(t) , un(t) is the nominalcontrol input and us1 and us2 are sliding control inputs.The sliding controller finally is given out as:(36)where d1max and d1max are the maximal absolute values of disturbance.IV. SIMULATION RESULTSUse the controller design process in above sections with the parameters of Tab.1. Simulation results are:TAB.1. IPMSM PARAMETERS.Fig.2. result of iq with parameter uncertainty and disturbance.Fig.3.result of id with parameter uncertainty and disturbance.Required output values are From the result of Fig.2and Fig.3, we can see that some kind of disturbance can not be solved only by H LMI T-S fuzzy. Combination with ISMC solves this perfectively.V. CONCLUSIONSThe Fuzzy LMI controller is used for IPMSM. It uses the linear models for each operating points. It is shown that only four operating points are enough for the proposed control method. The controller of this paper gives good control performance with only four membership functions which are determined easily. H fuzzy LMI solved theinitial big input for IPMSM from ISMC, while ISMC solved the problem of H fuzzy which is so dependent on fuzzy rules. The final results show that the combination control is efficient and perfect.具有积分滑模控制的内埋式永磁同步电动机基于线性矩阵不等式的模糊控制王发光, Seung Kyu Park, Ho Kyun Ahn韩国昌原国立大学电机工程学系近期摘要,内埋式永磁同步电动机被广泛的用于各种各样的应用中,例如电动汽车和压缩机。
3-电气工程及其自动化专业 外文文献 英文文献 外文翻译

3-电气工程及其自动化专业外文文献英文文献外文翻译1、外文原文(复印件)A: Fundamentals of Single-chip MicrocomputerThe single-chip microcomputer is the culmination of both the development of the digital computer and the integrated circuit arguably the tow most significant inventions of the 20th century [1].These tow types of architecture are found in single-chip microcomputer. Some employ the split program/data memory of the Harvard architecture, shown in Fig.3-5A-1, others follow the philosophy, widely adapted for general-purpose computers and microprocessors, of making no logical distinction between program and data memory as in the Princeton architecture, shown in Fig.3-5A-2.In general terms a single-chip microcomputer is characterized by the incorporation of all the units of a computer into a single device, as shown in Fig3-5A-3.ProgramInput& memoryOutputCPU unitDatamemoryFig.3-5A-1 A Harvard typeInput&Output CPU memoryunitFig.3-5A-2. A conventional Princeton computerExternal Timer/ System Timing Counter clock componentsSerial I/OReset ROMPrarallelI/OInterrupts RAMCPUPowerFig3-5A-3. Principal features of a microcomputerRead only memory (ROM).ROM is usually for the permanent,non-volatile storage of an applications program .Many microcomputers and microcontrollers are intended for high-volume applications and hence the economical manufacture of the devices requires that the contents of the program memory be committed permanently during the manufacture of chips . Clearly, this implies a rigorous approach to ROM code development since changes cannot be made after manufacture .This development process may involve emulation using a sophisticated development system with a hardware emulation capability as well as the use of powerful software tools.Some manufacturers provide additional ROM options by including in their range devices with (or intended for use with) user programmablememory. The simplest of these is usually device which can operate in a microprocessor mode by using some of the input/output lines as an address and data bus for accessing external memory. This type of device can behave functionally as the single chip microcomputer from which itis derived albeit with restricted I/O and a modified external circuit. The use of these ROMlessdevices is common even in production circuits where the volume does not justify the development costs of custom on-chip ROM[2];there canstill be a significant saving in I/O and other chips compared to a conventional microprocessor based circuit. More exact replacement for ROM devices can be obtained in the form of variants with 'piggy-back' EPROM(Erasable programmable ROM )sockets or devices with EPROM instead of ROM 。
电气工程及其自动化 外文翻译 外文文献 英文文献 短路电流
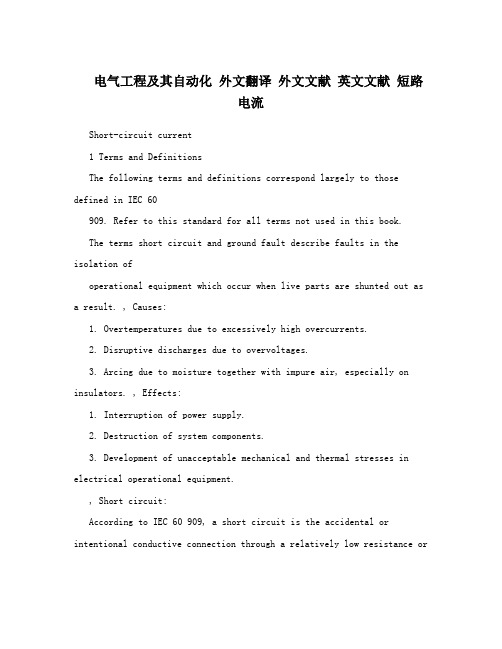
电气工程及其自动化外文翻译外文文献英文文献短路电流Short-circuit current1 Terms and DefinitionsThe following terms and definitions correspond largely to those defined in IEC 60909. Refer to this standard for all terms not used in this book.The terms short circuit and ground fault describe faults in the isolation ofoperational equipment which occur when live parts are shunted out asa result. , Causes:1. Overtemperatures due to excessively high overcurrents.2. Disruptive discharges due to overvoltages.3. Arcing due to moisture together with impure air, especially on insulators. , Effects:1. Interruption of power supply.2. Destruction of system components.3. Development of unacceptable mechanical and thermal stresses in electrical operational equipment., Short circuit:According to IEC 60 909, a short circuit is the accidental or intentional conductive connection through a relatively low resistance orimpedance between two or more points of a circuit which are normally at different potentials., Short circuit current:According to IEC 60 909, a short circuit current results from a short circuit in an electrical network.It is necessary to differentiate here between the short circuit current at the position of the short circuit and the transferred short circuit currents in the network branches., Initial symmetrical short circuit current:This is the effective value of the symmetrical short circuit current at the moment at which the short circuit arises, when the short circuit impedance has its value from the time zero., Initial symmetrical short circuit apparent power:The short circuit power represents a fictitious parameter. During the planning of networks, the short circuit power is a suitable characteristic number. , Peak short circuit current:The largest possible momentary value of the short circuit occurring. , Steady state short circuit current:Effective value of the initial symmetrical short circuit current remaining after the decay of all transient phenomena., DC aperiodic component:Average value of the upper and lower envelope curve of the short circuit current, which slowly decays to zero., Symmetrical breaking current:Effective value of the short circuit current which flows through the contact switch at the time of the first contact separation., Equivalent voltage source:The voltage at the position of the short circuit, which is transferred to the positive-sequence system as the only effective voltage and is used for the calculation of the short circuit currents., Superposition method:The superposition method considers the previous load of the network before the occurrence of the short circuit. It is necessary to know the load flow and the setting of the transformer step switch., Voltage factor:Ratio between the equivalent voltage source and the network voltage Un,divided by 3., Equivalent electrical circuit:Model for the description of the network by an equivalent circuit. , Far-from-generator short circuit:The value of the symmetrical AC periodic component remains essentially constant., Near-to-generator short circuit:The value of the symmetrical AC periodic component does not remain constant. The synchronous machine first delivers an initial symmetrical short circuit current which is larger than twice the rated current of the synchronous machine. , Positive-sequence short circuit impedance:The impedance of the positive-sequence system as seen from the position of theshort circuit., Negative-sequence short circuit impedance:The impedance of the negative-sequence system as seen from the position ofthe short circuit., Zero-sequence short circuit impedanceThe impedance of the zero-sequence system as seen from the position of theshort circuit. Three times the value of the neutral point to ground impedanceoccurs here., Short circuit impedance:Impedance required for calculation of the short circuit currents at the positionof the short circuit. p•••1.2 Short circuit path in the positive-sequence systemFor the same external conductor voltages, a three-pole short circuit allows three currents of the same magnitude to develop between the three conductors. It is therefor only necessary to consider one conductor in further calculations. Depending on the distance from the position of the short circuit from the generator, here it is necessary to consider near-to-generator andfar-from-generator short circuits separately. For far-from-generator and near-to-generator short circuits, the short circuit path can be represented by a mesh diagram with AC voltage source, reactances X and resistances R (Figure 1.2). Here, X and R replace all components such as cables,conductors, transformers, generators and motors.Fig. 1.2: Equivalent circuit of the short circuit current path in the positive-sequence systemThe following differential equation can be used to describe theshort circuit processwhere w is the phase angle at the point in time of the short circuit. This assume that the current before S closes (short circuit) is zero. The inhomogeneous first order differential equation can be solved by determining the homogeneous solution ik and a particular solution i?k.The homogeneous solution, with the time constant g = L/R, solution yields:For the particular solution, we obtain:The total short circuit current is composed of both components:The phase angle of the short circuit current (short circuit angle)is then, in accordance with the above equation,For the far-from-generator short circuit, the short circuit current is therefore made up of a constant AC periodic component and the decaying DC aperiodic component. From the simplified calculations, we can now reach the following conclusions:, The short circuit current always has a decaying DC aperiodic component inaddition to the stationary AC periodic component., The magnitude of the short circuit current depends on theoperating angle ofthe current. It reaches a maximum at c = 90 (purely inductive load). Thiscase serves as the basis for further calculations., .The short circuit current is always inductive.1.4 Methods of short circuit calculationThe equivalent voltage source will be introduced here as the only effective voltage of the generators or network inputs for thecalculation of short circuit currents. The internal voltages of generators or network inputs are short circuited, and at the position ofthe short circuit (fault position) the value ( is used as the only effective voltage (Figure 1.4)., The voltage factor c [5] considers (Table 1.1):, The different voltage values, depending on time and position, The step changes of the transformer switch, That the loads and capacitances in the calculation of the equivalentvoltage source can be neglected, The subtransient behavior of generators and motors, This method assumes the following conditions:, The passive loads and conductor capacitances can be neglected , The step setting of the transformers do not have to be considered , The excitation of the generators do not have to be considered , The time and position dependence of the previous load (loading state) ofthe network does not have to be consideredFig. 1.4: Network circuit with equivalent voltage sourcea) three-phase network, b) equivalent circuit in positive sequencesystem1.4.2 Superposition methodThe superposition method is an exact method for the calculation of the short circuit currents. The method consists of three steps. The voltage ratios and the loading condition of the network must be known before the occurrence of the short circuit. In the first step the currents, voltages and the internal voltages for steady-state operation before onset of the short circuit are calculated (Figure 1.5b). The calculation considers the impedances, power supply feeders and node loads of the active elements. In the second step the voltage applied to the fault location before the occurrence of the short circuit and the current distribution at the fault location are determined with a negative sign (Figure 1.5c). This voltage source is the only voltage source in the network. The internal voltages are short-circuited. In the third step both conditions are superimposed. We then obtain zero voltage at the fault location. The superposition of the currents also leads to the value zero. The disadvantage of this method is that the steady-state condition must be specified. The data for the network (effective andreactive power, node voltages and the step settings of the transformers) are often difficult to determine. The question also arises, which operating state leads to the greatest short circuit current. Figure 1.5 illustrates the procedure for the superposition method.Fig. 1.5: Principle of the superposition methoda) undisturbed operation, b) operating voltage at the faultlocation, c) superposition of a) and b)1.4.3 Transient calculationWith the transient method the individual operating equipment and, as a result, the entire network are represented by a system of differential equations. The calculation is very tedious. The method with the equivalent voltage source is a simplification relative to the other methods. Since 1988, it has been standardized internationally in IEC 60 909. The calculation is independent of a current operational state. Inthisbook, we will therefore deal with and discuss the method with the equivalent voltage source.1.5 Calculating with reference variablesThere are several methods for performing short circuit calculations with absolute and reference impedance values. A few are summarized here and examples are calculated for comparison. To define the relative values, there are two possible reference variables.For the characterization of electrotechnical relationships we require the four parameters:, Voltage U in V, Current I in A, Impedance Z in W, Apparent power S in VA.Three methods can be used to calculate the short circuit current:1. The Ohm system: Units: kV, kA, V, MVA2.The pu system:This method is used predominantly for electrical machines; allfour parameters u, i, z and s are given as per unit (unit = 1). The reference valueis 100 MVA. The two reference variables for this system are UB and SB.Example: The reactances of a synchronous machine Xd, X?d, X?d are givenin pu or in % pu, multiplied by 100 %.3.The %/MVA system:This system is especially well suited for thefastdetermination of short circuit impedances. As formal unit only the % symbol isadd.短路电流1 术语和定义以下术语和定义对应IEC 标准60 909。
电气工程及其自动化电压波动论文中英文资料外文翻译文献

中英文资料外文翻译文献原文:A SPECIAL PROTECTION SCHEME FOR VOLTAGESTABILITY PREVENTIONAbstractVoltage instability is closely related to the maximum load-ability of a transmission network. The energy flows on the transmission system depend on the network topology, generation and loads, and on the availability of sources that can generate reactive power. One of the methods used for this purpose is the Voltage Instability Predictor (VIP). This relay measures voltages at a substation bus and currents in the circuit connected to the bus. From these measurements, it estimates the Thévenin’s equivalent of the network feeding the substation and the impedance of the load being supplied from the substation. This paper describes an extension to the VIP technique in which measurements from adjoining system buses and anticipated change of load are taken into consideration as well.Keywords: Maximum load ability; Voltage instability; VIP algorithm.1.IntroductionDeregulation has forced electric utilities to make better use of the available transmission facilities of their power system. This has resulted in increased power transfers, reduced transmission margins and diminished voltage security margins.To operate a power system with an adequate security margin, it is essential to estimate the maximum permissible loading of the system using information about the current operation point. The maximum loading of a system is not a fixed quantity but depends on various factors, such as network topology, availability of reactive power reserves and their location etc. Determining the maximum permissible loading, within the voltage stability limit, has become a very important issue in power system operation and planning studies. The conventional P-V or V- Q curves are usually used as a tool for assessing voltage stability and hence for finding the maximum loading at the verge of voltage collapse [1]. These curves are generated by running a large number of load flow cases using, conventional methods. While such procedures can be automated, they are time-consuming and do not readily provide information useful in gaining insight into the cause of stability problems [2].To overcome the above disadvantages several techniques have been proposed in the literature, such as bifurication theory [3], energy method [4], eigen value method [5],multiple load flow solutions method [6] etc.Reference [7] proposed a simple method, which does not require off-line simulation and training. The Voltage Indicator Predictor (VIP) method in [7] is based on local measurements (voltage and current) and produces an estimate of the strength / weakness of the transmission system connected to the bus, and compares it with the local demand. The closer the local demand is to the estimated transmission capacity, the more imminent is the voltage instability. The main disadvantage of this method is in the estimation of the Thévenin’s equivalent, which is obtained from two measurements at different times. For a more exact estimation, one requires two different load measurements.This paper proposes an algorithm to improve the robustness of the VIP algorithm by including additional measurements from surrounding load buses and also taking into consideration local load changes at neighboring buses.2. Proposed MethodologyThe VIP algorithm proposed in this paper uses voltage and current measurements on the load buses and assumes that the impedance of interconnecting lines (12Z ,13Z ) are known, as shown in (Figure 1). The current flowing from the generator bus to the load bus is used to estimate Thévenin’s equivalent for the system in that direction. Similarly the current flowing from other load bus (Figure 2) is used to estimate Thévenin’s equivalent from other direction. This results in following equations (Figure 3). Note that the current coming from the second load bus over the transmission line was kept out of estimation in original (VIP) algorithm.)()()(111112211111----=-+th th th L Z E Z V Z Z V [1] )()()(122112112122----=-+th th th L Z E Z V Z Z V [2] 1111111)()(E th th th I Z V Z E =--- [3] 2122122)()(E th th th I Z V Z E =--- [4] Where 1E I and 2E I are currents coming from Th évenin buses no.1 and 2. Equation (1)-(4) can be combined into a matrix form:⎥⎥⎥⎥⎥⎦⎤⎢⎢⎢⎢⎢⎣⎡---++---++-------------121211111212112121-12111121111211000000th th th th th th L th th L Z Z Z Z Z Z Z Z Z Z Z Z Z Z *=⎥⎥⎥⎥⎦⎤⎢⎢⎢⎢⎣⎡2121th th E E V V ⎥⎥⎥⎥⎦⎤⎢⎢⎢⎢⎣⎡2100E E I I [5] Using the first 2 rows in the system Equations (1)-(4), the voltage on buses number 1 and 2 can be found as shown in Equation (6) below. From Equation (6) wecan see that the voltage is a function of impedances. Note that the method assumes that all Thévenin’s parameters are constant at the time of estimation.⎥⎥⎦⎤⎢⎢⎣⎡⎥⎥⎦⎤⎢⎢⎣⎡++--++=⎥⎦⎤⎢⎣⎡-----------12211111121212112112112111121*th th th th th L th L Z E Z E Z Z Z Z Z Z Z Z V V [6] Where, 111-=L Z y 11212-=Z y and 122-=L Z yThe system equivalent seen from bus no.1 is shown in Figure 3. Figure 4(a) shows the relationship between load admittances (1y and 2y ) and voltage at bus no.1. Power delivered to bus no.1 is (1S ) and it is a function of (1L Z ,2L Z ).1211*L y V S = [7]Equation 7 is plotted in figure 4 (b) as a ‘landscape’ and the maximum loading point depends on where the system trajectory ‘goes over the hill’.Fig. 1. 3-Bus system connections Fig. 2. 1-Bus modelFig. 3. System equivalent as seen by the proposed VIP relay on bus #1 (2-bus model)(a)Voltage Profile (b) Power ProfileFig. 4. Voltage and power profiles for bus #12.1. On-Line Tracking of Thévenin’s ParametersThévenin’s parameters are the main factors that decide the maximum loading of the load bus and hence we can detect the voltage collapse. In Figure3, th E can be expressed by the following equation:I Z V E th load th += [8]V and I are directly available from measurements at the local bus. Equation (8) can be expressed in the matrix form as shown below.⎥⎥⎥⎥⎦⎤⎢⎢⎢⎢⎣⎡--⎥⎥⎥⎥⎦⎤⎢⎢⎢⎢⎣⎡=⎥⎥⎥⎥⎦⎤⎢⎢⎢⎢⎣⎡000010000001)()(00..r i i r th th th th i r I I I I X R i E r E V V [9] B= A X [10] The unknown parameters can be estimated from the following equation:B A AX A T T = [11] Note that all of the above quantities are functions of time and are calculated on a sliding window of discrete data samples of finite, preferably short length. There are additional requirements to make the estimation feasible:• There must be a significant change in load impedance in the data window of at least two set of Measurements.• For small changes in Thévenin’s parameters within a particular data window, the algorithm can estimate properly but if a sudden large change occurs then the process of estimation is postponed until the next data window comes in.• The monitoring device based on the above principle can be used to impose a limit on the loading at each bus, and sheds load when the limit is exceeded. It can also be used to enhance existing voltage controllers. Coordinated control canalso be obtained if communication is available.Once we have the time sequence of voltage and current we can estimate unknowns by using parameter estimation algorithms, such as Ka lm an Filtering approach described [6].stability margin (VSM) due to impedances can be expressed as (Z VSM ); where subscript z denotes the impedance.Therefore we have: Load thev Load Z Z Z Z VSM -= [12] The above equation assumes that both load impedances (1Z , 2Z ) are decreasing at a steady rate, so the power delivered to bus 1 will increase according to Equation(7). However once it reaches the point of collapse power starts to decrease again.Now assume that both loads are functions of time. The maximum critical loading point is then given by Equation(13):011==dtds S Critical [13] Expressing voltage stability margin due to load apparent power as ( S VSM ), we have:Critical Load Critical S SS S VSM -= [14] Note that both Z VSM and S VSM are normalized quantities and their values decrease as the load increases.At the voltage collapse point, both the margins reduce to zero and the corresponding load is considered as the maximum permissible loading.Fig. 5. VIP algorithm2.2. Voltage Stability Margins and the Maximum Permissible LoadingSystem reaches the maximum load point when the condition: thev load Z Z =is satisfied (Figure5).Therefore the voltage stability boundary can be defined by a circlewith a radius of the Thévenin’s impedance. For normal operation the thev Z is smaller than load Z (i.e. it is outside the circle) and the system operates on the upper part (or the stable region) of a conventional P-V curve [2].However, when thev Z exceeds load Z the system operates on the lower part (or unstable region) of the P-V curve, indicating that voltage collapse has already occurred. At the maximum power point, the load impedance becomes same as the Thévenin’s (thev L Z Z ). Therefore, for a given load impedance (load Z ), the difference between thev Z and load Z can be considered as a safety margin. Hence the voltage as given in an IEEE survey, which described (111) schemes from (17) different countries [8].Fig. 6. Load actions to prevent from voltage instability2.3. Advantages of the proposed VIP algorithmBy incorporating the measurements from other load buses (Figure 3), the proposed VIP algorithm achieves a more accurate value of load Z . The on-line tracking of thev Z is used to track system changes.The proposed improvements in the VIP algorithm will result in better control action for power system voltage stability enhancement. The control measures are normally shunt reactor disconnection, shunt capacitor connection, shunt V ARcompensation by means of SVC’s and synchrouns condensers, starting of gas turbines, low priority load disconnection, and shedding of low-priority load [8]. Figure 6 shows the most commonly used remedial actions .3. ConclusionsAn improved V oltage Instability Predictor (VIP) algorithm for improving the voltage stability is proposed in this paper. The previous VIP method [7] used measurements only from the bus where the relay is connected. The new method uses measurements from other load buses as well. The voltage instability margin not only depends on the present state of the system but also on future changes.Therefore, the proposed algorithm uses an on-line tracking Thévenin’s equivalent for tracking the system trajectory. The algorithm is simple and easy to implement in a numerical relay. The information obtained by the relay can be used for load shedding activation at the bus or V AR compensation. In addition, the signal may be transmitted to the control centre,where coordinated system-wide control action can be undertaken. The algorithm is currently being investigated on an IEEE 30 bus system and results using the improved VIP algorithm will be reported in a future publication. References[1] M.H.Haque, “On line monitoring of maximum permissible loading of a power system within voltage stability limits”, IEE proc. Gener. Transms. Distrib.,V ol. 150, No. 1, PP. 107-112, January, 2003[2] V. Balamourougan, T.S. Sidhu and M.S. Sachdev, “Technique for online prediction of voltage collapse”, IEE Proc.Gener.Transm. Distrib., V ol.151, No. 4, PP. 453-460, July, 2004[3] C.A. Anizares, “On bifurcations voltage collapse and load modeling “IEEE Trans. Power System, V ol. 10, No. 1, PP. 512-522, February, 1995[4] T.J Overbye and S.J Demarco, “Improved Technique for Power System voltage stability assessment using energy methods“, IEEE Trans. Power Syst., Vol. 6, No. 4, PP. 1446-1452, November, 1991[5] P.A Smed Loof. T. Andersson, G. Hill and D.J,”Fast calculation of voltage stability index”, IEEE Trans. Power Syst. V ol. 7, No. 1, PP. 54-64, February, 1992[6] K. Ohtsuka ,” An equivalent of multi- machine power system and its identification for on-line application to decentralized stabilizers”, IEEE Trans. Power Syst., V ol. 4 No. 2, PP. 687-693, May, 1989[7] Khoi Vu, Miroslav M Begovic, Damir Novosel, Murari Mohan Saha, “ Use of local Measurements to estimate voltage –stability margin “ IEEE Trans. Power syst. Vol. 14, No. 3, PP. 1029-1035, August, 1999[8] G.V erbic and F. Gubina “Fast voltage-collapse line protection algorithm based on local phasors”, IEE Proc.Gener.Transm. Distrib., V ol. 150, No. 4, PP. 482-486, July, 2003译文:一种特殊的预防电压波动的保护方案摘要电压的波动与输电线路的最大负载能力密切相关。
电气工程与自动化外文翻译外文文献英文文献一种低成本智能式电容位置传感器

文献、资料题目: A Low-Cost, Smart Capacitive Position Sensor 文献、资料来源:IEEE TRANSACTIONS ON INSTRUMENT AND MEASUREMENT 文献、资料发表(出版)日期:1992.12 院(部):信息与电气工程学院__________________________________________专业:电气工程与自动化___________________________外文文献:A Low-Cost, Smart Capacitive Positi on Sen sorAbstractA new high-performanee, low-cost, capacitive position-measuring system is described. By using a highly linear oscillator, shielding and a three-signal approach, most of the errors are eliminated. The accuracy amounts to 1 卩m over a 1 mmcanig e .oStiput of the oscillatorcan directly be conn ected to a microc on troller, an A/D conv erter is not n eeded.I. INTRODUCTIONThis paper describes a no vel high-performa nee, low-cost, capacitive displaceme nt measuri ng system featuri ng:1 mm measuri ng ran ge,1 卩m accuracy,0.1 s total measuri ng time.Tran slated to the capacitive doma in, the specificati ons corresp ond to:a possible range of 1 pF;only 50 fF of this range is used for the displaceme nt tran sducer;50 aF absolute capacita nce-measuri ng in accuracy.Meijer and Schrier [l] and more rece ntly Van Drecht,Meijer, and De Jong [2] have proposed a displaceme nt-measuri ng system,us ing a PSD (Positi on Sen sitive Detector) as sensing eleme nt. Some disadva ntages of using a PSD are the higher costs and the higher power con sumpti on of the PSD and LED (Light-Emitting Diode) as compared to the capacitive sensor elements described in this paper.The sig nal processor uses the con cepts prese nted in [2],but is adopted for the use of capacitive elements. By the extensive use of shielding, guarding and smart A/D conversion,the system is able to combine a high accuracy with a very low cost-price. The transducer produces three-period-modulated sig nals which can be selected and directly read out by a microc on troller. The microcontroller,in return, calculates the displacement and can send this value to a host computer (Fig. 1) or a display or drive an actuator.Fig. 1. Block diagram of the systemII . THE ELECTRODE STRUCTUREThe basic sensing element consists of two simple electrodes with capacitance Cx, (Fig. 2). The smaller one (E2) is surro un ded by a guard electrode. Thanks to the use of the guard electrode, the capacita nce Cx betwee n the two electrodes is in depe ndent of moveme nts (lateral displaceme nts as well as rotati ons) parallel to the electrode surface.The in flue nce of the parasitic capacita nces Cp will be eliminated as will be discussed in Section M .According to Heerens [3], the relative deviation in the capacitance Cx between the two electrodes caused by the finite guard electrode size is smaller than:S<€冗(x/d)(1)where x is the width of the guard and d the distance between the electrodes. This deviationElectro nic CircuitHPCrefPers onal ComputerCsFI I 1 I 一 1Sli i&l rlir.f?Fig. 2. Perspective and dime nsions of the electrode structureintroduces a nonlinearity.Therefore we require that S is less than 100 ppm.Also the gap between the small electrode and the surro unding guard causes a deviati on:S <n (d/s)(2)with s the width of the gap. This deviati on is n egligible compared to (l), whe n the gap width is less than 1/3 of the distance between the electrodes.Another cause of errors originates from a possible finite skew angle a between the two electrodes (Fig. 3). Assu ming the follow ing con diti ons:the pote ntials on the small electrode and the guard electrode are equal to 0 V, the pote ntial on the large electrode is equal to V volt, the guard electrode is large eno ugh,it can be seen that the electric field will be concentric.To keep the calculations simple, we will assume the electrodes to be infinitely large in one direct ion. Now the problem is a two-dime nsio nal one that can be solved by using © ). In this case the electrical field can be described by:V sinV cos rTo calculate the charge on the small electrode, we set and in tegrat 命otveO r:with Bl the left border of the small electrode:polar-coordi nates (r,B^drB IFig. 3. Electrodes with angle . aQ V」ln 2d COS丨亦a 2d cos l sinFor small a's this can be approximated by:C 卫 1 4^ 2d 12dIt appears to be desirable to choose l smaller tha n d, so the error will depe nd only on the an glea .In our case, a change in the angle of 0.6 ° will cause an error less than 100 ppm.With a proper design the parameters £ o and l are constant,and then the capacitanee between thtwo electrodes will depe nd only on the dista nee d betwee n the electrodes.川.ELIMINATION OF PARASITIC CAPACITANCESBesides the desired sen sor capacita nee C, there are also many parasitic capacita nces in theactual structure (Fig.2). These capacitances can be modeled as shown in Fig.4. Here Cpl represe nts the parasitic capacita nces from the electrode E1 and Cp2 from the electrode E2 to the guard electrodes and the shield ing. Parasitic capacita nee Cp3 results from imperfect shield ing and forms an offset capacita nee. Whe n the tran sducer capacita nee Cx is conn ected to an AC voltage source and the current through the electrode is measured,Cpl and Cp2 will be eliminated. Cp3 can be elimi nated by perform ing an offset measureme nt.and Br the right border:Solvi ng (4) results in:B iB rdtandtan(8)Fig. 4. Elimination of parasitic capacitancesThe current is measuredby the amplifier with shunt feedback, which has a very low input impedanee. To obtain the required linearity, the unity-gain bandwidth fT of the amplifier has to satisfy the following condition:where T is the period of the in put sig nal.Since Cp2 con sists of cable capacita nces and the in put capacita nee of the op amp, it may in deed be larger tha n Cf and can not be n eglected.IV. THE CONCEPT OF THE SYSTEMThe system uses the three-sig nal con cept prese nted in [2], which is based on the follow ing principles. When we measure a capacitor Cx with a linear system, we obtain a value:Here, P is a value representing the position while a1 and aO are unknown, but stable constants.12 C f (9)C fCp2mC xMoff(10)where m is the unknown gain and Moff, the unknown offset.By perform ing the measureme nt of a refere nee qua ntity Cref, i n an ide ntical way and by measuri ng the offset, Moff,by maki ng m = 0, the parameters m and Moff are eliminated.The final measurement result P is defined as:MrefMoffM x M O ff(11)In our case, for the sen sor capacita nee C, it holds that:A x d o d(12)where Ax is the area of the electrode, do is the initial distance between them,con sta nt and A d is the displaceme nt to be measured. For the refere nce electrodes it holds that:A refC ref丁-(13)£ iswith Aref the area and dref the distance. Substitution of (12) and (13) into (10) and then into (11) yields:A ref d o dA x d refd a 1 — aodrefThe constant al =Aref/Ax is a stable constant provided there is a good mechanical matching betwee n the electrode areas.The con sta nt ao = (ArefdO/(Axdref) will also be a stable con sta nt provided that do and dref are constant. These constants can be determined by a one-time calibration. In many applications this calibration can be omitted; when the displacement sensor is part of a larger system, an overall calibrati on is required any way. This overall calibrati on elim in ates the requireme nt for a separate determ in atio n of a1 and a0.V . THE CAPACITANCE-TO-PERIOD CONVERSIONThe sig nals which are proporti onal to the capacitor values are con verted into a period, using a modified Martin oscillator [4] (Fig. 5j.When the voltage swing across the capacitor is equal to that across the resistor and the NAND gates are switched off, this oscillator has a period Toff:Toff = 4RCoff. (15) Since the value of the resistor is kept constant, the period varies only with the capacitor value. Now, by switching on the right NAND port, the capacitance CX can be connected in parallel to Coff. Then the period becomes:Tx=4R(Coff+Cx)=4RCx+Toff (16) The constants R and Toff are eliminated in the way described in Section IV.In [2] it is shown that the system is immune for most of the nonidealities of the op amp and the comparator, like slew ing, limitati ons of ban dwidth and gain, offset voltages,a nd in put bias curre nts. These noni dealities only cause additive or multiplicative errors which are elimi nated by the three-sig nal approach.VI. PERIOD MEASUREMENT WITH A MICROCONTROLLERPerformi ng period measureme nt with a microc on troller is an easy task. In our case, an INTEL 87C51FA is used,which has 8 kByte ROM, 256 Byte RAM, and UART for serial communication, and the capability to measure periods with a 333 ns resolution. Even though the counters are 16 b wide, they can easily be exte nded in the software to 24 b or more.The period measureme nt takes place mostly in the hardware of the microc on troller. Therefore, it is possible to let the CPU of the microc on troller perform other tasks at the same time (Fig. 6). For in sta nce, simulta neously with the measureme nt of period Tx, period Tref and period Toff,the relative capacitance with respect to Cref is calculated according to (11), and the result istran sferred through the UART to a pers onal computer.Fig. 5. Modified Martin oscillator with microcontroller and electrodes.Fig. 6. Period measureme nt as backgro und process.Fig. 7. Position error as function of the position and estimate of the nonlinearity.VII. EXPERIMENTAL RESULTSThe sensor is not sensitive to fabrication tolerances of the electrodes. Therefore in ourexperime ntal setup we used simple prin ted circuit board tech no logy to fabricate the electrodes, which have an effective area of 12 mm 12 mm.The guard electrode has a width of 15 mm, while the distance between the electrodes is about 5 mm. When the distance between the electrodes is varied over a 1 mm range, the capacitance changes from 0.25 pF to 0.3 pF.Thanks to the chosen concept, even a simple dual op amp (TLC272AC) and CMOS NAND ' s could be used allowing a single 5 V supply voltage. The total measurement time amounts to only 100 ms, where the oscillator was running at about 10 kHz.The system was tested in a fully automated setup, using an electrical XY table, the described sen sor and a pers onal computer. To achieve the required measureme ntaccuracy the setup was autozeroed every minute. In this way the nonlinearity, Iong-term stability and repeatability have been found to better than 1 卩m over a range of 1 mm (Fig.7). This is comparable to the accuracy and range of the system based on a PSD as described in [2].As a result of these experime nts, it was found that the resoluti on amounts to approximately 20 aF. This result was achieved by averag ing over 256 oscillator periods. A further in crease of the resolution by lengthening the measurement time is not possible due to the l/f noise produced by the first stages in both the integrator and the Comparator.The absolute accuracy can be derived from the positi on accuracy. Since a 1 mm displaceme nt corresponds to a change in capacitance of 50 fF, the absolute accuracy of 1 卩m in the amounts to an absolute accuracy of 50 aF.CONCLUSIONA low-cost, high-performance displacement sensor has been presented. The system is implemented with simple electrodes, an inexpensive microcontroller and a linearcapacitance-to-period converter. When the circuitry is provided with an accurate reference capacitor, the circuit can also be used to replace expe nsive capacity-measuri ng systems.REFERENCES[1]G. C. M. Meijer and R. Sch ner, “ A -ip e rio hrigince PSDdisplacement transducer with a microcontroller interfacing, ” Sensorsand Actuators, A21-A23, pp. 538-543, 1990.[2]J. van Drecht, G. C. M. Meijer, and P. C. de Jong, for'tBo nceptsdesig n of smart sen sors and smart sig nal processors and their applicatio nto PSD displaceme nt tran sducers. Digesr of Tech ni cal Papers, Transducers ' 91.[3]W. C. Heere ns. “ Applicati on of capacita nee tech niq ues in sen sor desig n, Phys. E: Sci. I nsfrum., vol. 19, pp. 897-906, 1986.[4]K. Marti n, '‘ A-c o lnageled switched-capacitor relaxation oscillator,IEEEJ., vol. SC-16, pp. 412-413, 1981.中文译文:一种低成本智能式电容位置传感器摘要本文描述了一种新的高性能,低成本电容位置测量系统。
- 1、下载文档前请自行甄别文档内容的完整性,平台不提供额外的编辑、内容补充、找答案等附加服务。
- 2、"仅部分预览"的文档,不可在线预览部分如存在完整性等问题,可反馈申请退款(可完整预览的文档不适用该条件!)。
- 3、如文档侵犯您的权益,请联系客服反馈,我们会尽快为您处理(人工客服工作时间:9:00-18:30)。
外文出处:Farhadi, A. (2008). Modeling, simulation, and reduction of conducted electromagnetic interference due to a pwm buck type switching power supply. Harmonics and Quality of Power, 2008. ICHQP 2008. 13th International Conference on, 1 - 6.Modeling, Simulation, and Reduction of Conducted Electromagnetic Interference Due to a PWM Buck Type Switching Power Supply IA. FarhadiAbstract:Undesired generation of radiated or conducted energy in electrical systems is called Electromagnetic Interference (EMI). High speed switching frequency in power electronics converters especially in switching power supplies improves efficiency but leads to EMI. Different kind of conducted interference, EMI regulations and conducted EMI measurement are introduced in this paper. Compliancy with national or international regulation is called Electromagnetic Compatibility (EMC). Power electronic systems producers must regard EMC. Modeling and simulation is the first step of EMC evaluation. EMI simulation results due to a PWM Buck type switching power supply are presented in this paper. To improve EMC, some techniques are introduced and their effectiveness proved by simulation.Index Terms:Conducted, EMC, EMI, LISN, Switching SupplyI. INTRODUCTIONFAST semiconductors make it possible to have high speed and high frequency switching in power electronics []1. High speed switching causes weight and volume reduction of equipment, but some unwanted effects such as radio frequency interference appeared []2. Compliance with electromagnetic compatibility (EMC) regulations is necessary for producers to present their products to the markets. It is important to take EMC aspects already in design phase []3. Modeling and simulation is the most effective tool to analyze EMC consideration before developing the products. A lot of the previous studies concerned the low frequency analysis of power electronics components []4[]5. Different types of power electronics converters are capable to be considered as source of EMI. They could propagate the EMI in both radiated and conducted forms. Line Impedance Stabilization Network (LISN) is required for measurement and calculation of conducted interference level []6. Interference spectrum at the output of LISN is introduced as the EMC evaluation criterion []7[]8. National or international regulations are the references forthe evaluation of equipment in point of view of EMC []7[]8.II. SOURCE, PATH AND VICTIM OF EMIUndesired voltage or current is called interference and their cause is called interference source. In this paper a high-speed switching power supply is the source of interference.Interference propagated by radiation in area around of an interference source or by conduction through common cabling or wiring connections. In this study conducted emission is considered only. Equipment such as computers, receivers, amplifiers, industrial controllers, etc that are exposed to interference corruption are called victims. The common connections of elements, source lines and cabling provide paths for conducted noise or interference. Electromagnetic conducted interference has two components as differential mode and common mode []9.A. Differential mode conducted interferenceThis mode is related to the noise that is imposed between different lines of a test circuit by a noise source. Related current path is shown in Fig. 1 []9. The interference source, path impedances, differential mode current and load impedance are also shown in Fig. 1.B. Common mode conducted interferenceCommon mode noise or interference could appear and impose between the lines, cables or connections and common ground. Any leakage current between load and common ground couldbe modeled by interference voltage source.Fig. 2 demonstrates the common mode interference source, common mode currents Iandcm1 and the related current paths[]9.The power electronics converters perform as noise source Icm2between lines of the supply network. In this study differential mode of conducted interference is particularly important and discussion will be continued considering this mode only.III. ELECTROMAGNETIC COMPATIBILITY REGULATIONS Application of electrical equipment especially static power electronic converters in different equipment is increasing more and more. As mentioned before, power electronics converters are considered as an important source of electromagnetic interference and have corrupting effects on the electric networks []2. High level of pollution resulting from various disturbances reduces the quality of power in electric networks. On the other side some residential, commercial and especially medical consumers are so sensitive to power system disturbances including voltage and frequency variations. The best solution to reduce corruption and improve power quality is complying national or international EMC regulations. CISPR, IEC, FCC and VDE are among the most famous organizations from Europe, USA and Germany who are responsible for determining and publishing the most important EMC regulations. IEC and VDE requirement and limitations on conducted emission are shown in Fig. 3 and Fig. 4 []7[]9.For different groups of consumers different classes of regulations could be complied. Class Afor common consumers and class B with more hard limitations for special consumers are separated in Fig. 3 and Fig. 4. Frequency range of limitation is different for IEC and VDE that are 150 kHz up to 30 MHz and 10 kHz up to 30 MHz respectively. Compliance of regulations is evaluated by comparison of measured or calculated conducted interference level in the mentioned frequency range with the stated requirements in regulations. In united European community compliance of regulation is mandatory and products must have certified label to show covering of requirements []8.IV. ELECTROMAGNETIC CONDUCTED INTERFERENCE MEASUREMENTA. Line Impedance Stabilization Network (LISN)1-Providing a low impedance path to transfer power from source to power electronics converter and load.2-Providing a low impedance path from interference source, here power electronics converter, to measurement port.Variation of LISN impedance versus frequency with the mentioned topology is presented inFig. 7. LISN has stabilized impedance in the range of conducted EMI measurement []7.Variation of level of signal at the output of LISN versus frequency is the spectrum of interference. The electromagnetic compatibility of a system can be evaluated by comparison of its interference spectrum with the standard limitations. The level of signal at the output of LISN in frequency range 10 kHz up to 30 MHz or 150 kHz up to 30 MHz is criterion of compatibility and should be under the standard limitations. In practical situations, the LISN output is connected to a spectrum analyzer and interference measurement is carried out. But for modeling and simulation purposes, the LISN output spectrum is calculated using appropriate software.基于压降型PWM开关电源的建模、仿真和减少传导性电磁干扰摘要:电子设备之中杂乱的辐射或者能量叫做电磁干扰(EMI)。