QCT663-2000汽车空调(HFC-134a)用热力膨胀阀
QC T 664-2000 汽车空调(HFC-134a)用软管及软管组合件

QC/T 664-2000(2000-11-06批准,2001-04-01实施)前言本标准是根据汽车空调用软管及软管组合件的工作原理、相关资料及试验数据,参考了国外先进国家的同类标准及国际标准等制定的。
本标准规定了汽车空调(HFC-134a)用软管及软管组合件的性能要求、试验方法、检验及种类、标志、包装运输贮存的基本要求,代表厂该类产品的总体技术水平。
是国内制造单位设计生产该类产品应达到的基本要求,也是使用单位检测此类产品的重要依据。
本标准由国家机械工业局提出。
本标准由全同汽车标准化技术委员会归口。
本标准起草单位:长春汽车研究所、南京7425工厂、固特异(青岛)工程橡胶有限公司。
本标准主要起草人:杨兆国、朱熠、孙克俭、韩同登。
中华人民共和国汽车行业标准汽车空调(HFC-134a)用软管及软管组合件 QC/T 664-20001 范围本标准规定了汽车空调系统中输送液态或气态HFC-134a制冷剂的空调软管及软管组合件的种类、尺寸、技术要求、试验方法、标志、检验及包装、运输和贮存。
本标准适用于汽车空调系统中输送液态或气态HFC-134a制冷剂用橡胶或热塑性软管及软管组合件。
软管的设计应尽可能减小HFC-134a的渗透及对环境的污染,并可在-40℃~+125℃温度范围内使用。
2 引用标准下列标准所包含的条文,通过在本标准中引用而构成为本标准的条文。
本标准出版时,所示版本均为有效。
所有标准都会被修订,使用本标准的各方应探讨使用下列标准最新版本的可能性。
GB/T 1690-1992 硫化橡胶耐液体试验方法GB/T 2941-1991 橡胶试样环境调节和试验的标准温度、湿度及时间3 种类3.1 A1、A2型——织物增强的合成橡胶软管软管内胶层为耐油橡胶,增强层由与内胶层和外胶层粘合的织物组成,外胶层为耐热和耐臭氧的橡胶。
Al型软管的外径比A2型软管小,且为一层增强层;A2型软管是两层增强层;A1、A2型软管的管接头通常不可互换使用。
QC T 664-2000 汽车空调用软管及软管组合件

QC T 664-2000 汽车空调用软管及软管组合件前言中华人民共和国汽车行业标准汽车空调(HFC-134a)用软管及软管组合件QC/T 664-20001范畴本标准规定了汽车空调系统中输送液态或气态HFC-134a制冷剂的空调软管及软管组合件的种类、尺寸、技术要求、试验方法、标志、检验及包装、运输和贮存。
本标准适用于汽车空调系统中输送液态或气态HFC-134a制冷剂用橡胶或热塑性软管及软管组合件。
软管的设计应尽可能减小HFC-134a的渗透及对环境的污染,并可在-40℃~+125℃温度范畴内使用。
2引用标准下列标准所包含的条文,通过在本标准中引用而构成为本标准的条文。
本标准出版时,所示版本均为有效。
所有标准都会被修订,使用本标准的各方应探讨使用下列标准最新版本的可能性。
GB/T 1690-1992 硫化橡胶耐液体试验方法GB/T 2941-1991 橡胶试样环境调剂和试验的标准温度、湿度及时刻3种类3.1A1、A2型——织物增强的合成橡胶软管软管内胶层为耐油橡胶,增强层由与内胶层和外胶层粘合的织物组成,外胶层为耐热和耐臭氧的橡胶。
Al型软管的外径比A2型软管小,且为一层增强层;A2型软管是两层增强层;A1、A2型软管的管接头通常不可互换使用。
3.2B型——钢丝增强的合成橡胶软管软管内胶层为耐油橡胶,增强层由钢丝组成,外层由用合成橡胶浸渍的耐热织物组成。
3.3C型——织物增强的带有热塑性绝缘层的软管软管内外橡胶层之间有热塑性绝缘层,以织物作为增强层,外胶层为耐热和耐臭氧的橡胶。
3.4D型——织物增强的热塑性内衬的软管在软管内胶层的内表面有薄薄一层热塑性塑料内衬,增强层由与内胶层和外胶层粘合的织物组成,外胶层为耐热和耐臭氧的橡胶。
4技术要求4.1尺寸4.1.1软管的内外径软管内外径尺寸应满足供需双方同意的图样的要求。
4.1.2软管壁厚偏差软管壁厚的偏差不应超过表1中规定的数值。
表1 软管壁厚偏差mm4.2外观质量软管及软管组合件上不承诺有阻碍使用性能和安装的缺陷;软管内外表面应清洁干燥、无破旧、裂纹、气泡、缩孔、起皱、凸起等缺陷;软管各层之间应结合牢固;软管组合件应连接牢固无缺陷。
qct656汽车空调制冷装置 性能要求
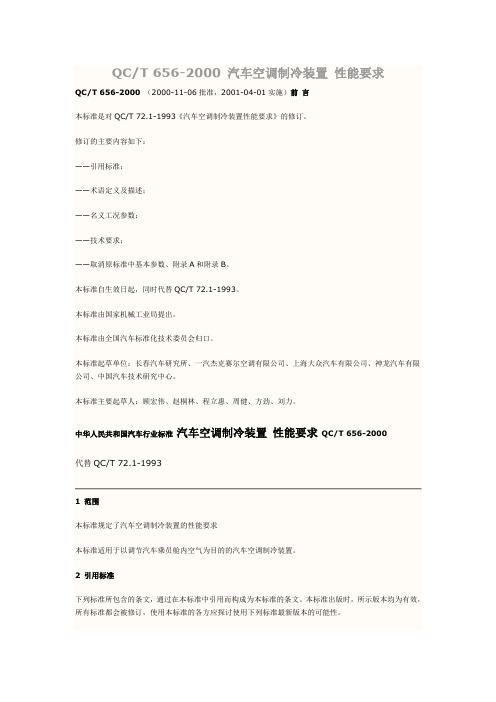
QC/T 656-2000 汽车空调制冷装置性能要求QC/T 656-2000(2000-11-06批准,2001-04-01实施)前言本标准是对QC/T 72.1-1993《汽车空调制冷装置性能要求》的修订。
修订的主要内容如下:——引用标准;——术语定义及描述;——名义工况参数:——技术要求;——取消原标准中基本参数、附录A和附录B。
本标准自生效日起,同时代替QC/T 72.1-1993。
本标准由国家机械工业局提出。
本标准由全国汽车标准化技术委员会归口。
本标准起草单位:长春汽车研究所、一汽杰克赛尔空调有限公司、上海大众汽车有限公司、神龙汽车有限公司、中国汽车技术研究中心。
本标准主要起草人:顾宏伟、赵桐林、程立惠、周健、方劲、刘力。
中华人民共和国汽车行业标准汽车空调制冷装置性能要求 QC/T 656-2000代替QC/T 72.1-19931 范围本标准规定了汽车空调制冷装置的性能要求本标准适用于以调节汽车乘员舱内空气为目的的汽车空调制冷装置。
2 引用标准下列标准所包含的条文,通过在本标准中引用而构成为本标准的条文。
本标准出版时,所示版本均为有效,所有标准都会被修订,使用本标准的各方应探讨使用下列标准最新版本的可能性。
QC/T 657-2000 汽车空调制冷装置试验方法QC/T 660-2000 汽车空调(HFC-134a)用压缩机QC/T 661-2000 汽车空调(HFC-134a)用液气分离器QC/T 662-2000 汽车空调(HFC-134a)用贮液干燥器QC/T 663-2000 汽车空调(HFC-134a)用热力膨胀阀3 术语3.1 汽车空调系统由暖气装置、制冷装置、通风装置、空气净化装置和加湿装置中的一个或多个部件以及必要的控制部件等构成,用于调节乘员舱内的温度、湿度、洁净度,并使其以一定速度在车室内定向流动和分配,从而给驾驶员和乘客提供舒适的环境及新鲜空气的系统。
3.2 制冷装置由压缩机、冷凝器、贮液干燥器或液气分离器、节流元件、蒸发器、制冷剂管路、风机等构成,将车室内的热量传递给室外环境的装置。
QC T656-2000汽车空调制冷装置 性能要求
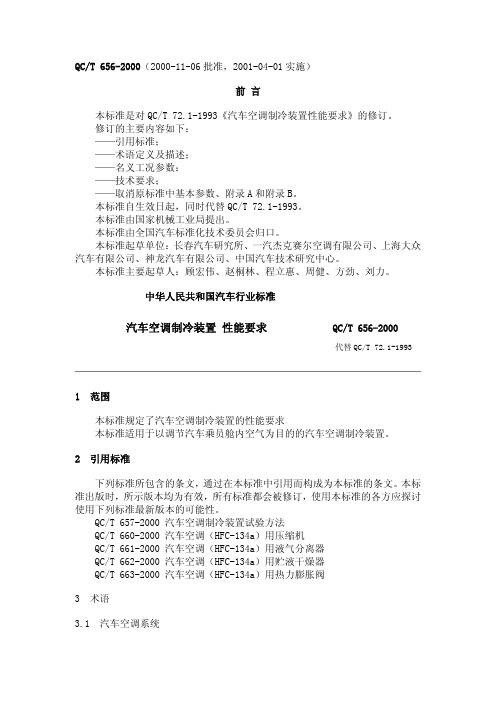
QC/T 656-2000(2000-11-06批准,2001-04-01实施)前 言本标准是对QC/T 72.1-1993《汽车空调制冷装置性能要求》的修订。
修订的主要内容如下:——引用标准;——术语定义及描述;——名义工况参数:——技术要求;——取消原标准中基本参数、附录A和附录B。
本标准自生效日起,同时代替QC/T 72.1-1993。
本标准由国家机械工业局提出。
本标准由全国汽车标准化技术委员会归口。
本标准起草单位:长春汽车研究所、一汽杰克赛尔空调有限公司、上海大众汽车有限公司、神龙汽车有限公司、中国汽车技术研究中心。
本标准主要起草人:顾宏伟、赵桐林、程立惠、周健、方劲、刘力。
中华人民共和国汽车行业标准汽车空调制冷装置 性能要求 QC/T 656-2000代替QC/T 72.1-19931 范围本标准规定了汽车空调制冷装置的性能要求本标准适用于以调节汽车乘员舱内空气为目的的汽车空调制冷装置。
2 引用标准下列标准所包含的条文,通过在本标准中引用而构成为本标准的条文。
本标准出版时,所示版本均为有效,所有标准都会被修订,使用本标准的各方应探讨使用下列标准最新版本的可能性。
QC/T 657-2000 汽车空调制冷装置试验方法QC/T 660-2000 汽车空调(HFC-134a)用压缩机QC/T 661-2000 汽车空调(HFC-134a)用液气分离器QC/T 662-2000 汽车空调(HFC-134a)用贮液干燥器QC/T 663-2000 汽车空调(HFC-134a)用热力膨胀阀3 术语3.1 汽车空调系统由暖气装置、制冷装置、通风装置、空气净化装置和加湿装置中的一个或多个部件以及必要的控制部件等构成,用于调节乘员舱内的温度、湿度、洁净度,并使其以一定速度在车室内定向流动和分配,从而给驾驶员和乘客提供舒适的环境及新鲜空气的系统。
3.2 制冷装置由压缩机、冷凝器、贮液干燥器或液气分离器、节流元件、蒸发器、制冷剂管路、风机等构成,将车室内的热量传递给室外环境的装置。
(整理)QC T 664-2000 汽车空调(HFC-134a)用软管及软管组合件 .
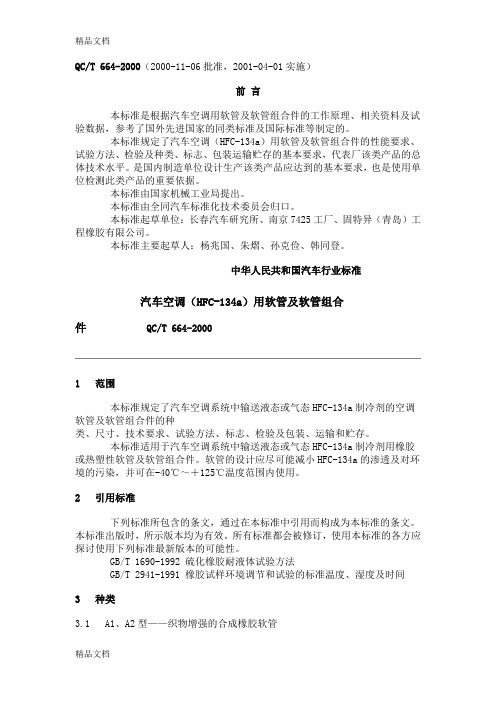
QC/T 664-2000(2000-11-06批准,2001-04-01实施)前言本标准是根据汽车空调用软管及软管组合件的工作原理、相关资料及试验数据,参考了国外先进国家的同类标准及国际标准等制定的。
本标准规定了汽车空调(HFC-134a)用软管及软管组合件的性能要求、试验方法、检验及种类、标志、包装运输贮存的基本要求,代表厂该类产品的总体技术水平。
是国内制造单位设计生产该类产品应达到的基本要求,也是使用单位检测此类产品的重要依据。
本标准由国家机械工业局提出。
本标准由全同汽车标准化技术委员会归口。
本标准起草单位:长春汽车研究所、南京7425工厂、固特异(青岛)工程橡胶有限公司。
本标准主要起草人:杨兆国、朱熠、孙克俭、韩同登。
中华人民共和国汽车行业标准汽车空调(HFC-134a)用软管及软管组合件 QC/T 664-20001 范围本标准规定了汽车空调系统中输送液态或气态HFC-134a制冷剂的空调软管及软管组合件的种类、尺寸、技术要求、试验方法、标志、检验及包装、运输和贮存。
本标准适用于汽车空调系统中输送液态或气态HFC-134a制冷剂用橡胶或热塑性软管及软管组合件。
软管的设计应尽可能减小HFC-134a的渗透及对环境的污染,并可在-40℃~+125℃温度范围内使用。
2 引用标准下列标准所包含的条文,通过在本标准中引用而构成为本标准的条文。
本标准出版时,所示版本均为有效。
所有标准都会被修订,使用本标准的各方应探讨使用下列标准最新版本的可能性。
GB/T 1690-1992 硫化橡胶耐液体试验方法GB/T 2941-1991 橡胶试样环境调节和试验的标准温度、湿度及时间3 种类3.1 A1、A2型——织物增强的合成橡胶软管软管内胶层为耐油橡胶,增强层由与内胶层和外胶层粘合的织物组成,外胶层为耐热和耐臭氧的橡胶。
Al型软管的外径比A2型软管小,且为一层增强层;A2型软管是两层增强层;A1、A2型软管的管接头通常不可互换使用。
QC T 663-2000汽车空调(HFC-134a)用热力膨胀阀
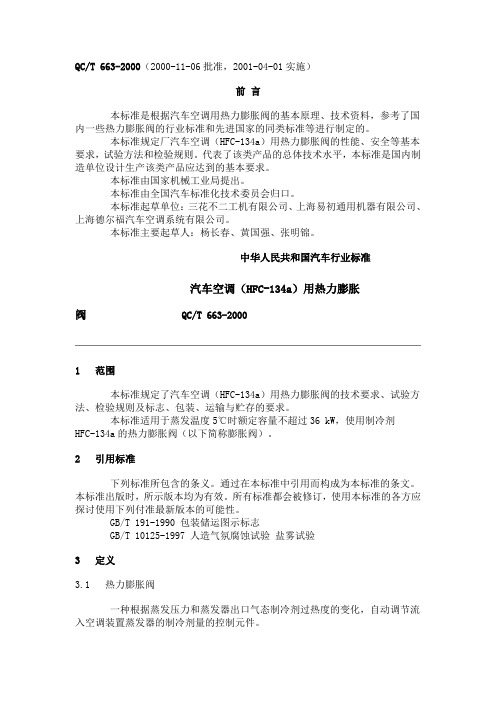
QC/T 663-2000(2000-11-06批准,2001-04-01实施)前言本标准是根据汽车空调用热力膨胀阀的基本原理、技术资料,参考了国内一些热力膨胀阀的行业标准和先进国家的同类标准等进行制定的。
本标准规定厂汽车空调(HFC-134a)用热力膨胀阀的性能、安全等基本要求,试验方法和检验规则。
代表了该类产品的总体技术水平,本标准是国内制造单位设计生产该类产品应达到的基本要求。
本标准由国家机械工业局提出。
本标准由全国汽车标准化技术委员会归口。
本标准起草单位:三花不二工机有限公司、上海易初通用机器有限公司、上海德尔福汽车空调系统有限公司。
本标准主要起草人:杨长春、黄国强、张明锦。
中华人民共和国汽车行业标准汽车空调(HFC-134a)用热力膨胀阀QC/T 663-20001 范围本标准规定了汽车空调(HFC-134a)用热力膨胀阀的技术要求、试验方法、检验规则及标志、包装、运输与贮存的要求。
本标准适用于蒸发温度5℃时额定容量不超过36 kW,使用制冷剂HFC-134a的热力膨胀阀(以下简称膨胀阀)。
2 引用标准下列标准所包含的条义。
通过在本标准中引用而构成为本标准的条文。
本标准出版时,所示版本均为有效。
所有标准都会被修订,使用本标准的各方应探讨使用下列付准最新版本的可能性。
GB/T 191-1990 包装储运图示标志GB/T 10125-1997 人造气氛腐蚀试验盐雾试验3 定义3.1 热力膨胀阀一种根据蒸发压力和蒸发器出口气态制冷剂过热度的变化,自动调节流入空调装置蒸发器的制冷剂量的控制元件。
3.2 膨胀阀的充注动力元件(感温包、毛细管、膜片或波纹管)内充注的介质与蒸发器出口处制冷剂的温度变化的对应方式。
3.3 膨胀阀的过热度内平衡型膨胀阀为膨胀阀出口压力,而外平衡型膨胀阀为蒸发器出口压力对应的饱和温度与感温包温度之差,此温度差为下述a)和b)之和。
a)静止过热度,膨胀阀从全闭状态到开始开启点的过热度;b)过热度变化(或过热度梯度)。
qct656(2000)汽车空调制冷装置性能要求
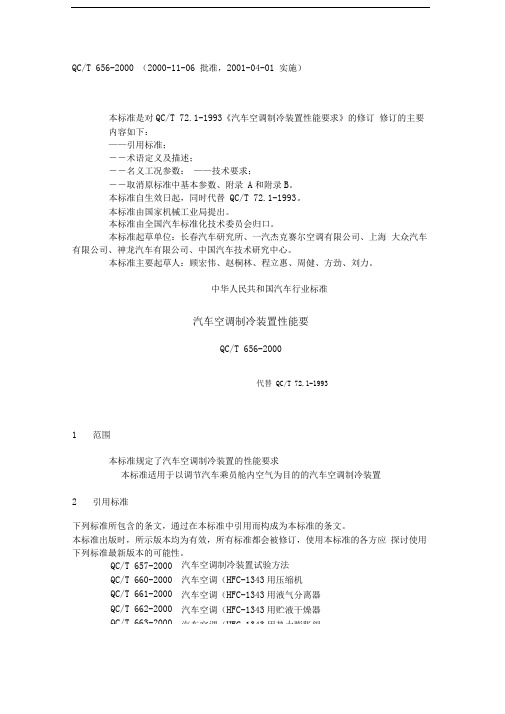
QC/T 656-2000 (2000-11-06 批准,2001-04-01 实施)本标准是对QC/T 72.1-1993《汽车空调制冷装置性能要求》的修订修订的主要内容如下:——引用标准;――术语定义及描述;――名义工况参数:——技术要求;――取消原标准中基本参数、附录A和附录B。
本标准自生效日起,同时代替QC/T 72.1-1993。
本标准由国家机械工业局提出。
本标准由全国汽车标准化技术委员会归口。
本标准起草单位:长春汽车研究所、一汽杰克赛尔空调有限公司、上海大众汽车有限公司、神龙汽车有限公司、中国汽车技术研究中心。
本标准主要起草人:顾宏伟、赵桐林、程立惠、周健、方劲、刘力。
中华人民共和国汽车行业标准汽车空调制冷装置性能要QC/T 656-2000代替QC/T 72.1-19931范围本标准规定了汽车空调制冷装置的性能要求本标准适用于以调节汽车乘员舱内空气为目的的汽车空调制冷装置2引用标准下列标准所包含的条文,通过在本标准中引用而构成为本标准的条文。
本标准出版时,所示版本均为有效,所有标准都会被修订,使用本标准的各方应探讨使用下列标准最新版本的可能性。
QC/T 657-2000 QC/T 660-2000 QC/T 661-2000 QC/T 662-2000 QC/T 663-2000 汽车空调制冷装置试验方法汽车空调(HFC-1343用压缩机汽车空调(HFC-1343用液气分离器汽车空调(HFC-1343用贮液干燥器汽车空调(HFC-1343用热力膨胀阀3术语3.1汽车空调系统由暖气装置、制冷装置、通风装置、空气净化装置和加湿装置中的一个或多个部件以及必要的控制部件等构成,用于调节乘员舱内的温度、湿度、洁净度,并使其以一定速度在车室内定向流动和分配,从而给驾驶员和乘客提供舒适的环境及新鲜空气的系统。
3.2制冷装置由压缩机、冷凝器、贮液干燥器或液气分离器、节流元件、蒸发器、制冷剂管路、风机等构成,将车室内的热量传递给室外环境的装置。
QC T 663-2019汽车空调(HFC-134a)用热力膨胀阀-10页精选文档
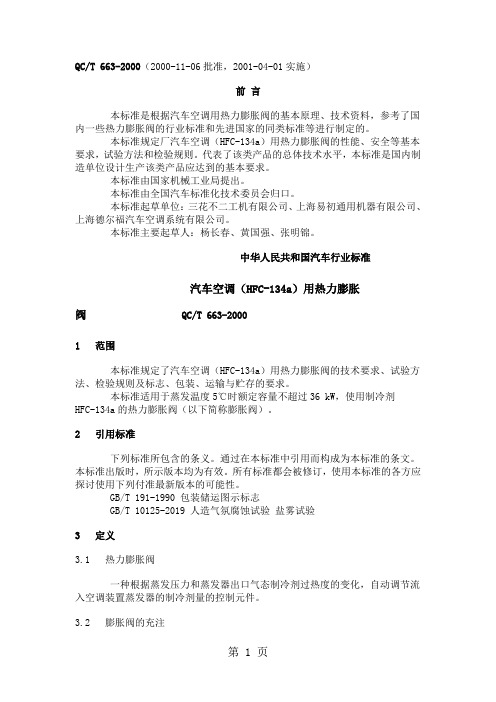
QC/T 663-2000(2000-11-06批准,2001-04-01实施)前言本标准是根据汽车空调用热力膨胀阀的基本原理、技术资料,参考了国内一些热力膨胀阀的行业标准和先进国家的同类标准等进行制定的。
本标准规定厂汽车空调(HFC-134a)用热力膨胀阀的性能、安全等基本要求,试验方法和检验规则。
代表了该类产品的总体技术水平,本标准是国内制造单位设计生产该类产品应达到的基本要求。
本标准由国家机械工业局提出。
本标准由全国汽车标准化技术委员会归口。
本标准起草单位:三花不二工机有限公司、上海易初通用机器有限公司、上海德尔福汽车空调系统有限公司。
本标准主要起草人:杨长春、黄国强、张明锦。
中华人民共和国汽车行业标准汽车空调(HFC-134a)用热力膨胀阀QC/T 663-20001 范围本标准规定了汽车空调(HFC-134a)用热力膨胀阀的技术要求、试验方法、检验规则及标志、包装、运输与贮存的要求。
本标准适用于蒸发温度5℃时额定容量不超过36 kW,使用制冷剂HFC-134a的热力膨胀阀(以下简称膨胀阀)。
2 引用标准下列标准所包含的条义。
通过在本标准中引用而构成为本标准的条文。
本标准出版时,所示版本均为有效。
所有标准都会被修订,使用本标准的各方应探讨使用下列付准最新版本的可能性。
GB/T 191-1990 包装储运图示标志GB/T 10125-2019 人造气氛腐蚀试验盐雾试验3 定义3.1 热力膨胀阀一种根据蒸发压力和蒸发器出口气态制冷剂过热度的变化,自动调节流入空调装置蒸发器的制冷剂量的控制元件。
3.2 膨胀阀的充注动力元件(感温包、毛细管、膜片或波纹管)内充注的介质与蒸发器出口处制冷剂的温度变化的对应方式。
3.3 膨胀阀的过热度内平衡型膨胀阀为膨胀阀出口压力,而外平衡型膨胀阀为蒸发器出口压力对应的饱和温度与感温包温度之差,此温度差为下述a)和b)之和。
a)静止过热度,膨胀阀从全闭状态到开始开启点的过热度;b)过热度变化(或过热度梯度)。
汽车空调(HFC-134a)用软管及软管组合件QCT 664
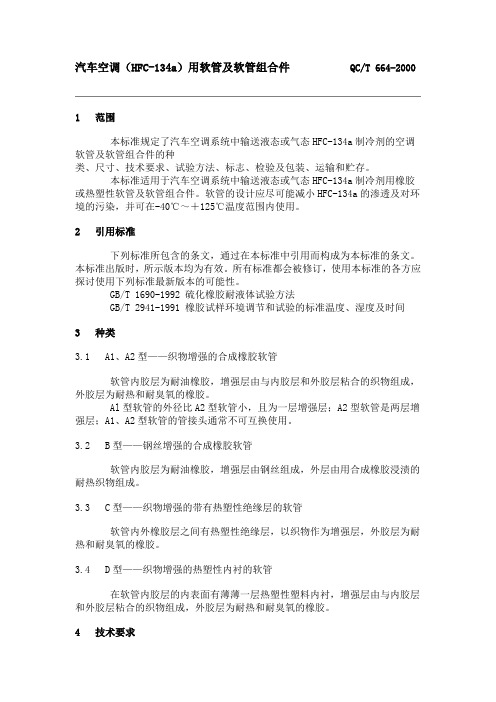
汽车空调(HFC-134a)用软管及软管组合件 QC/T 664-20001 范围本标准规定了汽车空调系统中输送液态或气态HFC-134a制冷剂的空调软管及软管组合件的种类、尺寸、技术要求、试验方法、标志、检验及包装、运输和贮存。
本标准适用于汽车空调系统中输送液态或气态HFC-134a制冷剂用橡胶或热塑性软管及软管组合件。
软管的设计应尽可能减小HFC-134a的渗透及对环境的污染,并可在-40℃~+125℃温度范围内使用。
2 引用标准下列标准所包含的条文,通过在本标准中引用而构成为本标准的条文。
本标准出版时,所示版本均为有效。
所有标准都会被修订,使用本标准的各方应探讨使用下列标准最新版本的可能性。
GB/T 1690-1992 硫化橡胶耐液体试验方法GB/T 2941-1991 橡胶试样环境调节和试验的标准温度、湿度及时间3 种类3.1 A1、A2型——织物增强的合成橡胶软管软管内胶层为耐油橡胶,增强层由与内胶层和外胶层粘合的织物组成,外胶层为耐热和耐臭氧的橡胶。
Al型软管的外径比A2型软管小,且为一层增强层;A2型软管是两层增强层;A1、A2型软管的管接头通常不可互换使用。
3.2 B型——钢丝增强的合成橡胶软管软管内胶层为耐油橡胶,增强层由钢丝组成,外层由用合成橡胶浸渍的耐热织物组成。
3.3 C型——织物增强的带有热塑性绝缘层的软管软管内外橡胶层之间有热塑性绝缘层,以织物作为增强层,外胶层为耐热和耐臭氧的橡胶。
3.4 D型——织物增强的热塑性内衬的软管在软管内胶层的内表面有薄薄一层热塑性塑料内衬,增强层由与内胶层和外胶层粘合的织物组成,外胶层为耐热和耐臭氧的橡胶。
4 技术要求4.1 尺寸4.1.1 软管的内外径软管内外径尺寸应满足供需双方同意的图样的要求。
4.1.2 软管壁厚偏差软管壁厚的偏差不应超过表1中规定的数值。
表1 软管壁厚偏差 mm4.2外观质量软管及软管组合件上不允许有影响使用性能和安装的缺陷;软管内外表面应清洁干燥、无破损、裂纹、气泡、缩孔、起皱、凸起等缺陷;软管各层之间应结合牢固;软管组合件应连接牢固无缺陷。
qct656(2000)汽车空调制冷装置性能要求
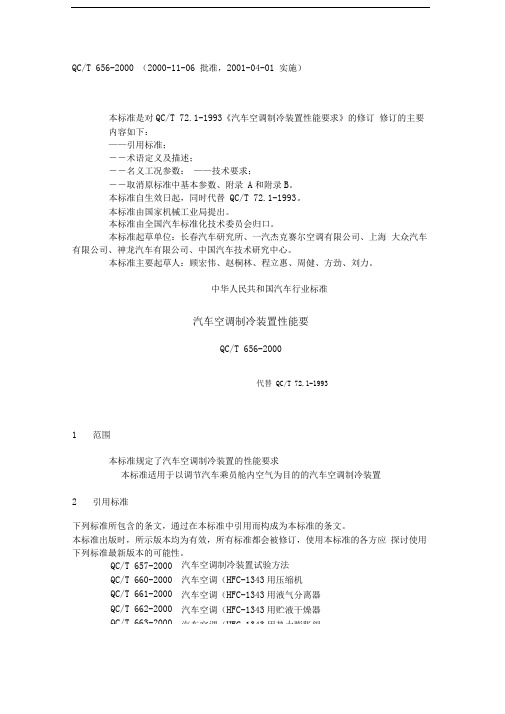
QC/T 656-2000 (2000-11-06 批准,2001-04-01 实施)本标准是对QC/T 72.1-1993《汽车空调制冷装置性能要求》的修订修订的主要内容如下:——引用标准;――术语定义及描述;――名义工况参数:——技术要求;――取消原标准中基本参数、附录A和附录B。
本标准自生效日起,同时代替QC/T 72.1-1993。
本标准由国家机械工业局提出。
本标准由全国汽车标准化技术委员会归口。
本标准起草单位:长春汽车研究所、一汽杰克赛尔空调有限公司、上海大众汽车有限公司、神龙汽车有限公司、中国汽车技术研究中心。
本标准主要起草人:顾宏伟、赵桐林、程立惠、周健、方劲、刘力。
中华人民共和国汽车行业标准汽车空调制冷装置性能要QC/T 656-2000代替QC/T 72.1-19931范围本标准规定了汽车空调制冷装置的性能要求本标准适用于以调节汽车乘员舱内空气为目的的汽车空调制冷装置2引用标准下列标准所包含的条文,通过在本标准中引用而构成为本标准的条文。
本标准出版时,所示版本均为有效,所有标准都会被修订,使用本标准的各方应探讨使用下列标准最新版本的可能性。
QC/T 657-2000 QC/T 660-2000 QC/T 661-2000 QC/T 662-2000 QC/T 663-2000 汽车空调制冷装置试验方法汽车空调(HFC-1343用压缩机汽车空调(HFC-1343用液气分离器汽车空调(HFC-1343用贮液干燥器汽车空调(HFC-1343用热力膨胀阀3术语3.1汽车空调系统由暖气装置、制冷装置、通风装置、空气净化装置和加湿装置中的一个或多个部件以及必要的控制部件等构成,用于调节乘员舱内的温度、湿度、洁净度,并使其以一定速度在车室内定向流动和分配,从而给驾驶员和乘客提供舒适的环境及新鲜空气的系统。
3.2制冷装置由压缩机、冷凝器、贮液干燥器或液气分离器、节流元件、蒸发器、制冷剂管路、风机等构成,将车室内的热量传递给室外环境的装置。
汽车标准-QC T 669-2000汽车空调(HFC-134a)用管接头和管件.doc

汽车标准-QC T 669-2000汽车空调(HFC-134a)用管接头和管件.docQC/T 669-2000(2000-12-07发布,2001-07-01实施)前言本标准等效采用国际汽车空调协会标准:MACA305-1997。
对原标准所推荐的汽车空调管接头型式与尺寸未作修改,仅将英制单位换算成了公制单位。
本标准中的螺纹管接头采用的是美国国家标准ANSI规定的统一螺纹(UN),因目前国内已有许多英制螺纹的生产和使用者,全国螺纹标准化技术委员会也正在考虑将英制螺纹采用过来制定为国家标准,在国家标准尚未制定之前,本标准只能将ANSI作为引用标准。
关于英制统一螺纹,ANSI B1.1与ISO 263:1973、ISO 725:1978、ISO 5864:1993、ISO 68.2:1998是一致的,但ISO标准中缺乏相应的量规和检验体系标准,因此,本标准在引用标准中不再列入ISO标准。
对于中性盐雾试验,原标准采用的是ASTM B117,本标准引用了方法与之等效的GB/T 10125。
本标准的附录A为提示的附录。
本标准由国家机械工业局提出。
本标准由全国汽车标准化技术委员会归口。
本标准起草单位:中国汽车技术研究中心、东风汽车工程研究院、岳阳恒立冷气设备股份有限公司。
本标准主要起草人:刘力、朱彤、郭亮、张远刚。
中华人民共和国汽车行业标准汽车空调(HFC-134a)用管接头和管件 QC/T 669-20001 范围本标准规定了汽车空调(HFC-134a)用管接头和管件端部的型式、尺寸及技术要求。
本标准适用于汽车空调(HFC-134a)用管接头和管件。
2 引用标准下列标准所包含的条文,通过在本标准中引用而构成为本标准的条文。
本标准出版时,所示版本均为有效。
所有标准都会被修订,使用本标准的各方应探讨使用下列标准最新版本的可能性。
GB/T 10125-1997 人造气氛腐蚀试验盐雾试验ANSI B1.1-1989 英制统一螺纹ANSI B1.2-1983 英制统一螺纹量规ANSI/ASME B1.3M-1992 螺纹量规体系ANSI B1.13-1983 米制螺纹牙型3 型式与代号螺纹管接头及其组件的型式与缩写代号按表1规定;4 一般要求4.1 范围本标准规定了汽车空调系统用扩口式和O形圈式管接头的螺纹连接件和管件端部型式,以及带“倒钩”的推入式软管接头。
QC T 659-2000汽车空调(HFC-134a)用标识
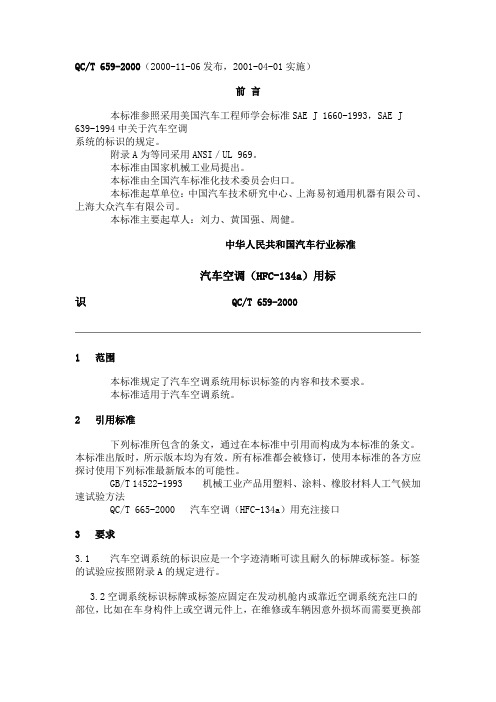
QC/T 659-2000(2000-11-06发布,2001-04-01实施)前言本标准参照采用美国汽车工程师学会标准SAE J 1660-1993,SAE J 639-1994中关于汽车空调系统的标识的规定。
附录A为等同采用ANSI/UL 969。
本标准由国家机械工业局提出。
本标准由全国汽车标准化技术委员会归口。
本标准起草单位:中国汽车技术研究中心、上海易初通用机器有限公司、上海大众汽车有限公司。
本标准主要起草人:刘力、黄国强、周健。
中华人民共和国汽车行业标准汽车空调(HFC-134a)用标识 QC/T 659-20001 范围本标准规定了汽车空调系统用标识标签的内容和技术要求。
本标准适用于汽车空调系统。
2 引用标准下列标准所包含的条文,通过在本标准中引用而构成为本标准的条文。
本标准出版时,所示版本均为有效。
所有标准都会被修订,使用本标准的各方应探讨使用下列标准最新版本的可能性。
GB/T 14522-1993 机械工业产品用塑料、涂料、橡胶材料人工气候加速试验方法QC/T 665-2000 汽车空调(HFC-134a)用充注接口3 要求3.1 汽车空调系统的标识应是一个字迹清晰可读且耐久的标牌或标签。
标签的试验应按照附录A的规定进行。
3.2空调系统标识标牌或标签应固定在发动机舱内或靠近空调系统充注口的部位,比如在车身构件上或空调元件上,在维修或车辆因意外损坏而需要更换部件时一般不更换。
标牌或标签上应包括对制冷剂的类型和润滑油牌号的说明,以及推荐的制冷剂充注量。
3.3 制冷剂类型和推荐的系统充注装置、润滑油牌号还应在车辆的用户手册中说明。
3.4 当汽车空调系统是在CFC-12制冷剂系统基础上进行改造使其适用于HFC-134a制冷剂时,制冷剂充注接口应符合QC/T 665的要求。
并在改造完成后,按以下所述标示一个标签,以说明改型。
3.4.1 改型的标签上应有标题:“注意:已改造用于HFC-134a”。
QCT6662021汽车空调用密封件

QCT6662021汽车空调用密封件前言本标准由国家机械工业局提出。
本标准由全国汽车标准化技术委员会归口。
本标准起草单位:南京7425工厂、中国汽车技术研究中心、岳阳恒立冷气设备股份、亚新科零部件(安徽)、江苏金坛密封件厂。
本标准要紧起草人:戴国粱、高宏、戚建国、龚德谷、彭卓。
中华人民共和国汽车行业标准汽车空调(HFC-134a)用密封件 QC/T 666-20001 范畴本标准规定了使用制冷剂HFC-134a的汽车空调用橡胶密封件的技术要求、试验方法、检验规则以及标志、包装、运输和贮存。
2 引用标准下列标准所包含的条文,通过在本标准中引用而构成为本标准的条文。
本标准出版时,所示版本均为有效。
所有标准都会被修订,使用本标准的各方应探讨使用下列标准最新版本的可能性。
GB/T 528-1998 硫化橡胶或热塑性橡胶拉伸应力应变性能的测定GB/T 531-1992 硫化橡胶邵尔A硬度试验方法GB/T 1682-1994 硫化橡胶低温脆性的测定单试样法GB/T 1690-1992 硫化橡胶耐液体试验方法GB/T 2941-1991 橡胶试样环境调剂和试验的标准温度、湿度及时刻 GB 3452.1-1992 液压气动用0形橡胶密封圈尺寸系列及公差GB/T 3452.2-1987 O形橡胶密封圈外观质量检验标准GB/T 3512-1983 橡胶热空气者化试验方法GB/T 5720-1993 O形橡胶密封圈试验方法GB/T 5721-1993 橡胶密封制品标志、包装、运输、贮存的一样规定 GB/T 5723-1993 硫化橡胶或热塑性橡胶试验用试样和制品尺寸的测定GB/T 7759-1996 硫化橡胶、热塑性橡胶在常温、高温顺低温下压缩永久变形测定GB/T 7762-1987 硫化橡胶耐臭氧老化试验静态拉伸试验法GB/T 9865.1-1996 硫化橡胶或热塑性橡胶样品和试样的制备第一部分:物理试验3 技术要求3.1 密封件中橡胶材料所用原材料及制造工艺应当遵照有关技术规范。
车用空调系统热力膨胀阀规格书-
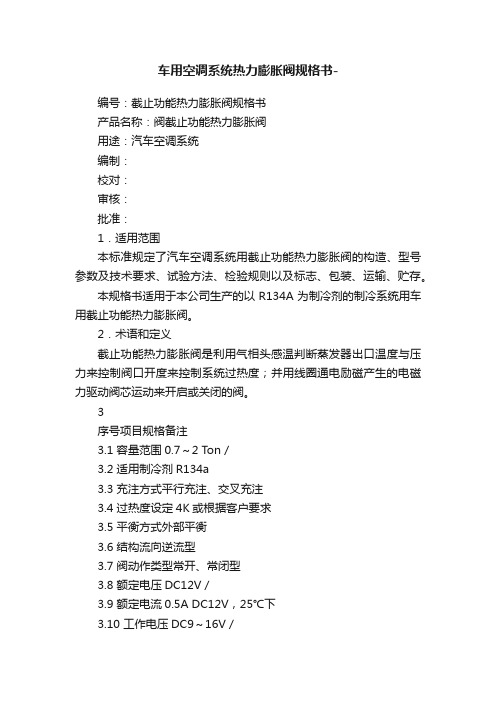
车用空调系统热力膨胀阀规格书-编号:截止功能热力膨胀阀规格书产品名称:阀截止功能热力膨胀阀用途:汽车空调系统编制:校对:审核:批准:1.适用范围本标准规定了汽车空调系统用截止功能热力膨胀阀的构造、型号参数及技术要求、试验方法、检验规则以及标志、包装、运输、贮存。
本规格书适用于本公司生产的以R134A为制冷剂的制冷系统用车用截止功能热力膨胀阀。
2.术语和定义截止功能热力膨胀阀是利用气相头感温判断蒸发器出口温度与压力来控制阀口开度来控制系统过热度;并用线圈通电励磁产生的电磁力驱动阀芯运动来开启或关闭的阀。
3序号项目规格备注3.1 容量范围0.7~2 Ton /3.2 适用制冷剂R134a3.3 充注方式平行充注、交叉充注3.4 过热度设定4K或根据客户要求3.5 平衡方式外部平衡3.6 结构流向逆流型3.7 阀动作类型常开、常闭型3.8 额定电压DC12V /3.9 额定电流0.5A DC12V,25℃下3.10 工作电压DC9~16V /3.11 最小工作电压DC9V(2.1MPa,20℃)/3.12 使用油POE /3.13 使用环境温度-40℃~+125℃/3.14 适用环境湿度≤95%RH /型号说明:STHXX-XXXX-XXSTH XX-XXXX-XX:XX为标识容量标识:07:0.7 Ton;10:1.0 Ton;15:1.5 Ton;20:2.0 TonSTHXX-XXXX-XX:XXXX 为型号区别码,第一位区分常开常闭0:常闭;1:常开,如0001、1001…STHXX-XXXX-XX:XX为不同过热度区别码,如01、02….标签说明:4.环保要求4.1 所用材料要求符合RoHS规定;4.2 外壳要求耐NaCl、H2S腐蚀;4.3 所用材料对人体无毒害且不产生有毒物质;客户代码制冷剂型号盾安logo产品型号生产编号4.4 阀体内部结构材料需满足耐冷媒腐蚀,冲击要求;4.5 阀内部材料强度,刚度能满足产,品性能要求。
- 1、下载文档前请自行甄别文档内容的完整性,平台不提供额外的编辑、内容补充、找答案等附加服务。
- 2、"仅部分预览"的文档,不可在线预览部分如存在完整性等问题,可反馈申请退款(可完整预览的文档不适用该条件!)。
- 3、如文档侵犯您的权益,请联系客服反馈,我们会尽快为您处理(人工客服工作时间:9:00-18:30)。
QC/T 663-2000(2000-11-06批准,2001-04-01实施)前言本标准是根据汽车空调用热力膨胀阀的基本原理、技术资料,参考了国内一些热力膨胀阀的行业标准和先进国家的同类标准等进行制定的。
本标准规定厂汽车空调(HFC-134a)用热力膨胀阀的性能、安全等基本要求,试验方法和检验规则。
代表了该类产品的总体技术水平,本标准是国内制造单位设计生产该类产品应达到的基本要求。
本标准由国家机械工业局提出。
本标准由全国汽车标准化技术委员会归口。
本标准起草单位:三花不二工机有限公司、上海易初通用机器有限公司、上海德尔福汽车空调系统有限公司。
本标准主要起草人:杨长春、黄国强、张明锦。
中华人民共和国汽车行业标准汽车空调(HFC-134a)用热力膨胀阀QC/T 663-20001 范围本标准规定了汽车空调(HFC-134a)用热力膨胀阀的技术要求、试验方法、检验规则及标志、包装、运输与贮存的要求。
本标准适用于蒸发温度5℃时额定容量不超过36 kW,使用制冷剂HFC-134a的热力膨胀阀(以下简称膨胀阀)。
2 引用标准下列标准所包含的条义。
通过在本标准中引用而构成为本标准的条文。
本标准出版时,所示版本均为有效。
所有标准都会被修订,使用本标准的各方应探讨使用下列付准最新版本的可能性。
GB/T 191-1990 包装储运图示标志GB/T 10125-1997 人造气氛腐蚀试验盐雾试验3 定义3.1 热力膨胀阀一种根据蒸发压力和蒸发器出口气态制冷剂过热度的变化,自动调节流入空调装置蒸发器的制冷剂量的控制元件。
3.2 膨胀阀的充注动力元件(感温包、毛细管、膜片或波纹管)内充注的介质与蒸发器出口处制冷剂的温度变化的对应方式。
3.3 膨胀阀的过热度内平衡型膨胀阀为膨胀阀出口压力,而外平衡型膨胀阀为蒸发器出口压力对应的饱和温度与感温包温度之差,此温度差为下述a)和b)之和。
a)静止过热度,膨胀阀从全闭状态到开始开启点的过热度;b)过热度变化(或过热度梯度)。
膨胀阀从开始开启点到规定开启点所需过热度的变化量。
3.4 额定容量在额定条件下通过试验而确定的容量。
3.5 膨胀阀迟滞膨胀阀的开度特性,过热度上升与下降时的开度差。
4 膨胀阀种类膨胀阀可以按以下型式进行分类,并可以是以下各型的组合。
4.1 按平衡型式4.1.1 内平衡型作用于动力元件的压力通过内部通路与阀出口压力形成平衡的一种结构。
4.1.2 外平衡型作用于动力元件的压力通过配管与蒸发器出口压力形成平衡的一种结构。
4.2 按充注型式4.2.1 液体充注型对于所有工作条件,充注在动力元件内的一部分介质以液体形态存在于感温包内的一种型式。
4.2.2 气体充注型充注的介质达到规定的感温温度,则所有液体全部气化,即使温度上升,动力元件内部压力几乎不上升的一种型式。
此时的内部压力称为最大工作压力(简称MOP)。
4.2.3 吸附充注型介质伴随吸附剂的作用而工作的型式。
4.3 按制冷剂流向4.3.1 正流型高压侧压力作用于打开方向的结构。
4.3.2 逆流型高压侧压力作用于关闭方向的结构。
4.4 按感温包位置4.4.1 感温包外置型4.4.2 感温包内藏型5 额定条件5.1 标准额定条件作为性能特性的比较基准而规定的条件,见表1中a。
5.2 适用额定条件除标准额定条件以外的额定条件,可根据制造者的技术资料或技术标准及其它而设定,可参照表1中b。
表1 额定条件6 技术要求6.1 尺寸与按规定程序批准的图样和技术文件一致。
6.2 外观没有明显的伤痕、变形、氧化腐蚀、毛刺等缺陷,阀内无切屑、杂质及游离水份存在。
6.3 开度、迟滞按供需双方的协议。
6.4 额定容量按供需双方的协议。
6.5 静止过热度按供需双方的协议。
6.6 阀口泄漏按供需双方的协议。
6.7 平衡部泄漏按供需双方的协议。
6.8 气密性6.8.1 出口侧气密性在1.5 MPa压力下,不应有泄漏现象。
6.8.2 进口侧气密性在3.5 MPa压力下,不应有泄漏现象。
6.9 耐压强度在出口侧2.2 MPa,进口侧5.3 MPa压力下,不应有泄漏或异常变形。
6.10 破坏强度在出口侧4.4 MPa,进口侧10.6 MPa压力下,不应有开裂破损现象。
6.11 耐久性按7.2.11耐久试验后,应满足以下要求:a)气密性满足6.8要求;b)静止过热度变化量在±0.02 MPa以内;c)阀口泄漏不超过允许值的120%;d)平衡部泄漏不超过允许值的120%。
6.12 耐振动性按7.2.12经振动试验后,应满足6.8和6.11.2的要求。
6.13 耐冷热冲击性按7.2.13经冷热冲击试验后,应满足6.8、6.11.2和6.11.4的要求。
6.14 耐高温性按7.2.14经耐高温试验后,应满足6.8和6.11.2的要求。
6.15 耐低温性按7.2.15经耐低温试验后,应满足6.8和6.11.2的要求。
6.16 耐腐蚀性按7.2.16经耐腐蚀试验后,不应有明显锈蚀产生,并满足6.8和6.11.2的要求。
7 试验方法7.1 试验条件7.1.1 环境条件温度:5℃~35℃气压:86 kPa~106 kPa7.1.2 测量仪器精度按表2规定。
表2 测量仪器精度7.2 试验方法7.2.1 尺寸检查用常规和专用量具进行检查。
7.2.2 外观检查用目测法检查。
7.2.3 开度、迟滞试验7.2.3.1 试验装置把按静止过热度设定的膨胀阀安装在图1所示的试验装置上,并加以处理以免试验用空气或氮气从高压接头部及阀开度测定部泄漏。
7.2.3.2 内部或外部平衡压力变化时的膨胀阀开度。
a)把感温包浸于按规定温度保温的恒温槽内,规定温度为0℃或按供需双方协议温度;b)内平衡型膨胀阀从低压接头侧,外平衡型膨胀阀从平衡接头处加压;c)以0.01 MPa以下间隔增加加压压力,并测得膨胀阀开度;d)然后以0.01 MPa以下的问隔降低加压压力,并测得膨胀阀开度;e)根据c)、d)测定结果,绘制图2所示曲线;f)根据图2曲线,针对相当膨胀阀额定容量的膨胀阀开度,计算出平衡压力上升时及下降时的压差,该压差即为迟滞。
7.2.3.3 相对感温包温度变化的膨胀阀开度a)内平衡型膨胀阀从低压接头侧,外平衡型膨胀阀从平衡接头侧加压(加压压力按标准额定条件);b)该状态下,以1℃以下的间隔增高感温包温度,并测得膨胀阀开度;c)然后以1℃以下的间隔降低感温包温度,并测得膨胀阀开度;d)根据b)、c)测定结果,绘制如图3所示的曲线;e)根据图3曲线,针对相当膨胀阀额定容量的膨胀阀开度,计算出感温包温度上升及下降时的温差,该温差即为迟滞。
7.2.4 额定容量试验7.2.4.1 相对感温包温度的膨胀阀开度试验根据7.2.3条开度及迟滞试验方法,绘制一感温包温度与膨胀阀开度的曲线(如图4所示)。
此时的压力及温度按照标准额定条件。
7.2.4.2 流量试验流量试验按7.2.4.3规定的制冷剂质量流量试验方法进行。
但在无法用制冷剂进行试验时,也可用其它的试验方法来代替,只要得到的试验结果用7.2.4.3所规定的试验方法能证实其准确性即可。
7.2.4.3 相对膨胀阀开度的制冷剂质量流量试验a)试验条件流入膨胀阀的液态制冷剂不得有蒸气,另外,自饱和温度再冷却3℃~6℃的状态。
而且用于试验的制冷剂含油浓度,质量比不得超过2%;b)取下膨胀阀的动力元件部分,在该部位安装一能任意开启、关闭膨胀阀,并能测定膨胀阀开度的机构。
将膨胀阀装在图5所示的试验装置上。
用手动膨胀阀把膨胀阀进出口压力保持在标准额定条件中的规定压力。
按0.1 mm以下的膨胀阀开度间隔,至少取10点以上,测得该膨胀阀不同开度时的制冷剂流量;c)根据测定值,绘制一相对膨胀阀开度的制冷剂流量曲线(如图6所示)。
7.2.4.4 根据7.2.4.1、7.2.4.2、7.2.4.3的测定结果,绘制相对感温包温度的制冷剂流量曲线(如图7所示)。
7.2.4.5 额定点过热度变化的确定在图7所示的相对感温包温度的制冷剂流量曲线中,从膨胀阀开始开启位置的制冷剂流量A作横轴平行线,再从和制冷剂流量曲线的交点,向感温包温度轴线作垂线确定膨胀阀的开始开启点a,然后,以额定点作横轴平行线,从和制冷剂流量曲线的交点上,向感温包温度轴线作垂直线确定b点。
该a、b 二点间的温度表示膨胀阀开始开启点到额定点时的过热度变化量,额定点时的制冷剂流量为膨胀阀的额定流量,记录为q。
另外,把膨胀阀开度为0.05 mm定为开mr启点。
7.2.4.6 额定容量按下述公式进行计算Q=qmr(h2-h1)K式中:Q——膨胀阀容量 W;qmr——额定点的制冷剂质量流量, kg/s;h2——蒸发器出口侧饱和蒸气制冷剂的比焓值,J/kg;h1——蒸发器进口侧饱和液态制冷剂的比焓值,J/kg;K——有关过冷度的修正值(液态制冷剂温度:55℃,过热度:0 ℃)见图8。
7.2.5 静止过热度试验将膨胀阀装在图9所示的试验装置上,用压力调整阀将压力P1调整为1.03 MPa±0.05 MPa,将感温包在0℃恒温槽内浸10 min以上,关闭、打开截止阀2~3次后,P2所示压力即为0℃时的静止过热度。
7.2.6 阀口泄漏试验在7.2.5静止过热度试验完毕后,关闭截止阀;1 min时出口压力P2的压力上升值即为阀口泄漏量(如图10所示)。
7.2.7 平衡部泄漏试验堵住膨胀阀高压侧接头,将膨胀阀安装在图11所示的试验装置上,将进气压力P1调整为0.2 MPa,打开截止阀,用流量计或排水法测得平衡部的气体流量。
7.2.8 气密性试验用于燥空气或氮气,在膨胀阀出口侧和进口侧分别加压至1.5 MPa和3.5 MPa,侵入水中.保压5min,观察是否有气泡产生。
7.2.9 耐压强度试验在膨胀阀中注满常温液体,完全排出空气后。
将出口侧和进口侧缓慢加压至2.2 MPa和5.3 MPa,保压1min,观察是否有液体泄漏或异常变形现象。
7.2.10 破坏强度试验在膨胀阀中注满常温液体,完全排出空气后,将出口侧和进口侧缓慢加压至4.4 MPa和10.6 MPa,保压1min,观察是否有破损开裂现象。
7.2.11 耐久性试验将感温包浸在0℃或12℃恒温槽中,内平衡阀从出口侧,外平衡阀从平衡侧作0 MPa~0.4 MPa的反复加压,各压力的保压时间为一个循环的20%以上,每分钟循环次数为10~15次,共进行10万次循环试验。
7.2.12 耐振动性试验用不会使毛细管和外平衡管产生共振的方法将膨胀阀阀体部固定在加振台上,以加振频率为33.3 Hz、振动加速度为44.1 m/s2作振动(全振幅为2 mm),振动时间为:上下方向4h,左右、前后方向各2h。
7.2.13 耐冷热冲击性试验以室温——高温——室温——低温的变化为1个循环,反复进行10个循环,在室温下放置20 min后,进行6.13规定的试验。