汽车蒙皮工艺
铝合金车身客车蒙皮接缝处理工艺方法研究
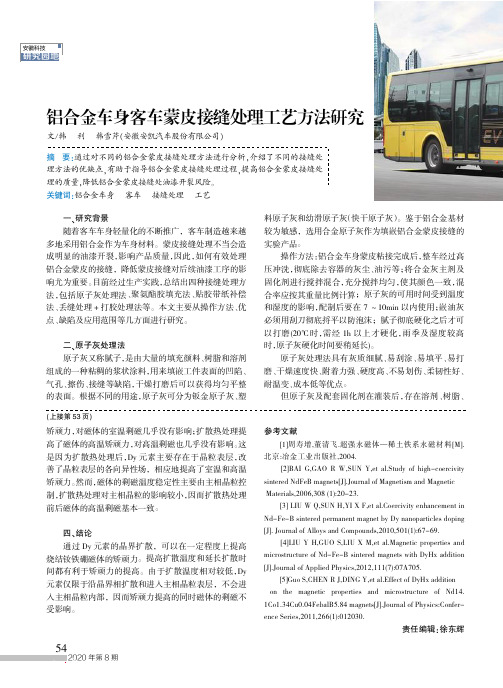
2020年第8期一、研究背景随着客车车身轻量化的不断推广,客车制造越来越多地采用铝合金作为车身材料。
蒙皮接缝处理不当会造成明显的油漆开裂,影响产品质量,因此,如何有效处理铝合金蒙皮的接缝,降低蒙皮接缝对后续油漆工序的影响尤为重要。
目前经过生产实践,总结出四种接缝处理方法,包括原子灰处理法、聚氨酯胶填充法、贴胶带纸补偿法、丢缝处理+打胶处理法等。
本文主要从操作方法、优点、缺陷及应用范围等几方面进行研究。
二、原子灰处理法原子灰又称腻子,是由大量的填充颜料、树脂和溶剂组成的一种粘稠的浆状涂料,用来填嵌工件表面的凹陷、气孔、擦伤、接缝等缺陷,干燥打磨后可以获得均匀平整的表面。
根据不同的用途,原子灰可分为钣金原子灰、塑料原子灰和幼滑原子灰(快干原子灰)。
鉴于铝合金基材较为敏感,选用合金原子灰作为填嵌铝合金蒙皮接缝的实验产品。
操作方法:铝合金车身蒙皮粘接完成后,整车经过高压冲洗,彻底除去容器的灰尘、油污等;将合金灰主剂及固化剂进行搅拌混合,充分搅拌均匀,使其颜色一致,混合率应按其重量比例计算;原子灰的可用时间受到温度和湿度的影响,配制后要在7~10min 以内使用;嵌油灰必须用刮刀彻底捋平以防泡沫;腻子彻底硬化之后才可以打磨(20℃时,需经1h 以上才硬化,雨季及湿度较高时,原子灰硬化时间要稍延长)。
原子灰处理法具有灰质细腻、易刮涂、易填平、易打磨、干燥速度快、附着力强、硬度高、不易划伤、柔韧性好、耐温变、成本低等优点。
但原子灰及配套固化剂在灌装后,存在溶剂、树脂、矫顽力,对磁体的室温剩磁几乎没有影响;扩散热处理提高了磁体的高温矫顽力,对高温剩磁也几乎没有影响。
这是因为扩散热处理后,Dy 元素主要存在于晶粒表层,改善了晶粒表层的各向异性场,相应地提高了室温和高温矫顽力。
然而,磁体的剩磁温度稳定性主要由主相晶粒控制,扩散热处理对主相晶粒的影响较小,因而扩散热处理前后磁体的高温剩磁基本一致。
四、结论通过Dy 元素的晶界扩散,可以在一定程度上提高烧结钕铁硼磁体的矫顽力。
汽车内饰用聚氨酯蒙皮的制备
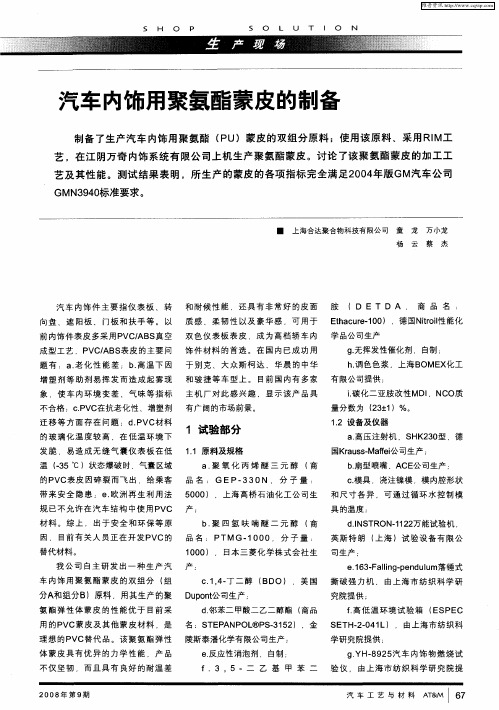
我 公 司 自主 研 发 出一 种 生 产 汽 产 ;
车 内饰 用 聚 氨 酯 蒙 皮 的双 组 分 ( 组
c 14 丁 二 醇 ( . ,一 BDO) .美 国 撕 破 强 力 机 .由 上海 市 纺 织科 学 研 究院提供 ;
f高 低 温 环 境试 验 箱 ( SPEC . E
GMN 9 0 3 4 标准 要求 。
一 上海合 达聚合物 科技有 限公 司 童
杨
龙 万小 龙
云 蔡 杰
汽 车 内饰 件 主要 பைடு நூலகம் 仪 表 板 、转 和耐 候 性 能 .还 具 有 非 常 好 的皮 面 胺 (D E T D A , 商 品 名 : 向盘 、遮 阳板 、 门板 和 扶手 等 。 以 质 感 、柔 韧 性 以及 豪华 感 .可 用于 E h c r. 0 t a ue 1 0).德 国Niol ti r 性能化
测 定 ;拉 伸 强 度 和 断 裂 伸 长 率 按 不均匀 , 物料 容易流到模 具最底端 ,
I 2. SO5 72:1 9 测 定 ;撕裂 强度按 给后 续工艺 带来 不便 。A 3 9 组分 料温 一
13 组分A和B 制备 . 的
生 产 汽 车 内饰 用聚 氯 酯 蒙 皮 的 I03 — :2 0  ̄ 定 。 S 42 0 7
量分数 为 (3 1 2 + )%。
迁 移 等 方 面存 在 问题 :d P C 料 .V 材
的 玻 璃 化 温 度较 高 .在 低 温环 境 下
1 试验部分
12 设备及仪器 -
a 高压 注射机 ,S 2 0 ,德 . HK 3 型 国K a s . f i ru sMaf 公司生产 : e
带 来 安 全 隐 患 :e. 欧洲 再 生利 用 法 5 0 0 0) .上 海高 桥 石油 化 工公 司生 和 尺 寸各 异 .可通 过 循 环 水 控制 模 规 已 不 允许 在 汽 车结 构 中使 用P 产 ; VC
客车制造工艺技术

第二章冲压工艺与车身零部件制造技术一、冲压基本工序冲压:利用模具和冲压设备使薄板料分离和变形的工序。
冲压设备:压力机、冲床成形原理:冲压时材料受应力超过剪切强度;变形时使材料受应力超过屈服极限,形状和轮廓决定于模具凸凹模形状客车冲压工艺主要用于客车车身覆盖件、底盘车架完全成型件的制作。
常用的基本工序为:冲裁、弯曲、拉伸、成型。
冲压按加工性质的不同,可以分为两大类型。
(1)分离工序(2)成型工序二、蒙皮和梁的冲压工序1、蒙皮的冲压工艺,通常都是由拉伸、修边、翻边三个基本工序组成,有的还需要落料或冲孔,有时根据需要和可能可以将一些工序合并,如修边冲孔、修边翻边等。
落料工序是为了获得拉伸工序所需的毛坯。
拉伸工艺是覆盖件(蒙皮)冲压的关键工序,覆盖件(蒙皮)的形状大部分是由拉伸工序形成的。
修边工序是为了切除拉伸件的工艺补充部分。
翻边工序是在修边工序之后,使覆盖件边缘的竖边成型。
冲孔工序是加工覆盖件的孔洞,一般在拉伸工序之后。
2、梁的冲压工序(1)纵梁的下料纵梁下料可采用剪板机的剪切、丙烷切割机、等离子切割机和激光切割机的切割等方法。
其中剪板机是广泛采用的下料设备,具有使用方便、送料简单、剪切速度快、精度高,能剪切交款的板料。
(2)纵梁的孔加工冲孔工序经常是采用液压机和冲模完成。
在小批量生产中长采用钻模在钻床上进行加工。
(3)纵梁的成型主要有三种方法(a)分成三段或四段成型分段处精度差(b)压弯成型构成一个大的30000KN或40000KN的压力机,整体成型。
(c)对于等截面纵梁,用折边机进行折弯成型(等截面纵梁,折边圆角精度差)。
三、连续模概念:连续模又称级进模,在压力机一次行程中,在不同工位上连续冲出一个或多个制件。
复合模概念:几个工序能同时在一个工位上完成的冲压模具称为复合模。
复合模的优点是结构紧凑,生产效率高,工作精度高,安全可靠。
控制方式:开环,闭环开环控制:计算机按照成形要求发指令,回弹的影响不实时考虑。
复合材料蒙皮工艺
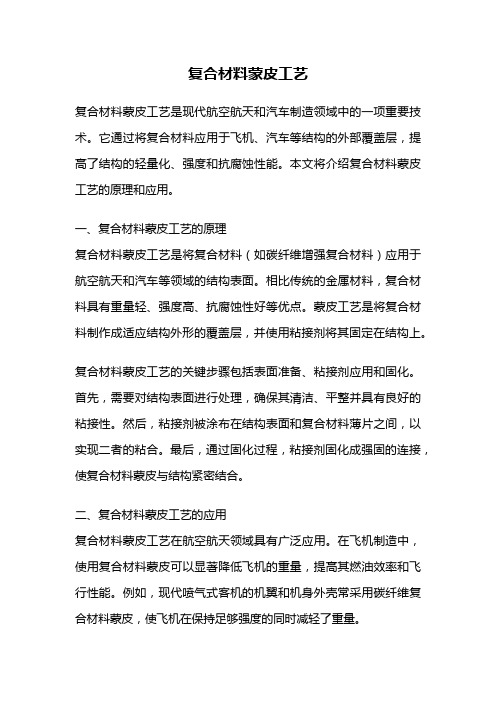
复合材料蒙皮工艺复合材料蒙皮工艺是现代航空航天和汽车制造领域中的一项重要技术。
它通过将复合材料应用于飞机、汽车等结构的外部覆盖层,提高了结构的轻量化、强度和抗腐蚀性能。
本文将介绍复合材料蒙皮工艺的原理和应用。
一、复合材料蒙皮工艺的原理复合材料蒙皮工艺是将复合材料(如碳纤维增强复合材料)应用于航空航天和汽车等领域的结构表面。
相比传统的金属材料,复合材料具有重量轻、强度高、抗腐蚀性好等优点。
蒙皮工艺是将复合材料制作成适应结构外形的覆盖层,并使用粘接剂将其固定在结构上。
复合材料蒙皮工艺的关键步骤包括表面准备、粘接剂应用和固化。
首先,需要对结构表面进行处理,确保其清洁、平整并具有良好的粘接性。
然后,粘接剂被涂布在结构表面和复合材料薄片之间,以实现二者的粘合。
最后,通过固化过程,粘接剂固化成强固的连接,使复合材料蒙皮与结构紧密结合。
二、复合材料蒙皮工艺的应用复合材料蒙皮工艺在航空航天领域具有广泛应用。
在飞机制造中,使用复合材料蒙皮可以显著降低飞机的重量,提高其燃油效率和飞行性能。
例如,现代喷气式客机的机翼和机身外壳常采用碳纤维复合材料蒙皮,使飞机在保持足够强度的同时减轻了重量。
在汽车制造中,复合材料蒙皮也得到了广泛应用。
与传统的金属外壳相比,复合材料蒙皮可以降低汽车的整体重量,提高燃油经济性和行驶稳定性。
此外,复合材料蒙皮还具有较好的抗腐蚀性能,可以延长汽车的使用寿命。
许多高端汽车品牌已开始采用复合材料蒙皮,提升汽车的性能和品质。
三、复合材料蒙皮工艺的优势和挑战复合材料蒙皮工艺相比传统的金属蒙皮工艺具有许多优势。
首先,复合材料的轻量化特性可以减轻结构的重量,提高整体性能。
其次,复合材料的强度高,可以提供更好的结构强度和抗冲击性能。
此外,复合材料具有较好的抗腐蚀性能,可以延长结构的使用寿命。
然而,复合材料蒙皮工艺也面临一些挑战。
首先,复合材料的成本相对较高,制造过程需要更多的专业设备和技术。
其次,复合材料的制造过程相对复杂,需要严格控制工艺参数和质量检测。
汽车蒙皮工艺

汽车蒙皮工艺汽车蒙皮工艺是汽车制造中至关重要的一步,它决定了汽车外观的美观度、质量的稳定性以及驾驶体验的舒适度。
本文将介绍汽车蒙皮工艺的全面内容,包括蒙皮材料的选择、蒙皮设计的考虑因素以及蒙皮工艺的流程和注意事项。
首先,选择适合的蒙皮材料是汽车蒙皮工艺的基础。
在现代汽车制造中,常用的蒙皮材料包括金属板、塑料板和碳纤维等。
金属板具有高强度和稳定性,适合用于发动机盖以及汽车车身的结构部位;塑料板可以被塑造成各种形状,适用于外观造型的定制和修复;碳纤维是一种轻质而且强度高的材料,常用于高端跑车的蒙皮制作。
其次,蒙皮设计需要考虑多种因素。
首先是外观美观度,蒙皮应能与整车的造型和风格相匹配。
其次是安全性,蒙皮应保证行车中的风阻和风噪较小,同时在碰撞时能够起到保护车内乘客的作用。
最后是使用寿命,蒙皮应具备一定的耐久性,能够适应不同的气候和道路条件,减少维修和更换的频率。
蒙皮工艺的流程包括模具制作、蒙皮成型和安装三个主要环节。
首先,根据汽车设计师的要求,制作蒙皮所需的模具。
模具的制作需要考虑到蒙皮的形状和尺寸,决定了蒙皮的最终外观。
然后,使用适当的工艺方法将蒙皮材料加热、压制或拉伸成型,并利用模具进行成型。
最后,将成型后的蒙皮安装在汽车车身上,确保与车身的吻合度,并采取适当的固定措施,如螺丝或胶水等。
在进行蒙皮工艺时,需要注意一些关键问题。
首先是工艺设备的选用和操作技能的培养,只有掌握了正确的操作方法和技巧,才能保证蒙皮的质量和效果。
其次是注意蒙皮材料的质量和合理的存储方式,以免受潮、变形或老化。
再次是要严格按照工艺流程进行操作,确保每个环节的准确和精细,避免出现错误或质量问题。
总之,汽车蒙皮工艺是一项需要重视和掌握的技术活。
正确选择蒙皮材料、合理考虑设计因素、严格按照工艺流程操作以及注意细节问题,都是保证汽车蒙皮质量的关键。
希望本文对汽车制造和维修行业的从业人员和爱好者有所启发,能够在实践中不断提高自己的技术水平。
大客车蒙皮及骨架检测修复的要点分析
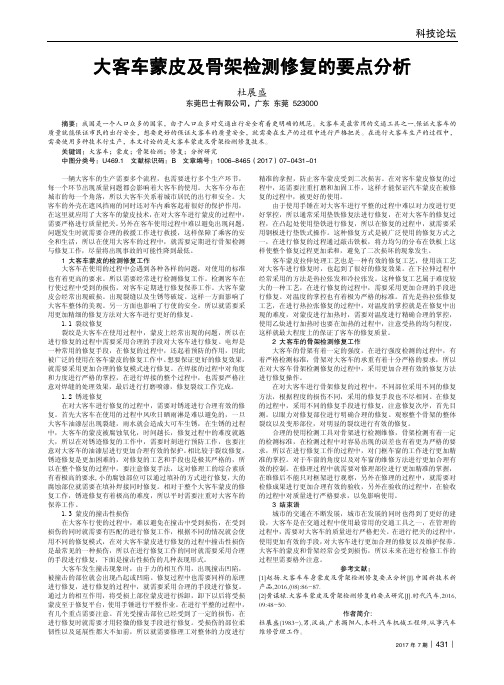
科技论坛2017年7期︱431︱大客车蒙皮及骨架检测修复的要点分析杜展盛东莞巴士有限公司,广东 东莞 523000摘要:我国是一个人口众多的国家,由于人口众多对交通出行安全有着更明确的规范。
大客车是最常用的交通工具之一,保证大客车的质量就能保证市民的出行安全,想要更好的保证大客车的质量安全,就需要在生产的过程中进行严格把关。
在进行大客车生产的过程中,需要使用多种技术行生产,本文讨论的是大客车蒙皮及骨架检测修复技术。
关键词:大客车;蒙皮;骨架检测;修复;分析研究中图分类号:U469.1 文献标识码:B 文章编号:1006-8465(2017)07-0431-01一辆大客车的生产需要多个流程,也需要进行多个生产环节,每一个环节出现质量问题都会影响着大客车的使用。
大客车分布在城市的每一个角落,所以大客车关系着城市居民的出行和安全。
大客车的外壳在遮风挡雨的同时还对车内乘客起着很好的保护作用,在这里就应用了大客车的蒙皮技术,在对大客车进行蒙皮的过程中,需要严格进行质量把关。
另外在客车使用过程中难以避免出现问题,问题发生时就需要合理的救援工作进行救援,这样保障了乘客的安全和生活,所以在使用大客车的过程中,就需要定期进行骨架检测与修复工作,尽量将出现事故的可能性降到最低。
1 大客车蒙皮的检测修复工作 大客车在使用的过程中会遇到各种各样的问题,对使用的标准也有着更高的要求。
所以需要经常进行检测修复工作。
检测客车在行使过程中受到的损伤,对客车定期进行修复保养工作。
大客车蒙皮会经常出现破损。
出现裂缝以及生锈等破绽。
这样一方面影响了大客车整体的美观。
另一方面也影响了行使的安全。
所以就需要采用更加精细的修复方法对大客车进行更好的修复。
1.1 裂纹修复 裂纹是大客车在使用过程中,蒙皮上经常出现的问题,所以在进行修复的过程中需要采用合理的手段对大客车进行修复。
电焊是一种常用的修复手段,在修复的过程中,还起着预防的作用,因此被广泛的使用在客车蒙皮的修复工作中。
浅谈对客车蒙皮技术的研究
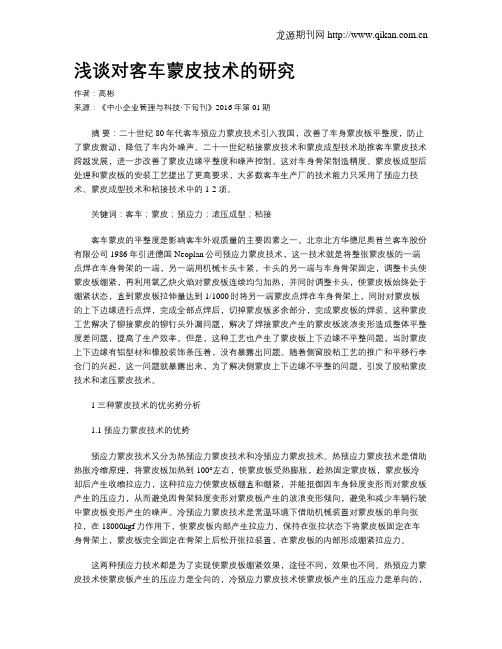
浅谈对客车蒙皮技术的研究作者:高彬来源:《中小企业管理与科技·下旬刊》2016年第01期摘要:二十世纪80年代客车预应力蒙皮技术引入我国,改善了车身蒙皮板平整度,防止了蒙皮震动,降低了车内外噪声。
二十一世纪粘接蒙皮技术和蒙皮成型技术助推客车蒙皮技术跨越发展,进一步改善了蒙皮边缘平整度和噪声控制。
这对车身骨架制造精度、蒙皮板成型后处理和蒙皮板的安装工艺提出了更高要求,大多数客车生产厂的技术能力只采用了预应力技术、蒙皮成型技术和粘接技术中的1-2项。
关键词:客车;蒙皮;预应力;滚压成型;粘接客车蒙皮的平整度是影响客车外观质量的主要因素之一,北京北方华德尼奥普兰客车股份有限公司1986年引进德国Neoplan公司预应力蒙皮技术,这一技术就是将整张蒙皮板的一端点焊在车身骨架的一端,另一端用机械卡头卡紧,卡头的另一端与车身骨架固定,调整卡头使蒙皮板绷紧,再利用氧乙炔火焰对蒙皮板连续均匀加热,并同时调整卡头,使蒙皮板始终处于绷紧状态,直到蒙皮板拉伸量达到1/1000时将另一端蒙皮点焊在车身骨架上,同时对蒙皮板的上下边缘进行点焊,完成全部点焊后,切掉蒙皮板多余部分,完成蒙皮板的焊装。
这种蒙皮工艺解决了铆接蒙皮的铆钉头外漏问题,解决了焊接蒙皮产生的蒙皮板波浪变形造成整体平整度差问题,提高了生产效率。
但是,这种工艺也产生了蒙皮板上下边缘不平整问题,当时蒙皮上下边缘有铝型材和橡胶装饰条压着,没有暴露出问题。
随着侧窗胶粘工艺的推广和平移行李仓门的兴起,这一问题就暴露出来,为了解决侧蒙皮上下边缘不平整的问题,引发了胶粘蒙皮技术和滚压蒙皮技术。
1 三种蒙皮技术的优劣势分析1.1 预应力蒙皮技术的优势预应力蒙皮技术又分为热预应力蒙皮技术和冷预应力蒙皮技术。
热预应力蒙皮技术是借助热胀冷缩原理,将蒙皮板加热到100°左右,使蒙皮板受热膨胀,趁热固定蒙皮板,蒙皮板冷却后产生收缩拉应力,这种拉应力使蒙皮板绷直和绷紧,并能抵御因车身轻度变形而对蒙皮板产生的压应力,从而避免因骨架轻度变形对蒙皮板产生的波浪变形倾向,避免和减少车辆行驶中蒙皮板变形产生的噪声。
蒙皮拉形工艺的基本原理
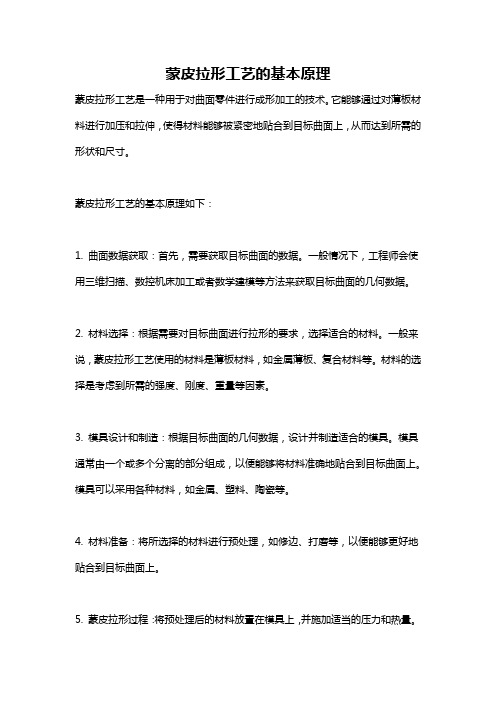
蒙皮拉形工艺的基本原理蒙皮拉形工艺是一种用于对曲面零件进行成形加工的技术。
它能够通过对薄板材料进行加压和拉伸,使得材料能够被紧密地贴合到目标曲面上,从而达到所需的形状和尺寸。
蒙皮拉形工艺的基本原理如下:1. 曲面数据获取:首先,需要获取目标曲面的数据。
一般情况下,工程师会使用三维扫描、数控机床加工或者数学建模等方法来获取目标曲面的几何数据。
2. 材料选择:根据需要对目标曲面进行拉形的要求,选择适合的材料。
一般来说,蒙皮拉形工艺使用的材料是薄板材料,如金属薄板、复合材料等。
材料的选择是考虑到所需的强度、刚度、重量等因素。
3. 模具设计和制造:根据目标曲面的几何数据,设计并制造适合的模具。
模具通常由一个或多个分离的部分组成,以便能够将材料准确地贴合到目标曲面上。
模具可以采用各种材料,如金属、塑料、陶瓷等。
4. 材料准备:将所选择的材料进行预处理,如修边、打磨等,以便能够更好地贴合到目标曲面上。
5. 蒙皮拉形过程:将预处理后的材料放置在模具上,并施加适当的压力和热量。
压力和热量的作用会使得材料发生可塑变形,并贴合到模具的几何形状上。
通常情况下,蒙皮拉形过程需要在控制的恒定温度和湿度条件下进行,以保证成形零件的质量。
6. 修饰和加工:如果需要,根据实际需要对成形后的零件进行修饰和加工。
这可能包括去除过剩材料、添加额外的结构件、涂装和表面处理等步骤。
蒙皮拉形工艺的优势在于它能够实现高质量、高精度的曲面成形,尤其适用于复杂曲面的制造。
与传统的加工方法相比,蒙皮拉形工艺具有以下优点:1. 节省材料:由于薄板材料能够被紧密地贴合到目标曲面上,蒙皮拉形工艺相对于传统的加工方法可以节省材料。
2. 减少成本和工时:相比于传统的加工方法,蒙皮拉形工艺不需要复杂的夹具和工具,可以减少制造成本和工时。
3. 提高生产效率:蒙皮拉形工艺可以通过自动化和机械化的方式进行,可以提高生产效率和工艺稳定性。
4. 提高产品质量:蒙皮拉形工艺可以实现高精度的曲面成形,能够减少或避免后续加工步骤,从而提高产品质量。
客车蒙皮热涨拉和冷涨拉工艺及设备对比分析
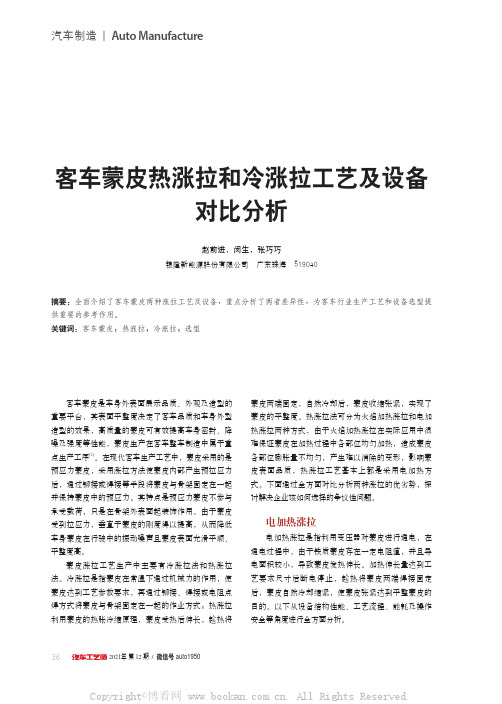
2.46元 结构简单,后期维 保简单、成本低
不受环境影响
无影响,安全性高
适用于铁、铝蒙皮 涨拉焊接和粘接
3)以车身铝蒙皮粘接设计和钢蒙皮焊接设计均兼 顾的客车企业,适合选用冷涨拉工艺及设备,可兼容 铝蒙皮涨拉粘接及铁蒙皮涨拉焊接,且能耗成本低。
结语
本文全面介绍了客车蒙皮两种涨拉设备及工艺,重 点分析了两者差异性,需要结合企业实际情况来确定选 用何种工艺和设备,为选择争议性提供了解决方案。 参考文献: [1] 陈晨.客车蒙皮涨拉工艺简析[J].商用汽车,2008
低
属车间危险源,存 在触电、烫伤危险
适用于钢、铝蒙皮 涨拉焊接
冷涨拉
50 15×5.2×5 架体、推进和拉伸 装置,结构复杂, 基建施工量大 施大拉力使蒙皮 产生弹性变形 仅左右拉动方向
拉力控制使蒙皮处 于所需弹性变形。
涨拉质量稍差, 蒙皮平面度较好 电泳后蒙皮容易发
生松弛情况 表面凹凸不平
45 能耗小,6kW,单 台涨拉能耗成本
图1 电加热涨拉设备
设备关键特点是无需基建施工,其中加热装置采 用三相次级整流变压器作为热源,加热效果好,加热 速度快,次级为直流回路,感抗可忽略。与交流加热 器相比,当输出相同电流时,加热器的功率因数大大 提高,可达0.8~0.9;这种加热器所需视在功率只有 交流加热器视在功率的1/3~1/5,对电网冲击小。直 流加热,避免了交流电幅值下降时冷却所造成的热量 损失,两根电缆间无交变电磁力,使用环境更安全、 更环保。用途广泛,除了能够加热低碳钢、镀层钢板 外,还可以加热涨拉铝蒙皮,为后续产品做基础行业常 规热涨拉设备主要参数详见表1。
客车侧围蒙皮涨拉工艺浅谈
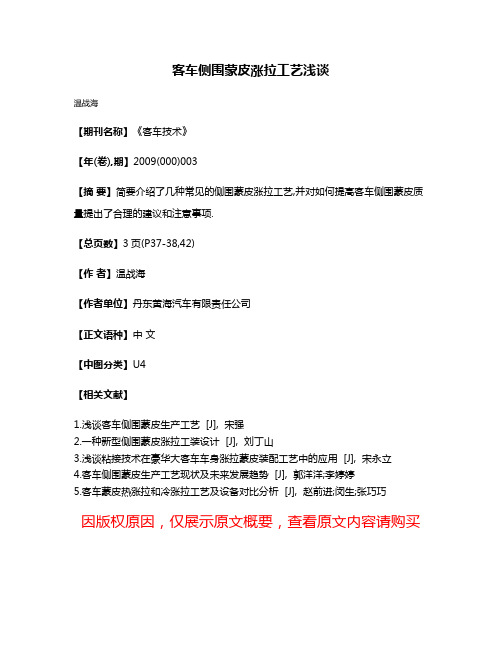
客车侧围蒙皮涨拉工艺浅谈
温战海
【期刊名称】《客车技术》
【年(卷),期】2009(000)003
【摘要】简要介绍了几种常见的侧围蒙皮涨拉工艺,并对如何提高客车侧围蒙皮质量提出了合理的建议和注意事项.
【总页数】3页(P37-38,42)
【作者】温战海
【作者单位】丹东黄海汽车有限责任公司
【正文语种】中文
【中图分类】U4
【相关文献】
1.浅谈客车侧围蒙皮生产工艺 [J], 宋强
2.一种新型侧围蒙皮涨拉工装设计 [J], 刘丁山
3.浅谈粘接技术在豪华大客车车身涨拉蒙皮装配工艺中的应用 [J], 宋永立
4.客车侧围蒙皮生产工艺现状及未来发展趋势 [J], 郭洋洋;李婷婷
5.客车蒙皮热涨拉和冷涨拉工艺及设备对比分析 [J], 赵前进;闵生;张巧巧
因版权原因,仅展示原文概要,查看原文内容请购买。
铝合金蒙皮的技术要求
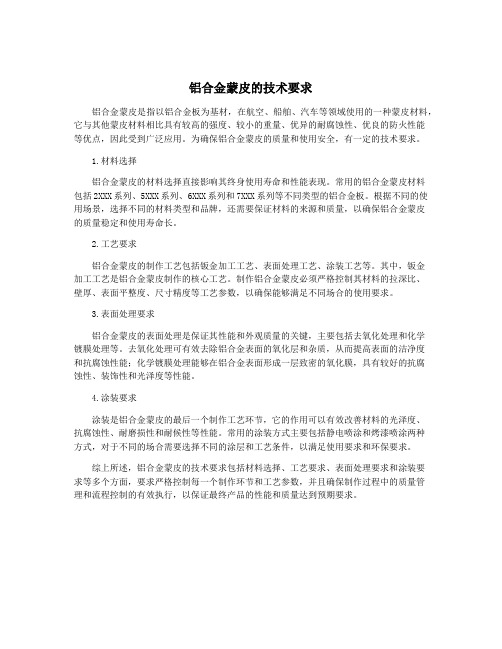
铝合金蒙皮的技术要求铝合金蒙皮是指以铝合金板为基材,在航空、船舶、汽车等领域使用的一种蒙皮材料,它与其他蒙皮材料相比具有较高的强度、较小的重量、优异的耐腐蚀性、优良的防火性能等优点,因此受到广泛应用。
为确保铝合金蒙皮的质量和使用安全,有一定的技术要求。
1.材料选择铝合金蒙皮的材料选择直接影响其终身使用寿命和性能表现。
常用的铝合金蒙皮材料包括2XXX系列、5XXX系列、6XXX系列和7XXX系列等不同类型的铝合金板。
根据不同的使用场景,选择不同的材料类型和品牌,还需要保证材料的来源和质量,以确保铝合金蒙皮的质量稳定和使用寿命长。
2.工艺要求铝合金蒙皮的制作工艺包括钣金加工工艺、表面处理工艺、涂装工艺等。
其中,钣金加工工艺是铝合金蒙皮制作的核心工艺。
制作铝合金蒙皮必须严格控制其材料的拉深比、壁厚、表面平整度、尺寸精度等工艺参数,以确保能够满足不同场合的使用要求。
3.表面处理要求铝合金蒙皮的表面处理是保证其性能和外观质量的关键,主要包括去氧化处理和化学镀膜处理等。
去氧化处理可有效去除铝合金表面的氧化层和杂质,从而提高表面的洁净度和抗腐蚀性能;化学镀膜处理能够在铝合金表面形成一层致密的氧化膜,具有较好的抗腐蚀性、装饰性和光泽度等性能。
4.涂装要求涂装是铝合金蒙皮的最后一个制作工艺环节,它的作用可以有效改善材料的光泽度、抗腐蚀性、耐磨损性和耐候性等性能。
常用的涂装方式主要包括静电喷涂和烤漆喷涂两种方式,对于不同的场合需要选择不同的涂层和工艺条件,以满足使用要求和环保要求。
综上所述,铝合金蒙皮的技术要求包括材料选择、工艺要求、表面处理要求和涂装要求等多个方面,要求严格控制每一个制作环节和工艺参数,并且确保制作过程中的质量管理和流程控制的有效执行,以保证最终产品的性能和质量达到预期要求。
大客车车身张拉蒙皮的修理

深凹坑。因此 , 在上述两种 情 况下, 焊点强度都明显降 低。由试验得 , 在采用 “ 强”规范条件下,电流密度 1 F 10 30 / m , / = 2 — 6 A m z在车身外蒙皮采用单面单
=
认为 , 要保证 车身外形平整光滑 、 增加美 感且蒙皮焊 点强度能承受行驶载荷 , 关键在 于蒙皮在点焊时选
个数字并不是绝对不变的, 如果采用的 d 越大, 焊接 时间越短, , 也就要越大。如果外蒙皮改为导电性 则 较好的铝台金, , 要加大为相同厚度低碳钢板的i 则 倍。
2 12 通 电时间 t ..
设 备, 节约运输成本 出发 , 从 采用分段更换 、 挖补等 方法修理外蒙皮, 恢复了车身使用寿命, 同时, 正确掌 握调漆技巧 , 也能恢复 车身外观 , 达到翻新的目的。
维普资讯
汽 车 工 艺 与材 料
A UI M O BI E " O L TECHNO LOG Y & M ATERI AL
・
维
修
・
文章 编 号 :0 3 8 7 2O 1 0 3 0 10 —8 l( 0 2 0 — 0 9 5 J
大客车车 身张拉 蒙皮 的修理
收 稿 日 期 :0 l 1 O 2 0 一1 一 l
作者简介: 吉国光 《9 2 , 上饶 市人 , 14 一) 男. 现任 江西上烧地区汽运 总, 司工程师, 厶 \ 一直从事汽车雏修检验工作。
20 0 2年第 1 蛸
一 39 —
维普资讯
吉 国光 : 客 车 身 张拉 蒙 皮 的修 理 太
为 , +, 。点 焊 时 , 如 果 * 大 , = 越 要 尽量 减小 分流 ,办 法如 下 。 就 越
部 分要消耗在焊接加热开始 前焊件 的变形上 , 即 P《 =P-+ 。 P 其次, P 还随焊件厚度 的 增加、 的
整车车身蒙皮的制作工艺
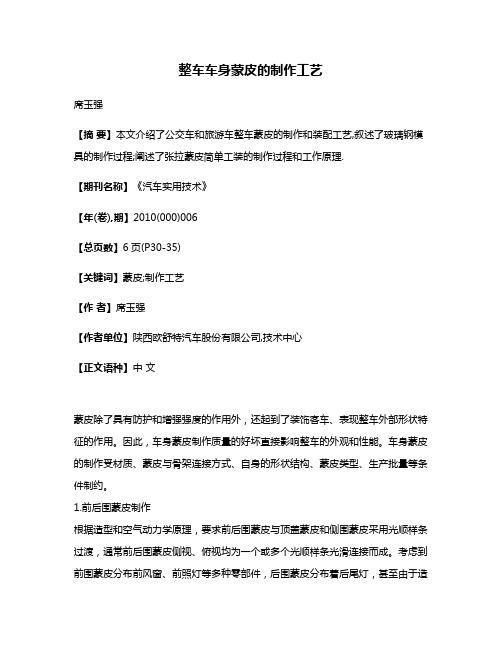
整车车身蒙皮的制作工艺席玉强【摘要】本文介绍了公交车和旅游车整车蒙皮的制作和装配工艺,叙述了玻璃钢模具的制作过程;阐述了张拉蒙皮简单工装的制作过程和工作原理.【期刊名称】《汽车实用技术》【年(卷),期】2010(000)006【总页数】6页(P30-35)【关键词】蒙皮;制作工艺【作者】席玉强【作者单位】陕西欧舒特汽车股份有限公司,技术中心【正文语种】中文蒙皮除了具有防护和增强强度的作用外,还起到了装饰客车、表现整车外部形状特征的作用。
因此,车身蒙皮制作质量的好坏直接影响整车的外观和性能。
车身蒙皮的制作受材质、蒙皮与骨架连接方式、自身的形状结构、蒙皮类型、生产批量等条件制约。
1.前后围蒙皮制作根据造型和空气动力学原理,要求前后围蒙皮与顶盖蒙皮和侧围蒙皮采用光顺样条过渡,通常前后围蒙皮侧视、俯视均为一个或多个光顺样条光滑连接而成。
考虑到前围蒙皮分布前风窗、前照灯等多种零部件,后围蒙皮分布着后尾灯,甚至由于造型需要增设浮雕结构,这些因素决定了前后围蒙皮结构较复杂,是由多种复杂空间曲面组成。
前后围蒙皮材料:1mm冷轧钢板或 2~3mm玻璃钢。
前围蒙皮的成功与否决定了整车的造型效果、驾驶员视野、安全性等。
1.1 前后围蒙皮的结构形式,如图所示:前围蒙皮后围蒙皮前后风窗玻璃与前后围蒙皮的连接有两种形式:(1)、柔性连接:前风窗玻璃与前围蒙皮通过橡胶条连接(如图所示)1-X型密封胶条; 2-橡胶嵌条(2)、直接粘接密封装配法:前风窗玻璃通过粘接剂直接与前围蒙皮粘接起来(如图所示)1-外装饰条;2-粘接剂;3-风窗玻璃;4-内装饰材料;5-风窗框架一般情况下我们采用那个第二种方法前后围蒙皮与骨架的连接形式有:焊接、粘接、铆接。
对采用1mm厚冷轧钢板成型的前后围蒙皮长采用焊接、铆接(凸出部分影响外观,腐蚀源)的连接形式固定,现在基本采用焊接。
对于采用2~3mm厚玻璃钢成型的前后围蒙皮通常采用粘接与铆接相结合的连接形式。
- 1、下载文档前请自行甄别文档内容的完整性,平台不提供额外的编辑、内容补充、找答案等附加服务。
- 2、"仅部分预览"的文档,不可在线预览部分如存在完整性等问题,可反馈申请退款(可完整预览的文档不适用该条件!)。
- 3、如文档侵犯您的权益,请联系客服反馈,我们会尽快为您处理(人工客服工作时间:9:00-18:30)。
汽车蒙皮工艺
汽车蒙皮工艺是指在汽车生产过程中对汽车车身进行覆盖的工艺。
蒙皮工艺旨在保护汽车车身,增加汽车的美观性和耐久性。
常见的汽车蒙皮工艺包括以下几种:
1. 喷涂蒙皮:利用喷涂设备将涂料喷涂在汽车车身表面,形成一层保护膜,使汽车具有防水、防腐、防锈等功能。
2. 贴膜蒙皮:使用专用的汽车膜将汽车车身进行贴膜,可以改变汽车的颜色、纹理和光泽,同时还能起到保护车身的作用。
3. 软包蒙皮:通过将汽车车身上的部位进行软包覆盖,使用各种材质的软包材料,使汽车更加柔软和舒适。
4. 金属蒙皮:使用金属材料,如铝合金、不锈钢等,覆盖在汽车车身上,提高车身的强度和耐久性。
5. 颜色涂装蒙皮:在汽车车身表面进行彩绘和涂装,通过不同颜色和图案的涂装,使汽车具有更多的个性和艺术感。
汽车蒙皮工艺的选择取决于汽车制造商的设计需求和消费者对汽车外观的喜好。
不同的蒙皮工艺可以给车辆带来不同的效果和使用体验。