1危险化学品企业的安全风险辩识分级管控标准
危险化学品企业安全风险辩识分级管控标准
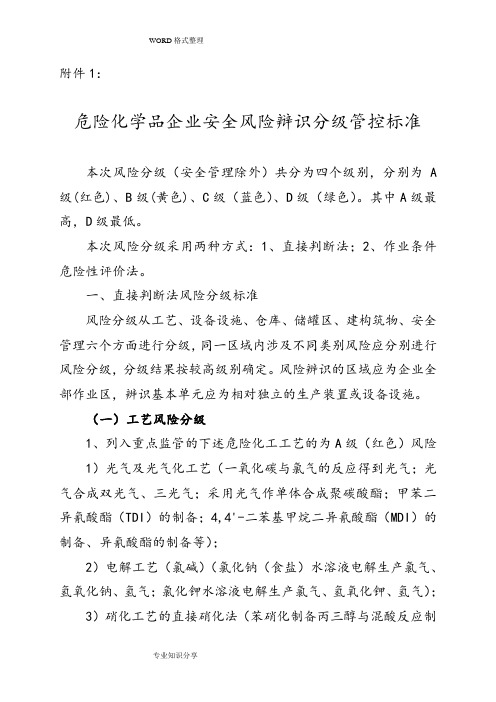
附件1:危险化学品企业安全风险辩识分级管控标准本次风险分级(安全管理除外)共分为四个级别,分别为A 级(红色)、B级(黄色)、C级(蓝色)、D级(绿色)。
其中A级最高,D级最低。
本次风险分级采用两种方式:1、直接判断法;2、作业条件危险性评价法。
一、直接判断法风险分级标准风险分级从工艺、设备设施、仓库、储罐区、建构筑物、安全管理六个方面进行分级,同一区域内涉及不同类别风险应分别进行风险分级,分级结果按较高级别确定。
风险辨识的区域应为企业全部作业区,辨识基本单元应为相对独立的生产装置或设备设施。
(一)工艺风险分级1、列入重点监管的下述危险化工工艺的为A级(红色)风险1)光气及光气化工艺(一氧化碳与氯气的反应得到光气;光气合成双光气、三光气;采用光气作单体合成聚碳酸酯;甲苯二异氰酸酯(TDI)的制备;4,4'-二苯基甲烷二异氰酸酯(MDI)的制备、异氰酸酯的制备等);2)电解工艺(氯碱)(氯化钠(食盐)水溶液电解生产氯气、氢氧化钠、氢气;氯化钾水溶液电解生产氯气、氢氧化钾、氢气);3)硝化工艺的直接硝化法(苯硝化制备丙三醇与混酸反应制备硝酸甘油;氯苯硝化制备邻硝基氯苯、对硝基氯苯;苯硝化制备硝基苯;蒽醌硝化制备1-硝基蒽醌;甲苯硝化生产三硝基甲苯;硝酸胍、硝基胍的制备; 浓硝酸、亚硝酸钠和甲醇制备亚硝酸甲酯;丙烷等烷烃与硝酸通过气相反应制备硝基烷烃等。
);4)合成氨工艺(节能AMV法;德士古水煤浆加压气化法;凯洛格法;甲醇与合成氨联合生产的联醇法;纯碱与合成氨联合生产的联碱法;采用变换催化剂、氧化锌脱硫剂和甲烷催化剂的“三催化”气体净化法等。
);5)新型煤化工工艺(煤制油(甲醇制汽油、费-托合成油)、煤制烯烃(甲醇制烯烃)、煤制二甲醚、煤制乙二醇(合成气制乙二醇)、煤制甲烷气(煤气甲烷化)、煤制甲醇、甲醇制醋酸等工艺)6)聚合工艺(聚烯烃生产;聚氯乙烯生产;合成纤维生产;橡胶生产;乳液生产;氟化物聚合);7)加氢工艺(不饱和炔烃、烯烃的三键和双键加氢;芳烃加氢;含氧化合物加氢;含氮化合物加氢;油品加氢。
危险化学品企业安全风险分级管控实施指南

危险化学品企业安全风险分级管控实施指南一、安全风险分级管控的重要性危险化学品企业的安全管理是保障企业正常生产和员工身体安全的重要工作。
对于危险化学品企业而言,安全风险是一直存在的,合理的风险管控可以降低事故的发生概率,减小事故对企业和社会的影响。
因此,实施危险化学品企业安全风险分级管控是非常必要的。
二、危险化学品企业安全风险分级管控的原则1.全员参与:危险化学品企业的安全责任应当由全员共同承担,要求所有员工都应当熟悉危险化学品的性质、危险性和相应的应急措施。
2.风险主体:危险化学品企业应明确风险主体,确定责任人并明确分工,建立有效的沟通机制和信息共享平台。
3.风险评估:对危险化学品的风险进行全面、科学的评估,确定其可能造成的危害程度和可能发生的频率。
4.风险控制:根据风险评估的结果,制定相应的风险控制措施,采取必要的防范措施和预防措施,确保危险化学品的安全生产。
5.应急准备:建立健全的应急预案和应急救援体系,培训员工具备应急处置能力,确保在事故发生时能够有效、迅速地响应和处置。
三、危险化学品企业安全风险分级管控的步骤1.风险识别:对企业所涉及的危险化学品进行全面的识别和评估,包括危险品种类、存储位置、数量等信息。
2.风险评估:根据识别的危险化学品信息,结合工艺过程、设备状态等因素,进行危险化学品的风险评估,包括危险性评价和可能造成的事故类型。
3.风险分级:根据风险评估的结果,对危险化学品进行分级,将其划分为底风险、中风险和高风险等级,以便采取相应的控制措施。
4.风险管控:根据风险分级结果,制定相应的管控措施,并落实到人员、设备、操作、管理等方面,确保危险化学品的安全生产。
5.风险监控:建立风险监控体系,对危险化学品的存储、使用、运输等过程进行监控,及时发现和处理潜在的安全隐患。
6.应急准备:制定完善的应急预案和应急救援措施,培训员工具备应急处置能力,确保能够有效应对突发事故。
7.风险评估与管控的持续改进:定期进行风险评估和管控效果的检查和评估,及时进行改进和优化,确保风险的控制处于良好的状态。
危险化学品企业安全风险辨识分级管控清单

危险化学品企业安全风险辨识分级管控清单一、危险化学品储存风险辨识分级管控清单:1.1储存设施风险辨识:-储存设施的结构、材料及能耗合理性是否满足相关安全标准;-储存设施的容量、设计排放口是否符合危险化学品储存的要求;-储存设施的检测、报警、监控系统是否完善;-储存设施周边区域的环境风险是否受到合理控制。
1.2危险化学品储存管理风险辨识:-储存设施的分类、标识、安全距离是否符合规定;-危险化学品的存放、搬运、装卸是否符合相关规范;-危险化学品储存的温度、湿度、通风是否满足要求;-危险化学品的漏损、泄漏、溢出是否得到及时处理。
1.3危险化学品储存安全防护风险辨识:-储存区域是否设置了灭火器、消防器材,以及灭火系统是否有效;-储存区域的防火间距、防爆设施是否满足规定;-储存区域是否设置了防火隔离带,消防通道是否畅通;-储存设施的防雷、防静电等安全措施是否到位。
二、危险化学品生产风险辨识分级管控清单:2.1生产设备风险辨识:-生产设备的结构、材料是否符合相关安全标准;-生产设备的设计、制造、安装是否符合相关规范;-生产设备的使用、维护、维修是否得到及时处理;-生产设备的自动化、智能化程度及其安全性是否满足要求。
2.2危险化学品生产工艺风险辨识:-生产工艺的原料、配方是否符合相关规范;-生产工艺的温度、压力、流量等参数是否得到有效控制;-生产工艺的步骤、工序是否符合相关规定;-危险化学品的反应、中间体的储存是否得到及时处理。
2.3危险化学品生产安全防护风险辨识:-生产区域是否设置了相关安全设施,如气体检测、报警、漏损监控等;-生产区域的通风、排气系统是否满足要求;-生产区域的消防设备、灭火系统是否齐全;-生产区域的人员防护措施、应急处置设施是否到位。
三、危险化学品使用风险辨识分级管控清单:3.1使用环境风险辨识:-使用环境的通风、温度、湿度是否符合安全要求;-使用环境的空间大小、防火隔离等措施是否得到有效控制;-使用环境的电气设备、线路是否符合相关安全标准;-使用环境的卫生、清洁、消防通道是否符合要求。
安全风险辨识分级管控管理制度
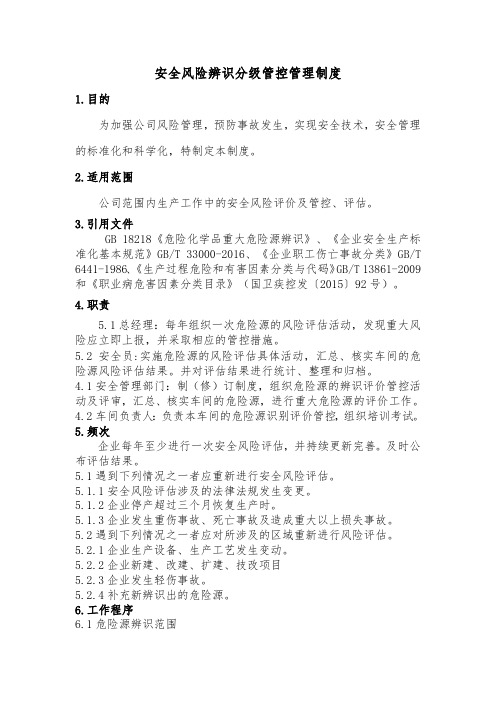
安全风险辨识分级管控管理制度1.目的为加强公司风险管理,预防事故发生,实现安全技术,安全管理的标准化和科学化,特制定本制度。
2.适用范围公司范围内生产工作中的安全风险评价及管控、评估。
3.引用文件GB 18218《危险化学品重大危险源辨识》、《企业安全生产标准化基本规范》GB/T 33000-2016、《企业职工伤亡事故分类》GB/T 6441-1986、《生产过程危险和有害因素分类与代码》GB/T 13861-2009和《职业病危害因素分类目录》(国卫疾控发〔2015〕92号)。
4.职责5.1总经理:每年组织一次危险源的风险评估活动,发现重大风险应立即上报,并采取相应的管控措施。
5.2安全员:实施危险源的风险评估具体活动,汇总、核实车间的危险源风险评估结果。
并对评估结果进行统计、整理和归档。
4.1安全管理部门:制(修)订制度,组织危险源的辨识评价管控活动及评审,汇总、核实车间的危险源,进行重大危险源的评价工作。
4.2车间负责人:负责本车间的危险源识别评价管控,组织培训考试。
5.频次企业每年至少进行一次安全风险评估,并持续更新完善。
及时公布评估结果。
5.1遇到下列情况之一者应重新进行安全风险评估。
5.1.1安全风险评估涉及的法律法规发生变更。
5.1.2企业停产超过三个月恢复生产时。
5.1.3企业发生重伤事故、死亡事故及造成重大以上损失事故。
5.2遇到下列情况之一者应对所涉及的区域重新进行风险评估。
5.2.1企业生产设备、生产工艺发生变动。
5.2.2企业新建、改建、扩建、技改项目5.2.3企业发生轻伤事故。
5.2.4补充新辨识出的危险源。
6.工作程序6.1危险源辨识范围6.1.1涵盖全公司所有范围。
6.1.2所有人员,包括部门员工、相关方。
6.1.3所有活动,指常规活动和非常规活动。
6.1.4所有设施,包括(自有的和租用的)建筑物、机械设备和物资材料等。
6.2危险源识别条件6.2.1辨识时应充分考虑三种状态,即:正常态:指正常、持续的生产运行;异常态:指生产时的开机、停机、检修等情况;紧急态:指发生事故等重大突发情况。
危险化学品企业安全风险辩识分级和隐患排查治理分级管控标准

危险化学品企业安全风险辩识分级管控标准本次风险分级(安全管理除外)共分为四个级别,分别为A 级(红色)、B级(橙色)、C级(黄色)、D级(蓝色)。
其中A级最高,D级最低。
本次风险分级采用两种方式:1、直接判断法;2、作业条件危险性评价法。
一、直接判断法风险分级标准风险分级从工艺、设备设施、仓库、储罐区、建构筑物、安全管理六个方面进行分级,同一区域内涉及不同类别风险应分别进行风险分级,分级结果按较高级别确定。
风险辨识的区域应为企业全部作业区,辨识基本单元应为相对独立的生产装置或设备设施。
(一)工艺风险分级1、列入重点监管的下述危险化工工艺的为A级(红色)风险1)光气及光气化工艺(一氧化碳与氯气的反应得到光气;光气合成双光气、三光气;采用光气作单体合成聚碳酸酯;甲苯二异氰酸酯(TDI)的制备;4,4'-二苯基甲烷二异氰酸酯(MDI)的制备、异氰酸酯的制备等);2)电解工艺(氯碱)(氯化钠(食盐)水溶液电解生产氯气、氢氧化钠、氢气;氯化钾水溶液电解生产氯气、氢氧化钾、氢气);3)硝化工艺的直接硝化法(苯硝化制备丙三醇与混酸反应制备硝酸甘油;氯苯硝化制备邻硝基氯苯、对硝基氯苯;苯硝化制备硝基苯;蒽醌硝化制备1-硝基蒽醌;甲苯硝化生产三硝基甲苯;硝酸胍、硝基胍的制备; 浓硝酸、亚硝酸钠和甲醇制备亚硝酸甲酯;丙烷等烷烃与硝酸通过气相反应制备硝基烷烃等。
);4)合成氨工艺(节能AMV法;德士古水煤浆加压气化法;凯洛格法;甲醇与合成氨联合生产的联醇法;纯碱与合成氨联合生产的联碱法;采用变换催化剂、氧化锌脱硫剂和甲烷催化剂的“三催化”气体净化法等。
);5)新型煤化工工艺(煤制油(甲醇制汽油、费-托合成油)、煤制烯烃(甲醇制烯烃)、煤制二甲醚、煤制乙二醇(合成气制乙二醇)、煤制甲烷气(煤气甲烷化)、煤制甲醇、甲醇制醋酸等工艺)6)聚合工艺(聚烯烃生产;聚氯乙烯生产;合成纤维生产;橡胶生产;乳液生产;氟化物聚合);7)加氢工艺(不饱和炔烃、烯烃的三键和双键加氢;芳烃加氢;含氧化合物加氢;含氮化合物加氢;油品加氢。
危险化学品企业安全风险辩识分级管控标准

危险化学品企业安全风险辩识分级管控标准危险化学品企业安全风险辨识分级管控标准是为了保障危险化学品企业生产运营中的安全,通过科学地评估、划分风险等级,进行有效的管控,从而最大程度地降低生产运营中潜在的安全风险。
一、安全风险辨识1.危险化学品企业应该制定安全风险辨识的流程和标准,明确培训和授权的人员,并通过实践验证该流程和标准的有效性。
2.明确辨识目的的范围和对象,分析可能产生的危险化学品安全风险的来源,包括生产、储存、运输、处理、废弃物处理等方面。
3.辨识的结果需要详细说明危险化学品对工作场所、环境和人的潜在危害,这些信息需要记录并及时更新,以便企业能够识别、理解和管理危险化学品相关风险。
4.危险化学品企业需要开发有效的不同风险等级的安全措施和措施实施方案。
二、安全风险等级划分1.危险化学品企业应根据危险化学品的性质、工艺流程、设备和场所、物流和管理等因素,评定危险化学品的风险等级,并对其进行分类,并将其记录在危险化学品安全风险等级划分表中。
2.根据危化品的物理、化学、毒性、燃爆危险性、放射性等特性,采用表格或图示的形式对不同等级进行标记和标注。
3.在每个等级中,应按照不同类型的危险化学品进行细分,并将其列出。
每种类型的危险化学品,应根据使用频率、数量、贮存位置、工艺流程、设备指标等作适当的评估和分类。
4.在各种危险化学品的风险等级划分中,应考虑每种可能存在的危险场景,例如泄漏、火灾等等,针对不同的罕见情况进行不同的处理。
三、安全风险管控1.在进行安全风险等级划分之后,企业应针对不同等级的安全风险,制定适当的管控措施。
2.对于高风险等级的危险化学品应特别关注,并制定应急预案等安全应对措施。
同时应加强现场管理,保证危险化学品的安全储存。
3.低风险等级的危险化学品,企业可以使用较为简单的管理措施,例如标记危险化学品容器、定期检查和保养等等。
4.安全风险管控的措施应该不断地监测、检查和评估,确保保证其有效性和及时性。
1危险化学品企业安全风险辩识分级管控标准

附件1:危险化学品企业安全风险辩识分级管控标准本次风险分级(安全管理除外)共分为四个级别,分别为A级(红色)、B级(黄色)、C级(蓝色)、D级(绿色).其中A级最高,D级最低。
本次风险分级采用两种方式:1、直接判断法;2、作业条件危险性评价法。
一、直接判断法风险分级标准风险分级从工艺、设备设施、仓库、储罐区、建构筑物、安全管理六个方面进行分级,同一区域内涉及不同类别风险应分别进行风险分级,分级结果按较高级别确定。
风险辨识的区域应为企业全部作业区,辨识基本单元应为相对独立的生产装置或设备设施.(一)工艺风险分级1、列入重点监管的下述危险化工工艺的为A级(红色)风险1)光气及光气化工艺(一氧化碳与氯气的反应得到光气;光气合成双光气、三光气;采用光气作单体合成聚碳酸酯;甲苯二异氰酸酯(TDI)的制备;4,4’—二苯基甲烷二异氰酸酯(MDI)的制备、异氰酸酯的制备等);2)电解工艺(氯碱)(氯化钠(食盐)水溶液电解生产氯气、氢氧化钠、氢气;氯化钾水溶液电解生产氯气、氢氧化钾、氢气);3)硝化工艺的直接硝化法(苯硝化制备丙三醇与混酸反应制备硝酸甘油;氯苯硝化制备邻硝基氯苯、对硝基氯苯;苯硝化制备硝基苯;蒽醌硝化制备1-硝基蒽醌;甲苯硝化生产三硝基甲苯;硝酸胍、硝基胍的制备;浓硝酸、亚硝酸钠和甲醇制备亚硝酸甲酯;丙烷等烷烃与硝酸通过气相反应制备硝基烷烃等。
);4)合成氨工艺(节能AMV法;德士古水煤浆加压气化法;凯洛格法;甲醇与合成氨联合生产的联醇法;纯碱与合成氨联合生产的联碱法;采用变换催化剂、氧化锌脱硫剂和甲烷催化剂的“三催化”气体净化法等。
);5)新型煤化工工艺(煤制油(甲醇制汽油、费-托合成油)、煤制烯烃(甲醇制烯烃)、煤制二甲醚、煤制乙二醇(合成气制乙二醇)、煤制甲烷气(煤气甲烷化)、煤制甲醇、甲醇制醋酸等工艺)6)聚合工艺(聚烯烃生产;聚氯乙烯生产;合成纤维生产;橡胶生产;乳液生产;氟化物聚合);7)加氢工艺(不饱和炔烃、烯烃的三键和双键加氢;芳烃加氢;含氧化合物加氢;含氮化合物加氢;油品加氢。
《危险化学品企业安全风险分级管控实施指南》.docx

危险化学品企业安全风险分级管控实施指南(试用版)目录1.总则............................. - 3 - 2.危害因素辨识. ........................ - 3 -3.风险评价. .......................... - 9 -4.风险控制. .......................... - 12 -5.风险培训. .......................... - 13 -6.风险信息更新. ....................... - 13 -7.工作程序和要求........................ - 13 -8.附件 ............................. - 15 -1. 导则为指导危险化学品企业开展生产安全风险分级管控工作,确保有效管控设备设施和作业过程存在的各类风险,消除事故隐患,杜绝生产安全事故的发生,编制本指南。
本指南介绍了危险化学品企业实施危险源、危险有害因素辨识(以下统称危害因素)、风险分析、风险分级和风险管控的定义、常用方法、工作程序、工作要求等。
1.1 范围适用于危险化学品企业的危害因素识别,生产安全风险分析、评价、分级、管控等全过程的管理工作。
1.2 基本程序化工企业实施风险管控工作,在制定相应的管理制度或程序文件的基础上,一般程序包括:成立组织机构——实施培训——编制文件(作业指导书、台账、记录)——辨识危害因素——风险分析——制定控制措施——判定风险等级——逐级评审与审核——组织全员学习、落实控制措施——组织定期评审、更新风险信息——实施分级管控——实现持续改进。
2. 危害因素辨识2.1危害因素辨识方法(1)工作危害分析法(简称JHA)主要用于对作业活动中存在的危害因素进行辨识。
通过对工作过程的逐步分析,找出存在危险的工作步骤,进行控制和预防,是辨识危害因素及其风险的方法之一。
危险化学品安全风险辩识、评估、分级标准及管控措施(全套)

危险化学品安全风险辩识、评估、分级标准及管控措施(全套)危险化学品安全风险辩识、评估、分级标准及管控措施为建⽴健全危险化学品事故隐患和安全风险分级管控机制,把风险管控挺在隐患前⾯,把隐患排查整治挺在事故前⾯,有效防范和遏制伤亡事故,根据有关法律、法规和政策,结合实际,制定本标准及管控措施。
⼀、编制依据《危险化学品安全管理条例》(国务院令第591号)《国务院关于进⼀步加强企业安全⽣产⼯作的通知》(国发〔2010〕23号)《关于危险化学品企业贯彻落实<国务院关于进⼀步加强企业安全⽣产⼯作的通知>的实施意见》(安监总管三〔2010〕186号)《危险化学品重⼤危险源监督管理暂⾏规定》(国家安全监管总局令第40号)《关于构建安全风险管控和隐患排查治理双重预防机制坚决遏制重特⼤事故的指导意见》(×安委发电〔2016〕5号)《重点监管的危险化⼯⼯艺⽬录》(2013年完整版)《重点监管的危险化学品名录》(2013年完整版)《危险化学品企业事故隐患排查治理实施导则》GB6441《企业职⼯伤亡事故分类标准》—1—GB/T28001《职业健康安全管理体系规范》GB/T13861《⽣产过程危险和有害因素分类与代码》AQ3013《危险化学品从业单位安全标准化通⽤规范》该⾏业涉及的其他标准、规范、⽂件。
⼆、安全风险和隐患辨识与分析(⼀)安全风险辨识。
安全风险辩识是安全风险分级管控的前提和基础,其⽬的是要识别出企业⽣产活动中存在的各种有害因素、可能导致的事故类型及其原因、影响范围和潜在后果。
危险化学品企业开展安全风险辨识时,要充分利⽤现有安全⽣产标准化、安全评价及安全专项研究等⼯作的成果,对这些⼯作中辨识出的危险源(危险有害因素)认真梳理,在此基础上,进⼀步从不同的⾓度和层次挖掘可能存在的风险,拓展风险辨识的深度和⼴度,同时提⾼辨识准确性和效率。
为提⾼安全风险辨识的完整性和准确性,要充分调动员⼯的积极性和创造性,发动全体员⼯特别是⽣产⼀线作业⼈员参与安全风险辨识,利⽤岗位⼈员对作业活动熟悉的优势,对单元中的作业活动、作业环境、设备设施、岗位⼈员、安全管理等⽅⾯进⾏全⾯的安全风险辨识。
企业安全风险分级管控辨识范围和辨识方法确定制度及流程

企业安全风险分级管控辨识范围和辨识方法确定制度及流程安全风险分级管控辨识范围和辨识方法确定制度一、明确辨识范围安全风险分级管控辨识范围应包括以下方面:1.设备设施:包括生产设备、辅助设备、起重机械、压力容器等。
2.作业活动:包括工艺操作、检维修、设备安装、调试、拆除等。
3.人员活动:包括员工培训、作业指导、检查、维护、应急等。
4.作业环境:包括厂区平面布局、建筑物结构、危化品储存与使用场所等。
5.管理过程:包括安全管理体系运行、应急预案与响应等。
二、划分风险类别根据导致事故的原因,可将风险分为以下几类:1.机械伤害:由于机械设备故障或操作失误导致的伤害。
2.电气风险:由于电气故障或违规操作导致的火灾、触电等。
3.自然灾害:由于地震、洪水、台风等自然灾害导致的安全风险。
4.工艺风险:由于工艺流程设计不合理、操作不当等导致的安全风险。
5.职业病危害:由于作业环境中存在的粉尘、噪声、化学毒物等导致的职业病风险。
三、选择适当的辨识方法根据不同的风险类别,可采用以下辨识方法:1.询问与交流:通过与员工和管理人员交流,了解企业生产工艺流程和设备设施运行情况。
2.现场观察:到现场实地观察设备设施运行状况,了解作业环境是否存在安全隐患。
3.检查记录:查阅企业安全检查记录、设备设施维护保养记录等,了解企业安全管理情况和设备设施运行状态。
4.工作危害分析(JHA):针对每个作业步骤进行详细分析,找出潜在的危险因素并制定相应的安全措施。
5.安全检查表(SCL):根据标准要求,列出检查项目并逐项进行打分,以确定设备设施或作业活动的安全状况。
6.危险与可操作性分析(HAZOP):针对特定的设备设施或工艺流程进行详细分析,找出潜在的安全风险并提出相应的解决方案。
7.事件树分析(ETA):通过对已发生事故的原因进行逐层分析,找出导致事故发生的所有可能因素并制定相应的预防措施。
8.故障类型与影响分析(FMEA):针对设备设施或工艺流程中可能发生的故障进行详细分析,找出潜在的危险因素并制定相应的应对措施。
危险化学品企业安全风险分级标准
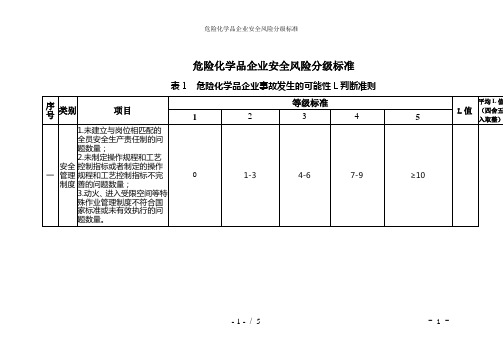
-2-
-2- / 5
危险化学品企业安全风险分级标准
1.使用淘汰落后安全技术
工艺、设备目录列出的工艺
四
设备
及设备的数量; 2.特种设备没有办理使用
0
登记证书,或者未按要求定
期检验的数量。
≥10;
或化工生产装置未
1-2
3-5
6-9
按国家标准要求设
置双电源或者双回
路供电的
五
自控
涉及“两重点一重大”装置 自动控制水平和化工安全
殊作业管理制度不符合国
家标准或未有效执行的问
题数量。
等级标准
2
3
4
1-3
4-6
7-9
平均 L 值
L 值 (四舍五
5
入取整)
≥10
-1- / 5
-1-
危险化学品企业安全风险分级标准
1.主要负责人和安全生产 管理人员未依法经考核合
格的人次;
2.涉及“两重点一重大”装 置的生产、设备及工艺专业
管理人员不具备相应专业
在化工园区 或专门区域 内且满足 13 号公告要求
在化工集中区 或专门区域内 且满足 13 号公
告要求
未在化工园区 (化工集中
区)或专门区 域内,满足 13
号公告要求
在化工园区 (化工集中 区)或专门区 域内,但不满 足 13 号公告 要求
未在化工园区 (化工集中
区)或专门区 域内,且不满 足 13 号公告要
1-2
3-4
5-6
7-9
≥10
八
应急 救援 能力
有应急预案,有应急预案,
应急预案、应急队伍和演练情况
自设专职消 自设专职消防 防应急队伍,应急队伍,未
江苏省化工(危险化学品)企业安全风险评估和分级办法
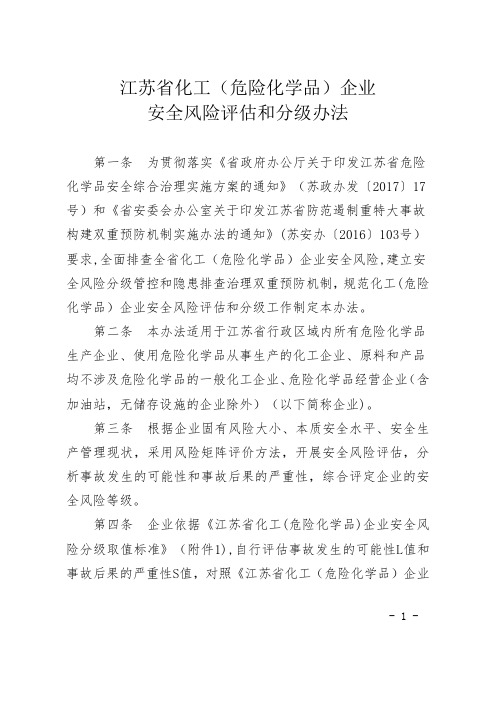
江苏省化工(危险化学品)企业安全风险评估和分级办法第一条为贯彻落实《省政府办公厅关于印发江苏省危险化学品安全综合治理实施方案的通知》(苏政办发〔2017〕17号)和《省安委会办公室关于印发江苏省防范遏制重特大事故构建双重预防机制实施办法的通知》(苏安办〔2016〕103号)要求,全面排查全省化工(危险化学品)企业安全风险,建立安全风险分级管控和隐患排查治理双重预防机制,规范化工(危险化学品)企业安全风险评估和分级工作制定本办法。
第二条本办法适用于江苏省行政区域内所有危险化学品生产企业、使用危险化学品从事生产的化工企业、原料和产品均不涉及危险化学品的一般化工企业、危险化学品经营企业(含加油站,无储存设施的企业除外)(以下简称企业)。
第三条根据企业固有风险大小、本质安全水平、安全生产管理现状,采用风险矩阵评价方法,开展安全风险评估,分析事故发生的可能性和事故后果的严重性,综合评定企业的安全风险等级。
第四条企业依据《江苏省化工(危险化学品)企业安全风险分级取值标准》(附件1),自行评估事故发生的可能性L值和事故后果的严重性S值,对照《江苏省化工(危险化学品)企业- 1 -安全风险矩阵与风险等级判别标准》(附件2),计算风险R值,确定安全风险等级.第五条企业安全风险分为4个等级,从高到低依次划分为红色风险、橙色风险、黄色风险和蓝色风险。
根据评估确定的安全风险等级,将企业依次划分为红色重大风险企业、橙色较大风险企业、黄色一般风险企业、蓝色低风险企业。
第六条在企业安全风险分级的基础上,对存在以下情况的企业进行安全风险等级校正,提高或降低风险等级:1.发生没有人员伤亡的火灾、爆炸事故的,自事故发生之日起提高1个风险等级。
2.发生一般生产安全事故的,自事故发生之日起,提高2个风险等级。
3.发生较大及以上生产安全事故的,自事故发生之日起,直接认定为红色高风险企业。
4.违反安全生产法律法规受到行政处罚5万元及以上的,自处罚生效之日起提高1个风险等级.5.安全生产一级标准化企业,自通过一级标准化公告之日起降低1个风险等级。
化工企业安全风险辨识分级管控清单

化工企业安全风险辨识分级管控清单为了降低化工企业的安全风险,保护人民生命财产安全,化工企业需要开展安全风险辨识分级管控。
针对此,本文提供的化工企业安全风险辨识分级管控清单,供化工企业参考和使用。
1.安全风险辨识分类标准1.1 事故影响范围:人身损害、影响周边环境等1.2 事故概率发生频率:高、中、低1.3 事故严重度:大(重大或重大以上)、中等(一般或一般以上)、小(较小或较小以上)2.化工企业安全风险辨识分级管控清单2.1 高风险区域高风险区域包括:储罐区、化学品输送管道附近、易燃易爆领域、高温区域、高压气体区域、危险场所等。
管控措施:1) 安装监测设备,如气体监测设备、测温设备等。
2) 配备防爆器材和消防设施。
3) 限制非相关人员进入。
4) 制定严格的工艺操作流程,工人进行相关岗位培训,确保操作规范,完全遵守操作流程。
5) 定期开展事故预案演练。
2.2 中等风险区域中等风险区域包括:储蓄区、废水处理区、垃圾处理区、危险废物储存区、危险品堆放区等。
管控措施:1) 配备安全设施,如硫酸铜中毒警示装置、安全防护栏杆等。
2) 制定合理的通风设计,确保室内空气流通。
3) 建设完善的处置系统和危险品处理方案。
4) 分类储存危险品,严禁混储。
5) 加强现场巡检,检查安全系数。
2.3 低风险区域低风险区域包括:办公区域、士工作区域、维护区域等。
管控措施:1) 定期开展安全培训,培训员工应急救援知识。
2) 制定工作规范,保证操作的正确性。
3) 定期开展演习,检查员工应对突发事件的能力。
4) 建立完善的管理制度,定期检查安全资料。
5) 在员工寝室、厕所等场所加装监控设备,预防事故发生。
化工企业安全风险辨识分级管控清单对化工企业来说非常重要。
只有根据实际情况,将实际风险进行分类,针对性地采取相应的管控措施,才能有效地防范和控制安全风险,减少安全事故的发生。
《危险化学品企业安全风险分级管控实施指南》

危险化学品企业安全风险分级管控实施指南(试用版)目录1.总则 .................................................... - 3 - 2.危害因素辨识............................................. - 3 - 3.风险评价................................................. - 9 - 4.风险控制................................................ - 12 - 5.风险培训................................................ - 13 - 6.风险信息更新............................................ - 13 - 7.工作程序和要求.......................................... - 13 - 8.附件 ................................................... - 14 -1.导则为指导危险化学品企业开展生产安全风险分级管控工作,确保有效管控设备设施和作业过程存在的各类风险,消除事故隐患,杜绝生产安全事故的发生,编制本指南。
本指南介绍了危险化学品企业实施危险源、危险有害因素辨识(以下统称危害因素)、风险分析、风险分级和风险管控的定义、常用方法、工作程序、工作要求等。
1.1范围适用于危险化学品企业的危害因素识别,生产安全风险分析、评价、分级、管控等全过程的管理工作。
1.2基本程序化工企业实施风险管控工作,在制定相应的管理制度或程序文件的基础上,一般程序包括:成立组织机构——实施培训——编制文件(作业指导书、台账、记录)——辨识危害因素——风险分析——制定控制措施——判定风险等级——逐级评审与审核——组织全员学习、落实控制措施——组织定期评审、更新风险信息——实施分级管控——实现持续改进。
化学品生产企业安全风险辨识分级管控清单
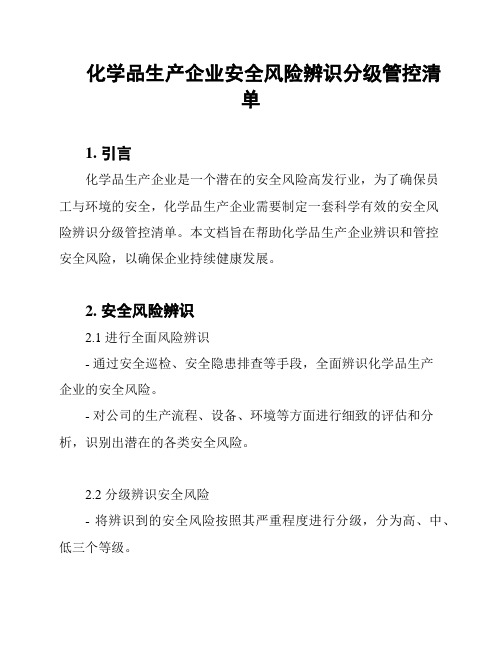
化学品生产企业安全风险辨识分级管控清单1. 引言化学品生产企业是一个潜在的安全风险高发行业,为了确保员工与环境的安全,化学品生产企业需要制定一套科学有效的安全风险辨识分级管控清单。
本文档旨在帮助化学品生产企业辨识和管控安全风险,以确保企业持续健康发展。
2. 安全风险辨识2.1 进行全面风险辨识- 通过安全巡检、安全隐患排查等手段,全面辨识化学品生产企业的安全风险。
- 对公司的生产流程、设备、环境等方面进行细致的评估和分析,识别出潜在的各类安全风险。
2.2 分级辨识安全风险- 将辨识到的安全风险按照其严重程度进行分级,分为高、中、低三个等级。
- 针对每个等级的安全风险,制定相应的管控措施,确保风险在可控范围内。
3. 安全风险管控3.1 高风险管控- 对高风险进行重点管控,优先解决高风险问题,以保障员工与环境的安全。
- 设立专门的责任部门,负责高风险问题的跟踪和解决。
- 制定详细的操作规程和应急预案,确保在高风险事件发生时能够迅速、有效地应对。
3.2 中风险管控- 针对中风险进行适当的管控,确保其不升级成高风险。
- 制定相应的管理措施,如实施系统监测、进行定期检查等,防患于未然。
3.3 低风险管控- 低风险问题可能不会对企业造成重大影响,但也不能忽视。
- 加强对低风险问题的监测和管理,及时采取修复措施,避免因小问题引发大风险。
4. 清单更新与维护4.1 定期更新清单- 清单应定期进行评估和更新,与企业实际情况相结合,及时增加、修改或删除条目。
- 建立清单更新的责任制,确保更新工作的及时性和有效性。
4.2 培训与宣导- 通过培训和宣导,提高员工对安全风险辨识和管控清单的理解和认同。
- 培养员工的安全意识,增强员工对安全风险的识别和应对能力。
5. 结论化学品生产企业安全风险辨识分级管控清单是保障企业持续健康发展的重要工具。
通过全面辨识安全风险,并分级进行管控和更新,可以有效减少安全事故的发生,保障员工和环境的安全。
危险化学品企业安全风险辩识分级管控标准

危险化学品企业安全风险辩识分级管控标准 IMB standardization office【IMB 5AB- IMBK 08- IMB 2C】附件1:危险化学品企业安全风险辩识分级管控标准本次风险分级(安全管理除外)共分为四个级别,分别为A 级(红色)、B级(黄色)、C级(蓝色)、D级(绿色)。
其中A 级最高,D级最低。
本次风险分级采用两种方式:1、直接判断法;2、作业条件危险性评价法。
一、直接判断法风险分级标准风险分级从工艺、设备设施、仓库、储罐区、建构筑物、安全管理六个方面进行分级,同一区域内涉及不同类别风险应分别进行风险分级,分级结果按较高级别确定。
风险辨识的区域应为企业全部作业区,辨识基本单元应为相对独立的生产装置或设备设施。
(一)工艺风险分级1、列入重点监管的下述危险化工工艺的为A级(红色)风险1)光气及光气化工艺(一氧化碳与氯气的反应得到光气;光气合成双光气、三光气;采用光气作单体合成聚碳酸酯;甲苯二异氰酸酯(TDI)的制备;4,4'-二苯基甲烷二异氰酸酯(MDI)的制备、异氰酸酯的制备等);2)电解工艺(氯碱)(氯化钠(食盐)水溶液电解生产氯气、氢氧化钠、氢气;氯化钾水溶液电解生产氯气、氢氧化钾、氢气);3)硝化工艺的直接硝化法(苯硝化制备丙三醇与混酸反应制备硝酸甘油;氯苯硝化制备邻硝基氯苯、对硝基氯苯;苯硝化制备硝基苯;蒽醌硝化制备1-硝基蒽醌;甲苯硝化生产三硝基甲苯;硝酸胍、硝基胍的制备;浓硝酸、亚硝酸钠和甲醇制备亚硝酸甲酯;丙烷等烷烃与硝酸通过气相反应制备硝基烷烃等。
);4)合成氨工艺(节能AMV法;德士古水煤浆加压气化法;凯洛格法;甲醇与合成氨联合生产的联醇法;纯碱与合成氨联合生产的联碱法;采用变换催化剂、氧化锌脱硫剂和甲烷催化剂的“三催化”气体净化法等。
);5)新型煤化工工艺(煤制油(甲醇制汽油、费-托合成油)、煤制烯烃(甲醇制烯烃)、煤制二甲醚、煤制乙二醇(合成气制乙二醇)、煤制甲烷气(煤气甲烷化)、煤制甲醇、甲醇制醋酸等工艺)6)聚合工艺(聚烯烃生产;聚氯乙烯生产;合成纤维生产;橡胶生产;乳液生产;氟化物聚合);7)加氢工艺(不饱和炔烃、烯烃的三键和双键加氢;芳烃加氢;含氧化合物加氢;含氮化合物加氢;油品加氢。
危险化学品企业安全风险分级标准
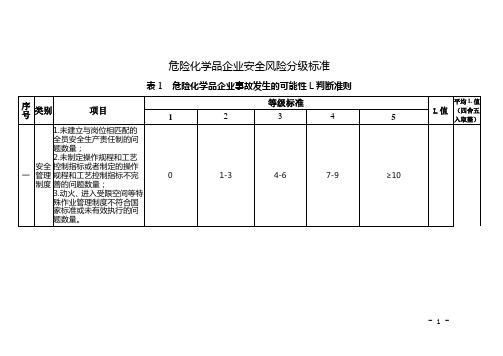
表 1 危险化学品企业事故发生的可能性 L 判断准则
序 号
类别
项目
1
1.未建立与岗位相匹配的
全员安全生产责任制的问
题数量;
2.未制定操作规程和工艺
安全 控制指标或者制定的操作
一 管理 规程和工艺控制指标不完
0
制度 善的问题数量;
3.动火、进入受限空间等特
殊作业管理制度不符合国
生产储存装置由 乙级及以下资质 设计单位进行全 面设计的,不涉 及首次工艺和精 细反应风险评估
生产储存装置 由甲级资质设 计单位全面设 计的,涉及首次 工艺或需要精 细反应风险评 估,已完成论证 或评估
生 由 资 的 艺 反 已 评产 乙 质 , 或 应 完 估涉储 级 全 需 风 成及存 及 面 要 险 论首装 以 设 精 评 证次置 下 计 细 估 或工,首 级 门 论 企 件 全次 人 组 证 业 要 风工 民 织 的 未 求 险艺 政 安 或 按 开 评未 府 全 精 规 展 估经 有 可 细 范 反 的过 关 靠 化 性 应省 部 性 工 文 安
在化工集中区 或专门区域内 且满足 13 号
公告要求
未在化工园区 (化工集中 区)或专门区 域内,满足 13 号公告要求
在化工园区 (化工集中 区)或专门区 域内,但不满 足 13 号公告 要求
未在化工园区 (化工集中
区)或专门区 域内,且不满 足 13 号公告
要求
受风险标准和社会可接受风险
标准(试行)》情况。
涉及且已实现自 控,完成安全仪 表系统评估和完 善工作,满足安 全功能或完整性
等级要求
不涉及且未实 现自控,未设置 独立的安全仪
表系统
企业安全风险辨识与分级管控制度

企业安全风险辨识与分级管控制度一、引言企业安全风险辨识与分级管控制度是企业安全管理的重要组成部分,旨在对企业可能存在的各类安全风险进行辨识与分级管控,以保障企业的正常运营和员工的生命安全。
本制度的目的是通过科学合理的管理措施,降低安全事故的发生概率,最大限度地保护企业资产和员工的安全。
二、辨识安全风险的方法1.概率与影响矩阵法:根据风险的可能性和影响程度分为不同级别,对安全风险进行分类辨识。
2.安全检查与评估法:通过定期进行安全检查和评估,发现和提前预防可能存在的安全风险。
3.经验总结法:通过分析历史安全事故案例,总结经验教训,找出潜在的安全风险。
三、安全风险的辨识与分级管控1.人员安全风险:包括员工生命安全、人为因素引发的事故等。
将人员安全分为员工基本安全、员工职业安全和员工生命安全三个级别进行管控。
-员工基本安全:通过建立健全的劳动保护制度和安全操作培训,提升员工的安全意识和保护能力。
-员工职业安全:通过对各岗位的职业风险进行评估,采取相应的防范措施,如佩戴个人防护装备、定期进行岗位培训等。
-员工生命安全:对于员工生命安全相关的工作环境和工作条件,必须严格按照法律法规要求进行管理,如消防设施、危险化学品管理等。
2.设备安全风险:包括设备故障、设备操作不当等。
将设备安全分为设备质量安全和设备操作安全两个级别进行管控。
-设备质量安全:采购设备时要确保设备的品质可靠,进行设备检测和验收,做好设备日常维护保养工作。
-设备操作安全:通过建立设备操作规程和制定设备操作培训计划,提高员工对设备操作的熟练程度,减少不当操作引发的安全风险。
3.信息安全风险:包括数据泄露、网络攻击等。
将信息安全分为信息资产安全和网络安全两个级别进行管控。
-信息资产安全:建立信息资产管理制度,严格控制数据的访问权限,加强信息加密和备份工作,防止信息泄露和损失。
-网络安全:采取防火墙、入侵检测等技术手段,保护企业内外部网络的安全,定期进行网络安全演练和培训。
- 1、下载文档前请自行甄别文档内容的完整性,平台不提供额外的编辑、内容补充、找答案等附加服务。
- 2、"仅部分预览"的文档,不可在线预览部分如存在完整性等问题,可反馈申请退款(可完整预览的文档不适用该条件!)。
- 3、如文档侵犯您的权益,请联系客服反馈,我们会尽快为您处理(人工客服工作时间:9:00-18:30)。
附件1:危险化学品企业安全风险辩识分级管控标准本次风险分级(安全管理除外)共分为四个级别,分别为A 级(红色)、B级(黄色)、C级(蓝色)、D级(绿色)。
其中A级最高,D级最低。
本次风险分级采用两种方式:1、直接判断法;2、作业条件危险性评价法。
一、直接判断法风险分级标准风险分级从工艺、设备设施、仓库、储罐区、建构筑物、安全管理六个方面进行分级,同一区域内涉及不同类别风险应分别进行风险分级,分级结果按较高级别确定。
风险辨识的区域应为企业全部作业区,辨识基本单元应为相对独立的生产装置或设备设施。
(一)工艺风险分级1、列入重点监管的下述危险化工工艺的为A级(红色)风险1)光气及光气化工艺(一氧化碳与氯气的反应得到光气;光气合成双光气、三光气;采用光气作单体合成聚碳酸酯;甲苯二异氰酸酯(TDI)的制备;4,4'-二苯基甲烷二异氰酸酯(MDI)的制备、异氰酸酯的制备等);2)电解工艺(氯碱)(氯化钠(食盐)水溶液电解生产氯气、氢氧化钠、氢气;氯化钾水溶液电解生产氯气、氢氧化钾、氢气);3)硝化工艺的直接硝化法(苯硝化制备丙三醇与混酸反应制备硝酸甘油;氯苯硝化制备邻硝基氯苯、对硝基氯苯;苯硝化制备硝基苯;蒽醌硝化制备1-硝基蒽醌;甲苯硝化生产三硝基甲苯;硝酸胍、硝基胍的制备; 浓硝酸、亚硝酸钠和甲醇制备亚硝酸甲酯;丙烷等烷烃与硝酸通过气相反应制备硝基烷烃等。
);4)合成氨工艺(节能AMV法;德士古水煤浆加压气化法;凯洛格法;甲醇与合成氨联合生产的联醇法;纯碱与合成氨联合生产的联碱法;采用变换催化剂、氧化锌脱硫剂和甲烷催化剂的“三催化”气体净化法等。
);5)新型煤化工工艺(煤制油(甲醇制汽油、费-托合成油)、煤制烯烃(甲醇制烯烃)、煤制二甲醚、煤制乙二醇(合成气制乙二醇)、煤制甲烷气(煤气甲烷化)、煤制甲醇、甲醇制醋酸等工艺)6)聚合工艺(聚烯烃生产;聚氯乙烯生产;合成纤维生产;橡胶生产;乳液生产;氟化物聚合);7)加氢工艺(不饱和炔烃、烯烃的三键和双键加氢;芳烃加氢;含氧化合物加氢;含氮化合物加氢;油品加氢。
);8)过氧化工艺(双氧水的生产;乙酸在硫酸存在下与双氧水作用,制备过氧乙酸水溶液;酸酐与双氧水作用直接制备过氧二酸;苯甲酰氯与双氧水的碱性溶液作用制备过氧化苯甲酰;异丙苯经空气氧化生产过氧化氢异丙苯;叔丁醇与双氧水制备叔丁基过氧化氢等。
);2、列入重点监管的下述危险化工工艺的为B级(黄色)风险1)氯化工艺(取代氯化;加成氯化;氧氯化;硫与氯反应生成一氯化硫;四氯化钛的制备;黄磷与氯气反应生产三氯化磷、五氯化磷等。
);2)裂解(裂化)工艺(热裂解制烯烃工艺;重油催化裂化制汽油、柴油、丙烯、丁烯;乙苯裂解制苯乙烯;二氟一氯甲烷(HCFC-22)热裂解制得四氟乙烯(TFE);二氟一氯乙烷(HCFC-142b)热裂解制得偏氟乙烯(VDF);四氟乙烯和八氟环丁烷热裂解制得六氟乙烯(HFP)等。
);3)氟化工艺(直接氟化;金属氟化物或氟化氢气体氟化;置换氟化;三氟化硼的制备);4)氧化工艺(乙烯氧化制环氧乙烷;甲醇氧化制备甲醛;对二甲苯氧化制备对苯二甲酸;异丙苯经氧化-酸解联产苯酚和丙酮;环己烷氧化制环己酮;天然气氧化制乙炔;丁烯、丁烷、C4馏分或苯的氧化制顺丁烯二酸酐;邻二甲苯或萘的氧化制备邻苯二甲酸酐;均四甲苯的氧化制备均苯四甲酸二酐;苊的氧化制1,8-萘二甲酸酐;3-甲基吡啶氧化制3-吡啶甲酸(烟酸);4-甲基吡啶氧化制4-吡啶甲酸(异烟酸);2-乙基已醇(异辛醇)氧化制备2-乙基己酸(异辛酸);对氯甲苯氧化制备对氯苯甲醛和对氯苯甲酸;甲苯氧化制备苯甲醛、苯甲酸;对硝基甲苯氧化制备对硝基苯甲酸;环十二醇/酮混合物的开环氧化制备十二碳二酸;环己酮/醇混合物的氧化制己二酸;乙二醛硝酸氧化法合成乙醛酸;丁醛氧化制丁酸;氨氧化制硝酸;克劳斯法气体脱硫;一氧化氮、氧气和甲(乙)醇制备亚硝酸甲(乙)酯;以双氧水或有机过氧化物为氧化剂生产环氧丙烷、环氧氯丙烷。
);5)胺基化工艺(邻硝基氯苯与氨水反应制备邻硝基苯胺;对硝基氯苯与氨水反应制备对硝基苯胺;间甲酚与氯化铵的混合物在催化剂和氨水作用下生成间甲苯胺;甲醇在催化剂和氨气作用下制备甲胺;1-硝基蒽醌与过量的氨水在氯苯中制备1-氨基蒽醌;2,6-蒽醌二磺酸氨解制备2,6-二氨基蒽醌;苯乙烯与胺反应制备N-取代苯乙胺;环氧乙烷或亚乙基亚胺与胺或氨发生开环加成反应,制备氨基乙醇或二胺;甲苯经氨氧化制备苯甲腈;丙烯氨氧化制备丙烯腈;氯氨法生产甲基肼。
);6)磺化工艺(三氧化硫磺化法;共沸去水磺化法;氯磺酸磺化法;烘焙磺化法;亚硫酸盐磺化法);7)重氮化工艺(顺法;反加法;亚硝酰硫酸法;硫酸铜触媒法;盐析法);8)烷基化工艺(C-烷基化反应;N-烷基化反应;O-烷基化反应);9)硝化工艺的间接硝化法和亚硝化法;10)电石生产工艺;11)偶氮化工艺。
3、列入下列化工工艺的为C级(蓝色)风险1)未列入典型化工工艺的烷基化、氧化、磺化和聚合等工艺;2)酯化、加成、中和等中等放热工艺;3)易燃易爆的物质的精馏工艺;4)含易燃易爆溶剂的脱溶工艺;5)变压吸附制氢工艺;4、其它生产工艺为D级(绿色)风险。
(二)设备设施风险分级1、满足下列条件的设备设施属于A级(红色)风险1)操作压力>20MPa的设备设施;2)介质中含有三硝基苯、硝化甘油、硝酸胍、硝化纤维素、硝酸铵(含可燃物≤0.2%)等爆炸品类的设备设施;3)介质中含有氰化氢、二氧化氮、异氰酸甲酯、磷化氢、碳酰氯(光气)的设备设施。
2、满足下列条件的设备设施属于B级(黄色)风险1)操作压力10MPa<P<20MPa 的设备设施;2)介质中含除氰化氢、二氧化氮、异氰酸甲酯、磷化氢、碳酰氯以外的列入《危险化学品目录》(2015版)的剧毒品的设备设施;3)介质中含有煤气的设备设施;4)介质中含甲类可燃气体、液化烃及甲A类液体、甲类固体的设备设施。
3、满足下列条件的设备设施属于C级(蓝色)风险1)操作压力1MPa<P<10MPa 的设备设施;2)介质中含甲B及乙类液体的设备设施;3)介质中含剧毒品以外的急性毒性为类别1、类别2的物质的设备设施。
注:急性毒性分类依据《化学品分类、警示标签和警示性说明安全规范急性毒性》(GB20592-2006)。
物质的火灾分类依据《石油化工设计防火规范》(GB50160-2008)4、其它设备设施属于D级(绿色)风险(三)库区风险分级1、下列条件的库区属于A级(红色)风险危险化学品数量构成一级重大危险源的库区2、下列条件的库区属于B级(黄色)风险危险化学品数量构成二级重大危险源的库区3、下列条件的库区属于C级(蓝色)风险危险化学品数量构成三级、四级重大危险源的库区4、其它库区属于D级(蓝色)风险(四)储罐区风险分级1、下列条件的储罐区属于A级(红色)风险危险化学品数量构成一级重大危险源的储罐区2、下列条件的储罐区属于B级(黄色)风险危险化学品数量构成二级重大危险源的储罐区3、下列条件的储罐区属于C级(蓝色)风险危险化学品数量构成三级、四级重大危险源的储罐区4、其它储罐区属于D级(蓝色)风险(五)建筑物风险分级1、下列情况属于A级(红色)风险1)有爆炸(含粉尘爆炸)或散发有毒气体危险的厂房,且当班操作人员30人以上的。
2、下列情况属于B级(黄色)风险1)有爆炸(含粉尘爆炸)或散发有毒气体危险的厂房,且当班操作人员29人以下10人以上的;2)其它厂房内操作人员30人以上的;3)全厂性高压配电室;4)占地面积大于1000m2的丙类仓库。
3、下列情况属于C级(蓝色)风险1)有爆炸(含粉尘爆炸)或散发有毒气体危险的厂房,且当班操作人员9人以下3人以上的;2)其它厂房内操作人员29人以下10人以上的;3)全厂性低压配电室。
4、其它有火灾爆炸或有毒危险作业厂房建筑属于D级(绿色)风险(六)安全管理风险分级1、下列情况属于A级(红色)风险1)未按规定设置专职安全管理机构和相应数量专职安全管理人员;2)岗位安全(工艺)操作规程和工艺控制指标落实不到位;3)安全管理人员、特种作业人员未经考试合格或未持证上岗;4)未严格执行动火作业、隐患排查等安全管理制度;5)新入厂员工未进行三级安全教育。
2、下列情况属于B级(黄色)风险1)三项制度不完善;2)未配备工艺、设备、仪表专业技术人员;3)仪表操作人员未经考试合格或未持证上岗;4)未按有关规定投入安全生产费用;5)未定期进行事故应急演练。
6)人员教育培训不到位;7)法律、法规识别不及时;8)未定期按规定进行风险评估的;9)事故应急演练走形式。
(七)维修作业分级1、下列情况属于A级(红色)风险1)特殊动火作业、一级动火作业;2)受限空间作业;3)交叉作业;4)高处作业(3人以上)。
2、下列情况属于B级(黄色)风险1)一级吊装作业、二级吊装作业;盲板抽堵作业、断路作业、临时用电作业、动土作业。
3、下列情况属于C级(蓝色)风险其它日常维修作业二、作业条件危险性评价法分级标准风险辨识的区域应为企业全部作业区,辨识基本单元应为岗位或工序。
作业条件危险性评价法,即LEC法(D=LEC),通过对危险源进行L值(发生事故的可能性大小)、E值(暴露于危险环境的频繁程度)和C值(发生事故可能出现的结果)打分之积,得出D值(风险值)。
依据D值大小判定岗位风险级别。
作业条件危险性评价法是对人员在具有潜在危险性环境中作业时危险性进行评价的半定量评价方法。
D值越大,作业条件的危险性就越大。
赋分标准见下表1-表2。
表1 作业条件危险性赋分标准事故发生可能性分值L分值事故发生的可能性分值事故发生的可能性10 完全会被预料到0.5 可以设想,很不可能6 相当可能0.2 极不可能3 可能,但不经常0.1 实际上不可能1 完全意外,很少可能————暴露于危险环境的频繁程度分值E分值暴露于危险环境的频繁程度分值暴露于危险环境的频繁程度10 连续暴露 2 每月暴露一次6 每天工作时间内暴露 1 每年几次暴露3 每周一次或偶然暴露0.5 非常罕见地暴露事故造成的结果分值C分值事故造成的后果分值事故造成的后果10十人以上死亡7 严重伤残40 数人死亡 3 有伤残15 一人死亡 1 轻伤,需救护表2 风险值(D)分级标准序号风险值风险级别1 D≥320A(红色)2 160≤D<320 B(黄色)3 70≤D<160 C(绿色)4 D<70 D(蓝色)三、风险管控措施(一)风险管控原则安全风险采用分级管理的原则,即A级最高,D级最低。
A级安全风险由公司进行管控;B级安全风险由分厂或车间进行管控;C级、D级安全风险由班组进行管控;企业实行挂牌制,A级挂红牌,B级挂黄牌,C级挂蓝牌,D级挂绿牌。