FANUC的进给运动误差补偿方法
FANUC常见问题
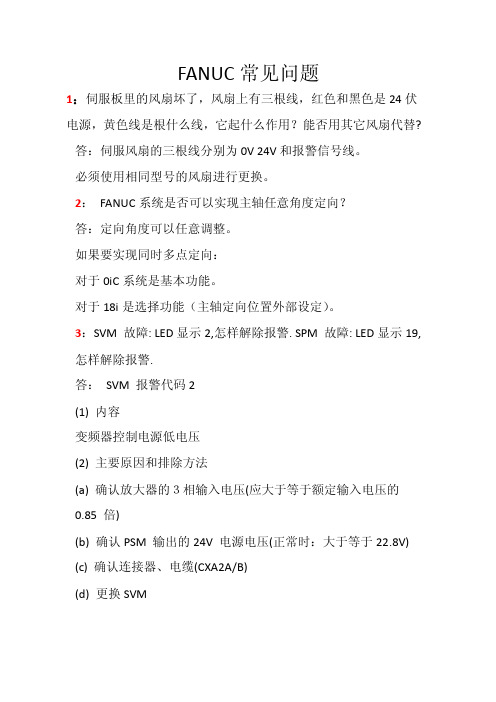
FANUC常见问题1:伺服板里的风扇坏了,风扇上有三根线,红色和黑色是24伏电源,黄色线是根什么线,它起什么作用?能否用其它风扇代替? 答:伺服风扇的三根线分别为0V 24V和报警信号线。
必须使用相同型号的风扇进行更换。
2:FANUC系统是否可以实现主轴任意角度定向?答:定向角度可以任意调整。
如果要实现同时多点定向:对于0iC系统是基本功能。
对于18i是选择功能(主轴定向位置外部设定)。
3:SVM 故障: LED显示2,怎样解除报警. SPM 故障: LED显示19,怎样解除报警.答:SVM 报警代码2(1) 内容变频器控制电源低电压(2) 主要原因和排除方法(a) 确认放大器的3相输入电压(应大于等于额定输入电压的0.85 倍)(b) 确认PSM 输出的24V 电源电压(正常时:大于等于22.8V)(c) 确认连接器、电缆(CXA2A/B)(d) 更换SVMSPM报警代码19、20U 相(报警代码19)、V 相(报警代码20)电流检测电路的偏移电压过大。
通电时进行检测。
发生报警时,请更换SPM。
发生在刚更换SPM 控制印制电路板后时,请确认功率单元与SPM 控制印制电路板之间连接器的插入情况。
4:SVM故障:LED显示2号报警,查资料是内部控制回路用电源电压已下降.或控制印刷版上的时钟已停止.我想问内部控制回路用电源电压是靠电池供电还是供给控制电源供电.通过怎样方法解决?答:内部控制回路用电源电压是靠PSM供给+24V电源供电LED显示2号报警变频器控制电源低电压报警(1) 内容变频器DC 链路部低电压(2) 主要原因和排除方法(a) 确认放大器的3相输入电压(应大于等于额定输入电压的0.85 倍)(b) 确认PSM 输出的24V 电源电压(正常时:大于等于22.8V)(c) 确认连接器、电缆(CXA2A/B)(d) 更换SVM5:取消软极限工作状态是同时按住字母“P”键及“CAN”键起动电源,还是同时按住“POST”键及“CAN”键起动电源.答:按住字母“P”键及“CAN”键起动电源6.空气开关跳下,X,Y,Z三轴显示401报警,稳压电源无输出.当开关打上又正常工作.答:"稳压电源无输出"中的稳压电源是否指+24电源?是否有可能有短路?7. GE fanuc O-M系统的pmc的类型是什么? 2 0-M系统的PMC从EPROM里面读出来,用什么设备? 3 PMC梯形图放在主板那一块EPROM芯片上?答:1。
FANUC数控系统基本参数的操作与设定
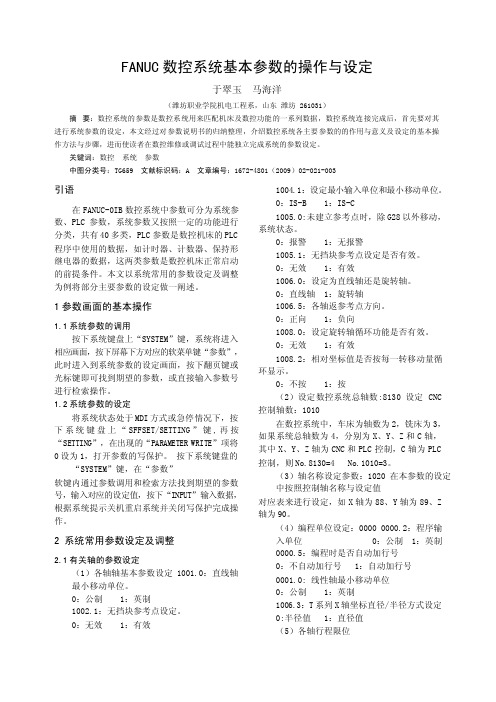
FANUC 数控系统基本参数的操作与设定于翠玉马海洋(潍坊职业学院机电工程系,山东潍坊 261031)摘要:数控系统的参数是数控系统用来匹配机床及数控功能的一系列数据,数控系统连接完成后,首先要对其进行系统参数的设定,本文经过对参数说明书的归纳整理,介绍数控系统各主要参数的的作用与意义及设定的基本操作方法与步骤,进而使读者在数控维修或调试过程中能独立完成系统的参数设定。
关键词:数控系统参数中图分类号:TG659 文献标识码:A 文章编号:1672-4801(2009)02-021-003引语在FANUC-0IB 数控系统中参数可分为系统参数、PLC 参数,系统参数又按照一定的功能进行分类,共有40 多类,PLC 参数是数控机床的PLC 程序中使用的数据,如计时器、计数器、保持形继电器的数据,这两类参数是数控机床正常启动的前提条件。
本文以系统常用的参数设定及调整为例将部分主要参数的设定做一阐述。
1 参数画面的基本操作1.1 系统参数的调用按下系统键盘上“SYSTEM”键,系统将进入相应画面,按下屏幕下方对应的软菜单键“参数”,此时进入到系统参数的设定画面,按下翻页键或光标键即可找到期望的参数,或直接输入参数号进行检索操作。
1.2 系统参数的设定将系统状态处于MDI 方式或急停情况下,按下系统键盘上“SFFSET/SETTING ”键, 再按“SETTING”,在出现的“PARAMETER WRITE”项将0 设为1,打开参数的写保护。
按下系统键盘的“SYSTEM”键,在“参数”软键内通过参数调用和检索方法找到期望的参数号,输入对应的设定值,按下“INPUT”输入数据,根据系统提示关机重启系统并关闭写保护完成操作。
2 系统常用参数设定及调整2.1 有关轴的参数设定(1)各轴轴基本参数设定 1001.0:直线轴最小移动单位。
0:公制1:英制1002.1:无挡块参考点设定。
0:无效1:有效1004.1:设定最小输入单位和最小移动单位。
发那科加工中心四轴旋转误差补偿参数

发那科加工中心四轴旋转误差补偿参数一、发那科加工中心简介发那科(FANUC)是一家全球知名的数控系统制造商,其生产的加工中心广泛应用于各类加工制造领域。
加工中心是集铣削、镗削、钻孔、切削等多种功能于一体的数控机床。
在实际加工过程中,四轴旋转误差补偿技术对于提高加工精度和效率具有重要意义。
二、四轴旋转误差补偿原理四轴旋转误差补偿技术主要是针对加工中心在四轴旋转过程中出现的误差进行实时修正,从而提高加工精度。
该技术通过采集实时数据,对比理论模型与实际运动轨迹,计算出误差值,并实时调整电机驱动信号,使加工部件的运动轨迹尽量接近理论模型。
三、误差补偿参数设置方法1.确定补偿类型:根据加工中心的结构和加工需求,选择合适的补偿类型,如线性补偿、角度补偿等。
2.采集数据:通过测量设备采集加工中心在四轴旋转过程中的实时数据,如位置、速度、加速度等。
3.建立数学模型:根据采集的数据,建立误差补偿的数学模型,以便后续计算和调整。
4.设置补偿参数:根据数学模型,合理设置补偿参数,如补偿值、补偿范围等。
5.调试与优化:在实际加工过程中,不断调试和优化补偿参数,使加工精度达到最佳状态。
四、实际应用中的注意事项1.确保测量数据的准确性:准确采集加工中心在四轴旋转过程中的数据,以便建立准确的数学模型。
2.合理选择补偿类型:根据加工中心和加工需求,选择合适的补偿类型,以提高加工精度。
3.定期检查与维护:定期检查加工中心四轴旋转系统的磨损情况,及时更换易损件,保证系统正常运行。
4.防止误操作:加强操作人员的培训,避免误操作导致的加工误差。
五、总结与建议发那科加工中心的四轴旋转误差补偿技术在实际应用中具有重要意义。
通过合理设置补偿参数,可以有效提高加工精度,提高生产效率。
为确保误差补偿效果,建议定期检查与维护加工中心,加强操作人员培训,确保加工过程的安全与稳定。
13、螺距误差补偿及反向间隙补偿

螺距误差补偿及反向间隙补偿根据下表设置螺距误差补偿相关参数:参数号参数位设定值设置说明3620 XZ 100200每个轴的参考点的螺距误差补偿点号3621 XZ 负方向最远的补偿位置号根据下面的公式进行计算:参考点的补偿位置号—(负方向的机床行程/补偿位置间隔)+ 1 100-(1000/50)+1=81 所以负方向补偿位置号设置为813622 XZ 正方向的最远补偿位置号根据下面的公式进行计算:参考点的补偿位置号+(正方向的机床行程/补偿位置间隔)+ 1 100+(0/50)+1=101 所以参考点正方向补偿位置号为101.3624 补偿点间隔输入格式为无小数点输入格式,由于X轴为直径值编程,所以X轴补偿点间隔应为实际补偿点间隔的2倍,应设置为100000,为100mm.参数号参数位设定值设置说明1800 #4(RBK) 是否分别进行切削进给/快速移动反向间隙补偿0: 不进行。
1: 进行。
1851 XZ 每个轴的反向间隙补偿量,设置后,回零生效1852 XZ 每个轴的快速移动时的反向间隙补偿量,回零生效由于FANUC系统螺距误差补偿采用增量式的补偿方式,所以在进行螺距误差补偿时,需根据补偿数据进行补偿数据的设定个。
下表为螺距误差补偿表由于每个补偿点的最大补偿值只能到7,在上表中可以看到,在-400mm测量位置处出现了一次22的值,此点是所有补偿点误差的最大值,所以补偿倍率按此点进行计算,而且考虑其它点的误差值,将补偿倍率设置为3倍。
补偿倍率设置为3倍,所有的补偿值都放大了三倍,所以在补偿数据处看到的是计算值的1/3,如果测量人员给出的是补偿值,那么补偿数据就按上图中的数据进行输入,如果给出的是误差值,则需将上图中的补偿数据取反。
螺距误差补偿在回零后即可生效。
基于激光干涉仪的FANUC系统VMC的定位精度检测与误差补偿

基于激光干涉仪的FANUC系统VMC的定位精度检测与误差补偿周丽霞;周树强;覃琴【摘要】利用英国雷尼绍公司生产的MLIO激光干涉仪,对配有FANUC 0i数控系统的立式加工中心进行误差数据采集,通过激光干涉仪配套软件绘制定位误差曲线,并生成误差补偿数据,将误差补偿数据输入FANUC 0i系统,可以显著提高机床的加工精度。
%Using Renishaw ML10 laser interferometer can measure the practice error data in FANUC 0i system VMC machine,draw the positioning accuracy error curve, and create dates of error compensation, which are interred into FANUC 0i system for improving the processing precision of CNC machine.【期刊名称】《机电工程技术》【年(卷),期】2015(000)010【总页数】4页(P94-96,122)【关键词】FANUC数控系统;激光干涉仪;误差补偿【作者】周丽霞;周树强;覃琴【作者单位】成都航空职业技术学院,四川成都610100;成都航空职业技术学院,四川成都 610100;成都航空职业技术学院,四川成都 610100【正文语种】中文【中图分类】TH17随着数控加工中心的广泛应用,对零件加工精度要求也越来越高,数控机床的精度也有了更高的要求。
为了保证加工质量,对数控机床的定位精度进行检测和补偿是最根本的,由于本文中的半闭环系统机床的定位精度主要是受到滚珠丝杠精度的影响,滚珠丝杠的精度主要受到制造误差和使用磨损的影响[1-2],所以通过对数控机床进行定期检测,并对数控系统进行正确螺距误差补偿,来提高数控机床的加工定位精度。
FANUC 0i进给伺服系统故障分析

FANUC 0i进给伺服系统故障分析一.F ANUC 0i进给伺服系统故障诊断及维修进给伺服一般采用闭环或半闭环控制,这种控制方法的特点就是任一环节发生故障都可能导致系统定位不准确、不稳定或失效,因此诊断并确定故障环节就成为维修的关键。
进给伺服常见故障如下:(1)超程。
当进给运动超过软件设定的软限位或由限位开关设定的硬件限位时,就会发生超程报警,一般会在LCD上显示报警内容,根据数控系统说明书,即可排除故障,解除报警。
主轴电机允许的轴端径向力(2)过载。
当进给运动的负载过大,频繁正反向运动以及传动链润滑状态不良时,均会引起过载报警。
一般会在LCD上显示伺服电动机过载、过热或过流等报警信息。
同时,在强电柜中的进给驱动单元上的指示灯或数码管会提示驱动单元过、过电流等信息。
(3)窜动。
如果在进给时出现窜动现象,可能的原因有:①测速信号不稳定,如测速装置故障、测速反馈信号干扰;②速度控制信号不稳定或收到干扰;③接线端子接触不良,如螺钉松动等;④当窜动发生在由正方向与反运动方向的换向瞬间时,一般是由于进给传动链的反向间隙或伺服系统增益过大所致。
(4)爬行。
发生在启动加速段或低速进给时,一般是由于进给传动链的润滑状态不良,伺服系统增益低及外加负载过大等原因所致。
伺服电机和滚珠丝杠用联轴器连接,由于连接松或联轴器本身的缺陷造成滚珠丝杠的转动和伺服电机的转动不同步造成爬行。
(5)震动。
机床以高速运行时,可能产生振动,这是就会出现过流报警。
机床振动问题一般属于速度问题,应查找速度调节器。
主要从给定信号、反馈型号和速度调节器本身这3方面去查找故障原因。
(6)伺服电动机不转。
数控系统值进给驱动单元出来速度控制信号外,还有使能控制信号,一般是DC+24V继电器线圈电压。
伺服电动机不转,常有诊断方法有:①检查数控系统是否有速度信号输出;②检查使能信号是否接通,通过LCD观察I/O状态,分析机床PLC梯形图,以确定进给轴的启动条件,如润滑、冷却等是否满足;③对带电磁制动的伺服电动机,应检查电磁制动是否释放;④进给驱动单元故障;⑤伺服电机故障。
FANUC-0i数控机床伺服系统的动态误差分析及补偿方法探讨

ZHANG S h a o — x i n
( An h u i I n d u s t r y a n d Tr a d e Vo c a t i on a l Te c h n i c a l Co l l e ge ,H u a i n a n 3 1 0 0 2 7 ,Chi n a )
t r o j me t h o d , a c c e l e r a t i o n  ̄ d e c e l e r a t i o n -t i me c o n s t a n t a d j u s t me n t me t h o d a n d S O o n .Th i s p a p e r p r e s —
t h i s p a p e r h a s d e c r e a s e d d y n a mi c a l e r r o r a n d e n h a n c e d wo r k i n g a c c u r a c y . Th i s c a n a l s o b e p r o v e d b y
a c t u a l p r o j e c t s .
Ke y w o r d s : d y n a mi c e r r o r ;e r r o r r e s t r a i n;c o mp e n s a t o r y o p t i mi z a t i o n
me t a l p a r t s .I t s s e r v o s y s t e m’ S d y n a mi c a l e r r o r ,wh i c h c o n t a i n s t wo a s p e c t s :s i g n a l d e l a y a n d s y s —
FANUC数控系统螺距误差补偿功能.

FANUC数控系统螺距误差补偿功能数控机床的直线轴精度表现在轴进给上主要由三项精度:反向间隙、定位精度和重复定位精度,其中反向间隙、重复定位精度可以通过机械装置的调整来实现,而定位精度在很大程度上取决于直线轴传动链中滚珠丝杠的螺距制造精度。
在数控机床生产制造及加工应用中,在调整好机床反向间隙、重复定位精度后,要减小定位误差,用数控系统的螺距误差螺距补偿功能是最节约成本且直接有效的方法。
FANUC数控系统已广泛应用在数控机床上,其螺距误差补偿功能有一定的典型性。
螺距补偿原理是将机械参考点返回后的位置作为螺距补偿原点,CNC系统以设定在螺距误差补偿参数中的螺距补偿量和CNC移动指令,综合控制伺服轴的移动量,补偿丝杠的螺距误差。
1 螺距误差补偿前的准备工作回参考点后,编程控制需要螺距误差补偿的轴,从参考点或机床机械位置某一点间歇移动若干个等距检测点,用激光干涉仪等检测计量仪器检测出各点的定位误差。
检测点数量可根据机床的工作长度自设。
2 设定螺距误差补偿参数打开参数开关在MDI方式下设置参数PWE=1,系统出现1000报警,同时按CAN和RESET键清除报警。
⑴参考点的螺距误差补偿点号码参数X轴参数No.1000Z轴参数No.2000⑵螺距误差补偿倍率参数参数No.0011的PML1,PML2。
.PML2 PML1 倍率( 0 0 31,0 1 32,1 0 34,1 1 38)设定的螺距补偿值,乘上该倍率,即为输出值.⑶螺距误差补偿点间隔X轴参数No.756Z轴参数No.757螺距误差补偿点为等间隔,设定范围从0到999999999。
一般设定单位是0.001毫米。
⑷螺距补偿点数目各轴从0到127共128个螺距补偿点⑸螺距补偿量及螺距补偿点的号X轴参数No.(1001+螺距补偿点号)Z轴参数No.(2001+螺距补偿点号)每个螺距补偿点螺距补偿量的范围为(-7)~(+7)乘以螺距补偿倍率。
负侧最远补偿点的号=原点补偿点-(负侧的机床长/补偿点间隔)+1正侧最远补偿点的号=原点补偿点+(正侧的机床长/补偿点间隔)3设定好螺距补偿参数后,在MDI方式下,设置参数PWE=0,关闭参数写状态。
FANUC_高速高精度控制的调整步骤

消除 机械共振
滤波器 (*2)
伺服控制中的伺服调整项目
(*1) 设定 HRV 电流控制 (HRV2 或 HRV3) (*2,*3) 调整消除机械共振滤波器并设定速度环路增益 (*4) 前馈调整 (*5) 位置增益调整
2021/10/10
HRV 电流控制 HRV2,3 (*1)
11 Tuning - 11
F A N U C L T D
速度增益和HRV滤波器调整 (2)
调整导航器提高增益后, 再测频率响应特性曲线.
我们推荐通过坐标轴的直线移动检测增益设定的正确性. 如果观察到有一些振动, 请将速度增益减小一点.
电机速度
转矩 指令
2021/10/10
降低增益
电机速度
转矩 指令
23 Tuning - 23
2021/10/10
7
Tuning - 7
伺服调整过程概述
F A N U C L T D
如何进行伺服调整 1
伺服指导 是支持伺服调整的一个强有力的工具. 伺服指导可以观测到伺服 系统的状态并能对伺服进行自动调整.
伺服 指导
PCMCIA LAN 卡
在伺服调整过程中, 增益调整和HRV 滤波器调整是最重要的. 通过提高伺服 系统的速度增益和位置增益能够高精度跟随位置指令和抑制伺服电机的干 扰. 调整指导 在伺服指导中自动进行增益调整.
2004
2040 2041 2003 #3 2017 #7 2006 #4 2016 #3
2119
1825 2021 2202 #1 2107
标准设定值
0X000011
(注 1)
标准参数 (注 1) 标准参数 (注 1)
1 1 1 1
FANUC0系统部分参数功能说明

FANUC0系统部分参数功能说明1.刀具半径补偿(CUTTER_R_COMP):该参数决定刀具半径补偿的大小。
当刀具在加工过程中出现偏差时,可以通过调整这个参数来使刀具路径与期望的路径更加接近。
2.预置刀具半径补偿(PRESET_R_COMP):该参数用于设置预置刀具半径补偿的大小。
预置刀具半径补偿是在程序中设置的,用于预先补偿刀具半径误差。
可以通过调整这个参数来改变刀具对工件的加工效果。
3.进给速度修正(FEED_SPEED):该参数用于修正进给速度的大小。
当切削条件或刀具磨损改变时,可以通过调整这个参数来使进给速度与期望的速度一致。
4.回转半径(RADIUS):该参数用于设置回转半径的大小。
当机床执行圆弧插补运动时,可以通过调整这个参数来改变圆弧的半径,从而实现不同大小的加工。
5.光滑度(SMOOTHNESS):该参数用于调整运动的光滑度。
光滑度越大,机床运动的曲线越平滑。
可以通过调整这个参数来改变机床的运动轨迹,从而实现更精确的加工。
6.切削力限制(FORCE_LIMIT):该参数用于限制切削力的大小。
当机床在加工过程中出现过大的切削力时,可以通过调整这个参数来限制切削力的大小,以保护机床和刀具的安全。
7.加工系数(PROCESS_COEFFICIENT):该参数用于调整加工的精度和速度。
可以通过调整这个参数来改变加工的速度和精度,以满足不同的加工需求。
8.安全高度(SAFE_HEIGHT):该参数用于设置安全高度的大小。
安全高度是机床在加工过程中离开工件的高度,以确保机床和刀具的安全。
可以通过调整这个参数来改变安全高度的大小。
9.原点补偿(ORIGIN_OFFSET):该参数用于补偿机床运动轴的原点位置。
可以通过调整这个参数来校正运动轴的原点位置,以保证加工的精度。
10.加速度(ACCELERATION):该参数用于调整机床的加速度。
加速度越大,机床的加工速度越快。
可以通过调整这个参数来改变机床的加工速度,以提高生产效率。
发那科螺距补偿、软限位、反向间隙

参数号 0011:#1,#0 712 713 714 715 含义 补偿倍率 X轴螺距误 差补偿间隔 Y轴螺距误 差补偿间隔 Z轴螺距误 差补偿间隔 第4轴螺距 误差补偿间 隔 X轴参考点 补偿号 X轴各点螺 距误差补偿 值 Y轴参考点 补偿号 Y轴各点螺 距误差补偿 Z轴参考点 补偿号 Z轴各点螺 距误差补偿 值 第4轴参考 点补偿号 第4轴各点 螺距误差补 偿值 第5轴参考 点补偿号 第5轴各点 螺距误差补 偿值 第6轴参考 点补偿号 第6轴各点 螺距误差补 偿值 设定值 备注
10补偿倍率712x轴螺距误差补偿间隔713y轴螺距误差补偿间隔714z轴螺距误差补偿间隔715第4轴螺距误差补偿间隔1000x轴参考点补偿号10011128x轴各点螺距误差补偿值2000y轴参考点补偿号20012128y轴各点螺距误差补偿3000z轴参考点补偿号30013128z轴各点螺距误差补偿值4000第4轴参考点补偿号40014128第4轴各点螺距误差补偿值5000第5轴参考点补偿号50015128第5轴各点螺距误差补偿值6000第6轴参考点补偿号60016128第6轴各点螺距误差补偿值参数号含义设定值备注700x轴正向限位701y轴正向限位702z轴正向限位703第4轴正向限位704x轴负向限位705y轴负向限位706z轴负向限位707第4轴负向限位软限位参数表12反向间隙补偿参数表13参数号含义设定值备注535x轴进给速度反向间隙补偿值536y轴进给速度反向间隙补偿值537z轴进给速度反向间隙补偿值538第4轴进给速度反向间隙补偿值686x轴快速移动反向间隙补偿值687y轴快速移动反向间隙补偿值688z轴快速移动反向间隙补偿值689第4轴快速移动反向间隙补偿值参数号含义备注x轴3620参考点补偿点号y轴z轴x轴3621负向最小点补偿号y轴z轴x轴3622正向最大点补偿号y轴z轴x轴3623补偿倍率y轴z轴x轴3624补偿间隔y轴z轴参数号含义备注x轴1320各轴正向限位y轴z轴设定值二fanuci系列螺距误差补偿参数表21设定值软限位参数表22x轴1321各轴负向限位y轴z轴参数号含义备注x轴1851进给速度反向间隙补偿值y轴z轴x轴1852快速移动反向间隙补偿值y轴z轴参数号含义设定值备注0011
数控机床的误差补偿

数控机床的误差补偿随着我国经济的飞速发展,数控机床作为新一代工作母机,在机械制造中已得到广泛的应用,精密加工技术的迅速发展与零件加工精度的不断提高,对数控机床的精度也提出了更高的要求。
尽管用户在选购数控机床时,都十分看重机床的位置精度,特别是各轴的定位精度与重复定位精度。
但是这些使用中的数控机床精度到底如何呢? 大量统计资料表明:65.7%以上的新机床,安装时都不符合其技术指标;90%使用中的数控机床处于失准工作状态。
因此,对机床工作状态进行监控与对机床精度进行经常的测试是非常必要的,以便及时发现与解决问题,提高零件加工精度。
目前数控机床位置精度的检验通常采用国际标准ISO230-2或国家标准GB10931-89等。
同一台机床,由于采用的标准不同,所得到的位置精度也不相同,因此在选择数控机床的精度指标时,也要注意它所采用的标准。
数控机床的位置标准通常指各数控轴的反向偏差与定位精度。
对于这二者的测定与补偿是提高加工精度的必要途径。
一、反向偏差在数控机床上,由于各坐标轴进给传动链上驱动部件(如伺服电动机、伺服液压马达与步进电动机等)的反向死区、各机械运动传动副的反向间隙等误差的存在,造成各坐标轴在由正向运动转为反向运动时形成反向偏差,通常也称反向间隙或失动量。
对于采用半闭环伺服系统的数控机床, 反向偏差的存在就会影响到机床的定位精度与重复定位精度, 从而影响产品的加工精度。
如在G01切削运动时, 反向偏差会影响插补运动的精度, 若偏差过大就会造成“圆不够圆,方不够方”的情形;而在G00快速定位运动中,反向偏差影响机床的定位精度,使得钻孔、镗孔等孔加工时各孔间的位置精度降低。
同时,随着设备投入运行时间的增长, 反向偏差还会随因磨损造成运动副间隙的逐渐增大而增加, 因此需要定期对机床各坐标轴的反向偏差进行测定与补偿。
(1)反向偏差的测定反向偏差的测定方法:在所测量坐标轴的行程内, 预先向正向或反向移动一个距离并以此停止位置为基准,再在同一方向给予一定移动指令值,使之移动一段距离,然后再往相反方向移动相同的距离,测量停止位置与基准位置之差,在靠近行程的中点及两端的三个位置分别进行多次测定(一般为七次),求出各个位置上的平均值, 以所得平均值中的最大值为反向偏差测量值。
FANUC连接说明书(功能篇)1

1.2.9位置开关概要这是控制轴的机械坐标值处在由参数所指定的范围内时输出信号的一种功能。
通过参数指定任意的控制轴,指定输出位置开关信号的机械坐标的动作范围。
位置开关信号最多可以输出16点。
(使用11点以上的位置开关信号时,将参数信号位置开关信号PSW01—PSW16<Fn070,Fn071>[分类] 输出信号[功能] 该信号通知由参数(NO.6910—NO.6925)所指定的控制轴的机械坐标值处在由参数(NO.6930—NO.6945,NO.6950—NO.6965)所指定的范围内。
对应第n个位置开关功能的位置开关信号为PSWn。
(n: 1—16)[输出条件] 下列情形下成为‘1’。
*控制轴的机械坐标值在所指定的范围内时。
下列情形下成为‘0’。
*控制轴的机械坐标值在所指定的范围内时。
信号地址:#08 #07 #06 #05 #04 #03 #02 #01参数:#7 #6 #5 #4 #3 #2 #1 #0[输入类型] 参数输入[数据类型] 位路径型#1 EPW 位置开关的最大数量为0: 10个。
1: 16个。
#2 PSA 在判断位置开关功能的动作范围时,是否考虑伺服中的迟延量(位置偏差量)、加/减速控制中的迟延量。
0:不予考虑。
1:予以考虑。
[数据类型] 字节路径型[数据范围] 0 —控制轴数按照顺序指定对应于第1—第16位置开关功能的轴控制信号。
对应轴的机械坐标值处在参数中所设定的范围内时,向PMC输出对应的位置开关信号。
[输入类型] 参数输入[数据类型] 实数路径型[数据单位] mm inch 度(机械单位)[数据最小单位] 取决于参考轴的设定单位。
[数据范围] 最小设定单位的9位数(见标准参数设定表(A))(若是IS-B,其范围为-999999.999~+999999.999)此参数依次设定第1—第16位置开关动作范围的最大值。
[输入类型] 参数输入[数据类型] 实数路径型[数据单位] mm inch 度(机械单位)[数据最小单位] 取决于参考轴的设定单位。
FANUC 系统数控机床误差过大报警处理

FANUC 系统数控机床误差过大报警处理摘要:阐述了FANUC系统数控机床410#、411#误差过大报警的工作原理,总结了出现上述报警的原因,并通过实例给出了排除此类故障的方法和步骤。
关键词:410#报警411#报警FANUC系统数控机床编码器、光栅尺、反馈电缆伺、服放大器、伺服电机或传动机构出现故障时往往系统会触发误差过大报警,如FANUC系统的410#报警和411#报警。
410#报警:SERVO ALARM:n- TH AXIS- EXCESS ERROR报警解释:①第n轴的停止位置偏差值超过参数1829的设定值。
②在简易同步控制中,同步补偿量超过参数8325的设定值。
411#报警:SERVO ALARM:n- TH AXIS- EXCESS ERROR报警解释:第n轴移动时的位置偏差值超过参数1828的设定值。
一、工作原理如图1所示,在数控机床进行伺服控制的过程中,系统的移动指令经脉冲分配处理,进入误差寄存器,对误差寄存器的数值递增,通过伺服的速度回路以及电流回路,由伺服放大器驱动伺服电机转动,使安装在电机后面的增量式编码器发出数字脉冲,反馈到伺服放大器,通过FSSB光缆由进入误差寄存器,对误差寄存器的数值进行递减,正常情况下误差寄存器里的数值始终保持在一定范围以内,伺服停止时,误差寄存器的数值为0。
如果移动指令或编码器反馈两者中有一个没有,就会造成误差寄存器里的绝对数值过大,在移动时,如果误差寄存器里的绝对数值>参数1828里设定的数值,机床就会出现411报警,在停止时如果误差寄存器里的绝对数值>参数1829里设定的数值,机床就会出现410报警。
误差寄存器的数值可以在FANUC系统的诊断300号看到。
图1 误差计数器的读数过程二、故障原因通过以上分析可知,每当伺服使能接通,或者轴定位完成时,都要进行上述误差比较。
当以上误差比较超值后,就会出现410#报警,即停止时的误差过大。
fanuc发那科0I-9000参数及0M的一些参数维修说明书故障分析解决
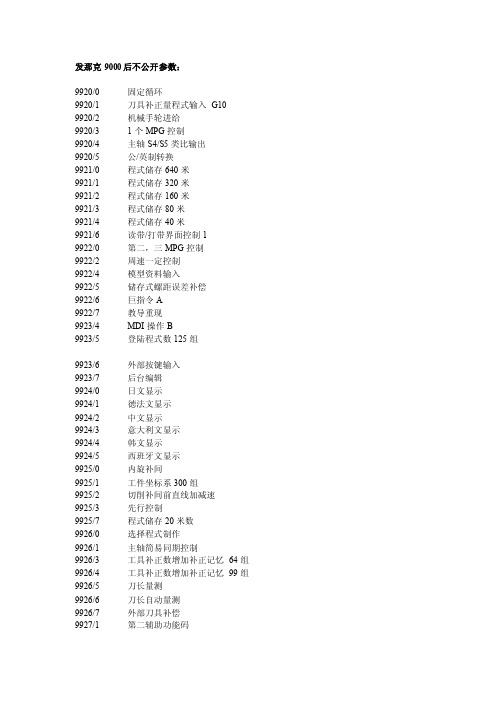
发那克9000后不公开参数:9920/0 固定循环9920/1 刀具补正量程式输入G10 9920/2 机械手轮进给9920/3 1个MPG控制9920/4 主轴S4/S5类比输出9920/5 公/英制转换9921/0 程式储存640米9921/1 程式储存320米9921/2 程式储存160米9921/3 程式储存80米9921/4 程式储存40米9921/6 读带/打带界面控制19922/0 第二,三MPG控制9922/2 周速一定控制9922/4 模型资料输入9922/5 储存式螺距误差补偿9922/6 巨指令A9922/7 教导重现9923/4 MDI操作B9923/5 登陆程式数125组9923/6 外部按键输入9923/7 后台编辑9924/0 日文显示9924/1 徳法文显示9924/2 中文显示9924/3 意大利文显示9924/4 韩文显示9924/5 西班牙文显示9925/0 内旋补间9925/1 工件坐标系300组9925/2 切削补间前直线加减速9925/3 先行控制9925/7 程式储存20米数9926/0 选择程式制作9926/1 主轴简易同期控制9926/3 工具补正数增加补正记忆64组9926/4 工具补正数增加补正记忆99组9926/5 刀长量测9926/6 刀长自动量测9926/7 外部刀具补偿9927/1 第二辅助功能码9927/2 三轴同动9927/3 增加轴控制9927/4 工件计数及跑合时间显示9927/6 工具径补正(切削补偿)C9927/7 工具径补正(切削补偿)B9928/1 原点复归速度设定9928/4 3次元坐标变换9929/0 绘图显示9929/1 程式图形对话9929/2 扩张内藏式行程检查9929/3 行程极限外部设定9929/6 外部讯息9930/1 程式再启动9930/1 程式再启动9930/2 外部资料输入9930/3 螺旋切削9903/5 PMC轴控制9930/6 自动转角进给率9931/0 单方向定位9931/2 刚性攻牙9931/3 时钟显示9931/6 卡式磁片资料显示9931/7 0.1单位增量系统9932/0 第三及第四回参考点9932/1 比率缩放9932/2 坐标系旋转9932/3 F15纸带格式9932/4 刀具寿命管理9932/5 工具补正数增加补正记?200组9932/6 增加选择性单节跳跃(最大)19个9932/7 巨集执行器9933/1 极坐标命令9933/3 F1段进给9933/4 I/O装置外部控制9933/5 四轴同动9933/6 中断形式巨集指令9933/7 巨集指令B9934/1 遥控式缓衡器9934/2 高速遥控式缓衡器A9934/3 高速遥控式缓衡器B9934/4 读带/打带界面控制29934/6 切削进给补间后直线加减速9935/0 高速循环加工9935/1 刀具补正记忆形式B9935/2 外部机械零点漂移9935/4 外部减速9935/5 动态绘图显示9935/6 登陆程式个数400组9935/7 登陆程式个数200组9936/0 刀具位置补正9936/2 选择性道角/转角R9936/3 简易同期制御9936/4 高速跳跃信号输入9936/7 扩张工件程式编辑程式COPY 9937/0 圆筒补间9937/1 S串列式输出9937/2 极坐标补间9937/3 Cs轴轮廓控制9937/5 C轴法线方向制御9937/6 刀具寿命管理512组9937/7 I/O同时操作9939/6 CAP19939/7 CAP19940/0 DNC-19940/3 索引功能9940/4 主轴同期制御9941/0 第一主轴定位9941/2 第一主轴输出切换9942/0 第二主轴定位9942/2 第二主轴定位9943/2 倾斜轴制御9943/3 制御轴扩张9943/5 登绿程式个数100组9943/6 程式儲存储1280米9943/7 工件座标系48组9944/0 切削进给速度调整9944/1 特殊JOG进给率调整9944/2 轴取出机能9944/3 浮动原点复归9944/4 圆弧半径速度箝制9944/5 自动转角减速9945/0 高精度轮廓控制9945/1 工具退避和复归9945/2 圆形拷贝9945/3 实际速度类比输出9945/4 工件坐标系预设9945/6 3次元工具補正9945/7 切削进给補间后锺形加减9946/0 PLC5000step9946/1 PLC8000step9946/2 PLC16000step9946/3 PLC24000step9946/4 PLC3000step9946/5 PLC12000step9946/6 PMC-RC程式语言-1M 9946/7 信号波形表示机能9947/0 PMC保持型记忆追加9947/1 PLC32000step9947/2 PMC程式语言256K 9947/3 PMC程式语言512K 9947/5 PMC程式语言2M 9948/0 NC格式转换输出9948/1 C语言9948/7 程式对话Super CAP-M 9952/4 指数函数补间9952/5 工具补正量499个9952/6 工具补正量999个9952/7 多段Skip9953/1 程式储存5120米数9953/2 程式储存2560米数9953/3 DNC29953/5 OSI网路9954/6 学习制御9962/3 马达速度信号输出9962/6 真直度补正9963/0 PMC轴制御扩张机能9963/1 HDISK9963/2 特殊高速循环9963/4 PMC轴速度指令机能9963/5 旋转轴控制9963/6 高速循环资料追加A 9963/7 高速循环资料追加B 9970/7 平滑补间9972/7 假想轴补间9972/4 实际速度类比输出B 9972/6 I/Olink29972/7 简易高精度9973/0 手动数值指令9973/2 姿势制御9973/5 非均匀B形云线补间9973/6 高速分配功能9976/2 PROFIBUS slave9976/3 PROFIBUS master 9976/4 多单节预读9977/2 二重位置检出机能9977/5 1CPU2系统101/7 NFD 数据输出时数据后的同步孔的输出 O O102 输入输出设备号:0:普通RS-232口设备(用DC1-DC4码)3:Handy File(3″软盘驱动器) O O 103 波特率:10:480011:960012:19200 O OI/O 通道1的参数:111/0 SB2 停止位数 O O111/3 ASI 数据输入代码:ASCII或EIA/ISO O O111/7 NFD 数据输出时数据后的同步孔的输出 O O112 输入输出设备号:0:普通RS-232口设备(用DC1-DC4码)3:Handy File(3″软盘驱动器) O O 113 波特率:10:480011:960012:19200 O O其它通道参数请见参数说明书。
数控机床加工尺寸不稳定原因及解决方法

数控机床加工中出现尺寸不稳定的机械原因分析1.伺服电机轴与丝杠之间的连接松动,致使丝杠与电机不同步,出现尺寸误差。
检测时只需在伺服电机与丝杠的联轴节上作好记号,用较快倍率来回移动工作台(或刀架),由于工作台(或转塔)的惯性作用,将使联轴节的两端出现明显相对移动。
此类故障通常表现为加工尺寸只向一个方向变动,只需将联轴节螺钉均匀紧固即可排除。
2.滚珠丝杠与螺母之间润滑不良,使工作台(或刀架)运动阻力增加,无法完全准确执行移动指令。
此类故障通常表现为零件尺寸在几丝范围内无规则变动,只需将润滑改善即可排除故障。
3.机床工作台(或刀架)移动阻力过大,一般为镶条调整过紧、机床导轨表面润滑不良所致。
该故障现象一般表现为零件尺寸在几丝范围内无规则变动。
检查时可通过观察DGN800-804的位置偏差量大小和变化来进行,通常为正反方向静止时相差较大。
此类故障只需将镶条重新调整并改善导轨润滑即可。
4.滚动轴承磨损或调整不当,造成运动阻力过大。
该故障现象也通常表现为尺寸在几丝范围内无规则变动。
检查时可通过DGN800-804的位置偏差量进行,方法同上。
此类故障只需将磨损轴承更换并认真调整,故障即可排除。
5.丝杠间隙或间隙补偿量不当,通过调整间隙或改变间隙补偿值就可排除故障。
加工尺寸不稳定类故障判断维修1.工件尺寸准确,表面光洁度差故障原因①刀具刀尖受损,不锋利②机床产生共振,放置不平稳③机械有爬行现象④加工工艺不好解决方案(与上对照)1.刀具磨损或受损后不锋利,则重新磨刀或选择更好的刀具重新对刀2.机床产生共振或放置不平稳,调整水平,打下基础,固定平稳3.机械产生爬行的原因为拖板导轨磨损厉害,丝杆滚珠磨损或松动。
机床应注意保养,上下班之后应清扫铁丝,并及时加润滑油,以减少摩擦4. 选择适合工件加工的冷却液;在能达到其它工序加工要求的情况下,尽量选用较高的主轴转速2.工件产生锥度大小头现象故障原因①机床放置的水平没调整好,一高一低,产生放置不平稳②车削长轴时,工件材料比较硬,刀具吃刀比较深,造成让刀现象③尾座顶针与主轴不同心解决方案1.使用水平仪调整机床的水平度,打下扎实的地基,把机床固定好提高其韧性2.选择合理的工艺和适当的切削进给量避免刀具受力让刀3. 调整尾座3.驱动器相位灯正常,而加工出来的工件尺寸时大时小故障原因①机床拖板长期高速运行,导致丝杆和轴承磨损②刀架的重复定位精度在长期使用中产生偏差③拖板每次都能准确回到加工起点,但加工工件尺寸仍然变化。
FANUC系统数控精度补偿方法
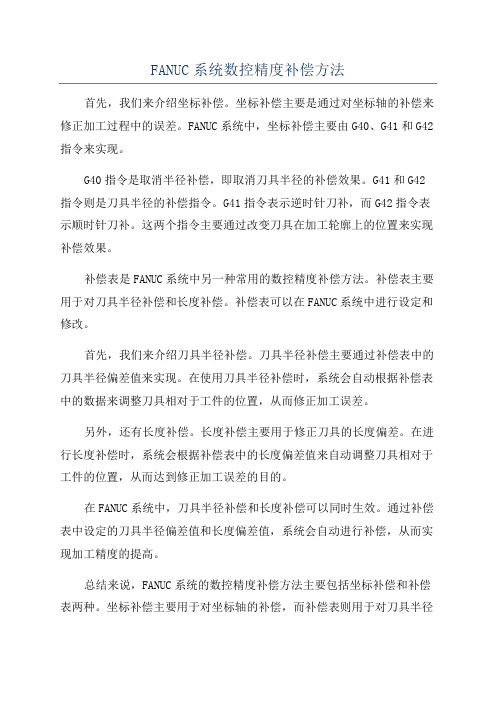
FANUC系统数控精度补偿方法
首先,我们来介绍坐标补偿。
坐标补偿主要是通过对坐标轴的补偿来修正加工过程中的误差。
FANUC系统中,坐标补偿主要由G40、G41和G42指令来实现。
G40指令是取消半径补偿,即取消刀具半径的补偿效果。
G41和G42指令则是刀具半径的补偿指令。
G41指令表示逆时针刀补,而G42指令表示顺时针刀补。
这两个指令主要通过改变刀具在加工轮廓上的位置来实现补偿效果。
补偿表是FANUC系统中另一种常用的数控精度补偿方法。
补偿表主要用于对刀具半径补偿和长度补偿。
补偿表可以在FANUC系统中进行设定和修改。
首先,我们来介绍刀具半径补偿。
刀具半径补偿主要通过补偿表中的刀具半径偏差值来实现。
在使用刀具半径补偿时,系统会自动根据补偿表中的数据来调整刀具相对于工件的位置,从而修正加工误差。
另外,还有长度补偿。
长度补偿主要用于修正刀具的长度偏差。
在进行长度补偿时,系统会根据补偿表中的长度偏差值来自动调整刀具相对于工件的位置,从而达到修正加工误差的目的。
在FANUC系统中,刀具半径补偿和长度补偿可以同时生效。
通过补偿表中设定的刀具半径偏差值和长度偏差值,系统会自动进行补偿,从而实现加工精度的提高。
总结来说,FANUC系统的数控精度补偿方法主要包括坐标补偿和补偿表两种。
坐标补偿主要用于对坐标轴的补偿,而补偿表则用于对刀具半径
补偿和长度补偿。
这些方法的应用可以提高数控机床的加工精度,从而得到更高质量的零件。
- 1、下载文档前请自行甄别文档内容的完整性,平台不提供额外的编辑、内容补充、找答案等附加服务。
- 2、"仅部分预览"的文档,不可在线预览部分如存在完整性等问题,可反馈申请退款(可完整预览的文档不适用该条件!)。
- 3、如文档侵犯您的权益,请联系客服反馈,我们会尽快为您处理(人工客服工作时间:9:00-18:30)。
无锡职业技术学院毕业设计说明书机械技术学院毕业设计论文FANUC的进给运动误差补偿方法学生姓名:指导教师姓名:所在班级所在专业论文提交日期论文答辩日期答辩委员会主任主答辩人系年月日FANUC的进给运动误差补偿方法目录毕业设计任务书 (1)开题报告 (2)第一章进给运动误差补偿方法 (6)1.1常见进给运动误差 (7)1.1.1反向间隙误差补偿 (8)1.1.2螺距误差补偿 (9)1.1.3摩擦补偿 (11)第二章进给误差数据采集与补偿参数的设置 (12)2.1激光干涉仪 (12)2.1.1单频激光干涉仪 (12)3.1 双频激光干涉仪 (13)3.1.1 雷尼绍激光校准系统 (14)3.1.2 测量误差分析 (19)3.2误差补偿参数的设置 (20)毕业设计总结 (23)参考文献 (24)致谢 (25)外文翻译 (26)2无锡职业技术学院毕业设计说明书机械技术学院毕业设计任务书课题名称FANUC的进给运动误差补偿方法指导教师王小平职称高级技师专业名称数控设备应用与维护班级数控设备10832学生姓名尹耀强学号1061083237课题需要完成的任务:1.根据课题调研查阅资料,了解国内外现状、进展,编写调研报告。
2.收集技术资料、图纸进行设计或分析探讨。
3.对不同类型设计的分析, 进行方案论证,确定总体方案。
4.完成毕业设计的论文。
5. 3000单词量的外文资料的翻译(专业相关科技类)。
课题计划:2月21日—2月25日;确定毕业设计课题。
2月28日—3月 4日;收集整理英文翻译资料。
3月 7日—3月11日;查阅技术资料,完成课题的前期调研工作,完成英文翻译。
3月14日—3月18日;完成课题相关资料收集,进行毕业论文构思。
3月21日—3月25日;完成毕业论文初稿。
3月28日—4月01日;完成毕业论文初稿。
4月04日—4月08日;修改、完善毕业论文,定稿。
4月11日—4月20日;整理打印毕业设计资料,完成答辩计划答辩时间:4月20日数控技术系(部、分院)2011 年3月 1 日1FANUC的进给运动误差补偿方法无锡职业技术学院(论文)开题报告(2011 届)题目FANUC的进给运动误差补偿方法指导教师王小平院系机械技术学院班级数控设备10832学号1061083237姓名尹耀强二〇一一年二月二十日2无锡职业技术学院毕业设计说明书一、选题的意义数控设备专业的毕业设计是我们完成学业的最后一个极为重要的实践性教学环节,是使我们综合运用所学过的基本课程,基本知识与基本技能去解决专业范围内的工程技术问题而进行的一次综合训练。
我们在完成毕业设计的同时,也培养了我们正确使用技术资料,国家标准,有关手册,图册等工具书,进行设计计算,数据处理,编写技术文件,数控编程等方面的工作能力,也为我们以后的工作打下坚实的基础,所以我们要认真对待这次综合能力运用的机会!二、研究的主要内容,拟解决的主要问题(阐述的主要观点)在数控机床加工零件的过程中,引起加工误差的原因有很多方面。
如机床零部件由于强度、刚度不够引起而产生的变形,从而造成的误差;还有因传动件的惯性、电气线路的时间滞后等原因带来的加工偏差等。
有些误差通过调整机床可以消除,但有些无法消除,这就需要我们通过数控系统参数补偿来消除。
目前,日本FANUC公司的数控系统在国内市场的占有率远远超过其他的数控系统。
本文以FANUC公司的数控系统为例来说明数控机床进给运动误差参数补偿方法。
三、研究(工作)步骤、方法及措施(思路)1.查阅技术资料,了解误差的形成2.翻译相关英文资料3.对误差补偿原理的理解4.完成误差补偿的相关图示5.查阅技术资料,了解误差的一般性的诊断与维修6.整理毕业设计资料,完成答辩四、毕业论文(设计)提纲1.课题研究的背景2.课题研究的意义3.课题研究内容4.课题研究目标3FANUC的进给运动误差补偿方法五、主要参考文献1.《数控机床故障诊断与维修》大连理工出版社出版2.《FANUC0i系列数控系统连接调试与维修诊断》化学工业出版社出版3.《FANUC0iC数控系统完全应用手册》人民邮电出版社4.《机械制图》机械工业出版社5.《CAD技术》电子出版社出版指导教师意见:签名:2010年 3月 6日系毕业设计(论文)工作指导小组意见:签名:年月日二级学院(直属系)毕业设计(论文)工作领导小组意见:签名:年月日4无锡职业技术学院毕业设计说明书摘要在数控机床加工零件的过程中,引起加工误差的原因有很多方面。
如机床零部件由于强度、刚度不够引起而产生的变形,从而造成的误差;还有因传动件的惯性、电气线路的时间滞后等原因带来的加工偏差等。
有些误差通过调整机床可以消除,但有些无法消除,这就需要我们通过数控系统参数补偿来消除。
关键词:数控机床、进给误差、激光干涉仪。
5FANUC的进给运动误差补偿方法第一章进给运动误差补偿方法背景在数控机床加工零件的过程中,引起加工误差的原因有很多方面。
如机床零部件由于强度、刚度不够引起而产生的变形,从而造成的误差;还有因传动件的惯性、电气线路的时间滞后等原因带来的加工偏差等。
有些误差通过调整机床可以消除,但有些无法消除,这就需要我们通过数控系统参数补偿来消除。
FANUC系统是日本富士通公司的产品,通常其中文译名为发那科。
FANUC系统进入中国市场有非常悠久的历史,有多种型号的产品在使用,使用较为广泛的产品有FANUC 0、FANUC16、FANUC18、FANUC21等。
在这些型号中,使用最为广泛的是FANUC0系列。
系统在设计中大量采用模块化结构。
这种结构易于拆装、各个控制板高度集成,使可靠性有很大提高,而且便于维修、更换。
FANUC系统设计了比较健全的自我保护电路。
PMC信号和PMC功能指令极为丰富,便于工具机厂商编制PMC控制程序,而且增加了编程的灵活性。
系统提供串行RS232C接口,以太网接口,能够完成PC和机床之间的数据传输。
FANUC系统性能稳定,操作界面友好,系统各系列总体结构非常的类似,具有基本统一的操作界面。
FANUC系统可以在较为宽泛的环境中使用,对于电压、温度等外界条件的要求不是特别高,因此适应性很强。
鉴于前述的特点,FANUC系统拥有广泛的客户。
使用该系统的操作员队伍十分庞大,因此有必要了解该系统的一些软、硬件上的特点。
目前,日本FANUC公司的数控系统在国内市场的占有率远远超过其他的数控系统。
日本FANUC公司的数控系统具有高质量、高性能、全功能,适用于各种机床和生产机械的特点,在市场的占有率远远超过其他的数控系统,主要体现在以下几个方面。
(1)系统在设计中大量采用模块化结构。
这种结构易于拆装,各个控制板高度集成,使可靠性有很大提高,而且便于维修、更换。
(2)具有很强的抵抗恶劣环境影响的能力。
其工作环境温度为0~45℃,相对湿度为75%。
(3)有较完善的保护措施。
FANUC对自身的系统采用比较好的保护电路。
(4)FANUC系统所配置的系统软件具有比较齐全的基本功能和选项功能。
对于一般的机床来说,基本功能完全能满足使用要求。
(5)提供大量丰富的PMC信号和PMC功能指令。
这些丰富的信号和编程指6无锡职业技术学院毕业设计说明书令便于用户编制机床侧PMC控制程序,而且增加了编程的灵活性。
(6)具有很强的DNC功能。
系统提供串行RS232C传输接口,使通用计算机PC和机床之间的数据传输能方便、可靠地进行,从而实现高速的DNC操作。
(7)提供丰富的维修报警和诊断功能。
FANUC维修手册为用户提供了大量的报警信息,并且以不同的类别进行分类。
2.主要系列(1)高可靠性的PowerMate 0系列:用于控制2轴的小型车床,取代步进电机的伺服系统;可配画面清晰、操作方便,中文显示的CRT/MDI,也可配性能/价格比高的DPL/MDI。
(2)普及型CNC 0—D系列:0—TD用于车床,0—MD用于铣床及小型加工中心,0—GCD用于圆柱磨床,0—GSD用于平面磨床,0—PD用于冲床。
(3)全功能型的0—C系列:0—TC用于通用车床、自动车床,0—MC用于铣床、钻床、加工中心,0—GCC用于内、外圆磨床,0—GSC用于平面磨床,0—TTC 用于双刀架4轴车床。
(4)高性能/价格比的0i系列:整体软件功能包,高速、高精度加工,并具有网络功能。
0i—MB/MA用于加工中心和铣床,4轴4联动;0i—TB/TA用于车床,4轴2联动,0i—mate MA用于铣床,3轴3联动;0i—mateTA用于车床,2轴2联动。
(5)具有网络功能的超小型、超薄型CNC 16i/18i/21i系列:控制单元与LCD 集成于一体,具有网络功能,超高速串行数据通讯。
其中FSl6i—MB的插补、位置检测和伺服控制以纳米为单位。
16i最大可控8轴,6轴联动;18i最大可控6轴,4轴联动;21i最大可控4轴,4轴联动。
除此之外,还有实现机床个性化的CNC 16/18 / 160/180系列。
本文就以FANUC公司的数控系统为例来说明数控机床进给运动误差参数补偿方法。
1.1常见进给运动误差进给运动:使工件的多余材料连续在相同或不同深度上被去除的工作运动。
运动误差是指由于数控机床结构间的相对运动和结构本身的原因而使刀具与工件间产生的相对位置误差。
进给运动误差可分成两类:一类是有常值系统性误差,如螺距积累误差、反向间隙误差等;一类是变值系统性误差,如热变形等。
数控机床上常见进给运动误差的原因有:7FANUC的进给运动误差补偿方法a.机床的热变形,机床构件的扭曲与变形,传动轴或丝杠在扭矩作用下的扭曲变形引起的无效运动,都会造成零件的加工偏差;b.螺距误差,开环和闭环数控机床的定位精度主要取决于滚珠丝杠的精度。
但丝杠总会存在一定的螺距误差,因此在加工过程中会造成零件的加工误差;c.齿隙或间隙,在齿轮传动系统中,齿轮间隙是引起传动误差的一个主要原因。
在丝杠螺母副传动时,其间的齿隙以及溜板的歪斜也会产生传动误差。
这类误差统称为齿隙误差;d.机床溜板的磨擦、磨损造成的误差。
进给运动误差的消除方法消除误差的方法很多,可通过机械设计提高部件的刚度、强度,以减少变形;也可通过控制系统消除误差。
过去用硬件电子线路和挡块补偿开关实现补偿,现在CNC系统中多用软件进行误差补偿。
1.1.1反向间隙误差补偿在进给传动链中,于丝杠和螺杆在制造、使用过程中配合所造成的.齿轮传动、滚珠丝杠螺母副等均存在反向间隙,这种反向间隙会造成工作台在反向运动时,电动机空转而工作台不动。
(反向间隙,即丝杠和螺母无相对转动时,丝杠和螺母之间的最大窜动。
由于螺母结构本身的游隙以及其受轴向载荷后的弹性变形,滚动丝杠螺母机构存在轴向间隙。
该轴向间隙在丝杠反向转动时表现为丝杠转动α角,而螺母未移动,形成了反向间隙。