效率提升工程--作业现场效率提升
不断改进喷砂作业流程提升工作质量与效率

不断改进喷砂作业流程提升工作质量与效率喷砂作业是一项常见的表面处理技术,被广泛应用于金属加工、建筑工程和汽车修复等领域。
然而,由于技术操作和流程管理的不完善,许多喷砂作业存在着工作质量不稳定和效率低下的问题。
为了提升喷砂作业的质量与效率,我们可以采取以下几个改进措施。
首先,改善喷砂材料的选择和使用。
喷砂材料的选择直接关系到喷砂作业的质量和效率。
不同材料具有不同的硬度和清理效果,我们需要根据具体工作需求选择适当的喷砂材料。
同时,喷砂材料的储存和使用也需要注意,保持储存环境的清洁和干燥,确保喷砂材料的质量和性能不受影响。
其次,优化喷砂设备和工艺参数。
喷砂设备的性能对作业质量和效率起着关键作用。
我们可以考虑更新现有设备,选择更加高效和节能的喷砂机器。
此外,根据具体的作业需求,调整喷砂的压力、喷嘴尺寸和喷砂距离等参数,以提高作业的效果和速度。
第三,加强操作人员的培训和技能水平。
操作人员的熟练程度对喷砂作业的质量和效率有着直接的影响。
提供必要的培训和学习机会,使操作人员了解喷砂作业的原理和操作要点,掌握正确的操作技能。
此外,建立一套健全的安全操作规程,确保操作人员能够按照规定的流程进行喷砂作业,提高工作质量和效率。
第四,加强作业现场的管理和协调。
有效的作业现场管理可以提高喷砂作业的质量和效率。
在作业前,对现场进行全面检查,确保喷砂设备和喷砂材料的准备工作完成;在作业过程中,严格遵守操作规程,确保操作人员的安全和作业质量;在作业后,及时清理和维护设备,保持作业现场的整洁和有序。
此外,加强与其他作业环节的协调和配合,提高整体作业效率。
最后,建立完善的质量管理体系。
建立一套科学、规范的质量管理体系,是提升喷砂作业质量和效率的重要保障。
制定相关的质量管理制度和标准,对作业过程进行监督和检查,及时发现和纠正问题,确保喷砂作业的质量稳定和可控。
此外,加强对作业结果的评估和反馈,不断改进和优化喷砂作业流程,实现技术的持续创新和提升。
效率提升改善方案报告

效率提升改善方案报告签于公司现有的生产及品质状况,结合与生产相关部门的工作,从人、机、料、法、环五个方面提出以下效率提升及品质改善方案:一、人员1、人员培训现有生产课人员流动率较大,作业熟手相对较少,应加强对新进员工及老员工各方面的培训。
要实行生产制程中的自主性管理,人员素质起到了一个至关重要的作用。
1)产品知识培训,公司新、老员工,包括管理层对公司产品都没有一个全面的认识。
对公司产品的性能及产品结构均没有足够的了解。
1)公司产品知识教材的编写,把公司的产品分类,根据每个类别的产品特点编写教材(需要开发部门的支持),教材的编写依据是公司的技术文件,教材中要提到各种产品依据的行业标准以及相关的一些要求。
(责任部门:研发课、生技课)2)培训方式采用部门内部教材培训(集中授课)、邀请研发课(或生技课)工程师对员工做培训(集中授课)、针对每一类型的产品以图片或实物的形式进行。
产品的知识培训要长期进行,最终达到部门员工对公司所有产品性能、作用熟悉,并且由此知道可能影响产品质量的材料因素和操作因素,从而达到质量控制的目的。
(责任部门:研发部、生技部)2)公司与生产相关的作业流程的培训在生产过程中,操作员和基层管理对生产各个环节或与相关部门的工作不知怎样去进行开展和配合。
完善与生产相关的作业流程,作业规范化、标准化,有利于各班组、各部门间的工作衔接。
(责任部门:生产课)3)作业技能相对生产过程的各个工站(如制线班:剪线、剥线、焊插针、沾锡、成型、检验;装配线:壳料装配、按键装配、打螺丝、焊线、焊分立元件、焊贴片件、修补焊、外观检验、电气检验等等工站)均进行作业技能、作业标准、常见不良及分析解决的培训,并建立文本及电子培训资料,以利于后期的员工培训及培训资料的补充完善。
(责任部门:生技课)4)品质培训提升生产及品质部员工的品质意识及品质分析能力,增强生产现场操作员、检验员及基层管理人员的现场分析解决问题的能力。
工程师的效率提升策略

工程师的效率提升策略工程师在日常工作中面临着各种任务和挑战,如何提高工作效率成为一个关键问题。
本文将介绍一些提升工程师效率的策略,帮助工程师更好地完成工作任务。
一、合理规划工作流程合理规划工作流程是提升工程师效率的基础。
工程师可以通过以下几点来规划工作流程:1. 设立明确的工作目标:在开始工作之前,工程师应明确自己的工作目标,明确需要完成的任务和所需的时间。
2. 制定任务优先级:根据工作的重要性和紧急程度,工程师应制定任务的优先级,合理安排工作顺序。
3. 分解任务细节:将大的任务分解为小的可执行的任务,并设立合理的时间节点,帮助工程师更好地管理和掌控任务进度。
二、充分利用工具与技术合理使用工具和技术可以帮助工程师提高工作效率。
以下是一些常用的工具和技术:1. 项目管理工具:使用项目管理工具可以帮助工程师更好地组织和管理项目,提高项目的执行效率。
2. 自动化工具:合理利用自动化工具可以节省大量的时间和精力,例如使用脚本进行自动化测试和部署。
3. 版本控制工具:使用版本控制工具可以对工程师的代码进行管理和追踪,提高代码开发和维护的效率。
4. 学习新技术:不断学习新的技术和工具,可以提高工程师的技术水平和解决问题的能力,从而提高工作效率。
三、良好的时间管理良好的时间管理是工程师提高效率的关键。
以下是一些时间管理的策略:1. 制定详细的工作计划:制定详细的工作计划可以帮助工程师合理安排时间,更加高效地完成任务。
2. 高效利用碎片时间:合理利用碎片时间,例如在等待会议开始前做一些简单的任务或者学习新知识,可以提高工作效率。
3. 避免多任务同时进行:尽量避免同时处理多个任务,因为分散注意力会降低工作效率,建议专注于一项任务直到完成。
4. 授权和委托:将一些简单的任务和日常事务委托给合适的人员,集中精力处理重要的工作,提高工作效率。
四、保持积极的工作态度保持积极的工作态度对于提高工程师效率非常重要。
以下是一些提升工作态度的建议:1. 善于沟通合作:与团队成员和其他相关人员保持良好的沟通和合作,能够更快地解决问题并提高工作效率。
建筑施工技术管理与提高工作效率的措施
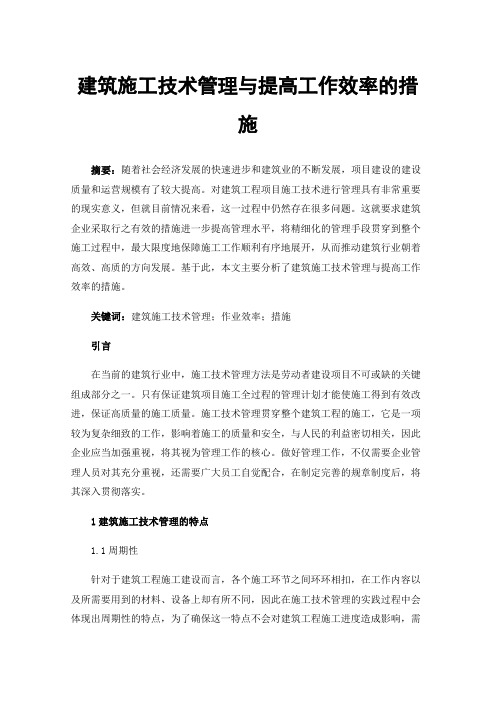
建筑施工技术管理与提高工作效率的措施摘要:随着社会经济发展的快速进步和建筑业的不断发展,项目建设的建设质量和运营规模有了较大提高。
对建筑工程项目施工技术进行管理具有非常重要的现实意义,但就目前情况来看,这一过程中仍然存在很多问题。
这就要求建筑企业采取行之有效的措施进一步提高管理水平,将精细化的管理手段贯穿到整个施工过程中,最大限度地保障施工工作顺利有序地展开,从而推动建筑行业朝着高效、高质的方向发展。
基于此,本文主要分析了建筑施工技术管理与提高工作效率的措施。
关键词:建筑施工技术管理;作业效率;措施引言在当前的建筑行业中,施工技术管理方法是劳动者建设项目不可或缺的关键组成部分之一。
只有保证建筑项目施工全过程的管理计划才能使施工得到有效改进,保证高质量的施工质量。
施工技术管理贯穿整个建筑工程的施工,它是一项较为复杂细致的工作,影响着施工的质量和安全,与人民的利益密切相关,因此企业应当加强重视,将其视为管理工作的核心。
做好管理工作,不仅需要企业管理人员对其充分重视,还需要广大员工自觉配合,在制定完善的规章制度后,将其深入贯彻落实。
1建筑施工技术管理的特点1.1周期性针对于建筑工程施工建设而言,各个施工环节之间环环相扣,在工作内容以及所需要用到的材料、设备上却有所不同,因此在施工技术管理的实践过程中会体现出周期性的特点,为了确保这一特点不会对建筑工程施工进度造成影响,需要对技术管理进行优化革新,确保其能够满足建筑工程的整体发展,为建筑工程的顺利完成提供保障。
1.2危险性建筑工程通常是在露天场所展开的,而且伴随着土地资源的日渐紧张,高层建筑越来越多,因此在施工过程中,会涉及高空作业等危险环节。
不仅如此,在施工中所需要用到大量的器械材料,大部分施工操作都是需要建筑工人来开展的,所以在施工中存在一定的安全隐患,这也就表示在建筑施工技术管理中还存在一定的危险性,需要建筑单位格外留意[1]。
1.3复杂性建筑工程作为一个系统性工作,其中所涉及的环节众多,各个环节都是由不同的分支组成,所包含的内容也是错综复杂,在具体施工过程中所应用到的施工设备、技术等施工要素也不尽相同,由此导致建筑工程更具复杂性。
效率提升工程--作业现场效率提升(PPT 56页)

一次因 (近因)
治本
n次因 (根因)
22
案例
背景:某车间生产效率一直偏低,连续三个月均在 定额指标65%—75%之间。
步骤一:特性为“生产效率低落”
生产效率低
步骤二:找出大方向原因,从5M1E方向着手
环境
管理
人员
方法
材料
机器
生产效率低
23
案例
步骤三:找出形成大原因之小原因
环境
温度 湿度
管理
薪资管理 污染 考核制度
19
作业分析的基本要求
通过删减、合并、简化,使操作总数 减至最低、工序排列最佳,并使每一操作简单易行。
合理利用肌肉群,防止某些肌肉群因动作频繁而产生劳损。 改进设备、工装或工位器具、物料规格或工艺,采用经济的切削用 量。 消除不合理的空闲时间,尽量实现人机同步工作。
综上所述,通过作业分析,应达到使作业的结构合理、作业者的劳动强 度减轻、作业的时间消耗减少,保证生产质量,提高作业效率。 双手操作分析(操作者作业分析); 人机操作分析; 联合操作分析(工组作业分析)。
46
要领书实施要点
7.作业要领书在编制后,需根据实际使用状况,不断地进行修订和优化。 这项工作将成为以后班长的日常工作。通过标准作业的开展,实现班长管 理行为的转变。 8.在产品型号较多、较复杂的状况下,标准作业导入初期,可先编制主流 产品(如产量前四位的产品)的作业要领书。 9.作业要领书的编制按照一个作业员一份要领书的原则进行。一人一机, 一人多机时均为一份作业要领书。多人一机和多人多机时,要领书的数量 与作业员数量一致。 10.作业要领书是公司保密文件,公司可根据需要适当揭示。 11.作业要领书编制完成后,如含有品质部门直接参与过程检验的内容, 需知会品质部门。
作业效率提升方案-作业效率提升方案51页PPT

作业效率分析—降低投入标准
标准• 时宽间放的的形定义成
1.操作过程中,作业人员的疲劳,需休息,以资恢复. 2.满足操作人员的个人需要. 3.领班之作业指示或外人干扰. 4.工作准备与清扫. 5.操作时之机器干扰. 6.材料不良 以上等因个人私务,疲劳或暂停工作所给予的时间称之. 宽放的种类: 1.生理宽放:因操作人员领生理需要或为操作人员工作书市所给予的时间;如
工时记录表
行动措施
4.按制程给出宽放表 5.汇总所有工位时间,完成标工资料初表
各个工位宽放系数表 标准人力工时资料表
6.缺人转嫁项目清单和责任单位
转嫁责任明细责任单位表,含内部工位间转嫁
7.设计生产效率日报表
生产日效率报表
8.试统计日生产效率
生产日效率报表数据
工作分工时间表
项目行动计划
D 措施执行 定期项目进度内部交流
熟练程度
精确区分、量化损 失工时,及时把握 作业效率与生产效 率起伏原因
不同班组的各种停线, 转化为责任工时,统一 做80/20分析及则责任 考核
生产效率分析
作业效率分析--提升实际产出
按工时责任单位层别分析改善 按工时损失原因层别分析改善
精确区分、量化损 失工时,及时把握 作业效率与生产效
率起伏原因
作业效率体系 工时组成:
作业工时
总出勤工时(投入工时) (投入人员*作业时间)
直接工时 直接人员*作业时间
投入工时
实动工时
(直接工时-无作业工时)
效率 损失
标准 生产 量 工时
纯作业工时
工程项目工作总结4篇:提升项目效率的关键要素
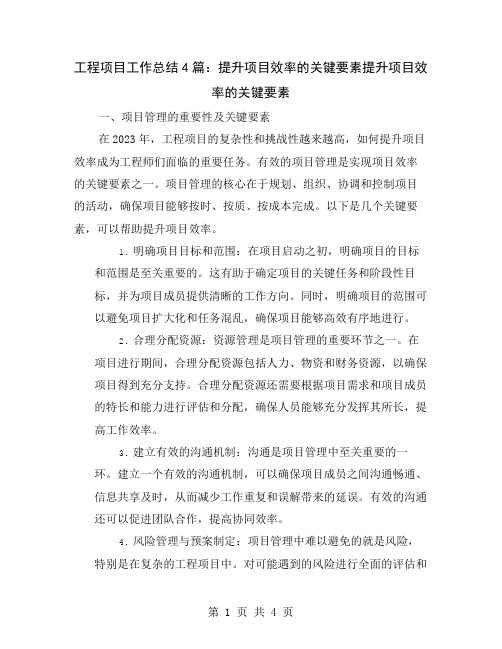
工程项目工作总结4篇:提升项目效率的关键要素提升项目效率的关键要素一、项目管理的重要性及关键要素在2023年,工程项目的复杂性和挑战性越来越高,如何提升项目效率成为工程师们面临的重要任务。
有效的项目管理是实现项目效率的关键要素之一。
项目管理的核心在于规划、组织、协调和控制项目的活动,确保项目能够按时、按质、按成本完成。
以下是几个关键要素,可以帮助提升项目效率。
1.明确项目目标和范围:在项目启动之初,明确项目的目标和范围是至关重要的。
这有助于确定项目的关键任务和阶段性目标,并为项目成员提供清晰的工作方向。
同时,明确项目的范围可以避免项目扩大化和任务混乱,确保项目能够高效有序地进行。
2.合理分配资源:资源管理是项目管理的重要环节之一。
在项目进行期间,合理分配资源包括人力、物资和财务资源,以确保项目得到充分支持。
合理分配资源还需要根据项目需求和项目成员的特长和能力进行评估和分配,确保人员能够充分发挥其所长,提高工作效率。
3.建立有效的沟通机制:沟通是项目管理中至关重要的一环。
建立一个有效的沟通机制,可以确保项目成员之间沟通畅通、信息共享及时,从而减少工作重复和误解带来的延误。
有效的沟通还可以促进团队合作,提高协同效率。
4.风险管理与预案制定:项目管理中难以避免的就是风险,特别是在复杂的工程项目中。
对可能遇到的风险进行全面的评估和预测,并制定有效的应对预案,可以最大限度地降低风险对项目的影响,并提高项目的执行效率。
二、技术应用与工程项目效率提升2023年的工程项目中,科技的应用成为提升项目效率的重要手段。
以下是几个关键要素,可以帮助提高项目效率。
1.智能化工具的应用:随着和大数据等技术的发展,智能化工具的应用正在逐渐渗透到工程项目管理中。
例如,利用智能计划软件可以自动优化项目进度和资源的调度,提高项目执行效率。
使用智能监控设备可以实时监测工程进度和质量,及时发现并解决问题。
2.虚拟技术的应用:虚拟技术在工程项目中的应用可以提高项目执行效率。
车间现场改善与效率提升

最小
最大
2
上线
2.1
3.4
2.3
3.2
3
带线入沟内
4.1
5.7
3.8
5.5
4
开机
20.8
17.7
22.9
18.6
5
过线
3.1
2.1
1.8
2.8
6
取线
15.6
10.9
11.6
12.8
7
结扎
4.2
7.0
4.8
4.2
合计
*
*
作业速度
作业条件
照明
温度、湿度
音响
色彩
身体条件
人际关系
经济状态
其他成员
上司
同事
工艺流程:清楚工艺流程及上、下道工序的配合要求
*
*
1
2
3
4
5
6
7
8
9
标准作业的四个要素
件数量;
1、周期时间:指生产一件工件需要的
按工艺要求先后排列的工件加工顺序。
停留的时间。
工时标准化即工时定额。是在正常操作条件下, 以标准的作业方法及合理的劳动强度和速度下完成 符合质量要求的工作所需的作业时间。它具有以下 五项主要因素: 1、正常的操作条件:不易引起疲劳的操作, 如女工搬运重量不宜超过4.5公斤; 2、熟练程度:大多数普通中等偏上作业者能 掌握; 3、作业方法:作业标准规定的方法; 4、劳动强度与速度:适合大多数操作者; 5、质量标准:以满足质量标准要求为准。
许振超的技术研究工作: 许振超和队员们在桥吊每个操作环节抠时间。桥吊启动时,说明书上写 着,达到最高时速需要5秒钟,许振超计算后提出,3.5秒钟就够用,一些司机不以为然地提出,抠.1.5秒有什么用?许振超为大家算了一笔账:“如果一船有1000个集装箱,就能节约25分钟出来”。
如何高效提升车间的生产效率
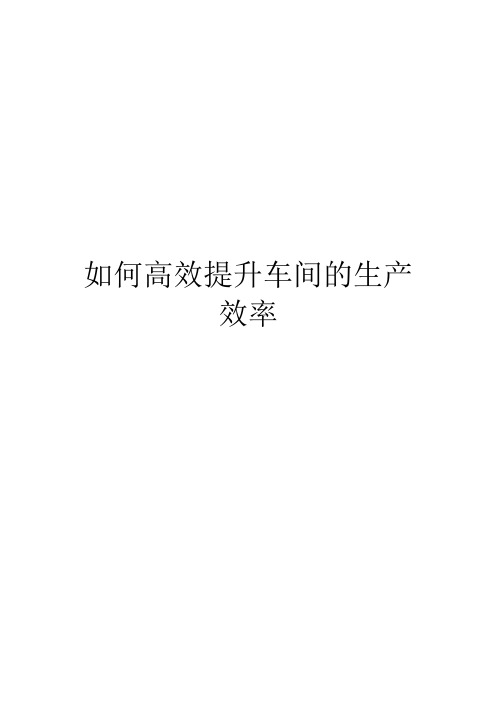
如何高效提升车间的生产效率生产率是衡量一个企业的生产要素(资源)使用效率的重要尺度,即在材料、劳动力和生产设施等方面花费相同的成本,能够生产多少产品。
对于制造业企业来说,有效的提高生产效率是降低生产成本的关键。
一、解决瓶颈生产工序这是最简单的一招,但也是最厉害的一招,我自己的“名言”是,“把简单的招式练到极至就是绝招”。
有一句格言:“瓶颈工序决定最大产能”。
众所周知,均衡是生产进度的重要保证,在100个环节中,只要存在一个环节效率低下,那么99个环节的努力都可能解决不了进度落后的问题。
因此,抓住瓶颈工序的生产节拍,不断予以改善,是提升效率最重要的法宝。
旧的瓶颈解决,新的瓶颈又产生,不断消除瓶颈,持续推动组合优化,实现生产效率大提升。
那么,如何有效解除瓶颈工序呢?常采用的解除瓶颈五步法:①.找出系统的瓶颈;②.决定如何挖尽瓶颈的潜能;③.给予瓶颈最优质的资源支持;④.给瓶颈松绑(绕过、替代、外包);⑤.假如步骤四打破了原有的瓶颈,那么就回到步骤一,持续改进,重新寻找新瓶颈。
二、实施绩效、计件薪酬记得一位管理大师曾说过:“如果一家企业员工的固定工资超过70%,这家企业就已经离死亡不远了”。
这句话很容易理解,因为“旱涝保收”的员工根本就不可能有积极性,我们经常讲的一句俏皮话是“计时不要脸(摸鱼),计件不要命”。
实际上,管理就是利益分配,分配得好就是双赢和多赢。
我曾到过一家上万人的企业,他们企业内部有10多名IE工程师,天天研究如何再提升效率,但效率就是提升不上来。
我的说法非常简单,“现场效率改善不是牺牲员工利益达成公司的利益,这样的改善注定会失败”。
意思是:“IE工程师是研究如何让员工做得更快更好,但员工做得更快更好相对于来讲就更辛苦,员工更辛苦如果工资没有上涨他肯定就不干了”。
实际上,生产管理最宝贵的财富是员工,员工的核心是激励,激励的重点是满足员工的需求。
生产现场作业部分(比如说点焊,焊锡等加工工序)必须采用计件制。
装配式建筑施工效率提升案例分析
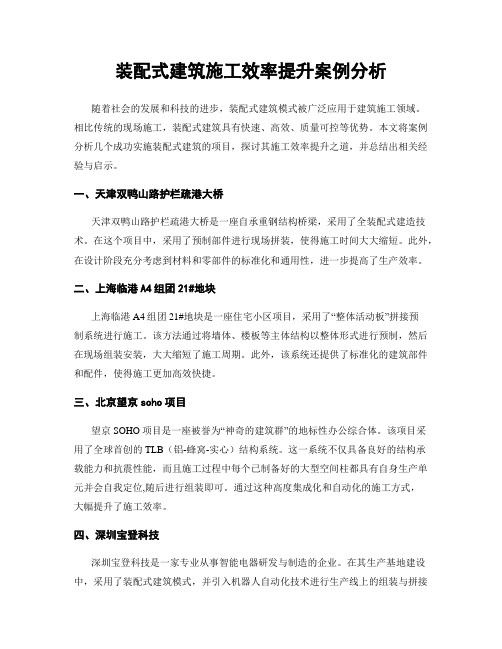
装配式建筑施工效率提升案例分析随着社会的发展和科技的进步,装配式建筑模式被广泛应用于建筑施工领域。
相比传统的现场施工,装配式建筑具有快速、高效、质量可控等优势。
本文将案例分析几个成功实施装配式建筑的项目,探讨其施工效率提升之道,并总结出相关经验与启示。
一、天津双鸭山路护栏疏港大桥天津双鸭山路护栏疏港大桥是一座自承重钢结构桥梁,采用了全装配式建造技术。
在这个项目中,采用了预制部件进行现场拼装,使得施工时间大大缩短。
此外,在设计阶段充分考虑到材料和零部件的标准化和通用性,进一步提高了生产效率。
二、上海临港A4组团21#地块上海临港A4组团21#地块是一座住宅小区项目,采用了“整体活动板”拼接预制系统进行施工。
该方法通过将墙体、楼板等主体结构以整体形式进行预制,然后在现场组装安装,大大缩短了施工周期。
此外,该系统还提供了标准化的建筑部件和配件,使得施工更加高效快捷。
三、北京望京soho项目望京SOHO项目是一座被誉为“神奇的建筑群”的地标性办公综合体。
该项目采用了全球首创的TLB(铝-蜂窝-实心)结构系统。
这一系统不仅具备良好的结构承载能力和抗震性能,而且施工过程中每个已制备好的大型空间柱都具有自身生产单元并会自我定位,随后进行组装即可。
通过这种高度集成化和自动化的施工方式,大幅提升了施工效率。
四、深圳宝登科技深圳宝登科技是一家专业从事智能电器研发与制造的企业。
在其生产基地建设中,采用了装配式建筑模式,并引入机器人自动化技术进行生产线上的组装与拼接作业。
这种方式不仅可以节省人力成本,还可以提高产品质量和产能。
在这个案例中,装配式建筑将工业生产和建筑施工相结合,实现了高效率的生产和施工。
五、广州新白云国际机场扩展项目广州新白云国际机场扩展项目是我国目前大规模采用装配式建筑技术的一项重大项目。
通过引入模块化、预制构件等先进技术,该项目实现了高度标准化和工程化的施工,大大提升了施工效率。
在这个项目中,预制构件的制造和现场组装过程几乎同时进行,有效缩短了工期。
钻井工程中提高钻井效率的措施
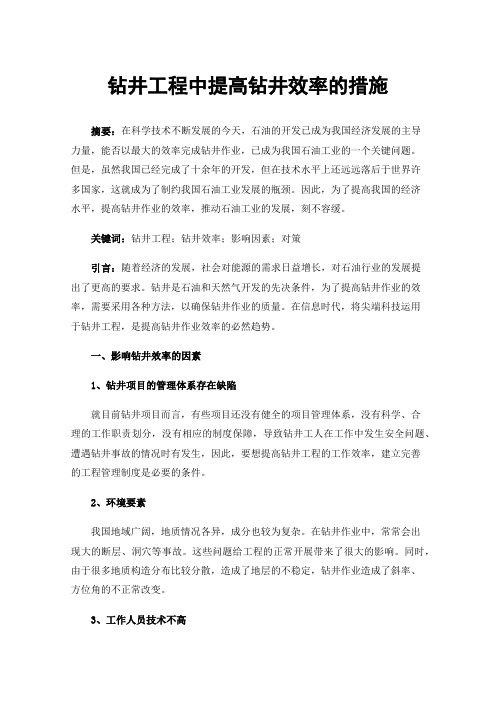
钻井工程中提高钻井效率的措施摘要:在科学技术不断发展的今天,石油的开发已成为我国经济发展的主导力量,能否以最大的效率完成钻井作业,已成为我国石油工业的一个关键问题。
但是,虽然我国已经完成了十余年的开发,但在技术水平上还远远落后于世界许多国家,这就成为了制约我国石油工业发展的瓶颈。
因此,为了提高我国的经济水平,提高钻井作业的效率,推动石油工业的发展,刻不容缓。
关键词:钻井工程;钻井效率;影响因素;对策引言:随着经济的发展,社会对能源的需求日益增长,对石油行业的发展提出了更高的要求。
钻井是石油和天然气开发的先决条件,为了提高钻井作业的效率,需要采用各种方法,以确保钻井作业的质量。
在信息时代,将尖端科技运用于钻井工程,是提高钻井作业效率的必然趋势。
一、影响钻井效率的因素1、钻井项目的管理体系存在缺陷就目前钻井项目而言,有些项目还没有健全的项目管理体系,没有科学、合理的工作职责划分,没有相应的制度保障,导致钻井工人在工作中发生安全问题、遭遇钻井事故的情况时有发生,因此,要想提高钻井工程的工作效率,建立完善的工程管理制度是必要的条件。
2、环境要素我国地域广阔,地质情况各异,成分也较为复杂。
在钻井作业中,常常会出现大的断层、洞穴等事故。
这些问题给工程的正常开展带来了很大的影响。
同时,由于很多地质构造分布比较分散,造成了地层的不稳定,钻井作业造成了斜率、方位角的不正常改变。
3、工作人员技术不高由于钻探技术人员的技能不能适应钻井作业的要求,技术水平达不到要求,极易因人为因素而发生钻探事故,给钻井工程带来重大的经济损失。
从事钻探作业的人员,必须具备各种作业的执照和井上的管理技能。
但是,现在的钻井技术人员在遇到突发事件时,应急反应能力不能满足要求,一旦出现突发事件,就不能确保安全,对钻井作业和施工作业造成极大的威胁,从而影响到钻井作业的正常开展。
4、技术要素随着世界上钻井工程技术的迅速发展,许多现代钻探技术被引进和应用于我国。
精益生产八大步骤:生产效率提升与合理化改善
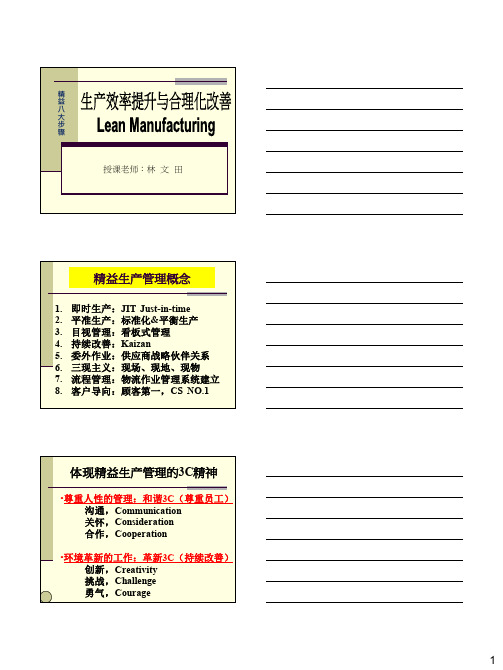
授课老师:林 文 田精益八大步骤1.即时生产:JIT Just-in-time2.平准生产:标准化&平衡生产3.目视管理:看板式管理4.持续改善:Kaizan5.委外作业:供应商战略伙伴关系6.三现主义:现场、现地、现物7.流程管理:物流作业管理系统建立 8.客户导向:顾客第一,CS NO.1精益生产管理概念体现精益生产管理的3C 精神•尊重人性的管理:和谐3C (尊重员工) 沟通,Communication 关怀,Consideration 合作,Cooperation•环境革新的工作:革新3C (持续改善) 创新,Creativity 挑战,Challenge 勇气,CourageWhat is Lean Manufacturing 什么是精益生产制造-五个原则LeanManufacturing精益生产Value 价值站在客户 的立场上Value Stream 价值流 从接单到发货 过程的一切活动Flow 流动象开发的河流 一样通畅流动Demand Pull需求拉动 BTR-按需求生产Perfect 完美没有任何事物 是完美的 不断改进降低成本, 改善质量, 缩短生产周期生产管理的新思维:Lean manufacturing1.精益生产管理的思维:PQCDMS2.精益生产管理的新4Ps3.生产管理工作者的六大职能4.准时化生产方式的思维:ECRSC 杜绝浪费精益生产管理的三大思维 &PQCDMSQ 改善品质D 加速流程P 流程计划M 团队士气S 工作安全TQM 人、机、料、法、测、环、信PI+SQ CD产能士气安全 S C 团队 C.D.IE生计5SMRPCRM 投入产出创造价值依据顾客需求建立价值创新的工作流程程序1. Phiosophy :长期理念:长期效益与价值选择。
2. Process :正确流程:重视流程管理(5M 管理)3. People + Partners :优秀员工+事业伙伴:重视人性、自主化4. Problems :解决问题:没有最好的,只有更好的!实践精益Lean Production 的4Ps实践精LP 的四大原则4Ps第一原则:长期经营的理念以长期为指标,既使牺牲短期利益。
提升工程施工效率的秘诀
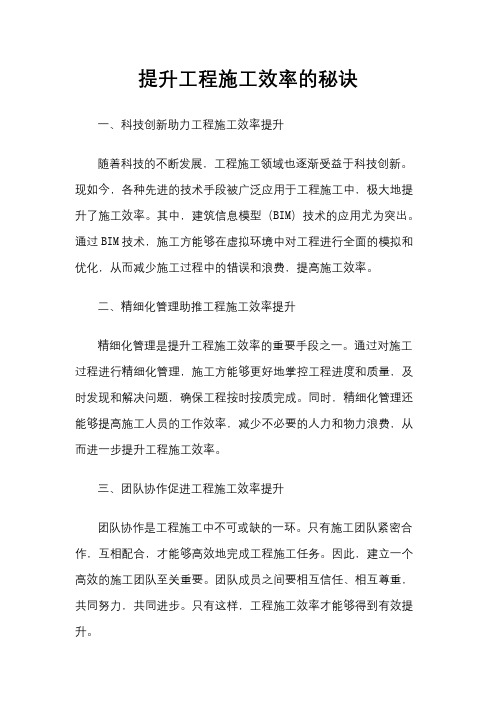
提升工程施工效率的秘诀一、科技创新助力工程施工效率提升随着科技的不断发展,工程施工领域也逐渐受益于科技创新。
现如今,各种先进的技术手段被广泛应用于工程施工中,极大地提升了施工效率。
其中,建筑信息模型(BIM)技术的应用尤为突出。
通过BIM技术,施工方能够在虚拟环境中对工程进行全面的模拟和优化,从而减少施工过程中的错误和浪费,提高施工效率。
二、精细化管理助推工程施工效率提升精细化管理是提升工程施工效率的重要手段之一。
通过对施工过程进行精细化管理,施工方能够更好地掌控工程进度和质量,及时发现和解决问题,确保工程按时按质完成。
同时,精细化管理还能够提高施工人员的工作效率,减少不必要的人力和物力浪费,从而进一步提升工程施工效率。
三、团队协作促进工程施工效率提升团队协作是工程施工中不可或缺的一环。
只有施工团队紧密合作,互相配合,才能够高效地完成工程施工任务。
因此,建立一个高效的施工团队至关重要。
团队成员之间要相互信任、相互尊重,共同努力,共同进步。
只有这样,工程施工效率才能够得到有效提升。
四、持续学习不断提升工程施工效率工程施工是一个不断发展和变化的领域,只有不断学习和提升自己,才能够跟上时代的步伐,提高工程施工效率。
施工人员应该保持学习的热情,不断学习新的施工技术和管理方法,不断提升自己的专业水平和综合素质。
只有这样,才能够在激烈的市场竞争中立于不败之地,实现工程施工效率的持续提升。
五、结语提升工程施工效率是每个施工方都在追求的目标。
通过科技创新、精细化管理、团队协作和持续学习,工程施工效率将得到有效提升,为工程建设事业的发展注入新的活力。
让我们携手并进,共同努力,为提升工程施工效率贡献自己的力量!。
部门工作效率提升计划9篇
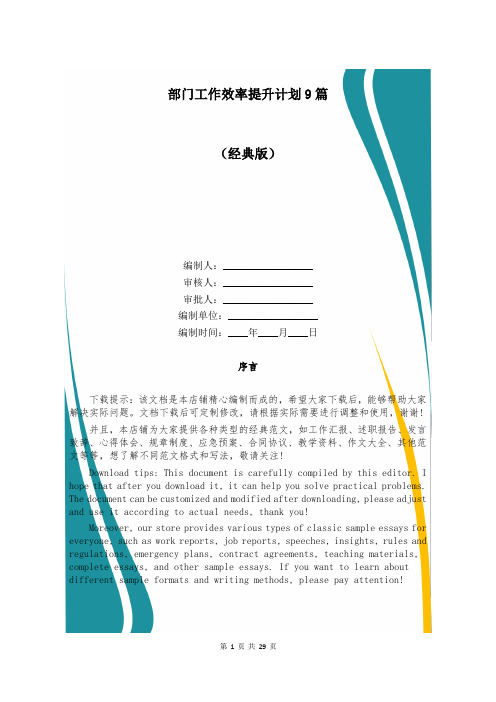
部门工作效率提升计划9篇(经典版)编制人:__________________审核人:__________________审批人:__________________编制单位:__________________编制时间:____年____月____日序言下载提示:该文档是本店铺精心编制而成的,希望大家下载后,能够帮助大家解决实际问题。
文档下载后可定制修改,请根据实际需要进行调整和使用,谢谢!并且,本店铺为大家提供各种类型的经典范文,如工作汇报、述职报告、发言致辞、心得体会、规章制度、应急预案、合同协议、教学资料、作文大全、其他范文等等,想了解不同范文格式和写法,敬请关注!Download tips: This document is carefully compiled by this editor. I hope that after you download it, it can help you solve practical problems. The document can be customized and modified after downloading, please adjust and use it according to actual needs, thank you!Moreover, our store provides various types of classic sample essays for everyone, such as work reports, job reports, speeches, insights, rules and regulations, emergency plans, contract agreements, teaching materials, complete essays, and other sample essays. If you want to learn about different sample formats and writing methods, please pay attention!部门工作效率提升计划9篇下面是本店铺收集的部门工作效率提升计划9篇,供大家参考。
建筑工程的施工效率
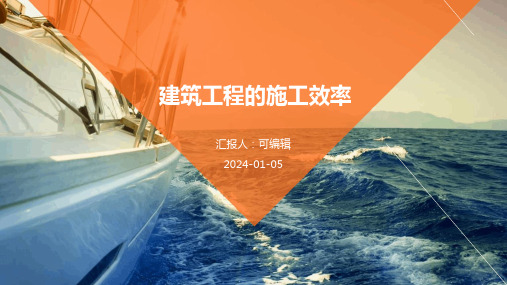
大数据分析与预测
利用大数据技术对施工过程中的数据进行分析和 预测,能够及时发现和解决潜在问题,优化施工 进度和资源分配。
05 施工效率的评估与改进
施工效率的评估方法
进度评估
通过比较实际完成进度与计划进度,评估施 工效率。
施工人员技能水平不高 、经验不足等会影响施 工效率。
施工现场环境
施工现场环境恶劣、安 全事故等也会对施工效 率产生影响。
提高施工效率的方法和策略
优化施工组织管理
制定科学合理的施工计划,加强现场协调管 理,确保各项工作的顺利进行。
加强施工人员培训与管理
提高施工人员技能水平,加强现场管理,确 保施工质量与安全。
根据施工需要,租赁适量 的施工设备,并做好设备 的维护和保养工作,确保 设备正常运行。
施工队伍的组建与培训
队伍组建
根据工程规模和要求,组建专业的施工队伍,确保人员具备相应的技能和资质 。
培训与交底
对施工人员进行岗前培训和安全教育,提高人员的技能水平和安全意识。同时 ,进行技术交底,使施工人员了解施工方案和技术要求。
施工质量的保证
建立质量管理体系
制定严格的质量标准和检 验制度,确保各环节的施 工质量符合要求。
加强材料管理
对进场的材料进行质量检 查和控制,确保材料质量 合格,防止因材料问题影 响施工质量。
提高施工人员素质
定期对施工人员进行培训 和考核,提高其技能水平 和质量意识。
施工安全的保障
制定安全规章制度
筑物的能效,降低能耗。
高强度材料
采用高强度材料,如高强钢和高 性能混凝土,能够减少结构构件 的尺寸和重量,提高施工效率。
施工工程效率(3篇)
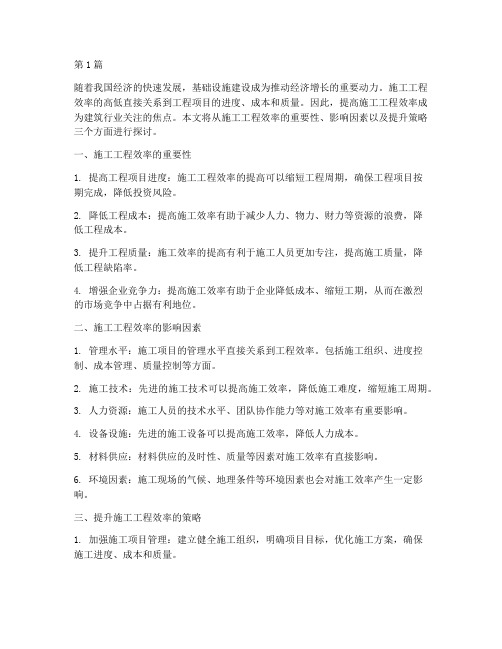
第1篇随着我国经济的快速发展,基础设施建设成为推动经济增长的重要动力。
施工工程效率的高低直接关系到工程项目的进度、成本和质量。
因此,提高施工工程效率成为建筑行业关注的焦点。
本文将从施工工程效率的重要性、影响因素以及提升策略三个方面进行探讨。
一、施工工程效率的重要性1. 提高工程项目进度:施工工程效率的提高可以缩短工程周期,确保工程项目按期完成,降低投资风险。
2. 降低工程成本:提高施工效率有助于减少人力、物力、财力等资源的浪费,降低工程成本。
3. 提升工程质量:施工效率的提高有利于施工人员更加专注,提高施工质量,降低工程缺陷率。
4. 增强企业竞争力:提高施工效率有助于企业降低成本、缩短工期,从而在激烈的市场竞争中占据有利地位。
二、施工工程效率的影响因素1. 管理水平:施工项目的管理水平直接关系到工程效率。
包括施工组织、进度控制、成本管理、质量控制等方面。
2. 施工技术:先进的施工技术可以提高施工效率,降低施工难度,缩短施工周期。
3. 人力资源:施工人员的技术水平、团队协作能力等对施工效率有重要影响。
4. 设备设施:先进的施工设备可以提高施工效率,降低人力成本。
5. 材料供应:材料供应的及时性、质量等因素对施工效率有直接影响。
6. 环境因素:施工现场的气候、地理条件等环境因素也会对施工效率产生一定影响。
三、提升施工工程效率的策略1. 加强施工项目管理:建立健全施工组织,明确项目目标,优化施工方案,确保施工进度、成本和质量。
2. 推广先进施工技术:引进和应用先进的施工技术,提高施工效率,降低施工难度。
3. 优化人力资源配置:加强施工人员培训,提高技术水平,培养一支高素质的施工队伍。
4. 提升设备设施水平:引进先进的施工设备,提高设备利用率,降低设备维护成本。
5. 保障材料供应:建立健全材料采购、储存、运输等环节的管理制度,确保材料供应及时、质量可靠。
6. 加强施工现场管理:优化施工流程,合理调配资源,提高施工现场管理效率。
建筑施工方案优化效率提升工程质量的关键步骤

建筑施工方案优化效率提升工程质量的关键步骤建筑施工方案在保证项目工程质量的同时,还应考虑效率的提升,以确保工期的合理控制。
本文将介绍建筑施工方案优化效率的关键步骤,以提升工程质量。
1. 定义项目目标在制定施工方案之前,首先需要明确项目目标和要求。
这包括了工程的质量要求、工期要求、安全要求等。
明确项目目标有助于全面考虑并合理安排施工方案的各项内容,确保最终的施工方案能够达到预期的效果。
2. 进行前期调研在制定施工方案之前,进行充分的前期调研非常重要。
这包括了对工程地点的环境、地质条件的了解,以及对类似项目的案例分析等。
通过前期调研,可以更好地了解项目的特点和难点,从而有针对性地制定施工方案。
3. 制定详细的施工流程基于前期调研的结果,制定详细的施工流程是提升工程质量的重要步骤之一。
施工流程应包括施工过程中的每一个环节和相应的工序,以及各个工序之间的协调关系。
详细的施工流程能够帮助施工人员更好地把握施工进度和质量,从而提高施工效率。
4. 合理设置施工工艺根据具体的工程要求,合理设置施工工艺是优化施工方案的一项关键步骤。
施工工艺的设置直接影响到施工效率和工程质量。
例如,在施工过程中使用先进的施工设备和技术,可以提高工程效率和质量;合理选择施工材料,有助于减少浪费和提高工程质量。
5. 引入信息化管理系统引入信息化管理系统是提升施工方案效率的重要手段之一。
通过信息化系统,可以实现施工过程的数字化管理和实时监控,从而提高施工效率和质量。
信息化管理系统可以包括施工进度管理、质量控制、材料管理等方面,有效地提升施工方案的管理水平和执行效率。
6. 加强沟通与协作施工方案的优化还需要加强施工团队的沟通与协作。
只有团队成员之间密切配合,及时解决施工中出现的问题,才能确保施工方案的顺利实施。
因此,在制定施工方案的过程中,建立良好的沟通机制和协作机制,加强各方之间的合作,对于提升施工质量和效率具有重要意义。
7. 进行施工方案评估最后,对制定的施工方案进行评估和反思是提升工程质量的关键步骤。
起重吊车施工效率提升策略
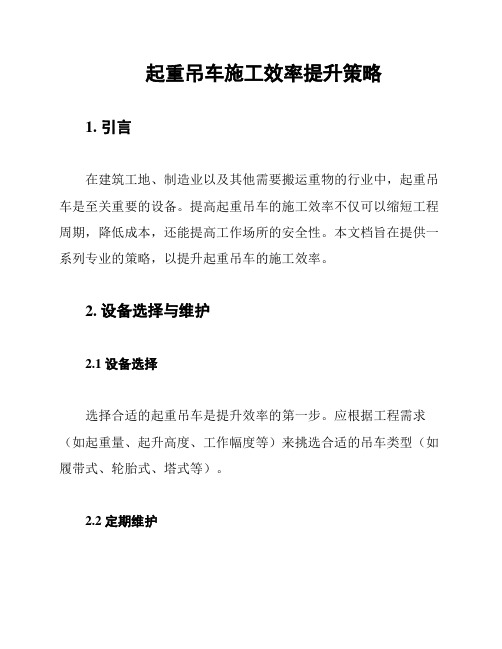
起重吊车施工效率提升策略1. 引言在建筑工地、制造业以及其他需要搬运重物的行业中,起重吊车是至关重要的设备。
提高起重吊车的施工效率不仅可以缩短工程周期,降低成本,还能提高工作场所的安全性。
本文档旨在提供一系列专业的策略,以提升起重吊车的施工效率。
2. 设备选择与维护2.1 设备选择选择合适的起重吊车是提升效率的第一步。
应根据工程需求(如起重量、起升高度、工作幅度等)来挑选合适的吊车类型(如履带式、轮胎式、塔式等)。
2.2 定期维护定期对起重吊车进行维护检查,包括对发动机、液压系统、传动系统、制动系统、钢丝绳、吊钩等关键部件的检查和保养,以确保设备始终处于良好的工作状态。
3. 作业流程优化3.1 作业前准备- 制定详细的作业计划和应急预案。
- 对操作人员进行专业培训和考核,确保其了解作业流程和安全规程。
- 对现场环境进行彻底检查,确保无妨碍吊车作业的障碍物。
3.2 作业中管理- 遵循“安全第一”的原则,严格遵守操作规程。
- 实施作业过程中的实时监控,确保吊装平稳、精准。
- 采用先进的调度系统,合理规划吊车的工作时间和任务分配。
3.3 作业后评估- 完成每次作业后,及时收集反馈信息,评估作业效率。
- 对遇到的问题进行记录和分析,不断优化作业流程。
4. 技术创新与应用4.1 自动化技术引入自动化技术,如自动导航、自动调节起重高度和角度等,减少人工操作,提高精准度和效率。
4.2 信息化管理利用信息化手段,如GPS定位、传感器监测等,实时监控吊车的位置、状态和工作环境,以便快速响应和调整作业策略。
4.3 节能技术采用节能型吊车和高效的传动技术,减少能源消耗,提高施工的可持续性。
5. 人员培训与团队建设5.1 培训内容- 专业技能培训:包括操作规程、设备维护、应急处理等。
- 安全意识培训:强化操作人员的安全意识,预防事故的发生。
5.2 团队建设- 建立高效的团队沟通机制,确保信息流畅无阻。
- 鼓励团队协作,培养操作人员之间的默契和信任。
- 1、下载文档前请自行甄别文档内容的完整性,平台不提供额外的编辑、内容补充、找答案等附加服务。
- 2、"仅部分预览"的文档,不可在线预览部分如存在完整性等问题,可反馈申请退款(可完整预览的文档不适用该条件!)。
- 3、如文档侵犯您的权益,请联系客服反馈,我们会尽快为您处理(人工客服工作时间:9:00-18:30)。
否 作业合理性 与符合性
是 作成正式 版要领书
44
要领书运作流程—修订流程
工艺条件 变更 作业改善
作业 观察
核对工序修订 的内容
修订作业 要领书
检查 确认
作业要领书 的验证
要领书的发 行与培训
作业要领 书审批
否 作业合理性 与符合性
是 作成正式 版要领书
45
要领书实施要点
1. 由班长或熟练员工编制。 2. 首先要符合技术和工艺、安全要求,并与品质标准保持一致;当工艺
50
作业转换改善体系
转换分析
内部 作业 转换
明确区分 转化
外部 作业 转换
将外部转换作业标准化 只把该设备必要的部分标准化 使用快速紧固件 使用辅助用具 推行同时作业 采用利用机械的自动作业转换方式
51
改进后的作业转换
❖ 一旦设备停止运转,作业人员绝对不要离开设备参与外部作业转换的操作。 ❖ 在外部作业转换中,模具、工具以及材料必须事前整整齐齐地准备到设备
TT = 一个班的生产时间/一天必须产量
(2)生产时间(C/T)。指作业者进行标准作业时,完成工作的实际作业时间。
(3)T/T与C/T的关系。 ➢C/T>T/T,说明此工位为瓶颈工位,需要改善; ➢C/T < < T/T,说明此工位有大量等待时间. ➢C/T=T/T是理想状态.通常C/T略小于T/T.
• 人员合理否?
• 安全隐患否?
30
躯体动作范围
31
动作分解
拔热水瓶盖的动作分解
放遥控器的动作分解
找到文件的动作分解
32
动作改善案例
螺丝螺母配合作业
尽量保持双手动作的 平衡
33
创意工夫实施流程
提案者
想法 报告
改善实施
上级
NO
许可
YES
指导、商量
效果确认
提案书写
事实确认/审查
优秀提案
YES
标准化、横展
动作改善、作业流程改善、物流改善、设 备模夹治具改善、品质改善、管理改善等
八大浪费
动作标准化、作业流程标准化、操作流 程标准化、包装运输标准化等
整理、整顿、清扫、清洁、素养等
11
浪费——万恶之源
12
拉动式管理
毛胚 准备
工序 1
工序 2
工序 n
组装
顾客 需求
生产 计划
拉动式生产的内容
a. 以市场需求拉动企业生产 b. 以后道工序拉动前道工序 c. 以生产一线拉动辅助生产和服务生产 d. 以主厂拉动协作配套厂
47
典型案例
作业观察与要领书的修订 作业观察
要领书不符的制订、修订计划
修订后的要领书
48
反思与分享
1. 外国两小时到一天,丰田一分钟以内!(丰田提出个位数 换模,即在10分钟之内)
2. 即使设备的运转率低,也要优先保证库存最小 ; 3. 单一作业转换 ;
49
作业的快速切换改善步骤
第一步:明确区分内部作业转换和外部作业转换
B
40unit/w k
5w探寻真因
瓶颈管理的原则
系统的能力是由瓶颈决定。 瓶颈能力的损失,则是系统的损失 非瓶颈能力提升,与系统能力无关。
21
问题冰山模型和5Why一问到底
现象 (可感觉、可衡量)
治标
一次因 (近因)
治本
n次因 (根因)
22
案例
背景:某车间生产效率一直偏低,连续三个月均在 定额指标65%—75%之间。
15
作业改善五要素
第五要素
自我完善
第一要素
更容易
第四要素
更稳定
改善的 思考
第三要素
更安全
第二要素
更便利
16
改善永无止境
改善原则
1、打破固有观念; 2、寻找可行的方法; 3、不要分辩,要否定现状; 4、不要力求完美,50分也好, 立即实施; 5、错了马上改善; 6、先从不花钱的改善做起; 7、穷则变,变则通! 8、追求根源,反复五次为什么; 9、十个人的智慧比一个人的智 慧高明; 10、改善是无限的!
A、质量的稳定与提高; B、提高作业的安全性、稳定性; C、降低劳动强度; D、降低成本、减少工时; E、减少在制品库存; F、全面贯彻目视化管理。
43
要领书运作流程—初编流程
制定《作业要领书制 定、修订计划》
编制作业 要领书
检查 确认
作业要领书 的验证
作业 观察
要领书的发 行与培训
作业要领 书审批
13
作业研究
作业 研究
方法 研究
时间 研究
生产过程分析 (工程分析) 动作分析 作业分析
制定 标准作业
秒表测时法 标准时间资料法 既定时间法
制定 时间标准
新工作 员工 实施 标准 培训 新标准
改进完善
14
工序瓶颈和人员浪费的原因何在?
工序间生产能力失衡 a. 生产能力规划失误 b. 设备故障、减员等突发事件 工序生产进度失控 a. 出现严重质量事故——大量返工 b. 原材料脱节 c. 环境、工艺条件不达标
厂家多
故障高
方法
材料
机器
24
案例
步骤四:找出主要原因,并把他圈起来
环境
温度 湿度
管理
薪资管理 污染 考核制度
人员
管理人员 缺乏训练
变化多 士气
不足 生手多
不良多 维修多
品质
场所乱
没有标准
工具
经常中断
方法
材料
不良多
不足
开机率低
厂家多
故障高
机器
25
案例
步骤五:主要原因再分析
缺乏训练计划
缺乏教导人员
缺乏时间
目识化板案例(公司级宣传栏)
先进人物表彰宣传栏
36
创意工夫的目视化管理
目识化板案例(公司级宣传栏)
优秀创意工夫宣传栏
37
创意工夫的目视化管理
目识化板案例(班组级宣传栏)
班组创意工夫宣传栏
38
效率提升与标准化
管理、监督者
教育、培训
作业者
制定
标出安 全标记 保证安全
管理 标准作业
规定标 准在库
降低库存
规定检 查频度
保障品质
执行
最有效 作业顺序 生产效率最高
39
标准化与改善
世界级
改善
标准化
没有标 准作业 的地方 就没有 改善!
改善
改善
改善
标准化
标准化 标准化
标准化
40
标准作业(SOS)十大要素
时间要素
(1)节拍时间(T/T)。有人也将其称为标准工时,是指应该用多长时间生 产一个或一件合格产品。它是由必须产量和一个班的生产时间。
9
共识
正确思维+心态+方法+行动+不断学习 才是
活的竞争力!
10
效率提升的本质内涵
竞争力提升
效率提升的本质内涵:企业三流的顺畅、 低波动和快速反应及资源的充分、低浪费;其 手法,是通过消除各类浪费、理顺价值链、进 行标准化、流程化和不断改善
品质提升
效&率提升
形象提升
改善 消除浪费 标准化 现场5S
动作难度 动作准确性 动作速度和节奏
动作最少
双手操作
基本 原则
轻松节奏
距离最短
动作效率的提升是综合上述五大要素,以便取得综合效果!
28
动作经济的4项实战原则
双手并用原则
对称反向原则
排除合并原则
降低动作等级原则
29
问题点的发现
动作效率检查表
项目
检查重点
结果
• 较难动作否?
• 易疲劳否?
难度
• •
环境便宜否? 动作轻松否?
标准作业的制定
作业观 察
作业分 析
作业测 定
组合图
组合表
标准文 件
42
标准作业与改善
标准作业是改善之本。 因为标准作业是以人的动作为中心而制定的,各项作业时间有出入, 则清楚地表明还有改善的余地。 持续性的改善活动是标准作业改善最出色的特点。 改善标准作业后,将以新的标准作业进行生产,并明确下一步的 改善方向。 标准作业的改善重点
大凡成功的案例,都有意无意的使用了一 定的谋略、技法和流程,不管你是否意识到这 些。
4
惊掉您的下巴
95%
26分钟 VS 28天
99.9%
5
意识—结果三部曲
意识
目标 行动 结果 一切
6
共识
意识远比工具重要!
7
现场效率提升三大意识
顾客价值
当家意识
效率3 大意识
彻底沟通
8
反思与分享
1. 我对意识的认识如何? 2. 我在工作和生活中的指导思想是什么? 3. 这些思想对我工作和生活的影响如何? 4. 我应具有什么样的指导思想?
46
要领书实施要点
7.作业要领书在编制后,需根据实际使用状况,不断地进行修订和优化。 这项工作将成为以后班长的日常工作。通过标准作业的开展,实现班长管 理行为的转变。 8.在产品型号较多、较复杂的状况下,标准作业导入初期,可先编制主流 产品(如产量前四位的产品)的作业要领书。 9.作业要领书的编制按照一个作业员一份要领书的原则进行。一人一机, 一人多机时均为一份作业要领书。多人一机和多人多机时,要领书的数量 与作业员数量一致。 10.作业要领书是公司保密文件,公司可根据需要适当揭示。 11.作业要领书编制完成后,如含有品质部门直接参与过程检验的内容, 需知会品质部门。
综上所述,通过作业分析,应达到使作业的结构合理、作业者的劳动强 度减轻、作业的时间消耗减少,保证生产质量,提高作业效率。 双手操作分析(操作者作业分析); 人机操作分析; 联合操作分析(工组作业分析)。