难熔金属粉末冶金制备新技术
难熔金属粉末冶金制备新技术
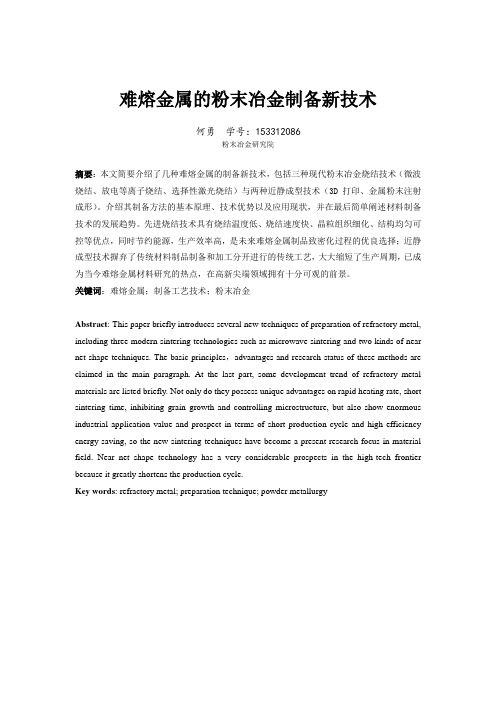
难熔金属的粉末冶金制备新技术何勇学号:153312086粉末冶金研究院摘要:本文简要介绍了几种难熔金属的制备新技术,包括三种现代粉末冶金烧结技术(微波烧结、放电等离子烧结、选择性激光烧结)与两种近静成型技术(3D打印、金属粉末注射成形)。
介绍其制备方法的基本原理、技术优势以及应用现状,并在最后简单阐述材料制备技术的发展趋势。
先进烧结技术具有烧结温度低、烧结速度快、晶粒组织细化、结构均匀可控等优点,同时节约能源,生产效率高,是未来难熔金属制品致密化过程的优良选择;近静成型技术摒弃了传统材料制品制备和加工分开进行的传统工艺,大大缩短了生产周期,已成为当今难熔金属材料研究的热点,在高新尖端领域拥有十分可观的前景。
关键词:难熔金属;制备工艺技术;粉末冶金Abstract: This paper briefly introduces several new techniques of preparation of refractory metal, including three modern sintering technologies such as microwave sintering and two kinds of near net shape techniques. The basic principles,advantages and research status of these methods are claimed in the main paragraph. At the last part, some development trend of refractory metal materials are listed briefly.Not only do they possess unique advantages on rapid heating rate, short sintering time, inhibiting grain growth and controlling microstructure, but also show enormous industrial application value and prospect in terms of short production cycle and high efficiency energy saving, so the new sintering techniques have become a present research focus in material field.Near net shape technology has a very considerable prospects in the high-tech frontier because it greatly shortens the production cycle.Key words: refractory metal; preparation technique; powder metallurgy1 前言难熔金属[1]一般是指熔点在2000℃以上的过渡金属元素,广义上包括钨(W)、钼(Mo)、钽(Ta)、铌(Nb)、钛(Ti)、钒(V)、铬(Cr)、锆(Zr)等十几种元素。
粉末冶金钛合金制备技术分析

粉末冶金钛合金制备技术分析摘要:钛合金的应用广泛,涵盖了航空航天、船舶运输、汽车工业、医疗器械等领域,究其根本,其金属属性优良,具备生物兼容性,虽然金属的整体密度较低,但强度很高,且具有良好的耐热性、耐腐蚀性。
但是,钛价格昂贵,因此,如何有效地降低产品成本、提高合金性能,是钛合金生产中亟待解决的问题。
相比传统的制备方式,粉末冶金方法简化了融化、锻造等过程,钛合金产品直接产出,减少了制备过程中的材料浪费,在提高产量的同时,也为生产企业节约了成本,因而广受业内人士关注。
关键词:粉末冶金;钛合金;制备技术一、粉末冶金钛合金特点目前,国内钛合金产品的生产方式以熔铸工艺和粉末熔炼工艺为主。
钛是一种化学性质非常活泼的金属性材料,熔点较高,不能使用传统的熔铸载体,只能选用无坩埚或水冷铜坩埚中的一种,这种熔铸方式,会产生较高的经济投入,熔炼过程中会产生较高的能耗,而最终产品的纯度却不高。
粉末冶金制备过程与传统工艺存在较大差异,对温度要求较低,只需要低于熔点的温度便可进行制备,以金属粉末为原料进行成型和烧结,可实现近净成形,且加工费用较低。
通常,企业可使用氢化脱氢法、气雾化法、旋转式电极雾化法等制备钛粉。
虽然钛的金属活泼性较高,但因为处于较低的温度,避免了与其他材料产生化学反应的情况,且组分均匀,因而这种制备方式潜力巨大,受到各领域的追捧。
二、粉末冶金钛合金制备技术(一)钛粉制备工艺钛粉制备工艺按钛粉的形状,可分为非规则粉体制备工艺和球体粉体制备工艺两大类。
其中,非规则粉体制备工艺主要包括氢化脱氢法和热还原法,球体粉体制备工艺主要包括气雾化法、旋转式电极雾化法和等离子球化法。
1.氢化脱氢法利用钛和氢的可逆反应实现钛粉制备。
Ti和H2在一定温度和压力条件下,反应生成TiH2,其脆性较高,通过机械手段破碎可以得到微粉,再将微粉脱去氢气,即可得到纯钛粉。
该工艺可选用海绵钛或残余钛作原料,对设备的要求较低,可有效降低制钛成本,是目前最常用的钛粉制备工艺,非常适合工业化的大量生产。
粉末冶金
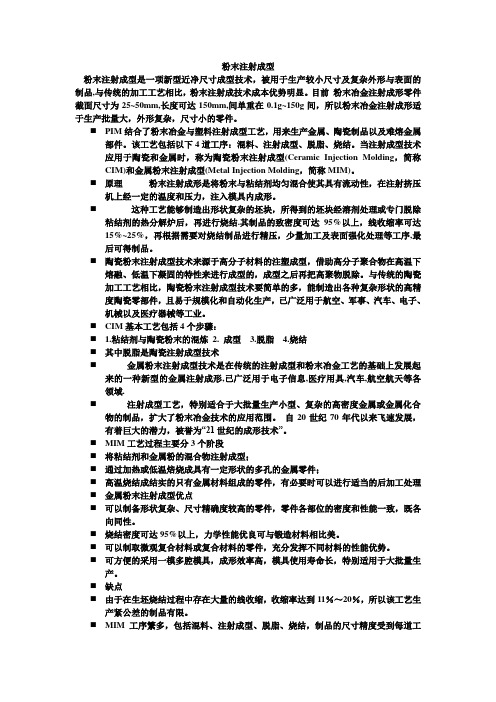
粉末注射成型粉末注射成型是一项新型近净尺寸成型技术,被用于生产较小尺寸及复杂外形与表面的制品,与传统的加工工艺相比,粉末注射成技术成本优势明显。
目前粉末冶金注射成形零件截面尺寸为25~50mm,长度可达150mm,间单重在0.1g~150g间,所以粉末冶金注射成形适于生产批量大,外形复杂,尺寸小的零件。
⏹PIM结合了粉末冶金与塑料注射成型工艺,用来生产金属、陶瓷制品以及难熔金属部件。
该工艺包括以下4道工序:混料、注射成型、脱脂、烧结。
当注射成型技术应用于陶瓷和金属时,称为陶瓷粉末注射成型(Ceramic Injection Molding,简称CIM)和金属粉末注射成型(Metal Injection Molding,简称MIM)。
⏹原理粉末注射成形是将粉末与粘结剂均匀混合使其具有流动性,在注射挤压机上经一定的温度和压力,注入模具内成形。
⏹这种工艺能够制造出形状复杂的坯块,所得到的坯块经溶剂处理或专门脱除粘结剂的热分解炉后,再进行烧结.其制品的致密度可达95%以上,线收缩率可达15%~25%,再根据需要对烧结制品进行精压,少量加工及表面强化处理等工序,最后可得制品。
⏹陶瓷粉末注射成型技术来源于高分子材料的注塑成型,借助高分子聚合物在高温下熔融、低温下凝固的特性来进行成型的,成型之后再把高聚物脱除。
与传统的陶瓷加工工艺相比,陶瓷粉末注射成型技术要简单的多,能制造出各种复杂形状的高精度陶瓷零部件,且易于规模化和自动化生产,已广泛用于航空、军事、汽车、电子、机械以及医疗器械等工业。
⏹CIM基本工艺包括4个步骤:⏹ 1.粘结剂与陶瓷粉末的混炼2. 成型 3.脱脂 4.烧结⏹其中脱脂是陶瓷注射成型技术⏹金属粉末注射成型技术是在传统的注射成型和粉末冶金工艺的基础上发展起来的一种新型的金属注射成形,已广泛用于电子信息,医疗用具,汽车,航空航天等各领域.⏹注射成型工艺,特别适合于大批量生产小型、复杂的高密度金属或金属化合物的制品,扩大了粉末冶金技术的应用范围。
难熔金属基复合材料的研究进展

难熔金属基复合材料的研究进展难熔金属基复合材料是一种具有卓越性能和广泛应用潜力的材料。
它由高熔点金属基体和分散相组成,具有高温强度、耐腐蚀性、耐磨损性和导电性等优点。
难熔金属基复合材料的研究已经取得了显著的进展,并在航空航天、能源、汽车和冶金等领域得到广泛应用。
难熔金属基复合材料的研究主要涉及材料的制备技术、性能优化和应用研究。
目前,常用的制备技术包括粉末冶金、熔融混合、机械合金化和表面改性等方法。
其中,粉末冶金是一种常用的制备难熔金属基复合材料的方法。
通过粉末冶金技术可以得到具有均匀分散相的复合材料,从而提高材料的力学性能和耐热性能。
难熔金属基复合材料的性能优化主要通过合金化和微结构控制实现。
通过合金化可以改变金属基体的组成,调整材料的力学性能和导热性能。
通过微结构控制可以调控分散相的尺寸、形状和分布,进一步提高材料的力学性能和耐热性能。
此外,难熔金属基复合材料的表面改性也是一种常用的性能优化手段。
通过在金属基体的表面引入功能性涂层,可以提高材料的表面硬度、耐磨损性和耐腐蚀性。
难熔金属基复合材料在航空航天领域具有广泛的应用前景。
在航空发动机中,难熔金属基复合材料可以作为高温结构材料使用,用于制造涡轮叶片、燃烧室和燃气轮机等部件。
难熔金属基复合材料具有出色的高温强度和耐热性能,可以提高发动机的工作效率和可靠性。
此外,在航天航空热保护系统中,难熔金属基复合材料也可以作为热隔断材料使用,有效减少空气动力热、压力热和辐射热对航天器的影响。
在能源领域,难熔金属基复合材料可以用于制造高温燃料电池和核能反应堆等设备。
难熔金属基复合材料具有优异的导电性能和耐腐蚀性,可以提高燃料电池和核能反应堆的运行效率和安全性。
此外,难熔金属基复合材料还可以用于制造高温储能设备,用于储存太阳能和风能等可再生能源。
在汽车领域,难熔金属基复合材料可以用于制造发动机和制动系统等关键部件。
难熔金属基复合材料具有出色的耐磨损性和耐高温性能,可以提高发动机和制动系统的性能和寿命。
CVD技术
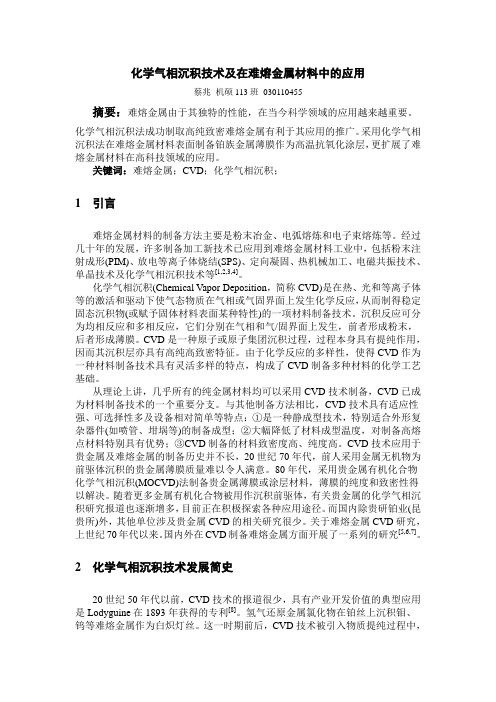
化学气相沉积技术及在难熔金属材料中的应用蔡兆机硕113班030110455摘要:难熔金属由于其独特的性能,在当今科学领域的应用越来越重要。
化学气相沉积法成功制取高纯致密难熔金属有利于其应用的推广。
采用化学气相沉积法在难熔金属材料表面制备铂族金属薄膜作为高温抗氧化涂层,更扩展了难熔金属材料在高科技领域的应用。
关键词:难熔金属;CVD;化学气相沉积;1引言难熔金属材料的制备方法主要是粉末冶金、电弧熔炼和电子束熔炼等。
经过几十年的发展,许多制备加工新技术已应用到难熔金属材料工业中,包括粉末注射成形(PIM)、放电等离子体烧结(SPS)、定向凝固、热机械加工、电磁共振技术、单晶技术及化学气相沉积技术等[1,2,3,4]。
化学气相沉积(Chemical V apor Deposition,简称CVD)是在热、光和等离子体等的激活和驱动下使气态物质在气相或气固界面上发生化学反应,从而制得稳定固态沉积物(或赋予固体材料表面某种特性)的一项材料制备技术。
沉积反应可分为均相反应和多相反应,它们分别在气相和气/固界面上发生,前者形成粉末,后者形成薄膜。
CVD是一种原子或原子集团沉积过程,过程本身具有提纯作用,因而其沉积层亦具有高纯高致密特征。
由于化学反应的多样性,使得CVD作为一种材料制备技术具有灵活多样的特点,构成了CVD制备多种材料的化学工艺基础。
从理论上讲,几乎所有的纯金属材料均可以采用CVD技术制备,CVD已成为材料制备技术的一个重要分支。
与其他制备方法相比,CVD技术具有适应性强、可选择性多及设备相对简单等特点:①是一种静成型技术,特别适合外形复杂器件(如喷管、坩埚等)的制备成型;②大幅降低了材料成型温度,对制备高熔点材料特别具有优势;③CVD制备的材料致密度高、纯度高。
CVD技术应用于贵金属及难熔金属的制备历史并不长,20世纪70年代,前人采用金属无机物为前驱体沉积的贵金属薄膜质量难以令人满意。
80年代,采用贵金属有机化合物化学气相沉积(MOCVD)法制备贵金属薄膜或涂层材料,薄膜的纯度和致密性得以解决。
粉末冶金制粉技术 全

粉末冶金制粉技术(一)粉末冶金新技术、新工艺的应用,不但使传统的粉末冶金材料性能得到根本的改善,而且使得一批高性能和具有特殊性能的新一代材料相继产生。
例如:高性能摩擦材料、固体自润滑材料、粉末高温合金、高性能粉末冶金铁基复合和组合零件、粉末高速钢、快速冷凝铝合金、氧化物弥散强化合金、颗粒增强复合材料,高性能难熔金属及合金、超细晶粒及涂层硬质合金、新型金属陶瓷、特种陶瓷、超硬材料、高性能永磁材料、电池材料、复合核燃料、中子可燃毒物、粉末微晶材料和纳米材料、快速冷凝非晶和准晶材料、隐身材料等。
这些新材料都需要以粉末冶金作为其主要的或惟一的制造手段。
本章将简要介绍粉末冶金的基本工艺原理和方法,重点介绍近年米粉末冶金新技术和新工艺的发展和应用状况。
1.雾化制粉技术粉末冶金材料和制品不断增多,其质量不断提高,要求提供的粉末的种类也愈来愈多。
例如,从材质范围来看,不仅使用金属粉末,也要使用合金粉末、金属化合物粉末等;从粉末形貌来看,要求使用各种形状的粉末,如生产过滤器时,就要求球形粉末;从粉末粒度来看,从粒度为500~1000m的粗粉末到粒度小于0.1m的超细粉末。
近几十年来,粉末制造技术得到了很大发展。
作为粉末制备新技术,第一个引人注目的就是快速凝固雾化制粉技术。
快速凝固雾化制粉技术是直接击碎液体金属或合金并快速冷凝而制得粉末的片法。
快速凝固雾化制粉技术最大的优点是可以有效地减少合金成分的偏析,获得成分均匀的合金粉末。
此外,通过控制冷凝速率可以获得具有非晶、准晶、微晶或过饱和固溶体等非平衡组织的粉末。
它的出现无论对粉末合金成分的设计还是对粉末合金的微观结构以及宏观特性都产生了深刻影响,它给高性能粉末冶金材料制备开辟了一条崭新道路,有力地推动了粉末冶金的发展。
雾化法最初生产的是像锡、铅、锌、铝等低熔点金属粉末,进一步发展能生产熔点在1600~1700℃以下的铁粉及其他粉末,如纯铜、黄铜、青铜、合金钢、不锈钢等金属和合金粉末。
粉末冶金新技术
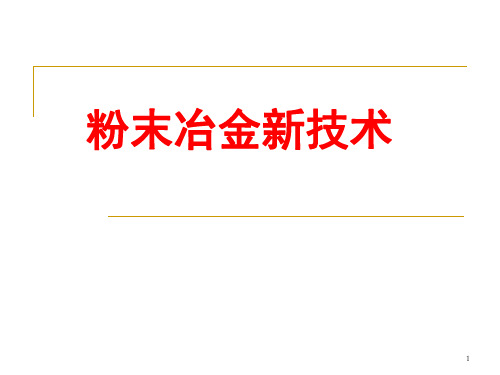
这些小的磁性金属原子簇,像顺磁体材 料一样,磁矩由原子簇的原子自旋构成,且 所有自旋均在同一方向上,因而磁矩比普通 材料高100多倍。包覆这些颗粒可形成稳定铁 胶体,颗粒永远处于悬浮态,现已作为“磁 流体”工业化生产,用于扬声器,磁性墨水, 磁流体密封,润滑剂,轴承,医学等。
制粉新技术 22
成型新技术 32
温压技术的特点 : • 能以较低成本制造出高性能粉末冶金零部件; • 提高零部件生坯密度和高强度,便于制造形状复杂
以及要求精密的零部件 ; • 产品密度均匀。
成型新技术 33
温压技术研究和开发的核心: • 预合金化粉末的制造技术; • 新型聚合物润滑剂的设计; • 石墨粉末有效添加技术; • 无偏析粉末的制造技术; • 温压系统制备技术。
23
二、成型新技术
1.动磁压制技术
原理:将粉末装于一个导 电的容器(护套)内,置于高强 磁场线圈的中心腔中。电容 器放电在数微秒内对线圈通 入高脉冲电流,线圈腔中形成 磁场,护套内产生感应电流。 感应电流与施加磁场相互作 用,产生由外向内压缩护套的 磁力,因而粉末得到二维压制。 整个粉体的压制过程不 足1ms。
该法生产速度为0.5-30g/min,比其他纳 米粉末制备方法生产率高。本方法所用反 应材料不污染环境,而以前生产银粉所用 的联氨是一种致癌物。用这种方法生产的 银粉可用于制造焊料、牙科填料、电路板、 高速摄影胶片等。
制粉新技术 15
5.电爆炸金属丝制取纳米粉 大功率电脉冲施于氩气保
护的金属丝上,并受到大功率脉 冲产生的特殊场约束。柱形等 离子体被加热到15000K以上高 温,因而电阻剧增,引起特殊场 崩溃。金属蒸气的高压引起爆 炸,产生冲击波,形成的金属气 溶胶快速绝热冷却,制得纳米粉。
粉末冶金技术

流、水流)对金属液
流作用的方式不同, 雾化具有多种形式:
平行喷射(气流与金
属液流平行)
垂直喷射(气流或水
流与金属液流互成垂 直方向)
水雾化时,控制好以下条件可以得细粉末:水 的压力高,水的流速、流量大,金属液流直径小, 过热温度高,金属的表面张力和粘度小,金属液流 长度短,喷射长度短,喷射顶角适当等。 控制好以下条件可以得球形粉末:金属表面张 力要大,过热温度高,水的流速低,喷射顶角大, 液流飞行路程长等。
粉末的羰基物热离解法
从气态金属卤化物气相还原制取金属、合金粉末
以及金属、合金涂层的气相氢还原法
从气态金属卤化物沉积制取金属化合物粉末以及
涂层的化学气相沉积法
从过程的实质来看,现有制粉方法大体上可归纳 为两大类,即机械法和物理化学法。
机械法是将原材料机械地粉碎,而化学成分基本
上不发生变化;
物理化学法是借助化学的或物理的作用,改变原
熔体淬火技术(Melt Quenching
Technology或MQT)。
静力学方法
针对通常铸造合金都是在非均匀形核条件下凝
固,因而针对合金凝固过冷度很小的问题,设法 尽管冷速不高但也同样可以达到很大的凝固过冷
提供近似均匀形核的条件。在这种条件下凝固时, 度,从而提高凝固速度。具体实现这种方法的技
炼法相比,性能优越:
高合金粉末冶金材料的性能比熔铸法生产的好,
例如,粉末高速钢、粉末超合金可避免成分的 偏析,保证合金具有均匀的组织和稳定的性能, 同时,这种合金具有细晶粒组织使热加工性大 为改善;
生产难熔金属材料或制品,一般要依靠粉末冶
金法,例如,钨、铝等难熔金属,即使用熔炼 法能制造,但比粉末冶金的制品的晶粒要粗, 纯度要低。
一种新型难熔金属异型件的制备技术及其应用

Va uu h tp e sng a d hih— r s u e o s sai e sn r e o i r v e i c to c m o r s i n g p e s r h tio t tc pr s ig wee us d t mp o e d nsf a in. Th rs ls s o i e e u t h w ta he r ltv e iy o r u se hr a l rfbrc td by p a m a s a o m ig i 5. h tt ea ie d nst fpu e t ng tn t o t i a ia e l s pr y fr n s 8 6% . t tb a uu ne ha y v c m h tp e sn s ic e s d t . o r s ig i n r a e o 91 7% . a d t a y hih— r s u e o s sai r s i s t n h tb g p e s r h tio ttc p e sng i o 96. 7% , whih n c ts c idiae ta i h p e s r o s sai r s ig c n rie d n i h th g — r s u e h tio ttc p e sn a as e st Hih e e g p a omi g tc n lg a lof b iae h a — y. g n r ys ry fr n e h oo y c n a s a rc t e t
压 可 大 大 提 高 喷 涂 成 形 件 的致 密 度 。 高 能 喷 涂 成 形 技 术 可 制 备 出形 状 复 杂 的 耐 高 温 材 质 构 件 , 钨 / 复 合 如 钼
喷 管 、 坩 埚 、钨 发 热体 、 甲 弹药 形 罩 等 异 形 构 件 和 二 硅 化 钼 回转 体 等 。 钨 破
科技成果——高性能特种粉体材料近终成形技术

科技成果——高性能特种粉体材料近终成形技术技术开发单位北京科技大学技术领域新材料成果简介该项目属于粉末冶金学科。
高性能特种材料具有其他材料不具备的特殊性能,在高技术领域中具有不可取代的关键作用。
然而,这类材料往往硬度高、脆性大,难以采用传统技术加工制备,成为许多国防和民用高技术装备发展的瓶颈。
为此,项目基于粉体流变成形原理,研发了难加工材料的近终形制造新技术,广泛应用于国防和民用高技术领域。
主要发明点如下:1、发明了高性能特种材料的粉末注射成形新工艺,实现了金属钨、氮化铝、含氮不锈钢等难加工材料制品的近终形制造;发明了专用注射成形机、侧抽芯新结构模具等关键工艺装备;创立了基于机器视觉的粉末注射成形产品尺寸和外观质量在线自动检测、工业机器人动态抓取和分拣软硬件系统,首次实现了全自动化生产和高质量稳定性控制,生产效率提高6倍以上。
2、首创了适合注射成形的近球形微细特种粉体制备和改性新技术。
提出基于酸根离子的化学推进剂理论,创立了可控溶液燃烧合成难熔金属和氮化物反应体系和工艺,制备出粒径小于50nm的高分散近球形氮化铝和钨基粉体。
创立了“气流分级分散-等离子球化”粉体改性技术,制备出满足精密多孔阴极需要的细粒径窄分布(5±2μm)球形钨粉。
3、发明了适合不同材料的粘结剂体系及成形和高效脱脂工艺。
提出基于聚合物功能基团的多组元粘结剂设计原理,创立了两相流协调运动模型,阐明了两相分离和缺陷产生的不确定性机制,发明了残碳型、低残留型和高粘性粘结剂体系,有效解决了坯体两相分离、变形、增氧、缺陷等控制难题,产品尺寸精度达到±0.2%。
4、发明了多孔脱脂坯强化烧结致密化和组织性能精确调控技术。
提出金属钨的低温无压活化烧结致密化理论和钝化处理孔隙结构精确调控技术,突破了高致密度钨的细晶化和多孔钨的孔隙均匀化技术瓶颈,烧结金属钨电极的晶粒尺寸仅570nm,抗电子轰击性能提高2个数量级,多孔钨的活性物质填充量提高20%;综合利用液相烧结和残碳“脱氧”原理,解决了氮化铝高致密化、晶界相控制和晶格净化等难题,热导率高达248W/m/K。
粉末冶金配方及工艺技术
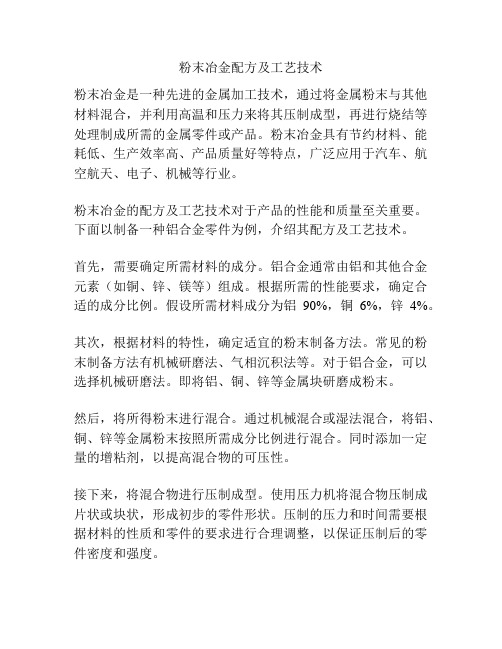
粉末冶金配方及工艺技术粉末冶金是一种先进的金属加工技术,通过将金属粉末与其他材料混合,并利用高温和压力来将其压制成型,再进行烧结等处理制成所需的金属零件或产品。
粉末冶金具有节约材料、能耗低、生产效率高、产品质量好等特点,广泛应用于汽车、航空航天、电子、机械等行业。
粉末冶金的配方及工艺技术对于产品的性能和质量至关重要。
下面以制备一种铝合金零件为例,介绍其配方及工艺技术。
首先,需要确定所需材料的成分。
铝合金通常由铝和其他合金元素(如铜、锌、镁等)组成。
根据所需的性能要求,确定合适的成分比例。
假设所需材料成分为铝90%,铜6%,锌4%。
其次,根据材料的特性,确定适宜的粉末制备方法。
常见的粉末制备方法有机械研磨法、气相沉积法等。
对于铝合金,可以选择机械研磨法。
即将铝、铜、锌等金属块研磨成粉末。
然后,将所得粉末进行混合。
通过机械混合或湿法混合,将铝、铜、锌等金属粉末按照所需成分比例进行混合。
同时添加一定量的增粘剂,以提高混合物的可压性。
接下来,将混合物进行压制成型。
使用压力机将混合物压制成片状或块状,形成初步的零件形状。
压制的压力和时间需要根据材料的性质和零件的要求进行合理调整,以保证压制后的零件密度和强度。
最后,对压制成型的零件进行烧结处理。
将零件置于特定的烧结炉中,在一定时间内进行高温加热处理。
在烧结过程中,金属粉末之间发生扩散,形成固相焊接,使零件的密度和强度得到提高。
在工艺过程中,还需要注意一些关键的技术要点。
首先,粉末的制备质量直接影响了最终零件的性能。
为了提高粉末的均匀性和细度,可以采用球磨法进行研磨,同时控制研磨时间和研磨介质的选择。
其次,压制过程中要注意控制压力和时间,避免压制过度或不足,以保证零件的密度和形状。
最后,在烧结过程中,温度、时间和气氛的控制都非常重要,以确保零件达到预期的物理和化学性能。
综上所述,粉末冶金配方及工艺技术对于产品的性能和质量具有重要的影响。
通过合理确定材料成分、选择适宜的粉末制备方法和控制关键工艺参数,可以生产出具有优异性能的粉末冶金产品。
粉末冶金新技术
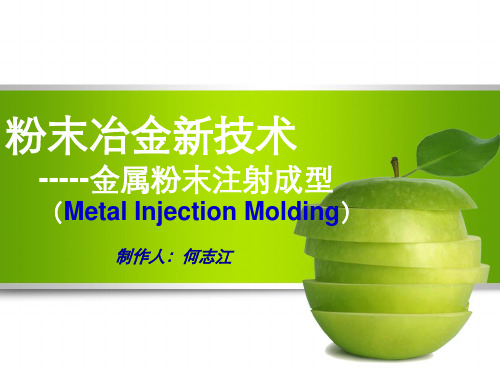
2、MIM工艺特点
2.1MIM工艺与其它加工工艺的对比
2.1.1 MIM与传统的粉末冶金(PM)的比较 MIM使用的原料粉末粒径在2-15µm,而传统粉 末冶金的原粉粉末粒径大多在50__100µm。 MIM工艺的成品密度高,原因是使用微细粉末。 MIM工艺具有传统粉末冶金工艺的优点,但是 形状上自由度高是传统粉末冶金所不能达到的, 传统粉末冶金限于模具的强度和填充密度,形 状大多为二维圆柱型。
注射成型与其他粉末冶金成型技术的比较
粉末冶金零件成型大致有两种:压制成型和注射 成型。 压制成型种类很多,在实际中有较广泛应用。冷 封闭钢模压制、冷等静压、热等静压、温压都属 于压制成型。压制成型,用干粉依靠重力填充于 模中,通过外界压力挤压成型。 注射成型,使用很细的粉末加大量的热塑性粘结 剂注射到成型模中。 喷射成型则是金属液滴在基体上雾化沉积的一种 工艺。 另外还有两种特殊粉末冶金零件加工方式:粉末 锻造和粉末轧制。
Page 3
1-1、MIM技术概述
该工艺技术不仅具有常规粉末冶金工艺 工序少、无切削或少切削、经济效益高等 优点,而且克服了传统粉末冶金工艺制品
密度低、材质不均匀、机械性能低、不易 成型薄壁、复杂结构的缺点,特别适合于
大批量生产小型、复杂以及具有特殊要求 的金属零件。
Page 4
1-2、MIM的发展史
由于MIM原料粉末要求很细,MIM原料粉 末价格一般较高,有的甚至达到传统PM粉 末价格的10倍,这是目前限制MIM技术广泛 应用的一个关键因素,目前生产MIM用原料 粉末的方法主要有羰基法、超高压水雾化法、 高压气体雾化法等。
Page 26
3 、MIM工艺过程
3.1羰基法 MIM最早使用的粉末是羰基法生产的,美国GAF 化学公司采用较粗的海绵铁粉作原料,制粒后在 350度氢气中退火活化,然后臵于反应器中,铁 粒暴露在循环的CO中,气体压力为6OPMa,温度 160度,铁与CO发生反应,得到气态的Fe(CO)5, 并加以冷凝收集,接下来,使Fe(CO)5蒸发通过 一个垂直的反应塔,反应塔加热到300度,在催 化剂NH3作用下,Fe(CO)5在塔顶部分解为Fe和 CO气体,将沉积的铁粉聚集体球磨,得到符合要 求的成品铁粉,粉中一般含0.8%C,0.7%N和 0.3%O(质量分数)。
金属冶炼中的新材料和新技术
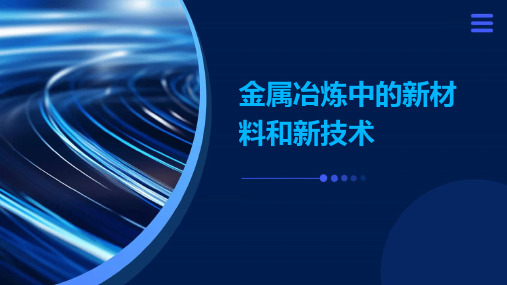
耐腐蚀材料
总结词
耐腐蚀材料在金属冶炼中具有重要地位,它们能够抵抗各种腐蚀环境,保证金 属产品的长期稳定性和可靠性。
详细描述
耐腐蚀材料如不锈钢、镍基合金和钛合金等,广泛应用于石油化工、海洋工程 和制药等领域。这些材料通过特殊的合金元素和表面处理工艺,具有良好的耐 腐蚀性能,能够延长设备使用寿命,减少维护成本。
复合材料
总结词
复合材料在金属冶炼中是一种新兴的材料形式,它们由两种或多种材料组成,通过复合效应提供优异的综合性能 。
详细描述
复合材料如碳纤维增强金属基复合材料、玻璃纤维增强塑料复合材料等,具有轻量化、高强度、高刚度和耐腐蚀 等优点。这些材料广泛应用于汽车、航空和体育用品等领域,对于推动产品创新和技术进步具有重要作用。
电渣重熔技术
原理
利用电流通过渣池产生热量对金 属进行重熔,去除杂质,提高金 属纯净度。
应用
适用于大型铸锭、特殊钢和高温 合金等材料的重熔处理。
连铸连轧技术
连续铸造
将熔融金属连续浇注到结晶器中,形 成一定形状的凝固坯壳,再经过轧制 形成连续的金属板材或型材。
技术优势
提高生产效率、节约能源、降低成本 、改善产品性能。
详细描述
高强度轻质材料如钛合金、铝合金等在金属结构件中得到广泛应用,通过采用先进的冶炼和加工技术 ,这些材料能够达到较高的强度和轻量化效果,从而降低能耗和提高结构效率。
耐腐蚀材料在石油化工领域的应用
总结词
耐腐蚀性强、使用寿命长、安全性高
详细描述
金属冶炼中的新材料如不锈钢、镍基合金等具有优异的耐腐蚀性能,适用于石油化工领 域的苛刻环境。这些材料的冶炼技术不断进步,提高了产品的稳定性和可靠性,减少了
2024年粉末冶金的烧结技术(三篇)

2024年粉末冶金的烧结技术⑴按原料组成不同分类。
可以将烧结分为单元系烧结、多元系固相烧结及多元系液相烧结。
单元系烧结是纯金属(如难熔金属和纯铁软磁材料)或化合物(Al2O3、B4C、BeO、MoSi2等)熔点以下的温度进行固相烧结。
多元系固相烧结是由两种或两种以上的组元构成的烧结体系,在其中低熔成分的熔点温度以下进行的固相烧结。
粉末烧结合金多属于这一类。
如Cu-Ni、Fe-Ni、Cu-Au、W-Mo、Ag-Au、Fe-Cu、W-Ni、Fe-C、Cu-C、Cu-W、Ag-W等。
多元系液相烧结以超过系统中低熔成分熔点的温度进行的烧结。
如W-Cu-Ni、W-Cu、WC-Co、TiC-Ni、Fe-Cu(Cu10%、Fe-Ni-Al、Cu-Pb、Cu-Sn、Fe-Cu(Cu10%)等⑵按进料方式不同分类。
分为为连续烧结和间歇烧结。
连续烧结烧结炉具有脱蜡、预烧、烧结、制冷各功能区段,烧结时烧结材料连续地或平稳、分段地完成各阶段的烧结。
连续烧结生产效率高,适用于大批量生产。
常用的进料方式有推杆式、辊道式和网带传送式等。
间歇烧结零件置于炉内静止不动,通过控温设备,对烧结炉进行需要的预热、加热及冷却循环操作,完成烧结材料的烧结过程。
间歇烧结可依据炉内烧结材料的性能确定合适的烧结制度,但生产效率低,适用于单件、小批量生产,常用的烧结炉有钟罩式炉、箱式炉等。
除上述分类方法外。
按烧结温度下是否有液相分为固相烧结和液相烧结;按烧结温度分为中温烧结和高温烧结(1100~1700℃),按烧结气氛的不同分为空气烧结,氢气保护烧结(如钼丝炉、不锈钢管和氢气炉等)和真空烧结。
另外还有超高压烧结、活化热压烧结等新的烧结技术。
2.影响粉末制品烧结质量的因素影响烧结体性能的因素很多,主要是粉末体的性状、成形条件和烧结的条件。
烧结条件的因素包括加热速度、烧结温度和时间、冷却速度、烧结气氛及烧结加压状况等。
⑴烧结温度和时间烧结温度的高低和时间的长短影响到烧结体的孔隙率、致密度、强度和硬度等。
难熔金属基复合制品的制备方法及性能研究

难熔金属基复合制品的制备方法及性能研究难熔金属基复合制品指的是以难熔金属为基体,并通过添加高熔点合金、陶瓷或纳米颗粒等强化相,以提高材料的力学性能、耐磨性、耐腐蚀性等特性的一类材料。
制备难熔金属基复合制品的方法有很多种,本文将主要介绍其中几种常用的方法,并对其制备的复合材料的性能进行研究。
首先,常用的制备难熔金属基复合制品的方法之一是粉末冶金法。
该方法通常包括粉末混合、压制和烧结等步骤。
粉末混合阶段涉及不同成分的金属和强化相粉末的混合,这一步骤的目的是实现均匀的分散,并促进金属与强化相之间的冶金反应。
压制过程是将混合后的粉末经过压力作用下成型为所需形状的材料。
最后,通过烧结工艺将压制成型的材料块进行加热,使金属粉末发生烧结反应,从而形成固体材料。
粉末冶金法制备的难熔金属基复合制品具有良好的成型性能和力学性能。
另一种常用的制备方法是熔融法。
该方法往往适用于需要制备大型复合制品或难以通过粉末冶金法实现的复杂结构的制备。
熔融法首先涉及将金属基体和强化相同时加热到高温,使其熔化并充分混合。
然后,通过快速冷却或凝固,将熔融体固化成所需形状的制品。
熔融法制备的难熔金属基复合制品具有较高的相容性和均匀的分布,因此通常具有良好的力学性能和耐磨性能。
此外,化学合成法也是一种制备难熔金属基复合制品的常用方法。
这种方法通过在溶液中反应金属盐和强化相之间的反应,从而将强化相沉积在金属基体上。
其中一种常用的化学合成方法是电沉积法。
该方法通过在电解槽中加入金属盐和强化相溶液,并通过施加电流使金属离子在基体上沉积,并与强化相发生反应。
化学合成法制备的难熔金属基复合制品可以控制复合材料的成分和微观结构,具有较好的加工性能和机械性能。
对于难熔金属基复合制品的性能研究,通常包括力学性能、耐磨性和耐腐蚀性等方面的评价。
力学性能包括材料的拉伸强度、屈服强度、硬度等。
耐磨性是指材料在摩擦和磨损条件下的性能表现,可以通过磨损实验来评价。
耐腐蚀性是指材料在腐蚀介质中的稳定性和抵抗腐蚀性的能力,可以通过浸泡试验和电化学测试等方法来评估。
粉末冶金简介
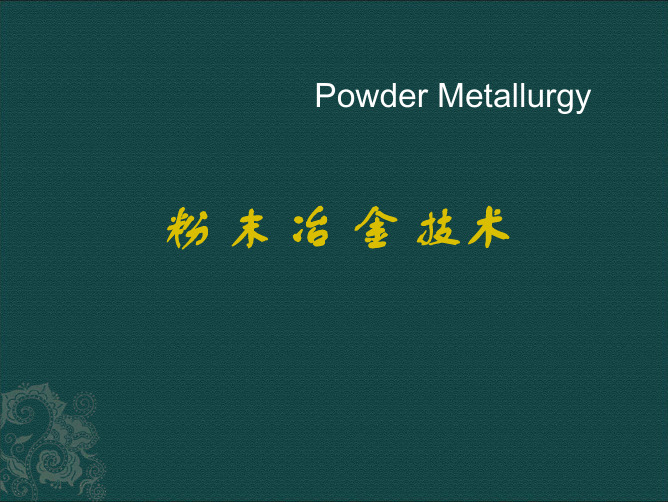
多孔材料(F2)
——铁及铁基合金(F20); ——不锈钢(F21); ——铜及铜基合金(F22); ——钛及钛合金(F23); ——镍及镍合金(F24); ——钨及钨合金(F25); ——难熔化合物多孔材料(F26)
工具材料类(F3)
——钢结硬质合金(F30); ——金属陶瓷和陶瓷(F36); ——工具钢(F37);
2.缺点
① 粉末成本高; ② 形状、尺寸受到一定限制; ③ 成形模具较贵;一般要生产量在5000~10000个/批,才经 济。 ④ 烧结零件韧性相对差(但可通过粉模锻造或复烧改善)。
1.和熔铸技术比较
粉末冶金优势: ① 粉末冶金制件表面光洁度高; ② 制造的尺寸公差很窄,尺寸精确; ③ 合金化与制取复合材料的可能性大 ④ 组织均一(无偏聚、砂眼、缩孔) 、力学性能可靠; ⑤ 在经济上,粉末冶金工艺能耗小。
历史部分: 武器, 生活用具, 艺术建筑
Weapon, life facilities, arts-construction, etc.
现代部分: 硬质合金, 高温材料, 汽车部件, 军事工程
目前, 粉末冶金最发达的国家瑞典(Sweden),硬质合金 工业非常发达,其次是北美(North American)和西欧 (western European) 。德国的粉末冶金工业也是处于世 界前列。瑞典山特维克 (Sandvik) 、美国肯纳金属 (Kennametal) 、以色列依斯卡 (Iscar)。。。
添加纳米陶瓷纤维的难熔金属基复合材料制备及性能研究
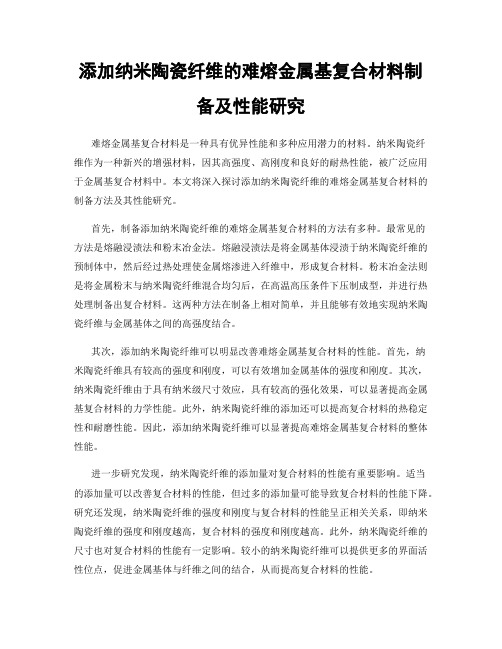
添加纳米陶瓷纤维的难熔金属基复合材料制备及性能研究难熔金属基复合材料是一种具有优异性能和多种应用潜力的材料。
纳米陶瓷纤维作为一种新兴的增强材料,因其高强度、高刚度和良好的耐热性能,被广泛应用于金属基复合材料中。
本文将深入探讨添加纳米陶瓷纤维的难熔金属基复合材料的制备方法及其性能研究。
首先,制备添加纳米陶瓷纤维的难熔金属基复合材料的方法有多种。
最常见的方法是熔融浸渍法和粉末冶金法。
熔融浸渍法是将金属基体浸渍于纳米陶瓷纤维的预制体中,然后经过热处理使金属熔渗进入纤维中,形成复合材料。
粉末冶金法则是将金属粉末与纳米陶瓷纤维混合均匀后,在高温高压条件下压制成型,并进行热处理制备出复合材料。
这两种方法在制备上相对简单,并且能够有效地实现纳米陶瓷纤维与金属基体之间的高强度结合。
其次,添加纳米陶瓷纤维可以明显改善难熔金属基复合材料的性能。
首先,纳米陶瓷纤维具有较高的强度和刚度,可以有效增加金属基体的强度和刚度。
其次,纳米陶瓷纤维由于具有纳米级尺寸效应,具有较高的强化效果,可以显著提高金属基复合材料的力学性能。
此外,纳米陶瓷纤维的添加还可以提高复合材料的热稳定性和耐磨性能。
因此,添加纳米陶瓷纤维可以显著提高难熔金属基复合材料的整体性能。
进一步研究发现,纳米陶瓷纤维的添加量对复合材料的性能有重要影响。
适当的添加量可以改善复合材料的性能,但过多的添加量可能导致复合材料的性能下降。
研究还发现,纳米陶瓷纤维的强度和刚度与复合材料的性能呈正相关关系,即纳米陶瓷纤维的强度和刚度越高,复合材料的强度和刚度越高。
此外,纳米陶瓷纤维的尺寸也对复合材料的性能有一定影响。
较小的纳米陶瓷纤维可以提供更多的界面活性位点,促进金属基体与纤维之间的结合,从而提高复合材料的性能。
除了力学性能的改善,添加纳米陶瓷纤维还可以提高复合材料的热稳定性和耐磨性能。
纳米陶瓷纤维具有较高的熔点和耐热性能,可以有效增加复合材料的热稳定性。
此外,纳米陶瓷纤维的添加还可以形成类似针状晶体的结构,提高复合材料的抗磨性能,延长材料的使用寿命。
- 1、下载文档前请自行甄别文档内容的完整性,平台不提供额外的编辑、内容补充、找答案等附加服务。
- 2、"仅部分预览"的文档,不可在线预览部分如存在完整性等问题,可反馈申请退款(可完整预览的文档不适用该条件!)。
- 3、如文档侵犯您的权益,请联系客服反馈,我们会尽快为您处理(人工客服工作时间:9:00-18:30)。
难熔金属的粉末冶金制备新技术何勇学号:153312086粉末冶金研究院摘要:本文简要介绍了几种难熔金属的制备新技术,包括三种现代粉末冶金烧结技术(微波烧结、放电等离子烧结、选择性激光烧结)与两种近静成型技术(3D打印、金属粉末注射成形)。
介绍其制备方法的基本原理、技术优势以及应用现状,并在最后简单阐述材料制备技术的发展趋势。
先进烧结技术具有烧结温度低、烧结速度快、晶粒组织细化、结构均匀可控等优点,同时节约能源,生产效率高,是未来难熔金属制品致密化过程的优良选择;近静成型技术摒弃了传统材料制品制备和加工分开进行的传统工艺,大大缩短了生产周期,已成为当今难熔金属材料研究的热点,在高新尖端领域拥有十分可观的前景。
关键词:难熔金属;制备工艺技术;粉末冶金Abstract: This paper briefly introduces several new techniques of preparation of refractory metal, including three modern sintering technologies such as microwave sintering and two kinds of near net shape techniques. The basic principles,advantages and research status of these methods are claimed in the main paragraph. At the last part, some development trend of refractory metal materials are listed briefly.Not only do they possess unique advantages on rapid heating rate, short sintering time, inhibiting grain growth and controlling microstructure, but also show enormous industrial application value and prospect in terms of short production cycle and high efficiency energy saving, so the new sintering techniques have become a present research focus in material field.Near net shape technology has a very considerable prospects in the high-tech frontier because it greatly shortens the production cycle.Key words: refractory metal; preparation technique; powder metallurgy1 前言难熔金属[1]一般是指熔点在2000℃以上的过渡金属元素,广义上包括钨(W)、钼(Mo)、钽(Ta)、铌(Nb)、钛(Ti)、钒(V)、铬(Cr)、锆(Zr)等十几种元素。
难熔金属元素均位于元素周期表的IIIB、IVB、VB族内,其中钨、钼、钽、铌和铼(Re)这五种元素应用最广。
难熔金属及其合金、金属间化合物以其高熔点、高硬度、高强度等一系列独特的物理与力学性能而广泛应用于国防军工、航空航天、电子信息、冶金化工、能源环保等领域, 历来受到世界各国的高度重视, 在国民经济中占有重要地位[2]。
例如钨钼及其合金由于耐高温性能好、密度大、抗高温冲击和疲劳, 广泛用于电力、冶金、兵器、核聚变、化工等行业中[3]。
难熔金属合金可以抵抗辐射、温度、腐蚀和拉伸应力的苛刻环境, 在高温时具有高蠕变强度, 且同碱流体材料具有很好的相容性, 因此可以作为高温结构材料使用。
随着现代工业技术的不断进步与发展,对于难熔金属材料性能的要求越来越严格,传统的熔炼铸造等制备加工方法已经无法满足现代制造业对难熔金属制品的性能要求,与之相比,粉末冶金技术能够制备出高纯、高强、高性能的特殊制品,是目前难熔金属制备发展的主流趋势。
2 难熔金属的烧结新技术粉末冶金烧结技术是制备难熔金属及其合金锭坯的主要方法,也是生产过程中的关键工序,对产品的最终性能起着决定性作用。
常规烧结方法有氢气烧结、真空烧结、热等静压烧结等,能够实现绝大多数情况下,难熔金属材料的制备要求。
随着粉末制备和烧结手段的发展,还能实现一些功能梯度材料、细晶粒材料和形状复杂的零件烧结制备[4]。
微波烧结、放电等离子烧结和选择性激光烧结都是这一方向的最新成果。
2.1 微波烧结技术微波烧结(Microwave Sintering, MS)是材料科学与微波技术结合的新产物,通过电磁场使材料整体加热至烧结温度来实现致密化。
由于微波烧结炉是采用微波发生器代替传统的热源,因此微波烧结的加热原理与常规烧结工艺有本质的区别。
常规烧结中热量是通过介质从材料表面向内部扩散,最终完成烧结过程;而微波烧结是将材料吸收的微波能转化为材料内部分子的动能和势能,使材料内部的每一个分子和原子都成为发热源[5]。
很显然,这种加热方式可以使材料整体受热更加,从而使材料的热应力减至最小,这对于改善材料的密度、强度和韧性都非常有利。
图1为微波烧结装置的工作原理图[6]。
在微波烧结过程中, 微波发生器产生的微波由波导管导入加热腔中, 对放置在腔体中的试样进行加热烧结, 部分微波能量会被反射回来,环行器的作用是将反射回的微波导向水负载从而保护磁控管。
微波烧结加热腔体是微波烧结设备的核心部分,腔体的合理设计、精密制作和正确调整是实现材料成功烧结的关键, 图2为微波烧结炉加热腔体的简图[7],微波加热腔体有多种形式,通常可分为行波加热器、多模炉式加热器、单模谐振腔式加热器3种。
多模炉式加热器由于结构简单, 适用于各种加热负载,目前在生产实际中应用最为广泛。
图1 微波烧结原理图图2 微波烧结炉加热腔简图难熔金属及其合金材料由于是微波反射型材料, 微波与这类材料的介电耦合作用很差, 一般情况下不能用来烧结金属材料。
20 世纪90 年代以来逐渐展开了微波烧结金属材料的研究。
美国宾夕法尼亚州立大学的Roy 教授等[8,9]首次用微波烧结法成功地制备出Fe、Cu、Ni、Co、W及Fe-Cu、Fe-Ni、Ni-Al-Cu 等金属粉末的粉末冶金样品。
经过十几年的发展,金属的微波烧结技术日渐成熟,最近D.Agrawal等[10]采用频率为2.45GHz的微波烧结炉分别烧结了WC-6Co和WC-10Co, 已经能够获得比热等静压烧结更均匀和更细小的组织。
与常规烧结技术相比,微波烧结具有许多独特的优势。
首先是烧结温度低且烧结速度快,这能够有效抑制烧结体晶粒组织的长大,在微波电磁能作用下,材料内部分子或离子的动能增加, 使烧结活化能降低,烧结温度最大降温幅度可达500℃左右,同时材料内外均匀加热, 烧结时间大大缩短了。
此外,微波烧结具有快速烧结的特征,烧结时间的缩短可使微波烧结的能耗大大降低,与常规烧结相比,节能70%~90%,不仅提高了能源的利用效率,而且降低了烧结能耗费用。
2.2 放电等离子烧结技术放电等离子体烧结(Spark Plasma Sintering, SPS)是将金属等粉末装入模具内,将直流脉冲电流和压制压力施加于烧结粉末,经放电活化、热塑变形和冷却完成制取高性能材料的一种新的粉末冶金烧结技术。
SPS烧结过程的基本原理是利用直流脉冲电流直接通电对材料进行烧结,它不但具有类似热压烧结的焦耳热和加压造成塑性变形促进烧结过程, 而且其独特之处在于SPS烧结过程中粉末颗粒间会产生直流脉冲电压, 使粉体颗粒间放电产生自发热[11]。
SPS的装置基本结构示意图如图3所示[12],主要包括三个部分:一是产生轴向压力的轴向加压装置;二是用以产生等离子体的脉冲电流发生器,以对材料进行活化处理;最后是电阻加热装置。
SPS烧结过程中有2个非常重要的步骤,首先特殊电源产生的直流脉冲电压将电能贮存在颗粒团的介电层中,电能的间歇式快速释放在粉体的空隙产生放电等离子体,撞击颗粒间的接触部分,使物质产生蒸发作用而净化金属颗粒表面,提高烧结活性,有助于加速原子的扩散。
此外放电也会瞬时产生高达几千摄氏度至几万摄氏度的局部高温,在颗粒表面引起蒸发和熔化,在颗粒接触点形成颈部,气相物质凝聚在颈部而达成物质的蒸发-凝固传递[11]。
国内外在利用SPS技术制备难熔材料方面做过不少研究和努力。
例如Y.Bilge等[13]研究WC-Co-cBN的放电等离子体烧结,整个过程是在1300℃和75MPa的条件下烧结7.5min完成,烧结后经测试发现,WC-Co-cBN的密度达到了近全致密程度;余洋等[14]对比研究了放电等离子体烧结(SPS)和真空烧结(VAS)平均粒径为160nm 的WC-12Co硬质合金粉末的组织和性能,结果表明,放电等离子体烧结能使WC-12Co 在较低温度、较短时间内完全致密化,烧结温度比真空烧结低250 ℃以上, 而烧结时间却只有真空烧结的1/26,具体的数据结果如表1。
表1 放电等离子体烧结和真空烧结块体硬质合金的力学性能烧结方式晶粒尺寸/nm 致密度/% HRA TRS/MPa SPS1150230 99.3 91.1 1704 SPS1200330 99.5 90.6 1604 VAS530 99.8 89.2 1424图3 放电等离子体烧结系统示意图2.3 选择性激光烧结技术选择性激光烧结技术(Selective Laser Sintering, SLS)又称为选区烧结技术,是利用激光有选择地由下而上逐层烧结固体粉末,叠加生成CAD预先设计三维图型的一种快速成形制造方法,是集新材料、激光技术、计算机技术于一体的快速原型制造技术的一个重要分支,它既是目前广泛发展的3D打印技术的前身,这种技术在下文中还会详细介绍。
选择性激光烧结的原理示意图如图4所示[15]。
SLS系统通常包含3个主要部分:激光源的主要作用是产生激光束;粉末摊铺系统的作用是在每层扫描结束后,迅速铺下一层粉末,铺粉厚度对烧结时间和制品精度将产生直接影响,是十分关键的步骤;气氛控制系统可以根据不同的烧结材料提供不同的烧结气氛,以防止烧结过程中粉末出现氧化、鼓泡和气孔等缺陷。
SLS烧结最初是由美国德克萨斯大学奥斯汀分校的Carl Deckard于1987年提出, 后由美国DTM公司于1992年推出该工艺的商业化生产设备Sinter Station 2000[16]。