大型电机转子离心铸铝工艺介绍
铸铝转子质量的工艺分析及措施

铸铝转子质量的工艺分析及措施转子质量问题专题调查分析如下:铸铝转子质量问题,最突出的表现就是转子内部存在的气孔的问题,其次就是转子内部的笼条细条、断条、夹渣以及端环部分的缩孔、冷裂、热裂、缺肉等。
这些问题的产生,最终导致整机的电气性能下降、转速不够、效率降低。
1、转子片间存油未去除:这是转子产生气孔的一个主要原因,由于转子铸铝是在高温、高压、瞬间形成的一个过程,在铝液刚刚充满转子型腔,高温铝还是液态而与转子片间的油类发生反应时,生成气体,这种气体有些被逸出,有些被铝液包围,然而铝液迅速固化,被包围的气体跑不出去,因此这些气体以气泡的形式残留在转子的笼条和端环中,呈不规则分布状态。
解决的办法为:铸铝前的转子铁芯应进行脱油处理,具体做法为:转子铁芯可用工业清洗剂冷态脱油,自来水冲洗,电炉烘干。
烘干温度以不破坏冲片表面保护膜为准,烘干时间以目测干透为准。
我们在5月19日已经做过96个转子脱油的实验,用拉上同型号转子和实验品转子各10个,装入同型号定子各10台,由抽查室做负载对比检查,结果装有实验品转子的电机比拉上同型号电机的转速平均提高2.5%以上。
2、铝液的清化问题:这个问题也是铸铝转子产生气孔的一个主要问题,铝锭及回炉铝在加热熔解过程中,与空气中的水蒸气接触时(尤其是多雨季节),一方面生成氧化铝沉于铝液底部,另一方面分解出氢气,同时氢气也渗入铝水中。
含有气体的铝水压铸出来的转子质量很差,因为铝水在压铸成型的瞬间,铝水迅速固化,一部分气体还未来得及逸出而被固化的铝包围,从而留在铸件内造成气孔。
另外就是铝液表面上的浮渣、铝液底部的沉渣以及留在铝液中间的其它杂物对转子的质量来说也是一个很大的隐患,一旦将这些渣滓和杂物压入转子内部,它们会使转子造成夹渣、形成冷隔(电阻系数增加)、热裂和冷裂的现象,热裂和冷裂严重时造成转子笼条断路。
为了解决上述问题,加入清化剂(氯盐:一般为NaCl 、ZnCl)可以较好的解决这一问题。
离心铸造工艺
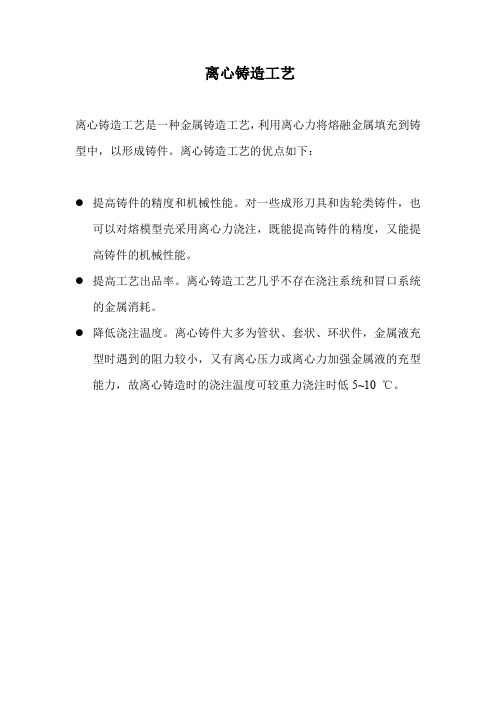
离心铸造工艺
离心铸造工艺是一种金属铸造工艺,利用离心力将熔融金属填充到铸型中,以形成铸件。
离心铸造工艺的优点如下:
●提高铸件的精度和机械性能。
对一些成形刀具和齿轮类铸件,也
可以对熔模型壳采用离心力浇注,既能提高铸件的精度,又能提高铸件的机械性能。
●提高工艺出品率。
离心铸造工艺几乎不存在浇注系统和冒口系统
的金属消耗。
●降低浇注温度。
离心铸件大多为管状、套状、环状件,金属液充
型时遇到的阻力较小,又有离心压力或离心力加强金属液的充型能力,故离心铸造时的浇注温度可较重力浇注时低5~10 ℃。
电动机转子铸铝工艺原理
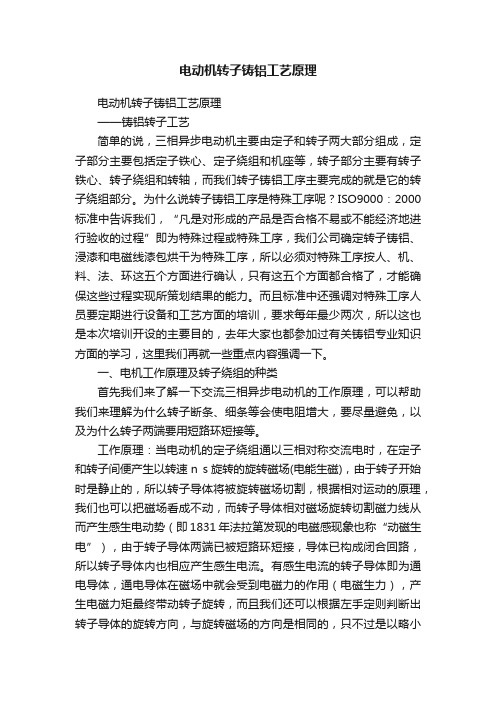
电动机转子铸铝工艺原理电动机转子铸铝工艺原理——铸铝转子工艺简单的说,三相异步电动机主要由定子和转子两大部分组成,定子部分主要包括定子铁心、定子绕组和机座等,转子部分主要有转子铁心、转子绕组和转轴,而我们转子铸铝工序主要完成的就是它的转子绕组部分。
为什么说转子铸铝工序是特殊工序呢?ISO9000:2000标准中告诉我们,“凡是对形成的产品是否合格不易或不能经济地进行验收的过程”即为特殊过程或特殊工序,我们公司确定转子铸铝、浸漆和电磁线漆包烘干为特殊工序,所以必须对特殊工序按人、机、料、法、环这五个方面进行确认,只有这五个方面都合格了,才能确保这些过程实现所策划结果的能力。
而且标准中还强调对特殊工序人员要定期进行设备和工艺方面的培训,要求每年最少两次,所以这也是本次培训开设的主要目的,去年大家也都参加过有关铸铝专业知识方面的学习,这里我们再就一些重点内容强调一下。
一、电机工作原理及转子绕组的种类首先我们来了解一下交流三相异步电动机的工作原理,可以帮助我们来理解为什么转子断条、细条等会使电阻增大,要尽量避免,以及为什么转子两端要用短路环短接等。
工作原理:当电动机的定子绕组通以三相对称交流电时,在定子和转子间便产生以转速n s旋转的旋转磁场(电能生磁),由于转子开始时是静止的,所以转子导体将被旋转磁场切割,根据相对运动的原理,我们也可以把磁场看成不动,而转子导体相对磁场旋转切割磁力线从而产生感生电动势(即1831年法拉第发现的电磁感现象也称“动磁生电”),由于转子导体两端已被短路环短接,导体已构成闭合回路,所以转子导体内也相应产生感生电流。
有感生电流的转子导体即为通电导体,通电导体在磁场中就会受到电磁力的作用(电磁生力),产生电磁力矩最终带动转子旋转,而且我们还可以根据左手定则判断出转子导体的旋转方向,与旋转磁场的方向是相同的,只不过是以略小于旋转磁场转速n s的速度运转的,这也是异步电动机名称的由来。
电动机转子铸铝工艺原理

电动机转子铸铝工艺原理——铸铝转子工艺简单的说,三相异步电动机主要由定子和转子两大部分组成,定子部分主要包括定子铁心、定子绕组和机座等,转子部分主要有转子铁心、转子绕组和转轴,而我们转子铸铝工序主要完成的就是它的转子绕组部分。
为什么说转子铸铝工序是特殊工序呢?ISO9000:2000标准中告诉我们,“凡是对形成的产品是否合格不易或不能经济地进行验收的过程”即为特殊过程或特殊工序,我们公司确定转子铸铝、浸漆和电磁线漆包烘干为特殊工序,所以必须对特殊工序按人、机、料、法、环这五个方面进行确认,只有这五个方面都合格了,才能确保这些过程实现所策划结果的能力。
而且标准中还强调对特殊工序人员要定期进行设备和工艺方面的培训,要求每年最少两次,所以这也是本次培训开设的主要目的,去年大家也都参加过有关铸铝专业知识方面的学习,这里我们再就一些重点内容强调一下。
一、电机工作原理及转子绕组的种类首先我们来了解一下交流三相异步电动机的工作原理,可以帮助我们来理解为什么转子断条、细条等会使电阻增大,要尽量避免,以及为什么转子两端要用短路环短接等。
工作原理:当电动机的定子绕组通以三相对称交流电时,在定子和转子间便产生以转速n s旋转的旋转磁场(电能生磁),由于转子开始时是静止的,所以转子导体将被旋转磁场切割,根据相对运动的原理,我们也可以把磁场看成不动,而转子导体相对磁场旋转切割磁力线从而产生感生电动势(即1831年法拉第发现的电磁感现象也称“动磁生电”),由于转子导体两端已被短路环短接,导体已构成闭合回路,所以转子导体内也相应产生感生电流。
有感生电流的转子导体即为通电导体,通电导体在磁场中就会受到电磁力的作用(电磁生力),产生电磁力矩最终带动转子旋转,而且我们还可以根据左手定则判断出转子导体的旋转方向,与旋转磁场的方向是相同的,只不过是以略小于旋转磁场转速n s的速度运转的,这也是异步电动机名称的由来。
所以说转子绕组的主要作用就是产生感生电动势和电流,并在旋转磁场的作用下产生电磁力矩而使转子转动,所以要求转子绕组的导电性能比较好(铝的电阻率为2.9×10-8m2/m,铜的电阻率为1.78×10-8Ωm2/m)。
谈转子离心铸铝的工艺方法

2 0 1 4
速 农机
AN N O N GJ FUJI I
谈转子 离心铸铝 的工艺方法
陈玉 宇
( 福建 南 电股份 有 限公 司 , 福建 南平 3 5 3 0 0 1 )
摘
要: 为 了保证电动机转子铸铝 的质量 , 对转子铸铝熔铝设备、 离心铸铝的工艺参数、 离心铸铝模 的结构
参数、 离心浇注的工艺方法及 离心力大小、 操作程序的具体实施步骤进行剖析介绍, 总结 了一套可用于指导生 产实际的离心铸铝转子生产工艺。
关键词: 转子; 铸铝 ; 坩锅; 涂料 ; 离心力; 温度 ; 速度
由于铸 铝转 子具有结构对称 、 紧凑 , 外形美观 , 易 于达到机械平衡 ; 槽形设计不受 铜条或铝条形 状
铝 过程 中最 容易产 生 的气体 , 在铝 中的溶解 度 随着温 度升高而增加 ( 见图2 ) 。 当铝 温 到 达 8 0 0  ̄ C 时, 由于
3 转子铁芯和铸铝模 的预热炉
预 热炉 必 须保 证 转 子铁 芯 预 热 温度 5 0 0 ℃左右 、
铸铝模预热温度 3 5 0  ̄ C 左右 , 而且温度均匀。 目前大
升随之提高 。所以铸铁坩埚使用前的处理就显得更 为 重要 。新 坩埚 必须 除净 铁锈 , 然后 加 热到 1 5 0 ~
的限制 , 可 以任 意选择能改善 电机性能 的理想槽形 ; 转子风叶、 笼条端环 以及平衡柱可同时铸出 , 槽满率 几乎达 1 0 0 %, 提高了散热效率 ; 生产周期短 、 成本低 、
都 采用反 射 炉或 电阻炉 等 。
4 离心铸铝模
离心铸铝模 由上 、 中、 下模 , 分流器 , 假轴等几部 分组成 。各种铸铝方法所用模具虽有不 同, 但其结构
铸铝转子工艺

铸铝转子工艺(铸铝工序)一、转子铸铝方法我公司所采用的转子铸铝方法主要有离心铸铝和压力铸铝两种。
下面分别来看一下这两种铸铝方法的工作原理和特点。
(一)压力铸铝工作原理是用压力将融化好的金属铝液注入型腔,待冷却凝固成铸件。
其特点有:(1)在压铸过程的始终,压力起着主要作用。
(2)压铸时,金属液在高速冲型过程中,如果型腔中的气体来不及排出,就会被卷入金属内产生气孔。
(3)由于金属液充型过程是在压力作用下进行的,转子铁心可在冷态下压铸。
(4)生产效率高,易实现机械化、自动化,从而可减轻劳动强度。
(二)离心铸铝工作原理是将融化好的金属铝液注入旋转着的铝模中,使之在离心力的作用下充满型腔,并凝固。
其特点有:(1)离心力对铸件的成型和金属结晶过程有重要影响,它有助于金属液中的气体和非金属杂物(比金属轻)的排出。
更重要的是影响到金属结晶过程,起到加强补缩和结晶细化的作用。
(2)转子铁心必须预热。
铁心加热后,在槽型断面上得到氧化,有利于降低电机的杂散损耗。
(3)转子离心铸铝用的设备比较简单。
但在浇铸过程中有不少手工操作,劳动强度较大。
二、离心铸铝和压力铸铝的优缺点及其常见的缺陷和防止措施1.离心铸铝优缺点离心铸铝所得到的铸件,金属组织比较紧密,质量比较好,所用设备不太复杂,操作技术比较简单,与压力铸铝相比较杂散损耗比较小,不过其生产率不高,劳动条件较差,劳动强度较高。
2.压力铸铝优缺点压力铸铝时,铝水压射到转子槽和型腔中的速度极高,其充填速度可达10~25m/s。
压铸时,不象离心铸铝那样铝水有一段流动时间,而是瞬间完成的,因此铁心和模具均可不必预热。
铁心和模具不预热,这就大大减化了操作工艺,改善了劳动条件。
此外由于没有离心铸铝那样复杂的凝固补缩过程,铸铝转子质量稳定,一次合格率达99%以上。
3.压力铸铝的质量,目前存在以下一些问题:(1)由于压力很大,铝水充满型腔的速度很高,原来在型腔中得空气难以排尽,会在铸件中产生气孔。
铸造技术离心铸造工艺要点讲解
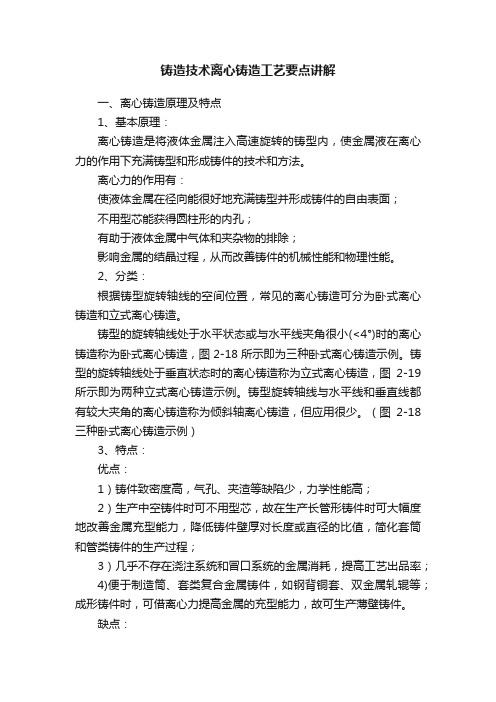
铸造技术离心铸造工艺要点讲解一、离心铸造原理及特点1、基本原理:离心铸造是将液体金属注入高速旋转的铸型内,使金属液在离心力的作用下充满铸型和形成铸件的技术和方法。
离心力的作用有:使液体金属在径向能很好地充满铸型并形成铸件的自由表面;不用型芯能获得圆柱形的内孔;有助于液体金属中气体和夹杂物的排除;影响金属的结晶过程,从而改善铸件的机械性能和物理性能。
2、分类:根据铸型旋转轴线的空间位置,常见的离心铸造可分为卧式离心铸造和立式离心铸造。
铸型的旋转轴线处于水平状态或与水平线夹角很小(<4°)时的离心铸造称为卧式离心铸造,图2-18所示即为三种卧式离心铸造示例。
铸型的旋转轴线处于垂直状态时的离心铸造称为立式离心铸造,图2-19所示即为两种立式离心铸造示例。
铸型旋转轴线与水平线和垂直线都有较大夹角的离心铸造称为倾斜轴离心铸造,但应用很少。
(图2-18 三种卧式离心铸造示例)3、特点:优点:1)铸件致密度高,气孔、夹渣等缺陷少,力学性能高;2)生产中空铸件时可不用型芯,故在生产长管形铸件时可大幅度地改善金属充型能力,降低铸件壁厚对长度或直径的比值,简化套筒和管类铸件的生产过程;3)几乎不存在浇注系统和冒口系统的金属消耗,提高工艺出品率;4)便于制造筒、套类复合金属铸件,如钢背铜套、双金属轧辊等;成形铸件时,可借离心力提高金属的充型能力,故可生产薄壁铸件。
缺点:1)铸件易产生比重偏析,因此不适合于合金易产生比重偏析的铸件(如铅青铜),尤其不适合于铸造杂质比重大于金属液的合金,但近年来,也有利用离心铸造的这个特点来生产梯度复合材料的情况;2)铸件内孔直径不准确,内孔表面比较粗糙,质量较差,加工余量大;3)用于生产异形铸件时有一定的局限性。
4、应用:用离心铸造法生产产量很大的铸件有:① 铁管:世界上每年球墨铸铁件总产量的近1/2是用离心铸造法生产的铁管② 柴油发动机和汽油发动机的汽缸套③ 各种类型的钢套和钢管④ 双金属钢背铜套,各种合金的轴瓦⑤ 造纸机滚筒。
转子离心铸铝

转子离心铸铝王江波离心铸铝工艺简介(一)开启熔解炉电源,打开燃气阀门,按下点火开关点燃熔解炉,炉温升到400℃以后将铝料投入熔解炉内(熔解炉第一次使用时,先用小伙缓慢升温两小时后在用大火升温。
铝料要事先预热保温,完全去除铝料中的水气),当铝温达到750-780℃将表面渣子消除干净,浇铸时温度控制在760-780℃。
(二)按照车间下发的任务单准备好转子冲片,假轴,针座,模具。
按生产单子换好卸转子的卸座和标识。
(三)开启预热炉电源,升温,开启传送带,调整温度和传送速度。
(四)根据需要选择相应模具,安装在铸铝机旋转组件的上旋转磁盘和移动磁盘上,打开离心铸铝机的控制系统有专人设置参数。
(五)将料勺和探针涂上料勺被覆剂,涂擦要均匀。
(六)手动时检查离心铸铝机的旋转磁盘上下移动和旋转是否正常,每次是否回到原点;机械手控制系统与离心铸铝机是否联机,手动检查机械手运转是否正常,一切正常后进入自动操作状态。
(七)开启冷却传送机电源,运转传送链。
(八)人工将假轴用液压机插入铁芯放到预热机的送带上,假轴有拉伤的必须挑出,经过预热炉预热后,到达预热炉出口,由人工放到离心铸铝机上,放置时位置要正。
(九)按下启动开关,离心铸铝机升降系统移动磁盘上升,将铁芯移动到上磁盘夹具内,然后高速旋转,机器人从溶解炉里舀出铝液,从装夹好转子铁芯的旋转浇铸口浇筑进去。
铝液在离心力作用下充满型腔,制冷空气循环冷却铸件,离心机停止旋转,移动托盘下移至原位,完成工作后工件由人工取下,放到冷却传送机上,安启动开关退顶料。
两个工位循环往复。
(十)工件冷却后由人工取下,退出假轴。
(十一)检查工件一.熔铝准备1.坩埚准备1.1对坩埚进行焙烧,充分去除坩埚表面的水分,控制温度缓慢上升,约4-5小时候达到400℃,开始装料熔炼。
1.2熔炼工具准备,凡是与铝液接触的捞渣勺,搅拌棒,铝勺都要进行预热刷涂料,以防被铝液腐蚀、增加铝液中的含铁量。
1.3铝料要进行充分预热,去除铝料中的水分。
大型电机转子离心铸铝工艺介绍

大型电机转子离心铸铝工艺介绍投稿邮箱:*******************摘要结合生产实际,论述了大型电机采用离心铸铝转子制造过程中离心机的改造、离心铸铝各工艺参数的确定、模具结构的设计等。
通过此番对大型电机离心铸铝工艺的研究,为大直径铸铝转子制造奠实了基础。
提高生产效率,降低电机制造成本,是公司在激烈的竟争中立于不败之地的关键。
众所周知,铜条转子制造成本高,周期长,难度大;而铸铝转子成本低,生产周期短。
采用铸铝转子取代铜条转子,即节约大量铜排,又降低了电机的制造成本,同时提高了生产效率,缩短供货周期,提高市场占有率,保证电机运行稳定性。
近来,我公司为了满足市场需求,在满足性能要求的前提下,采用铸铝转子替代铜条转子。
为保证大型电机制造质量,必须尽快完善大型电机转子离心铸铝制造工艺。
结合1000kW-4P电机铜条转子改为铸铝转子,研讨了转子离心铸铝工艺。
1 结构转子外径φ1030mm、端环外径φ1022mm、端环内径φ830mm、端环厚120mm、轴孔φ590 mm,铁心长1100mm,转子总重3.6T,其中铝水净重426kg。
转子装夹高度尺寸为1700mm。
2 工艺确定此大型铸铝转子,国内外都属首次生产,既无成熟经验可借鉴,又无资料可查。
经反复研究和分析,精心拟定了一整套离心浇铸工艺实施方案。
其中包括设备改制、工艺参数确定和工装结构确定等。
2.1 设备改制离心机是产生离心力的来源,离心力的大小和离心机的转速是否合理是决定铸铝转子质量的重要因素。
原有离心机最大承载重量3T,而该电机转子铁心与铸铝轴的重量就已接近5T。
底盘外径及装夹高度和离心机承重等各项远远满足不了生产条件。
经过反复研究论证,除满足该台转子直径外,同时兼顾我公司现有产品,确定离心机承重8T,底大盘直径为φ1200mm,另作一个辅助工作台,最大外径可扩大到φ1500 mm。
这样可兼顾小直径铸铝转子和大直径铸铝转子的要求。
扩大了设备的使用范围,提高了利用率。
离心铸铝的工艺流程
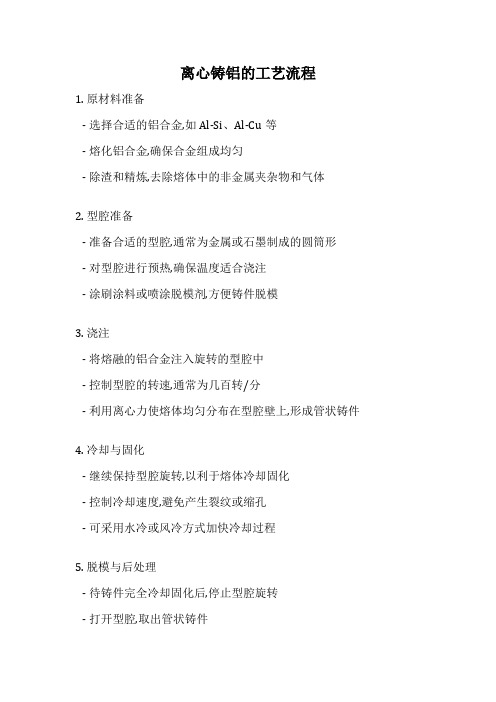
离心铸铝的工艺流程
1. 原材料准备
- 选择合适的铝合金,如Al-Si、Al-Cu等
- 熔化铝合金,确保合金组成均匀
- 除渣和精炼,去除熔体中的非金属夹杂物和气体
2. 型腔准备
- 准备合适的型腔,通常为金属或石墨制成的圆筒形
- 对型腔进行预热,确保温度适合浇注
- 涂刷涂料或喷涂脱模剂,方便铸件脱模
3. 浇注
- 将熔融的铝合金注入旋转的型腔中
- 控制型腔的转速,通常为几百转/分
- 利用离心力使熔体均匀分布在型腔壁上,形成管状铸件
4. 冷却与固化
- 继续保持型腔旋转,以利于熔体冷却固化
- 控制冷却速度,避免产生裂纹或缩孔
- 可采用水冷或风冷方式加快冷却过程
5. 脱模与后处理
- 待铸件完全冷却固化后,停止型腔旋转
- 打开型腔,取出管状铸件
- 对铸件进行切割、机加工等后续加工
- 进行热处理或其他工艺,改善铸件性能
6. 质量检测
- 检查铸件的尺寸、形状、表面质量等
- 进行无损检测,如射线检测、超声波检测等
- 确保铸件满足设计和使用要求
离心铸铝工艺可以生产管状、筒状或环状铸件,具有密实组织、良好的力学性能。
该工艺还可用于生产异型或特殊形状的铸件,在航空航天、汽车、机械等领域有广泛应用。
免翻转电机转子离心铸铝工艺芯轴
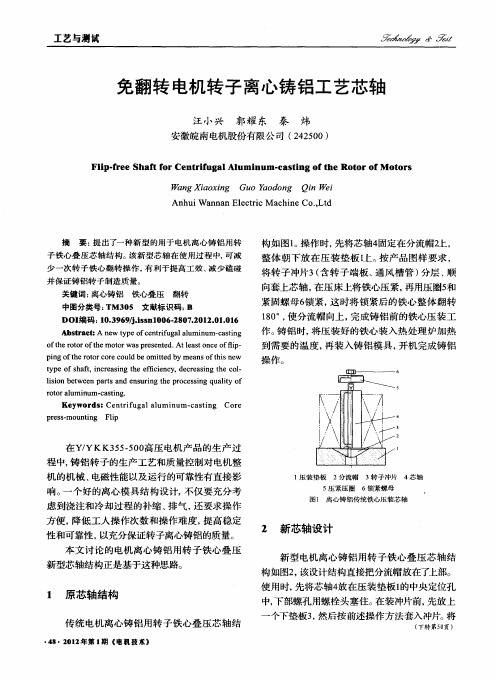
翻转
中图分类号 : TM3 5 文献标 识码 : 0 B
DOI 码 : 0 3 6  ̄. s l 0 -8 72 1 .10 6 编 1 .9 9 1 n 0 6 2 0 .0 20 . 1 s
Abs r c : n w p fc n rf g l l mi u c si g t a t A e t eo e t i a u n m— a tn y u a
作 。 铝 时, 压 装 好 的铁 心 装 入 热 处 理 炉 加 热 铸 将
子 铁心 叠压 芯 轴结 构 。 新型 芯 轴在 使 用过 程 中, 该 可减 少 一次转 子 铁 心翻 转操 作 , 利于提 高工 效 、 少磕碰 有 减
并保证 铸铝 转 子制造质 量。
关键 词: 心铸铝 离
铁心叠 压
・
个下垫板3 然后按 前述操作方 法套入冲片。 , 将
( 下转 第5 页 ) 0
4 ・ 0 2 第 1 《 机技 术》 8 21年 期 电
工艺与测试
的尾接入接线排2 C ; 相的头, 相 的尾接入接线 A 排 3 接线排4 ; 空着不用。 当电动机为Y 接法 , 这时 应将A、 和c B 三相 的头分别接入接线排 1 2 3 、 、, A、 和c B 三相 的尾接 入接线排4 如此 这样 变换 。 接线方式后, 满足了低压电动机两种电压 的使用
构如图1 操作时, 。 先将芯轴4 固定在分流帽2 上, 整体 朝下放在 压装 垫板 I 按产 品图样 要求 , 上。 将转 子冲片3 含转 子端板、 ( 通风 槽管 ) 分层 、 顺 向套上芯轴 , 在压床上将铁心压紧, 再用压 圈5 和 紧固螺母6 锁紧, 这时将锁 紧后的铁心整 体翻转 10 , 8 。 使分流帽向上, 完成铸铝前的铁心压 装工
大型离心铸造机工艺要求与设计
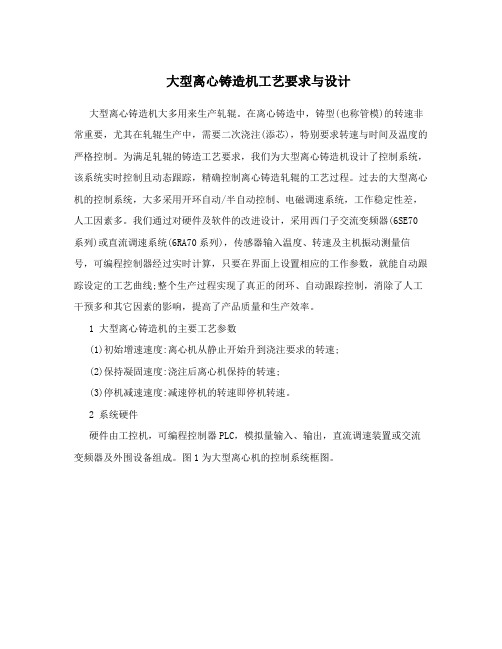
大型离心铸造机工艺要求与设计大型离心铸造机大多用来生产轧辊。
在离心铸造中,铸型(也称管模)的转速非常重要,尤其在轧辊生产中,需要二次浇注(添芯),特别要求转速与时间及温度的严格控制。
为满足轧辊的铸造工艺要求,我们为大型离心铸造机设计了控制系统,该系统实时控制且动态跟踪,精确控制离心铸造轧辊的工艺过程。
过去的大型离心机的控制系统,大多采用开环自动/半自动控制、电磁调速系统,工作稳定性差,人工因素多。
我们通过对硬件及软件的改进设计,采用西门子交流变频器(6SE70系列)或直流调速系统(6RA70系列),传感器输入温度、转速及主机振动测量信号,可编程控制器经过实时计算,只要在界面上设置相应的工作参数,就能自动跟踪设定的工艺曲线;整个生产过程实现了真正的闭环、自动跟踪控制,消除了人工干预多和其它因素的影响,提高了产品质量和生产效率。
1 大型离心铸造机的主要工艺参数(1)初始增速速度:离心机从静止开始升到浇注要求的转速;(2)保持凝固速度:浇注后离心机保持的转速;(3)停机减速速度:减速停机的转速即停机转速。
2 系统硬件硬件由工控机,可编程控制器PLC,模拟量输入、输出,直流调速装置或交流变频器及外围设备组成。
图1为大型离心机的控制系统框图。
工控机主要通过PLC完成离心铸造机远程实时监控和管理报表的制作,对现场的离心机转速、型腔金属液温度、轴承温度、离心铸造机振动的工作状态进行实时监控。
离心铸造过程中,计算机可以连续自动记录铸型中金属液的温度曲线。
工作原理:由界面设置离心铸造机主要工艺参数或调出原有产品的工艺参数,符合当前的产品时,则显示当前产品的控制曲线,按实际需要确认,通过控制按钮分别发出开始浇注、一次浇注、二次浇注等信号;PLC依据产品的工艺参数及通过现场模拟量输入得到当前离心铸造机的实际转速,经过计算,通过模拟量输出一个实际需要的转速,同时通过模拟量输入的离心机振动信号、温度信号,实时诊断离心铸造机的工作状态;离心铸造机的电机工作电流信号实时诊断离心机的负荷大小,实时显示其产品的工作曲线,确认产品的质量。
离心铸造

a)上模
1、上模内圈 2、上模压板 3、上模外圈
b)下模 4、下模外圈 5、下模内圈
上、下模结构(三拼结构) a)上模 b)下模
中模结构应能保证铸铝时不漏铝水,并保证在合 模时控制转子铁心的长度,而且便于装卸,现在 都做成两块或三块拼合的形式,拼合接缝处做成 止口,防止漏铝。为了加强中模的强度和刚度, 外围可加一些加强筋。
3r 1
离心浇注时铝液的自由表面形状
ρ──铝液的密度,约为2.38×10Kg/m3 r1──端环外圆的半径(m); r2──端环内圆的半径(m); ω──角速度
1-模具 2-铝液
Hale Waihona Puke 离心机的转速为r1 n 80 3 3 r1 r2
离心机转速是转子铸铝很重要的工艺参数。如果转速低,则离心力不够,结
2、铸铝模预热
铸铝模预热温度的高低,对铸件质量的影响很大。下模预热温度过高, 下端环容易出现缩孔,而且下模排气槽容易跑铝。温度太低,会把转子 铁心下端的热量导散,使铁心槽中的铝水先凝固,也会使下端环产生缩 孔。上、下模预热时模面朝下放置,以避免型腔落上烟灰。上、下模预 热温度一般为300~350℃,中模预热温度一般为150~200℃。 为了脱模方便和保护铸铝模型腔不受高温铝水的腐蚀,上、下模 在预热到200℃左右时,要刷一层涂料。涂料配方各厂不一样,有 的用滑石粉100g,水玻璃150g,水5kg;也可用滑石粉和机油
离心铸铝
离心铸铝是利用铸型旋转时所产生的离心力将铝液充满整个型腔并
凝固成型的。这是我国常用的一种笼型转子铸铝工艺。
1、工艺特点: 组织紧密,铸件质量好。 用于生产空心铸件。 2、工艺过程: 离心铸造
一、离心铸铝机
1-支架 2-平板 3-主轴 9-电动机 10-联轴器
转子离心铸铝的工作原理

转子离心铸铝的工作原理
转子离心铸铝是一种常用的铝合金零件制造方法,它的工作原理如下:
1. 铝液准备:将铝合金原料经过熔炼和调配,得到符合要求的铝液,通常包括铝和其他合金元素的混合物。
2. 模具准备:根据所需铝合金零件的形状和尺寸,制作出对应的模具,通常为铸造用模具。
3. 模具装置:将模具装入铸造设备,确保模具的稳定和正确放置。
4. 转子旋转:启动铸造设备,使转子开始旋转,通常在高速旋转状态下,以产生离心力。
5. 铝液注入:将预热至液态的铝液注入到模具的中心。
6. 离心力作用:由于转子的旋转,铝液受到离心力的作用,沿着模具壁面迅速扩散。
7. 金属凝固:随着离心力的作用,铝液逐渐冷却并凝固,形成铝合金零件的外形。
8. 铝合金零件脱模:待铝液完全凝固之后,停止转子旋转并取出模具,然后将铝合金零件从模具中取出。
9. 检验和后续处理:对铝合金零件进行外观检查、尺寸测量以及其他必要的质量检验,如有需要,还可以进行热处理、机械加工、表面处理等后续工艺。
通过上述工作原理,转子离心铸铝能够制造出形状复杂、壁厚薄、高精度的铝合金零件,适用于各种工业领域的应用。
离心铸铝的工艺流程

离心铸铝的工艺流程英文回答:Centrifugal casting is a casting process that involves pouring molten aluminum into a spinning mold. As the mold rotates, the centrifugal force pushes the molten metal against the mold walls, creating a hollow, cylindrical shape. This process is commonly used to produce pipes, tubes, and other cylindrical components.The centrifugal casting process can be broken down into several steps. First, a mold is prepared by coating the inner surface with a refractory material to prevent the molten aluminum from sticking to the mold. This refractory coating also helps to control the solidification process and improve the surface finish of the final product.Next, the mold is heated to a specific temperature to ensure proper solidification of the aluminum. The molten aluminum is then poured into the mold through a sprue,which is a channel that allows the metal to flow into the mold cavity. The sprue is usually positioned at the centerof the mold to ensure even distribution of the molten metal.Once the mold is filled with molten aluminum, it is rotated at a high speed. The centrifugal force generated by the rotation pushes the molten metal against the innerwalls of the mold, creating a hollow cylindrical shape. The rotation speed and duration are carefully controlled to ensure uniform thickness and proper solidification of the aluminum.After the molten aluminum has solidified, the mold is allowed to cool down. Once the mold has cooled, it is opened, and the newly formed aluminum component is removed. The component is then cleaned and finished to meet the desired specifications.Centrifugal casting offers several advantages overother casting methods. Firstly, it allows for theproduction of hollow cylindrical shapes with a high levelof accuracy and consistency. The centrifugal force helps toensure even distribution of the molten metal, resulting ina uniform wall thickness. Additionally, the centrifugal casting process can produce components with excellent mechanical properties, as the rapid solidification helps to refine the microstructure of the aluminum.中文回答:离心铸铝是一种铸造工艺,涉及将熔化的铝倒入旋转的模具中。
离心铸铝的工艺流程
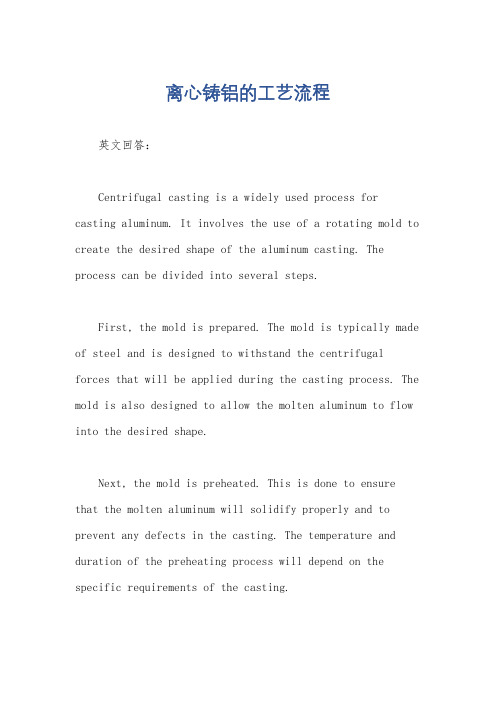
离心铸铝的工艺流程英文回答:Centrifugal casting is a widely used process for casting aluminum. It involves the use of a rotating mold to create the desired shape of the aluminum casting. The process can be divided into several steps.First, the mold is prepared. The mold is typically made of steel and is designed to withstand the centrifugal forces that will be applied during the casting process. The mold is also designed to allow the molten aluminum to flow into the desired shape.Next, the mold is preheated. This is done to ensurethat the molten aluminum will solidify properly and to prevent any defects in the casting. The temperature and duration of the preheating process will depend on the specific requirements of the casting.Once the mold is preheated, the molten aluminum is poured into the mold. The mold is then rotated at a high speed. The centrifugal force generated by the rotation of the mold causes the molten aluminum to spread evenly along the inner surface of the mold, creating a hollow casting with a uniform wall thickness.As the molten aluminum cools and solidifies, it takes on the shape of the mold. The rotation of the mold helps to ensure that the solidification process is uniform and that any impurities or gas bubbles are forced towards the center of the casting, where they can be easily removed.After the casting has solidified, the mold is stopped and the casting is removed. The casting is then cleaned and any excess material is removed, such as the sprue and risers. The casting may also undergo additional processes, such as heat treatment or machining, depending on the specific requirements of the final product.Centrifugal casting offers several advantages over other casting methods. It allows for the production ofcomplex shapes with a high degree of accuracy and repeatability. It also produces castings with a fine grain structure, which can result in improved mechanical properties. Additionally, the centrifugal force helps to eliminate porosity and other defects that can occur in traditional casting methods.In conclusion, centrifugal casting is a versatile and efficient process for casting aluminum. It offers numerous advantages and can be used to produce high-quality castings for a wide range of applications.中文回答:离心铸铝是一种广泛应用的铸造工艺,它利用旋转模具来制造铝铸件的所需形状。
- 1、下载文档前请自行甄别文档内容的完整性,平台不提供额外的编辑、内容补充、找答案等附加服务。
- 2、"仅部分预览"的文档,不可在线预览部分如存在完整性等问题,可反馈申请退款(可完整预览的文档不适用该条件!)。
- 3、如文档侵犯您的权益,请联系客服反馈,我们会尽快为您处理(人工客服工作时间:9:00-18:30)。
由于转 子冲片单槽 面 积 大 , 并且 为分段 转 子, 为避 免温度 高造 成铁心瓢 曲, 铁心温度不易 过 高 。 虑到 去 除装 夹 、 正 过程 中的热 量损 考 找 失, 铁心温度设定在40 ~ 0  ̄, 5  ̄ 5 0 分流帽的预热 C C
温 度 和 铁 心温 度相 同 。
工艺。
铝转 子 制造 过 程 中离心机 的改造 、 离心铸 铝 各工艺参数
的确 定 、 具结 构 的设 计等 。 过 此番对 大型 电机离 心 模 通 铸 铝工艺 的研 究, 为大直径铸 铝转 子制造奠实了基础 。
关键词 : 离心铸 铝 顺 序凝 固 预热 工装
中图分类号 : TM3 5 文献标识码 : 0 A
rv r ci eo eau i u — a t g r t ro el r e sz ie p a t f h l m n m - si o o ft a g -i e c t c n h - ee t i ma h n , n wh c ec n rf g l l mi u c s i g lc rc c i e i i ht e t i a u n m a t h u a n t c n q e s a p i d Th o g t d i g t e c n rf g l e h i u s wa p l . r u h su y n h e tiu a e au n m a tn e h i u s o e r t ro e l r e sz l mi u c si g t c n q e f t o o ft a g — ie h h ee t i c i e t e f u d t n t r c s h l mi u lc rc ma h n , h o n a i o p o e st e au n m— o c s i g r t r o e l r e- z l c rc ma h n s e t b- a t o o ft a g -i e e e ti c i e wa s a - n h s
.
4 4.2 1 第 2期 《 机 技 术 》 0 2年 电
研究与交流 满 足不了生产条件。 经过反 复研 究论证 , 除满足 该台转 子直径外 , 同时兼 顾我公 司现有产 品, 确 定离心机承重 8 , T 底大盘直径为 l 0 mm, 0 2 另
作 一 个 辅 助 工 作 台 , 大 外 径 可 扩 大 到 l 0 最 0 5 该 转 子 浇 铝 量 4 6 g 再 加 上 浇 口铝 水 补 2k , 缩 量及 漏 铝 问题 , 水总 量按 6 0 准 备。 铝 0 kg 为
在 激烈 的竞争 中立于不 败之 地 的关 键 。 所周 众 知, 铜条转子制造成本高, 周期长 , 难度大; 而铸 铝转 子成本低 , 生产周期短 。 采用铸铝转 子取代 铜条转子, 即节约大量铜排, 又降低了电机 的制 案。 其中包括设备改制 、 工艺参数确定和工装结 构确定等。
21 设备 改制 .
222 铁 心温度 ..
() a 壁厚 尺寸的确定 : 考虑 到下端 环先凝 固, 下模应 降温快 。 因此 , 保证模具强度 的前 在 提下, 按从下 向上 , 外向内的原则考虑模具 的 从
壁 厚 , 侧 和底 部 厚 度 选 择 3 mm ̄ 0 外 0 4 mm, 内侧 2 rm。 保证 自外 向 内的凝 固顺 序 , 0 a 为 下模 内部 应 聚集 一 定 的热 量 , 部应 连 成 一体 , 底 在适 当位 置 钻 4 4 mm的排 气 孔 。 个 0
DOI 编码 : 0 3 6 / is 0 62 0 .0 20 .1 1 .9 9j snl 0 -8 72 1 .20 3 .
Abs r c :T e r b i i g o e c n rf g l a h n , t a t h e u l n f t e tiu a c i e d h m s ti g o a i u i d ft c n c l a a t ro e t i - e t fv ro sk n so h ia r mee fc n rf n e p u g la u i u c si g a d d sg fmo l o sr c i n a l m n m a tn n e i n o u d c n t u to
1 结构
转 子外 径 1 3 mm、 环 外径 1 2 mm、 0 0 端 2 0
we e d s rb d i e a l o i e l s l t ep o u — r e c i e n d t i c mb n d c o ey wi t r d c h h
ls d. ihe Key wor :Ce r f ga l m i ds ntiu la u num a tng S ue c c s i eq n e s ldi c to Pr . a Fi t e oi f ain i e he t x ur
端环 内径 8 0 3 mm、 端环厚1 0 2 mm、 轴孔 5 0 9
满无 残缺 , 内致密和无缩孔 , 下模预 热温度 般 确 定为1 0C 1 0 由于转 子端环 比较 厚 、 0 "~ 5  ̄ C。 热 容量大 , 却时间会比较长 , 冷 下模预热 温度可 以 相对高一些。 生产 时, 具最 终预热温 度范围为 模 10 10 实际温度为10 。 2 ℃~ 5 ℃, 4 ̄ C
研究与交流
大 型 电机股 份 有 限公 司 ( 4 0 1 0 2) 5
I r d to f c nt o uc i n o hni s o h n r f g l um i um - a t n t r Te c ft e Ce t i u a Al n c s i g Ro o o r e s z e ti o o s fLa g - i e El c r c M t r
在顺序凝 固过程 中, 铸铝转子 的上端环 除了 浇 口外最 后凝 固, 因此 上模温 度应该高一些。 但
由于该 铸铝转 子用铝 量大, 浇冒口流量大 , 浇注
过 程中铝液传递 到上模的热量较多, 经计算上模
的温 度 确 定 为3 0 4 0C。 样 既 能 保 证 合 理 5 ̄ 0 ̄ 这 C一
在离心铸 铝工艺 中, 温度是 最为关键 的, 它
的高低 直接影 响铸铝转子质量。 要想获得合格 的 转 子, 必须控制好模具温 度、 铁心温度和铝水温
度, 只有达 到温度 的合理 配合, 严格 遵循 顺序凝 固原理 , 才能获得质量好的铸铝转子。
221 下模 预 热温度 ..
mi, n 最高10/ n 10/ n 实际生产时, 4r ~5r 。 mi mi 考虑
223 上 模 温度 的 确 定 ..
() b 铁心定位 止口尺寸的确定 : 下模 止口与
铁 心 外 径 是 在 热 态 下 定 位 的 , 寸小 了铁 心 放 尺 不 进 去 , 了又会 造 成 端 环 偏 心 , 响 平 衡 。在 大 影 生 产 实 践 中, 们 推 导 出 铁 心 外 径 与 模 具 止 口 我
保证铝 水熔化 质量 , 铝水 熔化温 度最高不超 过
8 0C。 虑 转 子用 铝 量 大 , 铝 从 坩 埚 取 到 吊 0 ̄ 考 将 包 的 时 间 长 , 减 少 热 量 损 失 , 用 保 温 吊 包 为 采
mm。 这样可兼顾小直径铸 铝转子和大直径铸铝
转 子 的要求 。 扩大了设备的使 用范围, 提高了利
Wa gAi ua n h Ja i mus e ti a hi e Co. d iEl c rc M c n ,Lt
摘
要: 结合生 产实际 , 论述了大型 电机 采用离心铸
能要求 的前提下’ 采用铸铝转子替代铜 条转 子。 为保证大型电机制造质量, 必须尽快 完善大型电 机转 子离心铸 铝制造工艺 。 合1 0 k 4 电 结 0 W.P O 机铜条转 子改为铸 铝转子, 研讨了转 子离心铸铝
用率。 为满足 不 同规格 转 子采 用不 同转 速 的要 求, 原设备没有调速装 置 , 次改造专 门配备了 此 无级调速装置和数显转速表 , 完全可以满足工艺
调 速 的要求 。 22 参 数 的确 定 .
并预 热到 3 0C 最 终 浇注 温度 确定 为7 0 8  ̄, 5 ̄ C~
线速度过大, 且转子铁心与模具质量较大 , 加之 端环厚度 l0 lmm, 铁心长1 0 mm, 0 1 装夹高度接
近 1 0 mm。 防止下 端 环 出现 抛 空现 象 , 用 0 7 为 采
比较 低的转 速 比较合 适 , 终确 定离心机 的调 最
速 过程 和 范 围为 9 r n7r nl0/ n 0/ 一0/ —1r mi mi mi。
mm, 心长 1 0 mm, 子总 重 36 , 中铝 水 铁 0 1 转 .T 其
净 ̄4 6 g 转子装夹高度尺寸为1 0 m 2k 。 0 m。 7
2 工艺确定
此大型铸 铝转子, 国内外都属首次 生产, 既 无成熟经验可借鉴, 又无资料可查 。 反复研 究 经
和分析, 精心拟定了一 套离心浇铸工艺实施 方 整 提高生产效率 , 降低 电机制造 成本 , 是公司
冷热 态参 数 的关 系 , 计算 出下模 止 口尺寸应 为
ql03 5 mm 。 b 6.
补缩 , 保证转子质量, 又能缩短整 个转 子的冷却 时间。 实际生产时测定上模温 度为30 。 7 ̄ C
224 铝 液 温 度 ..
( ) 气 槽 的设计 : C排 下模是 铝 水最 后到达 的部位 , 气槽 设计是否 合理 直接影 响下端环 排
离心机 是产生离心力的来源 , 离心力的大小
和离心机 的转 速是否合理是决 定铸 铝转子质量 的重要 因素。 原有 离心机 最大 承 载 重量 3 , T 而 该 电机 转子铁心与铸铝轴 的重量就 已接近 5 。 T 底盘外径 及装夹高度和离心机 承重等各项远远