主轴系统的连接与调试
蒙德驱动器主轴(MF)调试步骤
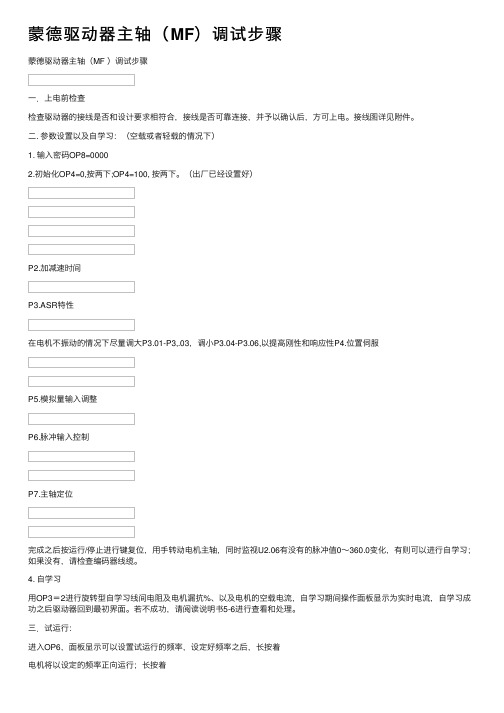
蒙德驱动器主轴(MF)调试步骤蒙德驱动器主轴(MF )调试步骤⼀.上电前检查检查驱动器的接线是否和设计要求相符合,接线是否可靠连接,并予以确认后,⽅可上电。
接线图详见附件。
⼆. 参数设置以及⾃学习:(空载或者轻载的情况下)1. 输⼊密码OP8=00002.初始化OP4=0,按两下;OP4=100, 按两下。
(出⼚已经设置好)P2.加减速时间P3.ASR特性在电机不振动的情况下尽量调⼤P3.01-P3,.03,调⼩P3.04-P3.06,以提⾼刚性和响应性P4.位置伺服P5.模拟量输⼊调整P6.脉冲输⼊控制P7.主轴定位完成之后按运⾏/停⽌进⾏键复位,⽤⼿转动电机主轴,同时监视U2.06有没有的脉冲值0~360.0变化,有则可以进⾏⾃学习;如果没有,请检查编码器线缆。
4. ⾃学习⽤OP3=2进⾏旋转型⾃学习线间电阻及电机漏抗%、以及电机的空载电流,⾃学习期间操作⾯板显⽰为实时电流,⾃学习成功之后驱动器回到最初界⾯。
若不成功,请阅读说明书5-6进⾏查看和处理。
三.试运⾏:进⼊OP6,⾯板显⽰可以设置试运⾏的频率,设定好频率之后,长按着电机将以设定的频率正向运⾏;长按着运⾏时,驱动器显⽰界⾯会⾃动从频率显⽰变化到实时电流显⽰,正反转电流接近⼤⼩则为正常。
注:如果试运⾏过程中电机振动,请将E5.01、E5.02、E5.03的增益参数设⼩再试运⾏同时检查电机参数以及编码器参数有没有设错。
试运⾏正常之后就可以接⼊系统由系统来控制。
附件:接线图5.5KW及以下(⼩机壳):三相电源340-420V50/60HzCN2端⼝(控制脉冲输⼊/脉冲反馈输出)模拟量输⼊/输出接⼝晶体管输出接⼝DC48V 50mA以下7.5KW及以上(⼤机壳):TM2端⼝三相电源340-420V 50/HzTS ~+10V 』以下TM3端⼝(模拟量输出接⼝)TM1端⼝(功能输出接⼝)TM3端⼝30mA30m 以下』~+10V 』。
840Dsl数控系统模拟主轴的调试
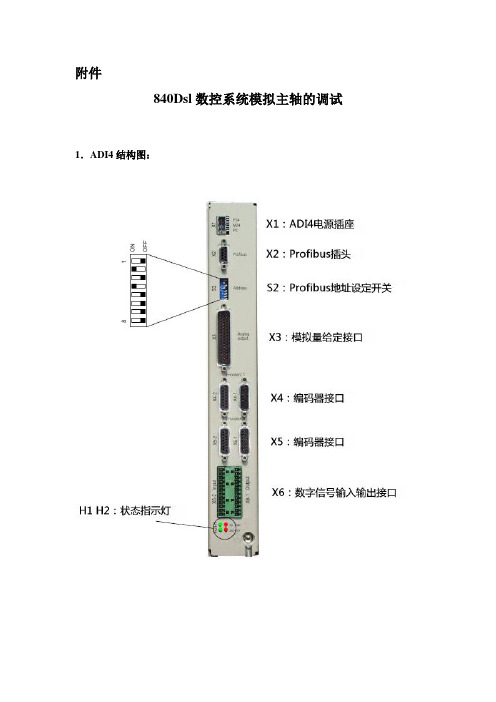
附件
840Dsl数控系统模拟主轴的调试1.ADI4结构图:
1.1 DC24V电源插头X1
P24 +24V
M24 0V
PE 接地
1.2 Profibus插头X2
ADI4通Profibus总线与数控系统通讯,在802Dsl中,通过总线连接的还有I/O信号的PP板,因此在正常连接的时候除了要正规标准的制作Profibus总线插头外,还要注意插头的ON/OFF的位置,避免拨错位置,导致无法通讯。
1.3 Profibus地址设定开关S2
地址分配采用的是BCD码
若总线地址是17:将1、5开关置位。
如下图:
1.4 模拟量输出X3
1.5 数字输入信号接口X6-2
1.6 在STEP7的“hardware”中挂站编译并保存
1.7 参数设置
因为ADI4可以配置4个轴,根据机床的实际情况将13050的轴号与ADI4匹配,在“hardware”中将ADI4中的数值改成参数[13050]的“4340—4460”。
MD13060=3
MD13070=80FH
MD13080=4
重新上电,调试结束。
FANUC主轴定向的调试步骤这么详细的教程不多了
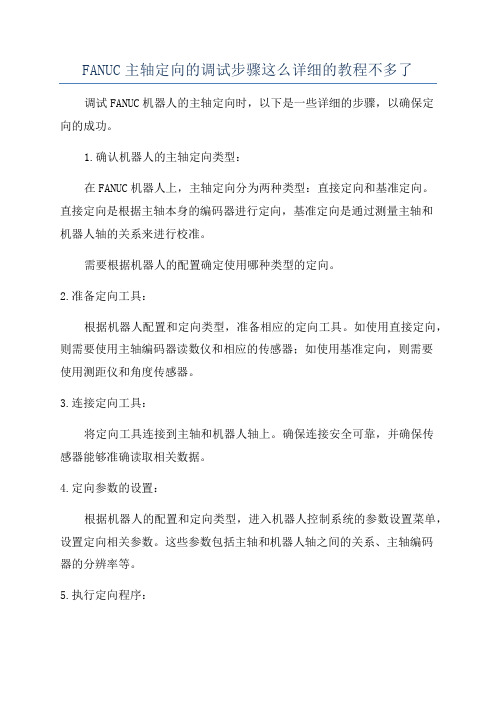
FANUC主轴定向的调试步骤这么详细的教程不多了调试FANUC机器人的主轴定向时,以下是一些详细的步骤,以确保定向的成功。
1.确认机器人的主轴定向类型:在FANUC机器人上,主轴定向分为两种类型:直接定向和基准定向。
直接定向是根据主轴本身的编码器进行定向,基准定向是通过测量主轴和机器人轴的关系来进行校准。
需要根据机器人的配置确定使用哪种类型的定向。
2.准备定向工具:根据机器人配置和定向类型,准备相应的定向工具。
如使用直接定向,则需要使用主轴编码器读数仪和相应的传感器;如使用基准定向,则需要使用测距仪和角度传感器。
3.连接定向工具:将定向工具连接到主轴和机器人轴上。
确保连接安全可靠,并确保传感器能够准确读取相关数据。
4.定向参数的设置:根据机器人的配置和定向类型,进入机器人控制系统的参数设置菜单,设置定向相关参数。
这些参数包括主轴和机器人轴之间的关系、主轴编码器的分辨率等。
5.执行定向程序:根据机器人控制系统的操作界面,执行主轴定向程序。
根据具体的指导操作,逐步进行定向。
这些步骤可能包括启动主轴、采集数据、分析数据等。
6.定向结果的评估:根据定向程序的结果,评估定向的质量。
检查定向误差是否在可接受范围内,如何校准误差的大小等。
7.重新校准:根据定向结果的评估,判断是否需要重新校准。
如果定向误差在可接受范围内,则可以继续下一步操作。
如果定向误差较大,则需要重新调整定向参数,并重新执行定向程序。
8.定向结果的记录:记录定向结果,包括定向参数、定向误差等。
这样可以方便以后的参考和调整。
总结:以上是FANUC机器人主轴定向的详细步骤,根据机器人的配置和定向类型,可能会有一些差异。
通过仔细遵循上述步骤,并根据实际的情况进行适当的调整,可以确保主轴定向的成功。
连接与调试主轴系统

模块三连接与调试主轴系统课题一连接变频器主线路一、任务引入数控机床上主轴系统的变频器接线图,如图3-1所示,认请变频器上主接线端子的功二、任务分析数控机床主轴的速度是由电压频率变换器(即变频器)实现的。
什么是变频器?变频器是由哪几部分组成?主接线端子有哪些功能?下面我们就对这些问题进行讲解。
三、相关知识1、变频电源的应用变频器即电压频率变换器,是一种将固定频率的交流电变换成频率、电压连续可调的交流电,以供给电动机运转的电源装置。
交流电动机变频调速与控制技术已经在机床、纺织、印刷、造纸、冶金、矿山以及工程机械等各个领域得到了广泛应用,因此提供进口和国产变频电源产品的单位已经十分普遍。
中小功率变频电源产品由于运行时其散热表面的温度可高达90℃,所以大多数要求壁挂立式安装,并在机壳内配有冷却风扇以保证热量得到充分的散发。
在电气柜中应注意给变频电源的两侧及后部留出足够空间,而且在它的上部不应安排容易受人影响的器件。
多台变频电源安装在一起时要尽量避免竖排安装,如必须竖排则要在两层间配备隔热板。
变频电源工作的环境温度不准超过50℃。
2. 变频电源的基本接线小功率变频电源产品的外形如图3-2所示。
一般三相输入、三相输出变频电源的基本电气接线原理图如图3-3所示。
在图3-3中,主电路接入口R、S、T处应按常规动力线路的要求预先串接符合该电动机功率容量的空气断路器和交流接触器,以便对电动机工作电路进行正常的控制和保护。
经过变频后的三相动力接出口为U、V、W,在它们和电动机之间可安排热继电器以防止电动机过长时间过载或单相运行等问题。
电动机的转向仍然靠外部的线头换相来确定或控制。
B1、B2用来连接外部制动电阻,改变制动电阻值的大小可调节制动的程度。
工作频率的模拟输入端为A11和A12,模拟量地端AGND为零电位点。
电压或电流模拟方式的选择一般通过这些端口的内部跳线来确定。
电压模拟输入也可以从外部接入电位器实现(有的变频电源将此环节设定在内部),电位器的参考电压从REF端获取。
发那科(FANUC)CNC系统与机床的连接及调试

发那科(FANUC)CNC系统与机床的连接及调试发那科计算机数控系统是最畅销的机床控制系统。
目前在国内主要使用0系统和0i系统,针对广大用户的实际情况,本文简要叙述这两种系统的连接及调试,掌握了这两种系统,其它FANUC系统的调试则迎刃而解。
1.调机步骤:⑴.接线:按照设计的机床电柜接线图和系统连接说明书(硬件)中(书号:B-61393或B-63503)绘出的接线图仔细接线。
⑵.拔掉CNC系统和伺服(包括主轴)单元的保险,给机床通电。
如无故障,装上保险,给机床和系统通电。
此时,系统会有#401等多种报警。
这是因为系统尚未输入参数,伺服和主轴控制尚未初始化。
⑶.设定参数:①. 系统功能参数(既所谓的保密参数):这些参数是订货时用户选择的功能,系统出厂时FANUC已经设好,0C和0i不必设。
但是,0D(0TD和0MD)系统,须根据实际机床功能设定#932--#935的参数位。
机床出厂时系统功能参数表必须交给机床用户。
②. 进给伺服初始化:将各进给轴使用的电机的控制参数调入RAM区,并根据丝杠螺距和电机与丝杠间的变速比配置CMR和DMR。
方法如下:·设参数SVS,使显示器画面显示伺服设定屏(Servo Set)。
0 系统设参数#389/0位=0;0i系统设参数#3111/0位=1。
然后在伺服设定屏上设下列各项:·初始化位置0。
此时,显示器将显示P/S 000报警,其意义是要求系统关机,重新启动。
但不要马上关机,因为其它参数尚未设入。
应返回设定屏继续操作。
·指定电机代码(ID)。
根据被设定轴实际使用的电机型号在“伺服电机参数说明书(B—65150)”中查出其代码,设在该项内。
·AMR设0。
·设定指令倍比CMR。
CMR=命令当量/位置检测当量。
通常设为1。
但该项要求设其值的1倍,所以设为2。
·设定柔性变速比(N/M)。
根据滚珠丝杠螺距和电机与丝杠间的降速比设定该值。
华中数控主轴的连接与调试

湖南工业职业技术学院毕业设计课题名称华中8型系统主轴控制的连接与调试系(院)名称机械工程系专业及班级数控技术S2014- 学生姓名学号指导教师李平化刘瑞已完成日期年月日湖南工业职业技术学院毕业设计任务书系(院)名称机械工程系专业及班级数控技术S2014-学生姓名学号设计题目华中8型系统主轴控制的连接与调试指导教师(签字)李平化刘瑞己教研室主任(签字)龙华系主任(签字)2016 年 11 月 15 日湖南工业职业技术学院毕业设计任务书课题简介(包括课题背景、价值、目的和意义、对学生知识和能力的要求、应具备的条件等)华中8型数控系统是全数字总线式高档数控装置,采用模块化、开放式体系结构,基于具有自主知识产权的NCUC工业现场总线技术。
支持总线式全数字伺服驱动单元和绝对值式伺服电机,支持总线式远程I/O单元,主要应用于全功能数控铣床、铣削中心。
本课题将从阅读华中8型系统主轴控制的连接与调试相关资料开始,了解华中8型系统各个模块的连接方法,根据数控铣床的工作要求,设计外围电路,将数控系统与外围电路安装起来,根据系统调试流程,完成系统调试工作。
课题目标和任务1、理解华中8型主轴的连接,绘制其主轴控制系统电气原理图。
2、掌握华中8型系统调试要点,撰写主轴控制系统调试报告。
(要求1.5万字)3、熟悉系统参数含义,学会配置相关参数、修改数控系统PLC程序,满足功能需求。
实施步骤和方法1、以一种驱动器为研究对象,查找资料,在老师的指导下掌握系统连接方法,完成系统电气连接;2、参照系统的连接调试手册,理解各个接线柱含义,并对它的参数进行试调从而得出合适的参数,完成主轴驱动器的连接和调试。
3、撰写调试报告,完成答辩。
进程安排(整个毕业设计的时间安排,还包括实习时间及地点、方式等方面的安排等)第一周:1、阅读华中8型系统相关手册,掌握系统连接方法;2、绘制主轴控制系统电气原理图。
第二周:1、完成系统电气连接;2、制作线缆;3、撰写连接调试报告。
数控系统的连接及调试

实训二数控系统的连接及调试一、实验目的1、熟悉HED—21S数控系统综合试验台各个组成部件的接口。
2、读懂电气原理图,通过电气原理图独立进行数控系统各部件之间的连接。
3、了解数控系统的调试运行方法。
二、实训设备HED—21S数控系统综合实验台万用表工具三、相关知识包括数控装置,由变频器和三相异步电机构成主轴驱动系统,由交流伺服单元和交流伺服电机构成的进给伺服驱动系统,由步进电机构成的进给伺服驱动系统等的数控系统,可实现主轴驱动系统的速度控制,进给伺服驱动系统的开环、半闭环、闭环控制。
1.电源部分图 4—1 电源部分接线图2.继电器与输入/输出开关量图4-2电器部分接线图图 4—3 继电板部分接口图 4—4 输入开关量接线图图 4—5 输出开关量接线图3.数控装置与手摇单元和光栅尺图 4—6 手摇单元接线图图 4—7 数控装置与光栅尺连接4.数控装置与主轴的连接图 4—8 数控装置与主轴连接5.数控装置与步进驱动单元连接图 4—9 数控装置与步进驱动单元的连接6.数控装置与交流伺服单元的连接图 4—10 数控系统与交流伺服单元的连接7.数控系统刀架的连接图 4—11 刀架电动部分四、实训内容及骤1.数控系统的连接(1)电源回路的连接按前图接线,并用万用表检查电源电压和变压器输出端电压。
(2)数控系统继电器的输入/输出开关量连接按前图连接继电器和接触器,以及输入/输出开关量。
(3)数控装置和手摇单元的连接按前图连接手摇单元和光栅尺。
(4)数控装置和变频主轴的连接连接变频器和主轴电机强电电缆,以及数控装置和变频器信号线。
确保地线可靠。
(5)数控装置和交流伺服器的连接按前图连接交流伺服电机的强电电缆和码盘信号线,接入伺服单元电源。
地线可靠正确接地。
(6)数控装置和步进电机驱动器的连接按前图连接步进电机驱动器和步进电机,以及驱动器电源。
(7)数控系统刀架电动机的连接连接刀架电机。
2、数控系统调试(1)线路检查。
项目6 任务6.3 串行数字主轴的调试与维修(标准)
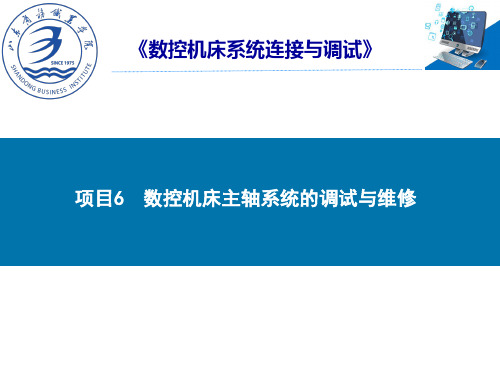
项目6 数控机床主轴系统的调试与维修
6.3.2串行主轴准停 1.主轴准停控制 (1)采用主轴电动机带MZi传感器实现主轴准停控制 利用主轴电动机内装传感器发出的主轴速度、主轴位置信号及主轴一转信 号实现主轴准停控制,如图6-24所示,这种方式适合主轴电动机与主轴1:1传 动的场合。由CNC发出主轴准停信号,通过伺服放大器JYA2进行主轴位置、主 轴速度及主轴一转信号的反馈。
图 6-25外接主轴独立编码器实现主轴准停控制
项目6 数控机床主轴系统的调试与维修
(3)采用外接接近开关实现主轴准停控制 利用外接接近开关发出主轴一转信号实现主轴准停控制,如图6-26所示, 这种方式适合主轴电动机与主轴任意传动比的场合。由CNC发出主轴准停信号, 通过伺服放大器JYA2进行主轴位置、主轴速度及JYA3进行主轴一转信号的反 馈。
♢主轴电动机内置Mi传感器:内部有A/B相两种信号,一般用来检测主轴 电动机回转速度,其不可以实现位置控制,也不能进行简单的定向。
♢主轴电动机内置MZi (BZi, CZi)传感器:除了和Mi传感器一样有A/B两相 信号外,其内部还有Z相信号,所以MZi传感器既可以进行速度控制,还可 以进行位置控制。BZi、CZi传感器检测精度比MZi要高。
表6-11参数“4002”设置说明
SSTYP3 SSTYP2 SSTYP1 SSTYP0
0
0
0
0
没有位置控制功能
0
0
0
1
使用电动机传感器作位置
0
0
1
0
α位置编码器
0
0
1
1Leabharlann 独立的BZi、CZi、传感器
数控系统连接与调试 78C3-4
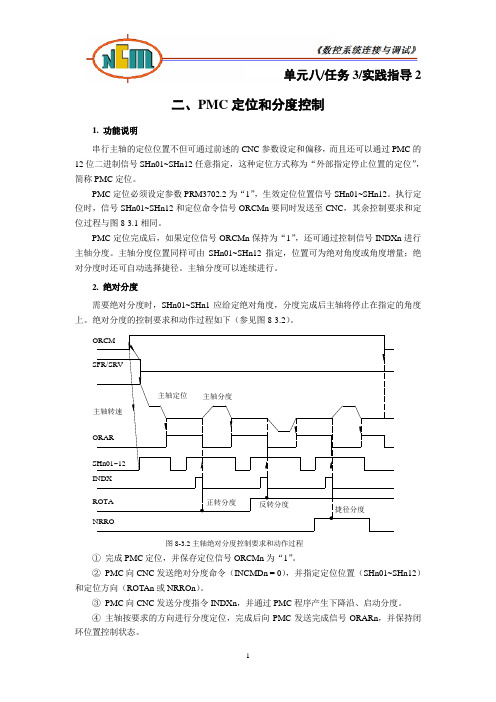
ORCM SFR/SRVORAR主轴转速SHn01~12 INDX ROTA NRRO 主轴定位捷径分度正转分度反转分度主轴分度单元八/任务3/实践指导2二、PMC定位和分度控制1. 功能说明串行主轴的定位位置不但可通过前述的CNC参数设定和偏移,而且还可以通过PMC的12位二进制信号SHn01~SHn12任意指定,这种定位方式称为“外部指定停止位置的定位”,简称PMC定位。
PMC定位必须设定参数PRM3702.2为“1”,生效定位位置信号SHn01~SHn12。
执行定位时,信号SHn01~SHn12和定位命令信号ORCMn要同时发送至CNC,其余控制要求和定位过程与图8-3.1相同。
PMC定位完成后,如果定位信号ORCMn保持为“1”,还可通过控制信号INDXn进行主轴分度。
主轴分度位置同样可由SHn01~SHn12指定,位置可为绝对角度或角度增量;绝对分度时还可自动选择捷径。
主轴分度可以连续进行。
2. 绝对分度需要绝对分度时,SHn01~SHn1应给定绝对角度,分度完成后主轴将停止在指定的角度上。
绝对分度的控制要求和动作过程如下(参见图8-3.2)。
图8-3.2主轴绝对分度控制要求和动作过程①完成PMC定位,并保存定位信号ORCMn为“1”。
②PMC向CNC发送绝对分度命令(INCMDn = 0),并指定定位位置(SHn01~SHn12)和定位方向(ROTAn或NRROn)。
③PMC向CNC发送分度指令INDXn,并通过PMC程序产生下降沿、启动分度。
④主轴按要求的方向进行分度定位,完成后向PMC发送完成信号ORARn,并保持闭环位置控制状态。
⑤PMC在定位点执行所需要的动作。
⑥如果需要,重复②~⑤动作,继续变换定位点、定位方向,进行其他位置的定位。
⑦撤消主轴定位信号ORCMn,解除闭环位置控制,回到速度控制状态。
3. 增量分度需要增量分度时,SHn01~SHn1应给定增量角度,增量分度不能选择捷径。
数控机床主轴变频调速系统的连接与调试

• 2.恒功率范围宽 • 主轴在全速范围内均能提供切削所需功率, 并尽可能在全速范围内提
供主轴电动机的最大功率。由于主轴电动机与驱动装置的限制, 主轴 在低速段均为恒转矩输出。
上一页 下一页 返回
任务5.1数控机床主轴控制系统的认知
• 为满足数控机床低速、强力切削的需要, 常采用分级无级变速的方法 (即在低速段采用机械减速装置),以扩大输出转矩。
一般不提供, 采用脉冲信号作为指令的进给驱动装置, 只有当脉冲指令 类型为“脉冲+ 方向”时, 可以把方向信号理解为改变电动机方向的 控制接口。而且主轴驱动装置的方向控制接口是和速度模拟指令接口 一起出现的, 多是DC24V 开关量接口: 进给驱动装置的“方向”控制 接口多是和“脉冲”信号一起出现的, 多是DC5V 数字信号。
上一页 下一页 返回
任务5.1数控机床主轴控制系统的认知
• 因此, 在接口上主轴驱动装置又具有自身的特点。 • 图5 -1 -3 是主轴装置(变频器)最基本的接口图, 如图所示采用三相交
流380V 电源供电; 速度指令由3、4 脚输入(图中通过电位器从单元内 部获得, 在数控机床上一般由数控装置或PLC 的模拟量输出接口输入 ), 指令电压范围是直流0 ~10V; 主轴电动机的启动/ 停止以及旋转方 向由外部开关5、6 控制, 当5 闭合时电动机正转, 当6 闭合时电动机反 转, 若5、6 同时都断开或闭合则电动机停止。也可以定义为5 控制电 动机的启动和停止, 6 控制电动机的旋转方向。变频器根据输入的速 度指令和运行状态指令输出相应频率和幅值的交流电源, 控制电动机 旋转。
模拟主轴的调试及参数设置 电子教材
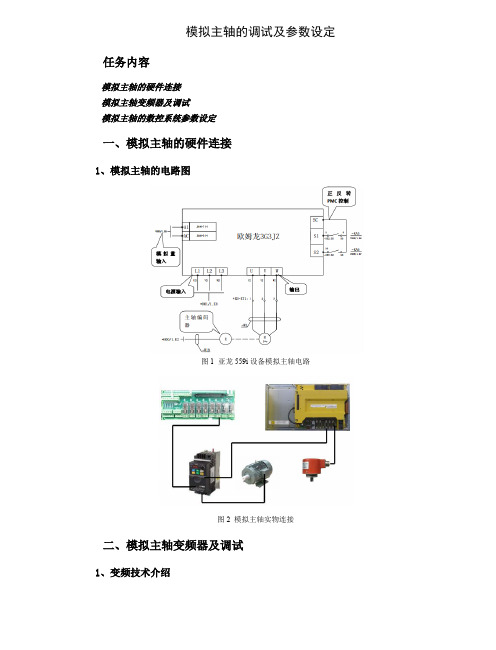
运行状态显示
变频器动作中亮灯/闪烁。亮灯:正转运行中,缓慢闪烁(1.4 秒 循环);反转运行中,快速闪烁(0.2 秒循环)。
参数设定模式显 示
参数设定模式时亮灯。
监视器显示
监视模式时亮灯。
停止运行
也可以进行报警复位。
用于切换 PU/外部运行模式。使用外部运行模式(通过另接的频率
运行模式切换 设定旋钮和启动信号启动运行)时请按此键,使表示运行模式的 EXT
监视器(4 位 LED)
显示频率、参数编号等。
M 旋钮
用于变更频率设定、参数的设定值。按该按钮可显示以下内容:监 视模式时的设定频率;校正时的当前设定值;错误历史模式时的顺序。
模式切换
用于切换各设定模式,长按此键(2 秒)可以锁定操作。
各设定的确定
运行中按此键则监视器出现以下显示:运行频率→输出电流→输出 电压
模拟主轴的调试及参数设定 任务内容
模拟主轴的硬件连接 模拟主轴变频器及调试 模拟主轴的数控系统参数设定
一、模拟主轴的硬件连接
1、模拟主轴的电路图
图 1 亚龙 559i 设备模拟主轴电路
图 2 模拟主轴实物连接
二、模拟主轴变频器及调试
1、变频技术介绍
变频调速技术是电力拖动控制系统的换代技术,它在提高产品产量和质量、节约电能、 实现自动化以及改善工作环境等方面,可以发挥很大作用,给工厂企业带来可观的经济效益。 国外一些厂家,在 60 年代末到 70 年代初就开始专业生产,进入 80 年代已相当普及。我国 与先进国家相比,起步较晚,相对落后,国家在五年规划中都把发展变频技术列为重点,大 力推广。90 年代以来,变频调速器在我国的应用也相当广泛,不仅在新设备、家电中,就 是对老设备(如风机,水泵、轧钢机、造纸机、化纤机械以及机床、电梯、起重机等等)的 技术改造也大量使用变频调速器。在数控机床中,变频调速技术常被用于主轴控制。
数控机床主轴变频调速系统的连接与调试
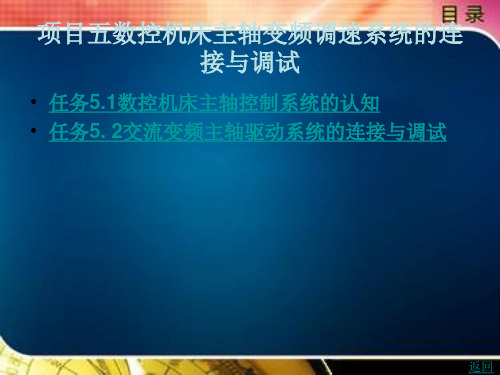
• 1.调速范围宽 • 保证加工时选用合适的切削用量, 以获得最佳的生产率、加工精度和
表面质量。特别对于具有自动换刀功能的数控加工中心, 为适应各种 刀具、工序和各种材料的加工要求, 对主轴的调速范围要求更高, 要求 主轴能在较宽的转速范围内根据数控系统的指令自动实现无级调速, 并减少中间传动环节, 简化主轴箱。
上一页 下一页 返回
任务5.1数控机床主轴控制系统的认知
• 二、主轴电动机的分类与特点
• 为了满足数控机床对主轴驱动的要求, 主轴且在大的调速范围内速度要稳定,恒功率调速范
围宽。 • ②在断续负载下电动机转速波动要小。 • ③加速、减速时间短。 • ④温升低,噪声和振动小,可靠性高,寿命长。 • ⑤电动机过载能力强。 • 常见主轴电动机可以分为以下三类: • 1.直流主轴电动机
上一页 下一页 返回
任务5.1数控机床主轴控制系统的认知
• 采用强切削电动机后, 由于无需机械调速, 主轴箱内省去了齿轮和离合 器, 主轴箱实际上成了主轴支架, 简化了主传动系统。
• 三、主轴驱动装置的接口
• 主轴驱动装置的接口与进给驱动装置有许多类似, 进给驱动装置具备 的接口, 在主轴驱动装置上一般都可以找到, 只是不同厂家不同档次的 主轴驱动装置所包含的接口类型不同,例如, 主轴伺服装置的接口类型 比变频器的接口要丰富; 具备矢量控制功能的变频器又比简易型变频 器接口丰富。不同的是: 进给驱动装置主要工作在位置控制模式下, 而主轴驱动装置主要工作在速度控制模式下; 同一台数控机床上主轴 输出功率比进给轴输出功率要大得多。
数控机床的电气连接与调试

840C型数控装置是32位微处理机系统,具有计算机辅助设计 (CAD)功能,能控制多轴,可5轴联动。
⑤SINUMERIK8型
8型数控装置时用于柔性制造的控制系统,它采用多微处理器, CPU均为8086
2021/9/15
7
项目1:数控系统的连接及调试
⑥SINUMERIK840D型 SINUMERIK 840D系统适用于所有的数控场合,10个加工通道,从2轴 到31轴控制。系统有三种基于不同计算机性能主板而分别适用于高级、 中级和基本的应用范围。840D系统控制器和相关的软件均按照模块化 结构进行配备,可以实现从复杂的多轴运动控制直到高速切削所需要 的数控系统基础平台和应用范围很广的应用操作知识库。零件的编程 以易于操作使用为原则,可使用循环方式和轮廓方式直接进行编程, 用通俗易懂的图形模拟方式验证切削路径和几何尺寸,可选定一个面、 顶部或三维观察的方式,采用带刀尖轨迹或不带刀尖轨迹进行模拟显 示
2021/9/15
1
项目1:数控系统的连接及调试
④F16系列
F16系列的性能位于F15系列和F0系列之间,结构为多主控总线, 它采用CISC处理器的基础上增加了用于高速运算处理的32位RISC 高速处理器
⑤F18系列
F18系列是在F16系列之后推出的32位数控装置,性能位于F15系列 和F0系列之间。但低于F16系列
简单的操作编程支持工具MANUAL GUIDE 0i
针对磨床的独特控制功能
以太网功能
数据服务器功能
2021/9/15
3
项目1:数控系统的连接及调试
2021/9/15
CP1:系统直流24V输入电源接 口FUSE:系统DC24V输入熔断
器(5A)。 JA7A:串行主轴/主轴位置编码器
FANUC数控系统连接与调试实训 任务4 0i-F伺服主轴硬件模块
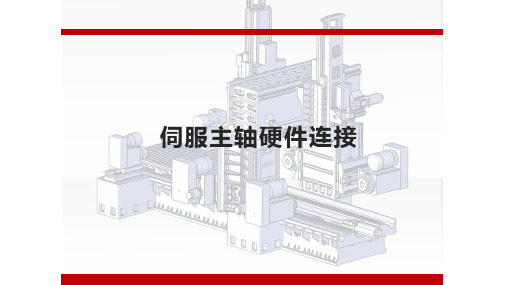
βiSVM-B
βiSVM2-B
3 αi-B电源模块硬件连接
αi-B电源模块硬件连接
控制电源
伺服或主轴 放大器
LED
PS表示电源 7.5(KW)表示
额定功率
订货号购买 备件时使用
CXA2A 跨接电缆 +24V
CXA2D 控制电源+24V
BA
4
3 2
+
1
_
αi-B电源模块硬件连接
动力电
依据电磁接触 器电压选择
伺服主轴硬件连接
1 αi-B&βi-B伺服概述 2 αi-B电源模块硬件连接 3 αi-B主轴放大器硬件连接 4 αi-B伺服放大器硬件连接 5 αi-B放大器整体连接 6 βi-B放大器硬件连接
1 αi-B&βi-B伺服概述
αi-B&βi-B伺服概述
αi&βi伺服概述
FANUC AC SERVO MOTOR αi-B SERIES
(3) CX3 (1)
3 2 1
电磁接触器线圈
DC LINK 直流300V
LED警示灯
CX3 MCC 接口
200V 三相 交流电
电磁接触器 触点
αi-B电源模块硬件连接
放大器急停
CX4 放大器急停
24V(A1) 24V(B1) 0V(A2)
0V(B2) MIFA(A3) BATL(B3) *ESP(A4) XMIFA(B4)
CX37 重力轴断电检测 (可有效防止重例轴下落)
①/②/③与 L1/L2/L3 需一一对应
3 2 1
CX48 电源监控接口
3 αi-B伺服放大器硬件连接
αi-B伺服放大器硬件连接
伺服放大器硬件连接
主轴变频器连接手动控制调试和外部控制调试过程
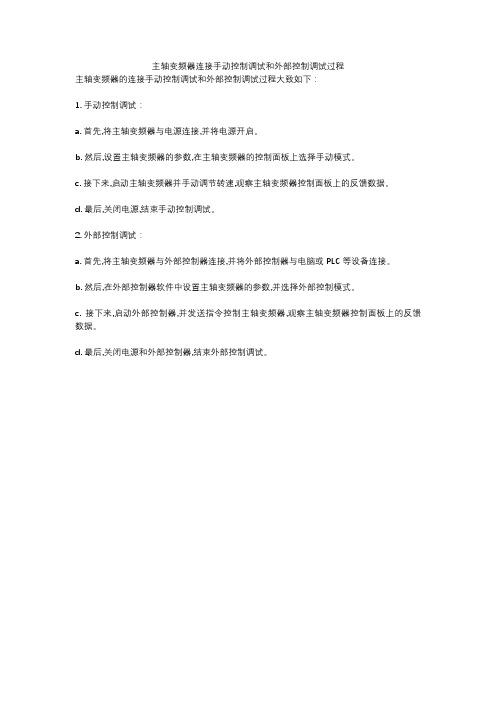
主轴变频器连接手动控制调试和外部控制调试过程
主轴变频器的连接手动控制调试和外部控制调试过程大致如下:
1. 手动控制调试:
a. 首先,将主轴变频器与电源连接,并将电源开启。
b. 然后,设置主轴变频器的参数,在主轴变频器的控制面板上选择手动模式。
c. 接下来,启动主轴变频器并手动调节转速,观察主轴变频器控制面板上的反馈数据。
d. 最后,关闭电源,结束手动控制调试。
2. 外部控制调试:
a. 首先,将主轴变频器与外部控制器连接,并将外部控制器与电脑或PLC等设备连接。
b. 然后,在外部控制器软件中设置主轴变频器的参数,并选择外部控制模式。
c. 接下来,启动外部控制器,并发送指令控制主轴变频器,观察主轴变频器控制面板上的反馈数据。
d. 最后,关闭电源和外部控制器,结束外部控制调试。
- 1、下载文档前请自行甄别文档内容的完整性,平台不提供额外的编辑、内容补充、找答案等附加服务。
- 2、"仅部分预览"的文档,不可在线预览部分如存在完整性等问题,可反馈申请退款(可完整预览的文档不适用该条件!)。
- 3、如文档侵犯您的权益,请联系客服反馈,我们会尽快为您处理(人工客服工作时间:9:00-18:30)。
一、 主轴伺服系统的组成、分类 二、 CNC装置与主轴驱动装置的信号连接 三、 主轴分段无级调速的控制 四、 主轴准停控制
4:主轴驱动系统的连接与测试
一、 主轴伺服系统的组成、分类
1.概念
主轴驱动系统也叫主传动系统,是在系统中完成主运动的动力装置 部分。主轴驱动系统通过该传动机构转变成主轴上安装的刀具或工 件的切削力矩和切削速度,配合进给运动,加工出理想的零件。它 是零件加工的成型运动之一,它的精度对零件的加工精度有较大的 影响。
图 三菱FR-A500系列 变频器接口
二、 CNC装置与主轴驱动装置的信号连接
3.交流主轴伺服驱动的原理 4.主轴转速的指定信号及开关量 控制信号的连接
速度指令
1
速 度 反 馈
3.交流主轴伺服控制原理的框图
3
89
U
பைடு நூலகம்
2 Ur 4
5
脉 冲 误振 差幅
CPU 6
V 7
10
UV ROM CW CCW
U UU V VV
(2)交流驱动系统
采用数字式矢量控制方法,控制模型和动态响应均由高速 微处理器实时控制,使伺服系统的自诊断能力、快速反应及控 制精度都有很大的提高。
二、 CNC装置与主轴驱动装置的信号连接
早期——直流主轴驱动系统(采用晶闸管调速) 20世纪90年代初——变频器驱动; 目前——交流主轴伺服系统时代,主流为全数字 交流主轴伺服系统。
16-微分回路
17-F/V变换器 18-同步整流电路
4.主轴转速的指定信号及开关量控制信号的连接
CNC通过主轴模拟电压输出接口,输出 0~±10V模拟电压到NCOM端和0端(1CN 接口的3、4端),电压正负控制电动机 的转向,电压的大小控制电动机的转速。
若CNC输出的电压为单极性0~+10V,
则可通过FORWARD RUN(8号端)与 REVERS RUN(9号端)开关量分别指定 正、反转
1)准备好信号RDY 2)急停信号EMG 3)正反转信号FOR、REV 4)转矩高低极限控制信号TLH、TLL 5)软起动信号SSC 6)速度调节器选择信号PPI 7)速度设定方式信号DAS 8)零速输出信号ZSPD……
5.实例:FANUC 0i系统对交流主轴驱动的 控制
(1)模拟主轴伺服的控制 模拟主轴控制即为传统的模拟量
一、任务引入
2.磁传感器准停
在主轴上安装磁 装置。在对应的部位 装检测装置。也是早 期使用,功能单一。
3.编码器准停: 在主轴上安装编码器。准停角由调节控制电路板上的拨码开关来实现。
4、 数控系统准停: 主轴上装编码器、系统将主轴作为位置轴来进行控制。
可以控制其停在任意角度、可通过指令来指令其停止角度。
任务4:主轴驱动系统的连接与测试
2CN端子
D1 D2 D3 D4 D5 D6 D7 D8 D9 D10 D11 D12
BIN
1 2 4 8 16 32 64 128 256 512 1024 2048
BPC 3-DIGIT
1 2 4 8 10 20 40 80 100 200 400 800
(BCD码) 2-DIGIT
1 2 4 8 10 20 40 80
控制,从CNC单元输出0~10V的模拟电压 控制主轴电动机的转速及转向,其中转 向控制由相应的参数决定。
(2)模拟主轴控制连接图
SPDL-1(JA7A)
A-OUT1(JA8A) CNC(主板)
位置编码器反馈信号(A/B/Z相) 位置编码器
模拟信号
模拟主轴 放大器
主轴 电机
从CNC单元输出0~10V的模拟电压控制主轴电动机的转速 及转向,其中转向控制由相应的参数决定。
W WW 11 12 13
M 3~
14
17 15
大于40r/min 1024脉冲/r
18 16
0~40r/min
1-比例积分回路 2-绝对值回路 3-负载表 4-函数发生器 5-V/F变换器 6-微处理器 7-DA强励磁 8-DA振幅器 9-乘法器 10-电流指令回路 11-电流控制回路
12-PWM控制回路 13-PWM变换器 14-脉冲发生器 15-四倍回路
二、 CNC装置与主轴驱动装置的信号连接
1.变频器控制方式的发展: 电压矢量控制——磁通矢量控制—
—直接转矩控制——采用通用变频器。 “通用”:
(1)可以和通用的笼型异步电动机 配套应用;
(2)具有多种可供选择的功能,可 应用于不同性质的负载。
二、 CNC装置与主轴驱动装置的信号连接
2.实例:三菱FR—A50系列主回路端子和控制回 路端子如图所示 (1)输入信号(用于起动和功能设定) (2)模拟信号(用于频率设定) (3)输出信号
4分类
按电气原理分为: (1)直流控制驱动 (2)交流控制驱动
1)直流驱动系统
20世纪70年代~90年代中期)直流伺服电动机 优点:
调速性能好、输出力矩大、过载能力强、控制精度高、控 制原理简单、易于调整等。 缺点:
由于电刷和换向器易磨损,需经常维护; 换向器换向时会产生火花,最高速度受到限制; 具有结构复杂、制造困难、制造成本高等缺点
小结
CNC数控装置对主轴驱动装置的控制包括主轴的速度控制和其他 开关量的动作控制。安川YASKAWA VS-626MT的连接图
开关量控 制信号及
连接
模拟电 压指定
数字电 压指定
输出信 号
安川YASKAWA VS-626MT连接
图
三、 主轴分段无级调速的控制
分段无级调速是数控机床常采用 1~4挡齿轮变速与无级调速
相结合的方式,即分段无级变速。低速时为恒转矩,当需要低速 强力切削时需要提高其转矩。措施是通过换挡,降低主轴速度, 增大转矩。
四、 主轴准停控制
主轴准停是指能主轴按指令要求准确停在指定换刀位置,也称作主轴 定向。其作用:换刀和镗孔时定向、确定反向退刀方向。
四、 主轴准停控制
1.机械准停
早期的机床使 用,现在很少使 用。但高速时动 平衡不好,调试 不方便。
一、 主轴伺服系统的组成、分类
2.数控机床对主轴驱动系统的要求
1、调速范围宽并实现无极调速 2、恒功率范围要宽 3、具有4象限驱动能力 4、具有位置控制能力 5、具有较高的精度与刚度,传动平稳,噪音低。 6、良好的抗振性和热稳定性
3.组成
1 主轴驱动系统 2 主轴驱动单元 3 传动单元 4 执行单元