防错 防呆管理办法
生产一线如何做到防错防呆管理讲义
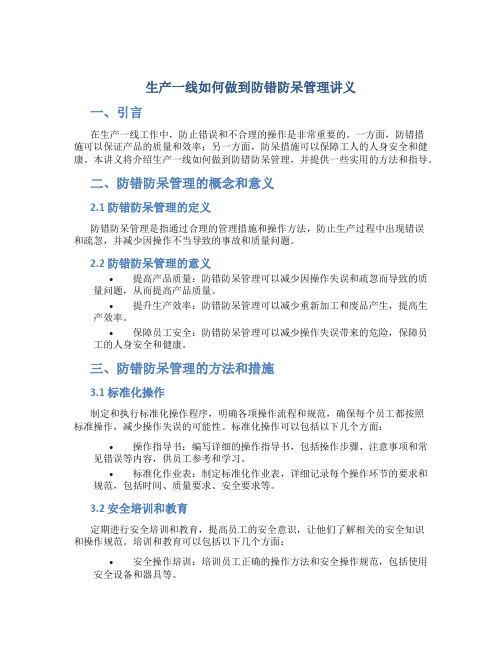
生产一线如何做到防错防呆管理讲义一、引言在生产一线工作中,防止错误和不合理的操作是非常重要的。
一方面,防错措施可以保证产品的质量和效率;另一方面,防呆措施可以保障工人的人身安全和健康。
本讲义将介绍生产一线如何做到防错防呆管理,并提供一些实用的方法和指导。
二、防错防呆管理的概念和意义2.1 防错防呆管理的定义防错防呆管理是指通过合理的管理措施和操作方法,防止生产过程中出现错误和疏忽,并减少因操作不当导致的事故和质量问题。
2.2 防错防呆管理的意义•提高产品质量:防错防呆管理可以减少因操作失误和疏忽而导致的质量问题,从而提高产品质量。
•提升生产效率:防错防呆管理可以减少重新加工和废品产生,提高生产效率。
•保障员工安全:防错防呆管理可以减少操作失误带来的危险,保障员工的人身安全和健康。
三、防错防呆管理的方法和措施3.1 标准化操作制定和执行标准化操作程序,明确各项操作流程和规范,确保每个员工都按照标准操作,减少操作失误的可能性。
标准化操作可以包括以下几个方面:•操作指导书:编写详细的操作指导书,包括操作步骤、注意事项和常见错误等内容,供员工参考和学习。
•标准化作业表:制定标准化作业表,详细记录每个操作环节的要求和规范,包括时间、质量要求、安全要求等。
3.2 安全培训和教育定期进行安全培训和教育,提高员工的安全意识,让他们了解相关的安全知识和操作规范。
培训和教育可以包括以下几个方面:•安全操作培训:培训员工正确的操作方法和安全操作规范,包括使用安全设备和器具等。
•安全意识培养:开展安全知识讲座、演练和案例分析,提高员工的安全意识和应对突发事件的能力。
3.3 检查和核查建立有效的检查制度,定期对生产过程中的操作进行检查和核查,发现问题及时纠正。
检查和核查可以包括以下几个方面:•自检:要求每个员工自行对自己的操作进行检查,确保操作的正确性和合理性。
•互检:员工之间相互检查和核查,发现问题及时纠正,确保操作的准确性。
防错、防呆管理办法

防错、防呆管理办法线路等设施要定期检查维护,确保操作员的安全。
5.1.3设备、工装夹具等方面,要进行定期检查维护,确保设备的正常运转,避免因设备故障而造成的生产中断及不良品产生。
5.2生产部、各车间要对生产过程中的防呆、防误、防错措施进行评估,并在必要的制程中,安装防呆、防误、防错设施,确保操作员的安全,避免不良品的产生。
5.2.1原材料、半成品、成品的防呆、防误、防错措施的提出与实施,要做到及时、准确,确保产品质量。
5.2.2针对半成品及成品多发异常或重大不良进行检讨,会同相关部门制订防呆、防误、防错设施,确保产品质量的稳定性。
5.3品质部要对防呆、防误、防错措施的实施效果进行验证,并跟踪标准化的完成,确保生产过程的质量稳定性。
本文旨在建立适当的错误防止法,防止因疏忽所造成的不良发生,提高生产效益,降低制造成本,满足顾客需求。
针对生产过程中的设施、设备、工装夹具等方面,制订防呆、防误、防错措施,并进行评估和改善。
工程部负责生产过程的策划和设施、设备、工装夹具等方面的防呆、防误、防错措施制订和指导实施及改善。
生产部、各车间负责防呆、防误、防错设施的实施和管理,确保产品质量。
品质部验证实施效果,并跟踪标准化的完成,确保生产过程的质量稳定性。
自动化生产,减少人为失误的可能性。
5.6.3工艺方面:对每一个工序进行详细的规范化操作流程制定,并在生产过程中进行严格的执行和监督,确保每一个环节都符合标准要求。
5.6.4管理方面:建立完善的质量管理体系,包括自检、互检、点检、巡检等多种品质控制方法,确保每一个细节都能够得到有效的监控和纠正,杜绝失误的发生。
5.7防错效果的评估和持续改进:5.7.1对防错措施的实施效果进行定期的评估和监控,及时发现和解决存在的问题。
并采取相应的改进措施。
5.7.2通过对失误原因的分析和总结,不断完善防错措施,提高生产效率和品质水平。
实现持续改进的目标。
在生产过程中,智能化和个性化的治具和夹具被广泛使用。
防呆管理方法
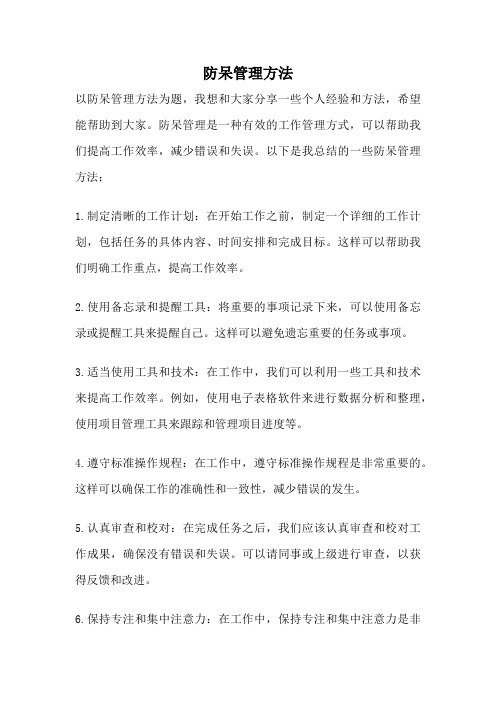
防呆管理方法以防呆管理方法为题,我想和大家分享一些个人经验和方法,希望能帮助到大家。
防呆管理是一种有效的工作管理方式,可以帮助我们提高工作效率,减少错误和失误。
以下是我总结的一些防呆管理方法:1.制定清晰的工作计划:在开始工作之前,制定一个详细的工作计划,包括任务的具体内容、时间安排和完成目标。
这样可以帮助我们明确工作重点,提高工作效率。
2.使用备忘录和提醒工具:将重要的事项记录下来,可以使用备忘录或提醒工具来提醒自己。
这样可以避免遗忘重要的任务或事项。
3.适当使用工具和技术:在工作中,我们可以利用一些工具和技术来提高工作效率。
例如,使用电子表格软件来进行数据分析和整理,使用项目管理工具来跟踪和管理项目进度等。
4.遵守标准操作规程:在工作中,遵守标准操作规程是非常重要的。
这样可以确保工作的准确性和一致性,减少错误的发生。
5.认真审查和校对:在完成任务之后,我们应该认真审查和校对工作成果,确保没有错误和失误。
可以请同事或上级进行审查,以获得反馈和改进。
6.保持专注和集中注意力:在工作中,保持专注和集中注意力是非常重要的。
避免分心和注意力不集中,可以减少错误的发生。
7.学会借鉴他人经验:在工作中,我们可以学会借鉴他人的经验和方法。
可以请教有经验的同事或上级,学习他们的工作方式和管理方法。
8.不断学习和提升自己:防呆管理是一种能力和技巧,需要不断学习和提升。
我们可以通过读书、培训和实践来提高自己的防呆管理能力。
以上是我总结的一些防呆管理方法,希望对大家有所帮助。
通过合理运用这些方法,我们可以提高工作效率,减少错误和失误,实现更好的工作成果。
希望大家都能成为优秀的防呆管理者,为工作的顺利进行做出贡献。
谢谢大家!。
防呆防错十种方法

6、隔离原理 隔离原理:用分隔不同区域的方式,来达到保护某些地区,使不能造成危险或错误的现象发生。隔离原理亦称保护原理。如将坏人抓入监狱、将不良品隔开等。
7、复制原理 复制原理:同一件工作,如需做二次以上,最好采用“复制”方式来达成,省时又不错误。一般以拓印、口诵、复写、复诵等方式来防错。
4、相符原理 相符原理:用检核是否相符合的动作,来防止错误的发生。一般依形状的不同、符号指示、数量指示、声音等方式来防错。
例ห้องสมุดไป่ตู้开刀手术前后必须点核数量有否符合,以免有工具遗留在人体内,忘了拿出来。
5、顺序原理 顺序原理:避免工作顺序或流程前后倒置,可依编号顺序排列,可以减少或避免错误的发生。一般以编号、斜线等方式来防错。
例:焊装焊件时会口诵:“一检(来料)、二放(零件)、三按(夹具按钮)、四打(点)、五松(夹具)、六取(零件)、七放(到零件存放区)。
8、层别原理 层别原理:为避免将不同的工作做错,而设法加以区别出来。一般以线条之粗细、不同的颜色来代表不同的意义来防错。
例:将不良品挂上“红色”标贴,将危险区域用“黄色”画上,将人行通道刷为“绿色”。
正宗精益生产学习平台
1.精益论坛:
2.加QQ群:精益生产促进中心(群号:564229307)
注:加群回复我是益友
3.加微信群:后台回复您的所在城市-姓名-职务-公司全称-微信号
9、警告原理 警告原理:如有不正常的现象发生,能以声光或其他方式显示出各种“警告”的讯号,以避免错误的即将发生。
例:车子速度过高时,警告灯就亮了。
10、缓和原理 缓和原理:用各种方法来减少错误发生后所造成的损害,虽然不能完全排除错误的发生,但是可发降低其损害程度。
防错、防愚笨管理办法

防错、防愚笨管理办法1. 强调培训与教育- 提供全面的培训计划,包括规章制度、操作流程、安全注意事项等内容。
- 鼓励员工参加专业培训和技能提升课程,以提高他们的工作能力和专业素养。
- 定期组织各种培训活动,以增强员工的意识和技能。
2. 设立检查与审查机制- 建立定期的检查机制,对操作过程和执行结果进行审查,及时发现和纠正错误。
- 设立明确的责任分工,明确各个环节的责任人和监督者,确保每个环节的正确执行。
- 运用科技手段,如监控摄像头、智能感知技术等,对关键环节进行监控和检测。
3. 规范操作流程- 制定详细的操作流程和标准操作规范,确保操作过程的一致性和可追溯性。
- 强调标准化操作,避免个人主观因素的干扰,减少错误发生的可能性。
- 定期对操作流程进行评估和改进,以适应业务发展和技术进步的需要。
4. 加强沟通与协作- 鼓励员工之间的沟通和交流,提高团队协作和问题解决能力。
- 建立有效的信息共享机制,确保相关信息的及时传递和反馈。
- 把握好上下级之间、部门之间和同事之间的沟通方式和频率,避免信息滞后和误解。
5. 鼓励反馈与改进- 鼓励员工提出问题和改进意见,及时采纳和处理反馈。
- 建立有效的错误管理机制,及时记录和分析错误的原因和影响,采取措施防止类似错误再次发生。
- 注重持续改进,通过总结经验教训,完善管理办法和流程。
6. 营造宽松的工作氛围- 营造积极向上、相互尊重、自由开放的工作氛围,鼓励员工敢于提问和创新。
- 建立有效的奖励与激励机制,给予优秀表现和有创意的员工相应的奖励和认可。
- 提供良好的工作条件和员工福利,增强员工对组织的归属感和忠诚度。
这些防错、防愚笨的管理办法可以帮助组织提高工作效率,减少错误和损失,建立良好的工作环境和企业形象。
请注意,以上内容仅供参考,具体的实施措施需要根据组织的实际情况进行调整和补充。
生产一线如何做到防错防呆管理

总结与展望
01
总结防错防呆管理的成果和经验教训
成果:提高了生产效率,降低了错误率
建议:加强员工培训,提高员工素质
展望:未来将继续推广防错防呆管理,提高生产质量
经验教训:需要持续改进,不断优化流程
分析存在的问题和不足,提出改进措施和建议
信息化:利用信息化手段,实现生产数据的实时采集和分析,提高生产过程的透明度和可控性
绿色化:注重环境保护和资源节约,实现绿色生产,降低生产成本和环境污染
人性化:关注员工需求和职业发展,提高员工满意度和忠诚度,实现企业和员工的共同发展
学院
汇报人:
感谢观看
物料短缺:物料短缺导致生产进度延误,影响生产效率
设备维护不当导致的故障
设备保养不及时,导致设备性能下降
设备操作不当,导致设备损坏
设备维修不及时,导致设备故障
设备使用不当,导致设备寿命缩短
人为因素导致的安全事故
操作失误:员工操作不当,导致设备损坏或人员受伤
安全意识薄弱:员工忽视安全规定,导致事故发生
定期检查实施计划的执行情况,及时调整计划和时间表
建立监督机制,确保实施计划的执行和监督的有效性
加强过程监督和检查,及时发现问题并整改
建立完善的监督和检查制度,明确责任分工
定期对生产一线进行巡查,确保生产流程的规范性和安全性
对发现的问题进行记录和分析,制定整改措施
对整改措施进行跟踪和评估,确保问题得到有效解决
防错防呆管理可以降低生产过程中的安全隐患,保障生产安全
防错防呆管理可以降低生产过程中的错误率,提高生产效率
防错防呆管理可以减少生产过程中的浪费,降低生产成本
仓库防呆防错措施方案

仓库防呆防错措施方案仓库是一个非常重要的环节,它承载着物品的储存和管理任务。
由于仓库通常容纳着大量的物品,一旦出现问题,可能会造成严重的损失。
因此,采取一系列的防呆防错措施是非常必要的。
首先,仓库的布局设计是关键。
合理的仓库布局可以提高工作效率,减少错误发生的可能性。
仓库的布局应该根据物品的特性和储存方式进行规划,不同类型的物品要分开储存,并且设置明确的标识。
货架和储存单元要安排合理,以便于物品的存取和管理。
同时,通道和操作区域要保持畅通,避免堆积物品导致阻塞或者意外事故的发生。
其次,员工培训是防呆防错的关键。
仓库工作人员需要具备一定的专业知识和操作技能,熟悉仓库的各项规定和操作流程。
通过培训,可以提高员工对物品特性和存放要求的了解,增强其辨别和处理问题的能力。
此外,培训内容还可以包括应急处理措施和事故防范知识,以应对突发情况的发生。
第三,信息化管理系统的应用是提高仓库管理效率和防呆防错的重要手段。
借助信息化系统,仓库管理人员可以实时掌握物品的存储和出入库情况,减少人为错误的发生。
通过扫描物品条码和使用RFID等技术,可以实现对物品的全程监控和追踪,减少误操作和遗漏。
同时,信息化系统还可以提供库存预警和定期盘点等功能,及时发现问题并采取有效措施。
此外,仓库还要加强货物质量检验和封装保护。
在物品进入仓库之前,应该严格按照规定的程序检查物品的质量和数量,以免质量问题或者缺失导致后续问题。
对于易损物品、易腐物品等特殊物品,要给予额外的保护措施,防止损坏和污染。
同时,要保证货物的包装符合要求,以提供良好的防护和存储环境。
此外,仓库还要制定完善的安全规章制度和操作规程。
这些规章制度和操作规程应该包括仓库设备的使用方法和维护要求、库区的管理要求、货物存放和出库的操作流程等内容。
所有工作人员都必须遵守这些规章制度和操作规程,不得擅自安排和变更工作流程,减少由于操作不当导致的错误和事故。
最后,仓库管理人员要加强对仓库工作的监督和检查。
防呆防错的8种方法

防呆防错是提高质量、减少不良事件的关键技术,它以改进人们的思考、行为和操作方式来减少出现错误的可能性。
下面就介绍8种防呆防错的方法:
一、拆分工序:将一个复杂的工作过程拆分成若干个单独的工序,每个工序只完成一个简单的任务,每一步都要经过审查,以确保每一步都没有出现错误。
二、强化审查:安排一位能够比较熟悉操作程序的人来审查被操作者的工作,以确保操作者按照程序要求完成工作,避免出现错误。
三、定期审查:定期审查操作者的工作,对可能出现的错误进行及时发现,以便及时纠正。
四、重复检查:对所做的一系列操作,进行重复检查,确保其中没有出现错误。
五、标准化操作:对操作过程中数据的输入、输出、处理等建立标准,以减少出现错误的可能性。
六、安装报警系统:在操作过程中,通过安装报警系统,及时发现错误,以便及时纠正。
七、进行培训:定期进行各种技能和知识的培训,使操作者具有更强的技能和知识,以便及时发现错误,提高工作效率。
八、实施质量体系:建立一套完整的质量管理体系,建立严格的工作流程,对工作过程进行监控,对可能出现的错误进行及时发现,以便及时纠正。
以上就是8种防呆防错的方法,采用这些方法可以有效减少出错的可能性,提高工作效率,保证质量。
- 1、下载文档前请自行甄别文档内容的完整性,平台不提供额外的编辑、内容补充、找答案等附加服务。
- 2、"仅部分预览"的文档,不可在线预览部分如存在完整性等问题,可反馈申请退款(可完整预览的文档不适用该条件!)。
- 3、如文档侵犯您的权益,请联系客服反馈,我们会尽快为您处理(人工客服工作时间:9:00-18:30)。
中山市诚泰金属有限公司防错、防呆管理办法编制:
审核:
批准:
文件发行/更改审批表
1、目的和范围﹕
为改善产品的不良,建立适当错误防止法,使其能够达到预防因疏忽所造成的不良发生,发现异常立即反馈,
使浪费及损失降至最低,从而激发员工的士气,提升生产力,降低制造成本,满足顾客需求,特制订本程序。
2、适用范围
2.1本司生产过程的策划,设施、设备、工装夹具的防呆、防误、防错措施实施与管理。
2.2避免人员受伤,强化工作的安全,防止不良品产生,避免机器损坏。
3、职责
3.1工程部:生产过程的策划及对设施、设备、工装夹具等方面,制订防呆、防误、防错措施及改善。
3.2生产部、各车间:评估并在必要的制程中,安装防呆、防误、防错设施,对防呆、防误、防错措施制订的提出、
实施与管理;负责对原材料、半成品、成品的防呆、防误、防错措施的提出与实施,并在实际作业中持续改进;
针对半成品及成品多发异常或重大不良进行检讨,会同相关部门制订防呆、防误、防错设施。
3.3品质部:验证实施效果,并跟踪标准化的完成。
4、定义:
4.1防呆法:不需要特别注意力、经验与直觉、专业知识与技能,通过采取措施,防止出现呆的状态,确保生产运
作环节顺畅。
4.2防误法:防止操作员在作业过程中由于此操作的失误而影响彼此环节或产生后果。
4.3防错法:防止操作员在作业过程中由于各种原因造成错误操作并产生后果。
5.0程序细则:
5.1工程部根据产品工艺要求,对生产过程进行策划,为确保安全,避免机器损坏,生产产品品质得以控制,提高
生产效益,生产过程所涉及到的设施、设备、工装夹具等方面,进行防呆、防误、防错措施制订与指导实施及改善,从技术能力方面做出评估,完成改进或制作作业,以逐步提高设备的自动化程度,达到减少人为或设备因素所造成的不良,并负责标准化工作。
5.1.1制订工艺流程图,编制工序布局图,以防生产环节遗漏、工序衔接不紧凑。
5.1.2在安全生产方面,冲床加工开关设置双按钮;下料切割加挡板,电动机、电源开关安置过载保护、漏电保护装
置;温度控制器安装保报警器等防错设施。
5.1.3在提高生产效益,确保品质方面:切割长度加工设置定位器;光孔及螺纹孔加工,使用通止规、针规、深度尺、螺纹规控制加工精度;焊接为防错位、变形,设置专用焊接夹具,利用专用检具检测及校正;焊接各项工艺参数在首件生产时就确认好,并锁定不变;弯管加工,设置专用夹具,并用专用检具检测及校正。
专用平面及小工件抛光加工时,设置夹具将工件成组固定加工。
设置自检、互检、点检、巡检品质控制方法,做到全员参与、人人品管。
5.1.4突出“5S”管理中的“目视管理”,将物料标示、检验状态标示,与所处区域行成一一对应,以免混淆;不良品规定放置在“不良品”标示的红色物料框内,以免流入下道工序。
5.1.5防错装:将相类似的零件进行样板标示,并标出不同之处,放置作业工位;相类似的零件放置再不同的盒内、标示;装配相类似的零件加工工序,尽可分为二道以上工序,不要重叠在一道工序,杜绝错装隐患。
5.1.3防漏装:未生产之前,每工序将所用物料点齐并记录,完成规定的装配数量后,将每工序所用物料清点数量对比,确认是否漏装。
5.2生产部、各车间根据产品工艺及品质要求,对所有工序进行审核确认,提出任何防呆、防误、防错措施的需求,并在生产中确认措施是否能起到预期的作用。
5.3品质部跟踪措施实施的整个过程,并确认效果、反馈、再确认及监督标准化作业实施。
5.4常见失误:
5.4.1制程中常见失误:漏掉某个作业步骤、作业失误、工件设置错误、缺件、用错部品、工件加工错误、误操作、
调整失误、设备参数设置不当、工装夹具准备不当。
5.4.2交易过程常见失误有以下几类:文件中漏掉重要信息、文件中存在错误信息、文件中存在与该交易无关的重要
信息。
5.5工作中产生失误的原因:
5.5.1人为原因:忘记、疏忽、行动迟缓、对过程/作业不熟悉、缺乏工作经验、故意失误、交易过程失误。
5.5.2其它因素:缺乏适当的现场作业指导书、机器设备突发故障。
5.6有效防错措施的实施:
5.6.1人员方面:进行多层次“三防”(防呆、防误、防错)培训教育,从入职开始就先在思想上进行灌输,强化认识,
塑造观念,为以后充分发挥防错奠定了基础。
5.6.2机器方面:关注机械功能和操作可靠性,改造不适宜的机器设备,尽可能实现智能化,并大量使用各种个性化
的治具和夹具。
5.6.3材料方面:深层次识别材料性能,掌握其理化特性,严格按手性的流程实施管理,把库存看作浪费,确保均衡
化,并努力减少车间的半成品
5.6.4方法方面:流程化管理,精细化控制,定点检验,样板示范,确保全部作业过程规范化、标准化;
5.6.5环境方面:因人而异,区别产品和过程,全面推进“5S”,创造优良的工作环境,努力用和谐的现场营造和谐的
气氛,尽可能消除产生各种错误的外因。
5.6.6技术层面的措施“自动化检测、自动化报警、自动化停机”。
5.6.7管理层面的措施:
5.6.7.1工具在规定的时间内用完后必须放回原处,否则,警铃会响;
5.6.7.2存放物品的盒子会按设置程序依次打开,想拿错是不可能的;
5.6.7.3电眼(感应器)可以全数检验关键器件的状态;
5.6.7.4限位开关能确保准确定位;
5.6.7.5均衡化生产,把半成品的数量减少到最低;
5.6.7.6培训人员,使他们转变观念,都能够按标准化规则进行作业。
5.7防止错误的手段:
5.7.1提醒装置:一旦发生异常,就会通过蜂鸣器的声音和红色的灯光发出信号,提醒操作人员注意的方式。
5.7.2纠错装置:一旦发生异常,就会自动停止机械和生产线,无法继续工作的方式。
5.8防错装置的种类:导轨、模板、微动开关、计数器、顺序限制、标准化、指示装置、制止器、感应开关、设计
对称、设计非对称、条件设定(选择)等。
6.0应用表单:无。
5、引用文件
无
6、运作流程及乌龟图
无
7、运作流程清单
无。