蒸氨法氨回收工艺及装置简介
蒸氨塔氨气分缩器结构-概述说明以及解释
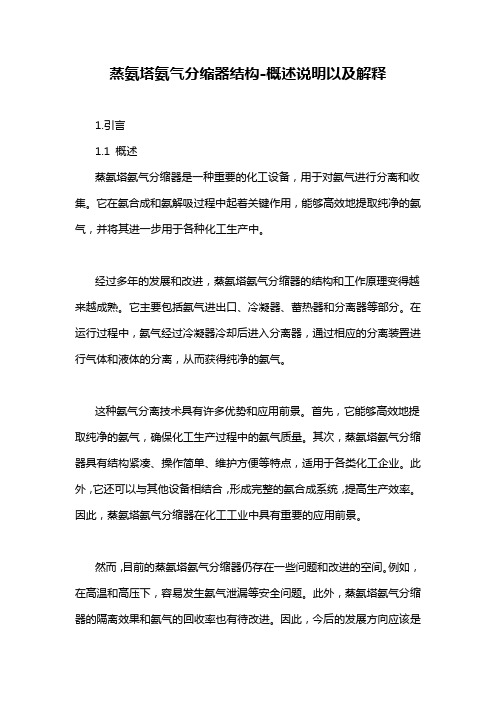
蒸氨塔氨气分缩器结构-概述说明以及解释1.引言1.1 概述蒸氨塔氨气分缩器是一种重要的化工设备,用于对氨气进行分离和收集。
它在氨合成和氨解吸过程中起着关键作用,能够高效地提取纯净的氨气,并将其进一步用于各种化工生产中。
经过多年的发展和改进,蒸氨塔氨气分缩器的结构和工作原理变得越来越成熟。
它主要包括氨气进出口、冷凝器、蓄热器和分离器等部分。
在运行过程中,氨气经过冷凝器冷却后进入分离器,通过相应的分离装置进行气体和液体的分离,从而获得纯净的氨气。
这种氨气分离技术具有许多优势和应用前景。
首先,它能够高效地提取纯净的氨气,确保化工生产过程中的氨气质量。
其次,蒸氨塔氨气分缩器具有结构紧凑、操作简单、维护方便等特点,适用于各类化工企业。
此外,它还可以与其他设备相结合,形成完整的氨合成系统,提高生产效率。
因此,蒸氨塔氨气分缩器在化工工业中具有重要的应用前景。
然而,目前的蒸氨塔氨气分缩器仍存在一些问题和改进的空间。
例如,在高温和高压下,容易发生氨气泄漏等安全问题。
此外,蒸氨塔氨气分缩器的隔离效果和氨气的回收率也有待改进。
因此,今后的发展方向应该是进一步优化设备结构,提高工作效率和安全性。
总之,蒸氨塔氨气分缩器具有广阔的应用前景和优势,能够提供高质量的氨气供应。
随着技术的不断发展和改进,相信蒸氨塔氨气分缩器将在化工工业中扮演更加重要的角色,并为相关企业带来更大的经济效益和发展空间。
1.2文章结构文章结构部分的内容如下:1.2 文章结构本文将围绕蒸氨塔氨气分缩器的结构展开介绍,分为以下几个方面进行阐述。
首先,我们将对蒸氨塔氨气分缩器的定义和作用进行概述。
在这一部分,将详细说明蒸氨塔氨气分缩器在化工领域中的重要性和应用场景,并探讨其在工业生产中的作用和意义。
通过介绍定义和作用,我们可以更好地理解蒸氨塔氨气分缩器的结构和工作原理。
接下来,我们将重点介绍蒸氨塔氨气分缩器的结构和工作原理。
将详细描述蒸氨塔氨气分缩器的构成部件、各部分之间的关联以及它们的功能和作用。
氨氮废水热泵汽提脱氨,氨氮废水蒸氨精馏处理设备
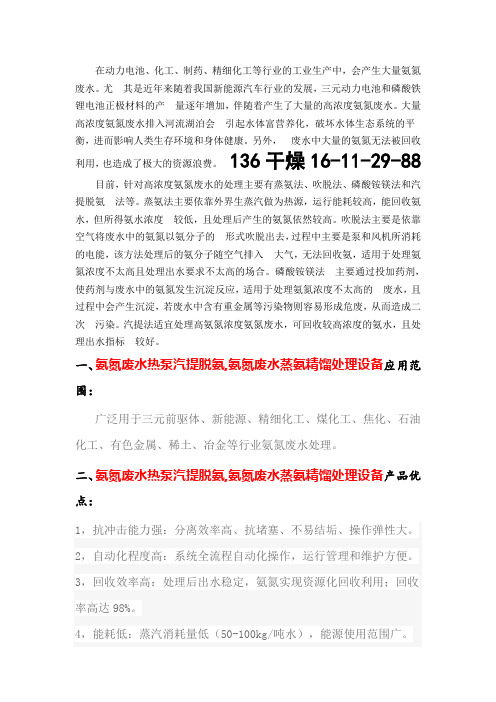
在动力电池、化工、制药、精细化工等行业的工业生产中,会产生大量氨氮废水。
尤其是近年来随着我国新能源汽车行业的发展,三元动力电池和磷酸铁锂电池正极材料的产量逐年增加,伴随着产生了大量的高浓度氨氮废水。
大量高浓度氨氮废水排入河流湖泊会引起水体富营养化,破坏水体生态系统的平衡,进而影响人类生存环境和身体健康。
另外,废水中大量的氨氮无法被回收利用,也造成了极大的资源浪费。
136干燥16-11-29-88目前,针对高浓度氨氮废水的处理主要有蒸氨法、吹脱法、磷酸铵镁法和汽提脱氨法等。
蒸氨法主要依靠外界生蒸汽做为热源,运行能耗较高,能回收氨水,但所得氨水浓度较低,且处理后产生的氨氮依然较高。
吹脱法主要是依靠空气将废水中的氨氮以氨分子的形式吹脱出去,过程中主要是泵和风机所消耗的电能,该方法处理后的氨分子随空气排入大气,无法回收氨,适用于处理氨氮浓度不太高且处理出水要求不太高的场合。
磷酸铵镁法主要通过投加药剂,使药剂与废水中的氨氮发生沉淀反应,适用于处理氨氮浓度不太高的废水,且过程中会产生沉淀,若废水中含有重金属等污染物则容易形成危废,从而造成二次污染。
汽提法适宜处理高氨氮浓度氨氮废水,可回收较高浓度的氨水,且处理出水指标较好。
一、氨氮废水热泵汽提脱氨,氨氮废水蒸氨精馏处理设备应用范围:广泛用于三元前驱体、新能源、精细化工、煤化工、焦化、石油化工、有色金属、稀土、冶金等行业氨氮废水处理。
二、氨氮废水热泵汽提脱氨,氨氮废水蒸氨精馏处理设备产品优点:1,抗冲击能力强:分离效率高、抗堵塞、不易结垢、操作弹性大。
2,自动化程度高:系统全流程自动化操作,运行管理和维护方便。
3,回收效率高:处理后出水稳定,氨氮实现资源化回收利用;回收率高达98%。
4,能耗低:蒸汽消耗量低(50-100kg/吨水),能源使用范围广。
5,操作简单:工艺流程简单,占地面积小,建设工期短;投资费用少。
三、精馏脱氨塔,脱氨精馏塔,氨氮废水蒸氨处理设备工艺路线;氨氮废水热泵汽提脱氨系统,包括有静态混合器、液碱槽,其特征在于:液碱槽经碱液输送泵连通静态混合器,静态混合器的出口经板式换热器连通精馏塔的入口,精馏塔顶部的物料蒸汽出口连通降膜蒸发器的壳程,蒸汽冷凝水罐的出口经冷凝水循环泵连通降膜蒸发器的管程,降膜蒸发器的蒸汽出口经压缩机连通耦合再沸器,耦合再沸器配设于精馏塔底部,精馏塔的重组分出口经重组分排液泵、板式换热器连通斜板沉降池的入口,斜板沉降池的排液口经沉降重组分输送泵连通精密过滤器的入口,精密过滤器的出口连通PH调节釜的入口;降膜蒸发器的物料出口连通缓冲罐的入口,缓冲罐的蒸汽出口连通冷凝器的入口,冷凝器的不凝气出口连通氨气吸收槽,冷凝器的液态物料出口连通缓冲罐的回流口,缓冲罐的液态物料出口经回流泵分别连通成品冷却器和精馏塔。
氨回收分离工艺简介
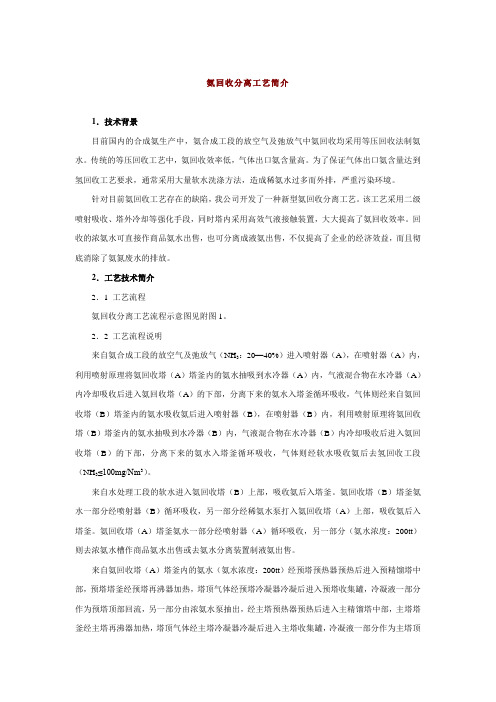
氨回收分离工艺简介1.技术背景目前国内的合成氨生产中,氨合成工段的放空气及弛放气中氨回收均采用等压回收法制氨水。
传统的等压回收工艺中,氨回收效率低,气体出口氨含量高。
为了保证气体出口氨含量达到氢回收工艺要求,通常采用大量软水洗涤方法,造成稀氨水过多而外排,严重污染环境。
针对目前氨回收工艺存在的缺陷,我公司开发了一种新型氨回收分离工艺。
该工艺采用二级喷射吸收、塔外冷却等强化手段,同时塔内采用高效气液接触装置,大大提高了氨回收效率。
回收的浓氨水可直接作商品氨水出售,也可分离成液氨出售,不仅提高了企业的经济效益,而且彻底消除了氨氮废水的排放。
2.工艺技术简介2.1 工艺流程氨回收分离工艺流程示意图见附图1。
2.2 工艺流程说明来自氨合成工段的放空气及弛放气(NH3:20—40%)进入喷射器(A),在喷射器(A)内,利用喷射原理将氨回收塔(A)塔釜内的氨水抽吸到水冷器(A)内,气液混合物在水冷器(A)内冷却吸收后进入氨回收塔(A)的下部,分离下来的氨水入塔釜循环吸收,气体则经来自氨回收塔(B)塔釜内的氨水吸收氨后进入喷射器(B),在喷射器(B)内,利用喷射原理将氨回收塔(B)塔釜内的氨水抽吸到水冷器(B)内,气液混合物在水冷器(B)内冷却吸收后进入氨回收塔(B)的下部,分离下来的氨水入塔釜循环吸收,气体则经软水吸收氨后去氢回收工段(NH3≤100mg/Nm3)。
来自水处理工段的软水进入氨回收塔(B)上部,吸收氨后入塔釜。
氨回收塔(B)塔釜氨水一部分经喷射器(B)循环吸收,另一部分经稀氨水泵打入氨回收塔(A)上部,吸收氨后入塔釜。
氨回收塔(A)塔釜氨水一部分经喷射器(A)循环吸收,另一部分(氨水浓度:200tt)则去浓氨水槽作商品氨水出售或去氨水分离装置制液氨出售。
来自氨回收塔(A)塔釜内的氨水(氨水浓度:200tt)经预塔预热器预热后进入预精馏塔中部,预塔塔釜经预塔再沸器加热,塔顶气体经预塔冷凝器冷凝后进入预塔收集罐,冷凝液一部分作为预塔顶部回流,另一部分由浓氨水泵抽出,经主塔预热器预热后进入主精馏塔中部,主塔塔釜经主塔再沸器加热,塔顶气体经主塔冷凝器冷凝后进入主塔收集罐,冷凝液一部分作为主塔顶部回流,另一部分则去液氨贮槽作商品液氨出售。
硫铵和蒸氨工艺流程简述主要设备工作原理和作用

硫铵和蒸氨工艺流程简述主要设备工作原理和作用一、硫铵工艺简述由脱硫工段送来的煤气,经煤气预热器预热至60--70℃后,进入喷淋式饱和器上段环形喷淋室,在此煤气被分为左右两股,沿饱和器内壁与内除酸器外壁的环形空间,由前室流向后室,并与逆煤气流向密集喷洒的循环母液充分接触。
被吸收除去氨的煤气在后室汇合成一股,并沿切线方向进入饱和器的内除酸器。
在器内经旋风分离除去夹带的酸雾,经饱和器顶部出口,煤气被引出饱和器送往终冷洗苯。
在饱和器下段结晶室上部的母液,用母液循环泵连续抽出送上段喷淋室循环喷洒,吸收煤气中的氨,并循环搅动母液以改善硫铵结晶过程。
饱和器在生产时,母液中不断有硫铵结晶生成,由上段喷淋室的降液管流至下段结晶室的底部,用结晶泵将其连同部分母液送至结晶槽,然后排放至离心机进行离心分离,滤出母液并用温水洗涤结晶,离心机分离母液与结晶槽满流出的母液一并自流回饱和器下段的母液中。
从饱和器满流口溢出的母液通过插入液封槽的满流管流入满流槽,再由满流槽流至母液贮槽,母液贮槽内贮存的母液用小母液泵送至后室喷洒进一步吸收煤气中的氨,油库来的硫酸被送入酸高位槽,再经流量计计量后自流入满流槽。
饱和器定期加酸及用温水冲洗,所形成的大量母液,由满流槽自流至母液贮槽。
由煤气带入母液中的焦油等杂质形成酸焦油,在饱和器上段喷洒室由满流管流入满流槽;饱和器下段结晶室上部的酸焦油,则经酸焦油排出口排出至满流槽,汇集于满流槽液面上的酸焦油,定时人工捞出。
硫酸高置槽设有满流管,当槽内液位超过满流口时,可满流至母液贮槽。
从离心机卸出的硫铵,由螺旋给料机输送至振动流化床干燥机,先被热风干燥,再被冷风降温后进入硫铵贮斗,然后装袋、称量、缝袋、推运至成品库。
干燥机顶部排出的尾气,经旋风分离器分离并回收尾气中夹带的硫铵颗粒之后排至大气。
二、主要设备的工作原理和作用1、喷淋式饱和器的工作原理和作用焦炉煤气在喷淋式饱和器内通过时,受到硫酸的喷淋,煤气中的氨与硫接触而发生反应,生成了中性盐硫酸铵(简称硫铵)其反应式为:2NH3+H2SO4→ (NH4)2SO4当喷淋的硫酸过量时,则生成酸式盐硫酸氢铵,其反应式为:NH3+H2SO4→ NH4HSO4随着溶液含氨达饱和的程度,酸式盐又转变成中性盐即硫铵。
蒸氨工艺流程

蒸氨工艺流程
蒸氨工艺流程是将氨气从氨水中提取出来的一种工艺。
下面将介绍一下蒸氨的工艺流程。
首先,将浓度为10%~30%的氨水加热至60℃以上,将氨水汇
入脱气柱,通过塔底加热,使氨水中的氨蒸发出来,提高氨水浓缩度。
其次,将脱气柱中的氨气通过冷凝器冷却,使氨气变成液态,然后进入分离器。
在分离器中,将氨气与水分离开,得到纯氨气。
然后,将纯氨气经过水冷器进一步冷却,并通过油水分离器分离杂质,在保证纯氨气质量的前提下,达到初步脱水的目的。
接下来,将初步脱水后的纯氨气通过进气口进入冷却器,进行再次冷却,降低氨气温度。
然后,将冷却后的氨气进入吸收器,在吸收器中与进入的吸收剂发生反应。
最后,经过吸收器后,氨气中的杂质已经被吸收剂吸收,得到了更为纯净的氨气。
吸收器顶部的吸收剂经过再生装置进行再生,然后再次进入吸收器进行循环使用。
总结起来,蒸氨工艺流程包括加热氨水、蒸发氨气、冷凝氨气、分离水和氨气、冷却氨气、脱水、吸收和再生等多个步骤。
通过这些步骤的循环,不断提纯氨气,最终得到高纯度的氨气。
蒸氨工艺流程的核心是蒸发和吸收,通过加热氨水,将其中的氨蒸发出来,然后利用冷凝器将氨气冷凝成液态,再通过分离器进行水和氨气的分离。
接着,需要对氨气进行冷却和脱水处理,以去除其中的杂质。
最后,通过吸收器的吸收和再生步骤,对氨气进行进一步净化,得到高纯度的氨气。
蒸氨工艺流程具有设备简单、操作容易、工艺成熟等优点,被广泛应用于化工、医药、冶金等领域。
随着技术的不断发展和改进,蒸氨工艺的效率和纯度也在不断提升,为各行各业提供更好的氨气供应。
蒸氨工艺和蒸氨塔构造与操作技术
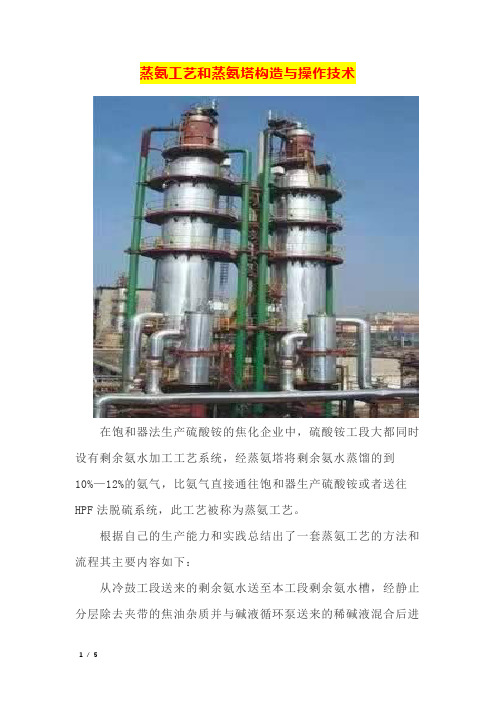
蒸氨工艺和蒸氨塔构造与操作技术在饱和器法生产硫酸铵的焦化企业中,硫酸铵工段大都同时设有剩余氨水加工工艺系统,经蒸氨塔将剩余氨水蒸馏的到10%—12%的氨气,比氨气直接通往饱和器生产硫酸铵或者送往HPF法脱硫系统,此工艺被称为蒸氨工艺。
根据自己的生产能力和实践总结出了一套蒸氨工艺的方法和流程其主要内容如下:从冷鼓工段送来的剩余氨水送至本工段剩余氨水槽,经静止分层除去夹带的焦油杂质并与碱液循环泵送来的稀碱液混合后进入螺旋板式换热器与蒸氨塔滴出来的蒸氨废水换热升温至98℃。
从内设25层垂直筛板的蒸氨塔第21层进入。
在塔中,被从塔底进入的低压蒸汽直接蒸馏,气提出来的蒸氨蒸汽经塔顶分缩器分缩,冷凝下来的液体回流塔中,浓缩氨蒸汽约含氨10%进入氨分缩器,冷却至95℃左右,送至喷淋式饱和器,利用硫酸铵将其回收。
从蒸氨塔底流出的废水,经与剩余氨水换热器降温后,自流入废水槽经蒸氨废水泵抽出加压,送废水冷却器进一步降温至48℃后被送至废水生化处理装置进行生物处理。
蒸氨塔的构造:焦化企业采用的蒸氨塔有咆罩式和栅板式两种。
我厂采用的是泡罩式蒸氨塔,它由多个高为0.5—0.7m的单个铸铁塔段组成,全塔塔数一般为25—29层(我厂为25层)。
塔径依氨水处理量计算确定。
每节塔段装有两层泡沸板,每层板上装有12个长履形泡罩,呈辐射状排列。
单数塔板设有中央大溢流管,双数塔板则沿周边设有12个小溢流管。
液体在塔板上依半径方向流动。
剩余氨水由上数第三块塔板进入,回流液由上数第一块塔板引入,并沿各层塔板溢流而下。
由塔底通入的直接蒸汽经过泡罩的齿缝泡沸穿过每层塔板上的氨水层,形成鼓泡区。
氨水中的氨、二氧化碳和硫化氢等物质则随着蒸汽的上升逐步进入气体中,这样的过程一直进行到塔底为止。
最后由塔顶溢出含氨浓度较高的氨气,而塔底排出的废水几乎全被脱出挥发氨。
主要工艺参数。
蒸氨塔底处温度:102—105℃,蒸氨塔顶部温度:100—102℃,蒸氨分缩器后氨气温度:92—98℃,换热器后剩余氨水温度:95—98℃,废水冷却器后蒸氨废水温度:40℃,蒸氨废水槽液位:1400—1600,浓氨水含氨:>10%,蒸氨废水含氨量:<250mg/L,PH值:8.5—9.5,进饱和器氨气温度:95℃左右。
蒲城蒸氨项目氨回收技术浅析

蒲城蒸氨项目氨回收技术浅析1、项目概况蒲城清洁能源70万吨/年煤制烯烃项目已经建设有污水处理装置,但是由于生产原料来源发生变化,即采用神渭管道公司输送的管道煤浆作为气化装置煤源后,打破了项目整体的水平衡,在原有废水的基础上,新增了七股废水,分别为:灰水过滤的滤液(含706沉渣池废水);变换低温凝液;低温甲醇洗废水;废碱液;高压富氢火炬凝液;水封罐溢流水;酸性气火炬凝液。
由于目前环保工作的重要性和迫切性,经过连续对管道煤浆使用后新增的几股废水进行标定和计量,本着彻底解决废水排放环保达标问题,公司将对新增污水建设污水处理装置,对新增的污水进行严格处理。
新增污水水量为:261m3/h,其中各装置连续排放水量为:252m3/h,火炬凝液部分排放水量约为9m3/h,设计规模为:300m3/h。
该项目由华陆工程科技有限责任公司E+PCM总承包,包括污水处理装置、灰水预处理装置等9个主项36个单项工程。
该建设项目于2016年7月5日开工,2018年3月份陆续投料试车,5月份环保竣工验收招标。
从天津晟远环境有限公司2017.3.10编制(该公司未参与建设,可能是前期交流资料)的一份“蒲城蒸氨项目概况”上看,设计处理量如下:处理冷凝液水量:Q=110t/h ,氨氮:7000-16000ppm,H2S :60~100ppm。
处理后:回收15-20%;氨水7t/h;净化后废水氨氮≤100 ppm。
2、资料分析从网上得到”新增污水蒸氨二(710)简介“PPT,以及709系统的PFD和PID 图,初步分析如下:2.1蒸氨二系统(710)蒸氨二系统采用单塔加压侧线抽氨汽提工艺,适用于三种工况,工况一:仅考虑现有变换汽提尾气凝液作为进水;工况二:在工况一的基础上,考虑酸性气火炬凝液进入系统;工况三:在工况一的基础上,考虑高压富氢火炬凝液进入系统。
加压汽提塔(T-101)侧线抽出富氨气经三级分凝系统冷却分离,产生的粗氨气(估计氨含量大于97%以上,但含有1%的H2S)一股直接送脱硫脱硝,另一股送氨气吸收塔(T-102)用氨水洗涤,洗涤氨水依次进入V-106分离器,经泵加压后分两股,其中一股则送氨气吸收塔(T-102)作为H2S的循环吸收液。
2 废氨水蒸馏为液氨及综合利用技术

9.经济性指标 以年回收7000吨液氨的蒸氨装置为例: (i)回收能力:7000吨/年液氨,设备总投资约350万元。 (2)蒸汽消耗≤3200kg/tNH。,循环水≤150m3/tNH。,电耗很低,不统计。
(3)投资回收期约三个月。
(4)岗位设置人力:按企业规定倒班,每班2----3人。 lO.节能减排管理实践 蒸汽和循环水消耗低:蒸汽消耗≤3200kg/tNH。,循环水≤150m3/tNH。,节能效果非 常好;通过回收稀氨水或含氨废气中的氨,得到产品液氨,残液可应用于变换饱和热水 塔工艺补水或者造气系统的工艺补水,也可直接排放,直接创造经济效益的同时,避免
使用工段,产品储运方便。 5.节能绩效
采用新型垂直筛板技术的蒸氨塔具有塔径小、塔板层数少、投资少、蒸脱率高、废
水含氨浓度低、蒸汽和循环水消耗低(蒸汽消耗<、3200kg/tNH。,循环水≤150m3/tNH。)、 抗堵塞、运转周期长,检修安装方便、使用寿命长等优点。DNl200蒸氨塔处理能力可达
216m3/天(氨水浓度为200tt),15万吨规模的合成氨厂每年可回收产品液氨约1000吨。
6.环境绩效
废氨水蒸馏为液氨及综合利用技术解决了氮肥企业一直存在的过剩氨水排放问题。 通过蒸氨装置,制取产品液氨,为企业解决过剩氨水处理难问题的同时产生巨大的经济 效益,并且装置不产生“三废”等污染物,对环境友好,是氮肥生产污水“零排放”
的关键技术之一。 7.交叉影响
蒸氨塔采用新型垂直筛板塔技术,不产生三废等污染物;产品液氨可直接应用合适 岗位,也可储存于液氨储罐;残液可用于变换系统饱和热水塔补水或者其它合适工段, 或者直接排放,其氨氮含量达到国家环保要求。 8.技术特点 采用新型垂直筛板技术的蒸氨塔具有塔径小、塔板层数少、投资少、蒸脱率高、废 水含氨低、蒸汽和循环水消耗低抗堵塞、运转周期长,检修安装方便、使用寿命长等优 点;蒸氨装置应用范围广泛;废氨水蒸馏为液氨及综合利用技术解决了氮肥企业一直存 在的过剩氨水排放问题。通过蒸氨装置,制取产品液氨,为企业解决过剩氨水处理难的 同时产生巨大的经济效益,并且装置不产生“三废”等污染物,对环境友好,是氮肥生 产污水“零排放”的关键技术之一。该技术已在氮肥企业和其它化工企业推广应用10
蒸氨工段操作规程(成型)
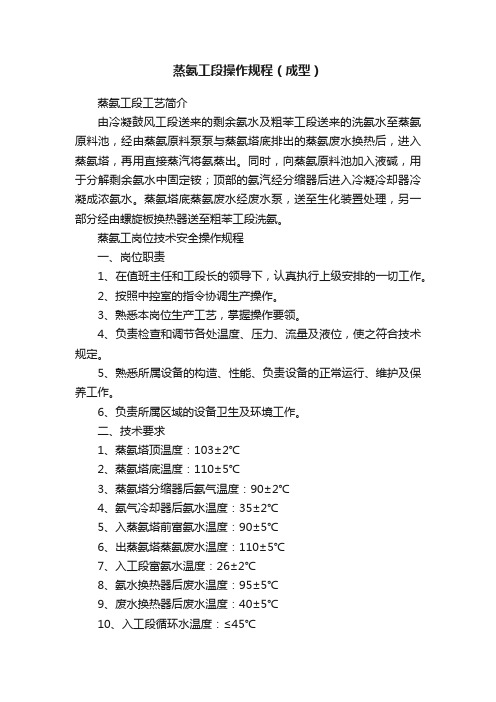
蒸氨工段操作规程(成型)蒸氨工段工艺简介由冷凝鼓风工段送来的剩余氨水及粗苯工段送来的洗氨水至蒸氨原料池,经由蒸氨原料泵泵与蒸氨塔底排出的蒸氨废水换热后,进入蒸氨塔,再用直接蒸汽将氨蒸出。
同时,向蒸氨原料池加入液碱,用于分解剩余氨水中固定铵;顶部的氨汽经分缩器后进入冷凝冷却器冷凝成浓氨水。
蒸氨塔底蒸氨废水经废水泵,送至生化装置处理,另一部分经由螺旋板换热器送至粗苯工段洗氨。
蒸氨工岗位技术安全操作规程一、岗位职责1、在值班主任和工段长的领导下,认真执行上级安排的一切工作。
2、按照中控室的指令协调生产操作。
3、熟悉本岗位生产工艺,掌握操作要领。
4、负责检查和调节各处温度、压力、流量及液位,使之符合技术规定。
5、熟悉所属设备的构造、性能、负责设备的正常运行、维护及保养工作。
6、负责所属区域的设备卫生及环境工作。
二、技术要求1、蒸氨塔顶温度:103±2℃2、蒸氨塔底温度:110±5℃3、蒸氨塔分缩器后氨气温度:90±2℃4、氨气冷却器后氨水温度:35±2℃5、入蒸氨塔前富氨水温度:90±5℃6、出蒸氨塔蒸氨废水温度:110±5℃7、入工段富氨水温度:26±2℃8、氨水换热器后废水温度:95±5℃9、废水换热器后废水温度:40±5℃10、入工段循环水温度:≤45℃11、分缩器后氨气压力:≤15KPa12、进蒸氨塔蒸汽压力:≥0.04MPa13、蒸氨塔底压力:≤40KPa14、蒸氨塔顶压力:≤15KPa15、蒸氨废水PH值:8.5~9.516、蒸氨塔液位:1000±200mm三、岗位操作1、正常操作(1)在正常生产过程中,应每小时进行一次巡回检查。
(2)检查设备、管道和阀门有无堵塞和泄漏,及时处理跑、冒、漏及其他问题。
(3)检查各泵的运转情况,响声、振动、轴承和电机温度,使之符合技术规定。
(4)检查各塔压力、温度、流量、液位等指标是否正常,换热器进出口温度、压力是否正常,发现问题及时与中控室联系,查找原因,及时处理。
蒸氨工段操作规程.doc

蒸氨工段操作规程.doc回收车间蒸氨工段工艺技术操作标准1 工艺流程鼓冷工段送剩余氨水至螺旋板换热器与蒸氨废水换热,然后进入蒸氨塔上部与含30%NaOH的碱液混合进入塔内;蒸氨塔底通入直接蒸汽加热蒸馏,氨汽经塔顶分缩器浓缩后送往脱硫工段以平衡脱硫液中的氨成份;蒸氨塔底蒸氨废水用蒸氨废水泵送到蒸氨废水换热器与剩余氨水换热,再经循环水冷却后,送往生化废水处理系统进一步处理;粗苯工段来的含30%NaOH的碱液送至原料氨水管上的管道混合器中,与剩余氨水混合后进入塔内,将剩余氨水中固定铵盐分解;-N≤300mg/L,PH值:8.5-10.5;采用的本工序的主要控制参数,指标是废水含NH3碱液浓度为含30%NaOH溶液;1.1影响废水水质的因素:来水水质、加碱量的控制、蒸汽压力(流量)、蒸氨塔处理量;1.2介质性质1.2.1氨汽性质:爆炸极限:上限25% 下限16%;禁忌物:酸类;1.2.2含30%NaoH液碱性质:禁忌物酸类、易燃;危险性与毒性:强碱性、强腐蚀性、遇酸中和发热;2 岗位职责范围2.1蒸氨塔工兼班长:蒸氨塔、分缩器及仪表照明等附属设施;2.2蒸氨工:放空槽、蒸氨废水换热器、蒸氨废水冷却器、蒸氨废水泵、液下泵、管道混合器及管道阀门、仪表等附属设施;3 主要设备概况3.1蒸氨塔2台DN2000 H=20450;3.2氨分缩器FV=120m2 2台;3.3氨水换热器f=70 m2 3台;3.4蒸氨废水冷却器f=100 m2 3台;3.5放空槽DN=1400 L=4500 VN=6m3 1台;3.6蒸氨废水泵Q=70m3/h H=40m 2台附电机N=15kW 2台;3.7液下泵Q=12m3/h H=25m 附电机N=5.5kW 1台;3.8管道混合器DN=125 L=1300 1台;4 岗位职责4.1蒸氨班长的职责;4.1.1在工段长的领导下进行工作;4.1.2严格执行本岗位安全技术操作规程和各种制度;4.1.3认真组织,精心操作完成本班的产品质量和废水的各项指标,保证生产安全稳定地运行;4.1.4做好交接班工作,积极参加上级安全的活动;4.1.5认真完成车间或工段交给的各项任务;4.1.6对本岗位的生产、安全、卫生等负全面责任,负责蒸氨系统设备的操作与维护;4.1.7坚持巡回检查,精心调节,保证蒸氨系统各部温度、压力、流量正常稳定且符合技术规程的要求,并认真填写记录;4.2蒸氨工的职责:4.2.1 负责组织本岗位的交接班检查及设备检修后的验收;4.2.1受蒸氨班长指挥,负责废水换热器、冷却器、废水泵、碱泵的操作和维护,协助本班班长完成生产任务;4.2.3负责本岗位设备的正确操作和维护,卫生清扫;4.2.4负责蒸氨塔口排沥青工作;4.2.5严格执行本岗位的安全技术规程和各种规章制度,班长不在时,代替班长工作;5 蒸氨系统技术要求:5.1蒸氨塔压力:0.03-0.04MPa;5.2分缩器出口氨汽温度93-95℃;5.3蒸氨废水含:NH-N≤300mg/L;PH值8.5-10.5;35.4蒸氨废水冷却器出口温度<40℃;5.5剩余氨水入塔温度:80℃;5.6蒸氨塔底温度:105℃;5.7蒸氨塔顶温度:101℃-103℃;5.8碱液浓度:含NaOH30%;6 岗位操作细则6.1正常操作:6.1.1蒸氨工班长:6.1.1.1根据蒸氨废水化验结果及时调节入塔剩余氨水量、碱液流量及蒸汽量,确保各项操作指标符合要求;6.1.1.2认真检查调节,保证蒸氨系统的温度、压力保持稳定,每小时记录各部指标一次;6.1.1.3严格按安全技术规程操作,发现问题及时处理;6.1.2蒸氨工:6.1.2.1每小时检查各泵的运转、冷却水上量情况并及时调节,保证流量稳定,发现问题及时处理,做好记录;6.1.2.2积极配合蒸氨班长的工作,保证蒸氨废水水质稳定;6.1.2.3定时排放蒸氨塔底部焦油;6.2蒸氨塔开工:6.2.1通知脱硫工段和生化废水处理系统,注意各自的操作并密切配合;6.2.2打开塔顶分流器出口放散管,通蒸汽吹扫,待蒸汽大量放散后且各部位温度达到开工要求时,关闭放散管,打开氨汽管上出口阀门;6.2.3送入剩余氨水(碱液与剩余氨水的混合液,待塔底液位升到一定位置时[1000mm-1100mm]),开启蒸氨废水泵;6.2.4当蒸氨塔顶分缩器温度上升到95℃,开启蒸氨废水冷却器冷却水入口,慢慢送入冷却水;6.2.5及时调节蒸氨废水泵和入塔剩余氨水的流量,保持塔内液位稳定,调节蒸汽量、冷却水量,保证塔压和各部温度正常,并使脱硫进口煤气压力和分缩口出口氨气压力平衡;6.3蒸氨塔停工:6.3.1打开蒸氨塔顶放散管,减小直接蒸汽量,关闭塔顶氨分缩器出口阀门以防脱硫塔煤气倒窜;6.3.2通知鼓冷工段停止送剩余氨水、粗苯工段停止送含NaOH30%的碱溶液,关闭塔顶氨分缩器的冷却水;6.3.3当塔底蒸氨废水抽完并停泵后,关闭蒸氨废水冷却器冷却水入口阀门;6.3.4开大入塔直接蒸汽量,对蒸氨塔进行全面吹扫;蒸氨塔顶放散管蒸汽大量放散约10分钟后,停止送蒸汽,塔顶放散管处于全开状态;6.3.5停工时塔内废水要及时放空,吹扫碱液管并放空;6.3.6根据停工检修的需要蒸氨废水泵、蒸氨废水换热器、蒸氨废水冷却器及其管道内的液体可有选择性放空;6.4蒸氨岗位特殊操作:6.4.1当蒸汽停汽时,首先打开塔顶氨分缩器出口上放散管,然后关闭分缩器出口阀门,停剩余氨水泵、蒸氨废水泵等,并按停工步骤进行处理;6.4.2若蒸汽压力低,则应适当降低入塔剩余氨水量和蒸氨废水外排量,以维持蒸氨塔的正常生产,且保证各项控制指标正常;6.4.3若蒸氨塔底压力偏高,则应减少入塔蒸汽量,并迅速查明原因及时处理;7 安全注意事项7.1上班时应穿戴好规定的一切劳保用品;7.2上班时严禁喝酒、斗欧、打瞌睡以及擅自离开工作岗位,不准做本职工作无关的事;7.3上蒸氨塔顶检查作业时,必须抓牢扶手和栏杆,严防高空坠落;7.4各设备接地应保持良好无损,发现问题及时处理;7.5工具及消防器材要保持完好无损,不得挪作它用;7.6尽量消除系统内各处的跑、冒、滴、漏现象,系统泄漏率控制在3%以下;7.7系统内电气设备运行时,不要超过设备的额定负荷,以防设备过热引起火灾;7.8系统内各运转设备应定期加油,保证其润滑良好;。
氨回收工艺
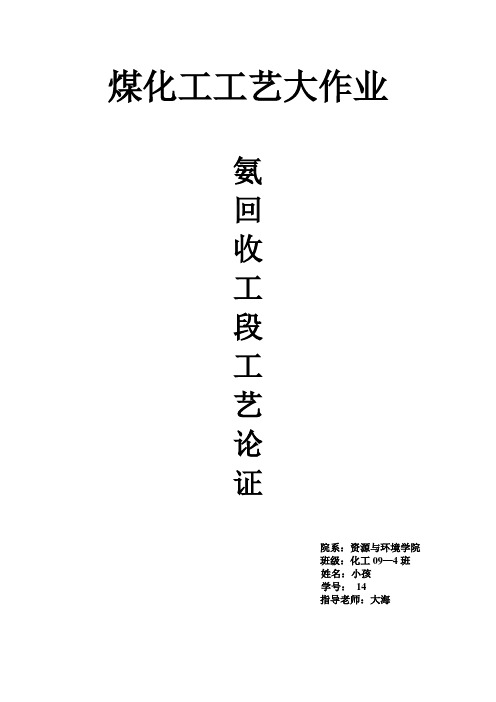
煤化工工艺大作业氨回收工段工艺论证院系:资源与环境学院班级:化工09—4班姓名:小孩学号:14指导老师:大海氨回收工段工艺论证作者:摘要:炼焦煤在焦炉干馏过程中,煤中的元素氮大部分与氢化合生成氨,小部分转化为吡啶等含氮化合物,氨的生成量相当于装入煤量的 0.25%~0.35%,粗煤气中的含氨量一般为6~9g/m3。
关键词:氨的回收饱和器无饱和器冷却器一、硫铵生产工艺生产硫铵是焦炉煤气净化工艺流程中回收氨的传统方法。
我国20世纪60年代以前建成的大中型焦化厂均采用半直接法鼓泡型饱和器生产硫铵,该工艺的主要缺点是设备腐蚀严重,硫铵质量差,煤气系统阻力大。
在宝钢一期工程的建设中,我们引进了酸洗法生产硫铵工艺,它是由酸洗、真空蒸发结晶以及硫铵离心、干燥、包装等三部分组成。
与饱和器法相比,由于实现了氨的吸收与硫铵结晶分离的操作,以获得优质大颗粒硫铵结晶。
酸洗塔结构为空喷塔,煤气系统阻力仅为饱和器的1/4,煤气鼓风机的电耗可大幅度下降。
采用干燥冷却机将干燥后的硫铵进一步冷却,防止结块,有利于自动包装。
鞍山焦耐院将此工艺经改进后用于天津煤气二厂,装置投产后已通过了技术鉴定。
在宣钢和北焦的建设中,我们引进了间接法饱和器生产硫铵工艺,该工艺是从酸性气体中回收氨,其硫铵的质量比饱和器法好,但因在较高温度(100℃左右)下操作,对设备和管道材质的要求高,加之饱和器尺寸并不比半直接法小,因此投资高于半直接法。
在杭钢焦化厂,我们将此工艺用于蒸氨塔后氨汽生产硫铵,并已正常投产。
除上述方法外,鞍钢二回收从法国引进的二手设备喷淋式饱和器,以代替半直接法的鼓泡型饱和器。
喷淋式饱和器的特点是煤气系统阻力较小,设备尺寸可相对减小,硫铵质量有所提高。
国内已有不少厂家用其代替老式的鼓泡型饱和器。
但是,不管采用那种生产硫铵的工艺,从经济观点分析,其共同的致命缺点是硫铵的收入远远不够支付其生产费用。
下面重点介绍一下酸洗法和喷淋式饱和器生产硫铵的工艺。
氨回收装置技术改造及运行

统存在的压力波动大、 液位控制不住 、 精馏工况不稳定 、 产品回收困难 常运行时, 氨库压力稳定 , 吸收塔负荷能够 自动调节, 压力和液位基本保 系 等一系列问题得到了全面解决 。 现该装置对全部贮罐气进行气氨回收操 液氨产量明显增加。 ’ 3 蒸氨塔 自动放空调节阀更换膜头。 . 2 根据工艺要求, 当蒸氨塔超压 作 , 时, 系统会 自动放空 , 以保证安全生产。但由于原设计放空位置不合理 , 由改造前的月平均回收液氨 6 吨增加到了 17吨, 4 2 改造获得成功。 在装置实际安装过程中, 我公司对其进行了改进 , 将该放空接至冷凝器 同时由于产量提高, 单位产品较改造前节约蒸汽量 3%以上 , 0 气氨回收 9 %以上。 5 与液氨贮罐平衡管处。 装置投产后, 满足了工艺放空要求, 但由此却造成 率在 9. 现该装置存在的问题是 , 设备露天设置 , 冬季运行时气温低 , 造成大 自动放空调节阀由于背压太小( = . a无法投入使用 。 AP 0 2MP ) 0 一旦系统 蒸汽消耗量明显增加。同时该装置多次出现由于仪表管线冻 出现波动 , 蒸氨 迢压, 便不能迅速做出反应 , 严重威胁着安全生产。迫 量热损失 , 停车检修隋况。 不得已只好降低蒸氨塔操作压力, 低负荷运行 。于是对该 白调阀更换了 结 ,
持 匿定 。
2工艺 流程
来 自氨库的贮罐气, 经减压阀减压后 , 从氨吸收塔的下部人塔 , 与从 塔中段氢回收来的氨水和上段喷淋下来的稀氨水逆流接触 , 气体中的氨 被水吸收生成浓氨水。 经水洗后的尾气经减压阀减压后送人气柜做燃料 图 1 氨 回 收装 置 工 艺 流 程 图 气使用。氨吸收塔中生成的浓氨水凭借压差, 经氨水换热器加热后从蒸 氨塔中部人塔。在蒸氨塔中浓氨水被循环水冷凝成液氨, 一部分回流至 蒸氨塔顶, 其余部分作为产品流人液氨储罐。在蒸氨塔中蒸出氨后的稀 氨水送至氨水换热器 , 加热吸收塔来的浓氨水后 , 经水冷却器进一步冷 却, 经氨水循环泵加压后从氨吸收塔的上段入塔 , 氨水在系统 内循环。 为 保证塔液位正常, 设有稀氨水排放阀。 . 蒸氨塔所需热量由进人再沸 此外, 器的蒸汽提供。工艺流程见图 1 。 3生产 运行 情况及 问题 改进 氨回收装置 自 19 年 1 月投入使用后陆续暴露出一些问题。主 96 0 要表现为:吸收塔压力波动大, 乱 液位控制不住 ;蒸氨塔自动放空由于调 b . 图 2蒸氨塔回凌管改选 节阀膜头背压小 , 不能投入使用 , 限制了生产负荷的提高 ;蒸氨塔塔顶 c . 系统开车后 自动放空投人使用 , 解决了安全隐患 , 生产负荷得以提 回流设计不合理 , 比过大, 回流 产品产量少 , 液氨在塔内循环 , 蒸汽消耗 膜头。 高。限于以上原因, 该装置一直在较低负荷下运行 , 贮罐气仍有大量放 高 。 3 蒸氨塔塔顶回流管线改造。由于蒸氨塔塔顶回流管线设计时无 - 3 空, 不仅浪费了大量气氨, 同时也污染了环境。针对这一情况, 我公司对 液封 , 并且产品液氨引出位置高于回流管近 1 图 2结果造成回流管 米( ) 系统存在的问题进行了改进 , 具体包括以下几个方面。 3 稳定吸收塔压力。氨吸收塔操作压力的稳定是氨回收装置稳定 阻力远小于收氨管阻力。虽然设计 匕 . 1 在回流管上设一截止阀 , 但仍然不 产品液氨少的问题。于是通过对回流管线进 运行的前提条件。我公司氨吸收塔压力控制有两方面调节, 一是氨库来 能解决液氨回流量不稳定, 对原管线进行了改造 , 增加了高度为 1 米 的 U型液封 , . 5 同时将 的贮罐气压力调节 , 二是尾气排放压力调节。 具体操作为, 给定吸收塔操 行核算, 作压力 , 当吸收塔压力低于给定值时, 氨库来贮罐气调节 阀打开向吸收 收氨管线引出位置下移到 U型弯的最低处( 2o 图 ) 改造后 由于液封的作 增大了液氨回流阻力, 液氨产量明显增加。同时由于回流比适合 , 精 塔充压, 反之停 l E 充压; 当去气柜压力低于给定值时, 尾气排放 自调阀打 用, 单位产品能耗大幅度降低。 开, 吸收塔向气柜充压 , 从而保证吸收塔压力稳定。采用这样的控制方 馏工况得到改善, 式, 其弊端在于, 以吸收塔压力稳定为调节原则 , 必然造成氨库压力波 3 尾气排放管线增加放空管。 . 4 氨回收装置 自投运以来 , 一直未能满 主要是由于原设计不合理 , 限制了系统只能在低负荷下运行。 动 。而对于我公 司尿素生产 ,要求 氨库压力必须平稳 ,且不能低 于 负荷运行, 21 a因此为保证氨库去尿素压力稳定 , . , MP 只好将贮罐气压力调节阀改 但还是—个客观原因, 就是氨回收尾气排放设计时只考虑送气柜做燃料 为手动操作, 给生产带来极大不便。 直接表现为吸收塔压力控制不住 , 气使用。但由于我公司实际隋况, 液 气柜过高时, 不允许放空, 目的是保证 空分装置正常生产 , 避免 C H化合物超标 。因而当气柜过高时, — 氨回收 位经常大幅度波动 , 生产无法正常进行。 针对这一隋况, 经过认真分析 , 并吸取操作上的经验 , 对吸收塔压力 只能减负荷运行 , 多余的贮罐气则通过氨库放空放掉 , 致使大量气氨 白 的控制方式进行了改进。将贮罐气压力调节, 取压点位置 由阀后位移至 白浪费。于是对氨回收尾气排放管线进行了改造 , 增加一旁路引至氨库 当气柜高时, 通过该管线将多余尾气放掉, 氨回收装置保证正常生 阀前, 目的是把保证氨库压力平衡作为氨回收装置i 生产的前提。当 放空 。 亍 确保了对全部 氨库压力高于工艺指标时, 阀门打开, 氨库向吸收塔释放贮罐气。 同时将 产。尾气排放管线的改造提高了氨回收装置的操作弹性 , 尾气压力调节阀取压点 由阀后移至阀前, 并更换调节阀膜头, 当吸收塔 贮罐气中的气氨进行回收。 操作压力高于给定值时 , 尾气排放阀打开 , 向气柜排气 , 从而保证吸收塔 4改造效果及问题讨论 我公司氨回收装置 自投运以来经过两年多的调试和技术改造 , 原有 压力稳定。 吸收塔压力控制方式经过改进后 , 收到了明显效果。 当装置正
氨的回收2
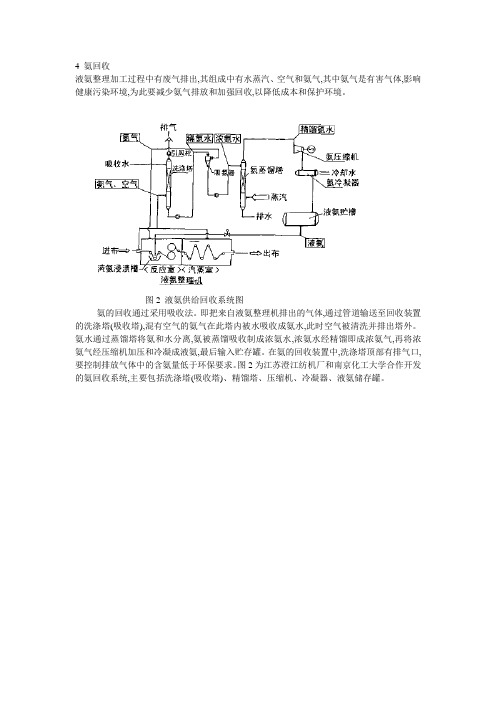
4 氨回收
液氨整理加工过程中有废气排出,其组成中有水蒸汽、空气和氨气,其中氨气是有害气体,影响健康污染环境,为此要减少氨气排放和加强回收,以降低成本和保护环境。
图2 液氨供给回收系统图
氨的回收通过采用吸收法。
即把来自液氨整理机排出的气体,通过管道输送至回收装置的洗涤塔(吸收塔),混有空气的氨气在此塔内被水吸收成氨水,此时空气被清洗并排出塔外。
氨水通过蒸馏塔将氨和水分离,氨被蒸馏吸收制成浓氨水,浓氨水经精馏即成浓氨气,再将浓氨气经压缩机加压和冷凝成液氨,最后输入贮存罐。
在氨的回收装置中,洗涤塔顶部有排气口,要控制排放气体中的含氨量低于环保要求。
图2为江苏澄江纺机厂和南京化工大学合作开发的氨回收系统,主要包括洗涤塔(吸收塔)、精馏塔、压缩机、冷凝器、液氨储存罐。
- 1、下载文档前请自行甄别文档内容的完整性,平台不提供额外的编辑、内容补充、找答案等附加服务。
- 2、"仅部分预览"的文档,不可在线预览部分如存在完整性等问题,可反馈申请退款(可完整预览的文档不适用该条件!)。
- 3、如文档侵犯您的权益,请联系客服反馈,我们会尽快为您处理(人工客服工作时间:9:00-18:30)。
效 益 分 析 节 能 减 排
中图 分 类 号 :T 2 . 文 献 标 识 码 : 文 章 编 号 :0 6 96 2 1 )6— 0 3 0 Qo 8 1 A 10 ~7 0 ( 0 10 0 4 — 3
。_刎 ..一 一翟_ 删~ 0=蕃 Ⅵ 帅 _堇 暇 lm 培 m∞ n rF 一 e“ . v兰 … a ~ 眦一 啦 u ~删 一m a ∞ ¨S 一n T 一 、¨ h ~~ 2删 ¨一 ㈦d ∞ 帆 哪l mp ns 眦 旷 — m 一 三 - . m n 刚 Ⅲ
变成 氨水 , 然后通 过 蒸 氨塔 的汽 提 作 用在 塔 顶 得 到
由于农 药 厂 要求 制 取无 水 液 氨 , 除一 部 分 自用
外, 其余 出售 , 故本项 目采 用 中压蒸 氨 的方 案 。
2 氨 回 收 工 艺 流 程
碱 解尾气 以 0 0 a的 压 力 、 5 C的 温度 .6 MP 约 o。 进入 氨 回收装 置 。碱解尾 气 首先 由洗氨塔 的底 部进
a ∞
m )
卟
m ] . 如 l
农药 厂 I AN法草 甘磷 在碱 解 投料 时反 应产 生 D
的氨尾气 目前 大部 分是 通过 风 机的 进 口负压 吸 收再
d . 至 Ⅻ 氨水 分 离的解 吸过 程 。低心 压解 吸蒸 氨 主要 是满 足塔
和生产工艺 的要 求 , 技改后草甘磷 离心母 液几乎 都用
可达 到 目的 。而 中压 蒸氨 塔顶 气氨 的纯度 可 以达到 大 于 或 等 于 9 . ( 质 的量 分 数 ) 采 用 中部 进 97 物 , 料 、 回流 的流程 , 解 吸压力 必须 在 1 8 19 有 但 . ~ .
MP ( )左 右 。 a表
于平衡 溶解 系统 中 , 由此必须首先解 决碱 解反应 产生 的大量氨气 吸收问题 。 现就氨 回收提出工艺方 案 。 本 项 目上 1 1 ta氨 回收装 置 , 套 2 / k 采用 连续 生 产 。含 氨 的废气 在洗 氨塔 中用界 外来 的脱盐 水 吸收
用塔底废液 的显热 , 不仅 实现 节 能降 耗 , 而且 由 于废 液 中氨物质 的量分 数较低 , 于1 0 0 。 可直接 当 小 5 ×1 一 ,
第 3 2卷 第 6期
2t O 1年 l 2月
化 学 工 业 与 工程 技 术
J u n l / Ch m ia n sr r a o o e c lI duty En i ern g n e ig
பைடு நூலகம்
Vo1 3 . 2 No. 6
De . c,2O 】1
蒸 氨 法 氨 回收 工 艺及 装 置 简 介
标 排放 或 回收利用 。低 压解 吸蒸 氨与 中压蒸 氨都是
作者简介 : 李爱仙 (95 , , 16一)女 江苏宜兴 人, 高级工程 师, 从事化
工 工艺 设 计 工 作 。
・4 ・ 4
化 学 工 业 与 工 程技 术
21 年第 3 01 2卷 第 6期
入二 段 洗 氨 塔 ; 泵 将 脱 盐 水 ( 0 1 水 1 ~ 5℃ , 量 控 流
李 爱 仙
( 国 石 化集 团南 京工 程有 限公 司 , 苏 南 京 2 1O ) 中 江 1 lO
一 m油 ~ 一㈨ = 一 0 l~ = 帅 G= 咖 ∞
摘 要 : 药 厂 I A 法 草 甘 磷 在 碱 解 反 应 中产 , 农 D N 大量 的 含氨 气 体 , 用 中压 蒸 氨 工 艺 回 收 氨 。 介 绍 采 了低 压 解 吸 蒸 氨 工 艺 和 中压 蒸 氨 工 艺 各 自的 特 点 , 削述 了 中压 蒸 氨 工 艺 流 程 、 品 质 量 、 耗 指 标 、 艺 产 消 工 指标 、 主要 设 备 , 绍 r生 产 成 本 、 益 情 况 , 进行 了分 析 。 介 收 并 , 关 键 词 : 氨气 体 洗 氨 塔 含 蒸氨塔
加 压送 去换热 器 , 氨水 温 度 降 到 3 将 5℃ , 与补 充 洗 氨水 混合 后入 洗 氨塔 第 一段 填 料 ; 段 洗后 气 再 进 一
收 稿 日期 : 0 1 6 4 2 1 一O —1 。
浓 氨水 分离 方 法有 低 压解 吸蒸 氨 和 中 压 蒸 氨
法 。中压蒸 氨制取 无 水 液 氨作 为产 品 , 氨 废 水达 蒸
底 排放指 标 要求 的 含 氨 小 于 或 等 于 1 0 0 , 0 x 1 一 塔 顶水 质量 分 数 小 于 或 等 于 3 , 用 塔 顶 有 回流 、 6 采
塔 顶进料 的方 式 , 吸压 力在 0 3 a 表 ) 右 即 解 . 9MP ( 左
S ● 1
吹入母 液通氨大槽 中进行 中和 反应 , 母液 是 目前 草甘 磷结 晶离 心后 的稀母 液 , 中和后 的 母 液送 至 蒸发 浓 缩; 另一部分氨气 是 通过 大 槽 吸 收成 1 ~1 ( 0 5 体 积分数) 的氨水 再 出售 。 根据 溶解 法技 改工 作 的 推进
入 一段 , 循环泵 将塔 底 大 部 分 含氨 水 ( 流量 调 节 ) 经
纯度较 高 的 富 氨 气 , 通 过 液 氨 冷 凝 器 制 取 含 氨 再
9 . % ( 量分数 ) 液态 氨 送 至 液 氨贮 槽 , 96 质 的 由液 氨
槽 车或 灌装 成液 氨钢瓶 外运 出售 。
1 蒸 氨方 案的确 定
制 ) 到洗 氨塔 的顶部 。 送
高 纯度 的氨气 经冷 却 器 冷 却后 到 液 氨 过 渡槽 , 氨 液
由泵加 压后一 部分 由液 氨过渡 槽冷 却器 冷却后 送 液 氨储槽 , 另一 部分 液氨 回流蒸 氨塔 。 蒸 氨塔底 部溶 液 ( 为贫 液 ) 经 贫 富液 换 热 器 称 , 换热后 , 再进 入贫 液 水 冷 却器 冷 却 到 2 O℃ , 回洗 氨 塔二 段作 为补充 循环水 。 该 工艺技术 的特点是 蒸氨塔前设预热 器 , 分利 充