内浮顶储罐施工方案
(整理)内浮顶储罐施工方案
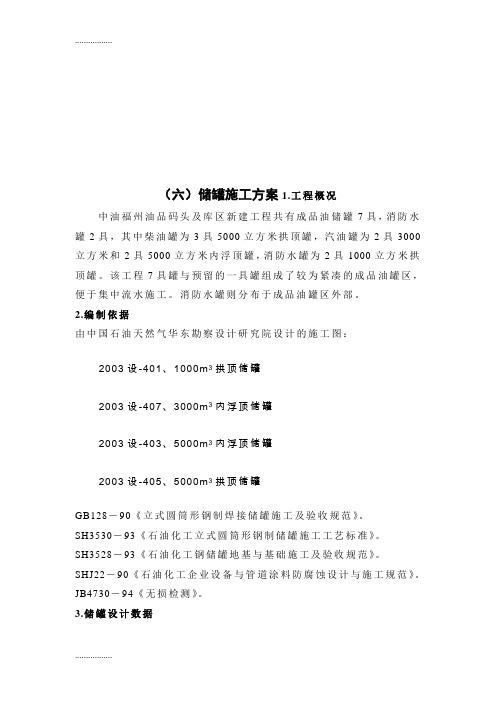
(六)储罐施工方案1.工程概况中油福州油品码头及库区新建工程共有成品油储罐7具,消防水罐2具,其中柴油罐为3具5000立方米拱顶罐,汽油罐为2具3000立方米和2具5000立方米内浮顶罐,消防水罐为2具1000立方米拱顶罐。
该工程7具罐与预留的一具罐组成了较为紧凑的成品油罐区,便于集中流水施工。
消防水罐则分布于成品油罐区外部。
2.编制依据由中国石油天然气华东勘察设计研究院设计的施工图:2003设-401、1000m3拱顶储罐2003设-407、3000m3内浮顶储罐2003设-403、5000m3内浮顶储罐2003设-405、5000m3拱顶储罐GB128-90《立式圆筒形钢制焊接储罐施工及验收规范》。
SH3530-93《石油化工立式圆筒形钢制储罐施工工艺标准》。
SH3528-93《石油化工钢储罐地基与基础施工及验收规范》。
SHJ22-90《石油化工企业设备与管道涂料防腐蚀设计与施工规范》。
JB4730-94《无损检测》。
3.储罐设计数据4.罐体数据(1)1000立方米拱顶罐罐体数据一览表:(单具总重28850Kg)(2)3000立方米内浮顶罐罐体数据一览表:(单具总重76797Kg)(3)5000立方米拱顶罐、内浮顶罐罐体数据一览表:(单具总重119731Kg)5.施工方法5.1施工方法采用群桅起升倒装法:5.2施工用料:每个罐所需倒链和桅杆如下表所示:5.3材料验收储罐所选用的材料和附件,应具有质量合格证明书当无质量合格证明书或质量合格说明书有疑问时,应对材料和附件进行复验。
储罐焊条选用J422、J427电焊条,焊条应具有质量合格说明书。
储罐所选用的钢板,必须逐张进行外观检查,其表面质量应符合现行的相应钢板标准的规定。
钢板表面锈蚀减薄量,划痕深度与钢板实际偏差之和,应符合下表规定。
5.4预制5.4.1罐底预制(1)罐底板预制前应根据实际来料绘制排版图。
并根据图纸放大样,检查无误后方可下料。
(2)罐底的排版直径,宜按设计直径放大0.1-0.2%。
50000M3立式浮顶储罐施工方案

50000M3立式浮顶储罐施工方案1.编制说明及工程概况1.1编制说明本方案仅叙述了50000M3储罐的主要施工程序,施工前将进行细化,满足指导施工的要求。
其焊接工作将以焊接专业方案为准。
1.2工程概况储罐基本结构由罐底、壁板、浮顶(包括罐顶附件)、抗风圈、加强圈、梯子平台、排水管等组成。
储罐公称容量50000 M3,储罐内径60M,高度19.46M,双盘浮顶,储罐共分八层带板,总重1207.4吨。
壁板纵缝、环缝、底板全部为对接焊,浮顶底板和顶板为搭接焊。
第一带壁板焊后立即进行消氢处理。
密封装置安装和罐体保温本方案没有考虑。
2.编制依据及施工方法的选择2.1编制依据SH3530-93 石油化工立式圆筒形钢制储罐施工工艺标准GBJ128-90 立式圆筒形钢制焊接油罐施工及验收规范2.2施工方法的选择根据储罐的特点,结合我单位的施工经验,选用内外悬挂脚手架正装法施工本储罐。
本方法可以增加工序交叉程度,充分利用机械和劳动力,有利于缩短工期。
同时也可以保证施工质量。
在土建施工阶段进点,及早介入。
节约中间交接时间。
并在土建交工前完成大部分预制工作和全部的安装准备工作。
在施工现场建立预制场,完成壁板卷制、浮顶分片预制、抗风圈卷制等工作,减少运输时间和费用。
焊接采用自动焊,壁板、底板、浮顶焊缝采用自动焊接,浮顶桁架使用手工焊接。
浮顶在临时支架上组对。
储罐组对采用150吨和50吨吊车吊装,使用间隙板、卡具固定调整。
消氢处理使用电加热。
外脚手架悬挂在壁板外面上,外架采用分段预制好的抗风圈,内架为挂在壁板上可移动的钢架。
外部盘梯在平台上分段预制,及时分段安装。
附罐管道在罐体试验时完成。
防腐工作与安装同时进行,在组装前完成罐底板底面打沙和刷漆,罐体和浮顶防腐在充水试验后进行,在预制厂完成梯子平台打沙和底漆、面漆涂刷,组装后及时补漆。
保温工作在防腐后及时完成。
3.施工准备完成施工图纸会审;施工方案、排板图通过审批;原材料、配件通过验收合格;施工现场三通一平完成;正装施工需要的脚手架、间隙板、卡具、弧形胎架等已准备好;打砂工机具准备好,具备打砂条件;施工人员、机具到位。
内浮顶储罐施工方案

(六)储罐施工方案1.工程概况中油福州油品码头及库区新建工程共有成品油储罐7具,消防水罐2具,其中柴油罐为3具5000立方米拱顶罐,汽油罐为2具3000立方米和2具5000立方米内浮顶罐,消防水罐为2具1000立方米拱顶罐。
该工程7具罐与预留的一具罐组成了较为紧凑的成品油罐区,便于集中流水施工。
消防水罐则分布于成品油罐区外部。
2.编制依据由中国石油天然气华东勘察设计研究院设计的施工图:2003设-401、1000m拱顶储罐32003设-407、3000m内浮顶储罐32003设-403、5000m内浮顶储罐32003设-405、5000m拱顶储罐3GB128-90《立式圆筒形钢制焊接储罐施工及验收规范》。
SH3530-93《石油化工立式圆筒形钢制储罐施工工艺标准》。
SH3528-93《石油化工钢储罐地基与基础施工及验收规范》。
SHJ22-90《石油化工企业设备与管道涂料防腐蚀设计与施工规范》。
JB4730-94《无损检测》。
据数计设罐储3.)T-301-01~Q235-A21300215.848172T-301-03~2Q235-A500419.817.863T-301-05~3Q235-A500罐719.817.8642Q235-A100罐2-1/11.513.18)4.罐体数据(1)1000立方米拱顶罐罐体数据一览表:(单具总重28850Kg)K量3933Q235-A6000 ××7罐1壁板板1钢2000 )一(16855罐2壁板2000×板钢56Q235-A×6000)二(168 1 3 =6 顶心板板钢δQ235-A 中46404 皮瓜板板钢16 δQ235-A=6Q235-A.F ×75×钢9 角758 326 钢边5 包角Q235-A 10 δ板9 钢=5 板6 垫6800Q235-A=7δ板钢1板底75.施工方法5.1施工方法采用群桅起升倒装法:5.2施工用料:每个罐所需倒链和桅杆如下表所示:3 5000mφ325×8,L=4000mm,22个3 1000m10T 8个倒手动3 3000m10T 16个链3 5000m10T 22个材5.3料验收合当量无质证合质,料选罐储所用的材和附件应具有量格明书进附料材和件行复验。
800m3浮仓内浮顶贮罐施工方案

800m3浮仓内浮顶贮罐施工方案(充气顶升法)1 制说明及依据1.1 **********,为了保证其制作质量和工期,特编制《800m3浮仓式内浮顶贮罐施工方案》,作为浮仓式内浮顶贮罐施工指导性文件。
1.2 主要编制依据1.2.1 《立式园筒形钢制焊接油罐施工及验收规范》 GBJ128-90 1.2.2 《钢制焊接常压容器》 JB/T4735-971.2.3 《石油化工立式园筒形钢制焊接储罐设计规范》 SH3046-92 1.2.4 《钢结构施工及验收规范》 GB50205-951.2.5 《安装工程质量检验评定手册》 (1990版,程协瑞主编)1.2.6 《十六建设公司焊接工艺评定资料汇编》1.2.7 《********项目招标书》2 要施工方法及施工程序2.1 施工准备及平面布置2.1.1 图纸会审、技术交底由施工技术负责人组织有关施工人员熟悉图纸、分析结构、核算图纸尺寸,对图纸进行全面审核,并作好记录。
由甲方邀请设计单位进行设计交底并解决图纸上有关疑难问题。
由施工技术员向施工人员作全面技术交底,其主要内容如下:施工图有关技术要求、设计要求、施工程序、工艺方法、质量要求、施工进度安排、交叉作业条件及安全注意事项,交底时由专业技术人员做好记录。
2.1.2 物资准备2.1.2.1 做好各类卡具、胎具的制作2.1.2.2 施工所用主要工、机具一览表见附表2.1.2.3 施工所用主要辅料、材料一览表见附表2.1.3 人力资源2.1.3.1 劳动力计划见下表2.1.3.2 电气焊工必须具有与施焊位置相适应的考试合格证书,其他各工种必须持各自上岗证施工。
2.1.4 施工平面布置2.1.4.1 临时钢平台:面积12×12,其基础应牢固,表面平整无毛刺。
2.1.4.2 钢平台、集装箱、现场办公室、卷板机、坡口机、鼓风机等施工机具安装位置详见本标段施工组织设计平面布置图。
2.1.4.3 罐体周转道路要畅通,路面应铺设一层卵石以利重车运行。
储罐全浸液式不锈钢双盘内浮顶施工安装方案

山东****有限公司全接液不锈钢双盘式浮顶及高校密封安装施工技术方案******科技安装服务有限公司2020年12月26日目录一、工程概况二、编制依据三、施工工艺四、安全防护和应急措施五、质量管理六、HSE管理一、工程概况1、我公司负责2台罐测绘安装工作,1台3000m³,1台10000m³罐,浮盘形式为全接液不锈钢双盘式浮顶高校密封,密封形式为全补偿高校密封。
结合工程的具体情况编制此施工方案,以保证为用户提供精品工程。
1.2主要实物工程量罐内不锈钢双盘式浮顶构成:主要部件有支柱、人孔装置、量油装置、通气装置、导静电装置、防旋转装置、立柱通过装置、周边密封装置(弹性压力板+聚四氟乙烯密封)、不锈钢浮箱、外圈梁、压条、不锈钢紧固件等。
二、编制依据1、储罐方位数据图及现场测绘数据。
2、不锈钢双盘式浮顶施工安装图。
3、《立式圆筒形钢制焊接油罐施工及验收规范》GB50341-2014。
4、《储罐用组装式铝制内浮顶安装验收技术条件》70B107-1997。
5、《石油化工立式圆筒形式钢制储罐施工技术规范》 SH/T3530-2011。
6、炼化板块《进入受限空间安全管理规定》7、《石油化工建设工程施工安全技术规范》 GB50484-2008三、施工准备1,技术准备1.1 图纸会审及设计交底完,熟悉设计标准及施工验收规范,领会设计意图。
对图纸会审形成的结论,作为过程控制文件指导施工。
1.2 编制施工方案并报监理业主公司审批,经批准的施工方案在施工中必须严格执行,不得随意修改。
实际施工中由于施工条件发生变化必须对施工方案进行修改时,编制补充施工方案,并报审。
1.3 施工前对作业人员进行技术交底,做好施工前的技术培训。
1.4浮盘安装前应对罐内气体取样分析,确保在安全的情况下,方能进罐安装。
2,现场准备2.1 油罐人孔和采光孔盖全部打开,油气浓度检测合格,在确保安全的条件下才能进入施工。
2.2组装使用的电器应符合防爆要求,必须有安全用电保护措施,进罐人员一律不准穿带有铁钉的鞋。
大型内浮顶储罐固定拱顶的整体吊装

3 . 吊装加强圈组装和 网壳起 吊
传统 的储罐倒装法施工 ,是在完成项 圈壁板组 装焊 接后 ,进行 固定 顶的组焊 ,随后利用气顶 升 、倒链 吊装
繁琐 ,液压顶升设备周转 比较 困难等缺点 ;相对于整体 正装法而 言 ,克服 了在2 0 米高空搭设组装平 台的缺点 , 使 得施 工 的安全性 得 到保 障 ,节 约 了大量 临时设施 材 料 ,缩短施工周期 。
2 根斜撑 ,以确保支撑体 系的稳 定性 。
图5 涨 圈及 吊点 设 置
图6 倒 链 挂 点 设 置
Hale Waihona Puke 网壳组装完成后 ,着手准备起 吊 ,即固定顶倒装法 施工 。起 吊前应在网壳下方装配由2 根2 8 号槽钢对拼组成 的涨圈 ,以维持起 吊过程 中网壳 的整体性和稳定性 ,同
时在涨圈上设置 电动倒链的 吊点 ,如图5 所示 。将每根 网
I N S T A L L AT I O N
45
2 . 网壳 组 装
拱形双 向子午线 网壳 由8 2 根网杆 组成 ,上 、下层各 4 l 根 ,单根最长6 6 . 2 米 。待支撑体 系布置完 成后 ,即可
进行 网壳 的组装 。 ‘ 网杆 长度在5 0 米 以上 有5 8 根 ,分3 段 吊装 ;长 度在 5 0 米 以下有2 4 根 ,分2 段 吊装 。 由于 网壳是 在浮盘 板上 组装 ,其边缘部分 的网杆 尚不 能和设计 的顶 部倒锥 体连
参考资料
门】《 立式圆筒形钢制焊接储罐施工及验收规范 》 G B 5 0 1 2 8 ~ 2 0 0 5 【 2 】 左涛 《 大型油气储罐的结构型式与变化趋势 》
或液压顶升等方法将 固定顶 和壁板整 体 由低 到高逐圈升 高 。这种 施工 方法 ,储 罐 的整个 施工 过程 均在 地 面进 行 ,安全性 比较高 。本工程 中储罐 的施工 ,罐体采 用正 装法 的施工工艺 ,仅 固定顶 的做法借 鉴倒装 法的工艺 , 即在 内浮盘 ( 相 当于地 面 ) 上进行 网壳及部 分蒙皮 板的 组装 ,然后利用 电动倒链起 吊至顶 圈壁板 ,按设计 要求
拱顶罐改造为内浮顶施工方案及流程
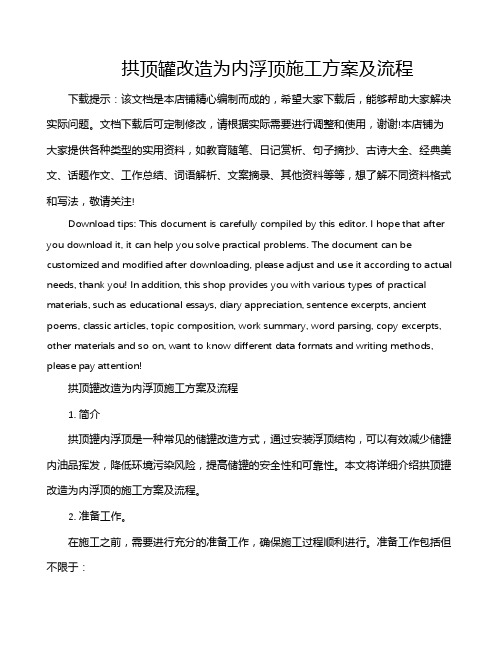
拱顶罐改造为内浮顶施工方案及流程下载提示:该文档是本店铺精心编制而成的,希望大家下载后,能够帮助大家解决实际问题。
文档下载后可定制修改,请根据实际需要进行调整和使用,谢谢!本店铺为大家提供各种类型的实用资料,如教育随笔、日记赏析、句子摘抄、古诗大全、经典美文、话题作文、工作总结、词语解析、文案摘录、其他资料等等,想了解不同资料格式和写法,敬请关注!Download tips: This document is carefully compiled by this editor. I hope that after you download it, it can help you solve practical problems. The document can be customized and modified after downloading, please adjust and use it according to actual needs, thank you! In addition, this shop provides you with various types of practical materials, such as educational essays, diary appreciation, sentence excerpts, ancient poems, classic articles, topic composition, work summary, word parsing, copy excerpts, other materials and so on, want to know different data formats and writing methods, please pay attention!拱顶罐改造为内浮顶施工方案及流程1. 简介拱顶罐内浮顶是一种常见的储罐改造方式,通过安装浮顶结构,可以有效减少储罐内油品挥发,降低环境污染风险,提高储罐的安全性和可靠性。
大型立式储罐铝制内浮顶整体支撑施工工法
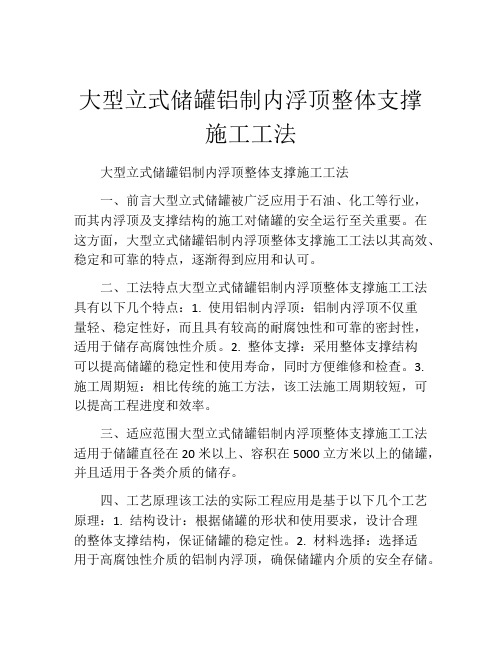
大型立式储罐铝制内浮顶整体支撑施工工法大型立式储罐铝制内浮顶整体支撑施工工法一、前言大型立式储罐被广泛应用于石油、化工等行业,而其内浮顶及支撑结构的施工对储罐的安全运行至关重要。
在这方面,大型立式储罐铝制内浮顶整体支撑施工工法以其高效、稳定和可靠的特点,逐渐得到应用和认可。
二、工法特点大型立式储罐铝制内浮顶整体支撑施工工法具有以下几个特点:1. 使用铝制内浮顶:铝制内浮顶不仅重量轻、稳定性好,而且具有较高的耐腐蚀性和可靠的密封性,适用于储存高腐蚀性介质。
2. 整体支撑:采用整体支撑结构可以提高储罐的稳定性和使用寿命,同时方便维修和检查。
3. 施工周期短:相比传统的施工方法,该工法施工周期较短,可以提高工程进度和效率。
三、适应范围大型立式储罐铝制内浮顶整体支撑施工工法适用于储罐直径在20米以上、容积在5000立方米以上的储罐,并且适用于各类介质的储存。
四、工艺原理该工法的实际工程应用是基于以下几个工艺原理:1. 结构设计:根据储罐的形状和使用要求,设计合理的整体支撑结构,保证储罐的稳定性。
2. 材料选择:选择适用于高腐蚀性介质的铝制内浮顶,确保储罐内介质的安全存储。
3. 施工步骤:按照施工工艺要求,依次进行基础施工、支撑结构安装、内浮顶安装和连接等工序,确保施工质量。
五、施工工艺 1. 基础施工:根据设计要求进行地基处理、基础浇筑,确保储罐的稳定性和承重能力。
2. 支撑结构安装:根据结构设计图纸进行支撑结构的安装,保证整体支撑的合理布局和稳定性。
3. 内浮顶安装及连接:将铝制内浮顶按照设计要求放置在支撑结构上,并与储罐顶部连接,然后进行密封处理。
4. 安全检查:进行工程的安全检查,确保施工质量达到设计要求和相关标准。
六、劳动组织在该工法下,施工需要组织一支专业施工队伍,包括具备相关资质和经验的工程师、技术人员和施工工人,以确保施工过程的顺利进行。
七、机具设备在该工法中,需要使用一系列机具设备来支持施工工艺,包括起重机械、焊接设备、支撑模板等,以确保施工质量和安全。
3000立方和2000立方储罐施工方案(精校版本)

目录1.工程概况及编制依据 (2)2、施工准备 (2)3、施工程序 (3)4、储罐的工厂化预制 (6)5、储罐安装 (11)6、焊接 (16)7、储罐整体组装检查 (18)8、贮罐充水试验 (18)9、防腐 (20)10、内浮顶安装 (20)11、内浮顶升降试验 (20)12、质量控制与检验计划 (20)13、安全保证措施 (23)14、劳动力计划 (24)15、施工设备及主要施工手段用料 (25)16、交工验收 (26)17、工作危险性分析(JHA)报告 (28)18、储罐专业质量检验计划 (31)19.储罐施工平面布置图 (34)1. 工程概况及编制依据1.1 工程概述本方案适用于宁夏石嘴山惠农油库贮罐区8台3000m3内浮顶油罐、4台2000m3内浮顶油罐的现场预制、组装。
储罐规格如下表:序号名称内径材料重量(公斤)备注1 3000m3内浮顶罐Φ18000 Q235-B 84945 铝浮盘重约1.62吨2 2000m3内浮顶罐Φ15500 Q235-B 62594 铝浮重约1.27吨1.2 编制依据GB50128-2005 《立式圆筒形钢制焊接油罐施工及验收规范》。
SH/T3530-2001 《石油化工立式圆筒形钢制储罐施工工艺标准》。
GB50236-98 《现场设备、工业管道焊接施工及验收规范》。
JB4708-2000 《钢制压力容器焊接工艺评定》。
JB/T4709-2000 《钢制压力容器焊接规程》。
JB4730-2005 《压力容器无损检测》。
施工图纸。
2. 施工准备2.1 施工技术准备(1)对施工图进行三级会审,并做详细记录,施工方案经业主批准且进行详细安全技术交底,施工记录表格齐全。
(2)工程所用材料,均要有合格的质量证明书。
若对材质合格证明书或货物有疑问时须进行复验,无合格证的材料不得使用。
检查材料的表面质量,表面应无严重锈蚀、损伤及表面裂纹、分层、重皮等缺陷。
(3)做好基础检查验收工作,基础应符合设计和规范要求,并结合土建交工资料进行检查和验收,做好检查验收记录。
浮仓内浮顶贮罐施工方案

浮仓内浮顶贮罐施工方案一、前言浮仓(浮式屋顶)内浮顶贮罐是一种常见的储罐形式,广泛应用于石油、化工、食品、饮料等行业。
本文将详细介绍浮仓内浮顶贮罐的施工方案。
二、施工准备工作1.施工组织设计:根据具体施工情况,制定施工组织设计方案,明确负责人和施工人员的职责。
2.打样审批:根据设计图纸和规范要求,制作浮式屋顶和浮顶,进行样板审批。
3.施工图纸和材料准备:根据设计要求,制定施工图纸,并准备好所需材料,如钢材、焊材、涂料等。
4.原材料检验:对所购买的原材料进行检验,确保其质量符合要求。
5.施工设备准备:准备好所需施工设备和机具,如起重机、电动焊机、气瓶等。
6.现场布置:对施工现场进行布置,划定区域,确保施工安全和顺利进行。
三、施工步骤1.钢结构制作:根据设计图纸,制作浮式屋顶的钢结构。
包括制作顶拱构件、校正并焊接顶拱,制作安装导轨等。
2.钢结构安装:将制作好的钢结构进行现场安装,按照设计要求进行组装,并进行调整和校正,确保各构件的精度和平整度。
3.焊接工艺:根据焊接工艺规程,进行钢结构的焊接。
确保焊缝的质量和可靠性。
4.涂装防腐:对已焊接好的钢结构进行涂装和防腐处理,保护其免受腐蚀和氧化。
选用耐酸碱的涂料,确保涂装层的质量。
5.安装浮顶:将制作好的浮顶安装在钢结构之上,并进行调整和校正,确保浮顶与钢结构的接触紧密、平整度良好。
6.导轨安装:安装导轨,确保浮顶的顺畅移动。
7.测量调整:对浮顶进行测量和调整,确保其水平度和平整度满足要求。
8.清洁挂钩:安装清洁挂钩,方便后续清洁维护工作。
9.试运行:对浮仓内浮顶贮罐进行试运行,检查其运行是否正常。
四、安全措施1.施工现场设置警示标志,划定施工区域,保持施工现场的秩序和安全。
2.使用符合规范要求的施工设备和机具,严格按照操作规程进行施工。
3.对施工人员进行安全培训和技术指导,确保其具备相关的安全知识和操作技能。
4.施工期间,严禁酒后上岗和疲劳驾驶,确保施工人员的身体健康和精力充沛。
内浮顶储罐施工方案
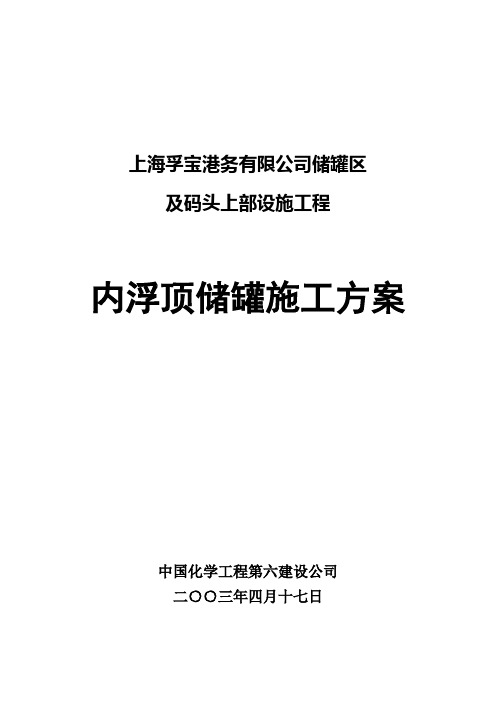
上海孚宝港务有限公司储罐区及码头上部设施工程内浮顶储罐施工方案中国化学工程第六建设公司二○○三年四月十七日目录1 编制说明2 编制依据3 施工方法及技术措施3.1 施工程序3.2 预制加工3.3 组装焊接3.4 罐体检验及试验3.5 罐体防腐施工4 劳动力计划5 工机具使用计划6 施工手段用料计划7 质量控制措施8 安全及文明施工1 编制说明上海孚宝港务有限公司储罐区共有内浮顶罐13台,其最大容积为5600m3。
罐体为普通C·S钢板材料,单台最大重量193.6吨,全部采用现场制造,各浮顶罐特性见下表。
2 编制依据2.1 上海孚宝港务有限公司包储顶目初步设计;2.2 《立式圆筒形钢制焊接油罐施工及验收规范》GBJ128-902.3 《现场设备、工业管道焊接工程施工及验收规范》GB50236-982.4 《石油化工立式圆筒形钢制焊接油罐设计规范》SH3064-923 施工方法及技术措施罐体制作采用倒装法施工,即采用先底、顶,后罐壁的方法,具体施工过程和控制措施如下:3.1 施工程序材料验收→放样下料→预制→基础验收→底板组焊及试验检验→最顶层带板组焊→拱顶组焊→倒数第二层带板组焊→钢结构、梯子平台及附件施工→罐体试验→内浮顶安装→罐体防腐→竣工验收。
3.2 基础验收3.2.1 基础表面尺寸要求见表3-1。
3.2.2 以基础中心为圆心,以不同直径作同心圆,将各圆周分成若干等分,在等分点测量基础表面的标高,同一圆周上的测点,其测量标高与计算标高之差不得大于12mm;检查基础表面凹凸度的同心圆直径及测量点数,见表3-2。
基础表面尺寸允许偏差表3-1基础表面凹凸度的同心圆直径及测量点数3.3.1 罐顶板预制3.3.1.1 罐顶下料依据施工图下料,采用氧乙炔焰半自动切割机切割。
罐顶弧形板采用胎具压制加工成形,现场拼装。
因为该板压制后有一定的反弹,该胎具的半径应比拱顶板的弧形半径小20mm。
3.3.1.2 罐顶弧形板每隔1米的距离加压一次,成型后的拱顶板必须用长L=2m的弧形样板检查,不合格的部位需重新压制。
浮顶储罐施工方案

浮顶储罐施工方案一、工程概况与目标本施工方案针对浮顶储罐的建设过程,涵盖了从施工准备到工程验收与交付的全部流程。
本工程旨在安全、高效地建设一座质量稳定、功能完备的浮顶储罐,以满足使用方的存储需求。
二、施工准备工作人员配置:组建专业的施工团队,包括项目经理、技术负责人、安全员、质检员等关键岗位。
材料采购:根据设计要求,采购合格的材料和构配件,并确保其质量和数量满足施工需求。
设备准备:准备必要的施工机械和设备,如挖掘机、吊车、焊接设备等。
现场勘查:对施工现场进行详细勘查,了解地形、地质、气象等条件,为施工提供基础数据。
三、基础施工与验收基础施工:按照设计要求进行基础施工,确保基础平整、稳固。
基础验收:基础施工完成后,进行基础验收,确保基础质量符合设计要求。
四、浮顶储罐安装罐体安装:按照设计图纸和工艺要求,进行罐体的安装工作。
浮顶安装:罐体安装完成后,进行浮顶的安装工作,确保浮顶与罐体连接紧密、密封良好。
五、防腐与保温处理防腐处理:对罐体进行防腐处理,以防止罐体受到腐蚀影响。
保温处理:根据使用需求,对罐体进行保温处理,以减少能源浪费。
六、安全与环保措施安全管理:制定详细的安全管理制度和操作规程,确保施工过程安全可控。
环保措施:采取有效的环保措施,减少施工对环境的影响。
七、质量控制与检验质量控制:建立严格的质量管理体系,确保施工质量符合设计要求。
检验与测试:对施工过程进行全程检验与测试,确保工程质量符合要求。
八、工程验收与交付工程验收:工程完成后,进行全面的工程验收,确保工程质量和使用功能符合设计要求。
交付与使用:工程验收合格后,进行交付使用,并提供必要的技术支持和售后服务。
本施工方案旨在确保浮顶储罐建设过程的安全、高效和质量稳定。
我们将严格按照施工方案进行操作,确保工程顺利完成,并满足使用方的需求。
10000M3储罐施工方案
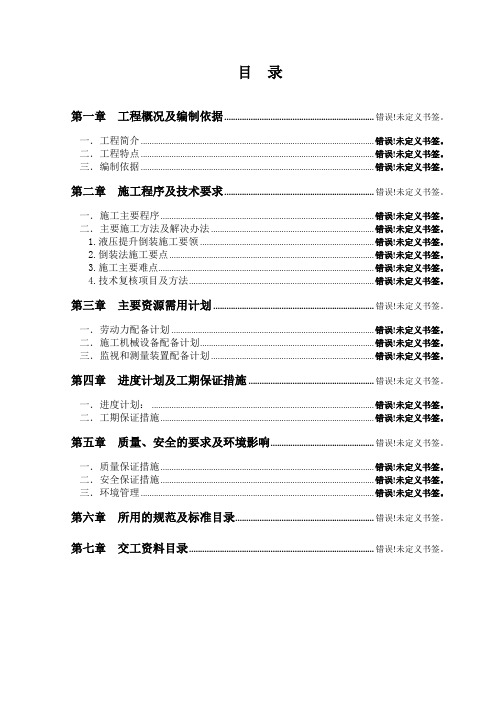
目录第一章工程概况及编制依据 .................................................................... 错误!未定义书签。
一.工程简介.......................................................................................................... 错误!未定义书签。
二.工程特点.......................................................................................................... 错误!未定义书签。
三.编制依据.......................................................................................................... 错误!未定义书签。
第二章施工程序及技术要求 .................................................................... 错误!未定义书签。
一.施工主要程序................................................................................................. 错误!未定义书签。
二.主要施工方法及解决办法 .......................................................................... 错误!未定义书签。
1.液压提升倒装施工要领 ............................................................................... 错误!未定义书签。
3000立方和2000立方储罐施工方案

目录1.工程概况及编制依据工程概述本方案适用于宁夏石嘴山惠农油库贮罐区8台3000m3内浮顶油罐、4台2000m3内浮顶油罐的现场预制、组装。
编制依据GB50128-2005《立式圆筒形钢制焊接油罐施工及验收规范》。
SH/T3530-2001《石油化工立式圆筒形钢制储罐施工工艺标准》。
GB50236-98《现场设备、工业管道焊接施工及验收规范》。
JB4708-2000《钢制压力容器焊接工艺评定》。
JB/T4709-2000《钢制压力容器焊接规程》。
JB4730-2005《压力容器无损检测》。
施工图纸。
2.施工准备施工技术准备(1)对施工图进行三级会审,并做详细记录,施工方案经业主批准且进行详细安全技术交底,施工记录表格齐全。
(2)工程所用材料,均要有合格的质量证明书。
若对材质合格证明书或货物有疑问时须进行复验,无合格证的材料不得使用。
检查材料的表面质量,表面应无严重锈蚀、损伤及表面裂纹、分层、重皮等缺陷。
(3)做好基础检查验收工作,基础应符合设计和规范要求,并结合土建交工资料进行检查和验收,做好检查验收记录。
基础验收合格并经业主同意方可进行罐底的施工。
(4)预制加工前要根据图纸、材料规格及施工规范的要求绘制贮罐排版图。
所有切割成型的专用钢板和罐顶支撑构件,在包装起运前按制造图注上标记。
施工机具准备按施工机具计划配备施工机械,并保证机具性能完好,机械运转记录随时填写。
施工现场准备施工场地应设置:材料、半成品存放场地;加工场地、办公设施等。
场地应平整,道路应畅通,临时用水、用电线路应按要求敷设。
3.材料的采购、验收、保管3.1材料的采购应根据储罐的排版图合理采购材料,既要考虑到缩短施工时间,节约施工材料,节省人力资源,又要考虑到施工的难易程度和施工质量控制。
材料供应厂家应是国家级大型企业、全国知名企业。
3.2材料入场后应按照相关的国家规范进行验收。
尤其是钢板的验收必须严格按照GB/709-2006进行验收,钢板的外形几何尺寸、不平整度、钢板的外观、厚薄、短面的变形情况、锈蚀情况进行检查。
内浮顶储罐施工方案
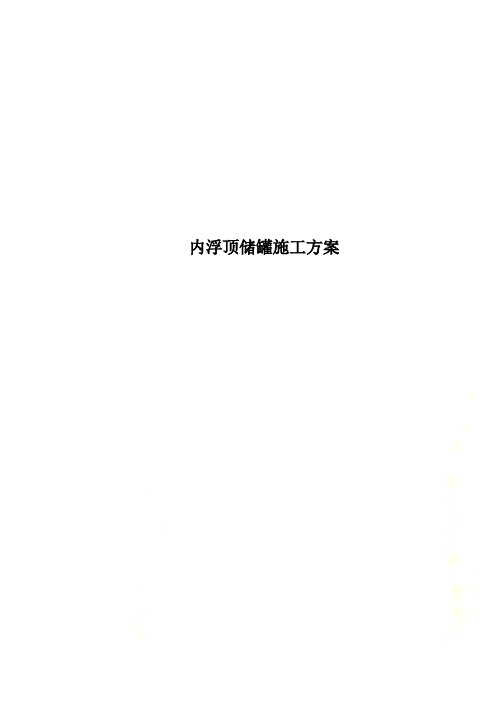
内浮顶储罐施工方案(六)储罐施工方案1.工程概况中油福州油品码头及库区新建工程共有成品油储罐7具,消防水罐2具,其中柴油罐为3具5000立方米拱顶罐,汽油罐为2具3000立方米和2具5000立方米内浮顶罐,消防水罐为2具1000立方米拱顶罐。
该工程7具罐与预留的一具罐组成了较为紧凑的成品油罐区,便于集中流水施工。
消防水罐则分布于成品油罐区外部。
2.编制依据由中国石油天然气华东勘察设计研究院设计的施工图:2003设-401、1000m3拱顶储罐2003设-407、3000m3内浮顶储罐2003设-403、5000m3内浮顶储罐2003设-405、5000m3拱顶储罐GB128-90《立式圆筒形钢制焊接储罐施工及验收规范》。
SH3530-93《石油化工立式圆筒形钢制储罐施工工艺标准》。
SH3528-93《石油化工钢储罐地基与基础施工及验收规范》。
SHJ22-90《石油化工企业设备与管道涂料防腐蚀设计与施工规范》。
JB4730-94《无损检测》。
3.储罐设计数据4.罐体数据(1)1000立方米拱顶罐罐体数据一览表:(单具总重28850Kg)(2)3000立方米内浮顶罐罐体数据一览表:(单具总重76797Kg)(3)5000立方米拱顶罐、内浮顶罐罐体数据一览表:(单具总重119731Kg)5.施工方法5.1施工方法采用群桅起升倒装法:5.2施工用料:每个罐所需倒链和桅杆如下表所示:5.3材料验收储罐所选用的材料和附件,应具有质量合格证明书当无质量合格证明书或质量合格说明书有疑问时,应对材料和附件进行复验。
储罐焊条选用J422、J427电焊条,焊条应具有质量合格说明书。
储罐所选用的钢板,必须逐张进行外观检查,其表面质量应符合现行的相应钢板标准的规定。
钢板表面锈蚀减薄量,划痕深度与钢板实际偏差之和,应符合下表规定。
5.4预制5.4.1罐底预制(1)罐底板预制前应根据实际来料绘制排版图。
并根据图纸放大样,检查无误后方可下料。
浮盘安装施工方案

一、工程概况本项目为某企业新建的2000立方米内浮顶储罐,用于储存石油化工产品。
浮盘是储罐的关键部件,其安装质量直接影响到储罐的安全运行。
为确保浮盘安装质量,特制定本施工方案。
二、施工准备1. 技术准备(1)组织施工人员进行浮盘安装技术培训,提高施工人员的技术水平。
(2)熟悉相关规范、标准和施工图纸,确保施工过程符合要求。
2. 材料准备(1)准备浮盘、膨胀螺栓、密封圈、支撑环等安装所需材料。
(2)检查材料质量,确保材料符合设计要求。
3. 工具准备(1)准备液压提升机、吊车、卷扬机、扳手、螺丝刀等安装工具。
(2)检查工具性能,确保工具完好。
4. 人员准备(1)组织施工队伍,明确各岗位人员职责。
(2)配备具有相关资质的施工人员,确保施工质量。
三、施工工艺1. 浮盘安装前准备(1)清理储罐内部,确保无杂物。
(2)检查储罐壁板、顶板等部位,确保无损伤。
(3)检查浮盘外观,确保无裂纹、变形等缺陷。
2. 浮盘安装步骤(1)将浮盘放置在储罐内,调整位置,使其与储罐壁板对齐。
(2)在浮盘底部安装膨胀螺栓,确保螺栓与储罐壁板紧密连接。
(3)在浮盘上安装密封圈,确保密封性能。
(4)将浮盘支撑环安装在浮盘上,调整支撑环位置,使其与储罐壁板平行。
(5)使用液压提升机将浮盘提升至设计高度,确保浮盘与储罐壁板垂直。
(6)检查浮盘安装质量,确保浮盘与储罐壁板连接牢固,密封性能良好。
3. 浮盘安装后检查(1)检查浮盘安装位置,确保浮盘与储罐壁板垂直。
(2)检查浮盘与储罐壁板连接牢固,无松动现象。
(3)检查密封圈密封性能,确保无泄漏。
四、施工注意事项1. 施工过程中,严格按照施工图纸和规范要求进行操作。
2. 施工人员应穿戴好安全防护用品,确保施工安全。
3. 施工过程中,注意观察浮盘安装质量,发现问题及时处理。
4. 施工完成后,进行验收,确保浮盘安装质量符合要求。
五、施工进度安排1. 施工准备:3天2. 浮盘安装:5天3. 浮盘安装后检查:1天4. 施工验收:1天总计:10天六、质量保证措施1. 施工过程中,严格执行施工规范和质量标准。
- 1、下载文档前请自行甄别文档内容的完整性,平台不提供额外的编辑、内容补充、找答案等附加服务。
- 2、"仅部分预览"的文档,不可在线预览部分如存在完整性等问题,可反馈申请退款(可完整预览的文档不适用该条件!)。
- 3、如文档侵犯您的权益,请联系客服反馈,我们会尽快为您处理(人工客服工作时间:9:00-18:30)。
上海孚宝港务有限公司储罐区及码头上部设施工程内浮顶储罐施工方案中国化学工程第六建设公司二○○三年四月十七日目录1 编制说明2 编制依据3 施工方法及技术措施3.1 施工程序3.2 预制加工3.3 组装焊接3.4 罐体检验及试验3.5 罐体防腐施工4 劳动力计划5 工机具使用计划6 施工手段用料计划7 质量控制措施8 安全及文明施工1 编制说明上海孚宝港务有限公司储罐区共有内浮顶罐13台,其最大容积为5600m3。
罐体为普通C·S钢板材料,单台最大重量193.6吨,全部采用现场制造,各浮顶罐特性见下表。
2 编制依据2.1 上海孚宝港务有限公司包储顶目初步设计;2.2 《立式圆筒形钢制焊接油罐施工及验收规范》GBJ128-902.3 《现场设备、工业管道焊接工程施工及验收规范》GB50236-982.4 《石油化工立式圆筒形钢制焊接油罐设计规范》SH3064-923 施工方法及技术措施罐体制作采用倒装法施工,即采用先底、顶,后罐壁的方法,具体施工过程和控制措施如下:3.1 施工程序材料验收→放样下料→预制→基础验收→底板组焊及试验检验→最顶层带板组焊→拱顶组焊→倒数第二层带板组焊→钢结构、梯子平台及附件施工→罐体试验→内浮顶安装→罐体防腐→竣工验收。
3.2 基础验收3.2.1 基础表面尺寸要求见表3-1。
3.2.2 以基础中心为圆心,以不同直径作同心圆,将各圆周分成若干等分,在等分点测量基础表面的标高,同一圆周上的测点,其测量标高与计算标高之差不得大于12mm;检查基础表面凹凸度的同心圆直径及测量点数,见表3-2。
基础表面尺寸允许偏差表3-1基础表面凹凸度的同心圆直径及测量点数表3-23.3 预制加工:施工前对罐体需要进行预制,具体如下:3.3.1 罐顶板预制3.3.1.1 罐顶下料依据施工图下料,采用氧乙炔焰半自动切割机切割。
罐顶弧形板采用胎具压制加工成形,现场拼装。
因为该板压制后有一定的反弹,该胎具的半径应比拱顶板的弧形半径小20mm。
3.3.1.2 罐顶弧形板每隔1米的距离加压一次,成型后的拱顶板必须用长L=2m的弧形样板检查,不合格的部位需重新压制。
成型后的顶板需放置在专用胎具上。
3.3.2 壁板加工3.3.2.1 壁板加工采用半自动氧乙炔焰切割机加工,壁板加工尺寸根据实际采购的钢板板幅进行排板,板边加工采用机械刨边。
3.3.2.2 壁板采用卷板机卷制,卷制成型的板需用弦长L=2m的弧形样板检验。
3.3.2.3 卷制合格后的壁板放置在专用胎具上,运至施工现场。
3.3.3 罐底板加工3.3.3.1 罐底板采用半自动氧乙炔焰切割机加工,尺寸依据实际采购的材料板幅进行排版,并将下好料的板按排版图编号。
排版形式依据罐底施工图进行。
3.3.3.2 边缘板按图示尺寸加工成型。
3.3.4 管口及梯子平台预制3.3.4.1 管口及梯子平台按要求预制完成后现场安装。
3.3.5 预制分工3.3.5.1 下料、煨弯、预焊在现场平台上进行。
3.3.5.2 卷板、剪板均采用机械进行加工。
3.3.6 相关技术说明3.3.6.1 底板在预制时的排料直径应按设计直径放大1‰~2‰(取2‰)下料。
3.3.6.2 单块罐顶板预制拼装采用对接,每块顶板应在胎具上成型,焊好后脱胎。
3.3.6.3 壁板的预制应根据排料图的规格和尺寸进行下料,预制的顺序应从最顶层壁板开始依次预制。
下料时每圈板的周长应按计算周长增加150mm的切割余量,以便调整罐的壁板周长。
3.4 组装焊接3.4.1 罐底板组装3.4.1.1 底板组装分两部分进行:边缘板组装和中幅板组装。
3.4.1.2 罐组装前的设备基础必须满足设计和规范要求,并通过检查验收。
3.4.1.3 在罐底板组装前的混凝土基础上,对边缘板的位置放线,才能就位,板号及位置应与施工图纸相符。
3.4.1.4 中幅板全部是搭接,为防止焊接变形,应由外到内先焊短焊缝,后焊长焊缝,初层焊道应采用分段倒退焊或跳焊法。
3.4.2 液压提升机安装3.4.2.1 提升机分两部分:1、液压油泵系统。
2、液压提升架。
3.4.2.2 顶升机有关参数(见表3-2)。
液压顶升机参数表3-33.4.2.3 负荷分析:罐壁重:Q1=141300 Kg顶板重:Q2=33277Kg梯子、平台、栏杆重:Q3=5744 Kg胀圈、弧型板及其他材料:Q4=3800 Kg∑Q=Q1+Q2 +Q3 + Q4 =184121 Kg顶升机总额定顶升负荷288000kg,顶升机实际负荷为额定负荷的63.9%。
顶升机使用台数为18台,沿圆周均布间距以5m左右为宜,每台顶升机负荷10229Kg。
3.4.2.4 需要提升的重量为184.12吨,该提升系统能力为288吨,其布置如下(见图3-1、图3-2)。
3.4.3 罐壁最顶层带板组装施工顺序为先组装最顶层及倒数第二层带板,组装完后组装罐包边角钢,吊装采用25吨汽车吊。
用临时工装卡具调整壁板之间的间隙,防止焊接变形。
3.4.4 罐顶板制作安装3.4.4.1 罐顶板胎具制作与安装·胎具立柱除中心柱和位于φ2圈内的支柱用φ89*4钢管外,其余立柱全部采用φ76*3.5钢管制作,支柱布置示意图见下图所示。
立柱长度按下式确定:L=H+H拱-(h+△+δ+δA)式中:H-最上两层壁板的实际高度,依据罐的制作排板图H拱-罐的拱顶高度h-罐不同位置的坡度增高,由顶圈位置计算确定,计算公式为:h1=R-√R2-(φ/2)2 ;Δ-各立柱位置的坡度增高,由立柱位置确定δ-顶圈板板厚,中心顶圈厚度10mm,其余8mmδA-顶板筋板宽度·所有储罐垫板一律采用[12.6槽钢,与底板相连的垫板一律用δ=10mm(100*100)钢板。
立柱根数以位于同一圆周内的立柱间距不大于2m来确定。
·胎具斜支撑:斜支撑用于各立柱的稳定支撑,安装时由内向外支顶,每根立柱一般设置2根斜支撑,斜支撑用φ76*3.5钢管,其长度约等于立柱长度的1.4倍。
·胎具顶圈:顶圈由钢板下料制作成环,安装于立柱顶部,圈宽100mm,厚10mm和8mm(中心顶圈厚10mm)。
顶圈制作尺寸现场安装时决定。
为了保护储罐底板,所有与底板连接的立柱和支撑底部均设垫板(δ=10mm、100*100mm2钢板)与底板点焊。
3.4.4.2 罐顶板由中心顶板和多块半瓜片板组成,焊缝均为上、下、左、右搭接焊缝,内部用加强筋板及连接板连接成一整体。
3.4.4.3 中心柱安装,如下图:3.4.4.4 拱顶拼装在现场进行,吊装时采用对称吊点进行,防止中心立柱受力不均匀。
3.4.5 在罐壁倒数第二层至最下层带板顶升组装焊接时,罐各带板间附件安装的组装顺序如下:围板→立缝焊接→顶升→环缝点焊→最后一道立缝组对焊接→环缝焊接→松开起升系统并降低至起始位置→切割胀圈→补焊部分未焊接的部位→焊接胀圈。
3.4.5.1 胀圈制作安装示意图如图3-4.3.4.5.2 倒数第二层至最下层带板依次组装焊接,每带板焊接完成后,根据要求经检验垂直度、椭圆度、直径、焊缝外观及焊缝内部质量等合格后,才能进行提升。
提升前,各带板上的预焊件必需完成,且经检验合格。
3.4.5.3 由于起升随着高度的增加重量会增加,在每次起升前应该仔细检查提升机的外观及焊缝,检查油压系统、千斤顶及锁紧装置是否有泄露、裂纹等情况。
3.4.5.4 操作平台的搭设:为方便罐体组对焊接,围绕罐基础四周应搭设牢固的操作平台,高度以方便操作为宜,一般为离罐底800mm~1200mm,内外搭设。
3.4.6 内浮顶安装(由于资料不全,待资料齐全后补充)。
3.4.7 梯子平台安装:平台安装难度不大,但是部分结构需要在吊车允许的范围内提前安装。
3.4.8 罐体开孔及管道安装按照图纸的方位要求进行施工,尽量避免由于焊接变形造成罐体局部塌陷。
3.4.9 焊接及及检验3.4.9.1 储罐本体焊缝采用CO2气体保护焊进行焊接施工,其余部分(梯子、平台、栏杆等)采用手工电弧焊焊接,焊丝选用H08Mn2A,电焊条选用J422(E4303)。
3.4.8.2 焊接工艺参数见表3-3焊接工艺参数表3-33.4.9.3 焊缝外观检查·底层罐壁内侧与罐底边缘板连接的角焊缝,应焊成下凹形圆滑过渡的不等边角焊缝,并打磨光滑。
·罐壁内侧纵、环焊缝余高不得大于1mm,且不允许有损伤内浮盘密封件的缺欠存在。
3.4.9.4 罐体的对接焊缝应进行射线探伤,其中底板对接焊缝100%探伤,底层罐壁的纵焊缝和底层罐壁与第二层罐壁之间的T型焊缝应100%探伤,其余焊缝探伤率为T型焊缝15%,纵焊缝10%,环焊缝1%,GB3323-87 Ⅲ级合格。
未进行无损探伤的焊缝应进行煤油渗透试验。
3.5 罐体检验及试验3.5.1 包括以下几个内容:1、罐底的真空试验,2、罐盛水试验。
3.5.2 罐底的真空试验:3.5.2.1 罐底板真空试验前的准备工作·罐底板真空箱试验在罐底板焊缝全部焊接完成且焊缝经过无损检验合格后进行。
·施工现场需要制作真空箱二个,尺寸如下:·现场需要准备真空泵2台,真空度范围为:-0.2Mpa~0.05 Mpa。
·真空箱试验压力负压值不得高于–53Kpa 。
3.5.2.2 真空箱试验方法·试验前,将底板焊缝表面及焊缝两侧50mm范围内,用钢丝刷处理干净。
焊缝清理干净后,用发泡剂(肥皂水或洗涤灵等)均匀涂刷在待试验焊缝表面。
·在待试验焊缝上部罩上真空箱,真空箱与贮罐底板接触部位用腻子进行密封。
·连接好真空泵,检查真空表。
·启动真空泵,观察真空表的压力;当真空度达到试验真空度时,关闭阀门、关闭真空泵,借助手电照明仔细检查试验焊缝是否发泡,如果没有泡沫出现,则认为该部位焊缝真空箱试验合格;否则,认为该试验部位焊缝真空箱试验失败,在该部位作好标记,对该焊缝进行返修,返修工艺与正式焊接工艺相同,返修合格后,进行无损检查,检查合格后,再次进行真空箱试验,直至合格。
·用同样的试验方法检查所有的底板焊缝。
3.5.3 罐盛水试验罐体盛水试验参数一览表表3-43.5.3.1 试验前应具备的条件·对贮罐的全部接管、附件、加强焊接部位的焊接点已经全部进行无损检查,并且合格。
·所有接管的加强板已经经过严密性试验。
·罐底板焊缝已经经过真空试验合格。
·进水管道阀门已经按照试验图施工完毕。
·施工人员已经到位,并且业经技术交底。
·所有的锚固件已经安装完,重新经过检查没有发现异常。
3.5.3.2 罐充水试验(检验罐壁严密性和强度),具体方法如下:在罐内充水高度大于1米后,将所有开口封闭继续充水,罐内空气达到设计规定的正压试验数据后,暂停充水,在罐顶焊缝表面上涂抹发泡剂(肥皂水或洗涤灵),如未发现气泡,且罐顶无异常变形,罐顶的严密性和强度试验即为合格。