常见焊接缺欠的产生原因和防止措施教程文件
焊缝缺欠及其预防措施

焊缝缺欠及其预防措施一、焊缝表面尺寸不符合要求1、缺欠特征焊缝表面高低不平、焊缝宽窄不齐、焊缝尺寸过大或过小、角焊缝单边以及焊脚尺寸不符合要求,均属于表面尺寸不符合要求,如下图所示。
▲焊缝表面尺寸不符合要求2、产生原因焊件坡口角度不对,装配间隙不均匀,焊接速度不当或运条手法不正确,焊条和角度选择不当或改变,埋弧焊焊接工艺选择不正确等都会造成该种缺陷。
3、预防措施选择适当的坡口角度和装配间隙;正确选择焊接参数,特别是焊接电流值,采用恰当的运条手法和角度,以保证焊缝成形均匀一致。
二、焊接裂纹在焊接应力及其他致脆因素的共同作用下,焊接接头局部地区的金属原子结合力遭到破坏而形成的新界面所产生的缝隙称为焊接裂纹,它具有尖锐的缺口和较大的长宽比特征。
1、热裂纹缺欠特征焊接过程中,焊缝和热影响区金属冷却到固相线附近的高温区产生的裂纹为热裂纹。
(1)产生原因由于熔池冷却结晶时,受到拉应力作用而凝固的过程中,低熔点共晶体形成的液态薄层共同作用的结果。
增大任何一方面的作用,都能促使形成热裂纹。
(2)预防措施控制焊缝中的有害杂质的含量,即碳、硫、磷的含量,减少熔池中低熔点共晶体的形成。
焊缝金属中硫、磷的质量分数一般小于0.03%。
焊丝的碳质量分数不超过0.12%。
重要构件焊接应采用碱性焊条或焊剂。
控制焊接参数,适当提高焊缝形状系数,尽量避免得到深而窄的焊缝。
采用多层、多道焊,焊前预热和焊后缓冷。
正确选用焊接接头形式,合理安排焊接顺序,尽量采用对称施焊。
采用引出板将弧坑引至焊件外面,这样,即使发生弧坑裂纹也不影响焊件本身。
2、冷裂纹缺欠特征焊接接头冷却到较低温度时(对钢来说在200~300℃)产生的焊接裂纹,称为冷裂纹。
(1)产生原因主要发生在中碳钢、低合金钢和中合金高强度钢中。
原因为:焊材本身具有较大的淬硬倾向;焊接熔池中溶解了多量的氢;焊接接头在焊接过程中产生了较大的拘束应力。
(2)预防措施焊前按规定要求严格烘干焊条、焊剂,以减少氢的来源。
焊缝缺欠缺陷产生原因及防止方法共41页文档
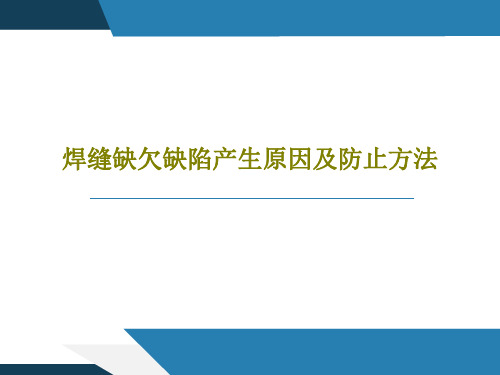
61、奢侈是舒适的,否则就不是奢侈 。——CocoCha nel 62、少而好学,如日出之阳;壮而好学 ,如日 中之光 ;志而 好学, 如炳烛 之光。 ——刘 向 63、三军可夺帅也,匹夫不可夺志也。 ——孔 丘 64、人生就是学校。在那里,与其说好 的教师 是幸福 ,不如 说好的 教师是 不幸。 ——海 贝尔 65、接受挑战,就可以享受胜利的喜悦 。——杰纳勒 尔·乔治·S·巴顿
焊缝缺欠缺陷产生原因及防止方法
1、纪律是管理关系的形式。——阿法 纳西耶 夫 2、改革如果不讲纪律,就难以成功。
3、道德行为训练,不是通过语言影响 ,而是 让儿童 练习良 好道德 行为, 克服懒 惰、轻 率、不 守纪律 、颓废 等不良 行为。 4、学校没有纪律便如磨房里没有水。 ——夸 美纽斯
5、教导儿童服从真理、服从集体,养 成儿童 自觉的 纪律性 ,这是 儿童道 德教育 最重要 的部分 。—— 陈鹤琴
谢谢!
ห้องสมุดไป่ตู้
各种焊接缺陷图解及原因预防措施

各种焊接缺陷图解及原因预防措施各种焊接缺陷图解及原因预防措施X未焊透的产生原因未焊透产生的原因主要有:坡口角度小,根部间隙过窄或钝边过厚,焊接规范选择不当电流过小、线能量小、焊接速度过快等。
1、冷裂纹冷裂纹的特征多出现在焊道与母材熔合线附近的热影响区中,多为穿晶裂纹。
冷裂纹无氧化色彩。
冷裂纹发生于或,高的含碳量和合金含量。
冷裂纹具有延迟性质,主要是延迟裂纹。
冷裂纹产生原因(和热影响区及熔合区)的淬火倾向严重,产生淬火组织,导致接头性能脆化。
含氢量较高,并聚集在处形成大量氢分子,造成非常大的局部压力,使接头脆化;磷含量过高同样产生冷裂纹。
存在较大的拉应力。
因氢的扩散需要时间,所以冷裂纹在焊后需延迟一段时间才出现。
由于是氢所诱发的,也叫氢致裂纹。
防止冷裂纹的措施选用碱性或,减少金属中氢的含量,提高金属塑性。
要烘干,焊缝及附近母材要去油、水、除锈,减少氢的来源。
工件焊前预热,焊后缓冷(大部分材料的温度可查表),可降低焊后冷却速度,避免产生淬硬组织,并可减少焊接。
采取减小焊接应力的工艺措施,如对称焊,小线能量的多层多道焊等,焊后进行清除应力的。
焊后立即进行去氢(后热)处理,加热到250℃,保温2~6h,使焊缝金属中的散氢逸出金属表面。
2、热裂纹(又称结晶裂纹)热裂纹的特征热裂纹可发生在焊缝区或热影响区,沿焊缝长度方向分布。
热裂纹的微观特征是沿晶界开裂,所以又称晶间裂纹。
因热裂纹在高温下形成,有氧化色彩。
焊后立即可见。
热裂纹产生原因。
焊缝金属的晶界上存在低熔点共晶体(含硫、磷、铜等杂质)。
接头中存在拉应力。
防止措施选用适宜的,严格控制有害杂质碳、硫、磷的含量。
Fe和FeS易形成低熔点共晶,其熔点为988℃,很容易产生热裂纹。
严格控制焊缝截面形状,避免突高,扁平过渡。
缩小结晶温度范围,改善焊缝组织,细化焊缝晶粒,提高塑性减少。
确定合理的参数,减缓焊缝的冷却速度,以减小焊接应力。
如采用小线能量,焊前预热,合理的焊缝布置等。
焊接缺陷产生原因及防止措施

焊接缺陷产生原因及防止措施焊接接头的不完整性称为焊接缺陷,主要有焊接裂纹、未焊透、夹渣、气孔和焊缝外观缺陷等。
这些缺陷减少焊缝截面积,降低承载能力,产生应力集中,引起裂纹;降低疲劳强度,易引起焊件破裂导致脆断。
一缺陷名称:气孔(blowhole)(1)焊条不当或干燥.(2)焊件存有水分、油污或锈.(3)冲压速度太快.(4)电流太弱.(5)电弧长度不适宜.(1)选用适当的焊条并注意烘干.(2)焊接前清洁被焊部份.(3)减少冲压速度,并使内部气体难逸(4)使用厂商建议适当电流.(6)施行适当的预热工作.(6)焊件厚度小,金属加热过速.(5)调整适度电弧长度.(1)母材不洁.(2)焊丝存有锈或焊药干燥.(3)点焊不当,焊丝挑选不当.(1)焊接前注意清洁被焊部位.(2)选用适当的焊丝并注意保持干燥.(3)点焊焊道不得有缺陷,同时要清洁(4)减小干伸长度,调整适当气体流(4)干伸长度太短,co2气体保与整洁,且采用焊丝尺寸必须适度.co2气体(5)风速较大,无挡风装置.(5)安装挡风设备.(7)注意清除喷嘴处焊渣,并涂以飞溅(8)co2纯度为99.98%以上,水分为0.005%以下.维护焊接(6)冲压速度太快,加热快速.体乱流.别含水分).(7)火花溅黏在燃烧室,导致气(6)减少速度并使内部气体逸出.(8)气体纯度不当,不含杂物多(特粘附避免剂,以缩短燃烧室寿命.(1)焊缝有锈、氧化膜、油脂等(1)焊缝需研磨或以火焰烧除,再以钢有机物的杂质.(2)焊剂潮湿.(3)焊剂受污染.(4)焊接速度过快.(5)焊剂高度不足.(2)约须要300℃潮湿(3)注意焊剂的储存及焊接部位附近地区的洁净,以免杂物混进.(4)降低焊接速度.(6)焊剂高度过小,并使气体难于(5)焊剂出口橡皮管口必须调整低些.逸出(特别在焊剂粒度细的情(6)焊剂出口橡皮管要调整低些,在自形).(7)焊丝锈蚀或沾满油污.动焊接情形适当高度30-40mm.(7)换用洁净焊丝.c+).(8)极性不适当(特别在对接时(8)将直流正接(dc-)改为直流反接(d受到污染可以产生气孔).(1)减压表冷却,气体无法流出.(1)气体调节器无附电热器时,要加装(2)喷嘴被火花飞溅物堵塞.电热器,同时检查表之流量.(2)经常清除喷嘴飞溅物.并且涂以飞(3)焊丝有油、锈.溅附着防止剂.(3)焊丝储藏或加装焊丝时不容跌破(1)电压过高.(2)焊丝注重长度过短.(1)降低电压.(2)依各种焊丝表明采用.(4)增加拖拽角至约0-20°.(5)调整适度.自保护药(3)钢板表面有锈蚀、油漆、水(3)焊前清除干净.芯焊丝分.(4)焊枪拖拽角弯曲太多.(5)卢瓦龙县速度太快,尤其斜焊接.二缺陷名称咬边(undercut)(1)电流太弱.(2)焊条不适宜.(3)电弧过长.(4)操作方法不当.(5)母材污秽.(6)母材失灵.(1)使用较低电流.(2)采用适度种类及大小之焊条.(3)维持适度的弧长.(4)采用正确的角度,较慢的速度,较短的电弧及狭窄的运转法.(5)清除母材油渍或锈.(6)使用直径较小之焊条.(1)电弧过长,冲压速度太快.(1)降低电弧长度及速度.(2)角焊时,焊条对准部位不正(2)在水平角焊接时,焊丝边线应离交点道二边填补不足产生咬边.(3)立焊转动或操作方式不当,并使焊接(3)废止操作方法.三缺陷名称:夹渣(slaginclusion)冲压方式出现原因(1)前层焊渣未完全清除.(1)彻底清除前层焊渣.(2)使用较低电流.(3)提升冲压速度.(4)增加焊条转动宽度.(5)废止适度坡口角度及间隙.(1)尽可能将焊接件置放水平边线.(2)特别注意每道焊道之洁净.(4)提升冲压速度(2)焊接电流太低.(3)焊接速度太慢.(4)焊条摆动过宽.(5)焊缝组合及设计不良.(1)母材倾斜(下坡)使焊渣超co2气体整洁.(2)前一道焊接后,焊渣未清洁(3)增加电流和焊速,使焊渣容易浮起.电弧焊(3)电流过大,速度慢,焊着量(4)用前进法焊接,开槽内焊渣(1)冲压方向朝母材弯曲方向,(1)冲压移向恰好相反方向冲压,或将母材因此焊渣流动超前.尽可能改成水平方向焊接.(2)多层冲压时,凹槽下受焊丝(2)凹槽侧面和焊丝之间距离,最少必须溶入,焊丝过于靠近开槽的侧大于焊丝直径以上.边.(3)在冲压起点存有导板处易产(3)导板厚度及开槽形状,需与母材相(4)提升冲压电流,并使残余焊渣难熔(4)电流过小,第二层间有焊渣化.存留,在冲压薄板时难产生(5)减少冲压电流及冲压速度.裂纹.(6)最后完成层电弧电压过高,(6)增大电压或提升焊速,必要时盖面(5)焊接速度过低,使焊渣超前.层由单道焊改为多道焊接.使游离焊渣在焊道端头产生弄卷.(1)电弧电压过低.(2)焊丝摆弧不当.(3)焊丝伸出过长.(4)电流过高,冲压速度过慢.(5)第一道焊渣,未充份去除.(6)第一道融合不当.(7)坡口太窄小.(1)调整适当.(2)加多练习.(3)依各种焊丝采用表明.(4)调整冲压参数.(5)全然去除(6)使用适当电压,注意摆弧.(7)改正适当坡口角度及间隙.自维护药芯焊丝焊接方式发生原因(1)前层焊渣未全然去除.(1)彻底清除前层焊渣.(2)采用较高电流.(3)提高焊接速度.(4)减少焊条摆动宽度.(5)改正适当坡口角度及间隙.(1)尽可能将焊件放置水平位置.(2)注意每道焊道之清洁.(4)提高焊接速度(2)冲压电流太低.(3)冲压速度很慢.(4)焊条转动过阔.(5)焊缝女团及设计不当.(1)母材弯曲(下坡)并使焊渣逊于co2气体干净.(2)前一道冲压后,焊渣未洁净(3)减少电流和焊速,并使焊渣难浮.电弧焊(3)电流过小,速度慢,焊着量(4)用行进法冲压,凹槽内焊渣(1)焊接方向朝母材倾斜方向,(1)焊接改向相反方向焊接,或将母材因此焊渣流动全面性.尽可能换成水平方向冲压.(2)多层焊接时,开槽面受焊丝(2)开槽侧面和焊丝之间距离,最少要渗入,焊丝过分紧邻凹槽的侧大于焊丝直径以上.边.(3)在焊接起点有导板处易产(3)导板厚度及凹槽形状,而因母材二者(4)提高焊接电流,使残留焊渣容易熔(4)电流过大,第二层间有焊渣化.留存,在焊接薄板时容易产生(5)增加焊接电流及焊接速度.裂纹.(6)最后顺利完成层电弧电压过低,(6)减小电压或提高焊速,必要时盖面(5)冲压速度过高,并使焊渣全面性.层由单道焊接改成多道冲压.使得游离焊渣在焊道端头产生搅卷.(1)电弧电压过高.(2)焊丝挂弧不当.(3)焊丝张开过长.(4)电流过低,焊接速度过慢.(5)第一道焊渣,未充分清除.(6)第一道结合不良.(7)坡口太狭窄.(1)调整适度.(2)加多练.(3)依各种焊丝使用说明.(4)调整焊接参数.(5)完全清除(6)采用适度电压,特别注意挂弧.(7)废止适度坡口角度及间隙.自保护药芯焊丝(1)焊条采用不当.(2)电流太低.(1)选用较具渗透力的焊条.(2)使用适当电流.(3)改用适当焊接速度.手工(3)冲压速度太快温度下降不电弧焊够,又进行速度太慢电弧冲力(4)增加开槽度数,增加间隙,并减少根被焊渣所抵挡,无法给与母材.深.(4)焊缝设计及组合不正确.(1)电弧过大,冲压速度过高.(2)电弧过长.(3)凹槽设计不当.(1)增加焊接电流和速度.(2)降低电弧长度.(3)减少凹槽度数.减少间隙增加根深.五缺陷名称:裂纹(crack)(1)焊件所含过低的碳、锰等再分(1)采用高氢系焊条.(2)焊条品质不良或潮湿.(3)焊缝拘束应力过大.(4)母条材质含硫过高不适于(2)采用适合焊条,并特别注意潮湿.(3)改进结构设计,特别注意冲压顺序,焊接接后进行热处理.(4)防止采用不当钢材.(5)冲压时需考量预演或后热.(6)预演母材,焊接后缓冷.(7)采用适度电流.(8)首道焊接之焊着金属须充分抵抗(5)施工准备工作严重不足.(6)母材厚度较大,冷却过速.(7)电流太强.(8)首道焊道严重不足抵抗膨胀应当(1)开槽角度过小,在大电流焊(1)注意适当开槽角度与电流的配合,直奔时,产生梨形和焊道裂纹.(2)母材含碳量和其它合金量必要时必须加强凹槽角度.(2)采用含碳量低的焊条.(3)第一道焊着金属须充份能够抵抗交(4)改进结构设计,特别注意冲压顺序,焊接(5)特别注意焊丝留存.(6)特别注意焊件女团之精度.过高(焊道及热影区).小.过强.(5)焊丝干燥,氢气入侵焊道.(3)多层焊接时,第一层焊道过缩应力.(4)冲压顺序不当,产生拘束力后展开热处理.(6)套板密接不良,形成高低不(7)注意正确的电流及焊接速度.平,并致应力集中.(7)因第一层焊接量过多,冷却缓慢(不锈钢,铝合金等).(1)对焊缝母材所用的焊丝和(1)采用含锰量较低的焊丝,在母材含(2)冲压电流及电压须要减少,冲压速度焊剂之配合不适当(母材含碳碳量多时,要有预热之措施.量过大,焊丝金属含锰量太少).(3)焊丝含碳、硫量过大.(4)在多层冲压之第一层所生降低,母材需加热措施.(4)第一层焊道之焊着金属须充份抵(2)焊道急速冷却,使热影响区(3)更换焊丝.(5)将冲压电流及冲压速度降低,发生改变焊道力,不足抵抗收缩应力.(5)在角焊时过浅的扩散或偏(6)注意规定的施工方法,并予焊接操析.作施工指导.(6)焊接施工顺序不正确,母材(7)焊道宽度与深度的比例约为1:1:六瑕疵名称:变形(distortion)焊接方式发生原因手焊、co(1)冲压层数太多.(2)冲压顺序不当.(3)施工准备工作严重不足.(4)母材加热过速.(5)母材失灵.(薄板)(6)焊缝设计不当.(7)焊着金属过多.(8)束缚方式不的确.(1)使用直径较大之焊条及较高电流.(3)冲压前,采用夹具将焊接件紧固以免护焊、自保护药芯焊丝焊接、自动埋弧焊接.(4)防止加热过速或预演母材.(5)采用穿透力高之焊材.(6)增加焊缝间隙,增加凹槽度数.(7)特别注意冲压尺寸,不并使焊道过小.(8)特别注意避免变形的紧固措施.(2)操作方法不适.(2)使用光滑适度之速度及冲压顺序.(4)减少电流.(5)多加练习.(6)更改导电嘴.(7)维持的定短、娴熟.焊道外观形(3)焊接电流过高,焊条直径过(3)选用适当电流及适当直径的焊接.状不良(bad粗.appearanc(4)焊件失灵.(5)焊道内,熔填方法不良.(6)导电嘴磨耗.(7)焊丝伸出长度不变.(1)使用焊条不当.(2)焊条潮湿.(3)母材冷却过速.(1)采用适度焊条,例如无法消解时用高(2)使用干燥过的焊条.(3)降低冲压速度,防止急冷,最出色施予凹痕(pit)(4)焊条不洁及焊件的偏析.(5)焊件含碳、锰成分过低.(4)使用良好低氢型焊条.(5)使用盐基度较高焊条.(1)在直流电焊接时,焊件所生磁(1)·电弧偏向一方复置一地线.场不均,使电弧偏向.(2)接地线边线不尽如人意.(3)焊枪拖拽角太大.(4)焊丝张开长度太短.(5)电压太高,电弧太长.(6)电流太大.(7)冲压速度太快.·正对偏向一方焊接.·采用短电弧.·改正磁场使趋均一.·改用交流电焊(2)调整接地线位置.(3)减小焊枪拖曳角.(4)增长焊丝伸出长度.(5)降低电压及电弧.(6)调整使用适当电流.(7)焊接速度变慢.偏弧(arcbl(1)在有开槽焊接时,电流过大.(1)降低电流.(2)因开槽不良焊缝间隙太大.(2)减少焊缝间隙.(1)导电嘴磨损,焊丝输出产生(1)将焊接导电嘴换新使用.焊道不光滑左右摇摆.(2)焊枪操作不熟练.(1)电流过大,焊接速度太慢.(2)多提操作方式练.(1)选用正确电流及焊接速度.(2)提高电弧长度.(3)焊丝不可离交点太远.(2)电弧太短,焊道低.(3)焊丝对准边线不适度.(角(2)电弧太长.(3)电流太高或太低.(2)采用较短之电弧.(3)采用适度之电流.(4)调整适度.(5)依各种焊丝使用说明.(7)注意仓库保管条件.(8)修理,平日注意保养.(1)使用适度的长度,比如实心焊丝在火花飞溅过(4)电弧电压太高或太低.(5)焊丝注重过长.(7)焊丝过度经久耐用.(8)焊机情况不当.(1)焊丝张开过长.(6)焊枪倾斜过度,拖曳角太大.(6)尽可能保持垂直,避免过度倾斜.(2)焊丝歪曲.(3)直线操作方式不当.大电流时伸出长20-25mm.在自保护焊接时伸出长度约为40-50mm.(2)更改崭新焊丝或将歪曲不予校正.(3)在直线操作方式时,焊枪必须维持横向.(1)焊枪前端之导电嘴比焊丝(1)焊丝心径必须与导电嘴配合.(2)更换导电嘴.(3)将焊丝卷曲拉直.(4)将输送机轴助威,并使调头杀菌.(5)更改运送轮.(6)压力要适当,太松送线不良,太紧焊(2)导电嘴出现磨损.(3)焊丝出现卷曲.(4)焊丝输送机调头不顺遂.(5)焊丝运送轮子沟槽磨损.(6)冷却轮子压入不当.(7)导管接点阻力太大.(7)导管弯曲过大,调整减少弯曲量.燃烧室与母材(1)燃烧室,导管或导电嘴间出现(1)火花溅物粘及燃烧室过多须除去,间出现电弧短路.(1)冷却水不能充分流出.或是采用焊枪存有绝缘维护之陶瓷管.(1)冷却水管不通,如冷却水管阻塞,必焊枪燃烧室过(2)电流过小.须清除使水压提升流量正常.(2)焊枪采用在允许电流范围及采用(1)导电嘴与母材间的距离过(1)采用适度距离或稍为短些去起至弧,焊丝粘住导短.(2)导管阻力过小,送来线不当.(3)电流太小,电压太大.然后调整到适当距离.(2)去除导管内部,CX600X稳定运送.(3)调整适度电流,电压值.典型缺陷照片-焊穿-。
4.焊缝缺欠、缺陷产生原因及防止方法

冷裂纹 冷裂纹是在焊后冷却过程中产 生的,产生于较低温度,或产生于焊后 一段时间以后,故又称延迟裂纹。冷裂 纹大多产生在基体金属或基体金属与焊 缝交界的熔合线上。其产生的主要原因 是由于热影响区或焊缝内形成了淬火组 织,在高应力作用下,引起晶粒内部的 破裂,焊接含碳量较高或合金元素较多 的易淬火钢材时,最易产生冷裂纹。焊 缝中熔入过多的氢,也会引起冷裂纹。 含氢量和拉应力是冷裂纹(这里指氢致裂 31 纹)产生的两个重要因素。 2013-7-7
29 2013-7-7
c.采用熔深较浅的焊缝,改善散热条件使低 熔点物质上浮在焊缝表面而不存在于焊缝中 ; d.合理选用焊接规范,并采用预热和后热, 减小冷却速度; e.采用合理的装配次序,减小焊接应力。 f.研究表明,在Ni-Cr系的单项奥氏体不锈钢 中加入Mo、W、Ti、Ta等铁素体形成元素, 可以有效阻止多边化过程,高温δ相的存在 ,打乱枝状奥氏体晶粒的结晶方向,有效地 防止多边化裂纹。 30
第四章
焊缝缺欠、缺陷及对策
1 2013-7-7
焊接缺陷和焊接缺欠的定义:
焊接缺欠——在焊接接头中因焊接 产生的金属不连续、不致密或连接不良 的现象,简称“缺欠”。 焊接缺陷——超过规定限值的缺欠, 称之为“缺陷”。
2 2013-7-7
缺欠种类
形状尺寸缺陷 有焊接变形,尺寸偏差(包括错
边、角度偏筹、焊缝尺寸过大或过小等),外形 不良(包括焊缝高低不平、波纹粗劣、宽窄不齐 等),飞溅和电弧擦伤。
热裂纹有沿晶界分布的特征。当裂纹贯穿 表面与外界相通时,裂纹面上有氧化色彩, 失去金属光泽。 防止结晶裂纹的措施: a.减小硫、磷等有害元素的含量,用含碳量 较低的材料焊接,加入焊缝金属中锰形成 MnS脱硫; b.加入一定的合金元素,减小柱状晶和偏析 。如钼、钒、铝、钛、铌和稀土等元素可以 细化晶粒;
史上最全的焊接缺陷产生原因及处理办法

史上最全的焊接缺陷产生原因及处理办法焊接缺陷是指焊接过程中出现的质量问题,包括焊接接头的裂纹、孔隙、夹杂物等缺陷。
这些缺陷会影响焊接接头的强度、密封性和耐腐蚀性,因此及时发现并处理焊接缺陷至关重要。
本文将介绍一些常见的焊接缺陷产生原因及相应的处理办法。
1.焊接接头裂纹:原因:(1)热裂纹:焊接过程中,金属在快速冷却过程中产生应力,导致裂纹产生。
(2)冷裂纹:焊接接头长时间在低温环境下使用,受到外部冻结和膨胀引起。
处理办法:(1)控制焊接温度和预热焊件,以减少热应力。
(2)使用低氢焊条或预热焊件,以减少氢原子的进入。
(3)进行适当的回火处理,以减少残余应力。
2.焊接接头孔隙:原因:(1)焊接材料含有气体,如铁锈或涂层。
(2)焊接过程中保护性气体不足。
(3)焊接参数设置不正确,如焊接电流过低或焊接速度过快。
(4)焊接材料含有水分。
处理办法:(1)使用清洁的焊接材料,并确保焊接表面干净。
(2)提供足够的保护气体,以减少氧气和水蒸气的进入。
(3)调整焊接参数,使其适合焊接材料。
(4)在焊接前进行预热,以减少水分含量。
3.焊接接头夹杂物:原因:(1)焊接材料中包含的杂质。
(2)焊接材料与辅助材料的不匹配。
(3)焊接材料的氧化物。
处理办法:(1)使用高纯度的焊接材料,以减少杂质含量。
(2)选用合适的焊接材料和辅助材料,确保它们的化学成分相似。
(3)确保焊接材料没有明显的氧化。
4.焊接接头下沉:原因:(1)焊接时材料太薄,导致热传导速度过快。
(2)焊接过程中温度不均匀分布。
(3)焊接电流过高,引起材料融化。
处理办法:(1)加大焊接电流,以增加热量传输。
(2)调整焊接速度和焊接参数,使其适合焊接材料。
(3)使用合适的焊接材料和辅助材料,以增加熔池的稳定性。
5.焊接接头变形:原因:(1)焊接过程中产生的应力导致材料变形。
(2)焊接过程中热膨胀引起的变形。
处理办法:(1)使用适当的夹具和支撑装置,以减少焊接过程中的应力。
常见焊接缺陷类型产生原因与防止措施(范文大全)
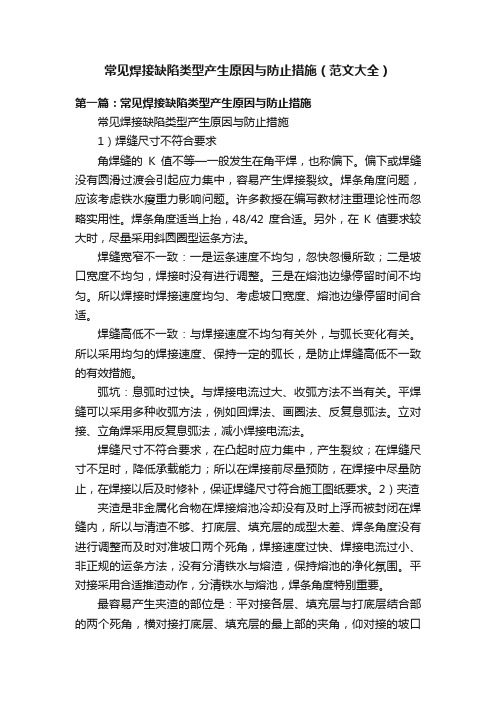
常见焊接缺陷类型产生原因与防止措施(范文大全)第一篇:常见焊接缺陷类型产生原因与防止措施常见焊接缺陷类型产生原因与防止措施1)焊缝尺寸不符合要求角焊缝的K值不等—一般发生在角平焊,也称偏下。
偏下或焊缝没有圆滑过渡会引起应力集中,容易产生焊接裂纹。
焊条角度问题,应该考虑铁水瘦重力影响问题。
许多教授在编写教材注重理论性而忽略实用性。
焊条角度适当上抬,48/42度合适。
另外,在K值要求较大时,尽量采用斜圆圈型运条方法。
焊缝宽窄不一致:一是运条速度不均匀,忽快忽慢所致;二是坡口宽度不均匀,焊接时没有进行调整。
三是在熔池边缘停留时间不均匀。
所以焊接时焊接速度均匀、考虑坡口宽度、熔池边缘停留时间合适。
焊缝高低不一致:与焊接速度不均匀有关外,与弧长变化有关。
所以采用均匀的焊接速度、保持一定的弧长,是防止焊缝高低不一致的有效措施。
弧坑:息弧时过快。
与焊接电流过大、收弧方法不当有关。
平焊缝可以采用多种收弧方法,例如回焊法、画圈法、反复息弧法。
立对接、立角焊采用反复息弧法,减小焊接电流法。
焊缝尺寸不符合要求,在凸起时应力集中,产生裂纹;在焊缝尺寸不足时,降低承载能力;所以在焊接前尽量预防,在焊接中尽量防止,在焊接以后及时修补,保证焊缝尺寸符合施工图纸要求。
2)夹渣夹渣是非金属化合物在焊接熔池冷却没有及时上浮而被封闭在焊缝内,所以与清渣不够、打底层、填充层的成型太差、焊条角度没有进行调整而及时对准坡口两个死角,焊接速度过快、焊接电流过小、非正规的运条方法,没有分清铁水与熔渣,保持熔池的净化氛围。
平对接采用合适推渣动作,分清铁水与熔池,焊条角度特别重要。
最容易产生夹渣的部位是:平对接各层、填充层与打底层结合部的两个死角,横对接打底层、填充层的最上部的夹角,仰对接的坡口边缘。
实际就是焊缝成型没有实现略凹、或平,而特别容易形成过凸的成型所致。
夹渣降低焊缝有效截面使用性能,容易产生裂纹等其他缺陷,影响焊缝的致密性。
3)未焊透与未熔合未焊透一般产生在坡口根部,与埋弧焊偏丝、焊接电流过小、焊接速度快、坡口角度过小、反面清根不彻底。
焊接缺陷产生原因及防止措施

焊接缺陷产生原因及防止措施焊接接头的不完整性称为焊接缺陷,主要有焊接裂纹、未焊透、夹渣、气孔和焊缝外观缺陷等。
这些缺陷减少焊缝截面积,降低承载能力,产生应力集中,引起裂纹;降低疲劳强度,易引起焊件破裂导致脆断。
一缺陷名称:气孔(Blow Hole)焊接方式发生原因防止措施手工电弧焊(1)焊条不良或潮湿. (2)焊件有水分、油污或锈. (3)焊接速度太快. (4)电流太强.(5)电弧长度不适合. (6)焊件厚度大,金属冷却过速.(1)选用适当的焊条并注意烘干.(2)焊接前清洁被焊部份. (3)降低焊接速度,使内部气体容易逸出.(4)使用厂商建议适当电流. (5)调整适当电弧长度. (6)施行适当的预热工作.CO2气体保护焊(1)母材不洁. (2)焊丝有锈或焊药潮湿. (3)点焊不良,焊丝选择不当. (4)干伸长度太长,CO2气体保护不周密.(5)风速较大,无挡风装置.(6)焊接速度太快,冷却快速.(7)火花飞溅粘在喷嘴,造成气体乱流. (8)气体纯度不良,含杂物多(特别含水分).(1)焊接前注意清洁被焊部位. (2)选用适当的焊丝并注意保持干燥.(3)点焊焊道不得有缺陷,同时要清洁干净,且使用焊丝尺寸要适当.(4)减小干伸长度,调整适当气体流量. (5)加装挡风设备. (6)降低速度使内部气体逸出. (7)注意清除喷嘴处焊渣,并涂以飞溅附着防止剂,以延长喷嘴寿命. (8)CO2纯度为%以上,水分为%以下.埋弧焊接(1)焊缝有锈、氧化膜、油脂等有机物的杂质. (2)焊剂潮湿. (3)焊剂受污染. (4)焊接速度过快. (5)焊剂高度不足. (6)焊剂高度过大,使气体不易逸出(特别在焊剂粒度细的情形). (7)焊丝生锈或沾有油污. (8)极性不适当(特别在对接时受污染会产生气孔).(1)焊缝需研磨或以火焰烧除,再以钢丝刷清除. (2)约需300℃干燥(3)注意焊剂的储存及焊接部位附近地区的清洁,以免杂物混入. (4)降低焊接速度. (5)焊剂出口橡皮管口要调整高些. (6)焊剂出口橡皮管要调整低些,在自动焊接情形适当高度30-40mm. (7)换用清洁焊丝. (8)将直流正接(DC-)改为直流反接(DC+).设备不良(1)减压表冷却,气体无法流出. (2)喷嘴被火花飞溅物堵塞. (3)焊丝有油、锈.(1)气体调节器无附电热器时,要加装电热器,同时检查表之流量. (2)经常清除喷嘴飞溅物.并且涂以飞溅附着防止剂. (3)焊丝贮存或安装焊丝时不可触及油类.自保护药芯焊丝(1)电压过高. (2)焊丝突出长度过短. (3)钢板表面有锈蚀、油漆、水分. (4)焊枪拖曳角倾斜太多. (5)移行速度太快,尤其横焊.(1)降低电压. (2)依各种焊丝说明使用. (3)焊前清除干净. (4)减少拖曳角至约0-20°.(5)调整适当.典型缺陷照片二缺陷名称咬边(Undercut)焊接方式发生原因防止措施手工电弧焊(1)电流太强. (2)焊条不适合. (3)电弧过长. (4)操作方法不当. (5)母材不洁. (6)母材过热.(1)使用较低电流. (2)选用适当种类及大小之焊条. (3)保持适当的弧长. (4)采用正确的角度,较慢的速度,较短的电弧及较窄的运行法.(5)清除母材油渍或锈. (6)使用直径较小之焊条.CO2气体保护焊(1)电弧过长,焊接速度太快.(2)角焊时,焊条对准部位不正确. (3)立焊摆动或操作不良,使焊道二边填补不足产生咬边.(1)降低电弧长度及速度. (2)在水平角焊时,焊丝位置应离交点1-2mm. (3)改正操作方法.典型缺陷照片三缺陷名称:夹渣(Slag Inclusion)焊接方式发生原因防止措施手工电弧焊(1)前层焊渣未完全清除.(2)焊接电流太低. (3)焊接速度太慢. (4)焊条摆动过宽. (5)焊缝组合及设计不良.(1)彻底清除前层焊渣. (2)采用较高电流. (3)提高焊接速度. (4)减少焊条摆动宽度. (5)改正适当坡口角度及间隙.CO2气体电弧焊(1)母材倾斜(下坡)使焊渣超前. (2)前一道焊接后,焊渣未清洁干净. (3)电流过小,速度慢,焊着量多. (4)用前进法焊接,开槽内焊渣超前甚(1)尽可能将焊件放置水平位置.(2)注意每道焊道之清洁. (3)增加电流和焊速,使焊渣容易浮起. (4)提高焊接速度多.埋弧焊接(1)焊接方向朝母材倾斜方向,因此焊渣流动超前. (2)多层焊接时,开槽面受焊丝溶入,焊丝过于靠近开槽的侧边. (3)在焊接起点有导板处易产生夹渣. (4)电流过小,第二层间有焊渣留存,在焊接薄板时容易产生裂纹. (5)焊接速度过低,使焊渣超前.(6)最后完成层电弧电压过高,使得游离焊渣在焊道端头产生搅卷.(1)焊接改向相反方向焊接,或将母材尽可能改成水平方向焊接. (2)开槽侧面和焊丝之间距离,最少要大于焊丝直径以上. (3)导板厚度及开槽形状,需与母材相同. (4)提高焊接电流,使残留焊渣容易熔化. (5)增加焊接电流及焊接速度. (6)减小电压或提高焊速,必要时盖面层由单道焊改为多道焊接.自保护药芯焊丝(1)电弧电压过低. (2)焊丝摆弧不当. (3)焊丝伸出过长. (4)电流过低,焊接速度过慢. (5)第一道焊渣,未充分清除. (6)第一道结合不良. (7)坡口太狭窄. (8)焊缝向下倾斜.(1)调整适当. (2)加多练习. (3)依各种焊丝使用说明. (4)调整焊接参数. (5)完全清除(6)使用适当电压,注意摆弧. (7)改正适当坡口角度及间隙. (8)放平,或移行速度加快.典型缺陷照片四缺陷名称:未焊透(Incomplete Penetration)焊接方式发生原因防止措施手工电弧焊(1)焊条选用不当. (2)电流太低. (3)焊接速度太快温度上升不够,又进行速度太慢电弧冲力被焊渣所阻挡,不能给予母材. (4)焊缝设计及组合不正确.(1)选用较具渗透力的焊条. (2)使用适当电流. (3)改用适当焊接速度. (4)增加开槽度数,增加间隙,并减少根深.CO2气体保护焊(1)电弧过小,焊接速度过低.(2)电弧过长. (3)开槽设计不良.(1)增加焊接电流和速度. (2)降低电弧长度. (3)增加开槽度数.增加间隙减少根深.自保护药芯焊丝(1)电流太低. (2)焊接速度太慢. (3)电压太高. (4)摆弧不当. (5)坡口角度不当.(1)提高电流. (2)提高焊接速度.(3)降低电压. (4)多加练习. (5)采用开槽角度大一点.典型缺陷照片五缺陷名称:裂纹(Crack)焊接方式发生原因防止措施手工电弧焊(1)焊件含有过高的碳、锰等合金元素. (2)焊条品质不良或潮湿. (3)焊缝拘束应力过大. (4)母条材质含硫过高不适于焊接. (5)施工准备不足. (6)母材厚度较大,冷却过速. (7)电流太强. (8)首道焊道不足抵抗收缩应力.(1)使用低氢系焊条. (2)使用适宜焊条,并注意干燥. (3)改良结构设计,注意焊接顺序,焊接后进行热处理. (4)避免使用不良钢材. (5)焊接时需考虑预热或后热. (6)预热母材,焊后缓冷. (7)使用适当电流.(8)首道焊接之焊着金属须充分抵抗收缩应力.CO2气体保护焊(1)开槽角度过小,在大电流焊接时,产生梨形和焊道裂纹. (2)母材含碳量和其它合金量过高(焊道及热影区).(3)多层焊接时,第一层焊道过小. (4)焊接顺序不当,产生拘束力过强. (5)焊丝潮湿,氢气侵入焊道. (6)套板密接不良,形成高低不平,致应力集中. (7)因第一层焊接量过多,冷却缓慢(不锈钢,铝合金等).(1)注意适当开槽角度与电流的配合,必要时要加大开槽角度. (2)采用含碳量低的焊条. (3)第一道焊着金属须充分能抵抗收缩应力. (4)改良结构设计,注意焊接顺序,焊后进行热处理. (5)注意焊丝保存. (6)注意焊件组合之精度. (7)注意正确的电流及焊接速度.埋弧焊接(1)对焊缝母材所用的焊丝和焊剂之配合不适当(母材含碳量过大,焊丝金属含锰量太少). (2)焊道急速冷却,使热影响区发生硬化. (3)焊丝含碳、硫量过大. (4)在多层焊接之第一层所生焊道力,不足抵抗收缩应力. (5)在角焊时过深的渗透或偏析. (6)焊接施工顺序不正确,母材拘束力大. (7)焊道形状不适当,焊道宽度与焊道深度比例过大或过小.(1)使用含锰量较高的焊丝,在母材含碳量多时,要有预热之措施. (2)焊接电流及电压需增加,焊接速度降低,母材需加热措施. (3)更换焊丝.(4)第一层焊道之焊着金属须充分抵抗收缩应力. (5)将焊接电流及焊接速度减低,改变极性. (6)注意规定的施工方法,并予焊接操作施工指导. (7)焊道宽度与深度的比例约为1:1:25,电流降低,电压加大.典型缺陷照片六缺陷名称:变形(Distortion)焊接方式发生原因防止措施手焊、CO 2气体保护焊、自保护药芯焊丝焊接、自动埋弧焊接.(1)焊接层数太多. (2)焊接顺序不当. (3)施工准备不足. (4)母材冷却过速. (5)母材过热.(薄板) (6)焊缝设计不当. (7)焊着金属过多.(8)拘束方式不确实.(1)使用直径较大之焊条及较高电流. (2)改正焊接顺序(3)焊接前,使用夹具将焊件固定以免发生翘曲. (4)避免冷却过速或预热母材.(5)选用穿透力低之焊材. (6)减少焊缝间隙,减少开槽度数. (7)注意焊接尺寸,不使焊道过大. (8)注意防止变形的固定措施.七其他缺陷缺陷名称发生原因防止措施搭叠(Overlap)(1)电流太低. (2)焊接速度太慢.(1)使用适当的电流. (2)使用适合的速度.焊道外观形状不良(Bad Appearance)(1)焊条不良. (2)操作方法不适. (3)焊接电流过高,焊条直径过粗. (4)焊件过热.(5)焊道内,熔填方法不良.(6)导电嘴磨耗. (7)焊丝伸出长度不变.(1)选用适当大小良好的干燥焊条.(2)采用均匀适当之速度及焊接顺序. (3)选用适当电流及适当直径的焊接. (4)降低电流. (5)多加练习.(6)更换导电嘴. (7)保持定长、熟练.凹痕(Pit)(1)使用焊条不当. (2)焊条潮湿. (3)母材冷却过速. (4)焊条不洁及焊件的偏析. (5)焊件含碳、锰成分过高.(1)使用适当焊条,如无法消除时用低氢型焊条. (2)使用干燥过的焊条. (3)减低焊接速度,避免急冷,最好施以预热或后热. (4)使用良好低氢型焊条. (5)使用盐基度较高焊条.偏弧(Arc Blow)(1)在直流电焊时,焊件所生磁场不均,使电弧偏向. (2)接地线位置不佳. (3)焊枪拖曳角太大. (4)焊丝伸出长度太短. (5)电压太高,电弧太长. (6)电流太大. (7)焊接速度太快.(1)·电弧偏向一方置一地线.·正对偏向一方焊接.·采用短电弧.·改正磁场使趋均一.·改用交流电焊(2)调整接地线位置. (3)减小焊枪拖曳角. (4)增长焊丝伸出长度. (5)降低电压及电弧. (6)调整使用适当电流. (7)焊接速度变慢.烧穿(1)在有开槽焊接时,电流过大. (2)因开槽不良焊缝间隙太大.(1)降低电流. (2)减少焊缝间隙.焊道不均匀(1)导电嘴磨损,焊丝输出产生摇摆. (2)焊枪操作不熟练.(1)将焊接导电嘴换新使用. (2)多加操作练习.焊泪(1)电流过大,焊接速度太慢.(2)电弧太短,焊道高. (3)焊丝对准位置不适当.(角焊时)(1)选用正确电流及焊接速度. (2)提高电弧长度. (3)焊丝不可离交点太远.火花飞溅过多(1)焊条不良. (2)电弧太长.(3)电流太高或太低. (4)电弧电压太高或太低. (5)焊丝突出过长 . (6)焊枪倾斜过度,拖曳角太大. (7)焊丝过度吸湿. (8)焊机情况不良.(1)采用干燥合适之焊条. (2)使用较短之电弧. (3)使用适当之电流.(4)调整适当. (5)依各种焊丝使用说明. (6)尽可能保持垂直,避免过度倾斜. (7)注意仓库保管条件. (8)修理,平日注意保养.焊道成蛇行状(1)焊丝伸出过长. (2)焊丝扭曲. (3)直线操作不良.(1)采用适当的长度,例如实心焊丝在大电流时伸出长20-25mm.在自保护焊接时伸出长度约为40-50mm.(2)更换新焊丝或将扭曲予以校正.(3)在直线操作时,焊枪要保持垂直.电弧不稳定(1)焊枪前端之导电嘴比焊丝心径大太多. (2)导电嘴发生磨损. (3)焊丝发生卷曲. (4)焊丝输送机回转不顺. (5)焊丝输送轮子沟槽磨损. (6)加压轮子压紧不良. (7)导管接头阻力太大.(1)焊丝心径必须与导电嘴配合.(2)更换导电嘴. (3)将焊丝卷曲拉直. (4)将输送机轴加油,使回转润滑. (5)更换输送轮. (6)压力要适当,太松送线不良,太紧焊丝损坏.(7)导管弯曲过大,调整减少弯曲量.喷嘴与母材间发生电弧(1)喷嘴,导管或导电嘴间发生短路.(1)火花飞溅物粘及喷嘴过多须除去,或是使用焊枪有绝缘保护之陶瓷管.焊枪喷嘴过热(1)冷却水不能充分流出.(2)电流过大.(1)冷却水管不通,如冷却水管阻塞,必须清除使水压提升流量正常. (2)焊枪使用在容许电流范围及使用率之内.焊丝粘住导电嘴(1)导电嘴与母材间的距离过短. (2)导管阻力过大,送线不良. (3)电流太小,电压太大.(1)使用适当距离或稍为长些来起弧,然后调整到适当距离. (2)清除导管内部,使能平稳输送. (3)调整适当电流,电压值.典型缺陷照片-焊穿--搭叠--焊道蛇形-。
焊接常见缺陷产生的原因及其预防措施
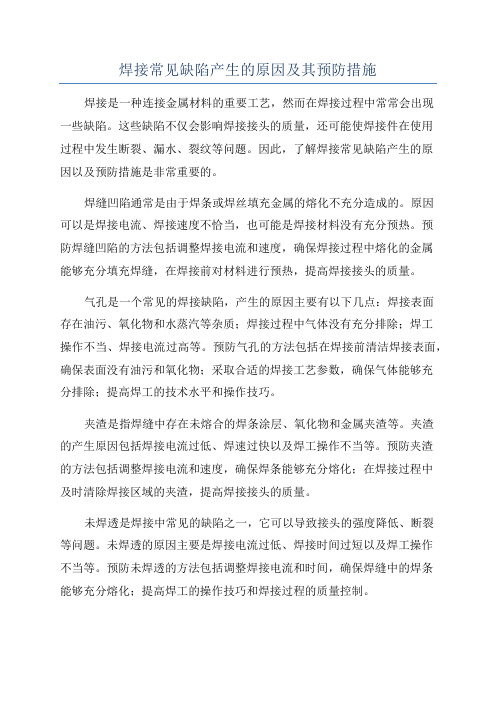
焊接常见缺陷产生的原因及其预防措施焊接是一种连接金属材料的重要工艺,然而在焊接过程中常常会出现一些缺陷。
这些缺陷不仅会影响焊接接头的质量,还可能使焊接件在使用过程中发生断裂、漏水、裂纹等问题。
因此,了解焊接常见缺陷产生的原因以及预防措施是非常重要的。
焊缝凹陷通常是由于焊条或焊丝填充金属的熔化不充分造成的。
原因可以是焊接电流、焊接速度不恰当,也可能是焊接材料没有充分预热。
预防焊缝凹陷的方法包括调整焊接电流和速度,确保焊接过程中熔化的金属能够充分填充焊缝,在焊接前对材料进行预热,提高焊接接头的质量。
气孔是一个常见的焊接缺陷,产生的原因主要有以下几点:焊接表面存在油污、氧化物和水蒸汽等杂质;焊接过程中气体没有充分排除;焊工操作不当、焊接电流过高等。
预防气孔的方法包括在焊接前清洁焊接表面,确保表面没有油污和氧化物;采取合适的焊接工艺参数,确保气体能够充分排除;提高焊工的技术水平和操作技巧。
夹渣是指焊缝中存在未熔合的焊条涂层、氧化物和金属夹渣等。
夹渣的产生原因包括焊接电流过低、焊速过快以及焊工操作不当等。
预防夹渣的方法包括调整焊接电流和速度,确保焊条能够充分熔化;在焊接过程中及时清除焊接区域的夹渣,提高焊接接头的质量。
未焊透是焊接中常见的缺陷之一,它可以导致接头的强度降低、断裂等问题。
未焊透的原因主要是焊接电流过低、焊接时间过短以及焊工操作不当等。
预防未焊透的方法包括调整焊接电流和时间,确保焊缝中的焊条能够充分熔化;提高焊工的操作技巧和焊接过程的质量控制。
热裂纹是焊接常见的缺陷之一,它与焊接材料的合金成分、材料的热膨胀系数、焊接应力等因素有关。
预防热裂纹的方法包括选择合适的焊接材料,确保焊接材料的成分和热膨胀系数与基材相匹配;控制焊接过程中的温度和应力,避免焊接接头过热和应力集中。
总之,预防焊接常见缺陷的关键是优化焊接工艺参数、提高焊工技术水平以及加强对焊接材料的选择和处理。
通过采取适当的预防措施,可以有效降低焊接缺陷的发生率,提高焊接接头的质量。
熔焊缺欠产生原因、检验方法及排除方法

2、焊接电流太小,焊接速度太快
3、熔渣密度太大
4、多层焊时熔渣未清除干净
1、X射线探伤检验
2、金相检验
3、超声波检验
铲除夹渣处的焊缝金属然后进行补焊
未焊透
母材与焊缝金属之间未熔化而留下的空隙常在单面焊根部和双面焊中间
1、焊接电流太小
2、焊接速度太快
3、坡口角度、间隙太小
4、操作技术不准
在裂纹两端钻止裂孔或铲除裂纹处的焊缝金属进行补焊
冷裂纹
断口无明显的氧化色,有金属光泽,产生在热影响区的过热区中
1、焊接结构设计不合理
2、焊缝布置不当
3、焊接工艺措施不周全,如未预热或焊后冷却快
再热裂纹
沿晶间巨局限在热影响区的粗晶区内
1、焊后热处理的工艺规范不正确
2、母材性能尚未完全掌握
夹杂
在焊缝内部存在的金属或非金属夹杂物
1、X射线探伤检验
2、金相检验
3、目视检验
铲去气孔处的焊缝金属,然后补焊
裂纹
热裂纹
沿晶界面出现,裂缝断口处有氧化色,一般出现在焊缝上,呈锯齿状
母材抗裂性能较差,焊接材料质量不好,焊接参数选择不当,焊接内应力大
1、目视检验
2、X射线探伤检验
3、超声波检验
4、磁粉探伤检验
5、金相检验
6、着色探伤和荧光探伤检验
焊缝增高量和宽度不符合技术条件,存在过高或过低,过宽或过窄及不平滑过渡的现象
1、焊接坡口不合适
2、操作时运条不当
3、焊接电流不稳定
4、焊接速度不均匀
5、焊接电弧高低变化太大
1、目视检验
2、用量具测量
过宽、过高的焊缝可用机械方法去除,过窄、过低的焊缝可用熔焊方法补焊
焊接缺陷产生的原因及防止方法教材

九:烧穿:焊接过程中,熔化金属自坡口背面流 出,形成穿孔的缺陷叫烧穿。 产生原因:对焊件加热过甚。 防止方法:正确选择焊接电流和焊接速度,严格 控制焊件的装配间隙。另外,还可以采用衬垫等 防止烧穿。
试述金属熔焊焊缝缺陷的分类及表示方法。 根据GB6417-86《金属熔化焊焊缝缺陷分类及说 明》的规定,将金属熔焊焊缝缺陷分为以下几类: 第1类裂纹;第2类孔穴;第3类固体夹杂;第4类 未熔合和未焊透;第5类形状缺陷和第6类上述以 外的其它缺陷。 本标准按缺陷性质分大类,按其存在的位置及状 态分小类,以表格的方式列出。缺陷用数字序号 标记。每一缺陷大类用一个三位阿拉伯数字标记, 第一缺陷小类用一个四位阿拉伯数字标记。因此, 每一数字序号仅适合于某一特定类型的缺陷。例 如,1021表示“焊缝横向裂纹”,1023表示“热 影响区横向裂纹”等。
(3)采用碱性焊条和焊剂 由于碱性焊条和焊 剂具有较强的脱硫、磷能力,因此具有较高的抗 热裂能力。 (4)适当调整焊接工艺参数 焊接工艺参数直 接影响焊缝的横断面形状,因此适当减小焊接电 流以减少焊缝厚度,有利于提高焊缝的抗裂性能。 (5)采用收弧板 焊接终了断弧时,由于弧坑 冷却速度较快,常因偏析而在弧坑处形成热裂纹, 即所谓的弧坑裂纹。所以终焊时应逐渐断弧,并 填满弧坑。必要时可采用收弧板,将弧坑移至焊 件外,此时即使产生弧坑裂纹,也因焊后需将收 弧板割掉,并不影响结构本身。
焊接缺陷产生的原因及防止方法
培训要求:了解电弧焊常见缺陷的产生原因,掌 握防止电弧焊焊接缺陷的方法。
焊接缺陷一:焊缝表面尺寸不符合要求
焊缝表面高低不平、焊缝宽窄不齐、尺寸过大或 过小、角焊缝单边以及焊角尺寸不符合要求。 产生原因:焊件坡口角度不对,装配间隙不均匀, 焊接速度不当或运条手法不正确,焊条和角度选 择不当或改变。 防止方法:选择适当的坡口角度和装配间隙;正 确选择焊接工艺参数,特别是焊接电流值,采用 恰当运条手法和角度,以保证焊缝成形均匀一致。
(完整版)常见焊接缺陷产生原因及处理办法
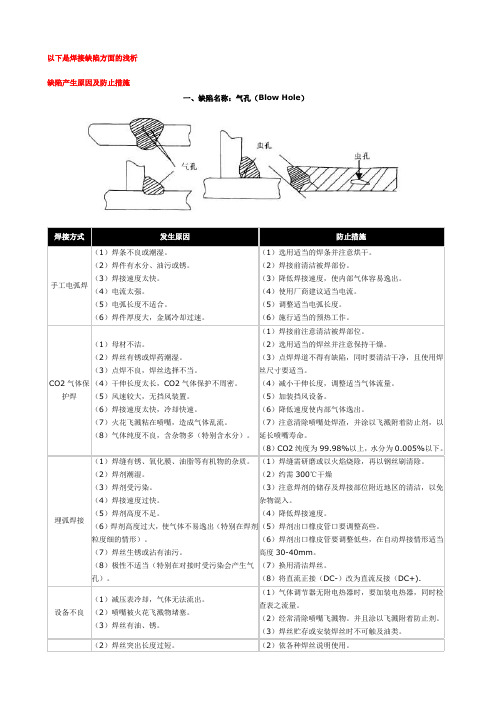
以下是焊接缺陷方面的浅析缺陷产生原因及防止措施一、缺陷名称:气孔(Blow Hole)焊接方式发生原因防止措施手工电弧焊(1)焊条不良或潮湿。
(2)焊件有水分、油污或锈。
(3)焊接速度太快。
(4)电流太强。
(5)电弧长度不适合。
(6)焊件厚度大,金属冷却过速。
(1)选用适当的焊条并注意烘干。
(2)焊接前清洁被焊部份。
(3)降低焊接速度,使内部气体容易逸出。
(4)使用厂商建议适当电流。
(5)调整适当电弧长度。
(6)施行适当的预热工作。
CO2气体保护焊(1)母材不洁。
(2)焊丝有锈或焊药潮湿。
(3)点焊不良,焊丝选择不当。
(4)干伸长度太长,CO2气体保护不周密。
(5)风速较大,无挡风装置。
(6)焊接速度太快,冷却快速。
(7)火花飞溅粘在喷嘴,造成气体乱流。
(8)气体纯度不良,含杂物多(特别含水分)。
(1)焊接前注意清洁被焊部位。
(2)选用适当的焊丝并注意保持干燥。
(3)点焊焊道不得有缺陷,同时要清洁干净,且使用焊丝尺寸要适当。
(4)减小干伸长度,调整适当气体流量。
(5)加装挡风设备。
(6)降低速度使内部气体逸出。
(7)注意清除喷嘴处焊渣,并涂以飞溅附着防止剂,以延长喷嘴寿命。
(8)CO2纯度为99.98%以上,水分为0.005%以下。
埋弧焊接(1)焊缝有锈、氧化膜、油脂等有机物的杂质。
(2)焊剂潮湿。
(3)焊剂受污染。
(4)焊接速度过快。
(5)焊剂高度不足。
(6)焊剂高度过大,使气体不易逸出(特别在焊剂粒度细的情形)。
(7)焊丝生锈或沾有油污。
(8)极性不适当(特别在对接时受污染会产生气孔)。
(1)焊缝需研磨或以火焰烧除,再以钢丝刷清除。
(2)约需300℃干燥(3)注意焊剂的储存及焊接部位附近地区的清洁,以免杂物混入。
(4)降低焊接速度。
(5)焊剂出口橡皮管口要调整高些。
(6)焊剂出口橡皮管要调整低些,在自动焊接情形适当高度30-40mm。
(7)换用清洁焊丝。
(8)将直流正接(DC-)改为直流反接(DC+).设备不良(1)减压表冷却,气体无法流出。
焊接缺陷产生原因及防止措施

焊接缺陷产生原因及防止措施焊接缺陷是指焊接工艺过程中产生的不符合要求的缺陷,会导致焊接接头的强度、密封性和耐腐蚀性等性能下降。
产生焊接缺陷的原因很多,包括焊接工艺参数不合理、材料质量不良、操作不当等。
为了避免焊接缺陷的产生,需要采取一系列防止措施。
1.工艺参数不合理:焊接工艺参数的选择与设置非常重要,如电流、电压、焊接速度等。
如果选择不当或设置不合理,容易导致焊缝结构不良、焊接接头强度降低等缺陷的产生。
因此,在焊接前应对工艺参数进行正确的评估,根据焊接件的要求和材料特性选择合适的参数。
2.材料质量不良:焊接材料的质量对焊接接头的质量有很大的影响。
材料存在裂纹、氧化物、夹杂物等缺陷时,焊接过程中很容易产生焊接缺陷。
因此,在选材过程中应选择质量良好的焊接材料,并进行必要的预处理,如清洗、除锈等。
3.焊接操作不当:焊接操作人员的技术水平和操作经验对产生焊接缺陷起着决定性的作用。
操作不当、不熟练或粗心大意容易导致焊接缺陷的产生。
因此,操作人员应具备良好的焊接技术和严谨的工作态度,严格按照焊接规程进行操作。
下面是预防焊接缺陷的措施:1.合理选择焊接工艺参数:根据焊件的材料特性和焊接要求,选择合适的焊接工艺参数,如适当的电流、电压、焊接速度等。
并进行试焊,通过试焊找出最佳的焊接参数,以保证焊接接头的质量。
2.选择质量良好的焊接材料:在选择焊接材料时,应选择质量可靠的材料,并进行必要的预处理,如清洗、除锈等。
同时,根据焊接件的材料特性和要求选择合适的焊接材料。
3.提高焊接操作人员的技术水平:培训焊接操作人员,提高其焊接技术水平和操作经验。
引导焊接操作人员积极参加焊接技能比赛和培训班,不断提高操作技能,增强工作责任心和自我监督能力。
4.制定严格的焊接规程:对于一些复杂的焊接工艺,应制定详细的焊接规程,并严格执行。
规程中要包括焊接参数、焊接顺序、焊接方法、检验标准等内容,以保证焊接接头的质量。
5.加强质量控制和检验:建立完善的焊接质量控制体系,加强对焊接工艺过程的监控和控制。
焊接缺陷产生原因分析及防治措施

焊接缺陷产生原因分析及防治措施随着现代工业和制造业的发展,焊接技术的应用越来越广泛。
然而,在不断增加的焊接工程中,焊接缺陷问题也日益凸显。
焊接缺陷对焊接接头的质量和性能有着不可忽视的影响。
为了提高焊接接头的质量,需要深入了解焊接缺陷的产生原因,采取有效的防治措施。
一、焊接缺陷的分类1.焊接孔洞:是最严重的缺陷之一。
它们出现的原因可能是由于焊接区域的污染、松散物质、气孔或有效焊接熔池成分的合金不足导致。
2.焊接裂纹:由焊接过程引起的应力、过热或过冷引起的应力,不良的焊接施工或材料导致的应力等因素造成的裂纹。
3.焊接夹渣:焊接时,渣和气泡也可能在焊接接头中被引入。
这些夹杂物的存在会导致焊接接头的强度下降。
4.焊接凸起:易于出现在对焊、拖焊和坡口焊焊接的开端,并且很难消除。
二、焊接缺陷产生的原因1.焊接材料的质量问题。
如果使用的焊丝或焊条受到了污染或材料不合格等问题,焊接接头质量就可能受到影响。
2.操作不当。
如果焊接时没有遵循标准的焊接工艺,如焊接电流、电压和气体流量等设置不当,也会导致焊接缺陷。
3.人为原因。
焊接操作者经验和技术的欠缺,不正确的操作和操作步骤,从而引起焊接缺陷。
4.材料选择不当。
对于不同的焊接材料,需要选用不同的焊接工艺和方法,如果选用不当,也会导致焊接缺陷的产生。
三、防治焊接缺陷的措施1.提高焊接材料的质量。
在焊接材料的选择过程中,应尽量选用高品质的焊接材料,并确保其焊接性能符合要求。
2.正确选用焊接工艺。
焊接工艺应合理,具有合适的焊接参数、清洁度和气体保护等等。
3.加强焊接培训。
工人必须受到焊接培训并掌握合适的焊接技术、方法和技巧。
4.加强质量管理。
通过加强质量管理,避免质量问题和无序操作,杜绝相关缺陷的出现。
5.实施检测和验证。
利用非毁性检测等试验方法,确保焊接质量,消除潜在缺陷。
综上所述,理解焊接缺陷产生的原因是关键,如何采取有效的防治措施,对保证焊接接头的安全和质量至关重要。
- 1、下载文档前请自行甄别文档内容的完整性,平台不提供额外的编辑、内容补充、找答案等附加服务。
- 2、"仅部分预览"的文档,不可在线预览部分如存在完整性等问题,可反馈申请退款(可完整预览的文档不适用该条件!)。
- 3、如文档侵犯您的权益,请联系客服反馈,我们会尽快为您处理(人工客服工作时间:9:00-18:30)。
常见焊接缺欠的产生原因和防止措施
一、裂纹
1.1热裂纹
1.1.1产生原因:
1、焊缝金属结晶时造成严重偏析,存在低熔点杂质;
2、焊接拉伸应力的作用。
1.1.2防止措施:
1、选择偏析元素和有害杂质含量低的钢材和焊接材料,控制碳、硫、磷等含量;
2、调节焊缝金属化学成分,改善焊缝组织,细化焊缝晶粒,以提高焊缝金属塑性;
3、改善工艺因素,控制焊接规范,调整焊缝形状系数;
4、采用收弧板逐渐断弧。
衰减焊接电流等,填满弧坑,防止弧坑裂纹;
5、避免产生应力集中的焊接缺欠,如未焊透、夹渣等;
6、采取各种降低焊接应力的工艺措施,如预热和后热等。
1.2冷裂纹
1.2.1产生原因:
1、焊接接头存在淬硬组织;
2、扩散氢的存在和浓集;
3、较大的焊接拉伸应力。
1.2.2防止措施:
1、选用低氢型焊接材料,严格按规程进行焊前烘烤,彻底清理坡口和焊丝表面的油、水、锈、污等,减少焊缝金属中的扩散氢含量;
2、选择合理的焊接规范和工艺措施,如焊前预热、控制层间温度、焊后缓冷、进行焊后热处理等。
避免产生淬硬组织;
3、采取降低焊接应力的工艺措施。
1.3再热裂纹
1.3.1产生原因:
1、过饱和固溶的碳化物在再次加热时析出,造成晶内强化;
2、焊接残余应力。
1.3.2防止措施:
1、减少焊接应力和应力集中程度,如焊前预热、焊后缓冷等以及使焊缝与母材平滑过渡;
2、在满足性能要求的前提下,选用强度等级稍低于母材的焊接材料;
3、选用合理的热处理规范,减少在敏感区的停留时间。
如能满足性能要求,可取消焊后热处理。
二、孔穴
2.1气孔
2.1.1产生原因:
1、焊条、焊剂潮湿,药皮剥落;
2、填充金属与母材坡口表面油、水、锈、污等未清理干净;
3、电弧过长,熔池面积过大;
4、焊接电流过大,焊条发红,保护作用减弱;
5、保护气体流量小,纯度低,气体保护效果差;
6、气焊火焰调整不合适、焊炬摆动幅度大,焊丝搅拌熔池不充分,对熔池保护差;
7、操作不熟练;
8、焊接环境湿度大。
2.1.2防止措施:
1、不使用药皮剥落、开裂、变质、偏心和焊芯锈蚀的焊条。
焊条和焊剂按规程要求烘烤;
2、按规程要求做好焊前清理工作;
3、选用合适的焊接规范,控制焊接电流和电弧长度;
4、保证保护气体纯度,调整合适流量;
5、气焊时选用中性焰,加强火焰对熔池的保护;
6、提高操作技术;
7、采取去湿措施等,改善焊接环境。
2.2弧坑缩孔
2.2.1产生原因:
1、焊接电流过大;
2、操作方法不当,灭弧时间短。
2.2.2防止措施:
1、选用合适的焊接规范参数;
2、填满弧坑或采用电流衰减灭弧。
三、固体夹杂
3.1夹渣
3.1.1产生原因:
1、多道焊层间清理不彻底;
2、电流过小,焊接速度快,熔渣来不及浮出;
3、焊条或焊炬角度不当;
4、操作不熟练;
5、坡口设计不合理,焊层形状不良。
3.1.2防止措施:
1、彻底清理层间焊道;
2、选用合理的焊接规范;
3、提高操作技术;
4、合理选用坡口,改善焊层成形。
3.2金属夹杂
3.2.1产生原因:
1、氩弧焊采用接触引弧,操作不熟练;
2、钨极与熔池或焊丝短路;
3、焊接电流过大,钨棒严重烧损
3.2.2防止措施:
1、氩弧焊时尽量采用高频引弧;
2、熟练操作技术;
3、选用合适的焊接规范。
四、未熔合和未焊透
4.1未熔合
4.1.1产生原因:
1、运条速度过快,焊条或焊炬角度不合适,电弧偏吹;
2、坡口设计不良;
3、焊接规范不合适、电流过小,电弧过长等;
4、坡口或夹层的渣、锈清理不彻底。
4.1.2防止措施:
1、提高操作技术;
2、选用合适的规范参数;
3、选用合理的坡口形式;
4、彻底清理焊件。
4.2未焊透
4.2.1产生原因:
1、坡口设计不良,间隙过小;
2、焊接规范不合适;
3、操作不熟练。
4.2.2防止措施:
1、选用合理的坡口形式,保证组对间隙;
2、选用合适的规范参数;
3、提高操作技术。
五、形状和尺寸不良
5.1咬边
5.1.1产生原因:
1、电流过大或电弧过长;
2、焊条和焊丝的角度不合适;
3、埋弧焊时电压过低。
5.1.2防止措施:
1、选用合适的规范参数;
2、提高操作技术。
5.2焊瘤
5.2.1产生原因:
1、电流偏大或火焰能率过大;
2、操作不熟练。
5.2.2防止措施:
1、选用合适的规范参数;
2、提高操作技术。
5.3下塌
5.3.1产生原因:
1、焊接电流过大,速度过慢,使熔沁金属温度过高,液态金属在高温停留时间过长;
2、操作不熟练。
六、其他缺欠
6.1电弧擦伤
6.1.1产生原因:
1、焊把与工件无意接触;
2、焊接电缆破损;
3、未按规程操作,未在坡口内引弧,而在母材上任意引弧。
6.1.2防止措施:
1、启动焊机前,检查焊把,禁止与工件短路,遵守安全规程;
2、包裹绝缘带;
3、在坡口内引弧,加强规程教育,严肃工艺纪律。
6.2飞溅
6.2.1产生原因:
1、焊接电流过大;
2、未采取防护措施;
3、CO2气体保护焊焊接回路电感量不合适。
6.2.2防止措施:
1、选用合适的规范参数;
2、采用涂白垩粉等措施;
3、调整CO2气体保护焊焊接回路的电感。
七、焊接缺陷的返修
焊接缺陷的返修应遵循一定的程序,通常包括确定返修方案、清除焊接缺陷、补焊和检验等主要环节。
首先,应根据焊接检验结果确定缺陷的种类、部位和尺寸大小,并在实物上作出标记。
然后根据返修工件的具体情况,确定返修焊采用的焊接工艺和焊接材料。
返修焊一般以焊条电弧焊为主,它适应性广,灵活方便;但对于薄件或管道的穿透性缺陷,也可以用手工氩弧焊进行返修焊。
返修焊采用的焊接材料通常与正式施焊的相同,但也可使用强度等级相同的碱性焊条,以增加焊缝金属的抗裂能力。
返修焊的焊接工艺包括清除缺陷的方法、焊条型号和焊条直径、焊接电流、预热温度、后热及层间温度控制、焊接层次及次序、焊后热处理、焊接质量检验方法及合格标准等。
重要工作的返修焊接工艺需进行工艺评定。
焊接缺陷的的清除可用手工铲凿、电动角向磨光机修磨或碳弧气刨刨削的方法进行。
在清除缺陷时,要随时注意观察,以求彻底清除。
在清除缺陷后,还要对补焊部位修整坡口,在头尾部位修磨成缓坡状,便于补焊操作。
返修焊时预热温度比原焊件的预热温度要高20~50℃。
第一道焊接时,一般用较细直径的焊条,焊接电流可稍偏大,应保证熔合良好。
返修焊宜采用多层多道焊,焊接速度较快,使焊层薄一些。
焊接时宜采用不摆动操作方法。
每补焊一层后,按规定使焊接区缓冷,控制好层间温度。
每层焊道焊完后应仔细清理、认真检查、确认无缺陷后再焊补下一层。
层间接头要错开,注意接头的质量。
不需要焊后热处理的焊缝返修时,每焊补一层可以伴随锤击工艺,以消除返修焊时的应力;要求热处理的焊缝,返修后应与原焊件的热处理要求一样进行热处理。
热处理结束后,应仔细修磨焊缝,使其与原焊缝基本一致。
返修结束的焊缝,应按规定的检验方法检查,其质量不低于标准要求的规定。
当再次发现有不允许的缺陷时,要进一步分析原因,采取措施,并办理必要的审批手续,然后进行再次返修。
重要结构的返修一般不得超过二次,以免影响焊接接头的综合性能。