薄壁圆管弯曲模设计
弯管原理和弯管模具设计

冷弯管原理和弯管模具设计一.弯管原理弯管机标准模具包括:弯管模、夹紧块、导板(或滚轮)。
多节活芯、防皱块为选件D管件外径t管件壁厚R弯曲半管件外径D仅反映管件大小,管件弯曲加工的易难程度取决于管件的壁厚和弯曲半径,管件壁厚越小,半径越小加工难度越大。
一般我们用相对壁厚,相对弯曲半径作为弯管的工艺参数相对壁厚tx=t/D,相对弯曲半径Rx=R/D弯管机对于Rx>3D,tx>0.04的管件使用标准模具即可,对于Rx<3D,tx<0.04D 的管件弯管机可加上防皱板, 多节芯头等工艺措施来保证管件弯曲质量弯管机主要采用缠绕弯管工艺,缠绕弯管工艺可以比较容易在弯管模具加上各种措施以得到较好的管件质量。
弯管工艺弯管工艺,口径从DN25~DN104,壁厚1~2mm,其弯曲半径一般为1D,即是管子口径。
弯管最难处理的就是内圆弧,弯径小了容易起皱,上述工艺主要是消皱器起作用,所以能弯小半径的工件那消皱器的材料很讲究,太硬了,磨伤工件,太软了,不起作用。
是一种铜合金。
弯管芯棒的选取和使用摘要:介绍了管子在冷态弯制时的变形情况,以及通过合理选择芯棒及掌握其正确的使用方法,达到弯制出理想小半径管件的方法。
键词:应力;芯棒;相对弯曲半径;相对壁厚一、引言弯管技术广泛应用于锅炉及压力容器行业,中央空调制造业、汽车工业、航空航天工业、船舶制造业等多种行业,弯管质量的好坏,将直接影响到这些行业的产品的结构合理性,安全性、可靠性等。
因此,为了弯制出高质量的管件,就应该掌握管件在不同工艺条件下的加工技巧。
对于冷态弯管,合理选择芯棒的形成及掌握其正确的使用方法非常必要。
二、工艺分析在纯弯曲的情况下,外径为D、壁厚为S的管子受外力矩M的作用发生弯曲时,中性层外侧的管壁受拉应力σ1的作用而减薄,内侧管壁受压应力σ2的作用而增厚(见图1a)。
同时,合力F1和F2又使管子弯曲处的横截面发生变形而成为近似椭圆形(见图1b),内侧管壁在σ2的作用下还可能出现失稳而起皱(见图1c),为弯制出理想的管件,就应采取相应的措施来防止上述这些缺陷的产生,其中有芯弯管就是最常用的有效方法之一。
薄壁圆管弯曲模设计
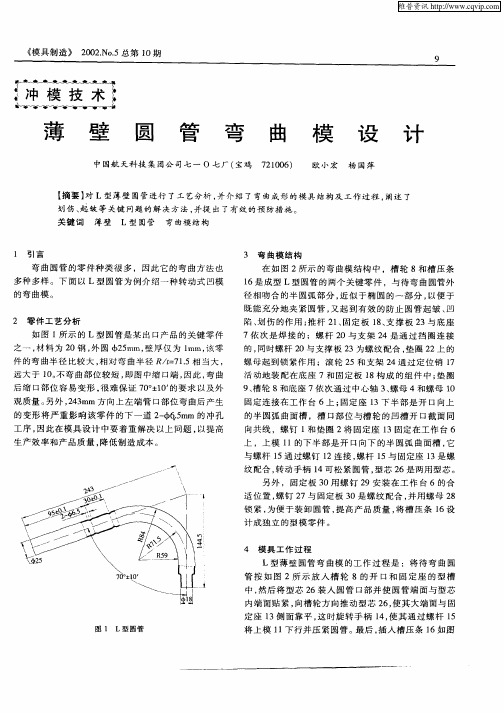
中 , 后 将 型芯 2 然 6装 入 圆管 口部并 使 圆 管端 面 与 型 芯 内端面 贴 紧 , 向槽 轮 方 向推 动 型 芯 2 , 6 使其 大 端面 与 固 定 座 1 面 靠 平 , 时 旋 转手 柄 1 , 其 通 过 螺 杆 1 3侧 这 4使 5
图 1 L型 圆 管
维普资讯
- 譬
. , { , 5 .
申 《 具 制造 》 2 0 .o5总 第 1 模 0 2N . 0期
9
. ◆ 一j 《 模一 技一 术一
二
薄 壁 圆 管 弯 曲 模 设 计
中 国航 天 科技 集 团公 司七 一 0 七厂 ( 宝鸡 7 1 0 ) 2 0 6 欧小 宏 杨 国萍
曲成 形 过程 。
中心 轴 3装 在 底 座 7中的 台 阶 高 度必 须 高 于 底 座
7的厚 度 O1 03 m, .- .m 以保 证 底 座 7能灵 活转 动 ; 时 , 同
中心 轴 3装 在 槽 轮 8中 的高 度 也 要 高 出槽 轮 8约 O1 . ~
03 m, .r 这样 能 从 根本 上 防 止 因槽 轮 8不 旋 转 而造 成 的 a
在 弯 曲过程 中 , 如果 槽 压条 1 槽轮 8和滚 轮 2 6与 5
之 间 的间 隙过 大或 过小 , 会 造成 圆管弯 曲 圆弧处 严 重 将
起皱 或划伤 , 时 , 通过旋 拧 螺杆 2 这 可 O来 调节 其 间隙 。
划 伤 现象 。
52 槽 轮 和槽 压 条 .
槽轮 8和 槽压 条 1 6的半 圆弧 曲面槽 的 截面 应 是性
将上 模 1 1下行 并压 紧 圆管 。最后 , 入槽 压 条 l 插 6如 图
薄壁大圆弧零件的折弯模具设计方法
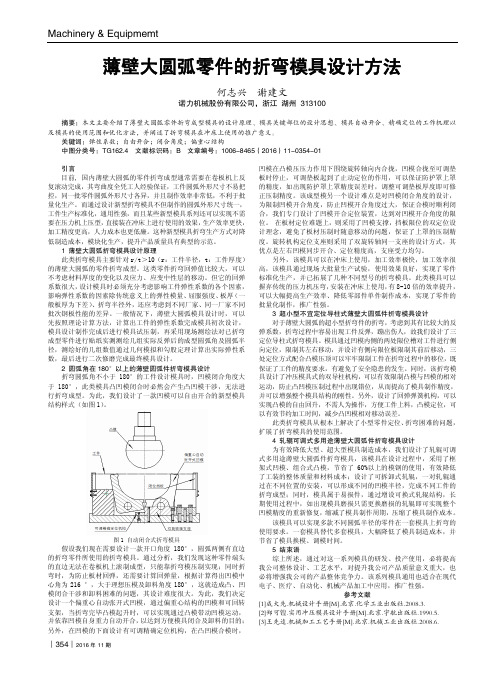
Machinery & Equipmemt︱354︱2016年11期薄壁大圆弧零件的折弯模具设计方法何志兴 谢建文诺力机械股份有限公司,浙江 湖州 313100摘要:本文主要介绍了薄壁大圆弧零件折弯成型模具的设计原理、模具关键部位的设计思想、模具自动开合、精确定位的工作机理以及模具的使用范围和优化方法,并阐述了折弯模具在冲床上使用的推广意义。
关键词:弹性系数;自由开合;闭合角度;偏重心结构中图分类号:TG162.4 文献标识码:B 文章编号:1006-8465(2016)11-0354-01引言 目前, 国内薄壁大圆弧的零件折弯成型通常需要在卷板机上反复滚动完成,其弯曲度全凭工人经验保证,工件圆弧外形尺寸不易把控,同一批零件圆弧外形尺寸各异,并且制作效率非常低,不利于批量化生产。
而通过设计新型折弯模具不但制作的圆弧外形尺寸统一,工件生产标准化,通用性强,而且某些新型模具系列还可以实现不需要在压力机上压型,直接装在冲床上进行使用的效果,生产效率更快,加工精度更高,人力成本也更低廉。
这种新型模具折弯生产方式对降低制造成本,模块化生产,提升产品质量具有典型的示范。
1 薄壁大圆弧折弯模具设计原理 此类折弯模具主要针对r/t>10(r:工件半径,t:工件厚度)的薄壁大圆弧的零件折弯成型。
这类零件折弯回弹值比较大,可以不考虑材料厚度的变化以及应力、应变中性层的移动。
但它的回弹系数很大,设计模具时必须充分考虑影响工件弹性系数的各个因素,影响弹性系数的因素除传统意义上的弹性模量、屈服强度、板厚(一般板厚为下差)、折弯半径外,还应考虑到不同厂家、同一厂家不同批次钢板性能的差异。
一般情况下,薄壁大圆弧模具设计时,可以先按照理论计算方法,计算出工件的弹性系数完成模具初次设计,模具设计制作完成后进行模具试压制,再采用现场测绘法对已折弯成型零件进行贴纸实测测绘几组实际反弹后的成型圆弧角及圆弧半径,测绘好的几组数值通过几何模拟和勾股定理计算出实际弹性系数,最后进行二次修磨完成最终模具设计。
圆管类弯曲模设计
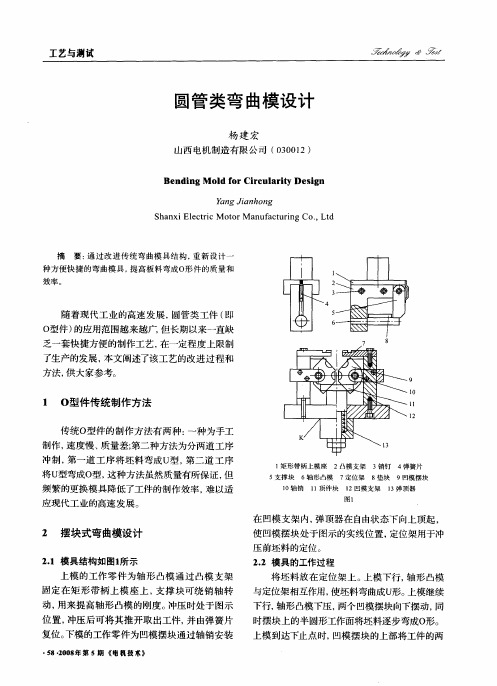
5 2 0 年 第 5期 《 帆 技 术 》 8.0 8 电
工艺与 j试 舅 I
个突耳弯曲成形。 上模 回程 , 弹顶器使凹模摆 块
摆 动 上升 , 形 后的 工件 套 在 轴 形 凸模 上 。 成 上模 到 上 止 点 时 , 开 支撑 块将 工件 取 出 , 撑 块在 推 支 弹簧 片 的作 用下复位 。 23 主 要计 算 .
R = / 13 E )  ̄ R (+ aR/t
MM 将使结构尺寸增大, 大, 增加模具成本。 若 MM 小 , 会使A A 和A2 2 过大, 11 A 影响圆管的 成型 ;【 0 角的值应使BB 1l稍大于工件外径。
25 主要 零部 件设 计 .
251上模设计 ..
若C 为M M 的 中点 , 两摆 块 的运 动 中及 两 在
摆块问无间隙的情况下, 点是经过O 点才到达 Al 2
A2 点的 , 以A2 所 与A2 两 点之 间一定 存在 间隙 , 且0M越 大 , 间隙值 越 小 。 1 其
B和B’ 1 1两点间的距离应近似于工件的外径 , 以便进行第一步的u 形弯曲; 它还须稍大于成品工
件的直径 , 以便 回程 时工件能从中间通过 。 在 设 计 时 , M 和 0 大 小 必 须 合 适 。 M 【 的 若
23 . 1回弹的计算 .
因圆 管 形 弯 曲件 的 弯 曲半 径 对 板 料 厚 度 的
比值 较大, 故弯曲的回弹不能忽略。 弯曲模的轴 形凸模直径计算公式为:
式中:F 自由弯曲力 ( 一 冲压行 程结束 , 尚未 进
行校 正 弯 曲时 的压 力 )N;
摆 块处 于非工作状 态 时, 在弹 顶器 的作用
下, 上 面紧 贴 在 定位 架 上 , 个 摆 块 的后 部设 其 两
薄壁方管的高效弯曲工艺分析和模具设计

薄壁方管的高效弯曲工艺分析和模具设计在多种健身器械的制造过程中,经常遇到矩形薄壁钢管小曲率半径的弯曲,这种弯管零件要求外观美观,加工时生产效率高,成本低。
为此,我们在生产中对该零件弯曲工艺、弯曲模具结构进行多次试验,并设计了一系列较合理的弯曲工艺和模具结构(□ 50× 50方管、□ 40× 40方管、□ 32× 32方管及30× 60矩形管等的弯曲) ,成功地解决了生产中的难题。
现就图1所示零件简述如下。
图1方形薄壁弯管1弯曲工艺分析各种资料对圆管弯曲工艺介绍的较多,而对方形钢管的弯曲,尤其是薄壁钢管的小曲率半径弯曲工艺和模具介绍得很少。
这种零件的弯曲与圆管的弯曲在工艺上存在较大的区别。
弯曲中容易出现外侧内凹、拉裂和内侧失稳起皱的缺陷。
通过分析,可把图1所示零件的弯角部分分解为四个部分的薄板件的弯曲。
即外壁的拉伸弯曲、内壁的压缩弯曲和左右侧壁的侧弯(如图2所示)。
a外壁拉伸弯曲;b内壁压缩弯曲;c侧壁薄板侧弯图2薄壁方管弯角部分的分解假定为纯塑性弯曲,图2内、外壁弯曲部分的受力状态和应力应变状态如图3所示。
弯曲时,外壁切向受拉应力伸长,其切向塑性应变<1 > 为ε =hρ× 1 0 0 % =2 01 1 0 × 1 0 0 % =1 8 2 %式中:ρ 弯曲中性层的曲率半径h弯曲外侧距中性层的距离考虑弯曲时的延伸,实际的弯曲中性层应在截面中心的内侧,故实际值将大于1 8 2 %。
管坯弯曲时切向应变ε 为最大的主应变,根据塑性变形体积不变条件,在另两个方向上必然产生与ε 符号相反的应变<1 > ,假定截面在弯曲过程中保持不变(管坯宽度方向上的应变εb为零)。
这时可视为平面应变状态,从而有|ε | =|εt| ,其中εt为管壁厚度方向上的变薄应变,当εt≥ 1 8 2 %时,管坯外壁极易发生断裂。
内壁的压缩弯曲变形部位的受力状态和应力应变状态(如图3)。
弯曲中等孔径薄壁方钢管的滚圆机的设计
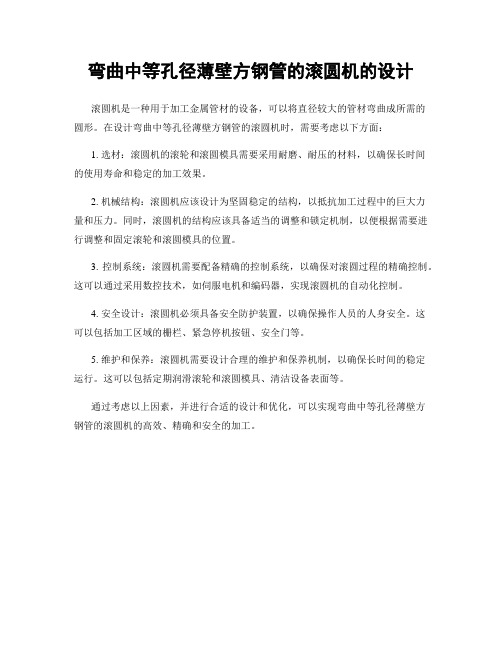
弯曲中等孔径薄壁方钢管的滚圆机的设计
滚圆机是一种用于加工金属管材的设备,可以将直径较大的管材弯曲成所需的
圆形。
在设计弯曲中等孔径薄壁方钢管的滚圆机时,需要考虑以下方面:
1. 选材:滚圆机的滚轮和滚圆模具需要采用耐磨、耐压的材料,以确保长时间
的使用寿命和稳定的加工效果。
2. 机械结构:滚圆机应该设计为坚固稳定的结构,以抵抗加工过程中的巨大力
量和压力。
同时,滚圆机的结构应该具备适当的调整和锁定机制,以便根据需要进行调整和固定滚轮和滚圆模具的位置。
3. 控制系统:滚圆机需要配备精确的控制系统,以确保对滚圆过程的精确控制。
这可以通过采用数控技术,如伺服电机和编码器,实现滚圆机的自动化控制。
4. 安全设计:滚圆机必须具备安全防护装置,以确保操作人员的人身安全。
这
可以包括加工区域的栅栏、紧急停机按钮、安全门等。
5. 维护和保养:滚圆机需要设计合理的维护和保养机制,以确保长时间的稳定
运行。
这可以包括定期润滑滚轮和滚圆模具、清洁设备表面等。
通过考虑以上因素,并进行合适的设计和优化,可以实现弯曲中等孔径薄壁方
钢管的滚圆机的高效、精确和安全的加工。
薄壁钢管弯曲模具设计

薄壁钢管弯曲模具设计弯管在制冷、机械、化工等行业中的应用十分广泛,薄壁钢管弯管的批量生产,一般是在弯管机上冷弯成形,由于薄壁钢管管壁支撑失稳临界力较低,弯曲部位常出现瘪皱等变形缺陷。
这些缺陷不但削弱钢管的强度,降低其承载能力,而且容易造成管内流动介质速度不均、产生涡流和弯曲部位积聚污垢等,影响弯管的正常使用,因此消除弯管缺陷成了弯管过程中最大难点,必须高度重视。
一、薄壁钢管弯曲受力与变形分析薄壁钢管弯曲时,管子在外力作用下弯曲变形,其弯曲部分的外缘在拉应力作用下管壁变薄,而管子内缘在压应力作用下管壁增厚。
由于在管子弯曲过程中,外缘拉应力和内缘压应力的合力都向中部作用,导致管子弯曲部位在水平面上的直径变大,垂直面上的直径减小,出现椭圆形。
同时,如果弯曲模具弧槽参数选择不当,不能起到强化弯曲部位管壁的作用,则管子内缘在压应力作用下,因管壁失稳临界力较低而产生波浪形皱褶。
由以上分析可知:薄壁钢管弯曲时极易产生瘪皱缺陷。
因此设计薄壁钢管弯曲模具时,必须合理确定其结构参数,以便钢管弯曲时,在模具作用下使管子产生一预加反应力,以抵消薄壁钢管弯曲时产生的椭圆变形,对弯曲部位的瘪皱缺陷进行合理控制.二、薄壁钢管弯曲模具设计简易薄壁钢管弯管机的结构如图1所示,弯管模具如图2所示,由弯管模块、滚动压轮和导轮组成。
滚动压轮和导轮安装于滚轮座中,并可在转盘的滑槽中上下移动。
弯管时,扳动手柄带动转盘绕轴转动,由导轮向管子施加压力,使其发生弯曲变形。
同时滚动压轮在钢管弯曲部位施加一定压力,通过轮上弧槽使之产生一反向预压力,以抵消钢管弯曲时产生的椭圆变形,使管子内缘与弯管模块弧槽紧密贴合,以强化弯曲部位管壁,消除内壁皱褶。
1.弯曲模块钢管弯曲后的半径和形状取决于弯管模块,因此,必须合理确定其结构参数,弯管模块如图3所示:图3 弯管模块1)弯管模块直径D由于外力取消后,被弯曲的钢管会产生回弹,所以弯管模块直径应小于两倍的弯管曲率半径,数值按下面的经验公式计算(2)圆弧槽半径r与倒圆半径r1因相对弯曲半径ε(ε=R0/d)的不同而有所不同,其目的是为了强化钢管弯曲部分管壁,避免皱褶,数值可按下式计算:r=Kd/2,其中K为按相对弯曲半径ε大小确定的系数,当ε≥3。
大口径薄壁小弯曲半径数控弯管有限元建模和实验
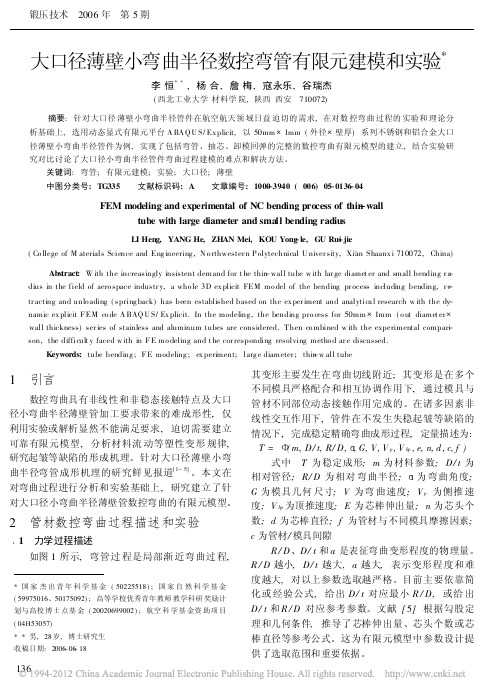
锻压技术 2006年 第5期大口径薄壁小弯曲半径数控弯管有限元建模和实验*李恒**,杨合,詹梅,寇永乐,谷瑞杰(西北工业大学材料学院,陕西西安 710072)摘要:针对大口径薄壁小弯曲半径管件在航空航天领域日益迫切的需求,在对数控弯曲过程的实验和理论分析基础上,选用动态显式有限元平台A BA Q U S/Ex plicit,以50mm 1mm (外径 壁厚)系列不锈钢和铝合金大口径薄壁小弯曲半径管件为例,实现了包括弯管、抽芯、卸模回弹的完整的数控弯曲有限元模型的建立,结合实验研究对比讨论了大口径小弯曲半径管件弯曲过程建模的难点和解决方法。
关键词:弯管;有限元建模;实验;大口径;薄壁中图分类号:TG335 文献标识码:A 文章编号:1000-3940(2006)05-0136-04FEM modeling and experimental of NC bending process of thin -walltube with large diameter and small bending radiusLI Heng,YANG He,ZHAN Mei,KOU Yong -le,GU Ru-i jie(Co llege of M aterials Science and Eng ineering ,N o rthwester n P olytechnical U niver sity,Xi'an Shaanx i 710072,China) Abstract:W ith the increasingly insistent demand for t he thin-wall tube w ith lar ge diamet er and small bending r a -dius in the field of aero space industr y,a who le 3D ex plicit FEM mo del of the bending pr ocess including bending,r e -tr acting and unlo ading (spring back)has been established based on the ex per iment and analytica l research w ith the dy -namic ex plicit F EM co de A BAQ U S/Ex plicit.In the modeling ,the bending pro cess for 50mm 1mm (o ut diamet er wall thickness)ser ies of stainless and aluminum tubes are considered.T hen co mbined w ith the experimental compar-i son,the difficult y faced w ith in F E mo deling and t he cor responding resolving metho d ar e discussed.Keywords:tube bending ;F E modeling ;ex periment;larg e diameter ;thin -w all tube*国家杰出青年科学基金(50225518);国家自然科学基金(59975016、50175092);高等学校优秀青年教师教学科研奖励计划与高校博士点基金(20020699002);航空科学基金资助项目(04H53057)**男,28岁,博士研究生收稿日期:2006-06-181 引言数控弯曲具有非线性和非稳态接触特点及大口径小弯曲半径薄壁管加工要求带来的难成形性,仅利用实验或解析显然不能满足要求,迫切需要建立可靠有限元模型,分析材料流动等塑性变形规律,研究起皱等缺陷的形成机理。
圆形工件的弯曲模具设计毕业设计
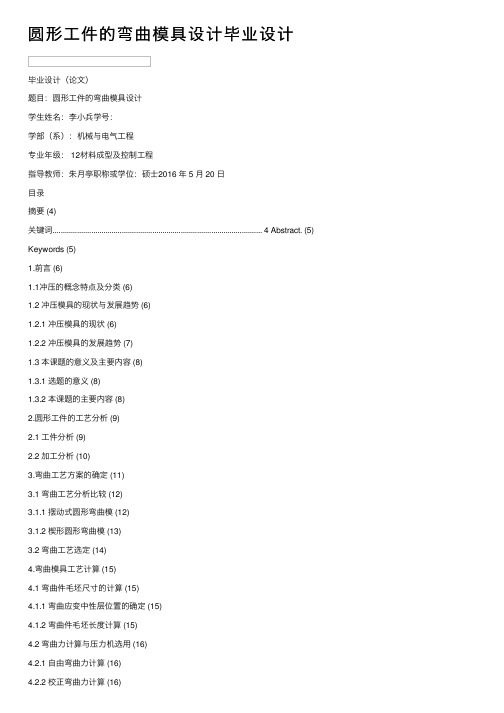
圆形⼯件的弯曲模具设计毕业设计毕业设计(论⽂)题⽬:圆形⼯件的弯曲模具设计学⽣姓名:李⼩兵学号:学部(系):机械与电⽓⼯程专业年级: 12材料成型及控制⼯程指导教师:朱⽉亭职称或学位:硕⼠2016 年 5 ⽉ 20 ⽇⽬录摘要 (4)关键词....................................................................................................... 4 Abstract. (5) Keywords (5)1.前⾔ (6)1.1冲压的概念特点及分类 (6)1.2 冲压模具的现状与发展趋势 (6)1.2.1 冲压模具的现状 (6)1.2.2 冲压模具的发展趋势 (7)1.3 本课题的意义及主要内容 (8)1.3.1 选题的意义 (8)1.3.2 本课题的主要内容 (8)2.圆形⼯件的⼯艺分析 (9)2.1 ⼯件分析 (9)2.2 加⼯分析 (10)3.弯曲⼯艺⽅案的确定 (11)3.1 弯曲⼯艺分析⽐较 (12)3.1.1 摆动式圆形弯曲模 (12)3.1.2 楔形圆形弯曲模 (13)3.2 弯曲⼯艺选定 (14)4.弯曲模具⼯艺计算 (15)4.1 弯曲件⽑坯尺⼨的计算 (15)4.1.1 弯曲应变中性层位置的确定 (15)4.1.2 弯曲件⽑坯长度计算 (15)4.2 弯曲⼒计算与压⼒机选⽤ (16)4.2.1 ⾃由弯曲⼒计算 (16)4.2.2 校正弯曲⼒计算 (16)4.2.3 压⼒机选⽤ (16)4.3 弯曲模⼯作部分尺⼨计算 (17)4.3.1 弯曲时凸模与凹模之间的间隙 (17)4.3.2 弯曲时凸模与凹模的宽度尺⼨ (18)5.弯曲模主要零件的设计 (18)5.1 模具主要零件⼆维三维图纸 (18)5.1.1 下模座 (18)5.1.2 下垫板 (19)5.1.3 凹模固定板 (20)5.1.4 凹模 (21)5.1.5 芯棒 (22)5.1.6 上凹模 (23)5.1.7 压料板 (24)5.1.8 上凹模固定板 (25)5.1.9 上垫板 (26)5.1.10 上模座 (27)5.2 模具三维总装配图 (28)5.3 模具关键冲压零件的⼯作过程 (1)6.弯曲模具数值模拟可⾏性分析及⼯艺矫正 (2)6.1 DEFORM软件分析流程 (3)6.2 DEFORM初次分析结果 (10)6.3模具改进后的分析 (12)结束语 (15)参考⽂献 (16)致谢 (17)圆形⼯件的弯曲模具设计摘要圆形⼯件是⼯业⽣产中⼀种不可或缺的零件,然⽽作为⼀种⾮典型弯曲件,⽬前对他的研究较少,本论⽂针对此情况,对圆形⼯件弯曲进⾏了细致的分析研究,主要内容为对圆形⼯件的多种弯曲⼯艺进⾏分析,设计⼀种弯曲⼯艺的模具,并运⽤三维软件PRO/E画出模具各零件并进⾏装配,运⽤⽬前⽐较先进的数值模拟软件DEFORM,对已设计的模具进⾏冲压模拟,分析其应⼒分布及可⾏性并对原始模具做改进,经过多次分析最终确定模具成型部位尺⼨,完成整个模具设计过程。
薄壁圆管冲孔模具设计

薄壁圆管冲孔模具设计1薄壁圆管冲孔模具设计初步构思按工艺流程先冲压翻边孔,并以翻边孔内插入定位销定位保证翻边孔和圆孔两孔间的中心距及角度尺寸公差。
在薄壁圆管圆弧外壁上冲孔,凸、凹模接触的零件工作面是圆弧面,因此凹模只能设计在圆管内腔,所以将凹模设计成镶嵌在仿形圆管内腔的芯棒上,刃口部位圆弧与芯棒外径圆弧重合,芯棒外径与圆管内径间隙单边0.2mm,方便装、卸工件;由于管壳将凹模包在圆管内,所以冲孔的落料只能在取下工件后排出;在取下工件前落料需在芯棒落料孔内暂时存放;上述是冲孔模具结构的初步构思,具体的模具零件结构、尺寸公差、零件的加工工艺性及装配工艺性还需从模具整体细致的设计。
构思冲压步骤:上料装卡管壳,将冲压完翻边孔的半成品管壳,插入芯棒,翻边孔端向外,将定位销插入翻边孔及芯棒定位孔,工件固定;凸模下行至冲压行程下限,冲孔完成;落料停留在芯棒落料孔内;凸模回程至行程上限,拔出定位销,取下工件,落料从落料孔排出。
2薄壁圆管冲孔模具设计分析按上述模具构思详细分析后进行冲孔模具零件的细节设计2.1凹模设计凹模设计成镶嵌在仿形圆管内腔的芯棒上;因此凹模外径Ф26±0.01mm与芯棒Ф26孔按过度配合设计;Ф14.1(0,-0.02)mm尺寸为凹模刃口,Ф15mm沉孔为冲压落料孔;R25.8mm 圆弧与芯棒外径圆弧一致,可采用将凹模镶嵌入芯棒后磨削芯棒外圆至凹模与芯棒圆弧完全重合;凹模刃口磨损后可通过底部多次增加垫片重新磨削开刃来增加凹模使用寿命。
2.2芯棒设计工件装卡胎具:芯棒外径Ф51.6mm按管壳内径尺寸间隙单边0.2mm设计,方便装、卸工件;芯棒根部50mm长度设计外径Ф52±0.01mm与底座Ф52mm圆孔过渡配合,防止冲压过程中芯棒前后窜动导致凸模及凹模报废;镶嵌固定凹模:Ф26±0.01mm沉孔为凹模镶嵌孔,与凹模外径按过渡配合装配;Ф16mm孔为冲压落料孔,暂时存放冲压圆孔的落料;60±0.01mm 尺寸扁与底座沉台外形过渡配合,避免芯棒在冲压过程中发生转动导致凸模及凹模报废;定位销孔定位管壳工件,Ф12mm销孔为定位管壳翻边孔的定位销孔,管壳插入芯棒后翻边孔与销孔对正,插入定位销,工件固定。
薄壁小弯曲半径管弯管模及工艺设计
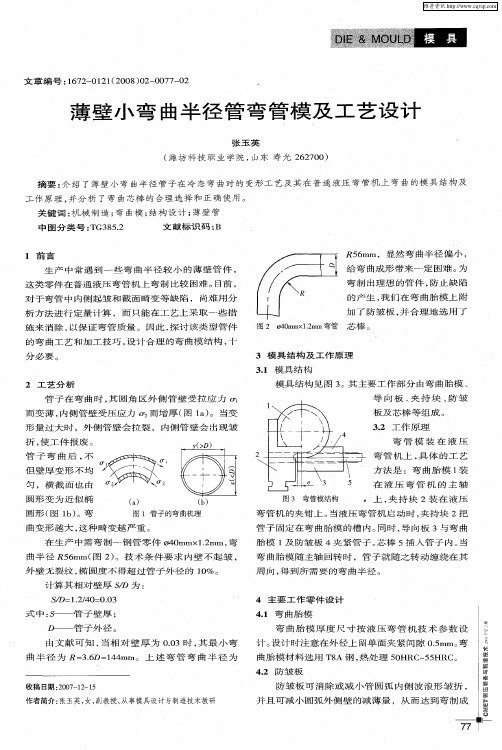
的形 状 是 影 响 弯 管 质 量 的两 个 重 要 因 素 。 如 果 芯 棒
超前 值 过 大 , 即芯 棒 伸 出 过 长 , 能 会 挤 裂 管 外 壁 ; 可 如果 插入 量不 足 , 起 不到 防变 扁 的作用 , 又 圆弧 内 侧 壁 还 可 能 起 皱 。 芯 棒 插 入 管 子 的 内侧 弯 曲 处 的 超 前
摘 要 : 绍 了薄 壁 小 弯 曲半 径 管 子 在 冷 态 弯 曲 时 的 变 形 工 艺 及 其 在 普 通 液 压 弯 管 机 上 弯 曲 的模 具 结 构 及 介
工 作 原 理 , 分 析 了弯 曲 芯 棒 的合 理 选 择 和 正 确 使 用 。 并 关 键 词 : 械 制 造 ; 曲模 ; 构 设 计 ; 壁 管 机 弯 结 薄
折 , 工 件 报废 。 使 管 子弯 曲后 , 不 但 壁厚 变 形不 均 匀 ,横 截 面 也 由 圆形 变 为 近 似 椭 圆形 ( l 。弯 图 b)
() a () b
弯 管 模 装 在 液 压
弯 管 机 上 , 体 的工 艺 具
方法 是 :弯 曲胎模 1 装
在 液 压 弯 管 机 的 主 轴 图 3 弯管模结构 , 上 , 持 块 2装 在 液 压 夹
周 向 , 到所 需 要 的弯 曲半径 。 得
计 算 其 相 对 壁 厚 SD 为 : /
S D = 1. 40=0. / 2/ 03
4 主要 工作 零件设 计
式中: . 卜
管 子 壁厚 ;
管子外 径 。
由 文 献 可 知 , 相 对 壁 厚 为 00 当 . 3时 , 最 小 弯 其
薄壁管数控弯曲芯轴的参数化设计及运动仿真
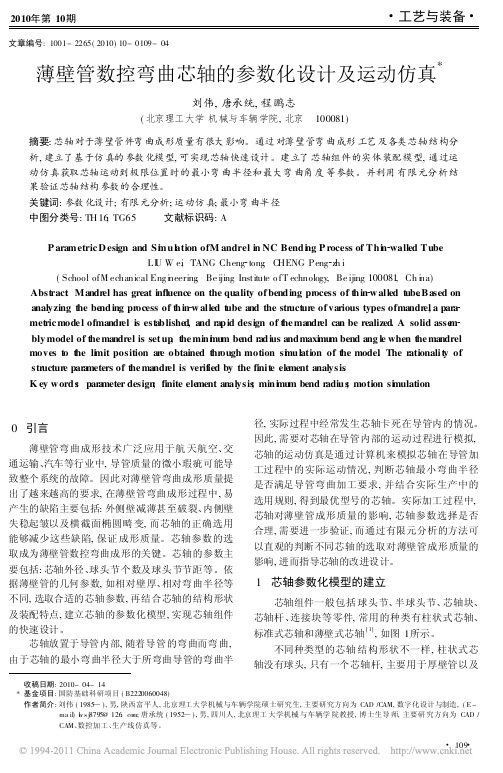
文章编号:1001-2265(2010)10-0109-04收稿日期:2010-04-14*基金项目:国防基础科研项目(B2220060048)作者简介:刘伟(1985 ),男,陕西富平人,北京理工大学机械与车辆学院硕士研究生,主要研究方向为CAD /CAM,数字化设计与制造,(E -ma il )l w s j 8795@126.co m;唐承统(1952 ),男,四川人,北京理工大学机械与车辆学院教授,博士生导师,主要研究方向为CAD /CA M 、数控加工、生产线仿真等。
薄壁管数控弯曲芯轴的参数化设计及运动仿真*刘伟,唐承统,程鹏志(北京理工大学机械与车辆学院,北京 100081)摘要:芯轴对于薄壁管件弯曲成形质量有很大影响。
通过对薄壁管弯曲成形工艺及各类芯轴结构分析,建立了基于仿真的参数化模型,可实现芯轴快速设计。
建立了芯轴组件的实体装配模型,通过运动仿真获取芯轴运动到极限位置时的最小弯曲半径和最大弯曲角度等参数。
并利用有限元分析结果验证芯轴结构参数的合理性。
关键词:参数化设计;有限元分析;运动仿真;最小弯曲半径中图分类号:TH 16;TG65 文献标识码:AP aram etric D esign and Si m ul a tion ofM andrel in NC Bendi n g P rocess of Thi n walled TubeLI U W e,i TANG Cheng tong ,C HENG Peng zh i(School ofM echanical Eng i n eering ,Be ijing Institute o fT echnology ,Be ijing 100081,Ch i n a)Abst ract :Mandr el has great influence on the quality of bending pr ocess of t hin w alled t ube .Based on analyzing t he be nding pr ocess of t hin w alled t ube and the str uct ur e of various types ofmandr el ,a par a met ric mode l ofmandr el is est ablishe d ,and r apid design of t he mandr el can be realized .A solid asse m bly model of t he mandrel is set up ,t he mini m u m be nd r adius andmaxi m u m bend ang le when t he mandrel moves t o t he li m it position ar e obtained t hr ough motion si m ulation of t he model .The r ationalit y of str uctur e par a meters of t he mandr el is verif ied by the finit e ele ment analysis .K ey w ords :par a meter design ;finite ele ment analysis ;mini m u m bend r adius ;motion si m ulation0 引言薄壁管弯曲成形技术广泛应用于航天航空、交通运输、汽车等行业中,导管质量的微小瑕疵可能导致整个系统的故障。
薄壁铝合金管手动折弯模
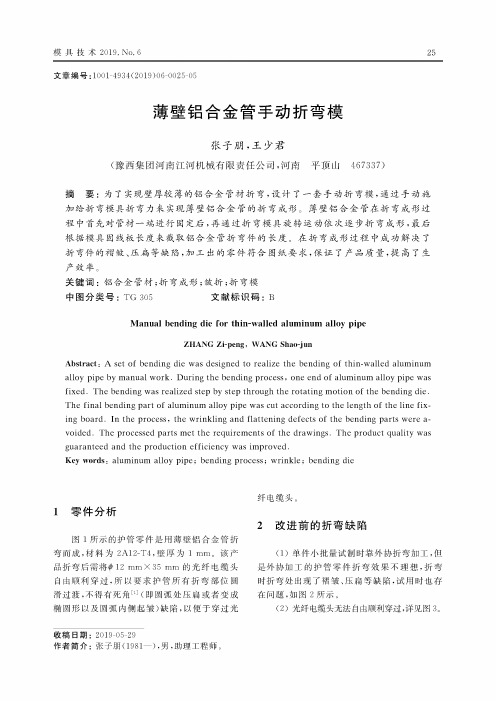
文章编号;1001-4934(2019)06-0025-05薄壁铝合金管手动折弯模张子朋,王少君(豫西集团河南江河机械有限责任公司,河南平顶山467337)摘要:为了实现壁厚较薄的铝合金管材折弯,设计了一套手动折弯模,通过手动施加给折弯模具折弯力来实现薄壁铝合金管的折弯成形。
薄壁铝合金管在折弯成形过程中首先对管材一端进行固定后,再通过折弯模具旋转运动依次逐步折弯成形,最后根据模具固线板长度来截取铝合金管折弯件的长度。
在折弯成形过程中成功解决了折弯件的褶皱、压扁等缺陷加口工出的零件符合图纸要求,保证了产品质量,提高了生产效率。
关键词:铝合金管材;折弯成形;皱折;折弯模中图分类号:TG305文献标识码:BManual bending die for thin-walled aluminum alloy pipeZHANG Zi-peng,WANGShao-junAbstract:A set of bending die was designed to realize the bending of thin-walled aluminum alloy pipe by manual work.During the bending process,one end of aluminum alloy pipe was fixed.The bending was realized step by step through the rotating motion of the bending die.The final bending part of aluminum alloy pipe was cut according to the length of the line fixing board.In the process,the wrinkling and flattening defects of the bending parts were avoided.The processed parts met the requirements of the drawings.The product quality was guaranteed and the production efficiency was improved.Key words:aluminum alloy pipe;bending process;wrinkle;bending die1零件分析图1所示的护管零件是用薄壁铝合金管折弯而成,材料为2A12-T4,壁厚为1mm。
- 1、下载文档前请自行甄别文档内容的完整性,平台不提供额外的编辑、内容补充、找答案等附加服务。
- 2、"仅部分预览"的文档,不可在线预览部分如存在完整性等问题,可反馈申请退款(可完整预览的文档不适用该条件!)。
- 3、如文档侵犯您的权益,请联系客服反馈,我们会尽快为您处理(人工客服工作时间:9:00-18:30)。
薄壁圆管弯曲模设计
中国航天科技集团公司七一O七厂(宝鸡721006)欧小宏杨国萍
【摘要】对L型薄壁圆管进行了工艺分析,并介绍了弯曲成形的模具结构及工作过程,阐述了划伤、起皱等关键问题的解决方法,并提出了有效的预防措施。
关键词薄壁L型圆管弯曲模结构
1引言
弯曲圆管的零件种类很多,因此它的弯曲方法也多种多样。
下面以L型圆管为例介绍一种转动式凹模的弯曲模。
2零件工艺分析
如图1所示的L型圆管是某出口产品的关键零件之一,材料为20钢,外圆ф25mm,壁厚仅为1mm,该零件的弯曲半径比较大,相对弯曲半径R/t=71.5相当大,远大于10。
不弯曲部位较短,即图中缩口端,因此,弯曲后缩口部位容易变形,很难保证70°±10′的要求以及外观质量。
另外,243mm方向上左端管口部位弯曲后产生的变形将严重影响该零件的下一道2-ф6.5mm的冲孔工序,因此在模具设计中要着重解决以上问题,以提高生产效率和产品质量,降低制造成本。
243
30±0.1
95±0.1
2-ф65
5
4
4
1
ф25
70°±10ˊ
ф18
图1L型圆管
3弯曲模结构
在如图2所示的弯曲模结构中,槽轮8和槽压条16是成型L型圆管的两个关键零件,与待弯曲圆管外径相吻合的半圆弧部分,近似于椭圆的一部分,以便于既能充分地夹紧圆管,又起到有效的防止圆管起皱、凹陷、划伤的作用;推杆21、固定板18、支撑板23与底座7依次是焊接的;螺杆20与支架24是通过挡圈连接的,同时螺杆20与支撑板23为螺纹配合,垫圈22上的螺母起到锁紧作用;滚轮25和支架24通过定位销17活动地装配在底座7和固定板18构成的组件中;垫圈9、槽轮8和底座7依次通过中心轴3、螺母4和螺母10固定连接在工作台6上;固定座13下半部是开口向上的半圆弧曲面槽,槽口部位与槽轮的凹槽开口截面同向共线,螺钉1和垫圈2将固定座13固定在工作台6上,上模11的下半部是开口向下的半圆弧曲面槽,它与螺杆
15通过螺钉12连接,螺杆15与固定座13是螺纹配合,转动手柄14可松紧圆管,型芯26是两用型芯。
另外,固定板30用螺钉29安装在工作台6的合适位置,螺钉27与固定板30是螺纹配合,并用螺母28锁紧,为便于装卸圆管,提高产品质量,将槽压条16设计成独立的型模零件。
4 模具工作过程
L型薄壁圆管弯曲模的工作过程是:将待弯曲圆管按如图2所示放入槽轮8的开口和固定座的型槽中,然后将型芯26装入圆管口部并使圆管端面与型芯内端面贴紧,向槽轮方向推动型芯26,使其大端面与固定座13侧面靠平,这时旋转手柄14,使其通过螺杆15将上模11下行并压紧圆管。
最后,插入槽压条16如图2所示的位置,扳动推杆21使其带动底座7围绕中心轴3旋转直至螺钉27限位,从而完成对L型圆管的弯曲成形过程。
在弯曲过程中,如果槽压条16与槽轮8和滚轮25之间的间隙过大或过小,将会造成圆管弯曲圆弧处严重起皱或划伤,这时,可通过旋拧螺杆20来调节其间隙。
27
2830 2921
22
232425261236 5 47
8
9
20
191817161514131210 11
图2 圆管弯曲模结构
1.螺钉
2.垫圈
3.中心轴
4.螺母
5.垫圈
6.工作台
7.底座
8.槽轮
9.垫圈 10.螺母 11.上模 12.螺钉
13.固定座 14.手柄 15.螺杆 16.槽压条 17.定位销 18.固定板 19.挡圈 20.螺杆 21.推杆 22.垫圈
23.支撑板 24.支架 25.滚轮 26.型芯 27.螺钉 28.螺母 29.螺钉 30.固定板
5模具设计中应注意的问题
5.1中心轴
中心轴3装在底座7中的台阶高度必须高于底座7的厚度0.1~0.3mm,以保证底座7能灵活转动;同时,中心轴3装在槽轮8中的高度也要高出槽轮8约0.1~0.3mm,这样能从根本上防止因槽轮8不旋转而造成的划伤现象。
5.2槽轮和槽压条
槽轮8和槽压条16的半圆弧曲面槽的截面应是性质和尺寸完全一致的,并且开口大端接缝处应为R0.2~0.5mm的圆弧倒角,这样不仅能有效地预防起皱、凹陷和变形问题,而且能防止因模口过锐而造成的划伤问题。
5.3型芯
型芯26伸入圆管部分长度不应太长,一般以不超过10mm为宜,其外径与圆管内孔ф23mm可以设计成0.1mm的双面间隙,这样既能防止变形,又便于顺利卸模;型芯26呈台阶状,大直径段靠近圆管的端面为定位用,将圆管套入型芯后,向模口部位推动型芯,使型芯的定位大端面与固定座13的外侧贴紧靠平,这样就保证了如图1所示的243mm和144.5mm的尺寸。
5.4回弹问题
回弹是弯曲件最常见的问题之一,对于本文所述的薄壁圆管,因原材料的供货批次不同,因而其材料性能上并不是完全一致的,因此解决回弹问题的方法不能完全限制,建议用如图2所示的固定板30及其它零件构成的组件结构,这种结构可以根据实际情况调节并限制弯曲行程,从而彻底解决回弹不一致的问题。
6结束语
经过生产实践表明,这种圆管弯曲模结构,不仅弥补了设计上的缺陷,而且能圆满地解决生产中存在的划伤、起皱、变形、凹陷及回弹等问题,并且使产品的合格率达到了98%以上,大大提高了生产效率,同时也降低了生产成本和能耗,为企业带来了一定的社会和经济效益。