机床与刀具5.5
机械制造技术基础习题-机械制造技术基础
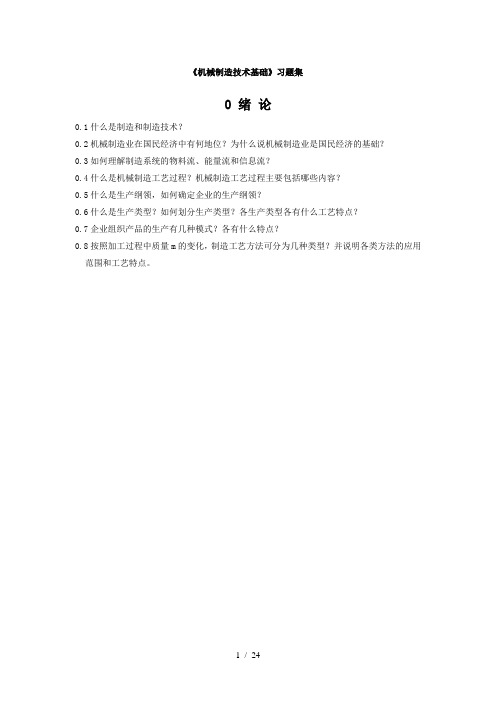
《机械制造技术基础》习题集0 绪论0.1什么是制造和制造技术?0.2机械制造业在国民经济中有何地位?为什么说机械制造业是国民经济的基础?0.3如何理解制造系统的物料流、能量流和信息流?0.4什么是机械制造工艺过程?机械制造工艺过程主要包括哪些内容?0.5什么是生产纲领,如何确定企业的生产纲领?0.6什么是生产类型?如何划分生产类型?各生产类型各有什么工艺特点?0.7企业组织产品的生产有几种模式?各有什么特点?0.8按照加工过程中质量m的变化,制造工艺方法可分为几种类型?并说明各类方法的应用范围和工艺特点。
1.金属切削加工的基本知识1.1何谓切削用量三要素?它们是怎样定义的?1.2刀具标注角度参考系有几种?它们是由什么参考平面构成的?试给这些参考平面定义? 1.3 试述刀具标注角度的定义。
一把平前刀面外圆车刀必须具备哪几个基本标注角度?这些标注角度是怎样定义的?它们分别在哪个参考平面内测量?1.4试述判定车刀前角γ0、后角α0和刃倾角λs,正负号的规则。
1.5试述刀具标注角度与工作角度的区别。
为什么横向进给时,进给量不能过大?1.6曲线主切削刃上各点的标注角度是否相同,为什么?1.7 试标出图1-1所示端面切削情况下该车刀的γ0,α0,λs,αn,k r,k r’,γ0’,α0’,以及αp,f,h D,b D。
如果刀尖的安装高于工件中心h值,切削时a,b点的实际前、后角是否相同?以图说明之。
图1-1 题1.7图示1.8 砂轮的特性有哪些?砂轮的硬度是否就是磨料的硬度?如何选择砂轮?1.9常用刀具材料的种类有哪些?它们有什么特性?从化学成分、物理机械性能说明陶瓷、立方氮化硼、金刚石刀具材料的特点和应用范围。
1.10刀具材料必须具备哪些性能?1.11 试列举普通高速钢的品种与牌号,并说明它们的性能特点及应用。
试列举常用硬质金的品种与牌号,并说明它们的性能特点及应用范围2.金属切削过程的基本规律及其应用2.1金属切削过程的本质是什么?切削过程中的三个变形区是怎样划分的?各变形区有特征? 2.2影响加工表面粗糙度的因素有哪些?如何减小表面粗糙度?2.3影响切屑变形的因素有哪些?它们是怎样影响切屑变形的?2.4 试判断题图2—1(a)、(b)两种切削方式哪种平均变形大,哪种切削力大,为什么?切削条件:k r=90°,rε=0.5 mm,αp=1 mm,f=1 mm/r。
CHD6163车削中心简介及参数

CHD6163数控车床简介一、产品简介及用途CHD6163机床是三轴联动半闭环控制的车削中心,主机由日本FANUC 0i-TC 系统控制,主电机采用广域交流伺服电机,功率为22/30KW,可对φ400以内的轴类零件和φ630以内的盘类零件进行各种车削、钻削、铣削,其最大加工长度为1000mm;2000mm。
CHD6163机床床身采用整体铸造成型,圆筒式筋板结构,床身导轨面与水平倾斜45度布局,具有较大的承载截面,刚性强,吸震性好,不易变形,可保证高精度切削加工。
主传动系统采用广域交流伺服电机驱动,配合高分辨率的脉冲编码器和主轴液压制动装置,可实现高精度的C轴分度功能和铣削功能,并具有低速大扭矩的输出特性。
机床纵横向运动副采用交流伺服电机驱动,配合THK滚珠丝杠和贴塑导轨,具有良好的动态特性和运动精度。
机床配备意大利进口十二工位动力刀台和轴向、径向动力刀具,可完成车削以外的钻削、铣削、攻丝等复合加工,提高零件加工的工序集中能力和加工精度。
机床配备独立的自动润滑系统和冷却排屑装置以及全封闭防护,保证机床始终处于良好的工作状态,可大大提高机械加工的自动化水平。
二、主要技术参数1. 加工范围最大回转直径:Φ680mm最大切削直径(轴 / 盘):Φ400mm/Φ630 mm最大切削长度:1000mm;2000mm2. 规格卡盘尺寸: 15"主轴型式: ISO A2–11主轴转速范围:20~2000r/min主轴通孔直径:Φ100mm通过棒杆直径:Φ84mm (采用中空卡盘和中空油缸时)最小分辨率: 0.001mm快速移动速度:X轴13m/min,Z轴13m/min切削进给速度: 0~5000 mm/minX/Z轴最大行程:X轴375mm,Z轴1030mm/2030mm3. 机床精度标准GB/T16462-1996《数控卧式车床精度检验》(等同于ISO 230/2-1997)定位精度:(X)0.012mm,(Z)0.025mm/0.03mm重复定位精度:(X)0.005mm,(Z)0.012mm/0.016mm反向差值 : (X)0.006mm,(Z)0.012mm4. 主轴传动系统主轴伺服电机功率(无级调速):22/30kW (FANUC αp50/6000i)主轴润滑:使用进口高级润滑脂润滑,全封闭,免维护5. 进给系统交流伺服电机扭矩X/Z轴:22NM/22NM6. 动力刀塔刀塔工位数:12工位 (12个工位均可安装动力刀具)动力刀具驱动电机功率(kW): 5.5/7.5 (FANUC主轴电机)外圆刀尖回转直径(㎜):φ606动力刀具最大回转直径(㎜):φ660换刀方式:按最短路径,任意换刀。
JDPANNT5.5五轴模块使用说明书要点
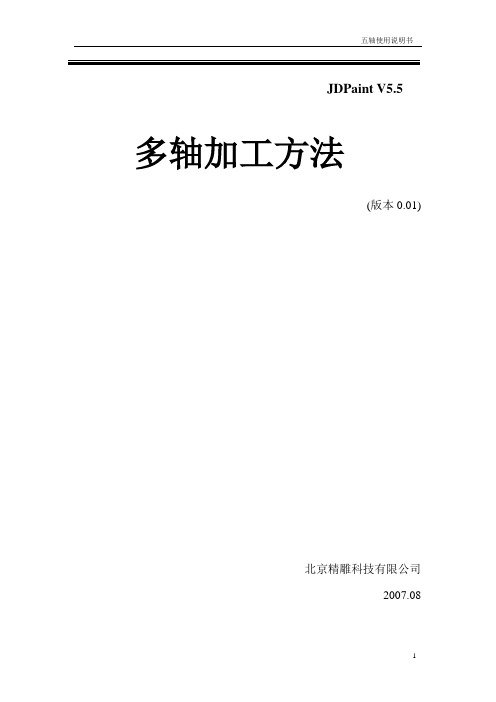
JDPaint V5.5 多轴加工方法(版本0.01)北京精雕科技有限公司2007.08前言本文档从多轴基本知识、控制系统及控制软件(EN3D)设定及加工、JDPAINT5.5五轴编程模块等方面介绍一些常用的多轴加工技术,用以帮助使用者了解多轴加工操作和设定,减少多轴路径编程时间,改善多轴刀具路径质量。
本文档主要以实例的方式来介绍多轴编程加工,在阅读时可以结合实例来学习,可以达到更好的效果。
不同的人有不同的思路,因此请不要把本文档中介绍的一些技术视为多轴加工的基本原理,多轴加工技术内容相当丰富,不是薄薄一本手册可以覆盖的。
同时需要进行大量的实际加工,从中体会多轴加工的不同之处,灵活运用我们现有的编程功能,才能对五轴加工有一定的领悟。
阅读文档的读者应具备以下几方面的背景知识:1、对三轴精雕机有一定了解;2、具备一些模型的三轴加工经验;3、具备一些三维建模(或者曲面造型)经验者更佳。
第一章绪论在过去模具加工很少使用五轴加工,问题在于多轴机床的价格昂贵及人员培训与技术上的困难,大家皆敬而远之。
近年来因模具交期紧迫及价格压缩,五轴机床标准化产量,价格逐年下降,使五轴加工渐渐的受到模具业重视,多轴机床将是继高速加工机后另一个有效的加工工具。
1.1 五轴加工与三轴加工比较五轴加工与三轴加工比较,有以下几方面的优点:1) 减少工件非加工时间,可以提高加工效率五轴加工的一个主要优点是仅需经过一次装夹即可完成复杂形状零件的加工。
和多次装夹相比,它可极大地提高加工和生产能力,显著缩短产品加工周期及加工成本,并且提高了加工精度。
2) 刀具可以摆到更好的位置来加工曲面五轴加工完成一些三轴加工无法完成的加工,比如有负角的曲面零件加工,刀具可以摆到更好的位置来加工曲面,如图1-1所示。
图1-1 刀具可以摆到更好的位置来加工曲面图1-2 缩短加工时间, 改善表面加工质量3) 可以缩短曲面加工时间,改善曲面表面的加工质量五轴加工可通过将刀具倾斜一定角度,例如用铣刀侧刃进行铣削等,缩短加工时间;另外路径间距相同的情况下,用五轴加工工件表面的残留量要比三轴加工小得多,有利于改善加工曲面的表面光洁度,如图1-2所示。
西门子 802D数控系统编程指令统
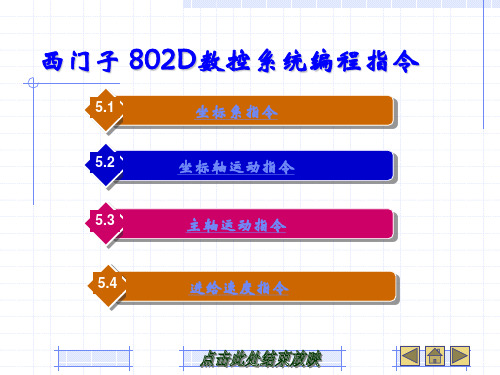
2.指令功能
通过在程序中写入 G25或 G26指令和 地址 S下的转速,可以限制主轴的极限值 范围。与此同时原来设定数据中的数据被 覆盖。
G25或 G26指令均要求一独立的程序段, 原先编程的转速 S保持存储状态。
5.3.3主轴定位SPOS
用 SPOS=ACP(…); SPOS=ACN(…)
利用功能 SPOS 可以把主轴定位到一 个确定的转角位置,然后主轴通过闭环位 置控制保持在这一位置。
程序在运行时可以通过插入程序跳转 指令改变执行顺序。NC 程序在运行时以 写入时的顺序执行程序段。
GOTOF Label; 向前跳转 GOTOB Label; 向后跳转
5.10.3有条件跳转
用IF-条件语句表示有条件跳转。如果 值不等于零,即满足跳转条件,则进行跳 转。跳转目标只能是有标记符的程序段。 该程序段必须在此程序之内。
图5-11 外角和内角的拐角特性
5.6辅助功能
5.6.1常用的辅助功能 5.6.2辅助功能的应用
5.6.1常用的辅助功能
西门子 802D数控系统常用的辅助功能 M代码:
M0-程序停止 M2-程序结束 M3-主轴顺时针旋转 M4-主轴逆时针旋转 M5-主轴停转
5.6.2辅助功能的应用
(1)程序段中最多有 5 个 M 功能。 (2)如果 M0,M1,M2 功能位于一个 有坐标轴运行指令的程序段中,则只有在 坐标轴运行之后这些功能才会有效。 (3)在执行 M5 指令时并不等待主轴停 止,坐标轴已经在主轴停止之前开始运动。
5.7.2切槽循环CYCLE93
切槽循环指令格式如下: CYCLE93(SPD,SPL,WIDG,DIAG, STA1,ANG1,ANG2,RCO1,RCO2, RCI1,RCI2,FAL1,FAL2,IDEP, DTB,VARI)
FANUC 0i-MC数控系统编程指令及应用

度补偿,如图5-1所示。对于数控铣床和加工中心,通常都是在XY坐
标平面内进行轮廓加工。该组指令为模态指令,一般系统初始状态为
G17状态,故G17可省略。
指令格式 ;
G17 G18 G19
下一页 返回
5.1 尺寸系统指令
G17用来选择X/Y平面 G18用来选择X/Z平面 G19用来选择Y/Z平面 G17、G18、G19三个坐标平面的含义见表5-2 。
第5章 FANUC 0i-MC数控系统编程指 令及应用
5.1 尺寸系统指令 5.2 坐标轴运动指令 5.3 主轴运动指令 5.4 进给速度指令(G94、G95) 5.5 刀具和刀具补偿 5.6 辅助功能(M) 5.7 标准铣削循环及子程序调用
下一页
第5章 FANUC 0i-MC数控系统编程指 令及应用
功能:刀具以圆弧轨迹从起始点移动到终点。
指令格式:在XY平面内的圆弧:
G02
R _
G17 G03 X_ Z_ I _ J _ F_;
上一页 下一页 返回
5.2 坐标轴运动指令
在XZ平面内的圆弧:
G02 G18 G03
X_ Z_
R_ I _ K _
F_;
在YZ平面内的圆弧:
G19
G02 G03
X_ Z_ R _ J _ K _
上一页 下一页 返回
任务一 DHCP服务的安装与配置
(9)在“添加排除”界面中,输入不打算租借给客户机使 用的1P地址范围,可以输入一个IP地址,也可输入一段1P 地址,单击“下一步”按钮,打开图6-11所示的“租约期限” 界面。
(10)在“租约期限”界面中,设置租约时间,租约期限默 认为8天。租约期限是指一个IP地址分配给DHCP客户机后, 此IP地址可以连续使用的最长时限。在租约期限到期时,将 更新租约或收回IP地址。单击“下一步”按钮打开图6-12所 小的“配置DHCP选项”界面。
数控机床机械机构

床
C
超精密 精密机床、精密数控机床、仪表机床、高精度
级
加工中心
第5章 数控机床机械机构
2) 结构尺寸的选择
滚珠丝杠螺母副的结构尺寸主要有:
(1)名义直径D0 (2)螺距t (3)丝杠长度L
(4)滚珠直径d0 (5)滚珠的工作圈数、列数和工作滚珠总数等
尤其是名义直径与刚度直接相关,直径越大,承载能力 和刚度越大,但直径大转动惯量也会随之增加,使系统的 灵敏度降低。所以,一般是在兼顾二者的情况下选取最佳 直径。
•(1) 传动效率高、摩擦损失小。 •(2) 运动灵敏,低速时无爬行。 •(3) 传动精度高,刚性好。 •(4) 滚珠丝杠螺母副的磨损很小,使用寿命长。 •(5) 无自锁能力,具有传动的可逆性,故对于垂直使用的丝杠,由于重 力的作用,当传动切断时不能立即停止运动,应增加自锁装置。 •(6) 滚珠丝杠螺母副制造工艺复杂,滚珠丝杠和螺母的材料,热处理和 加工要求与滚动轴承相同,且螺旋滚道必须磨削,因而制造成本高。
本章教学要求:
本章主要让学生了解数控机床对主传动 系统、进给传动系统的要求;了解主轴的调 速方法;熟悉主轴部件、滚珠丝杠螺母副、 直线电动机、数控机床的导轨、自动换刀装 置;认识数控回转工作台、分度工作台等主 要辅助装置。为学生初步具有设计机床传动 系统的能力打下基础。
第5章 数控机床机械机构
5.1 概 述
图5-5是啮合式电磁离 合器(也称牙嵌式电磁离 合器)的结构图。
图5-5 啮合式电磁离合器
1-线圈 2-衔铁 3-螺钉 4-弹簧 5-定位环 6-隔离环 7-螺钉 8-磁轭 9-旋转环
第5章 数控机床机械机构
4.内置电动机主轴变速(电主轴)
电主轴的出现 大大简化了主运 动系统结构,实 现了所谓的“零 传动”, 它具有 结构紧凑、重量 轻、惯性小、动 态特性好等优点, 并可改善机床的 动平衡,避免振 动和噪声,在超 高速切削机床上 得到了广泛的应 用。
上海西马特机械制造制造 家用车床CO 说明书

家用车床型号:CO使 用 说 明 书使用前请仔细阅读使用说明书 上海西马特机械制造有限公司制造重要的安全说明使用机床前,请仔细阅读全部安全使用说明书内容和警告字句。
操作者:1.为防止触电事故的发生,避免给人体带来伤害,在使用电动工具、机床和设备时,应加强基本的安全防护;2.要保持机床周围环境的整洁,混乱的环境只会带来不安全的危险; 3.切勿将机床安置在易受雨淋或潮湿的地带,机床周围不允许存放易燃液体(如汽油)等;4.孩子们都应该远离工作场地;5.为保护人身安全,机床的所有设备都应有安全接地装置;6.操作者应经常保持清醒的头脑,疲倦时不要进行操作;7.凡酗酒和使用麻醉剂者,易影响对事物的判断能力,所以有上述情况的不准进行操作;8.切勿穿着宽大衣服、领带或佩带贵重首饰,以免被正在运转的零件带走而给您带来危险;9.操作者应戴上工作帽,务必把长发罩住;10.要戴上防护眼镜防止铁屑飞入眼睛;工作期间,操作者要保持正确的姿势、人体应保持平衡状态;主要技术参数最大工件回转直径100 毫米最大工件长度 125 毫米主轴孔径 10 毫米尾座套筒孔径10 毫米主轴转速100-3800r p m±10%电机输出功率 150 W包装尺寸 600*400*310 毫米净/毛 重 13 / 22 公斤结构示意图1 2 3 4 5 6 7 8 9 10 11 12 1314 15 16 17主要构件1. 齿轮罩壳2. 头架3. 急停开关4. 变速旋钮5. 电源指示灯6. 故障指示灯7. 卡盘防护罩 8. 3爪 卡盘9. DC 电机 10. 刀架 (可选)11. 尾座 12. 尾座手轮13. 手轮 14. 底座15. 手轮 16. 床身17. 丝杆1.床头箱机床主轴的传动是通过电动机的同步带轮皮带与主轴同步带轮传动的,主轴的无级变速是由#4操作手柄进行调节的,在电器面板上可以找到转速的范围。
#7卡盘防护罩的作用是防止操作人员将卡盘钥匙遗忘在卡盘上,同时启动机床导致钥匙飞出来的安全防护。
刀具寿命管理办法

机加刀具寿命管理办法1.目的:跟踪刀具使用寿命,实现刀具定期更换、刃磨,减少刀具异常对生产和产品质量的影响。
2.范围:机加车间专机、加工中心/钻攻中心用刀具,这些刀具需刻印有刀具代号和编号方可进行寿命统计和管理。
3.职责:3.1机加车间负责初拟刀具寿命。
3.2技术部组织评审具体刀具寿命并确认,并配合机加车间对刀具寿命的更改和完善。
3.3机加车间现场管理员负责本办法在本部门的有效实施和推行,以及对生产现场刀具更换和刀具寿命的跟踪及记录。
3.4采购部、质管部、物管部分别负责刀具需外协时的刃磨、验收、收发,在此期间需保持刀具代号和编号不发生损失,以确保刀具寿命可持续追溯。
4.刀具寿命管理办法:4.1刀具寿命相关术语及定义4.1.1刀具寿命:是指一把新刀具从开始投入使用直到报废为止的总切削时间或切削工件的数量,其中包含多次刃磨时间(刃磨次数以n表示),所以刀具寿命等于刀具耐用度和(n+1)的乘积。
4.1.2刀具耐用度:刃磨后的刀具自开始切削直到磨损量达到磨钝标准所经历的总切削时间或切削工件的数量。
4.1.3正常损坏:指刀具在设定加工数量外损坏的状态定义。
4.1.4异常损坏:指刀具在设定加工数量内损坏的状态定义。
4.1.5特别情况举例说明:当一把刀在一个程序周期中先后加工一个产品的m 个部位(如钻孔攻丝等),则刀具寿命等于刀具耐用度与(n+1)以及m三者的乘积。
4.2刀具寿命标准的制定4.1.1机加车间各现场管理员负责对各生产线所使用的刀具寿命进行初稿的编制,并详细注明刀具名称、生产线及工序、刀具代号和刀具编号,参照《刀具寿命管理明细表》的格式填写。
4.1.2《刀具寿命管理明线表》初稿编制完成后提交技术部,由技术部组织评审,评审定稿之《刀具寿命管理明细表》由公司领导批准下发各生产线后使用,同时存档备案。
4.1.3《刀具寿命管理明细表》的变更应按工艺变更程序执行。
4.1.4《刀具寿命管理明细表》应悬挂于各工序生产设备上,以便实施刀具寿命的跟踪管理。
5.5 典型机床夹具《机械制造技术基础(第3版)》教学课件
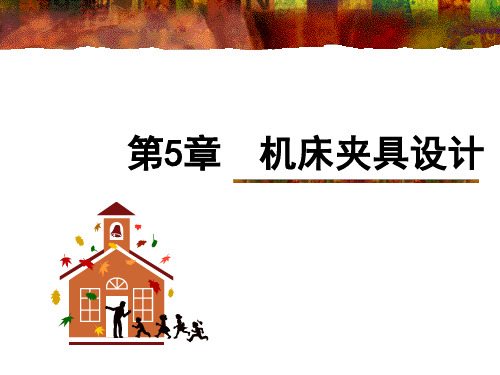
5.5.3 镗床夹具
1.镗床夹具的主要类型及使用范围
1)单支承前导向镗模 1)单支承前导向
5.5.3 镗床夹具
1.镗床夹具的主要类型及使用范围
(1)单支承导向镗模
2)单支承后导向
L/D>1(长孔)
L/D<1(短孔)
b)
c)
5.5.3 镗床夹具
1.镗床夹具的主要类型及使用范围
第5章 机床夹具设计
5.5 典型机床夹具
5.5.1 钻床夹具
1.钻床夹具的主要类型及使用范围
(1)固定式钻模
(1)固定式钻模
如何确定钻模在机床工作台的位置?
(2)回转式钻模
(3)翻转式钻模
(3)翻转式钻模
(4)盖板式钻模
(5)滑柱式钻模
5.5.1 钻孔夹具
2.钻床夹具的结构特点及设计
图5-97 后引导的双支承导向镗模
2.镗床夹具的结构特点及设计
2.镗床夹具的结构特点及设计
支架 镗套 支承板 压板 夹紧螺钉 可调支承
压板
(1) 镗套
1)回转式镗套
适用于镗杆速度高 于20m/min时的镗孔。
a-内滚式镗套 b-外滚式镗套 1、6-导向支架 2、5-镗套 3-导向滑套
4-镗杆
(1) 镗套
2)固定式镗套
适用于镗杆速度低 于20m/min时的镗孔。
(1) 镗套 镗刀杆的结构
d<50mm
D>50mm
(1) 镗套 镗套引刀槽
尖头 定向键 双螺旋面
(1) 钻套
钻套
1)固定钻套
钻套
2)可换钻套
钻套
3)快换钻套
钻套
数控刀具知识点总结归纳
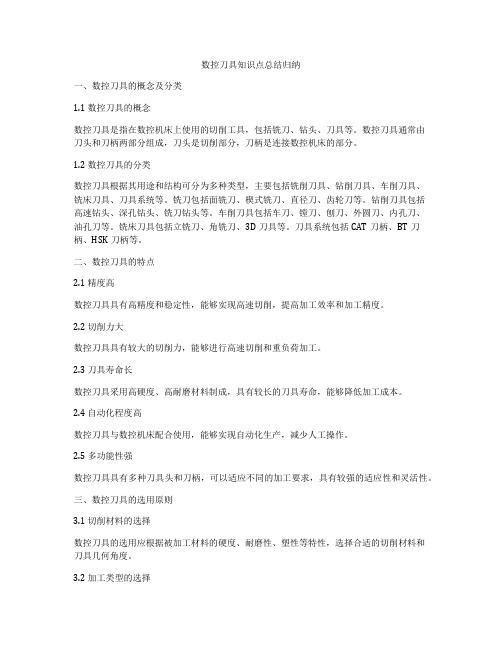
数控刀具知识点总结归纳一、数控刀具的概念及分类1.1 数控刀具的概念数控刀具是指在数控机床上使用的切削工具,包括铣刀、钻头、刀具等。
数控刀具通常由刀头和刀柄两部分组成,刀头是切削部分,刀柄是连接数控机床的部分。
1.2 数控刀具的分类数控刀具根据其用途和结构可分为多种类型,主要包括铣削刀具、钻削刀具、车削刀具、铣床刀具、刀具系统等。
铣刀包括面铣刀、楔式铣刀、直径刀、齿轮刀等。
钻削刀具包括高速钻头、深孔钻头、铣刀钻头等。
车削刀具包括车刀、镗刀、刨刀、外圆刀、内孔刀、油孔刀等。
铣床刀具包括立铣刀、角铣刀、3D刀具等。
刀具系统包括CAT刀柄、BT刀柄、HSK刀柄等。
二、数控刀具的特点2.1 精度高数控刀具具有高精度和稳定性,能够实现高速切削,提高加工效率和加工精度。
2.2 切削力大数控刀具具有较大的切削力,能够进行高速切削和重负荷加工。
2.3 刀具寿命长数控刀具采用高硬度、高耐磨材料制成,具有较长的刀具寿命,能够降低加工成本。
2.4 自动化程度高数控刀具与数控机床配合使用,能够实现自动化生产,减少人工操作。
2.5 多功能性强数控刀具具有多种刀具头和刀柄,可以适应不同的加工要求,具有较强的适应性和灵活性。
三、数控刀具的选用原则3.1 切削材料的选择数控刀具的选用应根据被加工材料的硬度、耐磨性、塑性等特性,选择合适的切削材料和刀具几何角度。
3.2 加工类型的选择数控刀具的选用应考虑加工类型,包括粗加工、精加工、半精加工等,选择合适的刀具结构和材料。
3.3 切削性能的选择数控刀具的选用应考虑切削速度、进给速度和切削深度等切削参数,选择合适的刀具材料和刀具形状。
3.4 经济性的选择数控刀具的选用应考虑加工成本和生产效率,选择经济性合适的刀具。
3.5 安全性的选择数控刀具的选用应考虑刀具的安全性能,包括刀具的断裂、飞溅、抛射等安全因素。
四、数控刀具的保养和维护4.1 刀具的清洁数控刀具在使用前后应进行清洁,去除切削刀具上的杂质和切屑,减少切削面的摩擦和磨损。
机械制造工程原理习题集
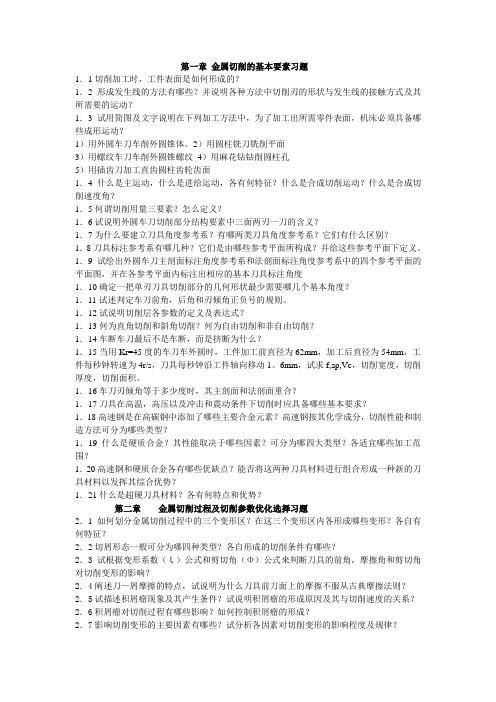
第一章金属切削的基本要素习题1.1切削加工时,工件表面是如何形成的?1.2形成发生线的方法有哪些?并说明各种方法中切削刃的形状与发生线的接触方式及其所需要的运动?1.3试用简图及文字说明在下列加工方法中,为了加工出所需零件表面,机床必须具备哪些成形运动?1)用外圆车刀车削外圆锥体。
2)用圆柱铣刀铣削平面3)用螺纹车刀车削外圆锥螺纹4)用麻花钻钻削圆柱孔5)用插齿刀加工直齿圆柱齿轮齿面1.4什么是主运动,什么是进给运动,各有何特征?什么是合成切削运动?什么是合成切削速度角?1.5何谓切削用量三要素?怎么定义?1.6试说明外圆车刀切削部分结构要素中三面两刃一刀的含义?1.7为什么要建立刀具角度参考系?有哪两类刀具角度参考系?它们有什么区别?1.8刀具标注参考系有哪几种?它们是由哪些参考平面所构成?并给这些参考平面下定义。
1.9试绘出外圆车刀主剖面标注角度参考系和法剖面标注角度参考系中的四个参考平面的平面图,并在各参考平面内标注出相应的基本刀具标注角度1.10确定一把单刃刀具切削部分的几何形状最少需要哪几个基本角度?1.11试述判定车刀前角,后角和刃倾角正负号的规则。
1.12试说明切削层各参数的定义及表达式?1.13何为直角切削和斜角切削?何为自由切削和非自由切削?1.14车断车刀最后不是车断,而是挤断为什么?1.15当用Kr=45度的车刀车外圆时,工件加工前直径为62mm,加工后直径为54mm,工件每秒钟转速为4r/s,刀具每秒钟沿工件轴向移动1。
6mm,试求f,ap,Vc,切削宽度,切削厚度,切削面积。
1.16车刀刃倾角等于多少度时,其主剖面和法剖面重合?1.17刀具在高温,高压以及冲击和震动条件下切削时应具备哪些基本要求?1.18高速钢是在高碳钢中添加了哪些主要合金元素?高速钢按其化学成分,切削性能和制造方法可分为哪些类型?1.19什么是硬质合金?其性能取决于哪些因素?可分为哪四大类型?各适宜哪些加工范围?1.20高速钢和硬质合金各有哪些优缺点?能否将这两种刀具材料进行组合形成一种新的刀具材料以发挥其综合优势?1.21什么是超硬刀具材料?各有何特点和优势?第二章金属切削过程及切削参数优化选择习题2.1如何划分金属切削过程中的三个变形区?在这三个变形区内各形成哪些变形?各自有何特征?2.2切屑形态一般可分为哪四种类型?各自形成的切削条件有哪些?2.3试根据变形系数(ξ)公式和剪切角(Φ)公式来判断刀具的前角,摩擦角和剪切角对切削变形的影响?2.4阐述刀—屑摩擦的特点,试说明为什么刀具前刀面上的摩擦不服从古典摩擦法则?2.5试描述积屑瘤现象及其产生条件?试说明积屑瘤的形成原因及其与切削速度的关系?2.6积屑瘤对切削过程有哪些影响?如何控制积屑瘤的形成?2.7影响切削变形的主要因素有哪些?试分析各因素对切削变形的影响程度及规律?2.8分析切削力的来源?切削合力为什么要分解为三个切削力?并说明各切削分力的定义及其作用。
JDPAINT5.5刀具路径模板功能介绍
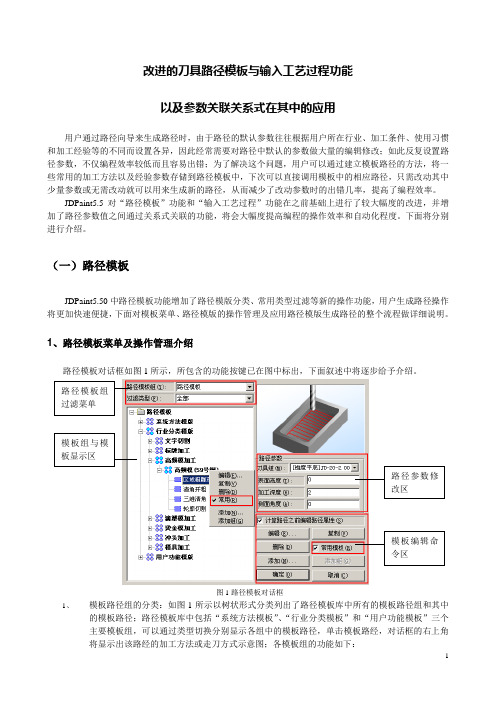
改进的刀具路径模板与输入工艺过程功能以及参数关联关系式在其中的应用用户通过路径向导来生成路径时,由于路径的默认参数往往根据用户所在行业、加工条件、使用习惯和加工经验等的不同而设置各异,因此经常需要对路径中默认的参数做大量的编辑修改;如此反复设置路径参数,不仅编程效率较低而且容易出错;为了解决这个问题,用户可以通过建立模板路径的方法,将一些常用的加工方法以及经验参数存储到路径模板中,下次可以直接调用模板中的相应路径,只需改动其中少量参数或无需改动就可以用来生成新的路径,从而减少了改动参数时的出错几率,提高了编程效率。
JDPaint5.5对“路径模板”功能和“输入工艺过程”功能在之前基础上进行了较大幅度的改进,并增加了路径参数值之间通过关系式关联的功能,将会大幅度提高编程的操作效率和自动化程度。
下面将分别进行介绍。
(一)路径模板JDPaint5.50中路径模板功能增加了路径模版分类、常用类型过滤等新的操作功能,用户生成路径操作将更加快速便捷,下面对模板菜单、路径模版的操作管理及应用路径模版生成路径的整个流程做详细说明。
1、路径模板菜单及操作管理介绍路径模板对话框如图1所示,所包含的功能按键已在图中标出,下面叙述中将逐步给予介绍。
路径模板组过滤菜单模板组与模板显示区路径参数修改区模板编辑命令区图1路径模板对话框1、模板路径组的分类:如图1所示以树状形式分类列出了路径模板库中所有的模板路径组和其中的模板路径;路径模板库中包括“系统方法模板”、“行业分类模板”和“用户功能模板”三个主要模板组,可以通过类型切换分别显示各组中的模板路径,单击模板路经,对话框的右上角将显示出该路经的加工方法或走刀方式示意图;各模板组的功能如下:①、系统方法模板组:此模板组提供了JDPaint5.50所有的加工方法及其走刀方式,用户可以直接设置其中各路径的默认参数和选项,替代路径向导快速生成某一加工路径;②、行业分类摸板组:此模板组提供了目前应用精雕机加工的几种典型行业加工工艺,如高频模、滴塑模等。
JDPAINT5.5快速定位路径和加工标记点

快速定位路径和加工标记点软件研发部陈虹在JDP5.50以前的版本输出的ENG路径都不包括快速定位路径,加工效率不高。
JDP5.50版本输出的ENG路径新增快速定位路径,弥补了这个缺陷。
为了方便JDP5.50版本输出的ENG路径的使用,我们在EN3D 7.10控制软件中新增了加工标记点功能。
下面我简单介绍一下快速定位路径的应用和加工标记点的使用。
一、JDP5.50版本中的快速定位路径的应用快速定位路径在G代码中用定位指令G00表示,用于快速连接相邻的两个区域之间的加工路径,运动过程中刀具不作切削加工,即空切运动。
在曲面模型加工中,加工定位的次数比较频繁,空切路径较多,减少定位路径的高度是提高加工效率的重要方法。
1、JDP5.50版本中的快速定位路径原理及意义1)JDP5.50版本中的快速定位路径的参数设置JDP5.50以前的版本输出的ENG路径没有快速定位路径,因此在加工过程中两个切削区域之间或者两切削层之间进行转换时,要先将刀具抬到一个安全的Z高度平面处,即EN3D 控制软件中所设定的定位高度处,再水平移动到下一个切削路径的起始位置下刀进行切削。
这个定位高度平面是从工件原点沿Z向往上抬起的高度平面。
它是一个相对高度值,一般应高于工件及夹具的最高点;其抬刀路径如图1所示,F6为机床设置的定位高度值。
使用这种方式加工具有相对较高的安全性,缺点是抬刀距离较长,对于抬刀比较频繁的路径来说,加工效率较低。
而且当工件原点低于曲面模型最高点时,确定机床上的定位高度参数值比较麻烦。
图1 机床设置的定位高度示意图我们在JDP5.50版本输出的Eng5.50格式中增加了快速定位路径输出。
机床加工时两个切削区域之间或者两切削层之间的抬刀将不再抬高到机床上所设定的定位高度平面处,而是根据路径中生成的快速定位轨迹抬高到曲面模型局部区域中一个相对安全的高度平面,然后再快速水平移动到下一个切削路径的起始位置下刀进行切削(如图2所示);此高度平面是相对于加工曲面模型的局部区域最高点向上抬起的高度位置,一般设置为2~5mm,设置过小则加工时有可能会划伤工件。
CNC刀具开发与管理规范[模板]
![CNC刀具开发与管理规范[模板]](https://img.taocdn.com/s3/m/06adcce64a7302768f993940.png)
CNC刀具开发与管理规范1.概述适用于所有CNC加工的刀具管理操作。
2.目的规范刀具(包括标准刀具和非标准刀具)的设计、验证、采购、验收、入库、使用、报废、回收等全过程的管理,确保刀具满足产品质量和产能的要求,降低采购成本特制作此作业办法。
3.术语无4. 角色与职责5. 内容5.1刀具开发:5.1.1新项目开发由制造工程提出刀具需求,通知采购邀请至少3家有资质的刀具供应商与我司一起进行刀具设计开发,根据我司提供参数(机台品牌、冷却介质、加工切削量、加工材料材质等)供应商给出设计方案,并预估出刀具寿命,方案评估确认后由供应商打样。
5.2 刀具验证:5.2.1采购通知供应商送样刀具不可以出现厂家标识,只标识供应商代号及刀具规格,每款刀至少验证5pcs,由开发主导进行,生产协助进行寿命统计、参数记录,品质参与产品品质判定,并形成试作报告,开发对试作出现异常进行分析总结,验证结果达到预期寿命形成刀具清单,试作报告由开发存档。
或验证NG则由采购通知供应商重新设计、送样。
5.2.2初次送样验证合格后,采购依据刀具清单进行小批量请购,由制造工程主导进行小批量验证,方法同上,若验证OK形成试作报告,并更新刀具清单,此时由采购通知供应商送承认书,一式三份。
5.2.3制程优化加工周期、加工效果或是更换冷却介质须由开发主导进行如上验证,验证OK后开发发行ECN 变更刀具清单。
5.3 刀具请购:6.3.1采购需求:由生产计划根据生产需求提出申请(安全库存由刀具仓库管理员或配刀技术员提出申请),刀具请购单由仓库提出需求。
6.3.2采购执行:采购部接到刀具请购单后按采购程序规定进行外购,并于1个工作日内回复刀具交期,如不回复,视为在请购单要求日期内购回。
5.4 仓库收货:刀具购回后,供应商将送货单和刀具一起送至刀具仓库,送货单上须注明采购单号和每种刀具的规格明细,送货单上的项目名称须和公司的规格一致。
仓管员开送检单给IQC,待IQC检验合格后录入系统,并每把刀做好账物卡一致。
- 1、下载文档前请自行甄别文档内容的完整性,平台不提供额外的编辑、内容补充、找答案等附加服务。
- 2、"仅部分预览"的文档,不可在线预览部分如存在完整性等问题,可反馈申请退款(可完整预览的文档不适用该条件!)。
- 3、如文档侵犯您的权益,请联系客服反馈,我们会尽快为您处理(人工客服工作时间:9:00-18:30)。
将工件放在托板和导轮间; 工件(连同导轮)或砂轮作横向进给; 导应轮用的:中用心于线加仅工倾具斜有微阶小梯的或角成度形(回约转3表0′面)的→工对件工件产 生小的轴→向气推缸力套,外使圆之磨靠削住。挡块5,得到可靠轴向定位。
5.6 磨床和砂轮
■特点(与外圆磨床比)
■①应生用产效率高 工件不打中心孔,装夹省时省力,可连续磨削; ②磨削表面的尺寸精度(IT5)、形状精度(圆 主要度用、于圆成柱批度、)大高量,生表产面中质加量工高圆(柱Ra面小连)续;的光 轴③和易阶于梯实轴现→自机动床化调→整配费自时动。上料机构;
活塞环磨床、齿轮磨床、螺纹磨床。 其它磨床:珩磨机、研磨机、抛光机、超精加工机床等。
5.6 磨床和砂轮
(一)外圆磨床:主要用来磨削外圆柱面和圆锥面
1●.床万身能1:外磨圆床磨的基床础(件M。14内32部A用)作液压缸的油池。
●头架2:安装和夹持工件,并带动工件旋转。在水平面内可逆时针转90°。
■→可组用成顶及尖或布卡局盘
●内圆磨具3:支承磨内孔的砂轮主轴→单独的电机驱动。 ●砂轮架4:支承并传动高速旋转的砂轮主轴。装在滑鞍6上,当需要磨削短 圆锥面时,可在水平面内调整到一定角度(±30°)。 ●尾座5:与头架2的前顶尖一起支承工件。 ●横向进给机构和滑鞍6:转动手轮7,使横向进给机构带动滑鞍6及其上砂 轮架作横向进给运动。 ●手轮7:操纵横向进给运动。 ●工作台8:上下两层组成。
v砂 70 ~ 80v导 通过切向磨削力带动工件旋转;
③导轮则依靠摩擦力限制工件旋转 v工 v导 10 ~ 50m / min
→利用磨削砂轮和工件间形成的(很大)速度差:v砂 v工
产生磨削作用。 改变导轮转速→调节工件的圆周进给速度。 导轮→(树脂或橡胶为粘结剂)刚玉砂轮。
5.6 磨床和砂轮
纵磨法
横磨法
5.6 磨床和砂轮
●纵磨法(贯穿磨削法):使工作台作纵向往复运动进行 磨削的方法。 表面成形方法→轨迹法。 ① 表面成形运动:
工件沿轴线往复移动→纵向进给运动( f纵 );
工件旋转——圆周进给运动( nw 、 f周 )。
砂轮旋转运动(磨外圆 n砂、磨内孔 n)内→主运动;
②砂轮的横向进给运动
■主参●●数砂用:轮内最架圆大偏磨磨转具削,,工磨 磨件短内直圆圆径锥柱3面面20((㎜横纵。磨磨法法));; 可以转动头架,磨圆锥面。
5.6 磨床和砂轮
磨削外圆柱面
扳转工作台 磨削长圆锥面
扳转砂轮架磨削短圆锥面
扳转头架磨削 内圆锥面
图6-9 M1432A型万能外圆磨床典型加工示意图
5.6 磨床和砂轮
上工作台可绕下工作台在水平面内回转一个角度 10→磨削锥度不大的长
圆锥面。
5.6 磨床和砂轮
头架
工作台
内圆 磨具
横向进操 作板
万能外圆磨床外观图
5.6 磨床和砂轮
■万能外圆磨床 的传动原理
5.6 磨床和砂轮
■磨削方式及所需要的运动 基本磨削方式:纵磨法(贯穿磨削法)和横磨法(切入磨削法)
5.6 磨床和砂轮
2.无心外圆磨床(无心磨床)→外圆磨削的一种特殊形式 ●磨削时,直接将工件放在砂轮、导轮之间,用托 板支承,工件被磨削的外圆面作定位面→定位基 准为工件外圆中心线。
5.6 磨床和砂轮
无心外圆磨削的加工示意图
5.6 磨床和砂轮
■工作原理 ①工件放在砂轮1和导轮3之间→托板支承磨削。 ②砂轮和导轮的同向旋转,磨削砂轮的圆周速度很大:
■磨削方式 ●纵磨法(贯穿磨削法)→加工光轴
将工件从机床前面放到托板上,推入磨削区后,工件旋转,
同工●时件v轴的导垂向轴直向向前进控移给制动→工,由件从导的机轮圆床的周另中进一心给端线速出在度去竖就直磨平削面完内毕向。前倾斜了
角引起。
● v导水平 使工件作纵向进给(导轮应修正成回转双曲面。
5.6 磨床和砂轮
5.6 磨床和砂轮
(二)平面磨床→主要用于磨削各种零件的平面 ■磨削方式 ➢ 端面磨削:用砂轮端面磨削。-立轴
特点:接触面积大,生产率↑,散热条件↓,Ra ↑
应用:主要用于粗加工和半精加工 ➢ 周边磨削(圆周磨削):用砂轮圆周磨削—卧轴
特点:接触面积小,生产率↓ ,散热条件↑,Ra↓
应用:主要用于精加工
■磨床的主要类型
■主及外内平应要非圆圆面用用金磨磨磨:于属床床床零材:::件料万普卧卧的的能通轴轴精精外内矩圆加加圆圆台台工工磨 磨 平平,。床床面面尤、磨、磨其无床普床是心通、、淬内外立立硬圆圆轴轴钢磨磨矩圆件床床台台、、、平平高行面无面硬星磨心磨度式床外床特内、圆。殊圆磨材磨床料床。 工具磨床:工具曲线磨床、钻头沟槽磨床、丝锥沟槽磨床。 刀具和刃具磨床:万能工具磨床、拉刀刃磨床、滚刀刃磨床。 各种专门化磨床:曲轴磨床、凸轮轴磨床、花键轴磨床、
5.6 磨床和砂轮
■主要类型和运动
5.6 磨床和砂轮
➢ 卧轴矩台平面磨床:用砂轮的周边磨削,工件往复移动。 表面成形方法→轨迹法。
f横 —间歇进给运动→切入运动。
5.6 磨床和砂轮
③辅助运动: 砂轮架的横向快进和快退运动; 尾座套筒伸缩移动→液压传动。
5.6 磨床和砂轮
●横磨法(切入磨削法):用宽砂轮进行横向切入磨削的方法 表面成形方法:成形—轨迹法。
① 表面成形运动:
工件旋转——圆周进给运动(nw 、 f周 )。
砂轮旋转运动(磨外圆 n砂 、磨内孔n内 )→主运动;
5 金属切削机床与刀具
5.1 机床的分类、型号与主要技术参数 5.2 工件表面成形方法和机床的运动分析 5.3 车床与车刀 5.4 孔加工机床(钻床、镗床)和刀具 5.5 铣床和铣刀 5.6 磨床和砂轮 5.7 齿轮加工机床与齿轮刀具
5.6 磨床和砂轮
5.6.1 磨床:用磨料磨具(砂轮、砂带、油石或研磨料)作为工 具进行切削加工的机床
② 砂轮的横向进给运动 f横 —连续横向进给运动→切入运动。
③ 辅助运动:
砂轮架横向快进和快退运动;尾座套筒伸缩移动→液压传动。
5.6 磨床和砂轮
■机床的用途: M14●32磨A是圆普柱通面精(度纵级磨万法能)外;圆磨床。主要用于磨削IT6~IT7级
精度●的工圆作柱台形偏或转圆,锥磨形锥的度外不圆大或长内圆孔锥,面R(a纵磨1.法25)~;0.08m