我国丙烯腈市场分析
国内己二腈和丙烯腈市场现状及投资分析

国内己二腈和丙烯腈市场现状及投资分析以高端化工材料为主业的上市公司齐翔腾达牵手中国化学集团工程有限公司及中国天辰工程有限公司,共同投资建设生产高新材料尼龙66项目的消息引起了行业内诸多关注。
而尼龙66的主要原料为己二腈,目前全部依赖进口。
丙稀腈作为高新材料中的一员,同样有着巨大的消费市场。
在此对目前国内己二腈和丙烯腈市场现状及投资前景进行分析,供决策参考。
一、国内己二腈市场现状目前,国内并无己二腈生产厂家,天辰齐翔将借此打破国外技术垄断,首次实现拥有自主产权技术的己二腈国产化。
己二腈是PA66(俗称尼龙66)生产的关键中间体,广泛应用于各种工程塑料、汽车、机械、电器零件、工业丝、民用丝等领域。
但由于技术壁垒及投资门槛较高,己二腈的行业集中度也极高。
目前全球己二腈产能184.5万吨,主要集中在英威达、奥升德、巴斯夫(含索尔维)和旭化成四家企业中。
其中英威达占比超过50%,也是唯一一家向外大量销售己二腈的生产商。
由于寡头高度垄断,技术封锁严重,完全依靠进口,定价受制于人。
2018年我国己二腈进口29.3万吨,同比增7.7%。
与此同时,尼龙66市场需求保持强劲,2018年消费量52万吨,同比增9%,其中进口27 万吨,对外依存度高达36%。
2018年己二胺、尼龙66切片报价分别一度超过8万元/吨、4万元/吨,涨幅分别达到2.5倍和1倍。
但由于被核心原料己二腈卡住了脖子,产业链利润分配都掌握在国外上游公司手中。
市场预计2020年,我国己二腈消费量将达到38万吨,其中尼龙66消费己二腈在35.7万吨左右。
事实上,己二腈国产化的努力从未停止过,但由于技术和资金门槛极高,迄今为止,能对垄断格局形成冲击的厂商还未真正出现。
上世纪七十年代,中石油辽阳分公司曾引进2 万吨/年己二酸催化氨化法生产己二腈,由于成本高,2002年停车。
2015年8月,山东润兴化工首次尝试自主技术生产10万吨/年己二腈,结果在试生产时发生爆炸,该项目至今仍未有重启的计划。
丙烯腈项目可行性研究报告

丙烯腈项目可行性研究报告一、项目背景和目标丙烯腈是一种重要的化工原料,广泛应用于合成纤维、合成橡胶、合成树脂等领域。
随着全球经济发展和人民生活水平提高,对丙烯腈的需求不断增加。
本项目旨在建立一条丙烯腈生产线,满足市场对丙烯腈的需求,实现盈利。
二、市场分析1.丙烯腈市场需求目前,全球丙烯腈的需求量约为2000万吨/年,且保持持续增长的趋势。
主要的应用领域是纺织品、合成橡胶、合成树脂等。
预计未来几年丙烯腈的需求将进一步增加。
2.主要竞争对手分析目前,国内外丙烯腈生产厂家众多,主要的竞争对手有中国化工集团公司、沙特石油化工公司、埃克森美孚公司等。
这些厂家在技术实力、规模经济上具有一定的优势,对市场份额有一定的把握。
3.市场前景分析由于丙烯腈的广泛应用,市场前景可观。
此外,随着环保意识的增强,对绿色低碳产业的需求不断增加,丙烯腈作为一种绿色环保的原料,有望在市场上获得更多机会。
三、技术分析1.生产工艺本项目采用丙烯的氰化法生产丙烯腈。
丙烯经过氯化和氰化反应,生成丙烯腈。
2.技术优势本项目采用成熟的氰化法生产丙烯腈的工艺,具有技术成熟、设备简单、操作方便等优势。
四、投资分析2.投资回收期和盈利能力根据市场需求和预测,预计本项目投资回收期为5年。
根据市场价格和生产成本估算,预计年收益为1500万元,年平均净利润率为20%。
五、可行性分析综合考虑市场需求、技术优势和投资回报等因素,本项目具有可行性。
1.市场需求量大,市场前景广阔。
2.采用成熟的生产工艺,技术可靠。
3.投资回收期合理,利润率高。
六、风险分析1.市场风险:市场竞争激烈,需求变化不确定。
2.技术风险:生产工艺可能存在技术问题,导致生产效率低下。
3.资金风险:资金筹集可能存在困难,导致项目延期或无法推进。
七、项目建议1.做好市场调研,确保项目的市场需求和前景。
2.加强技术研发,提高生产效率和产品质量。
3.多渠道筹集资金,降低资金风险。
4.加强管理和控制,提高项目效益。
我国丙烯行业发展趋势及市场分析

一、我国丙烯行业发展现状及特点1. 装置能力与隶属关系我国的丙烯工业是随乙烯工业的发展而日益发展壮大起来的。
多年来, 乙烯一直作为我国石化工业的龙头产品, 相应地, 丙烯则作为乙烯的联产品或炼厂副产品。
到2003年底, 我国有50余家丙烯生产工厂, 生产能力合计约为559万吨, 产量593.23万吨。
其中, 中国石化集团丙烯生产能力346.5万吨, 产量385.99万吨, 产量占全国的65.1%;中国石油集团丙烯生产能力197.1万吨, 产量194.6万吨, 产量占全国的32.8%;地方企业丙烯产量12.73万吨, 占全国的2.1%。
2003年我国丙烯产量超过10万吨的生产企业装置概况见表1。
由表1可知, 2003年我国丙烯生产能力最大的企业是燕山石化, 装置能力为45.6万吨(不包括东方乙烯);丙烯产量最大的企业是上海石化, 产量达到53.3万吨;丙烯能力在20万吨/年以上的主要有上海石化、扬子石化、燕山石化、齐鲁石化、吉林石化、大庆石化、兰州石化和大连石化等企业, 多数工厂丙烯生产能力在5万~20万吨/年之间, 此外还有20家工厂的生产能力在1万~5万吨/年之间。
在我国丙烯生产企业所产的丙烯产品中, 乙烯装置联产的丙烯均为企业自用, 用于生产大宗的丙烯下游产品, 如聚丙烯、丙烯腈、丁辛醇、丙烯酸系列以及苯酚/丙酮等;炼厂所产的丙烯一般作为本厂小聚丙烯装置以及丙烯腈、苯酚/丙酮装置等原料, 少数企业对外向固定下游厂家销售, 国内丙烯产品的市场贸易较少。
2. 丙烯的主要来源世界上丙烯的来源有蒸汽裂解制乙烯联产丙烯、炼厂催化裂化装置干气、丙烷脱氢、甲醇制烯烃以及近年所开发的烯烃转化、烯烃易位等工艺。
2003年世界丙烯生产能力约7314万吨, 其中乙烯联产丙烯占60%, 炼厂副产丙烯占35%, 丙烷脱氢占3%, 其他占2%。
我国丙烯主要来自乙烯裂解装置和炼厂催化裂化及催化裂解装置。
2003年我国丙烯生产能力559万吨, 其中乙烯联产丙烯能力约283万吨, 占丙烯总生产能力的50.6%, 产量约287万吨, 开工率约101%;炼厂副产丙烯能力约276万吨, 占丙烯总生产能力的49.4%, 产量约306.2万吨, 开工率110%。
丙烯腈市场分析
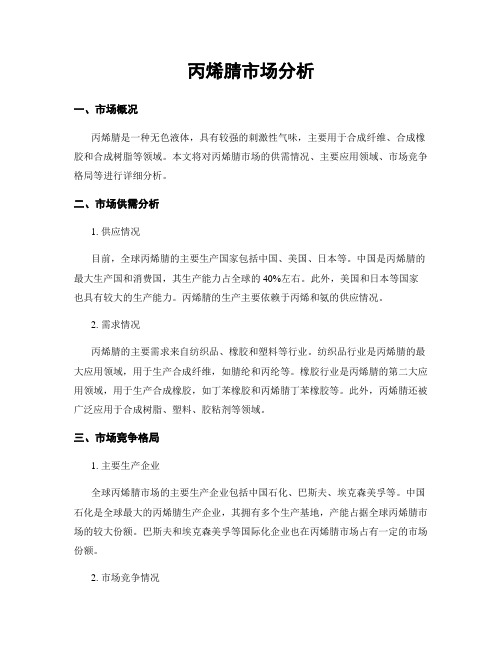
丙烯腈市场分析一、市场概况丙烯腈是一种无色液体,具有较强的刺激性气味,主要用于合成纤维、合成橡胶和合成树脂等领域。
本文将对丙烯腈市场的供需情况、主要应用领域、市场竞争格局等进行详细分析。
二、市场供需分析1. 供应情况目前,全球丙烯腈的主要生产国家包括中国、美国、日本等。
中国是丙烯腈的最大生产国和消费国,其生产能力占全球的40%左右。
此外,美国和日本等国家也具有较大的生产能力。
丙烯腈的生产主要依赖于丙烯和氨的供应情况。
2. 需求情况丙烯腈的主要需求来自纺织品、橡胶和塑料等行业。
纺织品行业是丙烯腈的最大应用领域,用于生产合成纤维,如腈纶和丙纶等。
橡胶行业是丙烯腈的第二大应用领域,用于生产合成橡胶,如丁苯橡胶和丙烯腈丁苯橡胶等。
此外,丙烯腈还被广泛应用于合成树脂、塑料、胶粘剂等领域。
三、市场竞争格局1. 主要生产企业全球丙烯腈市场的主要生产企业包括中国石化、巴斯夫、埃克森美孚等。
中国石化是全球最大的丙烯腈生产企业,其拥有多个生产基地,产能占据全球丙烯腈市场的较大份额。
巴斯夫和埃克森美孚等国际化企业也在丙烯腈市场占有一定的市场份额。
2. 市场竞争情况丙烯腈市场竞争激烈,主要表现在以下几个方面:(1) 价格竞争:丙烯腈市场价格波动较大,主要受到丙烯和氨的价格影响。
生产企业通过调整价格来应对市场竞争。
(2) 技术竞争:丙烯腈的生产技术要求较高,企业通过技术创新提高产品质量和降低生产成本,以增强竞争力。
(3) 市场拓展:企业通过扩大市场份额、拓展新的应用领域等方式来增加市场份额。
四、市场前景展望1. 市场增长预测随着全球经济的发展和人们对高性能纤维、高性能橡胶等产品的需求增加,丙烯腈市场有望保持稳定增长。
预计未来几年,丙烯腈市场将保持年均增长率在3%左右。
2. 发展趋势(1) 环保要求:随着环保意识的提高,丙烯腈市场对环保产品的需求将增加,企业需要加大环保投入,改进生产工艺,减少对环境的影响。
(2) 新技术应用:丙烯腈市场将面临新技术的应用,如生物基丙烯腈的研发和应用,将为市场带来新的增长点。
2023年ASA行业市场规模分析

2023年ASA行业市场规模分析ASA行业市场规模分析ASA(丙烯腈—丁二烯—苯乙烯共聚物)是一种高性能工程塑料,具有优良的耐候性、抗衰老性、耐化学腐蚀性等特点,在汽车、建筑、家电等领域广泛应用。
ASA行业市场规模受到多种因素的影响,本文将从需求、产量、出口、价格等方面进行分析。
市场需求ASA的主要应用领域是汽车和建筑领域,其次是家电领域。
随着消费者生活水平的提高和环保意识的提高,汽车、建筑领域对于高性能工程塑料的需求增加。
尤其是在安全性、舒适性、美观度等方面追求更高的要求。
而高性能工程塑料可以很好的满足这些需求。
另外,市场对于环境友好型材料的需求也越来越高,ASA作为一种环保型工程塑料,其需求相对较高。
根据市场研究机构的预测,未来几年ASA市场需求将逐步增加。
产量随着ASA在多个领域的广泛应用,其产量也相应增加。
据国家对塑料产量的统计数据显示,2019年ASA产量为39.6万吨,较上一年增长10%左右。
而从市场需求来看,ASA的产量增长还有很大的空间。
因此,增加ASA的生产能力和产量是必要的。
出口ASA主要出口地区包括欧美、亚洲和东南亚等地区。
其中,欧美地区是ASA的主要出口市场,占总出口量的40%以上。
据中国海关统计数据显示,2019年ASA出口量为6.5万吨,同比下降8.3%。
这主要是因为国内ASA的生产能力增加,满足了一部分国内市场需求,导致出口量有所下降。
但随着国内市场的扩大和优势产能的提升,未来ASA的出口量还有望保持稳定增长。
价格ASA价格受到多种因素的影响,包括原材料价格、生产成本、市场供需状况等。
目前ASA的价格波动比较大。
由于市场需求增加,ASA价格有所上涨,导致其应用范围受到限制。
另外,随着国产ASA的产量增加,价格逐步趋于稳定。
综上所述,ASA行业市场规模受到多种因素的影响,包括市场需求、产量、出口和价格等。
随着汽车、建筑、家电等领域对高性能工程塑料需求的增加,未来ASA市场需求还有望进一步增加。
丙烯腈下游产品市场概述与发展条件对比
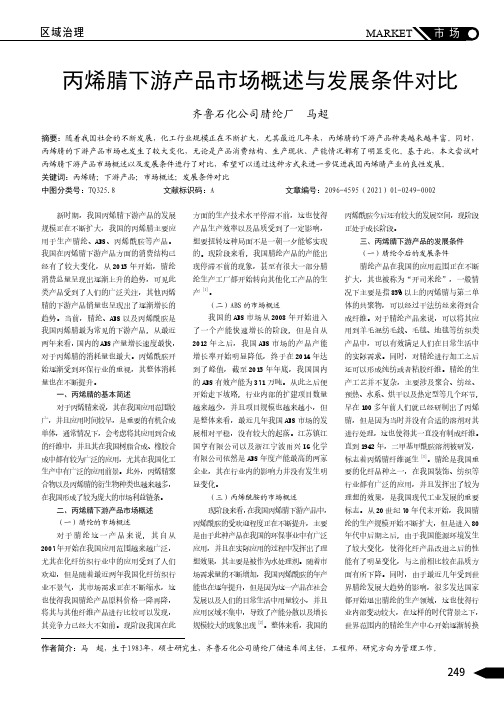
区域治理MARKET丙烯腈下游产品市场概述与发展条件对比齐鲁石化公司腈纶厂 马超摘要:随着我国社会的不断发展,化工行业规模正在不断扩大,尤其最近几年来,丙烯腈的下游产品种类越来越丰富。
同时,丙烯腈的下游产品市场也发生了较大变化,无论是产品消费结构、生产现状、产能情况都有了明显变化。
基于此,本文尝试对丙烯腈下游产品市场概述以及发展条件进行了对比,希望可以通过这种方式来进一步促进我国丙烯腈产业的良性发展。
关键词:丙烯腈;下游产品;市场概述;发展条件对比中图分类号:TQ325.8 文献标识码:A 文章编号:2096-4595(2021)01-0249-0002新时期,我国丙烯腈下游产品的发展规模正在不断扩大,我国的丙烯腈主要应用于生产腈纶、ABS、丙烯酰胺等产品。
我国在丙烯腈下游产品方面的消费结构已经有了较大变化,从2015年开始,腈纶消费总量呈现出逐渐上升的趋势,可见此类产品受到了人们的广泛关注,其他丙烯腈的下游产品销量也呈现出了逐渐增长的趋势。
当前,腈纶、ABS以及丙烯酰胺是我国丙烯腈最为常见的下游产品,从最近两年来看,国内的ABS产量增长速度最快,对于丙烯腈的消耗量也最大。
丙烯酰胺开始逐渐受到环保行业的重视,其整体消耗量也在不断提升。
一、丙烯腈的基本简述对于丙烯腈来说,其在我国应用范围较广,并且应用时间较早,是重要的有机合成单体,通常情况下,会考虑将其应用到合成的纤维中,并且其在我国树脂合成、橡胶合成中都有较为广泛的应用,尤其在我国化工生产中有广泛的应用前景。
此外,丙烯腈聚合物以及丙烯腈的衍生物种类也越来越多,在我国形成了较为庞大的市场利益链条。
二、丙烯腈下游产品市场概述(一)腈纶的市场概述对于腈纶这一产品来说,其自从2007年开始在我国应用范围越来越广泛,尤其在化纤纺织行业中的应用受到了人们欢迎,但是随着最近两年我国化纤纺织行业不景气,其市场需求正在不断缩水,这也使得我国腈纶产品原料价格一降再降,将其与其他纤维产品进行比较可以发现,其竞争力已经大不如前。
2023年腈纶市场持续低迷 我国腈纶企业资金链偏紧2

2023年腈纶市场持续低迷我国腈纶企业资金链偏紧网讯,我国腈纶行业生产原材料数量超标,腈纶企业盈利状况下滑。
目前,我国成全球腈纶行业主要生产地,国际腈纶行业格局基本稳定。
随着科学技术的不断进展,化纤替代产品的研发和生产成为了当前我国化纤纺织业生产的重要瓶颈,另外随着高新技术的不断应用,化纤腈纶产品的生产面临着被替代物取代的挑战。
2023年腈纶市场持续低迷腈纶一般指聚丙烯腈纤维。
聚丙烯腈或丙烯腈含量大于85%(质量百分比)的丙烯腈共聚物制成的合成纤维。
常用的其次单体为非离子型单体,如丙烯酸甲酯、甲基丙烯酸甲酯等,第三单体为离子型单体,如丙烯磺酸钠等。
受涤纶、粘胶纤维等其它化工产品替代的影响,腈纶市场需求持续低迷,腈纶行业进入到微利甚至亏损阶段,腈纶产品从服饰需求转向工业用途的转型升级势在必行。
我国腈纶行业近年来进展缓慢,2022-2027后新冠疫情环境下中国腈纶市场专题讨论及投资评估报告从近十年腈纶产量来看,2022-2022年我国腈纶产量维持在70万吨左右,2022年我国腈纶产量开头下滑,2022年我国腈纶产量下降至58万吨,同比下降5.7%,截至2022年1-7月我国腈纶产量33.72万吨,同比下降17.97%。
自上世纪八十年月以来我国腈纶行业乐观引入国外先进的生产技术,使得我国腈纶行业得到了快速的进展,到目前已经形成了较为完整的工业生产体系。
包括中国和东南亚一些国家在内的腈纶行业已经成为世界腈纶行业生产重心。
在中国大力进展化纤产业的政策指导下和地方政府的乐观参加下,中国化纤生产企业快速进展起来,遍地开花。
中国化纤原料主要来源大型石油加工企业和进口两部分,腈纶行业生产是比较集中的。
中国是一个腈纶纤维消费大国,年进口量在150万吨左右,国际大型化纤生产企业为了争夺中国市场经常压价销售,从而使得中国化纤行业早在自给率严峻不足的状况下就消失竞争特别激烈的局面。
我国腈纶企业资金链偏紧腈纶的聚集态结构与涤纶、锦纶不同,它没有严格讲的结晶部分,同时无定形部分的规整程度又高于其他纤维的无定形区。
丙烯腈市场分析
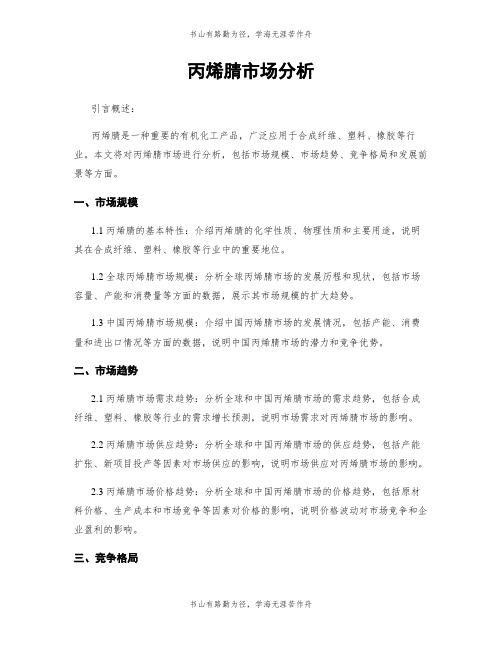
丙烯腈市场分析引言概述:丙烯腈是一种重要的有机化工产品,广泛应用于合成纤维、塑料、橡胶等行业。
本文将对丙烯腈市场进行分析,包括市场规模、市场趋势、竞争格局和发展前景等方面。
一、市场规模1.1 丙烯腈的基本特性:介绍丙烯腈的化学性质、物理性质和主要用途,说明其在合成纤维、塑料、橡胶等行业中的重要地位。
1.2 全球丙烯腈市场规模:分析全球丙烯腈市场的发展历程和现状,包括市场容量、产能和消费量等方面的数据,展示其市场规模的扩大趋势。
1.3 中国丙烯腈市场规模:介绍中国丙烯腈市场的发展情况,包括产能、消费量和进出口情况等方面的数据,说明中国丙烯腈市场的潜力和竞争优势。
二、市场趋势2.1 丙烯腈市场需求趋势:分析全球和中国丙烯腈市场的需求趋势,包括合成纤维、塑料、橡胶等行业的需求增长预测,说明市场需求对丙烯腈市场的影响。
2.2 丙烯腈市场供应趋势:分析全球和中国丙烯腈市场的供应趋势,包括产能扩张、新项目投产等因素对市场供应的影响,说明市场供应对丙烯腈市场的影响。
2.3 丙烯腈市场价格趋势:分析全球和中国丙烯腈市场的价格趋势,包括原材料价格、生产成本和市场竞争等因素对价格的影响,说明价格波动对市场竞争和企业盈利的影响。
三、竞争格局3.1 全球丙烯腈市场竞争格局:介绍全球丙烯腈市场的主要竞争对手,包括企业的规模、技术实力和市场份额等方面的情况,说明市场竞争的激烈程度。
3.2 中国丙烯腈市场竞争格局:介绍中国丙烯腈市场的主要竞争对手,包括企业的规模、技术实力和市场份额等方面的情况,说明市场竞争的现状和趋势。
3.3 丙烯腈市场竞争策略:分析丙烯腈市场的主要竞争策略,包括产品创新、市场拓展和成本控制等方面的措施,说明企业在市场竞争中的优势和劣势。
四、发展前景4.1 全球丙烯腈市场发展前景:展望全球丙烯腈市场的发展前景,包括市场需求的增长趋势、新技术的应用和市场竞争格局的变化等方面的因素,说明市场的发展潜力和机遇。
4.2 中国丙烯腈市场发展前景:展望中国丙烯腈市场的发展前景,包括国内需求的增长趋势、政策支持和市场竞争格局的变化等方面的因素,说明市场的发展潜力和机遇。
国内丙烯腈市场前景分析

以及丙烯腈 的价格走势 , 预测国内丙烯腈 市场需求量将逐年增加 , 市场价格也将继续上扬 , 国丙烯腈行业 我 在未来几年仍然有着广阔的市场前景。
关键词 : 丙烯腈 市场 前 景 中 图分 类 号 :Q 2 . T 26 6 文献标识码: A
文 章 编 号 : 17 6 4—19 ( 0 1 0 0 2 0 Leabharlann 09 2 1 ) 3— 0 3— 4
丙 烯腈是 一 种重 要 的有 机 化 工原 料 , 要用 主 于制造腈 纶 、 丙烯 腈一 丁 二 烯一苯 乙烯 三元 共 聚 物 ( B ) 苯 乙烯一丙 烯 腈 共 聚物 ( A 等热 塑 AS、 S N)
油 化 工 生 产技 术 、 量 管理 和 环 保 工 作 。 质
石 油 化 工 技 术 与 经 济
Te hn lg & Ec n mis i to h mi as c oo y o o c n Perc e c l
第2卷 7
21 年 01
第3 期
6 月
年我 国丙烯腈 下游装 置 的发 展情 况 ,0 5年 我 国 21 丙烯 腈 的消费量将会 达到 l 8 t届 时 国内丙烯 6k, 7
性 合成 树脂 , 是 生产 丁腈 橡 胶 、 也 己二 腈 、 丙烯 酰
胺及其 衍生物 的原 料 , 用途 十 分广 泛 。2 0 0 8年 全 球金融 危机 之后 , 内丙烯 腈行业 逐渐 回暖 , 烯 国 丙 腈 的市场 需求 量 和 市 场 价格 保 持稳 中有 升 的 态 势, 在此 将根据 目前 国 内丙烯 腈行业 的发 展情况 , 从 供需 、 本 、 格等 方 面 , 丙烯 腈 市 场 的前景 成 价 对
中国丙烯腈行业政策梳理竞争格局及行业发展趋势

中国丙烯腈行业政策梳理竞争格局及行业发展趋势
一、政策梳理
1.产业政策
中国政府一直高度重视丙烯腈产业的发展,对其进行了一系列的支持
政策。
比如,鼓励企业加大科技创新力度,提高产品质量与附加值;加大
对丙烯腈的技术研发和应用示范的支持力度,推动丙烯腈技术的升级和产
业转型;提升行业环保水平,推进清洁生产和循环经济,促进丙烯腈行业
的可持续发展。
2.贸易政策
中国丙烯腈行业的产品出口占据了全球市场的重要份额,因此贸易政
策对行业发展具有重要影响。
政府鼓励企业拓展海外市场,加强贸易合作,提高产品竞争力;同时也实施了一系列的贸易保护措施,如增设关税壁垒,限制进口数量,保护国内市场。
二、竞争格局
1.国内企业竞争激烈
2.国际竞争加剧
1.技术升级与转型升级
随着国内外市场需求的不断变化,中国丙烯腈行业需要不断进行技术
升级和转型升级,提高产品的质量和附加值,提升行业的竞争力。
例如,
发展高附加值的新型丙烯腈产品,如碳纤维等,满足新兴产业的需求。
2.环保要求提升
中国政府正在加大环保治理力度,促使丙烯腈行业加大环保投入,推动清洁生产和循环经济的发展。
行业发展趋势将会朝着低碳、环保、可持续发展的方向发展。
3.产业升级与优化布局
总之,中国丙烯腈行业在政府的支持下,取得了长足的发展。
未来,随着技术进步和市场需求的变化,中国丙烯腈行业将会面临更多的机遇和挑战。
只有不断创新和转型升级,加强环保治理和优化布局,才能在激烈的市场竞争中保持竞争优势并实现可持续发展。
2023年丙烯腈行业市场突围建议及需求分析报告
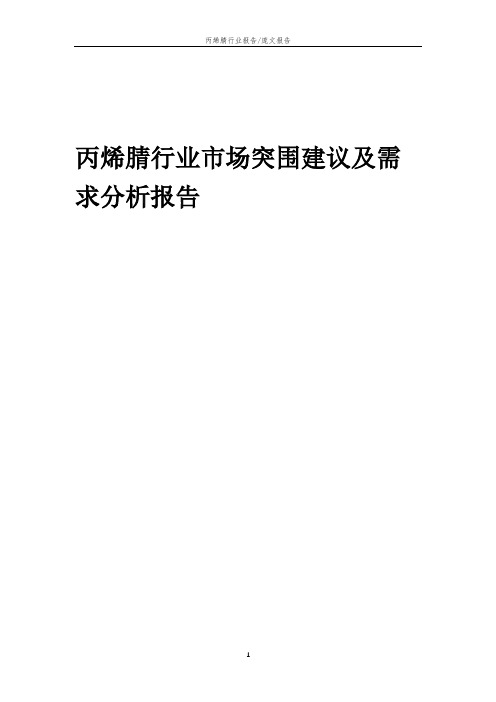
丙烯腈行业市场突围建议及需求分析报告目录概述 (4)一、丙烯腈行业政策环境 (5)(一)、政策持续利好丙烯腈行业发展 (5)(二)、行业政策体系日趋完善 (5)(三)、一级市场火热,国内专利不断攀升 (6)(四)、宏观环境下丙烯腈行业定位 (6)(五)、“十三五”期间丙烯腈业绩显著 (7)二、丙烯腈行业政策背景 (7)(一)、政策将会持续利好丙烯腈行业发展 (7)(二)、丙烯腈行业政策体系日趋完善 (8)(三)、丙烯腈行业一级市场火热,国内专利不断攀升 (8)(四)、宏观经济背景下丙烯腈行业的定位 (9)三、丙烯腈业数据预测与分析 (9)(一)、丙烯腈业时间序列预测与分析 (9)(二)、丙烯腈业时间曲线预测模型分析 (11)(三)、丙烯腈行业差分方程预测模型分析 (11)(四)、未来5-10年丙烯腈业预测结论 (12)四、2023-2028年丙烯腈业市场运行趋势及存在问题分析 (12)(一)、2023-2028年丙烯腈业市场运行动态分析 (12)(二)、现阶段丙烯腈业存在的问题 (13)(三)、现阶段丙烯腈业存在的问题 (13)(四)、规范丙烯腈业的发展 (15)五、2023-2028年丙烯腈产业发展战略分析 (15)(一)、树立丙烯腈行业“战略突围”理念 (15)(二)、确定丙烯腈行业市场定位,产品定位和品牌定位 (16)1、市场定位 (16)2、产品定位 (16)3、品牌定位 (18)(三)、创新力求突破 (19)1、基于消费升级的技术创新模型 (19)2、创新促进丙烯腈行业更高品质的发展 (20)3、尝试格式创新和品牌创新 (21)4、自主创新+品牌 (21)(四)、制定宣传方案 (23)1、学会制造新闻,事件行销--低成本传播利器 (23)2、学习通过出色的品牌视觉设计突出品牌特征 (23)3、学会利用互联网营销 (23)六、丙烯腈业的外部环境及发展趋势分析 (24)(一)、国际政治经济发展对丙烯腈业的影响 (24)(二)、国内政治经济发展对丙烯腈业的影响 (24)(三)、国内突出经济问题对丙烯腈业的影响 (25)七、2023-2028年丙烯腈业竞争格局展望 (25)(一)、丙烯腈业经济周期分析 (25)(二)、丙烯腈业的增长与波动分析 (26)(三)、丙烯腈业市场成熟度分析 (26)八、丙烯腈行业多元化趋势 (27)(一)、宏观机制升级 (27)(二)、服务模式多元化 (27)(三)、新的价格战将不可避免 (28)(四)、社会化特征增强 (28)(五)、信息化实施力度加大 (28)(六)、生态化建设进一步开放 (29)1、内生发展闭环,对外输出价值 (29)2、开放平台,共建生态 (29)(七)、呈现集群化分布 (29)(八)、各信息化厂商推动丙烯腈发展 (30)(九)、政府采购政策加码 (30)(十)、个性化定制受宠 (31)(十一)、品牌不断强化 (31)(十二)、互联网已经成为标配“风生水起“ (31)(十三)、一体式服务为发展趋势 (32)(十四)、政策手段的奖惩力度加大 (32)九、丙烯腈产业投资分析 (33)(一)、中国丙烯腈技术投资趋势分析 (33)(二)、大项目招商时代已过,精准招商愈发时兴 (33)(三)、中国丙烯腈行业投资风险 (34)(四)、中国丙烯腈行业投资收益 (34)十、“疫情”对丙烯腈业可持续发展目标的影响及对策 (35)(一)、国内有关政府机构对丙烯腈业的建议 (35)(二)、关于丙烯腈产业上下游产业合作的建议 (36)(三)、突破丙烯腈企业疫情的策略 (36)概述近年来,丙烯腈行业市场火爆,其应用场景跨越式发展的根本原因在于技术、安全和多样性的创新。
丙烯腈市场分析

丙烯腈市场分析一、市场概述丙烯腈,又称丙烯腈酸,是一种无色液体,具有刺激性气味。
丙烯腈广泛应用于合成纤维、塑料、橡胶等领域,是重要的有机化工原料。
本文将对丙烯腈市场进行详细分析,包括市场规模、市场趋势、竞争格局等方面的内容。
二、市场规模根据市场调研数据显示,2022年全球丙烯腈市场规模达到XX万吨,估计到2025年将达到XX万吨,年复合增长率约为X%。
亚太地区是丙烯腈市场的主要消费地区,占领全球市场份额的XX%。
中国是亚太地区丙烯腈市场的主要消费国家,估计到2025年,中国丙烯腈市场规模将达到XX万吨。
三、市场趋势1. 增长驱动因素丙烯腈作为纺织品、塑料和橡胶等行业的重要原料,随着这些行业的发展,对丙烯腈的需求也将持续增长。
同时,丙烯腈作为合成纤维的原料,具有良好的染色性能和耐久性,因此在纺织品市场中具有广阔的应用前景。
2. 技术创新随着科技的进步,丙烯腈生产技术也在不断创新。
传统的丙烯腈生产方法存在一些环境和安全问题,而新的生产技术能够降低能耗、减少废水排放,提高生产效率和产品质量。
这将进一步推动丙烯腈市场的发展。
3. 环保压力随着环保意识的提高,对于环境友好型产品的需求也在增加。
丙烯腈作为一种有机化工原料,其生产过程中会产生一定的废水和废气。
因此,丙烯腈生产企业需要加大环保设施建设和技术改造力度,以满足环保要求,提高产品竞争力。
四、竞争格局目前,全球丙烯腈市场竞争激烈,主要的市场参预者包括中国石化、巴斯夫、埃克森美孚等知名企业。
这些企业在技术研发、产品质量和市场拓展方面具有一定的优势。
此外,一些新兴企业也在不断涌现,加剧了市场竞争。
五、市场前景丙烯腈市场具有较好的发展前景。
随着全球经济的增长和工业化进程的推进,对丙烯腈的需求将持续增加。
同时,随着环保意识的提高,对环保型丙烯腈产品的需求也将增加。
因此,丙烯腈生产企业应加强技术创新,提高产品质量,积极拓展市场,以赢得更多的市场份额。
六、结论综上所述,丙烯腈市场具有较大的市场规模和发展潜力。
丙烯腈生产现状及市场

丙烯腈是生产聚丙烯腈纤维腈纶、丁腈橡胶NBR、丙烯腈-丁二烯-苯乙烯树脂ABS、苯乙烯-丙烯腈树脂SAN的主要原料,另外丙烯腈水解可制得丙烯酰胺和丙烯酸及其酯类,电解加氢偶联制得己二腈还可制造抗水剂和胶粘剂等,也用于其他有机合成和医药工业中,并用作谷类熏蒸剂等,是一种重要的有机化工原料,在合成树脂、合成纤维、合成橡胶等高分子材料中占有显着的地位;1.生产现状世界2012年,英力士集团是世界最大的丙烯腈生产商,生产能力为1355 kt/a,日本旭化成是世界上第一家大规模使用丙烷生产丙烯腈的公司,是亚洲最大的丙烯腈供应商,位居世界第二;2012年该公司拥有丙烯腈总生产能力950kt/a,其中包括日本冰岛300 kt/a,川崎150 kt/a,韩国蔚山300 kt/a,泰国马塔堡200kt/a;2013年韩国蔚山245 kt/a和沙特朱拜勒200 kt/a装置建成后,旭化成生产能力将达1395kt/a,将超过英力士集团成为世界最大的丙烯腈生产商;2014年,世界丙烯腈产能约为万t/a ;旭化成于2014年8月前关闭了位于川崎的15万t/a丙烯腈装置,之所以要关闭丙烯腈装置,是因为我国经济放缓和欧洲经济衰退导致需求下降,再加上大量新产能投产造成市场供应过剩,而原料丙烯价格持续上升使装置盈利能力严重收缩;2015年,世界丙烯腈产能约为万t/a;英力士集团的丙烯腈产能为万t/a,为全球最大的丙烯腈生产商;2015年全球主要丙烯腈生产企业及产能统计见表l.表1 2015全球主要丙烯腈生产企业及产能产能排序生产厂家装置所在地生产能力/万t/a1 英力士集团德国、美国2 旭化成日本、韩国、美国、泰国、沙特、中国台湾1123 中国石油化工集团公司中国4 中国石油天燃气总公司中国705 奥生德高Ascend性能材料公司美国6 美国首诺科特玻璃功能膜公司美国497 台湾塑料工业股份有限公司中国台湾8 美国氰特化学公司美国309 帝斯曼DSM公司荷兰10 韩国泰光Tae Kwang工业韩国11 BASF Plc 英国12 中国石化发展公司CPDC 中国台湾13 Cornerstone 化学公司美国14 日本Dia-Nitrix Co Ltd. 日本15 韩国东西Tungsuh石化韩国2016 卢克石油Luk Oil公司俄罗斯其他26合计近年来.世界丙烯腈产能稳步增长,新增产能主要来自韩国、泰国和中国大陆以及沙特阿拉伯 ;而北美和欧洲地区的生产能力基本上没有变化;预计未来几年,世界丙烯腈生产巨头仍计划新建或者扩建丙烯腈生产装置 ,主要有日本旭化成、三菱化学和沙特萨比克公司合资在沙特新建万t/a装置该项目原来计划在 2015年底建成投产,现在推迟到 2017年建成投产 ,英力士公司计划与天津渤海化工集团公司合资各占 50%的股份在我国天津新建一套万t/a丙烯腈生产装置;计划在 2016年底建成投产;加上我国大陆上海赛科、江苏斯尔邦、山东科鲁尔、山东海力以及广西科元等新建装置生产能力,预计到 2018年世界丙烯腈的总生产能力将达到约万t/a;未来几年国内还有几套新扩建装置建成投产,到 2020年,全球丙烯腈总产量有望达到 950万t/a;中国国内丙烯腈生产装置主要集中在中国石油化工集团公司简称:中石化和中国石油天然气集团公司简称:中石油所属企业 ,其中中国石油化工集团公司含合资企业的生产能力合计为 120.8万 t/a,约占总生产能力的 56%;中国石油天然气集团公司的生产能力为70万 t/a,约占 33%;上海赛科石油化工股份有限责任公司是目前我国最大的丙烯腈生产厂家,生产能力为万 t/a,约占总生产能力的 24%;其次是中国石油吉林石油化工公司,生产能力为 42万 t/a,约占20%;这些装置全部采用丙烯氨氧化法生产工艺 ,初期均采用国外 BP公司的技术,后来大多采用上海石油化工研究院的技术进行改扩建;除上海赛科之外,其余装置均配套建有下游生产装置腈纶、ABS树脂或者丁腈橡胶等;2015年国内丙烯腈总产能达到 216.8万 t/a 左右 ;总产量为万 t,开工率达到 74%以上;我国丙烯腈生产企业生产能力及产量如表 2 ;表 2 2015年我国丙烯腈生产企业生产能力及产量排序厂名生产能力/万t/a 产量/万t工厂地点1 中石化上海赛科石油化工有限责任公司52 上海市金山区2 中石油吉林石化公司丙烯腈厂42 吉林省吉林市3 中石化山东科鲁尔中国石化与万达控股集团的合资企业26 山东东营4 江苏斯尔邦石化有限公司26 0 江苏连云港市5 中石化安庆石化腈纶有限公司21 安徽省安庆市6 中石化上海石油化工股份有限公司13 上海市金山区7 中石油抚顺石油化工公司9 辽宁省抚顺市8 中石油大庆石化分公司8 黑龙江省大庆市9 中石油大庆炼化分公司8 黑龙江省大庆市10 中石化齐鲁分公司8 山东省淄博市11 中石油兰州石化分公司 3 甘肃省兰州市12 中石化山东齐泰石油化工有限公司山东省淄博市合计未来几年国内新建拟建的丙烯腈装置共计 5 套,见表 3;表3 未来几年国内新建拟建的丙烯腈装置公司名称产能/万t/a 备注青海庆华30 位于青海柴达木中海油东方石化海南精细化工公司20 位于海南,待定天津海力达化工有限公司英力士与渤海化工集团合资26 新建,预计2016年建成投产中化泉州26 新建,位于泉州广西科元20 新建,计划2016年投产山东海力集团13 位于淄博,待定合计135此外,中海油海南东方精细化工公司计划新建 20万 t/a生产装置,青海庆华集团也计划新建 3O万 t/年生产装置;如果这些项目均能够按照计划实施,预计到2018年,我国丙烯腈的总生产能力达到 351万 t/a,超过美国成为世界最大的丙烯腈生产国;2 国内市场分析及预测2.1 供求关系我国丙烯腈产品主要用于生产腈纶、ABS/SAN以及丙烯酰胺和丁腈橡胶等产品,2015年的消费结构为:腈纶消费量占总消费量的%,ABS/SAN约占%,丙烯酰胺约占% ,丁腈橡胶约占%,其它方面包括丙烯腈在己二腈/己二胺、抗水剂和胶粘剂、其它有机合成和医药以及非质子型极性溶剂等方面的消费量约占% ;预测 2018年丙烯腈的消费量将增至 235 万 t;2008--2015年国内丙烯腈供求关系如表 4所示;表 4 2008--2015年国内丙烯腈供求关系年份产量/万t 进口量/万t 出口量/万t表观消费量/万t进口依存度/%20082009201020112012201320142015丙烯腈产能增长过快,下游行业却未能紧跟脚步;据统计,丙烯腈主要用于生产ABS、腈纶、丙烯酰胺等产品,而这些产品在 2015年产能增长并不明显,以现在的下游需求量很难消化丙烯腈突飞猛进式的产能增长;在此前提下,人们自然而然将希望寄托在丙烯腈的下游新亮点——己二腈生产上;2015年年中,山东润兴 l0万 t/a己二腈装置开始试车 ,该套装置采用丙烯腈电解二聚法生产技术 ,由山东润兴自行研发 ,填补了国产己---N 技术的空白;据悉 ,该装置己二腈与丙烯腈的用量比为 l:1.3.即生产10万 t己二腈需要消耗 13万 t原料丙烯腈.恰好能够抵消科鲁尔装置所带来的新增产能 ;不出意外的话 ,在未来 ,己 z-N 将成为丙烯腈下游中最大的一匹黑马 ,逐步增大原料的用量占比然而事与愿违 ,2015年 8 月 ,装置储罐发生爆炸,己二腈的国产化之路从触手可及再度变成遥不可及,以己二腈救市的希望就此破灭;从后期来看,丙烯腈产能仍将快速增长,除江苏斯尔邦 26万 t/a丙烯腈装置已于 2015年 12月 17日开始试车之外,2O16—2018年期间还有英力士与渤海化工合资的 26万 t/a、广西科元 20 万 t/a、中化泉州 26万 t/a丙烯腈装置即将上马;而其下游发展却已进入瓶颈期 ,丙烯腈供需矛盾愈发凸显,前景令人担忧;预计 2016年我国对丙烯腈的表观消费量将达到约 230万 t,其中用于生产腈纶的丙烯腈比例将逐渐下降,而 ABS/SAN所占比例将不断增加;同时在低价进口资源的冲击下,行业整体产能将出现过剩的问题 ,市场供需平衡将被打破;2.2 价格走势2015年年初价格为13900元/t,在供需矛盾逐步加大的压力下,丙烯腈价格出现大幅跳水,于 l0月 12日达到 5年最低点 7 550元/t,相较年初跌幅已达%; 产能陡增是造成今年丙烯腈市场走势低迷的最大原因2014年年底至 2015年年底 ,山东科鲁尔 13万 t/a新丙烯腈、上海赛科 26万 t/a新丙烯腈装置以及江苏斯尔邦 26万 t/a丙烯腈装成功投产,国内丙烯腈产能由 2014 年的/a左右一跃涨至 2015年年底的216.8万 t/a,丙烯腈供应宽松时代已逐步逼近10月下旬,受抚顺石化及上海赛科装置意外停车影响,供应面出现短期紧缩,跌跌不休的局面终于得以缓解,厂家趁机拉涨价格,截至 l2月中旬已收复 9 000元/t关口;这轮上涨看似猛烈 ,但后市却并不乐观;从总体上来看,一旦装置开工踏上正轨,丙烯腈供需矛盾将再度浮出水面 ,下行之路仍会延续;2.3 进出口分析及预测2015年,丙烯腈下游腈纶和 ABS市场不旺,与 2014年相比,市场需求略有减少;全年累计进口量达到 39.79万t,比 2014年的进口量少 12万t;2015年我国大陆丙烯腈进口量及来源见表5;表5 2015年我国大陆丙烯腈主要进口来源及其进口量国家或地区进口数量/万t 所占份额/%韩国中国台湾美国泰国日本其他合计由表 5可知,我国大陆的丙烯腈进口来源主要是韩国、美国和中国台湾省,来自它们的总进口量约占我国大陆总进口量的 95%;2015年我国丙烯腈的进口贸易方式主要是一般贸易,一般贸易量占总进口贸易量的97.56%;近几年丙烯腈的进口贸易方式变化不大 ,一般贸易方式仍是最主要的进口方式 ;合理控制一般贸易总量不仅可以平衡国内丙烯腈市场的供需 ;间接提高国内工厂的开工率 ,这也将是国内丙烯腈行业生存的长久之计 ;国家安监总局会同相关部门制定发布的危险化学品目录 2015版将于5月 1日起实施;丙烯腈从剧毒危化品降级为一般危化品;对于丙烯腈以及下游市场来说 ,这一决定喜忧参半,降级后丙烯腈产品流通将更为顺畅活跃,但不排除国外产品涌入带来销售压力;3.发展建议1在消化吸收引进生产技术的同时,积极自主开发或引进新一代成本更低,收率更高和更环保的新技术,尤其是要进一步推进催化剂的国产化进程,并形成具有自主知识产权的自有技术;积极开发废水、尾气处理新技术,开发不产生硫酸铵的丙烯腈生产新工艺,以减少对环境的污染,提高原料的利用率;努力降低主要原料丙烯的成本,加强对副产乙腈和氢氰酸HCN的利用,以降低生产成本,提高企业的市场竞争力;2积极探索丙烷法制丙烯腈新技术的开发和应用,以降低产业成本,提高市场竞争力;3发挥一体化装置优势,上下游联动柔性化生产;由于丙烯腈装置在设计时一般和腈纶、 ABS、丙烯酰胺或者NBR装置配套,可以充分发挥这个优势来规避市场风险;建议生产企业对上下游装置统一进行成本核算,同时根据产品效益、市场需求进行合理定价并调整产品间价差,柔性调整上下游装置开工率,实现产业链协同发展;4丙烯腈生产所用原料和产品及副产物均为可燃或易燃气体,产生的废气、废液和废渣处理不当可能构成爆炸以及污染,因此需要注意安全环保问题;5积极探索新的销售手段和策略,扩大下游客户群和消费领域,并加大下游产品的开发与应用,如丙烯酰胺系列、NBR、己二腈等,实现产业链配套;拓宽潜在市场,以促进我国丙烯腈及其相关行业健康稳步发展;。
丙烯腈生产现状及市场

丙烯腈是生产聚丙烯腈纤维(腈纶)、丁腈橡胶(NBR)、丙烯腈-丁二烯-苯乙烯树脂(ABS)、苯乙烯-丙烯腈树脂(SAN)的主要原料,另外丙烯腈水解可制得丙烯酰胺和丙烯酸及其酯类,电解加氢偶联制得己二腈还可制造抗水剂和胶粘剂等,也用于其他有机合成和医药工业中,并用作谷类熏蒸剂等,是一种重要的有机化工原料,在合成树脂、合成纤维、合成橡胶等高分子材料中占有显著的地位。
1.生产现状1.1 世界2012年,英力士集团是世界最大的丙烯腈生产商,生产能力为1355 kt/a,日本旭化成是世界上第一家大规模使用丙烷生产丙烯腈的公司,是亚洲最大的丙烯腈供应商,位居世界第二。
2012年该公司拥有丙烯腈总生产能力950 kt/a,其中包括日本冰岛300 kt/a,川崎150 kt/a,韩国蔚山300 kt/a,泰国马塔堡200kt/a。
2013年韩国蔚山245 kt/a和沙特朱拜勒200 kt/a装置建成后,旭化成生产能力将达1395kt/a,将超过英力士集团成为世界最大的丙烯腈生产商。
2014年,世界丙烯腈产能约为673.2万t/a 。
旭化成于2014年8月前关闭了位于川崎的15万t/a丙烯腈装置,之所以要关闭丙烯腈装置,是因为我国经济放缓和欧洲经济衰退导致需求下降,再加上大量新产能投产造成市场供应过剩,而原料丙烯价格持续上升使装置盈利能力严重收缩。
2015年,世界丙烯腈产能约为814.7万t/a。
英力士集团的丙烯腈产能为135.5万t/a,为全球最大的丙烯腈生产商。
2015年全球主要丙烯腈生产企业及产能统计见表l.表1 2015全球主要丙烯腈生产企业及产能产能排序生产厂家装置所在地生产能力/(万t/a)1 英力士集团德国、美国135.52 旭化成日本、韩国、美国、泰国、沙特、中国台湾1123 中国石油化工集团公司中国120.84 中国石油天燃气总公司中国705 奥生德高Ascend性能材料公司美国52.26 美国首诺科特玻璃功能膜公司美国497 台湾塑料工业股份有限公司中国台湾32.08 美国氰特化学公司美国309 帝斯曼(DSM)公司荷兰24.510 韩国泰光(Tae Kwang)工业韩国29.011 BASF Plc 英国28.012 中国石化发展公司(CPDC)中国台湾24.013 Cornerstone 化学公司美国22.714 日本Dia-Nitrix Co Ltd. 日本20.515 韩国东西(Tungsuh)石化韩国2016 卢克石油(Luk Oil)公司俄罗斯18.5其他26合计814.7近年来.世界丙烯腈产能稳步增长,新增产能主要来自韩国、泰国和中国大陆以及沙特阿拉伯。
国内外丙烯腈市场及发展前景分析
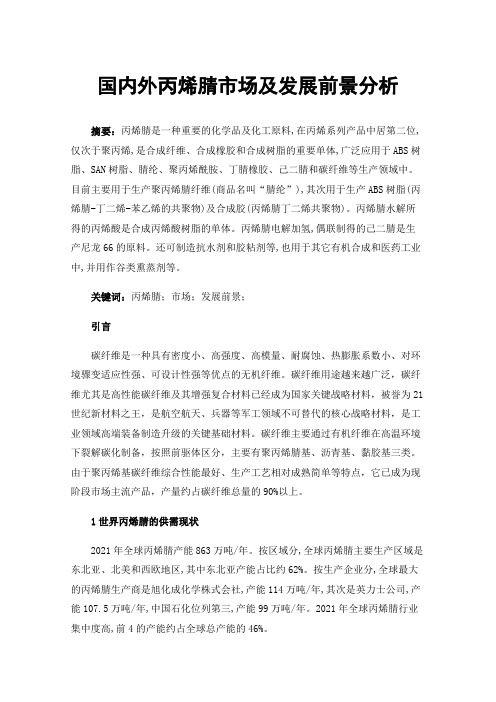
国内外丙烯腈市场及发展前景分析摘要:丙烯腈是一种重要的化学品及化工原料,在丙烯系列产品中居第二位,仅次于聚丙烯,是合成纤维、合成橡胶和合成树脂的重要单体,广泛应用于ABS树脂、SAN树脂、腈纶、聚丙烯酰胺、丁腈橡胶、己二腈和碳纤维等生产领域中。
目前主要用于生产聚丙烯腈纤维(商品名叫“腈纶”),其次用于生产ABS树脂(丙烯腈-丁二烯-苯乙烯的共聚物)及合成胶(丙烯腈丁二烯共聚物)。
丙烯腈水解所得的丙烯酸是合成丙烯酸树脂的单体。
丙烯腈电解加氢,偶联制得的己二腈是生产尼龙66的原料。
还可制造抗水剂和胶粘剂等,也用于其它有机合成和医药工业中,并用作谷类熏蒸剂等。
关键词:丙烯腈;市场;发展前景;引言碳纤维是一种具有密度小、高强度、高模量、耐腐蚀、热膨胀系数小、对环境骤变适应性强、可设计性强等优点的无机纤维。
碳纤维用途越来越广泛,碳纤维尤其是高性能碳纤维及其增强复合材料已经成为国家关键战略材料,被誉为21世纪新材料之王,是航空航天、兵器等军工领域不可替代的核心战略材料,是工业领域高端装备制造升级的关键基础材料。
碳纤维主要通过有机纤维在高温环境下裂解碳化制备,按照前驱体区分,主要有聚丙烯腈基、沥青基、黏胶基三类。
由于聚丙烯基碳纤维综合性能最好、生产工艺相对成熟简单等特点,它已成为现阶段市场主流产品,产量约占碳纤维总量的90%以上。
1世界丙烯腈的供需现状2021年全球丙烯腈产能863万吨/年。
按区域分,全球丙烯腈主要生产区域是东北亚、北美和西欧地区,其中东北亚产能占比约62%。
按生产企业分,全球最大的丙烯腈生产商是旭化成化学株式会社,产能114万吨/年,其次是英力士公司,产能107.5万吨/年,中国石化位列第三,产能99万吨/年。
2021年全球丙烯腈行业集中度高,前4的产能约占全球总产能的46%。
2我国丙烯腈的供需现状至2021年底,国内共有12家丙烯腈工厂,丙烯腈总产能达338万吨/年,占全球丙烯腈总产能的39%。
丙烯腈市场分析

丙烯腈市场分析一、市场概述丙烯腈是一种重要的有机化工原料,广泛应用于合成纤维、塑料、橡胶、涂料等领域。
本文将对丙烯腈市场进行详细分析,包括市场规模、市场趋势、竞争格局等方面。
二、市场规模根据市场调研数据显示,全球丙烯腈市场规模持续增长。
2022年,全球丙烯腈产量达到X万吨,市场规模约为X亿美元。
估计到2025年,全球丙烯腈市场规模将达到X亿美元。
亚太地区是丙烯腈的主要生产和消费地区,占领了全球市场份额的X%。
三、市场趋势1. 行业发展驱动因素a. 合成纤维需求增长:随着全球经济的发展和人民生活水平的提高,对纺织品的需求不断增加,推动了丙烯腈市场的增长。
b. 汽车工业的快速发展:丙烯腈作为一种重要的塑料原料,广泛应用于汽车零部件创造,汽车工业的快速发展也带动了丙烯腈市场的增长。
c. 新型材料的兴起:随着科技的进步,新型材料的研发和应用不断涌现,丙烯腈作为一种重要的化工原料,被广泛应用于新型材料的创造中。
2. 市场竞争格局目前,全球丙烯腈市场竞争激烈,主要的市场参预者包括公司A、公司B、公司C等。
这些公司在技术研发、生产能力、市场渠道等方面具有一定的竞争优势。
此外,新进入市场的公司也在不断增加,进一步加剧了市场的竞争。
四、市场分析1. 市场驱动因素分析a. 合成纤维需求增长:合成纤维作为丙烯腈的主要应用领域,随着人民生活水平的提高和纺织品需求的增加,合成纤维市场将继续保持稳定增长,进而推动丙烯腈市场的发展。
b. 新型材料的需求增加:随着科技的进步,新型材料在各个领域的应用越来越广泛,丙烯腈作为一种重要的化工原料,将在新型材料的创造中发挥重要作用。
2. 市场风险分析a. 原材料价格波动:丙烯腈的生产过程中需要大量的原材料,原材料价格的波动将直接影响到丙烯腈的生产成本和市场价格。
b. 环境监管政策:随着环境保护意识的增强,各国对化工行业的环境监管力度加大,可能会对丙烯腈的生产和销售带来一定的限制和影响。
- 1、下载文档前请自行甄别文档内容的完整性,平台不提供额外的编辑、内容补充、找答案等附加服务。
- 2、"仅部分预览"的文档,不可在线预览部分如存在完整性等问题,可反馈申请退款(可完整预览的文档不适用该条件!)。
- 3、如文档侵犯您的权益,请联系客服反馈,我们会尽快为您处理(人工客服工作时间:9:00-18:30)。
我国丙烯腈市场分析摘要:分析了我国丙烯腈的生产消费现状及发展前景,提出了今后的发展建议。
关键词:丙烯腈,市场调查,市场需求分析丙烯腈(AN)是一种重要的有机化工原料,在合成树脂、合成纤维、合成橡胶等高分子材料中具有重要的地位,主要用于生产丙烯腈纤维(腈纶),也是生产丙烯腈-丁二烯-苯乙烯树脂(ABS)、苯乙烯-丙烯腈树脂(SAN)等热塑性合成树脂、丁腈橡胶(NBR)、己二腈、丙烯酰胺及其它衍生物的原料,开发利用前景广阔。
1 生产技术目前,丙烯腈的生产方法主要有丙烯直接氨氧化法、丙烷直接氨氧化法和丙烷脱氢后再丙烯氨氧化法(即丙烷两步氨氧化法)。
1.1 丙烯直接氨氧化法该工艺过程以化学级丙烯(丙烯质量分数不低于93%)和肥料级氨及空气按摩尔比1.0:1.1:1.13送入流化床催化反应器中,催化剂采用二氧化硅负载的磷钼酸铋,反应温度为400-500t,压力为0.03-0.2MPa,接触时间为5-10s。
反应急剧放热,通过蛇形管换热器除去反应热并产生蒸汽,蒸汽在丙烯腈装置内利用。
BP、旭化成、首诺以及杜邦公司都拥有该技术的专利权。
其中,比欧西(BOC)公司开发的Petrox氨氧化工艺具有独特的优点。
该工艺采用烃类选择性分子筛设施,将废弃物料中未反应的烃原料分出,送回反应器,所有CO2和氮气不从循环物流中除去,而是通过增加氧平衡气体混合物。
该工艺的反应在较低速率下进行,提高了生成丙烯腈的转化率,减少了生成CO2的选择性。
生产试验表明,采用该方法可提高产率20%,减少CO2排放50%,降低投资费用20%,减少操作费用10%-20%。
目前,丙烯氨直接氧化法生产丙烯腈技术的进展主要集中在催化剂、流化床反应器以及节能降耗等方面。
催化剂是生产丙烯腈的关键,许多公司都着重于高性能催化剂的开发。
重点是低温型催化剂、较高压力型以及高丙烯负荷型催化剂的研究和开发。
目前居于世界领先水平的催化剂主要有美国BP公司的C-49MC、日东化学公司的NS-733D、旭化成工业公司的S-催化剂、Monsanto公司的MAC-3以及上海石油化工研究院的MB-96A催化剂等。
对流化床反应器的改进主要集中在气体分布、旋风分离器、催化剂补加方式等方面;在节能降耗方面包括萃取塔侧线出料、提高精制回收率、增设废热锅炉以及硫酸铵焚烧回收硫酸等。
1.2 丙烷直接氨氧化工艺该工艺是丙烷在催化剂作用下,同时进行丙烷的氧化脱氢和丙烯氨氧化反应的过程。
代表性工艺有BP-Amoco和日本三菱化学公司的技术。
BP-Amoco公司工艺技术的氧化反应在高浓度丙烷和氧不足的条件下进行。
由于以氧气作为氧化剂,避免了惰性气体的引入,加之丙烷转化率较低,所以未反应的丙烷需要回收。
相比之下,日本三菱化学公司工艺的氧化反应在低浓度丙烷和氧过量的条件下进行,由于以空气为氧化剂,加之丙烷转化率较高,所以未反应的丙烷不必回收。
丙烷直接氨氧化工艺虽然目前还没有实现工业化,但国外一些大公司已经进行了工业中试生产。
日本旭化成公司开发的丙烷氨氧化制备丙烯腈工艺,将丙烷、氨和氧气在装有专用催化剂的管式反应器中进行反应,其催化剂为二氧化硅上负载20%-60%的Mo、V、Nb或者Sn金属,反应中采用惰性气体进行稀释,反应条件为415℃和0.1MPa。
当丙烷转化率为90%时,丙烯腈的选择性为70%,总收率约为60%。
目前该技术已经完成了中试研究,旭化成公司计划采用该技术,与泰国FIT公司合作建设20万t/a丙烯腈生产装置,丙烷原料由PTT公司供应。
1.3 丙烷脱氢丙烯氨氧化工艺该工艺分两步进行,首先是以丙烷为原料,先脱氢生产丙烯,然后再用传统的丙烯氨氧化工艺生产丙烯腈。
该工艺的丙烷转化率和丙烯腈的选择性都比较高,但因为该工艺需要增加丙烷脱氢装置,因此固定投资费用要比丙烷直接氨氧化法所需费用高15%-20%。
2 供需现状及发展前景2.1 生产我国丙烯腈的工业生产始于20世纪60年代末期。
当时依靠国内自己开发的技术,相继在各地建成了十多套丙烯腈生产装置,但产能均较小,最大的也只有1.0万t/a。
1973年,中国石化上海石油化工公司率先引进BP公司生产技术,建成一套5.0万t/a丙烯腈生产装置。
此后,中国石油抚顺石油化工公司、中国石油大庆石油化工公司、中国石化齐鲁石油化工公司等又先后引进国外技术建成丙烯腈生产装置,20世纪末我国丙烯腈的总生产能力达到了约40.0万t/a。
进入21世纪以后,我国丙烯腈工业仍保持着迅猛发展的势头。
2005年,上海赛科石油化工股份有限责任公司采用BP公司技术新建一套26.0万t/a丙烯腈生产装置。
2007年到达阶段顶峰,丙烯腈的总产能与总产量分别达到了102.5万t/a和105.9万t,装置开工率高达103.3%。
2008年受全球金融危机影响,国内丙烯腈年产量下降到94.2万t,相比2007年下跌了约11.05%,但装置平均开工率仍达到约92%。
此后,伴随着需求的逐步恢复,我国丙烯腈生产又步入一个快速发展时期,生产能力稳步增加。
2010年6月,中国石油吉林石油化工公司采用国产技术建设的2套共计24.0万t/a丙烯腈生产装置顺利投产。
2011年6月,中石化齐鲁石油化工公司将其丙烯腈装置生产能力由4.0万t/a扩增至8.0万t/a。
2012年8月,中国石化安庆石油化工公司新建的13.0万t/a丙烯腈生产装置实现中交。
截止到2012年11月底,我国丙烯腈的生产厂家有9家,总生产能力达到140.5万t/a,同比增长约10.20%,2011年的产量约为111.4万t,同比增长约2.48%,生产装置全部采用丙烯氨氧化法生产工艺,初期均采用引进的BP公司技术,后来大多采用中石化上海石油化工研究院的技术进行改扩建。
除了上海赛科石油化工股份有限责任公司外,其余装置均配套建有下游生产装置(腈纶、ABS树脂或者丁腈橡胶等)。
我国的丙烯腈生产装置主要集中在中国石油化工集团公司和中国石油天然气集团公司。
其中,中国石油化工集团公司(含合资企业)的生产厂家有4家,生产能力合计为68.0万t/a,约占国内总生产能力的48.40%;中国石油天然气集团公司的生产厂家有5家,生产能力合计为72.5万t/a,约占国内总生产能力的51.60%。
中国石油吉林石油化工公司是目前我国最大的丙烯腈生产厂家,生产能力为42.4万t/a,约占国内总生产能力的30.18%;其次是上海赛科石油化工股份有限责任公司,生产能力为26.0万t/a,约占国内总生产能力的18.50%。
2012年我国丙烯腈的主要生产厂家情况见表1。
2.2 新建及拟建装置由于目前我国丙烯腈的生产能力和产量仍不能满足实际生产的需求,因此在“十二五”期间,我国仍将新建或者扩建多套丙烯腈生产装置。
主要有中国石化齐鲁石油化工公司生产能力由4.0万t/a扩建到8.0万t/a(已经于2011年6月完成);中国石油化工股份有限安庆分公司新建一套13.0万t/a丙烯腈生产装置,装置已经于2012年8月31日实现中交,目前正在进入生产准备阶段;2011年4月,中国石化与万达集团丙烯腈项目合资协议在东营签约。
据悉,此次中国石化与万达集团将合作投资39亿元,在东营港经济开发区建设年产26.0万t的丙烯腈项目;中国石油大庆石油化工公司扩建10.0万t/a装置,新加坡明志石化在江苏盐城大丰港经济开发区新建10.0万t/a装置,上海赛科石化公司拟新建一套26.0万t/a丙烯腈新装置,现已通过环保审批;中海油海南东方精细化工项目二期工程也包括20.0万t/a丙烯腈装置,青海庆华集团拟新建30.0万t/a装置等。
预计到2016年,我国丙烯腈的总生产能力将超过200.0万t/a。
2.3 进出口情况由于国内腈纶和ABS树脂等丙烯腈下游行业的稳步发展,以及国内各企业生产能力增长缓慢,我国丙烯腈市场多年来一直维持着供不应求的状况,产品大量进口。
2005年我国丙烯腈的进口量为31.64万t,2007年进口量突破40.0万t,达到43.55万t,同比增长约34.21%。
2008年下半年起,由于受到全球金融危机的影响,国内丙烯腈下游行业的需求整体萎缩,导致丙烯腈的进口量大幅度下降到只有28.52万t,同比下降约34.51%。
进入2009年以后,随着经济危机过后下游行业的逐步复苏,我国丙烯腈的进口量又回升到正常水平。
2009年我国丙烯腈的进口量为45.10万t,同比增长58.13%。
2010年进口量义下降到44.58万t,同比减少约1.17%。
2011年进口量又增加到54.17万t,同比增长约21.51%。
2012年(1-9)月的进口量为40.74万t,同比减少约2.35%。
在进口的同时,我国丙烯腈也有少量出口。
2000年的出口量为24.85t,2005年增加到31892.58t,2006年增加到51941.15t,创造出口历史最高纪录,同比增长约62.86%。
自2009年,近几年我国丙烯腈均没有出口。
2005-2012年我国丙烯腈的进出口情况见表2。
转载:我国丙烯腈市场分析2.3.1 进口国家和地区我国大陆丙烯腈的进口主要来源于美国、韩国、日本和我国台湾等国家和地区。
近几年我国大陆丙烯腈的主要进口国家和地区情况见表3。
2.3.2 进口贸易方式我国丙烯腈的进口贸易方式十分集中,几乎全部都来自一般贸易方式。
2011年一般贸易方式的进口量达到50.12万t,约占总进口量的92.52%,同比2010年的41.94万t增长约19.50%。
2.3.3 进口海关和省市我国丙烯腈的进口主要集中在南京海关和宁波海关。
2011年这2个海关的进口量合计达到50.98万t,约占总进口量的94.11%,同比2010年的44.55万t增长约14.43%。
其中南京海关的进口量为26.57万t,约占总进口量的49.05%,同比增长约5.11%;宁波海关的进口量为24.41万t,约占总进口量的45.06%,同比增长约26.66%。
我国丙烯腈的进口主要集中在浙江和江苏等省市。
2011年来自这2个省市的进口量合计达到48.37万t,约占总进口量的89.29%,同比2010年的41.93万t增长约15.36%。
其中浙江省的进口量为24.16万t,约占总进口量的44.60%,同比增长约30.63%;江苏省的进口量为24.21万t,约占总进口量的44.70%,同比增长约3.30%。
2.3.4 主要进口厂家我国丙烯腈的进口主要集中在宁波乐金甬兴化工有限公司、镇江奇美化工有限公司、台化塑胶(宁波)有限公司以及中国金山联合贸易有限责任公司等厂家。
2011年来自这4个厂家的进口量合计达到33.65万t,约占总进口量的62.12%。
2011年我国丙烯腈的主要进口厂家情况见表4。
2.4 供需现状及发展前景2005-2011年我国丙烯腈的供需平衡情况见表5。