(完整版)冷挤压模具设计及其成形过程_毕业设计
6.1冷挤压模具设计
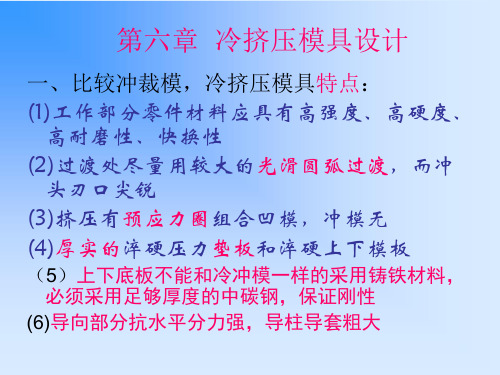
二、反挤压凸模高度确定
• 反挤纯铝时 l/d≤7-10 • 反挤紫铜时l/ d≤5—6; • 反挤黄铜时l/ d≤4—5; • 反挤低碳钢时l /d≤2.5—3 • 可用临界压杆 条件校核计算
三、反偏心方法、卸料方法
• 图12-26咬 住不变形区 减小失稳, 壁厚均匀; 图12-17工 作部分细长 过渡部分加 粗,加工卸 料槽;气孔 • 知识点:卸 料槽使用
六、反挤凸模与凹模制造尺寸与公差: 公差居中原则即入体原则
• 1.保证外径时图a
• 2.保证内径时图b
• Δ可选0.75、0.9系数 • 公差可选IT7-9级
例题1确定挤压凹模尺寸公差
• 原则:入体原则模具尺寸浮动 范围必须在挤压件尺寸公差允 许范围内 0.04 • 书本A100=(100-0.2) = 0 • 99.8 0.04 0 • 一般=(100-0.75*0.2) 1/ 4*0.2 0.05 0 • =99.85 0 • 简便=理想尺寸H7级公差 • =99.9 0.035 0 • 提问:如果挤压件是 φ100±0.2挤压凹模尺寸公差 如何? φ100±0.2= φ100.20-0.4表达不同而已 • 知识点:公差转化方法
0 +0.055
• 一般=(100-0.75*0.22)0+IT7=99.8350+0.035 • 简便=理想尺寸H7级公差=99.890+0.035 • 判断:三种算法的区别?哪个更合理?余量及胀 形影响
(三)反挤压顶杆设计 图6-18
• 设计要点: • 支承部分的直 径应放大, • 大R或斜锥过渡, 间隙0.1mm ,
0.3
0 解:书本T70=(70+0.18)0.036
例3如果是正挤压杆部直径φ100如何设 计正挤凹模工作带尺寸与公差?
冷镦挤变形工艺冷镦工艺与模具设计

镦锻比与镦锻次数的关系表
S=h0/d0 镦锻次数
≤2.5
2.5~4.5
1
2
4.5~6 3
变形抗力 (N/mm2)
形过程中,随着变形的增大,由于冷作硬化 作用使金属的硬度和强度随之增大,
电工纯铁
变形抗力也大大增加,而塑性却有所降
低,这将给后道工序带来变形的困难。
金属材料冷作硬化后实际变形抗力如 图1.1-1所示
变形程度 ε(%)
图1.1-1
材料的含碳量越高,其变形抗力越大。所以,在冷加工过程中需适当增加 中间热处理工序,以消除冷作硬化和内应力。否则,继续冷镦加工将是困 难的。
❖ 当前应用冷镦挤技术应解决的主要问题
❖ 由于冷镦挤金属变形所需变形单位挤压力很大,且作用时间较长,所以当前 冷镦挤技术的应用必须解决强大的变形抗力与模具承载能力的矛盾。为此,必 须做到:
① 设计合理的、工艺性良好的冷镦挤压件。 ② 恰到选择冷镦挤压件的原材料,正确确定坯料形状、尺寸及热处理规范,并应特
对冷镦用钢的要求: 力学性能的要求 化学成分的要求
金相组织的要求— 一般认为1~4级为粗晶粒,5~8为细晶粒。粗晶粒
材料的冷作硬化敏感性比细晶粒的要大,塑性比细晶粒的要差,适合 冷镦晶粒度以4、5、6级为宜。 材料表面质量的要求 — 钢材表面的缺陷 、表面脱碳。 尺寸精度要求 表面润滑要求
冷镦材料的改制过程
和最小阻力定律。
体积不变定律 — 冷镦加工时,变形前金属坯料的体积等于变形后工件的体 积。 最小阻力定律 — 金属受到外力作用发生塑性变形,金属晶粒有向各个不 同方向移动的可能时,总是沿着阻里最小的方向移动。
最小阻力定律应用很广泛,在设计冷镦模具时,怎样才能使金属流动阻力 减小和合理地控制金属的流动,这是设计人员必须考虑的问题。
第五章冷挤压工艺及模具设计
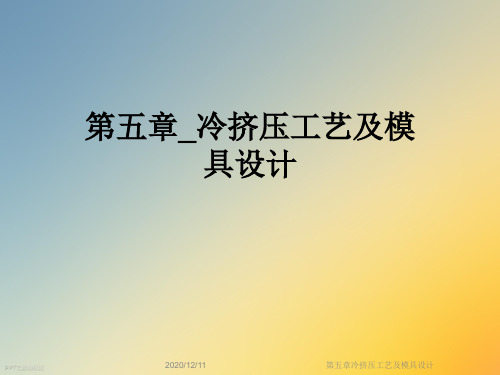
PPT文档演模板
2020/12/11
第五章冷挤压工艺及模具设计
冷挤压工艺及模具设计
•5.1 冷挤压工艺
•5.2 冷挤压模具设计 • •5.3 冷挤压模的典型结构
PPT文档演模板
第五章冷挤压工艺及模具设计
冷挤压工艺及模具设计
•5.1 冷挤压工艺
• 冷挤压是一种先进的少无切削加工工艺之一。它是在 常温下,使固态的金属在巨大压力和一定的速度下,通过模 腔产生塑性变形而获得一定形状零件的一种加工方法。冷挤 压的工艺过程是:先将经处理过的毛坯料放在凹模内,借助 凸模的压力使金属处于三向受压应力状态下产生塑性变形, 通过凹模的下通孔或凸模与凹模的环形间隙将金属挤出。它 是一种在许多行业广泛使用的金属压力加工工艺方法。
• (3) 冷挤压的变形方式 在变形程度相同的条件下, 反挤压的力大于正挤压的力。反挤压的许用变形程度比正挤 压小。
PPT文档演模板
第五章冷挤压工艺及模具设计
冷挤压工艺及模具设计
• (4) 毛坯表面处理与润滑 毛坯表面处理越好,润滑 越好,许用变形程度也就越大。
• (5) 冷挤压模具的几何形状 冷挤压模具工作部分的 几何形状对金属的流动有很大影响。形状合理时,有利于挤 压时的金属流动,单位挤压力降低,许用变形程度可以大些。
第五章冷挤压工艺及模具设计
冷挤压工艺及模具设计
•5.1.4.2 许用变形程度
• 冷挤压时,一次挤压加工所容许的变形程度,称为许 用变形程度。不同材料有不同的许用变形程度。在工艺上, 每道冷挤压工序的变形程度应尽量小于许用值,使模具承受 的单位挤压力不超过模具材料许用应力(目前一般模具材料 的许用应力为2500~3000N/mm2),确定许用变形程度数值 是冷挤压工艺计算的一个重要依据,因为冷挤压许用变形程 度的大小决定了制件所需的挤压次数。若计算出的冷挤压变 形程度超过许用值、则必须用多次挤压完成,以延长模具寿 命,避免损坏模具。
传动轴冷挤压工艺及模具设计
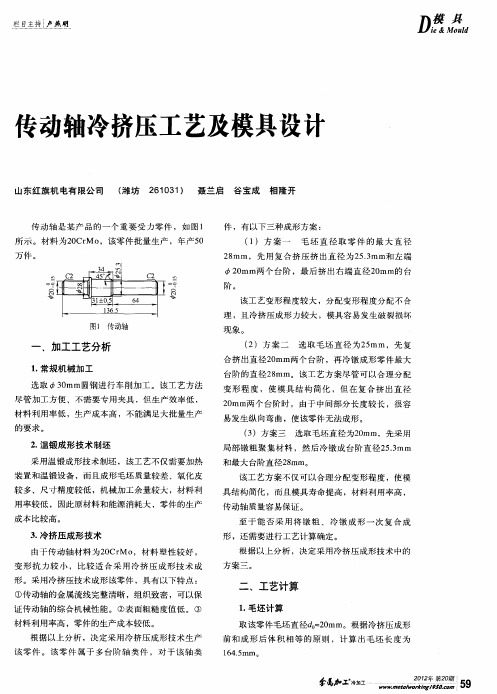
(3)配 合精 度 下 模 座 与下 模 板 之 间 的 配 合 精 度采 用 H7/g6的 配 合 。
(4)模 架 装 配 为 了保 证 上 下 模 架 之 间的 同 轴 度 ,设 计 了专用 的装 配 心轴 。
拦旦主持i 燕盟
D篡 。d
传动轴冷挤压工艺及模具设计
山东红旗 机 电有 限公司 (潍坊 261031) 聂兰启 谷 宝成 相 隆开
所示 。材料为20CrMo,该零件批量生产 ,年产50
重 l 蘼— ——_-]
一 加工工艺分析 .
1.常规机 械加工 选取 30mm圆钢进行车 削加 工。该工艺方法 尽 管加 工方 便 、不需 要 专 用 夹具 ,但 生 产效 率 低 , 材料 利 用 率 低 ,生 产 成 本 高 ,不 能 满 足大 批 量 生产
2.温锻成形 技术制坯 采 用 温 锻 成形 技术 制 坯 ,该 工艺 不 仅 需 要加 热 装 置和 温 锻 设 备 ,而 且 成 形毛 坯 质 量较 差 、氧 化皮 较 多 、尺 寸 精 度较 低 ,机 械 加 工 余量 较 大 ,材料 利 用率较低 ,因此原材料和能源消耗大 ,零件的生产 成 本 比 较 高 。 3.冷挤压成形技 术
处 理 ,才 能达 到 降低 坯料 与模 具 之 间的摩 擦 和 降 低 冷 挤 压 时 的变 形 力的 目的 。所 以 ,毛坯 磷 化 处 理 后 必须 进 行 皂化 处 理 。
四、模具结构及设计
剪 切 下料 模 按 照常 规 设 计 ,这 里 主 要 介 绍 局部 镦 粗 模 和 冷镦 成 形 模 的设 计 。
冷挤压工艺及模具设计

冷挤压工艺及模具设计
5.1.3 冷挤压毛坯的制备 5.1.3.1 冷挤压坯料形状与尺寸 挤压件的毛坯形状设计是否合理,将直接影响制件的形 状与尺寸,并且还将影响模具的寿命。冷挤压用毛坯通常都 是棒料或块料,其截面形状可根据制件的相应截面形状确定。 一般情况下,确定毛坯形状的原则是:旋转体及轴对称多角 类选用圆柱形毛坯;矩形零件可选用矩形毛坯。此外还应考 虑采用何种挤压方法,如图5-1所示,采用正挤压法时,用 实心毛坯能挤出实心件,用空心坯料能挤出空心件。反挤压 时,毛坯的形状采用实心和空心均可。
冷挤压工艺及模具设计
对于有些材料,为了确保冷挤压过程中的润滑层不被过 大的单位接触压力所破坏,毛坯要经过表面化学处理。例如 碳钢的磷酸盐处理(磷化)、奥氏体不锈钢的草酸盐处理、 铝合金的氧化、磷化或氟硅化处理、黄铜的钝化处理等。经 化学处理后的毛坯表面,覆盖一层很薄的多孔状结晶膜,它 能随毛坯一起变形而不剥离脱落,经润滑处理后在孔内吸附 的润滑剂可以保持挤压过程中润滑的连续性和有效的润滑效 果。
冷挤压工艺及模具设计
4.1.4.1 变形程度的表示方法 变形程度是表示挤压时金属塑性变形量大小的指标,其 最常用的表示方法有两种:截面收缩率和挤压面积比。 (1) 截面收缩率 式中
F0 − F1 εF = × 100% F0
(5-3)
ε F ——冷挤压的截面收缩率,见表5-1、表5-2;
F0——冷挤压变形前毛坯的横截面积,mm2; F1——冷挤压变形后工件的横截面积,mm2。
5.1.2 冷挤压的特点 5.1.2.1 冷挤压的特点主要包括以下三个方面: (1) 节约原材料,生产效率高 冷挤压是少无切削加工工艺,与切削加工相比,节约原 材料,同时,冷挤压是在压力机简单的往复运动中生产零件, 生产效率高,比切削加工高30倍。
冷挤压工艺及模具设计共65页

11、用道德的示腊
12、法律是无私的,对谁都一视同仁。在每件事上,她都不徇私情。—— 托马斯
13、公正的法律限制不了好的自由,因为好人不会去做法律不允许的事 情。——弗劳德
14、法律是为了保护无辜而制定的。——爱略特 15、像房子一样,法律和法律都是相互依存的。——伯克
1、最灵繁的人也看不见自己的背脊。——非洲 2、最困难的事情就是认识自己。——希腊 3、有勇气承担命运这才是英雄好汉。——黑塞 4、与肝胆人共事,无字句处读书。——周恩来 5、阅读使人充实,会谈使人敏捷,写作使人精确。——培根
挤压模具毕业设计论文

目录一、冷挤压零件分析 31、材料选择 32、形状设计 33、尺寸分析 4二、冷挤压工艺分析 41、坯料尺寸确定 42、毛坯软化处理 43、冷挤压毛坯表面处理与润滑 54、变形程度计算 65、确定挤压次数 66、工序设计 8三、冷挤压设备选择121、挤压力的确定 122、压力机吨位计算123、挤压设备类型选择 134、液压式压力机型号选择 13四、冷挤压模具结构设计13五、凸模设计141、凸模的长度尺寸计算 152、凸模加工工艺路线 15六、凹模设计161、组合凹模结构设计 172、棘轮套挤压齿形模芯的设计 173、齿形模芯加工20七、冷挤压件质量分析20八、凸模机加工工艺23九、非标准件三维结构图24 致谢30 参考文献31棘轮套冷挤压成形工艺及模具设计重庆工商大学机械设计制造及其自动化专业2006级模具班郭建军指导老师唐全波黄少东中文摘要:冷挤压是精密塑性体积成形技术中的一个重要组成部分。
冷挤压是指在冷态下将金属毛坯放入模具模腔内,在强大的压力和一定的速度作用下,迫使金属从模腔中挤出,从而获得所需形状、尺寸以及具有一定力学性能的挤压件。
显然,冷挤压加工是靠模具来控制金属流动,靠金属体积的大量转移来成形零件的。
本设计介绍了棘轮套零件结构分析、挤压工艺过程、挤压设备选择、模具结构的设计、凸凹模设计、挤压件质量分析、棘轮套齿形模芯的结构、凸模加工工艺及模具各部件三维造型进行了叙述,并计算了毛坯体积、毛坯尺寸、变形程度、挤压比和挤压力。
与常规的棘轮套加工工艺相比,冷挤压成形的棘轮套具有齿形强度高、齿形尺寸精度较高、表面粗糙度值低、材料利用率高、生产效率高、设备投资少等优势。
关键词:冷挤压棘轮套正挤压凸缘Gear Cold Extrusion of the process and die design(Chongqing Technology and Business University ,mechanical design automation and manufacturing professionals ,06 mold Guo JianJun)Abstract:V olume precision plastic cold extrusion forming technology is an important component. Cold extrusion is the next in the cold metal blank into the mold cavity, the strong pressure and under a certain speed, forced metal extrusion from the mold cavity to obtain the required shape, size, and has some mechanical performance of extrusion Obviously, the cold extrusion process is to control the metal flow by mold, by transfer to a large number of metal forming volume parts.Ratchet sets introduced structure of parts, extrusion process, extrusion equipment selection, die structure design, punch and die design, extrusion quality analysis, ratchet sets of the structure of tooth punch, punch and die processing of parts, Three-dimensional modeling of the narrative, and calculate the rough size, blank size, deformation, extrusion ratio and extrusion pressure. And conventional processing technology compared to ratchet set, ratchet set of cold extrusion with gear, high strength, high precision gear size, low surface roughness, high utilization ratio, high efficiency, less investment in equipment and other advantages.key words: Cold extrusion Ratchet sets Extrusion Flange图1—棘轮套零件图图1所示为棘齿套零件图。
冷挤压工艺和模具设计说明书模板

冷挤压工艺及模具设计
5.2 冷挤压模具设计
5.2.1 冷挤压模的特点
由于冷挤压时,单位挤压力较大,因此冷挤压模具的强 度、刚度及耐用度等方面其要求都比一般冲模高,它与一般 普通冲模相比,主要有以下特点: 1.模具的工作部分与上、下底板之间一般都设有足够 的支承面与足够厚度的淬硬垫板,以承受很大的压力,减少 上、下底板上的单位压力。
冷挤压时,一次挤压加工所容许的变形程度,称为许用 变形程度。不同材料有不同的许用变形程度。在工艺上,每 道冷挤压工序的变形程度应尽量小于许用值,使模具承受的 单位挤压力不超过模具材料许用应力(目前一般模具材料的 许用应力为2500~3000N/mm2),确定许用变形程度数值是 冷挤压工艺计算的一个重要依据,因为冷挤压许用变形程度 的大小决定了制件所需的挤压次数。若计算出的冷挤压变形 程度超过许用值、则必须用多次挤压完成,以延长模具寿命, 避免损坏模具。
冷挤压工艺及模具设计
3.复合挤如图5-3所示,挤压时,金属流动方向相对于 凸模运动方向,一部分相同,另一部分相反,适用于各种复 杂形状制件的挤压;改变凹模孔口或凸、凹模之间缝隙的轮 廓形状,就可以挤出形状和尺寸不同的各种空心件和实心件。
图5-1 正挤压图
5-2 反挤压图
5-3 复合挤
冷挤压工艺及模具设计
程度。
冷挤压工艺及模具设计
4.1.4.1 变形程度的表示方法 变形程度是表示挤压时金属塑性变形量大小的指标,其 最常用的表示方法有两种:截面收缩率和挤压面积比。 (1) 截面收缩率 式中
毕业设计(论文)-冷挤压模具设计说明书

毕业设计(论文)-冷挤压模具设计说明书摘要阶梯形零件是多种复杂形状的组合,其成形工艺较难,在工艺设计和变形方案的制定上,有其独自的特点。
这类零件一般可采用板料多道拉深来成形。
但是对于本设计中的阶梯方铝罩零件来说,其内外都呈现阶梯状且形状不一致辞,并且由于中间过渡部分形状不规则,因此不可能用板材成形工艺成形,而只能采用挤压等其他方法成形。
对于复杂的阶梯形零件,一次挤压不容易达到预期成形效果。
因此,一般采用有预成形的多道次挤压工艺。
其中的关键是如何合理分配材料变形程度,控制材料流动,减少过度变形,从而得到合格的零件。
本文探讨了阶梯方铝罩挤压的可行性,通过对产品零件图的分析,制定了几种工艺方案并进行分析比较,在选择最优方案的同时也制定了工艺流程。
在此基础上详细地介绍了阶梯方铝罩挤压模具的设计过程。
采用冷挤压工艺加工后,提高了零件的精度和表面质量,改善了强度和韧性,减少了切削加工量,节约了原材料,提高了生产效率,也改善了零件的组织性能。
关键词:阶梯方铝罩,成形工艺,冷挤压,模具设计IABSTRACTMulti-step part is a combination, which is composed with various complicated shapes. Its forming craft is more difficult. So it has its own characteristic in the technological design and the distortion plan formulation. Generally, this kind of components can be formed with the technology of multi-drawing the sheet. However, the product in this paper is not so regular. Its shape has steps both in exterior andinterior and the shape is irregular. At the same time, the middle transition part is so complex that it is impossible to adopt the drawing technology to form. Therefore, we need to consider the cold extrusionand other way to get the shape. It is no easy to achieve the anticipated formed effect with only one extrusion, because the step-shape is so complex. It should use multi-extrusion craft with pre-form forging. So the key is how to distribute rationally the distortion degree, control material flow, reduce the excessive deformation and obtain the qualified components. The feasibility of extrusion forming of multi-step part was discussed in this article. With the analysis of several technological programs, the optimal plan was made and selected, the technological process was determined. Based on the pre-discussion, the extrusion die was design and the design process is presented detailedly. By using the cold extrusion craft process, the precision and the surface quality of the product is improved, the intensity and toughness is got better, the cutting process is reduced, the raw material is saved. Not only does it enhanced the production efficiency, but also improve the organization of component.Keywords: multi-step part,forming technique,cold extrusion,die designII目录第1章冷挤压技术的介绍 .............................................11.1冷挤压工艺的实质 .................................................11.2冷挤压工艺的优点 .................................................11.3冷挤压工艺的缺点 .................................................21.4冷挤压工艺的应用范围 .............................................31.5冷挤压工艺的的发展方向 ...........................................3 第2章工艺分析及制定 ...............................................42.1产品零件的分析 ...................................................42.2工艺方案的分析 ...................................................5 第3章毛坯制备及处理 ..............................................113.1冷挤压件毛坯的制备 ..............................................113.2冷挤压件材料的软化热处理 ........................................133.3冷挤压件的表面处理与润滑 ........................................14 第4章冷挤压力 .....................................................164.1影响冷挤压压力的主要因素 ........................................164.2变形程度 ........................................................164.3冷挤压力的计算 ..................................................17 第5章冷挤压设备的选择 ............................................185.1冷挤压设备的基本要求 ............................................185.2冷挤压设备的选择 ................................................18 第6章冷挤压模具设计 ..............................................206.1冷挤压模具特点 ..................................................206.2冷挤压模架设计 ..................................................206.3凸、凹模设计 ....................................................216.3.1反挤压凸模的设计 (21)6.3.2反挤压凹模的设计 (23)6.3.3反挤压凸、凹模制造公差 (25)第7章模具结构部件设计 (26)7.1上模具部分结构设计 ..............................................267.2卸件装置设计 ....................................................27III7.3下模具部分结构设计 ..............................................297.4模具结构和工作原理 ..............................................307.5成形模具三维图 ................................ 错误~未定义书签。
冷挤压工艺及模具设计课件

对修复后的模具进行全面检测 和调试,确保其性能达到要求 。
05
冷挤压工艺与模具 设计的未来发展
新材料的应用
高强度轻质材料
随着新材料技术的不断发展,高强度轻质材料如钛合金、铝合金等在冷挤压工 艺中的应用将更加广泛,能够满足产品轻量化、高性能的要求。
复合材料
复合材料的出现为冷挤压工艺提供了更多的可能性,通过将不同材料组合在一 起,可以实现单一材料无法达到的性能,提高产品性能和降低成本。
合理布局
根据产品特点和工艺要求,合 理布置模具结构,确保产品成
型和出模顺利。
优化流道设计
优化模具流道设计,减少流动 阻力,降低成型难度和压力。
增强刚性和稳定性
为确保模具在使用过程中不易 变形和损坏,应加强模具的刚 性和稳定性设计。
易于维修和更换
模具结构应便于维修和更换损 坏或磨损的部件,降低维护成
本。
冷挤压特点
冷挤压工艺具有高效率、高精度、低 成本等优点,能够加工出形状复杂、 精度要求高的零件,广泛应用于汽车 、家电、电子、航空航天等领域。
冷挤压的应用范围
汽车零件制造
家用电器制造
冷挤压工艺可以用于制造汽车发动机、底 盘、电气系统等零部件,如活塞、连杆、 气瓶等。
家用电器中的金属零部件,如空调压缩机 、冰箱压缩机、洗衣机电机等,也广泛采 用冷挤压工艺制造。
模具的制造工艺
选择合适的加工方法
根据模具材料和结构特点,选择合适的加工方法,确保模具精度 和表面质量。
控制加工参数
合理控制加工参数,如切削速度、进给量等,以提高加工效率和模 具质量。
热处理和表面处理
根据需要,对模具进行热处理和表面处理,提高其硬度和耐久性。
03
冷挤压模的设计和分析
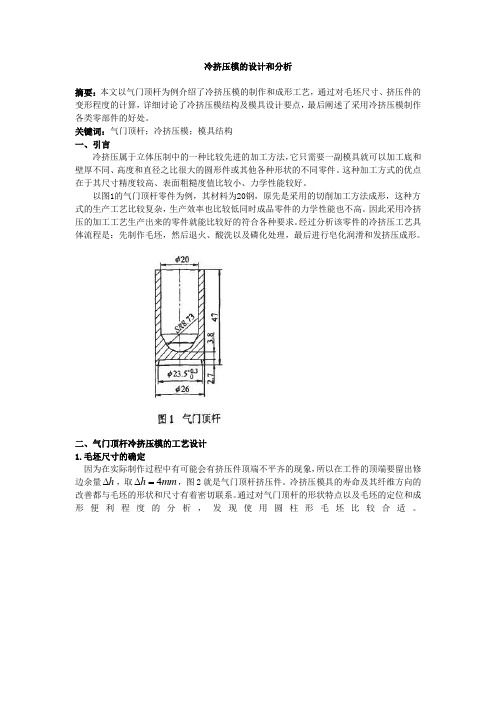
冷挤压模的设计和分析摘要:本文以气门顶杆为例介绍了冷挤压模的制作和成形工艺,通过对毛坯尺寸、挤压件的变形程度的计算,详细讨论了冷挤压模结构及模具设计要点,最后阐述了采用冷挤压模制作各类零部件的好处。
关键词:气门顶杆;冷挤压模;模具结构一、引言冷挤压属于立体压制中的一种比较先进的加工方法,它只需要一副模具就可以加工底和壁厚不同、高度和直径之比很大的圆形件或其他各种形状的不同零件。
这种加工方式的优点在于其尺寸精度较高、表面粗糙度值比较小、力学性能较好。
以图1的气门顶杆零件为例,其材料为20钢,原先是采用的切削加工方法成形,这种方式的生产工艺比较复杂,生产效率也比较低同时成品零件的力学性能也不高。
因此采用冷挤压的加工工艺生产出来的零件就能比较好的符合各种要求。
经过分析该零件的冷挤压工艺具体流程是:先制作毛坯,然后退火、酸洗以及磷化处理,最后进行皂化润滑和发挤压成形。
二、气门顶杆冷挤压模的工艺设计1.毛坯尺寸的确定因为在实际制作过程中有可能会有挤压件顶端不平齐的现象,所以在工件的顶端要留出修边余量h∆,图2就是气门顶杆挤压件。
冷挤压模具的寿命及其纤维方向的∆,取mm=h4改善都与毛坯的形状和尺寸有着密切联系。
通过对气门顶杆的形状特点以及毛坯的定位和成形便利程度的分析,发现使用圆柱形毛坯比较合适。
挤压件毛坯体积的计算是根据制件体积与毛坯体积相等的规则来进行的。
通过计算毛坯体积p V可得:3222119267.2)25.23()7.28.351()220(51)226(mm V p =⨯⨯---⨯⨯-⨯⨯=πππ 为了使得毛坯放入凹模型腔内更加的方便,同时使得模具的磨损减少到最低,进一步提高零件的表面质量,一般凹模型腔尺寸a D 要比毛坯的外径p D 要大,相对于反挤压件来说,凹模型腔尺寸要比毛坯尺寸大mm 5.0左右。
根据这样的原则我们可以计算出毛坯的外径p D ;mm D D a p 95.2505.02605.0=-=-=毛坯长度p l 为: mm D V l p p p 55.22)92.25()119264()()4(2=⨯⨯==ππ经过试验验证,最终将毛坯的实际尺寸确定为mm mm 6.2295.25⨯φ,如图3所示。
冷挤压模具课程设计

冷挤压模具课程设计学院:专业:年级: 指导老师:学生姓名:日期:目录1、冷挤压的定义及特点 (3)1.1.冷挤压的定义 (3)1.2.冷挤压的优点及技术难点 (3)2.材料分析 (5)2.1材料化学成分及机械性能 (5)2.2材料的力学性能分析 (6)2.3毛坯尺寸的确定 (6)2.4坯料制备方法 (6)2.5坯料的软化处理、表面处理及润滑 (6)2.5.1 坯料的软化处理 (6)2.5. 2 坯料的表面处理 (7)2.5. 3 坯料的润滑处理 (8)3 成形工序挤压力的计算 (9)3.1变形程度的计算 (9)3.2图算法冷挤压力的计算 (10)3.3总挤压力 (10)3.4挤压力经验公式的校正 (10)3.5压力机的选择(挤压设备的选择) (10)4.模具设计 (11)4.1挤压模具设计的基本要求 (12)4. 1. 1 模具设计时需考虑的安全措施 (12)4. 1. 2 挤压模具的整体设计 (12)5 . 2 凸、凹模的设计 (12)4. 2. 2 凹模的设计和尺寸 (13)4.3凸、凹模固定圈的设计 (16)4.3.1凸模固定板 (16)4.3.2 凹模固定板 (16)4.4压力垫板的设计 (17)4.5.顶出装置的设计 (17)4.6卸料板的设置 (18)4.7导向装置的设计(导柱导套的设计) (19)4.8模架的设计 (20)5.模具材料的选择 (20)1、冷挤压的定义及特点1.1.冷挤压的定义冷挤压是精密塑性体积成形技术中的一个重要组成部分。
冷挤压是指在冷态下将金属毛坯放入模具模腔内,在强大的压力和一定的速度作用下,迫使金属从模腔中挤出,从而获得所需形状、尺寸以及具有一定力学性能的挤压件。
显然,冷挤压加工是靠模具来控制金属流动,靠金属体积的大量转移来成形零件的。
1.2 . 冷挤压的优点及技术难点目前,冷挤压技术已在紧固件、机械、仪表、电器、轻工、宇航、船舶、军工等工业部门中得到较为广泛的应用,已成为金属塑性体积成形技术中不可缺少的重要加工手段之一。
冷镦挤变形工艺冷镦工艺与模具设计

镦锻比与镦锻次数的关系表
S=h0/d0 镦锻次数
≤2.5
2.5~4.5
1
2
4.5~6 3
酸洗方法:硫酸酸洗、盐酸酸洗、酸洗质量
润滑处理:牛油—石灰润滑、磷化—皂化处理 材料的改制
二、冷镦挤压工艺及模具设计
采用专用自动冷镦机来加工零件。 优点:材料利用率高、提高劳动生产率、使零件具有较高的机械 性 能和疲劳强度、使零件表面得到较高的光洁度。 缺点:模具制造费用高,不适合少量生产。
冷镦工艺基本概念:镦锻比(S) 、冷镦变形程度(ε) 1. 镦锻比(S) — 是指镦锻材料镦锻部分的长度和直径的比值。
a. 金属的结构 一切金属的组织是由许多小晶体组成的,这些小晶体称为“晶粒” 。 常用冷镦材料的晶体结构:体心立方晶格、面心立方晶格和密排六方 晶格 。
b. 金属变形的基本概念 金属材料在外力作用下,所引起尺寸和形状的变化称为“变形”。 金属变形是由弹性变形和塑性变形所组成。
所谓塑性—是指在外力作用下发生永久变形而不损伤其整体性能。 许多零件在成型过程中要求材料有较好的塑性。在冷镦时零件有的部位 变形量很大,如材料的塑性不好将会发生开裂。 在工程中金属材料的塑性用伸长率δ和断面收缩率ψ两个指标来表示,也 就以此衡量 材料的塑性。 δ和ψ的数值可由下公式表示:
4.冷镦变形力计算方法 F=KσT A 式种: F — 冷镦变形力 (MPa)
K — 镦锻头部的形状系数, 一般螺钉、螺栓取 2~2.4 σT — 考虑到冷作硬化后的变形抗力
σT = σbIn (A/A0) (MPa) σb — 金属材料的强度极限 (MPa)
A — 镦锻后头部的最大投影面积 (mm2) A0 —镦锻前坯的断面积 (mm2) ➢ 冷镦常用金属材料及材料准备 常用的金属材料有黑色金属和有色金属两大类。
冷挤压模具设计
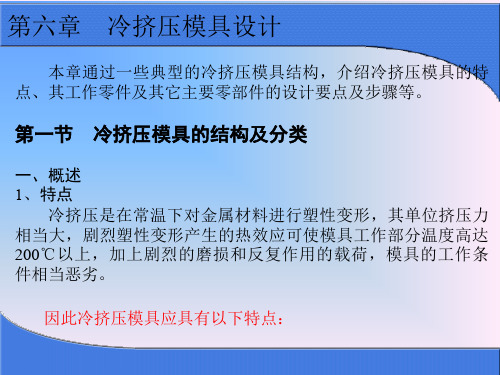
(6)模具工作部分与上下模板之间要设置淬硬压力垫板,以扩大承压 面积,减小上下模板的单位压力,防止压坏上下模板;
(7)上下模板应有足够的厚度,以保证模板具有较高的强度和刚度。
第六章 冷挤压模具设计
2、组成 典型的冷挤压模具由以下几部分组成: 1) 工作部分:如凸模、凹模、顶出杆等; 2) 传力部分:如上、下压力垫板; 3) 顶出部分:如顶杆、反拉杆、顶板等; 4) 卸料部分:如卸料板、卸料环、拉杆、弹簧等; 5) 导向部分:如导柱,导套、模口、导筒等; 6) 紧固部分:如上、下模板、凸模固定圈、固定板、压板、模柄、 螺钉等。
第六章 冷挤压模具设计
二、冷挤压模具分类
冷挤压模具有多种结构形式,可根据冷挤压件的形状、尺寸 精度及材料来选择合适的模具结构形式。 (一) 按工艺性质分类
正挤压模:
反挤压模:
复合挤压模:
镦挤压模:
第六章 冷挤压模具设计
1、正挤压模
图6-1为实心 件正挤压模。
第六章 冷挤压模具设计
图6-2为空心件正挤压模(坯料为黑色金属)。
图e为浮动式凸模,其在芯棒上部放一弹簧,在挤压中芯棒受拉,弹簧被压缩, 可以克服更大的拉力,能有效地防止芯棒拉断。这种凸模可以用于材料硬度和摩 擦力比较大的黑色金属挤压。
为了防止芯棒拉断及卸料方便,芯棒一般做出10’~30’的斜度。
第六章 冷挤压模具设计
2、正挤压凸模尺寸参数设计 凸模各部分尺寸参数见表6-1。
第六章 冷挤压模具设计
第二节 模具工作部分的设计
冷挤压模具工作部分是指凸模、凹模、顶杆等在挤压时直接 参与挤压过程的一些零件。 一、正挤压模具工作部分零件设计 (一) 正挤压凸模
冷挤压毕业设计

冷挤压毕业设计冷挤压技术是一种常用于金属加工的方法,它通过将金属材料置于高压下,利用冷挤压机械设备将其挤压成所需形状。
这种技术被广泛应用于汽车、航空航天、电子等领域,因其高效、精确的特点而备受青睐。
冷挤压技术的出现为工程师们提供了更多的设计空间。
在传统的金属加工方法中,常常需要进行多道工序的加工,而冷挤压技术则能够将多道工序合二为一,大大提高了生产效率。
同时,冷挤压技术还能够实现对材料的精确控制,使得产品的尺寸和形状更加准确,从而提高了产品的质量。
在汽车制造领域,冷挤压技术的应用尤为广泛。
例如,在车身制造中,冷挤压技术可以用于制造车门、车顶等部件。
相比传统的焊接工艺,冷挤压技术能够减少焊接接缝,提高了零部件的强度和密封性。
此外,冷挤压技术还可以实现对材料的局部加压,从而增加车身的刚性和安全性。
航空航天领域也是冷挤压技术的重要应用领域之一。
在飞机制造中,冷挤压技术可以用于制造飞机的翼梁、机身等部件。
由于航空航天领域对材料的要求非常高,冷挤压技术能够保证产品的尺寸精度和表面质量,满足飞机的性能和安全要求。
除了汽车和航空航天领域,冷挤压技术还在电子领域得到了广泛应用。
在电子设备的制造过程中,常常需要制造各种金属外壳和散热器。
利用冷挤压技术,可以将金属材料挤压成所需的形状,实现对外壳和散热器的精确控制。
此外,冷挤压技术还可以实现对导电材料的加工,制造出高精度的电子元器件,提高了电子设备的性能和可靠性。
冷挤压技术的应用不仅仅局限于以上几个领域,它还可以用于制造各种精密零部件、工具和模具等。
例如,在机械制造中,冷挤压技术可以用于制造各种齿轮、螺纹等零部件,提高了机械设备的运行效率和可靠性。
在模具制造中,冷挤压技术可以用于制造各种模具,提高了模具的耐用性和加工精度。
冷挤压技术的发展离不开材料科学的支持。
随着材料科学的不断进步,新型材料的开发为冷挤压技术的应用提供了更多的可能性。
例如,高强度钢、铝合金等新型材料的出现,使得冷挤压技术在汽车、航空航天等领域的应用更加广泛。
金属冷挤压成形工艺设计

2.毛坯体积计算: 三维建模后,利用计算机直接可求出零件体积,从而得毛坯体积:
V0 V 41051 .62mm 3
圆整后,取: V0 41050 mm 3
3.毛坯尺寸计算: 毛坯外径:取工件的外径
D0
40 mm
毛坯高度:H 0
V0 A0
32.08mm 圆整取: H 0
32mm
1. 凸模工作部分尺寸设计
凸模依据零件的内腔进行设计,其具体结构尺寸如 下零件图所示:
零件图2
零件的尺寸公差按普通精度等级查取为 0.12mm
凸模公差为 p 0.2 0.024 mm
则,凸模尺寸为
dp
(30
0.12)
0 0.024
mm
30.1200.024
mm
其他部分尺寸以此同样公差确定。
2. 凹模尺寸结构 凹模形状依据零件外表面截面确定为圆筒形即可,其尺寸如下图
凹模公差 d 0.2 0.024 mm
则,凹模尺寸为
Dd
(40
0.12
)
0.024 0
mm
40.12
0.024 0
mm
End.
PPT背景图片:/beijing/
式中,A0 为毛坯横断面积,A0 D02 1256 mm 2
4.计算总变形程度:
F
A0 A1 A0
100
0 0
1256 783 1256
37.6 0 0
式中,A1为零件的横断面积,建模后利用计算机可求得:A1 783 mm 2
5.工序设计 (1)下料:
H
0
D0
- 1、下载文档前请自行甄别文档内容的完整性,平台不提供额外的编辑、内容补充、找答案等附加服务。
- 2、"仅部分预览"的文档,不可在线预览部分如存在完整性等问题,可反馈申请退款(可完整预览的文档不适用该条件!)。
- 3、如文档侵犯您的权益,请联系客服反馈,我们会尽快为您处理(人工客服工作时间:9:00-18:30)。
目录目录 (1)冷挤压模具设计及其成形过程 (3)第一章绪论 (3)1.1冷挤压成形技术发展概况 (5)1.2选题依据和设计主要内容 (7)1.2.1毕业设计(论文)的内容 (7)1.2.2 毕业设计(论文)的要求 (7)第二章冷挤压工艺设计 (8)2.1挤压工艺步骤 (8)2.2工艺设计步骤 (10)2.2.1计算毛坯的体积 (10)2.2.2确定坯料尺寸 (10)2.2.3计算冷挤压变形程度 (11)2.2.4确定挤压件的基本数据 (12)2.2.5确定挤压次数 (12)2.2.6工序设计 (12)2.2.7工艺方案确定 (20)2.2.8各主要工序工作特点进一步分析 (21)第三章压力设备选择 (24)3.1各主要工序所需镦挤力 (24)3.2主要设备选用 (26)4.1冷挤压模具设计要求 (28)4.2凸模设计依据 (29)4.3冷挤压组合凹模设计依据 (31)4.4凸模设计 (37)4.4.1镦平凸模设计 (37)4.4.2凹模设计 (38)4.5预成形模具设计 (41)4.5.1预成形凸模设计 (41)4.5.2预成形凹模设计 (42)4.6终成形模具设计 (44)4.6.1终成形凸模设计 (44)4.6.2终成形凹模设计 (45)4.7冷挤压模架设计 (46)4.7.1冷挤压模架设计的基本原则 (46)4.7.2模架的设计 (47)4.7.3其它零件设计 (48)第五章挤压模具零件加工工艺的编制 (53)5.1加工工艺编制原则 (53)5.2加工工艺的编制 (55)第六章总结及课题展望 (58)6.1本文工作总结 (58)6.2课题展望 (59)参考文献 (59)附录一:英文科技文献翻译 (62)英文翻译: (67)附录二毕业设计任务书 (72)冷挤压模具设计及其成形过程机械与电气工程学院机械设计制造及其自动化专业06城建机械乔红娇指导老师雷声第一章绪论挤压就是零件金属毛坯放在挤压模腔中,在一定温度下,通过压力机上固定的凸模或凹模向毛坯施加压力,使金属毛坯产生塑性变形而制得零件的加工方法。
挤压的加工原理是金属坯料处于三向压应力状态下变形时,能大大提高金属的塑性,允许金属有较大的变形。
挤压变形的特征是由大截面向小截面的变形。
挤压即可在专用挤压机上进行,也可在一般的机械压力机、液压机、摩擦压力机以及高速锤上进行。
挤压加工有许多特点,主要表现在挤压变形过程的应力应变状态、金属流动行为、产品的综合质量、生产的灵活性与多样性、生产效率与工艺流程简单、设备投资较少等方面。
而冷挤压除了前面列出的共性优点外,还有它自己独特的优点。
如能够得到强度大、刚性好而质量轻的零件;零件的精度等级较高、表面粗糙度值较低;节约能源,工作环境得到较大改善。
挤压按照挤压坯料的温度分类一般可分为冷挤压、温挤压、热挤压三类,而其中冷挤压应用范围最广。
冷挤压一般是指在回复温度以下的挤压,对于黑色金属常指在室温中对坯料进行的挤压。
由于冷挤压具有很多优点,所以它已越来越多地用来大量生产软质金属、低碳钢、低合金钢零件。
但是冷挤压的优点往往不能用简单的方法发挥出来,因为冷挤压是金属在冷态下、强烈的三向压应力状态下变形的,变形抗力较大。
因此它也有些自己的缺点。
如模具易磨损,易破坏,因此要求模具材料好、对挤压设备要求较高、对所加工的原材料要求高;挤压前坯料处理复杂;工艺流程设计技术水准较高,研发过程周期长,投入大。
金属材料的冷、温、热变形通常是以金属成形过程中加工硬化、回复和再结晶状态来判定的。
金属塑性变形后,材料处于加工硬化状态,称为冷变形;金属塑性变形后,材料具有再结晶组织,称为热变形;介于了冷变形与热变形之间,材料处于回复状态,称为问温变形。
各种塑性变形的温度范围见图1.1。
图1.1 各种塑性变形的温度范围挤压工艺正是在金属材料冷变形、温变形、热变形这三种状态下进行,并按被挤压材料的温度分为了冷挤压、温挤压、热挤压三大类。
在此我们主要用到的是冷挤压加工。
1.1冷挤压成形技术发展概况挤压技术的发展经历了漫长的历史过程。
19世纪末,法、英、美、德等国开始用冷挤压法生产软质有色金属零部件。
第一次世界大战期间,美国采用冷挤压法大批量生产黄铜弹壳,并企图用冷挤压法生产钢质弹壳,但未获得成功,原因是当时不能用工具钢作为模具材料,也没有找到良好的表面处理方法和润滑剂。
第一次世界大战以后,德国人于1921年制造出冷挤钢管压力机,经过进十年的研究及实验,知道1931年冷挤钢管才在实验室里试制成功,但不能正式投入生产,其原因也是由于钢冷挤压时变形抗力过大,找不到用于生产的模具材料和表面润滑处理方法。
第二次世界大战前夕,德国对弹壳的需求量猛增,但是用黄铜材料制造弹壳,因原料来源不足,满足不了战争的需要。
为了扩大弹壳的生产量,德国秘密试验用冷挤压法生产钢弹壳,但一直没有成功,直到1942年德国人找到了采用表面磷化、皂化处理法,并用合金工具钢作为模具材料,成功地用冷挤压法大批量生产了钢弹壳,当时在战场上引起了极大的震动和惊诧。
第二次世界大战一结束,美国查明了德国人关于钢的冷挤压的全部资料,并聘用德国专家,继续深入地研究钢的冷挤压,大规模地开办了用冷挤压法生产弹壳和弹体的军工厂。
第二次世界大战以后冷挤压工艺的应用开始由军工向民用转化。
从949年开始,美、德等国在民用工业中采用冷挤压法加工各种钢质零件,并进一步开展了钢的冷挤压研究工作。
日本于1957年引进第一台专用冷挤压力机,首先在钟表等精密仪器工业中采用冷挤压加工。
由于这种加工方法的经济效益显著,不久,便在大批量生产的汽车和电器等工业部门中得到广泛应用,现在已成为一种重要的加工手段,遍及于各个工业部门。
在我国,解放前的冷挤压技术是很落后的,当时只有极少数工厂用铅、锡等有色金属挤压牙膏管、线和管材等。
解放后冷挤压技术得到了一定不敢程度的发展,20世纪50年代开始了铜及其合金的冷挤压,60年代开始了黑色金属的冷挤压,近年来随着我国工业生产和科学技术的蓬勃发展,冷挤压技术也得到了迅猛发展。
这种先进的压力加工工艺已在我国的工业建设中起着令人瞩目的作用。
目前,我国已对铝、锡、银、纯铜、无氧铜、黄铜、锡青铜、锌及其合金、纯铝、防锈铝、锻铝、硬铝、可伐合金、泊莫合金、低碳钢以及中碳钢等多种金属进行冷挤压,甚至对轴承钢、高速钢等也可进行一定变形量的冷挤压。
我国可以制造的冷挤压件及型材的品种也多种多样。
在模具材料的使用方面,除了采用高速钢、高碳高铬钼钢、滚珠轴承钢、弹簧钢等以外,还采用不少新型模具钢、硬质合金以及钢结硬质合金等。
在模具结构方面,采用近代的最优化设计方法以及计算机辅助设计,在保证强度、刚度、可靠性等要求的提下充分发挥了模具材料的潜力。
在冷挤压技术的理论研究方面,国内不少高校和研究院所正在采用有限元等计算方法、数值模拟冷挤压成形全过程,以及揭示冷挤压时的金属流动规律及应力应变规律,这些都会对冷挤压技术的发展这更大的推动作用。
综上所述,我国冷挤压技术的研究水平还是较高的,在冷压技术推广方面曾一度达到轰轰烈烈的局面,但发展速度较为缓慢。
其主要原因有:作为作为冷挤压零件最广泛应用领域的汽车工业尚不发达,汽车零部件生产厂点多、批量小,达不到规模经济生产;缺少专用冷挤压力机,用通用压力机又满足不了冷挤工艺的特殊要求;缺少冷挤压专用钢种,虽有标准件拥抱过冷镦钢,但品种少,规格小,不能满足较大零件冷挤压的要求等。
今年来,我国汽车工业、摩托车工业得到迅速发展,给冷挤压技术应用带来了新的机遇。
当代轿车某些关键部件,从设计开始就是立足于精密成形,从结构反方面很难用机加工方法来代替,这些关键零件的国产化,大大促进了精密锻造特别是冷挤压技术的发展。
1.2 选题依据和设计主要内容1.2.1毕业设计(论文)的内容螺钉是重要连接零件,要求结构强度高,宜采用冷精锻成形。
杆部变截面,采用正挤压工步;头部采用先聚料后镦挤的方法。
挤压变形力较大,模具设计时要保证模具有足够的强度。
1.2.2 毕业设计(论文)的要求1)正确排工步,在满足工艺要求的前提下,采用最少的工步;2)模具结构要合理;3)掌握组合凹模优化设计方法;4)手绘总装图1副和主要工作零件图;5)使用三维造型软件, 画局部总装图;第二章冷挤压工艺设计从坯料变为挤压件成品需要一系列工序。
挤压工艺设计要确定一系列必要的工序,达到以最少的工序,最短的流程,使坯料逐步变形成要求的挤压件形状,经济合理地生产出符合质量要求的挤压件。
典型的挤压工艺过程,由许多工序组合而成,其中包括下料、镦粗、校形(坯料准备工序),预成形工序和最终成形工序(正挤压、反挤压、复合挤压或镦挤相结合的组合工艺),以及中间的辅助工序(除油、酸洗、退火、润滑)和最后的机械加工工序。
无论是制坯工序、中间工序还是成形工序都是冷挤压过程中的重要组成部分。
冷挤压适合加工软质且延展性好,硬度大致在100HBS一下的金属材料。
冷挤压件的形状应保证金属在挤压方向的变形均匀,流速一致,同时使单位挤压力较低,使模具寿命较高。
最好的挤压件形状是轴对称的回转体。
挤压件内、外型面应避免直角过渡,直径变化小的零件不应采用挤压工艺成形,用切削加工方法较为有利。
挤压零件应尽量避免壁面上的环形槽和径向孔,避免挤压成形小直径的深孔。
冷挤压工艺设计是在确定挤压件形状、尺寸、精度和材料之后着手设计模具之前的一个阶段,在此之前要拟定制定的挤压加工工艺和有关的工艺顺序和数量,并研究如何具体实现符合要求的质量控制、经济性问题。
2.1挤压工艺步骤工艺设计时,从研究产品图进行工艺分析开始,首先根据变形前后材料体积不变法则及所设计的挤压件图形,计算出坯料体积,并由挤压件尺寸或中间工序尺寸,按照体积公式确定毛坯尺寸,再按变形程度,挤压力大小和形状复杂程度,确定工序数目,然后进行工序设计,决定中间成形工序的成形预备形状和尺寸,并选定成形方法,安排加工工序。
最后决定工艺方案,即选定材料和设备,编制工艺流程和构思模具结构,同时进行全面工艺评价和核算技术、经济指标。
挤压工艺设计程序可用以下一个工艺流程图来表示:图2.1 工艺设计程序在模具设计的过程中,还可能反过来对初始的工艺方案进行修正;在试验过程中进一步补充完善,并就实际作业条件,重新评价工艺设计。
在挤压工艺方案设计中,需要做出下述的评价和估算:1、工艺性评价(1)挤压件形状复杂程度;(2)挤压件成形难易程度;(3)挤压件变形程度的大小;(4)挤压件的尺寸范围;(5)挤压件的精度等级;(6)挤压件性能指标;(7)挤压件质量标准;(8)挤压材料的工艺性能;2、估算项目(1)总变形程;(2)总工序数目;(3)总工装套数;(4)效果分析及评价根据上面这些评价和估算,便可确定一种经济合理的最佳工艺方案。