丁二烯工艺
丁二烯萃取精馏工艺设计

丁二烯萃取精馏工艺设计丁二烯是一种重要的基础化学品,广泛应用于合成合成橡胶、塑料、树脂和油墨等领域。
丁二烯的生产通常采用烷基锂催化剂聚合反应,生成丁二烯和其他杂质。
为了获得高纯度的丁二烯,需要进行精馏分离。
丁二烯萃取精馏是目前广泛采用的一种分离技术,具有操作简便、分离效率高、产品纯度高等优点。
丁二烯萃取精馏工艺的设计涉及到多个关键参数,如萃取剂种类、萃取剂用量、精馏塔塔板数目、进料温度、进料流量等。
下面将从这些方面介绍丁二烯萃取精馏工艺的设计。
1. 萃取剂种类萃取剂是丁二烯萃取精馏中的关键因素之一。
常用的萃取剂有苯、甲苯、二甲苯、正庚烷等。
不同的萃取剂对丁二烯的分离效果有所不同。
例如,苯的选择性较高,但易与丁二烯发生加成反应,形成高沸点产物,影响精馏效果。
因此,在选择萃取剂时应综合考虑其分离效果和化学性质,并选择合适的物料组合。
2. 萃取剂用量萃取剂用量是影响丁二烯萃取精馏效果的另一个重要因素。
一般而言,萃取剂用量越大,分离效果越好,但同时也会增加成本。
在确定萃取剂用量时,应综合考虑经济性和工艺效果,选择合适的用量。
3. 精馏塔塔板数目精馏塔塔板数目对丁二烯萃取精馏的分离效果有着极大的影响。
塔板数目越多,精馏分离效果越好,但同时也会增加设备复杂度和成本。
在选择塔板数目时,应根据实际情况,综合考虑分离效果和成本,选择适当的塔板数目。
4. 进料温度和进料流量进料温度和进料流量是丁二烯萃取精馏中比较重要的参数。
进料温度过高会导致产物分解,影响精馏效果;进料流量过大会降低分离效率。
在确定进料温度和进料流量时,应综合考虑分离效果和工艺经济性,选择合适的操作条件。
丁二烯萃取精馏工艺的设计需要综合考虑多个参数,包括萃取剂种类、萃取剂用量、精馏塔塔板数目、进料温度和进料流量等。
在设计工艺时,应根据实际情况,综合考虑分离效果和成本,选择合适的操作条件,以获得高效、经济、稳定的生产工艺。
丁二烯生产工艺流程设计与设备选型
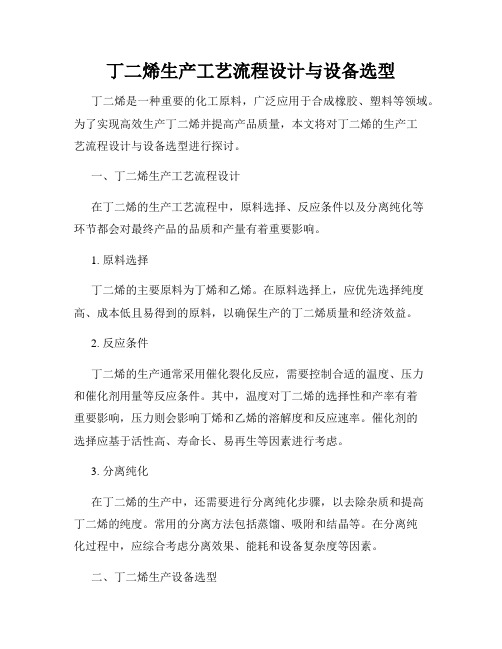
丁二烯生产工艺流程设计与设备选型丁二烯是一种重要的化工原料,广泛应用于合成橡胶、塑料等领域。
为了实现高效生产丁二烯并提高产品质量,本文将对丁二烯的生产工艺流程设计与设备选型进行探讨。
一、丁二烯生产工艺流程设计在丁二烯的生产工艺流程中,原料选择、反应条件以及分离纯化等环节都会对最终产品的品质和产量有着重要影响。
1. 原料选择丁二烯的主要原料为丁烯和乙烯。
在原料选择上,应优先选择纯度高、成本低且易得到的原料,以确保生产的丁二烯质量和经济效益。
2. 反应条件丁二烯的生产通常采用催化裂化反应,需要控制合适的温度、压力和催化剂用量等反应条件。
其中,温度对丁二烯的选择性和产率有着重要影响,压力则会影响丁烯和乙烯的溶解度和反应速率。
催化剂的选择应基于活性高、寿命长、易再生等因素进行考虑。
3. 分离纯化在丁二烯的生产中,还需要进行分离纯化步骤,以去除杂质和提高丁二烯的纯度。
常用的分离方法包括蒸馏、吸附和结晶等。
在分离纯化过程中,应综合考虑分离效果、能耗和设备复杂度等因素。
二、丁二烯生产设备选型丁二烯的生产设备选型是确保工艺流程连续高效运行的关键。
在设备选型时,应考虑以下几个方面。
1. 反应釜由于丁二烯的生产需要进行催化裂化反应,因此反应釜的选型非常重要。
反应釜应具备良好的耐压性能、优异的传热效果以及高度的密封性。
同时,对反应釜的清洗和维护也需要考虑便捷性。
2. 分离设备在分离纯化环节中,常用的设备包括蒸馏塔、吸附塔和结晶器等。
对于丁二烯生产来说,应选择具备高效传质和传热性能、操作稳定可靠的设备,以确保分离纯化的效果。
3. 冷却设备丁二烯的生产过程中,需要进行冷却以保证反应温度的控制。
冷却设备的选型应考虑冷却效果、能耗和操作可行性等因素,并且能够适应生产规模的变化。
4. 自动控制系统在丁二烯生产过程中,良好的自动控制系统能够提高工艺的稳定性和可靠性。
自动控制系统应具备实时监测、报警和调节功能,以及与其他设备的联动控制能力,实现高效自动化运行。
丁二烯生产工艺流程设计与质量控制

丁二烯生产工艺流程设计与质量控制一. 引言丁二烯是一种重要的合成橡胶原材料,广泛应用于橡胶工业、塑料工业等领域。
为了确保丁二烯的生产效率和质量稳定,需要进行合理的工艺流程设计和严格的质量控制措施。
本文将围绕丁二烯的生产工艺流程设计与质量控制展开探讨。
二. 丁二烯生产工艺流程设计丁二烯的生产可分为烷烃烯化法和烯烃裂解法两种主要工艺。
本文将重点介绍烷烃烯化法的工艺流程设计。
1. 原料准备烷烃烯化法中,常用的原料是丁烷、溶剂和催化剂。
丁烷作为丁二烯的原料,需要经过精炼处理以提高其纯度。
溶剂的选择要考虑其溶解能力和稳定性,一般选择具有较高热稳定性的溶剂。
催化剂的选择要考虑其活性和选择性,优选具有高效活性和较好选择性的催化剂。
2. 反应器设计反应器是丁烷烯化反应的核心设备,其设计要考虑反应条件和反应热平衡等因素。
反应器一般采用多管式或回流式设计,以提高反应的效率和选择性。
此外,反应器还需要考虑搅拌和加热冷却系统的设计,以确保反应均匀性和热平衡。
3. 分离与纯化反应后的产物中含有未反应的丁烷、副产物和杂质等物质,需要进行分离和纯化处理。
分离一般采用精馏、萃取和吸附等技术,以分离出纯净的丁二烯。
纯化过程中,还需要考虑对杂质的去除和如何提高丁二烯的纯度。
4. 支撑设施丁二烯生产过程中还需要考虑辅助设施的建设,如催化剂再生装置、废气处理系统和能源供应系统等。
这些支撑设施对于生产效率和环境保护都具有重要意义。
三. 丁二烯质量控制为保证丁二烯的产品质量稳定,需要采取一系列质量控制措施。
下面从原料控制、工艺控制和产品检测三个方面进行介绍。
1. 原料控制原料的质量直接影响到终产品的质量稳定性。
因此,对于丁烷、溶剂和催化剂等原料的选择要严格把控。
在原料进厂时需进行严格检验,确保原料符合相关标准和要求。
2. 工艺控制工艺参数对于丁二烯生产过程中反应的效率和选择性具有重要影响。
对于丁烷烯化反应,需要控制反应温度、压力和反应时间等参数,以确保反应的高效进行。
丁二烯抽提工艺技术路线选择概述课件

丁二烯抽提工艺技术路线选择
1.1 NMP法
•
NMP法工艺流程:
• 裂解碳四汽化后进入主洗塔底部,含水的N-甲基吡咯烷酮萃取剂进入该塔塔顶下的几块塔 板处,丁二烯和更易溶解的组分及部分丁烷、丁烯被吸收,抽余碳四从塔顶出装置。
• 主洗塔底部的富溶剂进入精馏塔,在该塔中,溶剂吸收的丁烷丁烯被更易溶的丁二烯-1,3、 甲基乙炔和碳四炔烃置换出来,含有碳四炔烃和甲基乙炔的丁二烯-1,3物流,从精馏塔的 侧线以气态排出,进入后洗塔。在后洗塔中,用新鲜溶剂进行萃取,比丁二烯-1,3更易溶
第10页/共26页
丁二烯抽提工艺技术路线选择
2.2 溶剂性能
N-甲基吡咯烷酮(NMP)、二甲基甲酰胺(DMF) 和乙腈(ACN)三种溶剂性能对比见表3-2。
序号
项目
N-甲基吡咯烷酮NMP
二甲基甲酰胺DMF
乙 腈ACN
1
50℃时的相对溶解度
对1,3-丁二烯
1
1
1
对顺丁烯-2
1.63
1.56
1.43
对1,2-丁二烯
第7页/共26页
丁二烯抽提工艺技术路线选择
1.3 ACN法
• 二级乙腈法的生产过程基本与DMF法相同, 其不同之处在于采用含水10%的溶剂,因乙 腈沸点低,又与丁二烯形成共沸物,所以须 增设水萃取回收并提浓乙腈的系统。
• 乙腈法具有萃取剂易于获得,工艺可靠,能 阻止双烯烃热聚,工艺流程中不需要压缩机 等优点。但由于乙腈沸点低,蒸汽压较高, 运转过程中损失较大。毒性也较大。
第4页/共26页
丁二烯抽提工艺技术路线选择
1.2 DMF法
• DMF法又称GPB法,系日本瑞翁公司研究开发,于 1965年工业化。由于该技术比较先进、成熟可靠,世 界各国相继采用,目前是生产丁二烯的各种方法中吨 位较高的一种。我国燕山石化公司于1976年首次从日 本引进一套年产4.5万吨的丁二烯装置,随后扬子、齐 鲁、南京、金山、抚顺、广州又陆续与乙烯装置一起 引进6套。经过消化吸收,现已建成投产国产化装置5 套(包括扬子石化一套),单套生产能力约5万吨/年。 至今我国利用DMF法共建成12套生产装置,总计生产 能力约占全国丁二烯抽提生产能力的70.2%。
丁二烯的生产—乙腈法生产丁二烯的工艺流程

乙腈法生产丁二烯的工艺流程
两级萃取流程
C4:丁烷(正丁烷,异丁烷) 、丁烯(1-丁烯,异丁烯,2-丁烯(顺式,反式) 、丁二烯、炔烃(丁炔,乙烯基乙炔)
溶剂
丁烷 丁烯 丁二烯 炔烃
丁烷 丁烯
丁二烯 炔烃 溶剂
丁二烯 炔烃
溶剂
丁二烯 溶剂炔烃 溶剂第一级萃取精馏第二级萃取精馏
丁二烯蒸出
炔烃 溶剂
炔烃蒸出
乙腈法生产丁二烯的工艺流程
乙腈法生产丁二烯的流程示意图
项目八 丁二烯的生产
石油化工产品生产技术
任 务 四
流 程 的 组 织
生 产 工 艺
乙腈法生产丁二烯的工艺流程
乙腈法生产丁二烯的工艺流程
萃取剂乙腈的特点
①选择性高,明显提高组分的相对挥发度。加入乙腈后,组分的挥 发度顺序为炔烃<二烯烃<单烯烃<烷烃。
②乙腈沸点81.6℃,比碳四馏分任一组分都高,挥发性小,不易混 入塔顶产品中,却易于与其他组分分离回收,损耗小。与其它萃 取剂比较沸点较低,可在较低温度下操作,降低能量损耗,回收 分离时也可以避免塔釜温度过高。
丁二烯生产工艺流程设计与安全评价

丁二烯生产工艺流程设计与安全评价丁二烯是一种重要的化工原料,在合成橡胶、塑料和化学品制造中具有广泛的应用。
为了确保丁二烯的生产过程高效、安全、稳定,需要进行工艺流程设计和安全评价。
本文将探讨丁二烯生产工艺的流程设计以及安全评价的相关内容。
一、工艺流程设计1. 原料准备:丁二烯的主要原料是丁烯和乙醇。
其中丁烯为乙醇脱水制备,需要确定合适的脱水剂、温度和时间等参数,以提高丁烯的纯度和产率。
2. 反应装置设计:丁二烯的生产主要是通过丁烯的烯烃加聚反应完成的。
反应器的设计应考虑反应温度、压力、催化剂的选择以及反应器的尺寸和材料等因素。
同时,为了提高反应效率和产品质量,还需要考虑适当的搅拌和冷却条件。
3. 分离纯化:在反应后,需要进行产品的分离纯化。
这包括对乙醇催化剂的回收利用、丁二烯和其他副产物的分离、纯化和再生等步骤。
分离纯化过程的设计需结合实际情况和工艺要求,选择适当的分离技术和设备,以提高产品的纯度和收率。
4. 产品储存和运输:生产完成后,丁二烯需要储存和运输至下游工艺或客户处。
应选择适当的储罐和容器,对丁二烯进行储存和包装,确保产品的安全性和稳定性。
二、安全评价1. 火灾和爆炸风险评估:丁二烯是易燃易爆的化学品,因此应对生产过程中的火灾和爆炸风险进行评估。
包括对原料、反应装置、储存设施和环境条件等因素进行分析,预测潜在的火灾和爆炸风险,并采取相应的措施进行防范。
2. 有害物质防护:丁二烯的生产过程中还包括一些有害物质的生成和释放,如有毒气体、废水和废气等。
应对这些有害物质进行评估,确定其对环境和人体的潜在风险,并采取相应的防护设施和处理措施,以减少对环境和人体的影响。
3. 装置安全设计:在丁二烯生产工厂的设计过程中,应考虑装置的安全设计。
包括对设备的选择、设计和材料的选择,以及安全设备的设置。
同时,在施工和运营过程中,还需要进行定期的安全检查和维护,确保装置的正常运行和安全性。
4. 应急预案和培训:针对丁二烯生产过程中可能发生的事故和紧急情况,需要制定相应的应急预案。
丁二烯生产技术
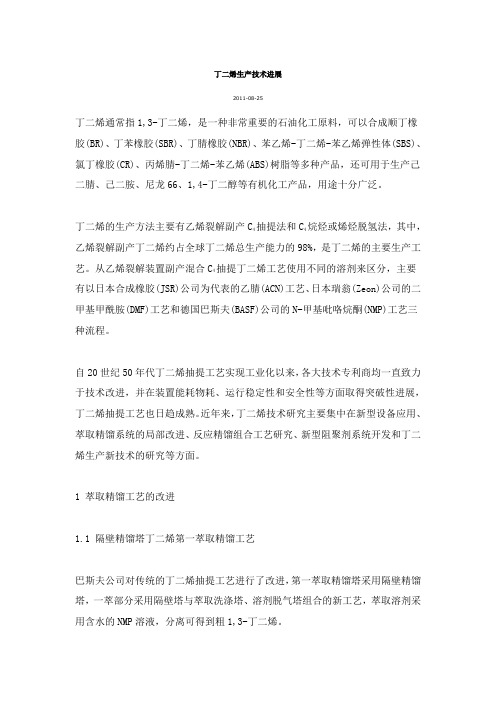
丁二烯生产技术进展2011-08-25丁二烯通常指1,3-丁二烯,是一种非常重要的石油化工原料,可以合成顺丁橡胶(BR)、丁苯橡胶(SBR)、丁腈橡胶(NBR)、苯乙烯-丁二烯-苯乙烯弹性体(SBS)、氯丁橡胶(CR)、丙烯腈-丁二烯-苯乙烯(ABS)树脂等多种产品,还可用于生产己二腈、己二胺、尼龙66、1,4-丁二醇等有机化工产品,用途十分广泛。
丁二烯的生产方法主要有乙烯裂解副产C4抽提法和C4烷烃或烯烃脱氢法,其中,乙烯裂解副产丁二烯约占全球丁二烯总生产能力的98%,是丁二烯的主要生产工艺。
从乙烯裂解装置副产混合C4抽提丁二烯工艺使用不同的溶剂来区分,主要有以日本合成橡胶(JSR)公司为代表的乙腈(ACN)工艺、日本瑞翁(Zeon)公司的二甲基甲酰胺(DMF)工艺和德国巴斯夫(BASF)公司的N-甲基吡咯烷酮(NMP)工艺三种流程。
自20世纪50年代丁二烯抽提工艺实现工业化以来,各大技术专利商均一直致力于技术改进,并在装置能耗物耗、运行稳定性和安全性等方面取得突破性进展,丁二烯抽提工艺也日趋成熟。
近年来,丁二烯技术研究主要集中在新型设备应用、萃取精馏系统的局部改进、反应精馏组合工艺研究、新型阻聚剂系统开发和丁二烯生产新技术的研究等方面。
1 萃取精馏工艺的改进1.1 隔壁精馏塔丁二烯第一萃取精馏工艺巴斯夫公司对传统的丁二烯抽提工艺进行了改进,第一萃取精馏塔采用隔壁精馏塔,一萃部分采用隔壁塔与萃取洗涤塔、溶剂脱气塔组合的新工艺,萃取溶剂采用含水的NMP溶液,分离可得到粗1,3-丁二烯。
C馏分换热后进入隔壁塔第一分区的中部,来自萃取洗涤塔的底部物流循环进入4第一分区的上部,来自溶剂脱气塔的一股溶剂进入第二分区的上部,第二分区的炔烃化合物塔顶抽出粗1,3-丁二烯产品,从隔壁塔的下部共用塔区域抽出含C4的溶剂,这股物流进入溶剂脱气塔进行溶剂再生,脱气塔塔釜物流循环。
来自隔壁精馏塔第一分区的顶部物流加入到萃取洗涤塔的下部,通过在萃取洗涤塔的上部区域加入一股溶剂进行逆流萃取,从萃取洗涤塔的顶部抽出抽余液。
丁二烯工艺基础知识
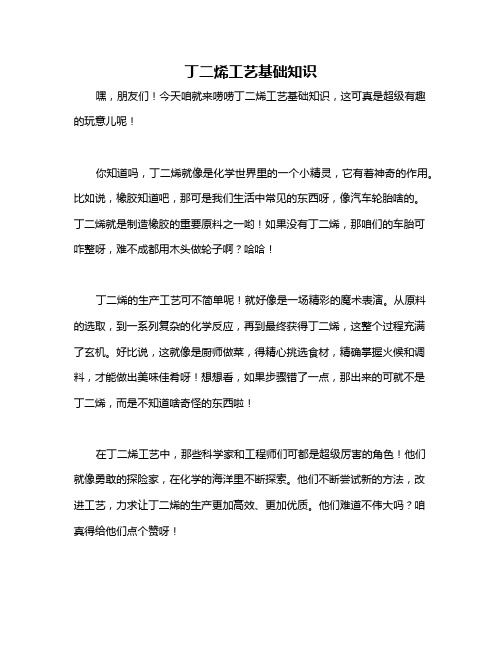
丁二烯工艺基础知识
嘿,朋友们!今天咱就来唠唠丁二烯工艺基础知识,这可真是超级有趣的玩意儿呢!
你知道吗,丁二烯就像是化学世界里的一个小精灵,它有着神奇的作用。
比如说,橡胶知道吧,那可是我们生活中常见的东西呀,像汽车轮胎啥的。
丁二烯就是制造橡胶的重要原料之一哟!如果没有丁二烯,那咱们的车胎可咋整呀,难不成都用木头做轮子啊?哈哈!
丁二烯的生产工艺可不简单呢!就好像是一场精彩的魔术表演。
从原料的选取,到一系列复杂的化学反应,再到最终获得丁二烯,这整个过程充满了玄机。
好比说,这就像是厨师做菜,得精心挑选食材,精确掌握火候和调料,才能做出美味佳肴呀!想想看,如果步骤错了一点,那出来的可就不是丁二烯,而是不知道啥奇怪的东西啦!
在丁二烯工艺中,那些科学家和工程师们可都是超级厉害的角色!他们就像勇敢的探险家,在化学的海洋里不断探索。
他们不断尝试新的方法,改进工艺,力求让丁二烯的生产更加高效、更加优质。
他们难道不伟大吗?咱真得给他们点个赞呀!
咱们再来说说这丁二烯的用途吧,那可真是广泛得很呐!不仅能做橡胶,还能在其他好多领域发挥作用呢!这就像一个全能选手,哪里需要往哪去。
哎呀呀,丁二烯可真是太重要啦!
总之,丁二烯工艺基础知识就像是一个宝藏,等待着我们去挖掘,去了解。
大家难道不想深入探究一下吗?赶紧行动起来吧,去发现丁二烯的更多奇妙之处!
我的观点结论就是:丁二烯工艺非常重要且有趣,值得我们去好好学习和了解!。
乙腈法抽提丁二烯工艺流程
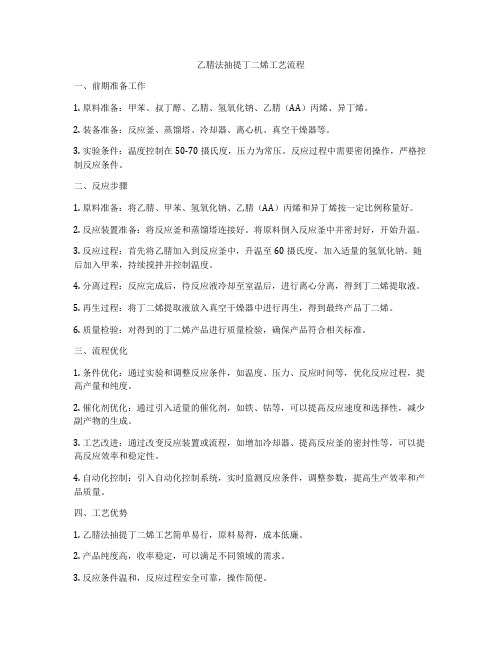
乙腈法抽提丁二烯工艺流程一、前期准备工作1. 原料准备:甲苯、叔丁醇、乙腈、氢氧化钠、乙腈(AA)丙烯、异丁烯。
2. 装备准备:反应釜、蒸馏塔、冷却器、离心机、真空干燥器等。
3. 实验条件:温度控制在50-70摄氏度,压力为常压。
反应过程中需要密闭操作,严格控制反应条件。
二、反应步骤1. 原料准备:将乙腈、甲苯、氢氧化钠、乙腈(AA)丙烯和异丁烯按一定比例称量好。
2. 反应装置准备:将反应釜和蒸馏塔连接好。
将原料倒入反应釜中并密封好,开始升温。
3. 反应过程:首先将乙腈加入到反应釜中,升温至60摄氏度,加入适量的氢氧化钠。
随后加入甲苯,持续搅拌并控制温度。
4. 分离过程:反应完成后,待反应液冷却至室温后,进行离心分离,得到丁二烯提取液。
5. 再生过程:将丁二烯提取液放入真空干燥器中进行再生,得到最终产品丁二烯。
6. 质量检验:对得到的丁二烯产品进行质量检验,确保产品符合相关标准。
三、流程优化1. 条件优化:通过实验和调整反应条件,如温度、压力、反应时间等,优化反应过程,提高产量和纯度。
2. 催化剂优化:通过引入适量的催化剂,如铁、钴等,可以提高反应速度和选择性,减少副产物的生成。
3. 工艺改进:通过改变反应装置或流程,如增加冷却器、提高反应釜的密封性等,可以提高反应效率和稳定性。
4. 自动化控制:引入自动化控制系统,实时监测反应条件,调整参数,提高生产效率和产品质量。
四、工艺优势1. 乙腈法抽提丁二烯工艺简单易行,原料易得,成本低廉。
2. 产品纯度高,收率稳定,可以满足不同领域的需求。
3. 反应条件温和,反应过程安全可靠,操作简便。
4. 通过流程优化和工艺改进,可以进一步提高产量和质量,增强竞争力。
以上就是乙腈法抽提丁二烯工艺流程的详细介绍,希望能对相关领域的研究和生产工作有所帮助。
丁二烯抽提工艺方法的比较与选择

丁二烯抽提工艺方法的比较与选择摘要:丁二烯的加工利用水平和化工利用技术的发展对国家合成橡胶工业生产的发展有着重要影响。
丁二烯的生产可分为乙腈法、二甲基甲酰胺法和N甲基吡咯烷酮法三种。
不论是哪种溶剂,抽提工艺一般都采用两段萃取精馏,即先用溶剂萃取丁二烯及炔烃,把它们与丁烷,丁烯馏分分开,再用同一溶剂在炔烃萃取精馏塔中萃取掉炔烃,得到丁二烯馏分,丁二烯馏分脱除轻重组分后,便得到丁二烯。
三种方法都有各自的特点,在选择生产丁二烯的方法时,要详细比较各自的优缺点,选择出最适合的工艺方法。
关键词:丁二烯工艺;溶剂;抽提1丁二烯的简介丁二烯,通常是指1,3-丁二烯,又称乙烯基乙烯,分子式C4H6,无色气体。
熔点108.9℃,沸点4.41℃,微溶于水和醇,易溶于苯、甲苯、氯仿、等有机溶剂。
丁二烯在常温常压下为无色而略带大蒜味的气体,易液化,易燃,聚合。
丁二烯具有麻醉和刺激作用,可能引起遗传缺陷,可致癌。
丁二烯是碳四馏分中最重要的组分,是石油化工的基本原料之一,在石油化工烯烃原料中的地位仅次于乙烯和丙烯,世界丁二烯主要用于合成橡胶以及ABS树脂等。
2丁二烯的生产方法我国丁二烯的生产经历了酒精接触分解、丁烯或丁烷氧化脱氢和蒸气裂解制乙烯联产C4抽提分离三个发展阶段。
C4抽提分离这种方法价格低廉,经济上占优势,是目前世界上丁二烯的主要来源。
只有少数一些丁烷、丁烯资源丰富的国家采用脱氢法。
目前我国正在运行的丁二烯生产装置,绝大多数都是随着乙烯工业的发展而逐步配套建设起来的[1]。
2.1乙腈法乙腈法(ACN法)乙腈法以含水10%左右的乙腈为溶剂,由两段萃取精馏、两段普通精馏、和溶剂回收等工艺单元组成。
原料裂解碳四第一萃取精馏塔,与塔顶来的乙腈接触。
丁烷、丁烯、反丁烯-2等从塔顶馏出,塔底含丁二烯和重组分的乙腈溶液由釜液泵送至汽提塔将烃类组分从乙腈溶液中汽提出来。
汽提塔中部炔烃浓度最高,侧线采出送入炔烃闪蒸塔汽提塔釜液由汽提塔釜液泵打出,作为循环溶剂。
中国丁二烯合成常用方法

中国丁二烯合成常用方法引言:丁二烯是一种重要的化工原料,广泛应用于橡胶、塑料、合成橡胶和合成纤维等领域。
在中国,丁二烯的合成方法主要有烷烃脱氢法和烯烃裂解法两种常用方法。
一、烷烃脱氢法烷烃脱氢法是通过在适当的催化剂存在下,使烷烃发生脱氢反应生成烯烃。
这种方法适用于丁烷、异丁烷和异戊烷等烷烃的合成。
1. 催化剂选择常用的催化剂有铂、钯、铑、铑铂等催化剂。
铂催化剂具有活性高、选择性好的特点,是丁二烯合成中最常用的催化剂。
2. 反应条件烷烃脱氢反应通常在高温和高压下进行。
以丁烷为例,反应温度在400-500摄氏度之间,压力在1-5兆帕之间。
同时,还需要添加适量的氢气作为反应助剂,提高反应的效率和选择性。
3. 工艺优化为了提高丁二烯的产率和选择性,可以通过调节反应温度、压力、氢气的添加量和催化剂的选择等方法进行工艺优化。
此外,还可以通过改变反应体系的配比和添加助剂等措施来改善反应的效果。
二、烯烃裂解法烯烃裂解法是将较长的烯烃分子裂解成较短的烯烃分子的方法。
这种方法适用于丁烯、戊烯等烯烃的合成。
1. 催化剂选择常用的催化剂有氧化铝、硅铝酸等。
氧化铝催化剂具有活性高、稳定性好的特点,是丁二烯合成中常用的催化剂之一。
2. 反应条件烯烃裂解反应通常在高温和低压下进行。
以丁烯为例,反应温度在500-600摄氏度之间,压力在0.1-0.5兆帕之间。
同时,还需要添加适量的惰性气体(如氮气)作为反应助剂,稀释反应体系,提高反应的选择性和稳定性。
3. 工艺优化为了提高丁二烯的产率和选择性,可以通过调节反应温度、压力、惰性气体的添加量和催化剂的选择等方法进行工艺优化。
此外,还可以通过改变反应体系的配比和添加助剂等措施来改善反应的效果。
总结:中国丁二烯的合成主要采用烷烃脱氢法和烯烃裂解法两种常用方法。
烷烃脱氢法适用于丁烷、异丁烷和异戊烷等烷烃的合成,而烯烃裂解法适用于丁烯、戊烯等烯烃的合成。
在实际应用中,可以根据具体需求选择合适的方法,并通过工艺优化来提高丁二烯的产率和选择性。
丁二烯胶乳工艺

丁二烯胶乳工艺丁二烯胶乳工艺简介•丁二烯胶乳工艺是一种常见的合成橡胶的工艺方法。
•丁二烯是一种重要的合成橡胶原料,具有优异的物理性质和化学稳定性。
•通过丁二烯胶乳工艺,可以生产出高质量的橡胶制品。
工艺流程1.原料准备–将丁二烯和一定比例的溶剂混合,并加入适量的稳定剂和促进剂。
2.聚合反应–将混合物加热至一定温度,触发聚合反应。
–聚合反应会引起丁二烯分子间的交联,形成聚合物链。
3.过滤和清洗–将反应液过滤,去除杂质。
–用溶剂进行清洗,去除未反应的物质。
4.调整胶乳性能–加入助剂,如防老化剂、增稠剂等,调整胶乳的性能。
5.包装和储存–将胶乳装入适当的容器中,进行包装。
–在合适的环境条件下,储存胶乳,以保持其品质稳定。
优势和应用•丁二烯胶乳工艺具有以下优势:–反应条件温和,适用于大规模生产。
–产品质量稳定,具有良好的物理性能。
–可通过调整工艺参数和添加剂来改变胶乳的性能。
•丁二烯胶乳广泛应用于以下领域:–汽车制造:制作车胎、密封件等橡胶制品。
–工程建设:用于防水、防震等工程橡胶制品。
–医疗保健:制作医用手套、乳胶制品等。
发展趋势•随着科学技术的不断进步,丁二烯胶乳工艺也在不断发展。
•新型催化剂的开发,可以提高聚合反应的速率和效率。
•新型添加剂的研发,可以改善胶乳的耐热性、耐寒性等性能。
•绿色环保的要求,推动了丁二烯胶乳工艺向更加环保的方向发展。
结论•丁二烯胶乳工艺是一种常见且重要的橡胶制品生产方法。
•通过优化工艺流程和添加剂的选择,可以获得高质量的丁二烯胶乳产品。
•随着技术的进步和环境要求的提高,丁二烯胶乳工艺将不断发展,并在各个领域发挥更大的作用。
挑战和解决方案•丁二烯胶乳工艺在应用过程中面临以下挑战:–聚合反应的温度控制:过高或过低的温度都会影响聚合反应的速率和产物品质。
通过合理调整反应温度和加热设备,可以实现温度的精确控制。
–反应液的升贴水性:丁二烯和溶剂之间存在升贴水性差异,会影响橡胶颗粒的稳定性和聚合反应的进行。
丁二烯的生产工艺
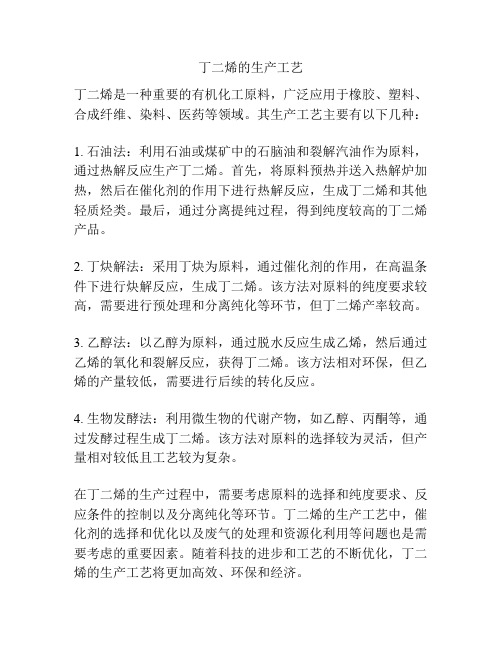
丁二烯的生产工艺
丁二烯是一种重要的有机化工原料,广泛应用于橡胶、塑料、合成纤维、染料、医药等领域。
其生产工艺主要有以下几种:
1. 石油法:利用石油或煤矿中的石脑油和裂解汽油作为原料,通过热解反应生产丁二烯。
首先,将原料预热并送入热解炉加热,然后在催化剂的作用下进行热解反应,生成丁二烯和其他轻质烃类。
最后,通过分离提纯过程,得到纯度较高的丁二烯产品。
2. 丁炔解法:采用丁炔为原料,通过催化剂的作用,在高温条件下进行炔解反应,生成丁二烯。
该方法对原料的纯度要求较高,需要进行预处理和分离纯化等环节,但丁二烯产率较高。
3. 乙醇法:以乙醇为原料,通过脱水反应生成乙烯,然后通过乙烯的氧化和裂解反应,获得丁二烯。
该方法相对环保,但乙烯的产量较低,需要进行后续的转化反应。
4. 生物发酵法:利用微生物的代谢产物,如乙醇、丙酮等,通过发酵过程生成丁二烯。
该方法对原料的选择较为灵活,但产量相对较低且工艺较为复杂。
在丁二烯的生产过程中,需要考虑原料的选择和纯度要求、反应条件的控制以及分离纯化等环节。
丁二烯的生产工艺中,催化剂的选择和优化以及废气的处理和资源化利用等问题也是需要考虑的重要因素。
随着科技的进步和工艺的不断优化,丁二烯的生产工艺将更加高效、环保和经济。
丁烯氧化脱氢制丁二烯技术研究
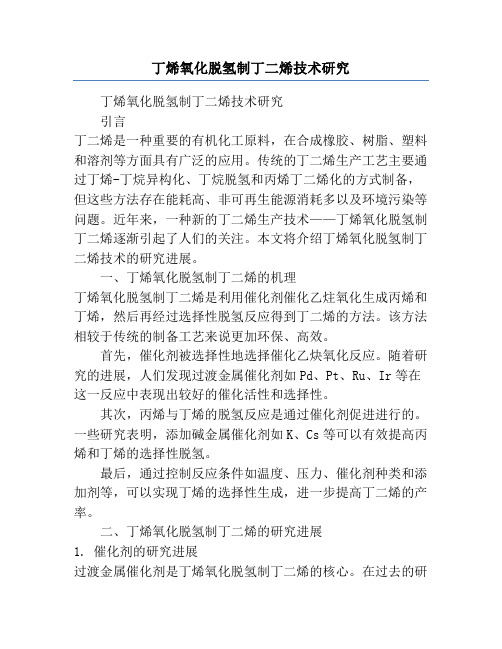
丁烯氧化脱氢制丁二烯技术研究丁烯氧化脱氢制丁二烯技术研究引言丁二烯是一种重要的有机化工原料,在合成橡胶、树脂、塑料和溶剂等方面具有广泛的应用。
传统的丁二烯生产工艺主要通过丁烯-丁烷异构化、丁烷脱氢和丙烯丁二烯化的方式制备,但这些方法存在能耗高、非可再生能源消耗多以及环境污染等问题。
近年来,一种新的丁二烯生产技术——丁烯氧化脱氢制丁二烯逐渐引起了人们的关注。
本文将介绍丁烯氧化脱氢制丁二烯技术的研究进展。
一、丁烯氧化脱氢制丁二烯的机理丁烯氧化脱氢制丁二烯是利用催化剂催化乙炷氧化生成丙烯和丁烯,然后再经过选择性脱氢反应得到丁二烯的方法。
该方法相较于传统的制备工艺来说更加环保、高效。
首先,催化剂被选择性地选择催化乙炔氧化反应。
随着研究的进展,人们发现过渡金属催化剂如Pd、Pt、Ru、Ir等在这一反应中表现出较好的催化活性和选择性。
其次,丙烯与丁烯的脱氢反应是通过催化剂促进进行的。
一些研究表明,添加碱金属催化剂如K、Cs等可以有效提高丙烯和丁烯的选择性脱氢。
最后,通过控制反应条件如温度、压力、催化剂种类和添加剂等,可以实现丁烯的选择性生成,进一步提高丁二烯的产率。
二、丁烯氧化脱氢制丁二烯的研究进展1. 催化剂的研究进展过渡金属催化剂是丁烯氧化脱氢制丁二烯的核心。
在过去的研究中,人们广泛探索了不同催化剂对该反应的催化活性和选择性的影响。
研究发现,Pd基催化剂表现出较好的活性和选择性,因此被认为是最有潜力的催化剂之一。
此外,制备高分散度催化剂也成为了研究的重点,以提高反应的效率和选择性。
2. 添加剂的研究进展在丁烯氧化脱氢制丁二烯的过程中,添加剂的引入对催化剂的活性和选择性起到了重要的作用。
研究表明,碱金属催化剂的引入可以提高丙烯和丁烯的选择性脱氢。
此外,添加一些促进剂如硫、氯等也能够改善催化剂的性能。
3. 反应条件的研究进展反应条件对丁烯氧化脱氢制丁二烯的反应效果具有重要影响。
温度、压力、反应物比例和催化剂用量等参数的优化可以提高反应的选择性和产率。
丁二烯生产技术现状及发展方向

丁二烯生产技术现状及发展方向1.丁烯氧化脱氢制丁二烯技术1.1反应原理在进行丁烯氧化脱氢生产丁二烯过程中,会释放出大量的热量,此时可以借助系统的提纯处理来获取丁二烯,丁烯完全氧化后可以得到一氧化碳、二氧化碳和水。
但是在实际反应过程中受多方面因素影响,从而导致氧化反应发生一系列的变化,最终得到多种含氧化合物。
氧化降解后会生成丙酮、甲醛等氧化合物,氧化生成四个碳原子的含氧化合物,如丁烯醛、丁酮等。
在进行深度氧化反应过程中,脱氢后可以得到乙烯基乙炔等产物,然后通过一系列的氧化后可以得到二氧化碳、一氧化碳和水等產物,该阶段所生成的产物与副产物又能够通过凝结聚合形成新的产物。
1.2工艺流程丁烯氧化脱氢制丁二烯的工艺生产流程主要包括油吸收和氧化脱氢反应两个单元。
其中氧化脱氢反应单元又能够细分为反应、水冷以及洗醛三个主要环节。
图一所示为氧化脱氢反应单元的主要流程示意图。
在反应器内,丁烯与空气在催化剂的作用下发生反应,从而生成丁二烯以及醛酸等一系列副产物。
由于整个反应为放热反应,为了避免放热温度过高对反应温度造成影响,需要在反应器内注入大量蒸汽,从而有效控制反应温度,以此来有效延长催化剂的操作周期。
之后对反应器生成的产物借助水冷塔进行冷却处理,将复合产物中的酸成分分离,再通过生成器压缩机对水冷后生成气进行加压,在洗醛塔中加压水洗清除产物中的醛和酮成分,最后将生成气引入油吸收系统进行下一个生成环节。
图二所示为油吸收单元的基本操作流程,通过油吸收单元可以有效分离和剔除生成气中的C4烃。
通常情况下,油吸收单元需要先进行吸收油吸收,随后开展重吸收油吸收,这样可以有效地减少C4以及吸收油的损耗。
在吸收塔中洗醛塔顶产生的C4物料与吸收油进行逆流接触,而C4相关物料能够溶于吸收油,从而在解析塔中被吸收油分解提取。
塔顶的C4物料能够直接参与到丁二烯抽提单元,该过程中塔釜的吸收油能够循环使用,并且还可以与尾气混合在一起进入重油吸收系统并进行二次抽取和循环利用,进一步对尾气中的C4物料进行收集和提取,并回收,从而有效提高吸收油的再利用效率。
NMP法制丁二烯工艺介绍
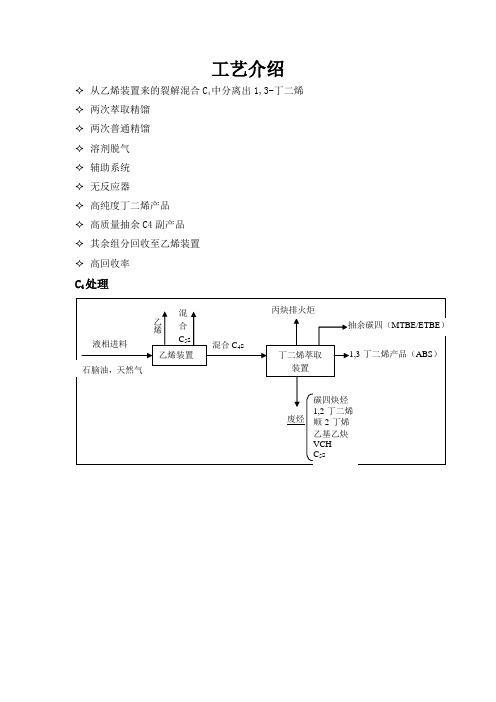
工艺介绍
✧从乙烯装置来的裂解混合C4中分离出1,3-丁二烯✧两次萃取精馏
✧两次普通精馏
✧溶剂脱气
✧辅助系统
✧无反应器
✧高纯度丁二烯产品
✧高质量抽余C4副产品
✧其余组分回收至乙烯装置
✧高回收率
C4处理
分离单元
⏹萃取精馏
丁烯、丁烷和C4烃类的沸点与1,3-丁二烯非常接近
普通精馏难以分离
在NMP溶剂中与1,3-丁二烯组分的溶解度差别较大
⏹普通精馏
1,2-丁二烯、丙炔和C5烃类的沸点远高于1,3-丁二烯
粗丁二烯可通过普通精馏分离
NMP溶剂工艺
⏹溶剂是丁二烯萃取的关键
⏹N MP溶剂是最好的选择,原因如下:
⏹具有很高的选择性,可以有效地降低操作成本和能耗,提高产量
⏹具有很好的环保效果,对环境影响最小
⏹低毒无致癌物
⏹稳定性好,无溶剂分解的副产物生成。
⏹无腐蚀性
⏹安全的溶剂。
NMP法丁二烯抽提生产工艺分析
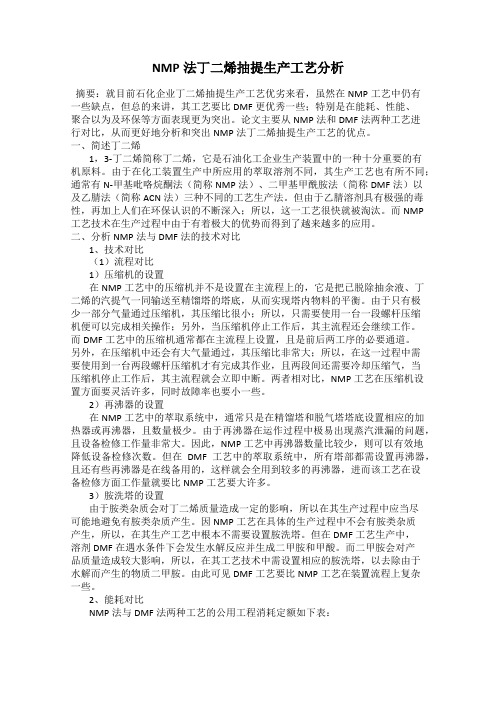
NMP法丁二烯抽提生产工艺分析摘要:就目前石化企业丁二烯抽提生产工艺优劣来看,虽然在NMP工艺中仍有一些缺点,但总的来讲,其工艺要比DMF更优秀一些;特别是在能耗、性能、聚合以为及环保等方面表现更为突出。
论文主要从NMP法和DMF法两种工艺进行对比,从而更好地分析和突出NMP法丁二烯抽提生产工艺的优点。
一、简述丁二烯1,3-丁二烯简称丁二烯,它是石油化工企业生产装置中的一种十分重要的有机原料。
由于在化工装置生产中所应用的萃取溶剂不同,其生产工艺也有所不同;通常有N-甲基吡咯烷酮法(简称NMP法)、二甲基甲酰胺法(简称DMF法)以及乙腈法(简称ACN法)三种不同的工艺生产法。
但由于乙腈溶剂具有极强的毒性,再加上人们在环保认识的不断深入;所以,这一工艺很快就被淘汰。
而NMP工艺技术在生产过程中由于有着极大的优势而得到了越来越多的应用。
二、分析NMP法与DMF法的技术对比1、技术对比(1)流程对比1)压缩机的设置在NMP工艺中的压缩机并不是设置在主流程上的,它是把已脱除抽余液、丁二烯的汽提气一同输送至精馏塔的塔底,从而实现塔内物料的平衡。
由于只有极少一部分气量通过压缩机,其压缩比很小;所以,只需要使用一台一段螺杆压缩机便可以完成相关操作;另外,当压缩机停止工作后,其主流程还会继续工作。
而DMF工艺中的压缩机通常都在主流程上设置,且是前后两工序的必要通道。
另外,在压缩机中还会有大气量通过,其压缩比非常大;所以,在这一过程中需要使用到一台两段螺杆压缩机才有完成其作业,且两段间还需要冷却压缩气,当压缩机停止工作后,其主流程就会立即中断。
两者相对比,NMP工艺在压缩机设置方面要灵活许多,同时故障率也要小一些。
2)再沸器的设置在NMP工艺中的萃取系统中,通常只是在精馏塔和脱气塔塔底设置相应的加热器或再沸器,且数量极少。
由于再沸器在运作过程中极易出现蒸汽泄漏的问题,且设备检修工作量非常大。
因此,NMP工艺中再沸器数量比较少,则可以有效地降低设备检修次数。
已腈法制丁二烯的工艺流程aspen的步骤
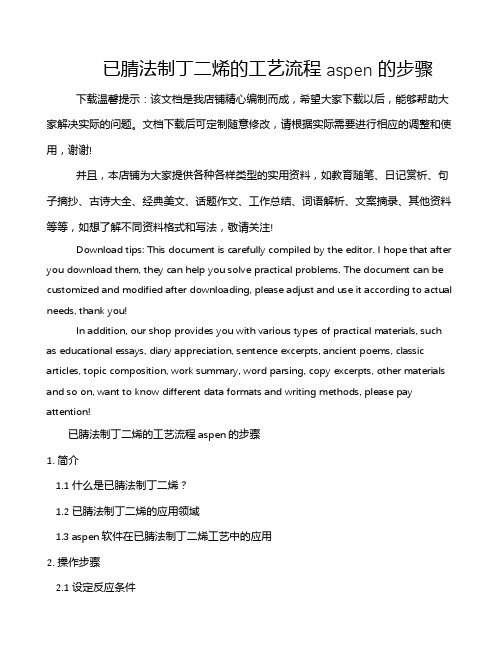
已腈法制丁二烯的工艺流程aspen的步骤下载温馨提示:该文档是我店铺精心编制而成,希望大家下载以后,能够帮助大家解决实际的问题。
文档下载后可定制随意修改,请根据实际需要进行相应的调整和使用,谢谢!并且,本店铺为大家提供各种各样类型的实用资料,如教育随笔、日记赏析、句子摘抄、古诗大全、经典美文、话题作文、工作总结、词语解析、文案摘录、其他资料等等,如想了解不同资料格式和写法,敬请关注!Download tips: This document is carefully compiled by the editor. I hope that after you download them, they can help you solve practical problems. The document can be customized and modified after downloading, please adjust and use it according to actual needs, thank you!In addition, our shop provides you with various types of practical materials, such as educational essays, diary appreciation, sentence excerpts, ancient poems, classic articles, topic composition, work summary, word parsing, copy excerpts, other materials and so on, want to know different data formats and writing methods, please pay attention!已腈法制丁二烯的工艺流程aspen的步骤1. 简介1.1 什么是已腈法制丁二烯?1.2 已腈法制丁二烯的应用领域1.3 aspen软件在已腈法制丁二烯工艺中的应用2. 操作步骤2.1 设定反应条件2.1.1 确定反应温度和压力2.1.2 确定催化剂种类和用量2.2 进料及配料2.2.1 确保进料质量和纯度2.2.2 配料准确称量2.3 反应过程2.3.1 控制反应温度2.3.2 监测反应进程2.3.3 确保反应过程稳定2.4 分离纯化2.4.1 采用合适的分离技术2.4.2 确保产品纯度和产率2.5 产品收集2.5.1 将产品从反应器中收集2.5.2 进行相应的储存和处理3. 操作细节说明3.1 温度和压力的控制3.1.1 在何种温度范围内反应最为有效 3.1.2 最佳压力条件是多少3.2 催化剂的选择3.2.1 各种催化剂的特点和适用性比较3.2.2 如何确定最合适的催化剂3.3 进料与配料3.3.1 进料的来源与质量要求3.3.2 配料的准确性对反应结果的影响3.4 分离纯化技术3.4.1 蒸馏法、结晶法等分离技术的特点比较3.4.2 如何选择最适合的分离技术3.5 产品收集处理3.5.1 产品的处理流程及注意事项3.5.2 如何确保产品的质量和保存期限4. 实验验证及结果分析4.1 进行实验验证4.1.1 设计实验方案4.1.2 进行实验操作4.2 结果分析4.2.1 分析实验结果与理论值的差异4.2.2 确认已腈法制丁二烯工艺的可行性5. 结论与展望5.1 对已腈法制丁二烯工艺流程aspen的步骤进行总结5.2 展望其在未来的应用前景及改进空间本文通过详细介绍已腈法制丁二烯的工艺流程aspen的步骤,从设定反应条件、进料及配料、反应过程、分离纯化、产品收集等方面进行了系统分析和说明,同时结合实验验证及结果分析,总结出该工艺流程的操作细节和关键环节,为相关领域的研究和生产提供了重要参考。
丁二烯储罐工艺

丁二烯储罐工艺丁二烯,这可是个神奇的家伙呀!丁二烯储罐工艺,那更是一门高深的学问呢!你知道吗,丁二烯就像是一个有点小脾气的精灵,存储它可真不是一件简单的事儿。
丁二烯储罐工艺涉及到好多方面呢。
从储罐的设计开始,就像是给这个小脾气精灵打造一个舒适的家。
这个家要足够坚固,能抵御各种外界的影响,还要有合适的温度和压力控制,就好像我们给自己的房间调节适宜的温度一样重要。
再说说丁二烯的储存条件,那可真是苛刻得很呢!温度不能太高也不能太低,压力也要恰到好处。
这就好像照顾一个娇贵的宝贝,稍有不慎就可能出问题。
这难道不像是在走钢丝吗?稍有偏差可能就会引发大麻烦。
还有啊,丁二烯的输送过程也不简单。
管道要畅通无阻,不能有任何泄漏。
这就像是人体内的血管,必须保证血液能够顺畅地流动。
如果管道出现问题,那可不得了,就如同人的血管堵塞一样危险。
丁二烯储罐工艺的安全措施更是重中之重。
毕竟丁二烯可不是好惹的,稍有不慎就可能引发大事故。
这就好像我们出门必须要带好钥匙一样重要,安全措施就是保障一切顺利进行的关键。
我们要时刻保持警惕,不能有丝毫的松懈,对吧?在整个丁二烯储罐工艺中,每一个环节都紧密相连,缺一不可。
这难道不像一场精彩的接力赛吗?每一棒都要跑得又快又稳,才能取得最终的胜利。
我们对待丁二烯储罐工艺也要像运动员对待比赛一样认真、专注。
丁二烯储罐工艺的重要性不言而喻。
它关系到生产的顺利进行,关系到人们的安全和环境的保护。
我们不能轻视它,而要以高度的责任感和专业精神去对待它。
只有这样,我们才能确保丁二烯这个小脾气精灵在我们的掌控之中乖乖听话,为我们的生产和生活服务。
所以说,丁二烯储罐工艺真的是非常非常重要啊,我们一定要重视起来呀!。
- 1、下载文档前请自行甄别文档内容的完整性,平台不提供额外的编辑、内容补充、找答案等附加服务。
- 2、"仅部分预览"的文档,不可在线预览部分如存在完整性等问题,可反馈申请退款(可完整预览的文档不适用该条件!)。
- 3、如文档侵犯您的权益,请联系客服反馈,我们会尽快为您处理(人工客服工作时间:9:00-18:30)。
一、反应原理:
1、主反应
一、反应原理:
2、副反应
一、反应原理:
一、反应原理:
3、反应动力学:
二、工艺条件:
1、反应温度:流化床H-198:593~603K;固定床B-02:603~843K 反应温度在一定范围内升高,丁烯转化率和丁二烯收率随之增加,而一氧
化碳和二氧化碳生成率之和仅略有增加,丁二烯选择性无明显变化。 温度过高,则深度氧化反应加剧,丁二烯收率下降,还会使催化剂失活;
工艺流程:
二、碳四馏分抽提丁二烯:
无论是裂解气深冷分离得到的碳四馏分,还是经丁烯氧化脱氢 得到的粗丁二烯,均是以碳四各组分为主的烃类混合物,主要含 有丁烷、正丁烯、异丁烯、丁二烯,它们都是重要的有机化工原 料。
C4的分离与C2、C3馏分相比,其最大的特点是各组分之间的 相对挥发度很小,使分离变得更加困难,采用普通精馏方法在通 常条件下将其分离是不可能的。为此工业生产中常用在碳四馏分 中加入一种溶剂进行萃取的特殊精馏来实现对C4馏分的分离。
第五章 碳四系列产品
从油田气、炼厂气和烃类裂解制乙烯的副产品中都可获得碳 四馏分。碳四系列的基本有机化工产品主要有丁二烯、顺丁烯二 酸酐、聚丁烯、二异丁烯、仲丁醇、甲乙酮等,它们是有机化学 工业的重要原料。
第一节 丁二烯的生产
丁二烯分子中具有共轭双键,化学性质活泼,能与氢、卤素、卤化氢 发生加成反应,容易发生自身聚合反应,也容易与其它不饱和化合物发 生共聚反应,是高分子材料工业的重要单体,也是有机合成的原料。其 生产方法有以下几种 1、酒精法生产丁二烯:消耗大量酒精且流程长,严重限制丁二烯发展 2、C4抽提丁二烯: 由烃类热裂解所得C4中加入某种溶剂使丁二烯分离出来。此法虽经济 简单,但数量上难以满足丁二烯发展需要。 3、丁烯催化脱氢生产丁二烯:(扩大丁二烯来源)
作业:P189 5、7
温度过低,则反应速度下降,转化率下降,设备生产能力降低。
工艺条件:
2、反应压力: 压力的增加虽有利
于丁烯分压提高而 加快反应速度,但 由于主反应级数低 于副反应,所以压 力升高更有利于副 反应的进行。工业 生产中操作压力的 确定,主要考虑流 体输送及过程压降 问题。
工艺条件:
3、丁烯空速: 固定床反应器(B-02):Sv↓,停留时间↑,转化率↑,二次反应加剧热
(一)基本原理:(萃取精馏)
分离时需向精馏系统中加入一种新的选择性溶剂(萃取剂),
这种溶剂对精馏系统中的某一组分具有较大的溶解能力,而对
其它组分溶解能力较小;其结果使分子间的距离加大,分子间
作用力发生改变,被分离组分之间的相对挥发度差值增大,使
分离变得容易进行。
萃取剂的选择考虑因素有很多,主要取决于其经济性和选
择性的大小。工业上常用的萃取剂有乙腈、糠醛、二甲基甲酰
胺、N-甲基吡咯烷酮等。
二、工艺条件:
1、溶剂的恒定浓度:是影响萃取精馏的主要因素,78~ 83%(质)
由于所用溶剂的相对挥发度比欲处理物料低得多,且
用量很大,因此在塔内从加料板至灵敏板,溶剂的浓度基
本维持在一个恒定的浓度值,此浓度称为溶剂恒定浓度,
工艺条件:
5、水烯比:固定床12~13,流化床9~12 水蒸汽作为稀释剂和热载体,具有调节反应物与产物分压、带出反应热、
避免催化剂过热的功能,水蒸汽的加入还具有缩小丁烯爆炸极限,清除 催化剂表面积炭以延长催化剂使用寿命的作用。但过量水会造成反应器 能力降低。
三、工艺流程:
该流程可分为有换热设备的流化床反应器工艺流程和绝热式固定床反应器工 艺流程两种。
工艺条件:
3、溶剂含水量:6~10%
溶剂中加入适量水可提高组分间的相对挥发度,降低溶液
的沸点,减少蒸汽的消耗,避免丁二烯在塔内的热聚,有利于
分离容易进行。但水含量的增加会使烃类在溶剂中溶解度降低,
为避免塔内分层现象的出现而破坏萃取效果需要控制适宜的含
水量。
4、回流比:略大于最小回流比,D=3.5
简称溶剂浓度。
溶剂浓度的提高,相对挥发度增加,选择性升高,
分离容易进行。但过高则设备投资和操作费用增加,经济
效益降低。
工艺条件:
2、溶剂的温度: 其主要影响塔内温度分布、气液负荷和操
作稳定性。通常溶剂的进料温度高于塔顶温度, 而低于进料板温度。若过高,易引起溶剂损失 的增加,塔顶丁二烯含量增加;若过低则造成 C4在塔内大量积累,导致塔釜产品不合格,严 重时,甚至会造成液相超负荷而使操作无法进 行。
在萃取精馏中,D↑,溶剂浓度↓,各组分的相对挥发度
↓,分离效果↓。回流液的作用只是为了维持各塔板上的物料
平衡,或者说是保证相邻板之间形成浓度差,稳定精馏操作。
三、工艺流程:
1、乙腈法碳四抽提丁二烯:
工艺流程:
2、二甲基甲酰胺法抽提丁二烯:(DMF) 该工艺由丁二烯萃取精馏、炔烃萃取精馏和普通精馏三部分组成。
效应↑,容易造成超温,严重时使催化剂烧毁,同时反应效果变差。一般 Sv=300~500h-1。 流化床反应器(H-198):Sv与流化质量有直接关系。Sv↑,线速度↑, 流化质量↑,避免催化剂局部聚集和过热,可保证催化剂活性和选择性。但空 速过高,则会造成催化剂带出量增加,造成催化剂的损失;过低则副反应增加, 选择性下降。一般空速控制在200~300h-1。
3、催化剂: 目前采用催化剂主要有两大类: 磷钼铋系:Bi-Mo氧化物-碱金属和铁族元素-SiO2(或 Al2O3)。其具有使用周期长,性能稳定,选择性高等特点, 但存在着明显放大效应,其收率与选择性明显低于中试条件, 含氧化合物高,丁烯定额消耗高,三废处理困难。 铁 系:克服了上述缺点,在技术经济指标都优于前者。主要 代表性催化剂是H-198和B-02尖晶石铁系催化剂。
工艺条件:
4、氧烯摩尔比:0.65~0.7
工业上一般采用的氧化剂是空气。氧烯比小,即氧气量不足将限制
丁烯的转化,促使催化剂中晶格氧的消耗,引起活性下降,大大降低转
ቤተ መጻሕፍቲ ባይዱ
化率和选择性;缺氧还会使催化剂表面积炭增快,寿命缩短。氧烯比过
高又将导致丁烯的深度氧化等副反应增加,增加后处理过程的负担,还
会造成爆炸的危险。工业上对氧烯比的控制是尾气中氧含量在1~2% 为宜。