反应器数据表(全)
乙醇脱水反应实验报告

乙醇脱水反应研究实验一、实验目的1.掌握乙醇脱水实验的反应过程和反应机理、特点,了解针对不同目的产物的反应条件对正、付反应的影响规律和生成的过程。
2.学习气固相管式催化反应器的构造、原理和使用方法,学习反应器正常操作和安装,掌握催化剂评价的一般方法和获得适宜工艺条件的研究步骤和方法。
3.学习动态控制仪表的使用,如何设定温度和加热电流大小,怎样控制床层温度分布。
4.学习气体在线分析的方法和定性、定量分析,学习如何手动进样分析液体成分。
了解气相色谱的原理和构造,掌握色谱的正常使用和分析条件选择。
5.学习微量泵和蠕动泵的原理和使用方法,学会使用湿式流量计测量流体流量。
二、实验仪器和药品及装置图乙醇脱水固反应器,气相色谱及计算机数据采集和处理系统,精密微量液体泵,蠕动泵。
ZSM-5型分子筛乙醇脱水催化剂,分析纯乙醇,蒸馏水。
三、实验原理乙醇脱水生成乙烯和乙醚,是一个吸热、分子数增不变的可逆反应。
提高反应温度、降低反应压力,都能提高反应转化率。
乙醇脱水可生成乙烯和乙醚,但高温有利于乙烯的生在,较低温度时主要生成乙醚,有人解释这大概是因为反应过程中生成的碳正离子比较活泼,尤其在高温,它的存在寿命更短,来不及与乙醇相遇时已经失去质子变成乙烯.而在较低温度时,碳正离子存在时间长些,与乙醇分子相遇的机率增多,生成乙醚。
有人认为在生成产物的决定步骤中,生成乙烯要断裂C—H 键,需要的活化能较高,所以要在高温才有乙烯的生成。
乙醇在催化剂存在下受热发生脱水反应,既可分子内脱水生成乙烯,也可分子间脱水生成乙醚。
本实验采用ZSM-5分子筛为催化剂,在固定床反应器中进行乙醇脱水反应研究,通过改变反应的进料速度,可以得到不同反应条件下的实验数据,通过对气体和液体产物的分析,可以得到在一定反应温度条件下的反应最佳工艺条件和动力学方程。
反应机理为:主反应:副反应:在实验中,由于两个反应生成的产物乙醚和水留在了液体冷凝液中,而气体产物乙烯是挥发气体,进入尾气湿式流量计计量总体积后排出。
艾默生 KTM EB1 系列分体式浮动球阀 数据表

KTM EB1 系列分体式浮动球阀一种多功能球阀,有低逸散、无空腔、空腔泄压、低温、高压和高温软阀座和金属座设计,适用于从-196˚C (-320˚F) 至 500˚C (932˚F)的各种应用。
特点• 符合 ASME B16.34、API 608、API 6D 和 ISO 17292 标准• 软密封双向零泄漏• 阀门逸散性排放第三方认证,符合ISO 15848-1 Class B 和 API 641标准• 执行机构安装面符合ISO 5211• 纯白色E 阀座(PTFE/PFA 聚合物)可避免对产品的污染• 两片式阀体主动式对齐• 通过 API 607 第6版和 ISO 10497 第3版认证的防火测试• PTFE 轴承和填料环可降低扭矩和减少磨损• 更小的操作扭矩使操作简便并降低执行机构成本• 主动式阀位指示• 防喷出阀杆• 材料符合NACE MR0175/ISO 15156或MR0103标准,可根据要求进行追踪• 可提供锁定设备• 静电接地装置• 在ISO 9001认证的质量系统下生产• 可根据要求提供符合 PED 2014/68/EU 标志• 除了标准的E 阀座之外,还有各种阀座类型可供选择。
每种阀座选项都满足宽泛的性能标准,以适应各种应用。
- PTFE/PFA 共聚物 E 阀座作为标准* - PEEK 阀座(选配)- Gratite ® 石墨阀座(选配) - Metaltite ®阀座(选配) - NoFill ® 无空腔(选配) *请参考压力/温度额定值一般应用化工、石化、纸浆和造纸、反应性单体、石油和天然气生产、蒸汽、热气、有毒和致命、防火安全和可燃物等选配• 阀杆延长件• 用于低温、氧气和真空工况• 特殊喷涂• 无损探伤测试选项 - X 射线探伤(RT) - 着色渗透检测(PT) - 材料化学成分鉴别(PMI)技术参数型号/尺寸: 全通径DN 15 至 DN 200 (NPS ½ 至 NPS 8)缩径 DN 150 至 DN 250(NPS 6 至 NPS 10)额定压力: ASME Class 150, 300, 600,900, 1500JIS 10K, 20K (JPI 可选)温度: -29°C ~ 270°C (-20°F ~ 518°F) -196°C 至 500°C(-320°F 至 932°F)可选阀座泄漏: 零泄漏(E-阀座),符合ISO 5208 Rate A 和API 598设计特征ISO 5211标准执行机构安装法兰:符合 ISO 标准的顶法兰可以精确安装执行机构;执行机构连接螺栓与填料压盖螺栓是相对独立的;准确的对中可以减小阀门开关扭矩及内件磨损。
化学反应工程

化学反应和反应器的分类(四种): 一、 按反应系统涉及的相态分类:均相反应、非均相反应 二、 按操作方式分类:间歇操作、连续操作、半连续操作 三、 按反应器型式来分类:管式反应器(长径比大于30)、槽式反应器(高径比为1—3)、塔式反应器(高径比在3—30)四、 按传热条件分类:等温反应器、绝热反应器、非等温、非绝热反应器 化学反应工程的基本研究方法:数学模型法 反应程度/进度:II I αξn n -=()()0S R B A =++-+-s r b an I 为参与反应的任意组分I 的摩尔数,αI 为其计量系数,n I0为起始时刻组分I 的摩尔数。
转化率(关键组分A )A0A 0A A A n n n A x -==组分的起始量组分量转化了的A,00A c c c A -= ξαA0AA n x -=化学反应速率:单位反应体积内反应程度随时间的变化率。
13s m mol d d 1--⋅=tV r ξ 13AA s m mol d d 1--⋅-=-tn V r n m c c k r B A c A =- 均相反应的速率是反应物系组成、温度和压力的函数 阿累尼乌斯关系: RTE k k -=ec0c ⎪⎭⎫ ⎝⎛-=T R E k k 1ln ln 0半衰期:反应转化率达到50%所需要的时间 二级反应:0A 211kc t =停留时间又称接触时间,用于连续流动反应器,指流体微元从反应器入口到出口经历的时间。
空间时间τRV V =τ (反应器有效容积V R 与流体特征体积流率V 0之比值) 空速S V 1R 0V h 1-==τV V S (在单位时间内投入单位有效反应器容积内的物料体积)标准空速 1RNO V h -=V V S 简单混合:停留时间相同(反应程度、反应前后物料相同)的物料之间的混合 返混:停留时间不同(组成、反应程度、反应速率不同)的物料之间的混合 按返混情况不同反应器被分为以下四种类型: 1. 间歇反应器 (物料之间的简单混合,不存在返混、有搅拌、釜式、间歇操作) 反应时间()⎰⎰'-==ArR A AA00r d d x t V r x n t t 恒容条件下 ()A 0A A 1x c c -= h化简:()()⎰⎰--=-=A A0AAAA A A0r d d c c x r c r x c t F A : kmol.h -1 C A0 : kmol.m -3反应器有效容积 ()t t V V C F V '+=''='r 0RA0AR或 反应器总体积ϕR R V V '= φ:装填系数 2.平推流/活塞流反应器 PFR (不存在返混、没有搅拌、管式、连续操作)β=0⎰-==A 0A A 0A 0R d x r x c V V τ 恒容过程:⎰--==2A 1A A A 0R d c c r c V V τ ⎰-==A 0AA0A 0A R d x r x c F V τ3. 全混流反应器 CSTR (返混达最大值) β→∞()f A 1A Af 0A 0R r x x c V V --==τ 恒容过程:()f A Af A1r c c --=τ =A0R F V τ/ 0A c4.非理想流反应器 (物料返混程度介于平推流反应器及全混流反应器之间) 0<β<∞变容反应过程: 1. 膨胀因子 ()A IA ααδ-=∑ (关键组份A 的膨胀因子等于反应计量系数的代数和除以A 组分计量系数的相反数) AA0A δεy =2. 膨胀率1A A A A ===-=x x x V V V ε (A 组分的膨胀率等于物系中A 组分完全转化所引起的体积变化除以物系的初始体积。
Aspen模拟反应器模块
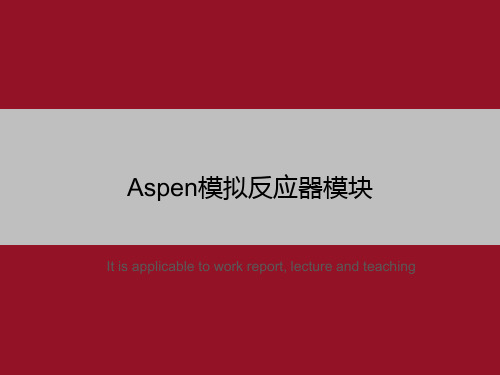
C, O2
RStoic
2 CO + O2 --> 2 CO2
IN
C + O2 --> CO2
2 C + O2 --> 2 CO
OUT
C, O2, CO, CO2
On the evening of July 24, 2021
反应器---基于物料平衡的反应Cou器rseware template
• RStoic规定屏
动力学参数: 正反应: Pre-exp. Factor(指前因子) = 1.9 x 108, Act. Energy(活化能)= 5.95 x 107 J/kmol 逆反应: Pre-exp. Factor (指前因子) = 5.0 x 107, Act. Energy (活化能)= 5.95 x 107 J/kmol 反应中每个反应物的反应都是1级 (总共为2级)。 反应发生在液相中。
• 在RStoic 反应器中,可以规定或计算参考温度、压 力下的反应热
On the evening of July 24, 2021
反应器---例题1
Courseware template
• 【例题1】对比不同类型反应器的使用
反应器条件: Temperature(温度) = 70 0C Pressure (压力)= 1 atm
On the evening of July 24, 2021
反应器---例题1
Courseware template
• 【例题1】对比不同类型反应器的使用
反应器条件: Temperature(温度) = 70 C Pressure (压力)= 1 atm
化学计量式:
Ethanol(乙醇)+ Acetic Acid(乙酸)<--> Ethyl Acetate(乙酸乙酯)+ Water(水)
IC厌氧反应器设计计算

IC厌氧反应器设计计算IC 厌氧反应器作为一种高效的厌氧处理技术,在废水处理领域得到了广泛的应用。
其独特的结构和运行原理,使其能够在处理高浓度有机废水时展现出出色的性能。
下面我们就来详细探讨一下 IC 厌氧反应器的设计计算。
一、设计基础数据在进行 IC 厌氧反应器的设计计算之前,首先需要明确一些基础数据,包括废水的水质水量、进水有机物浓度、温度、pH 值等。
这些数据将直接影响反应器的尺寸、容积和运行参数的确定。
例如,废水的流量决定了反应器的处理能力,进水有机物浓度则关系到反应器内微生物的负荷以及产气率。
一般来说,IC 厌氧反应器适用于处理高浓度有机废水,有机物浓度通常在数千毫克每升以上。
温度对厌氧反应的速率和微生物的活性有着重要影响,通常在 30 38℃之间较为适宜。
pH 值也需要控制在一定范围内,一般为 65 80 ,以保证微生物的正常生长和代谢。
二、IC 厌氧反应器的结构IC 厌氧反应器主要由两个反应区组成,即下部的第一反应区(也称流化床反应区)和上部的第二反应区(也称固液分离区)。
第一反应区是一个高负荷的反应区域,废水和颗粒污泥在此充分混合,有机物被快速降解。
这一区域通常具有较大的上升流速,以保证良好的传质效果。
第二反应区则主要用于泥水分离,使处理后的废水和污泥得以分离。
其结构相对较为简单,通常采用沉淀或过滤的方式实现泥水分离。
此外,IC 厌氧反应器还包括进水系统、出水系统、沼气收集系统和排泥系统等附属设施。
三、设计计算步骤1、确定反应器的容积负荷容积负荷是指单位容积反应器每天所能承受的有机物量,通常以千克 COD/(立方米·天)表示。
容积负荷的取值需要根据废水的水质、温度和处理要求等因素综合确定。
一般来说,对于高浓度有机废水,容积负荷可以取 10 20 千克 COD/(立方米·天)。
2、计算反应器的有效容积根据进水流量和容积负荷,可以计算出反应器的有效容积:有效容积=进水流量 ×进水有机物浓度 ÷容积负荷例如,假设进水流量为 100 立方米/天,进水有机物浓度为 10000 毫克/升(即 10 千克/立方米),容积负荷取 15 千克 COD/(立方米·天),则有效容积为:100 × 10 ÷ 15 ≈ 667(立方米)3、确定反应器的尺寸根据有效容积和反应器的高径比(一般为 2 5),可以确定反应器的直径和高度。
流化床反应器(1)

1 气固流化床设计基础数据流化床反应器的操作工艺参数为:反应温度为400 ℃,反应压力为 0.3 MPa (绝压),甲醇操作空速为 1~51h -。
MTO 成型催化剂粒径范围为50~140μm ,平均粒径为 80μm 。
颗粒密度为 1200 kg/m3,堆密度为 700 kg/m3。
甲醇在400℃下的粘度根据常压下气体粘度共线图查得为 0.021m Pa.s ,甲醇 400℃下的密度根据理想气体状态方程估算为 1.715kg/m3。
甲醇原料中水含量为 1%。
流化床催化反应器主要包括以下几个组成部分:反应器壳体尺寸、气体分布装置、换热装置、气固分离装置、内部构件、以及催化剂颗粒的加入和卸出装置。
MTO 反应为放热反应,工业装置中为避免反应器床层温度过高,需设置内取热或外取热器,由于小型固定流化床反应器尺度较小,散热效应较大,应考虑在反应器外设置加热炉保持 MTO 反应温度恒定,不必设置取热器。
我们在确定了操作条件(T :400 ℃,P :0.3 MPa )、反应器内气体原料和固体催化剂物化性质的条件下,计算了催化剂装填量、操作气速和反应器主体尺寸,并对气体分布器、气固分离装置和催化剂加卸料口的设置进行了简要介绍。
2 操作气速2.1 最小流化速度计算当流体流过颗粒床层的阻力等于床层颗粒重量时,床层中的颗粒开始流动起来,此时流体的流速称为起始流化速度,记作mf U 。
起始流化速度仅与流体和颗粒的物性有关,其计算公式如下式所示: 对于p mf ep d U R ρμ=20<的小颗粒2()1650p p mf d gU ρρμ-= (1) 对于1000p mf ep d U R ρμ=>的大颗粒1/2()[]24.5p p mf d gU ρρρ-= (2)式中: p d 为颗粒的平均粒径;.p ρρ分别为颗粒和气体的密度; μ为气体的粘度。
本流化床雷诺数:ep R <20将已知数据代入公式(1),25235()(810)(1200 1.715) 2.210/16501650(2.110)p p mf d gU m s ρρμ----⨯⨯-===⨯⨯⨯558100.0022 1.715202.110p mf ep d U R ρμ--⨯⨯⨯==<⨯ 将mf U 代入弗鲁德准数公式 2mf mf p U F d g =作为判断流化形式的依据。
sbr反应器设计计算

SBR反应器的设计计算一、设计说明经UASB处理后的废水,COD含量仍然很高,要达到排放标准,必须进一步处理,即采用好氧处理。
SBR结构简单,运行控制灵活,本设计采用4个SBR反应池,每个池子的运行周期为6h二、设计参数(一)参数选取(1)污泥负荷率Ns取值为0.13kgBOD5/(kgMLSS•d)(2)污泥浓度和SVI污泥浓度采用4000 mgMLSS/L,SVI取100(3)反应周期SBR周期采用T=6h,反应器一天内周期数n=24/6=4(4)周期内时间分配反应池数N=4进水时间:T/N=6/4=1.5h反应时间:3.0h静沉时间:1.0h排水时间:0.5h(5)周期进水量Q0= =156.25m3/s(二)设计水量水质设计水量为:Q=2500m3/d=104m3/h=0.029m3/s设计水质见下表2.3:三、设计计算(一)反应池有效容积V1=式中:n ------------ 反应器一天内周期数Q0 ------------ 周期进水量,m3/sS0 ------------ 进水BOD含量,mg/lX ------------- 污泥浓度,mgMLSS/LNs ------------- 污泥负荷率V1 = 280.45 m3(二)反应池最小水量V min =V1-Q=280.45-156.25=124.2m3(三)反应池中污泥体积Vx=SVI·MLSS·V1/106=100×4000×280.45/106=112.18 m3Vmin>Vx,合格(四)校核周期进水量周期进水量应满足下式:Q<(1-SVI·MLSS /106) ·V=(1- 100×4000 /106) ×280.45=176.46m3而Q=156.25m3<176.46m3 故符合设计要求(五)确定单座反应池的尺寸SBR有效水深取5.0m,超高0.5m,则SBR总高为5.5m,SBR的面积为280.45/5=56.09m2设SBR的长:宽=2:1则SBR的池宽为:5.5m;池长为:11.0m.SBR反应池的最低水位为: 1.97mSBR反应池污泥高度为:1.24m1.97-1.24=0.73m可见,SBR最低水位与污泥位之间的距离为0.8m,大于0.5m的缓冲层高度符合设计要求。
第9章 反应器

当新的数据库对象被加入时候, 将触发数据库反应器的 objectAppended 事件, 我们下面通过实例来监控这个事件并指定相应的操作。 通过 ObjectARX 向导从 AcDbDatabaseReactor 类派生自定义的数据库反应器 CSDatabaseReactor 并重载 objectAppended 事件处理函数, 添加数据库反应器的过 程与前面添加编辑反应器的过程类似,下面仅给出 objectAppended 事件处理函数 的实现内容。 void CSDatabaseReactor::objectAppended(const AcDbDatabase * dwg, const AcDbObject * dbObj) { //如果是圆,改变圆的颜色为红色 if(dbObj->isKindOf (AcDbCircle::desc ()) ) { AcDbCircle* pCir = AcDbCircle::cast(dbObj); //升级打开模式,修改对象 pCir->upgradeOpen (); pCir->setColorIndex (1); acutPrintf(_T("\n 创建了圆\n"));
PDF 文件使用 "pdfFactory Pro" 试用版本创建
第 1 章 AutoCAD 开发概览
过程。
图 9-1 事件处理过程 处理过程说明: 1. 在 ObjectARX 程序创建反应器对象。 2. ObjectARX 程序将反应器对象附着给事件的触发者 AcDbLine 对象 。 3. AcDbLine 对象改变,想反应器发送 objectModified 通知消息 。 4. 反应器对象接受事件,针对事件做出相应的处理。
9.4 反应器的使用
化学反应工程
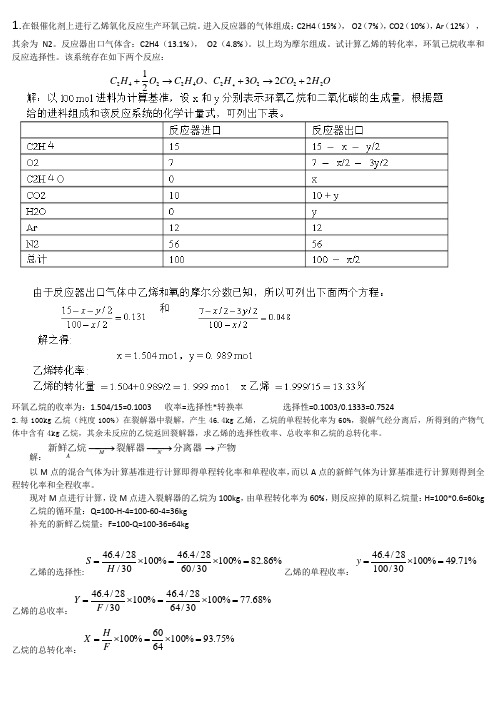
1.在银催化剂上进行乙烯氧化反应生产环氧己烷。
进入反应器的气体组成:C2H4(15%), O2(7%),CO2(10%),Ar (12%) ,其余为N2。
反应器出口气体含:C2H4(13.1%), O2(4.8%)。
以上均为摩尔组成。
试计算乙烯的转化率,环氧己烷收率和反应选择性。
该系统存在如下两个反应:环氧乙烷的收率为:1.504/15=0.1003 收率=选择性*转换率 选择性=0.1003/0.1333=0.75242.每100kg 乙烷(纯度100%)在裂解器中裂解,产生46.4kg 乙烯,乙烷的单程转化率为60%,裂解气经分离后,所得到的产物气体中含有4kg 乙烷,其余未反应的乙烷返回裂解器,求乙烯的选择性收率、总收率和乙烷的总转化率。
解:以M 点的混合气体为计算基准进行计算即得单程转化率和单程收率,而以A 点的新鲜气体为计算基准进行计算则得到全程转化率和全程收率。
现对M 点进行计算,设M 点进入裂解器的乙烷为100kg ,由单程转化率为60%,则反应掉的原料乙烷量:H=100*0.6=60kg 乙烷的循环量:Q=100-H -4=100-60-4=36kg 补充的新鲜乙烷量:F=100-Q=100-36=64kg乙烯的选择性:乙烯的单程收率:乙烯的总收率:乙烷的总转化率:产物分离器裂解器新鲜乙烷→−→−−→−NM A%86.82%10030/6028/4.46%10030/28/4.46=⨯=⨯=H S %71.49%10030/10028/4.46=⨯=y %68.77%10030/6428/4.46%10030/28/4.46=⨯=⨯=F Y %75.93%1006460%100=⨯=⨯=F H X O H CO O H C O H C O H C 222242242223214+→+→+、3.丁二烯是制造合成橡胶的重要原料,制取丁二烯的生产方法之一是将正丁烯和空气及水蒸气的混合气体在磷钼铋催化剂上进行氧化脱氢,其主反应为:此外还有许多副反应,如生成酮、醛及有机酸的反应。
实验二 连续搅拌釜式反应器液相反应的动力学参数测定
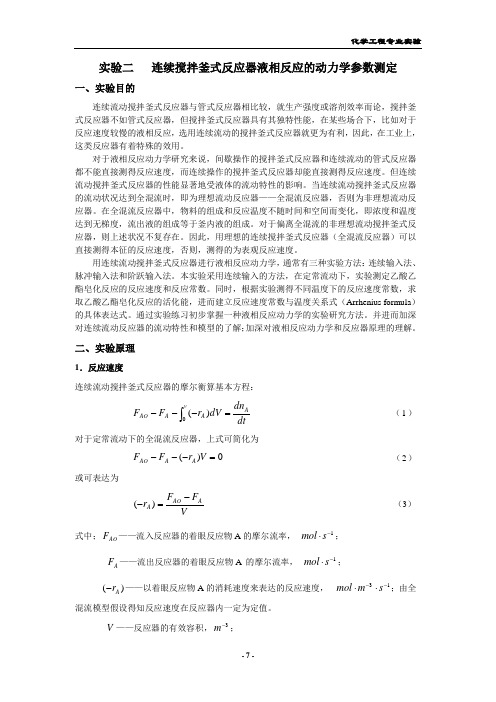
实验二 连续搅拌釜式反应器液相反应的动力学参数测定一、实验目的连续流动搅拌釜式反应器与管式反应器相比较,就生产强度或溶剂效率而论,搅拌釜式反应器不如管式反应器,但搅拌釜式反应器具有其独特性能,在某些场合下,比如对于反应速度较慢的液相反应,选用连续流动的搅拌釜式反应器就更为有利,因此,在工业上,这类反应器有着特殊的效用。
对于液相反应动力学研究来说,间歇操作的搅拌釜式反应器和连续流动的管式反应器都不能直接测得反应速度,而连续操作的搅拌釜式反应器却能直接测得反应速度。
但连续流动搅拌釜式反应器的性能显著地受液体的流动特性的影响。
当连续流动搅拌釜式反应器的流动状况达到全混流时,即为理想流动反应器——全混流反应器,否则为非理想流动反应器。
在全混流反应器中,物料的组成和反应温度不随时间和空间而变化,即浓度和温度达到无梯度,流出液的组成等于釜内液的组成。
对于偏离全混流的非理想流动搅拌釜式反应器,则上述状况不复存在。
因此,用理想的连续搅拌釜式反应器(全混流反应器)可以直接测得本征的反应速度,否则,测得的为表观反应速度。
用连续流动搅拌釜式反应器进行液相反应动力学,通常有三种实验方法:连续输入法、脉冲输入法和阶跃输入法。
本实验采用连续输入的方法,在定常流动下,实验测定乙酸乙酯皂化反应的反应速度和反应常数。
同时,根据实验测得不同温度下的反应速度常数,求取乙酸乙酯皂化反应的活化能,进而建立反应速度常数与温度关系式(Arrhenius formula )的具体表达式。
通过实验练习初步掌握一种液相反应动力学的实验研究方法。
并进而加深对连续流动反应器的流动特性和模型的了解;加深对液相反应动力学和反应器原理的理解。
二、实验原理1.反应速度连续流动搅拌釜式反应器的摩尔衡算基本方程: dtdn dV r F F AvA A AO =---⎰)(0(1)对于定常流动下的全混流反应器,上式可简化为0)(=---V r F F A A AO (2) 或可表达为VF F r AAO A -=-)( (3)式中;AO F ——流入反应器的着眼反应物A 的摩尔流率, 1-⋅smol ;A F ——流出反应器的着眼反应物A 的摩尔流率, 1-⋅smol ;)(A r -——以着眼反应物A 的消耗速度来表达的反应速度,13--⋅⋅sm mol ;由全混流模型假设得知反应速度在反应器内一定为定值。
连续搅拌釜式反应器详解
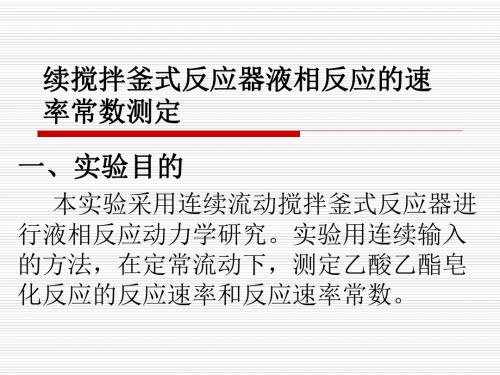
3.参考下列表格记录测定反应速率和反应速率常数的实验数据
实 验 序 号 1 2 3 4 5
反应温度T/℃
反应体积V/L 总体积流率Vs,0/L· min-1 反应物A的 出口浓 度 U/mV
(U-Uf)/mV
CA/mol· L-1
4.参考下列表格整理实验数据
实 验 组 号
反应温度T/K 空间时间/min 反应速率(-rA)/ mol· L-1· min-1 反应速率常数k/L· mol-1· min-1 (1) (2) (3) (4)
式中:τ=V/Vs,0,即为空间时间。对于恒容过程,进出口又无 返混时,则空间
时间也就是平均停留时间。因此,当V和Vs,0一定时,只要实验测得CA,0和CA, 即可直接测得在一定温度下的反应速率(-rA)。
2. 反应速率常数
CH3COOC2H5(A)+NaOH(B)→CH3COONa(C)+C2H5OH(D) 因为该反应为双分子反应,则反应速率方程为: (-rA)=kCACB 本实验中,反应物A和B采用相同的浓度和相同的流率,则上式可简为: (-rA)=kCA2 将上式线性化后,可得:lg(-rA)=2lgCA+lgk 当反应温度T和反应器有效容积V一定时,可利用改变流率的方法,测得 不同CA下的反 应速率(-rA)。由lg(-rA)对lgCA进行标绘,可得到一条 直线。由直线的截距lgk 求取k值。或用最小二乘法进行线性回归求得k 值。
2.
3.测定反应速率和反应速率常数的实验步骤
(1)停止加热和搅拌后,将反应器内的纯水放尽。启 动并调定计量泵,同时以等流率向器 内加入料液A和 B。待液面稳定后,启动搅拌器和加热器并控制转速和 温度恒定。当搅拌转速 在600r· min-1 时,总体积流率 在2.7~16L· h-1(相当于计量泵显示10~60 r·min-1)范围 (2)当操作状态达到稳定之后,按数据采集键,采集 与浓度CA相应的电压信号U。待屏幕 上 显示的曲线平直 之后,按终止采集键,取其平直段的平均值,即为与釜 内最终浓度CA相应 的U (3)改变流量重复上述实验步骤,测得一组在一定温 度下,不同流量时的U值数据。
AutoLISP使用反应器

vlr-beep-reaction的功能是让计算机发出“嘟嘟”声。 (2)vlr-trace-reaction函数
vlr-trace-reaction函数的功能是将参数列表打印到 VLISP的“跟踪”窗口。
11.3 创建反应器
创建反应器的主要工作就是将事件和回调函数相关联。创建 反应器用vlr--reactor函数。每种类型的反应器都有一个与 之对应的用于创建该反应器的AutoLISP函数,这些函数的名称 和反应器类型的名称相同,只是没有前面的冒号。例如,vlracdb-reactor为创建数据库反应器函数,vlr-toolbar-reactor 为创建工具栏反应器函数。所有创建反应器的构造函数都返回 一个反应器对象。
vlr-reaction-names函数返回与给定反应器类型相关的所有 事件组成的表:
(vlr-reaction-names reactor-type)
参数reactor-type是反应器类型的标识,见表11-1和表11-2。
例如,下列代码将返回和图形反应器相关的所有事件组成的表:
(vlr-reaction-names :VLR-DWG-Reactor)
通报对系统变量的修改
:VLR-Toolbar-Reactor
通报对工具栏上位图的修改
:VLR-Undo-Reactor
通报 undo 事件
:VLR-Wblock-Reactor
通报和写块有关的事件
:VLR-Window-Reactor
通报和移动或改变AutoCAD窗口大小的事件
:VLR-XREF-Reactor
:VLR-Insert-Reactor
化工系统工程_04热夹点技术解析
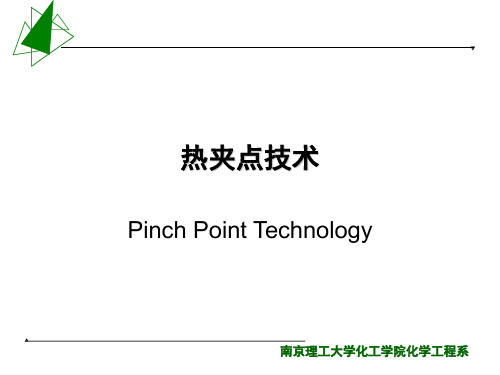
若改变最小传热温差ΔT min = 15℃,则结果如下:
表 子网络序号
k 1 2 3 4 5 6
问题表格(1)
冷物流及其温度
C1
C2
℃ 150
125 140
100 115
75 90
45 60
25
20
△Tmin = 15 ℃
热物流及其温度
H1
H2
问题表格(2)
表 子网络 序号 1 2 3 4 5 6
穿越夹点热量 = PPxp + HUxp +CUxp = 1620 + 220 + 0 = 1840kW
循环流股
南京理工大学化工学院化学工程系
PPXP是由热的过程物流在夹点上方的温位(180℃~270℃) 与冷过程物流在夹点下方的温位(50℃~149℃)换热引起, PPXP = CPH(270-180)= CPC(149-50)=1620kW。 HUXP是由冷过程物流在夹点下方的温位(149℃~160℃) 外加公用工程加热负荷引起,HUXP=CPC(160-49)=220kW。 即QXP=CUXP+HUXP+PPXP =0+220+1620 =1840kW。
3200
CP = 50 C2
2500
H H/kW
210° 160°
CP=70
CP=20
50° 2200
3500
H/kW
南京理工大学化工学院化学工程系
利用组合曲线确定夹点
T/º C
QH,min=1000
热组合曲线
C
冷组合曲线
最小热公用工程 QH,min=1000kW 最小冷公用工程 QC,min=800kW
UASB工艺设计计算(全)
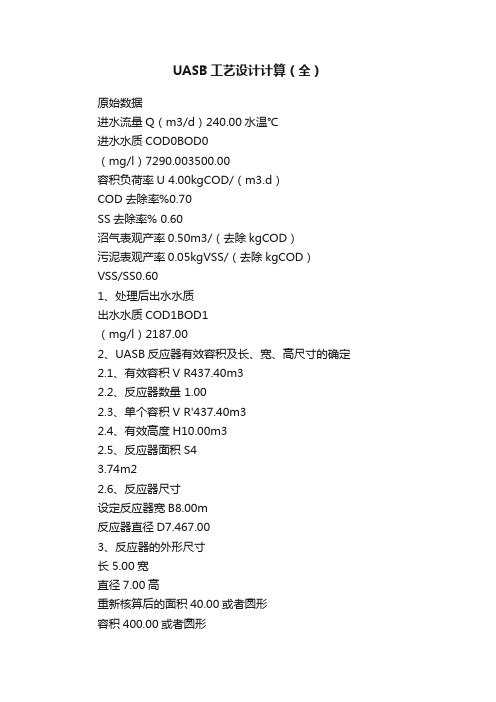
UASB工艺设计计算(全)原始数据进水流量Q(m3/d)240.00水温℃进水水质COD0BOD0(mg/l)7290.003500.00容积负荷率U 4.00kgCOD/(m3.d)COD去除率%0.70SS去除率% 0.60沼气表观产率0.50m3/(去除kgCOD)污泥表观产率0.05kgVSS/(去除kgCOD)VSS/SS0.601、处理后出水水质出水水质COD1BOD1(mg/l)2187.002、UASB反应器有效容积及长、宽、高尺寸的确定2.1、有效容积V R437.40m32.2、反应器数量 1.002.3、单个容积V R'437.40m32.4、有效高度H10.00m32.5、反应器面积S43.74m22.6、反应器尺寸设定反应器宽B8.00m反应器直径D7.467.003、反应器的外形尺寸长 5.00宽直径7.00高重新核算后的面积40.00或者圆形容积400.00或者圆形4、反应器的水力停留时间HRT40.00或者圆形5、三相分离器设计沉淀区的表面负荷0.13或者圆形沉淀区的水深h 1.00m停留时间 4.00或者圆形6、回流缝设计设集气罩的水平夹角55.00取保护高度h10.50m设下三角集气罩高度h30.80m上三角形顶水深h20.50m则有b10.56m设单元三相分离器宽b 2.50m则下部污泥回流缝宽度b2 1.38m下部污泥回流缝总面积a122.07或者圆形求得下三角形回流缝的上升流速v10.45或者圆形设上部三角形集气罩回流缝宽度b30.64m总面积a220.47或者圆形求得上部回流缝上升流速v20.24或者圆形7、三相分离器位置的确定上三角形集气罩底端到下三角形集气罩斜面的垂直距离CE上三角形集气罩底端到下三角形集气罩的竖直距离BC取上三角形集气罩与下三角形集气罩重叠的斜面长度AB求得上三角形集气罩底端与下三角形集气罩底端的高度h则确定上三角形集气罩底端到池顶的距离 1.80m下三角形集气罩底端到池顶的距离 3.11m8、气液分离设计沿下集气罩斜面方向的水流速度va0.60或者圆形气泡的直径dg设为0.01cm废水的动力粘滞系数μ=vρ10.01取(β*g/18μ)*(ρ1-ρg)*d2气泡在下集气罩边缘的上升速度vb=0.27cm/s9.59m/h9、核算设计结果BC/AB= 2.28vb/va=16.08或者圆形满足vb/va > BC/AB的要求,可以脱除直径等于或大于0.01cm 的气泡。
化学反应器大作业-二氧化硫转换器最优化
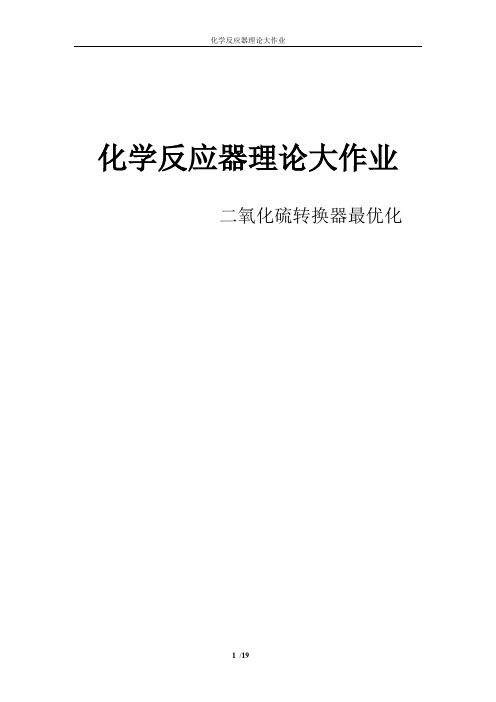
化学反应器理论大作业二氧化硫转换器最优化二氧化硫转换器最优化反应方程式:SO 2+1/2O 2=SO 3 (放热反应)四段绝热反应器,级间间接换热,常压下反应。
1. 基础数据• 混合物恒压热容Cp =0.2549 [kcal/kgK] • -ΔH =23135 [kcal/kmol] • 催化剂堆密度 ρb =554 [kg/m 3]• 进口SO 2浓度8.0 mol%,O 2浓度9.0 mol%,其余为氮气 • 处理量131 [kmol SO 2/hr],要求最终转化率98%2..动力学方程 式中:3. 基本要求• 在T -X 图上,做出平衡线;至少4条等速率线。
• 以一维拟均相平推流模型为基础,在催化剂用量最少的前提下,求总()()()[]sec ./11-2232323222gcat mol P P K P PB B P P K P k R SO SO SO SO SO SO O eff SO +-+-=ξ()()987.1,3.11295exp 1026203.227200exp 103.25.7355exp 48148600475,35992exp 105128.1475420,76062exp 106915.75218718223=⎪⎪⎭⎫⎝⎛⨯=⎪⎭⎫ ⎝⎛=⎪⎪⎭⎫ ⎝⎛⨯=⎪⎪⎭⎫⎝⎛-=-⎪⎪⎭⎫⎝⎛-⨯=-⎪⎪⎭⎫⎝⎛-⨯=--R T K P P K P RT K T B C RT k C RT k P O SO P SOoeff oeff ξ的及各段的催化剂装量,进出口温度、转化率并在T-X 图上标出折线。
•程序用C、Fortran、BASIC语言之一编制。
4.讨论•要求的最终转化率从98%变化到99%对催化剂用量的影响;•y O2+y SO2=21%,SO2进口浓度在7-9%之间变化,对催化剂装量的影响。
一.T-X图绘制平衡线与等反应速率线本次大作业计算程序,使用Matlab编程实现。