电熔锆刚玉砖的生产工艺
电熔锆刚玉砖的生产工艺
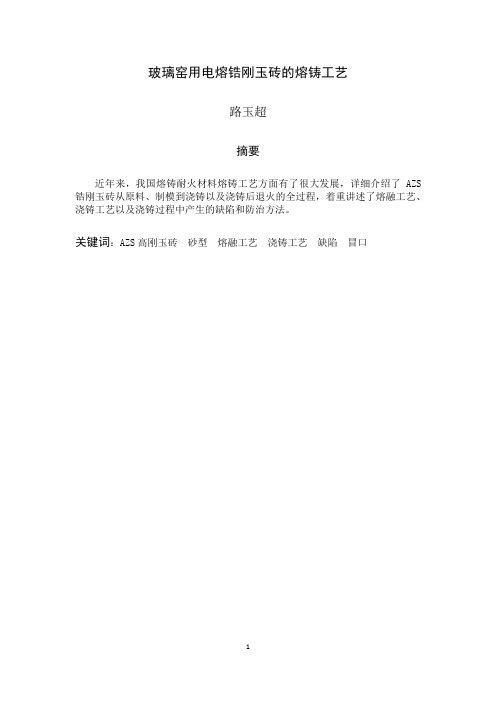
玻璃窑用电熔锆刚玉砖的熔铸工艺路玉超摘要近年来,我国熔铸耐火材料熔铸工艺方面有了很大发展,详细介绍了AZS 锆刚玉砖从原料、制模到浇铸以及浇铸后退火的全过程,着重讲述了熔融工艺、浇铸工艺以及浇铸过程中产生的缺陷和防治方法。
关键词:AZS高刚玉砖砂型熔融工艺浇铸工艺缺陷冒口目录一熔化工艺 (3)1. AZS原料 (3)2.电弧炉工作原理 (3)3.AZS熔化原理 (3)3.1 熔化过程的物理化学反应 (3)4. 熔融工艺 (5)4.1 还原法 (5)4.2 氧化法 (5)二.砂型的制作 (6)1. 砂型制备的原料 (6)1.1 有较好的透气性 (6)1.2 有良好的耐热冲击强度 (6)1.3有良好的热机械性能 (6)1.4锆刚玉砖表面不产生化学粘砂 (6)2. 砂型的制作工艺 (6)三.浇铸 (7)1. 浇铸的方法 (7)1.1普通浇铸法 (7)1.2 倾斜浇铸法 (7)1.3 无缩孔浇铸 (7)2. 浇铸过程的特征 (7)3. 浇铸工艺 (8)3.1 浇铸温度 (8)3.2浇铸速度和浇铸时间 (8)3.3 补浇 (9)4. 浇铸与浇铸中气孔的关系 (9)4.1 由铸型材料引发的气孔 (9)4.2 由浇铸操作引发的气孔 (9)5. 浇铸过程中的缺陷及防治措施 (10)5.1 浇铸过程中的缺陷 (10)5.2 铸件中缩松的形成及其影响因素 (11)5.3 减少铸件缩松和缩孔的基本方法 (11)5.4冒口 (11)四.AZS退火工艺 (12)1. 铸件的凝固 (12)2. 铸件的退火 (13)2.1 保温箱退火法 (13)2.2 隧道窑退火 (13)结论 (14)参考文献 (14)玻璃窑用锆刚玉砖的熔铸工艺一 熔化工艺1.AZS 原料AZS 用原料有五种:氧化铝、锆英砂、富锆砂、纯碱、硼砂。
1) 氧化铝的引入一般选用工业氧化铝,生产要求其含水量应小于0.3%,烧失量最好小于0.15%,一吨AZS-33电熔砖约需0.62吨氧化铝。
一种电熔氧化锆生产工艺

一种电熔氧化锆生产工艺
电熔氧化锆生产工艺是一种常用的锆合金制备工艺,其主要步骤包括以下几个方面:
1. 原料准备:选择优质的氧化锆矿石作为原料,经过石英砂、碳以及铝粉的混合和研磨处理,得到均匀的混合料。
2. 配料:将研磨好的混合料按照一定比例配料,使得锆和其他合金元素的含量及比例满足生产要求。
3. 电熔:将配料装入铸造炉中,进行电熔加热。
通过电流通过熔体,使熔体中的锆和其他合金元素全部熔融在一起。
4. 净化:在电熔过程中,通过熔体中加入适量的氩气或其他保护气体,去除熔体中的氧、硅等杂质,提高合金的纯度。
5. 浇铸成锭:将熔化好的锆合金倒入预先准备好的铸模中,待熔体冷却凝固后,得到锆合金锭。
6. 锭加工:对得到的锆合金锭进行加工处理,如热轧、锻造、热处理等,使其获得所需的形状和性能。
需要注意的是,电熔氧化锆生产工艺存在较高的温度和电流要求,需要保持合适的工艺参数和设备条件,以确保产品质量和生产效率。
一种电熔氧化锆生产工艺
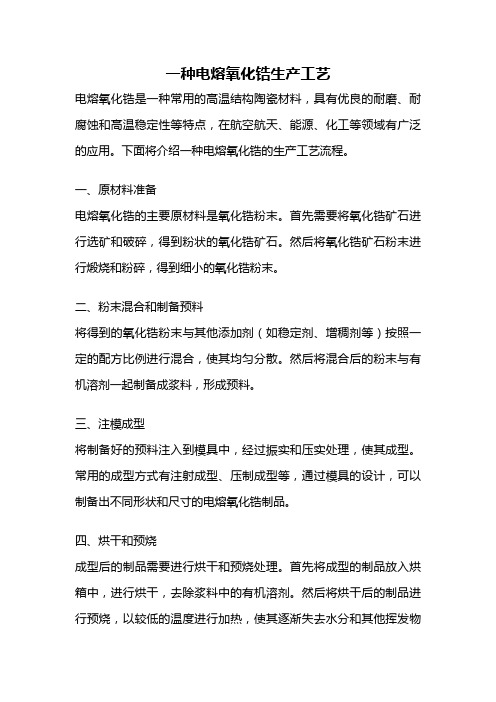
一种电熔氧化锆生产工艺电熔氧化锆是一种常用的高温结构陶瓷材料,具有优良的耐磨、耐腐蚀和高温稳定性等特点,在航空航天、能源、化工等领域有广泛的应用。
下面将介绍一种电熔氧化锆的生产工艺流程。
一、原材料准备电熔氧化锆的主要原材料是氧化锆粉末。
首先需要将氧化锆矿石进行选矿和破碎,得到粉状的氧化锆矿石。
然后将氧化锆矿石粉末进行煅烧和粉碎,得到细小的氧化锆粉末。
二、粉末混合和制备预料将得到的氧化锆粉末与其他添加剂(如稳定剂、增稠剂等)按照一定的配方比例进行混合,使其均匀分散。
然后将混合后的粉末与有机溶剂一起制备成浆料,形成预料。
三、注模成型将制备好的预料注入到模具中,经过振实和压实处理,使其成型。
常用的成型方式有注射成型、压制成型等,通过模具的设计,可以制备出不同形状和尺寸的电熔氧化锆制品。
四、烘干和预烧成型后的制品需要进行烘干和预烧处理。
首先将成型的制品放入烘箱中,进行烘干,去除浆料中的有机溶剂。
然后将烘干后的制品进行预烧,以较低的温度进行加热,使其逐渐失去水分和其他挥发物质,增强其强度和稳定性。
五、电熔烧结预烧后的制品需要进行电熔烧结处理,以提高其致密性和机械性能。
将预烧后的制品放入电熔炉中,通过高温下的电热作用,使其表面熔化和烧结。
在电熔炉中,通过控制温度和热处理时间,使氧化锆颗粒之间发生烧结反应,形成致密的晶体结构。
六、后处理经过电熔烧结处理后的制品还需要进行后处理。
包括去除表面氧化物、调整制品的形状和尺寸等工艺步骤。
最后,通过抛光、清洗等工序,得到最终的电熔氧化锆制品。
以上就是一种电熔氧化锆的生产工艺流程。
通过选矿、破碎、煅烧和粉碎等步骤,制备出细小的氧化锆粉末。
然后将粉末与添加剂混合,制备成浆料,注入模具中进行成型。
成型后的制品经过烘干、预烧和电熔烧结等处理,最终得到高密度、高强度的电熔氧化锆制品。
这种生产工艺具有工艺简单、成本低、制品质量稳定等优点,广泛应用于各个领域。
AZS熔铸电熔锆刚玉砖工艺及生产线简介

AZS熔铸电熔锆刚玉砖工艺及生产线简介李华栋;张国靖;陈胜英【摘要】为了提高电熔锆刚玉砖的生产效率,设计了自动化生产线,满足设备按照工艺流程进行自动化生产,给用户提高了产品质量与数量,节约了大量的人力,该生产线的成功运行有利于国内铸造锆刚玉砖的生产发展.【期刊名称】《铸造设备与工艺》【年(卷),期】2012(000)005【总页数】3页(P38-40)【关键词】电熔锆刚玉砖;生产工艺;自动化生产线【作者】李华栋;张国靖;陈胜英【作者单位】济南二机床集团有限公司,山东济南250022;济南二机床集团有限公司,山东济南250022;济南二机床集团有限公司,山东济南250022【正文语种】中文【中图分类】TG2491 AZS电熔锆刚玉简介[1-2]1.1 电熔锆刚玉定义电熔锆刚玉是用纯净的氧化铝粉与含氧化锆质量分数65%、二氧化硅质量分数34%左右的锆英砂在电熔炉内熔化后注入模型内冷却而形成的白色固体,其岩相结构由刚玉与锆斜石的共析体和玻璃相组成,从相学上讲是刚玉相和锆斜石相的共析体,玻璃相充填于他们的结晶之间。
1.2 电熔锆刚玉特性1)具有1850℃的荷重耐火度;2)硬度接近金刚石(金刚石的莫氏硬度为10,而锆刚玉的莫氏硬度为9);3)氧化锆的结晶体是串珠状,在高温下抵抗玻璃熔液浸蚀能力很强;4)由于本质纯净而不污染产品,所以是玻璃及玻璃制品的熔化池不可缺少的耐火材料。
随着我国玻璃工业的不断发展,对这种材料的需求将会越来越大。
电熔锆刚玉砖的缩写是AZS,是按A l2O3-Z r 02-S i O2三元系相图的三个化学成分,依其含量多少顺序排列的,A l2O3取 A,Z r 02取 Z,S i O2取 S,国家标准采用这个缩写,例如33号熔铸锆刚玉砖,缩写为AZS-33#,其余类推。
1.3 电熔锆刚玉的用途实践认为,AZS产品具有良好的作业特性温度,应限定在1500℃以下,这在现阶段的一般玻璃窑上是合适的。
【原料】看了这个才知道,原来这7种电熔刚玉是生产这些耐火材料的!
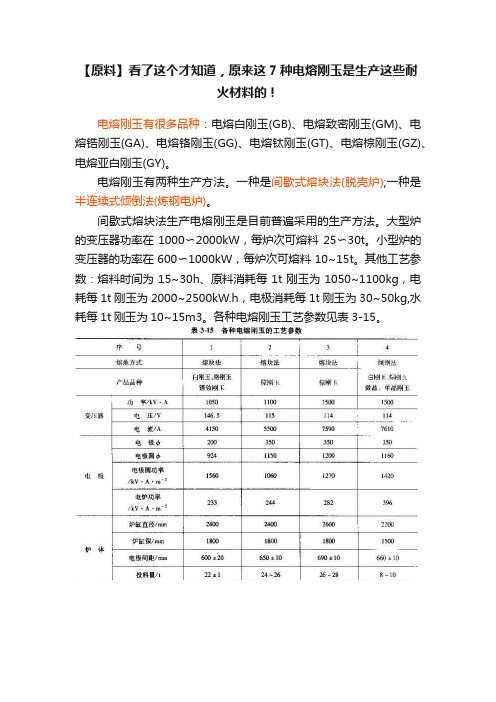
【原料】看了这个才知道,原来这7种电熔刚玉是生产这些耐火材料的!电熔刚玉有很多品种:电熔白刚玉(GB)、电熔致密刚玉(GM)、电熔锆刚玉(GA)、电熔铬刚玉(GG)、电熔钛刚玉(GT)、电熔棕刚玉(GZ)、电熔亚白刚玉(GY)。
电熔刚玉有两种生产方法。
一种是间歇式熔块法(脱壳炉);一种是半连续式倾倒法(炼钢电炉)。
间歇式熔块法生产电熔刚玉是目前普遍采用的生产方法。
大型炉的变压器功率在1000〜2000kW,每炉次可熔料25〜30t。
小型炉的变压器的功率在600〜1000kW,每炉次可熔料10~15t。
其他工艺参数:熔料时间为15~30h、原料消耗每1t刚玉为1050~1100kg,电耗每1t刚玉为2000~2500kW.h,电极消耗每1t刚玉为30~50kg,水耗每1t刚玉为10~15m3。
各种电熔刚玉工艺参数见表3-15。
电熔白刚玉:以工业氧化铝为原料,配入少量外加剂(AlF3)以提髙熔液的流动性。
在工业氧化铝中分别加入氧化锆、氧化铬、氧化钛可以分别生产锆刚玉、铬刚玉和钛刚玉。
电熔白刚玉的生产工艺如下:(1)电炉拖车结构,在拖车台面上铺髙铝砖4~5层,铺刚玉砖2~3层,铺炭砖厚度大于200tnm,在铺好的拖车底上面,放上水冷炉壳,并通过轨道送入电极中心下面。
(2)铺炉底料,在拖车台面上铺工业氧化铝,中间层厚约200mm,靠炉壳约300mm,防止起弧时溶液外溢。
在炉底料上面用小电极块铺成三角形或Y形,3个顶点要与3个电极相对应。
亦可用铝屑和炭粉的混合物做起弧材料。
用这种起弧材料起弧操作简单、不易断弧,对电熔料不增加杂质污染。
铝屑与炭粉的比例为2:1至3:1。
(3)起弧,先将一支电极下降到与起弧的电极块接触,并压紧,然后下降第二、第三支电极至全部起孤,随着电流、电压逐渐提高,熔区扩大后,边电熔边加料,以防止断弧影响操作。
(4)正常操作,正常操作电流控制在4000~5000A…电熔刚玉有还原和氧化两种操作方法。
电熔刚玉耐火材料的生产工艺

电熔刚玉耐火材料的生产工艺电熔刚玉耐火材料按照制造工艺可分为熔铸刚玉砖和再结合(半再结合)电熔刚玉砖。
熔铸刚玉砖是以工业氧化铝及少量纯碱和石英粉在电弧炉内熔融,再经铸型、退火等工序,最后机械加工成所需的形状、尺寸。
再结合(半结合)电熔刚玉砖使用粉碎好的电熔刚玉颗粒及粉料,加入结合剂,经充分混炼后,用压砖机成型,砖坯烘干后高温烧成。
熔铸刚玉制品将氧化铝原料配合料在高于熔融温度下熔化后,浇注在预制的耐火模型中,经过冷却固化使结晶发育长大而形成的制品,称为熔铸刚玉耐火材料。
一般采用电熔方法熔化。
以工业氧化铝为主要原料电熔的熔铸刚玉耐火材料是经过配合料熔化、精炼,然后浇铸到模型中,铸件经过凝固、退火、切割、磨削和预组装,称为合格产品。
按其化学矿物组成主要有三种类型。
熔铸a-Al2O3又称电熔a-Al2O3砖,是以a-Al2O3为主相的熔铸耐火材料。
a-Al2O3约95%,β-Al2O3为5%-10%,玻璃相较少。
这种砖的结构致密,耐火度和高温结构强度较高,高温化学稳定性好,但在碱金属氧化物的作用下,可能转化为β-Al2O3而发生体积增大,适用于砌筑玻璃窑冷却池部位上部结构,以及有色金属冶炼炉及高温隧道窑。
熔铸β-Al2O3砖又称电熔β-Al2O3砖,以β-Al2O3为主晶相的熔铸耐火材料,β-Al2O3含量约99.5%,玻璃相较少,约占0.5%以下,对碱蒸汽呈惰性。
在不含碱的气氛中,易分离出碱而转化为a-Al2O3,并伴随有体积收缩,而可能引起砖的碎裂。
熔铸β-Al2O3砖耐热震性较好,700度到常温空气循环可达40次左右,一般适用于砌筑玻璃熔窑的上部结构。
熔铸a、β-Al2O3砖又称电熔a、β-Al2O3砖,是含a-Al2O3和β-Al2O3的熔铸制品。
a-Al2O3约占40%-50%,β-Al2O3约占45%-60%,玻璃相极少。
同β-Al2O3型制品相比,抗玻璃液的侵蚀能力较强,高温下抗碱蒸汽的作用也较好,可用于玻璃窑上部结构,也可用于直接与玻璃液接触的低温部位。
锆刚玉砖——精选推荐

锆刚玉砖(zirconia-corundum refractory brick)利用工业氧化铝粉和精选锆英石砂为原料,制成的ZrO2含量为33%~45%的耐火制品。
锆刚玉砖主要用于玻璃工业池窑。
简史 1926年富尔歇尔(G.S.Fulcher)在电熔莫来石内加入10%~60%ZrO2。
为了达到提高浇铸能力,减少废品的目的,1939年菲尔德(T.E.Field)认识到含氧化锆的熔铸砖比电熔莫来石砖更耐玻璃液侵蚀,是提高玻璃池窑寿命的理想材料。
1956年苏联布德尼科夫等人首先发表关于ZrO2-Al2O3-SiO2三元系相图的研究结果。
当组成为Al2O353%、ZrO230%、SiO217%时有一共熔点,其共熔温度为1675℃±10℃。
1975年联邦德国西弗尔斯(G.Cevals)重新研究后作了修改:共熔温度在1685℃±10℃,组成为Al2O350.9%、ZrO232.8%、SiO216.3%。
证实工业上大量生产的33号熔铸砖的组成就在共熔点附近,分子式相当于ZrO2-2Al2O3-SiO2简称为AZS熔铸砖。
1958年法国格罗里埃巴隆(GrollierT.Baron)、戈丹(J.Gaudin)发布了电熔氧化锆的专利技术,降低了制品内碳的含量,从而减少玻璃制品中气泡或线痕等缺陷。
1960年苏联在埃里温电熔耐火材料厂试制出第一批BAKOP-33型AZS熔铸制品,试用于弋尔玻璃厂。
日本东芝电兴株式会社于1958年开始研究电熔浇铸砖。
1966年该公司与美国碳化硅公司合资经营改名为东芝MONOFRAX公司,1971年开始建设神崎工场。
1966年日本旭硝子公司从法国西普公司(Sepr)引进熔铸锆刚玉砖生产技术,生产的品种有ZB1681、ZB1691、ZB1710。
美国于1961年研制烧结锆刚玉砖。
中国于20世纪60年代开始生产熔铸莫来石砖;1966年研制生产30号AZS熔铸砖;1989年用氧化法生产33号及41号熔铸AZS砖和捣打料。
电熔氧化锆生产工艺

电熔氧化锆生产工艺我呀,今天要和大家唠唠电熔氧化锆的生产工艺,这可真是个超级有趣的事儿呢!咱们先来说说氧化锆是个啥。
氧化锆就像是材料界的一颗明珠,它有很多厉害的特性。
硬度高得很,就像一个钢铁硬汉,在很多需要耐磨的地方那可是大显身手。
而且它的耐高温性能也特别出众,就好比是在烈火中也面不改色的勇士。
那这么厉害的氧化锆,用电熔法生产出来就更了不起啦。
我有个朋友,他就在一个生产电熔氧化锆的厂里工作。
他跟我讲,这电熔氧化锆的生产原料那可得精挑细选。
就像咱们做饭,食材不好,做出来的饭肯定也不咋地。
原料主要是锆英砂,这锆英砂的纯度必须得高,要是里面杂质太多,就像在一锅好汤里掉进了沙子,那做出来的电熔氧化锆质量肯定不行。
他们在选原料的时候可认真啦,眼睛都不敢眨一下,生怕选错了。
接下来就是熔炼的过程啦。
这个过程就像是一场魔法表演。
把选好的原料放到电弧炉里,一通电,哇塞,那场面可壮观了。
电极之间产生强大的电弧,就像闪电一样,瞬间就把炉子里的温度升得超高。
这时候的锆英砂就开始发生奇妙的变化,就像冰雪遇到了暖阳,一点点融化。
不过这可不是简单的融化哦,里面还有好多复杂的化学反应呢。
我就问我朋友:“这化学反应你能看得懂吗?”他笑着说:“哪能全看懂啊,就像看天书一样,但是知道个大概就够啦。
”在熔炼的时候,温度的控制那是相当关键的,要是温度高一点或者低一点,就像烤蛋糕的时候火候没掌握好,烤出来的电熔氧化锆要么质量不好,要么就不符合标准。
在熔炼的过程中,还得不断地搅拌呢。
这搅拌就像是给锅里的菜翻炒一样,让原料能够充分地反应和融合。
我想象着那大大的搅拌器在火红的炉子里翻动着原料,就觉得特别神奇。
我朋友说,这搅拌的速度也是有讲究的,不能太快也不能太慢,太快了就像狂风把东西都吹乱了,太慢了又达不到充分混合的效果。
等熔炼完成之后,就到了冷却的阶段啦。
这冷却可不能心急,得慢慢来。
就像我们刚运动完不能马上冲凉水澡一样。
如果冷却得太快,电熔氧化锆可能会出现裂纹,就像一个精美的瓷器被摔出了裂缝,那可就不好啦。
- 1、下载文档前请自行甄别文档内容的完整性,平台不提供额外的编辑、内容补充、找答案等附加服务。
- 2、"仅部分预览"的文档,不可在线预览部分如存在完整性等问题,可反馈申请退款(可完整预览的文档不适用该条件!)。
- 3、如文档侵犯您的权益,请联系客服反馈,我们会尽快为您处理(人工客服工作时间:9:00-18:30)。
玻璃窑用电熔锆刚玉砖的熔铸工艺路玉超摘要近年来,我国熔铸耐火材料熔铸工艺方面有了很大发展,详细介绍了AZS 锆刚玉砖从原料、制模到浇铸以及浇铸后退火的全过程,着重讲述了熔融工艺、浇铸工艺以及浇铸过程中产生的缺陷和防治方法。
关键词:AZS高刚玉砖砂型熔融工艺浇铸工艺缺陷冒口目录一熔化工艺 (3)1. AZS原料 (3)2.电弧炉工作原理 (3)3.AZS熔化原理 (3)3.1 熔化过程的物理化学反应 (3)4. 熔融工艺 (5)4.1 还原法 (5)4.2 氧化法 (5)二.砂型的制作 (6)1. 砂型制备的原料 (6)1.1 有较好的透气性 (6)1.2 有良好的耐热冲击强度 (6)1.3有良好的热机械性能 (6)1.4锆刚玉砖表面不产生化学粘砂 (6)2. 砂型的制作工艺 (6)三.浇铸 (7)1. 浇铸的方法 (7)1.1普通浇铸法 (7)1.2 倾斜浇铸法 (7)1.3 无缩孔浇铸 (7)2. 浇铸过程的特征 (7)3. 浇铸工艺 (8)3.1 浇铸温度 (8)3.2浇铸速度和浇铸时间 (8)3.3 补浇 (9)4. 浇铸与浇铸中气孔的关系 (9)4.1 由铸型材料引发的气孔 (9)4.2 由浇铸操作引发的气孔 (9)5. 浇铸过程中的缺陷及防治措施 (10)5.1 浇铸过程中的缺陷 (10)5.2 铸件中缩松的形成及其影响因素 (11)5.3 减少铸件缩松和缩孔的基本方法 (11)5.4冒口 (11)四.AZS退火工艺 (12)1. 铸件的凝固 (12)2. 铸件的退火 (13)2.1 保温箱退火法 (13)2.2 隧道窑退火 (13)结论 (14)参考文献 (14)玻璃窑用锆刚玉砖的熔铸工艺一 熔化工艺1.AZS 原料AZS 用原料有五种:氧化铝、锆英砂、富锆砂、纯碱、硼砂。
1) 氧化铝的引入一般选用工业氧化铝,生产要求其含水量应小于0.3%,烧失量最好小于0.15%,一吨AZS-33电熔砖约需0.62吨氧化铝。
2) 锆英砂主要引入2ZrO 和2SiO ,但其中还含有少量的2TiO 和23Fe O ,23Fe O 能使AZS 产品染色,造成粗晶砂眼,同时也影响开裂,故其含量应小于0.2%,2TiO 影响铸件在冷却过程中开裂,另外也会影响产品的氧化工艺,故其含量应限制小于0.2%,吨AZS-33电熔砖约需0.65锆英砂。
3) 富锆砂又称脱硅锆,AZS 中的二氧化硅全部来源于锆英石,2ZrO 不足部分,由富锆砂补充。
4) 纯碱引入氧化钠,作为AZS 砖的助熔剂,一般采用二级品,一吨AZS-33电熔砖约需20kg 纯碱。
5) 硼砂也是AZS 砖的助熔剂,一吨AZS-33电熔砖约需20kg 硼砂。
2 .电弧炉工作原理电弧炉炉体由炉底、炉壁、和炉盖三部分组成,从炉盖插入三根石墨电极,成三角形,在三根电极中心投影位置铺上5-10kg 起弧焦,将焦炭拍实后,让三相电极同步下降,一处焦炭,便引发三极同时起弧,起弧后,缓慢加料,以不击断弧为原则,而电流不超过额定值为宜,一般起弧半小时后,电流便能稳定,其后便进入控制期。
配合料电阻很大,电弧达到配合料上便产生巨大的热量,以此来时配合料熔融。
3 .AZS 熔化原理AZS 熔化的工艺目的有四个:是配合料中的氧化铝熔融并重新结晶为刚玉;是锆英石分解后的氧化锆熔融并重新结晶为斜锆石;用钠硼做变性剂,一直莫来石生成并与二氧化硅生成制品所需的玻璃相;制取化学成分均匀,含碳量少,含气泡最少,并具有一定温度和良好浇铸性能的熔液,以便铸出优质产品。
3.1 熔化过程的物理化学反应1) 氧化铝12002323C r Al O Al O α︒−−−−→--(固)2323Al O Al O αα--−−→(固)(液)液态23Al O α-在冷却时结晶为刚玉2) 锆英石其中主要含硅酸锆,按下式分解:1540422C ZrSiO ZrO Si o ︒−−−−−→+开始22()ZrO ZrO −−→液锆英石的熔点是2430度,但在AZS 中的助熔剂作用下则无需这么高的温度,总之氧化锆要由低温晶型(六方晶系)向高温晶型(四方晶型)转化为斜锆石。
3) 纯碱与硼砂纯碱分解,硼砂分解,然后与锆英石中的二氧化硅及杂质铁钛等熔剂生成硅酸盐玻璃。
2322247222322223223,10210(,gO)Na CO Na O CO Na B O H O Na O B O H OSiO Na O B O TiO Fe O CaO M −−→+⋅−−→+++++−−→,硅酸盐玻璃4) 氧化钠不足熔体中的部分氧化硅生成莫来石,这是制品中不希望存在的结晶。
2322323+232Al O SiO Al O SiO −−→⋅(莫来石) 5) 熔化过程由于电极在不断的燃烧,还发生下列反应:部分氧化硅被炭还原:2+SiO C SiO CO −−→↑+↑22+SiO C Si CO ↑−−→↑+在炉上部较冷的地方,硅被氧化生成二氧化硅,沉淀为白色棉絮状物。
22Si O SiO −−→+↓2222SiO O SiO −−→+↓6) 原料潮湿或配合料吸潮水分在炉内高温作用下分解,产生的氢气边熔解在熔液中,使熔液出现泡沫或不易收缩,从而造成铸件缩孔分散或致密部分出现大量针孔,很多人认为水分会在炉内烘干,但实际观察发现,料层在电弧处直接塌落进入高温熔液,没有干燥阶段,电弧炉温度很高,炉料立即熔结,没有干燥时间,所以炉料必须是干燥无水的才能熔制出致密产品。
4.熔融工艺锆刚玉砖的熔融工艺分为还原法和氧化法两种4.1 还原法还原法又称埋弧法,是将石墨电极沉埋在炉料中,由于电极在缺乏氧气的气氛中燃烧,便发生一系列的还原反应,使熔体中的某些高价氧化物处于低价的不稳定状态,同时炭也渗入熔体,这最终会使熔体的颜色变暗,如果电弧很短或电极处于半埋弧状态,部分弧光裸露虽能减轻熔体的神坛程度,但也属于还原法的范畴。
4.2 氧化法电路中的炉料在融化过程中没有被渗碳或电熔渗炭又在浇铸前脱碳,这种最终使熔体不含炭的工艺方法称为氧化法,又称明弧法。
因为还原法使锆刚玉砖中有炭的存在,在玻璃窑中使用时,高温炭燃烧发出气体将软化的玻璃相挤出,加速了玻璃液对砖的侵蚀,所以炭的存在对锆刚玉砖的耐侵蚀性是不利的,现在多采用氧化法代替还原法,锆刚玉砖中炭的来源主要是石墨电极在放电时未燃烧而随电弧一起进入炉内的,因此要想办法阻止炭入炉。
以下是几种生产中常用得除炭的方法:4.2.1长电弧法:即电极不浸在炉熔体内,从而消除了电极和熔体之间的炭的传递。
此法是让电弧的长度足以使炭在到达熔体之前全部氧化燃烧,以二氧化碳或一氧化碳的形式挥发掉,明弧长度达到50毫米左右时就是长电弧熔融。
利用氩气保护电极的熔融的方法也属于长电弧的范畴,因为电弧本身成为了离子化了的氩气才能抑制炭的氧化或浸入熔液。
因而电极的消耗也很低。
4.2.2 通氧法:同样的形式很多,但都是在还原融化结束之后再将氧气鼓入熔体。
有的将氧枪自炉顶插入,有的将氧枪设置在炉嘴处,使炉体前倾让熔体浸没氧枪进行鼓氧,熔体中的微量炭经过与氧气接触而燃烧逸出。
4.2.3 加入氧化剂法:在配料中加入某些富氧原料,他在熔化过程中能放出氧气,使熔液表面上的炭燃烧挥发,但是孤立的这样做是不行的,一般是先用明弧熔化,在精炼时期用电弧熔化,为了增加电弧的长度和稳定性可加入某些电离物质以使炉内空气电离,作为电离物质的碳酸钠和氧化剂,一起在熔化后期加入。
由于熔液在电弧的搅动下不停的旋动,所以整个炉内的熔体会得到一定程度的净化。
二.砂型的制作1.砂型制备的原料由于AZS 砖的浇铸温度在1800度左右,故其铸型可以采用砂质铸型,砂型原料选用天然砂和石英砂,不同的粒度级配增强了砂型板的强度,石英砂采用细砂和面砂两种,硅含量都在99%以上,每一块砂型板浇铸面都要图一定厚度的面砂,防止杂质污染铸型。
砂型选用的结合剂有很多种,一般选用水玻璃,因为水玻璃来源质量稳定,价廉,易水洗,无异味,而且用水玻璃高纯硅啥制作的砂型能达到以下技术要求:1.1 有较好的透气性由锆刚玉砖熔体中析出的气体能从型壁硅砂颗粒间隙中渗透出去。
1.2 有良好的耐热冲击强度锆刚玉砖在浇铸时产生的热冲击能使砂型的内壁和外壁温度相差很大,但砂型在加热条件下比较稳定,因为其耐火度不低于1690度,它在20-450度之间的线膨胀系数约为0.03mm/度,所以他能承受高温熔液液流的静压而不破裂。
1.3有良好的热机械性能砂型在加热后强度降低,荷软实验表明约320度开始软化,400度开始破坏。
1.4锆刚玉砖表面不产生化学粘砂AZS 熔液和砂型接触后急剧冷却、硬化,砂型表面熔结成一薄层硅酸钠或硅砂,不和AZS 发生反应。
水玻璃的加入量通过实验证实最适宜为5.7%,少则降低砂型的耐火度,多则不能成型。
2.砂型的制作工艺−−−→→−−−→→↓←←←←水玻璃木模石英砂混砂机成型台湿砂型砂型架电炉铸型组型干砂型干燥炉制作好的比较大的湿砂型在入炉的搬运过程中常常会出现裂纹,为了使其具有一定的强度,常在砂型上插几个孔,然后向里面充二氧化碳,23222323Na SiO H O CO H SiO Na CO ++→↓+硅酸溶解度小,形成沉淀,所以湿砂型能在短时间内具有一定的强度。
制作好的砂型要放到电阻炉中烘干,使其具有一定的强度,以备浇铸使用,烘干温度上限在400度左右。
三.浇铸配合料在电弧炉中经过熔化和精炼阶段后达到浇铸标准以后,将将熔融液由电炉直接浇入铸型的操作过程称为浇铸。
此过程虽然短暂,但每一步都关系到最后产品的质量,是一个复杂的工艺阶段。
这里只介绍一下我国熔铸材料常用的几种方法:1. 浇铸的方法1.1普通浇铸法(代号:中国PT ,康宁、旭、东芝RC ,西普RN ):铸件采用普通的冒口浇铸,并在热态 时铲除冒口,其断面分为两个部分,一部分先固化,结晶细密,该区占铸件厚度的40%-50%,另一部分后固化,存在缩孔和粗大结晶。
用这种方法浇铸的砖价格较低,多用于窑的上部结构,澄清池壁等处。
1.2 倾斜浇铸法(代号:中国QX ,康宁TA 、旭TC 、东芝TCL ,西普RO ):倾斜浇铸法是在浇铸之前将铸型造成一个角度,并将冒口放到铸型的一端进行浇铸,这样既能在T 部得到一个致密区,又可利用普通模具在T 方向上得到较高的精确度。
所以用这种铸件砌筑池壁时,便可利用它的高度。
1.3 无缩孔浇铸(代号:中国WS ,康宁VF 、旭VF 、东芝DCL ,浇铸,将缩孔集中在某一区域内,退火后用金刚石锯把他切除,剩余的有用部分成分均匀,组织致密,其平均体积密度接近理论密度;另一种是切割铸腿法:从减少切割面积出发,将铸件浇铸成“L ”型,使缩孔的绝大部分集中在“L ”较小的腿上,此腿体积占铸件总体积的60%,整个铸件在退火时一直埋在保温材料里,并保持倾斜以促使缩孔向腿上集中。