长输管道腐蚀缺陷的评价
浅析长输压力管道无损检测技术
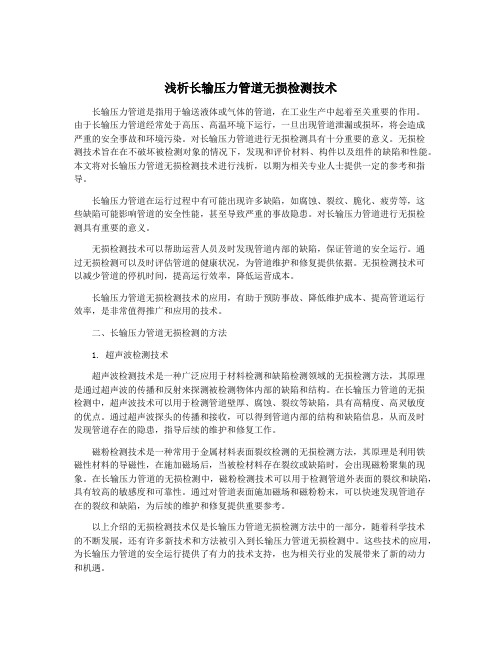
浅析长输压力管道无损检测技术长输压力管道是指用于输送液体或气体的管道,在工业生产中起着至关重要的作用。
由于长输压力管道经常处于高压、高温环境下运行,一旦出现管道泄漏或损坏,将会造成严重的安全事故和环境污染。
对长输压力管道进行无损检测具有十分重要的意义。
无损检测技术旨在在不破坏被检测对象的情况下,发现和评价材料、构件以及组件的缺陷和性能。
本文将对长输压力管道无损检测技术进行浅析,以期为相关专业人士提供一定的参考和指导。
长输压力管道在运行过程中有可能出现许多缺陷,如腐蚀、裂纹、脆化、疲劳等,这些缺陷可能影响管道的安全性能,甚至导致严重的事故隐患。
对长输压力管道进行无损检测具有重要的意义。
无损检测技术可以帮助运营人员及时发现管道内部的缺陷,保证管道的安全运行。
通过无损检测可以及时评估管道的健康状况,为管道维护和修复提供依据。
无损检测技术可以减少管道的停机时间,提高运行效率,降低运营成本。
长输压力管道无损检测技术的应用,有助于预防事故、降低维护成本、提高管道运行效率,是非常值得推广和应用的技术。
二、长输压力管道无损检测的方法1. 超声波检测技术超声波检测技术是一种广泛应用于材料检测和缺陷检测领域的无损检测方法,其原理是通过超声波的传播和反射来探测被检测物体内部的缺陷和结构。
在长输压力管道的无损检测中,超声波技术可以用于检测管道壁厚、腐蚀、裂纹等缺陷,具有高精度、高灵敏度的优点。
通过超声波探头的传播和接收,可以得到管道内部的结构和缺陷信息,从而及时发现管道存在的隐患,指导后续的维护和修复工作。
磁粉检测技术是一种常用于金属材料表面裂纹检测的无损检测方法,其原理是利用铁磁性材料的导磁性,在施加磁场后,当被检材料存在裂纹或缺陷时,会出现磁粉聚集的现象。
在长输压力管道的无损检测中,磁粉检测技术可以用于检测管道外表面的裂纹和缺陷,具有较高的敏感度和可靠性。
通过对管道表面施加磁场和磁粉粉末,可以快速发现管道存在的裂纹和缺陷,为后续的维护和修复提供重要参考。
长输管道腐蚀缺陷检测技术与应用
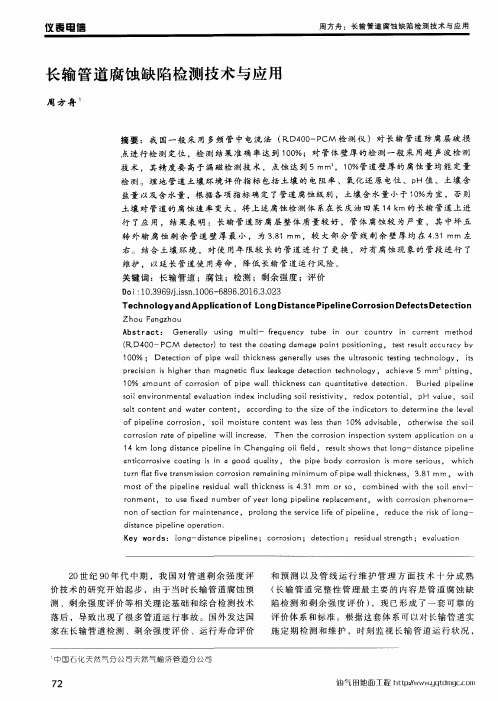
20世 纪 9O年 代 中期 ,我 国对 管 道 剩 余 强度 评 和 预 测 以及 管 线 运 行 维 护 管理 方 面技 术 十分 成 熟 价技 术 的研究 开始起 步 ,由于当 时长输 管道腐 蚀预 (长输 管 道 完整 性管 理 最 主要 的 内容 是管 道 腐蚀 缺 测 、剩余 强度 评价 等相 关理论 基 础和综 合检 测技术 陷检测 和 剩余 强 度评 价 ),现 已形成 了一 套 可靠 的 落后 ,导致 出现 了很多 管道 运行 事故 。 国外 发达 国 评 价体 系和标 准 。根据 这套 体系可 以对 长输 管道 实 家 在长 输管道 检测 、剩 余强 度评 价 、运 行 寿命评 价 施 定 期 检 测 和 维 护 , 时 刻 监 视 长 输 管 道 运 行 状 况 ,
仪 表电 信
周方舟:长输管道腐蚀缺陷测 技 术 与应 用
周 方 舟
摘 要 :我 国一般 采 用 多频 管 中电流 法 (R.D400一PCM 检 测仪 )对 长输 管 道 防腐 层破 损 点进行 检 测定 位 ,检 测结 果 准确 率达 到 1 00%;对 管体 壁厚 的检 测一般 采 用超 声 波检 测 技 术 ,其 精度要 高 于漏磁检 测技 术 ,点蚀 达到 5 mm ,1 O%管道 壁厚 的腐 蚀 量均 能定 量 检 测 。埋 地 管道 土壤 环境评 价 指标 包括 土壤 的 电 阻率 、氧化 还 原 电位 、pH值 、土壤 含 盐量 以及含 水量 ,根 据各 项指标 确 定 了管道腐蚀 级 别 ,土壤 含 水量 小于 10%为宜 ,否则 土壤 对 管道 的腐蚀 速率 变大 。将上 述腐蚀 检 测体 系在 长庆 油田 某 1 4 km的长输 管道 上进 行 了应 用 ,结 果表 明 :长输 管道 防 腐层 整 体质 量较 好 ,管体 腐 蚀较 为 严重 ,其 中坪 五 转 外输 腐 蚀 剩 余 管道 壁 厚 最 小 ,为 3.81 mm,较 大部 分 管线 剩 余 壁厚 均 在 4_31 mm左 右 。结合 土壤 环境 ,对使 用年 限较 长 的 管道进 行 了更换 ,对有 腐蚀 现 象的 管段 进 行 了 维护 ,以延 长 管道使 用寿命 ,降低 长 输 管道 运行 风险 。 关键 词 :长输管 道 ;腐 蚀 ;检测 ;剩余 强度 ;评 价
ICDA管道内腐蚀直接评价方法探析
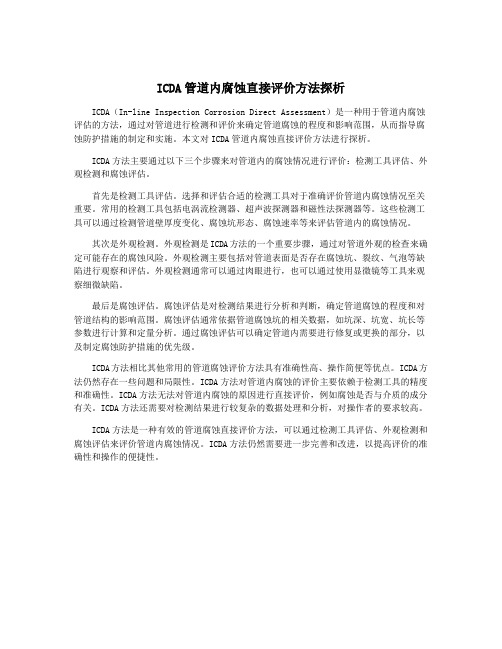
ICDA管道内腐蚀直接评价方法探析ICDA(In-line Inspection Corrosion Direct Assessment)是一种用于管道内腐蚀评估的方法,通过对管道进行检测和评价来确定管道腐蚀的程度和影响范围,从而指导腐蚀防护措施的制定和实施。
本文对ICDA管道内腐蚀直接评价方法进行探析。
ICDA方法主要通过以下三个步骤来对管道内的腐蚀情况进行评价:检测工具评估、外观检测和腐蚀评估。
首先是检测工具评估。
选择和评估合适的检测工具对于准确评价管道内腐蚀情况至关重要。
常用的检测工具包括电涡流检测器、超声波探测器和磁性法探测器等。
这些检测工具可以通过检测管道壁厚度变化、腐蚀坑形态、腐蚀速率等来评估管道内的腐蚀情况。
其次是外观检测。
外观检测是ICDA方法的一个重要步骤,通过对管道外观的检查来确定可能存在的腐蚀风险。
外观检测主要包括对管道表面是否存在腐蚀坑、裂纹、气泡等缺陷进行观察和评估。
外观检测通常可以通过肉眼进行,也可以通过使用显微镜等工具来观察细微缺陷。
最后是腐蚀评估。
腐蚀评估是对检测结果进行分析和判断,确定管道腐蚀的程度和对管道结构的影响范围。
腐蚀评估通常依据管道腐蚀坑的相关数据,如坑深、坑宽、坑长等参数进行计算和定量分析。
通过腐蚀评估可以确定管道内需要进行修复或更换的部分,以及制定腐蚀防护措施的优先级。
ICDA方法相比其他常用的管道腐蚀评价方法具有准确性高、操作简便等优点。
ICDA方法仍然存在一些问题和局限性。
ICDA方法对管道内腐蚀的评价主要依赖于检测工具的精度和准确性。
ICDA方法无法对管道内腐蚀的原因进行直接评价,例如腐蚀是否与介质的成分有关。
ICDA方法还需要对检测结果进行较复杂的数据处理和分析,对操作者的要求较高。
ICDA方法是一种有效的管道腐蚀直接评价方法,可以通过检测工具评估、外观检测和腐蚀评估来评价管道内腐蚀情况。
ICDA方法仍然需要进一步完善和改进,以提高评价的准确性和操作的便捷性。
含腐蚀缺陷管道的安全评价
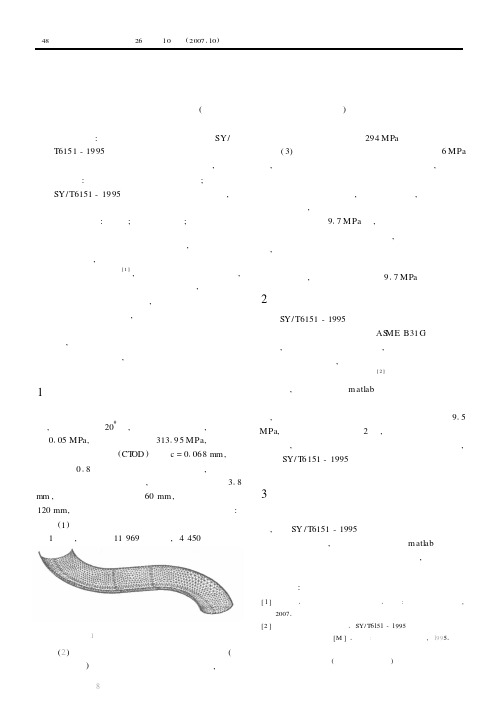
含腐蚀缺陷管道的安全评价吴绍明(福建省南平市锅炉压力容器检验所) 摘要:分别用有限元法和标准SY/T6151-1995的方法分析计算了含腐蚀性体积缺陷弯管的极限载荷和安全服役状况,结果表明:两种方法的计算结果接近;标准SY/T6151-1995所编制的分析评定软件,可简便而有效地评价管道腐蚀损伤。
关键词:管道;腐蚀性缺陷;安全评价 石油天然气管道服役时间比较长,普遍存在腐蚀性体积缺陷,以及第三方破坏、地质灾害和误操作等因素造成的损伤[1],为保障管道的安全运行,避免管体腐蚀所导致的爆裂、泄漏事故,确定是否需要立即停产检修更换管段,或因生产繁忙暂时不能停产而采取降压运行,需要及时发现缺陷并评估其安全可靠性。
鉴于含缺陷管道的极限应力分析比较复杂,本文试用有限元法分析某一天然气管道的极限强度及安全状况,并与有关评价标准进行了对比。
1 管道极限载荷的有限元分析本文研究对象为一含硫天然气输送管道的弯管段,管道材质为20#钢,工作温度为常温,工作压力0105MPa,最小屈服强度313195MPa,管材的裂纹尖端张开位移(CT OD )值δc =01068mm ,焊缝系数为018。
该管段在内部介质作用下,出现比较严重的腐蚀和减薄现象,最大蚀坑深度为318mm ,最大纵向投影长度60mm ,环向腐蚀长度120mm,利用有限元法分析其极限承载情况如下:(1)有限元模型。
管段的有限元单元模型如图1所示,共划分11969个单元,4450个节点。
图 含蚀坑管道有限元单元模型()材料的本构模型。
材料的本构模型(应力应变关系)用双线性表示。
经计算分析,材料的塑性极限许用应力值为294MPa 。
(3)弯管的弹塑性分析。
当内压增大到6MPa 时,管道内弯处局部材料开始进入屈服状态,但其屈服区域较小。
此时屈服区域外围未屈服的材料可限制屈服区域材料的变形,随载荷的增加,管道不会无限制地变形,因此管段还有进一步承载的能力。
当内压达到917MPa 时,最大应力处沿厚度方向整体屈服。
输气管道内腐蚀缺陷剩余强度评估方法分析
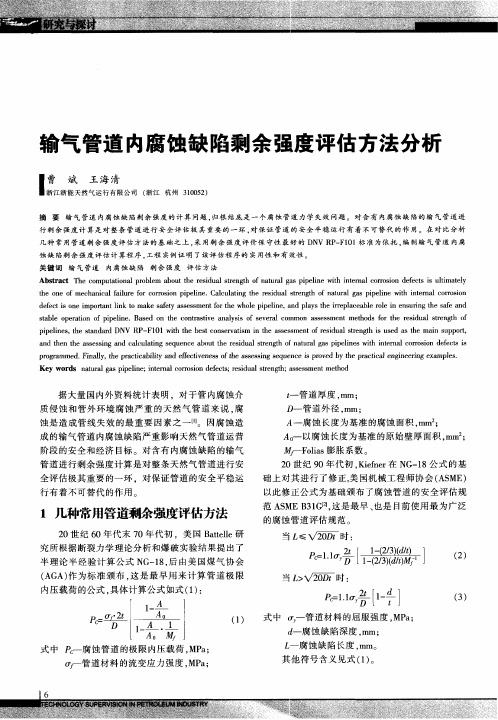
p i p e l i n e s , t h e s t a n d a r d DNV RP - F I O 1 wi t h t h e b e s t c o n s e r v a t i s m i n t h e a s s e s s me n t o f r e s i d u a l s t r e n th g i s u s e d a s t h e ma i n s u p p o t, r
输气 管道 内腐蚀缺 陷剩余 强度评估 方法分析
l 浙 然 公 司 浙 江 ㈤ 。 。
摘 要 输 气 管道 内腐 蚀 缺 陷剩 余 强度 的计 算 问题 , 归根 结底 是 一 个 腐 蚀 管道 力 学失 效 问题 。 对 含 有 内腐 蚀 缺 陷的 输 气管 道 进 行 剩余 强度 计 算 是 对 整 条 管道 进 行 安 全评 估 极 其 重要 的 一 环 . 对 保 证 管道 的安 全 平 稳 运 行 有 着不 可 替 代 的 作 用 。在 对 比分 析
据大 量 国内外 资料 统计表 明 ,对于管 内腐 蚀介 质侵 蚀 和 管外 环境 腐 蚀严 重 的天然 气 管 道来 说 . 腐 蚀 是造 成 管线 失 效 的最 重要 因素 之- -[ ” 。 因腐 蚀造 成 的输气 管道 内腐 蚀缺 陷严 重影 响天然 气管 道运 营 阶段 的安全 和经济 目标 。对 含有 内腐蚀 缺 陷的输气
腐蚀管道的剩余强度评价
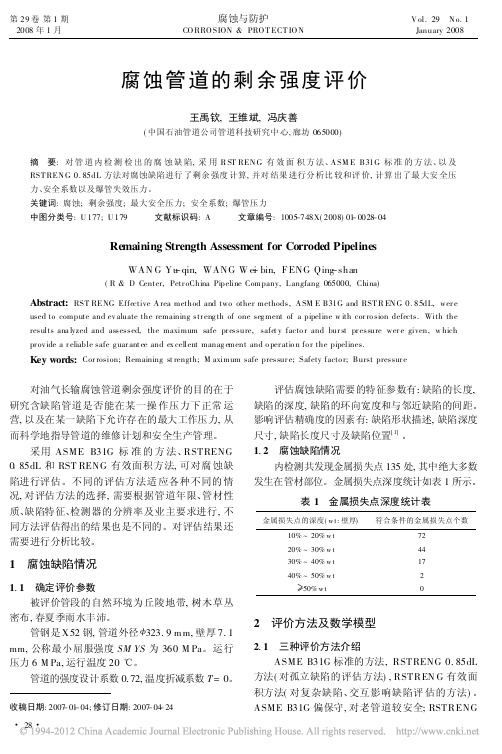
d Pc3 = 1 . 1P 1 ( 10) t 式中 : L total 是腐蚀缺陷长度 , d 是腐蚀缺陷深度, t 是
# 29 #
王禹钦等 : 腐蚀管道的剩余强度评价
管壁厚度 , D 是管道外径 , M 3 是 F olias 因子。 1 + 0. 8 L Dt 预测的爆管失效压力 P burs t3 M3 = 对于 L total [ 20: Dt 2t = 1. 1 D S M YS 11- 2 3 2 3 d t d 1 M3 t ( 12) 对于 L total > 20: Dt P burst3 = 1. 1 2t SM YS 1 - d D t ( 13)
第 29 卷 第 1 期 2008 年 1 月
腐蚀与防护
CO RRO SION & PRO T ECT IO N
V ol. 29 N o. 1 January 2008
腐蚀管 道的剩 余强度评 价
王禹钦, 王维斌, 冯庆善
( 中国石油管道公司管道科技研究中 心 , 廊坊 065000) 摘 要 : 对 管 道 内 检 测 检 出 的 腐 蚀 缺 陷 , 采 用 R ST REN G 有 效 面 积 方 法、 A SM E B31G 标 准 的 方 法、 以及
金属损失点的深度 ( w t : 壁厚) 10% ~ 20% w t 20% ~ 30% w t 30% ~ 40% w t 40% ~ 50% w t \ 50% w t 符合条件的金属损失点个数 72 44 17 2 0
浅析长输管道清管及内检测
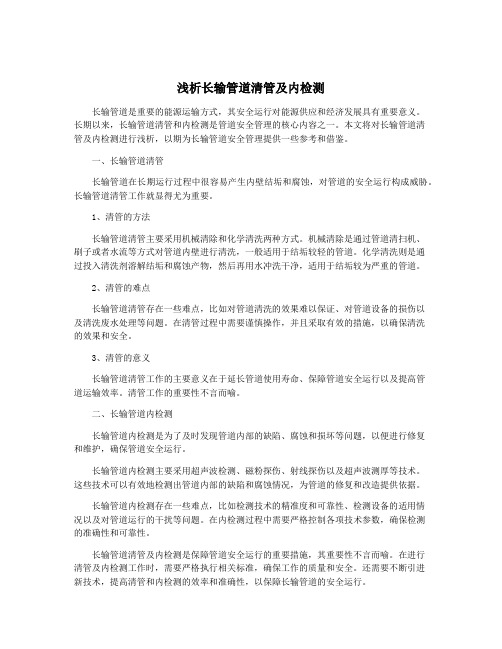
浅析长输管道清管及内检测长输管道是重要的能源运输方式,其安全运行对能源供应和经济发展具有重要意义。
长期以来,长输管道清管和内检测是管道安全管理的核心内容之一。
本文将对长输管道清管及内检测进行浅析,以期为长输管道安全管理提供一些参考和借鉴。
一、长输管道清管长输管道在长期运行过程中很容易产生内壁结垢和腐蚀,对管道的安全运行构成威胁。
长输管道清管工作就显得尤为重要。
1、清管的方法长输管道清管主要采用机械清除和化学清洗两种方式。
机械清除是通过管道清扫机、刷子或者水流等方式对管道内壁进行清洗,一般适用于结垢较轻的管道。
化学清洗则是通过投入清洗剂溶解结垢和腐蚀产物,然后再用水冲洗干净,适用于结垢较为严重的管道。
2、清管的难点长输管道清管存在一些难点,比如对管道清洗的效果难以保证、对管道设备的损伤以及清洗废水处理等问题。
在清管过程中需要谨慎操作,并且采取有效的措施,以确保清洗的效果和安全。
3、清管的意义长输管道清管工作的主要意义在于延长管道使用寿命、保障管道安全运行以及提高管道运输效率。
清管工作的重要性不言而喻。
二、长输管道内检测长输管道内检测是为了及时发现管道内部的缺陷、腐蚀和损坏等问题,以便进行修复和维护,确保管道安全运行。
长输管道内检测主要采用超声波检测、磁粉探伤、射线探伤以及超声波测厚等技术。
这些技术可以有效地检测出管道内部的缺陷和腐蚀情况,为管道的修复和改造提供依据。
长输管道内检测存在一些难点,比如检测技术的精准度和可靠性、检测设备的适用情况以及对管道运行的干扰等问题。
在内检测过程中需要严格控制各项技术参数,确保检测的准确性和可靠性。
长输管道清管及内检测是保障管道安全运行的重要措施,其重要性不言而喻。
在进行清管及内检测工作时,需要严格执行相关标准,确保工作的质量和安全。
还需要不断引进新技术,提高清管和内检测的效率和准确性,以保障长输管道的安全运行。
缺陷评价标准
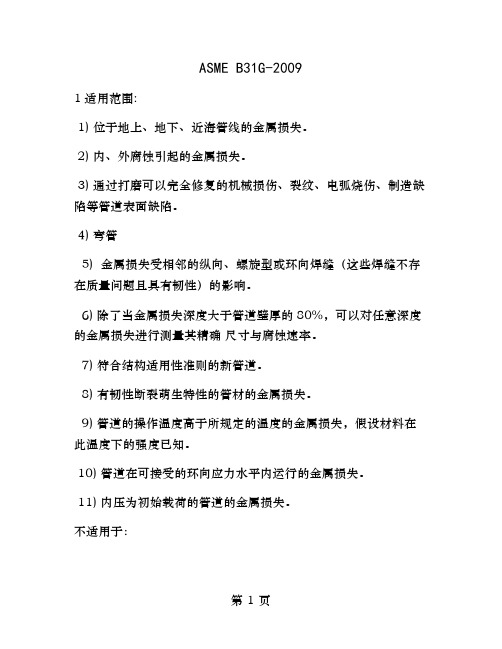
ASME B31G-20091适用范围:1) 位于地上、地下、近海管线的金属损失。
2) 内、外腐蚀引起的金属损失。
3) 通过打磨可以完全修复的机械损伤、裂纹、电弧烧伤、制造缺陷等管道表面缺陷。
4) 弯管5) 金属损失受相邻的纵向、螺旋型或环向焊缝(这些焊缝不存在质量问题且具有韧性)的影响。
6) 除了当金属损失深度大于管道壁厚的80%,可以对任意深度的金属损失进行测量其精确尺寸与腐蚀速率。
7) 符合结构适用性准则的新管道。
8) 有韧性断裂萌生特性的管材的金属损失。
9) 管道的操作温度高于所规定的温度的金属损失,假设材料在此温度下的强度已知。
10) 管道在可接受的环向应力水平内运行的金属损失。
11) 内压为初始载荷的管道的金属损失。
不适用于:1) 通过打磨仍不能恢复其光滑外形的裂纹型缺陷与表面机械损伤型缺陷。
2) 当管壁上由凹陷或褶曲导致的径向变形大于管道外壁的6%(除非依照三级评价参数与 2.3保持一致)。
3) 槽型腐蚀、选择性腐蚀或优先腐蚀对管道接缝与环形焊缝的影响。
4) 除了弯头弯管其他配件的金属损失。
5) 影响材料萌生脆性断裂的金属损失。
6) 管道运行的温度超出了标准允许操作温度范围,或工作温度在蠕变范围。
格外考虑:在一些特殊情况下,用户也要做格外的考虑,如下:1) 管道由于内压不足(如低于25%SMYS)在低环向应力条件下运行,易发生腐蚀从而导致穿孔,该标准里的方法不能解决此类穿孔失效问题。
2) 受均匀腐蚀的管壁(如因腐蚀而导致整个管道表面减薄)可以在一个较高的环向应力(高于原始管壁的额定环向应力)下有效运行。
评价均匀腐蚀区内存在的深凹陷对管道的影响时,应该考虑到均匀腐蚀造成的管壁减薄对管道的影响。
3) 对于普通的埋地管道,由内压引起的环向应力最大,它将会控制管道的失效形式。
在非固定管道上,大面积圆周范围的金属损失受拉伸作用产生高的纵向应力,该应力可以从纵向与环向改变失效形式。
该标准里所提供的方法不能够处理由很高的纵向拉伸应力而产生的环向失效。
长输管道检验中合于使用评价标准应用分析

长输管道检验中合于使用评价标准应用分析摘要:长输管道油气输送是公路、铁路、水路、航空运输之后的另一大运输方式,能够完成对商品介质在场地、储存库等单位之间的输送工作。
但是管道会受到输送过程中的腐蚀作用、疲劳问题影响,以及外力作用,导致管道可能会出现损伤,所以必须使用全面检验保证管道安全。
本文对合于使用评价在长输管道全面检验中的应用进行了讨论,分析应用的情况和问题,然后给出合于使用评价建议,以供参考。
关键词:长输管道检验,合于使用评价,标准应用,分析1、合于使用评价在长输管道全面检验中应用1.1 全面检验的地位与作用全面检验是特种设备检验机构按照一定的时间周期,在受检设备停机时对在用压力容器的安全状况进行的符合性验证活动,适用于压力容器、工业管道、锅炉类承压设备的定期检验。
比较成熟的容器和锅炉均是通过全面检验确定检验周期的,实施定期检验相对晚的工业管道定期检验也是通过全面检验确周期的。
1.2 实际检验与检验周期矛盾按《定检规》规定,长输管道定期检验分为年度检查、全面检验和合于使用评价。
其中全面检验的检验周期需要通过进一步实施合于使用评价来确定,所以合于使用评价实际上被强制性包含在全面检验中。
这种强制性包含关系与检验实践、长输管线及企业惯用做法等实际情况存在一定的矛盾。
首先,在实际检验工作中全面检验检出的缺陷大多为防腐层破损、阴极保护缺失、标示桩和警示桩丢失、露管、违规穿越和跨越等现象。
同时,长输管道直管段基本上不存在较大应力(除了泵、阀站等部位可能会有疲劳应力以外),因此实施合于使用评价的必要性很小。
其次,合于使用评价是在一定条件下开展的材料适用性评价,包括对管道进行的应力分析计算、对危害管道结构缺陷进行的剩余强度评估与超标缺陷安全评定,以及对危害管道安全的主要潜在危险因素进行的管道剩余寿命预测等多项复杂技术工作,因其实施费用高,企业在发现管体缺陷时通常会直接更换管道或者补焊管道,这种情况下完全没有必要再实施合于使用评价。
毕业论文-长输管道基于风险的评价方法
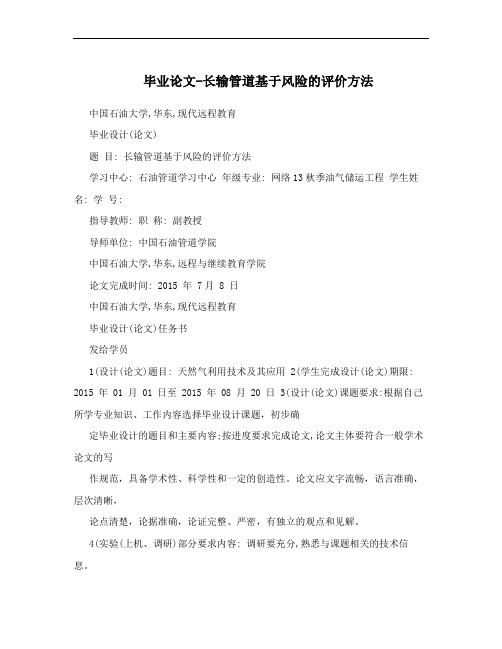
毕业论文-长输管道基于风险的评价方法中国石油大学,华东,现代远程教育毕业设计(论文)题目: 长输管道基于风险的评价方法学习中心: 石油管道学习中心年级专业: 网络13秋季油气储运工程学生姓名: 学号:指导教师: 职称: 副教授导师单位: 中国石油管道学院中国石油大学,华东,远程与继续教育学院论文完成时间: 2015 年 7月 8 日中国石油大学,华东,现代远程教育毕业设计(论文)任务书发给学员1(设计(论文)题目: 天然气利用技术及其应用 2(学生完成设计(论文)期限: 2015 年 01 月 01 日至 2015 年 08 月 20 日 3(设计(论文)课题要求:根据自己所学专业知识、工作内容选择毕业设计课题,初步确定毕业设计的题目和主要内容;按进度要求完成论文,论文主体要符合一般学术论文的写作规范,具备学术性、科学性和一定的创造性。
论文应文字流畅,语言准确,层次清晰,论点清楚,论据准确,论证完整、严密,有独立的观点和见解。
4(实验(上机、调研)部分要求内容: 调研要充分,熟悉与课题相关的技术信息。
5(文献查阅要求:参考文献反映毕业设计(论文)的取材来源、材料的广博程度和材料的可靠程度。
参考文献不宜过多,只列作者直接阅读过、在正文中被引用过的中外文献资料。
6(发出日期: 2015 年 01 月 01 日7(学员完成日期: 2015 年 7月 8 日指导教师签名: 王学东学生签名: 程慧荣摘要管道风险评价普遍采用以Kent打分法为代表的定性方法,本文提出了一种新方法,即定量风险评价(QRA),采用基于管道失效历史数据库和巳有成熟的数值模型,进行管道失效概率分析和失效后果分析,并以此方法在某输气管道上进行了验证,最后得到管段的绝对风险和人口密集段的个人风险,并进行了风险预剥。
研究表明,QRA受人员主观判断影响较小,计算方法科学合理,结果量化,对进行检测与维护维修资源的分配具有很好的指导意义。
关键词:管道,定量风险评价法(QRA),个人风险,失效历史数据库,完整性管理目录第1章前言………………………………………………………………………………….1第2章管道定量风险评价(QRA)简介……………………………………………………….1 第3章 QRA的主要技术…………………………………………………………………….2 3.1 管道失效概率分析…………………………………………………………………….3 3.2 管道失效后果的计算………………………………………………………………….4 3.3 风险的计算…………………………………………………………………………….4 第4章 QRA实例..................................................................................5 第5章结论. (8)参考文献..............................................................................................10 致谢. (11)第1章前言管道风险评价按照最后结果的量化程度,可以分为定性方法、定量方法两种。
油气长输腐蚀管道剩余强度评价技术研究

油气长输腐蚀管道剩余强度评价技术研究作者:焦江明王志强张露来源:《科技资讯》 2014年第2期焦江明王志强张露(塔里木油田塔西南分公司新疆塔里木 844804)摘要:油气管线在输送环境及输送介质的影响下发生腐蚀的现象在所难免,必须剩余强度评价腐蚀的管线,才能为管线的更换、修复、继续服役提供科学、正确决策。
文章对评价相关油气长输管线腐蚀曲线剩余强度的软件进行简要介绍,使评价具有可靠性。
关键词:分级评价;剩余强度评价;服饰缺陷;油气管线中图分类号:TE988.2 文献标识码:A文章编号1672-3791(2014)01(c)-0000-00长输管道在腐蚀性较强的土壤地段受到严重危害,特别是城镇地区,环境保护措施实施的效果不显著、以及工业生产发展速度过快等原因,局部土壤在大量工业废水排放后,增强了腐蚀性,而越来越强的土壤腐蚀性也加速着长输管道的腐蚀程度,腐蚀性穿孔漏油的可能性也就增大了。
油气技术能力的提升受到管道故障的严重影响与制约,与此同时增加了改造、维修的费用,而从另一方面来看,管线事故的发生在对生态环境造成破坏的同时,更严重的是会对人身安全产生直接威胁。
因此,腐蚀管道剩余强度的确定、确保管道可靠、安全地运行是亟待解决的课题。
1腐蚀原因概述腐蚀是自然现象,是一个自然的过程,并且是一种破坏,在电化学或者化学的作用下,金属的元素状态转变为离子状态就是腐蚀。
水、气、油等存在于油气管线的管内,管道内壁上的水会产生亲水膜,最终发生电化学腐蚀,或者二氧化碳、硫化物、硫化氢等有害物质与金属直接发生作用所引发的化学腐蚀都属于内壁腐蚀。
尤其是在管道气液交界面、低洼积水处、管道弯头等处,具有强烈的电化学腐蚀,这样,一系列腐蚀深坑就形成于管壁上。
相对于内壁,外壁腐蚀的情况更为复杂,对其的分析也必须从所处管道环境展开。
水中或土壤中的管道容易受到杂散电流腐蚀、细菌腐蚀、土壤腐蚀等。
而大气腐蚀则会给架空管道带来影响。
管道的防腐层一旦遭到破坏,环境条件的腐蚀会直接侵犯外壁。
含腐蚀缺陷管道安全评价准则选择探讨

pf
=
2tσ
f
1−
d t
D
−
t
1
−
d Qt
(7)
式中流变应力σ f = σ b ,Q缺陷长度校正系数。 2.5 PCORRC评价准则
图1 管道缺陷评价准则比较
技
P C O R R C 评 价 准 则 ( P i p e l i n e C o r r o s i o n 3 结语
术
Criterion)针对X65~X80中高强度等级管道因塑性
经验交流 Experience Exchange
含腐蚀缺陷管道
安全评价准则选择探讨
王风雷
(中国石油管道局工程有限公司第四分公司,河北 廊坊 065000)
摘 要:外腐蚀是威胁管道安全的重要因素,极易导致管道泄漏或失效断裂事故。我国长
输管道全面实施完整性管理,应根据管道历史失效事件,开展管道剩余强度评价与剩余寿命预
evaluation criteria. Key words: long distance pipeline; corrosion defect; failure; evaluation; criterion; accuracy
作者简介:王风雷 (1975-) ,河北廊坊人,工程师,主要从事管道工程项目管理工作。
式中流变应力σ f = σb ;R管道外径和内径的
平均值,mm。
(3)BS 7910准则、DNV RP-F101准则和 PCORRC准则适用于中高钢级含缺陷管道安全性评
2.6 管道缺陷安全评价准则比选
价,其中DNV RP-F101准则和 PCORRC准则最优;
收集50例不同钢级(X42~X100)含腐蚀缺陷
(1)根据管道运行状况和缺陷特征,考虑上述
腐蚀管道体积型缺陷评价方法

腐蚀管道体积型缺陷评价方法杨绪运;何仁洋;刘长征;周吉祥;黄辉【摘要】结合管道完整性管理和合于适用评价的管理理念,重点介绍了6种评价腐蚀管道体积型缺陷的方法,并对他们在流变应力、缺陷形状、鼓胀修正因子方面的差异进行了对比分析.最后介绍了一种国内科技工作者研究的评价方法,该方法考虑了弯矩、拉伸的组合作用,可科学准确地计算出腐蚀管道的剩余强度.便于评估人员选择合适的评价方法,确保管道安全运行管理.【期刊名称】《管道技术与设备》【年(卷),期】2009(000)001【总页数】4页(P47-50)【关键词】腐蚀管道;体积型缺陷;完整性管理;评价方法【作者】杨绪运;何仁洋;刘长征;周吉祥;黄辉【作者单位】中国特种设备检测研究院,北京,100013;中国特种设备检测研究院,北京,100013;中国特种设备检测研究院,北京,100013;中国特种设备检测研究院,北京,100013;中国特种设备检测研究院,北京,100013【正文语种】中文【中图分类】U179.8管道完整性[1]是指管道要始终处于安全可靠的受控工作状态,管理人员可不断采取措施防止管道事故的发生。
而目前国内管道的管理中,对管线仅进行简单的检测、修补,没有从更深层面考虑。
管理过程中,管道的腐蚀不是单一问题,而要从管道整个寿命周期的各个环节考虑,如何预测事故发生的时间,以及发生事故的严重程度,同时分析事故原因,如腐蚀可能是设计不当、制造缺陷、腐蚀防护系统缺陷造成的,而不是简单地局限于腐蚀本身。
目前,管道完整性管理程序主要有《managing system integrity of gas pipeline》(ASME B31.8S)[2]以及《managing system integrity for hazardous liquid pipelines》。
合于适用是只要管道在结构还未达到失效,则结构就能够满足使用要求。
合于适用评价要考虑结构发生事故的可能性和失效后果,从而产生了风险检测的概念。
长输管线防腐涂层失效的原因分析

长输管线防腐涂层失效的原因分析【摘要】对输油管线管体进行腐蚀漏磁检测,管线腐蚀属于氧去极化腐蚀,主要形式为局部腐蚀。
测试了管线经过地段土壤的土壤电阻率和管地电位等,土壤属于强腐蚀类。
管线焊口部位的裂纹、残余应力及管道在穿、跨越附近侧下方土壤的氧浓差电池是引起穿孔的主要部位,而防腐层破损加上杂散电流作用是引起防腐层开裂主要原因。
【关键词】输油管线防腐涂层失效分析1 前言原油管道采用防腐层及阴极保护联合保护方式。
外防腐层主要采用加强级熔接环氧粉末,简称FBE。
FBE防腐层的特点是其对管体的粘结力强,具有优良的抗阴极剥离、抗土壤应力、抗化学介质腐蚀和耐老化性能;缺点是抗冲击性能差,吸水率偏高,在土壤湿度大的地段容易产生鼓泡。
影响防腐层老化与失效的因素较多,各种自然因素、环境因素和人为因素均可以造成防护措施的失效,从而使材料直接暴露在腐蚀性介质中,造成设备及管线在服役期内提前失效。
对于FBE防腐层,涂层成分、固化程度、运行环境、介质离子状况等都可以影响其老化和失效。
本文研究了原油管线管道的防腐涂层,通过目检、测厚、现场测量涂层机械性能、电火花检测等方法直接检查管段防腐层现状,对现场取样进行SEM、红外、能谱等方法对微观形貌及涂层结构、化学键状态进行深入研究,分析原油管线管道防腐涂层现状及失效原因。
2 实验方法检测地点地貌为水田旁,挖开点有积水;管线特征为管直径610mm。
分别采用PosiTector6000测厚仪测量涂层厚度、PosiTest附着力测试仪测量涂层附着力、电火花对涂层捡漏、扫描电镜观察涂层微观形貌、红外和能谱分析涂层官能团。
3 结果分析3.1 防腐涂层现场检测图1a是挖开点涂层的宏观形貌,可见涂层出现了不同程度的暗斑块;涂层底部有部分管线金属露出来,发生了腐蚀(图1b);并且涂层可成片用小刀剥落(图1c)。
涂层漏点较多,达到了10个,附着力为3.75MPa,涂层厚度为454μm。
对于管道外防腐层来说,涂层的附着力检测是相当重要的指标,越来越受到学术界的重视。
3. 含腐蚀缺陷管道剩余强度评价

含腐蚀缺陷管道剩余强度评价方法SY/T 6151(ASME B31G )要点符号说明:D是管道的名义外径 mm t是管道名义壁厚 mmL腐蚀金属损失缺陷的轴向长度mm d实测的腐蚀区域最大深度 mm m L腐蚀允许轴向长度 mm‘P腐蚀区域最大安全运行压力 MPaMAOP 是指在根据适用的设计规范和规定确定的界限下,管道或管段可能操作的最大压力 MPa0P 为MAOP 与设计压力D2StFTP 之间的较大值 MPa S 管材屈服强度 MPa F 管道设计强度系数 T 管道设计温度系数1、缺陷剩余强度评价方法介绍本缺陷评价方法基于ASME B31G 。
该评估方法只使用两个缺陷参数(深度和长度)来评估在什么样的运行压力下有缺陷的管道不会发生断裂,主要用于对孤立缺陷进行评估。
在ASME B31G 中,缺陷环向宽度对破坏压力的影响可以忽略,因此在评价中不考虑宽度因素。
在ASME B31G 方法中,腐蚀缺陷的形态近似成抛物线形或半椭圆形。
图1 ASME B31G 缺陷强度评价方法参数2、缺陷评价流程1)测量腐蚀区域的最大深度d 并与管道壁厚t 相比如果缺陷的腐蚀深度小于10%名义壁厚(%10td<),该含缺陷管道可以继续留用。
不需要对缺陷进行修复。
但需要对缺陷进行防腐,防止缺陷的进一步扩大。
如果缺陷的腐蚀深度大于80%名义壁厚(%80td>),该含缺陷管道必须停输并换管。
2)对于缺陷的腐蚀深度介于10%~80%的情况,需要计算腐蚀允许轴向长度L m 并将L m 与实际腐蚀长度L 相比。
Dt B 12.1L m =B 是管道的腐蚀系数,按下列规定取值:当%5.17%10<<td时,B=4.0当%5.17>td时,115.01.12-⎪⎪⎭⎫ ⎝⎛-=t d t d B 3)如果L m >L ,则含缺陷管道可以留用。
但要做好防腐,防止缺陷的进一步扩大。
4)如果L m <L ,则需要计算腐蚀区域最大安全运行压力‘P ,并将‘P 与管道最大允许操作压力MAOP 比较。
优化腐蚀剩余寿命评价方法在油气长输管道中的应用
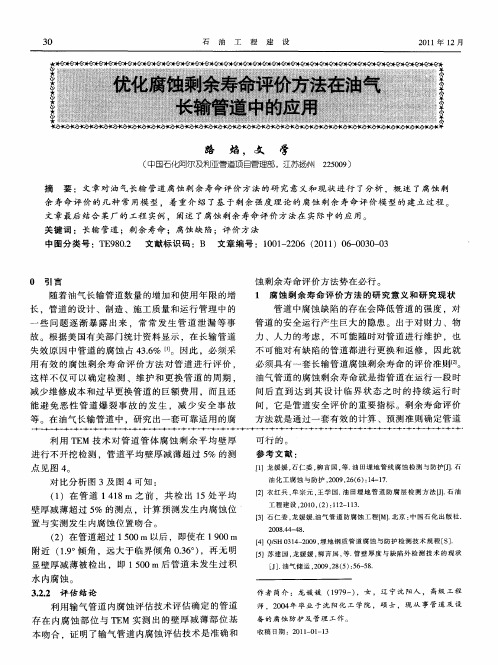
必须 确定该 管 道剩余 强 度 的评价 是 否适 用 。一般 的
评 价 步骤 如下【: 4 J ( )根 据 管 道 的公 称 壁 厚 t确 定 管道 的 金 属 1 。 损失 t ( l mE) 。
【]石 仁 委 , 3 龙媛 媛 . 气 管 道 防 腐蚀 工 程【 . 京 : 国 石 化 出 版 社 . 油 M]北 中
2 o . 4 48 o 84 - .
『]QS 34 2 0 埋 地 钢 质 管 道腐 蚀 与 防护 检 测 技 术 规 程 [ ] 4 /H 0 1 — 0 9, S. []苏 建 国 , 媛 媛 , 言 国 , . 壁厚 度 与 缺 陷 外 检 测 技 术 的 现 状 5 龙 柳 等 管 []油 气 储 运 ,0 92 ( )5 — 8 J. 20 ,85 :6 5 .
备 的 腐蚀 防 护及 管理 工作 。
收 稿 日期 :2 1 - 1 1 0 1O—3
第3 7卷第 6期
路 焰 等 :优 化 腐 蚀 剩 余 寿命 评 价 方 法 在 油 气 长 输管 道 中 的应 用
3 l
的 检 测 、维 修 周 期 ,找 到 管 道 安 全 运 营 与 经 济 效
油气长输管道腐蚀剩余寿命评价的方法很多mawprainmawpmawp大致可以分为基于管壁厚度的剩余寿命评价和基于根据map与的函数关系绘出map与剩余强度的腐蚀剩余寿命评价两大类根据实际情时间的关系曲线找到mawp曲线与设计的况又衍生出了根据现场实用性的腐蚀剩余寿命评价mawp曲线的交点所对应的ti则该就是管原则和基于可靠性的管道腐蚀剩余寿命评价原则
+
- +
- +
-・ — 一- + +
-・ - ● + — 卜 — 一-
长输管道腐蚀速率计算方法评述
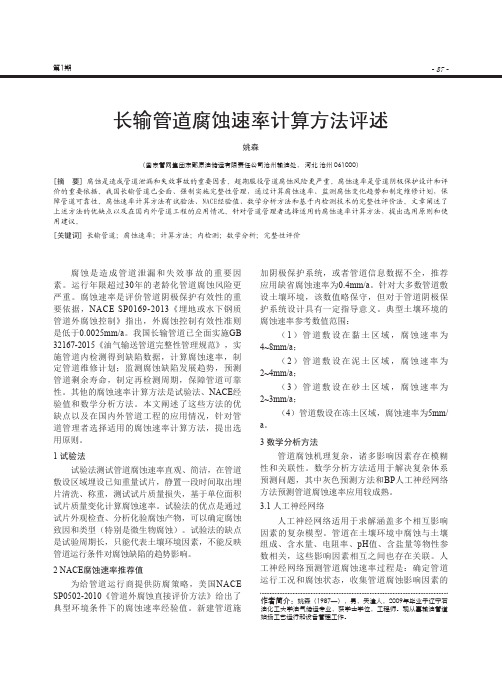
- 87 -第1期长输管道腐蚀速率计算方法评述姚森(国家管网集团东部原油储运有限责任公司沧州输油处, 河北 沧州 061000)[摘 要] 腐蚀是造成管道泄漏和失效事故的重要因素。
超期服役管道腐蚀风险更严重。
腐蚀速率是管道阴极保护设计和评价的重要依据。
我国长输管道已全面、强制实施完整性管理,通过计算腐蚀速率、监测腐蚀变化趋势和制定维修计划,保障管道可靠性。
腐蚀速率计算方法有试验法、NACE经验值、数学分析方法和基于内检测技术的完整性评价法。
文章阐述了上述方法的优缺点以及在国内外管道工程的应用情况。
针对管道管理者选择适用的腐蚀速率计算方法,提出选用原则和使用建议。
[关键词] 长输管道;腐蚀速率;计算方法;内检测;数学分析;完整性评价作者简介:姚森(1987—),男,天津人,2009年毕业于辽宁石油化工大学油气储运专业,获学士学位,工程师。
现从事输油管道站场工艺运行和设备管理工作。
腐蚀是造成管道泄漏和失效事故的重要因素。
运行年限超过30年的老龄化管道腐蚀风险更严重。
腐蚀速率是评价管道阴极保护有效性的重要依据,NACE SP0169-2013《埋地或水下钢质管道外腐蚀控制》指出,外腐蚀控制有效性准则是低于0.0025mm/a 。
我国长输管道已全面实施GB 32167-2015《油气输送管道完整性管理规范》,实施管道内检测得到缺陷数据,计算腐蚀速率,制定管道维修计划;监测腐蚀缺陷发展趋势,预测管道剩余寿命,制定再检测周期,保障管道可靠性。
其他的腐蚀速率计算方法是试验法、NACE 经验值和数学分析方法。
本文阐述了这些方法的优缺点以及在国内外管道工程的应用情况,针对管道管理者选择适用的腐蚀速率计算方法,提出选用原则。
1 试验法试验法测试管道腐蚀速率直观、简洁,在管道敷设区域埋设已知重量试片,静置一段时间取出埋片清洗、称重,测试试片质量损失,基于单位面积试片质量变化计算腐蚀速率。
试验法的优点是通过试片外观检查、分析化验腐蚀产物,可以确定腐蚀致因和类型(特别是微生物腐蚀)。
缺陷管道适用性评价

5缺陷管道适用性评价
埋地钢质燃气管道腐蚀的产生,严重降低了管道的剩余强度和承压能力,降低了管道腐蚀检测及维护的周期,增大了投资和运行费用,干扰了整个管道燃气输送系统的正常运行。
发生了腐蚀的钢制燃气管线,其强度会发生巨大变化,必需对腐蚀点进行适用性评价,确定腐蚀点是否危害结构的安全可靠性并基于缺陷腐蚀点的动力学发展规律研究,确定管道的安全服役寿命。
缺陷管道适用性评价主要包括两部分内容:剩余强度评价和剩余寿命预测。
5.1剩余强度评价
管道剩余强度评价的目的是为了研究缺陷能否在某一工作压力下允许存在,在确定当前腐蚀缺陷下的剩余强度和最大允许工作压力以及在某一工作压力下允许存在的最大腐蚀缺陷尺寸。
目前,剩余强度和最大工作(失效)压力的计算主要采用经验或半经验的关系式和国内外常用的规范进行。
缺陷管道剩余强度评价涉及的主要缺陷类型包括:体积型缺陷、裂纹型缺陷、几何缺陷、弥散损伤缺陷、机械损伤等,其特征及代表性评价标准见表5.1。
点腐蚀的剩余强度评价可以采用API RP759所提出的方法。
其主要是在管道外腐蚀缺陷检测的基础上,对缺陷管道剩余承压能力的定量评价。
若评价结果表明腐蚀管道适合目前的操作条件,则缺陷管道可以继续安全运行;否则,则可求出缺陷管道的最大允许工作压力MAWP r,对管道降压使用。
5.1.1剩余强度评价涉及参数
5.1.2剩余强度评价方法
5.2剩余寿命预测
管道剩余寿命预测则是在研究缺陷的动力学发展规律和材料性能退化规律的基础上,预测在役管道的未来发展、确定管道的检测周期及维修周期等重要参数,并给出管道的剩余安全服役时间。
剩余寿命预测可以采用一下方法:
5.3案例分析。
- 1、下载文档前请自行甄别文档内容的完整性,平台不提供额外的编辑、内容补充、找答案等附加服务。
- 2、"仅部分预览"的文档,不可在线预览部分如存在完整性等问题,可反馈申请退款(可完整预览的文档不适用该条件!)。
- 3、如文档侵犯您的权益,请联系客服反馈,我们会尽快为您处理(人工客服工作时间:9:00-18:30)。
第3 2 卷第 6 g g( 2 0 1 3 . 0 6 )( 基建管理)
长输管道腐蚀缺陷的评价
郭宏 大 庆 油田 设 计院
摘要 :对埋 地 输 油 管线 全线 腐 蚀检 测 数据 分析 表 明 ,管线 不 同 区段 腐 蚀程 度 差 别很 大 ,在 预 测其 腐蚀 管道 剩余 寿命 时 亦应 采 用分段 预 测 的原 则进 行 。 最普遍 的预测 腐 蚀增 长 率 的方 法就 是 对 比 两组 近 些 年 内的检 测数 据 。全 寿 命 腐 蚀 增 长 率 预 测 适 用 于 两 次检 测 间 隔时 间较 短 的情 况 ;半寿命 腐蚀 增 长率 预 测适 用 于 两次检 测 间隔 时间较 长 或 只有 一 次且距 投 产之 日起 时 间较 长 的情况。依据腐蚀增长速率可预测腐蚀缺 陷的未来发展 I 青 况 ,从 而判定 出计划修复时间和再检测时 间。
时间。
高的 高强度 钢 。
1 . 3 R S T R E N G 有效 面积法 该 方 法 不 再需 要 用 B 3 1 G法 中 的抛 物线 或 矩形
对腐蚀 的几何形 状进 行 面积近 似 。 由于 在对 检测数 据进 行分 析过 程 中 ,很难 获取 有效 面积 ,故 此方 法
金属损 失 面积 的表达 式 。 同样 不适 用于 强度 等级较
安全策略和可接受准则, 来确定所采用的腐蚀增长率 。 全寿 命腐 蚀增 长率 预测适 用 于两 次检测 间隔 时
间 较短 的情况 ;半 寿命腐 蚀增 长率 预测 适用 于两 次 检 测 间隔时 间较长 或 只有一 次且距 投产 之 日起 时 间 较 长 的情 况 。依据 腐蚀增 长 速率可 预测 腐蚀缺 陷 的 未 来发 展情况 ,从 而判 定 出计划修 复 时间 和再 检测
该 方 法 针 对 中高 强 度 等 级 管 道 ( 可达 到 X 8 0 ) ,
2 腐蚀 缺陷寿命 预测
对 埋 地输 油 管 线 全线 腐蚀 检 测 数据 分 析 表 明 ,
余强度 , 应该考虑更复杂的情况 ,如正确地考虑轴 向载 荷和 弯 曲载荷 ,及其 联合 作用下 以及更 复 杂 的
数 据 ,给 出 下 一 阶 段 的腐 蚀 速率 。检 测 的 次数 越 多 ,所获得 的结果 与 实际腐 蚀速率 越相 符合 。
A S ME B 3 1 G法依 其 准 则 简 单 、保 守 及 有 效 性 最普 遍 的预测腐 蚀增 长率 的方法 是对 比两 组 近 广 泛 用 于腐 蚀 管线 的评 估 。对 复杂 几 何 形 状 的腐 些 年 内的 检 测 数 据 。如果 仅 仅 有 一 次 的 内 检 测数 蚀 、相邻腐蚀 、环向腐蚀和有轴 向应力存在时,不 据 ,可 以采用 全寿命 或半 寿命 的方法 来 预测腐速率 ;预测
d o i : 1 0 . 3 9 6 9 / j . i s s n . 1 0 0 6 — 6 8 9 6 . 2 0 1 3 . 6 . 0 6 3
1 腐蚀 缺陷剩余 强度评估
1 . 1 A S M E B 3 1 G法
而是 应该 隔一定 时 间后再进 行 检测 ,结 合历次 检测
能用它来进行评估。也不适用于管材等级较高的高 陷的增长速率 ,获取最深腐蚀缺陷的腐蚀增长速率 强 度钢 管道 ,例 如 X 7 0 、X 8 0 管道 。 和全部腐蚀缺陷的平均增长速率 , 根据运营公司的
1 . 2 修正 的 B 3 1 G 方 法
该 方 法 采 用 失 效 爆 破 压 力 预 测 公 式 的形 式 与 A S ME B 3 1 G法 基本 相 同 ,主要 修 正 了 F o l i a s 系数 和
实际应 用 性差 。
1 . 4 D N V R P F 1 0 1 方法
3 结论
( 1 )对 于 腐 蚀 缺 陷剩 余 强 度 评 估 , A S ME
B 3 1 G法 、R S T R E N G 0 . 8 5 d L法 、R S T R E NG有 效 面
积法适 合 中 、低强 度钢 的评 价 ,D N V R P F 1 0 1 法适 更适 合 于现代 高强 度大 口径管 道 的安全 评价 。但 不 合 中 、高强 度等级 管道 的缺 陷评定 。 适 用于 超过 X 8 0 钢 的管线 钢 或深 度大 于 8 5 %壁厚 的 ( 2 )腐蚀管道剩余强度评价应在以下两个方面 缺陷。 进 一 步深入 研究 :用 有 限元 方法 研究 腐蚀 管道 的剩
腐蚀 形状 等 ;进 一步 研究 在 内压和 附加 载荷联 合作 用下 环 向腐蚀 缺陷 的剩余强 度评 价 。 ( 3 )基 于定期全 线腐 蚀检 测数 据为 基础 的剩余
管线不同区段腐蚀程度差别很大 。因此 ,在预测其 腐蚀管道剩余 寿命 时亦应 采用分段预测 的原则进 行 。随着漏磁内检测的深入开展,获取了管道腐蚀 缺陷 的大量 基础 数据 。通 过对 现场 管线 进行 阶段性 的腐蚀检测 , 得到腐蚀深度随时间的变化趋势 , 从 而得 到腐 蚀速 率发 展趋势 ,拟合 出经验 公式 ,即可 预测下一阶段的腐蚀速率 。预测 的时间不宜太长 ,
一
寿命预测模型,在数据依据充分的条件下 ,能充分 显 示管 段不 同 区段 腐蚀 发展差 别 ,预测 精度 和可 信
度 高 ,可为 管道再 检测周 期决 策提供 支持 。
( 栏 目主持 焦 晓梅 )
1 1 0一
油气 田地面 工程 ( h
t t p : / / 、 w, w. y q t d mg c . c o m)