煤加氢直接液化工艺
神华煤直接液化工艺及PU情况介绍-神华舒歌平

德国新IG工艺
Coal slurry: 40%
煤浆,40%浓度 R
Germany’s new IG Process
H S
溶剂,不含沥青
Solvent (non-bitumen)
减 压 闪 蒸
Flash Vaporization
残渣
Residue
• 操作条件:压力300bar,催化剂:赤泥
Operation condition: pressure 300bar Catalysts: Red Mud
分离单元 Separation unit
水
Water
液化油 Oil 残渣 Residue
煤炭直接液化工艺
煤炭直接液化是目前由煤生产液体产品 方法中最有效的路线。液体产率超过 70%(以无水无灰基煤计算),工艺的 总热效率通常在60-70%。
DCL is the most efficient way of Coal Liquefaction so far, through this way the Liquids yield rate over 70% (based on waterless and ashless coal) and the total thermal efficiency at 60-70%
神华煤直接液化工艺 及PDU情况介绍
Shenhua Direct Coal Liquefaction Process and PDU Introduction 舒歌平 Shu Geping 神华煤制油研究中心有限公司
Shenhua Coal Liquefaction R&D Co., Ltd
2007.6
• 停留时间:0.5t/m3h Residence time: 0.5t/m3h • 油收率:50% Oil Yield Rate: 50% • 由于溶剂中没有了沥青,处理能力增加,压力降低, 油收率增加 The pressure decreased, capacity increased and Oil Yield Rate increased, as the solvent without bitumen
煤的直接加氢液化工艺

张 伟,金俊杰,俞 虹,田莉雅
(兖矿集团煤化工办公室,山东 邹城介绍了煤液化的方法,重点对目前世界上较先进成 熟的煤直接液化技术的工艺特点进行了总结和比较,提出了综合利用煤直接加氢液化技术炼 油的可行性方案。
关键词:洁净煤技术;煤液化工艺;方案
南非因不产石油和天然气,而煤炭储量丰富且 价格低廉,在 1955 年建立了 SaSOI - !合成油厂, 生产柴油、石蜡等产品,以后又建立了 SaSOI - "、 SaSOI - #厂,分别于 1980、1982 年投产,主要生 产汽油,SaSOI 3 个厂每年可生产 450 万 t 车用燃料 和有价值的化工产品。
中图分类号:T @529
文献标识码:A 文章编号:1006-6772(2001)03-0031-03
石油是人类赖以生存和发展的最方便最重要的 能源。据 统 计, 目 前 石 油 占 世 界 能 源 消 费 结 构 的 39 % 。中国的石油资源有限,资源品位不高,难开 采资源比重较大。而中国又是一个石油消费大国, 90 年代以来一直靠进口石油弥补国内石油产量的 不足。随着中国经济的进一步发展,石油的供需矛 盾将日益突出。中国能源资源的特点,决定了中国 是以 煤 炭 为 主 的 能 源 结 构。 据 有 关 方 面 预 测, 到 2010 年,中国能源结构中煤炭的比例仍高居 70%, 能源结 构 中 以 煤 炭 为 主 的 局 面 长 期 不 会 改 变。 但 是,目前由于中国以煤为主的能源工业和化学工业 技术落后,给环境带来较严重的污染,面临着人类 环境保护要求的严重挑战。
洁净煤技术 2001 年第 7 卷第 3 期
兖矿集团的北宿及杨村高硫煤。
表 ! 几种煤直接液化工艺技术的比较
煤直接液化技术现状与发展趋势
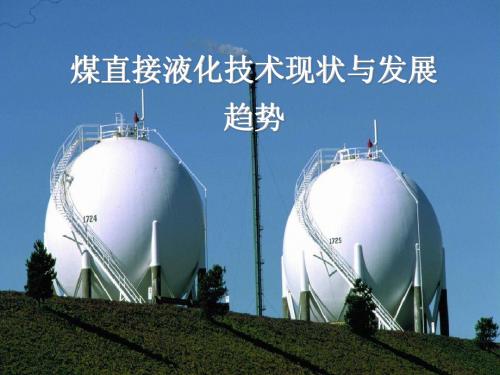
醚键和杂
(2)脱硫反应 煤有机结构中的硫以硫醚、硫醇和噻吩等形式存在,脱硫反应 与上述脱氧反应相似。由于硫的负电性弱,所以脱硫反应更容易进行。 (3)脱氮反应 煤中的氮大多存在于杂环中,少数为氨基,与脱硫和脱氧相比,脱 氮要困难得多。一般脱氮需要激烈的反应条件和有催化剂存在时才能 进行,而且是先被氢化后再进行脱氮,耗氢量很大。
(4)降低循环油中沥青烯含量 (5)缩短反应时间
11
五、煤加氢液化催化剂种类
(1)金属氧化物催化剂 对煤加氢液化催化活性大小顺序: SnO2、ZnO2、GeO2、MoO3、PbO、 Fe2O3、TiO2、 Bi2O3、V2O5. (2)铁系催化剂 主要为三氯化铁、硫酸亚铁、或者加入无水氧化铁,有的加硫 或者不加硫。 (3)卤化物催化剂 使用卤化物催化剂有两种方式: 一种是使用少量催化剂;另一种是使用大量催化剂,熔融金属 卤化物,催化剂与煤的质量比可高达1。
要将煤转化为液体产物,首先要将煤的大分子裂解为较小 的分子,而要提高H/C原子比,降低O/C比,就必须增加H 原子或减少C原子。 煤液化的实质就是在适当温度、氢压、溶剂和催化剂条件 下,比提高H/C ,使固体煤转化为液体的油。
6
直接液化
制 氢 煤制备 油煤浆 制 备 加氢液化
450OC,20MPa
煤 浆 预 热 器 煤浆
2014-4-3
第 一 反 应 器
第 二 反 应 器
高 温 分 离 器
中 温 分 离 器
低 温 分 离 器
常 减 压 蒸 馏
加 氢 反 应 装 置
常 压 蒸 馏
煤直接液化
残渣
循环溶 剂去制 15 15 煤浆
工艺特点:
①采用两段反应,反应温度455℃、压力19M Pa,提高了煤浆空速; ②采用人工合成超细铁基催化剂 ③固液分离采用成熟的减压蒸馏; ④循环溶剂全部加氢,提高溶剂的供氢能力; ⑤液化粗油精制采用离线加氢方案。
煤的直接加氢液化技术

自由基碎片加氢(一)
可用如下方程式表示加氢反应
R-CH2-CH2-R’→ RCH2·+R’CH2· RCH2·+R’CH2·+2H·→ RCH3+R’CH3
煤加氢液化过程包括一系列的顺序反应和平行反 应,但以顺序反应为主,每一级反应的分子量 逐级降低,结构从复杂到简单,杂原子含量逐 级减少,H/C原子比逐级上升。
直接液化工艺流程简图
催
化
剂
H2
煤煤
反
浆
应
分
提
离
质
循环溶剂
残渣
汽油 柴油
其它
工艺过程
该工艺是把煤先磨成粉,再和自身组的部分液 化油(循环制剂)配成煤浆,在高温(450oC) 和高压(20—30MPa)下直接加氢,获得液化油, 然后再经过提质加工,得到汽油柴油等产品.1t 无水无灰煤可产500—600Kg油,加上制氢用 煤,约3—4t原料煤产1t油。
催化剂作用
催化剂的作用是吸附气体中的氢分子,并将其 活化成活性氢以便被煤的自由基碎片接受。一 般选用铁系催化剂或镍、钼和钴类催化剂。硫 是煤直接液化的助催化剂,有些煤本身含有较 高的硫,可少加或不加助催化剂。
催化剂的影响
催化剂是煤直接液化过程的核心技术 优良的催化剂可以降低煤液化温度,减少副
煤的直接加氢液化技术
煤直接液化反应机理
把固体煤转化为液体油,就必须采用增加温 度或其他化学方法以打碎煤的分子结构,使大 分子物质变成小分子物质,同时外界要供给足 够量的氢,提高其H/C原子比。
煤直接液化反应比较复杂,大致可分为热解、 氢转移、加氢三个反应步骤
氢源
煤在热解过程中外界不提供氢 煤在热解过程中外界不提供氢,煤热解
煤炭液化技术

煤炭液化技术[编辑本段] 煤炭液化技术煤炭液化是把固体煤炭通过化学加工过程产品的先进洁净煤技术。
根据不同的加工,使其转化成为液体燃料路线,煤炭液化可分为直接、化工原料和液化和间接液化两大类:一、直接液化直接液化是在高温(400℃以上)、高压(10MPa以上),在催化剂和溶剂作用下使煤的分子进行裂解加氢,直接转化成液体燃料,再进一步加工精制成汽油、柴油等燃料油,又称加氢液化。
1、发展历史煤直接液化技术是由德国人于1913 年发现的,并于二战期间在德国实现了工业化生产。
德国先后有12套煤炭直接液化装置建成投产,到1944年,德国煤炭直接液化工厂的油品生产能力已达到423万吨/年。
二战后,中东地区大量廉价石油的开发,煤炭直接液化工厂失去竞争力并关闭。
70年代初期,由于世界范围内的石油危机,煤炭液化技术又开始活跃起来。
日本、德国、美国等工业发达国家,在原有基础上相继研究开发出一批煤炭直接液化新工艺,其中的大部分研究工作重点是降低反应条件的苛刻度,从而达到降低煤液化油生产成本的目的。
目前世界上有代表性的直接液化工艺是日本的NEDOL 工艺、德国的IGOR工艺和美国的HTI工艺。
这些新直接液化工艺的共同特点是,反应条件与老液化工艺相比大大缓和,压力由40MPa降低至17~30MPa,产油率和油品质量都有较大幅度提高,降低了生产成本。
到目前为止,上述国家均已完成了新工艺技术的处理煤100t/d 级以上大型中间试验,具备了建设大规模液化厂的技术能力。
煤炭直接液化作为曾经工业化的生产技术,在技术上是可行的。
目前国外没有工业化生产厂的主要原因是,在发达国家由于原料煤价格、设备造价和人工费用偏高等导致生产成本偏高,难以与石油竞争。
2、工艺原理煤的分子结构很复杂,一些学者提出了煤的复合结构模型,认为煤的有机质可以设想由以下四个部分复合而成。
第一部分,是以化学共价键结合为主的三维交联的大分子,形成不溶性的刚性网络结构,它的主要前身物来自维管植物中以芳族结构为基础的木质素。
煤炭液化

液化过程的氢耗量与煤自由氢含量关系
• 加氢液化过程中的耗量与原料 煤中的自由氢含量成反比关系。 • 泥炭的自由氢最低(3.2g/100g 碳),褐煤(4.1~4.3),烟煤 (4.0~4.4)
• 氢气占煤液化成本的比例很高,一 般为30%或更高。
溶剂的作用
• 煤炭的加氢液化中一般要使 用溶剂,因为溶剂在煤炭液 化过程中有下列左右:①热 溶解煤;②溶解氢气;③供 氢作用;④溶剂直接与煤质 反应。
催化剂在煤炭加氢液化中的作用
• ①催化剂活化反应物,加速加氢反应速度, 提高煤炭液化的转化率和油收率 • ②促进溶剂的再加氢化和氢源与煤之间的 氢传递 • ③选择性作用 • 适合于作煤加氢液化催化剂的物质很多, 铁系催化剂,Co、Mo、Ni等金属氧化物催 化剂及金属卤化物催化剂。
催化剂的活性
• 各种催化剂的活性是不相同的。造成 催化剂活性不同的决定性因素是催化 剂的化学性质和结构。催化剂在使用 过程中显示出活性的大小与下列因素 有关:①催化剂用量;②催化剂加入 方式;③煤中矿物质;④溶剂的影响; ⑤ 炭 沉 积 和 蒸 汽 烧 结 。
• 影响煤加氢难易程度的 因素是煤本身的稠环芳 烃结构,稠环芳烃结构 越密和相对分子质量越 大,加氢越难。
脱氧、硫、氮杂原子反应
• 加氢液化过程,煤结 构中的一些氧、硫、 氮也产生断链分别生 成气体而脱除。
缩合反应
• 缩合反应会生成半焦和焦炭, 使液化产率降低。为了提高 液化效率,必须严格控制反 应条件和采取有效措施,抑 制缩合反应,加速裂解、加 氢 等 反 应 。
第三阶段
• 1982年至今,煤液化新工艺的研究 期。1982年后期石油市场供大于求, 石油价格不断下跌,各大煤液化试 验工厂纷纷停止试验.但是各发达国 家的实验室研究工作及理论研究工 作仍在大量的进行。如近年来开发 出来的煤油共处理新工艺和超临界 抽提煤工艺等。
煤温和加氢液化制高品质液体燃料关键技术与工艺

煤温和加氢液化制高品质液体燃料关键技术与工艺引言在当前全球能源供应紧张的背景下,开发和利用高品质液体燃料成为了国际能源领域的研究热点之一。
煤温和加氢液化技术作为一种重要的液体燃料制备方法,具有资源成本低、适用范围广的优势,对我国能源战略和经济发展具有重要意义。
本文将从煤温和加氢液化的原理、关键技术及工艺流程等方面进行综合分析和探讨。
原理煤温和加氢液化是一种将固体煤转化为液体燃料的技术。
其原理是通过高温和高压的条件下,将煤在氢气的催化作用下进行化学反应,使煤中的高分子化合物裂解,并生成液体燃料。
这一过程主要包括三个步骤:煤的热解、煤的气化和煤的加氢。
煤的热解煤的热解是指将煤暴露在高温环境中,使煤中的有机质在没有氧气的条件下发生热解反应,生成气体和液体产物。
热解过程中,煤中的高分子化合物会发生裂解,生成低分子量的化合物,如烃类等。
煤的气化煤的气化是指将煤中的热解产物(如烃类)在高温和高压的条件下与氢气反应,生成更高价态的化合物。
在气化过程中,煤中的烃类会与氢气发生反应,生成一系列的液体和气体产物,其中液体产物就是液体燃料的主要来源。
煤的加氢煤的加氢是指将煤中的气化产物在高温和高压的条件下与氢气进一步反应,将气体产物中的不饱和化合物加氢饱和,生成高品质的液体燃料。
加氢反应可以提高液体燃料的氢碳比,增加其能量密度,提高其燃烧效率。
关键技术煤温和加氢液化制高品质液体燃料的关键技术包括催化剂选择、温度和压力控制、反应器设计等。
催化剂选择催化剂的选择对煤温和加氢液化的反应效果和产物质量起到关键作用。
优质的催化剂应具有高催化活性、良好的稳定性和选择性,能够在适宜的温度下催化反应进行。
常用的催化剂包括铁、镍、钼等金属催化剂以及复合催化剂。
温度和压力控制温度和压力是影响煤温和加氢液化反应进行的重要因素。
适当的温度和压力可以促进反应物的转化率和产物的质量。
一般来说,较高的温度和压力有利于提高反应速率和产品收率,但过高的温度和压力会增加能源消耗和设备投资。
煤的液化的原理

煤的液化的原理煤的液化原理煤的液化是通过化学反应将煤转化为液体燃料的过程。
煤是一种化石燃料,由碳、氢、氧、氮和硫等元素组成。
煤的液化过程可以将煤转化为液体燃料,从而提高煤的利用价值,并减少对传统石油资源的依赖。
煤的液化原理可以分为两个主要步骤:煤的破碎和煤的加氢裂解。
首先是煤的破碎。
煤通常是以固体形式存在的,因此需要将煤破碎成较小的颗粒,以增大其表面积,便于后续的反应。
煤的破碎可以通过物理方法,如机械破碎或磨碎来实现。
接下来是煤的加氢裂解。
在加氢裂解过程中,首先将煤与氢气反应,生成一系列的中间产物。
煤中的碳和氢与氢气发生反应,生成一系列的烃类化合物。
这些烃类化合物包括烷烃、烯烃和芳香烃等。
此外,还会生成一些小分子化合物,如水和一氧化碳等。
在加氢裂解过程中,煤中的碳和氢发生化学反应,生成烃类化合物。
这些烃类化合物可以用作燃料或化工原料。
煤的液化可以得到不同种类的液体燃料,如煤油、柴油和液化石油气等。
这些液体燃料可以用于发电、交通运输和工业生产等领域。
煤的液化过程中涉及到多种反应,其中最关键的是加氢反应。
加氢反应是指煤中的碳和氢与氢气发生反应,生成烃类化合物的过程。
在加氢反应中,需要适当的温度和压力条件,以及催化剂的存在。
催化剂可以加速反应速率,提高反应效率。
煤的液化是一项复杂的过程,涉及到多种化学反应和工艺步骤。
煤的液化技术已经得到了广泛应用,成为一种重要的能源转化技术。
煤的液化可以提高煤的利用价值,减少对传统石油资源的依赖,同时也有助于减少环境污染。
总结起来,煤的液化是通过化学反应将煤转化为液体燃料的过程。
煤的液化原理包括煤的破碎和煤的加氢裂解。
煤的液化可以得到不同种类的液体燃料,如煤油、柴油和液化石油气等。
煤的液化技术具有重要的能源转化意义,有助于提高煤的利用价值,并减少环境污染。
一种煤炭直接液化的方法

一种煤炭直接液化的方法引言煤炭作为一种主要的能源资源,在人类的生产和生活中起着重要的作用。
然而,由于煤炭的固体性质,其利用率相对较低,同时也会带来环境污染问题。
为了充分利用煤炭资源,并减少对环境的影响,科学家们不断探索煤炭直接液化技术。
本文将介绍一种新的煤炭直接液化方法,旨在提高煤炭的利用效率和降低对环境的负面影响。
方法1. 煤炭破碎首先,将原先的煤炭进行破碎处理。
通过采用高效的破碎设备,使煤炭颗粒的尺寸控制在一定范围内,以提高煤炭的可反应性。
同时,通过筛分,去除煤炭中的杂质,提高反应物的纯度。
2. 催化剂选择接下来,需要选择适合的催化剂。
催化剂在煤炭液化反应中起到重要作用,可以提高反应速率和产率。
优秀的催化剂应具有高活性、良好的稳定性和选择性。
3. 煤炭直接液化反应在反应器中,将破碎后的煤炭与催化剂加入。
反应过程中需要控制温度、压力和反应时间等参数。
合适的温度和压力可以提高反应的效果,并减少不良产物的生成。
此外,适当的反应时间可以保证反应的充分进行。
4. 产品分离反应结束后,需要对产物进行分离。
由于液化过程中产生了大量的混合气体和液状物质,需要采用先进的分离技术对其进行处理。
典型的分离技术包括蒸馏、萃取和凝结等。
5. 产品处理分离后得到的液体产物需要进行进一步的处理。
其中包括去除杂质、提高产品纯度、调整组分比例等。
这样可以得到高质量的液体燃料或化工产品,提高煤炭资源的综合利用价值。
优势和挑战这种煤炭直接液化方法相对于传统的加氢裂解、焦化和气化等方法具有以下优势:1. 可以充分利用煤炭资源,提高利用效率。
2. 产出的液体燃料或化工产品具有较高的能量密度和稳定性。
3. 可以减少自然气和石油等传统能源的依赖。
4. 通过去除杂质等后处理工艺,可以减少对环境的污染。
然而,该方法也面临一些挑战:1. 催化剂的选择和煤炭直接液化反应条件的调控需要深入研究和优化。
2. 分离和后处理过程需要先进的设备和技术支持。
煤直接液化(PDF)

煤的直接液化煤基产品燃烧固体–焦炭、炭材料转化气体–工业用燃气、民用燃气、合成气化学品–焦油化学品(芳烃)、氨、甲醇液体–车用燃料汽油间接液化(ICL)直接液化(DCL)柴油含氧燃料煤直接液化的宏观化学挥发分固定碳液体气体目的产物煤灰分残渣可利用的产物水分水煤直接液化的基本化学原理H/C = 0.8•汽油断键Coal•柴油H/C 2加氢三个目的:●煤大分子(M=5000-10000) 破碎为油小分子(M~200)●0.8H/C比从0.8 提高至1.9●从油品中脱除S、N、O等杂原子煤直接液化的基本化学原理目前的认识:和自由基大小相近的产物加氢自由基加热断键缩聚大分子固体产物煤直接液化的宏观化学煤直接液化反应的核心“自由基产生速率”和“加氢速率”匹配温度氢压400-450o C15-30 MPa工艺上如何实现?煤直接液化的过程•→煤要以粉的形式液化磨煤•固体煤粉输送?→ 管路、阀门→部分液化后怎么办?加液相介质-油(循环油)产物的分离加氢阻力?气泡•供氢溶剂•催化剂煤粒油煤直接液化过程的必备单元•磨煤(包括:干燥)•制氢(气化、水煤气变换)•制浆(煤+油+催化剂)•煤浆预热•液化•分离(气-液、液-液、液-固)•油品加工(脱硫、脱氮、脱氧、脱金属、芳烃转化)•残渣利用(燃烧、气化、…)煤直接液化的工艺分析: 煤油需要许多加氢过程煤(固体)加氢液体产物加氢液化过程炼油工艺煤油品•煤液化工艺缺乏对这两个过程的区分•已有的对比缺乏共同基础合理的界定:直接液化仅应包括煤(固体)的液化过程煤在不同条件下加氢的反应器数为DCL 的段数定义煤直接液化工艺“段数”的意义油加氢加热断键自由基缩聚焦煤直接液化技术的发展自由基碎片产生和加氢的平衡Two-stage-催化剂与反应器-供氢溶剂Single stage CTSL, HTI, Shenhuaa l l e v e lSingle-stage, HP Single-stageSRC, EDS, H-Coal, IGOR+, NEDOL, BCL, Pryosal, LSET e c h n i c g g190019201940196019802000•温度:变化不大(425-455 o C )•单段→两段•压力: 70 MPa →17 MPa :•催化剂: 大颗粒→纳米颗粒•循环油加氢?现代煤直接液化工艺应有的特征•两段液化-优化裂解和加氢的匹配(温度不同)-提高转化率•超细催化剂-减少催化剂用量-加强对缩聚反应的抑制-温和液化条件(压力)•循环油加氢-提高加氢能力,强化对缩聚反应的抑制-温和液化条件一般认为煤直接液化催化剂•开始不用催化剂,油品粘度大,操作困难,70 MPa 也不行用Mo/Fe 催化剂才解决了问题。
煤的直接液化
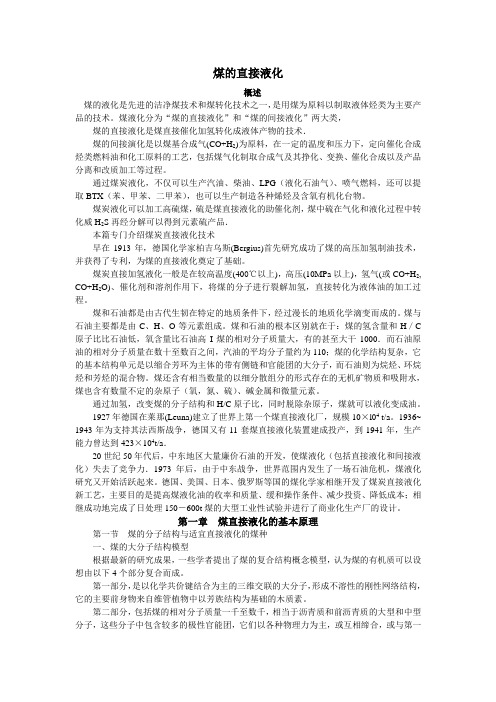
煤的直接液化概述煤的液化是先进的洁净煤技术和煤转化技术之一,是用煤为原料以制取液体烃类为主要产品的技术。
煤液化分为“煤的直接液化”和“煤的间接液化”两大类,煤的直接液化是煤直接催化加氢转化成液体产物的技术.煤的间接演化是以煤基合成气(CO+H2)为原料,在一定的温度和压力下,定向催化合成烃类燃料油和化工原料的工艺,包括煤气化制取合成气及其挣化、变换、催化合成以及产品分离和改质加工等过程。
通过煤炭液化,不仅可以生产汽油、柴油、LPG(液化石油气)、喷气燃料,还可以提取BTX(苯、甲苯、二甲苯),也可以生产制造各种烯烃及含氧有机化台物。
煤炭液化可以加工高硫煤,硫是煤直接液化的助催化剂,煤中硫在气化和液化过程中转化威H2S再经分解可以得到元素硫产品.本篇专门介绍煤炭直接液化技术早在1913年,德国化学家柏吉乌斯(Bergius)首先研究成功了煤的高压加氢制油技术,并获得了专利,为煤的直接液化奠定了基础。
煤炭直接加氢液化一般是在较高温度(400℃以上),高压(10MPa以上),氢气(或CO+H2, CO+H2O)、催化剂和溶剂作用下,将煤的分子进行裂解加氢,直接转化为液体油的加工过程。
煤和石油都是由古代生韧在特定的地质条件下,经过漫长的地质化学滴变而成的。
煤与石油主要都是由C、H、O等元素组成。
煤和石油的根本区别就在于:煤的氢含量和H/C 原子比比石油低,氧含量比石油高I煤的相对分子质量大,有的甚至大干1000.而石油原油的相对分子质量在数十至数百之间,汽油的平均分子量约为110;煤的化学结构复杂,它的基本结构单元是以缩合芳环为主体的带有侧链和官能团的大分子,而石油则为烷烃、环烷烃和芳烃的混合物。
煤还含有相当数量的以细分散组分的形式存在的无机矿物质和吸附水,煤也含有数量不定的杂原子(氧,氮、硫)、碱金属和微量元素。
通过加氢,改变煤的分子结构和H/C原子比,同时脱除杂原子,煤就可以液化变成油。
1927年德国在莱那(Leuna)建立了世界上第一个煤直接液化厂,规模10×l04 t/a。
煤制油之----直接液化技术解析

• 1952年,美国矿业局制定了煤炭液化的发展计划, 规划建设2座煤直接液化厂
• 联合碳化物公司从1935年开始就研究煤炭直接液化 技术,到五十年代初发展到300吨/天的试验规模, 试图生产各种芳香烃类化学品
• 1960年,成立了煤炭研究办公室(OCR)一直支持 一些公司和研究机构从事以气化、液化为重点的煤 炭加工利用的研究
煤制油之直接液化技术解析
• 基本原理 • 工艺问题 • 工程问题
第一部分 基本原理
• 定义 • 发展概况 • 基本过程 • 反应机理 • 煤质要求 • 催化剂 • 溶剂 • 液化油提质加工
一. 定义
1. 直接液化
煤
加氢
液化油 提质加工 成品油
2. 间接液化
煤 气化 合成气 合成 合成油 精炼 成品油
二战期间德国的煤直接液化厂
投产日期
1931 1936 1936 1936 1937 1939 1939 1940 1940 1941 1942 1943
所在地名
Leuna Bohlen Magdeberg Scholven Welheim Gelsenberg Zeitz Lutzkendorf Politz Wesseling Brux Blechhammer
Bottrop RAG VEBA
Saar SAAR Coal
日本鹿 NEDO 岛
澳大利 NEDO 亚
Point British of Ayr Coal 图拉市 ИГИ
试验煤种 鲁尔烟煤 烟煤 烟煤 褐煤 次烟煤 褐煤
国内煤液化的历史
五十年代: 抚顺石油三厂煤焦油加氢 锦州石油六厂合成油装置 煤低温热解计划
煤炭直接液化技术总结
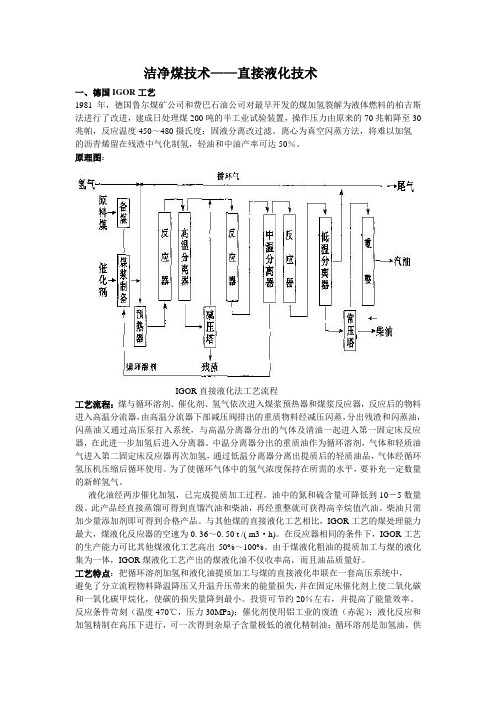
洁净煤技术——直接液化技术一、德国IGOR工艺1981年,德国鲁尔煤矿公司和费巴石油公司对最早开发的煤加氢裂解为液体燃料的柏吉斯法进行了改进,建成日处理煤200吨的半工业试验装置,操作压力由原来的70兆帕降至30兆帕,反应温度450~480摄氏度;固液分离改过滤、离心为真空闪蒸方法,将难以加氢的沥青烯留在残渣中气化制氢,轻油和中油产率可达50%。
原理图:IGOR直接液化法工艺流程工艺流程:煤与循环溶剂、催化剂、氢气依次进入煤浆预热器和煤浆反应器,反应后的物料进入高温分流器,由高温分流器下部减压阀排出的重质物料经减压闪蒸,分出残渣和闪蒸油,闪蒸油又通过高压泵打入系统,与高温分离器分出的气体及清油一起进入第一固定床反应器,在此进一步加氢后进入分离器。
中温分离器分出的重质油作为循环溶剂,气体和轻质油气进入第二固定床反应器再次加氢,通过低温分离器分离出提质后的轻质油品,气体经循环氢压机压缩后循环使用。
为了使循环气体中的氢气浓度保持在所需的水平,要补充一定数量的新鲜氢气。
液化油经两步催化加氢,已完成提质加工过程。
油中的氮和硫含量可降低到10-5数量级。
此产品经直接蒸馏可得到直馏汽油和柴油,再经重整就可获得高辛烷值汽油。
柴油只需加少量添加剂即可得到合格产品。
与其他煤的直接液化工艺相比,IGOR工艺的煤处理能力最大,煤液化反应器的空速为0. 36~0. 50 t /( m3·h)。
在反应器相同的条件下,IGOR工艺的生产能力可比其他煤液化工艺高出50%~100%。
由于煤液化粗油的提质加工与煤的液化集为一体,IGOR煤液化工艺产出的煤液化油不仅收率高,而且油品质量好。
工艺特点:把循环溶剂加氢和液化油提质加工与煤的直接液化串联在一套高压系统中,避免了分立流程物料降温降压又升温升压带来的能量损失,并在固定床催化剂上使二氧化碳和一氧化碳甲烷化,使碳的损失量降到最小。
投资可节约20%左右,并提高了能量效率。
反应条件苛刻(温度470℃,压力30MPa);催化剂使用铝工业的废渣(赤泥);液化反应和加氢精制在高压下进行,可一次得到杂原子含量极低的液化精制油;循环溶剂是加氢油,供氢性能好,液化转化率高。
《煤化工工艺学》__煤的直接液化

虽可实现煤就地液化,不必建井采煤,但还存在许多 技术和经济问题,近期内不可能工业化 。
§7.2 煤加氢液化原理
一、煤和石油的比较
煤和石油同是可燃矿物;有机质都由碳.氢、氧、氮和硫元素构 成,但它们在结构、组成和性质上又有很大差别: 化学组成上,石油的H/C原子比高于煤,而煤中的氧含量显著高
就会彼此结合,这样就达不到降低分子量的目的。多环芳
烃在高温下有自发缩聚成焦的倾向。
在煤加氢液化中结焦反应是不希望发生的。一旦发生,
轻则使催化剂表面积炭,重则使反应器和管道结焦堵塞。
采取以下措施可防止结焦:
•
① 提高系统的氢分压;
•
② 提高供氢溶剂的浓度;
•
③ 反应温度不要太高;
•
④ 降低循环油中沥青烯含量,
(3)高压催化加氢法
如:德国的新老液化工艺和美国的氢煤法。
(4)煤和渣油联合加工法
以渣油为溶剂油与煤一起一次通过反应器,不用循环 油。渣油同时发生加氢裂解转化为轻质油。美国、加 拿大、德国和苏联等各有不同的工艺。
(5)干馏液化法
煤先热解得到焦油,然后对焦油进行加氢裂解和提质 。
(6)地下液化法
为保证催化剂维持一定的活性,在反应中连续抽出约2%的催 化剂进行再生。同时补充足够的新催化剂。
反应产物的分离和IG新工艺相近,即经过热分离器到闪蒸塔4 ,塔顶产物经常压蒸馏塔7分为轻油、中油和重油;塔底产物经旋 流器10,含固体少的淤浆返回系统制煤浆,而含固体多的淤浆经 液固分离器9再进入减压蒸馏塔8进行减压蒸馏。塔底残渣用于气 化和中油与氢气混合后,经热交换器和预 热器,进入3个串联的固定床催化加氢反应器、产物 通过热交换器后进一步冷却分离,分出气体和油, 前者基本作为循环气,后者经蒸馏得到汽油作为主 要产品,塔底残油返回作为加氢原料油。
化工工艺学-第五章-煤的液化
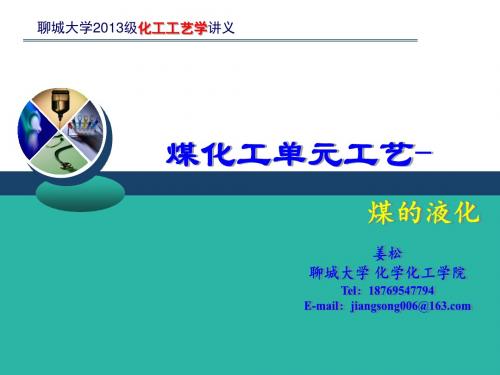
氢气 煤 催化剂 煤浆 制备
循环氢 尾气 液 化 分 离
水
液化油 残渣
提 质
加 工 成品油
循环溶剂
①原料煤 用于液化的煤应符合以下条件:
高挥发分年青烟煤和硬质褐煤,碳含量约在77~82%之间;
煤中惰性组分<15%; 灰分<10%; 硫含量要高,即需用高硫煤。
②催化剂 铁系催化剂(含氧化铁的矿物,铁盐及煤中硫铁矿) 使用时要求系统中有硫,否则活性不高
⑤反应温度与压力
温度:各工艺采用的温度大致相同,大多为450℃,也有475℃。反应 温度高有利于沥青烯向油的转化,但温度高会引起结焦和产生更多的气体。
压力:氢在煤浆中的溶解度随压力增加而增加,由于煤液化温度较高,
采用较高的压力才有足够的氢分压,一般压力控制在20MPa以下。
⑥液固分离 真空闪蒸方法,优点是操作简化,处理量剧增,蒸馏油用作循环油,煤 浆粘度降低。缺点是收率有所降低。 反溶剂法(anti-solvent),采用对前沥青烯和沥青烯等重质组分溶解度 很小的有机溶剂,把它们加到待分离的料浆中时,能促使固体粒子析出 和凝聚,颗粒变大,利于分离。 临界溶剂脱灰,它利用超临界抽提原理,使料浆中可溶物溶于溶剂而留 下不溶的残煤和矿物质,常采用的溶剂是含苯、甲苯和二甲苯的溶剂油。 液固分离出来的残渣占原料煤的30%左右,处理方法有干馏、锅炉 燃烧以及气化等,其中气化制氢是最方便的利用方法。
CO2+4H2 → CH4+ 2H2O
游离碳生成反应
2CO → C+ CO2
游离碳的生成可能堵塞催化剂的内孔。 在至今的技术条件下,含氧化合物仍是副产物。
F-T合成反应机理
费托合成的热力学分析简述
在50~350℃的范围内,有利于形成甲烷,产物生成的概率按 CH4
神华煤直接液化工艺技术特点和优势

神华煤直接液化工艺技术特点和优势神华煤直接液化示范工程采用的煤直接液化工艺技术是在充分消化吸收国外现有煤直接液化工艺的基础上,利用先进工程技术,经过工艺开发创新,依靠自身技术力量,形成了具有自主知识产权的神华煤直接液化工艺神华煤直接液化工艺技术特点1) 采用超细水合氧化铁(FeOOH)作为液化催化剂。
以Fe 2 + 为原料,以部分液化原料煤为载体,制成的超细水合氧化铁,粒径小、催化活性高。
2) 过程溶剂采用催化预加氢的供氢溶剂。
煤液化过程溶剂采用催化预加氢,可以制备45% ~50%流动性好的高浓度油煤浆;较强供氢性能的过程溶剂防止煤浆在预热器加热过程中结焦,供氢溶剂还可以提高煤液化过程的转化率和油收率。
3)强制循环悬浮床反应器。
该类型反应器使得煤液化反应器轴向温度分布均匀,反应温度控制容易;由于强制循环悬浮床反应器气体滞留系数低,反应器液相利用率高;煤液化物料在反应器中有较高的液速,可以有效阻止煤中矿物质和外加催化剂4)减压蒸馏固液分离。
减压蒸馏是一种成熟有效的脱除沥青和固体的分离方法,减压蒸馏的馏出物中几乎不含沥青,是循环溶剂的催化加氢的合格原料,减压蒸馏的残渣含固体50%左右。
5) 循环溶剂和煤液化初级产品采用强制循环悬浮床加氢。
悬浮床反应器较灵活地催化,延长了稳定加氢的操作周期,避免了固定床反应由于催化剂积炭压差增大的风险;经稳定加氢的煤液化初级产品性质稳定,便于加工;与固定床相比,悬浮床操作性更加稳定、操作周期更长、原料适应性更广。
神华示范装置运行结果表明,神华煤直接液化工艺技术先进,是唯一经过工业化规模和长周期运行验证的煤直接液化工艺。
神华煤直接液化工艺技术优势1)单系列处理量大。
由于采用高效煤液化催化剂、全部供氢性循环溶剂以及强制循环的悬浮床反应器,神华煤直接液化工艺单系列处理液化煤量为6000 t/d。
国外大部分煤直接液化采用鼓泡床反应器的煤直接液化工艺,单系列最大处理液化煤量为每天2500 ~3000 t。
煤直接液化工艺中的溶剂
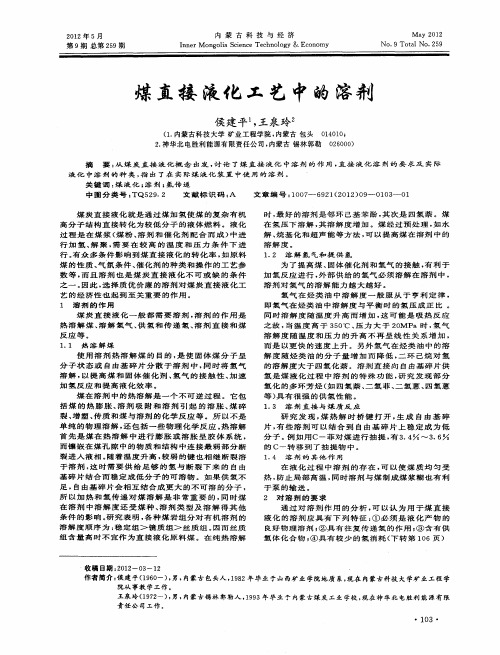
煤 炭 直 接 液 化 一 般 都 需 要 溶 剂 , 剂 的 作 用 是 溶 热 溶 解 煤 、 解 氢 气 、 氢 和 传 递 氢 、 剂 直 接 和 煤 溶 供 溶 反应 等 。
1 1 热 溶 解 煤 .
使 用 溶 剂 热 溶 解 煤 的 目 的 , 使 固 体 煤 分 子 呈 是
分 子 状 态 或 自 由 基 碎 片 分 散 于 溶 剂 中 , 时 将 氢 气 同
溶解 度 随温度 和压 力 的升 高 不再 呈线 性 关 系增 加 , 而 是 以 更 快 的 速 度 上 升 。 另 外 氢 气 在 烃 类 油 中 的 溶 解 度 随 烃 类 油 的 分 子 量 增 加 而 降 低 , 环 己烷 对 氢 二 的 溶 解 度 大 于 四 氢 化 萘 。溶 剂 直 接 向 自 由基 碎 片 供 氢 是 煤 液 化 过 程 中 溶 剂 的 特 殊 功 能 , 究 发 现 部 分 研 氢 化 的 多 环 芳 烃 ( 四 氢 萘 、 氢 菲 、 氢 蒽 、 氢 蒽 如 二 二 四 等) 有很强 的供氢性 能 。 具
研 究 发 现 , 热 解 时 桥 键 打 开 , 成 自 由 基 碎 煤 生
片 , 些 溶 剂 可 以 结 合 到 自 由基 碎 片 上 稳 定 成 为 低 有 分 子 。例 如 用 C一 菲 对 煤 进 行 抽 提 , 3 4 ~ 3 6 有 . . %
的 C一 转 移 到 了 抽 提 物 中 。
- 1、下载文档前请自行甄别文档内容的完整性,平台不提供额外的编辑、内容补充、找答案等附加服务。
- 2、"仅部分预览"的文档,不可在线预览部分如存在完整性等问题,可反馈申请退款(可完整预览的文档不适用该条件!)。
- 3、如文档侵犯您的权益,请联系客服反馈,我们会尽快为您处理(人工客服工作时间:9:00-18:30)。
煤(daf)可得到13.8t 汽油、47.7t 中油和24.3t C1~C4气 态烃产品。每生产1t 汽油和液化气需要煤3.6t,其中38% 用于制氢、27%用于动力和约35%用于液化本身,故液化 效率约为44%。 可见,德国煤直接加氢液化的老工艺能源转化效率低,再 加上反应条件苛刻,缺乏竞争性,人们纷纷寻求降低反应 压力和提高过程效率,最终降低液化过程成本的新工艺。
个反应器进行,有效缩短工艺流程 采用沸腾床催化反应器和钴-钼加氢催化剂,反应器中物料混合
充分,所以H-Coal工艺在反应器温度控制上,产品性质的稳定性 上具有较大的优势。
4.3 溶剂精炼煤工艺(SRC法)
1960年美国煤炭研究局组织开始溶剂精炼煤的研究工作。 SRC法是煤在较高的压力和温度下,在有氢存在的条件下
品。
4.6 俄罗斯低压液化工艺
前苏联在20世纪70~80年代针对世界上最大的、露天开 采煤矿坎斯克-阿钦斯克、库兹涅茨(西伯利亚)煤田的煤 质特点,开发了低压(6~10MPa)煤直接液化工艺。 该工艺采用乳化钼催化剂,反应温度425~435℃,液相 加氢阶段反应时间为30~60min。1983年在图拉州建成了处 理煤炭5~10t/d ~t/d的“CT-5”中试装置,实验工作进行了 7年。在此基础上前苏联先后完成了处理煤炭75t/d “CT75”和500t/d“CT-500”的大型中试厂的详细工程设计, 并初步完成年产50万吨油品的煤直接液化厂工程设计。
1981年鲁尔煤炭和菲巴石油在Bottrop建成了200t/d的中试 厂。该试验厂从1981年一直运行到1987年4月,从170,000 吨煤中生产出超过85,000吨的蒸馏产品,运行时间累计达 22,000小时。
1997年,中国煤炭科学研究总院与DMT和鲁尔煤炭公司 签订了2年的协议,进行中国云南先锋煤液化5000t/d示范 厂的可行性研究。
4.4 埃克森供氢溶剂工艺(EDS工艺)
埃克森供氢溶剂工艺(EDS工艺),是 美国Exxon石油公 司开发的一种煤炭直接液化工艺。
Exxon公司从1966年对EDS工艺进行开发,并在0.5t/d的连 续试验装置上确认了EDS工艺的技术可行性。
1975年6月,在Baytown建立了250t/d的工业性试验厂,完 成了EDS工艺的研究开发工作。
4.5 NEDOL工艺
工艺流程图
10MPa 320~400℃
4.5 NEDOL工艺
工艺特点
反应压力较低,压力为17~ 19MPa ,反应温度430~465 ℃; 催化剂采用合成硫化铁或天然硫铁矿; 固液分离采用减压蒸馏的方法; 配煤浆用的循环溶剂单独加氢,以提高溶剂的供氢能力; 液化油含有较多的杂原子,还须加氢提质才能获得合格产
4.3.1 SRC-Ⅰ直接液化工艺
SRC-I工艺
SRC-I工艺由美国匹兹堡密德威煤炭矿业公司 (Pittsburg and Midway Coal Mining Company , P&M)于六十年代初根据二次大战前德国的PottBroche工艺的原理开发出来的。
4.3.1 SRC-Ⅰ直接液化工艺
SRC-II,EDS,H-Coal,IGOR,NEDOL,CT-5
□两段液化工艺 通过两个液化反应器生产液体产品。第一段的主 要功能是煤的热解,在此段中不加催化剂或加入低活性可弃性催 化剂。第一段的反应产物在第二段反应器中在高活性催化剂存在 下加氢再生产出液体产品。
CTSL,HTI,神华工艺
□煤油共炼工艺 煤和石油混合处理,生产液化产品。此工艺也可
煤粉
煤制浆
循环溶剂
430℃ 10~15MPa
萃取器
过滤
加氢
60%
蒸馏
半焦
40%
干馏
加氢
德国:Pott-Broche 液化工艺(溶剂萃取法)
氢 液化油
◎液化反应器(萃取器):不加氢,不使用催化剂; ◎循环溶剂:离线加氢; ◎缺点:易结焦,过滤困难,传热差。
4.3.1 SRC-Ⅰ直接液化工艺
SRC-Ⅰ工艺流程
德国的IG工艺可分为两段加氢过程,第一段加氢是在高 压氢气下,煤加氢生成液体油(中质油等),又称煤浆液 相加氢。第二段加氢是以第一段加氢的产物为原料,进行 催化气相加氢制得成品油,又称中油气相加氢,所以IG 法也常称作两段加氢法。
2.1 工艺流程
第一段液相加氢
30~70 MPa
470~480℃
气体
汽油 柴油 航空燃料
残渣
380-390 oC 15-18 MPa
2、德国煤加氢液化老工艺
德国是世界上第一家拥有煤直接加氢液化工业化生产经验 的国家。其第一套生产装置由德国I.G.Farbenindustrie(燃 料公司)在1927年建成,也被称为IG工艺。德国煤加氢液 化老工艺是世界其他国家开发同类工艺的基础。
14MPa
438~466℃
371~399℃
4.3.2 SRC-Ⅱ直接液化工艺
SRC-Ⅱ工艺特点 SRC-Ⅱ法与SRC-Ⅰ法的不同点: 气液分离器底部分出的热淤浆的一部分作为循环溶剂返回
制煤浆,另一部分进减压蒸馏,部分淤浆循环的优点有, 一是延长中间产物在反应器内的停留时间,增加反应深度; 二是矿物含有硫铁矿,提高了反应器内硫铁矿浓度,相对 而言添加了催化剂,有利于加氢反应,增加液体油产率; 用减压蒸馏替代残渣过滤分离,省去过滤、脱灰和产物固 化等工序; 产品以油为主,氢耗量比SRC-Ⅰ高一倍。
以划到上述两种工艺中去。
HRI,CCLC
4.1 德国IGOR+工艺
IGOR+(Integrated Gross Oil Refining)工艺由德国矿业 研究院(DMT)、鲁尔煤炭公司(Ruhrkohle AG)和菲 巴石油公司(Veba Oil)在IG工艺基础上开发而成。该工 艺在DMT建立了0.2t/d连续试验装置。
让循环溶剂在进入煤预处理过程之前,先经过固定床加氢 反应器对溶剂加氢,以提高溶剂的供氢能力,这是EDS工 艺的关键特征,工艺名称也由此得来。
4.4 埃克森供氢溶剂工艺(EDS工艺)
工艺流程图
17.5MPa 425~450℃
工艺特点
供氢溶剂催化加氢,提高了 催化剂的使用寿命,催化剂 是Co-Mo和Ni-Mo;
4.2 氢煤法(H-Coal)
H-Coal工艺始于1963年,由美国Hydrocarbon Research Inc.( HRI)开发。H-Coal工艺的许多基本概念都来源于HRI的用于 重油提质加工的H-Oil工艺。
在美国政府的支持下,HRI于1974年9月开始着手设计 200~600t/d的工业性试验装置,1976年12月15日200~600t/d的 工业性试验装置在肯塔基的Catlettsburg破土动工,1980年开 始运转, 1983年运转结束。
4.1 德国IGOR+工艺
工艺流程图
350~420℃
30MPa 470℃
4.1 德国IGOR+工艺
工艺特点
液化残渣的固液分离由过滤改为减压蒸馏,设备 处理能力增大,操作简单,蒸馏残渣在高温下仍 可用泵输送;
循环油由重油改为中油与催化加氢重油混合油, 不含固体,也基本上不含沥烯,煤浆黏度大大降 低,溶剂的供氢能力增强,反应压力由70MPa降 低到30MPa,反应条件相对缓和些;
煤加氢直接液化工艺
煤直接液化基本工艺流程 德国煤加氢液化老工艺 典型煤直接液化工艺 煤-油共处理
1、煤直接液化基本工艺流程
煤直接液化工艺流程简图
催化剂
氢气 氢循环
煤
煤浆制
备单元
反应 单元
分离 单元
循环溶剂
煤:<0.2mm 催化剂: Fe-S系
420-470 oC 17-30 MPa
提质加 工单元
它的主要特点是采用了沸腾床催化反应器,这是H-Coal工艺 区别于其他液化工艺的显著特点,属于一段催化液化工艺。
455
℃
4.2 氢煤法(H-Coal)
工艺特点 操作灵活性大,对原料煤种的适应性和对液化煤种的可调性好 流化床内传热传质效果好,有助于提高煤的转化率。 煤的催化液化反应、循环溶剂加氢反应和液化产物精制过程在一
进行溶剂萃取加氢,生产低灰、低硫的清洁固体燃料和液 体燃料。过程中除煤中所含的矿物质以外,不用其他催化 剂。 该法属加氢抽提液化工艺。通常根据产品形态不同又分为 SRC-Ⅰ和SRC-Ⅱ。SRC-Ⅰ是以生产低灰、低硫固体精炼 煤(发热量38.7MJ/kg)为主,煤浆在反应器中的操作条 件是:停留时间40min;出口温度450℃;压力10~13MPa 。SRC-Ⅱ以生产液体燃料为主,煤浆停留时间1小时。
3、典型煤直接液化工艺
通常人们所谓的典型工艺一般是已通过50t/d以上规模工业
性试验验证的较成熟的工艺。
◎20世纪60年代工艺 SRC (SRC I和SRC II),美国,OCR EDS (供氢溶剂法),美国,Exxon H-Coal (氢煤法),美国,HRI (HTI)
◎20世纪70年代工艺 IGOR (IG新工艺),德国,DMT HTI (基于H-Coal),美国,HTI NEDOL (基于EDS和IGOR), 日本, NEDO
过滤分离得到的滤液,即重质油,含有较多的沥青烯和 2%~12%的固体,作为煤浆加氢循环溶剂,其供氢能力较差 ,沥青烯积累会使煤浆黏度上升,这正是德国老工艺需要 70MPa反应压力的主要原因之一;滤饼含固体38%~40%, 为回收滤饼中的油,对滤饼进行干馏,可回收滤饼中约30% 的油。
2.2 工艺特点
◎20世纪80年代工艺 CT-5(低压),俄罗斯,前苏联国家科学院 CTSL(两段液化),美国,HRI (HTI) HRI(煤油共炼),美国,HRI (HTI)
◎21世纪 (2004) 工艺 神华工艺(基于HTI和NEDOL), 中国, 神华