大型超高钢结构整体提升技术DOC
超大型项目钢结构安装施工技术
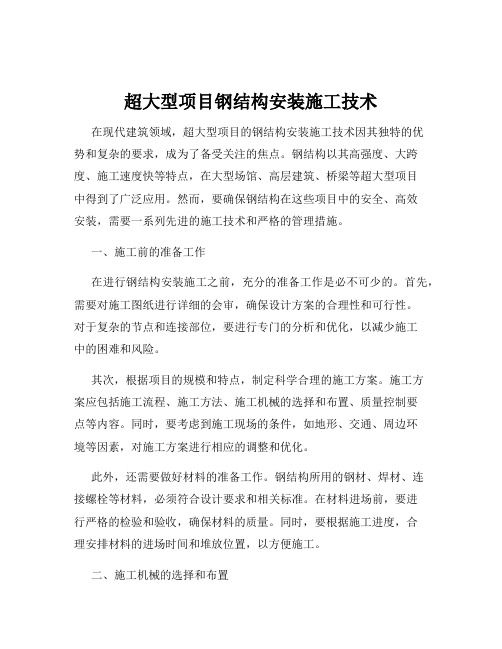
超大型项目钢结构安装施工技术在现代建筑领域,超大型项目的钢结构安装施工技术因其独特的优势和复杂的要求,成为了备受关注的焦点。
钢结构以其高强度、大跨度、施工速度快等特点,在大型场馆、高层建筑、桥梁等超大型项目中得到了广泛应用。
然而,要确保钢结构在这些项目中的安全、高效安装,需要一系列先进的施工技术和严格的管理措施。
一、施工前的准备工作在进行钢结构安装施工之前,充分的准备工作是必不可少的。
首先,需要对施工图纸进行详细的会审,确保设计方案的合理性和可行性。
对于复杂的节点和连接部位,要进行专门的分析和优化,以减少施工中的困难和风险。
其次,根据项目的规模和特点,制定科学合理的施工方案。
施工方案应包括施工流程、施工方法、施工机械的选择和布置、质量控制要点等内容。
同时,要考虑到施工现场的条件,如地形、交通、周边环境等因素,对施工方案进行相应的调整和优化。
此外,还需要做好材料的准备工作。
钢结构所用的钢材、焊材、连接螺栓等材料,必须符合设计要求和相关标准。
在材料进场前,要进行严格的检验和验收,确保材料的质量。
同时,要根据施工进度,合理安排材料的进场时间和堆放位置,以方便施工。
二、施工机械的选择和布置超大型项目的钢结构安装通常需要使用大型的施工机械,如塔吊、履带吊、汽车吊等。
在选择施工机械时,要根据钢结构的重量、形状、安装高度和位置等因素,综合考虑机械的起重能力、工作半径、起升高度等参数。
同时,要考虑到施工机械的经济性和通用性,尽量选择能够满足多种施工要求的机械。
在施工机械的布置方面,要根据施工现场的实际情况,合理规划机械的位置和行走路线。
要确保施工机械的工作范围能够覆盖整个施工区域,同时要避免机械之间的相互干扰和碰撞。
对于需要多台机械协同作业的情况,要制定详细的协同方案,明确各机械的工作任务和配合方式。
三、钢结构的运输和堆放钢结构在运输过程中,要采取有效的防护措施,防止构件的变形和损坏。
对于超长、超宽、超高的构件,要办理相应的运输手续,并制定专门的运输方案。
特大重型钢结构屋盖整体提升施工技术

特大重型钢结构屋盖整体提升施工技术是指在建设高层建筑时,对屋顶钢结构进行整体提升的一种施工技术。
该技术可以有效提高施工效率,减少施工风险,保障施工质量。
本文将从施工前的准备工作、具体施工步骤和施工中可能遇到的问题及解决方法等方面进行详细介绍。
一、施工前的准备工作:1.编制详细的施工方案:根据建筑设计图纸及实际情况,制定详细的施工方案,包括吊装设备的选择、吊装点的确定、吊装顺序的安排等。
2.准备好相关设备和工具:确保吊装设备、起重机械、钢丝绳等设备和工具的完好性和可用性。
3.进行安全评估:对整个施工过程进行全面的安全评估和风险分析,确保施工过程中的安全。
二、具体施工步骤:1.设置起重平台:根据施工方案,确定起重平台的位置和尺寸,并进行固定。
2.安装吊装设备:根据需要,选择合适的吊装设备,并进行安装和调试。
3.设置吊装点:根据设计要求,确定吊装点的位置和数量,并进行标记。
4.吊装准备:对吊装设备进行检查和维护,并进行试吊,确保吊装设备的正常运行。
5.进行吊装作业:根据施工方案,按照预定的吊装顺序对钢结构进行整体提升。
在吊装过程中,需要严格控制吊装速度和角度,确保吊装的平稳进行。
6.吊装完成后的检查和调整:在吊装完成后,对提升的钢结构进行检查和调整,确保钢结构的水平和垂直度达到设计要求。
三、施工中可能遇到的问题及解决方法:1.地面承载能力不足:在施工前需要进行地面的承载能力分析,如发现地基承载能力不足时,可以使用加固措施,如设置地基承台、加强地基等。
2.吊装设备故障:在施工过程中,吊装设备可能遇到故障,需要及时进行维修和更换,确保吊装作业的连续进行。
3.钢结构变形:在吊装过程中,钢结构可能发生变形,需要通过调整吊装速度和角度等方式进行控制,避免钢结构的进一步变形。
4.施工现场环境复杂:在特大重型钢结构屋盖整体提升施工中,施工现场环境复杂,需要严格控制施工现场的安全与秩序,确保施工顺利进行。
综上所述,特大重型钢结构屋盖整体提升施工技术是一种高效、安全、稳定的施工方法。
重型结构整体提升技术规范

8、专人辅助观察钢结构提升的同步情况,可采用专用仪器进行同步观察
检查,发现有异常情况及时叫停,进行检查,调整完毕后方可继续提升
四
施工方案里制定了详细的专项应急预案
1 现场设备故障发生的各种应急措施 ………… 2 环境影响 雨天停止高空作业,大雨停止现场作业; 湿度超过80%,停止吊装作业; 如遇大风天气(六级以上),停止吊装作业。 3 吊装间歇过程中的安全问题
液压泵源系统
二 液压提升器 液压提升器是穿芯式千斤顶结构,具有如下优点:
通过提升设备扩展组合,提升重量、跨度、面积不受限制;
采用柔性索具承重。如有合理的承重吊点,提升高度不受限制; 提升器锚具具有逆向运动自锁性,使提升过程十分安全,并且构
件可在提升过程中的任意位置、长期可靠锁定;
设备体积小、自重轻、承载能力大,适宜于在狭小空间或室内进 行大吨位构件提升; 设备自动化程度高,操作方便灵活,安全性好,可靠性高,能够 自行连续工作;
性有充分的保障; 3 将高空作业量降至最少,提升作业时间短,有效保证结构的安装工
期;
4 提升设备体积、重量较小,机动能力强,倒运和安装方便。
液压提升系统介绍:
一 液压泵源系统
液压泵源系统为提升器提供液压动力,在各种液压阀的控制下 完成相应动作。 泵源液压系统的设计采用了模块化结构。根据提升重物吊点的 布置以及提升器数量和泵源流量,可进行多个模块的组合,每一套 模块以一套泵源系统为核心,可独立控制一组液压提升器,同时可 用比例阀进行多吊点扩展,以满足实际提升工程的需要。
液压提升器
二
液压提升器工作原理
第1步:上锚紧,夹紧钢绞线;
第2步:提升器提升重物;
第3步:下锚紧,夹紧钢绞线;
大跨空间钢结构整体提升施工技术分析

大跨空间钢结构整体提升施工技术分析摘要:大跨度空间结构钢结构的应用,能够极大提升建筑物的观赏性和建设水平,还能够节省大量的建筑材料,确保建筑物的质量安全。
本文就大跨度空间钢结构的施工技术进行了探析,希望能够对今后的相关研究提供参考。
关键词:大跨空间钢结构;整体提升;施工技术1、大跨度空间钢结构施工技术的特点(1)空间钢结构跨度大,材质高档,钢板厚度大。
随着社会科学技术与经济的不断发展,我国建筑理念产生了巨大的变化,为了充分满足广大客户的实际生活需求,建筑功能技术有了进一步的革新。
其中现代空间钢结构的跨度开始朝着更大范围发展。
为了确保建筑物的质量与施工安全性,国家超限专家审查委员会规定,这种建筑物要利用高强度级别的钢材,通过严格检测,确保钢板材料的厚度与质量。
(2)空间钢结构形式多种多样。
现如今大跨度空间钢结构在原本的形式上进行了创新与发展,已经具备了全新的组合模式。
比如,将大跨度弦支穹顶作为钢结构的奥运会的羽毛球馆,利用泡沫理论式多面体作为空间钢结构的水立方,或者是利用仿生态的设计理念的现代空间钢结构,能够让建筑形式变得更加丰富。
(3)空间钢结构的构件数量多,设计难度大。
在大型工程当中,所需要的构建种类多样,数量大,这就增加了施工难度,直接对施工进程带来了影响。
所以,要通过多次试验以及研究才能确保施工质量同时按时竣工。
(4)构建精确度要求非常严格,焊接施工难度高。
现如今的大部分大跨度空间钢结构的建筑工程都是由国家指派的重点工程项目,它们在施工质量标准方面具有非常高的要求。
所以,有关部门在施工当中要保证空间钢结构的构建精确度与焊缝技术,这就增加了施工困难程度。
另外,施工当中还需要对材质预拼装以及焊接。
为了确保工程施工质量与安全程度,在传统技术手段的基础上来创新钢结构,工作人员要数量掌握好多种技术手段,解决施工当中的困难问题。
(5)空间钢结构的施工与预应力施工技术相结合。
空间钢结构当中的预应力技术具体是指运用预加应力的方式,针对空间钢结构的内力分布情况进行调整,通过向空间钢结构施加压力,加强材料强度,扩大结构刚度。
大型钢结构整体提升工法

大型钢结构整体提升工法哎,说起大型钢结构整体提升工法,这可真是个让人耳目一新的话题。
要是你没听说过,那就真得跟我一起走一趟这个神奇的工地现场了。
别看钢结构就那么硬邦邦的,它的“飞天”过程,简直像是变魔术一样,让人不禁想“哇,牛!”你想象一下,一栋几千吨重的钢铁建筑,居然能在几个小时内从地面“飞”到几十米高,稳稳地落在指定位置。
这可不是科幻片里才有的情节,这就是大型钢结构整体提升的日常操作。
想要搞清楚这个工法到底咋回事,还得先从“整体提升”这几个字说起。
你要是站在工地上看着,看到的不仅是几十根钢梁像拼图一样一块块拼接成大楼的骨架,钢结构的底座、框架甚至大梁,居然能一起整体抬起来,这个技术绝对不简单。
你想啊,钢结构的重量可是吓人的,一根梁重得跟大象差不多,要是一根梁崩了,那可真是“前途未卜”。
但这种整体提升工法就是通过一套巧妙的系统,先把建筑物下方架好支撑,接着利用一根根提升绳、液压千斤顶,把这个庞然大物一点一点抬起来,等它“腾空”之后,再缓缓移到新位置。
这种方法简直是把原本“想得可怕”的操作,变得既安全又高效。
你可能会问,这种技术难不难?其实不难。
你听我说,整个工法最大的挑战就是如何确保钢结构在升高的过程中不歪斜,不出现晃动。
想象一下,如果一根钢梁偏了,整个建筑就会不稳,后果不堪设想。
所以每一步都得精准到位。
这就像是大家一起搭积木,你手稍微抖一下,整个塔楼就得重新来过。
至于这套提升系统,简直像是钢铁版的“升降机”,整个过程中操作员得像老练的指挥家一样指挥每一根千斤顶、每一条钢索,丝毫不差。
不过,最有意思的地方还是在于,钢结构整体提升不仅仅是为了方便,而是为了节约时间和成本。
大家都知道,建一座高楼,光是地基部分就得浪费不少时间。
如果按照传统的方式,地基做完再一点一点地建上去,速度可想而知。
而通过提升技术,整个建筑可以提前拼装好,一旦完成整体提升,简直就是“秒完成”。
就好像你买个大件家具,提前在家拼好,到了现场一推就能装好了,省时省力,还避免了无谓的返工。
大跨度钢结构桁架整体提升施工工法

大跨度钢结构桁架整体提升施工工法大跨度钢结构桁架整体提升施工工法一、前言大跨度钢结构桁架整体提升施工工法是一种应用于大型建筑工程中的先进施工技术,通过整体提升的方式将钢结构桁架安装到预定位置,具有施工效率高、质量可控、安全可靠等优点。
二、工法特点1. 施工效率高:利用整体提升的方式可以将大跨度钢结构桁架一次性安装到位,避免了逐段组装的繁琐过程,提高了施工效率。
2. 质量可控:整体提升施工能够保证钢结构桁架的整体性和一致性,避免了由于拼装过程中产生的尺寸误差和接头强度不足等问题。
3. 安全可靠:利用整体提升施工方式,降低了施工现场的危险性,减少了高空作业和高风险作业的时间和频率,提高了工人的安全系数。
三、适应范围大跨度钢结构桁架整体提升施工工法适用于各类大型建筑工程,特别是那些要求结构整体性和施工进度的工程,如体育馆、展览中心、机场大厅等。
四、工艺原理采用大跨度钢结构桁架整体提升施工工法时,需要首先进行详细的工程测量和设计,确定提升方案和提升轨道。
在施工过程中,需要采取多项技术措施,包括施工设备的选择与调试、搭设提升轨道、提升控制技术等,以实现工法的成功应用。
五、施工工艺大跨度钢结构桁架整体提升施工工法的具体施工工艺包括以下几个阶段:1. 基础准备:确保施工场地平整,并按照设计要求搭设起提升轨道。
2. 提升之前准备:安装起重设备,进行设备调试和安全检查。
3. 支撑装置设置:在桁架下方安装支撑装置,以保证整体提升过程中的稳定性。
4. 钢结构桁架整体提升:通过起重设备将钢结构桁架整体提升到预定位置。
5. 安装调整:在提升到位后,进行调整和固定,确保钢结构桁架的水平度和垂直度。
6. 拆除支撑装置:在整体提升完成后,拆除支撑装置,完成钢结构桁架的安装。
六、劳动组织在大跨度钢结构桁架整体提升施工工法中,需要组织一支高效的施工队伍,包括项目经理、技术人员、操作工等,确保施工过程的顺利进行。
七、机具设备该工法所需的机具设备包括起重机、电动葫芦、调整工具等。
特大重型钢结构屋盖整体提升施工技术范本(2篇)
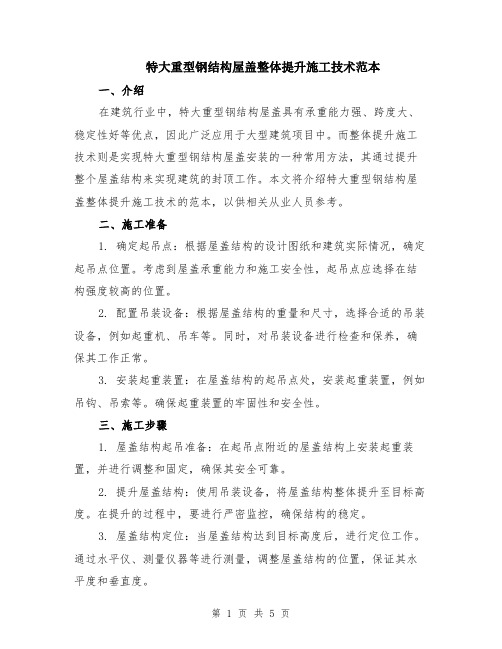
特大重型钢结构屋盖整体提升施工技术范本一、介绍在建筑行业中,特大重型钢结构屋盖具有承重能力强、跨度大、稳定性好等优点,因此广泛应用于大型建筑项目中。
而整体提升施工技术则是实现特大重型钢结构屋盖安装的一种常用方法,其通过提升整个屋盖结构来实现建筑的封顶工作。
本文将介绍特大重型钢结构屋盖整体提升施工技术的范本,以供相关从业人员参考。
二、施工准备1. 确定起吊点:根据屋盖结构的设计图纸和建筑实际情况,确定起吊点位置。
考虑到屋盖承重能力和施工安全性,起吊点应选择在结构强度较高的位置。
2. 配置吊装设备:根据屋盖结构的重量和尺寸,选择合适的吊装设备,例如起重机、吊车等。
同时,对吊装设备进行检查和保养,确保其工作正常。
3. 安装起重装置:在屋盖结构的起吊点处,安装起重装置,例如吊钩、吊索等。
确保起重装置的牢固性和安全性。
三、施工步骤1. 屋盖结构起吊准备:在起吊点附近的屋盖结构上安装起重装置,并进行调整和固定,确保其安全可靠。
2. 提升屋盖结构:使用吊装设备,将屋盖结构整体提升至目标高度。
在提升的过程中,要进行严密监控,确保结构的稳定。
3. 屋盖结构定位:当屋盖结构达到目标高度后,进行定位工作。
通过水平仪、测量仪器等进行测量,调整屋盖结构的位置,保证其水平度和垂直度。
4. 屋盖结构固定:在屋盖结构定位完成后,进行固定工作。
根据设计要求,使用螺栓、焊接等方式将屋盖结构与建筑主体连接起来,确保结构的牢固性。
四、施工注意事项1. 安全第一:在施工过程中,需严格遵守相关安全规定,确保施工人员的安全。
同时,要保证吊装设备和起重装置的安全可靠,防止发生意外事故。
2. 吊装控制:要进行严密的吊装控制,确保屋盖结构的稳定。
在起吊和下放的过程中,要注意保持结构的水平度和垂直度,避免结构变形或倾斜。
3. 定位精确:定位工作是整体提升施工中至关重要的环节。
要使用精密的测量工具,确保屋盖结构的位置精确,避免后续施工出现不符合设计要求的情况。
钢结构工程整体顶升法施工方案

钢结构工程整体顶升法施工方案1 定义:网架整体顶生法是把网架在设计位置的地面拼装成整体,然后用千斤顶将网架整体顶升到设计标高.2 技术准备1.顶升法利用原有结构柱作为顶升支架,也可另设专门的支架或枕木垛垫高.2.顶升法一般用液压千斤顶顶升,设备较小,当少支柱的大型网架采用顶升方法施工时,也用专用的大型千斤顶.3.除用专用支架外,顶升时网架支承情况与使用阶段基本一致.4.为了充分发挥千斤顶的起重能力,可将全部屋面结构及电气通风设备在地面安装完毕,一并顶升至设标高,减少高空作降低成本.5.顶升法是将千斤顶放在网架的下面,顶升行程路线必须设导向措施,以防网架顶升过程中网架发生偏转.3 材料要求1.顶升支架或枕木的材料应符合有关标准.2.导向滑道一般用园钢、槽钢、角钢等.3.其他材料按2.4.2条规定执行.4 主要机具1.除按2.4.3机具表外,补充如表4-1表4-1 主要机具5作业条件1.网架结构连地面就位拼好,检查验收完毕,其他附属结构及设备安装完毕,并通过验收.2.用原有结构柱作为顶升支架,或另设专门顶升支架进行稳定性计算,如果不够进行加固或采取缆风措施,经检查合格.3.选好和做好枕木垛,支搭牢固,做为千斤顶支座,验收合格.4.做好导向滑道,位置准确牢固.5.安装顶升设备,并试顶,检查合格.6.除以上几条外,遵照2.4.4作业条件执行.2.21 整体顶升法—材料和质量要点2.21.1材料的关键要求.1.对专用顶升支架,材料质量枕木做千斤顶支座的枕木质量,必须符合有关质量标准.2.缆风用的钢丝绳、导向用的型钢均符合有关标准.2.21.2技术质量关键要求.1.顶升的同步控制及垂直上升.网架整体顶升时必须严格保持同步,如各支点间产生升差会造成下列的影响.1)造成杆件内力和柱顶压力的变化.其影响程度与网架结构形成、顶升支点的间距、升差的大小等有关.网架刚度愈大、顶升点愈近、升差愈大,则对杆件内力影响就愈大,反之则小.网架规程中规定千斤顶负荷折减系取0.4-0.6大体上是合适的.网架整体顶升时,各顶升点的允许升差值为各顶升支柱间距的1/1000,且不大于30mm.2)造成网架的偏移.(1)由于顶升时升差值的影响,会引起结构杆件和千斤顶受力不均而造成危害.如提升差值控制在网架规程规定范围内,重屋盖时使杆力控制在容许应力范围内.但是,控制提升高差更重要的是为了减少网架的偏移.(2)影响网架偏移的主要因素是顶升时不同步造成的,其次是柱子的刚度.由顶升时不同步造成网架偏移值多大?这与网架的刚度和顶升点距离有关.网架的偏移,往往是这些因素的综合影响.网架偏移值和方向也是随机的,事先不易估计准确.纠偏方法也较麻烦且不安全.因此,在操作上应严格控制各顶升点的同步上升是积极的措施.即应以预防为主的观点,尽量减少这种偏移.(3)设置导轨很为重要.在试验工程中发现,网架在向上运动中不需要太大的水平力,网架即能平移.导轨的作用不但使网架垂直地上升而且是安全装置.在该工程中结构柱的四根角钢即起导轨的作用,角钢与支座板间空隙为20mm, 即顶升过程中不允许网架偏移20mm.在顶升过程中曾有数次接近角钢,均通过纠偏给予还原.(4)纠偏方法可以把千斤顶垫斜或人为造成反向升差,或将千斤顶平放,水平支顶网架支座.由于以上两点理由,网架顶升时应控制网架的同步上升,升差值应控制在规定范围内.2.柱子稳定当利用结构柱作为顶升的支承结构时,应注意柱子在顶升过程中的稳定性.1)应验算柱子在施工过程中承受风力及垂直荷载作用下的稳定性.2)并采取措施保证柱子在施工期间的稳定性.3)及时连接上柱间支撑、钢格构柱的缀板;当为钢筋混凝土柱时,如沿柱高度有框架梁及连系梁时, 应及时浇筑混凝土.(4)网架顶升时遇到上述情况,均应停止顶升,待柱的连系结构施工完毕,并达到要求强度后再继续顶升.。
大型钢结构整体提升与滑移施工工法
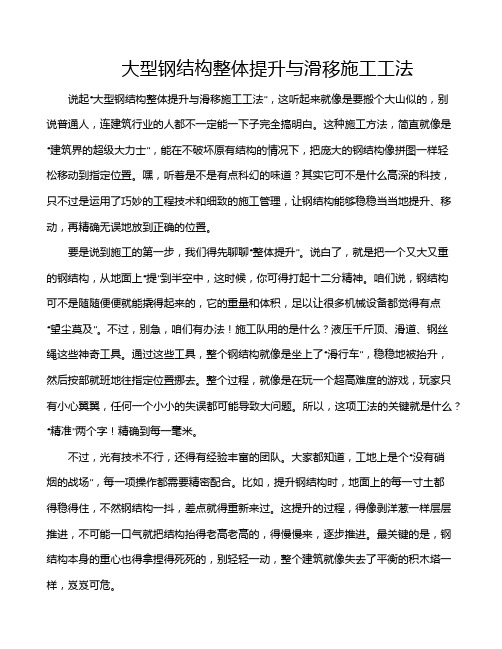
大型钢结构整体提升与滑移施工工法说起“大型钢结构整体提升与滑移施工工法”,这听起来就像是要搬个大山似的,别说普通人,连建筑行业的人都不一定能一下子完全搞明白。
这种施工方法,简直就像是“建筑界的超级大力士”,能在不破坏原有结构的情况下,把庞大的钢结构像拼图一样轻松移动到指定位置。
嘿,听着是不是有点科幻的味道?其实它可不是什么高深的科技,只不过是运用了巧妙的工程技术和细致的施工管理,让钢结构能够稳稳当当地提升、移动,再精确无误地放到正确的位置。
要是说到施工的第一步,我们得先聊聊“整体提升”。
说白了,就是把一个又大又重的钢结构,从地面上“提”到半空中,这时候,你可得打起十二分精神。
咱们说,钢结构可不是随随便便就能撬得起来的,它的重量和体积,足以让很多机械设备都觉得有点“望尘莫及”。
不过,别急,咱们有办法!施工队用的是什么?液压千斤顶、滑道、钢丝绳这些神奇工具。
通过这些工具,整个钢结构就像是坐上了“滑行车”,稳稳地被抬升,然后按部就班地往指定位置挪去。
整个过程,就像是在玩一个超高难度的游戏,玩家只有小心翼翼,任何一个小小的失误都可能导致大问题。
所以,这项工法的关键就是什么?“精准”两个字!精确到每一毫米。
不过,光有技术不行,还得有经验丰富的团队。
大家都知道,工地上是个“没有硝烟的战场”,每一项操作都需要精密配合。
比如,提升钢结构时,地面上的每一寸土都得稳得住,不然钢结构一抖,差点就得重新来过。
这提升的过程,得像剥洋葱一样层层推进,不可能一口气就把结构抬得老高老高的,得慢慢来,逐步推进。
最关键的是,钢结构本身的重心也得拿捏得死死的,别轻轻一动,整个建筑就像失去了平衡的积木塔一样,岌岌可危。
然后,再说到“滑移施工”。
滑移,就像是给钢结构穿上了溜冰鞋,缓慢而又平稳地在指定的轨道上滑行。
你可别以为这很简单,实际上,这里面有不少技术含量。
要确保滑移的路径是完全平整的,任何一处不平的地方,都会导致结构滑移的不顺畅。
特大重型钢结构屋盖整体提升施工技术模版

特大重型钢结构屋盖整体提升施工技术模版一、背景介绍钢结构在建筑领域中具有很大的应用潜力,特大重型钢结构屋盖是其中的一种重要应用形式。
这种屋盖的特点是体积庞大、承载能力高、施工难度大等。
传统的施工方式存在一些问题,例如施工周期长、人工劳动强度大、工序繁琐等。
因此,为了提高施工效率和质量,我们需要引入一种全新的整体提升施工技术。
二、施工技术原理整体提升施工技术是通过使用钢索和起重设备将重型钢结构屋盖整体提升到预定的高度,并进行定位、调整和固定。
该技术可以减少施工过程中的拼接工序,提高屋盖的整体性和施工效率。
具体的施工步骤如下:1. 预制基座:根据设计要求,在现场搭建基座,用于支撑整体提升施工过程中的起重设备。
2. 准备整体提升设备:将起重设备(例如起重机和钢绳)安装在基座上,并进行检查和调试,确保其正常工作。
3. 将屋盖分段吊装到指定位置:将钢结构屋盖按照设计图纸的顺序和要求分段吊装到指定位置。
在吊装的过程中,要保持屋盖的平衡和稳定,避免发生意外情况。
4. 整体提升:利用起重设备将已经吊装好的多个屋盖分段整体提升到预定的高度。
在整体提升的过程中,要保持屋盖的水平和垂直度,并进行调整和校正。
5. 定位和固定:将提升好的屋盖分段进行定位和固定,确保其位置和姿态与设计要求一致。
在进行定位和固定时,要使用专业的工具和设备,确保固定牢固和稳定。
6. 检查和验收:对整体提升施工进行检查和验收,确保屋盖的施工质量和安全性达到设计要求。
三、施工关键技术1. 预制基座的设计和搭建:预制基座是整体提升施工的基础,其设计和搭建需要考虑屋盖的形状、重量和施工条件等因素。
基座的设计要合理,并且能够承受屋盖整体提升的载荷。
2. 整体提升设备的选择和安装:整体提升设备的选择要考虑屋盖的重量和尺寸,以及施工现场的情况。
安装时,要确保设备的平稳和可靠。
3. 屋盖的吊装和整体提升:在屋盖吊装和整体提升的过程中,要保持屋盖的平衡和稳定,严格按照设计要求进行操作,避免发生意外情况。
特大重型钢结构屋盖整体提升施工技术

特大重型钢结构屋盖整体提升施工技术特大重型钢结构屋盖是指跨度大于50米、面积大于1000平方米的钢结构屋盖。
由于其结构特点复杂,施工难度大,传统的安装方法已经无法满足要求。
因此,发展特大重型钢结构屋盖整体提升施工技术已经成为解决这一问题的关键。
特大重型钢结构屋盖整体提升施工技术是一种将整个钢结构屋盖进行组装后,利用大型起重设备将其整体提升至设计位置的施工方法。
相较于传统的逐根安装方法,整体提升施工技术具有以下优势:首先,整体提升施工技术能够大幅度减少施工时间。
传统的逐根安装方法需要逐一安装并焊接每根钢梁,而整体提升施工技术可以一次性将整个钢结构屋盖安装到位,从而大大缩短了施工时间,提高了工作效率。
其次,整体提升施工技术能够减少工人的劳动强度。
传统的逐根安装方法需要工人在高空操作,身体的承重和危险性较大。
而整体提升施工技术使得工人可以在地面上进行组装和检查,减少了在高空操作的时间和频率,降低了工人的劳动强度,提高了工作安全性。
再次,整体提升施工技术能够减少施工误差。
传统的逐根安装方法容易造成施工误差,导致后期调整困难,影响施工质量。
而整体提升施工技术可以保证整个钢结构屋盖的精度和准确性,从而减少了施工误差,提高了施工质量。
最后,整体提升施工技术能够降低施工成本。
传统的逐根安装方法需要大量的人力、物力和时间成本,而整体提升施工技术可以通过减少施工时间和人员数量,从而降低施工成本,提高了经济效益。
然而,特大重型钢结构屋盖整体提升施工技术也面临一些挑战和问题。
首先是大型起重设备的需求和选择。
特大重型钢结构的整体提升需要大型起重设备来完成,要求设备的起重能力和精度都要满足要求。
其次是施工场地的要求和限制。
特大重型钢结构的整体提升需要充足的空间和平整的场地,施工现场的选择和准备也是影响施工进度和效果的重要因素。
为了克服这些问题,可以采取以下措施和技术。
首先,选择合适的大型起重设备。
根据钢结构屋盖的重量和要求,选择适当的大型起重设备,确保其起重能力和精度满足要求。
大型钢结构施工中的力学原理-整体提升法

整体提升法的介绍及应用随着我国经济建设的快速发展,各类工程建设项目规模日益扩大,重大工程项目包括高耸结构、大跨结构、超高层结构以及一些复杂异形结构等日益增多.这些工程的共同特点是施工规模大、范围广、周期长、过程复杂。
如此复杂的结构势必给工程施工带来更大的挑战,在土木工程建设规模迅速发展的同时,建筑施工中事故不断增多,严重影响人民的生命财产安全及工程建设速度。
工程事故产生的原因是多方面的.其中很多事故是源于设计者与施工企业对施工方法或施工过程对结构的影响估计不足。
事实表明大型复杂建筑物从开始施工建设到投入使用,再到若干年后进入老化维修阶段的整个生命周期过程中,施工阶段因结构的不完整性、材料性质的时变性、所受荷载的复杂性以及结构抗力的不成熟性,结构的平均风险率最高,失效概率最大。
特别对大型复杂钢结构工程而言,由于其结构复杂,施工方法繁琐及钢构件本身易失稳的特性决定了其在施工阶段的风险率要比普通混凝土结构更高.常用的施工方法高空散装法高空散装或满堂脚手原位拼装法高空散装法是指结构小拼单元或散件直接在设计位置进行拼装的方法,施工时有满堂脚手架和悬挑法两种,前者广泛用于网架和网壳的施工,尤其适宜螺栓球节点网架的施工;后者国外施工多用,并曾用于混凝土薄壳的施工。
高空散装法属于满堂脚手架原位拼装方法,单件重量轻,垂直运输无需大型起重设备,工序简单;但是需要架设脚手架,周期长、费用高,高空作业量大,精度难以控制,辅助材料多,费用高。
地面吊装法吊装法分为分段吊装法和整体吊装法。
分段吊装法是指将结构根据自身形式分成块状单元,分别由起重机械吊装至高空设计位置就位.然后再拼装成整体的安装方法.此方法的特点是大部分焊接、拼装工作在地面进行,有利于控制施工质量并可省去大量拼装作支架,但结构分段后需要考虑临时加固措施,后拼杆件、单元接头处仍然需要搭设拼装胎架.国家大剧院采用的安装方法是工厂分段制作,场外立体预拼,单件综合安装。
巨型超重钢结构连廊一次整体提升施工工法

巨型超重钢结构连廊一次整体提升施工工法巨型超重钢结构连廊一次整体提升施工工法一、前言巨型超重钢结构连廊是指由大型钢结构构成的连廊,通常用于连接建筑物或者设备,承载能力巨大,重量较重。
在施工过程中,为了保证连廊的整体安装和提升效果,需要采用一种高效可靠的施工工法。
本篇文章将介绍巨型超重钢结构连廊一次整体提升施工工法的特点、适应范围、工艺原理、施工工艺、劳动组织、机具设备、质量控制、安全措施、经济技术分析和工程实例。
二、工法特点巨型超重钢结构连廊一次整体提升施工工法具有以下特点:1. 整体提升:通过采用专业的施工顶升装置,将整个巨型超重钢结构连廊一次性提升到预定位置,避免了传统分段提升的缺点。
2. 施工高效:由于整个连廊在一次提升中完成,减少了施工时间和人力资源,提高了施工效率。
3.施工质量高:整体提升能够确保施工过程中的位置和尺寸的准确性,保证了连廊的整体结构稳定和强度要求。
4. 安全可靠:通过合理的劳动组织和安全措施,提高了施工安全性,减少了施工事故的发生。
三、适应范围巨型超重钢结构连廊一次整体提升施工工法适用于以下场景:1. 工地空间狭小:在有限的施工空间中,无法进行分段提升或者组装的情况下,利用整体提升工法可以将连廊一次性安装到位。
2. 连廊设计独特:对于设计结构独特,不适合采用传统组装方式的连廊,整体提升是一种更合适的施工方法。
3. 时间紧迫:需要迅速完成连廊的施工,整体提升能够缩短整个施工周期。
4. 连廊重量较大:连廊重量超过了普通施工设备的承载能力,需要采用整体提升工法来保证施工质量和安全性。
四、工艺原理施工工法与实际工程之间的联系、采取的技术措施进行具体的分析和解释,让读者了解该工法的理论依据和实际应用。
连廊一次整体提升施工工法的工艺原理是基于以下几点:1. 施工方案设计:根据连廊的结构特点,确定整体提升的施工方案和顶升装置的选择。
2. 吊装准备工作:在施工现场进行吊装准备工作,包括制定合理的吊装计划、布置吊装设备和搭建吊装平台等。
特大重型钢结构屋盖整体提升施工技术
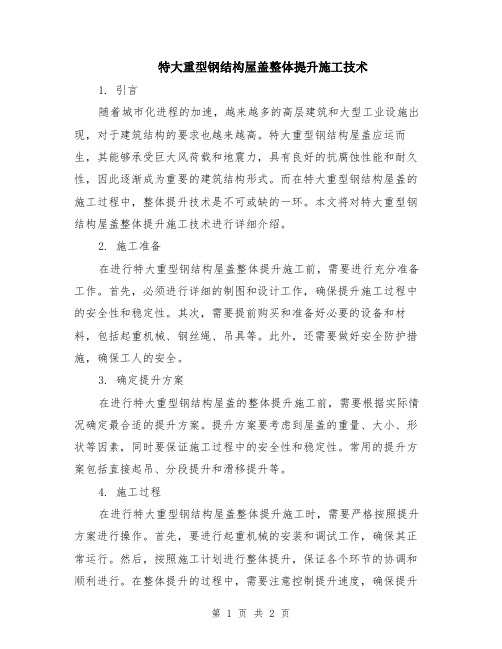
特大重型钢结构屋盖整体提升施工技术1. 引言随着城市化进程的加速,越来越多的高层建筑和大型工业设施出现,对于建筑结构的要求也越来越高。
特大重型钢结构屋盖应运而生,其能够承受巨大风荷载和地震力,具有良好的抗腐蚀性能和耐久性,因此逐渐成为重要的建筑结构形式。
而在特大重型钢结构屋盖的施工过程中,整体提升技术是不可或缺的一环。
本文将对特大重型钢结构屋盖整体提升施工技术进行详细介绍。
2. 施工准备在进行特大重型钢结构屋盖整体提升施工前,需要进行充分准备工作。
首先,必须进行详细的制图和设计工作,确保提升施工过程中的安全性和稳定性。
其次,需要提前购买和准备好必要的设备和材料,包括起重机械、钢丝绳、吊具等。
此外,还需要做好安全防护措施,确保工人的安全。
3. 确定提升方案在进行特大重型钢结构屋盖的整体提升施工前,需要根据实际情况确定最合适的提升方案。
提升方案要考虑到屋盖的重量、大小、形状等因素,同时要保证施工过程中的安全性和稳定性。
常用的提升方案包括直接起吊、分段提升和滑移提升等。
4. 施工过程在进行特大重型钢结构屋盖整体提升施工时,需要严格按照提升方案进行操作。
首先,要进行起重机械的安装和调试工作,确保其正常运行。
然后,按照施工计划进行整体提升,保证各个环节的协调和顺利进行。
在整体提升的过程中,需要注意控制提升速度,确保提升过程的平稳和安全。
同时,要及时进行调整和修正,保证屋盖的合理位置和姿态。
5. 安全措施在特大重型钢结构屋盖整体提升施工过程中,需要充分考虑安全因素。
首先,必须保证施工现场的安全,设置相应的警示标志和隔离设施,确保工人和周围人员的安全。
其次,需要保证起重机械和吊具的安全使用,定期检查和维护。
此外,还要进行培训和教育,提高工人的安全意识和操作技能。
6. 施工技巧在特大重型钢结构屋盖整体提升施工中,需要掌握一些施工技巧。
首先,要合理安排施工队伍的组织和配合,确保各个工序的顺利进行。
其次,要掌握吊点的选择和布置原则,确保屋盖的平稳提升。
特大重型钢结构屋盖整体提升施工技术模版(三篇)
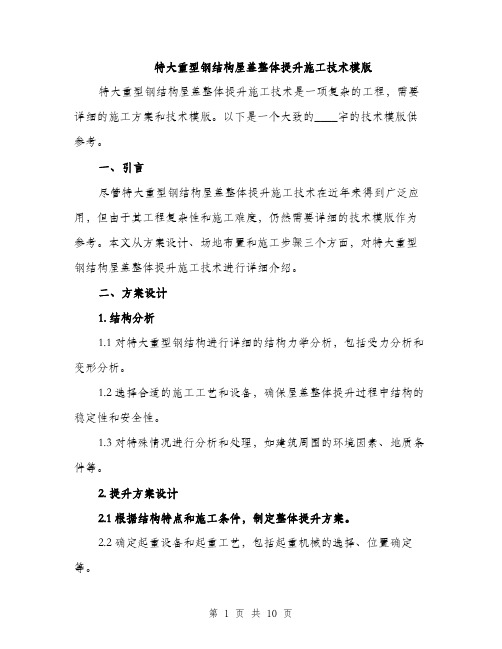
特大重型钢结构屋盖整体提升施工技术模版特大重型钢结构屋盖整体提升施工技术是一项复杂的工程,需要详细的施工方案和技术模版。
以下是一个大致的____字的技术模版供参考。
一、引言尽管特大重型钢结构屋盖整体提升施工技术在近年来得到广泛应用,但由于其工程复杂性和施工难度,仍然需要详细的技术模版作为参考。
本文从方案设计、场地布置和施工步骤三个方面,对特大重型钢结构屋盖整体提升施工技术进行详细介绍。
二、方案设计1. 结构分析1.1 对特大重型钢结构进行详细的结构力学分析,包括受力分析和变形分析。
1.2 选择合适的施工工艺和设备,确保屋盖整体提升过程中结构的稳定性和安全性。
1.3 对特殊情况进行分析和处理,如建筑周围的环境因素、地质条件等。
2. 提升方案设计2.1 根据结构特点和施工条件,制定整体提升方案。
2.2 确定起重设备和起重工艺,包括起重机械的选择、位置确定等。
2.3 制定提升进度计划,确保施工进度和质量。
三、场地布置1. 场地准备1.1 清理施工现场,确保场地整洁。
1.2 搭设施工临时设施,包括办公室、工棚、安全通道等。
2. 起重设备布置2.1 按照方案设计要求,布置起重设备的位置和方向。
2.2 确保起重设备的稳定性和安全性。
3. 安全措施3.1 制定施工安全方案,明确施工过程中应采取的安全措施。
3.2 指定专人负责安全管理,加强对工人施工操作的监督和指导。
3.3 提供必要的防护设备和培训,确保施工人员的工作安全。
四、施工步骤1. 钢结构准备1.1 对钢结构进行清理和防腐处理。
1.2 对钢结构进行拆解,便于整体提升。
2. 预装配2.1 将拆解的钢结构进行预装配,确保尺寸和连接的精确度。
2.2 对预装配后的钢结构进行检查,确保整体质量和稳定性。
3. 起重设备操作3.1 根据方案设计要求,进行起重设备的调试和校正。
3.2 按照提升方案,进行钢结构的整体提升。
3.3 在提升过程中,及时调整和修正起重设备的动态参数,确保提升稳定和准确。
特大重型钢结构屋盖整体提升施工技术
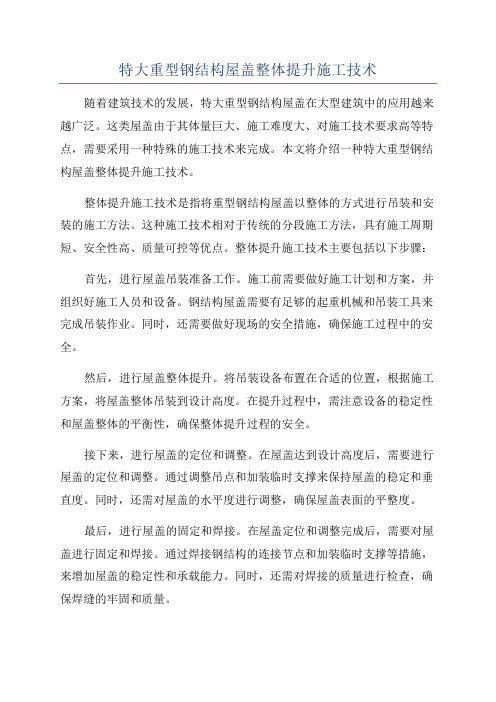
特大重型钢结构屋盖整体提升施工技术随着建筑技术的发展,特大重型钢结构屋盖在大型建筑中的应用越来越广泛。
这类屋盖由于其体量巨大、施工难度大、对施工技术要求高等特点,需要采用一种特殊的施工技术来完成。
本文将介绍一种特大重型钢结构屋盖整体提升施工技术。
整体提升施工技术是指将重型钢结构屋盖以整体的方式进行吊装和安装的施工方法。
这种施工技术相对于传统的分段施工方法,具有施工周期短、安全性高、质量可控等优点。
整体提升施工技术主要包括以下步骤:首先,进行屋盖吊装准备工作。
施工前需要做好施工计划和方案,并组织好施工人员和设备。
钢结构屋盖需要有足够的起重机械和吊装工具来完成吊装作业。
同时,还需要做好现场的安全措施,确保施工过程中的安全。
然后,进行屋盖整体提升。
将吊装设备布置在合适的位置,根据施工方案,将屋盖整体吊装到设计高度。
在提升过程中,需注意设备的稳定性和屋盖整体的平衡性,确保整体提升过程的安全。
接下来,进行屋盖的定位和调整。
在屋盖达到设计高度后,需要进行屋盖的定位和调整。
通过调整吊点和加装临时支撑来保持屋盖的稳定和垂直度。
同时,还需对屋盖的水平度进行调整,确保屋盖表面的平整度。
最后,进行屋盖的固定和焊接。
在屋盖定位和调整完成后,需要对屋盖进行固定和焊接。
通过焊接钢结构的连接节点和加装临时支撑等措施,来增加屋盖的稳定性和承载能力。
同时,还需对焊接的质量进行检查,确保焊缝的牢固和质量。
特大重型钢结构屋盖整体提升施工技术是一项复杂的工程,需要施工人员具备一定的经验和技能。
在实际施工中,需要根据具体情况进行调整和改进,以达到更好的施工效果。
相信随着技术的不断进步和研发,特大重型钢结构屋盖整体提升施工技术将会得到更好的应用和推广。
24超高层大跨度高空异形钢结构连廊整体提升施工技术

超高层大跨度异形高空钢结构连廊整体提升技术余自强胡明卿权奇李锦陈旭曹绍新张勤雄(中建三局集团有限公司西北分公司,西安,710065)摘要:西安迈科商业中心工程地上两栋不等高塔楼在高空设有钢结构连廊,该连廊结构异形、质量大、跨度大施工困难,施工时采用了“地面拼装、液压油缸集群、计算机控制、同步提升、应变监测”的施工技术,高效率、高质量地完成了高空钢连廊提升,该施工技术工艺先进、安全可靠、工期缩短。
关键词:地面拼装液压油缸集群计算机控制同步整体提升应变监测I ntegral Lifting Technology for Large-span and Special-shaped Altitude Steel ConnectingCorridor in the Super High-rise StructureYu Ziqiang,Hu Mingqing,Quan qi,Li Jin,Chen Xv,Cao Shaoxin,Zhang QinxiongChina Construction three Bureau Group Co., Ltd. Northwest BranchAbstract: There was a steel connecting corridor at high altitude between two towers of unequal height on the ground floor of Xi'an Maike commercial center project. Construction technology of "ground assembling, hydraulic clusters, computercontrolling,synchronizing lifting and strain monitoring " were used for the connecting bridge with special-shape, large mass, large span and construction difficulty. The altitude steel connecting bridge was lifted completely with high efficiency and high quality by the construction technology which has advantages of advanced craft, safety and reliability and shorten construction period.Key words: ground assembling, hydraulic clusters, computer controlling, synchronizing lifting for the integrated,strain monitoring0 引言随着社会经济的发展,高层、超高层建筑连体结构是近十几年发展起来的一种新型结构形式,一方面连体可以方便不同建筑物之间的联系;另一方面结构具有独特的外形,可以带来强烈的视觉效果,使建筑更具有特色。
高位大悬挑大型屋盖整体提升施工技术
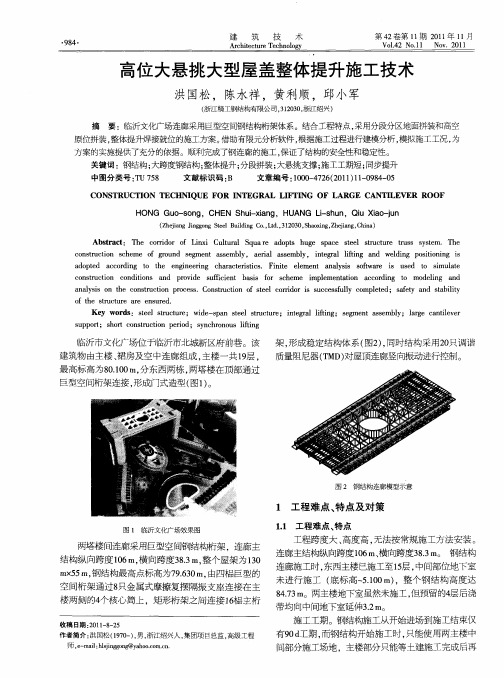
关键词 :钢结构 ; 大跨度钢 结构 ; 整体提升 ; 分段拼装 ; 大悬挑支撑 ; 施工工期短 ; 同步提升
中图分类号 :U7 8 T 5 文献标识码 : B 文章编号 :0 0 4 2 (0 1- 9 4 0 10 — 7 62 1) 0 8 — 5 1 1
CONS RUCT ON ECHNI T I T QUE F OR NT I EGRAL LI T NG ARGE C FI OF L ANT L VER OOF IE R
.
9 4. 8
建
筑
技
术
第 4 卷第 1 期 21 年 1 月 2 1 01 1
Vo . 2 N . 1 1 o1 4 NO .2 1 V 0 1
A c i c u eTe h 。。 Y r h t t r c n lg e
高位大悬挑大型屋 盖整体提升施工技术
洪国松 ,陈水祥 ,黄利 顺 ,邱小 军
工程跨度大 、 高度高 , 无法按常规施工方法安装 。 连廊主结构纵向跨度 16 横向跨度3.m 钢结构 0 m、 8 。 3
Байду номын сангаас
连廊施工时 , 东西主楼已施工至1层 , 5 中间部位地下室 m 5 钢结构最高点标高为7 . 0 "由四榀巨型 的  ̄5 m, 9 3 1, 6 1 未进行施工 ( 底标 高~ . 0 ) 51 ,整个钢结构高度达 0m 空间桁架通过8 只金属式摩擦复摆隔振 支座连接在主 8. 43 7 m。两主楼地下室虽然未施工 , 但预留的4 层后浇 楼两侧的4 个核心筒上 ,矩形桁架之间连接J榀主桁 6 带均 向中间地下室延t3 。 d .m 02
巨型空间桁架连接 , 形成门式造型( ) 图1 。
图 2 钢结构 连廊模型示意
大跨度钢结构网架整体提升平移安装施工工法

大跨度钢结构网架整体提升平移安装施工工法大跨度钢结构网架整体提升平移安装施工工法一、前言大跨度钢结构网架整体提升平移安装施工工法是一种快速、高效的建筑结构安装方法,特别适用于大型跨度建筑的施工。
本文将详细介绍该工法的特点、适应范围、工艺原理、施工工艺、劳动组织、机具设备、质量控制、安全措施、经济技术分析以及相关工程实例。
二、工法特点大跨度钢结构网架整体提升平移安装施工工法具有以下几个特点:1. 高效快速:采用整体提升平移安装施工方式,避免了传统方法中的分段拼装,大大提高了施工效率和进度。
2. 安全可靠:通过使用专业设备和严格的安全措施,确保施工过程中的安全性和可靠性。
3. 适应性强:适用于各种大跨度建筑,无论是屋盖结构还是体育馆、展览馆等公共建筑,都可以采用该工法进行施工。
4. 减少施工污染:由于整体提升平移安装,减少了临时支撑和拼装过程中的施工噪音和灰尘,降低了对周围环境的影响。
三、适应范围范围的建筑项目:1. 工业厂房:如大型厂库、生产车间等。
2. 商业综合体:如购物中心、超市等。
3. 文化体育设施:如体育馆、展览馆等。
4. 高速铁路站场:如高铁站、地铁站等。
四、工艺原理大跨度钢结构网架整体提升平移安装施工工法的工艺原理是通过利用专业设备,将预制好的钢结构网架整体提升至预定位置,并进行水平平移固定。
具体的实施方法如下:1. 提升:首先,利用大型起重设备将整体网架提升至预定高度,并准确定位。
2. 平移:接下来,利用专业的平移装置将网架水平平移至正确的位置,并进行固定。
3. 安装:在水平平移完成后,进行进一步的安装工作,如连接梁柱、搭设屋面等。
五、施工工艺大跨度钢结构网架整体提升平移安装施工工法的施工工艺可以分为以下几个阶段:1. 前期准备:确定施工方案、编制详细的施工计划和施工图纸,准备所需的材料和设备。
2. 提升施工:使用大型起重设备,将整体网架提升至预定高度,并进行准确定位。
3. 平移施工:利用平移装置,将网架水平平移至正确的位置,并进行固定。
超大跨度钢桁架多点整体提升施工工法

超大跨度钢桁架多点整体提升施工工法一、前言超大跨度钢桁架多点整体提升施工工法是目前在大型钢桁架工程中广泛采用的一种施工工法。
该工法具有适应范围广、对施工周期和成本可控等优点,并且有效保障施工过程的安全和质量。
本文将从工法特点、适应范围、工艺原理、施工工艺、劳动组织、机具设备、质量控制、安全措施、经济技术分析和工程实例等方面进行详细介绍。
二、工法特点超大跨度钢桁架多点整体提升施工工法是一种将大型钢桁架分段进行制作和组装,通过多点整体提升的方式将其整体提升至设定高度的施工工法。
该工法的特点主要包括以下几点。
1、适应范围广:该工法适用于大型钢桁架工程施工,如体育场馆、展馆等,且可适应不同尺寸的钢桁架工程。
2、施工周期可控:该工法通过分段制作和组装,并采取多点整体提升的方式施工,使施工周期可控,能够有效保障施工进度。
3、施工成本可控:该工法采用模块化设计和多点整体提升的方式施工,能够节省人力、物力资源,降低施工成本。
4、保障施工质量:该工法采用模块化设计,制作和组装钢桁架分段时能够控制误差,有效保障施工质量。
5、保障施工安全:该工法采用多点整体提升的方式施工,避免了单点吊装造成的不稳定和危险,有效保障施工安全。
三、适应范围超大跨度钢桁架多点整体提升施工工法主要适用于大型钢结构工程,如体育场馆、展馆等。
尤其对于跨度较大、高度要求较高的工程来说,该工法的优势更加明显。
同时,该工法还适用于有限的施工场地,能够通过模块化设计和多点整体提升的方式较少对施工场地的占用。
四、工艺原理1、施工工法与实际工程之间的联系超大跨度钢桁架多点整体提升施工工法是在实际工程中,针对大型钢结构工程的施工需要而研发出来的一种施工工法。
在实际工程中,大型钢结构的制作和组装需要考虑工程的高度和跨度等因素。
采用传统的单点吊装工法,容易造成危险和不稳定,同时施工周期和成本也难以控制。
而采用超大跨度钢桁架多点整体提升施工工法,能够有效地保障施工质量和安全,并控制施工周期和成本。
- 1、下载文档前请自行甄别文档内容的完整性,平台不提供额外的编辑、内容补充、找答案等附加服务。
- 2、"仅部分预览"的文档,不可在线预览部分如存在完整性等问题,可反馈申请退款(可完整预览的文档不适用该条件!)。
- 3、如文档侵犯您的权益,请联系客服反馈,我们会尽快为您处理(人工客服工作时间:9:00-18:30)。
大型超高钢结构整体提升技术1、工程概况本工程两塔楼之间在标高74.64m位置有一咖啡连廊,连廊上顶标高为86.07m,总高度11.43m,宽度9.2m,总长度为33. 6m,钢结构部分总重164吨,其中主体桁架部分66吨,在21层位置贯穿两塔楼。
连廊的主要受力部位为由上下弦组成的主体桁架,桁架长30.560m、宽9.2m、高3.6m,桁架主梁与次梁之间由大六角头M20高强螺栓连接,两塔楼间四根型钢混凝土柱(型钢尺寸:700×400×16×30)外伸焊制牛腿,H型桁架主钢梁与牛腿腹板用M20高强螺栓连接,翼板焊接连接。
钢梁和钢柱的工字型截面采用埋弧自动焊,主钢架梁柱上连接板和柱脚底板采用手工电弧焊。
在75.14m 位置桁架下弦为500×400×20×12H型焊制钢梁,两榀桁架下弦由500×250×16×12H型焊制钢梁连接;在78.74m位置桁架上弦为500×400×20×12H型焊制钢梁,两榀桁架上弦由500×250×16×12H型焊制钢梁连接;两榀桁架上下弦之间由300×300×20矩形方钢腹杆连接。
根据工程的具体实际情况,经多方论证,确定本工程钢结构部分的总的施工思路为:场外加工,场内拼装,桁架部分整体吊装,一次成活;围护部分散吊散拼。
即30.56m长桁架主钢梁分成两段在场外加工制作完毕后,运至现场,在两塔楼之间30m高裙房顶位置搭设拼装平台,将连廊的桁架主梁、次梁、腹杆、加劲板、压型钢板施工完毕后,运用计算机控制液压同步提升技术,采用四组液压千斤顶,整体提升,一次成活。
之后作为连廊围护结构施工的操作平台,围护结构安装,塔吊配合施工。
2、整体提升原理2.1概况本工程钢结构连廊的施工由于安装高度高,精度要求高,外伸牛腿与桁架上下弦杆之间每端仅有20的设计余量,如果使用传统的搭设支架和使用塔吊吊装的施工方法,从施工成本、工期、安全性、施工质量等方面都受到较大的限制。
因此经多方论证,本工程中的钢结构主体桁架部分施工采用整体吊装的施工方法,即将整个钢结构桁架各构件在拼装平台上拼装完毕后(包括压型钢板的施工),采用计算机控制液压同步提升技术进行整体吊装,然后进行桁架与牛腿间的连接。
整体吊装将会降低施工成本、缩短工期、提高施工安全性。
根据钢结构桁架本身的结构特点,提升点的布置要和结构的刚度分布相一致,同时也要保证提升状态的结构受力情况和实际使用状态的结构受力情况基本吻合。
故提升点的位置选在钢结构联廊的支座处,提升地锚距上弦端部500总共布置4个提升吊点提升地锚见后附图。
提升天锚设置在标高85.94m位置处的外伸牛腿上,其中心线与提升地锚的中心线在同一条垂线上。
提升吊点确定后,确定各提升吊点的提升力,并以此为确定提升油缸型号和数量的依据。
根据钢结构桁架的重量,每点的受力约20吨,故在每个提升吊点各布置一台50吨的提升油缸。
提升油缸的利用系数为0.4。
在联廊的两端23层平台上各布置一台液压泵站、在 B塔楼23层平台设置计算机控制系统一套。
2.2计算机控制液压同步提升技术2.2.1计算机控制液压同步提升技术简介计算机控制液压同步提升技术是一项新颖的构件提升安装施工技术,它采用柔性钢绞线承重、提升油缸集群、计算机控制、液压同步提升新原理,结合现代化施工工艺,将成千上万吨的构件在地面拼装后,整体提升到预定位置安装就位,实现大吨位、大跨度、大面积的超大型构件超高空整体同步提升。
计算机控制液压同步提升技术的核心设备采用计算机控制,可以全自动完成同步升降、实现力和位移控制、操作闭锁、过程显示和故障报警等多种功能,是集机、电、液、传感器、计算机和控制技术于一体的现代化先进设备。
计算机控制液压同步提升技术具有以下特点:(1)通过提升设备扩展组合,提升重量、跨度、面积不受限制;(2)采用柔性索具承重,只要有合理的承重吊点,提升高度与提升幅度不受限制;(3)提升油缸锚具具有逆向运动自锁性,使提升过程十分安全,并且构件可在提升过程中的任意位置长期可靠锁定;(4)提升系统具有毫米级的微调功能,能实现空中垂直精确定位,设备体积小,自重轻,承载能力大,特别适宜于在狭小空间或室内进行大吨位构件提升;(5)设备自动化程度高,操作方便灵活,安全性好,可靠性高,适应面广,通用性强。
2.2.2系统组成计算机控制液压同步提升系统由钢绞线及提升油缸集群(承重部件)、液压泵站(驱动部件)、传感检测及计算机控制(控制部件)和远程监视系统等几个部分组成。
钢绞线及提升油缸是系统的承重部件,用来承受提升构件的重量。
用户可以根据提升重量(提升载荷)的大小来配置提升油缸的数量,每个提升吊点中油缸可以并联使用。
本工程采用的提升油缸有350吨、200吨两种规格,均为穿芯式结构。
穿芯式提升油缸的结构示意图如图1所示。
钢绞线采用高强度低松弛预应力钢绞线,公称直径为15.24mm,抗拉强度为1860N/mm,破断拉力为260.7KN,伸长率在1%时的最小载荷221.5KN,每米重量为1.1Kg。
钢绞线符合国际标准ASTM A416-87a,其抗拉强度、几何尺寸和表面质量都得到严格保证。
液压泵站是提升系统的动力驱动部分,它的性能及可靠性对整个提升系统稳定可靠工作影响最大。
在液压系统中,采用比例同步技术,这样可以有效地提高整个系统的同步调节性能。
传感检测主要用来获得提升油缸的位置信息、载荷信息和整个被提升构件空中姿态信息,并将这些信息通过现场实时网络传输给主控计算机。
这样主控计算机可以根据当前网络传来的油缸位置信息决定提升油缸的下一步动作,同时,主控计算机也可以根据网络传来的提升载荷信息和构件姿态信息决定整个系统的同步调节量。
2.3同步提升控制原理及动作过程2.3.1同步提升控制原理主控计算机除了控制所有提升油缸的统一动作之外,还必须保证各个提升吊点的位置同步。
在提升体系中,设定主令提升吊点,其它提升吊点均以主令吊点的位置作为参考来进行调节,因而,都是跟随提升吊点。
图2是提升系统同步控制方框图。
主令提升吊点决定整个提升系统的提升速度,操作人员可以根据泵站的流量分配和其它因素来设定提升速度。
根据现有的提升系统设计,最大提升速度不大于6米/小时。
主令提升速度的设定是通过比例液压系统中的比例阀来实现的。
在提升系统中,每个提升吊点下面均布置一台激光测距仪,这样,在提升过程中这些激光测距仪可以随时测量当前的构件高度,并通过现场实时网络传送给主控计算机。
每个跟随提升吊点与主令提升吊点的跟随情况可以用激光测距仪测量的高度差反映出来。
主控计算机可以根据跟随提升吊点当前的高度差,依照一定的控制算法,来决定相应比例阀的控制量大小,从而,实现每一跟随提升吊点与主令提升吊点的位置同步。
为了提高构件的安全性,在每个提升吊点都布置了油压传感器,主控计算机可以通过现场实时网络监测每个提升吊点的载荷变化情况。
如果提升吊点的载荷有异常的突变,则计算机会自动停机,并报警示意。
2.3.2提升动作原理提升油缸数量确定之后,每台提升油缸上安装一套位置传感器,传感器可以反映主油缸的位置情况、上下锚具的松紧情况。
通过现场实时网络,主控计算机可以获取所有提升油缸的当前状态。
根据提升油缸的当前状态,主控计算机综合用户的控制要求(例如手动、顺控、自动)可以决定提升油缸的下一步动作。
提升系统上升时,提升油缸的工作流程见图3,提升系统下降时,提升油缸的工作流程见图4。
2.4计算机控制系统的布置2.4.1传感器的布置●激光测距仪:在每个提升吊点处,选择适当的位置,安装1台激光测距仪;激光测距仪的目标靶子安装在被提升结构上,随着被提升结构的提升,激光测距仪的测量距离越来越短;●压力传感器:在每个提升吊点的油缸中,选择一个油缸安装压力传感器;压力传感器安装在油缸的大腔侧,由于同一提升吊点的所有油缸的进油口并联,压力相同,所以一个油缸的压力就代表同一提升吊点的压力;●锚具及油缸位置传感器:在每个油缸的上下锚具油缸上各安装1只锚具传感器,在主缸上安装1只油缸位置传感器;●将各种传感器同各自的通讯模块连接。
2.4.2现场实时网络控制系统的连接●地面布置1台计算机控制柜,从计算机控制柜引出比例阀通讯线、电磁阀通讯线、油缸信号通讯线、激光信号通讯线、工作电源线;●通过比例阀通讯线、电磁阀通讯线将所有泵站联网;●通过油缸信号通讯线将所有油缸信号盒通讯模块联网;●通过激光信号通讯线将所有激光信号通讯模块、A/D通讯模块联网;●通过电源线将所有的模块电源线连接。
2.4.3系统布置当完成传感器的安装和现场实时网络控制系统的连接后,计算机控制系统的布置就完成。
2.5提升吊点同步控制的措施2.5.1提升油缸动作同步现场网络控制系统根据油缸位置信号和锚具信号,确定所有油缸的状态,根据提升油缸的当前状态,主控计算机综合用户的控制要求,决定提升油缸的下一步动作。
当主控计算机决定提升油缸的下一步动作后,向所有液压泵站发出同一动作指令,控制相应的电磁阀统一动作,实现所有提升油缸的动作一致,同时锚具动作、同时伸缸、缩缸或同时停止。
2.5.2提升吊点位置同步在每个提升吊点处,各安装一台激光测距仪,用于测量各提升吊点的高度。
在提升过程中,设定某一点为主令点,其余11点为跟随点。
根据用户希望的提升速度设定主令点的比例阀电流恒定,进而主令点液压泵站比例阀开度恒定,提升油缸的伸缸速度恒定,主令点以一定的速度向上提升。
其余跟随点通过主控计算机分别根据该点同主令点的位置高差来控制这点提升速度的快慢,以使该跟随点同主令点的位置高度跟随一致。
现场网络控制系统将各激光测距仪的高度信号采集进主控计算机,主控计算机通过比较主令点同每个跟随点的高度得出跟随点同主令点的高差。
如果某跟随点与主令点的高差为正,表示跟随点的位置比主令点高,说明该跟随点的提升油缸速度快,计算机在随后的调节中,就降低驱动这点提升油缸的比例阀控制电流,减小比例阀的开度,降低提升油缸的提升速度,以使该跟随点同主令点的位置跟随一致。
反之,如果某跟随点比主令点慢了,计算机控制系统就调节该点的提升油缸伸缸快一些,以跟随上主令点,保持位置跟随一致。
为了保证提升过程中的位置同步,系统中还设置了超差自动报警停机功能。
一旦某跟随点同主令点的同步高差超过某一设定值,系统将自动报警停机,以便检查。
整体提升同步控制系统见图5。
2.6提升准备2.6.1液压提升系统液压提升系统中所有元件、部件必须经过严格的检测后才能进场使用。
试验依据请参阅后叙内容。
应保存所有的试验原始记录。
2.6.2钢绞线安装●根据各点的提升高度,考虑提升结构的状况,切割相应长度的钢绞线;●钢绞线左、右旋各一半,要求钢绞线两头倒角、不松股,将其间隔平放地面,理顺;●将钢绞线穿在油缸中,上下锚一致,不能交错或缠绕,每个油缸中的钢绞线左右旋相间;●钢绞线露出油缸上端30厘米;●压紧油缸的上下锚;●将钢绞线的下端根据油缸的锚孔位置捆扎作好标记;●用起重机将穿好钢绞线的油缸安装在提升平台上;●按照钢绞线下端的标记,安装钢绞线地锚,确保从油缸下端到地锚之间的钢绞线不交叉、不扭转、不缠绕;●安装地锚时各锚孔中的三片锚片应能均匀夹紧钢绞线;其高差不得大于0.5mm,周向间隙误差小于0.3mm;●地锚压板与锚片之间应有软材料垫片,以补偿锚片压紧力的不均匀变形。