年产三十万吨合成氨合成工段工艺设计毕业论文
年产30万吨合成氨脱碳工段工艺设计

(签字)
年月日
注:本表可根据内容续页。
六.进度安排及参考文献
1.进度安排
2013.10-------2013.12工厂实习,采集数据
2014.2.23-------2014.3.08查阅文献,选定脱碳工艺方案,准备开题
2014.3.10-------2014.4.10脱碳工段主要装置工艺计算
2014.4.10-------2014.5.10绘制脱碳塔、脱水塔、氨冷器设备图,脱碳工段工艺流程图,脱碳工段车间平面图
电耗×10-6/KJ
1.302
1.1
1.016
冷却水/m3
15
80
70
综合能耗×10-6/KJ
2.725
5.233
4.186
①注:以氨计。
4.NHD脱Βιβλιοθήκη 脱碳技术通过比较,我选择的是NHD脱硫脱碳技术,它是一种新型的低能净化工艺。NHD溶剂的主要成分为聚乙二醇二甲醚的混合物,属于物理吸收溶剂.该工艺适用于天然气为原料的氨厂,也可用于以煤为原料,硫化物和二氧化碳含量较高的氨合成气、甲醇合成气等气体的净化。其优点有:吸收气体能力强、净化度高。溶剂的化学稳定性和热稳定性好,不氧化、不降解、不起泡,溶剂蒸汽压极低,使用过程中挥发损失少,运行中不需添加消泡剂、活化剂,生产运行稳定,操作方便,且运行及维修费低。NHD溶液无毒、挥发少、对环境无污染。溶剂无腐蚀性,吸收能力强。
四.在毕业设计中我要完成的任务
1.绘制脱碳塔氨冷气、脱水塔设备装配图、NHD脱碳系统带控制点流程图、脱碳车间平面布置图
2.对主要设备作物料衡算和热量衡算
五.本课题的研究目标和意义
通过对本课题的研究,对现在生产过程中的各种脱碳方法的研究和比较,对脱碳工段各个单元生产指标的计算和对比,可以对以往所学的专业知识进行全方位的巩固和梳理,将所学到的理论知识完全应用到生产实践上。本课题的目的是为了寻找出一套合理的脱碳工艺,以获得较高纯度的净化气,提高二氧化碳的回收率,简化合成氨脱碳流程,降低生产能耗,达到生产的较高经济效益指标。
【毕业设计】年产30万吨合成氨工艺设计

毕业设计题目名称:年产30万吨合成氨转变工序设计系别:化学工程系专业:应用化学班级: 06101学生:学号:指导教师(职称):(教授)摘要氨是重要的基础化工产品之一,在国民经济中占有重要地位。
合成氨生产经过多年的发展,现已发展成为一种成熟的化工生产工艺。
本设计是以天然气为原料年产三十万吨合成氨转变工序的设计。
近年来合成氨工业发展很快,大型化、低能耗、清洁生产均是合成氨设备发展的主流,技术改进主要方向是开发性能更好的催化剂、降低氨合成压力、开发新的原料气净化方法、降低燃料消耗、回收和合理利用低位热能等方面上。
设计采用的工艺流程简介:天然气经过脱硫压缩进入一段转化炉,把CH4和烃类转化成H2,再经过二段炉进一步转化后换热进入高变炉,在催化剂作用下大部分CO和水蒸气反应获H2和CO2,再经过低变炉使CO降到合格水平,去甲烷化工序。
本设计综述部分主要阐述了国内外合成氨工业的现状及发展趋势以及工艺流程、参数的确定和选择,论述了建厂的选址;介绍了氨变换工序的各种流程并确定本设计高-低变串联的流程。
工艺计算部分主要包括转化段和变换段的物料衡算、热量衡算、平衡温距及空速计算。
设备计算部分主要是高变炉催化剂用量的具体计算,并根据设计任务做了转化和变换工序带控制点的工艺流程图。
本设计的优点在于选择较为良好的厂址和原料路线,确定良好的工艺条件、合理的催化剂和能源综合利用。
另外,就是尽量减少设备投资费用。
关键字:合成氨;天然气;转化;变换;AbstractAmmonia is the most important one of basic chemical products, plays an important role in the national economy. Ammonia production after years of development, now has developed into a mature chemical production processes. The design is based on annual output of 300,000 tons of natural gas as raw material, the design of synthetic ammonia transformation process. In recent years, the large-scale industrial development soon ammonia, low energy consumption, the clean production of synthetic ammonia equipment development are the main direction of technical improvement, is to develop better performance of catalyst, reducing ammonia synthesis pressure, the development of new materials gas purification methods, reduce fuel consumption, low heat recovery and reasonable utilization, etc.The design process used in brief are: compressed natural gas afterdesulfurization and conversion into a furnace, the methane and hydrocarbons into hydrogen, through the Secondary reformer further transformed into the highly variable furnace heat exchanger, the great catalyst part of the reaction of carbon monoxide and hydrogen and carbon dioxide vapor, then through the low-temperature shift to reduce to an acceptable level of carbon monoxide to methanation process. The design review described some of the major domestic and international situation and the development of synthetic ammonia industry trends and technological process, parameter identification and selection, discusses the plant's location; introduced the transformation process of the various processes and determine the design of high temperature shift and low temperature Transformation series of the process. Calculation of some of the major transformation process, including segment and transform section material balance, heat balance, equilibrium temperature and airspeed calculation. Calculation of some of the major equipment is a high temperature shift catalyst of specific terms, and according to the design task to do the conversion and transformation process flow chart with control points.Advantage of this design is to choose a better site and raw materials line to determine the good conditions, reasonable catalyst and energy utilization. In addition, investment in equipment designed to minimize costs.Keywords: ammonia; natural gas; transformation; transformation;目录摘要 (I)Abstract (II)目录 (IV)1 综述.................................................................. - 1 -1.1 氨的性质、用途及重要性.......................................... - 1 -1.1.1 氨的性质................................................... - 1 -1.1.2 氨的用途及在国民生产中的作用............................... - 1 -1.2 合成氨生产技术的发展............................................ - 2 -1.2.1世界合成氨技术的发展....................................... - 2 -1.2.2中国合成氨工业的发展概况................................... - 5 -1.3合成氨转变工序的工艺原理......................................... - 6 -1.3.1 合成氨的典型工艺流程介绍................................... - 6 -1.3.2 合成氨转化工序的工艺原理................................... - 8 -1.3.3合成氨变换工序的工艺原理................................... - 8 -1.4 设计方案的确定.................................................. - 9 -1.4.1 原料的选择................................................. - 9 -1.4.2 工艺流程的选择............................................ - 10 -1.4.3 工艺参数的确定............................................ - 10 -1.4.4 工厂的选址................................................ - 11 -2 设计工艺计算......................................................... - 13 -2.1 转化段物料衡算................................................. - 13 -2.1.1 一段转化炉的物料衡算...................................... - 14 -2.1.2 二段转化炉的物料衡算...................................... - 17 -2.2 转化段热量衡算................................................. - 20 -2.2.1 一段炉辐射段热量衡算...................................... - 20 -2.2.2 二段炉的热量衡算.......................................... - 27 -2.2.3 换热器101-C、102-C的热量衡算............................. - 28 -2.3 变换段的衡算................................................... - 30 -2.3.1 高温变换炉的衡算.......................................... - 30 -2.3.2 低温变换炉的衡算.......................................... - 32 -2.4 换热器103-C及换热器104-C的热负荷计算......................... - 35 -2.4.1 换热器103-C热负荷........................................ - 35 -2.4.2 换热器104-C热负荷........................................ - 35 -2.5 设备工艺计算................................................... - 36 -参考文献............................................................... - 40 -致谢................................................................... - 41 -附录................................................................... - 41 -1 综述1.1 氨的性质、用途及重要性1.1.1 氨的性质氨分子式为NH,在标准状态下是无色气体,比空气轻,具有特殊的刺激性臭味。
(完整版)年产30万吨合成氨合成工段工艺设计毕业论文

年产30万吨合成氨合成工段工艺设计目录摘要 .......................................................................................................................................... Abstract ..................................................................................................................................引言......................................................................................................................................第一章合成氨综述............................................................................................................1.1 氨的用途....................................................................................................................................1.2 氨的性质....................................................................................................................................1.2.1 氨的物理性质 .......................................................................................................................1.2.2 氨的化学性质 .......................................................................................................................1.3 合成氨的生产方法 .................................................................................................................1.4 合成工艺条件的选择.............................................................................................................1.4.1操作压力.................................................................................................................................1.4.2 反应温度 ................................................................................................................................1.4.3空速..........................................................................................................................................1.4.4合成塔进口气体组成..........................................................................................................1.5 合成氨工业的发展 .................................................................................................................第二章合成工段工艺简介..............................................................................................2.1 合成工段工艺流程简述 ............................................................................................2.2 工艺流程方框简图 ....................................................................................................2.3 设备简述.....................................................................................................................2.3.1 氨合成塔..................................................................................................................2.3.3 冷交换器..................................................................................................................2.3.4 氨冷器......................................................................................................................第三章工艺设计计算 .......................................................................................................3.1 设计要求.....................................................................................................................3.2 工艺流程图.................................................................................................................3.3 物料计算.....................................................................................................................3.3.1合成塔入口气体组分 ..............................................................................................3.3.2 合成塔出口气体组分 .............................................................................................3.3.3 合成率......................................................................................................................3.3.4 氨分离器气液平衡计算 .........................................................................................3.3.5 冷交换器气液平衡计算 .........................................................................................3.3.6 液氨储槽气液平衡计算 .........................................................................................3.3.7 液氨储槽物料计算 .................................................................................................3.3.8 合成系统物料计算 .................................................................................................3.3.9 合成塔物料计算 .....................................................................................................3.3.10 水冷器物料计算 ...................................................................................................3.3.11 氨分离器物料计算................................................................................................3.3.12 冷交换器物料计算 ...............................................................................................3.3.13 氨冷器的物料计算 ...............................................................................................3.3.14 冷交换器物料计算 ...............................................................................................3.3.15 液氨贮槽物料计算 ...............................................................................................3.4 热量衡算.....................................................................................................................3.4.2 氨冷凝器热量计算 .................................................................................................3.4.3 循环机热量计算 .....................................................................................................3.4.4 合成塔热量衡算 .....................................................................................................3.4.5 废热锅炉热量计算: .............................................................................................3.4.6 热交换器热量计算 .................................................................................................3.4.7 水冷器热量衡算: .................................................................................................3.4.8 氨分离器热量衡算: .............................................................................................第四章设备的选型与计算..............................................................................................4.1 设备选型.....................................................................................................................4.1.1 设备简述..................................................................................................................4.1.2 流程说明..................................................................................................................4.2 合成塔设计.................................................................................................................4.2.1 合成塔筒体设计 .....................................................................................................4.2.2 催化剂层设计 .........................................................................................................4.2.3 下换热器..................................................................................................................4.2.4 层间换热器..............................................................................................................4.3 辅助设备选型 ............................................................................................................4.3.1 废热锅炉..................................................................................................................4.3.2 热交换器..................................................................................................................4.3.3 水冷器......................................................................................................................4.3.4 冷交换器..................................................................................................................4.3.5 氨冷器I ...................................................................................................................结论......................................................................................................................................致谢......................................................................................................................................参考文献.................................................................................................................................附录......................................................................................................................................年产30万吨合成氨合成工段工艺设计摘要:氨是一种重要的化工产品,在国民经济中有重要的作用。
「年产三万吨合成氨厂变换工段工艺设计」

年产三万吨合成氨厂变换工段工艺设计一、工艺流程概述1.原料准备:将天然气(主要是甲烷)与空气作为主要原料,通过气体净化系统去除其中的杂质、硫化物和水分。
2.原料配送:将净化后的天然气和空气分别输送至气体净化系统进行进一步的处理和分析。
3.变换反应槽:将净化后的天然气和空气通过压缩机压缩至一定压力后,经过暖气交换器加热至高温(约500-600℃),再进入变换反应槽。
4.变换催化剂:在变换反应槽中,使用催化剂(通常是高温高压下的铁-钴催化剂)促进N2和H2的反应。
反应生成的合成氨会随气流从反应槽中流出。
5.除气系统:将反应槽中的气体通过除尘器,冷却器和吸附剂等设备进行处理,去除其中的固体颗粒、水分和其他杂质。
6.合成氨回收:经过除气系统处理后的气体中仍含有未反应的氮气和氢气,通过压缩机再次压缩进入蒸馏塔。
在蒸馏塔中,根据不同的沸点,将氨气和氮气分离开来,再通过冷凝器冷凝为液态氨。
7.废水处理:在工艺过程中产生的废水会经过处理系统去除其中的有机物和杂质,以保证排放的废水符合环保要求。
二、设备布置和操作要点1.变换反应槽的设计要考虑到温度、压力和气体流动速度的控制。
同时,需要定期更换催化剂,以维持优良的反应性能。
2.除气系统中的设备要进行定期维护和清洁,确保其正常工作和去除气体中的杂质、固体颗粒和水分。
3.合成氨回收装置要根据产品质量要求设置合适的操作参数,例如蒸馏塔的温度和压力。
此外,冷凝器的冷却水流需要保持稳定,以确保气体顺利冷凝为液态氨。
4.废水处理系统应配置适当的物理和化学处理单元,如过滤器、沉淀池和生物处理等,以达到废水排放标准。
5.需要建立相应的安全措施,如设立监测系统,确保气体和液体在整个工艺中的安全运输和使用。
三、工艺控制和性能优化1.在变换反应槽中,可以通过调节供气比例、压力和温度等参数来控制合成氨的产率和选择性。
同时,也可以根据反馈控制系统监测和调整催化剂的性能。
2.除气系统中的设备可以通过监测气体的组成和温度、压力等参数,来调整操作参数,以达到满足产品质量要求的除气效果。
(论文)年产30万吨合成氨原料气脱碳工段工艺设计毕业论文[精选整理]
![(论文)年产30万吨合成氨原料气脱碳工段工艺设计毕业论文[精选整理]](https://img.taocdn.com/s3/m/4d7053837fd5360cbb1adbc1.png)
本科毕业设计年产30万吨合成氨原料气脱碳工段工艺设计Decarbonization Process design on synthetic ammoniaAt an output of 300,000 t/a目录摘要 (I)Abstract............................................................................................................................................................ I I 引言 . (1)第一章总论 (2)1.1 概述 (2)1.1.1 氨的性质 (2)1.1.2 氨的用途及在化工生产中的地位 (2)1.2 合成氨的发展历史 (3)1.2.1 氨气的发现 (3)1.2.2 合成氨的发现及其发展 (3)1.2.3 世界合成氨工业发展 (3)1.3 文献综述 (4)1.3.1合成氨脱碳 (4)1.3.2合成氨脱碳的方法概述 (5)1.4 设计的依据 (5)第二章流程方案的确定 (6)2.1各脱碳方法对比 (6)2.1.1化学吸收法 (6)2.1.2物理吸收法 (6)2.1.3物理化学吸收法 (7)2.2碳酸丙烯酯(PC)法脱碳工艺基本原理 (8)2.2.1 PC法脱碳技术国内外现状 (8)2.2.2发展过程 (8)2.2.3技术经济 (9)第三章生产流程的简述 (6)3.1.2 解吸气体回收流程 (10)3.2液体流程 (10)3.2.1 碳酸丙烯酯脱碳流程简述 (10)3.2.2 稀液流程循环 (11)3.3存在的问题及解决的办法 (11)3.3.1综合分析PC法脱碳存在的主要问题有 (11)3.3.2解决办法 (11)第四章物料衡算和热量衡算 (13)4.1工艺参数及指标 (13)在PC中的溶解度关系 (13)24.1.2 PC的密度与温度的关系 (14)4.1.3 PC的蒸汽压 (14)4.1.4 PC的黏度 (14)4.2物料衡算 (14)4.2.1各组分在PC中的溶解量 (14)4.2.2溶剂夹带量 (15)4.2.3溶液带出的气量 (15)4.2.4出脱碳塔净化气量 (15)4.2.5 计算PC循环量 (16)4.2.6 入塔液中CO2夹带量 (16)4.2.7 带出气体的质量流量 (16)4.2.8 验算吸收液中净化气中CO2的含量 (16)4.2.9出塔气的组成 (17)4.3热量衡算 (17)第五章吸收塔的结构设计 (20)5.1确定吸收塔塔径及相关参数 (20)5.1.1基础数据 (20)5.1.2求取塔径 (21)5.1.4填料层高度的计算 (22)5.1.5 气相总传质单元高度 (24)5.1.6塔附属高度 (29)第六章塔零部件和辅助设备的设计与选取 (31)6.1 吸收塔零部件的选取 (31)6.1.1筒体、封头等部件的尺寸选取 (31)6.1.2防涡流挡板的选取 (31)6.1.3液体初始分布器 (32)6.1.4 液体再分布器 (33)6.1.5 填料支撑装置 (33)6.1.6接管管径的确定 (33)6.2 解吸塔的选取 (33)贮槽的选择 (34)6.4泵的选择 (34)结论 (34)致谢 .............................................................................................................................错误!未定义书签。
年产30万吨合成氨工艺设计毕业论文
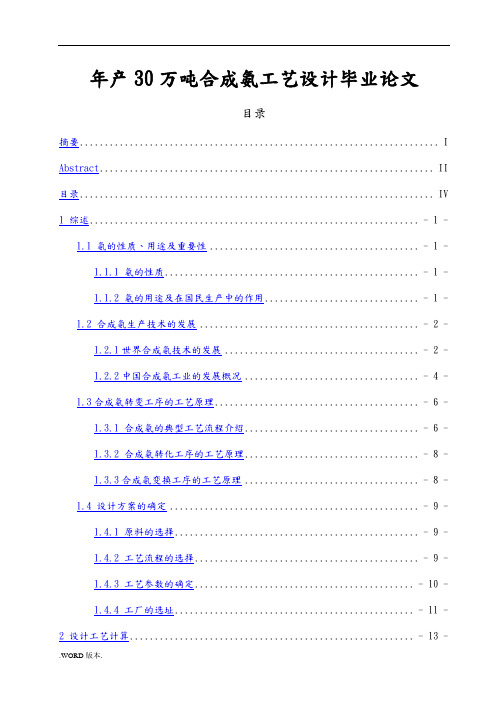
年产30万吨合成氨工艺设计毕业论文目录摘要 (I)Abstract (II) (IV)1 综述.................................................................. - 1 -1.1 氨的性质、用途及重要性.......................................... - 1 -1.1.1 氨的性质................................................... - 1 -1.1.2 氨的用途及在国民生产中的作用............................... - 1 -1.2 合成氨生产技术的发展............................................ - 2 -1.2.1世界合成氨技术的发展....................................... - 2 -1.2.2中国合成氨工业的发展概况................................... - 4 -1.3合成氨转变工序的工艺原理......................................... - 6 -1.3.1 合成氨的典型工艺流程介绍................................... - 6 -1.3.2 合成氨转化工序的工艺原理................................... - 8 -1.3.3合成氨变换工序的工艺原理................................... - 8 -1.4 设计方案的确定.................................................. - 9 -1.4.1 原料的选择................................................. - 9 -1.4.2 工艺流程的选择............................................. - 9 -1.4.3 工艺参数的确定............................................ - 10 -1.4.4 工厂的选址................................................ - 11 -2 设计工艺计算......................................................... - 13 -2.1 转化段物料衡算................................................. - 13 -2.1.1 一段转化炉的物料衡算...................................... - 14 -2.1.2 二段转化炉的物料衡算...................................... - 17 -2.2 转化段热量衡算................................................. - 20 -2.2.1 一段炉辐射段热量衡算...................................... - 20 -2.2.2 二段炉的热量衡算.......................................... - 27 -2.2.3 换热器101-C、102-C的热量衡算............................. - 28 -2.3 变换段的衡算................................................... - 30 -2.3.1 高温变换炉的衡算.......................................... - 30 -2.3.2 低温变换炉的衡算.......................................... - 32 -2.4 换热器103-C及换热器104-C的热负荷计算......................... - 35 -2.4.1 换热器103-C热负荷........................................ - 35 -2.4.2 换热器104-C热负荷........................................ - 35 -2.5 设备工艺计算................................................... - 36 -参考文献............................................................... - 40 -致谢................................................................... - 41 -附录................................................................... - 42 -1 综述1.1 氨的性质、用途及重要性1.1.1 氨的性质氨分子式为NH3,在标准状态下是无色气体,比空气轻,具有特殊的刺激性臭味。
年产30万吨合成氨工艺设计

年产30万吨合成氨工艺设计作者姓名000专业应用化工技术11-2班指导教师姓名000专业技术职务副教授(讲师)目录摘要 (4)第一章合成氨工业概述 (5)1.1氨的性质、用途及重要性 (5)1.1.1氨的性质 (5)1.1.2 氨的用途及在国民生产中的作用 (6)1.2 合成氨工业概况 (6)1.2.1发展趋势 (6)1.2.2我国合成氨工业发展概况 (7)1.2.3世界合成氨技术的发展 (9)1.3合成氨生产工艺 (11)1.3.1合成氨的典型工艺流程 (11)1.4设计方案确定 (13)1.4.1原料的选择 (13)1.4.2 工艺流程的选择 (14)1.4.3 工艺参数的确定 (14)第二章设计工艺计算2.1 转化段物料衡算 (15)2.1.1 一段转化炉的物料衡算 (16)2.2 转化段热量衡算 (24)2.2.1 一段炉辐射段热量衡算 (24)2.2.2 二段炉的热量衡算 (32)2.2.3 换热器101-C、102-C的热量衡算 (34)2.3 变换段的衡算 (35)2.3.1 高温变换炉的衡算 (35)2.3.2 低温变换炉的衡算 (38)2.4 换热器103-C及换热器104-C的热负荷计算 (41)2.4.1 换热器103-C热负荷 (41)2.4.2 换热器104-C热负荷 (42)2.5 设备工艺计算 (42)2.6 带控制点的工艺流程图及主要设备图 (46)2.7 生产质量控制 (46)2.8 三废处理 (47)摘要氨是重要的基础化工产品之一,在国民经济中占有重要地位。
合成氨生产经过多年的发展,现已发展成为一种成熟的化工生产工艺。
本设计是以天然气为原料年产三十万吨合成氨的设计。
近年来合成氨工业发展很快,大型化、低能耗、清洁生产均是合成氨设备发展的主流,技术改进主要方向是开发性能更好的催化剂、降低氨合成压力、开发新的原料气净化方法、降低燃料消耗、回收和合理利用低位热能等方面上。
年产30万吨合成氨基础工艺设计

毕业设计题目名称: 年产30万吨合成氨转变工序设计系别: 化学工程系专业: 应用化学班级: 06101 学生: 学号: 指导老师(职称): (教授)摘要氨是关键基础化工产品之一, 在国民经济中占相关键地位。
合成氨生产经过多年发展, 现已发展成为一个成熟化工生产工艺。
本设计是以天然气为原料年产三十万吨合成氨转变工序设计。
多年来合成氨工业发展很快, 大型化、低能耗、清洁生产均是合成氨设备发展主流, 技术改善关键方向是开发性能愈加好催化剂、降低氨合成压力、开发新原料气净化方法、降低燃料消耗、回收和合理利用低位热能等方面上。
设计采取工艺步骤介绍: 天然气经过脱硫压缩进入一段转化炉, 把CH4和烃类转化成H2, 再经过二段炉深入转化后换热进入高变炉, 在催化剂作用下大部分CO和水蒸气反应获H2和CO2, 再经过低变炉使CO降到合格水平, 去甲烷化工序。
本设计综述部分关键叙述了中国外合成氨工业现实状况及发展趋势以及工艺步骤、参数确定和选择, 叙述了建厂选址; 介绍了氨变换工序多种步骤并确定本设计高-低变串联步骤。
工艺计算部分关键包含转化段和变换段物料衡算、热量衡算、平衡温距及空速计算。
设备计算部分关键是高变炉催化剂用量具体计算, 并依据设计任务做了转化和变换工序带控制点工艺步骤图。
本设计优点在于选择较为良好厂址和原料路线, 确定良好工艺条件、合理催化剂和能源综合利用。
另外, 就是尽可能降低设备投资费用。
关键字: 合成氨; 天然气; 转化; 变换;AbstractAmmonia is the most important one of basic chemical products, plays an important role in the national economy. Ammonia production after years of development, now has developed into a mature chemical production processes.The design is based on annual output of 300,000 tons of natural gas as raw material, the design of synthetic ammonia transformation process. In recent years, the large-scale industrial development soon ammonia, low energy consumption, the clean production of synthetic ammonia equipment development are the main direction of technical improvement, is to develop better performance of catalyst, reducing ammonia synthesis pressure, the development of new materials gas purification methods, reduce fuel consumption, low heat recovery and reasonable utilization, etc.The design process used in brief are: compressed natural gas after desulfurization and conversion into a furnace, the methane and hydrocarbons into hydrogen, through the Secondary reformer further transformed into the highly variable furnace heat exchanger, the great catalyst part of the reaction of carbon monoxide and hydrogen and carbon dioxide vapor, then through the low-temperature shift to reduce to an acceptable level of carbon monoxide to methanation process. The design review described some of the major domestic and international situation and the development of synthetic ammonia industry trends and technological process, parameter identification and selection, discusses the plant's location; introduced the transformation process of the various processes and determine the design of high temperature shift and low temperature Transformation series of the process. Calculation of some of the major transformation process, including segment and transform section material balance,heat balance, equilibrium temperature and airspeed calculation. Calculation of some of the major equipment is a high temperature shift catalyst of specific terms, and according to the design task to do the conversion and transformation process flow chart with control points.Advantage of this design is to choose a better site and raw materials line to determine the good conditions, reasonable catalyst and energy utilization. In addition, investment in equipment designed to minimize costs.Keywords: ammonia; natural gas; transformation; transformation;目录摘要........................................................ 错误!未定义书签。
年产三十万吨合成氨合成工段任务书

题目:
年产30万吨合成氨合成工段工艺设计
学院
化学与材料工程学院
专 业
煤炭利用与深加工
班 级
1013101
学 号
101310127
学生姓名
庞雷
指导教师
赵海鹏
发放日期
2013.4.1
河南城建学院毕业设计(论文)任务书
一、主要任务与目标:
设计任务:合成氨厂合成工段的工艺设计
设计题目:年产30万吨合成氨合成工段的工艺设计
指导教师意见:
(建议就任务书的规范性;任务书主要内容和基本要求的明确具体性;任务书计划进度的合理性;提供的参考文献数量等方面写出意见。)
指导教师签名:
年月日
教研室审核意见:
教研室主任签名:
年月日
注:任务书必须由指导教师和学生互相交流后,由指导老师下达并交教研室主任审核后发给学生,最后同学生毕业论文等其它材料一起存档。
5、工艺流程图绘制
以单线图的形式绘制,表出主题设备和辅助设备的物料流向、物流量、能量流量和主要工艺参数测量点和控制点(即带控制点的工艺流程图)。
6、主要设备结构图的绘制
7、编写设计说明书:对工段概况的说明,流程叙述,设计特点,主要设备选型或计算说明,生产制度,并列表说明原材料与产品技术规格。
基本要求
设计条件:
新鲜氮氢气组成
组分
H2
N2
CH4
Ar
合计
体积%
73.16
25.17
1.29
0.38
100
新鲜气体温度:35℃
合成操作压力:30
水冷却器的冷却水温:25℃
气体部位的温度和压力自定
设计目标:
年产30万吨合成氨工艺设计毕业论文

合成氨是一种广泛应用于化肥、塑料、药品等领域的化学物质,具有
重要的经济和社会价值。
本文旨在设计一种年产30万吨合成氨的工艺,
以满足市场需求并提高生产效率。
首先,我们需要选择适合的反应器类型。
合成氨工艺通常采用催化剂
床层反应器,可有效控制反应温度和催化剂床的压力。
选择适宜的催化剂,如铁-铝催化剂,具有高催化活性和稳定性。
其次,反应器的设计需要考虑反应温度和压力。
合成氨反应的最佳工
艺条件为300-500摄氏度和150-250大气压。
通过调节反应条件,可以提
高氨气的产量和选择性。
在反应器后,需要进行气体分离和氨纯化处理。
气体分离通常采用低
温分离技术,如低温凝析法,可将氮气和未反应的氢气从产生的氨气中分
离出来。
随后,利用吸附剂和膜分离技术进行氨纯化处理,以提高氨气的
纯度和产品质量。
最后,废水处理也是一个重要的环节。
合成氨工艺中会产生废水,其
中含有高浓度的氨和其他有机物。
采用适当的废水处理工艺,如生物降解
和化学氧化等方法,可以有效降解有机物和去除氨,以达到环保要求。
总之,设计一种年产30万吨合成氨的工艺需要综合考虑反应器类型、反应条件、气体分离和氨纯化处理以及废水处理等因素。
通过合理设计和
优化工艺,提高生产效率和产品质量,将为合成氨行业的发展做出积极贡献。
年产三十万吨合成氨合成工段工艺设计_毕业设计说明书
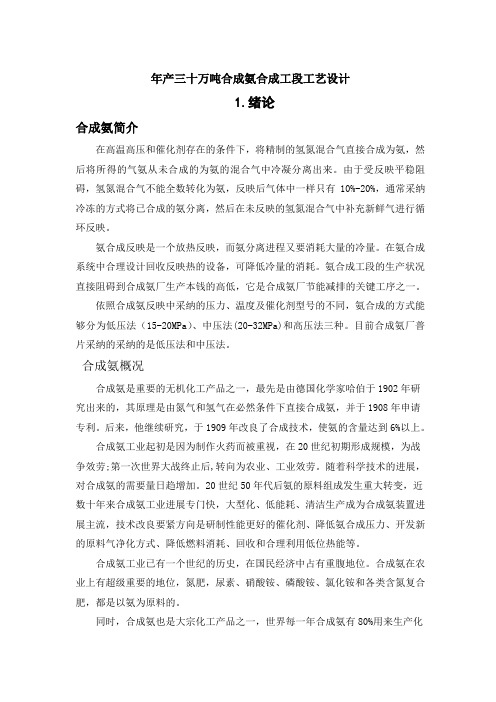
年产三十万吨合成氨合成工段工艺设计1.绪论合成氨简介在高温高压和催化剂存在的条件下,将精制的氢氮混合气直接合成为氨,然后将所得的气氨从未合成的为氨的混合气中冷凝分离出来。
由于受反映平稳阻碍,氢氮混合气不能全数转化为氨,反映后气体中一样只有10%-20%,通常采纳冷冻的方式将已合成的氨分离,然后在未反映的氢氮混合气中补充新鲜气进行循环反映。
氨合成反映是一个放热反映,而氨分离进程又要消耗大量的冷量。
在氨合成系统中合理设计回收反映热的设备,可降低冷量的消耗。
氨合成工段的生产状况直接阻碍到合成氨厂生产本钱的高低,它是合成氨厂节能减排的关键工序之一。
依照合成氨反映中采纳的压力、温度及催化剂型号的不同,氨合成的方式能够分为低压法(15-20MPa)、中压法(20-32MPa)和高压法三种。
目前合成氨厂普片采纳的采纳的是低压法和中压法。
合成氨概况合成氨是重要的无机化工产品之一,最先是由德国化学家哈伯于1902年研究出来的,其原理是由氮气和氢气在必然条件下直接合成氨,并于1908年申请专利。
后来,他继续研究,于1909年改良了合成技术,使氨的含量达到6%以上。
合成氨工业起初是因为制作火药而被重视,在20世纪初期形成规模,为战争效劳;第一次世界大战终止后,转向为农业、工业效劳。
随着科学技术的进展,对合成氨的需要量日趋增加。
20世纪50年代后氨的原料组成发生重大转变,近数十年来合成氨工业进展专门快,大型化、低能耗、清洁生产成为合成氨装置进展主流,技术改良要紧方向是研制性能更好的催化剂、降低氨合成压力、开发新的原料气净化方式、降低燃料消耗、回收和合理利用低位热能等。
合成氨工业已有一个世纪的历史,在国民经济中占有重腹地位。
合成氨在农业上有超级重要的地位,氮肥,尿素、硝酸铵、磷酸铵、氯化铵和各类含氮复合肥,都是以氨为原料的。
同时,合成氨也是大宗化工产品之一,世界每一年合成氨有80%用来生产化学肥料,20%作为其它化工产品的原料。
年产30万吨合成氨厂变换系统主要装置设计

CO2:
H2:
H2O:
将上述煤气各成分列为下表:
组成
N2
CH4
CO
CO2
H2
H2O
合计
含量(%)
1.78
6.469
17.257
20.265
29.99
24.242
100
含量(kmol)
1.78
6.469
17.257
20.265
29.99
24.242
100
2.3变换炉温升估算
式中 :出、进催化剂床气体温度℃
变换反应催化剂的选用,主要根据合成氨生产工艺要求来确定,主要依据为原料气和变换气中一氧化碳和二氧化碳的含量、原料气中硫化氢和有机硫化物的含量以及原料气最终精制工艺的要求。本合成氨装置采用低温甲醇洗﹙-65℃﹚脱硫脱碳以及液氮洗脱除一氧化碳、甲烷,和甲烷蒸汽转化的工艺路线。变换入口粗煤气中一氧化碳和二氧化碳的含量较高,硫化氢干基含量也很高。
含量(kmol)
1.78
6.469
2.741
34.812
44.537
9.695
100
第二变换炉入口温度为:280℃(553K)
第二变换炉出口温度为:410℃(683K)
第二变换炉入口CO变换率为:48.387%
第二变换炉出口CO变换率为:84.3%
2.4.3第三变换炉的物料衡算
第三变换炉入口压力假定为:2.81MPa=27.73atm
CH4:6.469kmol
CO2:28.615kmol
H2:38.34kmol
H2O:15.892kmol
第一变换炉出口各组分含量表:
表4—3
组成
N2
最新年产30万吨合成氨工程设计

年产30万吨合成氨工程设计年产30万吨合成氨工程设计摘要氨是重要的基础化工产品之一,在国民经济中占有重要地位。
合成氨生产经过多年的发展,现已发展成为一种成熟的化工生产工艺。
本设计是以煤为原料年产三十万吨合成氨转变工序的设计。
近年来合成氨工业发展很快,大型化、低能耗、清洁生产均是合成氨设备发展的主流,技术改进主要方向是开发性能更好的催化剂、降低氨合成压力、开发新的原料气净化方法、降低燃料消耗、回收和合理利用低位热能等方面上。
设计采用的工艺流程简介:采用煤造气出来的半水煤气,通入变换炉,采用煤气冷激及蒸汽换热的方式,使半水煤气在催化剂的作用下大部分CO和水蒸气反应获得H2,使CO降到合格水平。
本设计综述部分主要阐述了国内外合成氨工业的现状及发展趋势,介绍了合成氨的各个工序流程。
工艺计算部进行了一氧化碳变换工序的物料衡算、热量衡算。
设备计算部分主要是高变炉催化剂用量的具体计算,以及热水塔和换热器的计算。
本设计的优点在于选择较为良好的厂址和原料路线,确定良好的工艺条件、合理的催化剂和能源综合利用。
关键词:合成氨,水煤气,变换目录摘要 (I)第1章绪论 (1)1.1氨的性质、用途及重要性 (1)1.1.1氨的性质 (1)1.1.2氨的用途及在国民生产中的作用 (1)1.1.3产品世界产业状况 (2)1.2产品的市场需求预测 (2)1.3 产品价格分析 (3)1.4 项目内容 (3)1.4.1项目名称、地址、承办单位及性质 (3)1.4.2项目编制的依据和原则 (4)1.4.3项目背景 (4)1.5 原料的选择 (4)1.6 以煤为原料的合成氨厂总体流程选择 (5)1.7 常压气化主要工艺选择 (6)1.7.1 造气 (6)1.7.2 变换 (6)1.7.3 脱CO2 (7)1.7.4 净化 (7)1.7.5 合成氨 (7)1.7.6 结论 (7)1.8 项目意义 (8)第2章一氧化碳变换系统计算 (8)2.1 主要参数 (8)2.1.1参考操作指标 (8)2.1.2设计参数的规定 (10)2.2 中变炉工艺条件计算 (10)2.2.1中变炉一段出口温度t1的确定 (10)2.2.2中变炉生口温度2t'的确定 (12)2.2.3中变炉二段出口温度'2t的计算 (12)2.2.4出二段气体的组成含量 (13)2.2.5中变炉三段出口温度'3t的计算 (13)2.3中变炉的热量衡算 (15)2.3.1热量平衡量 (15)2.3.2喷淋水冷激段(一二段间) (16)2.3.3二段 (16)2.3.4喷水冷激段(二、三段) (16)2.3.5三段 (16)2.4 主热变换器的物热衡算 (16)2.4.1物料衡算 (16)2.4.2热量衡算 (17)2.5 低变炉工艺条件计算 (18)2.5.1低变炉出口温度t出计算 (18)2.5.2低变炉出口组成和量计算 (18)2.5.3热量衡算 (19)2.6 第一水加热器物热衡算 (19)2.6.1蒸汽露点温度115℃ (19)2.6.2第一热水塔出水绝热饱和温度ts (19)2.6.3物料衡算 (20)2.6.4热量衡算 (20)2.7 饱和塔的物热衡算 (21)2.7.1物料衡算 (21)2.7.2热量衡算 (21)2.8 热水塔的物料衡算 (22)2.8.1物料衡算 (22)2.8.2热量衡算 (22)2.8.3出热 (23)2.9 二水加热器的物热衡算 (24)2.9.1物料衡算 (24)2.9.2热量衡算 (24)2.9.3出热 (24)第3章公用工程设施 (25)3.1 公用工程方案 (25)3.2 给排水 (25)结论 (26)参考文献 (27)附录 A (28)附录 B (32)附录 C (33)附录 D (34)附录 E (35)附录 F (36)致谢 (37)第1章绪论1.1氨的性质、用途及重要性1.1.1氨的性质氨分子式为NH3,在标准状态下是无色气体,比空气轻,具有特殊的刺激性臭味。
年产30万吨合成氨转变工序设计

年产30万吨合成氨转变工序设计摘要氨是重要的基础化工产品之一,在国民经济中占有重要地位。
合成氨生产经过多年的发展,现已发展成为一种成熟的化工生产工艺。
本设计是以天然气为原料年产三十万吨合成氨转变工序的设计。
近年来合成氨工业发展很快,大型化、低能耗、清洁生产均是合成氨设备发展的主流,技术改进主要方向是开发性能更好的催化剂、降低氨合成压力、开发新的原料气净化方法、降低燃料消耗、回收和合理利用低位热能等方面上。
设计采用的工艺流程简介:天然气经过脱硫压缩进入一段转化炉,把CH4和烃类转化成H2,再经过二段炉进一步转化后换热进入高变炉,在催化剂作用下大部分CO和水蒸气反应获H2和CO2,再经过低变炉使CO降到合格水平,去甲烷化工序。
本设计综述部分主要阐述了国内外合成氨工业的现状及发展趋势以及工艺流程、参数的确定和选择,论述了建厂的选址;介绍了氨变换工序的各种流程并确定本设计高-低变串联的流程。
工艺计算部分主要包括转化段和变换段的物料衡算、热量衡算、平衡温距及空速计算。
设备计算部分主要是高变炉催化剂用量的具体计算,并根据设计任务做了转化和变换工序带控制点的工艺流程图。
本设计的优点在于选择较为良好的厂址和原料路线,确定良好的工艺条件、合理的催化剂和能源综合利用。
另外,就是尽量减少设备投资费用。
目录摘要 (I)Abstract ......................................................................................................... 错误!未定义书签。
目录.. (I)1 综述........................................................................................................................................ - 1 -1.1 氨的性质、用途及重要性.......................................................................................... - 1 -1.1.1 氨的性质.......................................................................................................... - 1 -1.1.2 氨的用途及在国民生产中的作用.................................................................. - 1 -1.2 合成氨生产技术的发展.............................................................................................. - 2 -1.2.1世界合成氨技术的发展................................................................................... - 2 -1.2.2中国合成氨工业的发展概况........................................................................... - 4 -1.3合成氨转变工序的工艺原理...................................................................................... - 6 -1.3.1 合成氨的典型工艺流程介绍.......................................................................... - 6 -1.3.2 合成氨转化工序的工艺原理.......................................................................... - 8 -1.3.3合成氨变换工序的工艺原理........................................................................... - 8 -1.4 设计方案的确定......................................................................................................... - 9 -1.4.1 原料的选择...................................................................................................... - 9 -1.4.2 工艺流程的选择............................................................................................ - 10 -1.4.3 工艺参数的确定............................................................................................ - 10 -1.4.4 工厂的选址.................................................................................................... - 11 -2 设计工艺计算...................................................................................................................... - 13 -2.1 转化段物料衡算........................................................................................................ - 13 -2.1.1 一段转化炉的物料衡算................................................................................ - 14 -2.1.2 二段转化炉的物料衡算................................................................................ - 17 -2.2 转化段热量衡算........................................................................................................ - 20 -2.2.1 一段炉辐射段热量衡算................................................................................ - 20 -2.2.2 二段炉的热量衡算........................................................................................ - 28 -2.2.3 换热器101-C、102-C的热量衡算.............................................................. - 29 -2.3 变换段的衡算........................................................................................................... - 30 -2.3.1 高温变换炉的衡算........................................................................................ - 30 -2.3.2 低温变换炉的衡算........................................................................................ - 33 -2.4 换热器103-C及换热器104-C的热负荷计算........................................................ - 35 -2.4.1 换热器103-C热负荷.................................................................................... - 35 -2.4.2 换热器104-C热负荷.................................................................................... - 36 -2.5 设备工艺计算........................................................................................................... - 36 -参考文献.................................................................................................................................. - 40 -致谢.......................................................................................................................................... - 41 -附录.......................................................................................................................................... - 41 -1 综述1.1 氨的性质、用途及重要性1.1.1 氨的性质氨分子式为NH,在标准状态下是无色气体,比空气轻,具有特殊的刺激性臭味。
30万吨合成氨毕业设计论文

前言本设计是年产30万吨合成氨转化、净化工段的设计。
设计说明书分两部分。
第一部分是综述,分九章讨论了氨的性质、用途及其在国民经济中的地位,合成氨工业的现状及其发展趋势,现代大型氨长的生产特点,设计方案的论证,生产方法的综述与选择,本设计主要工艺参数的论证与确定,生产工艺流程的评述与选择,合成氨生产原理与本设计生产流程的叙述及本设计主要设备一览表。
第二部分是工艺设计计算,分别进行了消耗定额,返氢量的计算、天然气催化转化的计算、CO变换、气体净化、甲烷化过程的物料与热量衡算,换热器热负荷计算,最后进行了设备计算-----加压两段填料吸收塔工艺设计计算。
本设计附有转化、净化工段带控制点的工艺流程图、CO2吸收塔的装配图。
本设计选用Kellogg节能型流程,具有能耗低、流程简单的特点。
目录第一章.综述 (5)1.1 氨的性质、用途及其在国民经济中的地位 (6)1.2合成氨工业的现状及其发展趋势 (6)1.3现代大型氨厂的生产特点 (8)1.4设计方案的论证 (8)1.4.1原料的选择 (9)1.4.2原料的脱硫 (9)1.4.3造气 (10)1.4.4一氧化碳变换 (12)1.4.5 CO2的脱除 (13)1.4.6微量CO、CO2的脱除 (14)1.5本设计主要工艺参数的确定与论证 (15)1.5.1水碳比 (15)1.5.2转化炉出口气甲烷含量 (15)1.5.3转化压力 (16)1.5.4高低变换出口气中的CO含量 (16)1.5.5脱碳后CO2残余含量 (16)1.5.6吸收、再生的温度、再生塔的水汽比及溶液组成 (17)1.5.7甲烷化炉入口温度 (18)1.6生产工艺流程的评述与选择 (18)1.6.1 M.W凯洛格公司 (19)1.6.2布朗公司 (19)1.6.3帝国化学公司(ICI) (20)1.6.4托普索(Hald TopsØe)公司 (20)1.6.5伍德(Uhde)公司 (20)1.7合成氨生产原理与本设计生产流程的综述 (28)1.7.1原料气的脱硫 (28)1.7.2烃类蒸汽转化 (21)1.7.3 CO变换 (21)1.7.4原料气中CO2的脱除 (22)1.7.5甲烷化脱除微量的CO及CO2 (23)第二章工艺设计计算 (34)2.1设计依据: (34)2.2消耗定额、返氢量的计算 (34)2.2.1计算条件: (35)2.2.2计算变量 (35)2.2.3求解变量 (35)2.2.4计算 (35)2.3转化 (38)2.3.1一段转化炉物料衡算 (38)2.3.2二段炉物料、热量衡算 (42)2.4变换 (50)2.4.1高变物料、热量计算 (50)2.4.2低变炉物料、热量衡算 (53)2.4.3 102-F排水量计算 (56)2.5 CO2吸收塔原料气系统物料衡算 (58)2.5.1计算条件: (58)2.5.2.计算 (58)2.6甲烷化 (45)2.6.1甲烷化炉的物料衡算 (46)2.6.2甲烷化炉热量衡算 (47)2.6.3校核 (48)2.6.4 104-F排水量的计算 (49)2.7净化 (66)2.7.1本菲尔溶液循环量的计算 (66)2.7.2 1103-F排水量及回流水量的计算 (68)2.7.3 1110-C、1104-C热负荷的计算 (72)2.7.4吸收、再生系统的热平衡 (57)2.8换热器热负荷的计算 (65)2.8.1 103-C热负荷计算 (65)2.8.2 104-C热负荷计算 (66)2.8.3 1107-C的热负荷 (66)2.8.4 114-C热负荷计算 (86)2.8.5 144-C热负荷计算 (87)2.8.6 115-C的热负荷计算 (89)2.8.7 1115-C热负荷计算 (90)2.8.8 136-C热负荷计算 (92)第三章加压两段填料吸收塔设计 (73)3.1设计项目: (94)3.2设计条件 (94)3.3设计计算 (96)3.3.1塔型设计 (96)3.3.2 流体接触方式及喷淋 (96)3.3.3填料选择 (96)3.3.4上塔塔径计算 (97)3.3.5上塔填料高度计算 (80)3.3.6下塔塔径计算及下塔填料计算 (82)3.3.7校核计算 (85)第1章综述氮(N),是植物生长所必需的重要元素之一,空气的主要成分是氧和氮,其中氮占78%体积。
毕业设计论文—30万吨合成氨设计

年产三十万吨合成氨装置的粗煤气一氧化碳耐硫变换工艺设计摘要本文介绍了合成氨生产基本情况以及年产三十万吨合成氨系统流程,介绍了一氧化碳变换的基本原理,工艺条件以及工艺参数和变换催化剂的选择原则。
并且对第一和第二变换炉进行热量和能量衡算,对催化剂装填量进行计算,掌握了变换系统的设计方法。
关键词:变换,催化剂,工艺条件,一氧化碳含量目录第一章前言 (4)第1.1节合成氨在国民经济中的重要地位 (4)第1.2节合成氨工业发展简介 (5)第1.3节天脊集团合成氨的生产方法 (5)第二章设计说明 (7)第2.1节设计目的 (7)第2.2节工艺原理 (7)第2.3节工艺条件对一氧化碳含量的影响 (7)第2.4节上下流程配置 (8)第2.5节催化剂的选择 (8)第2.6节热量回收 (9)第三章设计计算 (10)第3.1节已知条件与要求 (10)第3.2节核算蒸汽是否够用 (10)第3.3节计算煤气成分 (11)第3.4节变换炉温升的估算 (11)第四章物料衡算 (13)第4.1节第一变换炉的物料衡算 (13)第4.2节第二变换炉的物料衡算 (15)第五章热量衡算 (18)第5.1节第二换热器进口煤气温度的计算 (18)第5.2节第一换热器进口煤气温度的计算 (19)第5.3节第一换热器热量衡算 (21)第5.4节第二换热器热量衡算 (21)第5.5节第一变换炉热量衡算 (22)第5.6节第二变换炉热量衡算 (23)第六章变换炉的工艺计算 (23)第6.1节催化剂用量的计算 (23)第6.2节变换炉工艺尺寸的计算 (25)第6.3节催化剂床层阻力的计算 (26)第七章换热器选型 (29)第7.1节第一换热器的选型与计算 (29)第八章设备一览表 (34)第九章设计结果分析和改进方向 (34)第十章参考文献 (35)第十一章致谢 (36)第一章前言第1.1节合成氨工业在国民经济中的重要地位合成氨是化工的重要组成部分,在国民经济中有相当重要的位置。
-年产30万吨合成氨脱碳工段工艺设计

年产30万吨合成氨脱碳工段工艺设计[摘要]脱碳工段是合成氨工程中必不可少的工段之一,二氧化碳吸收塔和溶液再生塔是脱碳过程中不可缺少的塔设备。
本文权衡众多合成氨脱碳方法之利弊,最终选择碳酸丙烯酯脱碳法。
首先进行工艺流程分析并根据工艺参数及有关标准进行二氧化碳吸收塔和解析塔内的物、热量衡算;其次就二氧化碳吸收塔、溶液再生塔等设备利用物理吸收机理、传质传热方程、溶液物性数据等方面的知识进行塔体的总体结构设计和计算,设计出二氧化碳吸收塔的塔径为2.1m,塔高为27m,二氧化碳解吸塔塔径2.4m,塔高29m;然后对二氧化碳吸收和解吸塔进行了必要的强度校核;最后对脱碳工段车间结构布置进行合理的设计。
本设计作为理论上的准备工作,为分析工艺流程、设备设计上存在的问题、确定问题的根源、提出解决问题的合理方案准备了充分的理论依据。
[关键词] 碳酸丙烯酯法;脱碳工艺;工程设计The Design of the Decarbonization Section in the Production of the 40 thousand tons Synthetic Ammoniaper yearAbstract:Decarbonizing section is one of the absolutely necessary sections in the Synthetic Ammonia, and the Carbon dioxide absorption tower and the solution regeneration tower are indispensable tower equipment in the Synthetic Ammonia.This paper tradeoff advantages and disadvantages of much approach to decarbonization, propylene carbonate (PC)decarboniza-tion are selected finally. The technological process was analyzed, and the material and heat was balanced according to parameters and relevant standards firstly. The tower body general structure was designed calculation by using physical absorption Mechanism, mass transfer and heat transfer equation, solution -physical data stc secondly.The diameter of absorption tower is 2.1m, the height of tower is 27m, diameter of desorption tower is 2.4m, the height oftower is 29m, which were designed.,And then the strength of the Carbon dioxide absorption tower and the solutionregeneration tower are checked. The decarbonizing section structural arrangement was reasonable design finally. As the theoretical preparation work, this designing prepare sufficient theoretical basis for people to analysis the problems of technological process, equipment design, determined root of problems, posing reasonable plan to solve problems.Keywords: Decarbonization process; Carbon dioxide removal with PC method; Proeess design毕业设计(论文)原创性声明和使用授权说明原创性声明本人郑重承诺:所呈交的毕业设计(论文),是我个人在指导教师的指导下进行的研究工作及取得的成果。
大学毕业设计---年产30万吨合成氨造气工段工艺
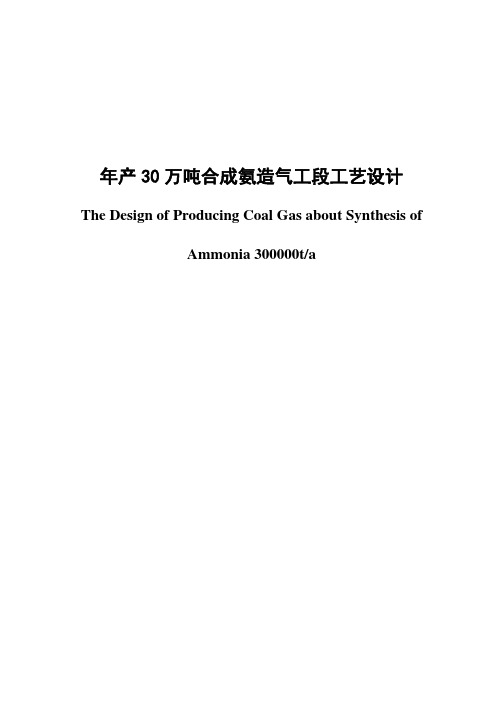
年产30万吨合成氨造气工段工艺设计The Design of Producing Coal Gas about Synthesis ofAmmonia 300000t/a目录摘要 (I)Abstract (II)引言 (1)第一章绪论 (3)1.1 煤气化发展史 (3)1.2 国内外发展现状 (4)第二章生产方法的选择 (5)2.1生产方法的介绍 (5)2.1.1 固定床气化法 (5)2.1.2 流化床气化 (5)2.1.3 气流床气化 (6)2.2 生产方案的选择及论证 (6)第三章常压固定床间歇气化法 (8)3.1 固定床气化法的特点 (8)3.2 半水煤气定义 (8)3.3 半水煤气制气原理 (8)3.3.1 煤气发生炉构造及气化反应的分区 (8)3.3.2 制气原理 (9)3.4 生产半水煤气对固体原料性能的要求 (10)3.5 间歇式制半水煤气的工艺条件 (11)3.6 生产流程的选择及论证 (12)3.7 间歇式气化的工作循环 (13)3.8 间歇式制半水煤气工艺流程 (14)3.9 各主要设备简介 (15)3.9.1 煤气发生炉 (15)3.9.2 燃烧室 (15)3.9.3 废热锅炉 (16)3.9.4 洗气箱 (16)3.9.5 洗涤塔 (16)3.9.6 烟囱 (17)3.9.7 自动机 (17)第四章工艺计算 (18)4.1 已知条件 (18)4.2 物料及热量衡算 (20)4.2.1 吹风阶段的计算 (20)4.2.2 制气阶段的计算 (22)4.2.3 总过程计算 (26)4.3 配气计算 (29)4.4 消耗定额 (30)4.5 吹净时间核算 (30)4.6 废热锅炉的热量衡算 (30)4.6.1 已知条件 (30)4.6.2 热量衡算 (32)4.6.3 热量平衡和总固体平衡 (35)4.7 夹套锅炉的物料及热量衡算 (35)4.7.1 已知条件 (35)4.7.2 产气量及消耗量计算 (36)第五章设备计算选型 (37)5.1 煤气炉指标 (37)5.2 煤气台数的确定 (38)5.3 空气鼓风机的选型及台数确定 (39)5.4 废热锅炉的选型 (39)结论 (41)致谢............................................................................................. 错误!未定义书签。
- 1、下载文档前请自行甄别文档内容的完整性,平台不提供额外的编辑、内容补充、找答案等附加服务。
- 2、"仅部分预览"的文档,不可在线预览部分如存在完整性等问题,可反馈申请退款(可完整预览的文档不适用该条件!)。
- 3、如文档侵犯您的权益,请联系客服反馈,我们会尽快为您处理(人工客服工作时间:9:00-18:30)。
年产三十万吨合成氨合成工段工艺设计毕业论文1.绪论1.1合成氨简介在高温高压和催化剂存在的条件下,将精制的氢氮混合气直接合成为氨,然后将所得的气氨从未合成的为氨的混合气中冷凝分离出来。
由于受反应平衡影响,氢氮混合气不能全部转化为氨,反应后气体中一般只有10%-20%,通常采用冷冻的方法将已合成的氨分离,然后在未反应的氢氮混合气中补充新鲜气进行循环反应。
氨合成反应是一个放热反应,而氨分离过程又要消耗大量的冷量。
在氨合成系统中合理设计回收反应热的设备,可降低冷量的消耗。
氨合成工段的生产状况直接影响到合成氨厂生产成本的高低,它是合成氨厂节能减排的关键工序之一。
根据合成氨反应中采用的压力、温度及催化剂型号的不同,氨合成的方法可以分为低压法(15-20MPa)、中压法(20-32MPa)和高压法三种。
目前合成氨厂普片采用的采用的是低压法和中压法。
1.2 合成氨概况合成氨是重要的无机化工产品之一,最早是由德国化学家哈伯于1902年研究出来的,其原理是由氮气和氢气在一定条件下直接合成氨,并于1908年申请专利。
后来,他继续研究,于1909年改进了合成技术,使氨的含量达到6%以上。
合成氨工业起初是因为制作炸药而被重视,在20世纪初期形成规模,为战争服务;第一次世界大战结束后,转向为农业、工业服务。
随着科学技术的发展,对合成氨的需要量日益增长。
20世纪50年代后氨的原料构成发生重大变化,近数十年来合成氨工业发展很快,大型化、低能耗、清洁生产成为合成氨装置发展主流,技术改进主要方向是研制性能更好的催化剂、降低氨合成压力、开发新的原料气净化方法、降低燃料消耗、回收和合理利用低位热能等。
合成氨工业已有一个世纪的历史,在国民经济中占有重要地位。
合成氨在农业上有非常重要的地位,氮肥,尿素、硝酸铵、磷酸铵、氯化铵以及各种含氮复,都是以氨为原料的。
同时,合成氨也是大宗化工产品之一,世界每年合成氨有80%用来生产化学肥料,20%作为其它化工产品的原料。
据IFA全球合成氨产能的调查,统计从2007年的1.763亿吨NH3已增加到2012年的4.652亿吨NH3,增加量的三分之一将通过产能改造实现,其余三分之二将通过全球围近50套生产装置的开车实现,其中有一半来自中国。
2008年中国合成氨新建或拟建项目产能达300万吨,其中平安化肥有限责任公司设计年产合成氨15万吨、硝铵30万吨,项目总投资8亿元,建设周期为2009年-2010年;潞安矿业集团有限责任公司计划投资年产合成氨30万吨建设周期为2009-2011年,总投资为28亿元;中国石油油田分公司投资建设年产合成氨45万吨,前期工作已开始,项目总投资25亿元;同德化工股份08年投资建设年产合成氨18万吨、硝酸铵10万吨、甲醇3万吨、尿素22万吨。
省市建设年产18万吨合成氨、年加工30万吨尿素的生产装置。
该项目建设周期为2008年-2010年,项目总投资为8.4399亿元;三星化工有限责任公司投资年产50万吨合成氨100万吨尿素6万吨三聚氰胺工程。
2009年初年国务院研究通过保障化肥生产供应,促进化肥行业改革和发展的政策,标志着国化肥市场化改革的正式启动,国家对支持农业生产、保障粮食安全给予了极大的重视,为了调动农民的种田积极性,各项农资补贴大幅度提高。
这些政策不但调动了农民种田、购肥的积极性,也成为支撑化肥市场的信心,国化肥市场产能大量释放。
春节过后,随着供电和运输逐步恢复,尿素和硝酸企业开始复工或加大生产负荷,春季用肥季节的逐渐临近,各地尿素市场开始出现回暖,对合成氨市场需求也逐渐上升,来自chemsino分析预测,09年合成氨市场仍将保持稳定,新建装置项目计划延展受到国家产业政策的鼓励,当前我国尿素供应依旧紧,今后5-10年,我国尿素的需求将增加1000万吨以上,合成氨行业景气度依旧看好。
1.3 合成氨工业的发展趋势原料路线的变化方向煤的储量约为石油、天然气总和的10倍,自从70年代中东石油涨价后,从煤制氨路线重新受到重视,但因以天然气为原料的合成氨装置投资低、能耗低、成本低的缘故,到20世纪末,世界大多数合成氨厂仍将以气体燃料为主要原料。
节能和降耗合成氨成本中能源费用占较大比重,合成氨生产的技术改进重点放在采用低能耗工艺、充分回收及合理利用能量上,主要方向是研制性能更好的催化剂、开发新的原料气净化方法、降低燃料消耗、回收和合理利用低位热能等。
与其他产品联合生产合成氨生产中副产大量的二氧化碳,不仅可用于冷冻、饮料、灭火,也是生产尿素、纯碱、碳酸氢铵的原料。
如果在合成氨原料气脱除二氧化碳过程中能联合生产这些产品,则可以简化流程、减少能耗、降低成本。
1.4 合成氨的工艺流程合成氨的主要原料可分为固体原料、液体原料和气体原料。
经过近百年的发展,合成氨技术趋于成熟,形成了一大批各有特色的工艺流程,但都是由三个基本部分组成,即原料气制备过程、净化过程以及氨合成过程。
由于本设计主要研究氨合成过程中的合成工段,所以对于原料制备和气体净化过程不做介绍,以免影响读者参阅,如有兴趣可查看其相关资料。
氨合成是将纯净的氢、氮混合气加压到高压,在催化剂的作用下合成氨。
氨的合成是提供液氨产品的工序,是整个合成氨生产过程的核心部分。
氨合成反应在较高压力和催化剂存在的条件下进行,由于反应后气体中氨含量不高,一般只有10%~20%,故采用未反应氢氮气循环的流程。
氨合成反应式如下:N2+3H2→2NH3(g) ΔH =-92.4kJ/mol1.5 工艺流程的选择合成氨的生产工艺条件必须满足产量高,消耗低,工艺流程及设备结构简单,操作方便及安全可靠等要求。
决定生产条件最主要的因素有操作压力、反应温度、空间速度和气体组成等。
氨合成反应是气体体积缩小的反应,提高压力有利于反应平衡向右移动。
压力增加平衡常数增大,因而平衡氨含量也增大。
所以,提高压力对氨合成反应的平衡和反应速度都有利,在一定空速下,合成压力越高,出口氨浓度越高,氨净值越高,合成塔的生产能力也越大。
氨合成压力的高低,是影响氨合成生产中能量消耗的主要因素之一。
主要能量消耗包括原料气压缩功、循环气压缩功和氨分离的冷冻功。
提高操作压力,原料气压缩功增加,合成氨净值增高,单位氨所需要的循环气量减少,因而循环气压缩功减少,同时压力高也有利于氨的分离,在较高气温下,气氨即可冷凝为液氨,冷冻功减少。
但是压力高、时,对设备的材料和制造的要求均高。
同时,高压下反应温度一般较高,催化剂使用寿命也比较短,操作管理比较困难。
所以。
要根据能量消耗、原料费用、设备投资等综合技术经济效果来选择操作压力。
目前我国中小型合成氨厂合成操作压力大多采用15~32MPa。
合成氨反应是一个可逆放热反应,当温度升高时,平衡常数下降,平衡氨含量必定减少。
因此从化学平衡角度考虑,应尽可能采用较低的反应温度。
实际生产中还要考虑反应速率的要求。
为了提高反应速率,必须使用催化剂才能实现氨合成反应。
而催化剂必须在一定的温度围才具有活性,所以氨合成反应温度必须维持在催化剂的活性围。
合成氨生产所用的催化剂活性温度在400~500 ℃。
反应温度不能低于活性温度,在活性温度围选用较低温度,也有利于延长催化剂的使用寿命。
在合成氨生产过程中,对应于任意一个瞬时转化率都存在一个最大的反应速率的温度,即最佳温度。
就整个反应过程来说,随着反应的进行,转化率不断增加,最佳温度随转化率增加而降低。
在实际生产中,应尽可能沿着最佳温度曲线进行。
反应温度的控制还与催化剂的使用时间有关。
新的催化剂因活性比较高,可采用较低的温度。
在中期活性降低,操作温度应比初期适当提高8~10 ℃。
催化剂使用到末期,活性因衰老而减弱,应再适当提高温度。
本设计采用冷凝法。
一般含氨混合气体的冷凝分离是经水冷却器和氨冷嚣二步实现的。
液氨在氨分离器中与循环气体分开,减压送入贮槽。
贮槽压力一般为1.6~1.8 MPa,此时,冷凝过程中溶解在液氨中的氢、氮及惰性气体大部分可减压释放出来。
1.6 合成工段工艺流程简述由高压机送来的新鲜气与冷凝塔一次出口循环气混合送入氨冷器,在氨冷器,气体走管,液氨走管外,由于液氨的蒸气吸取热量,气体被进一步冷却,并使气体中部分气氨冷凝管外蒸气的气氨经沫除器分离掉液氨后,去氨气柜或硝铵车间。
氨的高压混合气,自氨冷器出来,进入冷凝塔下部的氨分离器,分离液氨,除氨后的混合气,再经过冷凝塔上部的热交换器与循环机气体换热,二次出冷凝塔。
自冷凝塔二次出口的循环气其中一部分进入合成塔上部一次入口,气体沿着件与外箱间环隙向下冷却塔壁后,进入下部换热器管外,另一部分循环气直接进入塔外气-气换热器冷气入口,通过管外并与管废锅口出来气体换热后,设有副线气流分成四股,其中二股作为冷凝气分别从塔顶进入菱形分布器和层间换热器,一股为塔底副线,另一股进入合成塔下部二次入口与一次入口气体混合,通过下部热交换器与管气体换热后与塔底副线气混合,由中心管进入第一轴层反应,反应后气体与塔顶引入的第一冷凝气混合进入第二轴向层反应气体进入层间换热器管与第二冷凝气换热降低气体温度进入径向层,第二冷凝气换热后提高自身温度进入外中心管与中心管,气体混合进入第一轴向层,径向层自里向外径向流出,通过整个触媒层进入下部换热器管,与管外换热后出塔进入废锅炉,与脱氧水换热副产品,0.8MPa的蒸汽,气体温度降低到217 ℃以下,进入气-气换热器,气流经与管外气体换热器降温后进入水冷器,后进入循环机,补充压力,经滤油器除去油圬后,进入冷凝塔上部的热交换器,出热交换器后与新鲜气混后开始下一个循环。
2工艺计算2.1 物料衡算2.1.1计算依据(1)产量:W=37.88tNH/h3(2)催化剂用量: 70m3(3)精炼气成分见下表表1 精炼气成分=2.00%(4)合成塔入口氨含量:NH3入合成塔出口氨含量:NH3=17.00%出合成塔入口惰性气体含量:AR +CH4=18.00%(5)合成塔操作压力:30Mp(设备及管道造成的压力降;设备及管道的a冷热量损失;冷交换器及氨冷器中溶解在液氨中的气量均忽略不计)(6)精炼气温度:35 ℃(7)水冷器冷却水温度:25℃(8)循环机进出口压差:2.97MPa(9)年工作日:330天(10)计算基准:生产一吨液氨。
2.1.2 计算物料点流程图1 物料恒算流程图2.1.3 合成塔入口气组分由计算依据得:入塔氨含量: y 5 NH 3=2.000%入塔甲烷含量:y 5 CH 4=18.00%38.029.129.1+⨯=15.19% 入塔氩含量: y 5A R =18.00%38.029.138.0+⨯=4.48% 入塔氢气含量:y 5H 2=[100-(2.00+15.19+4.48)] ×(3/4) ×100%=58.77% 入塔氮含量: y 5 N 2=[100-(2.00+15.19+4.48)] ×(1/4) ×100%=19.56%表2 入塔气组分含量(%)2.1.4 合成塔出口气组分以1000kmol 入塔气作为计算基准求出塔气组分:塔生成氨含量:N NH3=3338NH 5NH 8NH 5y 1)-(+y y N =250.77kmol 出塔气量(N 8)=入塔气量-生成氨含量=1000-250.77=749.23kmol出塔氨含量: 38NH y =17.00%出塔甲烷含量:48CH y =⨯85N N45CH y =100015.19%749.23⨯=20.27% 出塔氩含量: 8AR y =⨯85N N 8AR y =1000 4.48%749.23⨯=5.98% 出塔氢气含量:y 8H2 = 43(1-y 8NH3-y 8CH4-y 8A R )⨯100%=43(1-0.17-0.20-0.06)⨯100% =42.75%出塔氮含量:y 8N2 = 41(1-y 8NH3-y 8CH4-y 8A R )⨯100% =41(1-0.17-0.20-0.06)⨯100%=14.25%2.1.5 合成率由式%100-1123,333⨯-+-=))(()(,入,出出,入,出i NH NH NH NH y y y y y α得: 式中 α——氨合成率,%;i y ——进合成塔气体中惰性气体含量,(摩尔分率)%。