5.5m捣固焦炉的优势
5.5m捣固焦炉简介
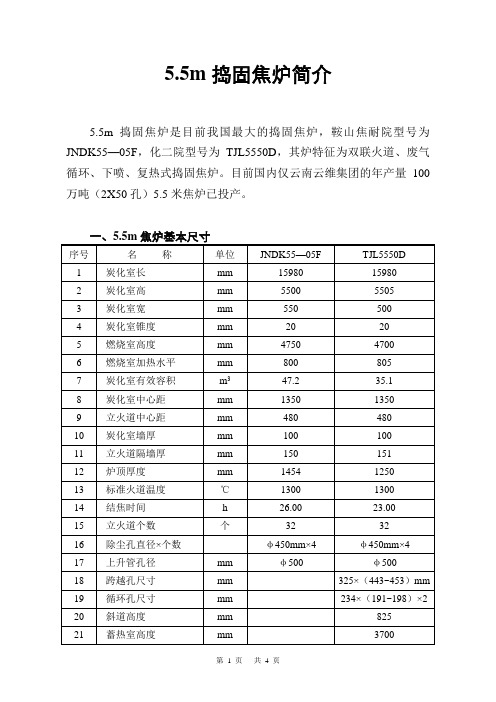
5.5m捣固焦炉简介5.5m捣固焦炉是目前我国最大的捣固焦炉,鞍山焦耐院型号为JNDK55—05F,化二院型号为TJL5550D,其炉特征为双联火道、废气循环、下喷、复热式捣固焦炉。
目前国内仅云南云维集团的年产量100万吨(2X50孔)5.5米焦炉已投产。
二、工艺参数(以公称能力100万吨/年干全焦规模计算)焦炉组数:2×50孔精煤堆比重(干):1.0t/m3煤饼尺寸(长×宽×高):15000×450×5200mm煤饼重量:35.1t焦炉周转时间:23hr产量计算:Q=365×24×2×50×35.1×0.75×0.97/23=97.26万吨/年三、焦炉的砖用量(1×50孔)四、焦炉机械(2×50孔)装煤推焦机2台720t/台除尘拦焦机2台216t/台熄焦车1台92t/台电机车1台45t/台导烟车2台85t/台24锤捣固机2台90t/台(固定)液压交换机2套 5.5/套五、焦炉新技术的应用1、蓄热室封墙内设计30mm厚硅酸钙隔热板,蓄热室外封墙设计50mm厚的复合硅酸盐整体面外加海泡石抹面,既减少了封墙漏气,又减少了热损失,改善了炉头加热,改善了操作环境。
2、在炉顶区和焦炉基础中采用强度大、隔热效率高的漂珠砖和高强度隔热砖,代替了传统焦炉采用的红砖和普通隔热砖,确保炉项表面层平整、严密,降低了炉顶面和焦炉顶板温度,改善了操作环境。
3、焦炉装煤过程产生的大量烟尘,采用炉顶导烟车收焦烟尘,送至地面站焚烧洗涤后达标排放。
4、出焦采用出焦地面站除尘工艺,除尘效率高,减少污染环境。
5、熄焦塔采用折流板除尘,预留干熄焦位置。
6、炉门采用新型弹簧炉门,加强炉门严密性,与敲打刀边炉门相比,显著减少炉门无组织排放。
近年来,焦炉不断向大型化、高效化、自动化、环保化发展,焦炉发展的主要标志是大容积,致密硅砖,提高火道温度,提高热效率及操作控制的自动化。
5.5米焦炉工艺优化建议

盛盟5.5米焦化工艺优化方案一:炉体方面机侧余煤皮带,焦耐设计院在初期推广时,没有这一项,约在07年以后,第一个试点焦炉投产,发现这一设计缺陷,焦耐院在焦炉机侧分烟道外侧增加了D500mm小皮带,基本可以解决机侧余煤集中堆放难题,但在现有实际情况看,存在一定问题,综合讲也就是效果差,尤其在频繁塌头塌尾次数多时,余煤从溜槽内直接冲出皮带,造成轨道积煤、道心余煤满地,道心、轨道卫生难以保持,刮风天气大量精煤被风刮走,增加损坏,污染环境。
改进方案,在建的焦炉可变更设计,皮带机采用宽度800mm,皮带两侧安装护皮,运料时,挡住精煤不下落,皮带机外部整体采用大包厢设计,既可以检修,杜绝扬尘,外观整齐美观,安装在机侧通廊内上部。
已经投产的焦炉,在整条皮带两侧增加挡皮,挡住物料不外掉。
下部增加清扫装置(最好采用无动力清扫器)安装在机头下部,清扫归堆,使整条皮带下部保持清洁。
(此方案甲方已采纳)。
机头接余煤位置,设计上为接煤斗,配一台叉车将接满煤的煤斗装在专用汽车上运回煤场,这样多了一道工序,人员配置相应增加,变更为、机头下部基础下挖1.5米,呈坡道状,用砼浇筑底板,两侧砌砖墙至上地平面,作用是能用汽车直接接料,省去叉车和接煤箱设施,既节省又方便。
道心清扫,由于焦炉机侧煤粉较大,治理的再好道心也会有余煤,清扫不干净,大风天气扬尘严重,设计上不考虑洒水抑尘措施,在盛盟作业区两辆推焦车上增加了水箱,喷淋洒水支管安装在垂直于道心车辆两侧的结构梁下部,不定时的对道心进行喷淋洒水作业,有效地抑制了扬尘效果。
二:设备方面装煤车、推焦车1#刮板机在使用中故障率高,尤其在塌煤塌焦量大时,瞬间刮板机就会卡死,严重时减速机底座断裂损坏,这种情况普变存在。
改进建议:(1)减速机外壳采用铸钢件,增加强度,电机和减速机型号相应变大。
(2)刮板机上部的Φ14篦条改为Φ25,间距30mm,提高强度。
2、装煤车煤壁下部漏煤的治理,由于煤壁下部和滑道之间间隙过大,(约10—25mm)之间,在每天装煤过程中,煤壁闭合时,从间隙处往外漏煤,并且量很大,清理不及时就会埋住移门油缸,卫生量很大。
5.5 m捣固焦炉设备的性能和结构特点

5.5 m捣固焦炉设备的性能和结构特点作者:樊海莲,吴刚来源:《科技创新与生产力》 2012年第7期樊海莲,吴刚(太原重型机械集团有限公司技术中心,山西太原 030024)摘要:针对太原重工股份有限公司生产的5.5 m捣固焦炉设备的性能作了介绍,就设备的重要参数和设备所使用的技术进行了描述。
5.5 m捣固焦炉设备的开发在最初确定方案时,就以高技术含量、高自动化水平、高环保效果为目标,现已成为具有市场竞争力的高可靠性、高实用性的设备。
关键词:5.5 m捣固焦炉成套设备;出焦;熄焦;烟尘处理中图分类号:TQ520.5 文献标志码:A DOI:10.3969/j.issn.1674-9146.2012.07.107太原重型机械集团有限公司的上市公司——太原重工股份有限公司(以下简称太原重工)于2007年成功开发出5.5 m捣固焦炉成套设备,到2012年6月已成功生产近百套,分布于黑龙江、新疆、甘肃、内蒙、河北、山东等地,并成功进入印度市场。
5.5 m捣固焦炉设备能够在捣固式焦炉生产中完成捣固煤饼、装煤、出焦、熄焦、烟尘处理等功能,具有环保高效、自控水平高的特点。
结合原有4.3 m捣固焦炉设备、热回收捣固焦炉设备、6 m和7 m顶装焦炉设备运行的情况以及所取得的经验,针对捣固时车辆的稳定性,装入炭化室时煤饼的完整性,装煤、推焦、接焦时产生烟尘的收集和处理,减小操作工人的劳动强度以及车辆的自动化水平等五方面,在5.5 m捣固焦炉设备中做了大量改进。
目前,该设备每年的需求达数十套,具有很好的社会效益和经济效益。
1 5.5 m捣固焦炉设备完成的功能5.5 m捣固焦炉设备适用于年产量100万~ 150万t焦化项目,其主要功能包括捣固煤饼、装煤、出焦、熄焦、烟尘处理、炉门清扫、炉框清扫、头尾焦处理等,其每炉理论出焦量为27.2~31.3 t。
侧装煤车用来完成洗精煤从煤塔落入装煤机构煤槽、用捣固机将洗精煤捣固成煤饼、用托煤板将煤饼装入炭化室内;推焦车用来完成将成熟焦炭推出炭化室,并在推焦前和送煤饼后启闭焦炉机侧炉门,进行余煤、头尾焦回收;除尘拦焦车用来将推出的成熟焦炭导入熄焦车,并将推焦时产生的烟尘导入地面除尘站,导焦前后启闭焦侧炉门;熄焦车用于盛装1 000 ℃炙热焦炭,并将其运送到熄焦塔下熄焦,送至卸焦位卸焦;导烟车用来完成将装煤时产生的荒煤气及烟尘导入相邻炭化室,防止烟尘逸散。
5.5m捣固焦炉空炉保温技术探索与实践
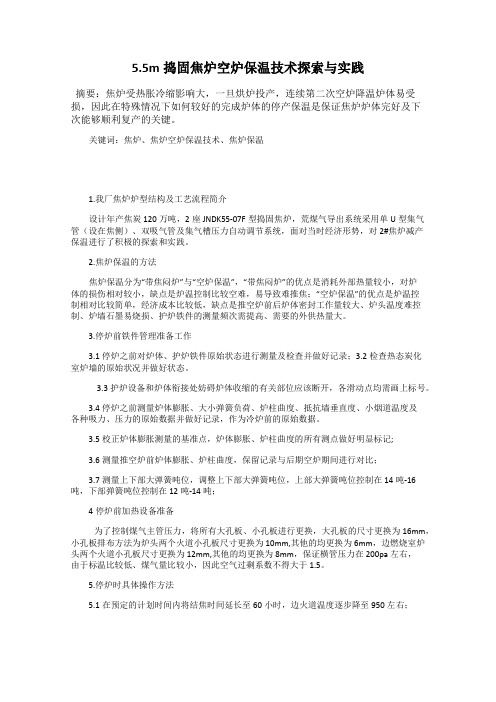
5.5m捣固焦炉空炉保温技术探索与实践摘要:焦炉受热胀冷缩影响大,一旦烘炉投产,连续第二次空炉降温炉体易受损,因此在特殊情况下如何较好的完成炉体的停产保温是保证焦炉炉体完好及下次能够顺利复产的关键。
关键词:焦炉、焦炉空炉保温技术、焦炉保温1.我厂焦炉炉型结构及工艺流程简介设计年产焦炭120万吨,2座JNDK55-07F型捣固焦炉,荒煤气导出系统采用单U型集气管(设在焦侧)、双吸气管及集气槽压力自动调节系统,面对当时经济形势,对2#焦炉减产保温进行了积极的探索和实践。
2.焦炉保温的方法焦炉保温分为“带焦闷炉”与“空炉保温”,“带焦闷炉”的优点是消耗外部热量较小,对炉体的损伤相对较小,缺点是炉温控制比较空难,易导致难推焦;“空炉保温”的优点是炉温控制相对比较简单,经济成本比较低,缺点是推空炉前后炉体密封工作量较大、炉头温度难控制、炉墙石墨易烧损、护炉铁件的测量频次需提高、需要的外供热量大。
3.停炉前铁件管理准备工作3.1停炉之前对炉体、护炉铁件原始状态进行测量及检查并做好记录;3.2检查热态炭化室炉墙的原始状况并做好状态。
3.3护炉设备和炉体衔接处妨碍炉体收缩的有关部位应该断开,各滑动点均需画上标号。
3.4停炉之前测量炉体膨胀、大小弹簧负荷、炉柱曲度、抵抗墙垂直度、小烟道温度及各种吸力、压力的原始数据并做好记录,作为冷炉前的原始数据。
3.5校正炉体膨胀测量的基准点,炉体膨胀、炉柱曲度的所有测点做好明显标记;3.6测量推空炉前炉体膨胀、炉柱曲度,保留记录与后期空炉期间进行对比;3.7测量上下部大弹簧吨位,调整上下部大弹簧吨位,上部大弹簧吨位控制在14吨-16吨,下部弹簧吨位控制在12吨-14吨;4停炉前加热设备准备为了控制煤气主管压力,将所有大孔板、小孔板进行更换,大孔板的尺寸更换为16mm,小孔板排布方法为炉头两个火道小孔板尺寸更换为10mm,其他的均更换为6mm,边燃烧室炉头两个火道小孔板尺寸更换为12mm,其他的均更换为8mm,保证横管压力在200pa左右,由于标温比较低、煤气量比较小,因此空气过剩系数不得大于1.5。
大型捣固焦炉资料

5.5米、6米、6.25米捣固焦炉使用情况6m捣固焦炉中鸿煤化有限公司年产260万吨焦炭项目一期工程建设的2*60孔炭化室高6m大型捣固焦炉,年产干全焦132万吨。
在国内属首座建成投产的6m捣固焦炉于2010年4月15日15时10分2#炭化室开始装煤;16日22时零9分推出第一炉焦炭。
该捣固焦炉炭化室长15980mm;高6000mm;平均宽500mm;锥度30mm;中心距1400mm;焦炉炉墙的极限侧负荷达10kpa ,加热水平高度805mm,采用12孔薄壁格子砖。
煤饼几何尺寸15140/14940*5800*450/430,煤饼体积38.882m3,煤饼高宽比13.18,单孔装干煤量42.22t,单孔产焦量31.67t,焦炉周转时间22.5h,每孔年产干焦炭12330t。
2*60孔捣固焦炉炉组配置60锤捣固机(其中4锤备用),捣固侧装煤车、推焦车2台(左右型各1台),炉顶导烟车2台(其中备用一台),拦焦车、熄焦车、电机车各2台(其中各备用1台),摇动给料机18台。
仅一套30锤固定式捣固机为德国制造进口,其余车辆等机械设备均为国内制造。
采用二轨式除尘拦焦车,设有装煤除尘地面站和推焦除尘地面站。
采用湿法熄焦,预留一套140t/h 干熄焦装置和牵车台位置。
捣固煤塔贮量为3000t.,在焦侧设置一座高125m烟囱,集气管布置在焦侧(焦炉与化产之间安全距离符合2008新版《焦化安全规程》之规定),采用双吸气管。
一组2痤60孔捣固焦炉用硅砖约23450吨6米捣固焦炉1、河南中鸿集团6米捣固焦炉(2号炉已完成炉体砌筑),计划明年1月份烘炉。
目前平煤集团已相对控股了该项目(占41%股权),建设过程已提速,1号炉建设也启动了,已完成炉体耐火砖订货。
武汉科技大学设计研究院设计的,拥有完全自主知识产权,并已得到专利授权。
炭化室中心距1400,炭化室平均宽500,锥度30,其余尺寸与6米顶装差不多,但加热水平做了调整。
5.5m捣固焦炉设备的性能和结构特点

煤 饼 质 量
/ t
1 9 ( 态 ) 61 0 热 1 10 热 态 ) 69 ( 1 9 ( 态 ) 61 0 热
5 2( 态) 2 热 6 5 7( 态) 7 热 5 5 7( 态) 7 热 5
74 0 7 65 0 0 65 0 热 态 ) 0 (
刹车功能,确保车辆的高速、低速 、定位要求 。 2 )为 了保 证 行 车 安 全 和对 位 准 确 ,电机 车 和
焦 罐 车都设 有 制 动系 统 。正 常操 作 时 只投 入 电机 车 的制 动系 统 ,事 故状 态 时按 下 “ 行 紧 急停 止 ”按 走 钮 同时投 入 电机车 和焦罐 车 的制动 系统 。 3 电机 、减 速 机 全 部 外 置 ,解 决 了 检 修 和 维 ) 护 保养 困难 的问题 。 35 熄 焦车 ( . 定点 接焦 )
●用技 术‘
表 1 对 应 炉 体 的 工 艺 参数
项 目 鞍 山 焦耐 院 赛 鼎 工 程公 司 北 京 众联 盛 炭 化 室 全 长
/ nm1
炭 化 室 高
/ n T r l1
炭 化 室底 标 高
/Tf1 1 f i
炭 化 室 平 均 宽
/ m m
锥 度 2 0 2 0 2 0
管 导 烟 车
7 8 0 7
0
20设 计 院 的参 数 本
托辊 ,既可以保证托煤板的运行方 向,又可 以减轻 托煤板与衬板的磨损 ,提高两者的使用寿命 :整体 托 煤板解 决 了双层 结构 易产生 冷热 交替 开裂 的潜 在 问题 :煤槽侧壁采用不锈钢复合板制造 ,并设置 自
动 清扫装 置 ,利用 后挡 板 的前 后运 动 , 自动 清扫 煤 槽 侧壁 上 的粘煤 ,减轻 工人 的劳 动强度 :设 置炉 头
55米捣固型焦炉天然气烘炉方案
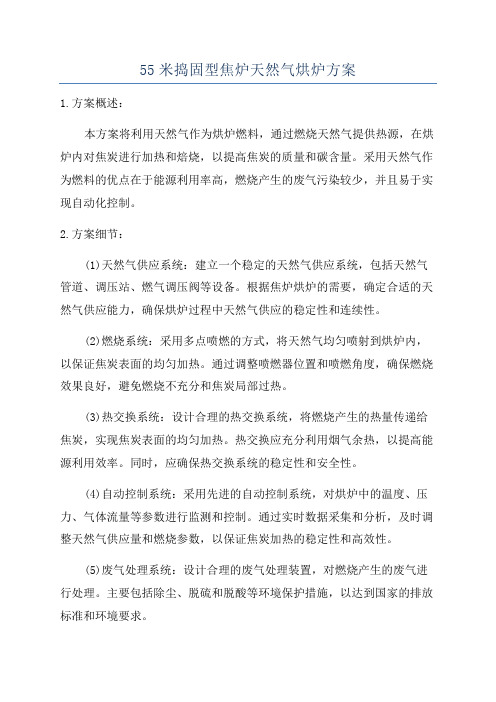
55米捣固型焦炉天然气烘炉方案1.方案概述:本方案将利用天然气作为烘炉燃料,通过燃烧天然气提供热源,在烘炉内对焦炭进行加热和焙烧,以提高焦炭的质量和碳含量。
采用天然气作为燃料的优点在于能源利用率高,燃烧产生的废气污染较少,并且易于实现自动化控制。
2.方案细节:(1)天然气供应系统:建立一个稳定的天然气供应系统,包括天然气管道、调压站、燃气调压阀等设备。
根据焦炉烘炉的需要,确定合适的天然气供应能力,确保烘炉过程中天然气供应的稳定性和连续性。
(2)燃烧系统:采用多点喷燃的方式,将天然气均匀喷射到烘炉内,以保证焦炭表面的均匀加热。
通过调整喷燃器位置和喷燃角度,确保燃烧效果良好,避免燃烧不充分和焦炭局部过热。
(3)热交换系统:设计合理的热交换系统,将燃烧产生的热量传递给焦炭,实现焦炭表面的均匀加热。
热交换应充分利用烟气余热,以提高能源利用效率。
同时,应确保热交换系统的稳定性和安全性。
(4)自动控制系统:采用先进的自动控制系统,对烘炉中的温度、压力、气体流量等参数进行监测和控制。
通过实时数据采集和分析,及时调整天然气供应量和燃烧参数,以保证焦炭加热的稳定性和高效性。
(5)废气处理系统:设计合理的废气处理装置,对燃烧产生的废气进行处理。
主要包括除尘、脱硫和脱酸等环境保护措施,以达到国家的排放标准和环境要求。
3.环保效益:相比于传统的焦炉烘炉方案,天然气烘炉具有显著的环保优势。
天然气燃烧过程中产生的废气中不含硫、氮等有害物质,废气排放量低,对大气环境的污染小。
同时,采用多点喷燃的方式,可以有效控制燃烧过程中的氧化性区域,降低焦炭的氧化损失,进一步降低二氧化碳的排放量。
4.能效提升:利用天然气作为燃料可以提高焦炉的能效。
天然气燃烧产生的热量传递效率高,可以有效提高焦炭的加热速度和加热均匀性。
此外,废气热能的回收利用也可以提高能源的利用效率。
总结起来,基于天然气的55米捣固型焦炉烘炉方案具有环保性好、能效高的优势。
5.5m炭化室捣固焦炉砌筑施工工法(2)

5.5m炭化室捣固焦炉砌筑施工工法一、前言5.5m炭化室捣固焦炉砌筑施工工法是一种用于炭化室捣固焦炉的砌筑施工工法。
通过对该工法的介绍,将详细介绍其特点、适用范围、工艺原理、施工工艺、劳动组织、机具设备、质量控制、安全措施、经济技术分析以及工程实例。
二、工法特点5.5m炭化室捣固焦炉砌筑施工工法具有以下特点:1. 施工工艺简单:该工法采用简单的施工工艺,易于掌握和操作。
2. 施工效率高:通过合理的施工流程和技术措施,能够提高施工效率,节省时间和人力。
3. 施工质量可靠:工法在实践中得到验证,具有可靠性和稳定性,能够保证施工质量。
4. 经济性好:该工法采用的机具设备简单,成本较低,能够满足工程要求的同时,节约成本。
三、适应范围5.5m炭化室捣固焦炉砌筑施工工法适用于炭化室捣固焦炉的砌筑施工,可以广泛应用于冶金、化工、能源等行业。
四、工艺原理该工法的工艺原理基于以下几个方面的联系和技术措施:1. 选择合适的砂浆配合比:根据炭化室捣固焦炉的使用环境和要求,选择合适的砂浆配合比,以确保砌筑后的炉体具有一定的强度和耐火性能。
2. 采取合理的砌筑方法:借助合适的砌筑工具和施工技术,确保砌筑过程中的砂浆浇筑均匀、结实可靠。
3. 严格控制砌筑质量:通过控制砌筑每一道的厚度和密实度,以及采取压实措施,保证整个炭化室捣固焦炉的砌筑质量。
4. 合理施工团队组织:通过合理的劳动组织和分工,提高施工效率和质量。
五、施工工艺5.5m炭化室捣固焦炉砌筑施工工艺主要包括以下几个施工阶段:1. 基础准备工作:包括炭化室捣固焦炉基础的清理和处理,确保基础平整、结实。
2. 锚固安装:在基础上安装锚固器具,确保炭化室捣固焦炉与基础牢固连接。
3. 火砖砌筑:按照设计要求,在锚固器具上逐层砌筑炭化室捣固焦炉的砖墙,注重砖墙的垂直度和水平度。
4. 砂浆浇筑:在砖墙砌筑完毕后,使用合适的砂浆进行浇筑,确保整个炭化室捣固焦炉的砌筑均匀、结实。
5. 护坡施工:根据需要,在炭化室捣固焦炉四周进行护坡施工,加强保护和固定炭化室捣固焦炉。
浅谈5.5米捣固焦炉的温度控制

浅谈5.5米捣固焦炉的温度控制发布时间:2022-08-02T00:47:47.700Z 来源:《中国科技信息》2022年33卷3月第6期作者:黄靖[导读] 鉴于捣实焦炉机焦侧气温变化较小,且焦侧温度大于机侧,容易造成机焦侧焦炭的形成质量不佳,黄靖甘肃省嘉峪关市酒泉钢铁宏兴股份有限公司焦化厂 735100摘要:鉴于捣实焦炉机焦侧气温变化较小,且焦侧温度大于机侧,容易造成机焦侧焦炭的形成质量不佳,因此我们就在横排管中采用节流孔板的方式,改善了机焦侧气体流动情况,进而改善机焦侧气温,从而改善了机焦侧的焦炭品质,同时也进行将火落管理和标准温度控制有机的结合,调整了集合并形成所需要的标准温度控制。
关键词:捣固焦炉;温度控制;问题一、引言捣实炼焦工艺流程中,将煤料在焦炉外侧与炭化室长度相似的大铁箱中加以捣实,将捣固后的煤饼从焦炉机侧,经过加煤车送到炭化室内。
煤料经捣实后,其堆密度可以从顶装煤的0.7~0.75t/m3增加至0.95~1.15t/m3,可以增加对煤料的黏附力,但也同时造成捣实焦炉温度的较难[1]。
二、现状分析焦化厂投入以来,5-6焦炉的生产装置故障频频出现,由于系统大修周期短、持续时间长,造成了焦炉的结焦时间不平衡,而且塌煤情况也频频出现,致使炭化房内出现了局部高温,长期易引起锅壁的破裂现象。
在推焦过程中,频频出现焦侧焦炭太热、塌焦,机侧煤焦油熏黑、推焦冒烟,煤焦油品质持续下滑。
三、焦炉烟尘问题及原因分析(一)装煤烟尘逸出原因分析1.集气管压力不稳二台焦炉共四条集气,二台抽气机为变频调压。
因为二个焦炉合用的一个鼓冷机组,装煤除尘工艺中使用了高压氢氧化铵,导致四个集气管的高压变化频率较高且耦合比较剧烈,当喷洒氢氧化铵、拦焦和放煤后,整个集气管的高压振荡更加剧烈,管内气压很快增加到了300~500Pa,从而造成大量荒烟气体不能再被抽进集气管,大部分烟气都从机侧炉头逸出。
2.高压氨水压力不足不稳目前的高压氨泵泵扬程约为506m,由泵至焦炉炉顶约有20m以下的高度和800m以下的管程,通过推算,由于氨水管道阻损力约2.5MPa,所以当氨水到炉顶时压强仅为2.5MPa以下;经检测,在装煤流程中高压氨水开始喷射时,每当开启一个高压氨水喷头,压力就降低了0.6MPa,当三个喷头全部开启,则压力就降低了1.8MPa。
5.5m捣固焦炉结焦时间对焦炭质量的影响

硫分比
S§搭* 0.882 O.884 0.891 0.894 O.895 O.906 0.912 0.9lD5 0.909
3,2结焦时间对焦炭热态强度的髟晦;。,h-, 根据表2的结果,绘制焦炭热态强度麓结焦时
间的变化趋势,见图3-、图4i
’。一≯鼍0、』一一+
y“SLd肘∞M10 CRI CSR
万方数据
2012年11月 第43卷第6期
燃抖与化工
Fuel&Chemical
n优e8嘲
13
配合煤细度( 准温度为1 短到3Ih。
3ram)≥84%,配合煤水分为 320℃,结焦时间从45h逐步缩
由图1、’图2可以看出,随结焦时间的缩短,
10%-12%,配合煤堆密度为1.05-1.13ffm3,焦炉标
配煤质量及焦炭质量结果
焦炭质量
y
高,降低了焦炭的挥发分,使气孔壁材质致密性提
高,焦炭的气孔率减少,裂纹降低,从而提高了焦
炭的耐磨强度栅抗碎强度。:但结焦时间超过32h 后,焦炭中的多数挥发分已随煤气排出。.气孔瘁和
焦炭裂纹已变化不大.・导致焦炭的耐磨强度和抗碎 强度不再有显著的变化。但结焦时间为3丑.5h时, 焦炭的Mm急剧变差。
Influence of coking period to coke quality for
5.Sin stamp-charging battery
Miao Jinfeng
Zhang Shengli‘(Henan Hongkong(Jiyuan)Coking Group Co.Lid.,Jiyuan 454650,China)
.20 O.75 85.5 6.9 .22 25.0 66.7
序号一l 结时以4
5.5米、6米、6.25米捣固焦炉使用情况

建设年产98万吨5.5米×2侧装捣固焦炉,建设周期2007年到2008年11月。
四川省达州钢铁集团有限责任公司
90万吨焦炭项目采用中冶焦耐工程技术有限公司2×45孔5.5米(JNDK55-05F型)复热式捣固焦炉。
攀钢集团成都钢铁有限公司
在广元旺苍县100万吨焦化项目采用化学工业第二设计院2×50孔5.5米(TJL5550D型)捣固焦炉,于2008年6月28日开工建设。
5.5米、6米、6.25米捣固焦炉使用情况
炉型
生产厂家
备注
5.5米捣固焦炉
乌克兰阿尔切夫焦
化厂
1993年投产,炭化室高5.0m捣固焦炉,焦炭供克里
沃罗格钢铁公司特大容积(5000m3)高炉使用
云南云维集团大为制焦有限公司
4×50孔TJL5550-D型,200万吨,已全部投产。化二院设计。
河北唐山中煤旭阳焦化有限公司
德国迪林根中央焦化厂
1984年投产,2×45孔6.25 m捣固焦炉(世界最高的捣固焦)
印度Tatasteel公司
正在建设6.25 m捣固焦炉,150万吨,配套3400m3高炉,预计2008年底投产
昆钢
草铺基地规划采用的是6.25米侧装捣固焦炉(配套高炉为3200 m3)。
莱钢
正和焦耐院联系建设6.25米捣固焦炉
河南豫港(济源)焦化集团有限公司
采用中冶焦耐工程技术有限公司新开发的新型2×55孔碳化室高度为5.5米的捣固焦炉技术,年生产120万吨焦炭,3月20日开工建设。
新疆伊力特煤化工有限责任公司
95万吨/年煤焦化项目,采用中冶焦耐工程技术有限公司2 ×55孔JNDK55-05型捣固焦炉,建设周期2008年4月10日到2009年10月。
河北旭阳焦炉炉型比较新

河北旭阳焦炉炉型比较新河北旭阳焦炉炉型比较通过最近与唐山嘉华6.25m焦炉、营口嘉辰6m焦炉、金牛天铁、鞍钢鲅鱼圈7m焦炉和耐焦研究所的设计人员的沟通,得到以下分析:一、焦炉分析1、jndk55-05规模:2×65孔,130万吨投资:7.3亿元(根据中煤旭阳焦炉投资)优点:1)二期120万吨5.5m捣固焦炉已于2022年投产,具有一定的施工管理经验。
2)部分设施已建成,可与三期配套,如煤场、预粉碎、粉碎配煤系统配套使用。
三)三期工程委托交奈院设计,预付20%的预付款。
如果考虑5.5m炉型,设计时间短,可在一个月内开始施工。
4) 5.5m炉型备件可作为二期的补充。
5)施工工期相对6.25米焦炉较短,预计12个月。
而6.25米约15-18个月。
6)每吨焦炭的投资成本较低。
二期炼焦每吨焦炭投资562元,6.25m焦炉每吨焦炭投资约770元(根据焦乃园至嘉华的数据)。
208元劣势:1)各大机车除熄焦车外均无备用。
2)与6.25m焦炉和7m焦炉相比,单孔焦炭年产量约低2000吨。
2、 jnd6。
25-07规模:2×53孔130万吨(理想建设为4×53孔260万吨)投资:10亿元(两台焦炉,一用一备)优势:1)设备装备水平较高,为同行业捣固炉型的领先水平。
2)捣固煤饼堆密度较5.5米较高,现5.5米焦炉堆密度约为1.17吨/立方米,6.25米焦炉可达到1.25吨/立方米,故焦炭的冷强度上略有提高。
3) jnd6。
25-07捣固焦炉借鉴了德国迪林根6.25m捣固焦炉和印度塔塔4.5m捣固焦炉的生产运行经验,增加了炭化室的锥度,增加了炉墙的极限侧负荷,延长了焦炉的使用寿命,减少了卸焦时对炉墙的损坏。
4)jnd6.25-07型捣固焦炉增加了炭化室铺底砖的厚度,提高铺底砖耐磨性,可以有效延长焦炉铺底砖的使用寿命。
5) jnd6。
25-07捣固焦炉将导烟车的轨道基础放在燃烧室顶部,不仅可以防止砖在炭化室顶部断裂,而且可以减少轨道变形。
5.5 m捣固焦炉设备的性能和结构特点

太原重型机械集团有限公司的上市公司———太原重工股份有限公司(以下简称太原重工)于2007年成功开发出5.5m 捣固焦炉成套设备,到2012年6月已成功生产近百套,分布于黑龙江、新疆、甘肃、内蒙、河北、山东等地,并成功进入印度市场。
5.5m 捣固焦炉设备能够在捣固式焦炉生产中完成捣固煤饼、装煤、出焦、熄焦、烟尘处理等功能,具有环保高效、自控水平高的特点。
结合原有4.3m 捣固焦炉设备、热回收捣固焦炉设备、6m 和7m 顶装焦炉设备运行的情况以及所取得的经验,针对捣固时车辆的稳定性,装入炭化室时煤饼的完整性,装煤、推焦、接焦时产生烟尘的收集和处理,减小操作工人的劳动强度以及车辆的自动化水平等五方面,在5.5m 捣固焦炉设备中做了大量改进。
目前,该设备每年的需求达数十套,具有很好的社会效益和经济效益。
1 5.5m 捣固焦炉设备完成的功能5.5m 捣固焦炉设备适用于年产量100万~150万t 焦化项目,其主要功能包括捣固煤饼、装煤、出焦、熄焦、烟尘处理、炉门清扫、炉框清扫、头尾焦处理等,其每炉理论出焦量为27.2~31.3t。
侧装煤车用来完成洗精煤从煤塔落入装煤机构煤槽、用捣固机将洗精煤捣固成煤饼、用托煤板将煤饼装入炭化室内;推焦车用来完成将成熟焦炭推出炭化室,并在推焦前和送煤饼后启闭焦炉机侧炉门,进行余煤、头尾焦回收;除尘拦焦车用来将推出的成熟焦炭导入熄焦车,并将推焦时产生的烟尘导入地面除尘站,导焦前后启闭焦侧炉门;熄焦车用于盛装1000℃炙热焦炭,并将其运送到熄焦塔下熄焦,送至卸焦位卸焦;导烟车用来完成将装煤时产生的荒煤气及烟尘导入相邻炭化室,防止烟尘逸散。
液压交换机用来完成焦炉煤气、焦炉废气、高炉煤气的交换。
2对应炉体的工艺参数对应炉体的工艺参数见第108页表1。
3各车结构特点3.1侧装煤车1)太原重工生产的侧装煤车有两种形式:第一种为常规的两条轨道运行,第二种为三条轨道运行(山东邹平铁雄属于该类)。
5.5m焦炉与4.3M焦炉的对比
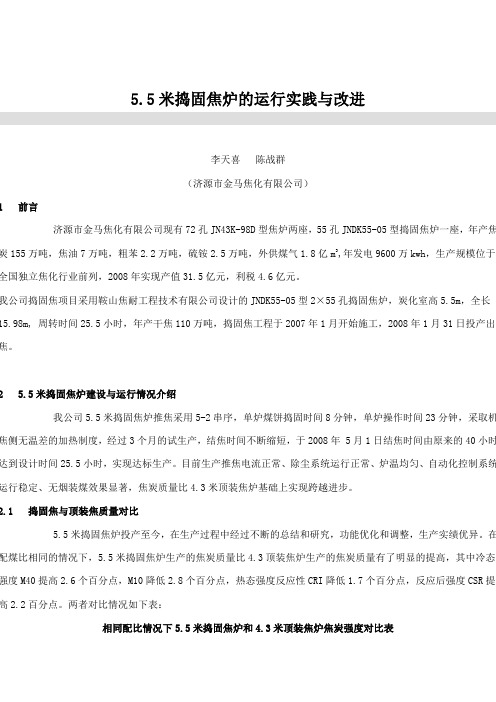
5.5米捣固焦炉的运行实践与改进李天喜陈战群(济源市金马焦化有限公司)1 前言济源市金马焦化有限公司现有72孔JN43K-98D型焦炉两座,55孔JNDK55-05型捣固焦炉一座,年产焦炭155万吨,焦油7万吨,粗苯2.2万吨,硫铵2.5万吨,外供煤气1.8亿m3,年发电9600万kwh,生产规模位于全国独立焦化行业前列,2008年实现产值31.5亿元,利税4.6亿元。
我公司捣固焦项目采用鞍山焦耐工程技术有限公司设计的JNDK55-05型2×55孔捣固焦炉,炭化室高5.5m,全长15.98m, 周转时间25.5小时,年产干焦110万吨,捣固焦工程于2007年1月开始施工,2008年1月31日投产出焦。
2 5.5米捣固焦炉建设与运行情况介绍我公司5.5米捣固焦炉推焦采用5-2串序,单炉煤饼捣固时间8分钟,单炉操作时间23分钟,采取机焦侧无温差的加热制度,经过3个月的试生产,结焦时间不断缩短,于2008年 5月1日结焦时间由原来的40小时达到设计时间25.5小时,实现达标生产。
目前生产推焦电流正常、除尘系统运行正常、炉温均匀、自动化控制系统运行稳定、无烟装煤效果显著,焦炭质量比4.3米顶装焦炉基础上实现跨越进步。
2.1 捣固焦与顶装焦质量对比5.5米捣固焦炉投产至今,在生产过程中经过不断的总结和研究,功能优化和调整,生产实绩优异。
在配煤比相同的情况下,5.5米捣固焦炉生产的焦炭质量比4.3顶装焦炉生产的焦炭质量有了明显的提高,其中冷态强度M40提高2.6个百分点,M10降低2.8个百分点,热态强度反应性CRI降低1.7个百分点,反应后强度CSR提高2.2百分点。
两者对比情况如下表:相同配比情况下5.5米捣固焦炉和4.3米顶装焦炉焦炭强度对比表2.2 5.5米捣固焦炉的配煤优势在保证用户需求的焦炭质量的情况下,为发挥5.5米捣固焦炉的优势,经过多次的小焦炉试验和生产实践,摸索出了一套5.5米捣固焦炉的配煤方案,与4.3米顶装焦炉相比,捣固配煤少用10%左右的主焦煤,多用5%的瘦煤和5%得1/3焦煤。
捣固焦参与市场竞争的优势、劣势及展望

捣固焦参与市场竞争的优势、劣势及展望王在葆对于一个新建的焦化项目,合理选择焦炉炉型是项目的关键。
影响焦炉炉型选择的因素主要有国家产业政策、业主性质、地区煤源、规模与投资等因素。
目前室式炼焦炉就其装煤工艺而言可分为两大类:顶装焦炉和捣固侧装焦炉。
顶装焦炉发展时间长,技术及装备成熟,是我国乃至世界焦炉的主流。
捣固侧装焦炉是最近10年在我国迅速发展起来的,是伴随着我国钢铁工业的大发展而成长起来的,具有明显的中国特色,其发展趋势不可小看。
以下结合××公司的实际情况,就捣固焦参与市场竞争的优势和劣势进行初步评估,并对捣固焦的未来市场走向予以展望。
一、捣固焦的发展概况捣固焦起源于德国,至今已有128年的历史。
我国使用捣固焦炉较早的厂家有:淮南化肥厂、镇江焦化厂、大连化工厂和北台钢铁厂焦化分厂等。
捣固焦炉的炭化室高度从开始的2.8m、3.2m和3.8m逐步向大型化方向发展:●2002年8月,第一座炭化室高4.3m的捣固焦炉在山西临汾同世达焦化厂成功投产(2×50孔)。
●2006年12月,第一座炭化室高5.5m的捣固焦炉在云南曲靖大维焦化厂成功投产(4×55孔)。
●2010年4月,第一座炭化室高6m的捣固焦炉在河南中鸿煤化有限公司成功投产(2×60孔)。
●2009年3月,第一座炭化室高6.25m的捣固焦炉在河北唐山佳华煤化工公司成功投产(4×46孔)。
十年来,随着钢铁工业的快速发展和优质炼焦煤资源的供应紧张,催化加速了我国捣固焦炉的发展。
目前已投产的捣固焦炉已超过400座,捣固焦炉产能在1亿吨左右,这些捣固焦炉(约占97%左右)基本上都是建在独立焦化厂,主要分布在山西、河南、河北和山东以及内蒙宁夏等省区。
捣固焦炭产能已占我国焦炭总产能的30%左右,主要应用于1000m3 以下的高炉以及化工和铸造等方面。
我国1000m3 以下的高炉数量众多,经过几轮的淘汰目前仍然有大约1150座,这些中小高炉主要对焦炭的冷强度M40和M10有一定的要求,对焦炭的热性质(CRI和CSR)没有具体要求,这为捣固焦提供了极为有利的市场,使捣固焦冷强度高和配煤成本低的两大优势得到充分发挥。
浅谈5.5米捣固焦炉烟囱烟气NOx超低排放达标前端控制措施

浅谈5.5米捣固焦炉烟囱烟气NOx超低排放达标前端控制措施目前国内炭化室高度4.3米捣固焦炉正在逐步淘汰,生产捣固焦炭的主力炉型有炭化室高度5.5米、6.0米、6.25米和6.78米等捣固焦炉。
正在生产的5.5米捣固焦炉有多家设计单位所做的设计版本,有炭化室全长为15.98米(冷态),立火道个数32个;炭化室全长为14.08米(冷态),立火道个数28个,有炭化室平均宽554、550、520和500mm,炉体结构有复热式和单热式(宽蓄热室)两种,捣固煤饼体积均为>35立方米。
由于5.5米捣固焦炉炉体结构仅有燃烧室立火道废气循环低NOx燃烧单一技术(考虑到在焦炉延长结焦时间时,炉头温度偏低,加热煤气交换时,可能会出现废气循环短路问题,故机、焦侧炉头边立火道大都末设有废气循环孔,即没有使用废气循环低NOx燃烧技术,下同),而6.0米及以上捣固焦炉炉体结构大都采用燃烧室立火道废气循环+分段加热低NOx燃烧组合技术,一般来讲,在相同工况生产条件下,加热燃烧生成排放的NOx浓度,5.5米捣固焦炉要相对高得多。
笔者通信调研了多家煤焦化企业正在生产的如上所述的捣固焦炉炉型,相同用焦炉煤气作加热燃料,燃烧生成排放的NOx浓度,通常情况下6米及以上的捣固焦炉为400~600mg/立方米(烟气中基准含氧8%,下同);5.5米捣固焦炉为700~1000mg/立方米(这也有与加热用焦炉煤气质量如HCN和氨含量较高、炉体状况、焦炉加热制度、工艺操作控制等因素有关)。
当前有数省、市、自治区发布地标或方案要求炼焦化学工业的焦炉烟囱烟气中NOx浓度超低排放标准限值为100~130mg/立方米(如河南、河北等),已有焦炉烟囱烟气NOx后端治理脱硝处理装置的脱除效率一般在70~85%,本文取NOx超低排放限值为130mg/立方米;脱硝效率暂按取值80%计,测算得出焦炉加热燃烧生成排放的NOx浓度不应超过650mg/立方米,否则不能满足地标NOx超低排放限值的要求(烟气脱硝装置改造或新建提升脱除效率例外)。
浅谈捣固炼焦

内容摘要:我国焦炭市场自2006年开始转暖,焦化企业扭亏为盈,国内焦煤价格及运输价格持续走高,炼焦企业利润空间有限,优化配煤方案,降低原煤成本,提高焦炭声生产效率,提高焦炭质量成了企业成了企业在激烈竞争中获得更大利润的基本任务。
各国都在改进现有炼焦工艺的同时不断探索新的工艺,而捣鼓炼焦作为一种经济适用性,现已成为一成熟的炼焦工艺,被国能外广泛采用。
捣鼓炼焦的特点是:配煤时可以多配备高挥发的分、弱粘的炼焦煤,而且可以提高焦炭质量。
本文主要论述为提高捣鼓式焦炉的焦炭质量如何结合实际采取延长捣鼓时间等措施来提高焦炭质量。
关键词:捣鼓炼焦;捣鼓炼焦特点;焦炭质量;捣鼓时间;一、捣鼓炼焦1、我国捣鼓炼焦的发展历程我国第一批近代炼焦炉于1919年在鞍钢建成投产,由于战乱,遭到破坏。
1949年~1959年我国新建、改建24座、1239孔炼焦炉。
1958年,我国自行设计和建设的第一座58型焦炉在北京焦化厂一次投产成功。
1970年,炭化室高3.8m的捣鼓焦炉建成的捣鼓焦炉建成投产。
1995年,青岛煤气厂使用引进德国摩擦传动、薄层给煤、连续捣打的捣固机。
2005年8月,景德镇焦化煤气总厂将炭化室高4.3m、宽450mm的80型顶装焦炉改造成捣固焦炉。
2006年2月邯郸裕泰实业有限公司将炭化室高4.3米、宽500mm的顶装焦炉改造成捣固焦炉,拉开了我国4.3m顶装焦炉改造成捣固焦炉的序幕。
2006年底,5.5m的捣固焦炉在云南曲靖建成投产,在全国掀起了建设5.5m捣固焦炉的热潮。
2007年6月,中冶焦耐公司总承包了河北唐山市佳华公司的炭化室高6.25m世界最高的捣固焦炉的建设,预计2008年8月投产,这标致着我国大型捣固焦炉技术达到了国际先进水平。
2007年9月,中冶焦耐公司中标建设印度塔塔钢铁公司5m的捣固焦炉,标致着我国大型捣固焦炉设计正式走向国际市场。
同期,涟源钢铁公司和攀枝花钢铁公司也决定新建捣固焦炉,标致着我国大中型钢铁企业开始接受和采用捣固炼焦技术。
5.5米捣固型焦炉天然气烘炉方案

目录第一章1号焦炉烘炉方案简述第二章烘炉气体流程第三章焦炉烘炉图表制定第四章焦炉烘炉前必须完成的主要工作项目第五章烘炉点火前的准备工作第六章焦炉烘炉组织体系与人员配置第七章烘炉点火第八章烘炉管理第九章烘炉热修工作第十章热态工程施工项目执行时间表第十一章烘炉材料表第十二章烘炉岗位职责和烘炉操作要点第十三章烘炉安全注意事项第一章1号焦炉烘炉方案简述XX公司1×65孔ZHJL5552D型焦炉,由北京XX公司设计,其特点为:双联火道、废气循环、焦炉煤气下喷、空气侧入.炭化室长15.98米,宽520mm,高5.5米。
烘炉就是把已经安装了护炉设备的冷态焦炉由常温逐步加热到能够装煤的温度.烘炉是焦炉投产前重要而复杂的工艺过程,其质量的优劣对焦炉的寿命有着至关重要的影响。
因此对烘炉工作必须给予高度重视。
烘炉前制定烘炉升温曲线,严格按计划升温,保持焦炉砌体的严密性。
烘炉干燥阶段的基本原则是要在保障灰缝严密性和砌体完整性的前提下有效地排出水分。
干燥期(100℃)前选定15 天,100℃后的升温期的确定是根据厂方提供的焦炉硅砖膨胀率及采用最大日安全膨胀率(0.030﹪-0.035﹪)计算而得,经计算,升温期为59.5天,烘炉时间共计74.5天(天然气热值是焦炉煤气的三陪多,900度转正常加热,更换孔板等工作相当麻烦,而且天然气和煤气不宜混合,建议直接升温到装煤开工,启动风机,煤气回炉改正常加热,然后停用天然气并拆除天然气管道设备)。
本方案采用天然气及带炉门烘炉,炉温达到850℃-900℃后开始转为正常加热.由于本方案采用气体燃料带炉门烘炉。
因此采用不砌外部小灶、不砌封墙、装上炉门、在炉门下部专设烘炉孔引入天然气进行烘炉。
从常温到转为正常加热前,使用高精度的热电偶及计算机系统进行温度检测和烘炉升温管理.转正常加热后,采用高温计测温并拆除烘炉测温设备。
为顺利完成烘炉工作,参加烘炉人员应事先进行岗位培训和安全教育。
5.5m捣固焦炉的优势

5.5米捣固型炼焦炉的优势自上世纪80年代末我国发展捣固炼焦技术以来,由于该项技术能提高焦炭的冷态强度和反应后强度,增加30%焦炉生产率,大幅度降低焦炭生产成本,增加企业利润。
特别是采用捣固工艺技术可以节省不可再生的优质焦煤资源,是焦化行业发展的主要方向。
焦炉大型化是上世纪70年代以来世界炼焦技术发展的总趋势。
三十多年来顶装煤焦炉炭化室的高度已由4.0m增高至8.0m,炭化室的宽度由407mm增至600mm以上,单孔容积已由20m3增大到90m3以上。
焦炉超大型化能带来生产效率高,节省能源,万吨规模占地面积小,焦炭质量好,其环境污染总量减小,年产万吨焦炭投资低的综合效益。
一.焦炉炉体的基本结构ZHJL 5552D型焦炉是双联火道,废气循环,下喷,复热式大型捣固焦炉。
1 炉体的主要尺寸(冷态)及工艺技术参数:炭化室全长:15980mm,有效长:15140mm,炭化室全高:5500mm,有效高:5200mm,炭化室平均宽:520mm,锥度:20mm,捣固煤饼尺寸:L×B×H=15000×470×5200mm,精煤堆比重(干)1.0t/ m3,煤饼重量:36.66t ,焦炉周转时间:23h,炭化室中心距:1350mm,立火道中心距480mm,立火道个数32,炉顶厚度:1200~1250mm,炭化室炉墙厚度:90mm,立火道隔墙厚度:151mm,斜道部分高度:825mm,蓄热室高度:3700mm,宽度:415mm,主墙厚:290mm,单墙厚:230mm蓄热室格子砖高度:2750mm,层数:22。
2 焦炉各部位构成2.1 焦炉基础砌砖:焦炉基础砌砖共四层,总厚度为240mm。
采用强度大、隔热效率高的漂珠砖和高强隔热砖砌筑。
降低了焦炉顶板的温度,改善了操作环境,减少了热量损失。
2.2 蓄热室蓄热室高度3700mm,主墙为37层砌筑。
小烟道截面为273×650mm,底部设有清扫孔。
捣固炼焦技术

重视应用捣固炼焦技术2009-12-10所谓捣固炼焦技术(StampCokingTechnology,简称SCT),是一种能够通过增加配煤中高挥发分、弱粘结性或不粘结性的低价煤的含量来扩大炼焦煤资源的方法。
其优点如下:(1)提高焦炭质量和节约资源:煤料经捣固后,堆密度可提高到0.95~1.15t/m3,煤粒间接触致密,比常规顶装煤煤粒子间的间距缩小28%~33%,所得焦炭的致密程度明显改善,有明显的改善焦炭质量的效果。
同时,在保证同样焦炭质量的前提下,可多用20%~30%左右的高挥发分弱粘煤及部分非粘结煤,扩大炼焦用煤源,降低对优质炼焦用煤的依赖度和提升焦炭生产的成本优势。
(2)经济效益显著:尽管捣固焦炉的捣固机和装煤车的投资高于顶装煤的机械费用,但是捣固煤饼的堆积密度比顶装煤高1/3,故相同生产规模的焦炉,捣固焦炉可以减少炭化室的孔数或炭化室容积,因此,捣固焦炉的总投资并不比顶装焦炉高。
此外,捣固炼焦工艺可以比顶装煤炼焦工艺配入更多的高挥发分或弱粘结性的低价煤,同时增加石油焦及焦粉的配入量,减少焦煤用量,直接降低了焦炭的生产成本,并使捣固焦炉焦炭质量提高,可相应提高销售价格,增加销售收入。
(3)减少环境污染:与顶装焦炉相比较,在产量相同的情况下,捣固焦炉具有减少出焦次数、减少机械磨损、降低劳动强度、改善操作环境和减少无组织排放的优点;装煤的污染物排放量减少90%;工艺除尘效率高,减少了环境污染。
捣固炼焦工艺由于具有诸多优点,已在许多国家大量采用,特别是在缺乏强粘结性煤资源的国家。
原苏联从1989年开始将一个顶装焦炉改造为捣固炼焦炉以后,开始在其高挥发分煤矿地区采用捣固炼焦工艺。
波兰由于其国内挥发分高的煤源比较多,适合炼焦的煤源不太丰富,因此也大量采用捣固工艺。
目前,世界上比较先进的捣固技术是由德国开发的萨尔堡捣固技术。
这种技术应用的较为广泛,我国青岛管道燃气公司采用的就是这种技术。
德国萨尔堡矿业公司开发的这种新一代捣固技术,采用薄层连续给料代替传统的分层捣固法,捣固时间由12min左右缩短到4min 左右,提高了捣固机效率,并有效控制了煤饼装炉时的烟尘。
- 1、下载文档前请自行甄别文档内容的完整性,平台不提供额外的编辑、内容补充、找答案等附加服务。
- 2、"仅部分预览"的文档,不可在线预览部分如存在完整性等问题,可反馈申请退款(可完整预览的文档不适用该条件!)。
- 3、如文档侵犯您的权益,请联系客服反馈,我们会尽快为您处理(人工客服工作时间:9:00-18:30)。
5.5米捣固型炼焦炉的优势自上世纪80年代末我国发展捣固炼焦技术以来,由于该项技术能提高焦炭的冷态强度和反应后强度,增加30%焦炉生产率,大幅度降低焦炭生产成本,增加企业利润。
特别是采用捣固工艺技术可以节省不可再生的优质焦煤资源,是焦化行业发展的主要方向。
焦炉大型化是上世纪70年代以来世界炼焦技术发展的总趋势。
三十多年来顶装煤焦炉炭化室的高度已由4.0m增高至8.0m,炭化室的宽度由407mm增至600mm以上,单孔容积已由20m3增大到90m3以上。
焦炉超大型化能带来生产效率高,节省能源,万吨规模占地面积小,焦炭质量好,其环境污染总量减小,年产万吨焦炭投资低的综合效益。
一.焦炉炉体的基本结构ZHJL 5552D型焦炉是双联火道,废气循环,下喷,复热式大型捣固焦炉。
1 炉体的主要尺寸(冷态)及工艺技术参数:炭化室全长:15980mm,有效长:15140mm,炭化室全高:5500mm,有效高:5200mm,炭化室平均宽:520mm,锥度:20mm,捣固煤饼尺寸:L×B×H=15000×470×5200mm,精煤堆比重(干)1.0t/ m3,煤饼重量:36.66t ,焦炉周转时间:23h,炭化室中心距:1350mm,立火道中心距480mm,立火道个数32,炉顶厚度:1200~1250mm,炭化室炉墙厚度:90mm,立火道隔墙厚度:151mm,斜道部分高度:825mm,蓄热室高度:3700mm,宽度:415mm,主墙厚:290mm,单墙厚:230mm蓄热室格子砖高度:2750mm,层数:22。
2 焦炉各部位构成2.1 焦炉基础砌砖:焦炉基础砌砖共四层,总厚度为240mm。
采用强度大、隔热效率高的漂珠砖和高强隔热砖砌筑。
降低了焦炉顶板的温度,改善了操作环境,减少了热量损失。
2.2 蓄热室蓄热室高度3700mm,主墙为37层砌筑。
小烟道截面为273×650mm,底部设有清扫孔。
采用扩散式箅子砖,每侧分7段。
蓄热室主墙采用三条沟舌,单墙采用一条沟舌。
蓄热室采用有单、主墙复热式结构砌筑比单蓄热室结构承载的强度要好。
封墙厚399mm,墙内设计有30mm厚硅酸钙隔热板新型高效保温材料,外封墙设计70mm厚的隔热和密封效果好的硅酸盐抹面,减少了热损失,改善了焦炉操作环境。
采用12孔格子砖,每块格子砖的蓄热面积为0.43107m2,水力直径为0.0273m。
2.3 斜道区斜道区部分总高825mm,共计8层。
在斜道一层和二层部位设蓄热室测温孔。
长短斜道的倾角均大于30°。
炉头斜道出口断面比中部要大50%。
2.4 炭化室——燃烧室炭化室墙厚90mm,采用“宝塔”形结构和残余石英含量低的优质硅砖砌筑。
比原4.3m焦炉有重大改进的是在立火道隔墙上采用了带有沟舌的异型砖砌筑。
在循环孔和跨越孔周围采用了带有沟舌结构的硅砖砌筑,大大增强了燃烧室的结构强度和炉墙的整体性,防止砖体松动和掉砖。
机焦两侧炉头火道断面为中间火道断面的85%,解决了炉头火道温度较低的问题,使炭化室内焦饼温度得以均匀。
焦炉加热水平为800mm,可使焦饼上下同时成熟,减少炉顶空间石墨生成。
燃烧室采用废气循环和加高焦炉煤气灯头的结构,保证了用焦炉煤气加热时炭化室高向加热的均匀性。
此外,因设计有废气循环可以降低废气中的氮氧化物含量,减少了对大气的污染;而当焦炉延长结焦时间操作时,由于用焦炉煤气加热采用了高灯头,因此不会造成短路现象出现。
燃烧室盖顶大砖采取在一对火道内设拱顶的结构,使上面的负荷归集在立火道隔墙上,可以承受住炉顶导烟车的机械震动而不易损坏。
2.5 炉顶炉顶区总高度为1200—1250 mm,从焦炉中心至机、焦两侧各有50mm的坡度,便于雨水排除。
炭化室盖顶砖采用硅砖可大大减少因砖的材质问题而产生的裂纹、断裂。
采用强度大,隔热效率高的漂珠砖和高强隔热砖代替传统焦炉采用红机砖和普通隔热砖,可减少炉顶散热、变形,同时也方便了焦炉砌筑。
二.焦炉热工计算2.1蓄热室计算2.1.1整个计算和数据是以高炉煤气为基准进行的。
蓄热室高向温度分布:2.1.2 格子砖蓄热面积及水力直径一块格子砖的蓄热面积 0.43107 m 2 焦侧单个蓄热室一层格子砖的蓄热面积 25.26101 m 2 焦侧单个蓄热室一层格子砖总空隙面积 1.496 m 2 焦侧单个蓄热室一层格子砖的总周长长度 219.7388 m 格子砖水力直径 0.0273m 2.1.3 煤气蓄热室热平衡:预热后高炉温度为 1077°C 2.1.4 一个煤气蓄热室的换热面积及格子砖层数:格子砖高度(设计值) 2750mm 格子砖层数(设计值) 22 换热面积(设计值) 555.74 m 2 计算需要换热面积412.95 m 2 计算需要格子砖层数 17 每小时换热1000Kcal 的换热面积 0.79m 2 2.2 炉体水力计算2.2.1焦炉内加热系统各部位阻力及浮力: mmH 2O 柱2.2.2 焦炉各部位压力mmH2O柱2.2.3 烟囱高度计算小烟道出口中心压力-14.807 mmH2O从交换开闭口至烟囱根部总阻力16.101 mmH2O从交换开闭口至烟囱根部总浮力-2.543 mmH2O烟囱阻力损耗 3.043 mmH2O备用烟囱吸力 5.00 mmH2O计算烟囱吸力41.494mmH2O计算烟囱高度111m三 5.5m捣固型焦炉配套机械根据5.5m 捣固焦炉的要求和特点,我公司与太原重机厂密切合作,在焦炉配套车辆方面做了大量的试验研究工作,开发出5.5m 捣固焦炉的配套车辆,这是集成了4.3m 捣固焦炉与6m 顶装煤焦炉相关机械的优点。
配套机械包括捣固装煤车、推焦车、除尘拦焦车、炉顶导烟车、电机车、熄焦车、21锤移动捣固机、30锤固定捣固机、摇动给料机等。
在开发配套机械时对捣固煤饼做了重锤试验。
捣固锤采用了480、500、520、540 kg /锤四种重锤实验。
锤重500 kg/锤,捣固时间6分钟,配合煤水分8.8%,获得煤饼堆比重1.16t/m3的效果,煤饼进行装煤移动不塌煤。
试验结果列表如下:通过以上试验考虑到540 kg/锤对装煤车的冲击力太大,不推荐使用。
推荐使用500,520kg /锤。
配套机械制作时采用捣固锤重量为500kg/锤,冲击行程400mm ,捣固频率67—72次/min,煤饼捣固成时间约6分钟。
装煤出焦时除尘方式为炉顶导烟车和除尘拦焦车与地面站相配合。
各车辆的操作时间四生产规模的确定与布置4.1 焦炉孔数的确定两座焦炉为一组,设一个熄焦塔,配备一套电机车和熄焦车,车辆操作时间最紧的为电机车与熄焦车,每操作一炉平均用时9.5min。
每一个周转时间内车辆、设备检修时间为两小时,则每一个周转时间内最大操作孔数为132孔。
再结合其他车辆的运行情况,每组焦炉的规模确定为2×65孔为宜年产全焦(干)约为130—135万吨。
4.2 炼焦车间平面布置炼焦车间由焦炉、煤塔、炉间台、炉端台、炉门修理站、推焦杆更换站、出焦地面除尘站、湿法熄焦塔、凉焦台、粉焦沉淀池、湿法熄焦泵房、烟囱及配套的焦炉机械组成。
同时布置有干法熄焦装置。
4.3设计开发中采用的节能,环保措施:4.3.1焦炉装煤过程产生的大量烟尘,采用炉顶导烟车收集烟尘,待焚烧后废气送到地面站除尘,达标后排放,有效减少烟尘及其它排放的污染物,使装煤烟尘去除率达标到90%以上。
装煤车增设装煤集尘罩,收集装煤时的烟尘,导烟车增设与装煤车集尘罩的对接机构,把集尘罩收集的烟尘抽入导烟车一起焚烧,彻底清除装煤时机侧炉门处烟尘外泄。
4.3.2 出焦采用地面站除尘工艺,除尘效率高,可大量减少环境污染。
4.3.3焦炉炉门采用弹簧炉门,增大炉门严密性,显著减少炉门无组织排放,污染物的排放量大大减少。
4.3.4 采用6.0m顶装煤焦炉采用的先进合理的炉门自动清扫装置,清扫效果好,减轻了工人的劳动强度,降低了炉门的泄漏率,加快了清扫速度。
4.3.5 荒煤气事故放散采用自动放散点火装置,保证在事故状态下不外排荒煤气。
4.3.6 上升管盖采用水封盖,减少污染物排放,使烟气中污染物明显减少。
4.3.7 焦炉蓄热室封墙、炉门衬砖、上升管衬砖采用特殊的保温隔热材料,减少散热损失,提高热工效率,改善操作环境。
4.3.8采用计算机集散系统,提高焦炉操作的自控水平及热效率,降低能源消耗。
焦炉加热采用自动加热技术,使焦炉加热随装煤条件(装煤量、装煤水分、堆密度等),操作条件(结焦时间、火道温度、焦饼温度、炉顶温度等)和加热煤气特性(煤气热值、温度、压力、密度)等的变化而自动进行调节,实现焦炉加热最优化控制,提高劳动生产率,稳定焦炭质量,降低焦炭单位能耗。
4.3.9 熄焦塔加高至55m,采用三层折板除尘,除尘效率达80%以上以改善环境。
4.3.10 采用较先进的二次熄焦技术,使焦炭水分可减少20—40%,吨焦的耗水量随之减少。
4.3.11设计中予留干熄焦的位置,采用较先进的节能减排的干熄焦技术,可大量回收焦炭显热,有益于环境保护,同时有利于焦炭质量指标的提高。
4.3.12 对焦炉的集气管压力调节,可根据业主要求,推荐采用国内较先进的模糊自动调节技术,有效的保障了焦炉压力的稳定,减少了跑冒现象,保障焦炉操作的稳定性,使焦炉操作强度大为降低。
五 5.5m捣固型焦炉的优势:捣固型炼焦装炉煤堆密度可比顶装焦炉装炉煤堆密度大35%到41%,即由0.74t / m 3提高到1.0 t / m 3—1.05 t / m 3。
在保证焦炭质量略好或相同的情况下,捣固型焦炉比顶装煤焦炉可多配入近20—30%的弱粘结性煤或高挥发分煤。
这就扩大了炼焦煤资源的范围,降低了炼焦配合煤的单位成本。
同时与顶装煤炼焦相比可提高焦炭的冷态强度和反应后强度及焦炭的筛分粒度。
德国迪林根萨尔中心焦化厂采用54%—58%的高挥发分配煤曾炼制出反应后强度(CSR)62.2%,反应性(CRI)27.6%的焦炭供高炉炼铁。
这是捣固型焦炉生产焦炭的共同优势。
但5.5m捣固型焦炉比4.3m捣固型焦炉更有显著的特点:5.1 5.5m 与4.3m 捣固型焦炉的不同点,突出的特点是将炭化室炉墙由100mm 减薄至90mm,炭化室宽度由500mm 增加到520mm ,炭化室锥度为20mm 。
炭化室一次装干煤量由24.26t /孔增加到36.66t /孔,每孔装煤量增加51%,每孔焦炭产出量增加48%。
炭化室炉墙减薄可获得最大的热流速率,炭化室加宽焦炉的结焦速度减缓,有利于改善焦炭的均匀性,提高块焦率。
同时捣固成的煤饼稳固性更好。
煤料的膨胀压力与结焦速度的平方成正比,结焦速度减缓,膨胀压力减小,结焦时间加长,焦饼的收缩值增加,焦饼与炭化室墙之间的间隙加大,这可降低推焦力使炉墙所承载的机械荷载减小,从而有利于延长炉体寿命。