生产工艺流程表(1)
A1半导体工艺生产流程(1)

Al半导体工艺生产流程一、洁净室通常的机械加工是不露要洁净室(dean room)的,由于加工分辨率在数十微米以上,远比日常环境的微尘颗粒为大。
但进入半导体组件或者微细加工的世界,空间单位都是以微米计算,因此微尘颗粒沾附在制作半导体组件的晶圆上,便有可能影响到其上精密导线布局的样式,造成电性短路或者断路的严重后果。
为此,所有半导体制程设备,都务必安置在隔绝粉尘进入的密闭空间中,这就是洁净室的来由。
洁净室的洁净等级,有一公认的标准,以class 10为例,意谓在单位立方英I尺的洁净室空间内,平均只有粒径0.5 微米以上的粉尘10粒。
因此class后头数字越小,洁净度越佳,当然其造价也越昂贵(参见图2-1)。
为营造洁净室的环境,有专业的建造厂家,及其有关的技术与使用管理办法如下:1、内部要保持大于一大气压的环境,以确保粉尘只出不进。
因此需要大型鼓风机,将经滤网的空气源源不绝地打入洁净室中。
2、为保持温度与湿度的恒定,大型空调设备须搭配于前述之鼓风加压系统中。
换言之,鼓风机加压多久,冷气空调也开多久。
3、所有气流方向均由上往下为主,尽量减少突兀之室内空间设计或者机台摆放调配,使粉尘在洁净室内回旋停滞的机会与时间减至最低程度。
4、所有建材均以不易产生静电吸附的材质为主。
5、所有人事物进出,都务必通过空气吹浴(air shower)的程序,将表面粉尘先行去除。
6、人体及衣物的毛屑是一项要紧粉尘来源,为此务必严格要求进出使用人员穿戴无尘衣,除了眼睛部位外, 均需与外界隔绝接触(在次微米制程技术的工厂内,工作人员几乎穿戴得像航天员一样。
)当然,化妆是在禁绝之内,铅笔等也禁止使用。
7、除了空气外,水的使用也只能限用去离子水(DlWater,de-ionized water)。
一则防止水中粉粒污染晶圆,二则防止水中重金属离子,如钾、钠离子污染金氧半(MOS)晶体管结构之带电载子信道(CarrierchanneI), 影响半导体组件的工作特性。
水泥熟料生产工艺流程(一)

水泥熟料生产工艺流程(一)水泥熟料生产工艺1. 概述水泥熟料是生产水泥的主要原料,其生产工艺包括多个流程,涉及到破碎、混合、配料、烧结、冷却等多个环节。
2. 破碎破碎是将原料破碎成小颗粒,以便于后续的工艺处理。
这个环节主要包括以下步骤:•原石进厂•破碎机破碎•破碎后再过筛3. 混合不同种类的原料需要混合在一起,生成符合要求的熟料配料。
混合的步骤包括:•须按一定比例配料•混合机搅拌,使混合均匀•将混合完的配料送至烧结炉4. 配料配料是指按照熟料成分要求将各种配料分别称量并混合在一起,常用的配料有石灰石、黏土、铁矿石等,其步骤包括:•确定熟料成分要求•仓库里先把需要的原料装进坡底下的斗•电子秤称重•直接美穗机料仓添加各组分原料•变频机调节5. 烧结烧结是指将配合均匀的生料进入烧结炉,按一定的烧成温度和时间进行物理变化,使其变为操作性能稳定、化学成份和物理性能达到工艺要求的熟料。
烧结步骤主要包括以下几个过程:1.送进烧结炉2.炉内高温烧结3.熟料的成型4.把烧后的熟料送到冷却系统6. 冷却烧结完的熟料需要进行冷却,以保证熟料质量。
熟料冷却步骤主要包括以下几个过程:•熟料经回转窑进入烟气冷却器冷却•熟料在冷却器中加水淬火•熟料冷却后送入仓库存放针对水泥熟料生产工艺,以上就是主要的流程。
随着技术的不断发展,可能会有所变化,但总体上仍然会遵循这些步骤进行生产。
7. 最终品质检验水泥熟料生产完毕后,需要进行最终品质检验,以确保其符合工业标准和客户需求。
最终品质检验主要包括以下几个方面:•成分分析:检测熟料的主要成分,如CaO、SiO2、Al2O3、Fe2O3、SO3、MgO等;•物理性能测试:对熟料的物理性能进行测试,如熟料比表面积、压缩强度、细度等;•着色指标检测:检测熟料着色指标,确保其颜色符合要求;•水泥标号检测:检测熟料中的硅酸盐含量,以确定其水泥标号。
8. 结束语水泥熟料生产工艺是一个复杂而重要的过程。
生产工艺流程

生产工艺流程一、滴定管生产玻璃原材料→剪裁到适当长度→经过碎火→慢慢吹制定形→拉伸成形→降温冷确→检验→不合格产品→合格产品→合格的成品→包装→入库二、水电解演示器玻璃原材料→剪裁到适当长度→经过碎火→慢慢吹制定形→拉伸成形→降温冷确→检验→不合格产品→合格产品→合格的成品→包装→入库三、抽气管玻璃原材料→剪裁到适当长度→经过碎火→慢慢吹制定形→拉伸成形→降温冷确→检验→不合格产品→合格产品→合格的成品→包装→入库四、气体发生器玻璃原材料→剪裁到适当长度→经过碎火→慢慢吹制定形→拉伸成形→降温冷确→检验→不合格产品→合格产品→合格的成品→包装→入库产品合格检验规程一、水电解器检验的内容:1.外观要求:由支架、底座、H形电解管、胶塞、铅电极、导线、连接胶管等组成,检验外观是否有破损,不规则变形等情况2.H形玻璃电解管要求95#3.产品全高为340±3 mm4.H形直径15±0.5 mm5.漏斗直径≥32 mm二、气体发生器检验的内容:1. 全高:306±15 mm2. 歪颈垂直度≥3 mm3. 球斗气泡直径≥5 mm4. 球斗节瘤最大直径≦3 mm5. 急冷温差≥80℃6. 耐碱等级≦2耐酸等级≦2耐水等级≦3三、抽气管检验的内容:1. 内外管应在同一轴线上,内管喷口正对下管口,,两口间距不大于3mm2. 内管喷口磨平,不允许有斜口和缺口3. 外观节瘤最大直径小于2mm,数量不超过3个,结石最大至今小于1.5mm,数量不超过2个四、滴定管检验内容:1. 酸式,25ml 采用透明玻璃制造2. 耐水等级≦33. 铜红扩散印线,容量误差±0.1ml4. 全高570mm5. 壁厚1.3±0.3mm6. 活塞2#玻璃制(6)、工装设备,检测设备情况:磁粉探伤机:数量:1台型号:DCB渗透探伤剂:数量1套(常备)探伤小车:数量1台理化试验设备万能试验机:数量1台型号:WF—300 制造厂:长春试验机厂冲击试验机:数量:1台型号:JB—300 制造厂:金华试验机厂分析天平:数量:1台型号:TG328B 制造厂:金华试验机厂分光光度机:数量:1台化学元素分析仪:数量:1台型号:C、Si、Mn、S、PV型玻口投影仪:数量:1台规格:50倍制造厂:上海光学仪器厂耐压设备水压试验电动泵:数量:3台规格:0-6MPa 型号:DSY—240 气密试验设备:数量:2台规格型号:Z—0.3/40A起重设备电动单梁起重机:数量:3台规格型号:LD—3(3T)、LD—5(5T)前移式装卸叉车:数量:1台规格型号:CPX—3L(3T)仪器试验室面积:310m2玻璃仪器压力容器制造车间:2010m2一级材料库20m2,二级 m2退火箱2台,保温筒15个现有的生产设备数控车床、型号:CNC、LATHE、0625 数控铣床、型号:XKT124成品检测室工作车间一角主要检验检测设备简介工序名设备名数量设备厂家、规格性能设备照片溶解光谱仪1台北京WDL-01Si Mg Fe Sr Ti Mn Ca Cu、PbSn Zn铸造测氢仪2台FMA SCHAAN硅氢含量热处理硬度计3台山东HB300 布氏硬度计检测数显镜2台武汉MI4000M 离子计量—11。
服装生产工艺流程(超详细)
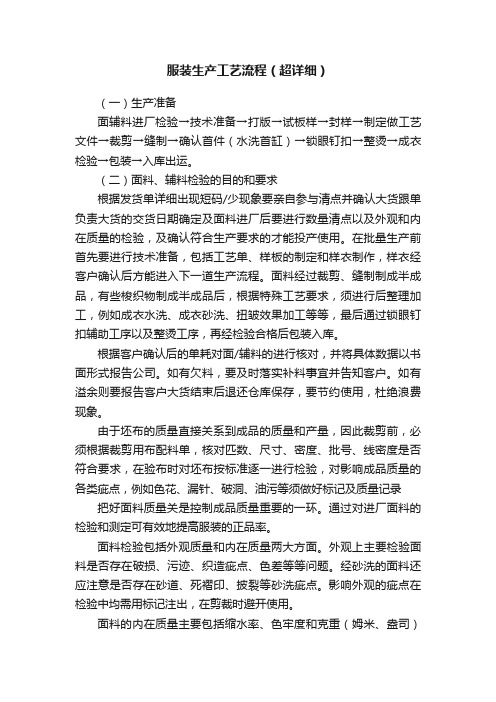
服装生产工艺流程(超详细)(一)生产准备面辅料进厂检验→技术准备→打版→试板样→封样→制定做工艺文件→裁剪→缝制→确认首件(水洗首缸)→锁眼钉扣→整烫→成衣检验→包装→入库出运。
(二)面料、辅料检验的目的和要求根据发货单详细出现短码/少现象要亲自参与清点并确认大货跟单负责大货的交货日期确定及面料进厂后要进行数量清点以及外观和内在质量的检验,及确认符合生产要求的才能投产使用。
在批量生产前首先要进行技术准备,包括工艺单、样板的制定和样衣制作,样衣经客户确认后方能进入下一道生产流程。
面料经过裁剪、缝制制成半成品,有些梭织物制成半成品后,根据特殊工艺要求,须进行后整理加工,例如成衣水洗、成衣砂洗、扭皱效果加工等等,最后通过锁眼钉扣辅助工序以及整烫工序,再经检验合格后包装入库。
根据客户确认后的单耗对面/辅料的进行核对,并将具体数据以书面形式报告公司。
如有欠料,要及时落实补料事宜并告知客户。
如有溢余则要报告客户大货结束后退还仓库保存,要节约使用,杜绝浪费现象。
由于坯布的质量直接关系到成品的质量和产量,因此裁剪前,必须根据裁剪用布配料单,核对匹数、尺寸、密度、批号、线密度是否符合要求,在验布时对坯布按标准逐一进行检验,对影响成品质量的各类疵点,例如色花、漏针、破洞、油污等须做好标记及质量记录把好面料质量关是控制成品质量重要的一环。
通过对进厂面料的检验和测定可有效地提高服装的正品率。
面料检验包括外观质量和内在质量两大方面。
外观上主要检验面料是否存在破损、污迹、织造疵点、色差等等问题。
经砂洗的面料还应注意是否存在砂道、死褶印、披裂等砂洗疵点。
影响外观的疵点在检验中均需用标记注出,在剪裁时避开使用。
面料的内在质量主要包括缩水率、色牢度和克重(姆米、盎司)三项内容。
在进行检验取样时,应剪取不同生产厂家生产的、不同品种、不同颜色具有代表性的样品进行测试,以确保数据的准确度。
同时对进厂的辅料也要进行检验,例如松紧带缩水率,粘合衬粘合牢度,拉链顺滑程度等等,对不能符合要求的辅料不予投产使用。
生产车间工艺流程表格

生产车间工艺流程表格英文回答:In the production workshop, the process flow is crucial for ensuring smooth and efficient operations. It outlines the sequence of steps involved in manufacturing a product, from raw materials to the finished product. Let me walk you through the process flow in our production workshop.Firstly, the raw materials are received and inspected for quality. This step is essential to ensure that only the best materials are used in the production process. For example, in our workshop, we receive steel sheets for manufacturing metal components. The sheets are checked for any defects or damages before they are moved to the next step.Next, the raw materials are prepared for production. This may involve cutting, shaping, or forming the materials to the required specifications. For instance, in the caseof the steel sheets, they are cut into smaller pieces using laser cutting machines. This step requires precision and accuracy to ensure the components are made to the correct size and shape.After the materials are prepared, they are moved to the assembly line for the actual production process. This is where the components are assembled together to create the final product. Each worker on the assembly line has a specific task or role to perform. For example, one worker may be responsible for attaching the metal components together using welding techniques, while another worker may be in charge of quality control, inspecting the finished product for any defects.Once the product is assembled, it undergoes a series of tests and inspections to ensure its quality and functionality. This may include performance tests, durability tests, and safety tests. For instance, if we are manufacturing electronic devices, we would test each unit to ensure that it functions properly and meets the required standards.Finally, the finished products are packaged andprepared for shipment. This involves carefully packagingthe products to protect them during transportation. For example, if we are shipping fragile items, we would use bubble wrap or foam padding to prevent any damage during transit.中文回答:在生产车间中,工艺流程对于确保生产的顺利和高效至关重要。
面粉厂和米厂生产工艺流程 (一)
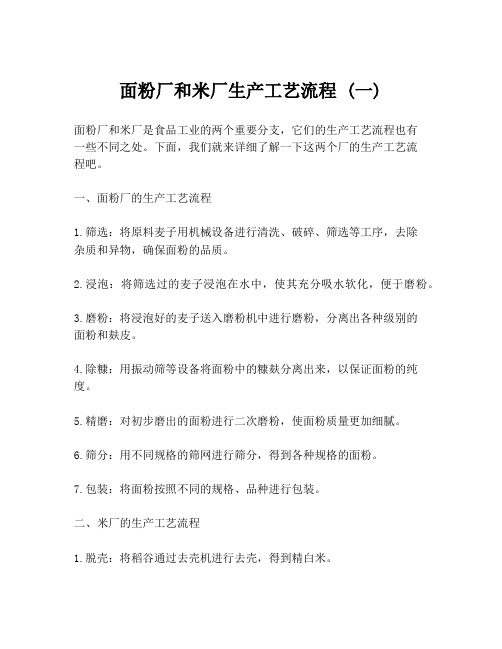
面粉厂和米厂生产工艺流程 (一)面粉厂和米厂是食品工业的两个重要分支,它们的生产工艺流程也有一些不同之处。
下面,我们就来详细了解一下这两个厂的生产工艺流程吧。
一、面粉厂的生产工艺流程1.筛选:将原料麦子用机械设备进行清洗、破碎、筛选等工序,去除杂质和异物,确保面粉的品质。
2.浸泡:将筛选过的麦子浸泡在水中,使其充分吸水软化,便于磨粉。
3.磨粉:将浸泡好的麦子送入磨粉机中进行磨粉,分离出各种级别的面粉和麸皮。
4.除糠:用振动筛等设备将面粉中的糠麸分离出来,以保证面粉的纯度。
5.精磨:对初步磨出的面粉进行二次磨粉,使面粉质量更加细腻。
6.筛分:用不同规格的筛网进行筛分,得到各种规格的面粉。
7.包装:将面粉按照不同的规格、品种进行包装。
二、米厂的生产工艺流程1.脱壳:将稻谷通过去壳机进行去壳,得到精白米。
2.筛分:用筛网将压碎后的稻谷分离出各个部分(头米、尖米、糠等)。
3.浸泡:将脱壳后的米浸泡在水中,让其吸水软化,减少损坏。
4.蒸煮:将软化后的米放入蒸锅中进行蒸煮,使其软硬适中。
5.糙米处理:对糙米进行碾磨或脱胚处理,使其变成白米。
6.精加工:对白米进行加工处理,如研磨、糠层去除、分选、精炒等。
7.包装:将处理好的米按照不同的规格、品种进行包装。
综上所述,面粉厂和米厂的生产工艺流程虽有区别,但都是经过多个工序的处理,才得到最终的成品。
这些工序都是为了保证产品的质量和卫生安全。
在实际生产中,各个环节的质量控制和卫生管理也是不可忽视的重要环节。
只有在全面保障质量和安全的前提下,才能让消费者放心购买、食用。
沉淀法二氧化硅生产工艺流程(一)
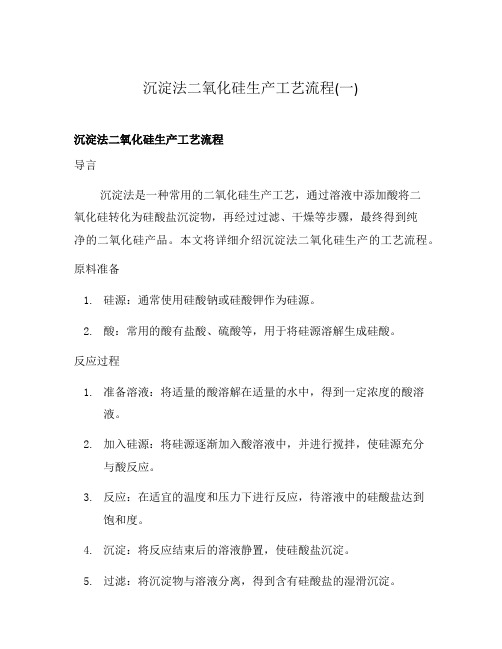
沉淀法二氧化硅生产工艺流程(一)
沉淀法二氧化硅生产工艺流程
导言
沉淀法是一种常用的二氧化硅生产工艺,通过溶液中添加酸将二
氧化硅转化为硅酸盐沉淀物,再经过过滤、干燥等步骤,最终得到纯
净的二氧化硅产品。
本文将详细介绍沉淀法二氧化硅生产的工艺流程。
原料准备
1.硅源:通常使用硅酸钠或硅酸钾作为硅源。
2.酸:常用的酸有盐酸、硫酸等,用于将硅源溶解生成硅酸。
反应过程
1.准备溶液:将适量的酸溶解在适量的水中,得到一定浓度的酸溶
液。
2.加入硅源:将硅源逐渐加入酸溶液中,并进行搅拌,使硅源充分
与酸反应。
3.反应:在适宜的温度和压力下进行反应,待溶液中的硅酸盐达到
饱和度。
4.沉淀:将反应结束后的溶液静置,使硅酸盐沉淀。
5.过滤:将沉淀物与溶液分离,得到含有硅酸盐的湿滑沉淀。
6.清洗:用适量的水将沉淀物进行清洗,去除杂质。
7.干燥:将清洗后的沉淀物进行干燥,得到二氧化硅颗粒。
后处理
1.粉碎:将干燥后的二氧化硅颗粒进行粉碎,使其达到所需的粒度。
2.筛分:经过粉碎后的二氧化硅颗粒进行筛分,得到适合不同用途
的颗粒大小。
3.包装:将筛分后的二氧化硅产品进行包装,保证其质量和安全。
总结
沉淀法是一种常用的二氧化硅生产工艺,通过酸与硅源的反应,
得到硅酸盐沉淀物,并经过过滤、清洗、干燥等步骤,最终得到纯净
的二氧化硅产品。
掌握了该工艺流程,能够高效、稳定地生产二氧化硅,满足不同领域的需求。
以上就是沉淀法二氧化硅生产工艺流程的详细介绍,希望对读者
有所帮助。
热熔胶生产工艺流程(1)

热熔胶生产原料及工艺流程
◆主要原材料:
热熔胶是环保固体胶黏剂,不含任何有机溶剂,对环境没有任何污染,加工和施工过程中,不产生任何有害气体和液体。
热熔胶加热融化,对被粘物质产生粘接,温度降低变成固态。
原材料:EVA、PE、增粘树脂、助剂等
◆主要工艺流程:
1.配料:按照配方配比配料
2.炼胶:按照制定的加料流程,将原料加入到炼胶设备中(比如捏合机或反应釜),加热到一定温度条件下,熔融炼胶。
3.挤出造粒:热熔胶炼制完毕,按照一定量比例加入单螺杆挤出机,造粒(水下造粒或拉条造粒)。
4.烘干包装:造粒后的热熔胶,烘干包装储存。
主要设备:
高搅机(配料)、炼胶设备(捏合机或反应釜)、挤出机、造粒设备(水下造粒或拉条设备)、烘干包装设备。
家具厂细木工板生产工艺流程(27页)生产制度表格

细木工板的生产工艺流程芯条占细木工板体积60%以上,与细木工板的质量有很大关系。
制造芯条的树种最好采用材质较软,木材结构均匀、变形小、干缩率小,而且木材弦向和径向干缩率差异较小的树种,易加工、芯条的尺寸、形状较精确,则成品板面平整性好,板材不易变形,重量较轻,有利于使用。
一般芯条含水率8%--12%,北方空气干燥可为6%--12%,南方地区空气湿度大,但不得超过15%芯条的生产流程:干板材 双面刨 多片锯 横截锯 芯条(压刨)芯条厚度:木芯板的厚度加上制造木芯板时板面刨平的加工余量。
芯条宽度:芯板的宽度一般为厚度倍,最好不要超过2倍,一些质量要求很高的细木工板芯条宽度不能大于20mm 芯条越宽,当含水率发生变化时,芯条变形就越大。
芯条长度:芯条越长,细木工板的纵向弯曲强度越高,然而芯条越长,木材利用率越低。
芯条的材质:芯条不允许有树脂漏,不允许腐朽,不允许有爬楞。
芯 条单 板木芯板 组坯 胶压 锯边 砂光 成品芯板的加工:使用芯条胶拼机木芯板胶拼后,板面粗糙不平,通常采用压刨加工,芯条加工精度很高的机拼木芯板,可以用砂光加工来代替刨光。
胶合板以木材为主要原料生产的胶合板,由于其结构的合理性和生产过程中的精细加工,可大体上克服木材的缺陷大大改善和提高木材的物理力学性能,胶合板生产是充分合理地利用木材、改善木材性能的一个重要方法。
定义:胶合板是由木段旋切成单板或由木方刨切成薄木,再用胶粘剂胶合而成的三层或多层的板状材料,通常用奇数层单板,并使相邻层单板的纤维方向互相垂直胶合而成。
胶合板的构成原则:对称原则:对称中心平面两侧的单板,无论树种单板厚度、层数、制造方法、纤维方向和单板的含水率都应该互相对应,即对称原则胶合板中心平面两侧各对应层不同方向的应力大小相等。
因此,当胶合板含水率变化时,其结构稳定,不会产生变形,开裂等缺陷;反之,如果对称中心平面两侧对应层有某些差异,将会使对称中心平面两侧单板的应力不相等,使胶合板产生变形、开裂。
奶酪生产工艺流程图

奶酪生产工艺流程图2、原谅进厂时必须有同批产品化验单,经本厂化验室检验合格后方可生产使用;3、关键质量控制点的主要设备及工艺参数:烘烤杀菌(温度:60℃~65℃:时间:1~1。
5h)危害分析(HA)指对食品原料及每步生产过程中潜在的、有健康危害的因子或生产环境的危险性和严重性做分析,收集信息,找出危害来源,评估危害,确定哪些因素对食品安全有显著意义,进而列入HACCP计划中.危害分析分为危害识别和危害评估两个阶段.主要从原料及加工过程中可能存在的生物危害、化学危害和物理危害3方面进行识别和评估.生物危害:牛乳中致病菌、芽孢菌等会造成微生物大量繁殖,产品腐败而产生危害.化学危害:主要是滥用的食品添加剂、防腐剂、润滑剂、清洁化合物、农药残留及抗菌素残留、有毒元素及化合物以及放射性物质等.物理危害:玻璃、金属、石块等存在于食品中不易被发现的物质.奶酪生产过程中的危害分析详见表1.表1 奶酪生产过程中危害分析工作单3 关键控制点(CCP) 及关键限值的确定关键控制点指所有会影响产品生物性、化学性或物理性的危险性生产步骤或程序.对食品加工过程中的某一点或某一步骤或工序进行控制后,就可以防止、消除食品安全危害或将其减少到可接受水平.借助CCP决策树来确定关键控制点,确定了生产过程中共存在6个CCP.根据关键控制点设置关键限值参数,进而对设置的参数进行监控,具体见表2.3。
1原料乳(CCP1)原料乳是生产安全的首要因素,特别是2008年乳制品的安全问题成为全国甚至全球的焦点,原料乳的优劣是乳制品质量的基础和根本.牛乳中含有对人体有益的丰富的营养物质,但是牛乳也是微生物良好的培养环境,挤奶及运输过程中易污染致病菌、腐败菌,如果处理不当,会破坏牛乳中的营养成分甚至对人们的健康造成危害;牛乳中的抗生素残留、亚硝酸盐、牛毛玻璃,甚至掺杂掺假都直接影响产品的品质.因此原料乳应选用新鲜、优质的牛乳,牛乳的验收符合国标GB/T6914-86.抗生素残留不得检出.3.2杀菌(CCP2)表2 HACCP计划表3.4加热搅拌(CCP4)加热促进凝块粒的进一步收缩,增加奶酪的硬度和强度.通常加热温度应缓慢上升,上升越快,奶酪硬度越大,而不同种类的奶酪所需硬度不同,温度上升速率也不同,而且加热过程时间较长,需要1~2h,视不同奶酪有所差别,长时间的缓慢加热过程容易引起环境中的微生物进入,因此要严格控制温度上升速率及最终温度并保持环境卫生状况良好.3.5加盐(CCP5)不同种类的奶酪加盐方式不相同,主要有盐渍和拌盐两种.拌盐法主要是预防盐中的杂质带入的危害,盐渍法除了要预防杂质外,盐水的卫生状况直接影响到奶酪的成熟和成品的安全性.另外盐渍的时间长短,不同奶酪也不尽相同,有的需要几十分钟到几个小时,有的甚至需要一两天时间,时间较长易受微生物污染.3.6成熟(CCP6)大多数奶酪都需要成熟过程,奶酪成熟经历了一系列物理化学和生物化学变化,其组织结构、风味和营养价值大大提高.成熟过程中需要保持一定的温度、湿度.不同品质的奶酪对成熟室的温度和湿度要求不同,成熟的时间也不相同,长则需要一两年,短则只需两三个月,由于成熟条件、温度湿度控制不当会造成霉变.4 纠偏措施和监控机制当监控表明偏离关键限值或不符合关键限值时,就要采取纠偏措施.原料乳不合要求要拒收;杀菌温度时间不当要重新调整;发酵剂被污染要重新分离纯化,并将被污染的产品弃去;因加热条件失控或加盐过程中遭微生物或化学试剂污染则产品应报废;奶酪成熟过程中因微生物原因造成的危害,产品要放弃,因温度湿度造成偏差要及时调整.HACCP工作必须通过一系列的记录来体现,如:操作监控记录、纠偏记录等,每个关键控制点都要有相应人员监控,HACCP小组应定期对各环节检查,保证HACCP 体系的正常运行.HACCP工作表至少要保留3年.。
氯碱生产工艺流程 (1)

重大事故发生后应急处理预案
1.事故报警:
当发生突发性危险化学品泄漏或火灾爆炸事故时,现场人员应在保护好自身安全的情况下,及时确认事故发生的部位,并向当班主任报告,逐级报告各有关部门。
报警过程中应着重说明事故发生的地点、时间、泄漏的化学品名称及泄漏量、事故性质、危险程度及有无人员伤亡及报警者姓名和联系电话。
6
3#Ⅰ效蒸发器
DN2600×17500
1台
T﹤153
7
3#Ⅱ效蒸发器
1台
8
3#Ⅲ效蒸发器
1台
4
盐酸炉
1台
5
氨压机
S8-12.5
7台
85000千大卡
-30℃
6
液氯贮槽
DN2000×6289
4台
TW-25—35℃
7
氨贮槽
ZA-1.5
2台
V=1.5m3
TW:50℃
8
汽化器
DN1000×2420
2台
9
液氯钢瓶
漂液工艺流程图:
来自液氯的尾氯残碱:5—10g/L
有效氯:4.5—5%
来自氯处理残氯
工业水网
推车运输
9.蒸发工艺流程简述:
电解液经两台串联的螺旋板式换热器预热至90℃—100℃,进入Ⅰ效蒸发器,料液靠压差过料到Ⅱ效蒸发器强制循环浓缩,然后由Ⅱ效采盐泵送至Ⅱ效旋液分离器采盐,盐泥流入盐泥高位槽,Ⅱ效旋液分离器顶部清液,当过料时送至Ⅲ效,不过料时回流至Ⅱ效,碱液在Ⅲ效蒸发器中强制循环浓缩至30%或42%,由Ⅲ效采盐泵送至Ⅲ旋液分离器采盐,盐泥入盐泥高位槽,顶部清液,当出料时送至出碱桶,当浓度不合格时回流入Ⅲ效蒸发器中。
双级制冷工艺流程简图:
生产工艺明细表(1)
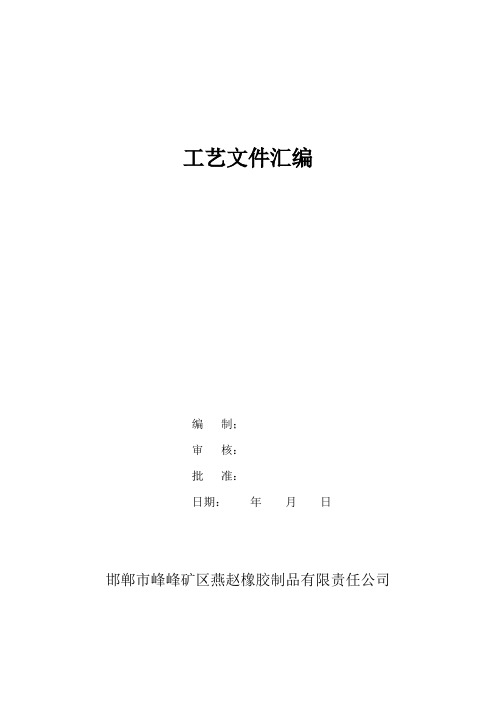
工艺文件汇编编制;审核:批准:日期:年月日邯郸市峰峰矿区燕赵橡胶制品有限责任公司工艺文件明细表一、钢丝缠绕胶管工艺文件1、产品基本特征2、生产用主要材料及标准3、热炼工艺4、压出工艺5、压延中胶片6、切割涂塑玻璃丝窗纱7、导钢丝线轴8、钢丝缠绕9、包外胶层10、卷水包布11、硫化12、成品检查与包装二、软心高压钢编胶管工艺文件1.产品基本特征2.生产用原材料3.胶料热炼4.内胶包覆工艺5.压延中胶片6.钢丝合股7.钢丝编织8.包外胶工艺9.缠水包布工艺10.胶管硫化工艺11.胶管脱芯工艺12.成品检查与包装三、硬芯高压钢编胶管工艺文件1、产品基本特征2、生产用主要材料及辅助材料3、工艺流程4、胶料热炼5、挤出内管6、延压中胶7、胶管成型(1)合股施工表(2)套管(3)一层钢丝编织施工表(4)钢丝编织工艺规定(5)两层钢丝编织施工表(6)三层钢丝编织施工表8、包外胶9、缠水包布10、硫化11、成品检验与包装四、喷浆用橡胶软管钢丝编织生产工艺文件1、产品基本特征2、生产用主要材料3、工艺流程图4、胶料热炼5、挤出内管6、压延中外胶7、套管8、钢丝编织9、缠水包布10、硫化11、成品检查与包装一、钢丝缠绕胶管工艺文件企标钢丝缠绕工艺表二、软性高压钢编胶管工艺文件企标硬芯高压钢丝编制工艺I软芯两层编织生产工艺企标软芯高压钢丝编制工艺I软芯编织生产工艺企业钢丝编织压出、包胶工艺三、硬芯高压钢编管工艺文件。
锂电池pack生产流程工艺标准(一)
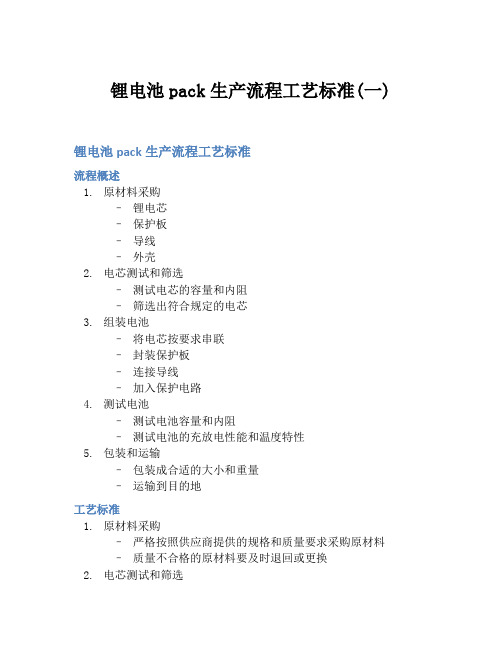
锂电池pack生产流程工艺标准(一)锂电池pack生产流程工艺标准流程概述1.原材料采购–锂电芯–保护板–导线–外壳2.电芯测试和筛选–测试电芯的容量和内阻–筛选出符合规定的电芯3.组装电池–将电芯按要求串联–封装保护板–连接导线–加入保护电路4.测试电池–测试电池容量和内阻–测试电池的充放电性能和温度特性5.包装和运输–包装成合适的大小和重量–运输到目的地工艺标准1.原材料采购–严格按照供应商提供的规格和质量要求采购原材料–质量不合格的原材料要及时退回或更换2.电芯测试和筛选–测试仪器要定期校准,确保准确度–电芯最大容量和内阻的标准值不能超过规定值–筛选出符合规定的电芯进行组装3.组装电池–串联电芯要保证电池的电压和容量一致–保护板封装要严密,保证不漏电–导线连接要稳固,不能出现接触不良的情况–保护电路要按要求安装到电池中4.测试电池–测试仪器要定期校准,确保准确度–电池的容量和内阻的标准值不能超过规定值–充放电性能和温度特性要符合规定要求5.包装和运输–包装要做到紧凑和牢固,以保护电池不受外界冲击–运输要按照相关规定,采取安全措施,保证电池的安全到达目的地总结在生产锂电池pack的过程中,必须要按照标准化的流程和工艺要求进行操作,以确保生产出的电池质量稳定、性能优良。
同时,在生产过程中要加强质量把控,定期检查和维护生产设备和仪表,确保生产过程的准确度和稳定度。
注意事项1.在原材料采购阶段,要做好供应商的资质审核,避免采购到劣质原材料。
2.在组装电池时,要避免出现短路或漏电的情况,以免出现火灾等意外情况。
3.在测试电池和电芯时,要保证测试仪器精度和准确度。
4.在包装和运输阶段,要严格按照相关规定和标准操作,避免损坏或丢失电池。
5.在生产中要注意环保和安全,避免对环境和人体健康的危害。
结语电池是现代社会中不可或缺的能源,作为其中最为重要的一种电池,锂电池pack的生产流程和工艺标准显得尤为重要。
硅片生产工艺技术流程1

顺大半导体发展有限公司太阳能用硅单晶片生产技术目录一、硅片生产工艺中使用的主要原辅材料1、拉制单晶用的原辅材料,设备和部件:2、供硅片生产用的原辅材料,设备和部件:二、硅片生产工艺技术1、硅单晶生产部(1)、腐蚀清洗工序生产工艺技术对处理后原材料质量要求(2)、腐蚀清洗生产工艺流程①多晶硅块料,复拉料和头,尾料处理工艺流程②边皮料酸碱清洗处理工艺流程③埚底料酸清洗处理工艺流程④废片的清洗处理工艺流程(3)、硅单晶生长工艺技术(4)、单晶生长中的必备条件和要求①单晶炉②配料与掺杂(5),单晶生长工艺参数选择(6)、质量目标:(7)、硅单晶生长工艺流程2、硅片生产部(1)、硅片加工生产工艺技术(2)、硅片加工工艺中的必备条件和要求①切割机②切割浆液(3)、质量目标(4)、硅片加工工艺技术流程①开方锭生产工艺流程②切片生产工艺流程(5)、硅片尺寸和性能参数检测前言江苏顺大半导体发展有限公司座落于美丽的高邮湖畔.公司始创生产太阳能电池用各种尺寸的单晶和多晶硅片.拥有国内先进的拉制单晶设备104台,全自动单晶炉112台。
年产量可达到××××吨.拥有大型先进的线切割设备×××台.并且和无锡尚德形成了合作联盟(伙伴),每×可以向尚德提供×××硅单晶片。
同时河北晶于2004年,占地面积××××。
公司现在有×××名员工, 从事澳、南京等光伏组件公司都和顺大形成了长年的合作关系。
为了公司的进一步发展,扩大产业链,解决硅单晶的上下游产品的供需关系,2006年在扬州投资多晶硅项目,投资规模达到××亿。
工程分两期建设,总规模年产多晶硅6000吨。
2008年底首期工程已经正式投入批量生产,年产多晶硅×××吨。
聚乙烯工艺流程图(1)
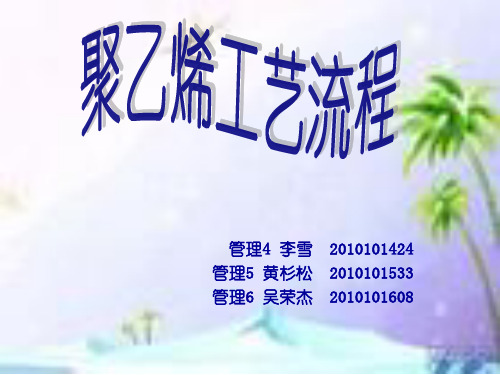
聚乙烯的性质
一、物理性质
1 聚乙烯为白色、蜡状半透明材料,具有优越的介 电性能。
2 易燃烧,且离火后继续燃烧。 3 透水率低,对有机蒸汽透过率则较大。 4 透明度随结晶度增加而下降,在一定结晶度下,
透明度随分子量增加而提高。 5 高密度聚乙烯熔点范围为132~135℃,低密度聚
乙烯熔点较低﹙112℃﹚且范围宽。 6 常温下不溶于任何已知溶剂中,70℃以上可少量
H 扬子石油化工股份有限公司 D 塑料 厂 P 燕山石化有限公司化工一厂
北京助剂二厂(UHMWPE)
E 上海金菲石化有限公司
兰州石化公司石油化工厂
77.53
97.3
小计
2010
2009
2010 2006 2004 2003
装置能力
设计 00.3 3.5
现有 0.8 7
14 24
14 14
14 16
使用技术
低压淤浆法(国内技术) 德国Hoechst淤浆法 三井油化淤浆法聚合工 艺 UCC气相流化床工艺
三井油化淤浆法聚合工艺
14 14
淤浆法(国内技术)
1
1
10 13.5 Philips环管淤浆法
7
7
淤浆法(国内技术)
聚乙烯国内外状况
最新进展和发展趋势
茂金属催化剂: 降低成本 链转移反应,生成长支链 非茂高性能催化剂高活性 高活性和单一活性中心 具有齐聚功能 双峰生产技术 熔体混合法(掺混) 多个反应器串联 复配两种以上的催化剂
无缝钢管生产工艺流程(一)

无缝钢管生产工艺流程(一)无缝钢管生产工艺1. 前置处理工序1.材料选料:根据使用要求和环境条件,选择相应的材料。
2.加热处理:将钢坯加热到一定温度,以便后面的轧制和穿孔等操作。
3.轧制:将加热后的钢坯进行轧制,使其成为所需大小和形状的毛坯。
2. 穿孔工序1.冷穿孔:用轮胎式轧辊将毛坯推入圆锥形模具中,从而穿出成型管。
2.热穿孔:将毛坯在高温下进行穿孔成型,常用的方法为两辊挤压法和三辊挤压法。
3. 热轧加工工序1.热轧加工:将穿孔成型后的钢管进行热轧加工,使其成为所需的精确尺寸和形状。
2.热处理:将热轧加工后的钢管进行淬火或回火处理,以改善其力学性能。
4. 表面处理工序1.啮缝:用啮合器将钢管表面的氧化物和锈垢去除。
2.直条砂轮:用研磨机将钢管表面进行粗磨。
3.高速砂带:用高速砂带机将钢管表面进行精磨,使其达到表面光洁度要求。
5. 检测工序1.超声波检测:用超声波探头对钢管进行检测,以发现可能存在的裂纹等问题。
2.磁粉探伤:涂上磁粉的钢管在磁粉感应下进行检测,以发现表面和内部的裂纹等问题。
3.气密性检测:将气密性要求高的钢管进行检测,以发现可能存在的气泄漏等问题。
6. 包装工序1.包装:将检测合格的钢管进行包装,以保护其表面不受污染和磨损。
2.贮存:将已包装的钢管进行贮存,等待出售或运输。
7. 总结无缝钢管的制造工艺是一个复杂的过程,需要严格的控制质量和工艺参数,以保证钢管的力学性能和表面质量符合使用要求。
从前置处理工序到最终的包装贮存,每个环节都有严格的要求和标准。
检测工序的重要性也不可小觑,只有通过科学的检测才能保证无缝钢管的质量和可靠性。