金属断裂的微观机制及显微特征
11.金属的脆性断裂机制

是材料断裂前基本上不产生明显的宏观塑性变形,没有明脆性断裂:显预兆,往往表现为突然发生的快速断裂过程。
☐由拉伸正应力影响。
☐微观机制:穿晶的解理断裂;沿晶断裂(晶间断裂)。
是材料在拉应力的作用下,由于原于间结合键遭到破坏,解理断裂:严格地沿一定的结晶学平面(即所谓“解理面”)劈开而造成的。
一些金属的解理面及解理临界正应力解理面一般是表面能最小的晶面,且往往是低指数的晶面,也就是原子密排面。
解理台阶解理断裂实际上不是沿单一的晶面,而是沿一族相互平行的晶面发生解理而引起的。
在不同高度上的平行解理面值之间解理台阶:形成了“解理台阶”。
裂纹AB与螺型位错CD交截后形成台阶解理台阶可认为是通过解理裂纹与螺型位错交割而形成。
河流状花样船用钢板解理断裂的河流花样典型的解理断口形貌特征A 台阶,B 河流花样河流的流向(一些支流的汇合方向)即为裂纹扩展方向。
舌状花样解理舌形成示意图舌状花样它是解理裂纹沿孪晶界扩展,越过孪晶后再在解理面扩展,形成舌状凸台。
准解理断裂与解理断裂一样都是穿晶断裂;都有解理形成的小的平面刻面,以及河流和台阶。
☐材料发生准解理断裂时,宏观上是脆性或者塑性很低的,因此认为准解理断裂属于解理断裂范畴。
☐从断裂机制而言,准解理断裂由解理断裂和微孔聚合这两种机理复合作用而构成。
有缘学习更多+谓ygd3076或关注桃报:奉献教育(店铺)沿晶断裂沿晶断裂:沿晶断裂多数为脆性断裂,是晶界结合力较弱的一种表现。
沿晶断裂沿晶断裂的断口形貌有缘学习更多+谓ygd3076或关注桃报:奉献教育(店铺)谢谢观赏!Thanks!。
10.金属的韧性断裂机制
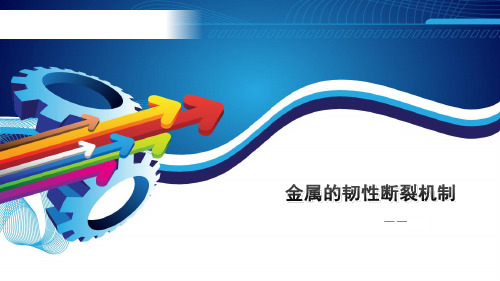
韧性断裂是材料断裂前及断裂过程中产生明显宏观塑性变形的断
裂过程。
韧性断裂
(延性断裂):杯
锥
状
断
口韧断前有明显的颈缩,断裂前有大量的塑性变形。
上下断口分别呈杯状和锥状,合称为杯锥状断口。
1、颈缩引起三向拉应力
2、微孔形成
3、微孔长大
4、微孔连接成中心空腔
5、沿45〫方向切断形成杯锥状断口
6061铝合金室温拉伸形成的韧窝
微观韧性断裂的形貌
是韧窝。
有缘学习更多+谓ygd3076或关注桃报:奉献教育(店铺)
形成韧窝形状示意图
韧窝的形状与受
力条件有关。
微孔形核与长大的位错模型
(a)绕质点的位错环;
(b)外力使位错环向界面推进;
(c)形成微孔;
(d)后续位错进入微孔后微孔长大。
韧性断裂的影响因素
钢中的碳化物、硫化物的体积分数和形状对断裂延性的影响
第二相或夹杂物的大
小、形状、密度、分布,
基体材料的塑性、应变硬
化指数,外加应力的大小
和应力状态均影响韧性断
裂。
谢谢观赏!Thanks!。
金属的断裂PPT课件

2.Griffith公式 (临界应力公式) 设有一块薄板,厚度=1个单位,内有 一椭圆形裂口,小裂口长度为 2c
薄板受均匀的拉应力σ作用 e —— 裂口扩展所需的能 e = e1+ e2 e1 —— 裂口扩展所降低的弹性能 e2 —— 裂口扩展所增加的表面能
第10页/共54页
e1=单位体积弹性能×裂口总体积 裂口所松驰的弹性能可近似看作形成直径为 2c 的无应 力区域所释放的能量 粗略估计值:e1 ≈ -1/2σ·ε×πc2 = -πc2σ2/2E 更精确计算出的值为粗略估计值的二倍,即:
特点:① 裂口生成、发展均很快 断裂前没有明显的塑性变形,ε<5% ②断口平整(破断面和拉应力接近
于 正交)有金属光泽 断口⊥σmax 断口沿解理面 在电镜下可看到解理亮面
二种情况:
沿解理面的穿晶断裂 —— 河流状、舌状花纹
沿晶界的晶间断裂 —— 冰糖状、颗粒状
第1页/共54页
穿晶断裂 ——断裂时裂纹发展穿过晶粒内部(韧断) 晶间断裂 ——断裂时裂纹发展沿着晶界 (脆断)
锻压圆锭时,相当于压缩厚件。假若没有外 端,则可自由地形成双鼓形,但由于外端的 拉齐作用,使工件中心产生附加拉应力。
第40页/共54页
当翻转90°锻成方坯时,裂纹如图(d), 十
字形 当旋转锻造圆坯时,裂纹如图(e),放射状
第41页/共54页
② 防止措施 采用槽形或弧形锤头,增加侧压,使附加 拉应力↓
沿τmax 方向断裂 形成杯锥状
二.微孔的形成 研究表明,微孔主要在析出物、夹杂物等第二相 粒子的地方形成 产生微孔的机理 1.杂质与基体界面发生剥离 这是由变形不协调产生的 杂质引起应力集中现象,产生 微孔
第22页/共54页
金属材料断口机理及分析
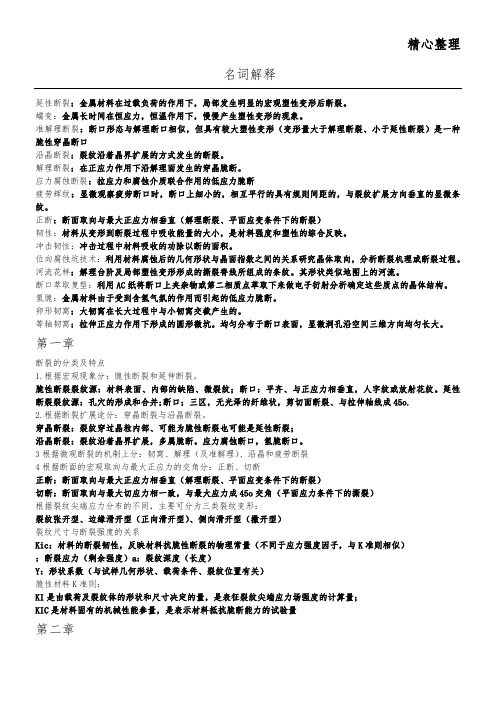
精心整理名词解释延性断裂:金属材料在过载负荷的作用下,局部发生明显的宏观塑性变形后断裂。
蠕变:金属长时间在恒应力,恒温作用下,慢慢产生塑性变形的现象。
准解理断裂:断口形态与解理断口相似,但具有较大塑性变形(变形量大于解理断裂、小于延性断裂)是一种脆性穿晶断口沿晶断裂:裂纹沿着晶界扩展的方式发生的断裂。
解理断裂:在正应力作用下沿解理面发生的穿晶脆断。
应力腐蚀断裂:拉应力和腐蚀介质联合作用的低应力脆断疲劳辉纹纹。
正断韧性: 河流花样 氢脆:卵形韧窝等轴韧窝1.2.34裂纹张开型、边缘滑开型(正向滑开型)、侧向滑开型(撒开型) 裂纹尺寸与断裂强度的关系Kic :材料的断裂韧性,反映材料抗脆性断裂的物理常量(不同于应力强度因子,与K 准则相似) :断裂应力(剩余强度)a :裂纹深度(长度)Y :形状系数(与试样几何形状、载荷条件、裂纹位置有关) 脆性材料K 准则:KI 是由载荷及裂纹体的形状和尺寸决定的量,是表征裂纹尖端应力场强度的计算量; KIC 是材料固有的机械性能参量,是表示材料抵抗脆断能力的试验量第二章裂纹源位置的判别方法:T型法(脆断判别主裂纹),分差法(脆断判别主裂纹),变形法(韧断判别主裂纹),氧化法(环境断裂判别主裂纹),贝纹线法(适用于疲劳断裂判别主裂纹)。
断口的试样制备:截取,清洗,保存。
断口分析技术设备:1.宏观断口分析技术(用肉眼,放大镜,低倍率光学显微镜观察分析)2.光学显微断口分析(扫描电子显微镜光学显微镜,透射电子显微镜),3.电镜断口分析。
第三章延性断裂:12.3.1(1约成45(2(321.2.(1)内颈缩扩展:质点大小、分布均匀,韧窝在多处形核(裂纹萌生),随变形增加,微孔壁变薄,以撕裂方式连接(2)剪切扩展:材料中具有较多夹杂物,同时具有细小析出相时,微孔之间可能以剪切方式相连接。
注意:内颈缩扩展与剪切扩展在同一韧窝断口上可能同时发生。
影响韧窝的形貌因素:夹杂物或第二相粒子,基体材料的韧性,试验温度,应力状态。
4金属材料的断裂和断裂韧性.

内颈缩
剪切裂纹
夹杂
(a)正常的微孔聚合;(b)快速剪切断开;(c)大片夹杂相连
脆性断裂的宏观特征
断裂前无明显的塑性变形,吸收的能量很少,而裂纹的 扩展速度往往很快,几近音速,故脆性断裂前无明显的 征兆可寻,且断裂是突然发生的,因而往往引起严重的 后果 。
在工程应用中,一般把Ψk <5%定为脆性断裂, Ψk =5%定
为准脆性断裂, Ψ k >5%定为韧性断裂。
材料处于脆性状态还是韧状态并不是固定不变的,往往因
2 基体的形变强化
基体的形变强化指数越大,则塑性变形后的强化越强烈,其结 * n 果是各处均匀的变形。微孔长大后的聚合,将按正常模式进行, Kep 韧性好;相反地,如果基体的形变强化指数小,则变形容易局 部化,较易出现快速剪切裂开。这种聚合模式韧性低。
21
第二相对断裂应变的影响
22
材质、应力状态和环境等因素而相互转化。
常见的脆性断裂有解理断裂和晶间断裂。
4
4.1.1 解理断裂
解理断裂是材料在拉应力的作用下,由于原子间结合键遭到破坏,
严格地沿一定的结晶学平面(即所谓“解理面”)劈开而造成的。
解理面一般是表面能最小的晶面,且往往是低指数的晶面。 解理断口的宏观形貌是较为平坦的、发亮的结晶状断面。 在电子显微镜下,解理断口的特征是河流状花样。河流状花样是由
(2)成分的影响
金属断口机理及分析
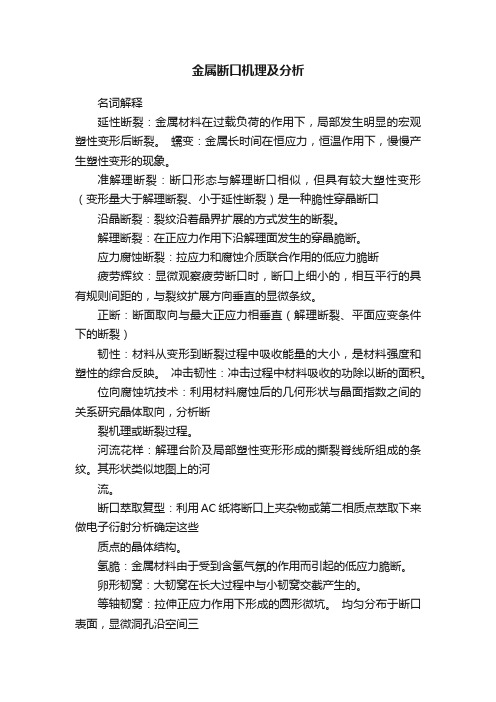
金属断口机理及分析名词解释延性断裂:金属材料在过载负荷的作用下,局部发生明显的宏观塑性变形后断裂。
蠕变:金属长时间在恒应力,恒温作用下,慢慢产生塑性变形的现象。
准解理断裂:断口形态与解理断口相似,但具有较大塑性变形(变形量大于解理断裂、小于延性断裂)是一种脆性穿晶断口沿晶断裂:裂纹沿着晶界扩展的方式发生的断裂。
解理断裂:在正应力作用下沿解理面发生的穿晶脆断。
应力腐蚀断裂:拉应力和腐蚀介质联合作用的低应力脆断疲劳辉纹:显微观察疲劳断口时,断口上细小的,相互平行的具有规则间距的,与裂纹扩展方向垂直的显微条纹。
正断:断面取向与最大正应力相垂直(解理断裂、平面应变条件下的断裂)韧性:材料从变形到断裂过程中吸收能量的大小,是材料强度和塑性的综合反映。
冲击韧性:冲击过程中材料吸收的功除以断的面积。
位向腐蚀坑技术:利用材料腐蚀后的几何形状与晶面指数之间的关系研究晶体取向,分析断裂机理或断裂过程。
河流花样:解理台阶及局部塑性变形形成的撕裂脊线所组成的条纹。
其形状类似地图上的河流。
断口萃取复型:利用AC 纸将断口上夹杂物或第二相质点萃取下来做电子衍射分析确定这些质点的晶体结构。
氢脆:金属材料由于受到含氢气氛的作用而引起的低应力脆断。
卵形韧窝:大韧窝在长大过程中与小韧窝交截产生的。
等轴韧窝:拉伸正应力作用下形成的圆形微坑。
均匀分布于断口表面,显微洞孔沿空间三维方向均匀长大。
第一章断裂的分类及特点1.根据宏观现象分:脆性断裂和延伸断裂。
脆性断裂裂纹源:材料表面、内部的缺陷、微裂纹;断口:平齐、与正应力相垂直,人字纹或放射花纹。
延性断裂裂纹源:孔穴的形成和合并;断口:三区,无光泽的纤维状,剪切面断裂、与拉伸轴线成45o .2.根据断裂扩展途分:穿晶断裂与沿晶断裂。
穿晶断裂:裂纹穿过晶粒内部、可能为脆性断裂也可能是延性断裂;沿晶断裂:裂纹沿着晶界扩展,多属脆断。
应力腐蚀断口,氢脆断口。
3根据微观断裂的机制上分:韧窝、解理(及准解理)、沿晶和疲劳断裂4根据断面的宏观取向与最大正应力的交角分:正断、切断正断:断面取向与最大正应力相垂直(解理断裂、平面应变条件下的断裂)切断:断面取向与最大切应力相一致,与最大应力成45o交角(平面应力条件下的撕裂)根据裂纹尖端应力分布的不同,主要可分为三类裂纹变形:裂纹张开型、边缘滑开型(正向滑开型)、侧向滑开型(撒开型)裂纹尺寸与断裂强度的关系Kic :材料的断裂韧性,反映材料抗脆性断裂的物理常量(不同于应力强度因子,与K 准则相似)a Y K c c πσ?=1:断裂应力(剩余强度) a :裂纹深度(长度)Y :形状系数(与试样几何形状、载荷条件、裂纹位置有关)脆性材料K 准则:KI 是由载荷及裂纹体的形状和尺寸决定的量,是表征裂纹尖端应力场强度的计算量;KIC 是材料固有的机械性能参量,是表示材料抵抗脆断能力的试验量第二章裂纹源位置的判别方法:T 型法(脆断判别主裂纹),分差法(脆断判别主裂纹),变形法(韧断判别主裂纹),氧化法(环境断裂判别主裂纹),贝纹线法(适用于疲劳断裂判别主裂纹)。
金属断裂的微观机理与典型形貌

金属断裂的微观机理与典型形貌金属断裂是指金属材料在受到应力作用下发生破裂现象。
金属断裂的微观机理和典型形貌是金属材料断裂过程中所呈现出的微观变化和破裂形态。
本文将从金属断裂的微观机理和典型形貌两个方面进行探讨。
一、金属断裂的微观机理在金属断裂的微观机理中,主要涉及到晶体的变形、晶界滑移和裂纹扩展等过程。
1. 晶体的变形金属材料的断裂是由于晶体内部发生了塑性变形。
当金属受到外力作用时,晶体内的原子会发生位移和重排,导致晶体的形状发生变化。
晶体的变形过程中,会产生位错,即晶格中的原子出现错位。
位错的运动和积累是金属材料塑性变形和断裂的基础。
2. 晶界滑移金属材料由多个晶粒组成,晶粒之间存在晶界。
晶界是晶粒内部晶格的不连续区域。
当金属受到应力作用时,晶界处的原子会沿着晶界面滑移,从而使晶粒发生形变。
晶界滑移是金属材料塑性变形和断裂的重要机制之一。
3. 裂纹扩展裂纹是金属材料中的缺陷,是断裂的起始点。
当金属受到应力作用时,应力集中在裂纹处,导致裂纹的扩展。
裂纹扩展的机理主要包括塑性扩展和脆性扩展两种形式。
塑性扩展是指裂纹周围发生塑性变形,裂纹沿着塑性区域扩展;脆性扩展是指裂纹周围没有发生塑性变形,裂纹直接沿着晶体的晶面或晶界扩展。
二、金属断裂的典型形貌金属断裂的典型形貌是指金属材料断裂后所呈现出的形态特征。
根据金属断裂的不同性质和机理,金属材料的断裂形貌可以分为韧性断裂、脆性断裂和疲劳断裂等。
1. 韧性断裂韧性断裂是指金属材料在受到较大应力时,发生大量的塑性变形和能量吸收,最终以拉伸断裂为主。
韧性断裂的断口面平滑,有明显的塑性变形迹象,断口两侧呈现出韧带状的纹理。
韧性断裂通常发生在具有良好延展性的金属材料中,如钢材、铝合金等。
2. 脆性断裂脆性断裂是指金属材料在受到较小应力时,发生较少的塑性变形和能量吸收,最终以断裂为主。
脆性断裂的断口面光洁平整,没有明显的塑性变形迹象,断口两侧呈现出晶粒状的纹理。
脆性断裂通常发生在具有较低延展性的金属材料中,如铸铁、高碳钢等。
金属断裂的微观机制及显微特征

金属断裂的微观机制为了阐明断裂的全过程(包括裂纹的生核和扩展,以及环境因素对断裂过程的影响等),提出种种微观断裂模型,以探讨其物理实质,称为断裂机制。
属于不同断裂机制的断裂,其断口微观结构各具有独特的形貌特征。
基本断裂机制的典型微观形貌:a沿晶脆性断裂 b 解理断裂c 准解理断裂 d 韧窝断裂] 属于不同基本断裂机制的断口所观察到的典型微观形貌,其物理本质和断口特征为:沿晶脆性断裂是指断裂路径沿着不同位向的晶界(晶粒间界)所发生的一种属于低能吸收过程的断裂。
根据断裂能量消耗最小原理,裂纹的扩展路径总是沿着原子键合力最薄弱的表面进行。
晶界强度不一定最低,但如果金属存在着某些冶金因素使晶界弱化(例如杂质原子P、S、Si、Sn等在晶界上偏聚或脱溶,或脆性相在晶界析出等等),则金属将会发生沿晶脆性断裂。
沿晶脆性断裂的断口特征是:在宏观断口表面上有许多亮面,每个亮面都是一个晶粒的界面。
如果进行高倍观察,就会清晰地看到每个晶粒的多面体形貌类似于冰糖块的堆集,故有冰糖状断口之称;又由于多面体感特别强,故在三个晶界面相遇之处能清楚地见到三重结点。
沿晶脆性断裂的发生在很大程度上取决于晶界面的状态和性质。
实践表明,提纯金属,净化晶界,防止杂质原子在晶界上偏聚或脱溶,以及避免脆性第二相在晶界析出等,均可以减少金属发生沿晶脆性断裂的倾向。
因此,应用X射线能谱分析法和俄歇电子能谱分析法确定沿晶断裂面的化学成分,对从冶金因素来认识材料的致脆原因,提出改进工艺措施有指导意义。
微观形态:在沿晶脆性断口上,几乎没有塑性变形的痕迹或仅看到极少的韧窝。
例如,过烧后的断口,就是沿晶界氧化物薄膜发生的一种沿晶脆性断裂。
另外,18-8奥氏体不锈钢沿晶界大量析出碳化物后,也易产生沿晶脆断;沿晶界化学腐蚀和应力腐蚀(包括氢脆)后产生的断口,也都是沿晶脆性断口。
属于这类断口的还有层状断口和撕痕状断口等。
解理断裂属于一种穿晶脆性断裂,根据金属原子键合力的强度分析,对于一定晶系的金属,均有一组原子键合力最弱的、在正应力下容易开裂的晶面,这种晶面通常称为解理面。
金属疲劳断裂的微观机理分析

金属疲劳断裂的微观机理分析一、金属疲劳断裂的基本概念金属疲劳断裂是指金属材料在受到重复或循环加载作用下,经过一定周期后发生的断裂现象。
这种现象在工程结构中极为常见,对材料的可靠性和安全性构成了严重威胁。
金属疲劳断裂是一个复杂的物理过程,涉及到材料的微观结构、应力状态、加载条件等多种因素。
1.1 金属疲劳断裂的定义与分类金属疲劳断裂通常可以分为低周疲劳和高周疲劳两种类型。
低周疲劳是指在较少的循环次数下,材料因塑性变形累积而发生断裂;而高周疲劳则是在大量的循环加载下,材料在没有明显塑性变形的情况下发生断裂。
此外,根据断裂的微观机制,金属疲劳断裂还可以进一步细分为穿晶断裂和沿晶断裂。
1.2 金属疲劳断裂的影响因素金属疲劳断裂的影响因素众多,包括但不限于材料的化学成分、微观组织、晶粒大小、应力集中、加载频率、环境条件等。
这些因素通过不同的机制影响材料的疲劳寿命和断裂行为。
1.3 金属疲劳断裂的研究意义深入研究金属疲劳断裂的微观机理,对于提高工程结构的可靠性、预测和防止疲劳失效具有重要的理论和实际意义。
通过优化材料设计、改进加工工艺、采用合理的加载方式等措施,可以有效延长材料的疲劳寿命,减少因疲劳断裂导致的损失。
二、金属疲劳断裂的微观机理金属疲劳断裂的微观机理是材料科学领域的研究热点之一。
通过对金属疲劳断裂过程中微观结构变化的观察和分析,可以揭示疲劳裂纹的萌生、扩展和最终断裂的内在机制。
2.1 疲劳裂纹的萌生机理疲劳裂纹通常在材料表面或内部的应力集中区域萌生。
在循环加载作用下,材料表面或内部的微观缺陷(如夹杂、孔洞、晶界等)会逐渐发展成为微裂纹。
微裂纹的形成和发展与材料的微观结构、应力状态和加载条件密切相关。
2.2 疲劳裂纹的扩展机理当微裂纹形成后,会在循环应力的作用下逐渐扩展。
疲劳裂纹的扩展过程可以分为三个阶段:裂纹的微观扩展、宏观扩展和快速断裂。
在微观扩展阶段,裂纹主要沿着晶粒内部扩展,受到晶粒取向、位错运动等因素的影响。
第4讲 金属的断裂(断裂类型、裂纹形成理论、断裂强度)

裂纹扩展所需要的能量:Eq.(1-43)
2 s
m
晶体弹性状态下的最大结合力:
1
m
E s
a0
2
Eq.(1-44)
2. 当解理裂纹通过扭转晶界时,因晶界由螺位错组成,其两 侧晶体以边界为公共面转动一小角度,使两侧解理面存在 位向差,故裂纹不能连续通过晶界而必须重新形核,在晶 界处形成新的“河流”,产生河流激增。当裂纹穿过大角 度晶界时也形成大量“河流”。
解理断裂的另一微观特征是舌状花样,因其在电子显微 镜下类似人的舌头而得名。在体心立方金属中,在主解理面 {100}上扩展的裂纹与孪晶面{112}相遇时,裂纹在孪晶处沿 {112}面产生二次解理(即二次裂纹),而孪晶以外的裂纹仍 沿{100}扩展,二次裂纹沿孪晶面扩展,超过孪晶再沿{100} 面继续扩展。因此,获得形似舌头的特征花样。
撕裂棱、韧窝
断口形态 以晶粒为大小, 原奥氏体晶粒大小,呈凹盆状
尺寸
解理平面
三 微孔聚集断裂(韧性断裂)
相对于脆性断裂的微观断口型貌的观察和研究,塑性微孔 聚集型断裂的定义比较模糊。
1. 微孔形核和长大
2. 微孔聚集断裂的微观断口特征
• 主要特征:等轴韧窝、拉长韧窝和撕裂韧 窝三种形貌。
韧窝形貌 a)等轴韧窝 b)拉长韧窝
• The process of brittle fracture consists of three stages(脆断三阶段):
– a. Plastic deformation which involves the pile-up of
–
dbi.sTlohceabtiou裂nildau纹lpono的gf sth形heeiar成rslsi理ptrep论slasnaetsthaet
解理断裂的微观断口特征

解理断裂的微观断口特征
本文将介绍微观断口的特征及其解理方法。
微观断口是指材料在断裂时,断口上显现出的微小细节。
这些细节包括断口的形状、颜色、纹理等,它们能够为我们提供有关材料断裂机理的重要信息。
解理微观断口特征的方法通常包括光学显微镜、扫描电子显微镜等技术。
这些技术能够以高分辨率观察断口上的微小细节,并通过对这些细节的分析来了解材料断裂的原因。
对于金属材料,微观断口通常具有明显的韧窝特征,这是由于材料在断裂前发生局部塑性变形所造成的。
此外,断口上的晶粒也能够提供关于材料强度和断裂韧性的信息。
对于塑料和复合材料等非金属材料,微观断口的特征则与其结构和成分有关。
例如,纤维增强复合材料的断口通常具有明显的纤维撕裂和树脂裂纹特征。
总之,通过解析微观断口的特征,我们能够了解材料的断裂机理,从而指导材料的设计和加工。
- 1 -。
典型的金属沿晶断裂的微观断口

典型的金属沿晶断裂的微观断口一、概述金属材料是工程材料中的重要一类,其力学性能与微观结构密切相关。
在金属材料断裂过程中,沿晶断裂是一种常见现象,其微观断口形貌对材料的力学性能和断裂机制有重要影响。
本文将围绕典型的金属沿晶断裂的微观断口展开讨论。
二、金属沿晶断裂的基本概念1. 沿晶断裂是指金属材料在断裂过程中,裂纹沿晶粒界面扩展,而不是穿过晶粒内部。
沿晶断裂通常发生在结构不均匀、晶粒尺寸较大的金属材料中。
2. 在金属沿晶断裂的过程中,裂纹先经过晶粒边界处的位错团聚区,由于位错堆积和局部应力集中,导致裂纹继续沿晶粒界面扩展。
三、金属沿晶断裂的特征1. 微观断口形貌典型的金属沿晶断裂的微观断口呈现出沿晶晶粒界面扭曲、剥离的特征。
在断口上可以观察到明显的晶粒边界和晶界气孔。
2. 显微组织观察通过金相显微镜等手段观察金属沿晶断裂的微观结构,可以发现断口附近晶粒边界处的位错裙积、晶界气孔等特征。
3. 断口形貌分析沿晶断裂的断口形貌具有一定的规律性,可以通过扫描电镜等手段对其进行形貌分析和特征识别。
四、金属沿晶断裂的影响因素1. 晶界特征金属晶界的取向、结构和清晰度等特征对沿晶断裂的发生和扩展起着重要作用。
2. 应力状态外界加载条件对金属沿晶断裂的影响很大,尤其是在动态加载条件下,应力波的传播对沿晶裂纹的扩展有重要影响。
3. 化学成分金属材料的化学成分会影响晶界的稳定性和塑性变形行为,进而影响沿晶裂纹的扩展路径和形貌。
五、典型案例分析通过对金属材料沿晶断裂的典型案例进行分析,可以更深入地理解其微观断口特征和力学性能表现。
六、结论金属沿晶断裂是金属材料断裂中常见的一种形式,其微观断口特征对材料的力学性能和断裂机制有重要影响。
深入研究金属沿晶断裂的微观特征和影响因素,有助于提高金属材料的力学性能和断裂韧性。
以上是关于典型的金属沿晶断裂的微观断口的相关内容,希望对您有所帮助。
金属材料是目前工程领域中被广泛应用的一种材料,其力学性能和断裂行为对于工程结构的安全性和可靠性至关重要。
典型断裂的微观分析

实验二典型断口的电子显微分析1.概述断口是断裂失效中两断裂分离面的简称。
由于断口真实地记录了裂纹由萌生、扩展直至失稳断裂全过程的各种与断裂有关的信息。
因此,断口上的各种断裂信息是断裂力学、断裂化学和断裂物理等诸多内外因素综合作用的结果,对断口进行定性和定量分析,可为断裂失效模式的确定提供有力依据,为断裂失效原因的诊断提供线索。
断口金相学不仅能在设备失效后进行诊断分析,还可为新产品、新装备投入使用进行预研预测。
断口、裂纹及冶金、工艺损伤缺陷分析是失效分析工作的基础。
实践证明,没有断口、裂纹及损伤缺陷分析的正确诊断结果,是无法提出失效分析的准确结论的。
采用扫描电镜可对金属断裂典型断口形貌进行观察,还可对其微区成分进行分析。
本实验具体内容为:利用二次电子成像,观察金属断裂典型断口形貌,了解典型断口的微观特征.的成分差别。
2.实验目的(1)熟悉二次电子成像观察方法,了解金属材料典型断口形貌特征:(2)掌握双相不锈钢冲击断口形貌特征;(3)掌握X70钢疲劳断口形貌特征。
3.实验装置及材料(1)扫描电子显微镜(JSM-6390A型)一台;(2)超声清洗仪一台;(3)断口试样若干;(4)放大镜一只;(5)吹风机一只;(6)无水酒精若干。
4.实验原理4.1金属材料典型断口特征:(1)断口宏观形貌特征在实际失效分析中, 按断口的表面宏观变形分类,断口分为脆性断口、韧性(延性)断口、韧-脆混合断口;按断裂类型分类,则分为解理断裂、准解理断裂、韧性断裂、疲劳断裂、沿晶断裂等。
对韧性金属材料一次过载造成的韧性断裂,宏观上的基本特征通常表现为三个特征区,即纤维区、放射区和剪切唇区。
这三个特征区是断口的三要素。
表13-1列出了几种典型断口的宏观形貌特征,根据这些特征,可诊断出断口的宏观类型。
表13-1 典型断口的宏观形貌特征(2)断口微观形貌特征按断口表面微观形貌分类,断口分为解理断口、准解理断口、韧窝断口、疲劳断口、沿晶断口等。
金属断裂的微观机理与典型形貌

金属断裂的微观机理与典型形貌金属断裂是指金属材料在受到外力作用下发生破裂的现象。
金属断裂具有微观机理与典型形貌,这些机理与形貌的研究对于金属材料的设计和应用具有重要意义。
金属材料的断裂主要有两种机制:韧性断裂和脆性断裂。
韧性断裂是金属材料在外力作用下发生塑性变形后断裂,具有较大的断口伸长率和断口收缩面积。
脆性断裂则是金属材料在外力作用下发生无明显塑性变形而迅速断裂,具有较小的断口伸长率和断口收缩面积。
金属材料的断裂机理与其晶体结构和微观缺陷密切相关。
金属材料的晶体结构是由原子通过原子键结合而成的,其中包含晶粒、晶界和位错。
当金属材料受到外力作用时,原子之间的键会受到拉伸、剪切等力的作用,从而导致晶界滑移、位错运动等塑性变形。
当外力继续增大时,晶界和位错可能无法继续运动,从而导致金属材料的断裂。
金属材料的断裂形貌可以通过金属断口的观察来研究。
金属断口通常包括拉伸断口、韧窝和脆窝等不同形貌。
拉伸断口是金属在拉伸过程中发生断裂后的断口形貌,通常呈现出光洁的平面面貌。
韧窝是金属在韧性断裂过程中形成的圆形凹陷,它是由于金属在拉伸过程中发生局部塑性变形而形成的。
脆窝则是金属在脆性断裂过程中形成的不规则凹陷,它是由于金属在受到外力作用下迅速断裂而形成的。
金属断裂的微观机理与典型形貌对于金属材料的设计和应用具有重要意义。
通过研究金属断裂机理,可以了解金属材料在外力作用下的变形和破裂行为,从而指导金属材料的合理设计和使用。
同时,通过观察金属断口的形貌,可以评估金属材料的断裂韧性和脆性,为金属材料的选择和应用提供依据。
金属断裂具有微观机理与典型形貌。
金属材料的断裂机理与其晶体结构和微观缺陷密切相关,包括晶粒、晶界和位错等。
金属材料的断裂形貌可以通过金属断口的观察来研究,包括拉伸断口、韧窝和脆窝等不同形貌。
金属断裂的微观机理与典型形貌对于金属材料的设计和应用具有重要意义,可以指导金属材料的合理设计和使用。
通过研究金属断裂机理和观察金属断口的形貌,可以评估金属材料的断裂韧性和脆性,为金属材料的选择和应用提供依据。
金属断裂机理(完整版)
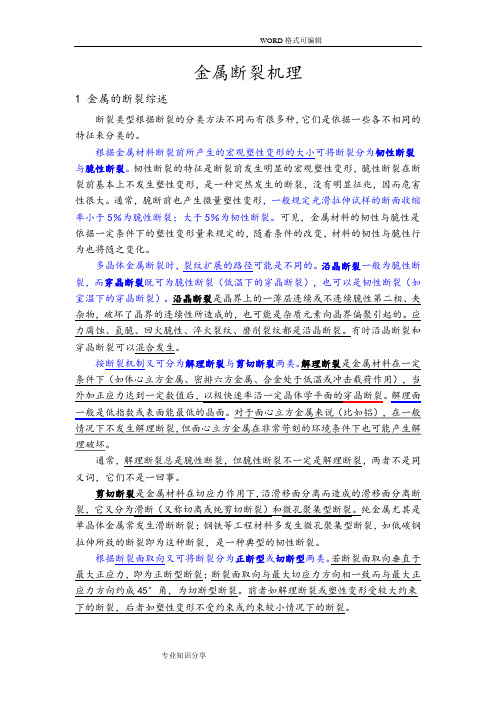
金属断裂机理1 金属的断裂综述断裂类型根据断裂的分类方法不同而有很多种,它们是依据一些各不相同的特征来分类的。
根据金属材料断裂前所产生的宏观塑性变形的大小可将断裂分为韧性断裂与脆性断裂。
韧性断裂的特征是断裂前发生明显的宏观塑性变形,脆性断裂在断裂前基本上不发生塑性变形,是一种突然发生的断裂,没有明显征兆,因而危害性很大。
通常,脆断前也产生微量塑性变形,一般规定光滑拉伸试样的断面收缩率小于5%为脆性断裂;大于5%为韧性断裂。
可见,金属材料的韧性与脆性是依据一定条件下的塑性变形量来规定的,随着条件的改变,材料的韧性与脆性行为也将随之变化。
多晶体金属断裂时,裂纹扩展的路径可能是不同的。
沿晶断裂一般为脆性断裂,而穿晶断裂既可为脆性断裂(低温下的穿晶断裂),也可以是韧性断裂(如室温下的穿晶断裂)。
沿晶断裂是晶界上的一薄层连续或不连续脆性第二相、夹杂物,破坏了晶界的连续性所造成的,也可能是杂质元素向晶界偏聚引起的。
应力腐蚀、氢脆、回火脆性、淬火裂纹、磨削裂纹都是沿晶断裂。
有时沿晶断裂和穿晶断裂可以混合发生。
按断裂机制又可分为解理断裂与剪切断裂两类。
解理断裂是金属材料在一定条件下(如体心立方金属、密排六方金属、合金处于低温或冲击载荷作用),当外加正应力达到一定数值后,以极快速率沿一定晶体学平面的穿晶断裂。
解理面一般是低指数或表面能最低的晶面。
对于面心立方金属来说(比如铝),在一般情况下不发生解理断裂,但面心立方金属在非常苛刻的环境条件下也可能产生解理破坏。
通常,解理断裂总是脆性断裂,但脆性断裂不一定是解理断裂,两者不是同义词,它们不是一回事。
剪切断裂是金属材料在切应力作用下,沿滑移面分离而造成的滑移面分离断裂,它又分为滑断(又称切离或纯剪切断裂)和微孔聚集型断裂。
纯金属尤其是单晶体金属常发生滑断断裂;钢铁等工程材料多发生微孔聚集型断裂,如低碳钢拉伸所致的断裂即为这种断裂,是一种典型的韧性断裂。
根据断裂面取向又可将断裂分为正断型或切断型两类。
金属的断裂条件及断口
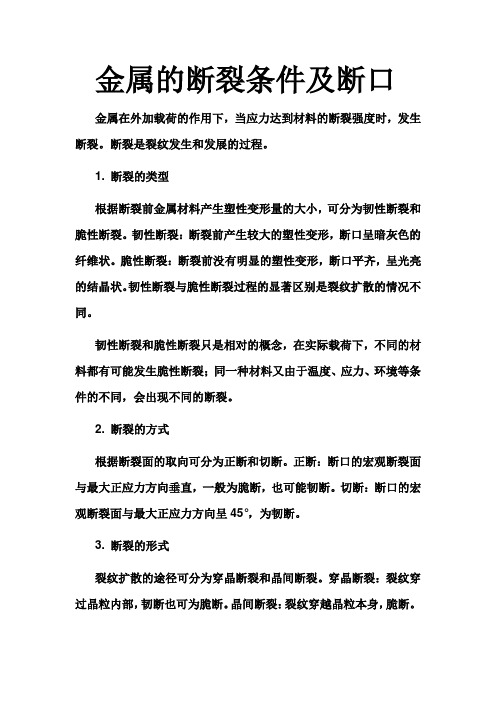
金属的断裂条件及断口金属在外加载荷的作用下,当应力达到材料的断裂强度时,发生断裂。
断裂是裂纹发生和发展的过程。
1. 断裂的类型根据断裂前金属材料产生塑性变形量的大小,可分为韧性断裂和脆性断裂。
韧性断裂:断裂前产生较大的塑性变形,断口呈暗灰色的纤维状。
脆性断裂:断裂前没有明显的塑性变形,断口平齐,呈光亮的结晶状。
韧性断裂与脆性断裂过程的显著区别是裂纹扩散的情况不同。
韧性断裂和脆性断裂只是相对的概念,在实际载荷下,不同的材料都有可能发生脆性断裂;同一种材料又由于温度、应力、环境等条件的不同,会出现不同的断裂。
2. 断裂的方式根据断裂面的取向可分为正断和切断。
正断:断口的宏观断裂面与最大正应力方向垂直,一般为脆断,也可能韧断。
切断:断口的宏观断裂面与最大正应力方向呈45°,为韧断。
3. 断裂的形式裂纹扩散的途径可分为穿晶断裂和晶间断裂。
穿晶断裂:裂纹穿过晶粒内部,韧断也可为脆断。
晶间断裂:裂纹穿越晶粒本身,脆断。
机器零件断裂后不仅完全丧失服役能力,而且还可能造成不应有的经济损失及伤亡事故。
断裂是机器零件最危险的失效形式。
按断裂前是否产生塑性变形和裂纹扩展路径做如下分类。
韧性断裂的特征是断裂前发生明显的宏观塑性变形,用肉眼或低倍显微镜观察时,断口呈暗灰色纤维状,有大量塑性变形的痕迹。
脆性断裂则相反,断裂前从宏观来看无明显塑性变形积累,断口平齐而发亮,常呈人字纹或放射花样。
宏观脆性断裂是一种危险的突然事故。
脆性断裂前无宏观塑性变形,又往往没有其他预兆,一旦开裂后,裂纹迅速扩展,造成严重的破坏及人身事故。
因而对于使用有可能产生脆断的零件,必须从脆断的角度计算其承载能力,并且应充分估计过载的可能性。
. 金属材料产生脆性断裂的条件(1)温度任何一种断裂都具有两个强度指标,屈服强度和表征裂纹失稳扩散的临界断裂强度。
温度高,原子运动热能大,位错源释放出位错,移动吸收能量;温度低反之。
(2)缺陷材料韧性裂纹尖端应力大,韧性好发生屈服,产生塑性变形,限制裂纹进一步扩散。
- 1、下载文档前请自行甄别文档内容的完整性,平台不提供额外的编辑、内容补充、找答案等附加服务。
- 2、"仅部分预览"的文档,不可在线预览部分如存在完整性等问题,可反馈申请退款(可完整预览的文档不适用该条件!)。
- 3、如文档侵犯您的权益,请联系客服反馈,我们会尽快为您处理(人工客服工作时间:9:00-18:30)。
金属断裂的微观机制及显微特征
金属断裂的微观机制为了阐明断裂的全过程(包括裂纹的生核和扩展,以及环境因素
对断裂过程的影响等),提出种种微观断裂模型,以探讨其物理实质,称为断裂机制。
属于不同断裂机制的断裂,其断口微观结构各具有独特的形貌特征。
基本脱落机制的典型微观形貌:a沿晶脆性断裂b霰石脱落c科东俄霰石脱落d韧窝
脱落]属相同基本脱落机制的断口所观测至的典型微观形貌,其物理本质和断口特征为:
沿晶脆性断裂是指断裂路径沿着不同位向的晶界(晶粒间界)所发生的一种属于低能吸
收过程的断裂。
根据断裂能量消耗最小原理,裂纹的扩展路径总是沿着原子键合力最薄弱
的表面进行。
晶界强度不一定最低,但如果金属存在着某些冶金因素使晶界弱化(例如杂
质原子p、s、si、sn等在晶界上偏聚或脱溶,或脆性相在晶界析出等等),则金属将会
发生沿晶脆性断裂。
沿晶脆性断裂的断口特征是:在宏观断口表面上有许多亮面,每个亮面
都是一个晶粒的界面。
如果进行高倍观察,就会清晰地看到每个晶粒的多面体形貌类似于
冰糖块的堆集,故有冰糖状断口之称;又由于多面体感特别强,故在三个晶界面相遇之处
能清楚地见到三重结点。
沿晶脆性断裂的出现在非常大程度上依赖于晶界面的状态和性质。
课堂教学说明,纯
化金属,净化晶界,避免杂质原子在晶界上偏聚或退溶,以及防止脆性第二相在晶界划出等,均可以增加金属出现沿晶脆性断裂的女性主义。
因此,应用领域x射线能谱分析法和俄歇
电子能谱分析法确认沿晶脱落面的化学成分,对从冶金因素去重新认识材料的致脆原因,
明确提出改良工艺措施存有指导意义。
微观形态:在沿晶脆性断口上,几乎没有塑性变形的痕迹或仅看到极少的韧窝。
例如,过烧后的断口,就是沿晶界氧化物薄膜发生的一种沿晶脆性断裂。
另外,18-8奥氏体不锈钢沿晶界大量析出碳化物后,也易产生沿晶脆断;沿晶界化学腐蚀和应力腐蚀(包括氢脆)后产生的断口,也都是沿晶脆性断口。
属于这类断口的还有层状断口和撕痕状断口等。
霰石脱落属一种穿着晶脆性断裂,根据金属原子键合力的强度分析,对于一定晶系的
金属,均存有一组原子键合力最强的、在也已形变下难脱落的晶面,这种晶面通常称作解
理面。
比如:属立方晶系的体心立方金属,其解理面为{100}晶面;六方晶系为{0001};三
角晶系为{111}。
一个晶体如果就是沿着解理面出现脱落,则称作霰石脱落。
面心立方金属
通常不出现霰石脱落(见到晶体结构)。
霰石脱落的特点就是:脱落具备显著的结晶学性质,即为它的脱落面就是结晶学的解理面{},裂纹拓展方向就是沿着一定的结晶方向〈〉。
为了则表示这种结晶学性质,通常用霰石系统{}〈〉去叙述。
对于体心立方金属,已观测
至的霰石系统存有{100},{100}〈011〉等。
霰石断口的特征就是宏观断口十分平缓,而
微观形貌则就是由一系列小裂面(每个晶粒的解理面)所形成。
在每个解理面上可以看见一
些十分吻合于裂纹拓展方向的阶梯,通常称作霰石阶。
解理阶的形态是多种多样的,同金属的组织状态和应力状态的变化有关。
其中所谓
“河流花样”是解理断口的最基本的微观特征。
河流花样解理阶的特点是:支
流霰石阶的合流方向代表脱落的拓展方向;合流角的大小同材料的塑性有关,而霰石
阶的原产面积和霰石阶的高度同材料中势能密度和势能组态有关。
因此,通过对河流花样
霰石阶展开分析,就可以协助我们找寻主脱落源的边线,推论金属的脆性程度,和确认晶
体中势能密度和势能容量。
微观形态:在电子显微镜下观察时,解理断口呈“河流花样”和“舌状花样”。
准解
理断裂也是一种穿晶断裂。
根据蚀坑技术分析表明,多晶体金属的准解理断裂也是沿着原
子键合力最薄弱的晶面(即解理面)进行。
例如:对于体心立方金属(如钢等),准解理
断裂也基本上是{100}晶面,但由于断裂面上存在较大程度的塑性变形(见范性形变),故
断裂面不是一个严格准确的解理面。
准解理断裂首先在回火马氏体等复杂组织的钢中发现。
对于大多数合金钢(如ni-cr钢和ni-cr-mo钢等),如果发生断裂的温度刚好在延性-
脆性转变温度的范围内,也常出现准解理断裂。
从断口的微观形貌特征来看,在准解理断
裂中每个小断裂面的微观形态颇类似于晶体的解理断裂,也存在一些类似的河流花样,但
在各小断裂面间的连结方式上又具有某些不同于解理断裂的特征,如存在一些所谓撕裂岭等。
撕裂岭是准解理断裂的一种最基本的断口形貌特征。
准解理断裂的微观形貌的特征,
在某种程度上反映了解理裂纹与已发生塑性变形的晶粒间相互作用的关系。
因此,对准解
理断裂面上的塑性应变进行定量测量,有可能把它同断裂有关的一些力学参数如:屈服应力、解理应力和应变硬化参数等联系起来。
微观形态:在电子显微镜和扫描电镜下观测,断口通常就是由大量韧窝相连接而变成的。
每个韧窝的底部往往存有着第二二者(包含非金属夹杂着)质点。
第二二者质点的尺
寸离大于韧窝的尺寸。
韧窝断裂金属多晶材料的断裂,通过空洞核的形成长大和相互连接的过程进行,这种
断裂称为韧窝断裂(dimplefracture)韧窝断裂是属于一种高能吸收过程的延性断裂。
其断
口特征为:宏观形貌呈纤维状,微观形态呈蜂窝状
脱落面就是由一些细小的窝坑形成,窝坑实际上就是长大了的空洞核,通常称作韧窝,它就是韧窝脱落的最为基本形貌特征和辨识韧窝脱落机制的最为基本依据。
系统的观测说明,韧窝的尺寸和深度同材料的延性有关,而韧窝的形状则同毁坏时的形变状态有关。
由
于形变状态相同,适当地在相互相匹配的断口偶合面上,其韧窝形状和相互相匹配关系就
是相同的。
微观形态:在断口表面可看到许多位向不同、无金属光泽的“小棱面”或“小平面”。
这些“小棱面”或“小平面”的尺寸与晶粒尺寸相对应(如果晶粒细小,则断口表面上的“小棱面”或“小平面”用肉眼就不能看到或不明显)。
在电子显微镜下观察“小校面”
或“小平面”,它是由大量韧窝组成的,韧窝底部往往存在有第二相质点(或薄膜)。
由于韧窝的形状与形变状态密切相关,故对断口耦合面上二者压板部位的韧窝形状、尺寸和深度展开分析,就可以确认脱落时所在部位的形变状态和裂纹拓展的方向,并对材料的延性展开评价。
除了其他脱落的机制例如:烦躁、塑性和形变
微观断裂机制的实际应用作为材料断裂韧性指标之一的裂纹扩展阻力,它不但是一个材料常数,而且也同断裂的微观机制有关。
例如:当断裂机制是沿晶脆性断裂或解理断裂时,值较小;反之,当断裂机制是韧窝断裂时,则值较大。
脱落微观机制的分析,有可能把断口的形貌分析同断裂力学指标联系出来,其中最重要的成果之一就是系统地创建了脱落机制图,这对化解一些工程脱落问题十分有价值。
所谓脱落机制图,就是指挑选适度的脱落参数、力学参数或物理参数做为坐标系,用它去奠定各种可能将发生的微观脱落机制的区域,以便辨认出各类金属脱落的普遍规律。
在工程应用领域上,脱落机制图对工程设计,材料的挑选,采用条件的管制,以及失灵分析等都能够提供更多十分关键的指导性意见和数据资料,目前正大力开展这方面的工作。
上面介绍的断口微观形态,是按照断裂的途径来分类的。
而实际生产中见到的断口有时往往是由几种类型并存的混合断口。
例如,石状断口中,如果“小棱面”或“小平面”不是贯穿整个断面,断口常常是沿晶和穿晶混合断口。
在实际生产中根据瑕疵断口的宏观形貌和微观形态就可以推论出来瑕疵的类型、瑕疵产生的原因和应当实行的对策。