制程不良品处理流程图
不合格品处理流程图
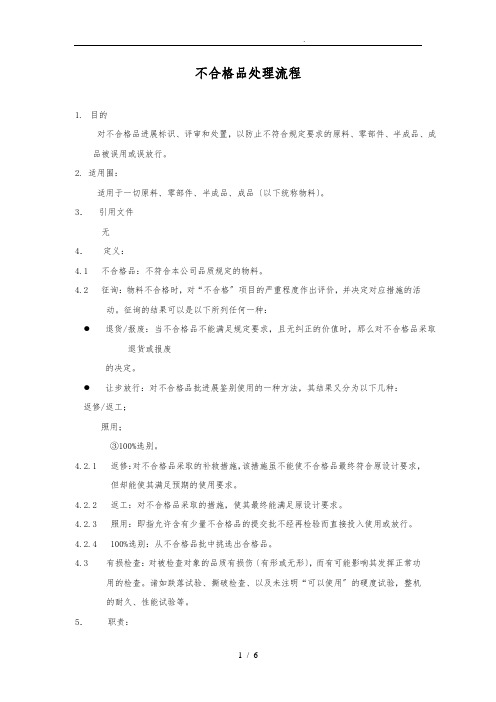
不合格品处理流程1.目的对不合格品进展标识、评审和处置,以防止不符合规定要求的原料、零部件、半成品、成品被误用或误放行。
2. 适用围:适用于一切原料、零部件、半成品、成品〔以下统称物料〕。
3.引用文件无4.定义:4.1不合格品:不符合本公司品质规定的物料。
4.2征询:物料不合格时,对“不合格〞项目的严重程度作出评价,并决定对应措施的活动。
征询的结果可以是以下所列任何一种:●退货/报废:当不合格品不能满足规定要求,且无纠正的价值时,那么对不合格品采取退货或报废的决定。
●让步放行:对不合格品批进展鉴别使用的一种方法,其结果又分为以下几种:返修/返工;照用;③100%选别。
4.2.1返修:对不合格品采取的补救措施,该措施虽不能使不合格品最终符合原设计要求,但却能使其满足预期的使用要求。
4.2.2返工:对不合格品采取的措施,使其最终能满足原设计要求。
4.2.3照用:即指允许含有少量不合格品的提交批不经再检验而直接投入使用或放行。
4.2.4100%选别:从不合格品批中挑选出合格品。
4.3有损检查:对被检查对象的品质有损伤〔有形或无形〕,而有可能影响其发挥正常功用的检查。
诸如跌落试验、撕破检查、以及未注明“可以使用〞的硬度试验,整机的耐久、性能试验等。
5.职责:5.1 品质部:●对不合格品进展标识、隔离;●对经返修/返工的物料进展再检验;并予以判断。
●参与“征询〞工作。
5.2 物控专员:●参与“征询〞工作;●安排返工/返修等事宜。
●将不适用的原料/零部件退回供给商;●安排供给商补料,对供给商进展经济等各方面约束。
●加强供给商管理、辅导、考核5.3 生产部门:对在制程中发现的不合格零部件、半成品进展回收隔离,并且以红色作明确的标注;●挑选、返修/返工遭品质检查人员(IQC\IPQC\FQC\QA)拒收之产品;●参与“征询〞;●针对本部门制造的不合格品申请进展征询。
5.5开发部:●参与“征询〞。
6.程序:6.1进料“不合格〞的处理〔IQC〕。
不良品处理流程图
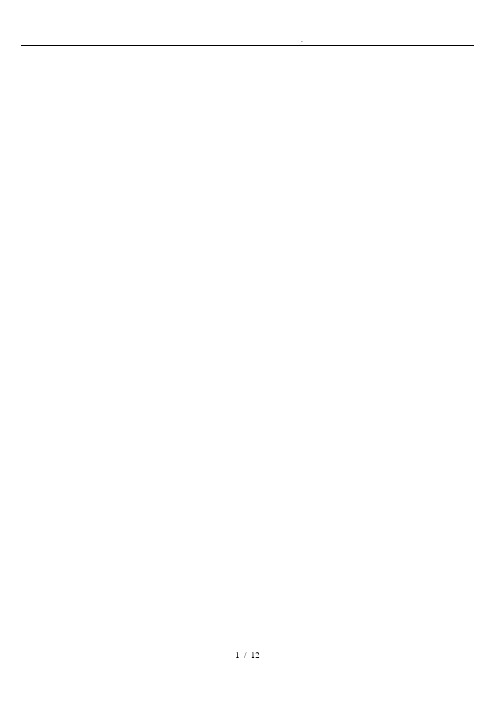
5.10.4IQC收到退料单,在没有急料的情况下须在2个工作小时全检〔在IQC现有设备可完成确
认〕,在全检过程中如检验到制程不良、包装方式不符、标识错误、误判、标识不清晰〔料
号、供给商〔客户〕、数量、不良标识、不良容、不良率〕、拉长/IPQC未签名确认等,
市XXXX
〔三级文件〕
文件名称:不良品处理流程
文件编号:CT-QC-XXXX版 本/次:B/1
制/修日期:2013年7月29日生效日期:2013年7月29
文件会签部门
会 签 人
文件会签部门
会 签 人
□人资部
■电源部
□品管部
□技术部
□市场部
□财务部
■单板生产部
□采购部
■整机生产部
□后勤部
■SMT部
□货仓部
5.9.2每天QC 日报表记录的不良总数量与维修工站的维修日报表统计数量相符。品管IPQC每天稽查此项容。如不相符计缺失项并追踪改善。
5.10 不良品退仓
5.10.1产线在每个投产工位,在上线时挑出的原材料不良,放置规定区域,IPQC与拉长在物料员开单退料前,针对原材料不良全检确认并做好标识,在退料单上签名。
注:所有测试发现的不良品,不可进展第二次测试。
5.2.4外观检验工站发现产品不良现象,用红色箭头标或美纹纸对不良部位进展标识,然后将不良品放入不良区域,并立即在QC 日报表作好相应记录。
5.2.5当检验连续3PCS不良时,应与时反应拉长&IPQC。
5.2.6各工序作业员不可私自维修不良品。
市XXXX
2.适用围:
适用于公司制程不良品、OQC验出不良品和客户检出不良品与不良品维修管制。
制程检验不合格品处理流程图
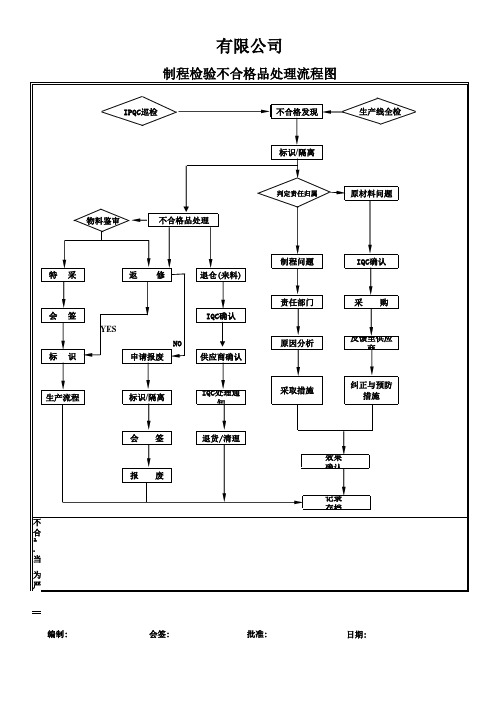
制程检验不合格品处理流程图
IPQC巡检 不合格发现 生产线全检
标识/隔离
判定责任归属
原材料问题
物料鉴审
不合格品处理
制程问题 特 采 返 修 退仓(来料) 责任部门 会 签 YES NO 标 识 申请报废 供应商确认 原因分析 IQC确认
IQC确认
采
购
反馈至供应商
生产流程
标识/隔离
IQC处理通知
采取措施
纠正与预防 措施
会
签
ቤተ መጻሕፍቲ ባይዱ
退货/清理 效果确认
报
废 记录存档
不合格品处理说明: 1.当某项不合格品数量超过“停机整改要求”的条件时,则必须要求生产进行停机调试,当异常较 为严重或必要时须以<品质异常通知单>形通知生产单位停机整改。
编制:
会签:
批准:
日期:
不良品退货流程(含图)

不良品退货流程首先,品质部先要明确不合格品的产生原因:是工废、还是料废。
工废的话就要追究生产部门责任,料废的话就要找供应商,同时加强进料检验。
生产开出退料单----品管确认-------生产人员退仓----仓库通知采购------采购通知供应商。
原因是什么在退仓时都应该注明,只是仓库与采购沟通过程中有问题,因为程序中没有规定要以什么方式来沟通(也就是没有特定的单据),采购的制度就是没有书面性的文件就不受理。
在和供应商签订采购合同时,先把这些售后退货问题解决好。
来料,制程,出货后出现不良品如何处理都要先协商好。
检验中挑选的不良品,由品管退仓库,并通知采购找供应商来收货。
仓库退货给供应商后,将数量的明细给采购扣款。
来料,制程,出货后出现不良品如何处理都要先协商好。
制造过程中挑选的不良品,由生产部门退仓库,仓库通知品管来检验,品管开出料废单据,仓库通知采购退货给供应商,将退料数量明细给采购扣款。
其实在不良品处理问题上需要两个方面来做的:A1.返工、返修品由检验员直接退回生产拉线,由生产部门自行安排处理。
[这样做有两个好处:生产部门可以根据自己的生产计划安排返工返修,而不会与正常生产发生过多冲突;返工返修品也要算在当日产量里,生产部门为完成当天产量自然会在当天完成返工返修品的工作],品管部门只需要每天统计相关数据,制定出改善措施要求生产部门执行就好了。
2.报废品[包括返修时产生的报废零件],必须由品管部门确认,并经评审会批准才可报废,最好要有一套《废品考核奖罚制度》,这样可以让生产部门自行评估报废的成本的[因为与他们的薪资挂钩了],从根本上可以让报废品降低的。
品保(品质保证员)与品管分开的,并且是实行的生产部门全检,品保抽检的方式.我们这边出现不良品,生产线先找工程分析原因。
B1.原因是作业不良,生产线自己返工,是能追查到那段工序的。
所以责任容易区分。
能返工就返工,不能返的,一律报废!2..不良比例为%比,那直接禁用该周期该供应商产品,换另一供应商产品使用。
ISO9001不合格品控制程序(含流程图)
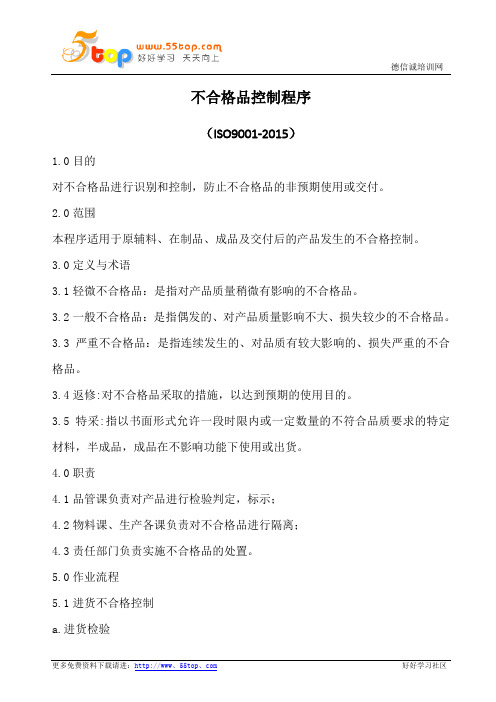
不合格品控制程序(ISO9001-2015)1.0目的对不合格品进行识别和控制,防止不合格品的非预期使用或交付。
2.0范围本程序适用于原辅料、在制品、成品及交付后的产品发生的不合格控制。
3.0定义与术语3.1轻微不合格品:是指对产品质量稍微有影响的不合格品。
3.2一般不合格品:是指偶发的、对产品质量影响不大、损失较少的不合格品。
3.3严重不合格品:是指连续发生的、对品质有较大影响的、损失严重的不合格品。
3.4返修:对不合格品采取的措施,以达到预期的使用目的。
3.5特采:指以书面形式允许一段时限内或一定数量的不符合品质要求的特定材料,半成品,成品在不影响功能下使用或出货。
4.0职责4.1品管课负责对产品进行检验判定,标示;4.2物料课、生产各课负责对不合格品进行隔离;4.3责任部门负责实施不合格品的处置。
5.0作业流程5.1进货不合格控制a.进货检验检验人员依据原物料检验标准、工程图纸、顾客要求等进行检验,判定为不合格品时开《品质异常处理单》并填写相关异常信息并附上不合格样品一并交给品管课长审核和管理部经理批准后扫描发邮件给采购课、生管课、物料课。
b.标示隔离进料不合格品由品管课检验人员进行标示,物料课人员将产品移至不合格品区域进行隔离。
c.不合格品处理1.退货:由物料课开具《退货单》,经品管、仓管确认后,经物料课长审核后通知采购课在7日内退货,若超出期限由我司自行处理。
当同一供应商因产品连续有2批因同样质量被拒收时,品管课开出《纠正和预防措施单》交采购课处理。
2.挑选使用:由采购课通知供应商,确定挑选方式:(1)由供应商进行挑选,挑选后的原物料须由品管课重新检验合格后方可入库使用;(2)由我公司安排物料课全检组人员进行挑选,挑选后的原物料须由品管课重新检验合格后方可入库使用;3.特采接收:在生产急需或紧急出货的情况下不影响安全,功能或结构的不合格品由采购课填写《品质异常处理单》交相关单位会审后由管理部经理核准后方可特采,同时品管员于该批产品上加贴“进料特采标签”;4.报废:制程中发现无法使用的来料不良品(含特采物料),由采购课与供应商沟通处理方式,物料课接收到可报废处理邮件或已扣款的财务部确认签署后开立《报废单》经资材部经理审核、副总核准后进行报废;5.不合格品的处理期限要求:采购课接单后需在24H内签回。
不合格品控制程序(含流程图)

5.1 品管:对不合格品标示及隔离,不合格品的确认,组织对不合格品进行评审,通知相关部门对不合格品进行处理,对返工品的重新检验;负责记录及归档不合格品处理的相关记录。
5.2采购:负责原物料特采提出及特采申请单的开立和特采物料的跟踪执行,负责来料不合格品的处理实施(退货、换货等),向供应商反馈产品的不合格信息及供应商品质改进跟踪。
文件制修订记录
NO
制/修订日期
修订编号
制/修订内容
版本
页次
1
2022-08-01
全新制订
01
制订
会审
核准
仓库
总经理
生产
人力资源
1.目的:
为使不符合要求的产品和服务处于受控状态,得到识别和控制,防止其非预期的使用或交付,确保公司产品及服务质量,特建此程序文件。
2.适用范围:
适用于本公司进料(原物料)、制程(半成品)、成品出货过程所发现的不合格品管制。
6.6特采提出时机(包括但不限于):
A、急于使用之材料,不良情形不会影响生产进程且不产生主要及致命缺点时。
B、生产过程中产生的或客户急于使用之产品,其不良状况经客户同意时。
C、客户急于使用之产品,仅为轻微之缺陷且不影响客户使用时。
6.7不合格成品降级提出时机:
A、不合格成品能实现部分或全部原设定的功能,符合法规要求,但无法进行特采或返工不经济时。
6.5不合格成品或半成品返工(数量超过100PCS)、报废及成品不合格品降级或特采,由生产填写《不合格品处理申请单》,制程(超过100PCS)或库存品的不良品报废由仓库、品管或生产填写《报废申请申》,提交相关部门会签,最后交总经理批准;对于少于100PCS的返工或少于100PCS的制程不良品报废处理,由供应链经理直接确认及安排实施(不必填写申请单)。
制程品质异常处理流程介绍ppt课件(图文)
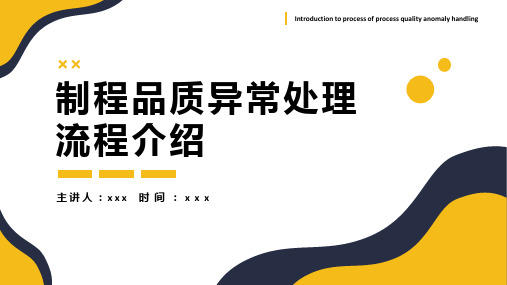
异常产品判定状态:
Please add the detailed description text here
报废
重工
挑选
报废 异常品 挑选
重工
特采
特采
FQC OQC Proces 产品不符合相关检验标准要求,且不良率超 过质量目标时; 严重功能不良时; 客户投诉或抱怨;
TEST Proces 严重功能不良;
戴明循环的优点:
Please add the detailed description text here
3. 戴明循环的优点: 适用于日常管理,且同时适用于个体管理 与团队管理; 戴明循环的过程就是发现问题、解决问题 的过程; 适用于项目管理; 有助于持续改进提高; 有助于供应商管理; 有助于人力资源管理; 有助于新产品开发管理; 有助于流程测试管理。
PDCA循环特点:
Please add the detailed description text here
1、大环带小环。如果把整个企业的工作作为一个大的戴明循环, 那么各个部门、小组还有各自小的戴明循环,就像一个行星轮系 一样,大环带动小环,一级带一级,有机地构成一个运转的体系。 2、阶梯式上升。戴明循环不是在同一水平上循环,每循环一次, 就解决一部分问题,取得一部分成果,工作就前进一步,水平就 提高一步。到了下一次循环,又有了新的目标和内容,更上一层 楼。
主要办法 排列图、直方图、控制图 因果图 排列图,相关图 回答“5W1H” 为什么制定该措施(Why)? 达到什么目标(What)? 在何处执行(Where)? 由谁负责完成(Who)? 什么时间完成(When)? 如何完成(How)?
排列图、直方图、控制图 制定或修改工作规程、检查规程及其 它有关规章制度
制程不良品处理流程

制程不良品处理流程
一、检测阶段
1.进行产品检测
(1)使用检测设备进行检测
(2)检测产品参数和质量要求
2.发现不良品
(1)标记不良品
(2)记录不良品数量和类型
二、不良品分类
1.临时不良品
(1)暂时隔离不良品
(2)等待处理决策
2.可修复不良品
(1)判断不良品是否可以修复
(2)安排维修人员处理
3.废品
(1)判断不良品无法修复或达不到质量标准(2)标记废品并丢弃
三、处理流程
1.临时不良品处理
(1)召开问题分析会议(2)制定解决方案
2.可修复不良品处理(1)完成维修
(2)重新检测质量
3.废品处理
(1)按规定流程处理废品(2)记录废品处理信息
四、改进措施
1.分析不良品原因
(1)进行根本原因分析(2)制定改进措施计划2.实施改进措施
(1)更新制程流程
(2)培训相关人员
3.监控改进效果
(1)持续监测不良率
(2)反馈改进效果。
不良品异常处置业务流程图

2-5 业务名:产品修正实施流程 部门名:唐山爱信品质G 会议体 检查作业部门
(责任 者) [责任部
不良品异常处置业务流程图
相关部门
步骤
票据类
(责任者) [责任部门]
厂家、制造部门 生产技术部门 申请部门
修理品
检查管理部门
标准类 规程类
工序内(慢
突发
①产品修正 申请书 不合格品处理 (慢性不良) 程序 (TL 科长) [申请部门] ②修正要领书 (TL 科长) [申请部门] ③管理帐簿 (TL 科长) [品质保证部] ④产品修正
唐山爱信品质g厂家制造部门生产技术部门责任者责任部责任者责任部门tl科长申请部门tl科长申请部门tl科长品质保证部tl科长申请部门步骤不良品异常处置业务流程图修理品工序内慢性不良突发不修正申请发行样式1修正申请发行样式3修正申请发行样式接收结果联络复印发放产品修正实施修正检查内容确认结果确认裁决批准者
③ ①② 修正申请发 修正申请发 行 行 修正申请发 行
(①复印添附)
④
接收
申请书
(突发不良) (TL 科长) [申请部门]
①②③ 内容确认 NO YES ①③ 结果联络 ①②③ 产品修正实施 NG ①③④
流动
NO 仅①③ 复印发放 ①③ 修正检查
OK
结果确认 裁决 ①②③复印保管
不合格品控制流程图(最完善、最经典)

采购部/业务外购/生产车间/品质部/业务部
品质部
采购/业务外购/生产车间/品质部/物控部/业务部/副总经办
品质部/生产/责任单位
采购/车间/品质部
车间/采购/仓管课
品质部
仓管课/采购部
6—8.品质出具挑选/加工/返工文件或封样,由生产或责任单位落实。
9-12.采购/车间重新送检,品质抽样检验,并根据检验结果贴绿标或红标。
13.合格品由责任单位办理入库或流转手续,不合格品返回处理.
14-16.让步或降级使用,由品质更换特采标识((注明让步/降级项目)再流转。
17—19。评审退货的由仓管课开立退货单并知会采购通知供应商。
LoGO
XXX有限公司
编号
QP—XX-XX
版次
B1版
不合格品控制流程图
页码
1/1
发行日期
201பைடு நூலகம்—5-6
流程图
流程说明
权责部门/单位
文件/表单
1—3。外购不合格品包括原材料、辅料、委外加工产品;制程不合格品指从原料投入到包装成品之前,包装后产品。
4.品质部负责不合格品标识,仓库/车间负责隔离。
5。外购不合格品由采购/业务外购提出评审,制程或成品不合格品由品质部或生产提出评审。
20-22.评审报废的由责任单位开立报废送检单送报废检验员确认,将可修与不可修分捡出来。
23-24将可修品修好再送检,不可修品由报废检验员开立报废单送领导审批后移至废品仓库,并作好数据记录。
25-26。由品质组织召开不合格分析改进会议,拟定纠正预防措施,并落实责任人与时限。
不合格品( HSF)处理流程图ppt课件

• 6.6 不合格品处理方式之定义
• 6.6.1 批退﹙Reject﹚:品保单位检验或接获材 料、半成品、成品及客供品有品质异常、不符需 求状况时,将入料品整批退还委外/供货商或制造 单位,并要求处理之情形。
• 6.6.2 挑选﹙Sorting﹚:当产品经判定,发现有 品质异常不符需求状况时,由委外/供应商或制造 单位整批性重检,将不合格品挑出,以确保质量 优良状态之情形属之。
20
• 6.5.4 资材单位负责对于久存成品及半成品﹙确 定已无可出售机会、逾保存期限或无法重工利用 者﹚,经判定不良需报废时,依流程报废处理。
• 6.5.5 客供品若有质量异常状况发生时,发现单 位须立即以「纠正及预防措施单」反应;业务单 位负责人员则主导通知客户,并告知相关单位客 户允收与否之判定结果或后续应急处理之要求。
• 6.2.2发生HSF不合格时,依上述相关处理程序对HSF不合 格品必须与其它产品和可能使用不符合的部件﹑副材料进 行区分、标识并隔离;一般采取退货或报废的处理方式。 按〈环境限用物质管制程序〉执行纠正措施并立即回报.
• 6.2.3 能够确定部件及副材料的履历、用途或所在,确保 已出货的不合格品能够顺利被召回:
MRB审查 可否重工
业务:客诉、MRB退货品→退货单
生管:委外半成品、成品进料
制造生产检验判退
NG
采购:采购品
批退/报废
作业流程
OK
重工作业申请
生管开出 生产重工单
挑选重工作业
标示区隔
不良状况 所费工时记录
重工需求单
NG 检验
OK
包装入库 保存作业
ppt课件完整
10
5.4维修品作业流程图:
嫌疑不良状态标示 嫌疑不良品隔离
生产线不良或异常处理流程图

正式开出《校正 行为报告》
制订解决方案
生产、工 程、品检
监督生产线作业员按工艺文件作业情况; 用样机校正各测试位,并填写样机校位记录表; 检查各仪器设备运行情况; 每小时填写《工序质量日报表》。
《样机校 位报告》
生产、工 程、品检、 SMT
组长、领班、物料员、IPQC、工程人员、SMT 管 理人员要有问题意识,及时迅速发现异常或不 良,能预见不良或异常产生的影响和后果。 当单项不良低于 3%时,生产管理要及时将不良品 交修理维修,修理将修好的不良品要贴修理编 号,并从第一 QC 位下机。
1. 目的 及时、迅速处理,解决生产过程中阻碍生产顺利进行的各种问题,保证生产的正常运行。
2. 适用范围 生产线不良或异常包括物料、工艺、设备、产品功能、作业及其它方面使生产不能顺利 进行的各种因素。
3. 生产线不良或异常处理流程/职责和工作要求
流程
职责
工作要求
相关文件 /记录
开始 巡线 发现生产 不良或异常
为报告》
程、 品检、 组长、领班、物料员、IPQC、工程人员、SMT 管 《 不 合 格
SMT
理人员开出的《校正行为报告》单要如实反映问 品 控 制 程
题,不得夸大事实。
序》
作业问题应在《校正行为报告》单上描述纠正改
善措施。
设计、物料问题按《不合格品控制程序》执行。
工 程 、 生 修正工艺要求;
产 、 开 发 、 重新修订物料规格要求;
品检
修改设计存在的不完善因素。
流程
NO 评审 方案
YES
职责
工作要求
相关文件 /记录
工程、开 发 、 品 管 、 根据方案的要求进行评审,经技术和品质评估通 品检、生产 过可实施方案,未通过可继续进行分析确认。
不良处理流程图

制程不良处理流程图
制程不良处理流程图
责任单位
表单记录/管控重点
1. 外观检验记录表 2. 电性检验记录表 3. 焊锡检查记录表 红色不良标签 红色不良品框 红色不良周转架
备 注
全检焊点
终检外 观
终检电性
品质/生产
不良品标示
生产
生产干部不良清理确认
生产
1. 2. 3. 4. 1. 2. 3. 4.
对不良品进行判别 不良统计确认 送维修区分析改善 标示组别,名称,数量,不良现象 不良品维修, 电性不良/外观不良区分标示, 不良记录<不良解析表> 标示组别,名称,数量,不良现象
维修工站 NG NG OK IPQC 确认 维修工站
生产
生产/品质
IPQC/生产干部维修 OK 后做判定, 不良重新维修或者直接报废处理. 一律经过维修之产品必须从制程 首工站流入不得直接包装. 1. 不良返修品按照正常测试条 件测试电性,检验外观. 2. 返修品应做特别标示 , 终检终 测人员加严检验.
流入检验工站
砍头品重做/报废
生产
终检/终测
前处理投入
生产
OK生产ຫໍສະໝຸດ 返修 OK 后之成品包装入库
核准: 陈文法
制定:邓江锋
品质不良品的管理流程图
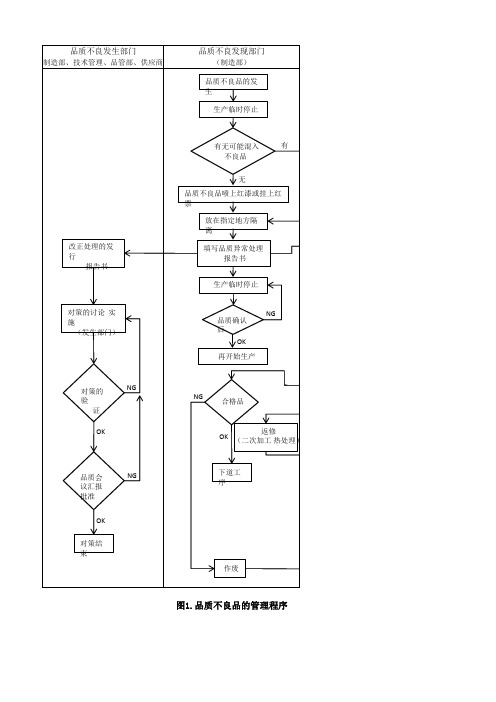
品质不良发生部门 (制造部、技术管理、品管部、供应商)
品质不良发现部门 (制造部)
品质不良品的发 生
生产临时停止
改正处理的发 行
报告书
对策的讨论 实 施
(发生部门)
对策的
NG
验
证
OK
品质会
NG
议汇报
批准
OK
对策结 束
有无可能混入
有
不良品
无 品质不良品喷上红漆或挂上红 票
放在指定地方隔 离
填写品质异常处理 报告书生产临时停止来自品质确认NG后
OK
再开始生产
NG
合格品
返修 OK (二次加工 热处理)
下道工 序
作废
图1.品质不良品的管理程序
品质管理部
追记
确认 过去的品质记 录
品质不良品
品质不良品的识 别
品质不良
NG
品的处理
决定
(品管部)
OK
挑
返修 特采使
退
作废
选
用
货
热处理)
向客户提交特
NG
殊采用申请书
(品管部)
返修件 的检查
OK 下道工 序
OK NG
根据客户要求生 产
出货