第五章 表面组装技术(SMT)与表面组装元器件(SMC、SMD)
SMT基本知识

第一节:SMT概述1.1. 什么是SMT技术表面组装技术(Surface Mounted Technology,简称SMT)又称为表面贴装技术,是指将片式元器件直接装贴、焊接在印制电路板指定位置的自动化装联技术,如图1-1所示。
SMT是在通孔插装技术(Through Hole Technology,简称THT)的基础上发展而来的,从技术角度上讲,SMT是一个复杂的系统工程,它集元器件、印制板、SMT设计、组装工艺、设备、材料和检测等技术,图1-2所示为表面组装技术体系。
表面贴装元件(Surface Mount Components,简称SMC)和表面贴装器件(Surface Mount Devices,简称SMD)是SMT的基础。
基板是元器件互连的结构件,在保证电子组装的电气性能和可靠性方面起着重要作用。
组装工艺和设备是实现SMT产品的工具和手段,决定着生产率和质量成果。
检测技术则是表面组装产品质量的重要保证。
1.2 SMT基本工艺SMT生产工艺一般包括焊膏印刷、贴片、回流焊、检测等四个环节。
SMT生产工艺按元器件的装贴方式可以分为纯SMT装联工艺和混合装联工艺;按线路板元件分布可以分为单面和双面工艺;按元件粘接到线路板上的方法可以分为锡膏工艺和红胶工艺;按照焊接方式可以分为回流焊工艺和波峰焊工艺。
下面主要介绍锡膏工艺和红胶工艺。
1.锡膏工艺先将适量的焊锡膏印刷到印制电路板的焊盘上, 再将片式元器件贴放在印制电路板表面规定的位置上, 最后将贴装好元器件的印制电路板放在回流焊设备的传送带上,从回流焊炉入口到出口,大约需要5分钟就可完成了干燥、预热、熔化、冷却等全部焊接过程。
2.红胶工艺先将微量的贴片胶( 红胶) 印刷或滴涂到印制电路板相应置(注意:贴片胶不能污染印制电路板焊盘和元器件端头) , 再将片式元器件贴放在印制电路板表面规定的位置上, 让贴装好元器件的印制电路板进行胶固化。
固化后的元器件被牢固地粘接在印制电路板上, 然后插装分立元器件, 最后与插装元器件同时进行波峰焊接。
表面组装技术(SMT工艺)
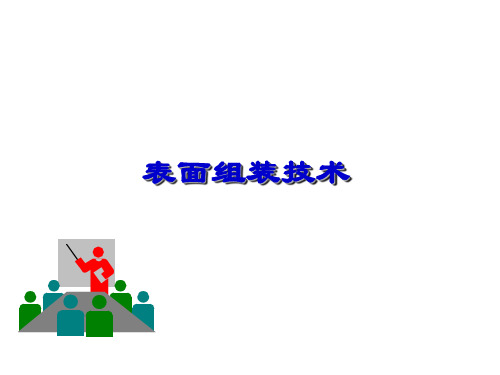
5、与PCB表面非常接近,间隙小,清洗困难。
二、分类: 1、按功能分为三大类(两类:SMC、SMD) 无源元件(SMC):片式电阻、电容、电感等 有源元件(SMD):SOT、SOP、PLCC、QFP、LCCC等
机电元件:异型元件,如继电器、开关、变压器等
2、按结构形状分:薄片矩形、圆柱形、扁平异型
A B
A面回流焊 清洗
B面胶水固化
翻板
B面波峰焊
检测
3.单面混合组装工艺流程
⑴ 先贴法 来料检测 B面点胶
A B
B面贴装元器件
A面插装元器件
B面波峰焊
翻板
检测
B面胶水固化
清洗
3.单面混合组装工艺流程
A B
⑵ 后贴法
来料检测 B面胶水固化 翻板 A面插装元器件 B面贴装元器件 B面波峰焊 检测 翻板 B面点胶 清洗
★ 环境温度
最佳: 23±3 ℃
一般:17~28℃
极限:15~35℃
★ 环境湿度 45%~70%RH
SMT发展趋势
一、绿色化生产 1、无铅焊料,无铅焊接 2、PCB制造过程中不再使用阻燃剂 3、使用无VOC助焊剂
二、元器件的发展 1、无源元件(小型化) 1812 1210 1206 0805 0603 0402 0201 01005 2、有源器件 SOT SOP PLCC QFP BGA CSP FC COB MCM
A
A B A B
4、双面混合组装
① ②
A B A B
二、基本工艺流程(两条
) ※ 先在印制电路板焊盘上印刷适量的焊膏,再将 片式元器件贴放到印制板规定位置上,最后将贴装 好元器件的印制板通过回流炉完成焊接过程。
※ 焊膏-回流焊工艺(表贴元器件)
电子产品制造工艺常用术语

表面组装技术术语1.表面组装元器件surface mounted components/surface mounteddevices(SMC/SMD)外形为矩形片状、圆柱形或异形,其焊端或引脚制作在同一平面内,并适用于表面组装的电子元器件。
同义词:表面安装元器件;表面贴装元器件。
2.表面组装技术surface mount technology(SMT)无需对印制板钻插装孔,直接将表面组装元器贴、焊到印制板表面规定位置上的装联技术。
同义词:表面安装技术;表面贴装技术。
3.表面组装组件surface mounted assemblys(SMA)采用表面组装技术完成装联的印制板组装件。
简称组装板或组件板。
同义词:表面安装组件。
4.再流焊reflow soldering通过重新熔化预先分配到印制板焊盘上的膏状软钎焊料,实现表面组装元器件焊端或引脚与印制板焊盘之间机械与电气连接的软钎焊。
5.波峰焊wave soldering将熔化的软钎焊料,经电动泵或电磁泵喷流成设计要求的焊料波峰,使预先装有电子元器件的印制板通过焊料波峰,实现元器件焊端或引脚与印制板焊盘之间机械与电气连接的软钎焊。
6. 组装密度assembly density单位面积内的焊点数目。
7.矩形片状元器件rectangular chip component两端无引线,有焊端,外形为薄片矩形的表面组装元件。
8.圆柱形表面组装元器件metal electrode face(MELF)component;cylindricaldevices两端无引线,有焊端的圆柱形表面组装元器件。
9.小外形封装small outline package(SOD)小外形模压塑料封装;两侧具有翼开或J形短引线的一种表面组装元器件封装形式。
10.小外形晶体管small outline transistor(SOT)采用小外形封装结构的表面组装晶体管。
11.小外形二极管small outline diode(SOD)采用小外形封装结构的表面组装二极管。
SMT常用术语解读

SMT常用术语解读1、产品Product活动或过程的结果。
如生产企业或科研单位与大专院校向市场或用户以商品形式提供的单一制成品或若干制成品的组合体或研究成果。
2、电路Circuit为达到某种电功能而设计的电子或电气通路的集合体。
3、电子装联Electronic Assembly电子或电器产品在形成中所采用的电连接和装配的工艺过程。
4、穿孔插装元器件THC/THDThrough Hole Components(穿孔插装元件)/Through Hole Devices(穿孔插装器件)一种外形封装,将电极的引线(或引脚)设计成位于轴向(或径向),并插入印制板的引线孔内在另一面与焊盘进行焊接,来实现电连接的电子元件与器件。
其同义词:通孔(或穿孔)组装元器件,通孔(或穿孔)安装元器件。
5、表面贴装元器件SMC/SMDSurface Mount Components(表面贴装元件)/Surface Mount Devices(表面贴装器件)。
一种外形封装,将电极的焊端或短引脚设计成位于同一平面,并贴于印制板的表面在同一面与焊盘进行焊接,来实现电连接的电子元件与器件。
其同义词:表面组装元器件、表面安装元器件、表面粘装元器件。
6、印制板PCBPrinted Circuit Board,以绝缘层为基材,将导电层以印刷蚀刻制作形成电气通络走线与焊盘的印制电路或印制线路成品板的通称。
材质上可分刚性、柔性以及刚一柔性等,印制电路上可分单面板、双面板与多层板等。
7、表面贴装印制板SMBSurface Mount Board,用于装焊表面贴装元器件的印制板。
由于SMT应用程度与水平的不同,这种印制板常常有贴插混凝土装与全贴装的两种。
该类印制板对于耐热性、可焊性、绝缘性、抗剥离强度、平整性/翘曲度、制作精确度与工艺适应性等各项指标要求明显高于全插装印制板。
8、通孔插装技术THTThrough Hole Technology,一种需要对焊盘进行钻插装孔,再将引线(或引脚)位于轴向(或径向)的电子元器件(即通孔插装元器件)插入印制板的焊盘孔内并加以焊接,与导电图形进行电连的电子装联技术。
表面组装技术术语
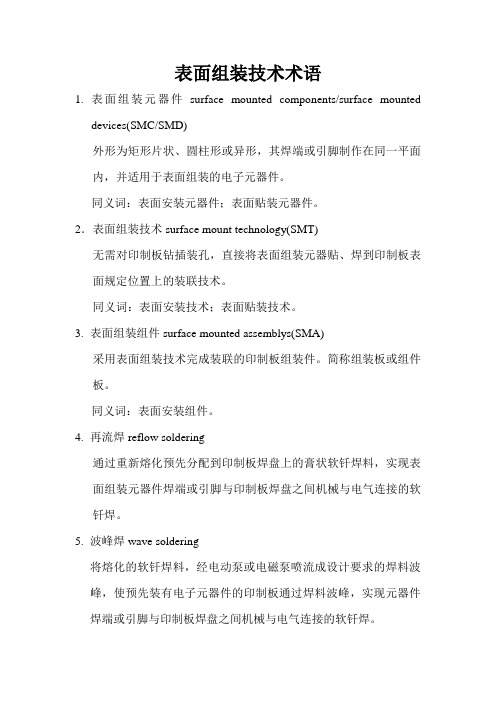
表面组装技术术语1.表面组装元器件surface mounted components/surface mounteddevices(SMC/SMD)外形为矩形片状、圆柱形或异形,其焊端或引脚制作在同一平面内,并适用于表面组装的电子元器件。
同义词:表面安装元器件;表面贴装元器件。
2.表面组装技术surface mount technology(SMT)无需对印制板钻插装孔,直接将表面组装元器贴、焊到印制板表面规定位置上的装联技术。
同义词:表面安装技术;表面贴装技术。
3.表面组装组件surface mounted assemblys(SMA)采用表面组装技术完成装联的印制板组装件。
简称组装板或组件板。
同义词:表面安装组件。
4.再流焊reflow soldering通过重新熔化预先分配到印制板焊盘上的膏状软钎焊料,实现表面组装元器件焊端或引脚与印制板焊盘之间机械与电气连接的软钎焊。
5.波峰焊wave soldering将熔化的软钎焊料,经电动泵或电磁泵喷流成设计要求的焊料波峰,使预先装有电子元器件的印制板通过焊料波峰,实现元器件焊端或引脚与印制板焊盘之间机械与电气连接的软钎焊。
6. 组装密度assembly density单位面积内的焊点数目。
7.矩形片状元器件rectangular chip component两端无引线,有焊端,外形为薄片矩形的表面组装元件。
8.圆柱形表面组装元器件metal electrode face(MELF)component;cylindrical devices两端无引线,有焊端的圆柱形表面组装元器件。
9.小外形封装small outline package(SOD)小外形模压塑料封装;两侧具有翼开或J形短引线的一种表面组装元器件封装形式。
10.小外形晶体管small outline transistor(SOT)采用小外形封装结构的表面组装晶体管。
11.小外形二极管small outline diode(SOD)采用小外形封装结构的表面组装二极管。
SMT电子表面组装技术
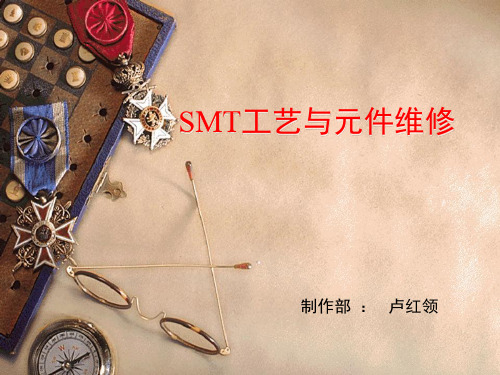
红外热风返修台
4.3 维修局部加热焊接方式
热丝回流焊
热气流回流焊
激光回流 焊
谢谢各位!
SOIC——小外型封装 QFP——方形扁平封装 BGA——球栅阵列结构
三、回流焊接
回流焊的主要设备就是再流焊炉。再流焊炉是将印 刷有焊膏和贴片元件的PBC送入再流焊炉,先经过 炉子的预热区预热,再经过炉子焊接区使焊膏融化 ,最后经过冷却区。
3.1 回流炉的温度设定
回流炉的温度设定:不同金属含量的焊膏有不同的温 度曲线首先应按照焊膏加工厂提供的温度曲线进行设 置,因为焊膏中的焊料合金决定了熔点,助焊剂决定 了活化温度(主要控制各温区的升温速率、峰值温度 和回流时间)。
焊膏的这些特性都可以通过添加不同金属物质或者 相同物质但是量不同改变。可以说差之毫厘谬以千 里。
二、零件贴装
SMT的零件贴装主要是通过贴片机完成。贴
片机工作主要有4个环节;组件拾取
组件检查
组件传送
组件放置。
在完成这些环节前,首先要对贴片机进行编 程,通过编程控制贴片机完成4项工作。
贴片程序是告诉机器到哪里去拾取组 、拾取什么样的物料、物料的封装形
这些参数的设定需要一定的经验累积,比如
刮刀速度设定太快会使得焊膏没全部印制到 各个网孔。
1.2 焊膏
印刷的锡膏是由金属颗粒和助焊剂混合而成的一种 触变性悬浮液。二者的比例为质量百分比金属颗粒 占90%左右。
焊膏多种类,其中最主要的不同分为有铅和无铅, 他们有很多属性不同,如触边性、活性、粘度、湿 度、熔点等,比如有铅焊膏的熔点在185度左右,无 铅焊膏在217度左右。
SMT工艺与元件维修
制作部 : 卢红领
SMT表面组装元器件知识

薄膜或厚膜电阻沉积在一个基板上,然后封装在一
个塑料或陶瓷外壳内。
电阻网络特点 电阻网络可分为厚膜电阻网络和薄膜片电阻 网络两大类。厚膜电阻网络具有体积小、重量轻、 机械强度高、高频特性好、适应再流焊与波峰焊、 电性能稳定、可靠性高、能与自动装贴设备匹配; 符合RoHS指令要求等特点,符合小型化、高密度 组装要求。
表面组装元器件
表面组装元器件简介
表面组装元器件又称片式元器件或贴片元器件,是适应 电子产品微小型化、制造与安装自动化生产需要发展起来的
微型元器件,广泛应用于电子产品制造中。
表面组装元器件主要包括: 【表面组装元件】-无源元件 【表面组装器件】-有源元件
【表面组装连接件】-接插件、开关、继电器和变压器等
→中间电极印刷→烧结→电阻膜印刷(RuO2) →烧结→一次玻璃釉(浆料)印刷→烧结→激光 刻调阻值→二次玻璃釉(浆料)印刷→标记印刷 →烧结→一次切割→封端→烧结→二次切割→电 镀电极→测试分选→编带包装。
矩形片式电阻器尺寸
按照矩形电阻的电极结构形状可分为D型和E型两 种。二者的区别在于反面电极有无公差要求。
矩形片式电阻器焊盘设计
矩形片式电阻器的标识
矩形片式电阻本体上通常会标有基本技术参数, 但不同厂家的电阻型号、规格和表示方法各有不同, 通常标注的基本参数包括:标称阻值、额定功率、阻 值公差、封装尺寸、包装形式等。
表面组装圆柱形片式电阻器
圆柱形片式电阻器结构形状和制造方法上与传统 的带引线电阻器相同,只是去掉了原来的轴向引线, 做成无引线端子。
全密封式电位器
密封式电位器有圆柱形和扁平矩形两种形式,常用于高 档电子产品中,密封性和耐热性好,分为顶调和侧调两种 方式,可采用波峰焊和再流焊两种焊接工艺。
SMT表面组装技术(表面贴装技术)简介

SMT表面组装技术(表面贴装技术)简介 SMT是表面组装技术(表面贴装技术)(Surface Mounted Technology的缩写),是目前电子组装行业里最流行的一种技术和工艺。
电子电路表面组装技术(Surface Mount Technology,SMT),称为表面贴装或表面安装技术。
它是一种将无引脚或短引线表面组装元器件(简称SMC/SMD,中文称片状元器件)安装在印制电路板(Printed Circuit Board,PCB)的表面或其它基板的表面上,通过再流焊或浸焊等方法加以焊接组装的电路装连技术。
SMT基本工艺构成要素包括:丝印(或点胶),贴装(固化),回流焊接,清洗,检测,返修1、丝印:其作用是将焊膏或贴片胶漏印到PCB的焊盘上,为元器件的焊接做准备。
所用设备为丝印机(丝网印刷机),位于SMT生产线的最前端。
2、点胶:它是将胶水滴到PCB板的固定位置上,其主要作用是将元器件固定到PCB板上。
所用设备为点胶机,位于SMT生产线的最前端或检测设备的后面。
3、贴装:其作用是将表面组装元器件准确安装到PCB的固定位置上。
所用设备为贴片机,位于SMT生产线中丝印机的后面。
4、固化:其作用是将贴片胶融化,从而使表面组装元器件与PCB 板牢固粘接在一起。
所用设备为固化炉,位于SMT生产线中贴片机的后面。
5、回流焊接:其作用是将焊膏融化,使表面组装元器件与PCB板牢固粘接在一起。
所用设备为回流焊炉,位于SMT生产线中贴片机的后面。
6、清洗:其作用是将组装好的PCB板上面的对人体有害的焊接残留物如助焊剂等除去。
所用设备为清洗机,位置可以不固定,可以在线,也可不在线。
7、检测:其作用是对组装好的PCB板进行焊接质量和装配质量的检测。
所用设备有放大镜、显微镜、在线测试仪(ICT)、飞针测试仪、自动光学检测(AOI)、X-RAY检测系统、功能测试仪等。
位置根据检测的需要,可以配置在生产线合适的地方。
8、返修:其作用是对检测出现故障的PCB板进行返工。
SMT介绍
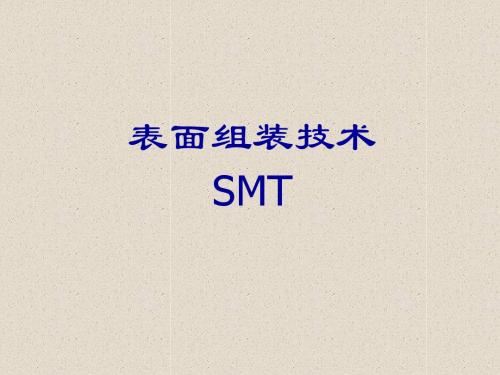
41
4 贴装元器件-贴片设备
YAMAHA贴片机
SAMSUNG贴片机
JUKI贴片机
42
目录:
1. 2. 3. 4. 5. 6. 7. 贴片技术简介 SMT主要制程介绍 锡膏印刷 贴装元器件 回流焊接 外观检验 ICT测试
43
5回流焊接
回流焊是英文Reflow Soldring的直译,是通过加热重新 熔化预先分配到PCB焊盘上的膏状焊料,实现表面组装 元器件焊端或引脚与PCB焊盘间电气与机械连接。 回流焊作为SMT生产中的关键工序,合理的温度曲线设 置是保证回流焊质量的关键。不恰当的温度曲线会使 PCB板出现焊接不全、虚焊、元件翘立、焊锡球过多等 焊接缺陷,影响产品质量。
机器贴装
39
4 贴装元器件
人工手动贴装主要工具:真空吸笔、镊子、IC吸放 对准器、低倍体视显微镜或放大镜等。
40
4 贴装元器件
随着表面贴装技术及新式零件封装设计之快速发展, 也连带刺激自动放置机的不断的革新。多数品牌的放置 机,其对SMD自动放置的基本理念均属大同小异。其工 作顺序是: 由真空转轴及吸头所组成的取料头先将零件拾起。 利用机械式夹抓或照像视觉系统做零件中心校正。 旋转零件方向或角度以便对准电路板面的焊盘。 经释放真空吸力后,使零件放置在板面的焊盘上。
5
有引线元器件:
6
3、SMT与THT区别 元器件不同 ”贴装”与”插装 ” 再流焊与波峰焊
7
微型化的关键—— 短引线/无引线元器件
8
表面安装板
通孔插装板
9
通孔插装板
10
表面安装板1
无线上网卡
11
表面安装板2
MEM模块
12
SMT 培训教程
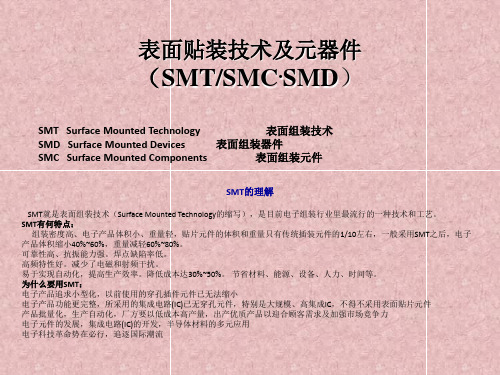
问题及原因
• 6.坍塌
SMA Introduce
•
• • • • •
SLUMPING 原因与“搭桥”相似。
对 策 增加锡膏中的金属含量百分 比。 增加锡膏粘度。 降低锡膏粒度。 降低环境温度。 减少印膏的厚度。 减轻零件放置所施加的压力。
• 7.模糊
SMEARING 形成的原因与搭桥或坍塌 很 类似,但印刷施工不善的原因 居多,如压力太大、架空高度 不足等。
成本最低 周转最快 提供完美的工艺定位 没有几何形状的限制 改进锡膏的释放 纵横比1:1
形成刀锋或沙漏形状 纵横比1.5:1 要涉及一个感光工具 电镀工艺不均匀失去 密封效果 密封块可能会去掉
电铸成行模板
激光切割模板
直接从客户的原始Gerber 数据产生,在作必要修改 后传送到激光机,由激光 光束进行切割
表面贴装技术及元器件
(SMT/SMC.SMD)
SMT Surface Mounted Technology SMD Surface Mounted Devices SMC Surface Mounted Components 表面组装技术 表面组装器件 表面组装元件
SMT的理解
SMT就是表面组装技术(Surface Mounted Technology的缩写),是目前电子组装行业里最流行的一种技术和工艺。 SMT有何特点: 组装密度高、电子产品体积小、重量轻,贴片元件的体积和重量只有传统插装元件的1/10左右,一般采用SMT之后,电子 产品体积缩小40%~60%,重量减轻60%~80%。 可靠性高、抗振能力强。焊点缺陷率低。 高频特性好。减少了电磁和射频干扰。 易于实现自动化,提高生产效率。降低成本达30%~50%。 节省材料、能源、设备、人力、时间等。 为什么要用SMT: 电子产品追求小型化,以前使用的穿孔插件元件已无法缩小 电子产品功能更完整,所采用的集成电路(IC)已无穿孔元件,特别是大规模、高集成IC,不得不采用表面贴片元件 产品批量化,生产自动化,厂方要以低成本高产量,出产优质产品以迎合顾客需求及加强市场竞争力 电子元件的发展,集成电路(IC)的开发,半导体材料的多元应用 电子科技革命势在必行,追逐国际潮流
表面组装元器件

F lip Chip (倒装芯片)
MC M (多芯片模块——如同混合电路,
将电阻做在陶瓷或
PCB 上,外贴多个
集成电路和电容等其它元件,再封装成
一个组件)
SMD常用器件封装介绍
QFP
quad flat package (四侧引脚扁平封装)
常用的封 装形式
种类和名称繁多 4边翼形引脚,间距一般为由0.3至1.0mm ;引脚数目 有32至360左右;有方形和长方形两类,视引脚数目。
器件
封装名称和外形
引脚数和间距
包装
类型
(mm)
方式
圆柱形二极管 (MELF)
两端
片 式 SOT23
三端
编带
晶 SOT89 体
四端
或 散装
管 SOT143
四端
SOP ( 羽翼形小外形塑料封装 ) TSOP (薄形 SOP ) SOJ (J 形小外形塑料封装 )
8 ~ 44 引脚 引脚间距: 1.27 、 1.0 、 0.8 、 0.65 、 0.5
路 BGA ( 球形栅格阵列 )
焊球数: 20 ~ 40 焊球间距: 1 .5 、
CSP ( 又称 μ BGA 。 外形与 BGA 相同, 封装尺寸比 BGA 小。芯片封装尺寸与芯 片面积比 1.2 )
1.27 、1 .0 、0.8 、0.65 、 0.5 、 0.4 、 0.3
( 0.8 以下为 CSP )
• 3 耐振动抗冲击。
SMT技术的优势
• 4 有利于提高可靠性——焊点面接触,消除了元器件与 PCB之间的二次互连。减少了焊接点的不可靠因素。
SMT技术的优势
• 5 工序简单,焊接缺陷极少(前提:设备、PCB设计、 元器件、材料、工艺)。
表面组装元器件SMDSMC
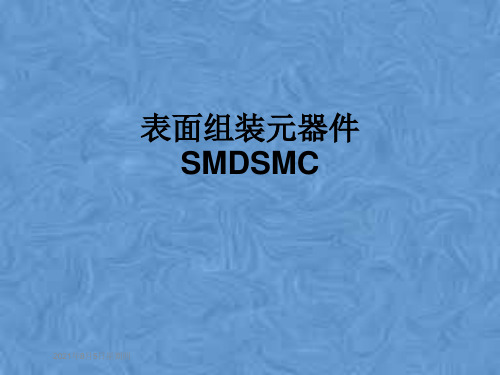
3.铝电解电容器
铝电解电容器是有极性的电容器,它的正极板用铝箔,将其浸 在电解液中进行阳极氧化处理,铝箔表面上便生成一层三氧化二铝 薄膜,其厚度一般为0.02~0.03mm。这层氧化膜便是正、负极板 间的绝缘介质。电容器的负极是由电解质构成的,电解液一般由硼 酸、氨水、乙二醇等组成。
铝电解电容器的构造
(a)立式接插件
表面贴装接插件
(b)侧卧式接插件
2.IC插座
集成电路插座有很多种用途。在工程开发中,插座允许IC迅速更 换,这样就能评价含有大量元器件的电路性能。在生产中,它们往 往用于常规的ROM芯片或ASIC。ASIC必须根据用户严格要求的技 术条件专门制作。当IC必须随时迅速地定期更换时,IC插座是做理 想的器件。
可变电容器适合于高频应用,如通信和视频产品。典 型的产品系列所包括的范围大约从1.5~50pF几个等级, 可调范围从小容值的2∶1左右到大容量值的7∶1。产品 因制造厂家而异,但在电位器中所讨论的许多相同机械 问题,也适用于可调电容器。
2.2.3 电感器
片式电感器亦称表面贴装电感器,它与其它片式元器件(SMC及 SMD)一样,是适用于表面贴装技术(SMT)的新一代无引线或短引 线微型电子元件。其引出端的焊接面在同一平面上。
从电子元器件的功能特性来说,SMC特性参数的数值 系列与传统元件的差别不大,标准的表称数值有E6、E12、 E24等。长方体SMC是根据其外形尺寸的大小划分成几个 系列型号的,现有两种表示方法,欧美产品大多采用英 制系列,日本产品采用公制系列,我国两种系列都在使 用。并且,系列型号的发展变化也反映了SMC元件的小型 化过程:5750(2220)→4532(1812)→3225(1210) →3216(1206)→2520(1008)→2012(0805)→1608
SMT物料基础知识
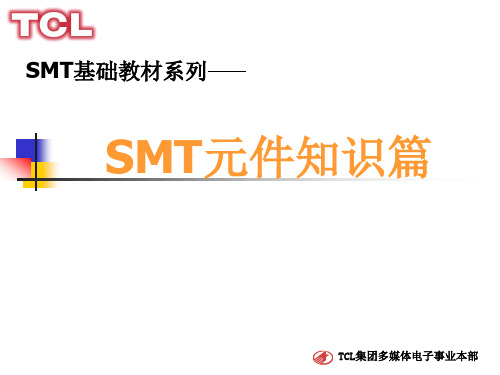
d) 表面组装印制板--- SMB (Surface Mount Board)。
e) 外形封装 SOP(Small Outline Package) 小外形模压塑料封装,两侧有翼形或J形短引脚的一种SMD。
b) 小外形晶体管SOT(Small Outline Transistor) 采用小外形封装结构的表面组装晶体管。
贴片物料编码
物品码12—可控硅,贴片三极管
12
D1 D2
D3
D4
D5
D6
S1
S2
S3
d1 ~ d6此6个字符 与 厂家的零件码相同 , 如厂家零件码小于
6 个字符,在前面加 “0”补齐;如多于 6个字符,挑选有
意 义的6个字符。
对贴片三极管, 表示 分档,如无分档 区分,则S1=0, 如厂家分档标识 多于一个字符,
TCL集团多媒体电子事业本部
SMT元件认识
贴片元件的种类比较多,在我公司目前的产品中通常使用的Chip 件有二极管、三极管、电感、电容、电阻、IC及异形元件,其 中IC包括QFP、SOP、SOJ等。
1:常见Chip件的规格(Chip是簿片) 见下图:
TCL集团多媒体电子事业本部
SMT元件认识
片状元件称呼方法
B:+/-0.1PF
C:+/-0.25PF
D:+/-0.5PF
TCL集团多媒体电子事业本部
贴片物料编码
普通贴片电容是我们公司贴片元件中最常见的贴片元
之一,它物料上面没有丝引,从表面看起来,看不出
其容值,需要用电桥测试议来测出其容值的大小;而
贴片铝电容在贴片须注意其极性问题。常用贴片电容
- 1、下载文档前请自行甄别文档内容的完整性,平台不提供额外的编辑、内容补充、找答案等附加服务。
- 2、"仅部分预览"的文档,不可在线预览部分如存在完整性等问题,可反馈申请退款(可完整预览的文档不适用该条件!)。
- 3、如文档侵犯您的权益,请联系客服反馈,我们会尽快为您处理(人工客服工作时间:9:00-18:30)。
3.凸点载带自动键合(BTAB) 结构特点: 将连接用的凸点制作在载带引线上,与TAB相反. 载带结构:
与载带配合的芯片电极结构类型:
与TAB相比的特点: 操作工艺比TAB有所提高和简化 实用化遇到的两个问题:
I. 引出线端部凸点的形成工艺较为复杂;
II. 载带连接引线端部的凸点成形,与芯片 电极连接的面在平面度上有一定的差别;
三引脚,最大芯片尺寸:0.760.76mm; SOT89(EIA TO223):
三引脚,从管子的同一侧引出, 最大芯片尺寸:1.5 1.5mm; SOT143(EIA TO253): 四引脚,最大芯片尺寸:0.64 0.64 焊接方法:波峰焊和再流焊
B.小外型塑封集成电路(SOP) 外形结构(三种引线结构):
特点:实现了高密度的芯片组装,突破了细 微电极间距集成电路芯片组装的难关。
§5.3 其他片式元件举例 一.表面波滤波器
表面波滤波器的工作原理
二.表面组装电磁继电器(机电元件) 1. EB2型的工作原理
2. EB2型继电器的结构
§5.4 表面组装件的设计 §5.4.1 设计工作概述
一. 步骤:
将LSI等装在具有特殊结构的载体上,制成合格 的微电子器件;
具有两种引出结构: 引线式-特殊结构的短引线 无引线式-引出端为焊料凸点结构
多层布线电路板: 陶瓷多层布线板:
❖ 特点:热膨胀系数相近,导热性好,不老化;但 介电常数大,增加信号的延迟,耐冲击性差,工 艺比较复杂
❖ 工艺:多层共烧 厚膜多层布线板:
加盖封装.
B.有引线陶瓷芯片载体: 目的:防止热胀冷缩引起的焊点开裂 类型: ❖ 预引线陶瓷芯片载体:
采用铜合金引线和可伐引线,由厂家将 其钎焊在顶上或附在城堡上 ❖ 后引线陶瓷芯片载体:
由用户通过再流焊把引线键合在城堡的 凹槽中(实际上很少用)
二.芯片组装器件:
1.倒装焊器件 特点:
芯片组装密度高,生产效率高,合格率高. 倒装焊的连接方法:
二.设计工作分述: 1.电路设计(分区原则): ❖ 按功能分区:输入输出靠边缘,设置测试点 ❖ 数、模分区 ❖ 高、中和低频分区:前者单独屏蔽 ❖ 大功率电路与其他电路分开 ❖ 噪声与干扰与其他部分分开 值得注意的特点:
尺寸小,功率密度大,相互干扰大
2.元器件的选择与布局
选择
❖ 成本,采购的稳定性,配套
设计-结构尺寸、端子形状、耐焊接热等; 各种元器件的制造技术;
包装– 编带式、棒式、散装等 B. 电路基板--单层或多层印制电路板、陶瓷、
瓷釉金属板等;
C. 组装设计 电设计、热设计、元器件布局、基板图形 设计等;
D. 组装工艺
组装材料:粘结剂、焊料、焊剂、清洗剂等 组装技术:涂敷技术、贴装技术、焊接技术、
70年代美国研制,以金属化焊盘代替引线 E. 80年代以后,各种片式电阻器,片式电容器和
片式电感器相继系列地占领市场,各种片式机电 元件,敏感元件和复合元件也相继研制成功.
3.表面组装技术的三个发展阶段
I.1970~1975年:
主要目标是微小型化,表面组装元器件主 要用于HIC、石英表和计算器;
II.1976~1980年:
的焊料波峰,使预先装有元器件的电路板通过焊料波峰,实 现元器件焊端或引脚与电路板焊盘之间机械与电气连接的 软钎焊. 优点: 同时焊接片式元件和插装件
规格品种很多,尺寸可归纳为四组: 第一组:
对表面组装起关键作用,代表互换性尺寸; 第二组:是器件贴装时应加以计测尺寸; 第三组:是为器件贴装所需的各项尺寸; 第四组:用户应该掌握的常规尺寸 焊接方法:再流焊
C.塑料有引线芯片载体(PLCC): 引线排列与外形:
焊接方法:再流焊和气相焊
D.方形扁平封装载体(QFP) 外形尺寸:
通孔组装元器件:2~4只/cm3; 单面表面组装:3~6只/cm3; 单面混合组装:4~8只/cm3; 双面混合组装:5~9只/cm3; 双面表面组装:6~12只/cm3
B. 电子元器件和电子产品的性能显著提高
❖ 无引线或短引线及表面组装技术使分布电 容和分布电感大幅度减小,提高了产品的 高频特性;
❖ 焊接的要求
❖ 焊接的要求
❖ 目测和检修的要求(P387,表25-1)
3.形状与覆盖率面积
A [ (ai Ii ) ni ]K M
4.电路基板的选择和布线设计 特点: ❖ 热膨胀系数(相对于PCB而言,要求更高), ❖ 散热(高于玻璃转变温度,聚合物膨胀,影响电气
性能) ❖ 根据整机总体结构确定单块电路板的尺寸,当
第五章 表面组装技术(SMT) 与表面组装元器件(SMC、SMD)
§5.1 绪 论
1. 表面组装技术(Surface Mounting Technology) 采用片式元器件,组装时把引线直接焊在基 片表面上,代替了传统的插装工艺,是当代 最先进的电子产品组装技术.它实际上是 HIC技术的延伸和发展.
9.SMT的发展展望 A.板上芯片技术(COB)
特点:节省空间 组装过程:
在基片上丝网印刷导电粘合剂(环氧银膏) 贴装IC 固化剂固化 用引线将管芯键合点连在基片上
不足:裸芯片在组装之前不能测试,组件成品率 面临严重问题. B.微组装技术MAT(高密度的立体组装技术) MAT的两大支柱: 载体器件:
载带自动键合示意图:
主要工艺流程图(载带为聚酰亚胺薄膜):
三种结构类型:
三种结构类型:
单层载带:只带一铜箔,在其上形成图形,键合后 不能进行测试,目前较少采用;
双层载带:铜箔直接粘附于薄膜上,要求底膜的绝 缘耐压高、机械强度高(聚酰亚胺和聚酯)。不带 粘结剂,高温稳定性高;
三层载带:底膜与铜箔之间有一粘结层,可选用廉 价的底膜
2.表面组装元器件(SMT之基础)的发展过程 A.小外型集成电路(SOIC)(塑料外壳)
菲利浦公司60年代开始,28针(1.27mm) B.塑料方型封装集成电路(QFP)
日本70年代研究,160针以上(1.27mm,0.65mm) C.塑料有引线芯片载体(PLCC)
美国研制,J型引线(1.27mm) D.无引线陶瓷芯片载体(LCCC)
特点:引出线极细,贴装技术要求高
2.陶瓷封装器件: A.无引线陶瓷芯特点:
在陶瓷外壳侧面有类似城堡状的金属化 凹槽与外壳底面的镀金电极相连.
制作过程:
基片:采用氧化铝或氧化铍瓷料经印刷布线 后叠层加压、烧结而成;
贴装芯片:粘贴半导体芯片,完成芯片与外 壳端子间的连接;
(2)电解电容器的正极、SOT封装管的单引线端、集 成电路和开关的第一号针应朝同一方向
Sn-Ag系
(3)功率器件尽可能分散分布
(4)元器件的排列方位:与工艺有关 传动式再流焊直立缺陷的形成
传动式再流焊正确的元件方位
波峰焊的阴影效应及克服办法
波峰焊时SMD(SMC)的方位
(5)元器件的间距 ❖ 焊接工艺的要求
通孔尺寸的限制: 成本
厚径比升高,通孔内电镀层开裂
建议用铜镀层,或焊锡填充
通孔位置:
再流焊 不应该放在焊盘中或者与焊盘直接相连
波峰焊 放在焊盘附近或者在焊盘中
测试通孔:
考虑与测试设备针床的网格分布相配合
[3] 布线设计
插装:0.3mm
SMT:小于上述值
生产细线宽电路板的措施:
❖
薄的覆铜板(控制侧向腐蚀)
❖
调大线宽,缩小线距(利用侧向腐蚀达到最终值)
❖
修整通孔焊盘
五种布线规则 一级:
低密度
二级和三级: 常用
四级: 高密度
五级: 极高密度
焊盘连线的设计(影响:元件泳动、热量控制、焊锡沿布线的 迁移)
焊盘连线导热路径的控制(SMOBC—阻焊膜涂在裸铜布线上):
阻焊膜工艺及其应用条件: 丝网漏印:用于布线密度低的电路板,焊盘间不通过布线导
体,当焊盘间距小时,可能污染焊盘造成焊接缺陷,或者 在元器件的引线与焊盘之间造成开路。 光图形转移湿膜(光刻工艺):适用于高密度电路板,价格适中 干膜:对准精度高,分辨率高,无流动性,不会污染焊盘, 能盖住通孔,但电路板与膜之间存留气隙,高温下膜易破 裂;不宜贴在无源元件下方(厚度较厚),否则再流焊时易 产生直立现象;价格较贵。
5.工艺选择
整体设计,生产设备,详见下述 6. 封装与焊点的可靠性设计
❖ 封装产生裂缝原因
❖ 解决方法 增大塑料强度和厚度 控制再流焊温度不能太高 注意芯片大小与塑料厚度之间的关系(P398 fig25-18) 封装好的器件烘烤去潮,贮存时加干燥剂
❖ 焊接技术及其优缺点 A.波峰焊—将熔化的焊料,经电动泵或电磁泵喷流成设计要求
关键:凸点的形成 基本结构:凸点电极/润湿层/保护层/芯片铝电极
几种形成凸点电极的方法与结构: IBM公司:
Philips公司:
Philclford公司:
日立公司:
2.载带自动键合(TAB)-凸点在芯片上 特点: 封装密度高,适用于多电极引线芯片; 键合后能进行电性能测试和老化测试; 通过群焊能一次完成键合,可靠性高; 具有良好的高频特性.
D.提高可靠性,降低成本 ❖ 片式元器件无引线,端电极直接焊在PCB上,无
断脚现象; ❖ 采用新的焊接技术减少了桥接、虚焊等焊接疵病; ❖ 加工工序少,节省原材料。 8. 目前存在的问题 ❖ 系列化和标准化问题; ❖ 热膨胀系数不一致导致的开焊问题; ❖ 散热问题及信号交叉耦合问题; ❖ 塑封器件的吸潮问题; ❖ SMT技术的初始投资太大.
III. 必须对引线镀金后再进行键合,以降低 接触电势差,使工艺复杂化。
4.微凸点连接(MBB)
工艺流程:
方法要点:
在同一块芯片上制作出2000多个高度为 3~10m,大小为5 m5m,间距为10 m的超微金凸点,经涂敷绝缘树脂、位置 校正、对基板加压及树脂硬化作用,实现 可靠的电连接。