大连理工大学精品课程-材料力学性能-第七章-金属的磨损(3)
[大连理工大学]材料科学基础课件7第七章
![[大连理工大学]材料科学基础课件7第七章](https://img.taocdn.com/s3/m/350d6e230066f5335a8121e4.png)
)
C�
x�
D(
�
C�
题问偶散扩 �题问散扩的棒长限无于用适
,0=x 2 / ) 2 � � 1� ( � s � 2� � � �∞-=x �∞+=x �件条界边 1� � � 2� � � 0< x 1� � � 0>x �时0=t�件条始初
散扩的中料材 章七第
致一向方的降下度浓与向方的流质物散扩�‖ �― 1-s.2mc ��tneiciffeoc noisuffid�数系散扩�D 离距的向方散扩沿�x 3-mc或3-mc.g �量质的质物散扩中质物积体位单即 ��noitartnecnoc�度浓的子原质溶�C 1-s.2-m c或1-s.2-mc.g ,量通散扩�J xd 比正成�tneidarg noitartnecnoc�度梯度浓的 处此与�J量通质物散扩的积面界位单一某的 向方散扩于直垂过通内间时位单�0=td/Cd即 �下�noisuffid etats-ydaets�件条散扩态稳在
tD 2 ) ( fre ) 1C � 2 C( � 2 C � C x 题问散扩的棒长限无半于用适 �解
01 � 2
4�
01 � 16. 1 � 2
�
� �
径途要主的散扩子原是 �散扩位空助借子原 �)msinahcem ycnacav ,c(制机位空 ● 置位隙间个一另 到移迁置位隙间个一从子原 �)msinahcem laititsretni ,d(制机隙间 ● 大不也性能可 �束约的动运体集受为因但 �小制机位换接直较量能 �)egnahcxe cilcyc ,b(制机位换形环 ● 大不性能可�能活激大较需 �置位换互接直子原邻相两 �)egnahcxe tcerid ,a(制机位换接直 ● 制机的置位衡平个一另到跳置位衡平个一从子原即 )msinahcem noisuffid(制机散扩 1 论理子原的散扩 2.7§
大连理工大学精品课程-材料力学性能-第一章-金属断裂(3)

2020年7月27日 第一章 单向静载下材料的力学性能 星期一
假设一完整晶体受拉应力
F
作用后,原子间结合力与
引力
m
原子间位移的关系曲线如
a0
图 1-69 所 示 。 曲 线 最 大 值
2
原子位移x
斥力
m代表了晶体在弹性状态
下的最大结合力——理论
图1-69 原子间作用力与 原子位移曲线
断裂强度。作为近似,该曲线用正弦曲线表示:
由和式可得:m E ········· 2 a0 ···
另一方面,晶体脆性断裂时产生两个新的表面。
设单位面积的表面能为s,形成单位裂纹表面外力所 4 作的功U0应为-x曲线下所包围的面积:
2020年7月27日 第一章 单向静载下材料的力学性能 星期一
U 0
2
m sin
2xdx
m
·········
材料的s实际上由表面能和塑性变形功组成,称为有效
表面能。塑性变形功与材料的有效滑移数目及裂纹尖端附近 可动位错数目有关。如bcc金属的有效滑移系数目多,但位 错受杂质原子的钉扎,可动位错数目少,易于脆性断裂。而
20 fcc金属的有效滑移系数目和可动位错数目都比较多,
2020年7月27日 第一章 单向静载下材料的力学性能 星期一
适用于塑性变形 诱发的裂纹
2020年7月27日 第一章 单向静载下材料的力学性能 星期一
三、断裂理论的意义
前已述及,公式 c 2Gs 是金属材料屈服时产
ky d
生解理断裂的判据。那么,应该有
1
c s i kyd 2
1
(id 2 ky)ky 2Gs
1
考虑应力状态的影响,上式可写成 (id 2 ky)ky 2Gsq
材料力学性能大连理工大学课后思考题答案解读

第一章 单向静拉伸力学性能 一、 解释下列名词。
1弹性比功:金属材料吸收弹性变形功的能力,一般用金属开始塑性变形前单位体积吸收的最大弹性变形功表示。
2.滞弹性:金属材料在弹性范围内快速加载或卸载后,随时间延长产生附加弹性应变的现象称为滞弹性,也就是应变落后于应力的现象。
3.循环韧性:金属材料在交变载荷下吸收不可逆变形功的能力称为循环韧性。
4.包申格效应:金属材料经过预先加载产生少量塑性变形,卸载后再同向加载,规定残余伸长应力增加;反向加载,规定残余伸长应力降低的现象。
5.解理刻面:这种大致以晶粒大小为单位的解理面称为解理刻面。
6.塑性:金属材料断裂前发生不可逆永久(塑性)变形的能力。
韧性:指金属材料断裂前吸收塑性变形功和断裂功的能力。
7.解理台阶:当解理裂纹与螺型位错相遇时,便形成一个高度为b 的台阶。
8.河流花样:解理台阶沿裂纹前端滑动而相互汇合,同号台阶相互汇合长大,当汇合台阶高度足够大时,便成为河流花样。
是解理台阶的一种标志。
9.解理面:是金属材料在一定条件下,当外加正应力达到一定数值后,以极快速率沿一定晶体学平面产生的穿晶断裂,因与大理石断裂类似,故称此种晶体学平面为解理面。
10.穿晶断裂:穿晶断裂的裂纹穿过晶内,可以是韧性断裂,也可以是脆性断裂。
沿晶断裂:裂纹沿晶界扩展,多数是脆性断裂。
11.韧脆转变:具有一定韧性的金属材料当低于某一温度点时,冲击吸收功明显下降,断裂方式由原来的韧性断裂变为脆性断裂,这种现象称为韧脆转变12.弹性极限:试样加载后再卸裁,以不出现残留的永久变形为标准,材料能够完全弹性恢复的最高应力。
13.比例极限:应力—应变曲线上符合线性关系的最高应力。
14.解理断裂:沿一定的晶体学平面产生的快速穿晶断裂。
晶体学平面--解理面,一般是低指数、表面能低的晶面。
15.解理面:在解理断裂中具有低指数,表面能低的晶体学平面。
16.静力韧度:材料在静拉伸时单位体积材料从变形到断裂所消耗的功叫做静力韧度。
材料力学性能大连理工大学课后思考题答案

第一章 单向静拉伸力学性能 一、 解释下列名词。
1弹性比功:金属材料吸收弹性变形功的能力,一般用金属开始塑性变形前单位体积吸收的最大弹性变形功表示。
2.滞弹性:金属材料在弹性范围内快速加载或卸载后,随时间延长产生附加弹性应变的现象称为滞弹性,也就是应变落后于应力的现象。
3.循环韧性:金属材料在交变载荷下吸收不可逆变形功的能力称为循环韧性。
4.包申格效应:金属材料经过预先加载产生少量塑性变形,卸载后再同向加载,规定残余伸长应力增加;反向加载,规定残余伸长应力降低的现象。
5.解理刻面:这种大致以晶粒大小为单位的解理面称为解理刻面。
6.塑性:金属材料断裂前发生不可逆永久(塑性)变形的能力。
韧性:指金属材料断裂前吸收塑性变形功和断裂功的能力。
7.解理台阶:当解理裂纹与螺型位错相遇时,便形成一个高度为b 的台阶。
8.河流花样:解理台阶沿裂纹前端滑动而相互汇合,同号台阶相互汇合长大,当汇合台阶高度足够大时,便成为河流花样。
是解理台阶的一种标志。
9.解理面:是金属材料在一定条件下,当外加正应力达到一定数值后,以极快速率沿一定晶体学平面产生的穿晶断裂,因与大理石断裂类似,故称此种晶体学平面为解理面。
10.穿晶断裂:穿晶断裂的裂纹穿过晶内,可以是韧性断裂,也可以是脆性断裂。
沿晶断裂:裂纹沿晶界扩展,多数是脆性断裂。
11.韧脆转变:具有一定韧性的金属材料当低于某一温度点时,冲击吸收功明显下降,断裂方式由原来的韧性断裂变为脆性断裂,这种现象称为韧脆转变12.弹性极限:试样加载后再卸裁,以不出现残留的永久变形为标准,材料能够完全弹性恢复的最高应力。
13.比例极限:应力—应变曲线上符合线性关系的最高应力。
14.解理断裂:沿一定的晶体学平面产生的快速穿晶断裂。
晶体学平面--解理面,一般是低指数、表面能低的晶面。
15.解理面:在解理断裂中具有低指数,表面能低的晶体学平面。
16.静力韧度:材料在静拉伸时单位体积材料从变形到断裂所消耗的功叫做静力韧度。
大连理工大学精品课程-材料力学性能-第四章-金属的断裂韧度(2)

建立符合塑性变形临界条件(屈服)的函数表达
式r=f(),该式对应的图形即代表塑性区边界形状,
其边界值即为塑性区尺寸。
由材料力学可知,通过一点的主应力1、2、 3和x、y、z方向上各应力分量的关系为:
7
2020年7月30日 星期四
第四章 金属的断裂韧度
1 x y
2
x
2
y
2
2 xy
1 K cos 1 sin
展。我们将x方向(=0)的塑
性区尺寸r0定义为塑性区宽 度。
10
图4-2 裂纹尖端附近塑性区 的形状和尺寸
2020年7月30日 星期四
第四章 金属的断裂韧度
r0
1
2
K
ys
2
KI—应力场强度因子
ys—有效屈服应力
s—单向拉伸时的屈服强度 —泊松比
r0
1
2
K
s
2
(平面应力)
r0
(1 2 2
)2
、有效裂纹及KI的修正 由于裂纹尖端塑性区的存在,会降
低裂纹体的刚度,相当于裂纹长度的增
加,因而会影响应力场及KI的计算,所 以要对KI进行修正。最简单和实用的方 法是在计算KI时采用虚拟等效裂纹代替 实际裂纹。
20
2020年7月30日 星期四
第四章 金属的断裂韧度
如图4-5所示,裂纹a前方
区域未屈服前,y的分布曲线
2020年7月30日 星期四
第四章 金属的断裂韧度
KI≥KI(KIC)是一个很有用的关系式,它将 材料的断裂韧度同机件的工作应力及裂纹尺寸 的关系定量地联系起来了。应用这个关系式可 解决有关裂纹体的断裂问题:如可以估算裂纹
体的最大承载能力、允许裂纹尺寸a及材料断
金属的磨损与接触疲劳

30/34
浅层剥落过程示意图
31/34
过程:在0.5-0.7b处,首先滑移变形→一 定循环N→产生疲劳裂纹→沿应力,夹杂物走 向发展→形成二次裂纹→扩展到表面→另一 端形成悬臂梁→压断,浅层剥落。
提高浅层剥落抗力措施:提高材料的塑 性变形抗力,进行整体或表面强化,使0.5- 0.786b处的切变强度↑。
7/34
摩擦副一方金属表面常粘附一层很薄的转
移膜,并伴有化学成分变化→判断粘着磨损的
主要特征。
图7-2 粘着磨损表面形貌
图7-3 粘着磨损过程示意图
8/34
(1) 粘着点强度比一方金属强时磨损量大, 表面较粗糙,甚至产生咬死。
(2) 粘着点强度比双方金属都低时,磨损 量小,摩擦面较平滑。
(3) 粘着点比双方金属都高时,剪断可发 生在摩擦金属的任何一方,较软金属的磨损量 大。
从综合切应力的分布和大小,材料的强 度相互比较,决定了裂纹产生的部位和接触 疲劳类型。
26/34
1、麻点剥落:裂纹起源于表面的接触疲劳损伤。 (1) 滑动加滚动条件下:切向摩擦力较大,
使最大综合切应力转移至表面。 (2) 表面存在质量缺陷:软点、硬点、夹杂
物等,造成抗剪强度不足。 深度:0.1-0.2mm的小块剥落。 形态:麻点是些针状或痘状的凹坑。
提高材料纯净程度,↓夹杂物数量。
32/34
3、深层剥落(压碎性剥落) 裂纹起源于表面硬化层下过渡区。 原因:过渡区强度不足。
深层剥落过程示意图
33/34
提高深层剥落抗力的措施:提高机件心部 强度;增大硬化层深度;控制渗层金相组织, 碳化物级别,马氏体级别,残余奥氏体级别 等。
感谢聆听
带着梦想,赢得这场胜利,成为英雄
第七章 金属的磨损

粘着磨损、磨粒磨损、冲蚀磨损、疲劳磨损、 腐蚀磨损、微动磨损
与材料整体变形与断裂的区别 整体加载时变形和断裂集中在一定的体积 内,并在这些部位产生应力集中形成裂纹。
表面加载变形和断裂发生在表面,变形和 断裂反复进行,具有动态特征。
普通力学性能试验得到的数据不一定能反映 材料的耐磨性。
3.磨损过程
细化晶粒提高耐磨性 软性基体中的碳化物提高耐磨性,硬基体中碳 化物降低耐磨性 加工硬化对低应力擦伤性磨损无影响,但可提 高高应力碾碎性磨损的耐磨性。 4、提高耐磨性的措施 (1)增加材料的硬度 (2)根据服役环境合理选择耐磨材料 (3)采用化学热处理提高表面硬度
三、冲蚀磨损 1.磨损机理 概念: 指流体或固体以松散的小颗粒按一定的 角度和速度对材料表面进行冲击所造成的磨损。 分类:气固冲蚀磨损、流体冲蚀磨损、液滴冲蚀 磨损、气蚀磨损。
转移硬材料上的粘着物又使软材料表面出现划痕所以擦伤主要发生在软材料表面当粘结点的强度低于摩擦副两材料的强度时剪切发生在界面上此时虽然摩擦系数增大但磨损却很小材料转移也不显著
第七章 金属的磨损和接触疲劳 第一节 磨损概念
一、磨损 1.概念 机件表面接触并做相对运动,表面有微小颗 粒分离出来形成磨屑,是材料表面逐渐流失, 造成表面损伤的现象。 2.分类
当粘结点的强度低于摩擦副两材料的强度时, 剪切发生在界面上,此时虽然摩擦系数增大, 但磨损却很小,材料转移也不显著。通常在 金属表面有氧化膜、硫化膜或其它涂层时发 生这种粘着磨损. 二.磨损量的估算 粘着磨损体积与法向力、滑动距离成正比, 与软方材料压缩屈服成反比,与接触面积无 关。 V=αKFLt/H 或 V=KFLt/9 scδ
1)跑和阶段 2)稳定磨损阶段 3)剧烈磨损阶段 二.耐磨性 通常用磨损量来表示。可以用摩擦试样表面法线 方向尺寸的减小,也可以用试样的质量或体积 的减少表示。
大连理工大学精品课程-材料力学性能-第一章-金属断裂(2)

解理面(001) 扩展方向[110]
挛晶面(112) 挛晶方向[111]
27
图1-67 解理舌形成示意图
2020年7月26日 第一章 单向静载下材料的力学性能 星期日 准解理
材料中弥散细小的第二
相影响裂纹的形成与扩展,
使裂纹难于严格按一定晶体
学平面扩展,断裂路径不再 与晶粒位向有关,主要与细 小碳化物质点有关。其微观 特征似解理河流但又非真正 28 解理,故称准解理。
24
图1-64 河流通过大角度 晶界时的扇形花样
2020年7月26日 第一章 单向静载下材料的力学性能 星期日
当解理裂纹通过扭转晶界时,因晶界两侧晶
体以边界为公共面转动一个角度,使两侧解理裂
纹存在位向差,故裂纹不能直接越过晶界而必须
重新成核,裂纹将沿若干组
新的相互平行的解理面扩展
而使台阶激增,形成为数众
1
m
E s
a0
2
s——表面能;
a0——原子面间距; E——弹性模量
1
1
形成裂纹的力学条件为: (f
i )
d
2
Es 2
2r a0
可得: f i 2Er s
da0
f——形成裂纹所需
的切应力;
7
2020年7月26日 第一章 单向静载下材料的力学性能 星期日 (二)、解理裂纹的扩展 以上所述主要涉及解理裂纹的形成,并不意味 着由此形成的裂纹将迅速扩展而导致材料断裂。解 理断裂过程包括以下三个阶段:塑性变形形成裂 纹;裂纹在同一晶粒内初期长大;裂纹越过晶界向 相邻晶粒扩展。
多的 “河流”,这与通过大角
度晶界的情况类似。
25
图1-65 河流花样通过扭转晶界
材料力学性能-第七章-金属的磨损(1)

一、粘着磨损
1.定义与特点:粘着磨损又称咬合磨损,是在 滑动摩擦条件下,当摩擦副相对滑动速度较小 (1m/s)时发生的。它是因缺乏润滑油,摩擦副 表面无氧化膜,且单位法向载荷很大,以致接 触应力超过实际接触点的屈服强度而产生的一 种磨损。
2021年11月27日 星期六
第七章 金属的磨损
图7-2 粘着磨损表面损伤形貌
2021年11月27日 星期六
第七章 金属的磨损
由于从较软一方金属材料的表面脱离下来的 碎屑不一定全部成为磨屑,有时碎屑可能仍附于 金属表面上,因此,磨屑形成有个几率问题,设 此几率为K,则单位滑动距离内的磨损体积为:
V l
K
N
d 3
12
··················
式中:V-磨损体积;l-滑动距离;K-磨屑形成几率; d-磨屑直径
2021年11月27日 星期六
第七章 金属的磨损
图7-3中所示的粘着磨损过程是粘着点强
度比摩擦副一方金属强度高的情况,此时常在
较软一方本体内产生剪断,其碎片则转移到较
硬一方金属上,软方金属在硬方金属表面逐步
积累最终使不同金属的摩擦副滑动成为相同金
属间的滑动,故磨损量较大,表面较粗糙,甚
至可能产生咬死现象,铅基合金与钢之间的滑
粘附一层很薄的转移膜并伴有化学成分变化,这
是粘着磨损的重要特征。
2021年11月27日 星期六
第七章 金属的磨损
分三个阶段:
接触面凸起因塑性变形被
碾平,并在接触面之间形成
剪断强度高的分界面;
❖摩擦副一方金属远离分界
面内断裂,从该金属上脱落
并转移到另一方金属表面;
转移的碎屑脱落下来形成
磨屑。
材料力学性能课后答案

1.解释下列名词①滞弹性:金属材料在弹性范围内快速加载或卸载后,随时间延长产生附加弹性应变的现象称为滞弹性,也就是应变落后于应力的现象。
②弹性比功:金属材料吸收弹性变形功的能力,一般用金属开始塑性变形前单位体积吸收的最大弹性变形功表示。
③循环韧性:金属材料在交变载荷下吸收不可逆变形功的能力称为循环韧性。
④包申格效应:金属材料经过预先加载产生少量塑性变形,卸载后再同向加载,规定残余伸长应力增加;反向加载,规定残余伸长应力降低的现象。
⑤塑性:金属材料断裂前发生不可逆永久(塑性)变形的能力。
⑥韧性:指金属材料断裂前吸收塑性变形功和断裂功的能力。
脆性:指金属材料受力时没有发生塑性变形而直接断裂的能力⑦加工硬化:金属材料在再结晶温度以下塑性变形时 ,由于晶粒发生滑移 , 出现位错的缠结,使晶粒拉长、破碎和纤维化,使金属的强度和硬度升高,塑性和韧性降低的现象。
⑧解理断裂:解理断裂是在正应力作用产生的一种穿晶断裂,即断裂面沿一定的晶面(即解理面)分离。
2.解释下列力学性能指标的意义弹性模量);(2)ζ p(规定非比例伸长应力)、ζ e(弹性极限)、ζ s(屈服强度)、ζ (屈服强度);(3)ζ b(抗拉强度);(4)n(加工硬化指数); (5)δ (断后伸长率)、ψ (断面收缩率)4.常用的标准试样有 5 倍和10倍,其延伸率分别用δ 5 和δ 10 表示,说明为什么δ 5>δ 10。
答:对于韧性金属材料,它的塑性变形量大于均匀塑性变形量,所以对于它的式样的比例,尺寸越短,它的断后伸长率越大。
5.某汽车弹簧,在未装满时已变形到最大位置,卸载后可完全恢复到原来状态;另一汽车弹簧,使用一段时间后,发现弹簧弓形越来越小,即产生了塑性变形,而且塑性变形量越来越大。
试分析这两种故障的本质及改变措施。
答:(1)未装满载时已变形到最大位置:弹簧弹性极限不够导致弹性比功小;(2)使用一段时间后,发现弹簧弓形越来越小,即产生了塑性变形,这是构件材料的弹性比功不足引起的故障,可以通过热处理或合金化提高材料的弹性极限(或屈服极限),或者更换屈服强度更高的材料。
材料力学性能第七章-金属的磨损
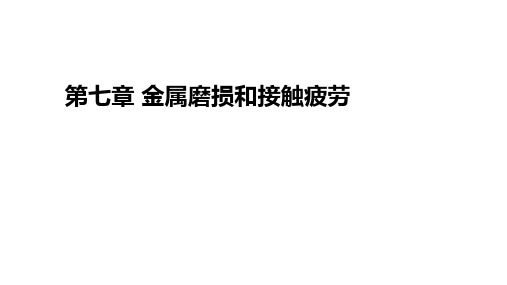
冲蚀磨损
定义:流体或固体以松散的小颗粒按一定的速度和角度对材料表面进行冲击所 造成的磨损。
分类:气固冲蚀、流体冲蚀、液滴冲蚀和气蚀磨损 现象:短程沟槽、冲蚀坑、微小裂纹 塑性材料,短程微切削;脆性材料,裂纹形成与快速扩展 影响因素:冲击角、粒子性态、材料硬度
腐蚀磨损
定义:在摩擦过程中,摩擦副之间或摩擦副表面与环境介质发生化学或电化学反 应形成腐蚀产物,腐蚀产物的形成和脱落引起腐蚀磨损。
飞机起落架
高性能炭/炭航空制动材料的制备技术 黄伯云:国家技术发明奖一等奖
2. 影响因素
摩擦副材料、润滑条件、加载方式和大小、相对运动性(方式和速度)以及工 作温度。
磨损是一个复杂的系统工程
机件正常运行的磨损过程
(a)磨损量与 时间或行程关系曲线;
(b)磨损速率与 时间或行程关系曲线
3. 磨损的分类方法
法向力 在V滑动一定时,F↑、V↑。F>1/3H,V ↑ ↑
滑动速度 在F一定时, V滑动↑、V先↑后↓
表面粗糙度、表面温度以及润滑状态
硬度及载荷的影响
粘着磨损一般随法向载荷增加到某一临界值后而急剧增加,如图所示,K/H的比
值实际上是材料硬度与许用压力的关系。当载荷值超过材料硬度值的1/3时,磨 损急剧增加,严重时咬死。 因此设计中选择的许用压力必须低于材料硬度值的1/3。
• 极压添加剂是在高温条件下,分解出活性的金属化合物薄膜,防止金属因干摩擦或边界摩擦条件 下而引起的粘着现象。
5. 改善粘着磨损耐磨性的措施
(1) 选择粘着倾向较小的摩擦副配对材料 互溶性小、表面易形成化合物、金属与非金属配对
(2) 采用表面化学热处理改变材料表面状态 渗硫、渗氮、磷化、氮碳共渗等。
材料力学性能教学日历2015-9-7

大连理工大学教学日历
课程名称材料力学性能主讲教师曹志强总学时数32
课程性质必修助课教师康慧君讲课32 实验2上机习题专业名称材成、材物、材损、材金授课对象材料13 授课地点材料馆212
注: 本教学日历由主讲教师填写,一式两份,由教研室主任和教学系主任签字后于每学期的第一周内交系教务办公室一份备案,并作为有关教学检查的依据。
按教学大纲、校历编排教学日历。
●课程性质:系指必修、选修或系列讲座。
❍教学性质:系指讲课、习题课、实验课等。
材料力学性能第七章金属的磨损ppt课件

➢ 根据剥落裂纹起始位置及形态不同,分为:
➢ (1) 麻点剥落(点蚀)
➢ (2) 浅层剥落
➢
(3) 深层剥落(表面压碎)
46
2. 接触应力
➢ 两物体相互接触时,在表面上产生的局部压入应力称 为接触应力,也称为赫兹应力。
➢ 线接触(齿轮)与点接触(滚珠轴承)
上图为温度对胶合磨损的影响,可以看出, 当表面温度达到临界值(约80℃)时, 磨损量 和摩擦系数都急剧增加。
17
润滑油、润滑脂的影响
在润滑油、润滑脂中加人油性或极压添加剂能提高润 滑油膜吸附能力及油膜强度,能成倍地提高抗粘着磨 损能力。
油性添加剂是由极性非常强的分子组成,在常温条件 下,吸附在金属表面上形成边界润滑膜,防止金属表 面的直接接触,保持摩擦面的良好润滑状态。
磨损是一个复杂的系统工程
6
机件正常运行的磨损过程
(a)磨损量与 时间或行程关系曲线;
(b)磨损速率与 时间或行程关系曲线
7
3. 磨损的分类方法
粘着磨损 磨粒磨损
冲蚀磨损 疲劳磨损 微动磨损 腐蚀磨损
8
§7.2 磨损模型
一、粘着磨损 1. 磨损机理 ➢定义:在滑动摩擦条件下,当摩擦副相对滑动速 度较小(钢小于1m/s)时发生的, ➢原因:缺乏润滑油,摩擦副表面无氧化膜,且单 位法向载荷很大,σ接触>σs又称咬合磨损
36
主轴转速 : 60r/min ~ 12000r/min
主轴转速示值准确度: ± 2r/min
高温炉温度范围: 室温~ 800℃;
高温炉密封性能: 在连续充入氮气(纯度
99.9%以上)的条件下,炉内 氧气含量应能达到1%以下。 最大负荷:
2015年材料力学性能思考题大连理工大学

一、填空:1.提供材料弹性比功的途径有二,提高材料的,或降低。
2.退火态和高温回火态的金属都有包申格效应,因此包申格效应是具有的普遍现象。
3.材料的断裂过程大都包括裂纹的形成与扩展两个阶段,根据断裂过程材料的宏观塑性变形过程,可以将断裂分为与;按照晶体材料断裂时裂纹扩展的途径,分为和;按照微观断裂机理分为和;按作用力的性质可分为和。
4.滞弹性是指材料在范围内快速加载或卸载后,随时间延长产生附加的现象,滞弹性应变量与材料、有关。
5.包申格效应:金属材料经过预先加载产生少量的塑性变形,而后再同向加载,规定残余伸长应力;反向加载,规定残余伸长应力的现象。
消除包申格效应的方法有和。
6.单向静拉伸时实验方法的特征是、、必须确定的。
7.过载损伤界越,过载损伤区越,说明材料的抗过载能力越强。
8. 依据磨粒受的应力大小,磨粒磨损可分为、、三类。
9.解理断口的基本微观特征为、和。
10.韧性断裂的断口一般呈杯锥状,由、和三个区域组成。
11.韧度是衡量材料韧性大小的力学性能指标,其中又分为、和。
12.在α值的试验方法中,正应力分量较大,切应力分量较小,应力状态较硬。
一般用于塑性变形抗力与切断抗力较低的所谓塑性材料试验;在α值的试验方法中,应力状态较软,材料易产生塑性变形,适用于在单向拉伸时容易发生脆断而不能充分反映其塑性性能的所谓脆性材料;13.材料的硬度试验应力状态软性系数,在这样的应力状态下,几乎所有金属材料都能产生。
14. 硬度是衡量材料软硬程度的一种力学性能,大体上可以分为、和三大类;在压入法中,根据测量方式不同又分为、和。
15. 国家标准规定冲击弯曲试验用标准试样分别为试样和试样,所测得的冲击吸收功分别用、标记。
16. 根据外加压力的类型及其与裂纹扩展面的取向关系,裂纹扩展的基本方式有、和。
17. 机件的失效形式主要有、、三种。
18.低碳钢的力伸长曲线包括、、、、断裂等五个阶段。
19.内耗又称为,可用面积度量。
大连理工金属切削原理

切削与磨削原理3.1.3 前刀面上刀-屑的摩擦与积屑瘤1.摩擦面上的接触状态1)峰点型接触(F 不太大时):m= f/F=tsAr/ss Ar=ts/ss=常数此时的摩擦状态为滑动摩擦(外摩擦)。
ss--材料的拉压屈服极限ts--材料的剪切屈服极限Aa--名义接触面积Ar--实际接触面积2)紧密型接触(F 很大时):m= f/F= tsAa/F=ts/sav≠常数此时的摩擦状态为粘结摩擦(内摩擦)。
2.前刀面上刀-屑的摩擦:既有粘结摩擦,也有滑动摩擦,以粘结摩擦为主。
前刀面上的平均摩擦系数可以近似用粘结区的摩擦系数表示:m= ts/sav≠常数当前刀面上的平均正应力sav增大时,m 随之减小。
4.积屑瘤1)现象:中速切削塑性金属时,在前刀面上切削刃处粘有楔形硬块(积屑瘤)。
2)形成原因:(1)在一定的温度和很大压力下,切屑底面与前刀面发生粘结(冷焊);(2)由于加工硬化,滞流层金属在粘结面上逐层堆积(长大)。
3)对切削过程的影响(1)积屑瘤稳定时,保护刀具(代替刀刃切削);(2)使切削轻快(增大了实际前角);(3)积屑瘤不稳定时,加剧刀具磨损;(4)降低尺寸精度;(5)恶化表面质量(增大粗糙度、加深变质层、产生振动)。
--粗加工时可以存在,精加工时一定要避免。
4)抑制方法(1)避免中速切削;(2)提高工件材料的硬度(降低塑性);(3)增大刀具前角(至30~35o);(4)低速切削时添加切削液。
5.剪切角公式∵第一变形区的剪切变形是前刀面挤压摩擦作用的结果,∴切削合力Fr的方向就是材料内部主应力的方向,剪切面的方向就是材料内部最大剪应力的方向。
根据材料力学,二者夹角应为p/4,即:p/4= c+ b- go (tgb= Ff/ Fn= m )f= p/4- b+ go --李和谢弗的剪切角公式(1952)由公式可知:go ↗→ f ↗→ Lh ↘b(m)↘→f ↗→ Lh ↘-前刀面上的摩擦直接影响剪切面上的变形。
- 1、下载文档前请自行甄别文档内容的完整性,平台不提供额外的编辑、内容补充、找答案等附加服务。
- 2、"仅部分预览"的文档,不可在线预览部分如存在完整性等问题,可反馈申请退款(可完整预览的文档不适用该条件!)。
- 3、如文档侵犯您的权益,请联系客服反馈,我们会尽快为您处理(人工客服工作时间:9:00-18:30)。
V-冲蚀磨损体积 M-冲蚀粒子的总质量 v0-粒子入射初速度
18
s-材料屈服强度 -冲击角 0-临界冲击角,0=18.43º
2020年8月7日星 期五
第七章 金属的磨损
由、式可知,冲击角对冲蚀磨损量有 重要影响:18.43º时,冲蚀磨损体积随冲击 角增加明显增加;>18.43º时,冲蚀磨损体积
10
2020年8月7日星 期五
第七章 金属的磨损
微动疲劳中,通常以疲劳强度下降比
frett 1
或疲劳强
1
度下降系数D
(
) frett
1
1
来表示微动损伤的影响。上式中的
1
通常是指寿命为107循环周次的疲劳强度,不一定是真正的
疲劳极限,因为在微动损伤后,即使原先有疲劳极限的材
料,此时也可能不再有疲劳极限了。表7-2示出了材料-1和
随冲击角增加逐渐降低。 实际上,塑性材料表面冲蚀坑是在短程微
切削和塑性变形作用下形成的,在粒子反复冲 击及材料反复塑性变形情况下形成磨屑致使材 料流失。 19
2020年8月7日星 期五
第七章 金属的磨损
脆性材料如陶瓷、玻璃等,其冲蚀磨损是 裂纹形成与快速扩展的过程。当用锐角粒子冲 击脆性材料表面时,人们发现产生两种形状的 裂纹:一种是垂直于表面的初生径向裂纹,另 一种是平行于表面的横向裂纹。在粒子冲击下, 径向裂纹形成及其扩展降低了材料强度,横向 裂纹形成并扩展到表面致使材料脱落变为磨屑 而流失,如图7-14所示。 20
Finnie认为,塑性材料如铝、低碳钢等,表面
受粒子冲击形成冲蚀坑并导致材料流失是由于短程
切削作用所致。他在几个假定的条件下给出下列估
算冲蚀磨损量的公式:
0 0
V
Mv0 2
1
s
sin
2
3sin2
2
·········
···
0 90
V
Mv02 2
1
s
cos2
6
················
w
1
(k 0F 2
k1F )
N
k2S F
N
f
w-微动磨损磨损量;F-法向力;N-振动周次; f-振动频率;
9
S-摩擦表面的峰间滑动距离,k0、k1、k2-常数
2020年8月7日星 期五
第七章 金属的磨损
在工程上,机械系统或部件如搭接接头、 健、推入配合的传动轮、金属静密封、发动 机固定件及离合器等常产生微动磨损。实验 室进行疲劳试验时,有时在试样夹头处出现 许多红色氧化物粉末,最后试样不在工作长 度内而在夹头处断裂,就是以微动磨损蚀坑 为疲劳源,裂纹快速扩展的结果。
材料 0.2%碳钢
b/MPa
-1/MPa
fre -1
tt/MPa
509
255
150
0.59
0.4%碳钢
772
266
87
0.33
0.7%碳钢(正火)
940
216
154
0.71
0.7%碳钢(冷拉)
1360
525
139
0.27
18/9奥氏体不锈钢
598
295
160
0.54
70/30黄铜(退火)
328
89
80
性材料最大冲蚀率出现在冲击角20º~30º之间;一般
工程材料介于二者之间。
粒子速度对材料冲蚀率的影响主要是影响粒子
动能。人们根据试验结果进行分析,可得:=kvn,
其中-冲蚀率;k-常数;v-粒子速度;n-速度指数,通常为2.3~2.4。
23
2020年8月7日星 期五
第七章 金属的磨损
粒子速度对冲蚀磨损的影响通常都是在高速
在研究各种影响因素时,通常要测定材料冲 蚀率的变化。对喷砂型冲蚀,其冲蚀率定义为单 22
2020年8月7日星 期五
第七章 金属的磨损
位 重 量 的 粒 子 造 成 材 料 流 失 的 重 量 (mg/g) 或 体 积
(mm3/g)。大量实验表明,陶瓷、玻璃等脆性材料最
大冲蚀率出现在冲击角90º附近;而铜、铝合金等塑
8
图7-11 微动磨损不同阶段示意图
2020年8月7日星 期五
第七章 金属的磨损
由于微动磨损集中在局部地区,又因两摩擦表
面永不脱落接触,故磨损产物不易排出。在连续振
动时,由于磨屑对于摩擦副表面产生交变接触压应
力,导致表面疲劳破坏形成麻点或蚀坑。蚀坑有可
能是应力集中源,并随后因疲劳裂纹发展引起机件
完全破坏。微动磨损可根据下式定量计算:
第七章 金属的磨损
当然,摩擦学参数如接触压力、滑动速 度、滑动距离、温度等也影响氧化磨损速率。 研究表明,氧化磨损体积与接触压力、滑动距 离成正比,而与氧化膜的厚度、密度、滑动速 度、摩擦副的屈服强度成反比。氧化磨损不一 定是有害的,如果先于其它磨损(如粘着磨损) 发生,还是有利的。
5
2020年8月7日星 期五
材料表面形成的冲蚀坑,可 犁削型
见材料表面被冲蚀的变形。
切削I型冲蚀坑和切削Ⅱ型 切削I型
冲蚀坑均为立方体粒子冲击
材料表面形成的冲蚀坑。切 切削Ⅱ型
削I型有较大的唇片隆起, 这部分材料在随后的冲击时 图7-13 三种典型的冲蚀坑侧面示意图
17 极易脱落形成磨屑。
2020年8月7日星 期五
第七章 金属的磨损
在冲蚀磨损过程中,表面材料的流失主要是由 机械力引起的。在高速粒子不断冲击下,塑性材料 表面逐渐出现短程沟槽和鱼鳞状小凹坑(冲蚀坑), 且变形层有微小裂纹,如图7-12所示。 15
2020年8月7日星 期五
第七章 金属的磨损
16
图7-12 冲蚀磨损
2020年8月7日星 期五
第七章 金属的磨损
犁削型为球型粒子犁削
0.90
70/30黄铜(冷加工)
508
139
90
0.64
Al-4Cu-1Mg-1Mn
430
108
60
0.56
Al-4Mg-0.7Mn
314
100
73
0.73
镍基Inconel 718
1316 550±295* 550±120*
C.P.钛(1M1130)
675
201
123
0.61
Ti-2.5Cu
578
改善微动磨损耐磨性的措施:首先是加强紧配, 保证足够的过盈量,避免产生微小振动。还可 以采用化学热处理方法提高摩擦副表面抗粘着 能力以减轻微动磨损。钢制机件经表面渗硫或 硫氮共渗处理可显著提高抗微动磨损能力。此 外,在摩擦副间加绝缘层或充填聚四氟乙烯, 既可以防止微凸起接触,又阻止氧参与磨损过 程,可以大大减轻微动磨损。 13
2020年8月7日星 期五
第七章 金属的磨损
粒 子 粒 度 对 冲 蚀 有 明 显 影 响 。 粒 度 在 20 ~
200m范围内,材料冲蚀率随粒子粒度的增加而增
加,但达到一定值后,冲蚀率几乎不再发生变化。
在相同条件下,尖角形粒子比圆形粒子造成的
磨损高4倍以上,甚至低硬度的尖角形粒子比高硬
度的圆形粒子造成的磨损还大。
第七章 金属的磨损
四、微动磨损
在机器的嵌合部位和紧
配合处,接触表面之间虽然
没有宏观相对位移,但在外
部变动载荷和振动的影响下
图7-9 微动磨损的产生
产生微小滑动,其振幅约为 10-2m数量级。接触面因
存在小振幅相对振动或往复运动而产生的磨损称为微
动磨损,其特征是摩擦副接触区有大量红色Fe2O3粉末,
还常有因接触疲劳破坏产生的麻点或蚀坑。
2 磨损在一般机械中比较少见,我们只介绍氧化磨损。
2020年8月7日星 期五
第七章 金属的磨损
氧化磨损:氧化磨损速率最小,约0.1~0.5μm/h,属 于 正常类型的磨损。任何存在于大气中的机件表面总会 有一层氧的吸附层。当摩擦副作运动时,由于表面凹 凸不平,在凸起部位单位压力很大,导致产生塑性变 形。塑性变形加剧了氧向金属内部扩散,从而形成氧 化膜。形成的氧化膜强度低,在摩擦副的继续运动下, 氧化膜逐渐被剥落,裸露出新的表面,从而又发生氧 化,随后再被磨去,如此过程反复进行,机件表面被 磨损,这就是氧化磨损过程。
278
123
0.44
Ti-6Al-4V
1095
540
154
0.28
Ti-4Al-4Mo-2Sn-0.5Si
1125
634
139
0.22
Ti-6Al-5Zr-0.5Mo-0.25Si 1054
432
154
0.36
12 *脉动拉伸疲劳,其他数据均为旋转弯曲疲劳。
2020年8月7日星 期五
第七章 金属的磨损
(60~400m/s)范围,速度低于60m/s时一般不会发生严
重的冲蚀磨损。若粒子速度进一步降低,则可能出
现产生冲蚀磨损的速度下限,即所谓门槛速度值,
低于此速度值的粒子与材料表面之间只有单纯的弹
性碰撞而观察不到破坏。例如用直径0.3mm球形铸铁
丸冲击玻璃,门槛速度为9.9m/s;而用同样直径的石
英砂冲击含碳0.11的某种钢时,门槛速度仅为2.7m/s。 24
粒子在冲击材料表面时有时会发生破碎,产生
的粒子碎片又会对表面产生第二次冲蚀,造成材料
25 冲蚀率增加。
2020年8月7日星 期五
第七章 金属的磨损
3.改善冲蚀磨损耐磨性的措施:
设法减小入射粒子和介质的速度。
改变冲击角。
合理利用粒子浓度和粒度。
合理设计机件形状。
尽可能选用冲蚀磨损抗力较高的材料或表面处