神雾转底炉处理钢铁厂粉尘及有色冶金渣研发及应用实践
基于转底炉直接还原技术

2020/1/24
9
返回目录
基于转底炉直接还原技术 钢铁厂粉尘、污泥处理工艺介绍
2.转底炉技术目前发展情况
2.1 转底炉技术由来及发展 2.2 转底炉技术特点 2.3 转底炉技术应用方向 2.4 转底炉产品用途
直接还原法 (产品多为固态团块)
熔融还原法 (产品多为液态铁水)
气基法(块矿或造块) 煤基法(块矿或造块) COREX(原料为块矿) FINEX(原料为粉矿)
HIsmelt(原料为粉矿)
2020/1/24
4
返回目录
基于转底炉直接还原技术 钢铁厂粉尘、污泥处理工艺介绍 1.直接还原技术的兴起及分类
1.1 直接还原技术简述
从1975年至2005年,全世界直接还原铁(DRI)的年产量从 80万吨增至5600万吨、即70倍。2007年世界非高炉炼铁产量达 6722万吨,约为粗钢产量的5%,同比增长12.4%。发展迅速。
2020/1/24
6
返回目录
基于转底炉直接还原技术 钢铁厂粉尘、污泥处理工艺介绍 1.直接还原技术的兴起及分类
1.3 直接还原技术的分类
直接 还原 炼铁 技术
气基还原技术 (还原剂为天然气等)
煤基还原技术 (还原剂为煤炭等)
…
Midrex 竖炉法 HYLⅢ 竖炉法
回转窑法 隧道窑法 转底炉法
…
2020/1/24
7
返回目录
基于转底炉直接还原技术 钢铁厂粉尘、污泥处理工艺介绍
1.直接还原技术的兴起及分类
1.4 国家发展政策
十四、钢铁; 8、直接还原。 3)2005年12月2日中华人民共和国国家发展改革委员会第40号令《产业结 构调整指导目录(2005年本)》:
转底炉处置含锌粉尘压球用粘结剂工业化应用研究

转底炉处置含锌粉尘压球用粘结剂工业化应用研究摘要:近些年来,随着钢铁工业的飞速发展,钢铁生产产生的粉尘对环境和人类的危害日益加重,这也对企业铁前生产造成危害。
钢铁企业一般将低锌含铁粉尘配入烧结使用,但中高锌粉尘配入烧结会降低烧结矿质量,并对高炉顺性和高炉寿命产生不良影响。
如何经济地实现含锌粉尘的高效利用成为难题。
关键词:转底炉;含锌粉尘;压球;粘结剂;工业化应用引言目前处理冶金尘泥的方式中,因转底炉工艺的适应性较好、可靠性高、易于操作和维护、且对环境污染相对较小,具有较大应用价值,更适合钢铁企业流程化生产。
转底炉生产线采用压球工艺对含锌粉尘进行成型及烘干含锌粉尘的脱锌处理,脱锌后的金属化物料返回炼铁炼钢工序得到循环利用,锌富集于烟尘进行收集后用于外售。
由于含锌粉尘种类多、性能差异大,必须使用粘结剂强化成球,以提高成球率及球团强度保证转底炉运转稳定及产品质量。
但是,目前大多使用淀粉类粘结剂,存在添加量大(3%~7%)、生产成本高、成品率较低及成品粉化率高(全流程返料量高达30%~60%),易导致转底炉底结块,影响排料等问题。
1转底炉发展概述转底炉工艺最初是一种煤基直接还原炼铁工艺,后来用于处理钢铁厂含锌粉尘,尤其在日本和中国得到快速发展。
20世纪50年代,美国Ross公司发明了转底炉直接还原法,取名为Fastmet工艺。
1974年,加拿大的国际镍集团公司用转底炉处理不锈钢的氧化物废料,并命名为Inmetco工艺。
日本神户钢铁厂与美国Miderx公司联合开发转底炉直接还原新工艺,在20世纪90年代中后期取得突破性进展,生产出了高纯度粒铁,该产品被命名为ITmk3。
新日铁于1998年从美国MaumeeR&E公司引进转底炉技术处理钢铁厂粉尘,技术改进后在日本Kimitsu、Hikari、Hirohata等企业建造了工业生产规模的转底炉。
北京科技大学是我国最早研究转底炉的科研院所,在1992、1996和2001年分别在河南舞钢、鞍山和山西冀城建成了不同规模的转底炉。
神雾节能全球首创 有色金属渣循环利用示范项目投产 引领世界清洁
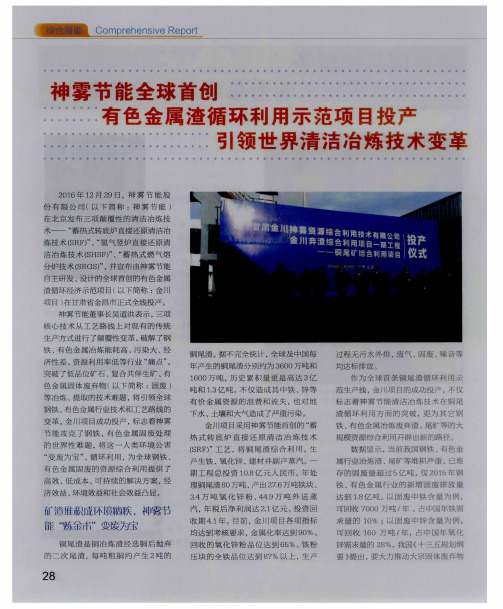
分炉技 术 ( S R GS ) ” , 并宣布 由神雾节 能
自主研发 、 设计 的全球首创的有 色金 属
渣循环经 济示范项 目( 以下简称 : 金 川 项目 ) 在 甘 肃省 金 昌 市 正 式 全 线 投 产 。 神雾节能 董事长吴道洪表 示 , 三 项
核 心技 术从 工 艺路 线上 对现 有 的传 统 生产方 式进行了颠覆性变 革 , 破解 了钢 铁、 有 色金 属 冶炼能 耗高 、污染大 、 经 济性 差 、 资源利 用率低 等行业 “ 痛点 ” , 突破 了低品 位矿 石 、 复合 共伴生矿 、 有 色金 属 固体 废弃物 (以下 简称 : 固废 ) 等冶 炼 、 提取 的技术难题 。 将引领全 球 钢铁 、 有色金属行 业技 术和工艺路线 的 变 革。金川项 目成功投 产 , 标志着神 雾
1 6 0 0万吨 ,历 史累 积 量 更是 高达 3亿 吨和 1 . 3亿吨 。不 仅造 成 其中 铁 、 锌 等
有 价 金 属 资 源 的 浪 费 和 流 失 ,也 对 地
下水 、 土壤和大气造成 了严重污染 。 金』 I l 项 目采用神 雾节能首 创的 “ 蓄 热 式 转 底 炉 直 接 还 原 清 洁 冶 炼 技 术 ( S RF ) ”工 艺 , 将 铜 尾渣 综 合 利 用 , 生 产 生铁 、 氧化锌 、 建材 并副 产蒸汽 。一 期 工 程 总投 资 1 0 . 8 亿元人民币, 年 处 理铜 尾渣 8 0万吨 , 产出2 7 . 6 万吨铁块 、 3 . 4万 吨 氧 化 锌 粉 、 4 4 . 9万 吨 外 送 蒸 汽, 年税 后 净利 润 达 2 . 1 亿元 、 投 资回 收期4 . 1 年 。目前 , 金 川项 目各 项 指标 均 达到 考核 要求 , 金 属化率达 到 9 0 %、 回收 的 氧 化锌 粉 品 位 达到 6 5 %、 铁 粉
神雾的最新的转底炉直接还原技术国际领先

神雾的最新的转底炉直接还原技术国际领先神雾集团的核心节能与大气雾霾治理技术创新专利成果“蓄热式转底炉直接还原技术及成套工程化装备”,可处理各种低品位难选矿、复合共伴生矿、低品位红土镍矿、钢铁厂粉尘、有色行业冶金渣等劣质含铁资源。
该技术在高效提取复杂原矿中铁资源的同时,还能够实现对Ni、Ti、V、K、Na、Pb、Zn等元素的协同提取和高值化利用。
该项技术摒弃传统高炉烧结、焦化等高能耗、高污染工序的弊端,对原料的适应性广,只采用普通煤炭资源,就能节能、环保、高效、经济的实现劣质含铁矿物的高效清洁冶炼。
从目前我国铁矿资源来看,普遍存在含铁品位低、含铁矿物粒度细、矿物组成复杂的特点,劣质含铁资源占国内铁矿石储量的97%以上。
此外,现有钢铁厂大量的含铁粉尘、有色行业每年产生的上亿吨冶金废渣的综合开发利用也已迫在眉睫。
为满足高炉炼铁对优质铁矿石资源的刚性需求,国内钢铁企业长期从国外进口优质铁矿石,在进口铁矿石价格谈判上十分被动,这使得积极开发国内现存的大量低品位劣质含铁资源意义重大。
神雾蓄热式转底炉直接还原技术处理劣质含铁资源和冶金固废的技术指标先进:低品位难选矿金属化球团磨矿磁选铁粉品位大于90%,铁回收率大于85%;劣质含铁资源熔分铁回收率大于95%;红土镍矿金属化球团熔分可获得高镍铁,镍回收率大于95%。
神雾技术的工艺能耗较低,以沙钢含锌粉尘的转底炉处理工艺为例,单位产品的投资额相比国外转底炉降低约60%以上,单位产品能耗为209.3kgce,比回转窑工艺节能25%,比普通转底炉工艺节能16%,二氧化碳排放下降15%以上,作业率超过90%。
沙钢30万吨转底炉项目年新增产值3.52亿元、利润1.14亿元,投资回收期1.84年(不含建设期),项目具有较好的经济效益。
据不完全统计,我国每年约产生1800万吨含锌粉尘,如全部采用神雾转底炉直接还原冶炼技术进行处理,可生产直接还原铁球团1100万吨,解决6000多人就业,每年新增产值180亿左右,未来随着含锌粉尘量的不断提高,转底炉处理含锌粉尘将具有更加广阔的市场前景。
转底炉直接还原铜渣回收铁、锌技术

pr o c e s s o f RHF d ir e c t r e d uc t i on a nd g a s m e l i t ng s e pa r a t i on. t h e r e c o ve r y r a io t i s m o r e t h a n 93 %
pi l o t e x pe im e r nt s ho we d t h a t a mo l t e n i r o n wi t h a p u it r y mo r e t ha n 94% ma s s c a n be g a i ne d rom f t he c o p pe r s l a g by
转 底炉 直 接还 原 铜 渣 回收铁 、锌 技 术
曹志成 ,孙体 昌 ,吴道 洪 ,薛 逊 ,刘 占华
( 1 .北京科技大学 金属矿 山高效开采与安全教育部重点实验室 ,北京 1 0 0 0 8 3 ; 2 北京神雾环境 能源科技集 团股份有 限公 司 ,北京 1 0 2 2 0 0 ) 摘 要 :采用转底炉直接还原工艺 ,将铜渣含碳球团在高温条件下直接还原得到金属化球团和高品位氧化锌
z i nc o x i d e d us t c a n be ob t a i n e d f r o m t h e c a r bo n b e a in r g pe l l e t s o f c o p pe r s l a g a t a h i g h t e mpe r a t u r e.The i r on c a n be r e c ov e r e d b y me l in t g o r g r i nd ing /m a g ne t i c s e pa r a t i on me t hod a s a r a w ma t e r i a l f o r s t e e l be a ing t c op pe r .Re s u l t s o f t h e
钢铁厂除尘灰及其他废弃物的再利用技术
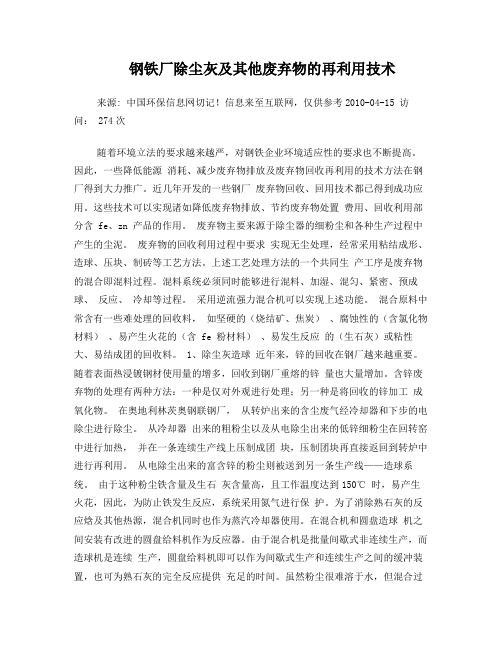
钢铁厂除尘灰及其他废弃物的再利用技术来源: 中国环保信息网切记!信息来至互联网,仅供参考2010-04-15 访问: 274次随着环境立法的要求越来越严,对钢铁企业环境适应性的要求也不断提高。
因此,一些降低能源消耗、减少废弃物排放及废弃物回收再利用的技术方法在钢厂得到大力推广。
近几年开发的一些钢厂废弃物回收、回用技术都已得到成功应用。
这些技术可以实现诸如降低废弃物排放、节约废弃物处置费用、回收利用部分含 fe、zn 产品的作用。
废弃物主要来源于除尘器的细粉尘和各种生产过程中产生的尘泥。
废弃物的回收利用过程中要求实现无尘处理,经常采用粘结成形、造球、压块、制砖等工艺方法。
上述工艺处理方法的一个共同生产工序是废弃物的混合即混料过程。
混料系统必须同时能够进行混料、加湿、混匀、紧密、预成球、反应、冷却等过程。
采用逆流强力混合机可以实现上述功能。
混合原料中常含有一些难处理的回收料,如坚硬的(烧结矿、焦炭)、腐蚀性的(含氯化物材料)、易产生火花的(含 fe 粉材料)、易发生反应的(生石灰)或粘性大、易结成团的回收料。
1、除尘灰造球近年来,锌的回收在钢厂越来越重要。
随着表面热浸镀钢材使用量的增多,回收到钢厂重熔的锌量也大量增加。
含锌废弃物的处理有两种方法:一种是仅对外观进行处理;另一种是将回收的锌加工成氧化物。
在奥地利林茨奥钢联钢厂,从转炉出来的含尘废气经冷却器和下步的电除尘进行除尘。
从冷却器出来的粗粉尘以及从电除尘出来的低锌细粉尘在回转窑中进行加热,并在一条连续生产线上压制成团块,压制团块再直接返回到转炉中进行再利用。
从电除尘出来的富含锌的粉尘则被送到另一条生产线——造球系统。
由于这种粉尘铁含量及生石灰含量高,且工作温度达到150℃ 时,易产生火花,因此,为防止铁发生反应,系统采用氮气进行保护。
为了消除熟石灰的反应焓及其他热源,混合机同时也作为蒸汽冷却器使用。
在混合机和圆盘造球机之间安装有改进的圆盘给料机作为反应器。
转底炉直接还原处理赤泥技术研究

3工艺研究
图1试验流程图
3.1 还原温度试验
先进行还原温度探索试验,固定碳氧比为1.8,石灰石用量为10%,焙烧时间固定为30min,选 择了1200。C、1250℃、1300℃、1330℃四个温度进行试验。试验考察球团的金属化率以及球团在高
一163—
罗第六届尾矿与冶金渣综合利用技术研讨会置衢州市项目招商对接会 温下是否熔化粘结。球团的金属化率见图2。
表6经济技术分析
处理40万吨赤泥,熔分工艺投资48000万元,磨矿磁选工艺投资42000万元。从投资回收期看, 磨矿磁选工艺投资回收期(不含建设期)为4.97年,由于熔分工艺投资较高,其投资回收期(不含 建设期)也较高为6.29年,但熔分工艺年税后利润相对较高。两种工艺流程处理赤泥都有较好的效益。 5结论
图3还原剂用■试验结果
从图中可以看出,随着还原剂用量的增加,金属化率先升高后降低,当碳氧比从1.5升高到1.8后, 增幅不明显。在碳氧比为1.5时,金属化率高于80%。因此,选择碳氧比为1.5时的还原剂用量。 3.3石灰石用量试验
固定碳氧比为1.5,焙烧温度1300。C,焙烧时间30rain。考察配人石灰石用量对球团金属化率的 影响。试验结果图4。
川1王洪,王静松,刘江,等.基于直接还原熔分的高铁赤泥综合利用试验研究[J].轻金属, 2013(11:19—21.
[2]朱强,齐波.国内赤泥综合利用技术发展及现状[J】.轻金属,2009(8):7-10. 李冬,潘利祥,赵良庆,等.赤泥综合利用的研究进展阴.环境工程,2014,32卷增刊:616-625. [3]何伯泉,周国华,薛玉兰.赤泥在环境保护中的应用[J].轻金属,2001,(2):24.26. [4]董凤芝,刘心中,姚德.粉煤灰和赤泥的综合利用[J].矿产综合利用,2004,(6):37-39. [5]周文献,谢友均,刘宝举.赤泥对粉煤灰激发作用的试验研究[J].混凝土,2002,(1):37-40.
【企业项目】转底炉处理含铁、锌尘泥资源循环利用关键技术及示范科技成果
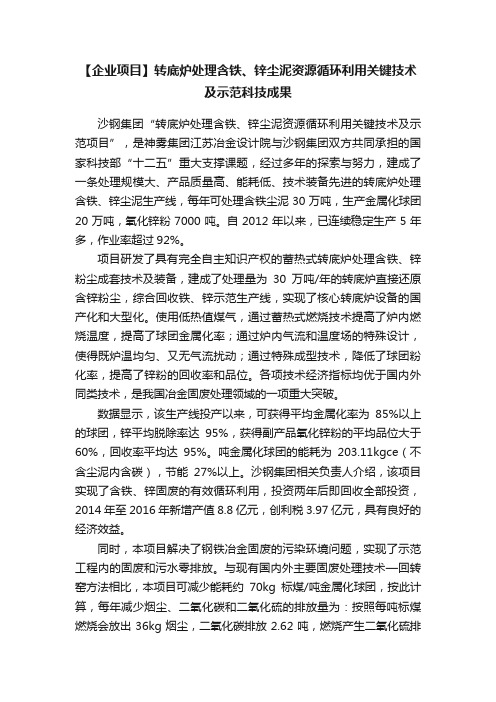
【企业项目】转底炉处理含铁、锌尘泥资源循环利用关键技术及示范科技成果沙钢集团“转底炉处理含铁、锌尘泥资源循环利用关键技术及示范项目”,是神雾集团江苏冶金设计院与沙钢集团双方共同承担的国家科技部“十二五”重大支撑课题,经过多年的探索与努力,建成了一条处理规模大、产品质量高、能耗低、技术装备先进的转底炉处理含铁、锌尘泥生产线,每年可处理含铁尘泥30万吨,生产金属化球团20万吨,氧化锌粉7000吨。
自2012年以来,已连续稳定生产5年多,作业率超过92%。
项目研发了具有完全自主知识产权的蓄热式转底炉处理含铁、锌粉尘成套技术及装备,建成了处理量为30万吨/年的转底炉直接还原含锌粉尘,综合回收铁、锌示范生产线,实现了核心转底炉设备的国产化和大型化。
使用低热值煤气,通过蓄热式燃烧技术提高了炉内燃烧温度,提高了球团金属化率;通过炉内气流和温度场的特殊设计,使得既炉温均匀、又无气流扰动;通过特殊成型技术,降低了球团粉化率,提高了锌粉的回收率和品位。
各项技术经济指标均优于国内外同类技术,是我国冶金固废处理领域的一项重大突破。
数据显示,该生产线投产以来,可获得平均金属化率为85%以上的球团,锌平均脱除率达95%,获得副产品氧化锌粉的平均品位大于60%,回收率平均达95%。
吨金属化球团的能耗为203.11kgce(不含尘泥内含碳),节能27%以上。
沙钢集团相关负责人介绍,该项目实现了含铁、锌固废的有效循环利用,投资两年后即回收全部投资,2014年至2016年新增产值8.8亿元,创利税3.97亿元,具有良好的经济效益。
同时,本项目解决了钢铁冶金固废的污染环境问题,实现了示范工程内的固废和污水零排放。
与现有国内外主要固废处理技术—回转窑方法相比,本项目可减少能耗约70kg标煤/吨金属化球团,按此计算,每年减少烟尘、二氧化碳和二氧化硫的排放量为:按照每吨标煤燃烧会放出36kg烟尘,二氧化碳排放2.62吨,燃烧产生二氧化硫排放17 kg计算,按转底炉现有产量,每年减少烟尘排放504吨,减少二氧化碳排放3.67万吨,减少二氧化硫排放238吨。
转底炉直接还原铜渣回收铁、锌技术

转底炉直接还原铜渣回收铁、锌技术曹志成;孙体昌;吴道洪;薛逊;刘占华【摘要】采用转底炉直接还原工艺,将铜渣含碳球团在高温条件下直接还原得到金属化球团和高品位氧化锌粉尘,再通过熔分或磨矿磁选方式将铁回收,得到的铁产品可作为冶炼含铜钢的原料.转底炉中试结果表明:采用"转底炉直接还原-燃气熔分"流程处理铜渣,可获得TFe品位94%以上、铁回收率93%以上的熔分铁水;采用"转底炉直接还原-磨矿磁选"流程处理铜渣,可获得TFe品位90%以上、铁回收率85%以上的金属铁粉;采用两种流程处理铜渣,均可获得锌品位60.02%的ZnO粉尘.结果表明,经过转底炉直接还原,铜渣中的铁橄榄石Fe2SiO4和磁铁矿Fe3O4相转变为含有金属铁Fe、二氧化硅SiO2和少量辉石相Ca(Fe,Mg)Si2O6的金属化球团,具备通过磨选或熔分进行进一步富集的条件.%By using RHF (Rotary hearth furnace) direct reduction method, the metallized pellets and a high grade zinc oxide dust can be obtained from the carbon bearing pellets of copper slag at a high temperature.The iron can be recovered by melting orgrinding/magnetic separation method as a raw material for steel bearing copper.Results of the pilot experiment showed that a molten iron with a purity more than 94% mass can be gained from the copper slag by process of RHF direct reduction and gas melting separation, the recovery ratio is more than 93% mass.An iron powder of more than 90% mass purity can be obtained by process of RHF direct reduction and grinding and magnetic separation,the recovery ratio is more than 85%.A dust of more than 60% mass Zinc can also be gained with the two kinds of process mentioned above.It is believed that after direct reduction in RHF, fayalite (Fe2SiO4)and magnetite (Fe3O4) in the copper slag can be changed into the metallized pellets containing iron(Fe), quartz (SiO2) and a small amount of augite (Ca(Fe,Mg)Si2O6), which can be recovered by the magnetic separation or melting process.【期刊名称】《材料与冶金学报》【年(卷),期】2017(016)001【总页数】4页(P38-41)【关键词】铜渣;转底炉;直接还原;磁选;燃气熔分【作者】曹志成;孙体昌;吴道洪;薛逊;刘占华【作者单位】北京科技大学金属矿山高效开采与安全教育部重点实验室,北京100083;北京神雾环境能源科技集团股份有限公司,北京102200;北京科技大学金属矿山高效开采与安全教育部重点实验室,北京100083;北京神雾环境能源科技集团股份有限公司,北京102200;北京神雾环境能源科技集团股份有限公司,北京102200;北京神雾环境能源科技集团股份有限公司,北京102200【正文语种】中文【中图分类】TF09;TD923从2006年至2015年,我国精炼铜产量持续快速增长.2015年我国铜产量达796万t,其中97%以上由火法冶炼生产,每生产1t铜平均要产生2~3 t铜渣[1],据此估计我国每年产生铜渣量约1 500万t.据统计,我国铜渣堆存量累计已达到1.4亿t以上,这些尾渣中不仅含有大量的铁元素,且富含Zn、 Pb、 Cu和Co等多种有价金属元素,是宝贵的二次资源[2-4].由于铜渣中的铁含量较高,其平均品位远高于我国铁矿石可采品位[5],因此铁元素的回收利用价值较高.然而铜渣中的铁主要以铁硅酸盐(铁橄榄石,2FeO·SiO2)的形式存在[6],渣中SiO2含量较高使其无法直接用于传统的高炉流程中,又因矿物嵌合紧密,难以采用传统的选矿方式分离出脉石生产铁精矿[7-8].近年来随着火法工艺的发展,采用高温还原等工艺[9-11]处理铜渣的技术也逐渐成熟起来,其中直接还原工艺成为研究的热点.本文采用“转底炉直接还原—磨矿磁选”和“转底炉直接还原—燃气熔分”技术对铜渣进行了大量的基础试验和中试研究.结果表明,该技术可有效实现铜渣中铁、锌元素的综合回收利用,减少堆存造成的土地占用及环保问题,是实现铜渣资源高效综合利用的有效途径.1.1 原料性质试验选用国内某铜冶炼渣经浮选回收铜的尾矿(以下简称“铜渣”)为原料,化学成分见表1.为探明铜渣中主要矿物组成,对试验铜渣进行了XRD衍射分析,详见图1.可见其中铁矿物主要为铁橄榄石Fe2SiO4和磁铁矿Fe3O4相,采用直接选矿的方法仅能回收其中的磁铁矿,无法高效回收铁橄榄石中的铁元素.试验选用无烟煤固定碳含量质量分数为72.36%,灰熔点为1 258 ℃;选用工业石灰石为磨矿磁选流程的助熔剂,其氧化钙含量为51%;选用工业石灰石块作为助熔剂,其氧化钙含量为53%.1.2 试验流程及原理试验的流程:将铜渣经原料处理后,与还原煤、添加剂和黏结剂等按一定比例配合混匀,经过圆盘造球机造块,制成含碳球团,含碳球团烘干后布入转底炉,在炉内1 200 ~1 300 ℃ 的还原区还原为金属化球团,球团中ZnO则被还原成金属Zn,挥发进入烟气中,经再氧化生成ZnO,随烟气富集到布袋收尘系统中,产出的金属化球团,可采用热装—熔分工艺实现渣铁分离从而得到熔分铁水,也可采用直接水淬冷却—磨矿磁选工艺得到金属铁粉.转底炉处理铜渣的工艺流程如图2所示. 试验原理:铜渣中的硅酸铁与还原剂中的碳反应方程见式(1),可见硅酸铁还原为金属铁为强吸热反应.Fe2SiO4(s)+2C(s)→2Fe(s)+SiO2(s)+2CO(g).59 T (J·mol-1)为了促进硅酸铁反应,添加了石灰石作为助熔剂,其反应方程见式(2)Fe2SiO4(s) + 2CaO(s) + 2C(s) → CaSiO4(s)+2Fe(s) + 2CO.71 T (J·mol-1)试验顺序为首先进行基础试验,在获得最佳工艺条件后再进行转底炉中试验证.分别采用“转底炉直接还原-燃气熔分”流程和“转底炉直接还原-磨矿磁选”流程对上述铜渣进行了转底炉中试,每种流程的铜渣处理量为120 t.转底炉处理量为2~3 t/h;燃气熔分炉处理量为 1 t/h;金属化球团磨矿磁选厂处理量为 2 t/h.2.1 直接还原—熔分流程基础试验获得最佳的工艺条件为:铜渣:还原煤=100∶25(质量比),还原温度1260 ℃,还原时间 40 min. 此时球团金属化率为85.96 %;将球团热装进行熔分试验,熔分前配入金属化球团质量18%的生石灰块,熔分温度1 530 ℃,熔分时间 50 min,此时获得熔分铁的TFe品位95.82 %,回收率为97.16 %.按照此工艺条件进行转底炉中试,将转底炉产出的约700 ℃的金属化球团热装入钢包,直接投入燃气熔分炉进行熔分,可获得铁品位96.73%、铁回收率96.81%的铁水,中试熔分铁水成分分析见表2.熔分铁水中w[S]为0.29%,经脱硫处理后作为炼钢原料进行销售,另外铁水中含0.35%的铜,可作为冶炼含铜耐候钢(铜质量分数0.25%~0.80%)的原料.2.2 直接还原—磨选流程基础试验获得最佳的工艺条件为:铜渣:还原煤:石灰石=100∶25∶18(质量比),还原温度1250 ℃,还原时间35min,此时球团金属化率为90.12 %.采用两段磨矿磁选流程,一段磨矿细度-0.074 mm占75.35 %,磁场强度 143.31 kA/m;二段磨矿细度-0.074 mm占60.13 %,磁场强度95.54 kA/m,得到金属铁粉TFe 品位91.83 %,铁回收率88.05 %.按照此工艺条件进行转底炉中试,转底炉产出的金属化球团直接落入水淬池冷却,由捞渣机捞出送往磨矿磁选厂,可获得铁品位91.78%、铁回收率87.81%的直接还原铁粉,中试铁粉成分分析见表3.对比熔分流程得到的铁水成分,磨选流程得到的金属铁粉中杂质硫含量较低,主要原因是85%以上的硫被固结在尾矿中,将铁粉干燥、成型后可作为冶炼含铜钢原料.2.3 中试氧化锌粉尘铜渣中的Pb、Zn等元素,在转底炉直接还原过程中挥发进入烟气,通过布袋除尘系统收集,得到氧化锌粉尘成分分析见表4.转底炉中试验证结果表明,通过上述两种流程处理铜渣,可获得锌品位60.02%的氧化锌粉尘,整个流程Pb、Zn的脱除率分别为98.89%和97.52%.为探明铜渣还原及后续处理流程得到产品中铁的矿相存在形式及变化规律,对铜渣原矿、熔分流程金属化球团、磨选流程金属化球团和磨选流程获得金属铁粉进行了XRD衍射分析,详见图3.由图3可见,铜渣中的铁橄榄石Fe2SiO4和磁铁矿Fe3O4相经过转底炉直接还原后,在球团中以金属铁Fe、二氧化硅SiO2和少量辉石相Ca(Fe,Mg)Si2O6相存在,为后续熔分流程或磨矿磁选流程提铁创造了有利条件.对比磨选流程与熔分流程,前者所得金属化球团中的辉石要多于后者,主要原因是磨选流程在配料中加入了石灰石,石灰石分解产生的氧化钙与铁橄榄石反应所致.(1)铜渣中铁主要以2FeO·SiO2的形式存在,采用常规工艺难以将其中的含铁资源进行回收,本文采用转底炉直接还原技术,对铜渣进行了燃气熔分和磨矿磁选两种流程的中试规模研究,在提取铁元素的同时,也实现了锌元素的高效回收.(2)转底炉中试结果表明:采用“转底炉直接还原—燃气熔分”流程,可获得TFe品位96.73%的熔分铁水,铁回收率96.81%;采用“转底炉直接还原—磨矿磁选”流程,可获得TFe品位91.78%的金属铁粉,铁回收率87.81%;两种流程均可获得锌品位60.02%的氧化锌粉尘.(3)通过XRD衍射分析,经过转底炉直接还原,铜渣中的铁橄榄石Fe2SiO4和磁铁矿Fe3O4相转变为含有金属铁Fe、二氧化硅SiO2和少量辉石相Ca(Fe,Mg)Si2O6的金属化球团,具备通过磨选或熔分实现进一步富集的条件. (4)目前,金川集团与神雾集团成立合资公司,在金川已建成年处理80万t铜渣转底炉示范生产线.该项目采用转底炉直接还原—磨矿磁选—铁粉压块工艺流程,项目的投产将为有色行业冶金弃渣的大规模综合利用起到重大的示范推动作用.【相关文献】[1]姜平国, 吴朋飞, 胡晓军, 等. 铜渣综合利用研究现状及其新技术的提出[J]. 中国矿业, 2016, 25(2): 76-79. (Jiang, Pingguo, Wu Pengfei, Hu Xiaojun, et al. Copper slag comprehensive utilization development and new technology is put forward[J]. China Mining Magazine, 2016, 25(2): 76-79.)[2]朱茂兰, 熊家春, 胡志彪, 等. 铜渣中铜铁资源化利用研究进展[J]. 有色冶金设计与研究, 2016,32(2): 15-17. (Zhu Maolan, Xiong Jiachun, Hu Zhibiao, et al. Research progress in resource utilization of iron and copper in copper smelting slag[J]. Nonferrous Metals Engineering & Research, 2016, 32(2): 15-17.)[3]李镇坤, 文衍宣, 苏静. 无烟煤直接还原铜渣中铁矿物工艺研究[J]. 无机盐工业, 2014, 46(6): 51-55. (Li Zhenkun, Wen Yanxuan, Su Jing. Directive reducing of iron minerals from copper slag with anthracite as reductant[J]. Inorganic Chemicals Industry, 2014, 46(6): 51-55.) [4]赵凯, 宫晓然, 李杰, 等. 直接还原法回收铜渣中铁、铜和锌的热力学[J]. 环境工程学报, 2016,10(5): 2638-2646. (Zhao Kai, Gong Xiaoran, Li Jie, et al. Thermodynamics of recovering iron, copper, zinc in copper slag by direct reduction method[J]. Chinese Journal ofEnvironmental Engineering, 2016, 10(5): 2638-2646.)[5]杨慧芬, 袁运波, 张露, 等. 铜渣中铁铜组分回收利用现状及建议[J]. 金属矿山, 2012,431(5):165-168. (Yang Huifen, Yuan Yunbo, Zhang Lu, et al. Present situation and proposed methodof recycling iron and copper from copper slag[J]. Metal Mine, 2012, 431(5): 165-168.) [6]王琛, 田庆华, 王亲猛, 等. 铜渣有价金属综合回收研究进展[J]. 金属材料与冶金工程, 2014, 42(6): 50-56. (Wang Chen, Tian Qinghua, Wang Qinmeng, et al. Research progress in comprehensive recovery of valuable metals from copper slag[J]. Metal Materials and Metallurgy Engineering, 2014, 42(6): 50-56.)[7]曾军龙, 肖坤明. 分散剂用于炉渣中回收铁的研究[J]. 有色金属科学与工程, 2011, 2(6):71-73. (Zeng Junlong, Xiao Kunming. The research on using dispersant agent to iron recovery in slag[J]. Nonferrous Metals Science and Engineering, 2011, 2(6):71-73.)[8]Rudnik E, Burzynska L, Gumowska W. Hydrometallurgical recovery of copper and cobalt from reduction-roasted copper converter slag[J]. Minerals Engineering, 2009, 22(1): 88-95.[9]聂溪莹, 肖绎. 模拟回转窑工艺研究铜渣中Fe、Pb、Zn 的提取[J]. 工业加热, 2015, 44(2): 71-74. (Nie Xiying, Xiao Yi. Studying on the extraction of Fe、Pb、Zn from the copper slag by simulation of the rotary kiln process[J]. Industrial Heating, 2015, 44(2): 71-74.)[10]杨慧芬,景丽丽,党春阁. 铜渣中铁组分的直接还原与磁选回收[J]. 中国有色金属学报, 2011, 21(5): 1165-1170. (Yang Huifen, Jing Lili, Dang Chunge. Iron recovery from copper-slag with lignite-based direct reduction followed by magnetic separation[J]. The Chinese Journal of Nonferrous Metals, 2011, 21(5): 1165-1170.)[11]王爽, 倪文, 王长龙, 等.铜尾渣深度还原回收铁工艺研究[J]. 金属矿山, 2014, 453(3): 156-160. (Wang Shuang, Ni Wen, Wang Changlong, et al. Study of deep reduction process for iron recovery from copper slag tailings[J]. Metal Mine, 2014, 453(3): 156-160.)。
干雾抑尘技术在炼钢厂混铁炉的应用与研究
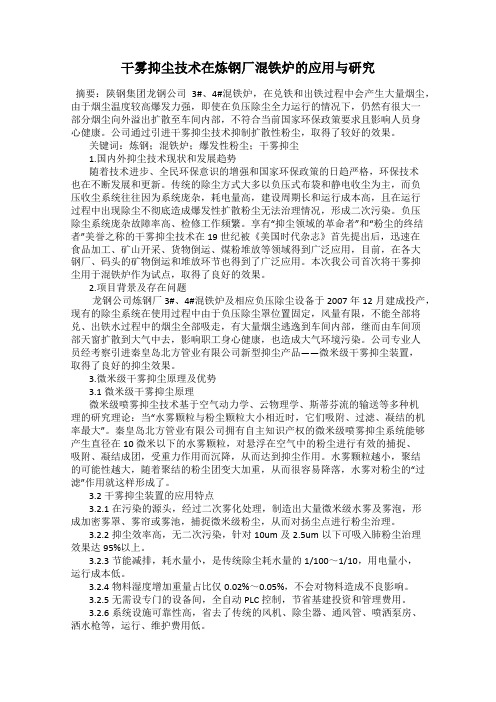
干雾抑尘技术在炼钢厂混铁炉的应用与研究摘要:陕钢集团龙钢公司3#、4#混铁炉,在兑铁和出铁过程中会产生大量烟尘,由于烟尘温度较高爆发力强,即使在负压除尘全力运行的情况下,仍然有很大一部分烟尘向外溢出扩散至车间内部,不符合当前国家环保政策要求且影响人员身心健康。
公司通过引进干雾抑尘技术抑制扩散性粉尘,取得了较好的效果。
关键词:炼钢;混铁炉;爆发性粉尘;干雾抑尘1.国内外抑尘技术现状和发展趋势随着技术进步、全民环保意识的增强和国家环保政策的日趋严格,环保技术也在不断发展和更新。
传统的除尘方式大多以负压式布袋和静电收尘为主,而负压收尘系统往往因为系统庞杂,耗电量高,建设周期长和运行成本高,且在运行过程中出现除尘不彻底造成爆发性扩散粉尘无法治理情况,形成二次污染。
负压除尘系统庞杂故障率高、检修工作频繁。
享有“抑尘领域的革命者”和“粉尘的终结者”美誉之称的干雾抑尘技术在19世纪被《美国时代杂志》首先提出后,迅速在食品加工、矿山开采、货物倒运、煤粉堆放等领域得到广泛应用,目前,在各大钢厂、码头的矿物倒运和堆放环节也得到了广泛应用。
本次我公司首次将干雾抑尘用于混铁炉作为试点,取得了良好的效果。
2.项目背景及存在问题龙钢公司炼钢厂3#、4#混铁炉及相应负压除尘设备于2007年12月建成投产,现有的除尘系统在使用过程中由于负压除尘罩位置固定,风量有限,不能全部将兑、出铁水过程中的烟尘全部吸走,有大量烟尘逃逸到车间内部,继而由车间顶部天窗扩散到大气中去,影响职工身心健康,也造成大气环境污染。
公司专业人员经考察引进秦皇岛北方管业有限公司新型抑尘产品——微米级干雾抑尘装置,取得了良好的抑尘效果。
3.微米级干雾抑尘原理及优势3.1微米级干雾抑尘原理微米级喷雾抑尘技术基于空气动力学、云物理学、斯蒂芬流的输送等多种机理的研究理论:当“水雾颗粒与粉尘颗粒大小相近时,它们吸附、过滤、凝结的机率最大”。
秦皇岛北方管业有限公司拥有自主知识产权的微米级喷雾抑尘系统能够产生直径在10微米以下的水雾颗粒,对悬浮在空气中的粉尘进行有效的捕捉、吸附、凝结成团,受重力作用而沉降,从而达到抑尘作用。
钢铁业含锌尘泥处理

钢铁业含锌尘泥处理由中国金属学会组织的江苏沙钢集团与北京神雾集团江苏省冶金设计院有限公司联合开发的“转底炉处理钢铁厂含锌尘泥关键技术及30万吨/年示范工程”科技成果评价会于2012年9月15日在江苏省张家港市召开。
由科技部首席科学家、中国金属学会荣誉理事长、中国工程院院士翁宇庆教授担任评价委员会主任;原北京科技大学校长、现中国金属学会炼铁分会理事长杨天钧教授及原河北钢铁集团董事长、现中国金属学会常务副理事长王天义任评价委员会副主任;由中国金属学会非高炉炼铁专委会主任、东北大学赵庆杰教授,北京钢铁研究总院炼铁室主任沙永志研究员,中科院过程所李会泉研究员等7位中国炼铁界著名的专家组成的评价委员会考察了神雾蓄热式转底炉处理钢铁厂含锌尘泥的生产现场,审查了有关资料,听取了沙钢集团有限公司的用户使用报告和经济效益分析,听取了北京神雾集团江苏省冶金设计院有限公司的技术汇报和查新报告,并进行了专家质询和成果完成单位的答辩。
最后,评价委员会一致认为该成果在关键技术上取得了突破,主要设备实现了国产化,投资省,设备运行稳定,指标先进,达到国际领先水平。
该项目针对钢铁行业含锌尘泥处理的世界性难题,特别是高炉原料含锌致害的问题,在大量试验研究、理论计算和工程优化的基础上,开发出了具有我国完全自主知识产权的蓄热式转底炉处理含锌尘泥、综合回收铁/锌的成套工艺技术和装备,建设了处理量30万吨/年冶金尘泥的蓄热式转底炉直接还原炼铁生产线,实现了连续、稳定的工业化运行。
自2011年12月投产以来,作业率达到了82.5%,金属化球团平均金属化率达到85.6%以上,转底炉脱锌率94%~97%,锌元素回收率平均达到95%,回收ZnO粉平均锌品位大于62%,金属化球团已作为废钢替代品在电炉、转炉生产中使用,很好地解决了含锌尘泥处理和资源综合回收利用问题。
2011年我国的钢产量已达到6.83亿吨,接近全球钢产量的50%,钢铁企业产生的粉尘污泥总量一般为钢产量的8-12%;以10%计算,全国钢铁行业每年产生的含铁尘泥约为6830万吨;其中含锌尘泥约占总尘泥量的20-30%,按25%计算约有1707万吨。
神雾转底炉直接还原炼铁技术介绍

RHF direct reduction pilot-scale plant
2020/8/14
四、神雾直接还原炼铁工厂鸟瞰图
沙钢30万吨/年含锌.含铁粉尘处理 生产线签约仪式
上料矿槽
流程布置示意图
转底炉室干燥机室
烟囱
高压压球机室
配料室成品料仓
热布压袋余块烟收润热气尘磨换锅处室热炉理降器尘室室
www.themeg还all原er炼y.c铁o及m 有色金属提
炼实验台
蓄热 式熔 炼炉
90m 神神雾雾转转底底炉炉实实验验室室
配5t
冷却
60m
混合 压球 干燥 还原 熔分
北京神雾节能低炭实验室
2020/8/14
某厂含钾钢铁粉尘处理工艺 物料平衡
粉尘47万吨
金属化球团30万吨
含氧化钾60%金属氧化物6.465万 吨
某厂含锌钢铁粉尘处理工艺 物料平衡
粉尘38.5万吨
金属化球团30万吨
含氧化锌70%金属氧化物1.7万吨
蓄热式转底炉示意图
生球及成品
含碳球团
海绵铁
直接还原铁
成品
直接还原铁热压块
神雾蓄热式转底炉煤基直接还原工艺的特点
神雾转底炉直接还原炼铁技术
神雾研究院 2010.7.25
一、传统高炉炼铁工艺分析
传统高炉炼铁工艺
占钢铁生产过程总能耗约70%
焦煤 铁矿石
焦炉 烧结机
高炉
铁水
转炉或电炉 钢水
深加工
蓄热式热处理炉 棒,板,带,管
连轧
蓄热式加热炉
占钢铁生产过程总能耗约30%
连铸
传统炼铁工艺存在的问题
必须要用高品位的优质铁矿石,导致铁资
转底炉处理含锌尘泥成套工艺装备技术
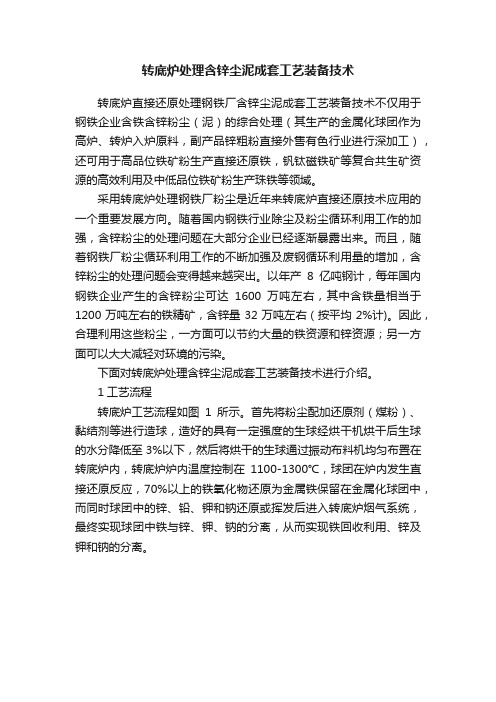
转底炉处理含锌尘泥成套工艺装备技术转底炉直接还原处理钢铁厂含锌尘泥成套工艺装备技术不仅用于钢铁企业含铁含锌粉尘(泥)的综合处理(其生产的金属化球团作为高炉、转炉入炉原料,副产品锌粗粉直接外售有色行业进行深加工),还可用于高品位铁矿粉生产直接还原铁,钒钛磁铁矿等复合共生矿资源的高效利用及中低品位铁矿粉生产珠铁等领域。
采用转底炉处理钢铁厂粉尘是近年来转底炉直接还原技术应用的一个重要发展方向。
随着国内钢铁行业除尘及粉尘循环利用工作的加强,含锌粉尘的处理问题在大部分企业已经逐渐暴露出来。
而且,随着钢铁厂粉尘循环利用工作的不断加强及废钢循环利用量的增加,含锌粉尘的处理问题会变得越来越突出。
以年产8亿吨钢计,每年国内钢铁企业产生的含锌粉尘可达1600万吨左右,其中含铁量相当于1200万吨左右的铁精矿,含锌量32万吨左右(按平均2%计)。
因此,合理利用这些粉尘,一方面可以节约大量的铁资源和锌资源;另一方面可以大大减轻对环境的污染。
下面对转底炉处理含锌尘泥成套工艺装备技术进行介绍。
1工艺流程转底炉工艺流程如图1所示。
首先将粉尘配加还原剂(煤粉)、黏结剂等进行造球,造好的具有一定强度的生球经烘干机烘干后生球的水分降低至3%以下,然后将烘干的生球通过振动布料机均匀布置在转底炉内,转底炉炉内温度控制在1100-1300℃,球团在炉内发生直接还原反应,70%以上的铁氧化物还原为金属铁保留在金属化球团中,而同时球团中的锌、铅、钾和钠还原或挥发后进入转底炉烟气系统,最终实现球团中铁与锌、钾、钠的分离,从而实现铁回收利用、锌及钾和钠的分离。
转底炉内发生的化学反应:Fe X O+C→Fe+COFe X O CO→Fe COZnO C=Zn(g) COZnO CO=Zn(g) CO22 关键技术1)转底炉本体热工调控技术◆基于数模计算的新型炉膛整体结构设计:五段式阶梯状炉膛结构和可移动式调压隔板。
减缓烟气聚集处的流速,将烟气流速与炉压合理匹配;◆转底炉温度、气氛调控结构设计:顶烧嘴、侧烧嘴喷嘴的结构。
转炉粉尘再利用的新工艺:宝钢二炼钢的粉尘热压块

转炉粉尘再利用的新工艺:宝钢二炼钢的粉尘热压块
金奎序
【期刊名称】《钢铁厂设计》
【年(卷),期】1999(000)001
【摘要】重点介绍了宝钢二炼钢粉尘热压块车间的设备组成及其功能,特点。
【总页数】4页(P59-62)
【作者】金奎序
【作者单位】无
【正文语种】中文
【中图分类】X757.01
【相关文献】
1.安钢第二炼轧厂转炉炼钢粉尘处理 [J], 肖永良
2.转炉粉尘用于转炉炼钢脱磷剂的可行性分析 [J], 黄东长;吴光亮
3.转炉粉尘压块在蒂森钢公司TBM—转炉中的应用 [J], Pfli.,HD;刘宗林
4.转炉粉尘热压块法的发展及其生产应用 [J], 刘宗林
5.转炉LT粉尘干式冷压块技术研究及工业应用 [J], 陈铁军;张一敏
因版权原因,仅展示原文概要,查看原文内容请购买。
- 1、下载文档前请自行甄别文档内容的完整性,平台不提供额外的编辑、内容补充、找答案等附加服务。
- 2、"仅部分预览"的文档,不可在线预览部分如存在完整性等问题,可反馈申请退款(可完整预览的文档不适用该条件!)。
- 3、如文档侵犯您的权益,请联系客服反馈,我们会尽快为您处理(人工客服工作时间:9:00-18:30)。
方案 1 2
TFe 81.74 90.11
MFe 68.07 76.60
3
92.22
83.17
金属化球团成分
金属化率(%) 83.27 85.01 90.19
残碳(%) 0.64 0.30 0.44
元素 TFe
MFe
C
CaO MgO
SiO2
Al2O3
S
P
含量 92.22 83.17 0.44 0.93 0.50 0.95 0.44 0.14 0.02
强
圆
力
盘
混
造
合
球
机
机
基
烘
础模 试拟
干
验转 还底
箱
原炉 炉
12
基础试验设备介绍—磨选熔分
棒
磁
磨
选
机
管
高
过
温
滤
熔 分
机
炉
13
基础试验设备介绍—制样化验
制
钻
孔
样
取
机
样
机
显
化
微
学
镜
分
分
析
析
实
设
验
备
室
14
神雾科研基地转底炉
以神雾转底炉为核心,可 处理高磷鲕状赤铁矿、难 选赤铁矿等低品位难选矿、 钒钛磁铁矿、铬铁矿、锰 铁矿、硼铁矿等复合共伴 生矿、红土镍矿、含锌尘 泥、氧化铁皮、铜渣、镍 渣、硫酸渣等冶金行业粉 尘与固废。
磁选后产品质量
产品名称
产率(%)
TFe(%)
MFe(%)
回收率(%)
金属铁粉
93.08
94.97
94.60
99.04
尾矿
6.92
12.36
3.74
0.96
DRI
100.00
89.25
88.31
100.00
25
案例2:某钢铁厂粉尘还原前后对比
1.原料与还原产品重要元素分析
元素 原料(混合后) 还原产品(DRI)
蓄热式转底炉还原
磨矿磁选
20
转底炉工艺过程描述
转底炉工艺流程为:原料和添加剂混合制球后,经干燥直接装入转底炉, 随着炉底的旋转,炉料依次经过预热、还原区,约有85﹪以上的铁氧化物 被还原成金属化球团。
Hale Waihona Puke 转底炉工艺过程描述转底炉炉体结构示意图
炉顶和炉墙固定不动,炉底带动球团进行还原,炉膛与转动的炉底之间有水 封防止烟气和粉尘逸出
2、神雾转底炉处理钢铁厂粉尘
添加剂
还原剂
粉尘、 铁皮
原料处理 转底炉直接还原
烟气
DRI
高炉或其它
磁选
熔分
换热 除尘 Zn、Pb等
外排
铁粉
铁水
压块
铸块
铁块
铁块
23
转底炉直接还原设备形象联系图
2008北京神雾热能技术有限公司
案例1:转底炉处理固废(转炉污泥、铁皮)
原料:铁皮、煤粉、粘结剂 转底炉中试结果
(4) “十二五”节能减排综合性工作方案:大力推进节能减排,推进资源综合利用。 加强共伴生矿产资源,特别是冶炼废渣的综合利用。
技术背景
炼铁
高炉炼铁 非高炉炼铁
熔融还原 直接还原
一步法 两步法
气基
煤基
Hismelt、Ausmet等 Corex、Finex等 竖炉、流化床等
转底炉、回转窑等
高炉炼铁
铁矿石 焦煤
国际第三代燃烧技术: 蓄热式高温空气燃烧技术
炉膛热利用率<55%
炉膛热利用率< 65% 系统热利用率< 93%
炉膛热利用率≥ 86% 系统热利用率≥94%
第三代技术的优势:
能提高各种反应器的热利用率;
能提高各种反应器的反应温度;
能降低燃料的品质和等级;
有利于实现低氧低氮燃烧,同时减少大
神雾2.4万吨/年转底炉
名称 炉子中心直径
炉膛外径 炉膛内径 炉膛宽度 炉膛高度
数量(mm) 8000 10000 6000 2000 1300
转底炉尺寸表
15
神雾科研基地转底炉工序过程
干转燥底机炉
混合机 压球机
给料装置 卸料装置
中试设备介绍
烘干机
自动化智能控制中心
17
中试设备介绍
混料机
圆盘造球机
18
转底炉还原产品
熔
出
分
料
流
现
程
场
磨
粒
矿
铁
磁
流
选
程
流
程
19
神雾蓄热式转底炉直接冶炼工艺研究路线
• 低阶煤炭 • 生物质 • 城市或工业垃圾 • 废旧有机物
蓄热式旋转床 中低温热解
中高阶煤炭
• 低品位贫矿、难选矿 • 复合共伴生矿 • 红土镍矿 • 冶金、有色行业固体
废物
焦炉煤气
焦油
含碳固体
含碳球团
神雾转底炉处理钢铁厂粉尘与 有色冶金渣研发与应用实践
二○一四年十一月六日
主要内容
1 神雾科研基地转底炉简介 2 神雾转底炉处理钢铁厂粉尘 3 神雾转底炉处理有色冶金渣
技术背景
2013年我国粗钢产量达7.79亿吨,占世 界粗钢总产量的48.5%。
2013年我国进口铁矿石达8.2亿吨,铁矿 石对外依存度高达60%。
(1)《绿色制造科技发展“十二五”专项规划中》明确指出:明确突破绿色设计、 节能减排工艺、绿色回收资源化与再制造、绿色制造技术标准等关键共性技术”
(2) 十二五规划纲要:冶金行业要……支持非高炉炼铁……鼓励再生资源循环利用 和低品位矿、共伴生矿、难选冶矿、尾矿和废渣资源综合利用。
(3)《钢铁工业“十二五”发展规划》:把转底炉处理含铁粉尘技术、冶金渣综合 利用技术列为“十二五”期间节能技术推广应用重点项目。
对进口铁矿石的过度依赖,导致炼铁成本居高不下,钢企全线亏损,严重影 响钢铁工业原料安全和健康发展。
技术背景
❖ 我国铁矿石资源利用现状
含Fe、Ni、Zn、V、Ti等 元素
铁矿资源的特点:低、贫、细、杂
❖ 传统冶金流程产生大量废渣,利 用率低
冶金粉尘年产量8000万吨,尚无高效利用 方式。 高炉渣利用率70%,钢渣利用率25%。 有色金属冶炼渣利用率低于10%。 冶金工业亟需实现“ 减量化、再利用、再 循环”转变!
气雾霾生成。
8
神雾蓄热式高温空气燃烧技术
9
1、神雾科研基地转底炉简介
投资5亿元,占地面积 96亩,拥有17个大型 中试平台及配套设施。 已获批“北京市劣质 铁矿石综合利用工程技 术研究中心”和设立 “博士后科研工作站”
节能与低碳技术联合实验室
10
基础实验室简介
基础实验室
11
基础试验设备介绍—造球还原
烧结厂 焦炉
高炉
转炉
连铸 热轧机
占钢铁生产总能耗的70%,污染物排放占整个流程的90% 神雾转底炉直接还原流程
劣质含铁资源 非焦煤
转底炉
电炉熔分 非电熔分
连铸 热轧机
磨矿磁选
铁粉压块
绿色炼铁,省去焦化、烧结高耗能、高排放工序
多种工艺流程选择
7
全球燃烧技术的变革
国际第一代燃烧技术 国际第二代燃烧技术
钒钛磁铁矿
红土镍矿
高磷矿
低品位赤铁矿
冶金废渣
工业排放37%
技术背景
餐饮油烟15%
火力发电30%
机动车排放18% 京津冀地区雾霾来源构成
钢铁工业产生的烟尘、粉尘、二氧化硫
和氮氧化物排放量占工业排放的45.8%
因此,钢铁工业面临转型发展,发展绿色节能的炼铁工艺迫在眉睫!
5
技术背景
针对绿色过程工艺及资源综合利用,国家给予了政策鼓励: