轮胎材料配方介绍Word版
半钢轮胎常规配方表

半钢轮胎常规配方表一、橡胶成分在半钢轮胎的常规配方表中,橡胶成分是最重要的部分之一。
橡胶成分主要包括天然橡胶和合成橡胶。
天然橡胶是从橡胶树中提取的胶乳,而合成橡胶是通过化学合成得到的。
这两种橡胶都具有良好的弹性和耐磨性。
二、填充剂填充剂是半钢轮胎中的另一个重要成分。
常用的填充剂有炭黑、硅灰和沙子等。
炭黑是一种黑色的粉末,具有良好的增强和耐磨性能,可以提高轮胎的耐磨性和抗老化性能。
硅灰是一种白色粉末,可以增加轮胎的硬度和耐磨性。
沙子则可以提高轮胎的抗滑性能。
三、增塑剂增塑剂是为了提高橡胶的可加工性和柔韧性,常见的增塑剂有橡胶油和树脂等。
橡胶油可以使橡胶更加柔软,提高轮胎的抗裂性和弯曲性能。
树脂则可以增加轮胎的硬度和强度。
四、硫化剂硫化剂是为了使橡胶成型后能够固化成轮胎的一种化学物质。
常见的硫化剂有硫磺和过氧化物等。
硫磺可以与橡胶中的双键发生反应,形成交联结构,使橡胶固化成轮胎。
过氧化物则可以通过热分解产生自由基,进而引发橡胶的交联反应。
五、促进剂促进剂是为了加快硫化反应的速度,常见的促进剂有硫醇和过硫酸铵等。
硫醇可以与硫磺发生反应,生成活性硫醇,进一步促进硫化反应的进行。
过硫酸铵则可以通过热分解产生自由基,引发橡胶的硫化反应。
六、防老剂防老剂是为了提高橡胶的耐热性和抗氧化性能。
常见的防老剂有苯并噻唑类和酚醛类等。
苯并噻唑类防老剂可以与橡胶中的活性氢发生反应,形成稳定的硫醇结构,起到抗氧化的作用。
酚醛类防老剂则可以通过抑制自由基的生成,延缓橡胶的老化过程。
七、其他添加剂除了以上的主要成分外,半钢轮胎的常规配方表中还包含一些其他的添加剂。
例如,加硫剂可以提高橡胶的硫化效果;消光剂可以改变橡胶的颜色和外观;促进剂可以改善橡胶的加工性能等。
总结:半钢轮胎的常规配方表是根据轮胎的性能要求和使用条件来设计的。
不同的车辆和使用环境需要不同的轮胎配方。
通过合理选择和调整橡胶成分、填充剂、增塑剂、硫化剂、促进剂、防老剂和其他添加剂的比例和种类,可以制备出性能优良的半钢轮胎。
轮胎配方及原材料介绍

国外载重汽车轮胎胎面胶配方单位:质量份轮胎主要可以由天然橡胶(NR)聚异戊二烯,丁苯橡胶(SBR)丁二烯和苯乙烯,顺丁橡胶(BR)是由丁二烯,异戊橡胶(IR)是由异戊二烯,丁基橡胶(IIR)是异丁烯和少量异戊二烯或丁二烯为主要原料,硬脂酸,氧化锌,微晶蜡,防老剂,操作油,硬质炭黑,防焦剂,促进剂,硫磺等为配料制成。
1、天然橡胶(NR)以橡胶烃(聚异戊二烯)为主,含少量蛋白质、水分、树脂酸、糖类和无机盐等。
弹性大,定伸强度高,抗撕裂性和电绝缘性优良,耐磨性和耐旱性良好,加工性佳,易于其它材料粘合,在综合性能方面优于多数合成橡胶。
缺点是耐氧和耐臭氧性差,容易老化变质;耐油和耐溶剂性不好,第抗酸碱的腐蚀能力低;耐热性不高。
使用温度范围:约-60℃~+80℃。
制作轮胎、胶鞋、胶管、胶带、电线电缆的绝缘层和护套以及其他通用制品。
特别适用于制造扭振消除器、发动机减震器、机器支座、橡胶-金属悬挂元件、膜片、模压制品。
2、丁苯橡胶(SBR)丁二烯和苯乙烯的共聚体。
性能接近天然橡胶,是目前产量最大的通用合成橡胶,其特点是耐磨性、耐老化和耐热性超过天然橡胶,质地也较天然橡胶均匀。
缺点是:弹性较低,抗屈挠、抗撕裂性能较差;加工性能差,特别是自粘性差、生胶强度低。
使用温度范围:约-50℃~+100℃。
主要用以代替天然橡胶制作轮胎、胶板、胶管、胶鞋及其他通用制品。
3、顺丁橡胶(BR)是由丁二烯聚合而成的顺式结构橡胶。
优点是:弹性与耐磨性优良,耐老化性好,耐低温性优异,在动态负荷下发热量小,易于金属粘合。
缺点是强度较低,抗撕裂性差,加工性能与自粘性差。
使用温度范围:约-60℃~+100℃。
一般多和天然橡胶或丁苯橡胶并用,主要制作轮胎胎面、运输带和特殊耐寒制品。
4、异戊橡胶(IR)是由异戊二烯单体聚合而成的一种顺式结构橡胶。
化学组成、立体结构与天然橡胶相似,性能也非常接近天然橡胶,故有合成天然橡胶之称。
它具有天然橡胶的大部分优点,耐老化由于天然橡胶,弹性和强力比天然橡胶稍低,加工性能差,成本较高。
轮胎配方及原材料介绍Word版

轮胎主要可以由天然橡胶(NR)聚异戊二烯,丁苯橡胶(SBR)丁二烯和苯乙烯,顺丁橡胶(BR)是由丁二烯,异戊橡胶(IR)是由异戊二烯,丁基橡胶(IIR)是异丁烯和少量异戊二烯或丁二烯为主要原料,硬脂酸,氧化锌,微晶蜡,防老剂,操作油,硬质炭黑,防焦剂,促进剂,硫磺等为配料制成。
1、天然橡胶(NR)以橡胶烃(聚异戊二烯)为主,含少量蛋白质、水分、树脂酸、糖类和无机盐等。
弹性大,定伸强度高,抗撕裂性和电绝缘性优良,耐磨性和耐旱性良好,加工性佳,易于其它材料粘合,在综合性能方面优于多数合成橡胶。
缺点是耐氧和耐臭氧性差,容易老化变质;耐油和耐溶剂性不好,第抗酸碱的腐蚀能力低;耐热性不高。
使用温度范围:约-60℃~+80℃。
制作轮胎、胶鞋、胶管、胶带、电线电缆的绝缘层和护套以及其他通用制品。
特别适用于制造扭振消除器、发动机减震器、机器支座、橡胶-金属悬挂元件、膜片、模压制品。
2、丁苯橡胶(SBR)丁二烯和苯乙烯的共聚体。
性能接近天然橡胶,是目前产量最大的通用合成橡胶,其特点是耐磨性、耐老化和耐热性超过天然橡胶,质地也较天然橡胶均匀。
缺点是:弹性较低,抗屈挠、抗撕裂性能较差;加工性能差,特别是自粘性差、生胶强度低。
使用温度范围:约-50℃~+100℃。
主要用以代替天然橡胶制作轮胎、胶板、胶管、胶鞋及其他通用制品。
3、顺丁橡胶(BR)是由丁二烯聚合而成的顺式结构橡胶。
优点是:弹性与耐磨性优良,耐老化性好,耐低温性优异,在动态负荷下发热量小,易于金属粘合。
缺点是强度较低,抗撕裂性差,加工性能与自粘性差。
使用温度范围:约-60℃~+100℃。
一般多和天然橡胶或丁苯橡胶并用,主要制作轮胎胎面、运输带和特殊耐寒制品。
4、异戊橡胶(IR)是由异戊二烯单体聚合而成的一种顺式结构橡胶。
化学组成、立体结构与天然橡胶相似,性能也非常接近天然橡胶,故有合成天然橡胶之称。
它具有天然橡胶的大部分优点,耐老化由于天然橡胶,弹性和强力比天然橡胶稍低,加工性能差,成本较高。
几种轮胎配方及原料讲解介绍解读
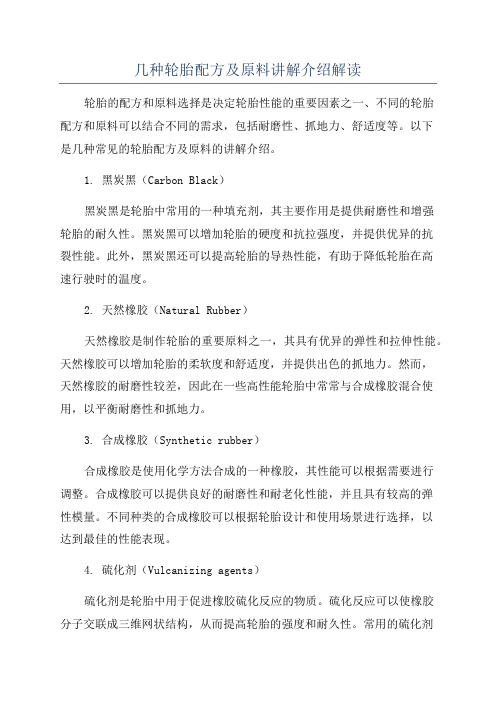
几种轮胎配方及原料讲解介绍解读轮胎的配方和原料选择是决定轮胎性能的重要因素之一、不同的轮胎配方和原料可以结合不同的需求,包括耐磨性、抓地力、舒适度等。
以下是几种常见的轮胎配方及原料的讲解介绍。
1. 黑炭黑(Carbon Black)黑炭黑是轮胎中常用的一种填充剂,其主要作用是提供耐磨性和增强轮胎的耐久性。
黑炭黑可以增加轮胎的硬度和抗拉强度,并提供优异的抗裂性能。
此外,黑炭黑还可以提高轮胎的导热性能,有助于降低轮胎在高速行驶时的温度。
2. 天然橡胶(Natural Rubber)天然橡胶是制作轮胎的重要原料之一,其具有优异的弹性和拉伸性能。
天然橡胶可以增加轮胎的柔软度和舒适度,并提供出色的抓地力。
然而,天然橡胶的耐磨性较差,因此在一些高性能轮胎中常常与合成橡胶混合使用,以平衡耐磨性和抓地力。
3. 合成橡胶(Synthetic rubber)合成橡胶是使用化学方法合成的一种橡胶,其性能可以根据需要进行调整。
合成橡胶可以提供良好的耐磨性和耐老化性能,并且具有较高的弹性模量。
不同种类的合成橡胶可以根据轮胎设计和使用场景进行选择,以达到最佳的性能表现。
4. 硫化剂(Vulcanizing agents)硫化剂是轮胎中用于促进橡胶硫化反应的物质。
硫化反应可以使橡胶分子交联成三维网状结构,从而提高轮胎的强度和耐久性。
常用的硫化剂包括硫醇类化合物和过氧化物等。
硫化剂的选择和使用量可以根据轮胎的需求进行调整,以获得理想的硫化效果。
5. 防氧化剂(Antioxidants)防氧化剂是用于防止轮胎老化和龟裂的物质。
轮胎在使用过程中会受到氧气、紫外线和高温等因素的影响,从而导致橡胶老化和性能下降。
防氧化剂可以稳定橡胶分子的结构,延缓老化过程。
常用的防氧化剂包括类似于二苯胺的化合物。
总之,轮胎的配方和原料选择是决定轮胎性能的关键因素之一、通过合理地选择填充剂、橡胶和添加剂等,可以实现不同性能指标的平衡。
在轮胎工艺和设计中,需要综合考虑不同配方的优缺点,以满足不同用户的需求。
轮胎的生产用材料

Study
C/B介绍
C/B是烃类不完全燃烧或热解制得的具有高度分散性的黑色粉末状 的物质,主要由元素C组成。
炭黑按制法的分类:
炉法C/B:烃类在反应炉中不完全燃烧制取的。 槽法C/B:是天然气与油类火焰与槽钢接触制造的。 热裂C/B:由天然气热解制得的。 乙炔C/B:由乙炔放热热解制得。 灯烟C/B:在敞口浅盘中燃烧烃类制取的。 现在轮胎行业使用的C/B主要是炉法C/B。
骨架材料 金属织物类:钢丝帘线,包括有纬及无纬两种,常用到的为无纬钢丝帘
线,按帘线的构成上分,又有OC、CC、普通分类,按强度上分又 有普强(NT)、高强(HT)、超高强(UT)等。
胎圈钢丝 作为轮胎受力的主要部位胎圈的主体,直径及强度不同有不同的分类。
CONTENTS
1 主体材料 2 补强填充 3 硫化体系 4 防护体系
公司用:SBR1712、SBR1500、SBR1721、SBR1502、 BR9000、IR、EPDM、Br_IIR等。
Study
SBR(丁苯胶料)简介
SBR:Styrene-Butadiene Rubber
SBR的基本情况
1)丁苯胶是世界产量、用量最大的合成胶,且70%用于轮胎制造业。 2)SBR单体为丁二烯(C=C-C=C)、苯乙烯( C=C)。 3)在正常的SBR中,苯乙烯含量为23.5%(重量%),摩尔比为1:6。 4)按聚合方法分类,SBR有乳液聚合(E-SBR)、溶液聚合(S-SBR)。 5)SBR较NR耐磨耗、湿地抓着力高,但生热高,加工困难。 6)溶聚较乳聚有较低的滚动阻力,高的抗湿滑性及良好的综合性能。
轮胎配方及原材料介绍

海中载沉汽车轮胎胎里胶配圆单位:品量份之阳内胎战睦门嘴垫胶的配圆轮胎主要不妨由天然橡胶(NR)散同戊两烯,丁苯橡胶(SBR)丁两烯战苯乙烯,逆丁橡胶(BR)是由丁两烯,同戊橡胶(IR)是由同戊两烯,丁基橡胶(IIR)是同丁烯战少量同戊两烯或者丁两烯为主要本料,硬脂酸,氧化锌,微晶蜡,防老剂,收配油,硬量冰乌,防焦剂,促进剂,硫磺等为配料制成.1、天然橡胶(NR)以橡胶烃(散同戊两烯)为主,含少量蛋黑量、火分、树脂酸、糖类战无机盐等.弹性大,定伸强度下,抗撕裂性战电绝缘性劣良,耐磨性战耐涝性劣良,加工性好,易于其余资料粘合,正在概括本能圆里劣于普遍合成橡胶.缺面是耐氧战耐臭氧性好,简单老化蜕变;耐油战耐溶剂性短好,第抗酸碱的腐蚀本领矮;耐热性没有下.使用温度范畴:约-60℃~+80℃.创制轮胎、胶鞋、胶管、胶戴、电线电缆的绝缘层战护套以及其余通用制品.特天适用于制制扭振取消器、收效果减震器、呆板收座、橡胶-金属悬挂元件、膜片、模压制品.2、丁苯橡胶(SBR)丁两烯战苯乙烯的同散体.本能靠近天然橡胶,是暂时产量最大的通用合成橡胶,其个性是耐磨性、耐老化战耐热性超出天然橡胶,量天也较天然橡胶匀称.缺面是:弹性较矮,抗伸挠、抗撕裂本能较好;加工本能好,特天是自粘性好、死胶强度矮.使用温度范畴:约-50℃~+100℃.主要用以代替天然橡胶创制轮胎、胶板、胶管、胶鞋及其余通用制品.3、逆丁橡胶(BR)是由丁两烯散合而成的逆式结构橡胶.便宜是:弹性取耐磨性劣良,耐老化性好,耐矮温性劣同,正在动向背荷下收热量小,易于金属粘合.缺面是强度较矮,抗撕裂性好,加工本能取自粘性好.使用温度范畴:约-60℃~+100℃. 普遍多战天然橡胶或者丁苯橡胶并用,主要创制轮胎胎里、输收戴战特殊耐热制品.4、同戊橡胶(IR)是由同戊两烯单体散合而成的一种逆式结构橡胶.化教组成、坐体结构取天然橡胶相似,本能也非常靠近天然橡胶,故有合整天然橡胶之称.它具备天然橡胶的大部分便宜,耐老化由于天然橡胶,弹性战强力比天然橡胶稍矮,加工本能好,成本较下.使用温度范畴:约-50℃~+100℃可代替天然橡胶创制轮胎、胶鞋、胶管、胶戴以及其余通用制品.5、氯丁橡胶(CR)是由氯丁两烯干单体乳液散合而成的散合体.那种橡胶分子中含有氯本子,所以取其余通用橡胶相比:它具备劣良的抗氧、抗臭氧性,没有简单焚,着火后能自熄,耐油、耐溶剂、耐酸碱以及耐老化、气稀性好等便宜;其物理板滞本能也比天然橡胶好,故可用做通用橡胶,也可用做特种橡胶.主要缺面是耐热性较好,比沉较大、相对于成本下,电绝缘性短好,加工时易粘滚、易焦烧及易粘模.别的,死胶宁静性好,没有简单保存.使用温度范畴:约-45℃~+100℃.主要用于制制央供抗臭氧、耐老化性下的电缆护套及百般防备套、呵护罩;耐油、耐化教腐蚀的胶管、胶戴战化工衬里;耐焚的天下采矿用橡胶制品,以及百般模压制品、稀启圈、垫、粘结剂等.6、丁基橡胶(IIR)是同丁烯战少量同戊两烯或者丁两烯的同散体.最大个性是气稀性好,耐臭氧、耐老化本能好,耐热性较下,少久处事温度可正在130℃以下;本领无机强酸(如硫酸、硝酸等)战普遍有机溶剂,吸振战阻僧个性劣良,电绝缘性也非常好.缺面是弹性好,加工本能好,硫化速度缓,粘着性战耐油性好.使用温度范畴:约-40℃~+120℃.主要用做内胎、火胎、气球、电线电缆绝缘层、化工设备衬里及防震制品、耐热输收戴、耐热老化的胶布制品.7、丁阴橡胶(NBR)丁两烯战丙烯阴的同散体.个性是耐汽油战脂肪烃油类的本能特天好,仅次于散硫橡胶、丙烯酸酯战氟橡胶,而劣于其余通用橡胶.耐热性好,气稀性、耐磨及耐火性等均较好,粘结力强.缺面是耐热及耐臭氧性较好,强力及弹性较矮,耐酸性好,电绝缘性短好,耐极性溶剂本能也较好.使用温度范畴:约-30℃~+100℃.主要用于制制百般耐油制品,如胶管、稀启制品等.8、氢化丁阴橡胶(HNBR)丁两烯战丙烯阴的同散体.它是通过局部或者部分氢化NBR的丁两烯中的单键而得到的.其个性是板滞强度战耐磨性下,用过氧化物接联时耐热性比NBR好,其余本能取丁阴橡胶一般.缺面是代价较下.使用温度范畴:约-30℃~+150℃. 主要用于耐油、耐下温的稀启制品.9、乙丙橡胶(EPM\\EPDM)乙烯战丙烯的同散体,普遍分为两元乙丙橡胶战三元乙丙橡胶.个性是抗臭氧、耐紫中线、耐天候性战耐老化性劣同,居通用橡胶之尾.电绝缘性、耐化教性、冲打弹性很好,耐酸碱,比沉小,可举止下弥补协同.耐热可达150℃,耐极性溶剂-酮、酯等,但是没有耐脂肪烃战芳香烃,其余物理板滞本能略次于天然橡胶而劣于丁苯橡胶.缺面是自粘性战互粘性很好,没有简单粘合.使用温度范畴:约-50℃~+150℃. 主要用做化工设备衬里、电线电缆包皮、蒸汽胶管、耐热输收戴、汽车用橡胶制品及其余工业制品.。
橡胶轮胎的配方和工艺流程成型加工共7页word资料
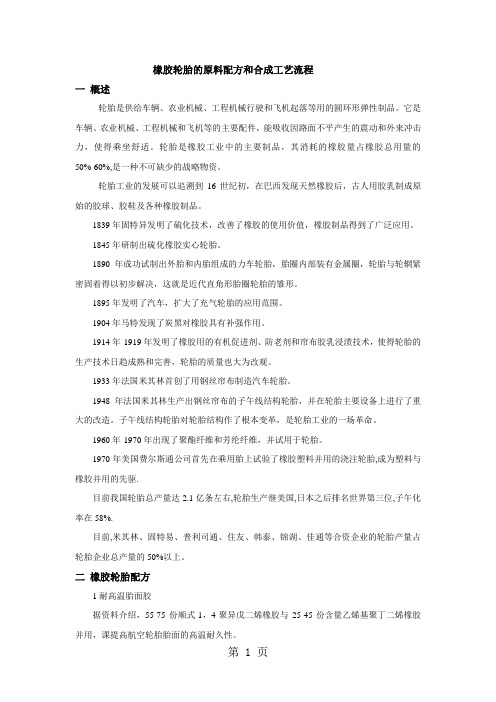
橡胶轮胎的原料配方和合成工艺流程一概述轮胎是供给车辆、农业机械、工程机械行驶和飞机起落等用的圆环形弹性制品。
它是车辆、农业机械、工程机械和飞机等的主要配件,能吸收因路面不平产生的震动和外来冲击力,使得乘坐舒适。
轮胎是橡胶工业中的主要制品,其消耗的橡胶量占橡胶总用量的50%-60%,是一种不可缺少的战略物资。
轮胎工业的发展可以追溯到16世纪初,在巴西发现天然橡胶后,古人用胶乳制成原始的胶球、胶鞋及各种橡胶制品。
1839年固特异发明了硫化技术,改善了橡胶的使用价值,橡胶制品得到了广泛应用。
1845年研制出硫化橡胶实心轮胎。
1890年成功试制出外胎和内胎组成的力车轮胎,胎圈内部装有金属圈,轮胎与轮辋紧密固着得以初步解决,这就是近代直角形胎圈轮胎的雏形。
1895年发明了汽车,扩大了充气轮胎的应用范围。
1904年马特发现了炭黑对橡胶具有补强作用。
1914年-1919年发明了橡胶用的有机促进剂、防老剂和帘布胶乳浸渍技术,使得轮胎的生产技术日趋成熟和完善,轮胎的质量也大为改观。
1933年法国米其林首创了用钢丝帘布制造汽车轮胎。
1948年法国米其林生产出钢丝帘布的子午线结构轮胎,并在轮胎主要设备上进行了重大的改造。
子午线结构轮胎对轮胎结构作了根本变革,是轮胎工业的一场革命。
1960年-1970年出现了聚酯纤维和芳纶纤维,并试用于轮胎。
1970年美国费尔斯通公司首先在乘用胎上试验了橡胶塑料并用的浇注轮胎,成为塑料与橡胶并用的先驱.目前我国轮胎总产量达2.1亿条左右,轮胎生产继美国,日本之后排名世界第三位,子午化率在58%.目前,米其林、固特易、普利司通、住友、韩泰、锦湖、佳通等合资企业的轮胎产量占轮胎企业总产量的50%以上。
二橡胶轮胎配方1耐高温胎面胶据资料介绍,55-75份顺式-1,4-聚异戊二烯橡胶与25-45份含量乙烯基聚丁二烯橡胶并用,课提高航空轮胎胎面的高温耐久性。
2耐割口胎面胶耐割口胎面胶配方见表1.据资料介绍,该组配方适用于航空轮胎胎面。
轮胎配方总结报告范文(3篇)

第1篇一、前言轮胎作为汽车的重要部件,其性能直接影响到汽车的安全、舒适性和燃油经济性。
轮胎配方是轮胎制造的核心技术之一,直接影响着轮胎的质量和性能。
本报告对轮胎配方进行了全面总结,旨在为轮胎制造企业提供技术支持,提高轮胎产品的市场竞争力。
二、轮胎配方概述1. 轮胎配方组成轮胎配方主要由以下几部分组成:(1)橡胶:作为轮胎的主体材料,其性能直接影响轮胎的耐磨性、抗湿滑性和抗老化性等。
(2)炭黑:作为轮胎的补强剂,提高轮胎的强度和抗磨损性能。
(3)白炭黑:作为轮胎的填充剂,提高轮胎的弹性和抗撕裂性能。
(4)油料:作为轮胎的软化剂,提高轮胎的柔韧性和耐低温性能。
(5)其他助剂:如抗氧剂、抗臭氧剂、抗静电剂等,用于提高轮胎的耐老化、耐臭氧和抗静电性能。
2. 轮胎配方设计原则(1)满足轮胎性能要求:轮胎配方设计应满足轮胎的耐磨、抗湿滑、抗老化、抗撕裂等性能要求。
(2)提高生产效率:优化配方,降低生产成本,提高生产效率。
(3)环保要求:选用环保型原材料,降低轮胎生产过程中的环境污染。
(4)成本控制:在满足性能要求的前提下,降低原材料成本。
三、轮胎配方优化方法1. 优化橡胶配方(1)选用高性能橡胶:选用耐高温、耐老化、耐磨等性能优异的橡胶材料。
(2)调整橡胶配方:通过调整橡胶的配方,提高轮胎的耐磨、抗湿滑、抗老化等性能。
2. 优化炭黑配方(1)选用高性能炭黑:选用具有良好补强性能的炭黑材料。
(2)调整炭黑用量:在满足性能要求的前提下,适当降低炭黑用量,降低生产成本。
3. 优化白炭黑配方(1)选用高性能白炭黑:选用具有良好填充性能的白炭黑材料。
(2)调整白炭黑用量:在满足性能要求的前提下,适当降低白炭黑用量,降低生产成本。
4. 优化油料配方(1)选用环保型油料:选用环保型油料,降低轮胎生产过程中的环境污染。
(2)调整油料配方:通过调整油料配方,提高轮胎的柔韧性和耐低温性能。
5. 优化其他助剂配方(1)选用高性能助剂:选用具有良好抗老化、抗臭氧、抗静电等性能的助剂。
轮胎橡胶配方

轮胎橡胶配方
轮胎橡胶配方是制造轮胎的关键部分,它决定了轮胎的主要性能。
配方中包含多种成分,每种成分都有其特定的作用。
以下是一个典型的轮胎橡胶配方及其成分说明:
1、基础橡胶:这是配方的核心成分,通常使用天然橡胶或合成橡胶。
天然橡胶具有良好的弹性和耐久性,而合成橡胶则提供了更多的性能选项,如低滚动阻力、高耐磨性和耐高温性。
2、填充剂:用于增加橡胶的体积,使其更坚固和耐磨。
常见的填充剂包括碳黑和白炭黑。
碳黑提供了优异的耐磨性和抗撕裂性,而白炭黑则增加了橡胶的抗湿滑性能。
3、硫化剂:使橡胶分子相互交联,形成网状结构,从而提高其弹性和耐久性。
4、增塑剂:如石油和油脂,有助于改善橡胶的加工性能和柔韧性。
5、防老剂:有助于延缓橡胶老化过程,提高其耐久性。
6、抗氧剂:防止橡胶在高温下氧化,有助于延长轮胎的使用寿命。
7、抗紫外线剂:用于抵抗紫外线对橡胶的降解,延长轮胎的使用寿命。
8、粘合剂:有助于增强橡胶与纤维材料之间的粘附力,提高轮胎的结构稳定性。
9、钢丝与纤维材料:用于增强轮胎的结构强度和稳定性。
钢丝主要用于轮胎的骨架结构,而纤维材料则提供额外的支撑和稳定性。
10、其他添加剂:根据特定需求,还可以添加其他一些添加剂,如抗湿滑剂、降噪剂等,以改善轮胎的性能。
除了以上成分外,正确的配方比例也是至关重要的。
不同成分的比例会直接影响轮胎的性能。
通过精确控制这些成分的比例,可以生产出具有优异性能的轮胎。
这需要经验丰富的工程师和技术人员来研发和调整配方,以满足各种不同的应用需求。
轮胎用橡胶塑料及配方
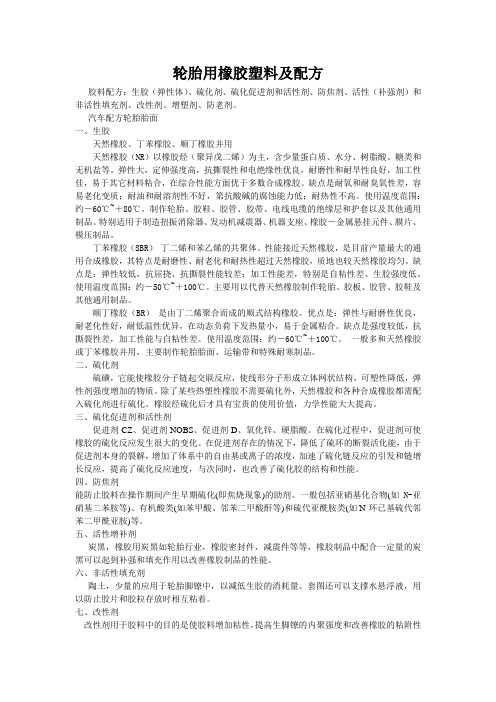
轮胎用橡胶塑料及配方胶料配方:生胶(弹性体)、硫化剂、硫化促进剂和活性剂、防焦剂、活性(补强剂)和非活性填充剂、改性剂、增塑剂、防老剂。
汽车配方轮胎胎面一、生胶天然橡胶、丁苯橡胶、顺丁橡胶并用天然橡胶(NR)以橡胶烃(聚异戊二烯)为主,含少量蛋白质、水分、树脂酸、糖类和无机盐等。
弹性大,定伸强度高,抗撕裂性和电绝缘性优良,耐磨性和耐旱性良好,加工性佳,易于其它材料粘合,在综合性能方面优于多数合成橡胶。
缺点是耐氧和耐臭氧性差,容易老化变质;耐油和耐溶剂性不好,第抗酸碱的腐蚀能力低;耐热性不高。
使用温度范围:约-60℃~+80℃。
制作轮胎、胶鞋、胶管、胶带、电线电缆的绝缘层和护套以及其他通用制品。
特别适用于制造扭振消除器、发动机减震器、机器支座、橡胶-金属悬挂元件、膜片、模压制品。
丁苯橡胶(SBR)丁二烯和苯乙烯的共聚体。
性能接近天然橡胶,是目前产量最大的通用合成橡胶,其特点是耐磨性、耐老化和耐热性超过天然橡胶,质地也较天然橡胶均匀。
缺点是:弹性较低,抗屈挠、抗撕裂性能较差;加工性能差,特别是自粘性差、生胶强度低。
使用温度范围:约-50℃~+100℃。
主要用以代替天然橡胶制作轮胎、胶板、胶管、胶鞋及其他通用制品。
顺丁橡胶(BR)是由丁二烯聚合而成的顺式结构橡胶。
优点是:弹性与耐磨性优良,耐老化性好,耐低温性优异,在动态负荷下发热量小,易于金属粘合。
缺点是强度较低,抗撕裂性差,加工性能与自粘性差。
使用温度范围:约-60℃~+100℃。
一般多和天然橡胶或丁苯橡胶并用,主要制作轮胎胎面、运输带和特殊耐寒制品。
二、硫化剂硫磺,它能使橡胶分子链起交联反应,使线形分子形成立体网状结构,可塑性降低,弹性剂强度增加的物质。
除了某些热塑性橡胶不需要硫化外,天然橡胶和各种合成橡胶都需配入硫化剂进行硫化。
橡胶经硫化后才具有宝贵的使用价值,力学性能大大提高。
三、硫化促进剂和活性剂促进剂CZ、促进剂NOBS、促进剂D、氧化锌、硬脂酸。
轮胎原材料

PL CHINA
12
帘子线材料
棉 重量(同強度) 強度(同体积) 刚度(同负荷) 与橡胶结合 抗疲劳 热时体积稳定性 120 61 93 中 中 是 人造絲 100 100 100 好 好 是 尼龙 58 152 25 好 很好 否 涤纶 68 157 58 中 好 到 中 否 玻璃纤维 58 270 150 好 很差 是 芳族聚酰胺 27 380 130 中 中 是 钢 130 540 500 好 好 是
用于制造轮胎的材料
◆ 天然橡胶 Natural Rubber
◆ 合成橡胶 Synthetic Rubber
丁苯乙烯橡胶SBR 聚丁二烯橡胶 Poly butadiene 丁基橡胶 Butyl
◆ 炭黑 Carbon Black
◆ 油 Oil
◆ 帘子线材料 Tyre Cord Materials: 棉 Cotton; 人造丝 Rayon 尼龙 Nylon 涤纶 Polyester 钢丝 Steel 玻璃纤维 Glass Fiber 芳族聚先胺Aramid ◆ 化学添加剂 Chemicals
14
帘子线材料
人造丝: 轿车和商用卡车的胎体。 尼龙: 广泛用于制造斜交线轮胎。 涤纶: 轮胎胎体层。 玻璃纤维: 早期有问题,一直在测试和发展。 芳族聚酰胺: 强度高、重量轻、价格贵。 钢: 载重轮胎和胎冠层及胎体帘布层。
PL CHINA
15
PL CHINA
16
3.放在架上,送 入烘干室
PL CHINA
7
事实数据
米其林拥有…
13个橡胶种植园
-
Brazil : 3 sites 3 facilities 30,000 Tons 6,000 ha 1,300 employees
轮胎用原材料介绍表

ISAF 中超耐磨炉黑 HAF 高耐磨炉黑 HAF 高耐磨炉黑 新工艺炭黑 FEF 快压出炉黑 GPF 通用炉黑
脂肪酸表面改性碳酸钙。
普通芳烃油,精提取制得
辛基作为改性剂
叔丁基作为酚醛树脂改性剂
热塑性对-特辛基苯酚-甲醛树脂
丁基苯酚和乙炔的缩合物 碳氢烷基系树脂 碳氢芳香基系树脂 改性非自固化酚醛树脂 改性非自固化酚醛树脂 妥尔油改性的热塑性苯酚-甲醛树脂 间苯二酚 苯乙烯 甲醛反应制得 N-(1,3-二甲基丁基)-N'-苯基对苯 二胺 2,2,4-三甲基丁基-1,2-二氢喹啉聚 微晶蜡 微晶蜡 微晶蜡 微晶蜡和石蜡混合物 石蜡
二苯胍
47
促进剂HMT
HMT
48
防焦剂
CTP/PVI
49
普通硫磺
硫原子八元环
50
母胶粒
51
不溶性硫磺IS7020
硫磺-80
IS-HS-7020
硫原子八元环 线性硫(不溶性) 芳烃油
52
不溶性硫磺OT20
53
粘合剂RA-65
54
硅烷偶联剂TESPT
55
癸酸钴
HD OT20
硫原子八元环 线性硫(不溶性) 芳烃油
SL-2101ST
SL-3022
丁基苯酚 乙炔 饱和碳五氢烷基 裂解石油制乙烯的副产物 碳九馏分
间苯二酚 苯乙烯 甲醛
35
防老剂4020
4020/6PPD
36
防老剂RD
RD/TMQ
OKERIN1987
37
橡胶防护蜡
FNL-67T 盛丰I号
ANTILUX 111
38
普通石蜡
58号
一种全钢子午线轮胎基部胶配方

一种全钢子午线轮胎基部胶配方全钢子午线轮胎是一种高性能轮胎,其具有较高的抗剪切性能和胎侧稳定性,适用于各种复杂路况下的高速行驶。
下面是一种全钢子午线轮胎基部胶的配方示例。
1.橡胶基料-天然橡胶(NR):45份-丁苯橡胶(BR):55份-高耐磨橡胶:25份-聚异戊二烯橡胶(IR):15份2.碳黑-尖晶石碳黑(N339):80份-针状碳黑(N550):40份3.防老剂-防老剂RD:2份-防老剂4010NA:1份4.加固剂-石蜡:2份-草酸石墨:1份5.软化剂-塑化剂DAE:5份6.加工助剂-偏磷酸钠:2份-硫磺:2份7.粘合剂-乳化胶:10份8.抗热老化剂-强力抗氧剂:2份9.其他添加剂-网络剂、硫醇交联剂等:适量以上配方的基本比例可以根据具体的要求进行调整。
制备过程如下:1.将天然橡胶、丁苯橡胶和高耐磨橡胶混合搅拌,加入到密封搅拌机中,加入适量的软化剂DAE,搅拌至均匀。
2.将碳黑、防老剂、加固剂、硫磺等添加到橡胶中,继续搅拌混合,使各成分充分分散。
3.加入粘合剂乳化胶,搅拌至均匀。
4.将网络剂和硫醇交联剂等其他添加剂适量加入橡胶中,继续搅拌混合。
5.将搅拌好的胶料放入混炼机中进行混炼,控制混炼温度、混炼时间和混炼速度,使胶料达到理想的混合效果。
6.将混炼好的胶料通过挤压机挤压成型,形成轮胎基部胶条。
以上制备过程中的温度、时间和速度等参数需要根据具体的橡胶材料和设备条件进行调整,以保证胶料的品质。
这种全钢子午线轮胎基部胶配方具有很好的耐磨性和抗剪切性能,能够提供良好的行驶稳定性和舒适性。
同时,经过适当的调整,还可以改善轮胎的抗热老化性能和湿滑性能,以满足不同路况下的要求。
轮胎配方word版
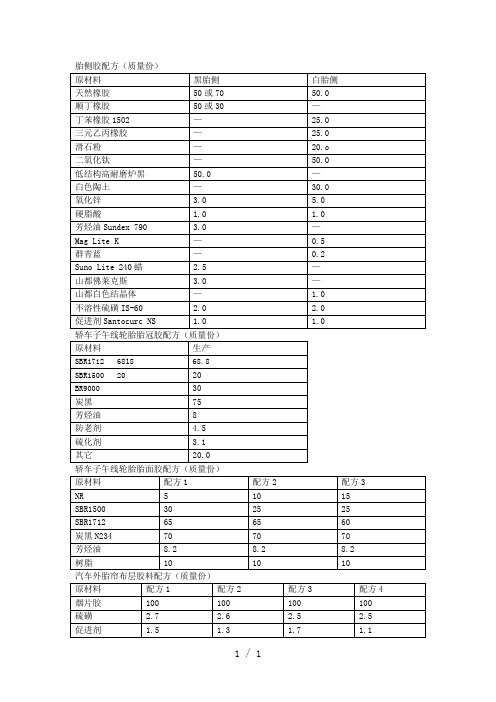
0.5
群青蓝
—
0.2
Suno Lite 240蜡
2.5
—
山都佛莱克斯
3.0
—
山都白色结晶体
—
1.0
不溶性硫磺IS-60
2.0
2.0
促进剂Santocurc NS
1.0
1.0
轿车子午线轮胎胎冠胶配方(质量份)
原材料
生产
SBR17126818
68.8
SBR150020
20
BR9000
30
炭黑
75
芳烃油
胎侧胶配方(质量份)
原材料
黑胎侧
白胎侧
天然橡胶
50或70
50.0
顺丁橡胶
50或30
—
丁苯橡胶1502
—
25.0
三元乙丙橡胶
—
25.0
滑石粉
—
20.o
二氧化钛
—
50.0
低结构高耐磨炉黑
50.0
—
白色陶土
—
30.0
氧化锌
3.0
5.0
硬脂酸
1.0
1.0
芳烃油Sundex 790
3.0
—
Mag Lite K
8
防老剂
4.5
硫化剂
3.1
其它
20.0
轿车子午线轮胎胎面胶配方(质量份)
原材料
配方1
配方2
配方3
NR
5
10
ห้องสมุดไป่ตู้15
SBR1500
30
25
25
SBR1712
65
65
60
炭黑N234
70
- 1、下载文档前请自行甄别文档内容的完整性,平台不提供额外的编辑、内容补充、找答案等附加服务。
- 2、"仅部分预览"的文档,不可在线预览部分如存在完整性等问题,可反馈申请退款(可完整预览的文档不适用该条件!)。
- 3、如文档侵犯您的权益,请联系客服反馈,我们会尽快为您处理(人工客服工作时间:9:00-18:30)。
第三节材料和配方一、轮胎原材料1、橡胶橡胶是轮胎胶料的基体,在配方胶料中橡胶的比率会超过50%,也就是说轮胎胶料中主要的成分是橡胶。
子午线轮胎中采用的橡胶分为天然橡胶和合成橡胶两种。
(1)、天然橡胶天然橡胶是原产于热带地区的一种乔木——橡胶树的产物。
当割开橡胶树干,便有乳白似的胶液从树皮里流出,因此在有些地方称为“流泪的树”。
含有橡胶的植物有二千多种,但最有价值的是三叶橡胶树(如上图),原产于巴西亚马逊河一带。
因此这些树的学名为巴西橡胶树(Hevea brasiliensis)。
巴西虽然是巴西橡胶树的原产地,但由于南美叶疾病的危害和劳动力缺乏,种植面积却很小。
目前巴西橡胶树的种植地区主要集中在东南亚,占世界种植面积的80%以上。
天然橡胶的采集是通过割开橡胶树干,使乳白似的胶液从树皮里流出,收集后使它凝固,再经过一系列工序,就成为半透明的橡胶块。
据记载,世界上最早应用天然橡胶的是古代美洲的印第安人。
他们常用当地橡胶树产出的胶汁制作雨衣、瓶罐及玩具之类的东西。
1492年,哥伦布率领船队横渡大西洋,想寻找通向中国和印度的海路,不料由于航行的错误而跑到了美洲。
就在这次闻名世界的航行中,他把印第安人制作的橡胶用具和玩的橡胶球带回了欧洲,使欧洲人第一次见到了橡胶。
中国在1904年开始种植橡胶树,主要产地在海南省和云南省。
目前轮胎生产使用的天然橡胶主要分为烟片胶和标准橡胶两种,烟片胶常用的为1号烟片胶(RSS1)和3号(RSS3)胶;标准橡胶为标准橡胶10号和20号。
天然橡胶的主要的化学成分为一种以异戊二烯为主要成份的高分子化合物。
烟片胶和标准橡胶性质是相同的只是在加工方面的区别,由于标准橡胶产品具有良好的均一性,加工方便,目前子午胎使用的天然橡胶多为标准橡胶。
烟片胶的生产过程为:鲜胶乳—→加保存剂—→过滤除杂质—→加水稀释—→澄清—→加酸凝固—→凝块压片—→熏烟干燥—→分级—→包装。
标准胶的生产过程为:鲜胶乳—→加保存剂—→过滤除杂质—→加水稀释—→澄清—→加酸凝固—→凝块压片—→造粒—→干燥—→分级—→包装。
烟片胶的生产已有大约100年的历史,是一种传统的生产工艺,熏烟是通过烧木产生的烟气和热量来熏干胶片制成烟片胶的一种方法。
标准橡胶产生于60年代。
由于传统的制胶方法在工艺、设备和分级制度上都束缚了天然橡胶事业的发展,特别是天然橡胶产量大的国家。
因此,马来西亚于1965年开始实行标准橡胶计划,目前标准橡胶已成为天然橡胶最主要的品种。
标准橡胶与烟片胶相比的优势在于:——使用生胶的理化性能分级更能合理的区分橡胶的内在质量。
——机械化程度高,生产周期短,由于集中加工产品质量的一致性得到进一步保证。
质量也容易控制。
目前使用的标准橡胶根据产地进行区分:SMR(Standard Malaysian Rubber)马来西亚标准橡胶SIR(Standard Indonesian Rubber)印度尼西亚标准橡胶SLR(Standard Srilanka Rubber)斯里兰卡标准橡胶SSR(Standard Singapore Rubber)新加坡标准橡胶“SMR10”即表示马来西亚10号标准橡胶(2)、合成橡胶合成橡胶顾名思义就是通过人工合成得到的橡胶。
大约一个世纪前,随着西方国家工业化步伐的加快,天然橡胶的品种和数量已远远不能满足人们的需要。
于是,科学家开始考虑合成橡胶的问题。
人工合成橡胶的关键首先是了解它的化学组成,弄清其分子构造,否则人工合成时将无从下手。
最早在这方面作出贡献的是英国化学家法拉第等人。
橡胶的特点是它的每个分子呈蜷曲状,而且互相纠缠在一起,好像一个乱七八糟的毛线球。
当你用力拉它时,分子就伸开,一松手,分子又蜷缩成原来的样子。
因此,橡胶具有奇特的弹性。
到目前科学家先后合成了顺丁橡胶、丁基橡胶、氯丁橡胶、乙丙橡胶、丁苯橡胶、丁腈橡胶、硅橡胶等一系列具有奇异功能的新产品。
现对轮胎生产使用的主要合成橡胶介绍如下:●丁二烯-苯乙烯橡胶(Styrene-Butadiene Rubber)丁二烯-苯乙烯橡胶为丁二烯与苯乙烯的共聚物,简称丁苯橡胶,代号SBR,是最早工业化的通用合成橡胶,1933年由德国I.G.FARBEN公司研制,1937年进行工业化生产。
丁苯橡胶具有较好的综合性能,其加工性能、物理机械性能和所制橡胶产品的使用性能较接近于天然橡胶,且耐磨耗、耐热老化等性能还优于天然橡胶。
丁苯橡胶能与天然橡胶、顺丁橡胶等橡胶并用,是主要的通用橡胶,广泛用于制造轮胎、胶管、胶带、胶鞋以及各种工业橡胶制品。
其年耗用量占合成橡胶的首位。
合成丁苯橡胶可分为乳聚和溶聚丁苯橡胶两种类型。
乳聚丁苯橡胶乳聚丁二烯-苯乙烯橡胶简称(Emulsion polymerized styrene butadiene rubber或Emulsion styrene-bu-tadiene rubber)乳聚丁苯橡胶,代号为E-SBR。
根据聚合温度不同,分热法乳聚丁苯橡胶(50℃)和冷法乳聚丁苯橡胶(5℃)前者也称"热橡胶"(hot rubber)或高温丁苯橡胶;后者则称"冷橡胶"(Cold rubber)或低温丁苯橡胶。
一般丁苯橡胶中苯乙烯含量为23.5±1%,但也有含量高达40%以上的称高苯乙烯橡胶(high styrene rubber);结合苯乙烯70-90%则为高苯乙烯树脂;个别也有结合苯乙烯低的。
除纯丁苯橡胶外,还有充油乳聚丁苯橡胶和充油充炭黑乳聚丁苯母炼胶。
乳聚丁苯橡胶生产已近60年,加工应用技术成熟,应用广泛,其生产能力和消耗量一直位居合成橡胶中的首位。
早期的乳聚丁苯大多为高温乳聚丁苯。
目前使用的SBR1500、SBR1502等是低温乳聚丁苯。
SBR1500、SBR1502二者的区别在于SBR1500使用松香酸皂为乳化剂使用污染的防老剂因此不能用于浅色的制品;而SBR1502使用松香酸和脂肪酸的混合酸皂为乳化剂使用非污染的防老剂因此可用于浅色的制品;目前使用的另外一种乳聚丁苯橡胶是SBR1712是充油丁苯橡胶是在橡胶中充入了37.5份的高芳烃油。
乳聚丁苯橡胶以数码分别表示各种系列如下: 1000系列高温聚合非充填丁苯橡胶;1100系列高温聚合充炭黑丁苯母炼胶;1200系列高温聚合充油丁苯橡胶;1300系列高温聚合充油充炭黑丁苯炼胶;、1500系列低温聚合无充填丁苯橡胶;1600系列低温聚合充炭黑丁苯母炼胶(充油量14份/100份橡胶以下);1700系列低温聚合充油丁苯橡胶;1800系列低温聚合充油充炭黑丁苯母炼胶(充油量14份/100份以上);1900系列乳聚树脂橡胶母炼胶。
溶聚丁苯橡胶Solution polymerized styrenebutadiene rubber 溶液聚合丁苯橡胶是丁二烯和苯乙烯单体在有机溶剂中采用锂或烷基锂催化剂或有机金属催化体系,于溶液中进行共聚合而得,简称溶聚丁苯橡胶,代号S-SBR。
与乳聚丁苯橡胶相类似,但有以下特点。
(1)混炼胶收缩少,表面光滑。
(2)硫化起步较乳聚丁橡胶快,硫化平坦性好。
(3)动态性能优良。
(4)屈挠龟裂和裂口增长性能好。
(5)低温性能良好。
(6)与天然胶、乳聚丁苯橡胶并用性能优良。
(7)由于高分子化学分设计技术的发展,一些新的品种性能有了新的突破,具有抗湿滑性好、滚动阻力低和耐磨耗好,三者较佳平衡,目前在国外轮胎公司主要用于轿车轮胎中。
●聚丁二烯橡胶聚丁二烯橡胶是1,3-丁二烯单体聚合所得的系列聚合物。
简称顺丁橡胶,代号BR。
聚丁二烯的生产能力已仅次于丁苯橡胶,在合成橡胶各胶种中仍居第二位。
聚丁二烯橡胶多以溶液聚合方法制得。
按微观结构有顺式-1,4-聚丁二烯、反式-1,4-聚丁二烯和1,2-聚丁二烯等;按引发剂体系则有;钛系、钴系、镍系、锂系、稀土系聚丁二烯和醇烯橡胶,其中醇烯橡胶因加工性能不好,且价格昂贵,已停产。
也有采用乳液聚合方法得到的乳聚聚丁二烯橡胶。
聚合物又有充油的充油胶、充炭黑的炭黑母炼胶、充油和炭黑的充油充炭黑母炼胶。
除干聚合物外,还有聚丁二烯胶乳、液体聚丁二烯。
充油胶所充的油有高芳烃油、芳烃油、环烷烃油和链烷烃油。
充炭黑母炼胶所充的炭黑品种有高耐磨炉黑、高结构高耐磨炉黑、中超耐磨炭黑、高结构中超耐磨炉黑和新工艺炭黑如N234,N339,N351等。
现充炭黑和充油充炭黑聚丁二烯母炼胶已停产,未见有商品了。
我国国家标准GB5577-85规定聚丁二烯橡胶牌号为BR9000,稀土顺丁橡胶为BR9100。
●丁基橡胶(Isobutylene-isoprene rubber,缩写为IIR)是一种线型无凝胶的共聚物(即无支链,未硫化胶无交联),是以异丁烯与少量异戊二烯采用离子型聚合法生产的。
丁基胶的优点:a、丁基橡胶的气透性在烃类橡胶中是最低的。
丁基橡胶的气体溶解度与基它烃类橡胶接近,但是它的气体扩散速度比其它橡胶低得多,这有利于丁基橡胶在内胎、气密层等方面的应用。
b、丁基橡胶的化学不饱和度低,加上聚异丁烯链的不活泼性,使丁基橡胶的耐热和耐氧化性能远优于其它通用橡胶。
丁基橡胶耐热老化性能较优异。
硫化胶的热氧老化属降型,老化趋向软化。
c、炭黑补强的丁基硫化胶,耐候性是很突出的,能长时间曝露于阳光和氧气中而不损坏。
丁基橡胶表面降解的速度、深度和程度受填充剂对光的反射和对氧的吸收以及填充剂的性质和用量的影响,使用高反射的填充剂(例如二氧化钛和氧化锌)的丁基硫化胶耐候性能更佳。
d、与高不饱和橡胶相比,丁基橡胶耐臭氧性能特别好。
典型的丁基硫化胶的抗臭氧性能比高不饱和的天然橡胶、丁苯橡胶等橡胶约高10倍。
e、丁基橡胶特别耐动植物油,在酒精、乙酸等多种极性有机介质中溶胀也甚微,溶胀程度随硫化程度的提高和填充剂特别是炭黑用量的增大而降低。
丁基橡胶不耐浓氧化酸,但耐非氧化酸和中等浓度的氧化酸,耐碱溶液和氧化-还原溶液。
丁基橡胶是第一个高饱和橡胶品种,少量异戊二烯的引入是为了获得可供硫化的双键。
由于结构的特点,丁基橡胶有良好的气密性和耐老化性。
但也限制了其与聚二烯烃橡胶的并用,此外,分子中缺少极性基团,也使其与金属或橡胶的粘合性能差,随着合成橡胶工业发展和应用的需要,IIR现已开发成拥有衍生橡胶、改性橡胶、热塑性弹性体和热塑性硫化胶等品种的通用橡胶。
氯化丁基橡胶氯化丁基橡胶(CIIR)的制备方法分干胶混炼氯化和溶液氯化两种方法。
前一法是在开炼机上把吸附了氯气的活性炭或其它氯化剂混入丁基橡胶中经加热和混炼后制得;后一法是先把其橡胶溶于四氯化碳、氯仿或己烷等溶剂中,然后在常温下通过氯气进行氯化,即制得氯化丁基橡胶,由于该法已实现连续氯化工艺生产,故已成为主要的制造方法。
极性氯原子的引入,可克服丁基橡胶硫化速度慢、粘合性能差,与高不饱和橡胶难于共硫化等的问题。