铁水装入量吨的提钒转炉车间工艺设计
含钒铁水转炉提钒渣冶炼方案(初稿)

含钒铁水转炉提钒渣冶炼方案目录1.钒相关基础知识 (4)1.1钒元素的发现与发展 (4)1.2国内钒的发展 (5)1.3钒的矿物简介 (6)1.4钒及其化合物的性质 (6)1.4.1金属钒的性质 (6)1.4.2金属钒的制备: (7)1.4.3钒的主要氧化物 (7)1.4.4含钒化合物的理化性能 (8)1.5钒在钢铁上的应用 (9)1.6钒的生产方法 (10)2.转炉提钒基本原理 (11)2.1转炉提钒的意义 (11)2.2转炉提钒的原理 (12)2.3铁质初渣与金属熔体间的氧化反应 (12)2.4转炉提钒脱钒、脱碳规律 (12)2.5铁水中钒与碳氧化的转化温度 (13)2.6影响转炉提钒的主要因素 (15)2.6.1铁水成分的影响 (15)2.6.2 铁水中钒的影响 (15)2.6.3.铁水硅的影响 (15)2.6.4.吹炼终点温度对钒渣中全铁含量影响 (16)2.6.5.供氧制度的影响 (17)3.提取钒渣方法 (17)3.1顶底复吹转炉提钒 (17)3.2转炉单联法提钒 (18)3.3攀钢转炉提钒工艺 (20)3.3.1转炉提钒工艺流程图 (20)3.3.2攀钢转炉提钒工艺过程 (20)3.3.3攀钢转炉提钒主要设备参数 (21)3.3.4攀钢转炉提钒用原材料 (21)3.3.5 不同氧枪的提钒效果 (22)3.3.6攀钢转炉提钒冷却制度 (23)3.3.7攀钢转炉提钒终点控制 (24)3.3.8出半钢和倒钒渣 (24)3.3.9攀钢提钒钒渣 (25)4.八钢炼钢提钒渣方案 .......................................................................... 错误!未定义书签。
1.钒相关基础知识1.1钒元素的发现与发展钒(V),呈银灰色,原子序数为23,原子量为50.942,在元素周期表中属VB族,具有体心立方晶格。
1801年,墨西哥矿物学家德尔·里奥在研究铅矿时,发现一种化学性质与铬、铀相似的新元素,其盐类在酸中加热时呈红色,故名为红色素。
低钒铁水提钒炼钢工艺分析

氧化转化临界温度为 131317e 。可见, 提钒的终点
半钢温度不宜过高。提钒过程前期以钒氧化为主,
后期以钒还原为主, 吹钒反应可表示为:
k1
))) y
[V ]
(V )
( 1)
z )))
k2
式中 k1) ) ) 钒正向反应常数; k2) ) ) 钒逆向反应常数。
吹钒反应速率可表示为:
(
-
d
[ V] dt
半钢碳含量平均 314% , 范围 2194% ~ 4102% , 分布见图 2。根据图 2, 半钢 [ C] \312% 者占 85% 。 说明保碳操作较为合理。
图 2 半钢碳含量分布
4. 2 半钢温度 由于铁水到转炉后无铁水成份, 只能根据上一
炉的温度情况确定生铁块量, 并且是先进铁水再测 温, 生铁块的重量已无法改变, 只能用铁皮球来调整 温度。因铁水 [ Si] 存在一定的波动, 再加上温度控 制水平参差不齐, 半钢温度控制存在一定的波动, 总 体上控制较好, 平均 1373e , 范围 1331~ 1418e , 其 分布见图 3。根据图 3, 半钢温度控制在试生产要求 的 1340~ 1400e 者占 82% 。
7远程监控功能实现远程对高炉上料计量数据的监控管理功结束语在高炉上料计量自动计量管理系统设计中使用数据自动采集数据自动处理数据库网络通讯等多项技术使整个系统实时高效运行系统完成后将公司的计量管理提升到了一个新的高度为炼铁厂成本核算提供基础数据为分厂生产经营提供坚实决策依据同时为今后公司的erp系统提供了真实准确有效及时的基础数据
半钢温度与 [ V ]半的对应值
1250
1300
0. 180
0. 075
1350 0. 042
第五章 含钒铁水炼钢工艺及钢渣(钒渣)提钒

前期:开吹枪位1.4米,快速升温
化渣枪位2.2米,增加熔池∑(FeO)含量
中期:多次变化枪位 1.4~2.0米
后期:1.2米 减少渣中∑(FeO)含量,均匀钢水温度、成分,有 利于溅渣护炉。
2.2
2.0
2.0
1.8
枪位/m
1.4
1.4
吹炼前期
1.4
1.4
吹炼中期
1.2 吹炼后期
吹炼时间
分阶段恒压变枪位供氧操作(攀钢)
2、钒渣直接使钢合金化
采用钒渣直接合金化原理:是用钒渣和还原剂进行混合, 还原渣中的钒氧化物,并使钒转入钢中。
优点:可显著降低合金化的成本,减少生产钒铁造成的 钒损失,提高钒利用率。目前俄罗斯许多企业采用钒渣直接 合金化。采用不同含钒原料使钢合金化时,钒进入钢的比率 及工艺流程图见下页。
含钒铁精矿100%V 造块原料(烧结球团)97.8%
⑶渣料加入时间和炉渣的控制 攀钢渣料一般分两批加入,第一批占总渣料的60%以上,其余在第二批
分小批加入。如拉碳后需调整炉渣或炉温,则再加入第三批渣料。 ①渣料加入时间
第一批渣料在兑铁前或开吹时加入,包括石灰、镁质材料和酸性材料。 第二批渣料在第一批渣料化好、化透后分小批量多次加入(每次不超过 0.5吨),这样有利于石灰熔化,避免炉渣“返干”,同时还可以较好控制 炉内泡沫渣,防止喷溅和溢渣,在吹炼终点前3~5min全部加完。 第三批渣料是否加入,根据拉碳后硫、磷去除情况而定。 注意:无论加几批渣料或加多少渣料,都必须保证终点炉渣化好,确 保渣料的有效利用。
注意:要提高合金钒含量可配入V2O5,这样可得到V50%以上 的钒铁。
国际上钒铁根据钒含量分为低钒铁FeV35~50,一般用硅热法 生产;中钒铁FeV55~65和高钒铁FeV70~80,一般用铝热法生产。
提钒与转炉炼钢工艺共86页文档

提钒与转炉炼钢工艺
6
、
露
凝
无
游
氛
,
天
高
风
景
澈
。
7、翩翩新 来燕,双双入我庐 ,先巢故尚在,相 将还旧居。
8
、
吁
嗟
身
后
名
,
于
我
若
浮
烟
。
9、 陶渊 明( 约 365年 —427年 ),字 元亮, (又 一说名 潜,字 渊明 )号五 柳先生 ,私 谥“靖 节”, 东晋 末期南 朝宋初 期诗 人、文 学家、 辞赋 家、散
拉
60、生活的道路一旦选定,就要勇敢地 走到底 ,决不 回头。 ——左
1
0
、
倚
南
窗
以
寄
傲
,
审容膝ຫໍສະໝຸດ 之易安。
56、书不仅是生活,而且是现在、过 去和未 来文化 生活的 源泉。 ——库 法耶夫 57、生命不可能有两次,但许多人连一 次也不 善于度 过。— —吕凯 特 58、问渠哪得清如许,为有源头活水来 。—— 朱熹 59、我的努力求学没有得到别的好处, 只不过 是愈来 愈发觉 自己的 无知。 ——笛 卡儿
转炉双联法提钒工艺流程

转炉双联法提钒工艺流程下载温馨提示:该文档是我店铺精心编制而成,希望大家下载以后,能够帮助大家解决实际的问题。
文档下载后可定制随意修改,请根据实际需要进行相应的调整和使用,谢谢!并且,本店铺为大家提供各种各样类型的实用资料,如教育随笔、日记赏析、句子摘抄、古诗大全、经典美文、话题作文、工作总结、词语解析、文案摘录、其他资料等等,如想了解不同资料格式和写法,敬请关注!Download tips: This document is carefully compiled by theeditor. I hope that after you download them,they can help yousolve practical problems. The document can be customized andmodified after downloading,please adjust and use it according toactual needs, thank you!In addition, our shop provides you with various types ofpractical materials,such as educational essays, diaryappreciation,sentence excerpts,ancient poems,classic articles,topic composition,work summary,word parsing,copy excerpts,other materials and so on,want to know different data formats andwriting methods,please pay attention!转炉双联法提钒工艺流程转炉双联法提钒工艺是一种常用的钢铁生产工艺,其流程主要包括炼钢、连铸和提钒等环节。
提钒与转炉炼钢工艺

湿法提钒工艺流程示意图
1-2-2 火法提钒
• 火法提钒是用含钒的磁铁烧结矿,经过高 炉冶炼出含钒铁水,再进行提钒处理。中 国、俄罗斯等国家采用这种方法提取钒 • 通过电炉,将含钒铁矿预还原成金属球团 矿后,再经电炉冶炼出含钒铁水,提取钒 渣。南非和新西兰等国家采用这种方式提 取钒
火 法 提 钒 工 艺 流 程 示 意 图
教学内容
1
2 3
任务单元1:1-1 钒相关知识介 绍 任务单元2:1-2 提取钒的方法
任务单元3:1-3 氧化法提钒的方法
4
任务单元4:1-4 氧气顶吹转炉吹炼提取钒
任务单元1:1-1 钒相关知识介绍
钒钛资源用途
钒 相关知识介绍
钒的性质
钒的用途
1-1-1钒钛资源
1-1-1钒钛资源
• 攀西地区是中国矿产资
火法提钒的发展方向
转炉顶底复合吹炼提钒是今后转炉提钒顶底 发展方向
1-4 氧气顶吹转炉吹炼提取钒
1 2
1-4-1 氧气顶吹转炉吹炼提取钒原理
1-4-2 氧气顶吹转炉吹炼提取钒的准备
3
1-4-3 氧气顶吹转炉吹炼提钒工艺
提钒任务
含钒铁水
提钒
半钢
把含钒铁水吹炼成 高碳含量并满足下 一步炼钢要求的半 钢,包括成分、温 度
1-3-3转炉提钒方法
1
空气侧吹转炉提钒
2
氧气顶吹转炉吹炼提取钒
3
氧气顶底复吹转炉提钒法
1-3-3-1 空气侧吹转炉提钒
空气侧吹转炉是利用侧吹供入空气,使转炉 内铁水钒氧化而获得钒渣。
1-3-3-2 氧气顶吹转 炉吹炼提取钒
氧气顶吹转炉吹炼提钒法是 我国火法提钒生产广泛采用的 工艺
转炉提钒工艺与设备(钒渣-五氧化二钒-三氧化二钒-金属钒-钒铁-钒铝合金-碳氮化钒-钒电池)

转炉提钒工艺与设备(钒渣-五氧化二钒-三氧化二钒-金属钒-钒铁-钒铝合金-碳氮化钒-钒电池)原创邹建新崔旭梅教授等转炉提钒工艺与设备提钒的原材料:高炉铁水;提钒的产品:钒渣+半钢;提钒的工艺:氧气顶吹法;提钒的主体设备:炼钢转炉。
1 转炉提钒工艺过程(1)铁水供应将脱硫后的铁水扒渣,再用起重机将铁水兑入转炉。
(2)冷却剂供应a.生铁块、废钒渣:用电磁起重机装入生铁料槽,再用起重机加入提钒炉。
b.铁皮球、污泥球、铁矿石:用翻斗汽车运至地面料仓,由单斗提升机运到37.56m平台,经胶带运输机送到炉顶料仓内。
使用时由炉顶料仓电磁振动给料机给料,经称量斗称量后加入转炉。
(3)氧气和氮气供应氧气用管道输送到车间内,氧气纯度为99.5%;压力0.49~1.18 MPa;氮气压力0.294~0.392Mpa。
(4)吹炼提钒吹炼前根据铁水条件加入生铁块或废钒渣,然后兑入铁水,摇正炉体下枪供氧吹炼,在吹炼过程中可根据吹炼情况加适量铁皮球、铁矿石、污泥球,吹炼结束时先出半钢进入半钢罐。
(5)出钒渣转炉炉下钒渣罐采用16m3渣罐,每个渣罐能容纳吹炼钒渣8~12炉。
钒渣罐通过炉下电动渣罐车拉至钒渣跨,用起重机吊至16m3钒渣罐车上;每4辆车组成一列(3辆钒渣罐车,一辆废渣车),用火车拉至钒渣破碎间,废渣拉至弃渣场。
2 转炉提钒设备以攀钢转炉提钒主要设备为例。
设计工艺参数:公称容量120吨,设计炉产半钢138吨,提钒周期30min/炉,纯吹氧时间8min,日提钒最大炉数68炉(2吹2时),设计年产钒11万吨/年,半钢295万吨/年。
转炉炉型参数:高9050mm,炉壳外径6530mm,高宽比1.386,熔池内经5180mm,熔池深度1400mm,转炉有效容积136m3,炉容比V/t 0.986,炉口外径2480mm。
提钒转炉主要设备有冷却料供应系统、转炉及其倾动系统、氧枪系统、烟气净化及回收、挡渣镖加入装置等。
(1)冷却料供应系统冷却剂供应系统包括地下料坑、单斗提升机、皮带运输机、卸料小车、高位料仓、振动给料器、称量料斗以及废钢槽、天车等设备,这些设备保证提钒用原料的正常供应。
提钒与转炼钢工艺6

部分冷却剂
增碳剂及各种气体等
各种铁合金
锰铁、硅铁及硅锰合金等
炼钢原料的分类—分类方法二
铁水
金属料
废钢
原
铁合金
料
非金属料
造渣料 部分冷却剂
增碳剂等
各种气体
氧气、氮气、氩气等 返回目录
3-1 主原料
3-1-1 铁水(半钢) 3-1-2 废钢 3-1-3 生铁块
3-1-1 铁水
• 铁水是转炉炼钢的主要原 料,一般装入炉量的 70~100%,由于攀钢转炉 炼钢工艺的特殊性,铁水作 为炼钢的基本原料时,半钢 更是主要的原料。
• 废钢应清洁干燥,尽量避免带入泥土沙石、耐火 材料和炉渣等杂质;
• 废钢应具有合适的外形尺寸和单重。
返回子目录
3-1-3 生铁块
生铁块
• 生铁块也叫冷铁, 是铁锭、废铸件、 罐底铁和出铁沟铁 的总称,其成分与 铁水相近,但没有 显热。
• 冷却效应比废钢低, 同时还需要配加适 量石灰渣料。有的 厂家将废钢与生铁 块搭配使用。
Mg/CaC2) • 苏打粉(Na2CO3)
电石粉脱硫
主要成分:CaC2 ,熔点为2300℃,粒度在0.1~ 1mm,脱硫反应:
CaC2(固) FeS CaS(固)+Fe+2C
• 脱硫特点: • CaC2有很强的脱硫能力 • 易于扒渣,对混铁车或铁水包内衬侵蚀较轻 • 污染环境,必须安装除尘装置 • 电石粉是工业产品,价格较贵 • 5)要特别注意电石粉在运输和储存过程的安全
前言 单元一:主原料 单元二:辅原料 单元三:铁合金
前言
• 原材料是炼钢的物质基础 • 原材料的质量和供应条件对炼钢生产的各项技
术经济指标有重大影响 • 原材料质量评价内容——化学成分和物理性质
铁水提钒

பைடு நூலகம்理
原理
含钒生铁提钒工艺以选择性氧化为理论基础。向铁水吹入空气或氧气,必须使铁水中钒迅速、优先氧化,而 其他组分少氧化,方能获得含钒高的钒渣。吹炼过程中应使铁水中的碳氧化最少,保证半钢炼钢时仍有足够的化 学反应热。铁的损耗要降至最低限度,即半钢的收得率要高,以降低钒渣生产成本。
影响因素
钒渣的氧化性
温度控制
钒渣碱度
温度控制
图2钒的氧化反应属于放热的多相复杂反应,但其热效应值在数量上差别很大,反应产物的表示也各不相同。 铁水提钒过程中各元素的氧化反应的标准生成自由能与温度的关系示于图2。由图可见,提钒初期熔池温度比较低 (约1300℃左右)时
(△F°)Ti<(△F°)Si<(△F°)Cr<(△F°)V<(△F°)Mn<(△F°)C
简史
简史
从含钒铁矿中回收钒是从19世纪初期开始的。德国和法国在第二次世界大战时期,用高炉—托马斯转炉法从 含钒0.06%~0.10%的洛林铁矿中(不含钛)回收钒。以含钒铁矿作为高炉原料生产生铁时钒也被还原,获得含钒 0.10%~0.15%的铁水,用此生铁炼钢时钒又被氧化进入托马斯炉渣中,炉渣含钒量可以达到0.5%,是一种无直接 使用价值的低钒渣。德国赫尔曼·戈林钢厂将这种低钒渣与转炉钢厂的其他产物(如厂房屋顶积灰,含0.8%~ 1.0%钒)在另一座高炉内冶炼成含钒和含磷较高的生铁,再经托马斯转炉吹炼得到含钒量较高的钒渣,可直接作 为化工厂生产钒的原料,但含钒铁水提钒后含磷较高,给炼钢带来困难。
第四章+攀钢转炉提钒工艺
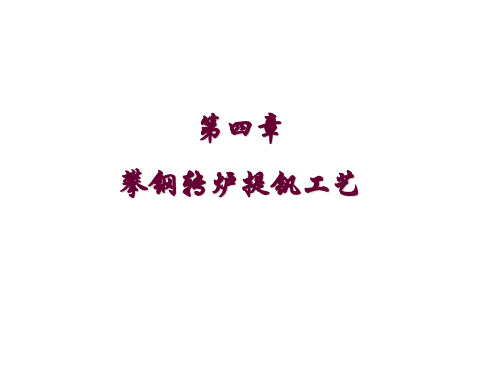
转炉炉下钒渣罐采用16m3渣罐,每个渣罐能容纳吹炼钒渣8~12
炉。钒渣罐通过炉下电动渣罐车拉至钒渣跨,用起重机吊至16m3 钒渣罐车上;每4辆车组成一列(3辆钒渣罐车,一辆废渣车),用火车 拉至钒渣破碎间,废渣拉至弃渣场。
三、攀钢转炉提钒主要设备
设计工艺参数:
公称容量120吨,设计炉产半钢138吨,提钒周期30min/炉,纯吹
B 托圈和耳轴
托圈和耳轴的作用:支撑炉体并传递转矩。 ① 托圈:是由优质钢板焊成,断面呈矩形的中空圆环,内部通水冷却, 以降低热应力。其两侧各固定了两个耳轴,为炉壳受热膨胀不受限制 和通风冷却,在托圈和炉壳之间留有100mm间隙。 ② 耳轴:是给转炉和托圈传递低速、重载荷、大力矩的传动件,要求其
具有足够的强度和刚度,可用40Cr制作。
头圆锥形的护板→防止托圈上
堆积炽热的炉渣。
炉帽
炉帽上设有出钢口,出钢口最易损坏,一般设计成可拆卸式的。
出钢口
b. 炉身
炉身为圆筒形,它是整个炉壳受力最大的部分,转炉的整
体重量通过炉身钢板支撑在托圈 上,并承受倾炉力矩。
c. 炉底
炉为球
形,其下部焊有 底座以提高强度。
炉底
炉帽、炉身、 炉底三部分之间 采用不同曲率的 圆滑曲线连接,以 减少应力集中。
1、首钢3吨LD转炉提钒试验 1965年7月~11月在首钢进行了三个方案的试验。 a. 同炉单渣法 试验了39炉
b. 同炉双渣法
c. 双联法 实验结论:
试验了61炉
试验了145炉
a.双联法:钒回收率较高,钒渣的水浸率可高达90.0—97.7%,是一次 从生铁中提出优质钒渣的较好方法。缺点是生产调度上较为复杂。 b.同炉双渣法:钒渣含钒低,钒回收率较低,CaO、P、S高,不适宜 用现行工艺进行焙烧浸出处理。可作为石灰代用品返回高炉利用。 c.同炉单渣法:钒渣含钒更低,余钒较高0.08%以下, CaO、P高。
100T转炉45#钢生产工艺要点

100T转炉45#钢生产工艺要点(冶炼部分)1.工艺路线:混铁炉—提钒转炉—炼钢转炉—精炼—方坯保护浇铸2•原料条件:尽量组织用铁水(半钢)[S]W0.040%冶炼,以保高拉碳为原则控制冷料用量。
3.成份控制4.温度控制(表中温度为贺利氏测温偶头的夏季温度,冬季连拉炉次温度上调5C)。
5.1吹炼前期化好渣,化透渣,避免熔池温度上升过快及炉渣“返干”现象发生5.2吹炼终点:尽量一次拉成,保证C-T协调,补吹不大于两次。
终点[C]最佳控制为0.10〜0.20%;[S]W0.030%,[P]W0.015%。
5.3挡渣:用挡渣塞、挡渣锥或专用挡渣设施进行挡渣操作,确保渣层厚W出钢时间保证出钢口圆滑出钢时间三秒。
其中在出钢前加入,其余部分在加完合金料后加入,氧化性强靠上限,氧化性弱靠下限。
合金参考:用合金化。
根据出钢终点氧化性随合金料均匀加入炉调渣剂,出钢后加入顶渣袋炉。
5.7在冶炼此钢种时,转炉复吹必须执行切换。
精炼要求6.1吹氩时间三分钟,前分钟执行吹氩操作,其余执行弱吹氩操作。
吹氩过程中尽量少喂或不喂线,若氩前a[o]三,可喂米线进行调整,a[o]注:结合脱氧剂的加入量,氧化性强喂线量靠上限,氧化性弱喂线量靠下限。
注意事项开新炉前炉和大补炉后第炉禁止冶炼此钢种。
冶炼此钢种时,调度室提前炉通知转炉岗位和化验室,转炉岗位根据实际情况调整冷料用量,化验室提前做标样。
严禁使用新包,及时处理炉口积渣和包沿,要求钢包内无残渣和包底,保证红包出钢。
本制度自年月日起执行,原年月日工艺要点同时作废。
技术科大包保护管中间包浸入式水口结晶器铸坯三、拉钢前的准备要求结晶器使用寿命W分钟,内腔表面光滑,上下水缝无漏水。
要求使用干式料中间包烘烤达到小时以上并且中间包内保持清洁无杂物溢流口修砌符合排渣要求。
石英质(或铝碳质)浸入式水口和快换下水口必须烘烤后使用。
四、拉钢过程的控制生产断面():x大中包温度控制及浇注周期贺利氏偶头夏季温度,注:五流、六流拉钢时总蹲包时间W分钟,七流、八流拉钢时总蹲包时间W 分钟,调度室开作业卡要温度时蹲包温降按1・O°C/min计算(不区分冬夏季)。
提钒与钢炉炼钢工艺——转炉炼钢工艺

录像网址: http://www.scemi. com/jpkc/tfyzl/Arti cle/ShowArticle.a sp?ArticleID=38
钢与生铁的比较
铁合金
生铁
钢
成分
含碳量
2%~4.3%
其它元素 硅、锰、硫、磷(少量)
0.03%~2% 硅、锰(少量)
机械性能
硬而脆无韧性 可铸、不可锻
单元2:2-2 气体射流与熔池的相互作用 单元3:2-3 氧气转炉冶炼的基本反应
单元4:2-4 转炉冶炼的基本特征 单元5: 2-5 转炉冶炼的基本判断方法
2-1 炼钢的任务
铁水
炼钢过程
•脱碳 •脱硫 •脱磷 •脱氧
炼钢过程
•去气体 •去夹杂 •合金化 •调 温
钢
钢与生铁的比较
根据标准规定,钢的定义是:以 铁为主要元素,碳含量一般在2 %以下,并含有其他元素材料的 统称
4
底吹气体对熔池的作用
5 复合吹炼供气对熔池的搅拌
前言
观看录像2-3
录像网址: http://www.scemi. com/jpkc/tfyzl/Arti cle/ShowArticle.a sp?ArticleID=38
根据图2-1 和图2-2讲
解
叙述
前 言
前言
顶吹氧气转炉是将高压、高 纯度的氧气通过水冷氧枪,以 一定距离从熔池上面吹入的。
• 顶吹氧气转炉是将高压、 高 上纯 )度 的( 氧含气通O2过99水.5冷%氧以 枪,以一定距离(喷头 到熔池面的距离约为1~ 3米)从熔池上面吹入的。 为了使氧流有足够的能 力穿入熔池,使用拉瓦 尔型多孔喷头,氧气的 使用压力0.8~1.2MPa, 氧流出口速度可达 500m•s-1左右
转炉含钒钢渣入矿热炉预处理工艺设计

第47卷第4期2020年12月有色金属设计Nonferrous Metals Desig]Vol.47 No.4Dec.2020转炉含钒钢渣入矿热炉预处理工艺设计吕韬,李秦灿,宁晓宇,李凌楠,贾定慧(中冶东方工程技术有限公司,山东青岛266555)摘要:利用火法冶金可以有效提取转炉钢渣中未利用的机,为了满足含机钢渣的矿热炉入炉要求,需将之进行制粒、烧结。
文章对这套原料储存、运输、烧结工艺进行了详细阐述,为后续矿热炉冶炼含机钢渣生产含机生铁提供有利条件,具有一定的生产借鉴意义。
关键词:转炉钢渣;制粒;烧结中图分类号:TF046 文献标识码:A文章编号!1004:660 (2020) 04-0053-04P re tre a tm e n t P ro cess D e s ig n o f V a n a d iu m- b e a rin g B O F S l a g s fo r S A F S m e lt in gL v T a o,L i Qincan,NingXiaoyu,L i Lingnan,JiaDinghui(BERIS Engineering&Research Corporation,Qingdao266555,China)Abstract:Pyrometallurgy can efectively extractsremaining vanadium in BOF slags.BOF slags need to be granulated and sintered to meet tlie requirements of subsequent SAF smelting.T his paperelaborates the storage,transportation and sintering,a preparation for vanadium—bearing pig iron production in submerged arcfurnace(SAF),providing a reference for production concerned.Keywords:BOF slags;Granulation;Sintering〇引言钒是一种重要的金属元素,主要用于钢铁工 业,以改善钢的强度、韧性及耐蚀性等性能。
- 1、下载文档前请自行甄别文档内容的完整性,平台不提供额外的编辑、内容补充、找答案等附加服务。
- 2、"仅部分预览"的文档,不可在线预览部分如存在完整性等问题,可反馈申请退款(可完整预览的文档不适用该条件!)。
- 3、如文档侵犯您的权益,请联系客服反馈,我们会尽快为您处理(人工客服工作时间:9:00-18:30)。
铁水装入量吨的提钒转炉车间工艺设
计
文档仅供参考
攀枝花学院本科毕业设计(论文)
铁水装入量150吨的提钒转炉
车间工艺设计
学生姓名: 钟志乾
学生学号: 11303123 院(系): 资源与环境工程学院
年级专业: 级冶金工程
指导教师: 丁满堂副教授
助理指导教师:
二〇一六年五月
摘要
本设计的主要任务是设计一个铁水装入量150吨的转炉提钒车间工艺设计,重点介绍了顶底复吹工艺部分。
该设计介绍了一系列的提钒工艺。
从物料平衡与热平衡计算开始进行初期参数的确定,设计内容主要包括:转炉炉型选择、供氧压力、供氧时间、底气选择、转炉底吹元件选择与布置、复吹工艺设计,其中复吹工艺设计是本设计的核心。
该设计由一座顶底复吹转炉采用”一吹一”模式提钒,转炉公称容量均为150t,底吹元件采用细钢管多孔型供气元件,选取6支0.61D的供气元件,底枪布置采用沿耳轴连接线30°,90°150°,210°270°,330°分布。
复吹模式采用顶吹氧气底吹氮气,顶吹氧气强度为3.11m3/t·min,吹氧时间7min,每炉含钒水供氧量为540.553m3/min。
底吹供气强度为0.03·0.08Nm3/t•min。
平均吹炼时间为25min,转炉提钒冶炼一炉钒渣主要原料用量:含钒铁水装入量135t、含钒生铁块15t、石英砂1.8t、半钢温度为1390℃。
`
关键词:顶底复吹转炉,提钒方法,含钒铁水,转炉提钒
ABSTRACT
The main task of this design is to design a furnace with 150 tons of molten iron. This design introduces a series of vanadium extraction process. From material balance and heat balance calculation to determine the early parameters, design content mainly include: selection of converter furnace type choosing, oxygen pressure, oxygen supply time, emboldened, converter bottom blowing component selection and layout, combined blowing process design, which combined blown process design is the core of this design.
The design by a top bottom combined blown converter vanadium using "blows" mode, the converter nominal capacity were 150t, bottom blowing elements by thin steel tube type porous gas components, select 6 0.61D gas components,bottom lance arrangement by along the ear axis connecting line to 30°, 90° and 150°, 210°and 270°, 330°distribution. Combined blowing pattern the top blown oxygen bottom blowing nitrogen, strength of top blown oxygen 3.11m3/t - min, oxygen blowing time of 7min, each furnace containing vanadium oxygen supply water quantity
for 540.553m3/min. The bottom blowing gas supply intensity is 0.03~0.08Nm3/t / min. Average blowing time is 28min, converter provided the amount of vanadium smelting furnace vanadium slag as the main raw material: hot metal charging amount 135t, containing vanadium iron 15t, quartz sand 1.8T, semi steel temperature 1390 ℃.
Key words: top bottom combined blowing converter, vanadium extraction method, vanadium containing molten iron, converter vanadium extraction。