电梯安装说明翻译件
电梯专业词汇英文翻译汇总

电梯专业词汇的英语翻译hacksaw 锯子hair line 发纹hair-line finish 发纹处理hairline finished stainless steel 发纹处理不锈钢half wrap 半绕halfway junction box 中间接线盒hall门厅,候梯厅hall buttons召唤盒,呼梯按钮hall call厅门呼梯hall call button厅门呼梯按钮hall call cancel厅门呼梯取消hall door层门,厅门hall fixtures门厅讯号装置hall landing门厅停站hall lantern厅外指示灯hall position indicator 层门指示灯hall station门厅讯号装置hall stop门厅呼梯停车hall wait passenger seconds 门厅候梯时间hall waiting time门厅候梯时间hall way门厅通道hammer锤子hand drill手电钻hand hammer 手锤hand lamp手提灯hand operated手动操作hand operated door 手动门hand powered lift手动提升机hand pump手压泵hand reset手动复位hand rope 绳hands-on experence 实地经验handwheel手动盘车装置,盘车手轮handwinding device盘车手轮,手动盘hanger悬吊器,吊门滑轮盒hanger plate 吊门板hanger rail吊门轨道hanger roller吊门滚轮hanger sheave 吊门轮hanger track 吊门轨道hanger trough吊门槽板hard disc 硬盘hard wire硬电线harden quench 硬淬hard—hat安全帽hardware (计算机)硬件,(机械)标准件,五金件harm损伤harmonic distortion 谐波失真harmonics 谐波harness 把,束hatch围井(船用电梯井道)出口hatchway 井道hatchway enclosure 井道围封hatchway type elevator 井道式电梯hauling hope 曳弓|绳haunched beam井道内牛腿,加腋梁hazard危险HCR (highest call reversal)顶层呼梯反向head jamb 上门套,顶门套head room顶房,顶部空间head room height 顶层高度head trim 上门套,顶门套header上门坎,门顶部header case 门顶箱header cover 门顶罩header track门上坎轨道,门顶部轨道headquarters 总部headroom height 顶层高度heat absorption 热量吸收heat accumulation 热量积聚heat dissipation 热量消耗heat emission热量散发heat output热量输出heat transfer传感器,热传导heat treatment 热处理heater发热器heating device 取暖器heatsink散热片heavy demand floor 繁忙楼层heavy demand floor call 繁忙楼层呼梯heavy demand floor control 繁忙楼层控制heavy duty dloor 繁忙楼层heavy duty dloor call繁忙楼层呼梯heavy duty dloor control 繁忙楼层控制heavy duty traffic 繁忙交通heavy duty zone 繁忙区域heavy traffic繁忙交通heavy-duty大载重,交通繁忙height above the hightest level 顶层高度helical螺旋的helical gear斜齿轮的,斜齿轮传动的,螺旋齿轮helical gear machine 斜齿轮曳弓|机helical gear reducer 斜齿轮减速器helical machin斜齿轮曳弓机helical speed reduction gear 斜齿轮减速机helical spring 螺旋弹簧helper助手,帮工hemp core 麻芯hemp rope 麻绳hemp rope core 大麻绳芯hermetically sealed 气封的Hertz (Hz)赫兹(频率单位,周/秒)hex head bolt (HHB) 六角螺栓hex screw六角螺钉hexagon head 六角头hexagonal screw 六角螺钉high efficiency 高效率的high frequency chopping 高频斩波high gain高增益high grade高级的high pressure rubber hose 高压胶皮管high pressure rubber hydraulic hose 高压橡胶液压管high rise building 高层建筑high rise elevator 高层电梯high rise escalator大高度自动扶梯high rise lift高层电梯high rise zone 高层区high signal-noise ratio 高信号噪声比high speed escalator高速自动扶梯high speed steel 高速钢high speed winding 高速绕组high tension 高张力high tension bolt耐拉螺栓,强力螺栓high tension supply 高电压higher harmonics 高次谐波highest call reversal (HCR)顶层呼梯反向highest reversal floor 最高反向楼层highlighting bar (计算机)强光线条,重点线条high-speed slevator/lift 高速电梯hight高度hilti bolt膨胀螺栓hinge铰链hinge door铰链门,外敞门hinge plate 铰链板hinged platform sill轿箱铰接式地坎hitch plate钢丝绳绳头夹板hitch rod绳头杆hob滚刀hobbing滚铳齿hobbing machine 滚齿机hohder固定架hoist起重器hoist machine提升机,曳引机hoist ropes 曳弓|绳hoist ropes ratio of lift电梯曳引绳曳引比hoisting cable 曳引绳hoisting machine提升机,曳弓|机hoisting motor曳引电动机hoisting rope 曳引绳hoistway 井道hoistway access switch 井道通道开关hoistway door 厅门hoistway door catch门厅挈,厅门捕捉器hoistway door electric contact 井道门触点hoistway door interlock 厅门联锁装置hoistway door lock device 厅门门锁装置hoistway door mechanical lock 厅门机械锁hoistway enclosure 井道围封hoistway equipment 井道设备hoistway rope 起重绳hoistway sill aprope 厅门地坎裙板hoistway sill guard厅门地坎护板hoistway telltale井道内信号灯hoistway wall井道壁,井道墙hoistway wiring harness 井道内把线holding time保持时间hole 孔hole base system 基孔制hole countersunk 沉孔holeless无孔的,无孔式hollow guide rail 空心导轨hollow rivet空心铆钉home car驻停轿箱,停在基站的轿箱home elevator/lift 家用电梯home floor驻停楼层,基站home landing 基站hood挡板hook钩,圈horizontal 水平horizontal axis 水平轴horizontal elevator 水平电梯horizontal projection 水平投影horizontal seismic force 水平地震力horizontal shaft governor 横轴式限速器horizontal transportation 水平运输horizontally sliding door 水平滑动门horizontally step run梯级水平移动距离hose软管hose connector软管连接器hose coupling软管接头hose fitting软管接头hose proof软管套hospital elevator 病床梯host主机,宿主hostile environments 有害环境hotel旅馆hourly rate小时定额housing 套hub轮毂,中心hudraulic lift 液压电梯hum嗡嗡声human interface 人机界面human safety人身安全humidity 湿度hung door悬吊门hydrant消防栓,消防龙头hydraulic液压的hydraulic buffer油压缓冲器,耗能型缓冲器hydraulic drive 液压驱动hydraulic driving machine 液压驱动机hydraulic equipment液压梯,液压设备hydraulic fluid液压用液体hydraulic hose 液压软管hydraulic installation 液压设备hydraulic jack液压千斤顶hydraulic lift nominal speed of up (down)motion 液压梯上(下)行额定速度hydraulic lift of directly-pushed 直顶式液压梯hydraulic lift of double 倍率液压梯hydraulic oil 液压油hydraulic parts 液压件hydraulic piping 液压配管hydraulic power unit 液压泵站hydraulic pump 液压泵hydraulic relevelling device 液压再平层装置hydraulic valve 液压阀I-bar工字钢I-beam工字梁idea想法,概念,意见ideal理想的identical相同的identification 鉴定,鉴别identification tag 标签idler pulley空转轮,惰轮idler sheave 惰轮IGBT (isolated grid binary transistor)隔离双栅极晶体管ignition voltage 点火电压illuminate透明,透光illuminated button 发光按钮illumination 照明illustrated sheet 图解说明iluminate ceiling 透光吊顶immunity抗干扰度impact冲击impact load冲击载荷impact loading to pit floor底坑地面冲击载荷impedance 阻抗imperfection不完整性,缺陷imperforate无孔洞的imperial system 英制impregnation 注入,饱和impulse generator 脉冲发生器impulse processing 脉冲处理in car inspection 轿内检修in service服务中,运行中in use在使用中inaccessible 准入内inadvertent operation 粗心大意操作incandescent lamp 白炽弧光灯incandescent tube 白炽灯管inch英寸inching 点数inching button 点动按钮inching feature 点动,微动inching switch 点动开关incident 事件inclination 倾斜度incline 斜面incline section 倾斜部分inclined elevator 倾斜式电梯inclined lift倾斜式电梯inclined wheel chair lift 倾斜式轮椅电梯incombustible非易燃的,不燃的ncoming panel 受电盘ncoming traffic进入交通,来到交通ncrease 增力口ncrement disk 增加盘ncrement pulse generator增量盘脉冲发生器ndependent operation 独立操作ndependent service 独立服务ndicatiing lamp 指示灯ndicating arrow 指示箭头ndicating circuit 指示电路ndicating electrical instrument 指示型电气仪表ndication contral 显示控制ndicator指示器ndicator device 指示装置ndicator face plate 指示器(灯)面板ndicator for stop 层站指示器ndicator lamp 指示灯ndicator machine 指示器(灯)机械ndirect间接的ndirect acting hyfraulic lift 间接式液压梯ndirect back plunger 柱塞后置式ndirect side plunger 柱塞侧置式ndirectly heated cathod 旁热式阴极ndirect-plunger hydraulic elevator 间接柱塞式液压梯nduced感应的nductance 电感nduction asynchtonous motor 感应异步电动机nduction furnace 感应电炉nduction motor感应电动机nductor 电感nductor plate感应器板nductor replay感应继电器ndustrial building 工业建筑物ndustrial plant 工业工厂ndustrial television 工业电视机ndustry 工业ner ledge内凹缘(壁架)nertia转动惯量nfermation 信息nformation apparatus信息器件,信息装置nformation transmitter 信息传送器nfra-red multi-beam screen detector 红外线光幕检查器,电眼nfrared ray 红外线n-ground掩埋式initial excitation timer 额外励磁时间initial failure 初期故障initial position 起始位置initial setting 初期设定initialization初始化(计算机)预置initialization travel 起始运行inlet入口,吸收inlet guard 入口护板inlet of handrail 扶手带入口inlet switch扶手带入口开关inner deck内侧盖板inoperative不运行,不工作inoperative position 不工作位置i叩ut输入input signal输入信号inrush current冲击电流,启动电流insert插件,井道预埋件insert nut嵌入螺母inserting mortar 添缝insopection traveling speed 检修运行速度inspection检查,检修inspection button 检修按钮inspection control 检修控制inspection control device 检修控制装置inspection device on top of the car 轿箱检修装置inspection door 检修门inspection operation 检修操作inspection speed 检修速度inspection switch 检修开关inspection trap检修用活板门inspection travel 检修运行inspector检测人员,验收机构inspector knife switch 检修闸刀开关installation 安装installation documents 安装文件installation drawing 安装图纸installation instructions 安装说明书installation manager 安装经理installation period 安装周期installation personnel 安装人员installation superintendent 安装总监installer安装工instantaneous瞬时的,瞬息的instantaneous safety 瞬时式安全钳instantaneous safety gear瞬时式安全钳装置instantaneously type safety gear 瞬时式安全钳institute building公共事业机构性建筑instructed person受过训练的人员instruction指示,指令instruction drawing 要领图instruction ROM指令寄存器instruction system 指令系统instruction user经训练的使用者instrument仪器,仪表insulating coupling 绝缘接头insulating material 绝缘材料insulating resistance 绝缘电阻insulating sleeve 绝缘套管insulating strength 绝缘强度insulating tape 绝缘带insulation 绝缘insulation class 绝缘等级insulation rubber防震橡胶,绝缘橡胶insulation test 绝缘试验insulator绝缘子,电瓷integrate积分,整化,结合integrated circuit 集成电路integrating electronic element 集成电子元件integrating error 累计误差intense traffic密集交通,繁重交通intense up peak 上行密集交通intensive duty traffic密集客流,繁重交通intensive traddic 稠密交通intercom device 对讲装置interconnect elevator 并联梯interface 接口,界面interference 干扰interference suppression 消除干扰interfloor balance traffic 楼层间平衡交通interfloor distance 层间距离interfloor flight time 层间运行时间interfloor height 层间高度interfloor jump time 层间跨越时间interfloor passenger arrival-rate 层间乘客至胜占率interfloor passenger traffic 层间客流交通interfloor traffic层间交通,中间楼层交通interfloor traffic mode中间楼层交通模式interim payment 分期付款nterior 内部nterior circuit 内绕圈nterior decoration 内部装潢nterior panel 内侧板nterior paneling护壁板,护栏板nterior profile 内侧盖板nterlock门联锁nterlock circuit 互锁电路nterlock switch 联锁开关nterlocking contact 联锁触点nterlocking device 联锁装置nterlocking element 联锁元件nterlocking motor 联锁电动机ntermediate floor 中间楼层ntermediate landing 中间层站ntermediate machine room 中间机房ntermediate speed 中间速度ntermediate stop中间停车,中间停站ntermediate support中心支撑,中间支撑,第三支撑ntermediate support beam 中间支撑架ntermediate tie-bracket 中间束架ntermittent间歇的,周期性的ntermittent problem间歇性的问题,时有时无的问题ntermittent service 间隙运行nternal fault内部故障nternal gear 内齿轮nternal resistance 内阻nternal soore apparaus 内部存储器nternal stress 内应力nternal traffic 内部交通nternational safety standard 国际安全标准nterphone对讲机nterpole中间极nterpole coil附加磁极线圈nterpole winding换向极绕组nterruption control 中断控制nterstice 间隙nterval 间隔ntroductory message 弓I导信息nventory 库存nventory verification 库存盘点nverse current 反向电流nverse proportion 成反比例nverse ratio 反比inverter逆变器,变频器inverter control逆变器控制inverter panel 逆变器盘investigation 调查研究invoice 发票invoicing 结账involuntary operation 偶然性操作involute tooth 渐开线齿iope slippage绳滑移,绳打滑IPM (incidental phase modulation)偶发的相位控制IPM (intelligent power module)智能化电力模块,智能功率元件iron ore 铁矿iron vronze 铁青铜irregular不规则的irregularity 不匀度irreversibility 不可逆性irreversible不可逆的I-section工字钢截面I-shape工字形ISO国际化标准组织isolate 分离isolation 隔离isolation pad 隔离垫isolation rubber 隔震橡胶item项目。
家用曳引电梯安装说明书
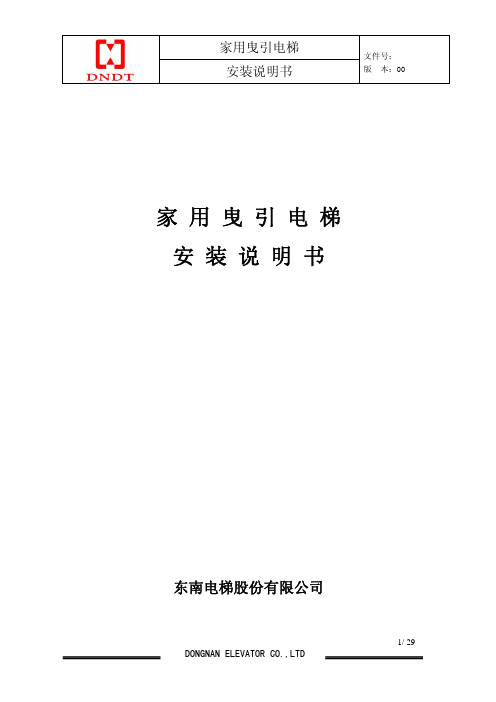
家 用 曳 引 电 梯 安 装 说 明 书东南电梯股份有限公司1.1 安全说明请遵守以下安全规则:•电梯各有关区域应保持清洁维护好(必要时更换)工地的安全设备•工作地点应有足够照明•穿戴必要的保护服装和装备:工作帽,安全鞋,手套,安全带,护耳等•始终使用安全带•工具始终保持良好的使用状态•注意设备和工具的装配说明•避免危险情况•确保机房门(如果有的话)上锁•对井道门口需设警告标记和相应的保护措施穿戴防护用品,例如:安全帽 护目镜 安全手套 安全鞋 安全带1.2 现场材料的存放和搬运1.2.1 存放当电梯设备必须存放在现场时,必须把货箱堆放在清洁、干燥和有遮棚的地方。
应注意箱子堆放处周围应无易燃物,不得进行气割类或其他易燃性工作。
所有货箱应整齐堆放在厚木板上,保证若突发流水时货箱不会受潮。
工地主管应保证下水道畅通无阻,并在设备存放期间始终保持清洁。
货箱不得堆放在交通繁忙地段,应防止坠落的碎石。
所有货箱应用帆布或塑料布复盖,并用绳子扎牢以防被风吹掉。
施工方应安排安保值班,保证复盖物,货箱及所装货物不遭盗窃或破坏。
货箱不应堆放得太高,除非迫不得已,重箱子不应放在轻箱子的上面。
导轨上不得放置任何东西。
货箱存放的位置必须有计划。
箱子应按设备安装需要的顺序摆放。
同一台梯的设备应放在一起,不要与别的电梯混放。
工地主管必须保证货箱不因其他工地需要某件东西打开后,而不关上。
向工地所借部件不管多小必须签字。
所需部件的定单或投拆文件必须复印并保存在文件夹中。
部件的发货必须与安装计划相一致。
电梯设备决不可存放在露天!若发生这种情况,迅达公司不承担提供的保质期和材料保证,由买主自己负责,因此工地主管的责任是保证不发生此种情况。
对于不在现场存放的电梯材料,存放要求同上。
1.2.2 搬运在现场搬运电梯设备时必须特别小心,确保不损坏设备。
搬运电梯材料时,特别是导轨,不得使用机械拖拉的方法。
搬运笨重部件必须使用合适的机械设备。
电梯专业英语-安装与维保ppt课件

2 Safety During Installation 装梯平安
Look closely at the chain and lower hook. The lower hook is the weakest part of the hoist.
近间隔 观察链条和底部的挂钩。底部的挂钩是整个手 拉葫芦的最薄弱部分。
New word 〔新单词〕
travel fire extinguisher lifeline paramount fatigue key ring inhibit
行程 灭火器 救生索 最重要的 疲劳 钥匙圈 抑制
Elevator Installation 电梯安装
• Before installing an elevator,应该做哪 些准备工作?
2 Safety During Installation 装梯平安
Place a sticker in the controller near the inspection switch that reads as follows: "GATE OR SAFETY CIRCUITS SHALL NEVER BE JUMPED OUT."
一旦电梯投入使用,必须定期维护以保持其在平安 工作状态。
Question & Answer 〔问答〕
Question & Answer 〔问答〕
A. Safety is supervisor’s responsibility. B. We can replace or lengthen the hoist chain by ourselves. C. Which part is the weakest part of the hoist? D. Elevator platform can be accessible to the public. E. Always wear __ when handling wire rope. F. Compare components in shipment against __. G. What should be verified before commencing installation? H. At the jobsite, quality is more important than safety. I. Glasses with __ can be worn when working on live circuit.
电梯安装说明书

电梯安装说明书尊敬的用户您好,非常感谢您选择使用我们的电梯产品。
为了确保电梯安装过程顺利进行,并使您的使用体验更加安全与舒适,我们特别编写了本电梯安装说明书。
在阅读本说明书之前,请您务必确保已经阅读并理解了电梯技术规范以及相关安全法规。
一、施工准备1. 基础准备:在进行电梯安装前,要确保电梯井道基础施工已完成,并符合相关规范要求。
同时要确保井道顶部、底部和周围空间的平整度和净高度均符合设计要求。
2. 电力准备:接入电源应符合当地电力公司要求,并且确保供电线路稳定可靠,电源标有正确的电压和电流标识。
在施工现场应配备专人进行电力接线工作。
二、电梯安装1. 安装前准备:在进行电梯安装前,要仔细检查各个部件是否完好,特别是安全装置是否齐全可靠。
还要确保安装人员已经接受过正规培训,并持有相应的操作证书。
2. 吊装电梯:在将电梯吊装至井道前,请确保起重设备符合安全要求,并按照提供的吊装方案进行操作。
吊装过程中,要确保电梯机房、井道壁、顶棚等部位不受损坏。
3. 安装电气系统:安装电梯电气系统时,请严格按照电气布线图和接线图进行操作,并确保所有接线牢固可靠。
电梯的电气系统应与建筑物的电气系统有效隔离,以防止相互干扰和故障。
4. 安装井道设备:在进行井道设备安装时,请按照电梯设计图纸和相关标准规范进行操作,特别是对于导轨、轿厢、平衡重块等部件的安装要严格按照要求进行。
三、验收与调试1. 安全检查:在电梯安装完成后,必须进行严格的安全检查。
包括轿厢门、门锁、光幕、安全钳、上、下限位开关等各个安全装置的功能是否正常可靠。
2. 调试与测试:对于安全装置正常的电梯,可以进行调试和测试。
调试过程中,需确保各项功能正常,并根据所提供的测试方法进行验证。
四、培训与维护1. 培训操作人员:在电梯安装调试完成之后,需要对维护人员及操作人员进行培训,使其熟悉电梯的操作方法,了解各项安全规范,以保证日后的运行安全。
2. 定期维护:为确保电梯的正常运行和安全性,我们建议定期进行电梯的维护保养工作。
Installation instruction for traction elevator(绳梯安装说明英文版)

Contents Page1. Preparations before installation 22. Procedure of installation 43. Work in the shaft in earlier stage 64. Install guide rails 75. Install machine room equipment 96. Install landing door system 127. Install car frame and car system 168. Deformity COP field installation sketch drawing 229. Install car door 2310. Install counterweight frame 2811. Install wire ropes 2912. Install compensating chain and shaft attachments 3213. Shaft connection sketch drawing of elevator 3814. Lubrication instruction 3915. MS2-C Installation instruction 4116. MS3-C Installation instruction 4717. Alarm system of Elevator 511. Preparations before installation1.1 GeneralThe installation work has a close relationship with the customer. In order to perform the installation work smoothly and with high efficiency, the erectors shall keep a nice contact with the customer. They shall do their best to get the help from the customer.Before starting the installation work, the program of installation work shall be agreed by the customer. The exact opening date shall be decided by Thyssen Aufzuge. The installation work shall be performed on schedule as soon as all the required site conditions are ready.1.2 Safety precautions in the work1.2.1 Check before daily workEvery day before starting work, must check the following items for safety:a) Safety protection facilities (scaffolding, safety nets, hoisting hooks, etc.)b) Mechanical, electric devices (welding machines, hoisting tackles, etc.)c) Auxiliary tools (oxygen and acetylene cylinders, etc.)d) Safety features (safety belts, safety helmets, etc.)e) Other operating facilities.1.2.2 Surrounding of workingThe installation working space must keep clean and tidy, so as to prevent from being stumbled. Take care of the risk of fire.1.2.3 Safety precautions for working in the shaftIn doing the erecting, removing or modifying the scaffolding, the competent person with licence for lift installation must be present. The appropriate working clothing must be worn, such as working dresses, safety helmet, safety belt, etc. in doing the erecting work.Avoid the works in shaft on different floors with each other at the same time.1.2.4 Protection at the openings of the shaft.The shaft openings shall be enclosed to prevent from falling in. Set shields or worning boards at the openings to mind people that there is the danger of falling into the shaft. 1.2.5 Fire preventionWhenever using hand cutter, welding machine or gas cutting tool, mind to prevent from fire. Put the inflammable materials to a safe place.1.2.6 Handling of the gas cylinder and oil containerDangerous gas like oxygen and acetylene must be handled by competent person.Whenever using the oil container, ensure to keep it perpendicular to the ground. Gas cylincers and oil containers should be stored in a well ventilated place, kept away from high temperature, not exposed to the sunshine for a long time.1.2.7 Safety protectionGoggles must be worn whenever do the welding, gas cutting or drilling work. Welding machine must be ensured to be faultfree before working. Live line and earth line must be both connected for safety.1.2.8 Trial run operationUnauthorized persons are prohibited to enter the machine room and shaft.Acknowledge before operating that all the safety circuits work properly. Any work on electric device shall only be performed in power off condition. Switching off the main switch must be performed by competent person. During switching off time, a warning notice must be put on the main switch to mind people do not turn on this switch.1.2.9 Safety inspectionEvery day when finish the work, check if the electric switches and the gas valves are closed, if fire-protection devices are in proper position and if any unsafe condition exists. Any abnormal condition must be eliminated immediately.1.3 Preparations at site1.3.1 Negotiation with the customerAfter entering the site the erectors shall observe the respective regulations of the customer, and negotiate with the customer about the stipulations regarding the installation work, such as the safety notice, etc.1.3.2 Re-check the shaftCheck the dimensions of the shaft and machine room, if these dimensions are coincide with the shaft arrangement drawing which has already been confirmed by customer.Check the lift pit for watertight. Check if the temporary power supply is proper.1.3.3 Material storageCheck the store area for adequate size and safety.1.3.4 Confirm the installation programDiscuss and confirm the installation program with the customer after complete the preparation work.It is very important to set up a procedure of installation to perform the installation work on schedule and with high efficiency. Many problems like the building work progress; materials supplying, etc. must be negotiated and settled with the relative department in the planning stage.3. Work in the shaft in earlier stage3.1 ScaffoldingThe vertical arrangement of scaffolding shall be selected properly. It must not disturb the erection of guide rails and the sills.3.2 Templates and plumb wiresMounting of the templates is for fixing the plumbing wires. According to shaft arrange-ment drawing, the plumbing wires shall act as the reference lines for installing the lift components in shaft. So the correct mounting and positioning of the templates is the key point for the whole lift erection.The templates are divided in top template and bottom template. The top template is mounted at 1 m below the ceiling in the shaft, the bottom template is mounted at 1 m above the pit floor.Plumbing in shaft is a reference for checking the adequate space for the trace of car running along the full travelling height. It is also a reference for deciding the mounting positions of guide rails and landing door equipment.CW G (轿厢导轨距)W G (对重导轨距)A S L (对重导轨中心与轿厢导轨中心距)厅门地坎与轿厢导轨中心距开门宽C/W rail gaugeCar rail gaugedoor widthD i s t a n c e b e t w e e n c a r c e n t e r a n d C /W c e n t e rD i s t a n c e b e t w e e n c a r c e n t e r a n d l a n d i n g s i l l The dimensions indicated in the drawing shown above are these which have to be measured carefully. These dimensions must be observed in making the templates.The positions of all the other components of the lift can be determined as soon as the center line of the guide rails (car rails) to be fixed.4. Install guide railsThe installation of guide rails is a major item, and generally speaking it will exist throughout the lifespan of a building. The installation of guide rails is a very important factor for the running characteristic of the lift. Since any improper installation of the guide rails shall lead to the vibration and noise.4.1 Type model of railRail for car T90/B; T125/B; T127/B; T89/BRail for counterweight T50/A; T70-1/A; T75-3/B; TK5Abracketsrail4.2 MountMark out the fixing holes on the shaft wall according to the shaft arrangement drawing and fix the hole centers, adjust the horizontality. Adjust the mounting position of the rail4.3 Install guide railsAt first, Clean the processed surfaces of every rail and fish-plate with kerosene. Check the tenon and mortise end of every rail. file the burr, if any.Fix the bottom rail on the floor pan, as shown in the figure above. Ensure the floor pan to be levelled and the guiding face of the rail to be vertical to the pan. Then fix the rails one by one on the rail brackets, and adjust the verticality of the rails by rail brackets.The ensured verticality of the guide rails is one of the important factors of the quality of lift installation. The distance between top end of the rail and shaft ceiling is allowed to 150 mm.4.4 Guide rails adjustmentLet the rail brackets to be semi-tightened when adjusting the guide rails. Adjust the guide rails by plumb wires and rail gauge. After acknowledgement of the verticality of guide rails, tighten the bolts on rail clips.5. Install machine room equipmentThe machine room equipment is the important control part of the lift. And the running characteristic of the lift mostly depends on the quality of lift installation. So that, the excellent operation of the lift can only be ensured by the high quality installation. For this purpose, the traction machine and electric devices shall be handled carefully, and must be performed strictly according to the operating procedures of safety. The equipments shall be strictly protected against dust and moisture. For moving parts exposed to the weather, special care must be taken.5.1 Center line mark in machine roomIn machine room, the marked lines shall be:a) Center line of traction sheave;b) Center line of car;c) Center line of counterweight.5.2 Install the traction machine5.2.1 Install the I-beam frame for traction machineT he I-beam frame shall be supplied by customer. It must be supported by load-bearing concrete beam or load-bearing wall. The length of supporting end of the frame must not5.2.2 The adjustment of I-beam frame for traction machineAfter mounting, The I-beam frame shall be levelled, so as to properly install themachine frame.Position the damping rubber pieces on the I-beam frame according to the machineroom arrangement drawing. Mount the machine frame and traction machine ondamping rubbers. Adjust the position and levelness then tighten the components.Ensure that the axial deviation between traction sheave and deflection sheave shall not exceed 0.5 mm.Warning: Must add oil in the top oil box before the mainframe’s running,otherwise the mainframe is be attainted easily. Open the cover and inject about0.2L gear oil into the left-right oil box, and then tight the cover before running.Attention: The time of the crawl running of the mainframe must be less than 40seconds, this request specially for low-speed change-pole motor, if runningunder the shortage of lubricant, the turbine、the worm bearings and the axes will be attainted easily5.3 Install control cabinetPosition the control cabinet according to the machine room arrangement drawing.Mount the cabinet with 4 x M8 bolts and 4 pieces of plastic anchor nuts inside the floor.5.4 Install the speed governorMount the speed governor with 2 x M8 bolts and 2 pieces of plastic anchor nuts inside the floor. Position the governor according to the machine room arrangement drawing.The governor and its basement are factory-assembled. The position deviation in both direction shall not exceed 1.5 mm. For installation, lay down a plumb line from the rope groove of governor wheel through the floor to the rope groove of pit tensioning wheel via the center point of governor rope fastener on car top. Then fix the speed governor.The speed governor has been factory-tested and sealed, so as to prevent it from malfunction. Dismantling the speed governor is strictly forbidden during installation.The speed governor is an important safety component of the lift. The governor ropeshall be securely clamped. The governor shall respond sensitively. In case thegovernor rope to be elongated or even broken, turn off the power switch of the controlcircuit to stop the lift immediately.6. Install the Landing Door SystemThe installation position of landing door system is according to the installation dimension that was supplied by GAD and the position of plumb line.6.1 Install Landing Door SillThe center position of sill was decided according to hanger line of sample frame, fix the sill supported angle on the shaft well with M16 expansion bolt, and fix the sill support, sill and toe plate on the sill supported angle. Pay attention to according to thedimension of GAD during the installation, ensure the top floor of sill and the floor at the same level. Adjust the sill level, and ensure the landing door sill to keep parallel to the car door sill, the clearance of them is 30mm, then after adjustment, tighten the all connection part of sill.6.2 Install Landing Door Standing Pole and Door Suspension GearAfter adjust the sill, fix the landing door standing pole on the sill support, install the landing door suspension gear on the top of landing door standing pole, then they were fixed with the two thread plate, 8 M8X25 bolts and lock gasket that supplied by the landing door installation accessory.Connect and fix the mounting angle and landing door suspension gear with M12X25 bolt that from landing door suspension gear, fix the mounting angle on the shaft well with M16 expansion bolt, ensure the landing door suspension gear keep parallel to the sill. Fix the bracket that was connected with landing door standing pole on the shaft well with M12 expansion bolt, the bracket need bent according to the shaft at building site, ensure the landing door standing pole keep plumb to the landing door sill and suspension gear during the installation, then adjust the landing door dimension according to the GAD.At that time the key point of installation quality is the level and straight of adjustment of door guide in landing door part, and ensure the door guide keep parallel to the door sill is the key point of landing door running well or not, so the adjustment must be precision. The uprightness of door standing pole will affect the level of door head, during the adjustment, pay attention to the max uprightness error of the door standing pole not exceed 1.0mm.Landing door standing pole Landing door suspension gearStanding poleSill supportWhen all parts of landing door system are tighten, pay attention to the tighten workmust made after the finishing of technical parameter adjustment of all parts of landing door.6.3Install Landing Door PanelErect the door panel before the door panel installation, put the door guide shoe into the sill trouth, push the door hang plate of landing door suspension gear to the relevantposition, then fix the landing door panel on the door hang plate with the adjusting part, adjusting washer, M10X20 bolt and gasket that were supplied by landing doorinstallation accessory.The quantity of adjusting washer can change the clearance of door panel and standing pole. The position of adjusting part can change the distance of door panel and sill; The position of adjusting guide shoe can change the clearance and uprightness of doorpanel and door standing pole.Adjust the parameter of landing door, let the clearance of door panel and door standing pole, the both of door panels is 3-6mm, keep the door panel plumb, door guide shoeand sill should work in well and glide normal.After the finishing of landing door installation, when push or pull the landing doorwithout noise、concussion or jumpiness phenomena, the closing is well.6.4Install the Open-lock Stopper (option)When the elevator is with car door lock, it need to install open-lock stopper on everyfloor landing door, fix the open-lock stopper on the landing door suspension gear with bolt part(drawing as follows): pay attention to the open-lock stopper work in well withthe idler wheel of care door lock of car door suspension gear.7.Install car frame and car systemMostly the assembly work of the car is performed at top floor level in shaft. Since thetop floor is closely near the machine room, so that it is convenient to do the hoistingwork and check the dimensions. When the car is assembled at the top floor level, twopieces of square timber are needed and fixed. These two pieces of timber shall bearthe total weight of the car. Hang a hand tackle on the hook on top crossbeam ofmachine room, drop down the tackle chain or rope through the machine room flooropening (coincide with the car center) for hoisting the car frame.7.1 Install car frame7.1.1 Bottom crossbeam of car framePut the bottom crossbeam on the square timber and and adjust for its horizontality. The horizontal error shall not exceed 0.1%. Mount the bottom guide shoes. Adjust the gaps between the convex surface of rail and concave surface of guide shoe, and make the gaps at upper end and lower end to be equal.Erect the two uprights at both side of car frame and connect them with the gusset plates on bottom crossbeam by bolts. Adjust the uprights. The vertical error along the total height of upright shall not exceed 1.5 mm.7.1.3Top crossbeam of car frameHoist the top crossbeam by hand tackle. Mount the top crossbeam with uprights via the gusset plates by bolts. Adjust the horizontal error of the top crossbeam and make it for torsion-free.Some components like safety gear linkage etc. have been factory-mounted on topcrossbeam. Do not dismantle them at will during installation.Mount the top guide shoes. Adjust the gaps between the convex surface of rail andconcave surface of guide shoe, and make the gaps at upper end and lower end to beequal.7.1.4 Safety gearA ll the adjustable parts of the safety gear have been sealed. Do not dismantle them atwill. Mount the safety gears. Adjust the wedge position to make the gap between wedge face and side face of rail to be even. In case of safety gear activating, the safety switch set on lifting rod must be activated before the safety gear activation and stop the motor.Using the electrically, hydraulically or pneumatically operated safety gear is strictly prohibited.Governor rope end, the tangential lines of governor wheel and pit tensioning wheelmust be on a same straight line. The safety gear must be movable nimbly and securely.The locale adjustment method of up safety gear in double direction safety gear carframe(please see the drawing as upwards):a、Take out the moving bolt and connecting pin axis of the safety gear drag link.b、A djust the height of the moving bolt, let the bottom of safety gear drag link beclinged with the top of crank, keep the safety gear vertical by the support of crank,avoid the up safety gear loose during the elevators’ running.c、Install the moving bolt and the connecting pin axis of the safety gear drag link well.7.2Install the car7.2.1 Install car platformConnect the platform assembly to bottom crossbeam with damper units. Adjust thelevelness of platform with shims. The levelness error shall not exceed 1.5/1000.Attention: The protective pressboard set on the car platform before delivery must be kept on until the whole facility to be handed-over to customer.7.2.2 Install car enclosure wallA fter finish the platform installation, firstly put in the rear enclosure walls. loosely connect them with platform by bolts. Mount the left-hand piece and right-hand piece of the rear enclosure walls as per the same way.Put the joint strip between the adjacent encloswure walls. Use bolts to connect the adjacent walls securely. The rear enclosure wall(s) must joint with left-hand and right-hand walls. Mount the left-hand and right-hand walls as per the same way. Distribute the possible deviation evenly to the left and right side of the car entrance.Then, put the car roof onto the enclosure walls. connect them loosely with bolts. Fix the kick plates with exclusive bolts. Finally, tighten all the bolts securely.7.2.3 Install the car operating panel (COP) and front enclosure wallThe COP is divided in side mounting and front mounting types. With all exertions, mount the COP in the meantime with the mounting of enclosure walls, i.e. mount the COP and front enclosure wall just after finish the car roof mounting. Use the exclusive clips to connect the COP with front wall, as shown below.7.2.4 Connect car roof to uprights of safety-gear frameConnect the car roof to uprights of safety-gear frame with connecting angles and damper units. An emergency guide plate is attached to every damper unit to preventthe car from tilting in case of damper failure. There are gaps of 5 mm. between bothside of emergency guide plates and uprights.7.2.5Install safety railings on car roofThe safety railings are fixed on top crossbeam of safety-gear frame. The railings are composed of two angle irons with punched triangular notches. The erector is requested to bend at site the angle irons at the notches into right angle. In case of car with front and rear doors, cut the angle irons at the notches, and file the end smooth.Fix the bended (and cut, if so) angle irons onto top crossbeam with brackets. Connect the overlapped length by bolts. Hang the guard plates onto the angle irons and fix them by bolts. Different guard plates shall be supplied according to the car depth. No guard plate shall be fixed above the COP and car entrance. The same applies to narrow distance between car and shaft wall (less than 150 mm).On the angle iron in the area above COP, drill holes for hanging the inspection box.7.2.6Install car attachmentsInstall car lighting (wiring it before).Install the special features specified in the contract, such as handrail, mirror, decorative boards, etc.The mounting of handrails must observe the contract stipulation. The erector shall mount the upper edge of handrails at the level of 900 mm above the car floor.For mounting the handrail, mirror or decorative boards, the erector shall drill holes in the individual positions at site. Pay attention that the mounting holes must not be positioned in the area of uprights.7.2.7Install the load weighing sensorThe mounting styles of weighing sensor have a little bit difference between each other depending upon the safety-gear frame types. Basically the mounting style is: one partto be fixed on car roof profile, the counter part to be fixed on top crossbeam.7.2.8 Install the fan of car roofInstall the fan of car roof after all shaft work was finished, install the fan on the fan hole in car roof, and fix it with bolt, the wind exit of fan must cooperate with the fan hole ofcar roof well, there is plastic between the pedestal of fan and car roof pan in order toreduce the shake of each other. Ensure the fan without sand, dirt etc. and must beserviced some time.7.2.9 Install car handrailThe car handrail is collocated according to the request of client, if the car with thehandrail, need to drill hole in the car wall to install it at site, during the installation,please pay attention to the following points:a. The height between car floor and handrail be about 900mm, before the installation,confirm the position that can drill hole(don’t permit drill hole at the joint of car wainscot).After installation, ensure the handrail is level.b. The same distance of the handrail installed on the back wainscot and left wainscot orand right wainscot.c. The handrail can’t affect the opening of COP.8. Deformity COP field installation sketch drawing8.1 Field installation step:8.1.1 First take out the screws from the COP bottom, Separate the COP cover and COP box.8.1.2 Put the COP box on Car side-panel according to GAD (all COP pushbuttons between900mm to 1200mm from Car floor) and bore 6-D20 hole an 4-D5 hole in Car side-panel.8.1.3 Fix the COP box on the Car side-panel with screw, then make electrical connections.8.1.4 Final fix the COP cover on the COP box with screw.9. Install Car Door9.1 Install Car Door SillBefore the installation of car door, we need to check the installation of car if accord with the dimension demand of GAD. In front of the bottom car and aside the landing door, install the car door sill support, and install the sill and toe plate on the sill support, the connecting parts have indie packing from installation accessory. During the installation, pay attention to keep the landing door sill parallel to the car door sill and the clearance of them is 30mm.9.2 Install Car Door Standing PoleInstall car door standing pole on the car door sill support, the bottom of the standing pole equiped damping pad, socketing and M8X60 bolt. The weight of car door and car door suspension gear act on the rubber pad through door standing pole(drawing as follows). Install a rubber pad on every standing pole in center opening car door; Install two rubber pads on every standing pole in side opening car door.9.3 Install Car Door Suspension GearLoosen the bolts of the teeth strap wheel of car door suspension gear, install the teeth in-phase strap to ensure the length, then fix the teeth strap on the door cam, fix the door cam with 3 bolts of door hang panel(two of them is used together with switchbracket); circle the in-phase strap on the teeth strap wheel parts and drive parts, move the strap wheel parts and tight the bolts, pull the teeth in-phase strap tight.Door camInsert the head of car door standing pole into the long hole in the bottom panel of the car door suspension gear, fix the car door standing pole and car door suspension gear with bolts from car door suspension gear. Put the stopping bolts that were equiped by installation accessory into the C profile back of the car door suspension gear. Install rubber pad and socketing on the stopping bolts, connect it with the mounting angle was fixed on car roof with big washer and bolts. Can adjust the uprightness of the standing pole by the position adjustment of mounting angle.9.4 Install Car Door MotorFix the door motor on the motor seat, then fix the motor seat on the installation seat of car door suspension gear by buffer rubber and bolts. Install V type teeth drive strap, adjust M8X80 bolt, make the drive strap receive the force accord with the technical demand: act on the strap with 100N pull or pressure, the displacement of the strap is 6mm. Tighten all bolts after the adjustment.9.5 Install Car Door PanelErect the door panel before the door panel installation, put the door guide shoe into the sill trouth, push the door hang panel of landing door suspension gear to the relevant position, then fix the landing door panel on the door hang panel with theadjusting part, adjusting washer, M10X20 bolt and gasket that were supplied by landing door installation accessory.The quantity of adjusting washer can change the clearance of door panel and standing pole.The position of adjusting part can change the distance of door panel and sill; The position of adjusting guide shoe can change the clearance and uprightness of door panel and door standing pole.Adjust the parameter of landing door, let the clearance of door panel and door standing pole, the both of door panels is 3-6mm, keep the door panel plumb, door guide shoe and sill should work in well and glide normal. The distance of door cam and landing door sill side is 8mm, the centers of door cam and idler wheel of landing door lock is superposition and their distance is 12mm. After the finishing of landing door installation, when push or pull the landing door without noise, concussion or jumpiness phenomena, the closing is well.9.6 Install Light GridInstall the light grid on the corresponding light grid installation panel that was equiped connecting parts, adjust the light grid to vertical position, make the light grid on a line, and connect the light grid cable, at last fix the light grid cable with the bracket and rope that from light grid.9.7 Install Car Door Lock and Open-lock StopperSide opening car door divide into three brackets, lock-hook plate and car door lock, fix the installation bracket on the car door suspension gear with M8X25 six-angle bolt and gasket, then fix the car door lock on the installation bracket(drawing as follows).。
电梯中英对照

电梯说明书-中英对照-武汉翻译公司PARCEL S3-PLOT C26 TOWER F部分 s3-图表 c26塔楼 fService/Firefighters’ Lift:设施 / 消防电梯NUMBER:编号: ONE, CAR F9一、F9轿厢CAPACITY:载量: 2000KG2000千克CLASS LOADING:类装: PASSENGER CLASS A客运A级CONTRACT SPEED:合同速度 3.5 MPSROPING:挂绳 1:1MACHINE:机械装置: GEARLESS无齿轮MACHINE LOCATION:机械位置: OVERHEAD高架OPERATIONAL CONTROL:操作控制: SELECTIVE COLLECTIVE MICROPROCESSOR BASED SYSTEM 集选微处理器控制系统MOTOR CONTROL:电动机控制: AC VARIABLE VOLTAGEVARIABLE FREQUENCYMICROPROCESSOR BASED WITH DIGITAL CLOSED-LOOP FEEDBACKAC可变电压;可变频率;微处理器数字闭合回线反馈;POWER CHARACTERISTICS:功率特性: 400 VOLTS, 3 PHASE, 50 HERTZ400伏特;3相;50 赫兹;STOPS:停站: 54OPENINGS:启动: 54, IN LINE54;行FLOORS SERVED:服务楼层 G (CANAL), 1 (STREET), 2 53G (波道);1 (通道),2 53TRAVEL:行程:195.10 M ±PLATFORM SIZE:平台尺寸: 2600MM WIDE X 1850MM DEEP2600mm宽X 1850mm 深MINIMUM CLEAR INSIDE CAR:轿厢内最小间隙: 2500MM WIDE X 1550MM DEEP2500mm宽X 1550mm深ENTRANCE SIZE:入口尺寸: 1200MM WIDE X 2400MM HIGH1200mm宽X 2400mm高ENTRANCE TYPE:入口类型:TWO SPEED, SIDE OPENING双速;侧面开门ENTRANCE FINISH:入口装置饰面: FURNITURE STEEL WITH BAKED ENAMEL FINISH设施的钢材料经过烤搪瓷处理DOOR OPERATION:电梯门操作装置: HIGH SPEED, HEAVY-DUTY, MASTER, CLOSED LOOP ACV3F DOOR OPERATOR, MINIMUM OPENING SPEED 0.75 0.90 MPS高速、重载、主导;闭合回线ACV3F门自动开闭装置,最小启动速度0.75 0.90 MPSDOOR PROTECTION:电梯门保护装置 3 DIMENSIONAL INFRARED, FULL SCREEN DEVICE WITH DIFFERENTIAL TIMING, NUDGING AND INTERRUPTED BEAM TIME3维红外;不同计时的全屏设备;强迫关门和中断的束流时间SAFETY:安全: FLEXIBLE GUIDE CLAMP-TYPE B ONLY, CAR挠性导轨压板类型B,仅限轿厢GUIDE RAILS:导轨: PLANED STEEL TEES平面T字钢BUFFERS:缓冲器: OIL, SPRING RETURN WITH BLOCKING, ACCESS LADDERS AND PLATFORMS油料、弹簧回程阻块、通道梯和平台;COMPENSATION:校正: WIRE ROPE WITH PIT GUIDE SHEAVE AND TIE-DOWN DEVICE导轨槽轮钢丝绳和栓系设备CAR ENCLOSURE:轿厢壁板AS SPECIFIED参见说明CAR INTERIOR FINISHES PROVIDED UNDER THIS SECTION RIGIDIZED STAINLESS STEEL轿厢内面漆采用硬化不锈钢3000MM CLEAR HEIGHT UNDER CANOPY轿厢净高3000mmBATTERY POWERED EMERGENCY CAR LIGHTING. PROVIDE SEPARATECONSTANT PRESSURE TEST BUTTON IN CAR SERVICE COMPARTMENT.ILLUMINATE PORTION OF NORMAL CAR LIGHTING单独提供轿厢紧急事件电池照明;轿厢恒压力测试;轿厢正常照明部件SIGNAL FIXTURES:信号装置PROVIDER’S STANDARD VANDAL RESISTANT ASSEMBLY供方提供的标准防破坏部件HALL AND CAR PUSH BUTTON STATIONS门厅和轿厢按钮站 SINGLE HALL PUSHBUTTON RISERSINGLE CAR OPERATING PANEL单个门厅按钮提升装置单个轿厢操作面板CAR POSITION INDICATORS:轿厢位置指示器: DIGITAL AT TOP OF CAR OPERATING PANEL WITH CAR DIRECTION ARROWS轿厢顶部的数字操作面板SECURITY CONTROL PANEL安全控制面板FIREFIGHTERS’ CONTROL PANEL消防装置控制面板HALL LANTERNS:门厅指示灯: AT ALL FLOORS WITH VOLUME ADJUSTABLE ELECTRONIC CHIME OR TONE. SOUND TWICE FOR DOWN DIRECTIONVANDAL RESISTANT ASSEMBLY可调节电子式谐音系统;两次的声音表示下方;防破坏部件COMMUNICATION SYSTEM: INTERCOM WITH DISTRESS SIGNALFIXTURE SUBMITTAL:固定设备建议:SUBMIT BROCHURE DEPICTING PROVIDER’S PROPOSED DESIGNS WITH TENDER提交的手册描绘供方精心提出的设计;ADDITIONAL FEATURES –其它特征(CAR F9):(F9号轿厢): CAR AND COUNTERWEIGHT ROLLER GUIDES轿厢和对重滚柱导轨CAR TOP INSPECTION STATION轿厢最高检查站FIREFIGHTERS’ SERVICE, PHASE I AND II, INCLUDING ALTERNATE FLOOR RETURN消防设施,相位I和II,包括隔层返回STANDBY POWER TRANSFER (AUTOMATIC TO MAIN FLOOR) WITH MANUAL OVERRIDE IN FIREFIGHTERS' CONTROL PANEL备用电源转移(自动返回到主楼层)不受消防控制面板控制STATIONARY CAR RETURN PANEL ARRANGED FOR APPLIED CAR OPERATING PANEL为轿厢操作面板的应用安排固定轿厢返回面板;HOISTWAY DOOR UNLOCKING DEVICE ALL FLOORS所有楼层垂直通路的解锁装置PLATFORM ISOLATION平台隔离LOAD-WEIGHING DEVICE负荷测量装置ANTI-NUISANCE FEATURE防干扰特征INDEPENDENT SERVICE FEATURE独立服务特征CARD READER PROVISIONS提供卡片阅读机CCTV PROVISIONS提供闭路电视DIGITAL VIDEO DISPLAY PROVISIONS提供数字视频显示SECURITY CONTROL PANEL AND REMOTE WIRING TO B.M.S. ROOM安全控制面板和B.M.S.空间远程接线FIREFIGHTERS’ CONTROL PANEL AND REMOTE WIRING消防控制面板和远程接线;MACHINE, POWER CONVERSION UNIT, AND CONTROLLER SOUND ISOLATION机器,动力转换装置和控制器声音隔离装置TAMPER RESISTANT FASTENERS FOR ALL FASTENINGS EXPOSED TO THE PUBLIC所有固定紧固件的防篡改紧固装置;ONE YEAR WARRANTY MAINTENANCE WITH 24-HOUR CALL-BACK SERVICE一年保修;24个时回叫服务;FIREFIGHTERS’ TELEPHONE JACK消防电话插孔;SEISMIC DEVICES, ZONE 2A减震装置;2A 区域SIGNAGE ENGRAVING FILLED WITH BLACK PAINT OR APPROVED ETCHING PROCESS 告示牌使用黑色油漆或者蚀刻NO VISIBLE COMPANY NAME OR LOGO无可见公司名字或者标识WIRING DIAGRAMS, OPERATING INSTRUCTIONS, AND PARTS ORDERING INFORMATION 布线图、操作指南和部分订货信息MONITORING SYSTEM监控系统SYSTEM DIAGNOSTIC MEANS AND INSTRUCTIONS系统诊断方法和指令PARCEL S3-PLOT C26 TOWER G部分 s3-图表 c26塔楼 GLow Rise Residential Passenger Lifts:底层居用载人电梯:NUMBER:编号: FOUR, CARS G1 G4g1-g4轿厢CAPACITY:载量: 1350KG1350 千克CLASS LOADING:类装: PASSENGER CLASS A客运A级CONTRACT SPEED:合同速度: 2.0 MPSROPING:挂绳: 1:1 OR 2:11:1或者2:1MACHINE:机械装置: GEARLESS无齿轮MACHINE LOCATION:机械位置: OVERHEAD高架SUPERVISORY CONTROL:操作控制: GROUP AUTOMATIC MICROPROCESSOR BASED SYSTEM 组群自动微处理器系统MOTOR CONTROL:电动机控制: AC VARIABLE VOLTAGEVARIABLE FREQUENCYMICROPROCESSOR BASED WITH DIGITAL CLOSED-LOOP FEEDBACK AC可变电压可变频率;微处理器数字化闭合回线反馈;POWER CHARACTERISTICS:功率特性: 400 VOLTS, 3 PHASE, 50 HERTZ400伏特,3相,50 赫兹STOPS:停站: 30OPENINGS:启动: 30, IN LINE30行,FLOORS SERVED:服务楼层: 1 (STREET), 2 12, 13, 14 301(通道),2 12,13,14 30TRAVEL:行程106.05 M ±106.05 MPLATFORM SIZE:平台尺寸: 1900MM WIDE X 1850MM DEEP1900mm宽X 1850mm深MINIMUM CLEAR INSIDE CAR:轿厢内最小间隙: 1800MM WIDE X 1600MM DEEP1800mm宽X 1600mm深ENTRANCE SIZE:入口尺寸: 1100MM WIDE X 2400MM HIGH1100mm宽X 2400mm高ENTRANCE TYPE:入口类型: SINGLE SPEED, CENTER OPENING单速度,侧面开门ENTRANCE FINSIH:入口装置面漆: STAINLESS STEEL NO.4 BRUSHED FINISH4号不锈钢;刷饰面修饰DOOR OPERATION:电梯门装置: HIGH SPEED, HEAVY-DUTY, MASTER, CLOSED LOOP ACV3F DOOR OPERATOR, MINIMUM OPENING SPEED 0.75 0.90 MPS.高速;重载;主导;闭合回线ACV3F门自动开闭装置,最小启动速度0.75 0.90 MPS。
电梯专业英语中文翻译(Elevator English major Chinese Translation)

电梯专业英语中文翻译(Elevator English major ChineseTranslation)the lid washer (l / w) 斜垫片lockable 可闭锁的, 可锁定的locker 摇杆, 锁紧器lock-in circuit 自保电路locking jaw 锁紧爪locking relay 自锁继电器locks 门锁装置, 联锁装置log diary 运行日记记录器 loggerlogic analysis 逻辑分析器logic circuit 逻辑电路logic diagram 逻辑图logic elements 逻辑元件logical combination 逻辑结合long ton 长吨, 英制吨the long wait hall call 候梯时间较长的门厅呼梯the long wait landing call 候梯时间较长的层站呼梯longitudinal 纵向的long's lay rope 同向捻 (顺捻) 钢丝绳loop 环圈loop circuit 环形电路loop current 环流loose bearing 松配轴承loose fit 动配合loose 损耗loss of power 功率损耗loudness level 响度louver 气窗low carbon steel 低碳钢low cost 低成本的, 廉价的low rise building 低层建筑物low speed 低速的, 慢速的the low speed winding 低速绕组the lower chord 下楔材料the lower cost solution 低成本方案the lower frame 底部框架the lower / upper landing (自动扶梯) 下部 / 上部通道最低叫反转(LCR)最低层呼梯反向最低层最低反向楼层逆转低层电梯集团低层区电梯组群低层区低层区低速门低速门LS(限位开关)支架限位开关支架LS(限位开关)凸轮限位开关碰铁润滑油润滑剂润滑装置润滑装置润滑说明润滑说明书润滑润滑润滑环润滑油杯润滑润滑器耳线桥行李电梯行李电梯腔流明(光通量单位)发光指示器发光指示器力士勒克司(照明单位)可加工性切削性机曳引机机梁曳引机承重钢梁机梁板曳引机支撑板机床曳引机座机床插入砂浆曳引机座(砂浆)灌缝机床床身板机器底板,曳引机底板机驱动曳引机机床防震塞曳引机防震挡止器曳引机高度调整装置机升降装置机架曳引机架机器的安装曳引机安装机隔离曳引机隔震机隔离装置曳引机隔震装置机器语言机器语言机号板曳引机编号牌机房机房机房面积机房面积机房布置机房布置机房深度机房深度机房高度机房高度机房检查机房检修机房下下机房液压升降液压电梯机房机房机房规划机房布置图机上上机房房间机房宽度机房宽度机房配线线束机房配线束机轮盖曳引机绳轮罩机上曳引机高度调整底座间距机械曳引机链轮机支撑钢曳引机承重钢楔承重梁承重梁机曳引机承重钢结构支撑钢结构机床机床加工机加工的机械机械加工机械加工加工余量加工余量加工一般普通机械加工磁磁条磁制动磁力制动器磁线圈电磁线圈磁层电磁铁芯片柱塞插棒式电磁磁铁叶片隔磁板磁铁磁放大器磁放大器电磁制动器电磁制动器磁吸磁闩磁特性磁特性电磁离合器磁性离合器磁力检查器磁探测器磁通磁通量磁通密度磁通密度磁平开关磁性离合开关磁噪声电磁噪声磁极磁极磁电阻磁阻磁开关磁感应开关磁磁性磁性极磁棒大小大小,数量,等级磁核心磁铁芯红木红木主主链条主电路主电路主断路器主断路器主电路控制主电路控制主要联系主触点主接触器主接触器主传动主驱动装置主传动链主驱动链主驱动链保护装置主驱动链保护装置主传动轴主驱动轴主传动链轮主驱动链轮主驱动轮主驱动装置主驱动轮主驱动轮主场基站主起落基站主厅门开关基站门开关大堂大厅,主厅主菜单主菜单主电源主电源主程序主程序主要储油箱主绳主钢丝绳主停基站主开关总开关主阀主阀门主传动总成主驱动总成,主驱动部件维护合同维修合同维护控制检修控制维护成本维修成本维修钳工维修保养工维修说明书维修说明书维修人员维修人员维护操作维修作业免维护免费维修使接触触点闭合制造商的名字板制造商铭牌动合按钮制作按钮男性雄导轨导轨,带凸榫导轨故障误动作,失灵,不正常工作锤木槌锰青铜锰青铜强制强制的锰锰沙井人孔工时的COUTPUT人小时产量操作利用,操纵机械手操纵器,机械手人造纤维人造纤维计压力计大厦大厦手动松闸手动松闸装置手动下降阀手动下降阀手动打开门手动门手动打开电梯厅门手动厅门手动调整人工调节,手动调节手动式控制手动控制盘车手轮手动轮manualemergency操作装置手动应急操作装置手动下降阀手动下降阀手动操作门手动门制造制造,生产制造商生产者制造和销售生产和销售许可通知释放制造释放生产许可通知制造公差制造公差枫枫木缘极限,边界,范围边缘条件边际条件船用电梯船用电梯市场的概念市场观念市场定位市场地位市场报告市场报告市场份额市场占有率砌体墙转砌墙砌好砖砌井道质量质量,块,团,大量的惯性矩质量惯性矩大规模生产大量生产主主任,硕士,主导的,精通的主PC板主印数电路板主站总站主从法主/从方法,防效方法Mat垫块,罩面罩面开关垫开关匹配匹配材料管理费本草开销材料材料材料处理材料搬运材料供应计划材料供应计划乱蓬蓬的设计闷光图案最大最大的最大容量最大容量,最大能力最大净开口最大净开口最大负荷最大载荷最大速度最高速度最大候梯乘客量最大等待队列最大等待时间最长候梯时间均方均方平均值平均值,有效值〕平均速度平均速度意味着方法,装置实测负荷测定值测量仪器测量仪表测量仪测量计测量范围测量范围计量单位计量单位〕机械钳工机械制动机械式制动器汽车机械式轿厢位置指示器机械位置指示器门机械联锁门机械联锁装置机械门安全机械式门安全装置机械效率机械效率机械锁机械式锁重新机械式重开门装置机械装置机械安全鞋机械式安全触板机械开关机械开关机制转换机器开关机械停车库设备机械化停车库设备中型交通中级负荷交通中速中速,单层运行最高速兆欧表兆欧表,高阻表,摇表兆欧兆欧姆熔点融化点成员部件备忘录备忘录记忆记忆装置内存地址存储地址内存位置存储位置菜单菜单水星汞,水银汞弧汞弧水银开关水银开关汞气整流汞气整流器汞蒸气水银蒸汽,汞气汞弧整流器汞弧整流器水银湿簧继电器水银湿润继电器优点优点,指标网格网网状网式的网状设计网状图案金属金属金属部分金属型材金属垫片金属垫片表计量器,仪表,米,公尺在电路电路仪表米计量阀计量阀方法方式,方法度量公制公制刻度公(米)制刻度吨公吨镁(发电机)电动机发电机组镁(发电机)设置电动机发电机组主要终端大端子电力网手段目前馈路电流手段电压波动电源电压波动手段miantainer维修工,维修人员保持维修,保养维修协议保持一致限位开关微动限位开关微安微安培微机微型计算机microcontroller 微型控制器microfarad 微法punched card 微缩胶片冲孔卡 microformthe micro processor 微处理器, 微机microprodessor opertation control 微处理机操作控制微动开关 micro switch微伏 microvolts中线段 middle conductor中速电梯 middle speed elevator中间 midpointmid rise building 中层建筑物, 中高度建筑物mild steel 软钢 (低碳)mileage recorder (电梯) 运行次数记录器mill 铣削, 轧钢机 (厂)milliampere 毫安培毫米 etmilling cutter 铣刀铣床 milling machine毫伏特 millivolt矿井电梯 mine liftmineral cotton 矿物棉mineral fiber 矿物纤维mineral wool 矿物毛负数. 负极.分钟.mirror 镜子mirror finish 镜面抛光, 镜面加工mirror finished stainless steel 镜面不锈钢对影像的 mirror invertedmiscellaneous 杂项的, 其他的mixing 混合method 铸模车床 casting millmethod of supplly 供货方式调制解调器 modemmodern 现代的these 更新改造现代化 (电梯)these 全面改造全面现代化 overlay. amendment 修改change 调节器modular 组模式, 组合式modular concept 组模化原理modular escalatot 多坡度自动扶梯 (组合式)modular system 组模系统modular unit 组模单元调制解调器 modulationthe module (组件, 继电器, 固态继电器集成电路) 模数 modulusmodulus of elasticity 弹性模数modulus of longitudinal elasticity 纵向弹性模数横向弹性模数 modulus of transverse elasticity moisture 湿度moisture proof 防潮的molding 壁板缝压板, 模压molybdenum 钼(力, 弯, 矩转)moment of inertia 惯性矩瞬时的 momentary pressuremoniflop 单稳态触发器监视监控, 检测).梯群监控盘 monitor panel监控程序 monitor programmonitoring 监视, 监控, 检测contact 监控触点.monitoring device 监测装置, 监控装置活动扳手 monkey wrenchmono 单一的one 单色的单件安全装置 mono mass safety monostable 单稳态电路 circuitthe 松散绳 preformed ropemortuary lift 殡仪馆电梯, 太平间电梯MOS(金属氧化物半导体)金属氧化物半导体MOS(金属氧化物半导体)金属氧化物硅运动运动运动控制拖动控制运动速度运行速度电机电动机,马达电机频率电机频率电机基速电动机额定速度电机容量电机功率电机驱动单元电机驱动装置风扇电机电动机(冷却)风扇电机励磁开关电动机磁场激励开关盘车手轮电机手柄电机皮带轮电机皮带轮电动机额定速度电动机额定速度电机防护罩电机端罩电机试验台电机试验台汽车电梯汽车电梯电动状态驾驶条件成型模压,模制零件,制模安装托架固定架安装板固定板鼠标鼠,鼠标移动凸轮可动凸轮,可动碰铁移动车平台活动轿厢底盘动圈式马达动圈式电动机移动接触活动触点自动人行道移走消声器消音器多芯电缆多线电缆多芯电缆多芯电缆多功能多功能的多组多组群(电梯)多叶的门多扇门多扇滑动门多扇滑动门多面板的滑动门多扇滑动门多多重的多个电梯井多电梯井道多个楼层的飞行时间多层运行时间多叶的门多扇门多套(多套)多线悬挂的多租户大楼多个承用者大楼“多线程工作,“多螺纹蜗杆多好的多梯井道多线插头多线插接多地跑多层运行时间多重下集体自动操作多层下集选全自动控制倍增滑轮倍增滑轮多层胶合板多层胶合板多点连接板(PCB)插式接头板(印刷电路板)多程序多程序系统多绳提升多绳悬挂电梯多节门多扇门多速驱动多速驱动系统多速启动多速起动杰克多段式液压升降装置多级多级内存多段式柱塞多头蜗杆多头蜗杆多层平多层公寓多层建筑多层建筑物多stpreu公寓多层公寓多用多用途的多电压控制多极电压控制多针多路开关多线电缆多线电缆孟塞尔颜色系统蒙塞尔色调突变转变,更换NC(常闭)接触常闭触点NO(常开)接触常开触点铭牌铭牌铭牌电流铭牌电流,额定电流与非门非与门窄门套小门套,窄门套国家代码国家标准国家规定国家规定天然纤维天然纤维固有频率固有频率自然采光自然照明自然周期固有周期自然通风自然通风nbuilder的工作土建工程轴颈轴颈针针滚针轴承滚针轴承针罩针笼尖嘴钳针钳负负电微不足道的可忽略的霓虹氖辉光管霓虹灯霓虹灯氯丁橡胶合成橡胶净网络,净值,有效的轿厢地板净面积轿厢地板净面积净截面有效截面神经网络神经网络中性线中性导体中性点接地中性接地中性点接地中性接地中性点中性点neutral position 中性位置newel 中性, 楼梯扶栏柱newel was 中柱台nib 牛腿, 凸边nickel 镍nickel chromium molybdenum steel 镍铬钼钢nickel molybdenum steel 镍钼钢nickel steel 镍钢night traffic 夜间交通no load test 空载实验noise 噪声noise insulation 隔音noise level 噪声电平, 干扰电平noise proof 隔音noise protction 噪声防护noise reduced 减噪声的noise suppression 消音的no load current 空载电流no load operation 空载操作no load running no. of poles 空载运行极对数nomenclature 术语, 命名nominal 标定的nominal diameter 标称直径nominal dimension 公称尺寸nominal spedd of up motion 上行额定速度nominal speed of down motion 下行额定速度nominal tensile strength 标称抗拉强度nominal torque 额定扭矩nominal data 额定数据non combustible 不易燃的non combustible material 不可燃材料non contact electronic door safety sensor 不接触电子传感式门安全装置none return valve 单向阀non ferrous 非铁的非易燃不可燃的非磁性屏蔽隔磁屏非金属非金属的无换向装置防逆转装置,防反向装置非选择性集体自动操作非集选自动控制不停的无停站不停的按钮直驶按钮不停的开关直驶开关非易失性存储器(NV)非易失性存储器中午高峰午间交通高峰中午午间交通交通模式也不非或电路电路或非门非或门正常弯曲耦合普通管接头联轴器正常照明正常照明正常的限位开关限位开关正常位置正常位置终端正常停车开关终端常位停车开关正常的旅游正常运行正火正常化常闭(N / C)常闭的常开(N / O)常开的鼻线凸出线梳梳齿端鼻子牛腿收口不非电路电路没有门非门型槽缺口V,V凹口注加注,说明使用使用须知通知轻推强迫关门讨厌捣乱旅客乘客人数数革命转数数换向片数段数电机槽数槽数站停站数数绕线匝数匝数电梯电梯编号编号螺母螺帽,螺母尼龙尼龙尼龙衬套尼龙衬里尼龙管尼龙管橡树橡木对象物体观察室观光轿厢观察电梯观光电梯电梯观光电梯天文台入住占用,居住乘员占用者,居住者建筑大楼居住者乘员,大楼住户非高峰非高峰的,峰值外的关闭位置断开位置办公楼办公大楼非高峰期的交通非高峰交通状态欧姆表欧姆计油油刹车油油压制动器油压缓冲器油压缓冲器,耗能型缓冲器油压缓冲器开关油压缓冲器开关油可以油壶集油器集油器油冷却器油冷却器挡油板挡油圈油碟积油盘油滴盘接油盘加油管充油管油膜油膜滤油滤油器油表油量表油浸式变压器油浸式变压器石油泄漏漏油油位油位油位计油标,油位计油位指示器油位指示器油底壳油盘石油管道油管油淬火油淬火油油盘接收机油藏油池油环油环油封油封油雾油雾油底壳密封垫油槽垫圈油罐油箱垃圾箱油渣盒油油芯油绳刮油环挡油环油给油器油浸式浸油的无油轴承无油式轴承防油耐油的油密油封探究询问,询价板上的延迟登梯延时,登梯后的等候时间船上乘客登梯及等候时间秒延迟在呼叫控制呼梯控制一楼跑单层运行一个小时的评级小时定额一级柱塞一段式柱塞一种自动找平装置单向自动平层装置单向节流单向节流阀(液压梯)一对一的绳1:1绕绳比一到两绳1:2绕绳比在线在线的,联机的onlocking区开锁区域现场救援现场帮助蛋白石乳白的不透明的不透明的不透明的栏杆不透明扶栏开放式电梯露天电梯开路断路开环开环控制开放式电梯敞开式电梯开闭开关开关操纵器开启式电动机敞开式电动机开口扳手开口扳手平炉钢平炉钢开角张角,开启角开口方向开启方向操作可操作的操作操作操作按钮操作按钮凸轮操作碰头操作装置操作装置操作元件操作元件操作说明操作说明书,使用说明书操作磁操作磁铁操作面板操作盘工作压力操作压力经营范围操作范围,使用范围工作电压操作电压,工作电压操作操作,运转,控制操作面板操纵箱,操纵盘操作系统操作系统,操作方式运算放大器运算放大器操作制动操作制动器运行可靠性操作可靠性手术节操作部分运营商操作碰铁,司机反对门两面开门对方安排对面布置自动门贯通式自动门反对相反贯通式轿厢出入口汽车入口对面的门贯通式门贯通式出入门相反的入口按位置岗位依赖位置检查器状况检测器位置偏差状况差光光学的光纤光导纤维光纤电缆光缆,光导纤维电缆发光指示器光学指示器光信号发光信号光纤通信光导纤维通讯可选的可选择的可选的规范监督可选规格管理光电耦合器光电耦合光电光电耦合或电路或电路“或”门或门为了订单,订货单,次序订单处理合同(订单)处理订货文件订货文件订货须知订货说明书普通捻普通绳股普通捻钢丝绳普通捻股钢丝绳普通电梯一般用电梯孔节流孔,阻尼孔原原装的,原件,原图原包装原包装O型型圈装饰图案的表面装饰花纹表面振荡器示波器示波器示波器示波器示波器同步示波器同步示波器户外使用的自动扶梯户外自动扶梯不平衡负载不均衡负载异相相移180的淘汰°相移180°90的淘汰°相移90°从服务故障,停止运行缺货无现货外侧盖板外甲板外窗台外侧边缘外架支架外侧架支架外板外侧板外管出口管外护套外套出口插座,引线,出口概述轮廓,外形桁架框架外形概述输出输出输出电流输出电流输出信号输出信号输出扭矩输出扭矩输出电压输出电压外面以外,外边外径外径椭圆形的椭圆形在平衡超平衡在驱动蜗轮蜗杆在上方的蜗轮蜗杆传动在加热过热电力过负载在运行超程在上吊架吊索在上悬吊式吊挂式超速开关超速开关总成本总成本,总费用过流过电流过电流继电器过流继电器过电流释放过电流释放过流vreaker过流断路器悬悬臂式,外伸的悬臂式曳引轮倒悬牵引滑轮检修大修架空顶层空间,顶部架空梁顶楔架空高度顶层高度,顶部高度顶置曳引机架空机顶部轮架空滑车顶轮顶部绳轮架空结构顶部构件架空(O / H)顶房上置overhoisting限位开关井道上部限位开关重叠重叠覆盖(墙壁等)饰面过载超载超载蜂鸣器超载蜂鸣器超载控制过载控制超载装置过载装置过载指示超载装置过载灯超载灯超载试验过载试验过载报警超载报警超载微动开关超载微动开关超限越程超过冲,速度调节过量特大型大号,超大号大号螺栓大号螺栓汽车上方悬臂轿厢上置超速超速限速器限速器限速器开关超速保护装置行程越层倾覆力矩倾倒力矩防倾倒房倾倒装置超重超重过卷保护开关防过卷开关业主物主,所有者氧化氧化电脑主板印刷电路母板包的一部分零件组合包装材料包装材料用螺栓门厅用配套螺栓着陆包装包装包装费用包装费用包装成本包装成本填料环密封环垫衬垫,垫片桨扇叶片式通风扇寻呼业务传呼服务油漆油漆画涂漆,涂装苍白的踏板托盘式移动行走平板式自动扶梯托盘踏板潘盘面板板,扇,屏盘门板式门观光电梯观光电梯全景升降机观光电梯受壁杆受电弓型液压电梯壁杆式液压梯石蜡煤油,石蜡平行并联并联电路并联电路平行连续排列并列设置关键平键并行平行捻钢丝绳平行捻钢丝绳参数参数女儿墙防护栏杆寄生信号寄生信号停车驻停停车场驻停轿厢。
3电梯安装说明书(有机房V1.4)

电梯安装说明书 Elevator installation manual适用有机房电梯For Elevator With Machine RoomV 1.42010.09前 言本说明书适用于上海爱登堡电梯有限公司生产的VF系列全电脑控制交流变频变压调速的有机房电梯的安装。
有关基本部件的安装方法均在本说明书中有较详尽的说明。
当实际的井道机房土建布置与安装该电梯所需的井道机房土建布置图不一致时,请及时与本厂有关部门联系,以便采取特殊的安装方法。
电梯安装的质量要求,均按GB10060《电梯安装验收规范》及本企业的规定。
电梯质量的好坏,很大程度上取决于安装质量,我们要求负责安装的主要人员应有丰富的理论知识和实践经验,我们希望安装人员严格按照本说明书的要求进行作业。
在安装前认真了解电梯的结构和工作原理并在实践中完善和提高,以保证向客户提供质量稳定,性能优良,外观悦目的电梯。
目录1.电梯安装基本要求 (1)1.1电梯安装基本程序图 (1)1.2人员组织 (1)1.3安装工具配置 (1)1.4核查土建及材料清点 (2)1.5脚手架 (3)1.6施工照明 (4)1.7样板架的制作 (4)2.井道部件安装 (6)2.1导轨支架安装 (6)2.2导轨安装与校正 (10)2.3缓冲器安装 (13)2.4轿厢架安装 (15)2.5对重装置安装 (22)2.6曳引钢丝绳安装 (25)2.7张紧轮、限速器钢丝绳安装 (27)2.8轿厢拼装 (29)2.9开门机安装 (35)2.10井道信息装置安装 (38)2.11随行电缆安装 (40)2.12补偿装置安装 (42)2.13轿厢称重装置安装 (44)2.14井道电缆安装 (45)3.机房部件安装 (46)3.1承重梁与曳引机安装 (46)3.2控制屏安装 (52)3.3限速器安装 (53)3.4机房线槽、电缆安装 (55)4.层门部件安装 (56)4.1 地坎的安装 (56)4.2层门门套的安装 (57)4.3层门上坎架等的安装 (58)4.4层门的安装 (59)4.5指示器和召唤按钮的安装 (62)附录1 电梯井道保护接地装置 (63)附录2 EDT-04、EDT-05、EDT-11、EDT-19型吊顶安装步骤 (64)附录3 平层感应器、撞弓及限位开关、限速器和随行电缆在井道中的布置 (68)附录4 钢丝绳的释放方法 (71)附录5 应急通话系统 (72)附录6 EDL-508K系列曳引系统及减震垫安装方法 (73)附录7 EDL-508K系列上梁安装方法 (76)附录8无障碍电梯的残疾人操纵壁、扶手、镜子以及外呼的安装说明: (80)附录9 轿厢保护安装说明 (81)附录10有机房电梯机房线槽布置图及标识 (82)1.电梯安装的基本要求1.1电梯安装基本程序图1.2人员组织一般由2~3人组成安装小组,其中必须有熟练的机械安装工和有经验电工,安装工人必须持有焊工、电工和电梯安装上岗证。
电梯安装使用维护说明书 曳引式客梯
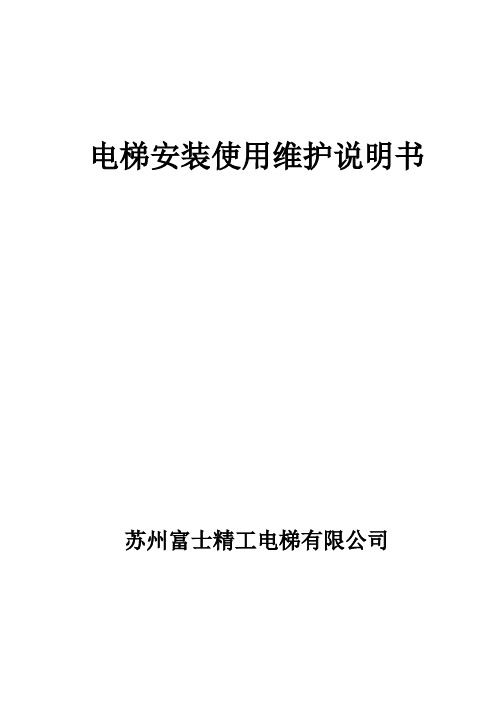
1-铅垂线 2-对重中心线
3-轿厢架中心线 4-连接铁钉
注:图 3-1 中的 G 尺寸布置图上标注的导轨端面间距加二倍的导轨高加 20mm 间隙(见图 3-2b);C 尺 寸为布置图上标注的导轨端面间距加二倍的导轨高(见图 3-2a) 。
图 3-2a 对重导轨安装示图 轿厢导轨安装示图
图 3-2b 3.1.2 样板架上标出轿厢架中心线, 门中心线, 门口净宽线, 导轨中心线, 各线的位置偏差不应超过 0.3mm。 3.1.3 在样板架放铅垂线的各点处,用薄锯条据个斜口,其旁钉一铁钉,作为悬挂固定铅垂线之用(见 图 3-3) 。 3.2 样板架的安置和悬挂铅垂线。 3.2.1 在机房楼板下面 500~600mm 的井道墙上,水平地凿四个 150×150mm 孔洞, 用两根截面大于 100 ×100mm 刨平的木梁,两端放入墙孔内,用水平仪校正水平后固定(见图 3-4) 。 3.2.2 在样板架上标记悬挂铅垂的各处,用 0.4~0.5mm 直径钢丝挂上 10~20 公斤的重锤放于底坑,待铅 垂线张紧稳定后,根据各层层门,校正样板架的正确位置后钉牢固在木梁上。 3.2.3 固定铅垂线。 在底坑距地 800~1000mm 高处,固定一个与顶部样板架相似的底坑样板架,样板架 安置符合要求后,用U形钉将铅垂线钉固于底坑样板架上(见图 3-5) 。 3.2.4 样板架的安置应符合下列要求:
7.6 轿门的安装 7.7 导靴安装 8 钢丝绳类 8.1 钢丝绳的使用 8.2 钢丝绳施工时处理方法 8.3 补偿链 8.4 钢丝绳孔的保护 9 对重安装 9.1 安装方法 1 10 光电装置安装和调试 10.1 光电装置安装注意事项 10.2 调试要点 11 平层装置 11.1 平层装置的安装与调整 12 称重装置 12.1 “王”字型称重装置的安装调整 12.2 ECW-L220+称重装置的安装调整 附件 1 电梯层高标识参考表
电梯安装图英文翻译

序号 1 2 3 4 5 6 7 8 9 10 11 12 13 14 15 16 17 18 19 20 21 22 23 24 25 26 27 28 29 30 31 32 33 34 35 36 37 38 39 40 41 42 43 44 45 英文 trap door bal. weights safety regulations headroom & pit demensions pit clearances section pit door deviations by builder top clearances FFL CH SH WW WD LR HR HH LL MW MH MD PH non served floor emergency floor main floor floor height CL shaft CL car CL load forces lifting beams plumb line openings floor design entrance expander bolt safety code rated load rated speed acceleration deceleration travel car area 中文翻译 安全窗 平衡重 安全标准 顶层与底坑尺寸 底坑空间 剖视 底坑检修门 偏离 客户自理 顶层空间 装修完成面 轿内净高 顶层高度 井道宽度 井道深度 门洞宽度 门洞高度 开门高度 开门宽度 机房宽度 机房高度 机房深度 底坑深度 不服务楼层 应急服务楼层 主楼层 楼层高度 井道中心线 轿厢中心线 门中心线 载荷 受力 起吊梁 铅垂线 预留洞 楼层标识 厅门入口 膨胀螺栓 安全标准 额定载荷 额定速度 加速度 减速度 行程 轿厢有效面积
有机房电梯安装说明书

1. 安装前的准备工作:1.1在电梯安装组进安装现场之前,各组带班人应检查以下工具是否齐备:1.2 劳动力配置:一般由3人组成,但人员的多少决定于所装电梯的工作量大小(层数、台数、工期),每组必须有熟练的机械安装工师傅带班,且所有施工人员均须有相关的资职证书及文件,带班人全面负责安装工程计划、安全及安装质量并向负责部门定期汇报施工进度。
1.3安装计划进度表安装组进场前必须按客户要求工期合理配置人力,并对电梯安装先行编制进度表,并按预期计划,保证工程进度、工期、质量,除质检人员到现场检查外,安装组长必须每星期把实际进度表交上级安装部。
电梯安装(机械)进度表工程名称电梯编号进场日期电梯安装地点控制形式负责人1.4井道尺寸的查验:为了保证安装组进场后,安装各工序顺利进行,安装组必须根据公司出具的电梯安装平面布置图和标准GB50310--2002等有关文件,根据电梯机房及平面布置图,检测井道高度、井道内净尺寸、顶层高度、提升高度、底坑尺寸、预留孔位置尺寸、停层数、机房高度、吊钓等是否与图纸相符。
在检查井道的同时,必须注意井道壁是否有突击的钢筋与混凝土块,若发现井道相关尺寸与图纸有较大偏差,且超出可调整范围时,应立即通知工程科或甲方,马上按图纸进行修改。
主控项目1.4.1机房内部、井道土建(钢架)结构及布置必须符合电梯土建布置图的要求。
1.4.2主电源开关必须符合下列规定:1主电源开关应能够切断电梯正常使用情况下最大电流;2对有机房电梯该开关应能从机房入口处方便地接近;3对无机房电梯该开关设置在井道外工作人员方便接近的地方,且应具有必要的安全防护。
1.4.3井道必须符合下列规定:1当底坑底面下有人员能到达的空间存在,且对重(或平衡重)上未设有安全钳装置时,对重缓冲器必须能安装在(或平衡重运行区域的下边必须)一直延伸到坚固地面上的实心桩墩上;2电梯安装之前,所有层门预留孔必须设有高度不小于1.2m的安全保护围封,并应保证有足够的强度;3当相邻两层门地坎间的距离不大于11m时,其间必须设置井道安全门,井道安全门严禁向井道内开启,且必须装有安全门处于关闭时电梯才能运行的安全装置。
电梯安装电梯安全中英文对照外文翻译文献

电梯安装电梯安全中英文对照外文翻译文献(文档含英文原文和中文翻译)E L E V A T O R S AF E T Y:G I V E TH E MI N E R A B R A K E ABSTRACTOver a five-year period, there were at least 18 documented cases of ascending elevators striking the overhead. In some cases, theaccidents resulted in serious injuries or fatalities. These accidents occurred on counter weighted elevators as a result of electrical,mechanical, and structural failures. Elevator cars are fitted withsafeties that grip the guide rails and stop a falling car; however,these devices do not provide protection in the upward direction.Rules and regulations applying to elevator safety have come under review in response to these accidents. Some governing authoritieshave already revised their regulations to require ascending caroverspeed protection. This paper will discuss basic elevator design, hazards, regulations, and emergency braking systems designed toprovide ascending car overspeed protection. In addition, a case-studyreport on a pneumatic rope brake system installed and tested on a mineelevator will be discussed.I NTRODUCT I ONElevators incorporate several safety features to prevent the carfrom crashing into the bottom of the shaft. Safeties installed on thecar can prevent this type of accident from occurring when the machine brake fails or the wire ropes suspending the car break. However, the inherent design of the safeties render them inoperative in the ascending direction.In the upward direction, the machine brake is required to stop the cage Irvhen an emergency condition occurs. Under normal operation, the machine brake serves only as a parking braked to hold the cage at rest. However, when an emergency condition is detected, modern elevator control system designs rely solely on the machine brake to stop the car.In the United States mining industry, the accident history has proven that this is not the best control strategy [2], [3]. These accidents occurred when the retarding effort of the drive motor was defeated when the mechanical brakes were inoperative. This allowed the counterweight to fall to the bottom of the shaft, causing the car to overspeed and strike the headframe. The high-speed elevator crashes into the overhead structure caused extensive mechanical damage and potentially fatal injuries.ELEVATOR DES I GNA basic understanding of elevator operation is required in order to assess the safety hazards present and determine the accident prevent methods available. Figure 1 shows a complete view of a mine elevator.Fig.1 Mico ElevatorIn a typical elevator, the ear is raised and loered by six toeight motor–driven wire ropes that are attached to the top of the car at one end, travel around a pair of sheaves, and are again attachedto a counterweight at the other end.The counterweight adds accelerating force when the elevator car is ascending and provides a retarding effort when the car is descending so that less motor horsepower is required. The counterweight is a collection of metal weights that is equal to the weight of the car containing about 45% of its rated load. A set of chains are looped from the bottom of thecounterweight to the underside of the car to help maintain balance byoffsetting the weight of the suspension ropesGuide rails that run the length of the shaft keep the car andcounterweight from swaying or twisting during their travel. Rollersare attached to the car and the counterweight to provide smooth travel along the guide rails.The traction to raise and lower the car comes from the friction of the wire ropes against the grooved sheaves. The main sheave is driven by an electric motor.Motor-generator (M-G) sets typically pro-vide to dc power for the drive motor. Newer systems use a static drive control. The elevator controls vary the motor' s speed based on a set of feedback signals that indicate the car' s position in the shaftway. As the car approaches its destination, a switch near the landing signals the controls to stop the car at floor level. Additional shaftway limit switches are installed to monitor overtravel conditions.The worst fear of 'litany passengers is that the elevator will go out of control and fall through space until it smashes into the bottom of the shaft. There are several safety features in modern elevators to prevent this from occurring. The first is the high-strength wire ropes themselves. Each 0. 625-in-diameter extra-high-strength wire rope can support 32, 000 lb, or about twice the average weight of a mine elevator filled with 20 passengers. For safety' s sake and to reduce wear, each car has six to eight of these cables. In addition, elevators have buffers installed at the shaft bottom that can stop the car without killing its passengers if they are struck at the normal speed of the elevator As previously discussed, modern elevators have several speed control features. If they do not work, the controls will disconnect the motor and apply the machine brake. Finally, the elevator itself is equipped with safeties mounted underneath the car. If the car surpasses the rated speed by 15 to 25%, the governor will trip, and the safeties will grip the guide rails and stop the car. This was the invention that made elevator transportation acceptable for the general public.SAFETY HAZARDSA historical perspective of elevator development can account for today' s problems with elevator safety rules and regulations [4]. In the beginning of modern elevator history, it was realized that although there were several factors of safety in the suspension rope design, the quality of construction and periodic inspection could not be assured. Therefore,the elevator car was equipped with reliable stand by 'safeties" that would stop the car safely if the suspension ropes failed. In 1853, Elisha. Otis, a New York mechanic, designed and demonstrated an instantaneous safety capable of safely stopping a free–falling car. This addressed the hazard shown in figure 2.Later on, it was realized that passengers may be injured when the car overspeeds in the down direction with suspension ropes intact, as shown in figure 3. To prevent this hazard, an o-verspeed governor with gradually applied safeties was developed. It detected the over peeling condition and activated the safeties.Furthermore, it was noticed that frequent application of safeties caused mechanical stress on the elevator structure and safety system.Therefore, a governor overspeed switch was installed that would try to stop the car by machine brake before the safeties activated. The switch was a useful idea because it could also initiate stopping in the case of overspeeding in the up direction as well.The problem started in the 1920's when the American Elevator Safety Code was developed. The writers most likely looked at the technology that was available at that time and subsequently required it on all elevators covered by the Code.The writers were so concentrated on describing the design of the required devices that they forgot to acknowledge the hazards that the devices are guarding against and the elevator components that may fail and cause the hazards. They did not consider the fact that for 90% of the elevator trips, the elevator is partially loaded (i. e. less than 45% of rated load) [5]. Therefore, if a brake failure occurs, the elevatorwill overspeed and crash in the up direction as shown in figure 4.Fig.4 Car overspeed UPUntil recently, elevator safety systems have not differed significantly from the early 1900' s designs. The problem arises because rulernaking committees and regulatory authorities are reluctant to require new safeguards when the technology has not been fully developed. Conversely, the elevator manufacturing industry cannot justify the product development expense for a new safety device with little marketability. This problem will be addressed in the following sections RULES AND REGULATIONSSeveral rulemaking committees and government safety authorities have addressed the deficiencies in the existing elevator regulations and have proposed revisions to the elevator safety codes.The report from the American Society of Mechanical Engineers - A17 Mechanical Design Committee on "Cars ascending into the building overhead, "-dated September 1987, contained the types of failures that could result in elevators accelerating into overhead structure and an analysis of the possible solutions. In addition, a proposal to the A17.1 Committee for a new code Rule 205. 6 was introduced as follows:Rule 205. 6 ("Prevention of overspeeding car from striking the overhead structure') : All traction elevators shall be provided with a means to prevent an ascending car from striking the overhead structure. This rneans shall conform to the following requirements:1.Prior to the time when the counterweight strikes its buffer, it shall reduce the speed of the car to the speed for which the counterweight buffer is designed.2.It shall not develop an average retardation of the car in excess of 32.2 ft /s2 (9.81 m/s2) during the stopping phase.3.1t shall be a mechanical means independent of the driving machine brake.4.1t shall prevent overspeeding of the elevator system through the control of one or more of the followinga.counterweightb.carc.suspension or compensating rope system.This proposed rule is currently under committee review, and consideration has been given to requiring protection to prevent the car from leaving the landing with the doors opened or unlocked. Pennsylvania Bureau of Deep Mine SafetyAn ascending elevator car accident occurred at a western Pennsylvania coal mine on February 4, 1987 and caused extensive structural damage and disabled the elevator for two months. Following this accident, the Pennsylvania. Bureau of Deep Mine Safety established an advisory committee to determine these devices that are available to provide ascending car overspeed protection for new and existing mine elevator installations.The following four protective methods were determined to be feasible based on engineering principles or extensive mine testing.1.Weight balancing (counterweight equals the empty car weight)2.Counterweight safeties3.Dynamic braking4.Rope brakeThe Pennsylvania Bureau of Deep Mine Safety has approved these four methods and has made ascending car overspeed protection mandatory on all existing counterweighted mine elevators.Dynamic BrakingA second solution used in the United States mining industry is the application of passive dynamic braking to the elevator drive motor [6]. As mentioned earlier, most elevators use direct current drive motors that can perform as generators when lowering an overhauling load. Dynamic braking simply connects a resistive load across the motor armature to dissipate the electrical energy generated by the falling counterweight. The dynamic braking control can he designed to function when the main power is interrupted. Dynamic braking does not stop the elevator but limits the runaway speed in either direction; therefore, the buffers can safely stop the conveyance.Rope BrakeA pneumatic rope brake that grips the suspension ropes and stops the elevator during emergency conditions has been developed by Bode Aufzugel [7]. This rope brake has been used in the Netherlands since August 12, 1957.Case Study: Rope Brake Testing and EvaluatioThe first pneumatic rope brake was installed in the United States at a western Pennsylvania coal mine on September 8, 1989. The largest capacity Bode rope brake (model 580) was installed on this coal mine melevator. This rope brake installation was tested extensively by Mine Safety and Health Administration engineers from the Pittsburgh Safety and Health Technology Center. A summary of the findings will be presented in this study.FunctionThe rope brake is a safety device to guard against overspeed in the upward and downward directions and to provide protection for uncontrolled elevator car movementsThe rope brake is activated when the normal running speed is exceeded by 15%as a result of a mechanical drive, motor control system, or machine brake failure. The rope brake does not guard against free fall as a result of a break in the suspension ropes.Standstill of the elevator car is also monitored by the rope brake system. If the elevator car moves more than 2 to 8 inches in either direction when the doors are open or not locked, the rope brake is activated and the control circuit interrupted. The rope brake control must be manually reset to restore normal operation.The rope brake also provides jammed conveyance protection for elevators and friction driven hoists. If the elevator car does not movewhen the drive sheave is turning, the rope brake will set, and the elevator control circuit will be interrupted.The rope brake control contains self-monitoring features. The rope brake is activated if a signal is not received from the pulse tachometer when the drive is runningThe rope brake requires electrical power and air pressure to function properly. The rope brake sets if the control power is interrupted. When the power is restored, the rope brake will automatically release.Typically, elevator braking systems are spring applied and electrically release. Therefore, no external energy source is needed to set the brake. The rope brake requires stored pressurized air to set the brake and stop the elevator. Therefore, monitoring of the air pressure is essential. If the working air pressure falls below a preset minimum, the motor armature current is interrupted, and the machine brake is set. When the air pressure is restored, the fault string is reset. Pneumatic DesignThe rope brake system is shown in figure 5. Starting from the air compressor tank, the pressurized air passes through a water separator and manual shut off valve to a check valve. The check valve was required to ensure the rope brake remains set even if an air leak develops in the compressed air supply. A pressure switch monitors for low air pressure at this point and will set the machine brake as mentioned earlier. The air supply is split after the check valve and goes to two independent magnetic two-way valves. The air supply is shut off (port A), while the magnetic valve coil is energized. When the magnetic valve coil is deenergized, the air supply is directed to the B port, which is open to the rope brake cylinder. The air pushes the piston inside the rope brake cylinder and forces a movable brake pad toward a stationary brake pad. The suspension ropes are clamped between the two brake pads. The rope brake is released by energizing the magnetic valve, which vents the pressurized rope brake cylinder to the atmosphere through a blowout silencer on port S.The force exerted on the suspension ropes equals the air pressure multiplied by the surface area of the piston. The rope brake model number 580 designates the diamoter of the brake cylinder in millimeters. This translates into 409. :36 in of surface area.. The working air pressure varies from 90 to 120 lbf/in2. The corresponding range of force applied to the suspension ropes is 36, 842 to 49, 123 lb. The force experienced by the ropes as they pass over the drive sheave under fully loaded conditions is about 34, 775 lb. Therefore, the ropes experience a 6 to 41% greater force during emergency conditions than normally encountered during full load operation.Mechanical ModificationsPrior to testing, several mechanical modifications were required to protect the rope brake system from environmental and mechanical damage. The modifications also reduced the possibility and the undesirable effect of an air leak in the pneumatic system. The following modifications were included in the rope brake design:1.The 200 lbf/in2 rated plastic air hose was replaced with 2, 000 lbflin2 rated metal braided hose with integral couplings.2.The air hose compression fittings were replaced by stainlesssteel threaded connectors.3.All the electrical components were installed in protectiveenclosures, and the wiring was installed in conduit.4. A check valve was installed in the compressed air supply line to hold the rope in the applied position once it was set even if air pressure was lost in the air compressor tank.5. The added check valve required an additional pressure switch to monitor the supply air pressure. The original pressure switch would not detect a. pressure loss in the air compressor tank when the check valve was installed. The contacts of the two pressure switches were installed in series.Mechanical TestingTests were conducted to determine if the rope brake would operate reliably in the mining environment to provide ascending car overspeed protection.First, accelerated mechanical testing was performed to determine if the braking system could withstand repeated operation without experiencing significant wear or failure. These tests were performed while the suspension ropes were stationary. This testing was conducted at both the mine site installation and in the laboratory.Mine site testing was conducted every 4 hr. Mechanical counters were installed on both the machine brake and the rope brake to record the total number of operations for each brake. Every 4 hr, the number of times the machine brake had set during the previous 4 hr period was noted, and then, the rope brake was operated an equal number of times.The mechanical testing concluded after 30 days of around the clock testing. The total number of rope brake operations was 3430. The temperature range varied from 25 to 83.One of the rope brake components subjected to wear was the piston ring gasket. This gasket provides the air seal between the moving piston, which presses against the traveling brake pad, and the stationary cylinder. An overload test was conducted to determine theintegrity of this seal.For the test, 8750 lb (125% of rated load) was loaded onto the car at the bottom of the shaft. Then, the rope brake was set, and the machine brake was disengaged. The air pressure was released from the air compressor tank, and the air pressure inside the rope brake cylinder was monitored. The load was successfully held stationary for 1 hr. The initial air pressure was 114 lbflin2, and after 1 hr, the pressure was 102 lbflin2. The pressured reduction may be attributedto an air leak through the check valve or past the piston ring gasket as a result of wear.Laboratory mechanical tests were also performed on the rope brake in the Mine Electrical Systems Division laboratories located at. The Pittsburgh Safety and Health Technology Center. The testing was performed on the smaller Bode rope brake model 200. The rope brake system was positioned outside the laboratory building under an awning that allowed the brake system to be exposed to the outside air temperature and humidity but was protected from direct contact with the rain and snow. The rope brake was activated remotely by computer control. The computer was programmed to apply and then release the rope brake every 38 s and log the number of operations. The outside air temperature, relative humidity, and barometric pressure were also continuously recorded.After 2 mo of testing and 146, 836 operations, the rope brake was disassembled and inspected for wear. The pneumatic. piston ring gasket exhibited minimal wear. Superficial rust was evident where the compressed air entered the rope brake and displaced the lubricant.Over the 70 days of testing, the temperature ranged from 5 to 82, and the relative humidity varied from 25 to 100%. At times, thick accumulations of frost build up on the air line between the magnetic valve and the rope brake cylinder. Therefore, the formation of ice inside the compressed air lines was possible; however, no adverse affects were observed. Rope Brake Control Failure Analysis In addition to the previously discussed mechanical analysis, testing and evaluation of the rope brake electrical control system was conducted. Brake control system studies were performed at the mine site and in the laboratory. The safety evaluation was conducted to ensure that a single undetected failure would not defeat the protection provided by the rope brake.Component failure should be detected by the brake control system and cause the elevator to stop safely and remain at rest until the failure is corrected. If automatic detection was not feasible, the periodic inspection and maintenance procedures were required to specify detailed testing of the possible failed component.T h e r o p e b r a k e c o n t r o l s y s t e m, w h i c h i s s h o wni n f i g u r e 6, m o n it or s th e f ol l ow in g fo ur in p ut s: N I c on ta ct o r, s p ee d re la y, pressure switch, and the rope pulse tachometer. Based on this input information, the brake logic decides to set the machine brake or both the machine brake and the rope brake. A test board was designed and built to simulate the brake control inputs with toggle switches and to provide relay coil loads for the brake logic output. A separate power source supplied 24 Vdo to the simulator board and brake control b o x.E v a l u a t i o n o f t h i s s i m u l a t i o n b o a r d p r o v i d e d t h e f o l l o w i n g information on the function of each input.翻译:电梯安全摘要在五年期间,至少有18起上升电梯撞毁高架建筑物的案例。
电梯安装说明书.

电梯安装说明书Elevator Installation Manual本安装说明书适用于电力拖动,曳引驱动,额定载重量3000Kg以下,额定速度不大于2.5m/s的各类电梯的安装。
电梯安装标准按额定速度分为三类:A类电梯:电梯的额定速度为>2.0m/s~2.5m/s(简称高速梯)B类电梯:电梯的额定速度为 1.0m/s~2.0m/s(简称中速梯)C类电梯:电梯的额定速度为<1.0m/s (简称低速梯)注:随着技术进步,内容如有改动,恕不另行通知。
第一章安装前的准备工作 (1)第二章缓冲器底座的安装 (5)第三章导轨支架及导轨的安装 (5)第四章曳引机承重梁的安装 (9)第五章轿厢架、轿厢安全钳及导靴的安装 (10)第六章门动系统的安装 (12)第七章曳引机支架、减震器装置、曳引机、导向轮的安装 (17)第八章缓冲器的安装 (20)第九章对重装置的安装 (21)第十章钢丝绳锥套和曳引绳的安装 (21)第十一章限速器装置的安装 (27)第十二章补偿链的安装 (28)第十三章平层装置、极限、限位、强换开关的安装、调整 (28)第十四章电梯层门、指示器和召唤箱的安装 (29)第十五章机房电器装置的安装 (34)第十六章随行电缆的安装 (35)第十七章配线、接地线及绝缘 (36)第十八章电梯调试 (37)第一章安装前的准备工作1.1安装队伍的组成1.1.1根据电梯的种类、技术要求、规格参数、层站数和安装设备自动化程度等因素来确定所需劳动力及技术工人。
1.1.2所有安装人员必须持有经当地质量技术监督局培训考核并取得电梯安装特种作业证。
1.1.3电梯安装负责人必须向安装成员介绍有关电梯井道、机房、库房、电梯安装材料、堆货场地、施工现场、施工办公室、电话、厕所、电源、灭火器、火警、警报处、医疗站、附近医院及工作周期等事项的介绍,并应进行安全交底和技术交底。
并且作好记录。
1.1.4安装人员应熟知电梯安装、验收的国家标准,地方法规、企业产品标准,熟悉所装电梯的土建资料、电梯部件及整机安装图、安装说明书、电梯使用维护说明书、电气控制原理图、电气接线图、结构、控制方式等,并作出具体的进度计划和安装工艺。
安装说明书(简体)
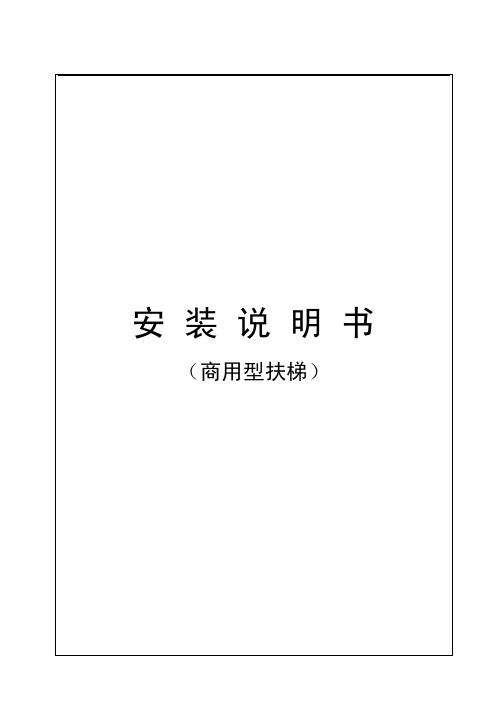
安 装 说 明 书 (商用型扶梯)目 录第一章安装进度..............................................................................................- 3 -1.1安装进度流程图 (3)1.2扶梯工地工作安全标准 (5)第二章扶梯安装过程的安全部分....................................................................- 7 -2.1个人作业和现场施工的安全要求.. (7)第三章扶梯安装的工作流程............................................................................- 9 -3.1扶梯安装的工作流程图 (9)第四章扶梯安装前的准备工作......................................................................- 10 -4.1防护栏的安装 (10)4.2井道的准备工作 (11)第五章扶梯安装的吊装就位..........................................................................- 13 -5.1扶梯的典型布置方式 (13)5.2扶梯的卸载 (14)5.3扶梯的连接 (18)5.4吊装扶梯 (21)5.5调整 (24)第六章扶梯现场安装......................................................................................- 28 -6.1扶手系统安装 (28)6.2梯级安装 (47)6.3前沿板安装 (49)6.4电器装置(工地现场) (52)第七章测试与维护..........................................................................................- 53 -7.1安装后调试.. (53)7.2使用防水油布进行保护 (55)7.3预防性维护 (56)附录 分段扶梯/人行道卸载与拼装说明.......................................................- 57 -用户须知1.电扶梯安装必须按规定由具备安装资质的公司负责实施。
电梯专业词汇的英语翻译

gold plated 镀金的
gondola lift 架空缆车,架空索道
goods lift 载货电梯
goods passwnger lift 客货两用电梯
goods paternoster 货用斗式升降机
government inspection 政府部门验收
hanger plate 吊门板
hanger rail 吊门轨道
hanger roller 吊门滚轮
hanger sheave 吊门轮
hanger track 吊门轨道
hanger trough 吊门槽板
hard disc 硬盘
hard wire 硬电线
harden quench 硬淬
group selective collective full automatic operation 组群集选全自动操作
group supervision panel 群控监视屏
group supervisory control 梯群监控
group supervisory control algorithm 梯群监控规则系统
guard sheaver 防护轮
guest lift 贵宾电梯
guide 导轨
guide rail bracket 导轨架
guide rail clip 导轨压板
guide rails 导轨
guide rod 导向杆
guide shoe 导靴
guide shoe bush 导靴衬
gearless machine 无齿轮曳引机
general contractor 总承包商
电梯安装作业指导书

电梯安装作业指导书1. 安装过程安全注意事项:1.1 必须牢记“安全第一”的生产观念,从思想上保持警惕。
1.2 进入施工现场,必须头戴安全帽,工作时穿上合适的工作服和安全鞋,不可戴手镯、戒指等其它装饰品,严禁在工作时玩耍、打斗、饮酒。
1.3 在井道脚手架上工作,上、下爬行时要注意站稳抓实,每层脚手架中间须搭一根钢管铺两层脚手片,除非已提供某些防护措施,当工作高度超过2米而有坠落危险时,必须戴上安全带,并紧系在牢固的物体上。
当拆除脚手架时,必须把附在木板上的钉子除去或弄弯。
1.4 在每个井道顶部挂两根生命线,用足够强度的支架固定。
1.5 在厅门未安装前,必须在预留洞处设置防护栏,其高度不低于1米,并且张贴醒目的危险标记。
防护栏底部用约150mm的踢脚板固定。
1.6 应避免在井道内的不同楼层进行两项或多项工作。
1.7 工作区域及周围地区必须保持清洁,任何时间均应防止绊倒,或其他损伤,保持安全的环境。
在留有预留孔的机房内,须用木板固定或重物覆盖预留孔,以防物体坠入井道。
机房内承重吊钩须有用户单位出具的承重载荷保证书。
1.8 井道内要有足够的照明,严禁使用明火或者220V电源作照明,必须使用36V以下的电源作照明。
1.9 当使用易燃、易爆及有害液体时,必须要有足够的空气流通,并有保护措施和设置消防器材。
在现场严禁吸烟和引入火种。
如在密封场所,又无通风设施,则必须戴上许可的口罩,防止溶液接触到皮肤。
切勿将氧气、氯气等和这些溶液混合,以免发生爆炸。
1.10 在使用电动工具时,必须保证有可靠而有效的接地,并配有漏电保护器,电动工具不得在潮湿或水中使用,切不可将电动工具当作其它用途使用。
1.11 气割设备应放置妥善地方,并有《禁止吸烟》标志、消防措施和灭火工具。
氧气瓶和乙炔瓶存放距离不得小于7米,且远离火源至少10米。
1.12 当进行电焊或气割工作时,应提前与业主防火部门取得联系,申请动火证,操作者必须持有操作证方可动火,动火必须有监护人并配备灭火器。
东洋砖混结构杂物电梯安装说明书
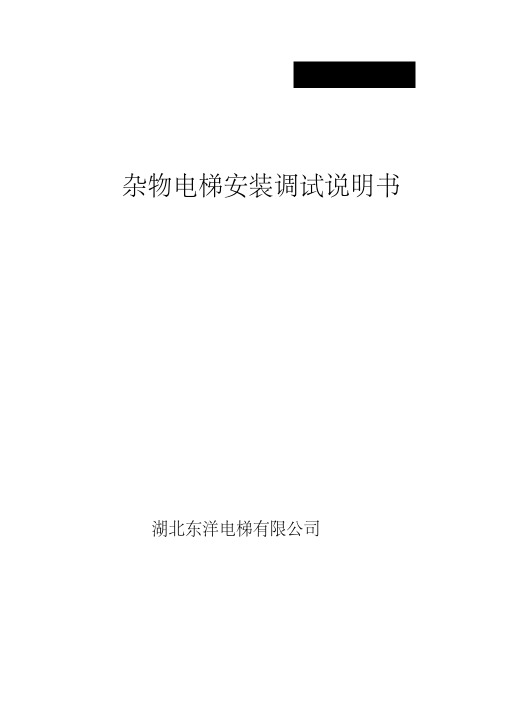
电梯随机文件杂物电梯安装调试说明书湖北东洋电梯有限公司杂物电梯安装说明书本杂物电梯采用目前比较先进的井道式结构,它不但安装方便,同时,井道尺寸相对减少了很多,这样就节省了电梯在整个建筑物的占有量,以及机房所需空间。
在实际的工作中用户应提供以下设施:1、井道顶部用户应提供380V三相五线动力电源,功率应在0.75-4KW,本动力电源应由独立的空气开关控制。
2、井道尺寸应符合生产厂提供的土建方案内所示尺寸,且出入口侧应为敞开式。
待电梯安装调试后再装修封闭。
3、井道顶部应提供载荷不小于1000kg承重吊钩。
井道顶层机房位置应提供一个不小于600×800的检修孔。
4、所提供的电梯井道、外装饰及安装规范应附合JG135-2000《杂物电梯》标准。
电梯安装的具体步骤如下:一、导轨的安装1、先将主轨支架用用膨胀螺栓固定井道的圈梁上,注意每步支架的上下垂直度都应在同一铅垂线上。
2、校正导轨支架的垂直度,每档支架都应在同一铅垂线上。
3、将预先制好的配重架置放在配重支架侧的井道底部,然后把由40角钢制成的副轨道安装在对重侧的轨道支架上,在安装最底部副轨道同时,将对重架安装在副轨道内。
4、另一侧主导轨支架直接用螺栓固定在副轨的支架上,同样保持每档在同一铅垂线上。
5、校正所有导轨支架的垂直度,然后将T型轨分别用导轨压道板固定在留有预制孔的导轨支架纵梁上,每节导轨连接处由导轨连接板连接固定,一定保证导轨的垂直度。
6、配重架上的导靴衬与副轨道之间应是在1-2mm间隙,可以通过调整支架来进行调整7、用同样的方法将副轨道安装完成,副轨道的连接处也是由副轨连接板固定的。
二、主机的安装1、在井道事先预留的吊钩处挂一个手拉葫芦,将预制好的曳引机横梁、导向轮、曳引加高台准备好。
2、将曳引机加高台先安装在曳引机的底座上,在保证安全的情况下,用手拉葫芦将曳引机吊起,高度应超过井道顶部圈梁200cm。
3、将曳引机横梁安装固定在井道框架的顶部圈梁上。
加装电梯工程合同翻译英文

加装电梯工程合同翻译英文Contract for the Installation of ElevatorThis Agreement is made and entered into this ______ day of______, 20__, by and between ______ (hereinafter referred toas "Owner"), a legal entity with its principal place of business at ______, and ______ (hereinafter referred to as "Contractor"), a legal entity with its principal place of business at ______.WHEREAS, Owner desires to have an elevator installed in its building located at ______, and Contractor is a licensed and qualified elevator installation company;NOW, THEREFORE, in consideration of the mutual promises and covenants contained herein, the parties agree as follows:1. Scope of WorkThe Contractor shall provide all labor, materials, and equipment necessary to install an elevator system in accordance with the specifications set forth in Exhibit A attached hereto and made a part hereof. The elevator shall be designed to meet the Owner's requirements for capacity, speed, and accessibility.2. Compliance with Laws and RegulationsThe Contractor shall comply with all federal, state, andlocal laws, ordinances, codes, and regulations applicable tothe installation of the elevator, including but not limitedto the Americans with Disabilities Act (ADA) and any other accessibility requirements.3. Permits and InspectionsThe Contractor shall be responsible for obtaining all necessary permits and approvals from the appropriate authorities. The Contractor shall also ensure that all workis completed in a manner that will pass all required inspections by the relevant authorities.4. ScheduleThe Contractor shall commence work on the elevatorinstallation within 30 days of the execution of this Agreement and shall complete the work within ______ monthsfrom the commencement date, subject to any delays caused bythe Owner or forces beyond the Contractor's control.5. Payment TermsThe Owner shall pay the Contractor for the work in the following manner:- A deposit of ______% of the total contract price upon execution of this Agreement;- Progress payments based on the percentage of work completed, as verified by the Contractor and approved by the Owner;- The balance of the contract price upon satisfactory completion of the work and issuance of a final inspection certificate by the relevant authorities.6. Warranties and GuaranteesThe Contractor warrants that all work performed under thisAgreement shall be free from defects in materials and workmanship for a period of ______ years from the date of completion. The Contractor shall also provide amanufacturer's warranty for the elevator equipment for a period specified by the manufacturer.7. IndemnificationThe Contractor shall indemnify, defend, and hold harmless the Owner from and against any and all claims, damages, losses, and expenses, including attorney's fees, arising out of or related to the Contractor's performance under this Agreement.8. TerminationThis Agreement may be terminated by either party in the event of a material breach by the other party, provided that the breaching party is given written notice and a reasonable opportunity to cure the breach.9. Governing LawThis Agreement shall be governed by and construed in accordance with the laws of the State of ______.10. Entire AgreementThis Agreement, including any exhibits or attachments hereto, constitutes the entire agreement between the parties and supersedes all prior negotiations, understandings, or agreements, whether written or oral.IN WITNESS WHEREOF, the parties have executed this Agreement as of the day and year first above written.Owner: ___________________________By: ___________________________Date: ___________________________Contractor: _________________________By: ___________________________Title: ___________________________Date: __________________________Exhibit A: Specifications for Elevator Installation (attached)。
- 1、下载文档前请自行甄别文档内容的完整性,平台不提供额外的编辑、内容补充、找答案等附加服务。
- 2、"仅部分预览"的文档,不可在线预览部分如存在完整性等问题,可反馈申请退款(可完整预览的文档不适用该条件!)。
- 3、如文档侵犯您的权益,请联系客服反馈,我们会尽快为您处理(人工客服工作时间:9:00-18:30)。
TYPICAL MAST TIE ARRANGEMENT
Typical mast ties are comprised of a structural mast mounting bracket which is clamped to mast horizontal sections onto which three adjustable turnbuckles are mounted. Tie shoe
brackets are attached to the turnbuckle ends and bolted to the structural steelwork at
appropriate position. This enables installation personnel -
turnbuckles by rotating the tubular body to lengthen or
providing the necessary structural support for the mast during the lift operation. (See Fig.2-7 and Fig.2-8).
Mast Mounting
Bracket
Tie Shoe Bracket
Turnbuckle Body
Fig. 2-7: Typical illustration of Mast Structural Tie
标准节连接装置的布置
标准节连接装置是由固定到标准节水平部分的钢结构标准节安装支架构成,安装支架上装有三个可调整的花篮螺栓。
鞋型支架连接到花篮螺栓末端并在合适的位置用螺栓固定到钢结构上。
这样使安装人员能够操作花篮螺栓,通过旋转管状的丝杆可以加长或者缩短花篮螺栓进而往外推动或拉回安装支架,如此实现竖直调整标准节,另外在提升过程中为标准节提供必要的结构支撑。
(见图2-7和2-8)
鞋型支架
花篮螺栓
标准节支架
图2-7:标准节钢结构连接装置的插图
Tie shoe bracket bolted to existing structural steelwork
Adjustable turnbuckle for precise mast alignment
Beam flange cut away for clarity
Fig. 2-8: Plan View Showing typical Mast Tie arrangement
鞋型支架用螺栓
固定到现有的钢结构上
为了清楚地显示 去掉了梁的凸缘
可调整的花篮螺栓 用于精确调整标准节
图2-8:平面图-标准节连接装置的布置图
DRIVE CARRIAGE
(See
Fig.2-10)
Rack blocking safety tools are inserted into the drive side racks at equal height and
drive carriage assemblies lowered on to the masts. This is repeated on the rear face of the mast with the counterweight carriages.
Load cell payload monitoring devices are fitted on to the carriages and the lift car
moved into place.
Balance bar and the encoding device are fitted into their respective location
Install temporary power supply to drive controls.
Continue to fit mast sections and structural ties progressively. Continue installation of landing gates, mast sections and structural mast ties to full
operational height.
Install cable chain brackets and guide channels. Install counterweights
and all associated hardware. Assemble and install counterweight cable cathead assembly.
Install counterweight cables including cable disc springs and electrical (broken or
stretched) cable monitoring mechanism.
Remove temporary power supply and install permanent power and controls cable chain
system.
Complete all control cable installation to landing gates.
Carry out final function tests to all landing gates.
Check that all landing screens are securely installed, all landing lighting in working order.
Complete final function tests to the satisfaction of Notified Body and client representative.
Complete operator training and maintenance personnel briefing to the satisfaction of client representative.
驱动箱
(见图2-10)在有配重箱的标准节的后侧重复这样做。
载荷传感器监控装置安装到箱体上,升降机箱移动到位。
平衡棒和编程装置安装到相应的位置。
安装驱动控制开关的临时电源。
继续安装标准节并将其与结构连接。
继续安装电梯口,标准节及其结构连接件一直到可运行最高高度。
安装电缆链式支架以及导向槽。
安装配重及相关的硬件。
组装并安装配重电缆锚架。
安装配重电缆,包括电缆碟形弹簧和电缆监控装置。
拆掉临时电源,安装永久电源和控制开关电缆。
所有电梯口安装控制开关电缆。
对所有电梯口实施功能测试。
检查确保所有的电梯口屏障已经安装完善,所有着陆灯都工作正常。
为让被通知方和客户代表满意,完成最后的功能测试。
按照客户代表的要求,对操作员进行培训,给维护人员做简要介绍。
MAST ERECTION
Mast section assemblies including bolted-in-place racks are now added in equal quantities to the two mast location positions on the base frame and securely connected with M20 fasteners. Sufficient mast sections are erected until the first structural tie can be fitted. Mast verticality is checked and if required adjusted at this stage using the three adjustable turnbuckles of the mast tie.
VERTICALITY OF MAST
Check that the mast is vertical using a suitable spirit level or a theodolite when installing
the first tie. It should be vertical in all directions to within 0.5º.
Use a straight edge approximately 1.5m long to check for twist at each tie level.
Fig. 2-6: Metallurgical Plant Mast Erection
Base frame
Mast 标准节安装
现在可以将带螺栓的齿条的标准节(数量相同)放到底部框架上的两个标冶炼厂标准节安装
标准节
底部框架
用一条约1.5米长的直/平尺检查每个连接位置处是否弯曲。
标准节的垂直度安装第一个连接装置的时候,用一个合适的水平仪或者经纬仪检查其垂直度。
任何方向都要保证 垂直,偏差在0.5°范围内。
准节位置上并用M20的紧固件固定。
安装标准节到第一个结构连接装置处。
检查井架的垂直度, 如有需要用三个可调整的花篮螺栓调整。