模具的发展 外文翻译 外文文献 英文文献 中英对照
塑料模具发展中英文对照外文翻译文献

中英文对照外文翻译文献(文档含英文原文和中文翻译)外文:The development of plastic mouldChina's industrial plastic moulds from the start to now, after more than half a century, there has been great development, mold levels have been greatly enhanced. Mould has been at large can produce 48-inchbig-screen color TV Molded Case injection mold, 6.5 kg capacity washing machine full of plastic molds, as well as the overall car bumpers and dashboards, and other plastic mould precision plastic molds, the camera is capable of producing plastic mould , multi-cavity mold small modulus gear and molding mold. --Such as Tianjin and Yantai daysElectrical Co., Ltd Polaris IK Co. manufactured multi-cavity mold VCD and DVD gear, the gear production of such size precision plastic parts, coaxial, beating requirements have reached a similar foreign the level of product, but also the application of the latest gear design software to correct contraction as a result of the molding profile error to the standard involute requirements. Production can only 0.08 mm thickness of atwo-cavity mold and the air Cup difficulty of plastic doors and windows out of high modulus, and so on. Model cavity injection molding manufacturing accuracy of 0.02 to 0.05 mm, surface roughness Ra0.2 μ m, mold quality, and significantly increase life expectancy,non-hardening steel mould life up to 10~ 30 million, hardening steel form up to 50 ~ 10 million times, shorten the delivery time than before, but still higher than abroad,and the gap between a specific data table.Process, the multi-material plastic molding die, efficient multicolor injection mould, inserts exchange structure and core pulling Stripping the innovative design has also made great progress. Gas-assisted injection molding, the use of more mature technologies, such as Qingdao Hisense Co., Ltd., Tianjin factorycommunications and broadcasting companies, such as moldmanufacturers succeeded in 29 ~ 34-inch TV thick-walled shell, as well as some parts on the use of gas-assisted mould technology Some manufacturers also use the C-MOLD gas-assisted software and achieved better results. Prescott, such as Shanghai, such as the newcompany will provide users with gas-assisted molding equipment and technology. Began promoting hot runner mold, and some plants use rate of more than 20 percent, the general heat-thermal hot runner, or device, a small number of units with the world's advanced level of rigorous hot runner-needle device, a small number of units with World advanced level of rigorous needle-hot runner mould. However, the use of hot runner overall rate of less than 10%, with overseas compared to 50 ~ 80%, the gap larger. In the manufacturing technology, CAD / CAM / CAE technology on the level of application of a new level to the enterprise for the production of household appliances representatives have introduced a considerable number of CAD / CAM systems, such as the United States EDS UG Ⅱ, the United States Parametric Technology Pro / Engineer, the United States CV CADS5 company, the British company DOCT5 Deltacam, HZS's CRADE Japan, the company's Cimatron Israel, the United States AC-C-Tech Mold Company and Australia's MPA Mold flow Mold analysis software, and so on. These systems and the introduction of the software, although a lot of money spent, but in our country die industry, and achieving a CAD / CAM integration, and to support CAE technology to forming processes such as molding and cooling, such as computer simulation, and achieved certain The technical and economic benefits, promote and facilitate China's CAD / CAM technology. In recent years, China's own development of the plasticmould CAD / CAM system has achieved significant development, the main guarantor Software Engineering Institute, is the development of CAXA, Huazhong University of Science HSC5.0 development of the system and injection mold CAE software, and so on, these Die of domestic software with the specific circumstances in the application of computer and lower prices, and other characteristics, in order to further universal CAD / CAM technology has created good conditions.In recent years, China has been more extensive use of some new plastic mold steel, such as: P20, 3Cr2Mo, PMS, SM Ⅰ, SM Ⅱ, and the quality of life of mold has a direct significant impact on the overall use of the still less . Plastic Moulds standard model planes, such as standard putter and spring has given more applications, and there have been some of the commercialization of domestic hot runner system components. However, at present China Die level of standardization and commercialization in the general level of below 30 percent and foreign advanced industrial countries has reached 70 percent compared to 80 percent, still a large gap. Table 1, at home and abroad plastic mould technology comparison table? Domestic projects abroad cavity injection model mm0.02 accuracy of 0.005 ~ 0.01 ~ 0.05mm cavity surface roughness Ra0.01 ~ 0.05 μ mRa0.20 μ m non-hardened steel die life 10 to 60 million 10 ~ 30 million hardened steel die life 160 ~ 300 million of 50 ~ 100 million hot runner mould overall utilization rate of more than 80per cent less than 10 per cent level of standardization of 70 ~ 80% less than 30% of medium-sized plastic mould production cycle about a month 2 ~ 4 months in the mold industry in the amount of 30 to 40% 25 to 30% According to the parties concerned forecast, the market's overall vigorous mold is a smooth upward, in the next Die market, the development of plastic mould faster than the other Die, die in the proportion of industry will gradually improve. With the continuous development of the plastics industry, put on the plastic mold growing demands is a normal, and so sophisticated, large-scale, complex, long-life plastic mould development will be higher than the overall pace of development. At the same time, imports in recent years because of the mold, precision, large, complex, long-life die in the majority, therefore, reduce imports, increase Guochanhualu: perspective, in the mold of such high-end market share will gradually increase. The rapid development of theconstruction industry so that the various Profile Extrusion Die, PVC plastic pipe fittings Die Die market become a new economic growth point, the rapid development of highways, car tires also put a higher demand, radial tire Die, Die particularly active pace of development will also be higher than the overall average level of the plastic and wood, plastic and metal to make plastic molds in the automotive, motorcycle industry in the demand for huge household appliances industry in the "10th Five-Year Plan" period have greater development, especially refrigerators,air-conditionersand microwave ovens, and other parts of the great demand for plastic moulds, and electronics and communications products, in addition to audio-video products, such as color televisions, laptop computers and set-top boxes will be given a wider network development, which are Plastic Mold market is the growth point. Second, China's industrial and technological plastic mould the future direction of the major developments will include:1, raising large, sophisticated, complex, long-life mold design and manufacturing standards and proportion. This is due to the molding plastic mould products increasingly large, complex and high-precision requirements, as well as requirements for high productivity and the development of a multi-mode due.2, in the design and manufacture of plastic mould fully promote the use of CAD / CAM / CAE technology. CAD / CAM technology has developed into a relatively mature technology common in recent years CAD / CAM technology hardware and software prices has been reduced to SMEs generally acceptable level of popularity for further create good conditions; based on network CAD / CAM / CAE system integration structure the initial signs of emerging, and it will solve the traditional mixed CAD / CAM system can not meet the actual production process requirements of the division of collaboration; CAD / CAM software will gradually improve intelligence plastic parts and the 3-D mold design andprototyping process 3-D analysis will be in our plastic mould industries play an increasingly important role.3, promote the use of hot runner technology, gas-assisted injection molding technology and high-pressure injection molding technology. Using hot runner mould technology can improve the productivity and quality of parts and plastic parts can be substantial savings of raw materials and energy conservation, extensive application of this technology is a big plastic mould changes. Hot Runner components formulate national standards, and actively produce cheap high-quality components, the development of hot runner mold is the key. Gas-assisted injection molding product quality can be guaranteed under the premise of substantially lower cost. Currently in the automotive and appliance industries gradually promote the use of the Chiang Kai-shek. Gas-assisted injection molding of the ordinary than the traditional injection of more parameters need to identify and control, and its more commonly used in large, complex products, mold design and control more difficult, therefore, the development of gas-assisted molding flow analysis software It seems very important. On the other hand in order to ensure precision plastic parts to continue to study the development of technology and high-pressure injection molding and injection-compression molding mould and die technology is also very important.4, the development of new plastics molding technology and rapid economic mold. To adapt to more variety, less volume of production.5, and improve standardization of plastic mould standard parts usage. China's mold and die level of standard parts standardization still low, the gap between the large and foreign, to a certain extent constraining the development of industries in our country die, die to improve quality and reduce manufacturing costs Die, Die standard parts to vigorously promote the application. To this end, first of all, to formulate a unified national standards, and in strict accordance with the standards of production, secondly it is necessary to gradually scale production, to improve the commercialization of the standard of quality, and reduce costs; again it is necessary to further increase the standard specifications of varieties.6, Die application quality materials and advanced surface treatment technology for improving the quality of life and mold it is necessary.7, research and application of high-speed die measurement technology and reverse engineering. CMM-use 3D scanner or reverse engineering is the realization of plastic moulds CAD / CAM one of the key technologies.Research and Application of diversity, adjustment, cheap detection equipment is to achieve the necessary precondition for reverse engineering.译文:塑料模具的发展我国塑料模工业从起步到现在,历经半个多世纪,有了很大发展,模具水平有了较大提高。
塑料注塑模具中英文对照外文翻译文献
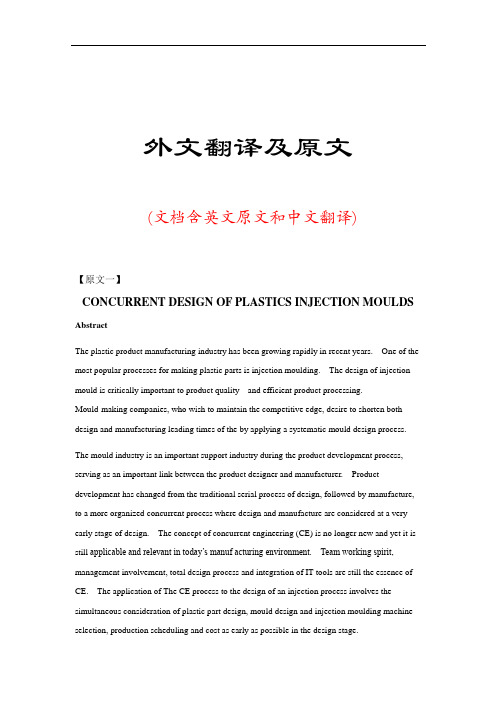
外文翻译及原文(文档含英文原文和中文翻译)【原文一】CONCURRENT DESIGN OF PLASTICS INJECTION MOULDS AbstractThe plastic product manufacturing industry has been growing rapidly in recent years. One of the most popular processes for making plastic parts is injection moulding. The design of injection mould is critically important to product quality and efficient product processing.Mould-making companies, who wish to maintain the competitive edge, desire to shorten both design and manufacturing leading times of the by applying a systematic mould design process. The mould industry is an important support industry during the product development process, serving as an important link between the product designer and manufacturer. Product development has changed from the traditional serial process of design, followed by manufacture, to a more organized concurrent process where design and manufacture are considered at a very early stage of design. The concept of concurrent engineering (CE) is no longer new and yet it is still applicable and relevant in today’s manuf acturing environment. Team working spirit, management involvement, total design process and integration of IT tools are still the essence of CE. The application of The CE process to the design of an injection process involves the simultaneous consideration of plastic part design, mould design and injection moulding machine selection, production scheduling and cost as early as possible in the design stage.This paper presents the basic structure of an injection mould design. The basis of this system arises from an analysis of the injection mould design process for mould design companies. This injection mould design system covers both the mould design process and mould knowledge management. Finally the principle of concurrent engineering process is outlined and then its principle is applied to the design of a plastic injection mould.Keywords :Plastic injection mould design, Concurrent engineering, Computer aided engineering, Moulding conditions, Plastic injection moulding, Flow simulation1.IntroductionInjection moulds are always expensive to make, unfortunately without a mould it can not be possible ho have a moulded product. Every mould maker has his/her own approach to design a mould and there are many different ways of designing and building a mould. Surely one of the most critical parameters to be considered in the design stage of the mould is the number of cavities, methods of injection, types of runners, methods of gating, methods of ejection, capacity and features of the injection moulding machines. Mould cost, mould quality and cost of mould product are inseparableIn today’s completive environment, computer aided mould filling simulation packages can accurately predict the fill patterns of any part. This allows for quick simulations of gate placements and helps finding the optimal location. Engineers can perform moulding trials on the computer before the part design is completed. Process engineers can systematically predict a design and process window, and can obtain information about the cumulative effect of the process variables that influence part performance, cost, and appearance.2.Injection MouldingInjection moulding is one of the most effective ways to bring out the best in plastics. It is universally used to make complex, finished parts, often in a single step, economically, precisely and with little waste. Mass production of plastic parts mostly utilizes moulds. The manufacturing process and involving moulds must be designed after passing through the appearance evaluation and the structure optimization of the product design. Designers face a hugenumber of options when they create injection-moulded components. Concurrent engineering requires an engineer to consider the manufacturing process of the designed product in the development phase. A good design of the product is unable to go to the market if its manufacturing process is impossible or too expensive. Integration of process simulation, rapid prototyping and manufacturing can reduce the risk associated with moving from CAD to CAM and further enhance the validity of the product development.3. Importance of Computer Aided Injection Mould DesignThe injection moulding design task can be highly complex. Computer Aided Engineering (CAE) analysis tools provide enormous advantages of enabling design engineers to consider virtually and part, mould and injection parameters without the real use of any manufacturing and time. The possibility of trying alternative designs or concepts on the computer screen gives the engineers the opportunity to eliminate potential problems before beginning the real production. Moreover, in virtual environment, designers can quickly and easily asses the sensitivity of specific moulding parameters on the quality and manufacturability of the final product. All theseCAE tools enable all these analysis to be completed in a meter of days or even hours, rather than weeks or months needed for the real experimental trial and error cycles. As CAE is used in the early design of part, mould and moulding parameters, the cost savings are substantial not only because of best functioning part and time savings but also the shortens the time needed to launch the product to the market.The need to meet set tolerances of plastic part ties in to all aspects of the moulding process, including part size and shape, resin chemical structure, the fillers used, mould cavity layout, gating, mould cooling and the release mechanisms used. Given this complexity, designers often use computer design tools, such as finite element analysis (FEA) and mould filling analysis (MFA), to reduce development time and cost. FEA determines strain, stress and deflection in a part by dividing the structure into small elements where these parameters can be well defined. MFA evaluates gate position and size to optimize resin flow. It also defines placement of weld lines, areas of excessive stress, and how wall and rib thickness affect flow. Other finite element design tools include mould cooling analysis for temperature distribution, and cycle time and shrinkage analysis for dimensional control and prediction of frozen stress and warpage.The CAE analysis of compression moulded parts is shown in Figure 1. The analysis cycle starts with the creation of a CAD model and a finite element mesh of the mould cavity. After the injection conditions are specified, mould filling, fiber orientation, curing and thermal history, shrinkage and warpage can be simulated. The material properties calculated by the simulation can be used to model the structural behaviour of the part. If required, part design, gate location and processing conditions can be modified in the computer until an acceptable part is obtained. After the analysis is finished an optimized part can be produced with reduced weldline (known also knitline), optimized strength, controlled temperatures and curing, minimized shrinkage and warpage.Machining of the moulds was formerly done manually, with a toolmaker checking each cut. This process became more automated with the growth and widespread use of computer numerically controlled or CNC machining centres. Setup time has also been significantly reduced through the use of special software capable of generating cutter paths directly from a CAD data file. Spindle speeds as high as 100,000 rpm provide further advances in high speed machining. Cutting materials have demonstrated phenomenal performance without the use of any cutting/coolant fluid whatsoever. As a result, the process of machining complex cores and cavities has been accelerated. It is good news that the time it takes to generate a mould is constantly being reduced. The bad news, on the other hand, is that even with all these advances, designing and manufacturing of the mould can still take a long time and can be extremely expensive.Figure 1 CAE analysis of injection moulded partsMany company executives now realize how vital it is to deploy new products to market rapidly. New products are the key to corporate prosperity. They drive corporate revenues, market shares, bottom lines and share prices. A company able to launch good quality products with reasonable prices ahead of their competition not only realizes 100% of the market before rival products arrive but also tends to maintain a dominant position for a few years even after competitive products have finally been announced (Smith, 1991). For most products, these two advantages are dramatic. Rapid product development is now a key aspect of competitive success. Figure 2 shows that only 3–7% of the product mix from the average industrial or electronics company is less than 5 years old. For companies in the top quartile, the number increases to 15–25%. For world-class firms, it is 60–80% (Thompson, 1996). The best companies continuously develop new products. AtHewlett-Packard, over 80% of the profits result from products less than 2 years old! (Neel, 1997)Figure 2. Importance of new product (Jacobs, 2000)With the advances in computer technology and artificial intelligence, efforts have been directed to reduce the cost and lead time in the design and manufacture of an injection mould. Injection mould design has been the main area of interest since it is a complex process involving several sub-designs related to various components of the mould, each requiring expert knowledge and experience. Lee et. al. (1997) proposed a systematic methodology and knowledge base for injection mould design in a concurrent engineering environment.4.Concurrent Engineering in Mould DesignConcurrent Engineering (CE) is a systematic approach to integrated product development process. It represents team values of co-operation, trust and sharing in such a manner that decision making is by consensus, involving all per spectives in parallel, from the very beginning of the productlife-cycle (Evans, 1998). Essentially, CE provides a collaborative, co-operative, collective and simultaneous engineering working environment. A concurrent engineering approach is based on five key elements:1. process2. multidisciplinary team3. integrated design model4. facility5. software infrastructureFigure 3 Methodologies in plastic injection mould design, a) Serial engineering b) Concurrent engineeringIn the plastics and mould industry, CE is very important due to the high cost tooling and long lead times. Typically, CE is utilized by manufacturing prototype tooling early in the design phase to analyze and adjust the design. Production tooling is manufactured as the final step. The manufacturing process and involving moulds must be designed after passing through the appearance evaluation and the structure optimization of the product design. CE requires an engineer to consider the manufacturing process of the designed product in the development phase.A good design of the product is unable to go to the market if its manufacturing process is impossible. Integration of process simulation and rapid prototyping and manufacturing can reduce the risk associated with moving from CAD to CAM and further enhance the validity of the product development.For years, designers have been restricted in what they can produce as they generally have todesign for manufacture (DFM) – that is, adjust their design intent to enable the component (or assembly) to be manufactured using a particular process or processes. In addition, if a mould is used to produce an item, there are therefore automatically inherent restrictions to the design imposed at the very beginning. Taking injection moulding as an example, in order to process a component successfully, at a minimum, the following design elements need to be taken into account:1. . geometry;. draft angles,. Non re-entrants shapes,. near constant wall thickness,. complexity,. split line location, and. surface finish,2. material choice;3. rationalisation of components (reducing assemblies);4. cost.In injection moulding, the manufacture of the mould to produce the injection-moulded components is usually the longest part of the product development process. When utilising rapid modelling, the CAD takes the longer time and therefore becomes the bottleneck.The process design and injection moulding of plastics involves rather complicated and time consuming activities including part design, mould design, injection moulding machine selection, production scheduling, tooling and cost estimation. Traditionally all these activities are done by part designers and mould making personnel in a sequential manner after completing injection moulded plastic part design. Obviously these sequential stages could lead to long product development time. However with the implementation of concurrent engineering process in the all parameters effecting product design, mould design, machine selection, production scheduling,tooling and processing cost are considered as early as possible in the design of the plastic part. When used effectively, CAE methods provide enormous cost and time savings for the part design and manufacturing. These tools allow engineers to virtually test how the part will be processed and how it performs during its normal operating life. The material supplier, designer, moulder and manufacturer should apply these tools concurrently early in the design stage of the plastic parts in order to exploit the cost benefit of CAE. CAE makes it possible to replace traditional, sequential decision-making procedures with a concurrent design process, in which all parties can interact and share information, Figure 3. For plastic injection moulding, CAE and related design data provide an integrated environment that facilitates concurrent engineering for the design and manufacture of the part and mould, as well as material selection and simulation of optimal process control parameters.Qualitative expense comparison associated with the part design changes is shown in Figure 4 , showing the fact that when design changes are done at an early stages on the computer screen, the cost associated with is an order of 10.000 times lower than that if the part is in production. These modifications in plastic parts could arise fr om mould modifications, such as gate location, thickness changes, production delays, quality costs, machine setup times, or design change in plastic parts.Figure 4 Cost of design changes during part product development cycle (Rios et.al, 2001)At the early design stage, part designers and moulders have to finalise part design based on their experiences with similar parts. However as the parts become more complex, it gets rather difficult to predict processing and part performance without the use of CAE tools. Thus for even relatively complex parts, the use of CAE tools to prevent the late and expensive design changesand problems that can arise during and after injection. For the successful implementation of concurrent engineering, there must be buy-in from everyone involved.5.Case StudyFigure 5 shows the initial CAD design of plastics part used for the sprinkler irrigation hydrant leg. One of the essential features of the part is that the part has to remain flat after injection; any warping during the injection causes operating problems.Another important feature the plastic part has to have is a high bending stiffness. A number of feeders in different orientation were added to the part as shown in Figure 5b. These feeders should be designed in a way that it has to contribute the weight of the part as minimum aspossible.Before the design of the mould, the flow analysis of the plastic part was carried out with Moldflow software to enable the selection of the best gate location Figure 6a. The figure indicates that the best point for the gate location is the middle feeder at the centre of the part. As the distortion and warpage of the part after injection was vital from the functionality point of view and it has to be kept at a minimum level, the same software was also utilised to yiled the warpage analysis. Figure 5 b shows the results implying the fact that the warpage well after injection remains within the predefined dimensional tolerances.6. ConclusionsIn the plastic injection moulding, the CAD model of the plastic part obtained from commercial 3D programs could be used for the part performance and injection process analyses. With the aid ofCEA technology and the use of concurrent engineering methodology, not only the injection mould can be designed and manufactured in a very short of period of time with a minimised cost but also all potential problems which may arise from part design, mould design and processing parameters could be eliminated at the very beginning of the mould design. These two tools help part designers and mould makers to develop a good product with a better delivery and faster tooling with less time and money.References1. Smith P, Reinertsen D, The time-to-market race, In: Developing Products in Half the Time. New York, Van Nostrand Reinhold, pp. 3–13, 19912.Thompson J, The total product development organization. Proceedings of the SecondAsia–Pacific Rapid Product Development Conference, Brisbane, 19963.Neel R, Don’t stop after the prototype, Seventh International Conference on Rapid Prototyping, San Francisco, 19974.Jacobs PF, “Chapter 3: Rapid Product Development” in Rapid Tooling: Technologies and Industrial Applications , Ed. Peter D. Hilton; Paul F. Jacobs, Marcel Decker, 20005.Lee R-S, Chen, Y-M, and Lee, C-Z, “Development of a concurrent mould design system: a knowledge based approach”, Computer Integrated Manufacturing Systems, 10(4), 287-307, 19976.Evans B., “Simultaneous Engineering”, Mechanical Engi neering , V ol.110, No.2, pp.38-39, 19987.Rios A, Gramann, PJ and Davis B, “Computer Aided Engineering in Compression Molding”, Composites Fabricators Association Annual Conference , Tampa Bay, 2001【译文一】塑料注塑模具并行设计塑料制品制造业近年迅速成长。
文献翻译原文-模具的历史发展

1 The historical development of moldDavid O.Kazmer.Injection mold design engineering.Hanser Gardner PublicationsThe emergence of mold can be traced back thousands of years ago, pottery and bronze foundry, but the large-scale use is with the rise of modern industry and developed.The 19th century, with the arms industry (gun's shell), watch industry, radio industry, dies are widely used. After World War II, with the rapid development of world economy, it became a mass production of household appliances, automobiles, electronic equipment, cameras, watches and other parts the best way. From a global perspective, when the United States in the forefront of stamping technology - many die of advanced technologies, such as simple mold, high efficiency, mold, die and stamping the high life automation, mostly originated in the United States; and Switzerland, fine blanking, cold in Germany extrusion technology, plastic processing of the Soviet Union are at the world advanced. 50's, mold industry focus is based on subscriber demand, production can meet the product requirements of the mold. Multi-die design rule of thumb, reference has been drawing and perceptual knowledge, on the design of mold parts of a lack of real understanding of function. From 1955 to 1965, is the pressure processing of exploration and development of the times - the main components of the mold and the stress state of the function of a mathematical sub-bridge, and to continue to apply to on-site practical knowledge to make stamping technology in all aspects of a leap in development. The result is summarized mold design principles, and makes the pressure machine, stamping materials, processing methods, plum with a structure, mold materials, mold manufacturing method, the field of automation devices, a new look to the practical direction of advance, so that pressing processing apparatus capable of producing quality products from the first stage.Into the 70's to high speed, launch technology, precision, security, development of the second stage.Continue to emerge in this process a variety of high efficiency, business life, high-precision multi-functional automatic school to help with. Represented by the number of working places as much as other progressive die and dozens of multi-station transfer station module. On this basis, has developed both a continuous pressing station there are more slide forming station of the press - bending machine. In the meantime, the Japanese stand to the world's largest - the mold into the micron-level precision, die life, alloy tool steel mold has reached tens of millions of times, carbide steel mold to each of hundreds of millionsof times p minutes for stamping the number of small presses usually 200 to 300, up to 1200 times to 1500 times. In the meantime, in order to meet product updates quickly, with the short duration (such as cars modified, refurbished toys, etc.) need a variety of economic-type mold, such as zinc alloy die down, polyurethane rubber mold, die steel skin, also has been very great development.From the mid-70s so far can be said that computer-aided design, supporting the continuous development of manufacturing technology of the times. With the precision and complexity of mold rising, accelerating the production cycle, the mold industry, the quality of equipment and personnel are required to improve. Rely on common processing equipment, their experience and skills can not meet the needs of mold. Since the 90's, mechanical and electronic technologies in close connection with the development of NC machine tools, such as CNC wire cutting machine, CNC EDM, CNC milling, CNC coordinate grinding machine and so on. The use of computer automatic programming, control CNC machine tools to improve the efficiency in the use and scope. In recent years, has developed a computer to time-sharing by the way a group of direct management and control of CNC machine tools NNC system.With the development of computer technology, computers have gradually into the mold in all areas, including design, manufacturing and management. International Association for the Study of production forecasts to 2000, as a means of links between design and manufacturing drawings will lose its primary role. Automatic Design of die most fundamental point is to establish the mold standard and design standards. To get rid of the people of the past, and practical experience to judge the composition of the design center, we must take past experiences and ways of thinking, for series, numerical value, the number of type-based, as the design criteria to the computer store. Components are dry because of mold constitutes a million other differences, to come up with a can adapt to various parts of the design software almost impossible. But some products do not change the shape of parts, mold structure has certain rules, can be summed up for the automatic design of software. If a Japanese company's CDM system for progressive die design and manufacturing, including the importation of parts of the figure, rough start, strip layout, determine the size and standard templates, assembly drawing and parts, the output NC program (for CNC machining Center and line cutting program), etc., used in 20% of the time by hand, reduce their working hours to 35 hours; from Japan in the early 80s will be three-dimensional cad / cam system for automotive panel die. Currently, the physical parts scanning input, map lines and data input,geometric form, display, graphics, annotations and the data is automatically programmed, resulting in effective control machine tool control system of post-processing documents have reached a high level; computer Simulation (CAE) technology has made some achievements. At high levels, CAD / CAM / CAE integration, that data is integrated, can transmit information directly with each other. Achieve network. Present. Only a few foreign manufacturers ca2 StampingStamping is a kind of plastic forming process in which a part is produced by means of the plastic forming of the material under the action of a die.Stamping is usually carried out under cold state, so it is also called cold stamping. Heat stamping is used only when the blank thickness is greater than 8-100mm. The blank material for stamping is usually in the form sheet or strip, and therefore it is also called sheet metal forming. Some non-metal sheets (such as plywood, mica sheet, asbestos, leather) can also be formed by stamping.Stamping is widely used in various metalworking industry, and it plays a crucial role in the industries for manufacturing automobiles, instruments, military parts and household electrical appliances, etc.The process,equipment and die are the three foundational problems that needed to be studied in stamping.The characteristics of the sheet metal forming are as follows:(1) High material utilization.(2) Capacity to produce thin-walled parts of complex shape.(3) Good interchangeability of stamping parts precision in shape and dimension.(4) Parts with lightweight,high strength and fine rigidity can be obtained.(5) High productivity, easy to operate and to realize mechanization and automatization. The manufacture of the stamping die is costly, and therefore it only fits to mass production. For the manufacture of products in small batch and rich variety, the simple stamping die and the new equipment such as a stamping machining center, are usually adopted to meet he market demands.The materials for sheet metal stamping include mild steel, copper, aluminum, magnesium alloy and high-plasticity alloy steel, etc.Stamping equipment includes plate shear and punching press. The former shears plate into strips with a definite width, which would be pressed later. The later can be used both in shearing and forming.There are various processes of stamping forming with different working patterns and names,but these processes are similar to each other in plastic deformation.There are following conspicuous characteristics in stamping:(1) The force per unit area perpendicular to the blank surface is not large but is enough to cause the material plastic deformation. It is much less than the inner stresses on the plate plane directions.In most cases stamping forming can be treated approximately as that of the plane stress state to simplify vastly the theoretical deformation mechanics analysis and the calculation of the process parameters.(2) Due to the small relative thickness,the anti-instability capability of the blank is weak under compressive stress.As a result,the stamping process is difficult to proceed successfully without using the anti-instability device (such as blank holder).Therefore the variety of the stamping processes dominated by tensile stress are more than those dominated by compressive stress.(3) During stamping forming,the inner stress of the blank is equal to or sometimes less than the yield stress of the material.In this point,the stamping is different from the bulk forming. During stamping forming,the influence of the hydrostatic pressure of the stress state in the deformation zone to the forming limit and the deformation resistance is not so important as to the bulk forming.In some circumstances,such influence may be neglected.Even in the case when this influence should be considered,the treating method is also different from that of bulk forming.(4) In stamping forming,the restrain action of the die to the blank is not severe as in the case of the bulk forming(such as die forging).In bulk forming, the constraint forming is proceeded by the die with exactly the same shape of the part.Whereas in stamping,in most cases,the blank has a certain degree of freedom, only one surface of the blank contacts with the die.In some extra cases, such as the forming of the suspended region of sphere or cone,and curling at the end of tube, neither sides of the blank on the deforming zone contact with the die. The deformation in these regions are caused and controlled the die applying an external force to its adjacent area.Due to the characteristics of stamping deformation and mechanics mentioned above,the stamping technique is different from the bulk metal forming:(1) The importance of the strength and rigidity of the die in stamping forming is less than that in bulk forming because the blank can be formed without applying large pressure unit area on its surface.Instead,the techniques of the simple die and the pneumatic and hydraulic forming are developed.(2) Due to the plane stress or simple strain state in comparison with bulk forming,more research on deformation or force and power parameters has been done, stamping forming canbe performed by more reasonable scientific methods.Based on the real time measurement and analysis on the sheet metal properties and stamping parameters, by means of computer and some modem testing apparatus research on the intellectualized control of stamping process is also in proceeding.(3) It is shown that there is a close relationship between stamping forming and raw material. The research on the properties of the stamping forming,that is,forming ability and shape stability, has become a key point in stamping technology. The research on the properties of the sheet metal stamping not only meets the need of the stamping technology development,but also enhances the manufacturing technique of iron and steel industry, and provides a reliable foundation for increasing sheet metal quality.3 China's mold industry and its development trendDue to historical reasons for the formation of closed, "big and complete" enterprise features, most enterprises in China are equipped with mold workshop, in factory matching status since the late 70s have a mold the concept of industrialization and specialization of production. Mold production industry is small and scattered, cross-industry, capital-intensive, professional, commercial and technical management level are relatively low.According to incomplete statistics, there are now specialized in manufacturing mold, the product supporting mold factory workshop (factory) near 17 000, about 600 000 employees, annual output value reached 20 billion yuan mold. However, the existing capacity of the mold and die industry can only meet the demand of 60%, still can not meet the needs of national economic development. At present, the domestic needs of large, sophisticated, complex and long life of the mold also rely mainly on imports. According to customs statistics, in 1997 630 million U.S. dollars worth of imports mold, not including the import of mold together with the equipment; in 1997 only 78 million U.S. dollars export mold. At present the technological level of China Die & Mould Industry and manufacturing capacity, China's national economy in the weak links and bottlenecks constraining sustainable economic development.3.1 Research on the Structure of industrial products moldIn accordance with the division of China Mould Industry Association, China mold is divided into 10 basic categories, which, stamping die and plastic molding two categoriesaccounted for the main part. Calculated by output, present, China accounts for about 50% die stamping, plastic molding die about 20%, Wire Drawing Die (Tool) about 10% of the world's advanced industrial countries and regions, the proportion of plastic forming die die general of the total output value 40%.Most of our stamping die mold for the simple, single-process mode and meet the molds, precision die, precision multi-position progressive die is also one of the few, die less than 100 million times the average life of the mold reached 100 million times the maximum life of more than accuracy 3 ~ 5um, more than 50 progressive station, and the international life of the die 600 million times the highest average life of the die 50 million times compared to the mid 80s at the international advanced level.China's plastic molding mold design, production technology started relatively late, the overall level of low. Currently a single cavity, a simple mold cavity 70%, and still dominant.A sophisticated multi-cavity mold plastic injection mold, plastic injection mold has been able to multi-color preliminary design and manufacturing. Mould is about 80 million times the average life span is about, the main difference is the large deformation of mold components, excess burr side of a large, poor surface quality, erosion and corrosion serious mold cavity, the mold cavity exhaust poor and vulnerable such as, injection mold 5um accuracy has reached below the highest life expectancy has exceeded 20 million times, the number has more than 100 chamber cavity, reaching the mid 80s to early 90s the international advanced level.3.2 mold Present Status of TechnologyTechnical level of China's mold industry currently uneven, with wide disparities. Generally speaking, with the developed industrial countries, Hong Kong and Taiwan advanced level, there is a large gap.The use of CAD / CAM / CAE / CAPP and other technical design and manufacture molds, both wide application, or technical level, there is a big gap between both. In the application of CAD technology design molds, only about 10% of the mold used in the design of CAD, aside from drawing board still has a long way to go; in the application of CAE design and analysis of mold calculation, it was just started, most of the game is still in trial stages and animation; in the application of CAM technology manufacturing molds, first, the lack of advanced manufacturing equipment, and second, the existing process equipment (including the last 10years the introduction of advanced equipment) or computer standard (IBM PC and compatibles, HP workstations, etc.) different, or because of differences in bytes, processing speed differences, differences in resistance to electromagnetic interference, networking is low, only about 5% of the mold manufacturing equipment of recent work in this task; in the application process planning CAPP technology, basically a blank state, based on the need for a lot of standardization work; in the mold common technology, such as mold rapid prototyping technology, polishing, electroforming technologies, surface treatment technology aspects of CAD / CAM technology in China has just started. Computer-aided technology, software development, is still at low level, the accumulation of knowledge and experience required. Most of our mold factory, mold processing equipment shop old, long in the length of civilian service, accuracy, low efficiency, still use the ordinary forging, turning, milling, planing, drilling, grinding and processing equipment, mold, heat treatment is still in use salt bath, box-type furnace, operating with the experience of workers, poorly equipped, high energy consumption. Renewal of equipment is slow, technological innovation, technological progress is not much intensity. Although in recent years introduced many advanced mold processing equipment, but are too scattered, or not complete, only about 25% utilization, equipment, some of the advanced functions are not given full play.Lack of technology of high-quality mold design, manufacturing technology and skilled workers, especially the lack of knowledge and breadth, knowledge structure, high levels of compound talents. China's mold industry and technical personnel, only 8% of employees 12%, and the technical personnel and skilled workers and lower the overall skill level. Before 1980, practitioners of technical personnel and skilled workers, the aging of knowledge, knowledge structure can not meet the current needs; and staff employed after 80 years, expertise, experience lack of hands-on ability, not ease, do not want to learn technology. In recent years, the brain drain caused by personnel not only decrease the quantity and quality levels, and personnel structure of the emergence of new faults, lean, make mold design, manufacturing difficult to raise the technical level.3.3 mold industry supporting materials, standard parts of present conditionOver the past 10 years, especially the "Eighth Five-Year", the State organization of the ministries have repeatedly Material Research Institute, universities and steel enterprises, research and development of special series of die steel, molds and other mold-specific carbide special tools, auxiliary materials, and some promotion. However, due to the quality is not stable enough, the lack of the necessary test conditions and test data, specifications andvarieties less, large molds and special mold steel and specifications are required for the gap. In the steel supply, settlement amount and sporadic users of mass-produced steel supply and demand contradiction, yet to be effectively addressed. In addition, in recent years have foreign steel mold set up sales outlets in China, but poor channels, technical services support the weak and prices are high, foreign exchange settlement system and other factors, promote the use of much current.Mold supporting materials and special techniques in recent years despite the popularization and application, but failed to mature production technology, most still also in the exploratory stage tests, such as die coating technology, surface treatment technology mold, mold guide lubrication technology Die sensing technology and lubrication technology, mold to stress technology, mold and other anti-fatigue and anti-corrosion technology productivity has not yet fully formed, towards commercialization. Some key, important technologies also lack the protection of intellectual property.China's mold standard parts production, the formation of the early 80s only small-scale production, standardization and standard mold parts using the coverage of about 20%, from the market can be assigned to, is just about 30 varieties, and limited to small and medium size. Standard punch, hot runner components and other supplies just the beginning, mold and parts production and supply channels for poor, poor accuracy and quality.3.4 Die & Mould Industry Structure in Industrial OrganizationChina's mold industry is relatively backward and still could not be called an independent industry. Mold manufacturer in China currently can be divided into four categories: professional mold factory, professional production outside for mold; products factory mold factory or workshop, in order to supply the product works as the main tasks needed to die; die-funded enterprises branch, the organizational model and professional mold factory is similar to small but the main; township mold business, and professional mold factory is similar. Of which the largest number of first-class, mold production accounts for about 70% of total output. China's mold industry, decentralized management system. There are 19 major industry sectors manufacture and use of mold, there is no unified management of the department. Only by China Die & Mould Industry Association, overall planning, focus on research, cross-sectoral, inter-departmental management difficulties are many.Mold is suitable for small and medium enterprises organize production, and our technical transformation investment tilted to large and medium enterprises, small and medium enterprise investment mold can not be guaranteed. Including product factory mold shop, factory, including, after the transformation can not quickly recover its investment, or debt-laden, affecting development.Although most products factory mold shop, factory technical force is strong, good equipment conditions, the production of mold levels higher, but equipment utilization rate.Price has long been China's mold inconsistent with their value, resulting in mold industry "own little economic benefit, social benefit big" phenomenon. "Dry as dry mold mold standard parts, standard parts dry as dry mold with pieces of production. Dry with parts manufactured products than with the mold" of the class of anomalies exist.4 EngineeringEngineering is the discipline, art and profession of acquiring and applying scientific, mathematical, economic, social, and practical knowledge to design and build structures, machines, devices, systems, materials and processes that safely realize solutions to the needs of society.The American Engineers' Council for Professional Development (ECPD, the predecessor of ABET) has defined "engineering" as:The creative application of scientific principles to design or develop structures, machines, apparatus, or manufacturing processes, or works utilizing them singly or in combination; or to construct or operate the same with full cognizance of their design; or to forecast their behavior under specific operating conditions; all as respects an intended function, economics of operation and safety to life and property.One who practices engineering is called an engineer, and those licensed to do so may have more formal designations such as Professional Engineer, Chartered Engineer, Incorporated Engineer, or European Engineer. The broad discipline of engineering encompasses a range of more specialized subdisciplines, each with a more specific emphasis on certain fields of application and particular areas of technology.4.1 Engineering HistoryThe concept of has existed since ancient times as humans devised fundamental inventions such as the pulley, lever, and wheel. Each of these inventions is consistent with the modern definition of engineering, exploiting basic mechanical principles to develop useful tools and objects.The term engineering itself has a much more recent etymology, deriving from the word engineer, which itself dates back to 1325, when an engine’er (literally, one who operates an engine) originally referred to “a constructor of military engines.” In this context, now obsolete, an “engine” referred to a military machine, i.e., a mechanical contraption used in war (for example, a catapult). Notable exceptions of the obsolete usage which have survived to the present day are military engineering corps, e.g., the U.S. Army Corps of Engineers.The word “engine” itself is of even older origin, ultimately deriving from the Latin ingenium (c. 1250), meaning “innate quality, especially mental power, hence a clever invention.”Later, as the design of civilian structures such as bridges and buildings matured as a technical discipline, the term civil engineering entered the lexicon as a way to distinguish between those specializing in the construction of such non-military projects and those involved in the older discipline of military engineering.4.2 Ancient eraThe Pharos of Alexandria, the pyramids in Egypt, the Hanging Gardens of Babylon, the Acropolis and the Parthenon in Greece, the Roman aqueducts, Via Appia and the Colosseum, Teotihuacán and the cities and pyramids of the Mayan, Inca and Aztec Empires, the Great Wall of China, among many others, stand as a testament to the ingenuity and skill of the ancient civil and military engineers.The earliest civil engineer known by name is Imhotep. As one of the officials of the Pharaoh, Djosèr, he probably designed and supervised the construction of the Pyramid ofDjoser (the Step Pyramid) at Saqqara in Egypt around 2630-2611 BC. He may also have been responsible for the first known use of columns in architecture[citation needed].Ancient Greece developed machines in both the civilian and military domains. The Antikythera mechanism, the first known mechanical computer, and the mechanical inventions of Archimedes are examples of early mechanical engineering. Some of Archimedes' inventions as well as the Antikythera mechanism required sophisticated knowledge of differential gearing or epicyclic gearing, two key principles in machine theory that helped design the gear trains of the Industrial revolution, and are still widely used today in diverse fields such as robotics and automotive engineering.Chinese, Greek and Roman armies employed complex military machines and inventions such as artillery which was developed by the Greeks around the 4th century B.C., the trireme, the ballista and the catapult. In the Middle Ages, the Trebuchet was developed.4.3 Renaissance eraThe first electrical engineer is considered to be William Gilbert, with his 1600 publication of De Magnete, who was the originator of the term "electricity".The first steam engine was built in 1698 by mechanical engineer Thomas Savery. The development of this device gave rise to the industrial revolution in the coming decades, allowing for the beginnings of mass production.With the rise of engineering as a profession in the eighteenth century, the term became more narrowly applied to fields in which mathematics and science were applied to these ends. Similarly, in addition to military and civil engineering the fields then known as the mechanic arts became incorporated into engineering.4.4 ModernThe International Space Station represents a modern engineering challenge from many disciplines.Electrical engineering can trace its origins in the experiments of Alessandro Volta in the 1800s, the experiments of Michael Faraday, Georg Ohm and others and the invention of the electric motor in 1872. The work of James Maxwell and Heinrich Hertz in the late 19thcentury gave rise to the field of Electronics. The later inventions of the vacuum tube and the transistor further accelerated the development of electronics to such an extent that electrical and electronics engineers currently outnumber their colleagues of any other Engineering specialty.The inventions of Thomas Savery and the Scottish engineer James Watt gave rise to modern Mechanical Engineering. The development of specialized machines and their maintenance tools during the industrial revolution led to the rapid growth of Mechanical Engineering both in its birthplace Britain and abroad.Chemical Engineering, like its counterpart Mechanical Engineering, developed in the nineteenth century during the Industrial Revolution. Industrial scale manufacturing demanded new materials and new processes and by 1880 the need for large scale production of chemicals was such that a new industry was created, dedicated to the development and large scale manufacturing of chemicals in new industrial plants. The role of the chemical engineer was the design of these chemical plants and processes.Aeronautical Engineering deals with aircraft design while Aerospace Engineering is a more modern term that expands the reach envelope of the discipline by including spacecraft design. Its origins can be traced back to the aviation pioneers around the turn of the century from the 19th century to the 20th although the work of Sir George Cayley has recently been dated as being from the last decade of the 18th century. Early knowledge of aeronautical engineering was largely empirical with some concepts and skills imported from other branches of engineering.The first PhD in engineering (technically, applied science and engineering) awarded in the United States went to Willard Gibbs at Yale University in 1863; it was also the second PhD awarded in science in the U.S.Only a decade after the successful flights by the Wright brothers, the 1920s saw extensive development of aeronautical engineering through development of World War I military aircraft. Meanwhile, research to provide fundamental background science continued by combining theoretical physics with experiments.In 1990, with the rise of computer technology, the first search engine was built by computer engineer Alan Emtage.。
模具制造论文中英文对照资料外文翻译文献

中英文对照资料外文翻译文献英文原文:High-speed cutting processing in mold manufactureapplicationAbstractThe current mold application is widespread, also had the very big development with it related die making technology. At present, used the high-speed cutting production mold already to become the die making the general trend. In some mold Manufacturer, the high speed engine bed big area substitution electrical discharge machine, the high-speed cutting production mold already gradually became the die making the general trend. It can improve mold's size, the shape and the surface roughness, reduces even omits the manual sharpening, thus reduces production cost and the reduction manufacturing cycle. This article through to the traditional mold processing craft and the high speed mold processing craft's contrast, elaborated the high-speed cutting processing superiority. In the article also briefly introduced the high-speed cutting processing in the processing craft aspect key technologies.Keywords High-speed cutting Grinding tool Grinding tool processing Process technology1 Introduction1.1 IntroductionAlong with the advance in technology and the industry swift development, the mold already became in the industrial production to use the extremely widespread main craft to equip now. The mold takes the important craft equipment, in Industry sectors and so on consumable, electric appliance electron, automobile, airplane manufacture holds the pivotal status. The manufactured products components rough machining 75%, the precision work 50% and the plastic parts 90% will complete by the mold. At present the Chinese mold market demand has reached 50,000,000,000 Yuan scales, our country die making market potential is huge. The mold is one kind of special-purpose tool, uses in forming () each metal or the nonmetallic material needs the components the shape product, this kind of special-purpose tool general designation mold. The mold is in the industrial production the most foundation equipment, is realizes the few cuttings and the non-cutting essential tool. The mold has widely used in the industrial production each domain, like the automobile, the motorcycle, the domestic electric appliances, the instrument, the measuring appliance, the electron and so on, in them 60%~80% components need the mold to carry on the manufacture; The highly effective production in enormous quantities's, bolt, nut and gasket standard letters and so on plastic also need the mold to produce; The engineering plastics, the powder metallurgy, the rubber, the alloy compression casting, the glass formation and so on need to use the mold to take shape.1.2 High-speed cutting process technologyAs the name suggests, the high-speed cutting, first is the high speed, namely must have the high spindle speed, for instance 12000r/min, 18000r/min, 30000r/min, 40000r/min, even also had a higher rotational speed still in the experiment; On the other hand, should also have the bigger to feed quantity, like 30000mm/min, 40000mm/min, even 60000mm/min; Has is after again the rapid traverse, trades fast the knife, the main axle trade the knife, from the static state arrives its needs rotational speed rise time and so on, only then achieved the above standards to be able to call it high speed.Next is must aim at the different processing object, the different degree of hardness, thedifferent material quality, the different shape to choose the corresponding reasonable parameter, but cannot pursue constantly to be high speed and be high speed, regarding the die space processing, the shape is specially complex, but the cutting tool diameter is also small time, because cutting tool's path is not the simple translation, but is the curve, even has right angle corner time, technological parameter rational especially important, if because wants to maintain the identical feed rate carries on the orthogonal cutting, will not be able to do well will cause as a result of the engine bed moving part's huge inertia the cutting tool will make when the bend angle movement to break suddenly, but the variable motion can, becauseMovements and so on acceleration and deceleration create the thickness of cutting the instantaneous change, but causes the cutter change to enable the work piece surface to have cuts, from this causes the processing drop in quality, therefore, in view of the different processing object, needs the programmers to choose the reasonable cutting tool path, optimized cutting parameter; On the other hand, according to needs to choose the suitable cutting velocity, only then can display the high-speed cutting truly like the strong point.The high-speed cutting (HSC) is an advanced technique of manufacture which for the past ten years rapidly rises. Because the high-speed cutting technology has the cutting efficiency to be high, the processing quality high, can process the hard steel stock and the good efficiency directly, causes profession and so on aviation, mold, automobile, light industry and information production efficiencies and the manufacture quality obviously enhances, and causes the processing craft and the equipment corresponding renewal. Therefore is similar to the numerical control technology is the same, the high-speed cutting and the high speed processing have become in the 21st century a machine-building industry influence profound technological revolution. At present, adapts the HSC request high speed machining center and other high speed numerically-controlled machine tool has assumed the popularization tendency in the developed country, our country recently is also speeding up the development.The high-speed cutting processing is faces for the 21st century a high technology and new technology, it is one kind is different with the traditional processing processing way. Compares with it, the high-speed cutting processing main axle rotational speed high, cuts high for the speed, the cutting quantity is small, but in the unit time material excises the quantity to increase 3 ~ 6 times actually. It take the high efficiency, the high accuracy and the high surface quality as the basic characteristic, in profession and so on in automobile industry, aerospace, mold manufacture and instrument measuring appliance has obtained the increasingly widespread application, and has obtained the significant technology economic efficiency, is the contemporary advanced manufacture technology important constituent.When with traditional way processing mold, often uses the electric spark machining, but the electrode design and makes itself is the technological process which time-consuming takes the trouble. But after uses the high-speed cutting processing, because the narrow and small region processing realization and the high grade superficial result, let the electrode the utilization ratio reduce greatly. Moreover, makes the electrode with the high speed mill also to be possible to make the production efficiency to enhance to a new scale.The major part mold may use the high-speed cutting technology to process, like the forging die, the compression casting mold, cast with the blow molding mold and so on. Hammers the cavity body shallowly, the cutting tool life is long; Compression casting mold size moderate, the productivity is high; Casts with the blow molding mold general size small, quite is economical.2 the high-speed cutting processing mold relative traditionprocesses the mold the superiority2.1 Enhances the productivityIn the high-speed cutting the main axle rotational speed and enters for the speed enhancement, may enhance material removing rate. At the same time, theThe high-speed cutting processing permission use big to feed rate, enhances 5~10 times compared to the convention machining, the unit interval/unit time material excision rate may enhance 3~6 times, the process period may reduce greatly. This may use in processing needs to excise the metal massively the components, specially has the very vital significance regarding the aviation industry.2.2 Improvement processing precishon and surface qualhtyThe high rpeed engine bed must have high performance and so on rigidity and high accuracy, at the same time because cutting force low, the work piece thermal deformation reduces, the cutting tool distorts slightly, the high-speed cutting processing precision Is very high. Depth of cut small, but enters for the speed quickly, the processing surface roughness is very small, cuts when the aluminum alloy may reach Ra0.4 ~ 0.6, when cutting steel stock may reach Ra0.2 ~ 0.4.Compares with the conventional cutting, when high-speed cutting processing the cutting force may reduce 30% at least, this may reduce the processing regarding the processing rigidity bad components to distort, causes some thin wall class fine work piece the machining into possible. Because revolves high speed time the cutting tool cuts the excitation frequency is far away from the craft system's forced oscillation, has guaranteed the good processing condition. Because the cutting force is too small, cut the hot influence to be small, causes the cutting tool, the work piece distortion to be small, maintained the size accuracy, moreover also caused the friction between the cutting tool work piece changes is small, the cutting destruction level thinned, the residual stress was small, has realized the high accuracy, the low roughness processing.2.3 The reduced cutting produces quantity of heatBecause the high-speed cutting processing is the shallow cutting, simultaneously the feed rate is very quick, the knife edge and the work piece contact length and the contact duration were short,reduced the knife edge and the work piece heat conduction, has avoided when the traditional processing met everywhere in the cutting tool and the work piece to have the big calorimetry shortcoming, guaranteed that the cutting tool worked under the temperature not high condition, lengthened cutting tool's service life. As shown in Figure 1, A is time the high-speed cutting processing heat conduction process, B is the traditional processing heat conduction process.Fig.1 high speed processing and traditional processing heat conductionThe high-speed cutting processing process is extremely rapid, 95% above cutting quantity of heat are extremely few, components not because the temperature rise will cause the warp or the inflation distortion. The high-speed cutting is suitable specially for the processing easy thermal deformation components. Is low regarding the processing melting point the metal which, easy to oxidize (for example magnesium), the high-speed cutting has certain significance.2.4 advantageoued in the processing thin wall componentsTime high-speed cutting's cutting force is small, has the high stability, but the high quality processes the thin wall components. Uses as shown in Figure 2 the lamination down milling the processing method, but high-speed cutting wall thickness 0.2mm, wall high 20mm thin wall components. This time, the knife edge and the work piece contact duration was short, has avoided the sidewall distortion.Figure.2 high-speed cutting thin wall components2.5 change the part substitutes certain crafts, like electric spark machining, abrasive machining and so onHigh strength and the high degree of hardness's processing is also a high-speed cutting major characteristic, at present, the high-speed cutting has been possible the work hardness to reach HRC60 the components, therefore, the high-speed cutting can process after the heat treatment hardens the work piece. In the tradition processes in mold's craft, before the precision work, hardens the work piece after the heat treatment to carry on the electric spark machining, may omit in the die making craft with the high-speed cutting processing substitution tradition cutting's processing method the electric spark machining, simplified the processing craft and the cost of investment.the mold's size, the shape and the surface roughness are very important, if after processing the mold cannot meet the requirements the quality precision, needs the massive handworks to rub repairs the work, the handwork rubs repairs can obtain the good surface quality, but it will affect mold's size and the shape precision. Therefore must omit as far as possible in the mold processing rubs manually repairs, improves the mold quality, reduces the production cost and the manufacturing cycle.Figure 3 is the traditional mold processing process: The semifinished materials -> rough machining -> semi-finishing -> heat treatment hardens -> the electric spark machining -> precision work -> to rub manually repairs. Figure 4 is the high speed mold processing process: Hardened semifinished materials -> rough machining -> semi-finishing -> precision work.Figure.3 the traditional mold processes processFigure 4 the high speed mold processes processin Figure 4, in the high speed mold machining process reduced two technological processes,probably reduces the process period 30%~50%. In the traditional processing craft's electric spark machining forms the hardened level easily in the melting processing surface layer, degree of hardness may reach 1000Hv, brings the difficulty for the following machining and the abrasive machining. The electric spark machining also easy to cause the surface layer fatigue cracking and cutting tool's breakage.2.6 Economic efficiency remarkable enhancementSynthesis above all sorts of merits, namely: The comprehensive efficiency will improve, the quality enhances, the working procedure simplifies, the engine bed investment and the cutting tool investment as well as the maintenance cost increase and so on, will use the high-speed cutting craft to cause the synthesis economic efficiency remarkable enhancement.3 high-speed cutting processing craft essential technologyThe high speed engine bed and the high speed cutter are the realization high-speed cutting premise and the basic condition, has the strict request in the high-speed cutting processing to the high speed engine bed performance and the cutting tool material choice.In order to realize the high-speed cutting processing, uses the high flexible high speed numerical control engine bed, the processing center generally, also some use special-purpose high speed mills, drilling machine. At the same time the engine bed has the high speed main axle to be systematic and the high rapid advance or progress gives the system, the high main axle rigidity characteristic, the high accuracy localization function and the high accuracy insert makes up the function, specially the circular arc high accuracy inserts makes up the function.The high-speed cutting cutting tool and ordinary processes the cutting tool the material to have is very greatly different. The main use cutting tool material has the hard alloy, the crystal combination diamond (PCD), the crystal combination cube boron nitride (PCBN) and the ceramics and so on.The high-speed cutting craft technology also is carries on the high-speed cutting processing the key. The cutting method chooses is improper, can make the cutting tool to intensify the attrition, cannot achieve the high speed processing completely the goal. The practice proved, if only then the high speed engine bed and the cutting tool but do not have the good craft technology to make the instruction, the expensive high-speed cutting processing equipment cannot fully play the role. The high-speed cutting processing craft essential technology mainly includes the cutting method and the cutting parameter choice optimization.a. Cutting way choiseIn the high-speed cutting processing, should select the down milling processing as far as possible, because in down milling time, the cutting tool just cut into the thickness of chip which the work piece produces to a big way, afterward reduces gradually. When up milling, the cutting tool just cut into the thickness of chip which the work piece produces to be smallest, afterward the accumulation, increased the cutting tool and the work piece friction like this gradually, has the big calorimetry on the knife edge, therefore produces in the up milling quantity of heat when down milling are more than, the radial force also greatly increases. Meanwhile in the down milling, the knife edge main compression stress, but when the up milling the knife edge tension stress, the stressful condition is bad, reduced cutting tool's service life, the down milling and the up milling the cutting tool cuts into the work piece the process, as shown in Figure 5.Figure.5 the cutting tool cuts into the work piece the process hintb. Maintains constant metal removing rateThe high-speed cutting processing is shallowly suitable for shallowly to cut the depth, the depth of cut should not surpass 0.2/ 0.2mm (ae/Ap), this is for avoids the cutting tool the position deviation, guarantees processes the mold the geometry precision. Maintains constant metal removing rate, guaranteed adds on the work piece the cutting load is constant, by obtains following several good processing effect: (1) may maintain constant cutting load; (2) may maintain the scrap size constant; (3) has the good hot shift; (4) the cutting tool and the work piece maintain at the cold condition; (5) does not need skilled to operate for the quantity and the main axle rotational speed;(6) may lengthen the cutting tool the life; (7) can guarantee the good processing quality and so on.c.choice of the Feeds wayRegarding has opens the mouth die space the region, feeds as far as possible from material outside, by real-time analysis material cutting condition. But regarding does not have the die space enclosed area, selects the screw feed method, cuts into the local region.d. As far as possible reduced cutting tool's commutation rapidlyReduces the cutting tool as far as possible the rapidly commutation, because the zigzag pattern mainly applies in the traditional processing, mainly chooses the return route or the sole way cutting in the high-speed cutting processing. This is because in commutation time the NC engine bed must stop (urgently changing down) immediately then the again execution next step of operation. As a result of engine bed acceleration limitation, but is easy to create the time the waste, stops anxiously or whips then can destroy the surface roughness, also has the possibility because has cut but produces the broach or in the outside undercut. Chooses the sole way cutting pattern to carry on the down milling, does not sever the cutting process and the cutting tool way as far as possible, reduces the cutting tool to cut into as far as possible cuts the number of times, by obtains the relatively stable cutting process.For example, in the cutting mold corner processing, the traditional processing method is usesthe translation (G1), when the cutting tool cuts to the fillet place, the velocity of movement reduces speed, at the same time when enters for the commutation the cutting tool movement is not continuously, can have the massive friction and the quantity of heat in the intermittent process, if processes the aluminum alloy or other light metal alloys, produces the quantity of heat will damage the work piece surface quality.If uses the high-speed cutting processing the method, the use is smaller than the cutting mold corner radius cutting tool, the use high speed engine bed high accuracy circular arc inserts makes up the function (G2, G3) processes the mold corner, the high speed engine bed circular arc inserts makes up the movement is the continuous process, cannot have the cutting tool intermittent motion, thus reduced the cutting tool and the mold contact length and the time, avoids having the massive heat.e In Z direction cutting continual planeThe traditional processing die space's method uses the profile milling, this processing way increased the cutting tool to cut into, to cut the work piece the number of times, has affected the work piece surface quality, has limited the engine bed and the cutting tool formidable function display. In the high-speed cutting processing, often uses the Z direction cutting continual plane. Uses step pitch which is smaller than the convention, thus reduces each tooth cutting elimination quantity, the improvement processing surface's quality, reduced the process period.4 High-speed cutting process technology in die makingapplicationThe high-speed cutting process technology has a series of characteristics and the production benefit aspect's great potential, already becomes country competition research and so on Germany, US and Japan important areas of technology. Now, US, Germany, Japan, France, Switzerland, Italy produce the different specification's each kind of commercialization high speed engine bed already entered the market, applies in the airplane, the automobile and the die making.Along with the high-speed cutting process technology introduction mold industry, has had the very tremendous influence to the traditional mold processing craft, changed the mold processing technical process. Because the mold profile is the very complex free surface generally, and degree of hardness is very high, uses conventional the machining method to satisfy the precision and the shape request with difficulty. The conventional processing method is after the annealing carries on the milling processing, then carries on the heat treatment, the grinding or the electric spark machining, finally the manual polish, polishing, cause the processing cycle to be very long like this. Specially the manual process period, must account for the entire processing cycle to be very big a part. HSC may achieve the accuracy requirement which the mold processes, reduced has even cancelled the manual processing, because and new cutting tool material (for example PCD, PCBN, cermet and so on) the appearance, HSC may the work hardness achieve HRC60, even degree of hardness higher work piece material, after might process hard mold, substitution electric spark machining and abrasive machining.The high speed milling processing has the highly effective high accuracy in the die making as well as may process the high hard material the merit, already obtained the widespread application in the industrially advanced country. The high-speed cutting process technology introduction mold industry, mainly applies in the following several aspects:1) hard mold die space direct processing. After using the high-speed cutting to be possible to process the hard material the characteristic direct processing hard mold die space, improved the quality which and the efficiency the mold processes, may substitute for the electric spark machining.(2) EDM (electric spark) electrode processing. Applied the high-speed cutting technology processing electrode to raise the electric spark machining efficiency to play the very major role. The high-speed cutting electrode improved electrode's surface quality and the precision, reduced the following working process.3) fast sample workpiece manufacture. Uses the high-speed cutting processing efficiencyhigh characteristic, may use in processing the plastic and the aluminum alloy model. After the CAD design produces the 3D full-scale mockup fast, is higher than the fast prototype manufacture efficiency, the quality is good.(4) mold's fast repair. The mold often needs to repair in the use process, lengthens the service life, in the past was mainly completes depending on the electrical finishing, now uses the high speed processing to be possible to complete this work quickly, moreover might use the original NC procedure, did not need to establish.5 ConclusionThe high-speed cutting processing uses the high cutting velocity and the feed rate, the small radial direction and the axial depth of cut, the cutting force is small, the processing surface roughness is very small, cutting tool life enhancement; With the high-speed cutting processing way substitution tradition processing way processing mold, might omit the electric spark machining and rub manually repairs, raised the productivity which the mold processed, reduced the production cost, reduced the processing cycle; When research high-speed cutting processing, must unify closely with the high-speed cutting processing technology, realizes the high efficiency, the high accuracy truly and the redundant reliable goal.The high-speed cutting process technology is the advanced technique of manufacture, has the broad application prospect. Replaces EDM with the high-speed cutting processing (or majority of replaces) speeds up the mold development speed, realizes the craft update major step. The promoted application high-speed cutting process technology applies in the mold manufacturing industry, not only may enhance the machine-finishing large scale the efficiency, the quality, reduces the cost, moreover may lead a series of high technology and new technology industry the development. Therefore, current strengthens the high-speed cutting technology the basic research, establishes the high-speed cutting database, the high-speed cutting safety work standard, enhances the engine bed and tool profession development innovation ability, speeds up the high-speed cutting cutting tool system, the high-speed cutting engine bed system's research development and the industrial production, already was the urgent matter.References[1] A.C. Low, J.W. Kyle, Grinding tool technology recent development, The Mechanical Engineers Association, London, 1986. High-speed cutting and grinding tool manufacture[2] K.L. Johnson, High-speed cutting and grinding tool manufacture, Cambridge University Press, Cambridge, 1985.[3] W.DMay, E.L. Morris, D. Atack, new using of Cutting technology, Applied Physics 30 (1959) 1713–1724.[4] S.C. Hunter, Grinding tool manufacture, Applied Mechanics 28 (1961) 611–617.[5] G. Lodewijks, Dynamics of Belt Systems, Thesis, Delft University of Technology, Delft, 1995.[6] A.N. Gent, High-speed cutting outline, Carl Hanser Verslag, 2001.中文翻译高速切削加工在模具制造中的新应用摘要当前模具应用广泛,与之相关的模具制造技术也有了很大的发展。
模具制造中英文翻译

Modern mold makingI.The stamping die development history and status of technologyIn 1953, the Changchun First Automobile Works in China for the first time established a die shop, the car plant in 1958 began manufacturing automotive panel die. 60 years of the 20th century began producing fine blanking dies. Come a long road of development, China has formed about 300 billion (not including Hong Kong, Macao and Taiwan statistics.) Production capacity of various types of stamping dies. Formed, such as Ningbo and Zhejiang HUANGYAN region "Die village"; Guangdong Corporation and some large rapid rise of township enterprises, K el o n, M id e a, K on ka and other groups have established their own mold manufacturing center; joint ventures and wholly foreign-owned the mold companies now have thousands. With the pace with international standards continues to accelerate, increasing market competition, production and design of the mold has been growing recognition that product quality, cost, and new product development capacities. Mold manufacturing technology to measure a country's manufacturing sector has become an important indicator of the level, and largely determine the survival space. At present, China stamping die, whether in quantity or in quality, technology and other capabilities have made significant progress, but with national needs and the world advanced level, the gap is still great. In the international competition situation, I had the mold industry has rapidly developed, many specialized research centers continue to die set up, mold steel of the structure and made significant achievements, but there is still a big gap. First, imports of high-tech mold most of the large precision molds, mold and exports most of the lower middle and low-tech die, so high-tech high-grade die stamping die market, the overall satisfaction rate is lower than satisfaction rate, which mold development has lagged behind the production of stamping parts, and low-technology market to meet the rate of middle and low die stamping die is higher than the overall market to meet the rate; second is due to the price of the mold is much lower than international market prices, has some competition force, so its prospects in the international market; third in recent years, Hong Kong-and Taiwan-owned, foreign-funded enterprises in China developed rapidly in a large number of these enterprises stamping dies produced for own use no precise statistics, it is not included in the figures being.II. Modern mold manufacturing technology developmentThe development of modern technology should die mold products to meet the "short delivery time", "high precision", "good quality", "low price" request for service. Urgent need to develop to meet this requirement as a number of(1) to comprehensively promote universal DBD / DBM / DBE technologyDie DBD / DBM / DBE technology is the development direction of mold design and manufacturing. With the computer software development and progress, universal DBD / DBM / DBE technology, conditions are ripe, the businesses will increase DBD / DBM technical training and technical service efforts; further expand the scope ofDBE technology. The development of computers and networks are making DBD / DBM / DBE technology trans-regional, cross-enterprise, campus-wide in the industry as possible to promote and achieve re-integration of technical resources to enable virtual manufacturing possible.(2) High-speed millingThe development of foreign high-speed milling process in recent years, significantly improve the processing efficiency, and to get a high surface finish. In addition, the module can also be processed with high hardness, but also with low temperature rise, thermal deformation and so on. High-speed milling technology, automotive, home appliance manufacturing industry in the large cavity mold injected new vitality. It currently has more agile, intelligent, integrated direction.(3) die scanning and digitizing systemHigh-speed scanner provides scanning system and mold from the model or in kind to the processing of the scanned model of the desired number of features required, greatly reducing the manufacturing cycle in the development of mold. Some quick scan system can be quickly installed in existing CNC milling machine and machining center, for fast data acquisition, automatic generation of a variety of CNC machining process, the DBD data in different formats, for mold manufacturing "reverse engineering . "(4) the degree of standardization to improve dieDegree of standardization of the mold is increasing, estimates that the current use of standard mold coverage has reached about 30%. Developed countries is generally about 80%.(5) high-quality materials and advanced surface treatment technologyApplication of high quality steel and the corresponding surface treatment technology to improve the life of the mold it is very necessary. Mold heat treatment and surface treatment can fully mold steel material properties play a key part. Direction of development of mold heat treatment is the use of vacuum heat treatment. In addition to the mold surface should improve the development of advanced technologies such as laser surface treatment.(6) Mold PolishingAutomation, intelligent mold surface quality of mold life, the appearance of quality parts and so have a greater impact of automation and intelligence of the grinding and polishing methods replace the existing manual in order to improve the quality of the mold surface is important trends.(7) die development of automatic processing systemThis is our long-term development goals mold industry. Automatic mold machine processing system should be more than the rational combination; with accompanying plate positioning fixture or positioning; a complete equipment, tool CNC database; a complete CNC flexible synchronization system; a quality monitoringand control system. Of course, as the user to choose the right equipment, if the selection properly, not only can not make money but make the machine work into the bitter situation.III. Modern mold manufacturing technology trendsDie technology is mainly towards the future development trend of information technology, high-speed high-precision production and development. Therefore, the design technology, the development focus is to promote DBD / DBE / DBM technology, and continue to improve efficiency, especially in sheet metal forming process of the computer simulation analysis. Die DBD, DBE technology should be declared human, integration, intelligence and network direction, and improve the mold DBD, DBM system-specific level. To improve the DBD, DBE, DBM technology, establish a complete database and development of the mold expert systems and improve software usability is very important.From the processing technology, the development focused on high-speed processing and precision machining. At present, the development of highly processed high-speed milling, high speed polishing and high-speed electronic processing and rapid tooling technologies. At present, the development of precision machining parts precision mold and the surface roughness of less 1μm Pa ≤ 0.1μm variety of precision machining.IV.the modern mold manufacturing1.CAD/CAE/CAM computer-aided design, simulation, manufacturing integration CAD / CAE / CAM integration, integration technology is the most advanced modern mold making the most reasonable mode of production. Use of computer-aided design, support engineering and manufacturing systems, according to the respective mold parts designed to prepare the NC machining of parts from design to manufacturing process is an inevitable process, which is from CAD / CAE / CAM system carried out, The processing line cable input directly from the processing machine, can be used in the preparation of procedures of processing the system analog functions, will be part tool, tool holder, fixture, platform and tool speed, path, etc. are displayed, to check the program prepared correctness. In short the CAD / CAE / CAM system development and simulation of processing can not fully understand the problems identified, resulting in processing prior to prepare the complete set of processing change work, which for the efficient and accurate processing of the mold has a very important part .2. Advanced equipment in the modern mold making roleThe inevitable trend of modern mold making, machining is possible to replace the manual process, especially now that CNC lathes, multi-axis machine tools, CNC mold engraving machine, EDM machine, CNC precision grinding machines, coordinate measuring machines, scanners and other modern equipment widely used in factories, but most of these devices are basically the application of the procedures used CAD / CAE / CAM system to produce, the operator of work procedures in accordance with the provisions of work piece clamping, with a cutting tool and operation of the machine will be able to automatically complete the processing tasks,and created the ideal mold parts or complete the processing operation for the next part.3. Die materials and surface treatment technologyDue to improper selection and use of materials, resulting in premature failure of the mold, which accounts for more than 45% die failure. Price structure throughout the mold, the materials, the proportion of small, generally 20% to 30%, therefore, the choice of high quality steel and application of surface treatment technology to improve the life of the mold it is very necessary. For tool steel, the ESR technique to be used, such as the use of powder metallurgy high speed steel powders manufactured. Variety of different specifications tool steel, refined products, products of, try to shorten the delivery time is also an important trend.Mold heat treatment of the main trends: the infiltration of a single element to the multi-element penetration, complex permeability (such as TD method) development; by the general spread of the CVD, PVD, PCVD, ion penetration, ion implantation and other direction; addition, the current laser enhanced glow plasma technology and electroplating (plating) and other anti-corrosion technology to strengthen more and more attention.V.reverse engineeringReverse engineering is the first of the parts (the processing of the product) to scan the CAD data generated in multiple formats, and then in the other CAD / CAE / CAM software in the modified design, the technology is the most popular modern mold manufacturing mold manufacturing technology. mold manufacturing company dedicated to development and production of the scanning system, it can be successfully applied to reverse engineering, mold manufacturing, it can not only improve the performance of CNC machine tools, expanding the function of CNC machine tools, CNC machine tools but also improve efficiency., Renscan200, Cyclone high-speed scanner has been Qingdao H a I e r, Jinan Q I n g q i, national mold center and other units started.VI. Summary and OutlookWith the development and progress of computer software, CAD / CAE / CAM technology is getting more mature, and its application in the modern mold will become more widespread. Can be expected in the near future, mold manufacturing to separate from the machine manufacturing industry, and independent national economy to become an indispensable pillar industries, while also further promote the integration of the mold manufacturing technology, intelligence, beneficiary , efficient direction.现代模具制造一.冲压模具发展历史和技术水平状况1953年,长春第一汽车制造厂在中国首次建立了冲模车间,该汽车厂于1958年开始制造汽车覆盖件模具。
模具设计与制造大学毕业论文外文文献翻译及原文
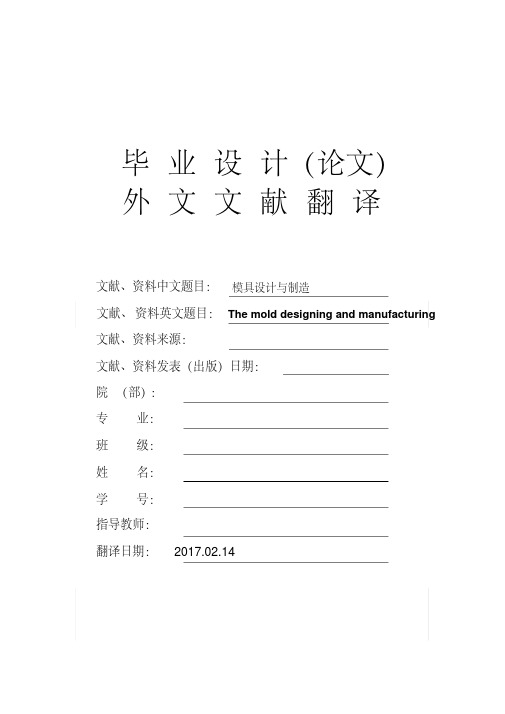
Although our country mold total quantity had at present achieved the suitable scale, the mold level also has the very big enhancement, after but design manufacture horizontal overall rise and fall industry developed country and so on Yu De, America, date, France, Italy many. The current existence question and the disparity mainly display in following several aspects:
冲压模具成型外文翻译参考文献
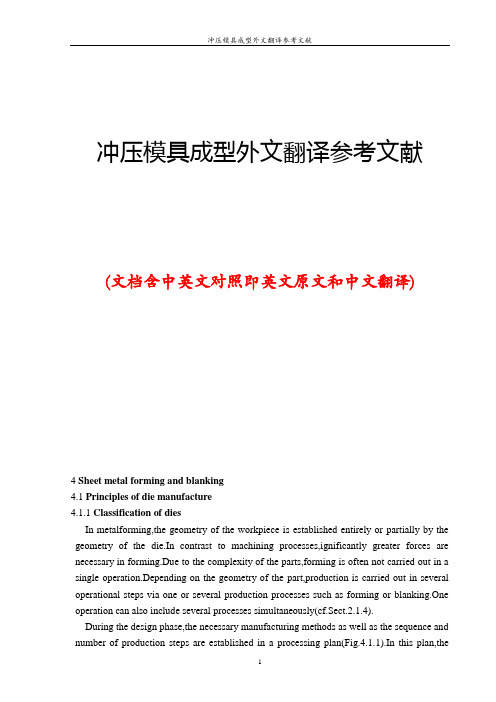
冲压模具成型外文翻译参考文献(文档含中英文对照即英文原文和中文翻译)4 Sheet metal forming and blanking4.1 Principles of die manufacture4.1.1 Classification of diesIn metalforming,the geometry of the workpiece is established entirely or partially by the geometry of the die.In contrast to machining processes,ignificantly greater forces are necessary in forming.Due to the complexity of the parts,forming is often not carried out in a single operation.Depending on the geometry of the part,production is carried out in several operational steps via one or several production processes such as forming or blanking.One operation can also include several processes simultaneously(cf.Sect.2.1.4).During the design phase,the necessary manufacturing methods as well as the sequence and number of production steps are established in a processing plan(Fig.4.1.1).In this plan,theavailability of machines,the planned production volumes of the part and other boundary conditions are taken into account.The aim is to minimize the number of dies to be used while keeping up a high level of operational reliability.The parts are greatly simplified right from their design stage by close collaboration between the Part Design and Production Departments in order to enable several forming and related blanking processes to be carried out in one forming station.Obviously,the more operations which are integrated into a single die,the more complex the structure of the die becomes.The consequences are higher costs,a decrease in output and a lower reliability.Fig.4.1.1 Production steps for the manufacture of an oil sumpTypes of diesThe type of die and the closely related transportation of the part between dies is determined in accordance with the forming procedure,the size of the part in question and the production volume of parts to be produced.The production of large sheet metal parts is carried out almost exclusively using single sets of dies.Typical parts can be found in automotive manufacture,the domestic appliance industry and radiator production.Suitable transfer systems,for example vacuum suction systems,allow the installation of double-action dies in a sufficiently large mounting area.In this way,for example,the right and left doors of a car can be formed jointly in one working stroke(cf.Fig.4.4.34).Large size single dies are installed in large presses.The transportation of the parts from oneforming station to another is carried out mechanically.In a press line with single presses installed one behind the other,feeders or robots can be used(cf.Fig.4.4.20 to 4.4.22),whilst in large-panel transfer presses,systems equipped with gripper rails(cf.Fig.4.4.29)or crossbar suction systems(cf.Fig.4.4.34)are used to transfer the parts.Transfer dies are used for the production of high volumes of smaller and medium size parts(Fig.4.1.2).They consist of several single dies,which are mounted on a common base plate.The sheet metal is fed through mostly in blank form and also transported individually from die to die.If this part transportation is automated,the press is called a transfer press.The largest transfer dies are used together with single dies in large-panel transfer presses(cf.Fig.4.4.32).In progressive dies,also known as progressive blanking dies,sheet metal parts are blanked in several stages;generally speaking no actual forming operation takes place.The sheet metal is fed from a coil or in the form of metal ing an appropriate arrangement of the blanks within the available width of the sheet metal,an optimal material usage is ensured(cf.Fig.4.5.2 to 4.5.5). The workpiece remains fixed to the strip skeleton up until the laFig.4.1.2 Transfer die set for the production of an automatic transmission for an automotive application-st operation.The parts are transferred when the entire strip is shifted further in the work flow direction after the blanking operation.The length of the shift is equal to the center line spacing of the dies and it is also called the step width.Side shears,very precise feeding devices or pilot pins ensure feed-related part accuracy.In the final production operation,the finished part,i.e.the last part in the sequence,is disconnected from the skeleton.A field of application for progressive blanking tools is,for example,in the production of metal rotors or stator blanks for electric motors(cf.Fig.4.6.11 and 4.6.20).In progressive compound dies smaller formed parts are produced in several sequential operations.In contrast to progressive dies,not only blanking but also forming operations areperformed.However, the workpiece also remains in the skeleton up to the last operation(Fig.4.1.3 and cf.Fig.4.7.2).Due to the height of the parts,the metal strip must be raised up,generally using lifting edges or similar lifting devices in order to allow the strip metal to be transported mechanically.Pressed metal parts which cannot be produced within a metal strip because of their geometrical dimensions are alternatively produced on transfer sets.Fig.4.1.3 Reinforcing part of a car produced in a strip by a compound die setNext to the dies already mentioned,a series of special dies are available for special individual applications.These dies are,as a rule,used separately.Special operations make it possible,however,for special dies to be integrated into an operational Sequence.Thus,for example,in flanging dies several metal parts can be joined together positively through the bending of certain metal sections(Fig.4.1.4and cf.Fig.2.1.34).During this operation reinforcing parts,glue or other components can be introduced.Other special dies locate special connecting elements directly into the press.Sorting and positioning elements,for example,bring stamping nuts synchronised with the press cycles into the correct position so that the punch heads can join them with the sheet metal part(Fig.4.1.5).If there is sufficient space available,forming and blanking operations can be carried out on the same die.Further examples include bending,collar-forming,stamping,fine blanking,wobble blanking and welding operations(cf.Fig.4.7.14 and4.7.15).Fig.4.1.4 A hemming dieFig.4.1.5 A pressed part with an integrated punched nut4.1.2 Die developmentTraditionally the business of die engineering has been influenced by the automotive industry.The following observations about the die development are mostly related to body panel die construction.Essential statements are,however,made in a fundamental context,so that they are applicable to all areas involved with the production of sheet-metal forming and blanking dies.Timing cycle for a mass produced car body panelUntil the end of the 1980s some car models were still being produced for six to eight years more or less unchanged or in slightly modified form.Today,however,production time cycles are set for only five years or less(Fig.4.1.6).Following the new different model policy,the demands ondie makers have also changed prehensive contracts of much greater scope such as Simultaneous Engineering(SE)contracts are becoming increasingly common.As a result,the die maker is often involved at the initial development phase of the metal part as well as in the planning phase for the production process.Therefore,a muchbroader involvement is established well before the actual die development is initiated.Fig.4.1.6 Time schedule for a mass produced car body panelThe timetable of an SE projectWithin the context of the production process for car body panels,only a minimal amount of time is allocated to allow for the manufacture of the dies.With large scale dies there is a run-up period of about 10 months in which design and die try-out are included.In complex SE projects,which have to be completed in 1.5 to 2 years,parallel tasks must be carried out.Furthermore,additional resources must be provided before and after delivery of the dies.These short periods call for pre-cise planning,specific know-how,available capacity and the use of the latest technological and communications systems.The timetable shows the individual activities during the manufacturing of the dies for the production of the sheet metal parts(Fig.4.1.7).The time phases for large scale dies are more or less similar so that this timetable can be considered to be valid in general.Data record and part drawingThe data record and the part drawing serve as the basis for all subsequent processing steps.They describe all the details of the parts to be produced. The information given in theFig.4.1.7 Timetable for an SE projectpart drawing includes: part identification,part numbering,sheet metal thickness,sheet metal quality,tolerances of the finished part etc.(cf.Fig.4.7.17).To avoid the production of physical models(master patterns),the CAD data should describe the geometry of the part completely by means of line,surface or volume models.As a general rule,high quality surface data with a completely filleted and closed surface geometry must be made available to all the participants in a project as early as possible.Process plan and draw developmentThe process plan,which means the operational sequence to be followed in the production of the sheet metal component,is developed from the data record of the finished part(cf.Fig.4.1.1).Already at this point in time,various boundary conditions must be taken into account:the sheet metal material,the press to be used,transfer of the parts into the press,the transportation of scrap materials,the undercuts as well as thesliding pin installations and their adjustment.The draw development,i.e.the computer aided design and layout of the blank holder area of the part in the first forming stage–if need bealso the second stage–,requires a process planner with considerable experience(Fig.4.1.8).In order to recognize and avoid problems in areas which are difficult to draw,it is necessary to manufacture a physical analysis model of the draw development.With this model,theforming conditions of the drawn part can be reviewed and final modifications introduced,which are eventually incorporated into the data record(Fig.4.1.9).This process is being replaced to some extent by intelligent simulation methods,through which the potential defects of the formed component can be predicted and analysed interactively on the computer display.Die designAfter release of the process plan and draw development and the press,the design of the die can be started.As a rule,at this stage,the standards and manufacturing specifications required by the client must be considered.Thus,it is possible to obtain a unified die design and to consider the particular requests of the customer related to warehousing of standard,replacement and wear parts.Many dies need to be designed so that they can be installed in different types of presses.Dies are frequently installed both in a production press as well as in two different separate back-up presses.In this context,the layout of the die clamping elements,pressure pins and scrap disposal channels on different presses must be taken into account.Furthermore,it must be noted that drawing dies working in a single-action press may be installed in a double-action press(cf.Sect.3.1.3 and Fig.4.1.16).Fig.4.1.8 CAD data record for a draw developmentIn the design and sizing of the die,it is particularly important to consider the freedom of movement of the gripper rail and the crossbar transfer elements(cf.Sect.4.1.6).These describe the relative movements between the components of the press transfer system and the die components during a complete press working stroke.The lifting movement of the press slide,the opening and closing movements of the gripper rails and the lengthwise movement of the whole transfer are all superimposed.The dies are designed so that collisions are avoided and a minimum clearance of about 20 mm is set between all the moving parts.4 金属板料的成形及冲裁4. 模具制造原理4.1.1模具的分类在金属成形的过程中,工件的几何形状完全或部分建立在模具几何形状的基础上的。
模具的历史发展外文文献翻译、中英文翻译、外文翻译
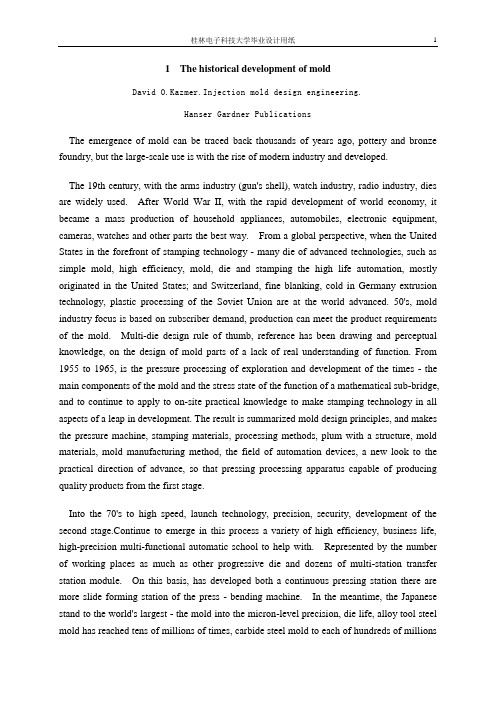
1 The historical development of moldDavid O.Kazmer.Injection mold design engineering.Hanser Gardner PublicationsThe emergence of mold can be traced back thousands of years ago, pottery and bronze foundry, but the large-scale use is with the rise of modern industry and developed.The 19th century, with the arms industry (gun's shell), watch industry, radio industry, dies are widely used. After World War II, with the rapid development of world economy, it became a mass production of household appliances, automobiles, electronic equipment, cameras, watches and other parts the best way. From a global perspective, when the United States in the forefront of stamping technology - many die of advanced technologies, such as simple mold, high efficiency, mold, die and stamping the high life automation, mostly originated in the United States; and Switzerland, fine blanking, cold in Germany extrusion technology, plastic processing of the Soviet Union are at the world advanced. 50's, mold industry focus is based on subscriber demand, production can meet the product requirements of the mold. Multi-die design rule of thumb, reference has been drawing and perceptual knowledge, on the design of mold parts of a lack of real understanding of function. From 1955 to 1965, is the pressure processing of exploration and development of the times - the main components of the mold and the stress state of the function of a mathematical sub-bridge, and to continue to apply to on-site practical knowledge to make stamping technology in all aspects of a leap in development. The result is summarized mold design principles, and makes the pressure machine, stamping materials, processing methods, plum with a structure, mold materials, mold manufacturing method, the field of automation devices, a new look to the practical direction of advance, so that pressing processing apparatus capable of producing quality products from the first stage.Into the 70's to high speed, launch technology, precision, security, development of the second stage.Continue to emerge in this process a variety of high efficiency, business life, high-precision multi-functional automatic school to help with. Represented by the number of working places as much as other progressive die and dozens of multi-station transfer station module. On this basis, has developed both a continuous pressing station there are more slide forming station of the press - bending machine. In the meantime, the Japanese stand to the world's largest - the mold into the micron-level precision, die life, alloy tool steel mold has reached tens of millions of times, carbide steel mold to each of hundreds of millionsof times p minutes for stamping the number of small presses usually 200 to 300, up to 1200 times to 1500 times. In the meantime, in order to meet product updates quickly, with the short duration (such as cars modified, refurbished toys, etc.) need a variety of economic-type mold, such as zinc alloy die down, polyurethane rubber mold, die steel skin, also has been very great development.From the mid-70s so far can be said that computer-aided design, supporting the continuous development of manufacturing technology of the times. With the precision and complexity of mold rising, accelerating the production cycle, the mold industry, the quality of equipment and personnel are required to improve. Rely on common processing equipment, their experience and skills can not meet the needs of mold. Since the 90's, mechanical and electronic technologies in close connection with the development of NC machine tools, such as CNC wire cutting machine, CNC EDM, CNC milling, CNC coordinate grinding machine and so on. The use of computer automatic programming, control CNC machine tools to improve the efficiency in the use and scope. In recent years, has developed a computer to time-sharing by the way a group of direct management and control of CNC machine tools NNC system.With the development of computer technology, computers have gradually into the mold in all areas, including design, manufacturing and management. International Association for the Study of production forecasts to 2000, as a means of links between design and manufacturing drawings will lose its primary role. Automatic Design of die most fundamental point is to establish the mold standard and design standards. To get rid of the people of the past, and practical experience to judge the composition of the design center, we must take past experiences and ways of thinking, for series, numerical value, the number of type-based, as the design criteria to the computer store. Components are dry because of mold constitutes a million other differences, to come up with a can adapt to various parts of the design software almost impossible. But some products do not change the shape of parts, mold structure has certain rules, can be summed up for the automatic design of software. If a Japanese company's CDM system for progressive die design and manufacturing, including the importation of parts of the figure, rough start, strip layout, determine the size and standard templates, assembly drawing and parts, the output NC program (for CNC machining Center and line cutting program), etc., used in 20% of the time by hand, reduce their working hours to 35 hours; from Japan in the early 80s will be three-dimensional cad / cam system for automotive panel die. Currently, the physical parts scanning input, map lines and data input,geometric form, display, graphics, annotations and the data is automatically programmed, resulting in effective control machine tool control system of post-processing documents have reached a high level; computer Simulation (CAE) technology has made some achievements. At high levels, CAD / CAM / CAE integration, that data is integrated, can transmit information directly with each other. Achieve network. Present. Only a few foreign manufacturers ca2 StampingStamping is a kind of plastic forming process in which a part is produced by means of the plastic forming of the material under the action of a die.Stamping is usually carried out under cold state, so it is also called cold stamping. Heat stamping is used only when the blank thickness is greater than 8-100mm. The blank material for stamping is usually in the form sheet or strip, and therefore it is also called sheet metal forming. Some non-metal sheets (such as plywood, mica sheet, asbestos, leather) can also be formed by stamping.Stamping is widely used in various metalworking industry, and it plays a crucial role in the industries for manufacturing automobiles, instruments, military parts and household electrical appliances, etc.The process,equipment and die are the three foundational problems that needed to be studied in stamping.The characteristics of the sheet metal forming are as follows:(1) High material utilization.(2) Capacity to produce thin-walled parts of complex shape.(3) Good interchangeability of stamping parts precision in shape and dimension.(4) Parts with lightweight,high strength and fine rigidity can be obtained.(5) High productivity, easy to operate and to realize mechanization and automatization. The manufacture of the stamping die is costly, and therefore it only fits to mass production. For the manufacture of products in small batch and rich variety, the simple stamping die and the new equipment such as a stamping machining center, are usually adopted to meet he market demands.The materials for sheet metal stamping include mild steel, copper, aluminum, magnesium alloy and high-plasticity alloy steel, etc.Stamping equipment includes plate shear and punching press. The former shears plate into strips with a definite width, which would be pressed later. The later can be used both in shearing and forming.There are various processes of stamping forming with different working patterns and names,but these processes are similar to each other in plastic deformation.There are following conspicuous characteristics in stamping:(1) The force per unit area perpendicular to the blank surface is not large but is enough to cause the material plastic deformation. It is much less than the inner stresses on the plate plane directions.In most cases stamping forming can be treated approximately as that of the plane stress state to simplify vastly the theoretical deformation mechanics analysis and the calculation of the process parameters.(2) Due to the small relative thickness,the anti-instability capability of the blank is weak under compressive stress.As a result,the stamping process is difficult to proceed successfully without using the anti-instability device (such as blank holder).Therefore the variety of the stamping processes dominated by tensile stress are more than those dominated by compressive stress.(3) During stamping forming,the inner stress of the blank is equal to or sometimes less than the yield stress of the material.In this point,the stamping is different from the bulk forming. During stamping forming,the influence of the hydrostatic pressure of the stress state in the deformation zone to the forming limit and the deformation resistance is not so important as to the bulk forming.In some circumstances,such influence may be neglected.Even in the case when this influence should be considered,the treating method is also different from that of bulk forming.(4) In stamping forming,the restrain action of the die to the blank is not severe as in the case of the bulk forming(such as die forging).In bulk forming, the constraint forming is proceeded by the die with exactly the same shape of the part.Whereas in stamping,in most cases,the blank has a certain degree of freedom, only one surface of the blank contacts with the die.In some extra cases, such as the forming of the suspended region of sphere or cone,and curling at the end of tube, neither sides of the blank on the deforming zone contact with the die. The deformation in these regions are caused and controlled the die applying an external force to its adjacent area.Due to the characteristics of stamping deformation and mechanics mentioned above,the stamping technique is different from the bulk metal forming:(1) The importance of the strength and rigidity of the die in stamping forming is less than that in bulk forming because the blank can be formed without applying large pressure unit area on its surface.Instead,the techniques of the simple die and the pneumatic and hydraulic forming are developed.(2) Due to the plane stress or simple strain state in comparison with bulk forming,more research on deformation or force and power parameters has been done, stamping forming canbe performed by more reasonable scientific methods.Based on the real time measurement and analysis on the sheet metal properties and stamping parameters, by means of computer and some modem testing apparatus research on the intellectualized control of stamping process is also in proceeding.(3) It is shown that there is a close relationship between stamping forming and raw material. The research on the properties of the stamping forming,that is,forming ability and shape stability, has become a key point in stamping technology. The research on the properties of the sheet metal stamping not only meets the need of the stamping technology development,but also enhances the manufacturing technique of iron and steel industry, and provides a reliable foundation for increasing sheet metal quality.3 China's mold industry and its development trendDue to historical reasons for the formation of closed, "big and complete" enterprise features, most enterprises in China are equipped with mold workshop, in factory matching status since the late 70s have a mold the concept of industrialization and specialization of production. Mold production industry is small and scattered, cross-industry, capital-intensive, professional, commercial and technical management level are relatively low.According to incomplete statistics, there are now specialized in manufacturing mold, the product supporting mold factory workshop (factory) near 17 000, about 600 000 employees, annual output value reached 20 billion yuan mold. However, the existing capacity of the mold and die industry can only meet the demand of 60%, still can not meet the needs of national economic development. At present, the domestic needs of large, sophisticated, complex and long life of the mold also rely mainly on imports. According to customs statistics, in 1997 630 million U.S. dollars worth of imports mold, not including the import of mold together with the equipment; in 1997 only 78 million U.S. dollars export mold. At present the technological level of China Die & Mould Industry and manufacturing capacity, China's national economy in the weak links and bottlenecks constraining sustainable economic development.3.1 Research on the Structure of industrial products moldIn accordance with the division of China Mould Industry Association, China mold is divided into 10 basic categories, which, stamping die and plastic molding two categoriesaccounted for the main part. Calculated by output, present, China accounts for about 50% die stamping, plastic molding die about 20%, Wire Drawing Die (Tool) about 10% of the world's advanced industrial countries and regions, the proportion of plastic forming die die general of the total output value 40%.Most of our stamping die mold for the simple, single-process mode and meet the molds, precision die, precision multi-position progressive die is also one of the few, die less than 100 million times the average life of the mold reached 100 million times the maximum life of more than accuracy 3 ~ 5um, more than 50 progressive station, and the international life of the die 600 million times the highest average life of the die 50 million times compared to the mid 80s at the international advanced level.China's plastic molding mold design, production technology started relatively late, the overall level of low. Currently a single cavity, a simple mold cavity 70%, and still dominant.A sophisticated multi-cavity mold plastic injection mold, plastic injection mold has been able to multi-color preliminary design and manufacturing. Mould is about 80 million times the average life span is about, the main difference is the large deformation of mold components, excess burr side of a large, poor surface quality, erosion and corrosion serious mold cavity, the mold cavity exhaust poor and vulnerable such as, injection mold 5um accuracy has reached below the highest life expectancy has exceeded 20 million times, the number has more than 100 chamber cavity, reaching the mid 80s to early 90s the international advanced level.3.2 mold Present Status of TechnologyTechnical level of China's mold industry currently uneven, with wide disparities. Generally speaking, with the developed industrial countries, Hong Kong and Taiwan advanced level, there is a large gap.The use of CAD / CAM / CAE / CAPP and other technical design and manufacture molds, both wide application, or technical level, there is a big gap between both. In the application of CAD technology design molds, only about 10% of the mold used in the design of CAD, aside from drawing board still has a long way to go; in the application of CAE design and analysis of mold calculation, it was just started, most of the game is still in trial stages and animation; in the application of CAM technology manufacturing molds, first, the lack of advanced manufacturing equipment, and second, the existing process equipment (including the last 10years the introduction of advanced equipment) or computer standard (IBM PC and compatibles, HP workstations, etc.) different, or because of differences in bytes, processing speed differences, differences in resistance to electromagnetic interference, networking is low, only about 5% of the mold manufacturing equipment of recent work in this task; in the application process planning CAPP technology, basically a blank state, based on the need for a lot of standardization work; in the mold common technology, such as mold rapid prototyping technology, polishing, electroforming technologies, surface treatment technology aspects of CAD / CAM technology in China has just started. Computer-aided technology, software development, is still at low level, the accumulation of knowledge and experience required. Most of our mold factory, mold processing equipment shop old, long in the length of civilian service, accuracy, low efficiency, still use the ordinary forging, turning, milling, planing, drilling, grinding and processing equipment, mold, heat treatment is still in use salt bath, box-type furnace, operating with the experience of workers, poorly equipped, high energy consumption. Renewal of equipment is slow, technological innovation, technological progress is not much intensity. Although in recent years introduced many advanced mold processing equipment, but are too scattered, or not complete, only about 25% utilization, equipment, some of the advanced functions are not given full play.Lack of technology of high-quality mold design, manufacturing technology and skilled workers, especially the lack of knowledge and breadth, knowledge structure, high levels of compound talents. China's mold industry and technical personnel, only 8% of employees 12%, and the technical personnel and skilled workers and lower the overall skill level. Before 1980, practitioners of technical personnel and skilled workers, the aging of knowledge, knowledge structure can not meet the current needs; and staff employed after 80 years, expertise, experience lack of hands-on ability, not ease, do not want to learn technology. In recent years, the brain drain caused by personnel not only decrease the quantity and quality levels, and personnel structure of the emergence of new faults, lean, make mold design, manufacturing difficult to raise the technical level.3.3 mold industry supporting materials, standard parts of present conditionOver the past 10 years, especially the "Eighth Five-Year", the State organization of the ministries have repeatedly Material Research Institute, universities and steel enterprises, research and development of special series of die steel, molds and other mold-specific carbide special tools, auxiliary materials, and some promotion. However, due to the quality is not stable enough, the lack of the necessary test conditions and test data, specifications andvarieties less, large molds and special mold steel and specifications are required for the gap. In the steel supply, settlement amount and sporadic users of mass-produced steel supply and demand contradiction, yet to be effectively addressed. In addition, in recent years have foreign steel mold set up sales outlets in China, but poor channels, technical services support the weak and prices are high, foreign exchange settlement system and other factors, promote the use of much current.Mold supporting materials and special techniques in recent years despite the popularization and application, but failed to mature production technology, most still also in the exploratory stage tests, such as die coating technology, surface treatment technology mold, mold guide lubrication technology Die sensing technology and lubrication technology, mold to stress technology, mold and other anti-fatigue and anti-corrosion technology productivity has not yet fully formed, towards commercialization. Some key, important technologies also lack the protection of intellectual property.China's mold standard parts production, the formation of the early 80s only small-scale production, standardization and standard mold parts using the coverage of about 20%, from the market can be assigned to, is just about 30 varieties, and limited to small and medium size. Standard punch, hot runner components and other supplies just the beginning, mold and parts production and supply channels for poor, poor accuracy and quality.3.4 Die & Mould Industry Structure in Industrial OrganizationChina's mold industry is relatively backward and still could not be called an independent industry. Mold manufacturer in China currently can be divided into four categories: professional mold factory, professional production outside for mold; products factory mold factory or workshop, in order to supply the product works as the main tasks needed to die; die-funded enterprises branch, the organizational model and professional mold factory is similar to small but the main; township mold business, and professional mold factory is similar. Of which the largest number of first-class, mold production accounts for about 70% of total output. China's mold industry, decentralized management system. There are 19 major industry sectors manufacture and use of mold, there is no unified management of the department. Only by China Die & Mould Industry Association, overall planning, focus on research, cross-sectoral, inter-departmental management difficulties are many.Mold is suitable for small and medium enterprises organize production, and our technical transformation investment tilted to large and medium enterprises, small and medium enterprise investment mold can not be guaranteed. Including product factory mold shop, factory, including, after the transformation can not quickly recover its investment, or debt-laden, affecting development.Although most products factory mold shop, factory technical force is strong, good equipment conditions, the production of mold levels higher, but equipment utilization rate.Price has long been China's mold inconsistent with their value, resulting in mold industry "own little economic benefit, social benefit big" phenomenon. "Dry as dry mold mold standard parts, standard parts dry as dry mold with pieces of production. Dry with parts manufactured products than with the mold" of the class of anomalies exist.4 EngineeringEngineering is the discipline, art and profession of acquiring and applying scientific, mathematical, economic, social, and practical knowledge to design and build structures, machines, devices, systems, materials and processes that safely realize solutions to the needs of society.The American Engineers' Council for Professional Development (ECPD, the predecessor of ABET) has defined "engineering" as:The creative application of scientific principles to design or develop structures, machines, apparatus, or manufacturing processes, or works utilizing them singly or in combination; or to construct or operate the same with full cognizance of their design; or to forecast their behavior under specific operating conditions; all as respects an intended function, economics of operation and safety to life and property.One who practices engineering is called an engineer, and those licensed to do so may have more formal designations such as Professional Engineer, Chartered Engineer, Incorporated Engineer, or European Engineer. The broad discipline of engineering encompasses a range of more specialized subdisciplines, each with a more specific emphasis on certain fields of application and particular areas of technology.4.1 Engineering HistoryThe concept of has existed since ancient times as humans devised fundamental inventions such as the pulley, lever, and wheel. Each of these inventions is consistent with the modern definition of engineering, exploiting basic mechanical principles to develop useful tools and objects.The term engineering itself has a much more recent etymology, deriving from the word engineer, which itself dates back to 1325, when an engine’er (literally, one who operates an engine) originally referred to “a constructor of military engines.” In this context, now obsolete, an “engine” referred to a military machine, i.e., a mechanical contraption used in war (for example, a catapult). Notable exceptions of the obsolete usage which have survived to the present day are military engineering corps, e.g., the U.S. Army Corps of Engineers.The word “engine” itself is of even older origin, ultimately deriving from the Latin ingenium (c. 1250), meaning “innate quality, especially mental power, hence a clever invention.”Later, as the design of civilian structures such as bridges and buildings matured as a technical discipline, the term civil engineering entered the lexicon as a way to distinguish between those specializing in the construction of such non-military projects and those involved in the older discipline of military engineering.4.2 Ancient eraThe Pharos of Alexandria, the pyramids in Egypt, the Hanging Gardens of Babylon, the Acropolis and the Parthenon in Greece, the Roman aqueducts, Via Appia and the Colosseum, Teotihuacán and the cities and pyramids of the Mayan, Inca and Aztec Empires, the Great Wall of China, among many others, stand as a testament to the ingenuity and skill of the ancient civil and military engineers.The earliest civil engineer known by name is Imhotep. As one of the officials of the Pharaoh, Djosèr, he probably designed and supervised the construction of the Pyramid ofDjoser (the Step Pyramid) at Saqqara in Egypt around 2630-2611 BC. He may also have been responsible for the first known use of columns in architecture[citation needed].Ancient Greece developed machines in both the civilian and military domains. The Antikythera mechanism, the first known mechanical computer, and the mechanical inventions of Archimedes are examples of early mechanical engineering. Some of Archimedes' inventions as well as the Antikythera mechanism required sophisticated knowledge of differential gearing or epicyclic gearing, two key principles in machine theory that helped design the gear trains of the Industrial revolution, and are still widely used today in diverse fields such as robotics and automotive engineering.Chinese, Greek and Roman armies employed complex military machines and inventions such as artillery which was developed by the Greeks around the 4th century B.C., the trireme, the ballista and the catapult. In the Middle Ages, the Trebuchet was developed.4.3 Renaissance eraThe first electrical engineer is considered to be William Gilbert, with his 1600 publication of De Magnete, who was the originator of the term "electricity".The first steam engine was built in 1698 by mechanical engineer Thomas Savery. The development of this device gave rise to the industrial revolution in the coming decades, allowing for the beginnings of mass production.With the rise of engineering as a profession in the eighteenth century, the term became more narrowly applied to fields in which mathematics and science were applied to these ends. Similarly, in addition to military and civil engineering the fields then known as the mechanic arts became incorporated into engineering.4.4 ModernThe International Space Station represents a modern engineering challenge from many disciplines.Electrical engineering can trace its origins in the experiments of Alessandro Volta in the 1800s, the experiments of Michael Faraday, Georg Ohm and others and the invention of the electric motor in 1872. The work of James Maxwell and Heinrich Hertz in the late 19thcentury gave rise to the field of Electronics. The later inventions of the vacuum tube and the transistor further accelerated the development of electronics to such an extent that electrical and electronics engineers currently outnumber their colleagues of any other Engineering specialty.The inventions of Thomas Savery and the Scottish engineer James Watt gave rise to modern Mechanical Engineering. The development of specialized machines and their maintenance tools during the industrial revolution led to the rapid growth of Mechanical Engineering both in its birthplace Britain and abroad.Chemical Engineering, like its counterpart Mechanical Engineering, developed in the nineteenth century during the Industrial Revolution. Industrial scale manufacturing demanded new materials and new processes and by 1880 the need for large scale production of chemicals was such that a new industry was created, dedicated to the development and large scale manufacturing of chemicals in new industrial plants. The role of the chemical engineer was the design of these chemical plants and processes.Aeronautical Engineering deals with aircraft design while Aerospace Engineering is a more modern term that expands the reach envelope of the discipline by including spacecraft design. Its origins can be traced back to the aviation pioneers around the turn of the century from the 19th century to the 20th although the work of Sir George Cayley has recently been dated as being from the last decade of the 18th century. Early knowledge of aeronautical engineering was largely empirical with some concepts and skills imported from other branches of engineering.The first PhD in engineering (technically, applied science and engineering) awarded in the United States went to Willard Gibbs at Yale University in 1863; it was also the second PhD awarded in science in the U.S.Only a decade after the successful flights by the Wright brothers, the 1920s saw extensive development of aeronautical engineering through development of World War I military aircraft. Meanwhile, research to provide fundamental background science continued by combining theoretical physics with experiments.In 1990, with the rise of computer technology, the first search engine was built by computer engineer Alan Emtage.。
模具制造科学外文文献翻译、模具类中英文翻译、外文翻译
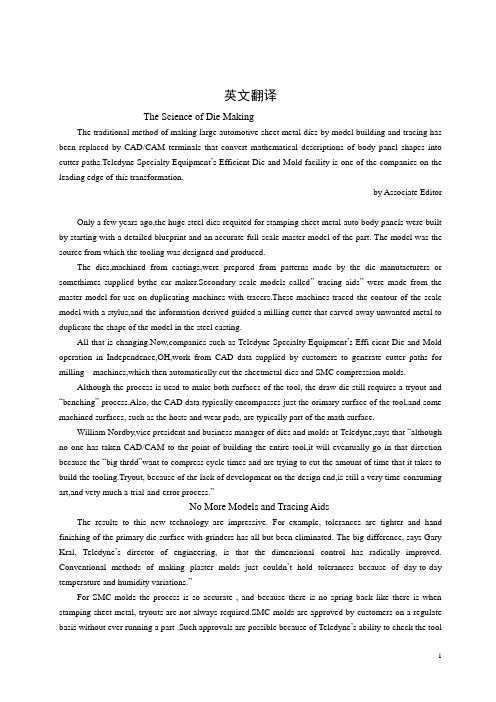
英文翻译The Science of Die MakingThe traditional method of making large automotive sheet metal dies by model building and tracing has been replaced by CAD/CAM terminals that convert mathematical descriptions of body panel shapes into cutter paths.Teledyne Specialty Equipment’s Efficient Die and Mold facility is one of the companies on the leading edge of this transformation.by Associate EditorOnly a few years ago,the huge steel dies requited for stamping sheet metal auto body panels were built by starting with a detailed blueprint and an accurate full-scale master model of the part. The model was the source from which the tooling was designed and produced.The dies,machined from castings,were prepared from patterns made by the die manutacturers or somethimes supplied bythe car maker.Secondary scale models called”tracing aids”were made from the master model for use on duplicating machines with tracers.These machines traced the contour of the scale model with a stylus,and the information derived guided a milling cutter that carved away unwanted metal to duplicate the shape of the model in the steel casting.All that is changing.Now,companies such as Teledyne Specialty Equipment’s Effi cient Die and Mold operation in Independence,OH,work from CAD data supplied by customers to generate cutter paths for milling machines,which then automatically cut the sheetmetal dies and SMC compression molds.Although the process is uesd to make both surfaces of the tool, the draw die still requires a tryout and “benching” process.Also, the CAD data typically encompasses just the orimary surface of the tool,and some machined surfaces, such as the hosts and wear pads, are typically part of the math surface.William Nordby,vice president and business manager of dies and molds at Teledyne,says that “although no one has taken CAD/CAM to the point of building the entire tool,it will eventually go in that direction because the “big thrdd”want to compress cycle times and are trying to cut the amount of time that it takes to build the tooling.Tryout, because of the lack of development on the design end,is still a very time-consuming art,and vety much a trial-and-error process.”No More Models and Tracing AidsThe results to this new technology are impressive. For example, tolerances are tighter and hand finishing of the primary die surface with grinders has all but been eliminated. The big difference, says Gary Kral, Teledyne’s director of engineering, is that the dimensional control has radically improved. Conventional methods of making plaster molds just couldn’t hold tolerances because of day-to-day temperature and humidity variations.”For SMC molds the process is so accurate , and because there is no spring back like there is when stamping sheet metal, tryouts are not always required.SMC molds are approved by customers on a regulate basis without ever running a part .Such approvals are possible because of Teledyne’s ability to check the toolsurface based on mathematical analysis and guarantee that it is made exactly to the original design data.Because manual trials and processes have been eliminated, Teledyne has been able to consider foreign markets.” The ability to get a tool approved based on the mathe gives us the opportunity to compete in places we wouldn’t have otherwise,” says Nordby.According to Jim Church, systems manager at Teledyne, the company used to have lots of pattern makers ,and still has one model maker.” But 99.9 percent of the company’s work now is from CAD data. Instead of model makers, engineers work in front of computer monitors.”He says that improvenents in tool quality and reduction in manufacturing time are significant. Capabilities of the process were demonstrated by producing two identical tools. One was cut using conventional patterns and tracing mills, and the other tool was machined using computer generated cutting paths. Although machining time was 14 percent greater with the CAM-generated path, polishing hours were cut by 33 percent. In all ,manufacturing time decreased 16.5 percent and tool quality increased 12 percent.Teledyne’s CAD/CAM system uses state-of-the-art software that allows engineers to design dies and molds, develop CNC milling cutter paths and incorporate design changes easily. The system supports full-color, shaded three-dimensional modeling on its monitors to enhance its design and analysis capabilities. The CAD/CAM system also provides finite element analysis that can be used to improve the quality of castings , and to analyze the thermal properties of molds. Inputs virtually from any customer database can be used either directly or through translation.CMM Is CriticalTeledyne’s coordinate measuring machine(CMM),says’ Church,”is what has made a difference in terms of being able to move from the traditional manual processes of mold and die making to the automated system that Teledyne uses today.”The CMM precisely locates any point in a volume of space measuring 128 in, by 80 in, by 54 in, to an accuracy of 0.0007 in. It can measure parts, dies and molds weighing up to 40 tons. For maximum accuracy,the machine is housed in an environmentally isolated room where temperature is maintained within 2 deg.F of optimum. To isolate the CMM from vibration, it is mounted on a 100-ton concrete block supported on art cushions.According to Nordby, the CMM is used not only as a quality tool, but also as a process checking tool. “ As a tool goes through the shop, it is checked several times to validate the previous operation that was performed.” For example, after the initial surface of a mold is machined and before any finish work is done, it is run through the CMM for a complete data check to determine how close the surface is to the required geometry.The mold is checked with a very dense pattern based on flow lines of the part. Each mold is checked twice, once before benching and again after benching. Measurements taken from both halves of the mold are used to calculate theoretical stock thickness at full closure of the mold to verify its accuracy with the CAD design data.Sheet Metal Dies Are Different“Sheet metal is a different ballgame,” says Nordby, “because you have the issue of material springback and the way the metal forms in the die. What happens in the sheet metal is that you do the same kinds of things for the male punch as you would with SMC molds and you ensure that it is 100 percent to math data. But due to machined surface tolerance variations, the female half becomes the working side of the tool. And there is still a lot of development required after the tool goes into the press. The math generated surfaces apply primarily to the part surface of the tool.”EMS Tracks the Manufacturing ProcessTeledyne’s business operations also are computerized and carried over a network consisting of a V AX server and PC terminals. IMS (Effective Management Systems) software tracks orders, jobs in progress, location of arts, purchasing, receiving, and is now being upgraded to include accounting functions.Overall capabilities of the EMS system include bill-of-material planning and control, inventory management, standard costing, material history, master production scheduling, material requirements planning, customer order processing, booking and sales history, accounts receivable, labor history, shop floor control, scheduling, estimating, standard routings, capacity requirements planning, job costing, purchasing and receiving, requisitions, purchasing and receiving, requisitions, purchasing history and accounts payable.According to Frank Zugaro, Teledyne’s scheduling manager, the EMS software was chosen because of its capabilities in scheduling time and resources in a job shop environment. All information about a job is entered into inventory management to generate a structured bill of material. Then routes are attached to it and work orders are generated.The system provides daily updates of data by operator hour as well as a material log by shop order and word order. Since the database is interactive, tracking of materials received and their flow through the build procedure can be documented and cost data sent to accounting and purchasing.Gary Kral, Teledyne’s director of engineering, says that EMS is really a tracking device, and one of the systems greatest benefits is that it provides a documented record of everything involving a job and eliminates problems that could arise from verbal instructions and promises. Kral says that as the system is used more, they are finding that it pays to document more things to make it part of the permanent record. It helps keep them focused.模具制造科学传统的通过制造模具加工大型板材的方法已经被可以把实体的形状信息转换为切削路径的CAD/CAM所取代了。
文献翻译译文-模具的历史发展
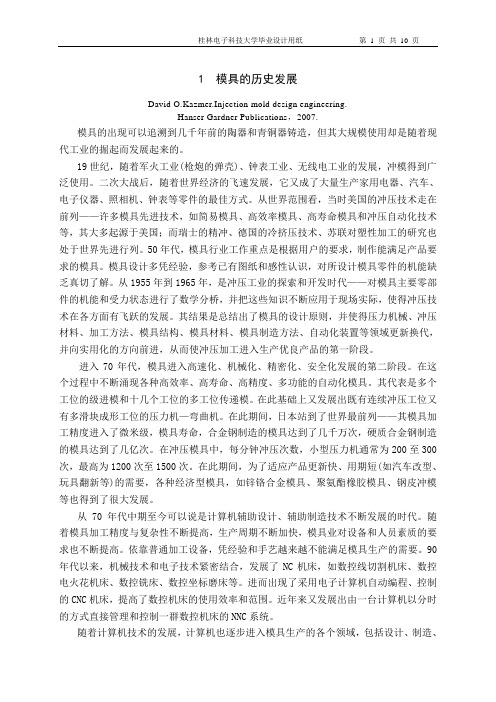
1 模具的历史发展David O.Kazmer.Injection mold design engineering.Hanser Gardner Publications,2007.模具的出现可以追溯到几千年前的陶器和青铜器铸造,但其大规模使用却是随着现代工业的掘起而发展起来的。
19世纪,随着军火工业(枪炮的弹壳)、钟表工业、无线电工业的发展,冲模得到广泛使用。
二次大战后,随着世界经济的飞速发展,它又成了大量生产家用电器、汽车、电子仪器、照相机、钟表等零件的最佳方式。
从世界范围看,当时美国的冲压技术走在前列——许多模具先进技术,如简易模具、高效率模具、高寿命模具和冲压自动化技术等,其大多起源于美国;而瑞士的精冲、德国的冷挤压技术、苏联对塑性加工的研究也处于世界先进行列。
50年代,模具行业工作重点是根据用户的要求,制作能满足产品要求的模具。
模具设计多凭经验,参考已有图纸和感性认识,对所设计模具零件的机能缺乏真切了解。
从1955年到1965年,是冲压工业的探索和开发时代——对模具主要零部件的机能和受力状态进行了数学分桥,并把这些知识不断应用于现场实际,使得冲压技术在各方面有飞跃的发展。
其结果是总结出了模具的设计原则,并使得压力机械、冲压材料、加工方法、模具结构、模具材料、模具制造方法、自动化装置等领域更新换代,并向实用化的方向前进,从而使冲压加工进入生产优良产品的第一阶段。
进入70年代,模具进入高速化、机械化、精密化、安全化发展的第二阶段。
在这个过程中不断涌现各种高效率、高寿命、高精度、多功能的自动化模具。
其代表是多个工位的级进模和十几个工位的多工位传递模。
在此基础上又发展出既有连续冲压工位又有多滑块成形工位的压力机—弯曲机。
在此期间,日本站到了世界最前列——其模具加工精度进入了微米级,模具寿命,合金钢制造的模具达到了几千万次,硬质合金钢制造的模具达到了几亿次。
在冲压模具中,每分钟冲压次数,小型压力机通常为200至300次,最高为1200次至1500次。
模具外文翻译外文文献英文文献注塑模

模具外文翻译外文文献英文文献注塑模The Injection Molding1、The injection moldingInjection molding is principally used for the production of the thermoplastic parts,although some progress has been made in developing a method for injection molding some thermosetting materials.The problem of injection a method plastic into a mold cavity from a reservoir of melted material has been extremely difficult to solve for thermosetting plastic which cure and harden under such conditions within a few minutes.The principle of injection molding is quite similar to that of die-casting.The process consists of feeding a plastic compound in powered or granular form from a hopper through metering and melting stages and then injecting it into a mold.After a brief cooling period,the mold is opened and the solidified part ejected.Injection-molding machine operation.The advantage of injection molding are:(ⅰ)a high molding speed adapter for mass production is possible;(ⅱ)there is a wide choice of thermoplastic materials providing a variety of useful properties;(ⅲ)it is possible to mold threads,undercuts,side holes,and large thin section.2、The injection-molding machineSeveral methods are used to force or inject the melted plastic into the mold.The most commonly used system in the larger machines is the in-line reciprocating screw,as shown in Figure 2-1.The screw acts as a combination injection and plasticizing unit.As the plastic is fed to the rotating screw,it passes through three zones as shown:feed,compression,and metering.After the feed zone,the screw-flight depth is gradually reduced,force theplastic to compress.The work is converted to heat by conduction from the barrel surface.As the chamber in front of the screw becomes filled,it forces the screw back,tripping a limit switch that activates a hydraulic cylinder that forces the screw forward and injects the fluid plastic into the closed mold.An antiflowback valve presents plastic under pressure from escaping back into the screw flight.The clamping force that a machine is capable of exerting is part of the size designation and is measured in tons.A rule-of-thumb can be used to determine the tonnage required for a particular job.It is based on two tons of clamp force per square inch of projected area.If the flow pattern is difficult and the parts are thin,this may have to go to three or four tons.Many reciprocating-screw machines are capable of handing thermosetting plastic materials.Previously these materials were handled by compression or transfer molding.Thermosetting materials cure or polymerize in the mold and are ejected hot in the range of 375°C~410°C.T hermosetting parts must be allowed to cool in the mold in order or remove them without distortion. Thus thermosetting cycles can be faster.Of course the mold must be heated rather than chilled,as with thermoplastics.3、Basic Underfeed MouldA simple mould of this type is shown in Figure3-1,and the description of the design and the opening sequence follows.The mould consists of three basic parts,namely:the moving half,the floating cavity plate and the feed plate respectively.The moving half consists of The moving mould plate assembly,support block,backing plate,ejector assembly and the pin ejection system.Thus the moving half in this design is identical with the moving half of basic moulds.The floating cavity plate,which may be of the integer or insert-bolster design,is located on substantial guide pillars(not shown)fitted in the feed plate.These guide pillars must be of sufficient length to support the floating cavity plate over its full movement and still project to perform the function of alignment between the cavity and core when the mould is being closed.Guide bushes are fitted into the moving mould plate and the floating cavity plate respectively.The maximum movement of the floating cavity plate is controlled by stop or similar device.The moving mould plate is suitably bored to provide a clearance for the stop bolt assembly.The stop bolts must be long enough to provide sufficient space between the feed plate and the floating cavity plate for easy removal of the feed system.The minimum space provide for should be 65mm just sufficient for an operator to remove the feed system by hand if necessary.The desire operating sequence is for the first daylight to occur between the floating cavity plate.This ensures the sprue is pulled from the sprue bush immediately the mouldis opened.T o achieve this sequence,springs may be incorporated between the feed plate and the floating cavity plate.The springs should be strong enough to give an initial impetus to the floating cavity plate to ensure it moves away with the moving half.It is normal practice to mount the springs on the guide pillars(Figure3-2)and accommodate them in suitable pocket in the cavity plate.The major part of the feed system(runner and sprue)is accommodated in the feed plate to facilitate automatic operation,the runner should be of a trapezoidal form so that once it is pulled from the feed plate is can easily beextracted.Note that if a round runner is used,half the runner is formed in the floating cavity plate,where it would remain,and be prevented from falling or being wiped clear when the mould is opened.Now that we have considered the mould assembly in the some detail,we look at the cycle of operation for this type of mould.The impressions are filled via the feed system(Figure3-1(a))and after a suitable dwell period,the machine platens commence to open.A force is immediately exerted by the compression springs,which cause the floating cavity plate to move away with the moving half as previously discussed.The sprue is pulled from the sprue bush by the sprue puller.After the floating cavity plate has moved a predetermined distance,it is arrested by the stop bolts.The moving half continues to move back and the moldings,having shrunk on to the cores,are withdrawn from the cavities.The pin gate breaks at its junction with the runner(Figure3-1(b)).The sprue puller,being attached to the moving half,is pulled through the floating cavity plate and thereby release the feed system which is then free to fall between the floating cavity plate and the feed plate.The moving half continues to move back until the ejector system is operated and the moldings are ejected (Figure3-1(c)).When the mould is closed,the respective plates are returned to their molding position and the cycle is repeated.4、Feed SystemIt is necessary to provide a flow-way in the injection mould to connect the nozzle(of the injection machine)to each impression.This flow-way is termed the feed system.Normally thefeed system comprises a sprue,runner and gate.These terms applyequally to the flow-way itself,and to the molded material which is remove from the flow-way itself in the process of extracted the molding.A typical feed system for a four-impression,two plate-type mould is shown in Figure4-1.It is seen that the material passes through the sprue,main runner,branch runner and gate before entering the impression.As the temperature of molten plastic is lowered which going through the sprue and runner,the viscosity will rise;however,the viscosity is lowered by shear heat generated when going through the gate to fill the cavity.It is desirable to keep the distance that the material has to travel down to a minimum to reduce pressure and heat losses.It is for this reason that careful consideration must be given to the impression layout gate’s design.4.1.SprueA sprue is a channel through which to transfer molten plastic injected from the nozzle of the injector into the mold.It is a part of sprue bush,which is a separate part from the mold.4.2.RunnerA runner is a channel that guides molten plastic into the cavity of a mold.4.3.GateA gate is an entrance through which molten plastic enters the cavity.The gate has the following function:restricts the flow and the direction of molten plastic;simplifies cutting of a runner and moldings to simplify finishing of parts;quickly cools and solidifies to avoid backflow after molten plastic has filled up in the cavity.4.4.Cold slug wellThe purpose of the cold slug well,shown opposite the sprue,is theoretically to receive the material that has chilled at the front of nozzle during the cooling and ejection phase.Perhaps of greater importance is the fact that it provides position means whereby the sprue bush for ejection purposes.The sprue,the runner and the gate will be discarded after a part is complete.However,the runner and the gate are important items that affect the quality or the cost of parts.5、EjectionA molding is formed in mould by injecting a plastic melt,under pressure,into animpression via a feed system.It must therefore be removed manually.Furthermore,all thermoplastic materials contract as they solidify,which means that the molding will shrink on to the core which forms it.This shrinkage makes the molding difficult to remove. Facilities are provided on the injection machine for automatic actuation of an ejector system,and this is situated behind the moving platen.Because of this,the mould’s ejector system will be most effectively operated if placed in the moving half of the mould,i.e. the half attached to the moving platen.We have stated previously that we need to eject the molding from the core and it therefore follows that the core,too,will most satisfactorily be located in the moving half.The ejector system in a mould will be discussed under three headings,namely:(ⅰ)the ejector grid;(ⅱ)the ejector plate assembly; and(ⅲ)the method of ejection.5.1、Ejector gridThe ejector grid(Figure5-1)is that part of the mould which supports the mould plate and provides a space into which theejector plate assembly can be fitted and operated.The grid normally consists of a back plate on to which is mounted a number of conveniently shaped “support blocks”.The ejector plate assembly is that part of the mould to which the ejector element is attached.The assembly is contained in a pocket,formed by the ejector grid,directly behind the mould plate.The assembly(Figure5-2)consists of an ejector plate,a retaining plate and an ejector rod.One end of this latter member is threaded and it is screwed into the ejector plate.In this particular design the ejector rod function not only as an actuating member but also as a method of guiding the assembly.Note that the parallel portion of the ejector rod passes through an ejector rod bush fitted in the back plate of the mould.5.2、Ejection techniquesWhen a molding cools,it contracts by an amount depending on the material being processed.For a molding which has no internal form,for example,a solid rectangular block,the molding will shrink away from the cavity walls,thereby permitting a simple ejection technique to be adopted.However,when the molding has internal form,the molding,as it cools,will shrink onto the core and some positive type of ejection is necessary.The designer has several ejection techniques from which to choose,but in general,the choice will be restricted depending upon the shape of the molding.The basic ejection techniques are as follows:(ⅰ)pin ejection(ⅱ)sleeve ejection(ⅲ)stripper plate ejection and(Ⅳ)air ejection.Figure 2-1aFigure 2-1bFigure 3-1Figure 3-2Figure 4-1aFigure 4-1bFigure 5-1Figure 5-2注塑模1、注塑模尽管成型某些热固性材料的方法取得了一定的进步,但注塑模主要(还是)用来生产热塑性塑件。
模具发展历程毕业课程设计外文文献翻译

Die historyMeorice WilkesAbstract Functional parts are needed for design verification testing, field trials, customer evaluation, and production planning. By eliminating multiple steps, the creation of the injec-tion mold directly by a rapid prototyping (RP) process holds the best promise of reducing the time and cost needed to mold low-volume quantities of parts. The potential of this integration of injection molding with RP has been demonstrated many times. What is missing is the fundamental understandi ng of how the modifications to the mold material and RP manufacturing process impact both the mold design and the injection molding process. In addition, numerical simulation techniques have now become helpful tools of mold designers and process engineers for traditional injection molding. But all current simulation packages for conventional injection molding are no longer applicable to this new type of injection molds, mainly because the property of the mold material changes greatly. In this paper, an integrated approach to accomplish a numerical simulation of injection molding into rapid-prototyped molds is established and a corresponding simulation system is developed. Comparisons with experimental results are employed for verification, which show that the present scheme is well suited to handle RP fabricated stereolithography (SL) molds. Keywords Injection molding Numerical simulation Rapid prototyping IntroductionIn injection molding, the polymer melt at high temperature is injected into the mold under high pressure [1]. Thus, the mold material needs to have thermal and mechanical properties capable of withstanding the temperatures and pressures of the molding cycle. The focus of many studies has been to create theinjection mold directly by a rapid prototyping (RP) process. By eliminating multiple steps, this method of tooling holds the best promise of reducing the time and cost needed to create low-volume quantities of parts in a production material. The potential of integrating injection molding with RP technologies has been demonstrated many times. The properties of RP molds are very different from those of traditional metal molds. The key differences are the properties of thermal conductivity and elastic modulus (rigidity). For example, the polymers used in RP-fabricated stereolithography (SL) molds have a thermal conductivity that is less than one thousandth that of an aluminum tool. In using RP technologies to create molds, the entire mold design and injection-molding process parameters need to be modified and optimized from traditional methodologies due to the completely different tool material. However, there is still not a fundamen tal understanding of how the modifications to the mold tooling method and material impact both the mold design and the injection molding processparameters. One cannot obtain reasonable results by simply changing a few material properties in current models. Also, using traditional approaches when making actual parts may be generating sub-optimal results. So there is a dire need to study the interaction between the rapid tooling (RT) process and material and injection molding, so as to establish the mold design criteria and techniques for an RT-oriented injection molding process.In addition, computer simulation is an effective approach for predicting the quality of molded parts. Commercially available simulation packages of the traditional injection molding process have now become routine tools of the mold designer and process engineer [2]. Unfortunately, current simulation programs for conventional injection molding are no longer applicable to RP molds, because of the dramatically dissimilar tool material. For instance, in using the existing simulation software with aluminum and SL molds and comparing with experimental results, though the simulation values of part distortion are reasonable for the aluminum mold, results are unacceptable, with the error exceeding 50%. The distortion during injection molding is due to shrinkage and warpage of the plastic part, as well as the mold. For ordinarily molds, the main factor is the shrinkage and warpage of the plastic part, which is modeled accurately in current simulations. But for RP molds, the distortion of the mold has potentially more influence, which have been ne glected in current models. For instance, [3] used a simple three-step simulation process to consider the mold distortion, which had too much deviation.In this paper, based on the above analysis, a new simulation system for RP molds is developed. The proposed system focuses on predicting part distortion, which is dominating defect in RP-molded parts. The developed simulation can be applied as an evaluation tool for RP mold design and process opti mization. Our simulation system is verified by an experimental example.Although many materials are available for use in RP technologies, we concentrate on using stereolithography (SL), the original RP technology, to create polymer molds. The SL process uses photopolymer and laser energy to build a part layer by layer. Using SL takes advantage of both the commercial dominance of SL in the RP industry and the subsequent expertise base that has been developed for creating accurate, high-quality parts. Until recently, SL was primarily used to create physical models for visual inspection and form-fit studies with very limited functional applications. However, the newer generation stereolithographic photopolymers have improved dimensional, mechanical and thermal properties making it possible to use them for actual functional molds.1 Die position in industrial productionMold is a high-volume products with the shape tool, is the main process of industrial production equipment.With mold components, with high efficiency, good quality, low cost, saving energy and raw materials and a series of advantages, with the mold workpieces possess high accuracy, high complexity, high consistency, high productivity and low consumption , other manufacturing methods can not match. Have already become an important means of industrial production and technological development. The basis of the modern industrial economy.The development of modern industrial and technological level depends largely on the level of industrial development die, so die industry to national economic and social development will play an increasing role. March 1989 the State Council promulgated "on the current industrial policy decision points" in the mold as the machinery industry transformation sequence of the first, production and capital construction of the second sequence (after the large-scale power generation equipment and the corresponding power transmission equipment), establish tooling industry in an important position in the national economy. Since 1997, they have to mold and its processing technology and equipment included in the "current national focus on encouraging the development of industries, products and technologies catalog" and "to encourage foreign investment industry directory." Approved by the State Council, from 1997 to 2000, more than 80 professional mold factory owned 70% VAT refund of preferential policies to support mold industry. All these have fully demonstrated the development of the State Council and state departments tooling industry attention and support. Mold around the world about the current annual output of 60 billion U.S. dollars, Japan, the United States and other industrialized countries die of industrial output value of more than machine tool industry, beginning in 1997, China's industrial output value has exceeded the mold machine tool industry output.According to statistics, home appliances, toys and other light industries, nearly 90% of the parts are integrated with production of chopsticks; in aircraft, automobiles, agricultural machinery and radio industries, the proportion exceeded 60%. Such as aircraft manufacturing, the use of a certain type of fighter dies more than 30,000 units, of which the host 8000 sets, 2000 sets of engines, auxiliary 20 000 sets. From the output of view, since the 80's, the United States, Japan and other industrialized countries die industry output value has exceeded the machine tool industry, and there are still rising. Production technology, according to the International Association predicts that in 2000, the product best pieces of rough 75%, 50% will be finished mold completed; metals, plastics, ceramics, rubber, buildingmaterials and other industrial products, most of the mold will be completed in more than 50% metal plates, more than 80% of all plastic products, especially through the mold into.2 The historical development of moldThe emergence of mold can be traced back thousands of years ago, pottery and bronze foundry, but the large-scale use is with the rise of modern industry and developed.The 19th century, with the arms industry (gun's shell), watch industry, radio industry, dies are widely used. After World War II, with the rapid development of world economy, it became a mass production of household appliances, automobiles, electronic equipment, cameras, watches and other parts the best way. From a global perspective, when the United States in the forefront of stamping technology - many die of advanced technologies, such as simple mold, high efficiency, mold, die and stamping the high life automation, mostly originated in the United States; and Switzerland, fine blanking, cold in Germany extrusion technology, plastic processing of the Soviet Union are at the world advanced. 50's, mold industry focus is based on subscriber demand, production can meet the product requirements of the mold. Multi-die design rule of thumb, reference has been drawing and perceptual knowledge, on the design of mold parts of a lack of real understanding of function. From 1955 to 1965, is the pressure processing of exploration and development of the times - the main components of the mold and the stress state of the function of a mathematical sub-bridge, and to continue to apply to on-site practical knowledge to make stamping technology in all aspects of a leap in development. The result is summarized mold design principles, and makes the pressure machine, stamping materials, processing methods, plum with a structure, mold materials, mold manufacturing method, the field of automation devices, a new look to the practical direction of advance, so that pressing processing apparatus capable of producing quality products from the first stage.Into the 70's to high speed, launch technology, precision, security, development of the second stage. Continue to emerge in this process a variety of high efficiency, business life, high-precision multi-functional automatic school to help with. Represented by the number of working places as much as other progressive die and dozens of multi-station transfer station module. On this basis, has developed both a continuous pressing station there are more slide forming station of the press - bending machine. In the meantime, the Japanese stand to the world's largest - the mold into the micron-level precision, die life, alloy tool steel mold has reached tens of millions of times, carbide steel mold to each of hundreds of millions of times p minutes for stamping the number of small presses usually 200 to 300, up to 1200 times to 1500 times. In the meantime, in order to meet product updates quickly, with the short duration (such as cars modified, refurbished toys, etc.) need a variety of economic-typemold, such as zinc alloy die down, polyurethane rubber mold, die steel skin, also has been very great development.From the mid-70s so far can be said that computer-aided design, supporting the continuous development of manufacturing technology of the times. With the precision and complexity of mold rising, accelerating the production cycle, the mold industry, the quality of equipment and personnel are required to improve. Rely on common processing equipment, their experience and skills can not meet the needs of mold. Since the 90's, mechanical and electronic technologies in close connection with the development of NC machine tools, such as CNC wire cutting machine, CNC EDM, CNC milling, CNC coordinate grinding machine and so on. The use of computer automatic programming, control CNC machine tools to improve the efficiency in the use and scope. In recent years, has developed a computer to time-sharing by the way a group of direct management and control of CNC machine tools NNC system.With the development of computer technology, computers have gradually into the mold in all areas, including design, manufacturing and management. International Association for the Study of production forecasts to 2000, as a means of links between design and manufacturing drawings will lose its primary role. Automatic Design of die most fundamental point is to establish the mold standard and design standards. To get rid of the people of the past, and practical experience to judge the composition of the design center, we must take past experiences and ways of thinking, for series, numerical value, the number of type-based, as the design criteria to the computer store. Components are dry because of mold constitutes a million other differences, to come up with a can adapt to various parts of the design software almost impossible. But some products do not change the shape of parts, mold structure has certain rules, can be summed up for the automatic design of software. If a Japanese company's CDM system for progressive die design and manufacturing, including the importation of parts of the figure, rough start, strip layout, determine the size and standard templates, assembly drawing and parts, the output NC program (for CNC machining Center and line cutting program), etc., used in 20% of the time by hand, reduce their working hours to 35 hours; from Japan in the early 80s will be three-dimensional cad / cam system for automotive panel die. Currently, the physical parts scanning input, map lines and data input, geometric form, display, graphics, annotations and the data is automatically programmed, resulting in effective control machine tool control system of post-processing documents have reached a high level; computer Simulation (CAE) technology has made some achievements. At high levels, CAD / CAM / CAE integration, that data is integrated, can transmitinformation directly with each other. Achieve network. Present. Only a few foreign manufacturers can do it.3 China's mold industry and its development trendDie & Mould Industry StatusDue to historical reasons for the formation of closed, "big and complete" enterprise features, most enterprises in China are equipped with mold workshop, in factory matching status since the late 70s have a mold the concept of industrialization and specialization of production. Production efficiency is not high, poor economic returns. Mold production industry is small and scattered, cross-industry, capital-intensive, professional, commercial and technical management level are relatively low.According to incomplete statistics, there are now specialized in manufacturing mold, the product supporting mold factory workshop (factory) near 17 000, about 600 000 employees, annual output value reached 20 billion yuan mold. However, the existing capacity of the mold and die industry can only meet the demand of 60%, still can not meet the needs of national economic development. At present, the domestic needs of large, sophisticated, complex and long life of the mold also rely mainly on imports. According to customs statistics, in 1997 630 million U.S. dollars worth of imports mold, not including the import of mold together with the equipment; in 1997 only 78 million U.S. dollars export mold. At present the technological level of China Die & Mould Industry and manufacturing capacity, China's national economy in the weak links and bottlenecks constraining sustainable economic development.3.1 Research on the Structure of industrial products moldIn accordance with the division of China Mould Industry Association, China mold is divided into 10 basic categories, which, stamping die and plastic molding two categories accounted for the main part. Calculated by output, present, China accounts for about 50% die stamping, plastic molding die about 20%, Wire Drawing Die (Tool) about 10% of the world's advanced industrial countries and regions, the proportion of plastic forming die die general of the total output value 40%.Most of our stamping die mold for the simple, single-process mode and meet the molds, precision die, precision multi-position progressive die is also one of the few, die less than 100 million times the average life of the mold reached 100 million times the maximum life of more than accuracy 3 ~ 5um, more than 50 progressive station, and the international life ofthe die 600 million times the highest average life of the die 50 million times compared to the mid 80s at the international advanced level.China's plastic molding mold design, production technology started relatively late, the overall level of low. Currently a single cavity, a simple mold cavity 70%, and still dominant.A sophisticated multi-cavity mold plastic injection mold, plastic injection mold has been able to multi-color preliminary design and manufacturing. Mould is about 80 million times the average life span is about, the main difference is the large deformation of mold components, excess burr side of a large, poor surface quality, erosion and corrosion serious mold cavity, the mold cavity exhaust poor and vulnerable such as, injection mold 5um accuracy has reached below the highest life expectancy has exceeded 20 million times, the number has more than 100 chamber cavity, reaching the mid 80s to early 90s the international advanced level.3.2 mold Present Status of TechnologyTechnical level of China's mold industry currently uneven, with wide disparities. Generally speaking, with the developed industrial countries, Hong Kong and Taiwan advanced level, there is a large gap.The use of CAD / CAM / CAE / CAPP and other technical design and manufacture molds, both wide application, or technical level, there is a big gap between both. In the application of CAD technology design molds, only about 10% of the mold used in the design of CAD, aside from drawing board still has a long way to go; in the application of CAE design and analysis of mold calculation, it was just started, most of the game is still in trial stages and animation; in the application of CAM technology manufacturing molds, first, the lack of advanced manufacturing equipment, and second, the existing process equipment (including the last 10 years the introduction of advanced equipment) or computer standard (IBM PC and compatibles, HP workstations, etc.) different, or because of differences in bytes, processing speed differences, differences in resistance to electromagnetic interference, networking is low, only about 5% of the mold manufacturing equipment of recent work in this task; in the application process planning CAPP technology, basically a blank state, based on the need for a lot of standardization work; in the mold common technology, such as mold rapid prototyping technology, polishing, electroforming technologies, surface treatment technology aspects of CAD / CAM technology in China has just started. Computer-aided technology, software development, is still at low level, the accumulation of knowledge and experience required. Most of our mold factory, mold processing equipment shop old, long in the length of civilian service, accuracy, low efficiency, still use the ordinary forging, turning,milling, planing, drilling, grinding and processing equipment, mold, heat treatment is still in use salt bath, box-type furnace, operating with the experience of workers, poorly equipped, high energy consumption. Renewal of equipment is slow, technological innovation, technological progress is not much intensity. Although in recent years introduced many advanced mold processing equipment, but are too scattered, or not complete, only about 25% utilization, equipment, some of the advanced functions are not given full play.Lack of technology of high-quality mold design, manufacturing technology and skilled workers, especially the lack of knowledge and breadth, knowledge structure, high levels of compound talents. China's mold industry and technical personnel, only 8% of employees 12%, and the technical personnel and skilled workers and lower the overall skill level. Before 1980, practitioners of technical personnel and skilled workers, the aging of knowledge, knowledge structure can not meet the current needs; and staff employed after 80 years, expertise, experience lack of hands-on ability, not ease, do not want to learn technology. In recent years, the brain drain caused by personnel not only decrease the quantity and quality levels, and personnel structure of the emergence of new faults, lean, make mold design, manufacturing difficult to raise the technical level.3.3 mold industry supporting materials, standard parts of present conditionOver the past 10 years, especially the "Eighth Five-Year", the State organization of the ministries have repeatedly Material Research Institute, universities and steel enterprises, research and development of special series of die steel, molds and other mold-specific carbide special tools, auxiliary materials, and some promotion. However, due to the quality is not stable enough, the lack of the necessary test conditions and test data, specifications and varieties less, large molds and special mold steel and specifications are required for the gap. In the steel supply, settlement amount and sporadic users of mass-produced steel supply and demand contradiction, yet to be effectively addressed. In addition, in recent years have foreign steel mold set up sales outlets in China, but poor channels, technical services support the weak and prices are high, foreign exchange settlement system and other factors, promote the use of much current.Mold supporting materials and special techniques in recent years despite the popularization and application, but failed to mature production technology, most still also in the exploratory stage tests, such as die coating technology, surface treatment technology mold, mold guide lubrication technology Die sensing technology and lubrication technology, mold to stress technology, mold and other anti-fatigue and anti-corrosion technology productivity has notyet fully formed, towards commercialization. Some key, important technologies also lack the protection of intellectual property.China's mold standard parts production, the formation of the early 80s only small-scale production, standardization and standard mold parts using the coverage of about 20%, from the market can be assigned to, is just about 30 varieties, and limited to small and medium size. Standard punch, hot runner components and other supplies just the beginning, mold and parts production and supply channels for poor, poor accuracy and quality.3.4 Die & Mould Industry Structure in Industrial OrganizationChina's mold industry is relatively backward and still could not be called an independent industry. Mold manufacturer in China currently can be divided into four categories: professional mold factory, professional production outside for mold; products factory mold factory or workshop, in order to supply the product works as the main tasks needed to die; die-funded enterprises branch, the organizational model and professional mold factory is similar to small but the main; township mold business, and professional mold factory is similar. Of which the largest number of first-class, mold production accounts for about 70% of total output. China's mold industry, decentralized management system. There are 19 major industry sectors manufacture and use of mold, there is no unified management of the department. Only by China Die & Mould Industry Association, overall planning, focus on research, cross-sectoral, inter-departmental management difficulties are many.Mold is suitable for small and medium enterprises organize production, and our technical transformation investment tilted to large and medium enterprises, small and medium enterprise investment mold can not be guaranteed. Including product factory mold shop, factory, including, after the transformation can not quickly recover its investment, or debt-laden, affecting development.Although most products factory mold shop, factory technical force is strong, good equipment conditions, the production of mold levels higher, but equipment utilization rate. Price has long been China's mold inconsistent with their value, resulting in mold industry "own little economic benefit, social benefit big" phenomenon. "Dry as dry mold mold standard parts, standard parts dry as dry mold with pieces of production. Dry with parts manufactured products than with the mold" of the class of anomalies exist.4 Die trend4.1 mold CAD / CAE / CAM being integrated, three-dimensional, intelligent and network direction(1) mold software features integratedDie software features of integrated software modules required relatively complete, while the function module using the same data model, in order to achieve Syndicated news management and sharing of information to support the mold design, manufacture, assembly, inspection, testing and production management of the entire process to achieve optimal benefits. Series such as the UK Delcam's software will include a surface / solid geometric modeling, engineering drawing complex geometry, advanced rendering industrial design, plastic mold design expert system, complex physical CAM, artistic design and sculpture automatic programming system, reverse engineering and complex systems physical line measurement systems. A higher degree of integration of the software includes: Pro / ENGINEER, UG and CATIA, etc.. Shanghai Jiaotong University, China with finite element analysis of metal plastic forming systems and Die CAD / CAM systems; Beijing Beihang Haier Software Ltd. CAXA Series software; Jilin Gold Grid Engineering Research Center of the stamping die mold CAD / CAE / CAM systems .(2) mold design, analysis and manufacture of three-dimensionalTwo-dimensional mold of traditional structural design can no longer meet modern technical requirements of production and integration. Mold design, analysis, manufacturing three-dimensional technology, paperless software required to mold a new generation of three-dimensional, intuitive sense to design the mold, using three-dimensional digital model can be easily used in the product structure of CAE analysis, tooling manufacturability evaluation and CNC machining, forming process simulation and information management and sharing. Such as Pro / ENGINEER, UG and CATIA software such as with parametric, feature-based, all relevant characteristics, so that mold concurrent engineering possible. In addition, Cimatran company Moldexpert, Delcam's Ps-mold and Hitachi Shipbuilding of Space-E/mold are professional injection mold 3D design software, interactive 3D cavity, core design, mold base design configuration and typical structure . Australian company Moldflow realistic three-dimensional flow simulation software MoldflowAdvisers been widely praised by users and applications. China Huazhong University of Science have developed similar software HSC3D4.5F and Zhengzhou University, Z-mold software. For manufacturing, knowledge-based intelligent software function is a measure of die important sign of advanced and practical one. Such as injection molding experts Cimatron's software。
外文翻译
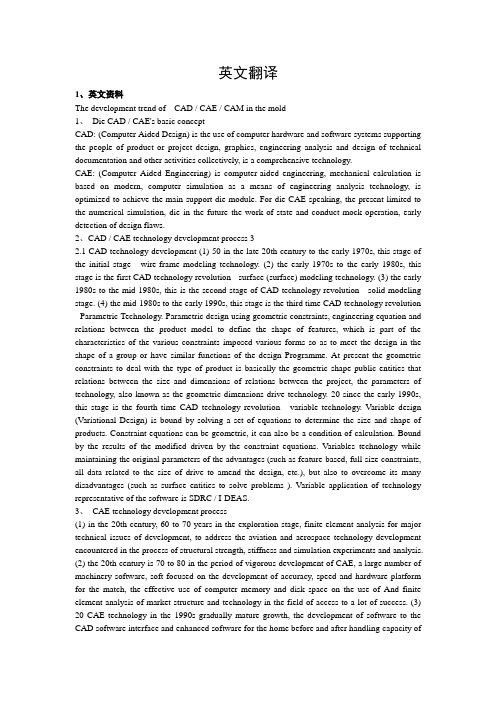
英文翻译1、英文资料The development trend of CAD / CAE / CAM in the mold1、Die CAD / CAE's basic conceptCAD: (Computer Aided Design) is the use of computer hardware and software systems supporting the people of product or project design, graphics, engineering analysis and design of technical documentation and other activities collectively, is a comprehensive technology.CAE: (Computer Aided Engineering) is computer-aided engineering, mechanical calculation is based on modern, computer simulation as a means of engineering analysis technology, is optimized to achieve the main support die module. For die CAE speaking, the present limited to the numerical simulation, die in the future the work of state and conduct mock operation, early detection of design flaws.2、CAD / CAE technology development process 32.1 CAD technology development (1) 50 in the late 20th century to the early 1970s, this stage of the initial stage - wire-frame modeling technology. (2) the early 1970s to the early 1980s, this stage is the first CAD technology revolution - surface (surface) modeling technology. (3) the early 1980s to the mid-1980s, this is the second stage of CAD technology revolution - solid modeling stage. (4) the mid-1980s to the early 1990s, this stage is the third time CAD technology revolution - Parametric Technology. Parametric design using geometric constraints, engineering equation and relations between the product model to define the shape of features, which is part of the characteristics of the various constraints imposed various forms so as to meet the design in the shape of a group or have similar functions of the design Programme. At present the geometric constraints to deal with the type of product is basically the geometric shape public entities that relations between the size and dimensions of relations between the project, the parameters of technology, also known as the geometric dimensions drive technology. 20 since the early 1990s, this stage is the fourth time CAD technology revolution - variable technology. V ariable design (V ariational Design) is bound by solving a set of equations to determine the size and shape of products. Constraint equations can be geometric, it can also be a condition of calculation. Bound by the results of the modified driven by the constraint equations. V ariables technology while maintaining the original parameters of the advantages (such as feature-based, full-size constraints, all data related to the size of drive to amend the design, etc.), but also to overcome its many disadvantages (such as surface entities to solve problems ). V ariable application of technology representative of the software is SDRC / I-DEAS.3、CAE technology development process(1) in the 20th century, 60 to 70 years in the exploration stage, finite element ana lysis for major technical issues of development, to address the aviation and aerospace technology development encountered in the process of structural strength, stiffness and simulation experiments and analysis.(2) the 20th century is 70 to 80 in the period of vigorous development of CAE, a large number of machinery software, soft-focused on the development of accuracy, speed and hardware platform for the match, the effective use of computer memory and disk space on the use of And finite element analysis of market structure and technology in the field of access to a lot of success. (3) 20 CAE technology in the 1990s gradually mature growth, the development of software to the CAD software interface and enhanced software for the home before and after handling capacity ofdirection.Currently, CAE software system is a feature common with the integrated use of CAD software, that is, using CAD software components to complete assembly of parts or design, automatically generate finite element mesh and computing or structural dynamics, such as kinematics In the calculation, if the calculation of the results do not meet design requirements, revise modeling and calculation, to meet demand until the date, thus greatly enhancing the design and efficiency.4、CAD / CAE technology development trendsIn recent years the software developers around the world has invested enormous human and material resources, for the characteristics of various molds, a common CAD / CAM system of industry-specific mold for the system, and achieved great results. Have been put into use in the United States UGS's Progressive Die Design System NX-PDW, plastic injection mould design system Mold Wizard, Israel Cimatron's mold design and manufacturing system Quick, the United Kingdom DELCAM company's plastic mould design and manufacturing systems PS-Moldmaker , France Misslel software company's software for Injection Mould and Top Mold Progressive Die special software Top Progress, Japan UNISYS Corporation plastic mould design and manufacturing systems, such as CADCEUS. The technical characteristics of such software is in the unified system environment, the use of a unified database, to complete the design of a particular mold. NX-PDW initial realization of the mold parts of the structure of association, CADCEUS the characteristics of 2D and 3D design view of the linkage, PS-Moldmaker to the processing of information automatically package, these features make the software more pleasant.At present, some software developers have been able according to the actual production process of functional products, in the network system under CAD / CAE / CAM integration, to solve the traditional hybrid CAD / CAM system can not meet the actual production process collaboration division of the requirements . DELCAM companies such as the United Kingdom in the original software DUCT5 on the basis of the latest software to adapt to the development of industrial production and the actual launch of the CAD / CAM integrated system Delcam's Power Solution, the system covers the geometric modeling, reverse engineering, industrial design, engineering Mapping, simulation, rapid prototyping, data programming, measurement and analysis and other fields. System of each module can operate independently, but also through the data interface compatible with other systems, and to require the use of the combination, in order to develop specialized CAD / CAE / CAM system, to open, compatibility And the unity of specialization. It can be expected, Die CAD / CAE / CAM system in the next few years will be gradually developed to support the design, analysis, management of the entire process of processing the product of the integrated management information system.At this stage, die design and manufacture a large extent, still rely on the experience of the workers die alone computer numerical functions such as mold to complete the design of choice, process parameters and optimize the structure of the mold, molding defects in the diagnosis and die Forming the evaluation of performance is unrealistic. Mold a new generation of CAD / CAE / CAM system is using KBE (Knowledge-based engineering) technology for the transformation completely. UG-II as provided in the artific ial intelligence module KF (Knowledge Fusion). KF use of knowledge can be designed into systems for pattern recognition and reasoning.Numerical computation and artificial intelligence technology will be the combination for quite a long time, a very arduous and important task. Traditional simulation software are basically passive calculation tools, before the needs of users in advance of forming the design parameters ofthe programme and the identification process, the results are often difficult to directly used to guide production, in large measure the impact of simulation software and the promotion of universal,Plastic injection mould CAD / CAE / CAM Development ofPlastic injection mould CAD / CAM is accompanied by a common mechanical CAD / CAM technology development and constantly deepening. From the 1960s on wire-frame model of the CAD system, to the 1970s to surface modeling as the core of the CAD / CAM system, 80 of the entity modeling the successful application of the 1990s, based on the characteristics of the parameters of the entities / surface modeling technology Perfect, plastic injection mould used for CAD / CAE / CAM technology to provide a reliable guarantee. At present overseas markets have emerged in a number of successful application of plastic injection mould of CAD / CAE / CAM system.Now the commercialization of some well-known three-dimensional modeling software have a separate injection mould design modules, such as the United States PTC's Pro / E, UGS's UG-II, SDRC's I-DEAS system. The three CAD / CAM system is currently in the plastic mold industry in the most widely used. There is also the U.S. CV's CADDS system, France MA TRA's EUCLID, France DASSAULT company's CA TIA, the British company's DUCT DELCAM system, the Japanese shipbuilding Information Systems Inc. of Space-E system, and Japan UNISYS Corporation CADCEUS system And so unique, have their own user base.CAE plastic injection mould the development of technology is also very rapidly, from the 1960s and the one-dimensional flow to the cooling of the two-dimensional movement of the 1970s and 1990s and then to the cooling of the quasi-three-dimensional flow and cooling analysis, the scope of its application has been extended To the packing of fiber orientation and warping elements in areas such as forecasts and the effectiveness of Chaplin.Plastic injection molding CAE commercialization of software applications in the most extensive when the number of U.S. companies Moldflow simulation software MF, the main flow simulation software (MF / FLOW), cooling analysis (MF / COOL), warpage analysis (MF / WARP) , Gas-assisted analysis (MF / GAS) and stress analysis (MF / STRESS), and so on. The company was launched in 1998-the double-sided flow of 3D software (Part Adviser), 2002 launch of the true three-dimensional entities flow software modules2翻译议文CAD/CAE/CAM在模具中的的发展趋势1、模具CAD/CAE的基本概念CAD:(Computer Aided Design)是利用计算机硬、软件系统辅助人们对产品或工程进行总体设计、绘图、工程分析与技术文档等设计活动的总称,是一项综合性技术。
冲压模具类外文文献翻译、中英文翻译、外文翻译

模具工业是国民经济的基础工业,是国际上公认的关键工业,工业发达国家称之为“工业之母”。
模具成型具有效率高,质量好,节省原材料,降低产品成本等优点。
采用模具制造产品零件已成为当今工业的重要工艺手段。
模具在机械,电子,轻工,纺织,航空,航天等工业领域里,已成为使用最广泛的工业化生产的主要工艺装备,它承担了这些工业领域中60%--80%产品零件,组件和部件的加工生产。
“模具就是产品质量”,“模具就是经济效益”的观念已被越来越多的人所认识和接受。
在中国,人们已经认识到模具在制造业中的重要基础地位,认识更新换代的速度,新产品的开发能力,进而决定企业的应变能力和市场竞争能力。
在目前用薄钢板制造发动机罩盖的传统还是会持续相当一段时间,所以有必要在钢板的基础上通过利用计算机软件的功能分析零件的工艺性能(结构合理,受力,是否容易冲出破面、、、),发现现有零件的不足之处,讨论并确定改进这些不足之处,进而改善模具的设计,改良冲裁方式;最终实现产品的改良,改善产品的力学性能,外观,使用效果,和造价等等。
冲压加工是通过模具来实现的,从模具角度来看,模具生产技术水平的高低,已成为衡量一个国家产品制造水平高低的重要标志,因为模具在很大程度上决定着产品的质量、效益和新产品的开发能力。
“模具是工业生产的基础工艺装备”也已经取得了共识。
据统计,在电子、汽车、电机、电器、仪器、仪表、家电和通信等产品中,60%~80%的零部件都要依靠模具成形。
用模具生产制件所具备的高精度、高复杂程度、高一致性、高生产率和低消耗,是其他加工制造方法所不能比拟的。
同时,冲压加工也创造了巨大的价值增值,模具是“效益放大器”,用模具生产的最终产品的价值,往往是模具自身价值的几十倍、上百倍。
目前全世界模具年产值约为600亿美元,日、美等工业发达国家的模具工业产值已超过机床工业,从1997年开始,我国模具工业产值也超过了机床工业产值。
其中冲压模具在所有模具(锻造模、压铸模、注塑模等)中,无论从数量、重量或者是从价值上都位居榜首。
我国模具工业发展现状中英文对照外文翻译文献

中英文对照外文翻译外文资料:China's mold industry and its development trend The mold is the manufacturing industry important craft foundation, in our country, the mold manufacture belongs to the special purpose equipment manufacturing industry. China although very already starts to make the mold and the use mold, but long-term has not formed the industry. Straight stabs 0 centuries 80's later periods, the Chinese mold industry only then drives into the development speedway. Recent years, not only the state-owned mold enterprise had the very big development, the three investments enterprise, the villages and towns (individual) the mold enterprise's development also quite rapid .Although the Chinese mold industrial development rapid, but compares with the demand, obviously falls short of demand, its main gap concentrates precisely to, large-scale,complex, the long life mold domain. As a result of in aspect and so on mold precision, life, manufacture cycle and productivity, China and the international average horizontal and the developed country still had a bigger disparity, therefore, needed massively to import the mold every year .The Chinese mold industry except must continue to sharpen the productivity, from now on will have emphatically to the profession internal structure adjustment and the state-of-art enhancement. The structure adjustment aspect, mainly is the enterprise structure to the specialized adjustment, the product structure to center the upscale mold development, to the import and export structure improvement, center the upscale automobile cover mold forming analysis and the structure improvement, the multi-purpose compound mold and the compound processing and the laser technologyin the mold design manufacture application, the high-speed cutting, the superfinishing and polished the technology, the information direction develops .The recent years, the mold profession structure adjustment and the organizational reform step enlarges, mainly displayed in, large-scale, precise, complex, the long life, center the upscale mold and the mold standard letter development speed is higher than the common mold product; The plastic mold and the compression casting mold proportion increases; Specialized mold factory quantity and its productivity increase; "The three investments" and the private enterprise develops rapidly; The joint stock system transformation step speeds up and so on. Distributes from the area looked, take Zhujiang Delta and Yangtze River delta as central southeast coastal area development quickly to mid-west area, south development quickly to north. At present develops quickest, the mold produces the most centralized province is Guangdong and Zhejiang, places such as Jiangsu, Shanghai, Anhui and Shandong also has a bigger development in recent years .Although our country mold total quantity had at present achieved the suitable scale, the mold level also has the very big enhancement, after but design manufacture horizontal overall rise and fall industry developed country and so on Yu De, America, date, France, Italy many. The current existence question and the disparity mainly display in following several aspects:(1) The total quantity falls short of demandDomestic mold assembling oneself rate only ,about 70%. Low-grade mold , center upscale mold assembling oneself rate only has 50% about .(2) The enterprise organizational structure, the product structure, the technical structure and the import and export structure does not gather In our country mold production factory to be most is from the labor mold workshop which produces assembles oneself (branch factory), from produces assembles oneself the proportion to reach as high as about 60%, but the overseas mold ultra 70% is the commodity mold. The specialized mold factory mostly is "large and complete", "small and entire" organization form, but overseas mostly is "small but", "is specially small and fine". Domestic large-scale, precise, complex, the long lifemold accounts for the total quantity proportion to be insufficient 30%, but overseas in 50% above 2004 years, ratio of the mold import and export is 3.7:1, the import and export balances the after net import volume to amount to 1.32 billion US dollars, is world mold net import quantity biggest country .(3) The mold product level greatly is lower than the international standardThe production cycle actually is higher than the international water broad product level low mainly to display in the mold precision, cavity aspect and so on surface roughness, life and structure .(4) Develops the ability badly, economic efficiency unsatisfactory.Our country mold enterprise technical personnel proportion low the level is lower, also does not take the product development, frequently is in the passive position in the market. Our country each mold staff average year creation output value approximately ,ten thousand US dollars, overseas mold industry developed country mostly 15 to 20 thousand US dollars, some reach as high as 25 to 30 thousand US dollars, relative is our country quite part of molds enterprises also continues to use the workshop type management with it, truly realizes the enterprise which the modernized enterprise manages fewTo create the above disparity the reason to be very many, the mold long-term has not obtained the value besides the history in as the product which should have, as well as the most state-owned enterprises mechanism cannot adapt the market economy, but also has the following several reasons: .(1) Country to mold industry policy support dynamics also insufficientlyAlthough the country already was clear about has promulgated the mold profession industrial policy, but necessary policy few, carried out dynamics to be weak. At present enjoyed the mold product increment duty enterprise nation 185, the majority enterprise still the tax burden is only overweight. The mold enterprise carries on the technological transformations introduction equipment to have to pay the considerable amount the tax money, affects the technology advancement, moreover privately operated enterprise loan extremely difficult .(2) Talented person serious insufficient, the scientific research development and the technical attack investment too urineMold profession is the technology, the fund, the work crowded industry, along with the time progress and the technical development, grasps the talented person which and skilled utilizes the new technology exceptionally short, the high-quality mold fitter and the enterprise management talent extremely is also anxious. Because the mold enterprise benefit unsatisfactory and takes insufficiently the scientific research development and the technical attack, the scientific research unit and the universities, colleges and institutes eye stares at is creating income, causes the mold profession invests too few in the scientific research development and the technical attack aspect, causes the mold technological development step not to be big, progresses not quick .(3) The craft equipment level to be low, also necessary is not good, the use factor lowrecent years our country engine bed profession progressed quickly, has been able to provide the quite complete precision work equipment, but compared with the overseas equipment, still had a bigger disparity. Although the domestic many enterprises have introduced many overseas advanced equipment, but the overall equipment level low are very more than the overseas many enterprises. As a result of aspect the and so on system and fund reason, introduces the equipment not not necessary, the equipment and the appendix not necessary phenomenon are extremely common, the equipment utilization rate low question cannot obtain the comparatively properly solution for a long time .(4) Specialization, standardization, commercialized degree low, the cooperation abilityBecause receives "large and complete" "small and entire" the influence since long ago, mold specialization level low, the specialized labor division is not careful, the commercialized degree is low. At present domestic every year produces mold, commodity mold minister 40% About, other for from produce uses for oneself. Between the mold enterprise cooperates impeded, completes the comparativelylarge-scale mold complete task with difficulty. Mold standardization level low, mold standard letter use cave rare is low also to the mold quality, the cost has a more tremendous influence, specially has very tremendous influence .(5) To the mold manufacture cycle) the mold material and the mold correlation technology fallsThe mold material performance, the quality and the variety question often can affect the mold quality, the life and the cost, the domestically produced molding tool steel and overseas imports the steel products to compare has a bigger disparity. Plastic, plate, equipment energy balance, also direct influence mold level enhancement .At present, our country economy still was at the high speed development phase, on the international economical globalization development tendency is day by day obvious, this has provided the good condition and the opportunity for the our country mold industry high speed development. On the one hand, the domestic mold market will continue high speed to develop, on the other hand, the mold manufacture also gradually will shift as well as the transnational group to our country carries on the mold purchase trend to our country extremely to be also obvious. Therefore, will take a broad view the future, international, the domestic mold market overall development tendency prospect will favor, estimated the Chinese mold will obtain the high speed development under the good market environment, our country not only can become the mold great nation, moreover certainly gradually will make the powerful nation to the mold the ranks to make great strides forward. "15" period, the Chinese mold industry level not only has the very big enhancement in the quantity and the archery target aspect, moreover the profession structure, the product level, the development innovation ability, enterprise's system and the mechanism as well as the technology advancement aspect also can obtain a bigger development .The mold technology has gathered the machinery, the electron, chemistry, optics, the material, the computer, the precise monitor and the information network and so on many disciplines, is a comprehensive nature multi-disciplinary systems engineering. The mold technology development tendency mainly is the mold productto larger-scale, preciser, more complex and a more economical direction develops, the mold product technical content unceasingly enhances, the mold manufacture cycle unceasingly reduces, the mold production faces the information, is not having the chart, is fine, the automated direction develops, the mold enterprise to the technical integration, the equipment excellent, is producing approves the brand, the management information, the management internationalization direction develops. Our country mold profession still will have to enhance from now on the general character technology had :(1) To establish in the CAD/CAE platform the advanced mold design technology, enhances modernization which the mold designed, information, intellectualization, standardized level .(2) Establishes in the CAM/CAPP foundation the advanced mold processing technology and the advanced manufacture technology unifies, raises the automated level and the production efficiency which the mold processes .(3) The mold production enterprise's information management technology. For example PDM (product data management), ERP (enterprise resource management), MIS (mold manufacture management information system) and information network technology the and so on INTERMET platform application, the promotion and the development .(4) Are high speed, Gao Jing, the compound mold processing technology research and the application. For example the ultra fine ramming mold manufacture technology, the precise plastic and the compression casting mold manufacture technology and so on .(5) Enhances the mold production efficiency, reduces the cost and reduces the mold production cycle each kind of fast economical mold manufacture technology .(6) The advanced manufacture technology application. For example hot technology and so on flow channel technology, gas auxiliary technology, hypothesized technology, nanotechnology, rapid scanning technology, reversion project, parallel project in the mold research, the development, the processing process application .(7) The raw material the simulation technology which forms in the mold .(8) The advanced mold processing and the appropriation equipment research andthe development .(9) The mold and the mold standard letter, the important auxiliary standardizedtechnology .(10) The mold and its the product examination technology.(11) High quality, the new mold material research and the development and itsthe correct application .(12) The mold production enterprise's modern management technology □Mold profession in "十15" period needs to solve the key essential technologyshould be the mold information, the digitized technology and precise, ultra fine,high speed, the highly effective manufacture technology aspect breakthrough Along with the national economy total quantity and the industry producttechnology unceasing development, all the various trades and occupations to the molddemand quantity more and more big, the specification more and more is also high.Although mold type many, but its development should be with emphasis both canmeet the massive needs, and has the comparatively high-tech content, specially atpresent domestic still could not be self-sufficient, needs the massive imports themold and can represent the development direction large-scale, precise, is complex,the long life mold. The mold standard letter type, the quantity, the level, theproduction a and so on have the significant influence to the entire mold professiondevelopment. Therefore, some important mold standard letters also must theprioritize, moreover its development speed should quickly to the mold developmentspeed, like this be able unceasingly to raise our country mold standardization level,thus improves the mold quality, reduces the mold production cycle, reduces the cost.Because our country mold product holds the bigger price superiority in theinternational market, therefore regarding the exportation prospect good moldproduct also should take key develops. According to the above required quantity big,the technical content is high, represents the development direction, the exportprospect good principle choice prioritize product, moreover chooses the product tohave at present to have the certain technology base, belongs has the condition, has the product which the possibility develops .According to "十15" the mold profession development plan, "十15" the period mold product development mainly has following several kind of the automobile cover mold(1)Ramming mold to occupyThe mold total quantity dish with emphasis above 40%. Automobile cover mold mainly for automobile necessary, also includes for the agriculture with the vehicle, the project machinery and the farm machinery necessary cover mold, it has the very big representation in the ramming mold, the mold mostly is large and middle scale, structure complex, the specification is high. For the passenger vehicle necessary cover mold, the request is in particular higher, may represent the ramming mold the level. This kind of mold our country had the certain technology base, already for middle-grade passenger vehicle necessary, but the level is not high, the ability is insufficient, at present satisfying rate only has one about the half. Center the upscale passenger vehicle cover mold main dependence import, has become the bottleneck which the automobile develops, enormous influence vehicle type development .(2)The precise ramming moldMulti- locations level was entering the mold and fine represents the ramming mold development direction, the precision request life request has been extremely high, mainly for the electronics industry, the automobile, the instrument measuring appliance, the electrical machinery electric appliance and so on formed a complete set. These two kind of molds, domestic had the suitable foundation, and has introduced the overseas technology and the equipment, the individual enterprise produces the product has achieved the world level, but the majority of enterprises still had a bigger disparity, the supply total quantity insufficient, the import were very many(3) The large-scale precise plastic moldPlastic mold accounts for the mold total quantity 10%, moreover this proportion also is rising. In the plastic mold necessary large-scale casts the mold for the automobile and the electrical appliances, necessary models for the integrated circuit seals the mold, for the electronic information industry and the machinery and the packing necessary multilayer, the multi- cavities, the multi- material qualities, the multicolor precise note , and saves water the agricultural necessary plastic different molding for the new building materials to squeeze out the mold and the pipeline and the nozzle mold and so on, at present although had the suitable technology base and fast is developing, but the technical level and overseas still had a bigger disparity, the total quantity falls short of demand, Every year import amount reaches several hundred million US dollar.(4) The main mold standard to imitateeAt present domestically to have an greater output the mold standard letter mainly is the mold frame, the guidance, the throwout lever pushes the tube, the elastic part and so on. These products not only the domestic necessary massive need, the exportation prospect very is also good, should continue vigorously to develop. The nitrogen cylinder and the hot flow channel part main dependence import, should raise the level in the existing foundation, forms the standard and organization scale production.(5) The other high-tech content moldsOccupiesin the mold total quantity green 8% compression casting mold, large-scale thin wall precise compression casting technology content high, the difficulty is big. The magnesium alloy compression casting mold at present although just started, but the prospects for development were good, have the representation. The meridian rubber tire mold also is the development direction, detachable mold technology difficulty is biggest. With fast takes shape some fast pattern making technologies and the corresponding fast economical mold which the technology unifies has the very good prospects for development. These high-tech content molds in "十15" period also should the prioritize .中文翻译:我国模具工业现状及发展趋势模具是制造业的重要工艺基础,在我国,模具制造属于专用设备制造业。
塑料模具外文文献
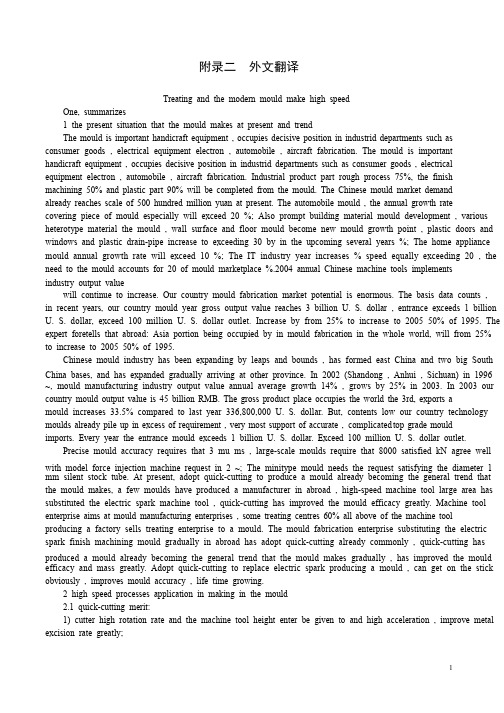
附录二附录二 外文翻译外文翻译Treating and the modern mould make high speed One, summarizes 1 the present situation that the mould makes at present and trend The The mould mould mould is is is important important important handicraft handicraft handicraft equipment equipment equipment , , , occupies occupies occupies decisive decisive decisive position position position in in in industrid industrid industrid departments departments departments such such such as as consumer consumer goods goods goods , , , electrical electrical electrical equipment equipment equipment electron electron electron , , , automobile automobile automobile , , , aircraft aircraft aircraft fabrication. fabrication. fabrication. The The The mould mould mould is is is important important handicraft handicraft equipment equipment equipment , , , occupies occupies occupies decisive decisive decisive position position position in in in industrid industrid industrid departments departments departments such such such as as as consumer consumer consumer goods goods goods , , , electrical electrical equipment equipment electron electron electron , , , automobile automobile automobile , , , aircraft aircraft aircraft fabrication. fabrication. fabrication. Industrial Industrial Industrial product product product part part part rough rough rough process process process 75%, 75%, 75%, the the the finish finish machining machining 50% 50% 50% and and and plastic plastic plastic part part part 90% 90% 90% will will will be be be completed completed completed from from from the the the mould. mould. mould. The The The Chinese Chinese Chinese mould mould mould market market market demand demand already already reaches reaches reaches scale scale scale of of of 500 500 500 hundred hundred hundred million million million yuan yuan yuan at at at present. present. present. The The The automobile automobile automobile mould mould mould , , , the the the annual annual annual growth growth growth rate rate covering piece of mould especially will exceed 20 %; Also prompt building material mould development , various heterotype material the mould , wall surface and floor mould become new mould growth point , plastic doors and windows and plastic drain-pipe increase to exceeding 30 by in the upcoming several years %; The home appliance mould annual growth rate will exceed 10 %; The IT industry year increases % speed equally exceeding 20 , the need need to to to the the the mould mould mould accounts accounts accounts for for for 20 20 20 of of of mould mould mould marketplace marketplace marketplace %.2004 %.2004 %.2004 annual annual annual Chinese Chinese Chinese machine machine machine tools tools tools implements implements industry output value will continue to increase. Our country mould fabrication market potential is enormous. The basis data counts , in recent years, our country mould year gross output value reaches 3 billion U. S. dollar , entrance exceeds 1 billion U. S. dollar, exceed 100 million U. S. dollar outlet. Increase by from 25% to increase to 2005 50% of 1995. The expert foretells that abroad: Asia portion being occupied by in mould fabrication in the whole world, will from 25% to increase to 2005 50% of 1995. Chinese mould industry has been expanding by leaps and bounds , has formed east China and two big South China bases, and has expanded gradually arriving at other province. In 2002 (Shandong , Anhui , Sichuan) in 1996 ~, mould manufacturing industry output value annual average growth 14% , grows by 25% in 2003. In 2003 our country country mould mould mould output output output value value value is is is 45 45 45 billion billion billion RMB. RMB. RMB. The The The gross gross gross product product product place place place occupies occupies occupies the the the world world world the the the 3rd, 3rd, 3rd, exports exports exports a a mould increases 33.5% compared to last year 336,800,000 U. S. dollar. But, contents low our country technology moulds moulds already already already pile pile pile up up up in in in excess excess excess of of of requirement requirement requirement , , , very very very most most most support support support of of of accurate accurate accurate , complicated , complicated top top grade grade grade mould mould imports. Every year the entrance mould exceeds 1 billion U. S. dollar. Exceed 100 million U. S. dollar outlet. Precise mould accuracy requires that 3 mu ms , large-scale moulds require that 8000 satisfied kN agree well with model force injection machine request in 2 ~; The minitype mould needs the request satisfying the diameter 1 mm silent stock tube. At present, adopt quick-cutting to produce a mould already becoming the general trend that the mould makes, a few moulds have produced a manufacturer in abroad , high-speed machine tool large area has substituted the electric spark machine tool , quick-cutting has improved the mould efficacy greatly. Machine tool enterprise enterprise aims aims aims at at at mould mould mould manufacturing manufacturing manufacturing enterprises enterprises enterprises , , , some some some treating treating treating centres centres centres 60% 60% 60% all all all above above above of of of the the the machine machine machine tool tool producing a factory sells treating enterprise to a mould. The mould fabrication enterprise substituting the electric spark finish machining mould gradually in abroad has adopt quick-cutting already commonly , quick-cutting has produced a mould already becoming the general trend that the mould makes gradually , has improved the mould efficacy and mass greatly. Adopt quick-cutting to replace electric spark producing a mould , can get on the stick obviously , improves mould accuracy , life time growing. 2 high speed processes application in making in the mould 2.1 quick-cutting merit: 1) cutter high rotation rate and the machine tool height enter be given to and high acceleration , improve metal excision rate greatly; 2) quick-cutting diminutions cut a force; 3) quick-cutting heat major part generate heat from the cuttings entrainment , workpiece being short; 4) quick-cutting cut down vibration , improve treating mass; 2.2 high speed treating apply to the beneficial result that the mould processes 1) fleetness rough process and half finish machining, improve treating efficiency; 2) high speed high-accuracy finish machining replace only entire the height processing , indicating mass , form accuracy rise , 50%, cuts down repair a mill by hand than EDM processes a potentiation; 3) cuts the surface processing final molding stiffly , improve surface mass , form accuracy, the treating (not only being that surface harshness is low, and the surface radiance is high) , being used for complicated surface has more advantage; 4) the surface loss that EDM treating produces , improve mould life-span 20%; 5) 5) processes processes processes an an an electrode electrode electrode rapidly rapidly rapidly combining combining combining with with with the the the CAD/CAM CAD/CAM CAD/CAM technology technology technology , , , especially, especially, the the form form form is is complicated , thin-wall is similar to an electrode. 3 adopt quick-cutting to process a mould needing the problem solving In in the homeland, since the aspect cause such as fund , technology , the quick-cutting applying produce a mould be in the initial stage stage. Return the machine tool , cutter , handicraft back to existence as well as some problem of aspect needs to proceed orderly other solve. The shortcoming is that finished cost is high, correct cutter sigmatism have comparatively high demand, can not have used big cutters , need to have the complicated computer programming technology to be used for support , equipment running cost height. Two, the high speed processing a mould's processes a machine tool Mould finish machining and hard cutting treating require that the numerical control high-speed machine tool , form form board board board , , , model model model put put put up up up the the the precision precision precision processing processing processing need need need , , , high-effect high-effect high-effect numerical numerical numerical control control control machine machine machine tool tool tool etc.The etc.The mould aiming at produces a lot of machine tool enterprise , some treating centres 60% all above of the machine tool producing a factory sells enterprise to a mould. The The fixed assets fixed assets having having 5 5 billion billion yuan yuan yuan without without without exception exception exception in in in the the the upcoming upcoming upcoming several several several years years years throws throws throws into into into mould mould industry , 80% is the machine tool buying a mould process equipment , just saying every year having 4 billion yuan of RMB to buy Jinqie among them. At At present present present average average average our our our country country country numerical numerical numerical control control control machine machine machine tool tool tool utilization utilization utilization ratio ratio ratio approximately approximately approximately 20%, 20%, 20%, the the high-speed machine tool utilization ratio 3 ~ 5%. Also, mould enterprise has the unit suitable to buy a high-speed machine tool , complies with 6000 ~ 40000 rmp's to have. 1 high-speed machine tool technology parameter demands Process Process centre centre centre chief chief chief axis axis axis high-power high-power high-power , , , high high high rotation rotation rotation rate rate rate , , , satisfied satisfied satisfied rude rude rude finish finish finish machining; machining; machining; The The The finish finish machining mould wants to need to reach 15000 ~ 20000 rmp like the cutter , the machine tool with minor diameter. Generally, the chief axis rotation rate machine tool under 10000 rpm can carry out rough process and half finish machining , cannot reach the finish machining accuracy; Have no way to reach 400 the above m/min cutting speed. 2 five scrolls of machine tools application increases a trend 1) treating route is nimble , the surface form is complicated; 2) treating range is big , the various type mould suitable processes; 3) cuts life-span of condition easy to cut down cutter wear , to raise a cutter,; 3 the softwares buying CAD/CAM and high-speed machine tools assort On the grounds of the machine tool , major part counting , having several billions U. S. dollar to be used to enter port every year, the electromachining machine tool and the high-speed machine tool need to import. Three, quick-cutting mould cutter technology Quick-cutting processes the cutter needing allocating proper quick-cutting. Progressing processing cutter material's in high speed has urged development of high speed treating. The cutter , knife edge headquarter and high tenacity base gathering crystal strengthening the ceramics cutter being able to be used giving consideration to high hardness experience and observe carbide alloy coating becoming possibility. Gather the crystal cube nitriding boron (PCBN) (PCBN) bit, bit, bit, whose whose whose hardness hardness hardness may may may amount amount amount to to to 3500 3500 3500 ~ ~ ~ 4500 4500 4500 HV HV HV. . . Gather Gather Gather crystal crystal crystal miamond miamond miamond (PCD) (PCD) (PCD) it's it's it's hardness hardness hardness but but amount to 6000 ~ 10000 HV . Germany SCS , Japan Mitsubishi (magical steel) and Sumitomo , Switzerland Switzerland Shanteweike Shanteweike Shanteweike , , , USA USA USA Kenna Kenna Kenna are are are in in in recent recent recent years years years swiftly swiftly swiftly large large large wait wait wait for for for the the the famous famous famous abroad abroad abroad cutter cutter company company to to to successively successively successively have have have debuted debuted debuted the the the respective respective respective quick-cutting quick-cutting quick-cutting cutter, cutter, cutter, not not not only only only cutter cutter cutter having having average structural steel of quick-cutting, the ceramics cutter still still having having direct direct quick-cutting quick-cutting of of energy energy quenching hard steel is waiting for an effect to surpass the hard cutter, especially the coating cutter appears all of a sudden sudden , , , bringing bringing bringing into into into play play play in in in quenching quenching quenching half half half finish finish finish machining machining machining and and and finish finish finish machining machining machining of of of hard hard hard steel. steel. steel. New New New cutter cutter material and cutter technology appearing already make the bottleneck problem that high speed has processed no longer be able to appear on the cutter. But, expensive entrance cutter price also blocks quick-cutting mould key factor. Above to come to saying the cutter and the cutter holder acceleration reach 3 gs the sort, the cutter circular runout needs to be smaller than 0.015 mm, but the knife length is unable greater than 4 times cutters diameter. The reality according to SANDVIK company has counted , the carbide alloy has stood on in the entirety using carbon nitriding nitriding titanium titanium titanium (TICN) (TICN) (TICN) coating coating coating when when when milling milling milling cutters cutters cutters (58 (58 (58 HRC) HRC) HRC) carry carry carry out out out high high high speed speed speed bright bright bright metal metal metal chopping chopping chopping , , rough process cutter linear speed has been 100 m/min about , whose linear speed has exceeded but 280 m/min when finish machining and microstoning. Such demands to cutter material (include the hardness , tenacity , red hardness keep the form (include row of crumbs function , surface accuracy , dynamic balance sex etc. (cutting the function) , the cutter under high temperature state)) as well as cutter life-span all has very highly. Experience according to in the homeland mould high speed finish machining, linear speed has exceeded 400 ~ 800 800 m/min m/min m/min when when when adopt adopt adopt the the the young young young diameter diameter diameter ball ball ball head head head milling milling milling cutter cutter cutter to to to carry carry carry out out out mould mould mould finish finish finish machining. machining. machining. The The machine tool choosing sufficient high-speed's cuts mould finish machining stiffly. Delcam adopt 0.8 mm diameter cutter to process the narrow slot , rotation rate 40000 rpm , 0.1 mm depth, feed speed 30 m/min. 1 chooses the cutter parameter , the cutter waits if shouldering an anterior angle. The cutter requires that the ability processing request shock resistance tenacity more highly , requiring that heat resistance pounds than average is strong; 2 adopts various method improving cutter life-span , reduces cutter cost. 3 adopt the high speed hilt , HSK hilt , heat pressing applying the most being at present to pretend to grip a 3 adopt the high speed hilt , HSK hilt , heat pressing applying the most being at present to pretend to grip a cutter. Pay attention to a cutter pretend to grip overall in the day afer tomorrow dynamic balance; 4current cutter enterprise has already done many jobs in the field of the technology resolving the quick-cutting cutter cutter , , , serving serving serving facing facing facing the the the cutter cutter cutter processing processing processing may may may help help help to to to solve solve solve much much much problem problem problem , , , the the the cutter cutter cutter has has has produced produced produced a a manufacturer manufacturer becoming becoming becoming the the the main main main body body body , , , the the the reference reference reference cutter cutter cutter has has has produced produced produced the the the technology technology technology parameter parameter parameter that that that the the manufacturer provides. Four, improve quick-cutting mould efficiency technology 1 cutter diameter and the length choice 2 HSM and the EDM choice 3 does cutting and the lubricating cooling 4 feeds choice: Move forward generally giving amounts <milling cutter diameters 10% , move forward giving a a width width width <milling <milling <milling cutter cutter cutter diameter diameter diameter 40%. 40%. 40%. According According According to to to material, material, material, condition condition condition chooses chooses chooses the the the parameter parameter parameter processing processing handicraft rationally High speed bright metal cuts the mass processing part material abroad fairly good, material quality level is identical , the treating function comparison is stable; But, the cutter that the company produces abroad is also that the the standard standard standard makes makes makes an an an experiment experiment experiment with with with their their their material; material; material; The The The treating treating treating being being being recommended recommended recommended by by by is is is suitable suitable suitable to to to their their standard standard comparatively comparatively comparatively like like like the the the parameter parameter parameter , , , material material material quality quality quality has has has the the the certain certain certain difference difference difference with with with domestic domestic domestic part part part , , , this this difference difference shows shows shows comparatively comparatively comparatively obviously obviously obviously , , , some some some parameters parameters parameters can can can apply apply directly, directly, but but but some some effect dispatches right away comparatively during the period of high speed bright metal chops if using their cutter. But select and use part material quality in the homeland like enterprise having the certain standard, what be put into use part material, can use the part material quality that high speed processes especially , the general meeting is limited in some part material range inner, that this applies the high speed processing technology to us has also provided advantageous condition , has been able to apply to less treating material within range. Being needing to emphasize that here, must choose the treating technological parameter optimizing out a set of capital suitable enterprise on these material , is brought into company standard and. The technology selecting and using the domestic cutter , seldom having the bright metal recommending high speed to chop parametric , is necessary making an experiment, get the comparatively satisfied parameter , produce a manufacturer had better to select and use the fixed cutter , cut down the number of times testing that , the standard forming forming a a a processing processing processing technology, technology, technology, such such such can can can improve improve improve effective effective effective utilization utilization utilization ratio ratio ratio of of of equipment equipment equipment , , , lowers lowers lowers production production costs , can get the fairly good economic effect. Five, quick-cutting route processing a cutter and programming 1) flat surface feeds the route choice 2) 2) outlines process the route choice 3) Keep cutting loading stable 4) keeps relatively stable moving forward giving amounts and feed speed 5) keeps the garden corner in flat surface cutting 6) chooses the finish machining margin rationally Programming demand of HSC finish machining to CAM: 1) the bright metal avoiding a corner to the full cuts motion; 2) tries one's best to avoid external feed of workpiece and enter next depth return knife motion , direct from the outline. Or adopt a helical line or being sure enter slanting to moving forward; 3) constant each edge feed , improve the quality, prolongs cutter life-span; 4) outline treating are kept waiting in level surface. Quick-cutting CAM software: Several years ago will have started quick-cutting processing programming technology research, the Delcam company company , , , has has has developed developed developed the the the quick-cutting quick-cutting quick-cutting automation automation automation programming programming programming software software software module; module; module; Lately, Lately, Lately, the the the MasterCAM MasterCAM company has also developed the quick-cutting automation programming software module; You also are in in the homeland north navigation developing the quick-cutting automation programming software module; Six, high-speed machine tool numerical control system characteristic 1) high speed data is processed 2) corner forecasts are handled 3) NURBS are not justified appearance strip runin curve treating Seven, safe quick-cutting mould problem 1) Monitoring wearing a cutter away and destroying; 2) Intensity that the bit links; 3) Strict with the machine tool and the cutter examination is very important and before the average machine tool processing diversity , safety protects and starts up. Eight, there exists problem in our country at present in adopt high speed to process the mould technology 1 machine tool: 1) domestic high-speed machine tool overall function still has the gap , the function component function to be able to not satisfy a request. Power and rotation rate including the electricity chief axis, entrance machine tool price is high; 2)Under the machine tool high speed, the dynamic behaviour studies the function being not enough to affect a complete machine as a result,; 3)The five scroll of machine tool is not enough mature , entrance machine tool price is very high; 4) supporting technology and equipment are fairly incomplete 2 cutters: 1) domestic cutter is not able to adapt to the quick-cutting application , high speed cuts only entire treating is to affect quick-cutting processing a key especially stiffly. Entrance cutter price is high. The cutter technology factor of mould. 2) supporting technologies are not enough to include hilt , online dynamic balance in complete set etc.. 3 high speed moulds process the technology and the experiment 1) Be short of the accumulation applying experience since high speed processes the mould history comparatively shortly,; 2)The comparison studying comparison stops throwing into lack, sets up a project to quick-cutting handicraft is difficult; 3) Be short of the quick-cutting data base or the handbook , is still blank space at present; 4) moulds produce the manufacturer cognition lack to quick-cutting , the analysis contrast being short of long range beneficial result; 4 Be short of the quick-cutting automation programming software; 5 Be short of a five scroll of gear quick-cutting automation programming CAM software. Concluding remark The mould marketplace has the intense need, but technology to be unable to keep abreast with to high speed treating. Starting is late , the basis is relatively poor , overall engineering level not being taller than , develops slowlyRequire that one by one, aspect coordinated growth , the product mimic inkstone throwing into combining with enlarging, each comprehensive utilization aspect strengths drive quick-cutting application in making in the mould.. Our hope , effort passing every aspect, before the market demand push go down , pass technological progress, look like automobile , machine tool , home appliance , before long, not only our country being going to become a mould producing Great Power, and be going to become a mould producing the powerful country. References1, Jin Diecheng , Song Fangzhi. The modern mould makes the technology , Beijing: Mechanical industry press, 2001. 2, Xu Hefeng, The digitization mould makes the technology , Beijing: Chemical industry press, 2001. 3,Zhao Bo ,High speed processes the forward position technology that the mould processes. Mould technology , 2000 , (2) 4,Zhang Haiou,The fleetness mould makes the technology current situation and their developing trend. Mould technology , 2000 , (6) 5,Guo Dongming,Wang Xiaoming,Be geared to the needs of the particular kind processing technology that the fleetness creates. Chinese mechanical engineering , 2000 , (11) 高速加工和现代模具制造一、概述一、概述1.目前模具制造的发展现状和趋势.目前模具制造的发展现状和趋势模具作为重要的工艺装备,在消费品、电器电子、汽车、飞机制造等工业部门中,占有举足轻重的地位。
冲压模具技术外文文献翻译中英文
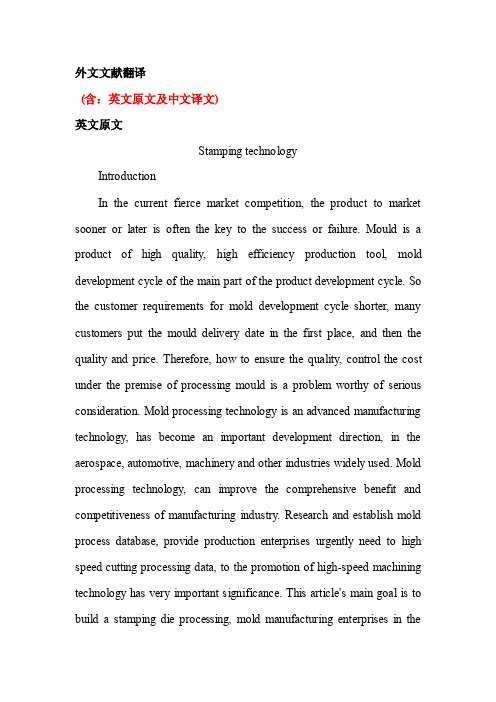
外文文献翻译(含:英文原文及中文译文)英文原文Stamping technologyIntroductionIn the current fierce market competition, the product to market sooner or later is often the key to the success or failure. Mould is a product of high quality, high efficiency production tool, mold development cycle of the main part of the product development cycle. So the customer requirements for mold development cycle shorter, many customers put the mould delivery date in the first place, and then the quality and price. Therefore, how to ensure the quality, control the cost under the premise of processing mould is a problem worthy of serious consideration. Mold processing technology is an advanced manufacturing technology, has become an important development direction, in the aerospace, automotive, machinery and other industries widely used. Mold processing technology, can improve the comprehensive benefit and competitiveness of manufacturing industry. Research and establish mold process database, provide production enterprises urgently need to high speed cutting processing data, to the promotion of high-speed machining technology has very important significance. This article's main goal is to build a stamping die processing, mold manufacturing enterprises in theactual production combined cutting tool, workpiece and machine tool with the actual situation of enterprise itself accumulate to high speed cutting processing instance, process parameters and experience of high speed cutting database selectively to store data, not only can save a lot of manpower and material resources, financial resources, but also can guide the high speed machining production practice, to improve processing efficiency, reduce the tooling cost and obtain higher economic benefits.1. The concept, characteristics and application of stampingStamping is a pressure processing method that uses a mold installed on a press machine (mainly a press) to apply pressure to a material to cause it to separate or plastically deform, thereby obtaining a desired part (commonly referred to as a stamped or stamped part). Stamping is usually cold deformation processing of the material at room temperature, and the main use of sheet metal to form the required parts, it is also called cold stamping or sheet metal stamping. Stamping is one of the main methods of material pressure processing or plastic processing, and is affiliated with material forming engineering.The stamping die is called stamping die, or die. Dies are special tools for the batch processing of materials (metal or non-metallic) into the required stampings. Stamping is critical in stamping. There is no die that meets the requirements. Batch stamping production is difficult. Without advanced stamping, advanced stamping processes cannot be achieved.Stamping processes and dies, stamping equipment, and stamping materials constitute the three elements of stamping. Only when they are combined can stampings be obtained.Compared with other methods of mechanical processing and plastic processing, stamping processing has many unique advantages in both technical and economic aspects, and its main performance is as follows;(1) The stamping process has high production efficiency, easy operation, and easy realization of mechanization and automation. This is because stamping is accomplished by means of die and punching equipment. The number of strokes for ordinary presses can reach several tens of times per minute, and the high-speed pressure can reach hundreds or even thousands of times per minute, and each press stroke is Y ou may get a punch.(2) Since the die ensures the dimensional and shape accuracy of the stamping part during stamping, and generally does not destroy the surface quality of the stamping part, the life of the die is generally longer, so the stamping quality is stable, the interc hangeability is good, and it has “the same” Characteristics.(3) Stamping can process parts with a wide range of sizes and shapes, such as stopwatches as small as clocks, as large as automobile longitudinal beams, coverings, etc., plus the cold deformation hardening effect of materials during stamping, the strength of stamping and Thestiffness is high.(4) Stamping generally does not generate scraps, material consumption is less, and no other heating equipment is required. Therefore, it is a material-saving and energy-saving processing method, and the cost of stamping parts is low.However, the molds used for stamping are generally specialized, and sometimes a complex part requires several sets of molds for forming, and the precision of the mold manufacturing is high and the technical requirements are high. It is a technology-intensive product. Therefore, the advantages of stamping can only be fully realized in the case of large production volume of stamping parts, so as to obtain better economic benefits.Stamping is widely used in modern industrial production, especially in mass production. A considerable number of industrial sectors are increasingly using punching to process product components such as automobiles, agricultural machinery, instruments, meters, electronics, aerospace, aerospace, home appliances, and light industry. In these industrial sectors, the proportion of stamped parts is quite large, at least 60% or more, and more than 90%. Many of the parts that were manufactured in the past using forging = casting and cutting processes are now mostly replaced by light-weight, rigid stampings. Therefore, it can be said that if the stamping process cannot be adopted in production, it isdifficult for many industrial departments to increase the production efficiency and product quality, reduce the production cost, and quickly replace the product.2. Basic process and mould for stampingDue to the wide variety of stamped parts and the different shapes, sizes, and precision requirements of various parts, the stamping process used in production is also varied. Summarized, can be divided into two major categories of separation processes and forming processes; Separation process is to make the blank along a certain contour line to obtain a certain shape, size and section quality stamping (commonly referred to as blanking parts) of the process; forming process refers to The process of producing a stamped part of a certain shape and size by plastic deformation of the blank without breaking.The above two types of processes can be divided into four basic processes: blanking, bending, deep drawing and forming according to different basic deformation modes. Each basic process also includes multiple single processes.In actual production, when the production volume of the stamped part is large, the size is small and the tolerance requirement is small, it is not economical or even difficult to achieve the requirement if the stamping is performed in a single process. At this time, a centralized scheme is mostly used in the process, that is, two or more singleprocesses are concentrated in a single mold. Different methods are called combinations, and they can be divided into compound-graded and compound- Progressive three combinations.Composite stamping - A combination of two or more different single steps at the same station on the die in one press stroke.Progressive stamping - a combination of two or more different single steps on a single work station in the same mold at a single working stroke on the press.Composite - Progressive - On a die combination process consisting of composite and progressive two ways.There are many types of die structure. According to the process nature, it can be divided into blanking die, bending die, drawing die and forming die, etc.; the combination of processes can be divided into single-step die, compound die and progressive die. However, regardless of the type of die, it can be regarded as consisting of two parts: the upper die and the lower die. The upper die is fixed on the press table or the backing plate and is a fixed part of the die. During work, the blanks are positioned on the lower die surface by positioning parts, and the press sliders push the upper die downwards. The blanks are separated or plastically deformed under the action of the die working parts (ie, punch and die) to obtain the required Shape and size of punching pieces. When the upper mold is lifted, the unloading and ejecting device of the moldremoves or pushes and ejects the punching or scrap from the male and female molds for the next punching cycle.3. Current status and development direction of stamping technologyWith the continuous advancement of science and technology and the rapid development of industrial production, many new technologies, new processes, new equipment, and new materials continue to emerge, thus contributing to the constant innovation and development of stamping technology. Its main performance and development direction are as follows:(1) The theory of stamping and the stamping process The study of stamping forming theory is the basis for improving stamping technology. At present, the research on the stamping forming theory at home and abroad attaches great importance, and significant progress has been made in the study of material stamping performance, stress and strain analysis in the stamping process, study of the sheet deformation law, and the interaction between the blank and the mold. . In particular, with the rapid development of computer technology and the further improvement of plastic deformation theory, computer simulation techniques for the plastic forming process have been applied at home and abroad in recent years, namely the use of finite element (FEM) and other valuable analytical methods to simulate the plastic forming process of metals. According to the analysis results, the designer can predict the feasibility and possiblequality problems of a certain process scheme. By selecting and modifying the relevant parameters on the computer, the process and mold design can be optimized. This saves the cost of expensive trials and shortens the cycle time.Research and promotion of various pressing technologies that can increase productivity and product quality, reduce costs, and expand the range of application of stamping processes are also one of the development directions of stamping technology. At present, new precision, high-efficiency, and economical stamping processes, such as precision stamping, soft mold forming, high energy high speed forming, and dieless multi-point forming, have emerged at home and abroad. Among them, precision blanking is an effective method for improving the quality of blanking parts. It expands the scope of stamping processing. The thickness of precision blanking parts can reach 25mm at present, and the precision can reach IT16~17; use liquid, rubber, polyurethane, etc. Flexible die or die soft die forming process can process materials that are difficult to process with ordinary processing methods and parts with complex shapes, have obvious economic effects under specific production conditions, and adopt energy-efficient forming methods such as explosion for processing. This kind of sheet metal parts with complex dimensions, complex shapes, small batches, high strength and high precision has important practical significance; Superplastic forming of metal materialscan be used to replace multiple common stampings with one forming. Forming process, which has outstanding advantages for machining complex shapes and large sheet metal parts; moldless multi-point forming process is an advanced technology for forming sheet metal surfaces by replacing the traditional mold with a group of height adjustable punches. Independently designed and manufactured an international leading-edge moldless multi-point forming equipment, which solves the multi-point press forming method and can therefore be Changing the state of stress and deformation path, improving the forming limit of the material, while repeatedly using the forming technology may eliminate the residual stress within the material, the rebound-free molding. The dieless multi-point forming system takes CAD/CAM/CAE technology as the main means to quickly and economically realize the automated forming of three-dimensional surfaces.(2) Dies are the basic conditions for achieving stamping production. In the design and manufacture of stampings, they are currently developing in the following two aspects: On the one hand, in order to meet the needs of high-volume, automatic, precision, safety and other large-volume modern production, stamping is To develop high-efficiency, high-precision, high-life, multi-station, and multi-function, compared with new mold materials and heat treatment technologies, various high-efficiency, precision, CNC automatic mold processing machine toolsand testing equipment and molds CAD/CAM technology is also rapidly developing; On the other hand, in order to meet the needs of product replacement and trial production or small-batch production, zinc-based alloy die, polyurethane rubber die, sheet die, steel die, combination die and other simple die And its manufacturing technology has also been rapidly developed.Precision, high-efficiency multi-station and multi-function progressive die and large-scale complex automotive panel die represent the technical level of modern die. At present, the precision of the progressive die above 50 stations can reach 2 microns. The multifunctional progressive die can not only complete the stamping process, but also complete welding, assembly and other processes. Our country has been able to design and manufacture its own precision up to the international level of 2 to 5 microns, precision 2 to 3 microns into the distance, the total life of 100 million. China's major automotive mold enterprises have been able to produce complete sets of car cover molds, and have basically reached the international level in terms of design and manufacturing methods and means. However, the manufacturing methods and methods have basically reached the international level. The mold structure and function are also close to international Level, but there is still a certain gap compared with foreign countries in terms of manufacturing quality, accuracy, manufacturing cycle and cost.4. Stamping standardization and professional productionThe standardization and professional production of molds has been widely recognized by the mold industry. Because the die is a single-piece, small-volume production, the die parts have both certain complexity and precision, as well as a certain structural typicality. Therefore, only the standardization of the die can be achieved, so that the production of the die and the die parts can be professionalized and commercialized, thereby reducing the cost of the die, improving the quality of the die and shortening the manufacturing cycle. At present, the standard production of molds in foreign advanced industrial countries has reached 70% to 80%. Mould factories only need to design and manufacture working parts, and most of the mold parts are purchased from standard parts factories, which greatly increases productivity. The more irregular the degree of specialization of the mold manufacturing plant, the more and more detailed division of labor, such as the current mold factory, mandrel factory, heat treatment plant, and even some mold factories only specialize in the manufacture of a certain type of product or die The bending die is more conducive to the improvement of the manufacturing level and the shortening of the manufacturing cycle. China's stamp standardization and specialized production have also witnessed considerable development in recent years. In addition to the increase in the number of standard parts specialized manufacturers, the number ofstandard parts has also expanded, and the accuracy has also improved. However, the overall situation can not meet the requirements of the development of the mold industry, mainly reflected in the standardization level is not high (usually below 40%), the standard parts of the species and specifications are less, most standard parts manufacturers did not form a large-scale production, standard parts There are still many problems with quality. In addition, the sales, supply, and service of standard parts production have yet to be further improved.中文译文冲压模具技术前言在目前激烈的市场竞争中, 产品投入市场的迟早往往是成败的关键。
- 1、下载文档前请自行甄别文档内容的完整性,平台不提供额外的编辑、内容补充、找答案等附加服务。
- 2、"仅部分预览"的文档,不可在线预览部分如存在完整性等问题,可反馈申请退款(可完整预览的文档不适用该条件!)。
- 3、如文档侵犯您的权益,请联系客服反馈,我们会尽快为您处理(人工客服工作时间:9:00-18:30)。
Die history1 Die position in industrial productionMold is a high-volume products with the shape tool, is the main process of industrial production equipment.With mold components, with high efficiency, good quality, low cost, saving energy and raw materials and a series of advantages, with the mold workpieces possess high accuracy, high complexity, high consistency, high productivity and low consumption , other manufacturing methods can not match. Have already become an important means of industrial production and technological development. The basis of the modern industrial economy.The development of modern industrial and technological level depends largely on the level of industrial development die, so die industry to national economic and social development will play an increasing role. March 1989 the State Council promulgated "on the current industrial policy decision points" in the mold as the machinery industry transformation sequence of the first, production and capital construction of the second sequence (after the large-scale power generation equipment and the corresponding power transmission equipment), establish tooling industry in an important position in the national economy. Since 1997, they have to mold and its processing technology and equipment included in the "current national focus on encouraging the development of industries, products and technologies catalog" and "to encourage foreign investment industry directory." Approved by the State Council, from 1997 to 2000, more than 80 professional mold factory owned 70% VAT refund of preferential policies to support mold industry. All these have fully demonstrated the development of the State Council and state departments tooling industry attention and support. Mold around the world about the current annual output of 60 billion U.S. dollars, Japan, the United States and other industrialized countries die of industrial output value of more than machine toolindustry, beginning in 1997, China's industrial output value has exceeded the mold machine tool industry output.According to statistics, home appliances, toys and other light industries, nearly 90% of the parts are integrated with production of chopsticks; in aircraft, automobiles, agricultural machinery and radio industries, the proportion exceeded 60%. Such as aircraft manufacturing, the use of a certain type of fighter dies more than 30,000 units, of which the host 8000 sets, 2000 sets of engines, auxiliary 20 000 sets. From the output of view, since the 80's, the United States, Japan and other industrialized countries die industry output value has exceeded the machine tool industry, and there are still rising. Production technology, according to the International Association predicts that in 2000, the product best pieces of rough 75%, 50% will be finished mold completed; metals, plastics, ceramics, rubber, building materials and other industrial products, most of the mold will be completed in more than 50% metal plates, more than 80% of all plastic products, especially through the mold into.2 The historical development of moldThe emergence of mold can be traced back thousands of years ago, pottery and bronze foundry, but the large-scale use is with the rise of modern industry and developed.The 19th century, with the arms industry (gun's shell), watch industry, radio industry, dies are widely used. After World War II, with the rapid development of world economy, it became a mass production of household appliances, automobiles, electronic equipment, cameras, watches and other parts the best way. From a global perspective, when the United States in the forefront of stamping technology - many die of advanced technologies, such as simple mold, high efficiency, mold, die and stamping the high life automation, mostly originated in the United States; and Switzerland, fine blanking, cold in Germany extrusion technology, plastic processing of the Soviet Union are at the world advanced. 50's, mold industry focus is based on subscriber demand, production can meet the product requirements of the mold. Multi-die design rule of thumb, reference has been drawing and perceptual knowledge, on the design of mold parts of a lack of real understanding of function. From 1955 to 1965, is the pressure processing of exploration and development of the times - the main components of the mold and the stress state of the function of a mathematical sub-bridge, and to continue to apply to on-site practical knowledge to make stamping technology in all aspects of a leap in development. The result is summarized mold design principles, and makes the pressure machine, stamping materials, processing methods, plum with a structure, mold materials, mold manufacturing method, the field of automation devices, a new look to the practical direction of advance, so that pressing processing apparatus capable of producing quality products from the first stage.Into the 70's to high speed, launch technology, precision, security, development of the second stage. Continue to emerge in this process a variety of high efficiency, business life, high-precision multi-functional automatic school to help with. Represented by thenumber of working places as much as other progressive die and dozens of multi-station transfer station module. On this basis, has developed both a continuous pressing station there are more slide forming station of the press - bending machine. In the meantime, the Japanese stand to the world's largest - the mold into the micron-level precision, die life, alloy tool steel mold has reached tens of millions of times, carbide steel mold to each of hundreds of millions of times p minutes for stamping the number of small presses usually 200 to 300, up to 1200 times to 1500 times. In the meantime, in order to meet product updates quickly, with the short duration (such as cars modified, refurbished toys, etc.) need a variety of economic-type mold, such as zinc alloy die down, polyurethane rubber mold, die steel skin, also has been very great development.From the mid-70s so far can be said that computer-aided design, supporting the continuous development of manufacturing technology of the times. With the precision and complexity of mold rising, accelerating the production cycle, the mold industry, the quality of equipment and personnel are required to improve. Rely on common processing equipment, their experience and skills can not meet the needs of mold. Since the 90's, mechanical and electronic technologies in close connection with the development of NC machine tools, such as CNC wire cutting machine, CNC EDM, CNC milling, CNC coordinate grinding machine and so on. The use of computer automatic programming, control CNC machine tools to improve the efficiency in the use and scope. In recent years, has developed a computer to time-sharing by the way a group of direct management and control of CNC machine tools NNC system.With the development of computer technology, computers have gradually into the mold in all areas, including design, manufacturing and management. International Association for the Study of production forecasts to 2000, as a means of links between design and manufacturing drawings will lose its primary role. Automatic Design of die most fundamental point is to establish the mold standard and design standards. To get rid of the people of the past, and practical experience to judge the composition of the design center, we must take past experiences and ways of thinking, for series, numerical value, the number of type-based, as the design criteria to the computer store.Components are dry because of mold constitutes a million other differences, to come up with a can adapt to various parts of the design software almost impossible. But some products do not change the shape of parts, mold structure has certain rules, can be summed up for the automatic design of software. If a Japanese company's CDM system for progressive die design and manufacturing, including the importation of parts of the figure, rough start, strip layout, determine the size and standard templates, assembly drawing and parts, the output NC program (for CNC machining Center and line cutting program), etc., used in 20% of the time by hand, reduce their working hours to 35 hours; from Japan in the early 80s will be three-dimensional cad / cam system for automotive panel die. Currently, the physical parts scanning input, map lines and data input, geometric form, display, graphics, annotations and the data is automatically programmed, resulting in effective control machine tool control system of post-processing documents have reached a high level; computer Simulation (CAE) technology has made some achievements. At high levels, CAD / CAM / CAE integration, that data is integrated, can transmit information directly with each other. Achieve network. Present. Only a few foreign manufacturers can do it.3 China's mold industry and its development trendDie & Mould Industry StatusDue to historical reasons for the formation of closed, "big and complete" enterprise features, most enterprises in China are equipped with mold workshop, in factory matching status since the late 70s have a mold the concept of industrialization and specialization of production. Production efficiency is not high, poor economic returns. Mold production industry is small and scattered, cross-industry, capital-intensive, professional, commercial and technical management level are relatively low.According to incomplete statistics, there are now specialized in manufacturing mold, the product supporting mold factory workshop (factory) near 17 000, about 600 000 employees, annual output value reached 20 billion yuan mold. However, the existing capacity of the mold and die industry can only meet the demand of 60%, still can not meet the needs of national economic development. At present, the domestic needs of large, sophisticated, complex and long life of the mold also rely mainly on imports. According to customs statistics, in 1997 630 million U.S. dollars worth of imports mold, not including the import of mold together with the equipment; in 1997 only 78 million U.S. dollars export mold. At present the technological level of China Die & Mould Industry and manufacturing capacity, China's national economy in the weak links and bottlenecks constraining sustainable economic development.3.1 Research on the Structure of industrial products moldIn accordance with the division of China Mould Industry Association, China mold is divided into 10 basic categories, which, stamping die and plastic molding two categories accounted for the main part. Calculated by output, present, China accounts for about 50% die stamping, plastic molding die about 20%, Wire Drawing Die (Tool) about 10%of the world's advanced industrial countries and regions, the proportion of plastic forming die die general of the total output value 40%.Most of our stamping die mold for the simple, single-process mode and meet the molds, precision die, precision multi-position progressive die is also one of the few, die less than 100 million times the average life of the mold reached 100 million times the maximum life of more than accuracy 3 ~ 5um, more than 50 progressive station, and the international life of the die 600 million times the highest average life of the die 50 million times compared to the mid 80s at the international advanced level.China's plastic molding mold design, production technology started relatively late, the overall level of low. Currently a single cavity, a simple mold cavity 70%, and still dominant. A sophisticated multi-cavity mold plastic injection mold, plastic injection mold has been able to multi-color preliminary design and manufacturing. Mould is about 80 million times the average life span is about, the main difference is the large deformation of mold components, excess burr side of a large, poor surface quality, erosion and corrosion serious mold cavity, the mold cavity exhaust poor and vulnerable such as, injection mold 5um accuracy has reached below the highest life expectancy has exceeded 20 million times, the number has more than 100 chamber cavity, reaching the mid 80s to early 90s the international advanced level.3.2 mold Present Status of TechnologyTechnical level of China's mold industry currently uneven, with wide disparities. Generally speaking, with the developed industrial countries, Hong Kong and Taiwan advanced level, there is a large gap.The use of CAD / CAM / CAE / CAPP and other technical design and manufacture molds, both wide application, or technical level, there is a big gap between both. In the application of CAD technology design molds, only about 10% of the mold used in the design of CAD, aside from drawing board still has a long way to go; in the application of CAE design and analysis of mold calculation, it was just started, most of the game is stillin trial stages and animation; in the application of CAM technology manufacturing molds, first, the lack of advanced manufacturing equipment, and second, the existing process equipment (including the last 10 years the introduction of advanced equipment) or computer standard (IBM PC and compatibles, HP workstations, etc.) different, or because of differences in bytes, processing speed differences, differences in resistance to electromagnetic interference, networking is low, only about 5% of the mold manufacturing equipment of recent work in this task; in the application process planning CAPP technology, basically a blank state, based on the need for a lot of standardization work; in the mold common technology, such as mold rapid prototyping technology, polishing, electroforming technologies, surface treatment technology aspects of CAD / CAM technology in China has just started. Computer-aided technology, software development, is still at low level, the accumulation of knowledge and experience required. Most of our mold factory, mold processing equipment shop old, long in the length of civilian service, accuracy, low efficiency, still use the ordinary forging, turning, milling, planing, drilling, grinding and processing equipment, mold, heat treatment is still in use salt bath, box-type furnace, operating with the experience of workers, poorly equipped, high energy consumption. Renewal of equipment is slow, technological innovation, technological progress is not much intensity. Although in recent years introduced many advanced mold processing equipment, but are too scattered, or not complete, only about 25% utilization, equipment, some of the advanced functions are not given full play.Lack of technology of high-quality mold design, manufacturing technology and skilled workers, especially the lack of knowledge and breadth, knowledge structure, high levels of compound talents. China's mold industry and technical personnel, only 8% of employees 12%, and the technical personnel and skilled workers and lower the overall skill level. Before 1980, practitioners of technical personnel and skilled workers, the aging of knowledge, knowledge structure can not meet the current needs; and staff employed after 80 years, expertise, experience lack of hands-on ability, not ease, do not want to learn technology. In recent years, the brain drain caused by personnel not onlydecrease the quantity and quality levels, and personnel structure of the emergence of new faults, lean, make mold design, manufacturing difficult to raise the technical level.3.3 mold industry supporting materials, standard parts of present conditionOver the past 10 years, especially the "Eighth Five-Year", the State organization of the ministries have repeatedly Material Research Institute, universities and steel enterprises, research and development of special series of die steel, molds and other mold-specific carbide special tools, auxiliary materials, and some promotion. However, due to the quality is not stable enough, the lack of the necessary test conditions and test data, specifications and varieties less, large molds and special mold steel and specifications are required for the gap. In the steel supply, settlement amount and sporadic users of mass-produced steel supply and demand contradiction, yet to be effectively addressed. In addition, in recent years have foreign steel mold set up sales outlets in China, but poor channels, technical services support the weak and prices are high, foreign exchange settlement system and other factors, promote the use of much current.Mold supporting materials and special techniques in recent years despite the popularization and application, but failed to mature production technology, most still also in the exploratory stage tests, such as die coating technology, surface treatment technology mold, mold guide lubrication technology Die sensing technology and lubrication technology, mold to stress technology, mold and other anti-fatigue and anti-corrosion technology productivity has not yet fully formed, towards commercialization. Some key, important technologies also lack the protection of intellectual property.China's mold standard parts production, the formation of the early 80s only small-scale production, standardization and standard mold parts using the coverage of about 20%, from the market can be assigned to, is just about 30 varieties, and limited to small and medium size. Standard punch, hot runner components and other supplies just thebeginning, mold and parts production and supply channels for poor, poor accuracy and quality.3.4 Die & Mould Industry Structure in Industrial OrganizationChina's mold industry is relatively backward and still could not be called an independent industry. Mold manufacturer in China currently can be divided into four categories: professional mold factory, professional production outside for mold; products factory mold factory or workshop, in order to supply the product works as the main tasks needed to die; die-funded enterprises branch, the organizational model and professional mold factory is similar to small but the main; township mold business, and professional mold factory is similar. Of which the largest number of first-class, mold production accounts for about 70% of total output. China's mold industry, decentralized management system. There are 19 major industry sectors manufacture and use of mold, there is no unified management of the department. Only by China Die & Mould Industry Association, overall planning, focus on research, cross-sectoral, inter-departmental management difficulties are many.Mold is suitable for small and medium enterprises organize production, and our technical transformation investment tilted to large and medium enterprises, small and medium enterprise investment mold can not be guaranteed. Including product factory mold shop, factory, including, after the transformation can not quickly recover its investment, or debt-laden, affecting development.Although most products factory mold shop, factory technical force is strong, good equipment conditions, the production of mold levels higher, but equipment utilization rate.Price has long been China's mold inconsistent with their value, resulting in mold industry "own little economic benefit, social benefit big" phenomenon. "Dry as drymold mold standard parts, standard parts dry as dry mold with pieces of production. Dry with parts manufactured products than with the mold" of the class of anomalies exist.4 Die trend4.1 mold CAD / CAE / CAM being integrated, three-dimensional, intelligent and network direction(1) mold software features integratedDie software features of integrated software modules required relatively complete, while the function module using the same data model, in order to achieve Syndicated news management and sharing of information to support the mold design, manufacture, assembly, inspection, testing and production management of the entire process to achieve optimal benefits. Series such as the UK Delcam's software will include a surface / solid geometric modeling, engineering drawing complex geometry, advanced rendering industrial design, plastic mold design expert system, complex physical CAM, artistic design and sculpture automatic programming system, reverse engineering and complex systems physical line measurement systems. A higher degree of integration of the software includes: Pro / ENGINEER, UG and CATIA, etc.. Shanghai Jiaotong University, China with finite element analysis of metal plastic forming systems and Die CAD / CAM systems; Beijing Beihang Haier Software Ltd. CAXA Series software; Jilin Gold Grid Engineering Research Center of the stamping die mold CAD / CAE / CAM systems .(2) mold design, analysis and manufacture of three-dimensionalTwo-dimensional mold of traditional structural design can no longer meet modern technical requirements of production and integration. Mold design, analysis, manufacturing three-dimensional technology, paperless software required to mold a new generation of three-dimensional, intuitive sense to design the mold, using three-dimensional digital model can be easily used in the product structure of CAEanalysis, tooling manufacturability evaluation and CNC machining, forming process simulation and information management and sharing. Such as Pro / ENGINEER, UG and CATIA software such as with parametric, feature-based, all relevant characteristics, so that mold concurrent engineering possible. In addition, Cimatran company Moldexpert, Delcam's Ps-mold and Hitachi Shipbuilding of Space-E/mold are professional injection mold 3D design software, interactive 3D cavity, core design, mold base design configuration and typical structure . Australian company Moldflow realistic three-dimensional flow simulation software MoldflowAdvisers been widely praised by users and applications. China Huazhong University of Science have developed similar software HSC3D4.5F and Zhengzhou University, Z-mold software. For manufacturing, knowledge-based intelligent software function is a measure of die important sign of advanced and practical one. Such as injection molding experts Cimatron's software can automatically generate parting direction based parting line and parting surface, generate products corresponding to the core and cavity, implementation of all relevant parts mold, and for automatically generated BOM Form NC drilling process, and can intelligently process parameter setting, calibration and other processing results.(3) mold software applications, networking trendWith the mold in the enterprise competition, cooperation, production and management, globalization, internationalization, and the rapid development of computer hardware and software technology, the Internet has made in the mold industry, virtual design, agile manufacturing technology both necessary and possible. The United States in its "21st Century Manufacturing Enterprise Strategy" that the auto industry by 2006 to achieve agile manufacturing / virtual engineering solutions to automotive development cycle shortened from 40 months to 4 months.4.2 mold testing, processing equipment to the precise, efficient, and multi-direction(1) mold testing equipment more sophisticated, efficientSophisticated, complex, large-scale mold development, testing equipment have become increasingly demanding. Precision Mould precision now reached 2 ~ 3μm, more domestic manufacturers have to use Italy, the United States, Japan and other countries in the high-precision coordinate measuring machine, and with digital scanning. Such as Dongfeng Motor Mould Factory not only has the capacity 3250mm × 3250mm Italian coordinate measuring machine, also has a digital photography optical scanner, the first in the domestic use of digital photography, optical scanning as a means of spatial three-dimensional access to information, enabling the establishment from the measurement of physical → model output of engineering drawings → → the whole process of mold making, reverse engineering a successful technology development and applications. This equipment include: second-generation British Renishaw high-speed scanners (CYCLON SERIES2) can be realized and contact laser probe complementary probe, laser scanner accuracy of 0.05mm, scanning probe contact accuracy of 0.02 mm. Another German company GOM ATOS portable scanners, Japan Roland's PIX-30, PIX-4 desktop scanner and the United Kingdom Taylor Hopson's TALYSCAN150 multi-sensor, respectively Three-dimensional scanner with high speed, low-cost and functional composite and so on.(2) CNC EDMJapan Sodick linear motor servo drive using the company's AQ325L, AQ550LLS-WEDM have driven fast response, transmission and high positioning accuracy, the advantages of small thermal deformation. Switzerland Chanmier company NCEDM with P-E3 adaptive control, PCE energy control and automatic programming expert systems. Others also used the powder mixed EDM machining technology, micro-finishing pulse power and fuzzy control (FC) technologies.(3) high-speed milling machine (HSM)Milling is an important means of cavity mold. The low-temperature high-speed milling with the workpiece, cutting force is small, smooth processing, processing quality, processing efficiency (for the general milling process 5 to 10 times) and can process hard materials (<60HRC) and many other advantages. Thus in the mold processing more and more attention. Ruishikelang company UCP710-type five-axis machining center, machine tool positioning accuracy up to 8μm, home-made closed-loop vector control spindle with a maximum speed 42000r/min. Italy RAMBAUDI's high-speed milling, the processing range of up to 2500mm ×5000mm ×1800mm, speed up 20500r/min, cutting feed speed of 20m/min. HSM generally used large, medium-sized mold, such as motor cover mold, die casting mold, large plastic surface machining, the surface precision up to 0.01mm.4. 3 rapid economic modeling techniquesShorten the product development cycle is an effective means of market competition to win one. Compared with the traditional mold process, fast economic modeling technology is a short molding cycle, the characteristics of low cost, precision, and life can meet the production needs, overall economic efficiency is more significant in the mold manufacturing technology, specifically the following main technology.(1) rapid prototyping and manufacturing (RPM). It consists of three-dimensional laser lithography (SLA); laminated profile manufacturing (LOM); laser powder sintering prototyping (SLS); Fused Deposition Molding (FDM) and three-dimensional printing forming technology (3D-P) and so on.(2) the surface forming tooling. It refers to the use of spray, chemical corrosion, electroforming and new method for the formation of the cavity surface and a fine pattern technology.(3) Casting forming tooling. There are bismuth tin alloy tooling, zinc alloy tooling, resin composite forming technology and silicon rubber mold molding technology.(4) cold extrusion mold technology and ultra-molded shapes.(5) multi-point forming technology.(6) KEVRON steel blanking blanking tooling.(7) mold blank rapid manufacturing technology. Mainly dry sand Mold Casting, Vacuum Mold Casting, Resin Sand Mold Casting Lost Wax Casting, and other technologies.(8) Other aspects of technology. Such as the use of nitrogen gas spring pressure side, discharge, quick die technology, stamping unit technology, and cutting edge technology and solid surfacing edge inserts die casting technology.4.4 mold materials and surface treatment technology developed rapidlyIndustry to the level of mold, material application is the key. Due to improper selection and use of materials, causing premature die failure, which accounts for more than 45% failure die. In the mold material, commonly used cold work tool steel with CrWMn, Cr12, Cr12MoV and W6Mo5Cr4V2, flame hardened steel (such as Japan, AUX2, SX105V (7CrSiMnMoV), etc.; used a new type of hot work die steel American H13, Sweden QRO80M, QRO90SUPREME, etc.; used a pre-hardened plastic mold steel (such as the U.S. P20), age-hardening steel (such as the U.S. P21, Japan NAK55, etc.), heat treatment hardened steel (such as the United States, D2, Japan, PD613, PD555, Sweden wins the White 136, etc.), powder die steel (such as Japan KAD18 and KAS440), etc.; panel drawing die used HT300, QT60-2, Mo-Cr, Mo-V cast iron, large-scale mold with HT250. more regular use of Precision Die Hard Steel Results YG20 and other alloys and carbide. in the mold surface treatment, the main trends are: the infiltration of a single element to the multi-element penetration, complex permeability (such as TD method) development; by the general diffusion to the CVD, PVD, PCVD, ion penetration , the direction of ion implantation, etc.; can use the coating are: TiC, TiN, TiCN, TiAlN, CrN, Cr7C3, W2C, etc., while heat from the air treatment means to the development of vacuum heat treatment. In addition, the current strengthening of the laser, glow plasma。