全尺寸检验报告、样件检验和确认记录表
2-8 样件检验和确认记录表
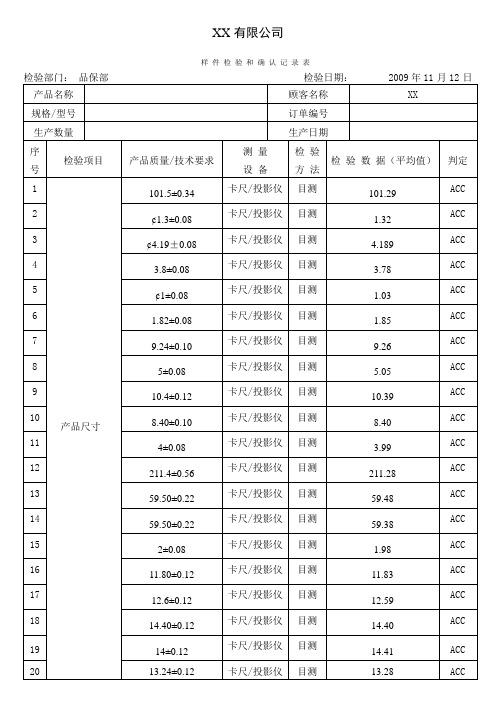
28.4
ACC
31
18±0.14
卡尺/投影仪
目测
17.98
ACC
32
22.4±0.14
卡尺/投影仪
目测
22.39
ACC
33
11.44±0.12
卡尺/投影仪
目测
11.48
ACC
34
5.08±0.08
卡尺/投影仪
目测
5.12
ACC
35
13.55±0.12
卡尺/投影仪
目测
13.60
ACC
36
4.25±0.08
ACC
13
¢1.2±0.08
卡尺/投影仪
目测
1.20
ACC
14
¢20.14±0.08
卡尺/投影仪
目测
20.16
ACC
15
¢14.67±0.12
卡尺/投影仪
目测
14.70
ACC
16
1.50±0.08
卡尺/投影仪
目测
1.52
ACC
17
1.8±0.08
卡尺/投影仪
目测
1.82
ACC
18
8.75±0.10
卡尺/投影仪
目测
2.02
ACC
11
0.5±0.08
卡尺/投影仪
目测
0.48
ACC
12
4±0.08
卡尺/投影仪
目测
4.01
ACC
13
8±0.10
卡尺/投影仪
目测
8.0
ACC
备注
核 准
审 查
制 表
XX有限公司
全尺寸检测

检验员/InspectorName:
姓名/ Name:
部门/ Department:
rejected, new samples required
首批检验的原因/Reason for initial inspection:
尺寸/Dimension
■
新零件/New part
功能ห้องสมุดไป่ตู้Function
产品更改/Productmodification
材料/Material
产地变更/Productionrelocation
拒绝/rejected
过程能力证据/Processcapabilityevidence
拒绝,但可以使用/
证书/Certificates
rejected, installation possible with measure
执行FMEA/FMEA carried out
拒绝,要求提交新样件/
自行认可的供应商/Self-certifyingsupplier
属性检验/Attributive inspection
供应商/Supplier
收件人/ Receiver
地区代码,供应商/
Code number, supplier:
地区代码,收件人
Code number, receiver:
检验报告编号/
InspectionreportNo.:
检验报告编号/
ISO9001-2015样件鉴定管理程序

样件鉴定管理程序(ISO9001:2015)1.目的本制度规定了产品零部件样件鉴定的工作流程和要求,以防止出现因对样件质量控制不当而产生批量质量问题。
2.范围适用于本公司外协外购件及自制件初物中需进行样件鉴定的情况。
3.定义3.1样件:是指按量产条件(正常生产用的设备、工装、量检具、工艺、材料、操作者、生产环境和过程参数等)生产的经检验合格的首批零部件。
3.2样件鉴定:是指在批量生产前通过对样件及其相关资料的检查和确认,验证供方或公司制造部门是否具有相应的质量保证能力及产品是否符合设计要求的一种符合性判定。
4.职责5.工作流程(详见附件1)5.1样件送样要求(外协外购件)5.1.1 样件及所附资料要求Ⅰ)样件必须编号且和自检报告一一对应,需进行材料性能试验或焊接/铆接后不能再分解测量的总成件的样件必须随样提供相应的试棒、试片、工艺散件等试样(见附表2)。
Ⅱ)随附资料按技术质量交流时确定的要求提交。
检验主管工程师认为无需交流时,应在鉴定书上签字备注,样件随附资料按表a要求提交。
Ⅲ)对于有3C认证要求的零部件(详见附表8)的样件鉴定,厂家还必须提供3C认证证书、产品描述报告、检测报告、3C模压标志批准证书复印件;尚未取得证书的,厂家必须提交已申请3C认证的申请书、产品描述报告、检测报告的复印件,否则不予鉴定。
5.1.2 样件的数量要求Ⅰ)送样数量一般为6件(套),需较多样件进行型式试验的总成零部件见附表6,特殊数量要求应在前期技术质量交流时明确。
Ⅱ)如果样件为一模多腔的模具成型件,送样时应提供每一模腔的零件,数量为3件/腔;Ⅲ)变更样件(不涉及到材质、性能的变更)的送样数量为2件(套)。
5.2样件的接收审查(外协外购件)5.2.1供方必须按照样件送样的要求提供样件、试样、相关资料,同时填写《样件鉴定申请单》提交物资公司。
5.2.2物资公司主管工程师负责按照样件送样的要求对厂家提供的样件数量,试样以及必须提供的相关资料进行核对,符合要求的在《样件鉴定申请单》上签名确认后送至鉴定部门,不符合送样条件的拒绝接收。
新产品开发评审表格
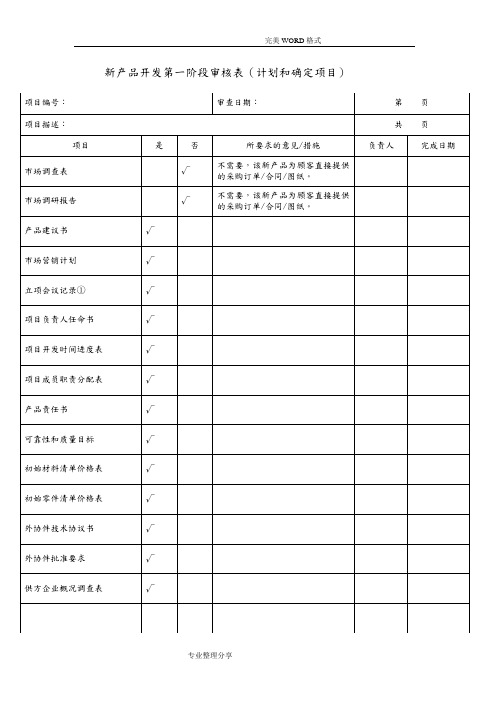
新产品开发第一阶段审核表(计划和确定项目)新产品开发第二阶段审核表(产品设计和开发)新产品开发第三阶段审核表(过程设计和开发)新产品开发第四阶段审核表(产品和过程确认)新产品开发第五阶段审核表(反馈、评定和纠正措施)A — 1 设计FMEA检查表修订日期第1页,共1页制定人:专业整理分享A — 2 设计信息检查表修订日期第1页,共4页专业整理分享A—2 设计信息检查表(续)修订日期第2页,共4页制定人:专业整理分享A — 2 设计信息检查表(续)修订日期第3页,共4页制定人:专业整理分享A — 2 设计信息检查表(续)修订日期第4页,共4页制定人:专业整理分享A— 3 新设备、工装和试验设备检查表修订日期第1页,共2页制定人:专业整理分享A — 3 新设备、工装和试验设备检查表(续)专业整理分享A — 4 产品 / 过程质量检查表修订日期第1页,共4页本检查表并不打算代替克莱斯勒、福特和通用汽车公司的质量体系评定专业整理分享A — 4 产品 / 过程质量检查表(续)修订日期第2页,共4页专业整理分享A — 4 产品 / 过程质量检查表(续)修订日期第3页,共4页专业整理分享A — 4 产品 / 过程质量检查表(续)修订日期第4页,共4页制定人:专业整理分享A — 5 车间平面布置检查表修订日期第1页,共2页制定人:专业整理分享A — 5 车间平面布置检查表(续)修订日期第2页,共2页制定人:专业整理分享A — 6 过程流程图检查表修订日期第1页,共1页制定人:专业整理分享A — 7 过程FMEA检查表修订日期第1页,共1页制定人:专业整理分享A —8 控制计划检查表修订日期第1页,共1页制定人:专业整理分享专业整理分享。
IATF16949 APQP产品先期质量策划控制程序【范本模板】
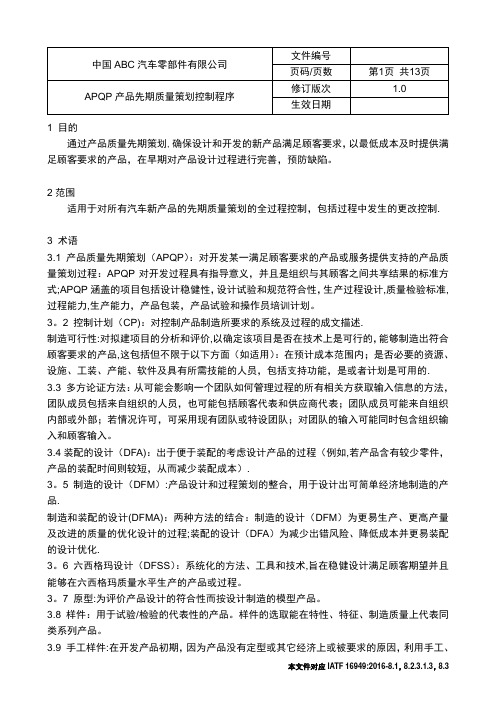
1 目的通过产品质量先期策划,确保设计和开发的新产品满足顾客要求,以最低成本及时提供满足顾客要求的产品,在早期对产品设计过程进行完善,预防缺陷。
2范围适用于对所有汽车新产品的先期质量策划的全过程控制,包括过程中发生的更改控制.3 术语3.1 产品质量先期策划(APQP):对开发某一满足顾客要求的产品或服务提供支持的产品质量策划过程:APQP对开发过程具有指导意义,并且是组织与其顾客之间共享结果的标准方式;APQP涵盖的项目包括设计稳健性,设计试验和规范符合性,生产过程设计,质量检验标准,过程能力,生产能力,产品包装,产品试验和操作员培训计划。
3。
2 控制计划(CP):对控制产品制造所要求的系统及过程的成文描述.制造可行性:对拟建项目的分析和评价,以确定该项目是否在技术上是可行的,能够制造出符合顾客要求的产品,这包括但不限于以下方面(如适用):在预计成本范围内;是否必要的资源、设施、工装、产能、软件及具有所需技能的人员,包括支持功能,是或者计划是可用的.3.3 多方论证方法:从可能会影响一个团队如何管理过程的所有相关方获取输入信息的方法,团队成员包括来自组织的人员,也可能包括顾客代表和供应商代表;团队成员可能来自组织内部或外部;若情况许可,可采用现有团队或特设团队;对团队的输入可能同时包含组织输入和顾客输入。
3.4装配的设计(DFA):出于便于装配的考虑设计产品的过程(例如,若产品含有较少零件,产品的装配时间则较短,从而减少装配成本).3。
5制造的设计(DFM):产品设计和过程策划的整合,用于设计出可简单经济地制造的产品.制造和装配的设计(DFMA):两种方法的结合:制造的设计(DFM)为更易生产、更高产量及改进的质量的优化设计的过程;装配的设计(DFA)为减少出错风险、降低成本并更易装配的设计优化.3。
6六西格玛设计(DFSS):系统化的方法、工具和技术,旨在稳健设计满足顾客期望并且能够在六西格玛质量水平生产的产品或过程。
IATF16949-2016质量管理体系PPAP提交登记规定及全套记录表格

IATF16949-2016质量管理体系PPAP提交登记规定及全套记录表格R=组织必须在适当的场所保存,并应在顾客有要求时易于得到。
*=组织必须在适当的场所保存,并在有要求时向顾客提出。
编号:035-060-168-006T蒙凌工程机械有限公司技术部编号:编号:035-060-168-006T编号:035-060-168-006T1、本表由一级供应商认真填写,并加盖二级供应商和供应商公章后将原件提交给Motiontec品管部;2、本表是最终批准的重要输入之一,如有变动应及时通知Motiontec品管部。
3、当二级供应商变化时,应及时通过Motiontec品管部,以确定是否进行生产件批准。
1编号:035-060-168-006T编号:Motiontec/R.706.13编号:035-060-168-006TMotiontec采购部:1.必要时,供应商应附详细的自审报告;2.在完成各过程的内部批准并确认满足批量生产、供货要求时才可提交本表; 3.SQE 尽量携带本表去供应商现场确认; 4.在不适用的选项的 ”。
Motiontec采购部:生产件批准状况通知PRODUCTION PART APPROVAL STATUS NOTICENO:致:先生/女士(职务)供应商名称:地址:供适用范围(产品型号)APPLICATION(VEHICLES)零件号PART NUMBER零件名称PART NAME更改等级/更改日期CHENGE LEVEL/DATED更改号CHENGE NUMBER原用零件号ORIGINAL PART NUMBERPPAP 编号MOTIONTEC PPAP NUMBER生产件批准状况如下:Production part approval status is as follow批准状态有效截止日期/数量CLASS THROUGH DATE/QUANTITY备注:Motiontec品管工程师Motiontec SQE采购工程师MANAGER编号:035-060-168-006TMotiontec2、版面不够,可附页;3、任何产品变更、物流/运输方式变化导致包装改变时,应向Motiontec品管部门确认是否进行重新认可。
IATF16949过程识别表(完整版)
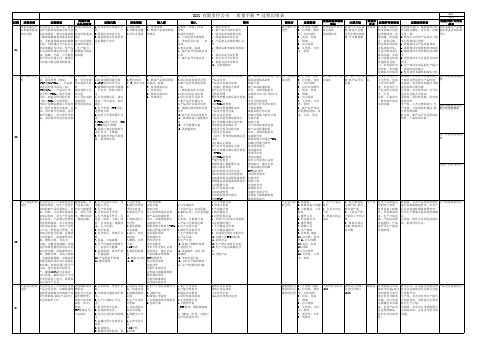
与培训管性评估、员工培训档案建立,以及员工满意度测量等管理要求。
急速扩张,可能导致岗
位培训不充分
5.培训需求识别不充分/
承担特定任务人员应具
备的资格要求不明确
培训
5.调整或重新
识别培训需求
企业文化
顾客报怨
8.岗位配置状况识别
9.产品开发培训方案
岗计划汇总表
8.员工外部培训档案
9.员工培训效果评估表
10.培训师效果评估表
16.KPI考核报表夹、资料
7、培训场地、投
影仪
8、培训讲师
9、培训教材/课件
训管理过程、岗位能力确定、员工聘用第三方咨询公 2.员工不清楚自己的工 2.质量目标培展战略 2.KPI考核项目 2.上岗证管理,负责培训需求的提出、人员的日常管
记表(含专项培训)制过程2、打印机、复印成率培训计划次数×
7.2.1/7.2.2/7.2.。
APQP流程管理各阶段输出资料一览表

P2-18试制原材料采购计划 原材料及零件检验
P2-19C?零件全尺寸检验记录 P2-19A?材质报告 P2-19B?首样试装单 采购员提交,质量部确认
P2-20OTS样件制造计划 P2-19 P2-20 编制OTS样件制造计划 供应商OTS提交 P2-21供应商OTS提交通知 结构硬件设计师
P2阶段输出资料清单 P2-2 P2-3 P2-4 P2-5 P2-6 P2-7 P2-8 P2-9 P2-11 产品设计质量功能展开QFD P2-1C产品需求说明书评审报告 技术条件
P2-2A《产品技术条件》 P2-2B《实验大纲》 P2-2C《硬件设计说明书》 硬件设计师
产品设计师编制、实验室汇总
P2-15B新工装、量具、检具设计评审报告 P2-15C新工装、量具、检具制造进度计划 P2-15D《软件功能测试用例》 P2-15E《编程文档》 工程部
测试设计师
包装标准规范
P2-16A包装2D图 P2-16B包装设计评审 P2-16C供应商包装方案确认结构设计师 P2-24 P2-26 样件控制计划(几轮样件的控制 P2-17A《样件控制计划》 P2-17B《功能测试报告》 P2-17C《出厂检验报告》 测试工程师
4.6生产控制计划 生产控制计划
4.7 P-FMEA P-FMEA 4.8 PPAP 首批样件送样报告
客户信息反馈及不断的改进
4.9产品审核 产品审核报告
4.10过程审核 过程审核报告
4.11型式试验大纲 总成型式试验大纲
功能性能报告
敏锋公司试验报告(自检报告)
总成试验报告(第三方)附实验室认可文件
P2-7A《分供方清单表》 P2-7B《设计制造职能矩阵表》 采购员
样件确认管理规定(3篇)

第1篇第一章总则第一条为确保产品质量,提高生产效率,规范样件确认流程,特制定本规定。
第二条本规定适用于公司所有产品在研发、生产、检验等环节中的样件确认工作。
第三条样件确认应遵循以下原则:1. 科学性:确保样件符合设计要求和技术标准;2. 系统性:建立完善的样件确认体系,涵盖所有相关环节;3. 及时性:样件确认工作应迅速、高效地进行;4. 责任性:明确各相关部门和人员的责任,确保样件确认工作落到实处。
第二章样件确认范围第四条本规定中的样件确认范围包括:1. 新产品研发阶段的样件确认;2. 生产过程中的关键部件样件确认;3. 生产批量前的试制样件确认;4. 产品质量改进过程中的样件确认;5. 其他需要确认的样件。
第三章样件确认流程第五条样件确认流程如下:一、样件准备1. 设计部门根据产品技术要求,完成样件设计;2. 生产部门根据设计图纸,准备生产所需的原材料、设备、工艺等;3. 检验部门制定样件检验标准和方法。
二、样件生产1. 生产部门按照设计图纸和工艺要求,进行样件生产;2. 检验部门在生产过程中对样件进行检验,确保样件质量。
三、样件检验1. 检验部门对样件进行全面检验,包括外观、尺寸、性能等方面;2. 检验部门将检验结果填写在样件检验报告中,并提交给设计部门和生产部门。
四、样件评审1. 设计部门对样件检验报告进行评审,确认样件是否符合设计要求;2. 生产部门对样件评审结果进行审核,确保生产过程符合样件要求;3. 检验部门对样件评审结果进行跟踪,确保样件质量。
五、样件确认1. 设计部门、生产部门和检验部门共同确认样件,签署样件确认书;2. 样件确认书应包括样件名称、型号、规格、检验结果、确认日期等内容。
六、样件改进1. 若样件不符合设计要求,设计部门应提出改进措施,并与生产部门、检验部门共同实施;2. 改进后的样件重新进行检验和确认。
第四章样件确认责任第六条样件确认责任如下:一、设计部门1. 负责样件设计的合理性和可行性;2. 参与样件评审和确认工作;3. 对样件改进提出意见和建议。
APQP全套表格
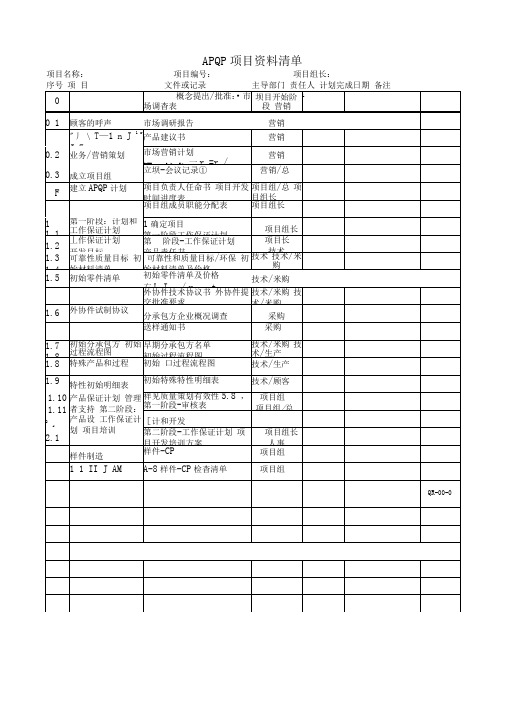
APQP项目资料清单项目名称:项目编号:项目组长:序号项目文件或记录主导部门责任人计划完成日期备注市场调查表-营销功能调查项日期(请贵公司配合营1 填表部门销员填写,谢谢--------填表人1. 贵公司有无需增加供应商?□有□否2. 贵公司所需的原料产品购自□国内:□华东□华南□华中□华北□东北□西北□其它□国外:□英国□日本□德国□台湾□美国□巴西□其它4. 贵公司去年之全球总营业额为:□ $ □¥□ 500 万以下□ 501-1000 万口1001-20卩卩万□ 20PP-3000 万□ 3000 万以上5. 过去曾听说过本公司产品吗?□没有□有▲使用者是否满意□是□否▲使用者是否有提出改进之处,如:□颜色□外表粗糙□阻燃性□耐久性□吸声性□安全性6. 是否有在寻求新的原料供应商?□电子□五金□机械□______________________ .□否□是▲何种原料及产品□板材□管材□内饰件□.□橡胶□塑料□包装□.7. 若贵公司在寻求新的原料供应商▲已有家被列入考虑范围▲产品的需求量为每年 ______ 套(pcs),平均月供货量为希望最早在年月开始供货。
8. 目前所使用其它公司产品的评价:营销员签名/日期:套(pcs).很满意扌两意、外观 ______________________________________颜色 ______________________________________耐久性吸声性—阻燃性目前所使用其它公司产品的价格是否满意―?—□是可否告知价格________________ RMB□否希望调整价格为_________ R MB对目前所使用其它公司产品的售后服务是否满意□满意可否简述原因:______________________________ □不满意可否简述原因:_______________________ 您对产品的意见和建议:顾客签名/日期:不满意很不满意QR-01-01评价项目启动市场调研报告营销功能市场调研报告附件:主机厂车型调研人项目描述产品功能项目编号项目名称编制日期成交得失剖析适销症结所在重要特性特殊要求功能定位手段定位时间定位丿告策应支持□企业宣传□同行竞争_________□—拓展市场□信函传播□广告灯箱□电子媒体□产品开发前□产品开发中□产品开发后产品质量产品开发制造能力经营策略初步结论竞争对手情况分析市场分析概述数据综合比较论结□启动项目□关闭项目□暂时停止□同意□ 不同意项目组长签名日期总经理签名日期QR-01-02APQP产品建议--------- —顾客名称:产品名称:企业本部顾客接口联系人员=联系电话业务洽谈人物资采购部产品工程部附件:洽谈日期质量保证部提供产品功能要求功能项目功能项目说明顾客产品装终检验项目装配特滙_______ 质量保证方行目____配要求装配特性说明供质量证明顾客服务标准□现场服务□定期拜访□技术支持□产品说明书□—安装辅导—□—早期报警_□提供配件□首批送样日期顾客代表签字日期□火车□货车□—空运□船运□质保书□均值极差图□ 全尺寸报告□性能报告□材质报告产品包装要求交货运输方式—运输路线:业务代表签字日期运输里程PPAP提交日期KM业务经理签字日期QR-01-03计划周期:计戈U提—要市场营销计划-营销功能市市场形势产品情况营销现状竞争形势分销情况宏观环境商业价值分析标市场营销策略i术行动方案捕......... 算制编制: 审核: 批准:QR-02-01APQP会议记项目编号: 项目负责人: .希望各部门能通力协作,支持项目负责人的工作,共同完成新产品的开发工作! 管理者代表签名/日期由 / FROM : 致 / TO : 传 /COPP : 日期/ DATA : 营销部[ 总经理[ 项目负责人[20PP.01.00------------------ 项目启动 卜技术部[ 卜管理者代表[ ------- ] ] ——]根据总经理室决定于 日起启动 项目总经理 签名/日期。
IATF16949质量记录控制程序
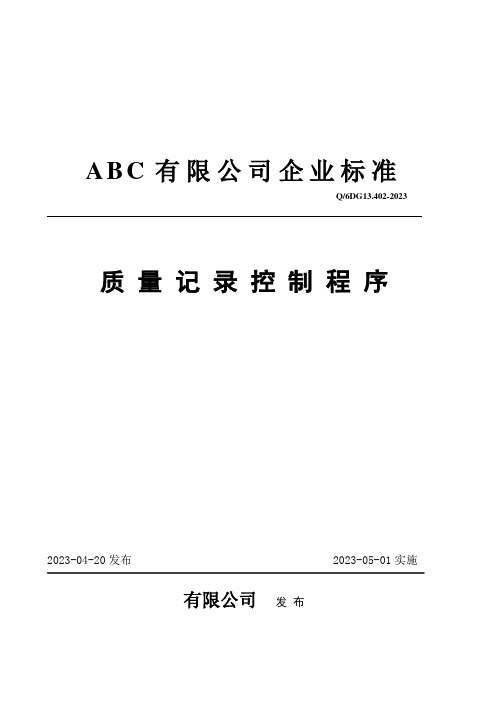
《产品标识和可追溯性程序》
成零件领用单
使用单位
3年
155
工艺路线记录卡
156
配单
159
《顾客财产管理程序》
顾客财产标识卡
使用单位
3年
160
顾客财产管理表
161
外购外协件检验报告单
162
《产品搬运、贮存、包装与防护管理程序》
零组件移交单
使用单位
3年
163
89
供应商和分包商的产品/工艺评定情况(10.3)
90
逻辑流动程序/调节/标签/安全存放(11.1)
91
产品评定/工艺评定计划(12.1)
92
《顾客需求管理程序》
合同订单汇总一览表
经理部和
分厂
3年
93
豫新机械有限公司合同(合同修订)评审表
94
豫新机械有限公司口头订单评审
表
95
《成本核算报价管理程序》
4 术语和定义
质量记录:是指公司按照质量体系文件实施过程的文件化的证据和记录的结果。
日历年:指从一年的1月1日到年底的12月31日共365天
5 职责
各单位负责相关质量记录的标识、收集、编目、归档、贮存、防护、保管、处理和销毁等管理。
6工作流程和内容
工作流程
工作内容说明
使用表单
6.1.表单由各使用单位设计,经质量部核准后编入《程序文件表单集》,按程序文件中的要求选用。
6.5.2各单位按第8条的保存期限要求保管(可参考附件一)。
6.5.3质量记录的防护须注意保管环境(如防火、防水等),避免受潮、损坏、遗失;对于电子媒体的记录应至少备份二份。
《程序文件表单集》
工作流程
APQP项目资料清单excel格式(全套)

4.1 工作保证计划
4.2
试生产 试生产-过程质量记录 试生产产品检验 试生产-状况确认记录
4.3 工时测算
工作时间测算表 PPAP-尺寸结果报告
第 四 阶 段
4.4 试生产产品测试 PPAP-材料试验报告
第 四 阶 段 产 品 和 过 程 确 认
4.4 试生产产品测试 PPAP-性能试验报告 4.5 测量系统评价 4.6 Ppk研究 4.7 生产件批准 4.8 包装评价 测量系统评价 报告 Ppk分析报告 质量 质量 技术 ▲ ▲ ▲ ☆ ▲ ☆ ▲
APQP 项目资料清单
项目名称: 工 作 序号 阶 0 项目 项目编号: 文件或记录 主导部门 责任人 项目经理: 计划完成日期 重要性 备注
概念提出/批准:项目开始阶段 市场调查表 营销 营销 营销 营销 营销 营销/总经理 项目经理 项目经理 项目经理 ★ ▲ ○ ★ ☆ ★ ★ ▲ ▲
0.1 顾客的呼声 项 目 开 始 阶 段
3.1 工作保证计划
3.2 样件生产
样件-过程质量记录 样件-状况确认记录 样件-全尺寸检验报告
3.3 样件测试、检验 样件-性能测试报告 样件-材质检测报告 3.4 样件提交 样品提交顾客认可
3.5 包装标准:顾/供 产品包装标准/规格 产品/过程质量 体系评审 A-4产品/过程质量检查 清单 过程流程图 3.7 过程流程图 A-6过程流程图检查单 场地平面布置图 3.8 场地平面布置图 发目标
1.3 可靠性质量目标 可靠性和质量目标/环保 1.4 初始材料清单 1.5 初始零件清单 第 一 阶 段 计 划 和 确 定 项 目 1.6 外协件试制协议 外协件提交批准要求 分承包方企业概况调查 送样通知书 1.7 初始分承包方 早期分承包方名单 初始材料清单及价格 初始零件清单及价格 外协件技术协议书 外协件质量协议 外协件商务协议
IATF16949项目管理程序
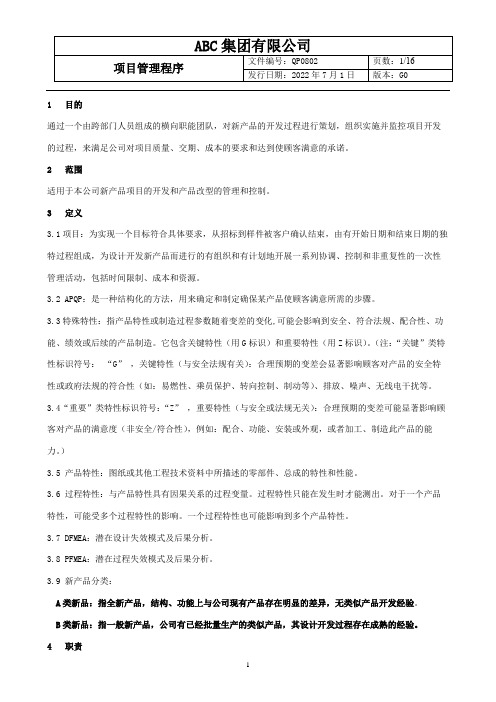
1目的通过一个由跨部门人员组成的横向职能团队,对新产品的开发过程进行策划,组织实施并监控项目开发的过程,来满足公司对项目质量、交期、成本的要求和达到使顾客满意的承诺。
2范围适用于本公司新产品项目的开发和产品改型的管理和控制。
3定义3.1项目:为实现一个目标符合具体要求,从招标到样件被客户确认结束,由有开始日期和结束日期的独特过程组成,为设计开发新产品而进行的有组织和有计划地开展一系列协调、控制和非重复性的一次性管理活动,包括时间限制、成本和资源。
3.2 APQP:是一种结构化的方法,用来确定和制定确保某产品使顾客满意所需的步骤。
3.3特殊特性:指产品特性或制造过程参数随着变差的变化,可能会影响到安全、符合法规、配合性、功能、绩效或后续的产品制造。
它包含关键特性(用G标识)和重要特性(用Z标识)。
(注:“关键”类特性标识符号:“G”,关键特性(与安全法规有关):合理预期的变差会显著影响顾客对产品的安全特性或政府法规的符合性(如:易燃性、乘员保护、转向控制、制动等)、排放、噪声、无线电干扰等。
3.4“重要”类特性标识符号:“Z”,重要特性(与安全或法规无关):合理预期的变差可能显著影响顾客对产品的满意度(非安全/符合性),例如:配合、功能、安装或外观,或者加工、制造此产品的能力。
)3.5 产品特性:图纸或其他工程技术资料中所描述的零部件、总成的特性和性能。
3.6 过程特性:与产品特性具有因果关系的过程变量。
过程特性只能在发生时才能测出。
对于一个产品特性,可能受多个过程特性的影响。
一个过程特性也可能影响到多个产品特性。
3.7 DFMEA:潜在设计失效模式及后果分析。
3.8 PFMEA:潜在过程失效模式及后果分析。
3.9 新产品分类:A类新品:指全新产品,结构、功能上与公司现有产品存在明显的差异,无类似产品开发经验。
B类新品:指一般新产品,公司有已经批量生产的类似产品,其设计开发过程存在成熟的经验。
4职责4.1 集团总经理负责集团战略新产品项目小组的组建,任命项目组组长;子公司总经理负责组建子公司提出的新项目小组的组建,任命项目小组组长,对项目计划及项目报告进行批准,参与阶段评审。
APQP资料目录

技术
2.4
可制造性和装配设计
对设计的产品可制造性和可装配性进行分析
《可制造性和装配设计》
小组
2.5
样件制造-控制计划
编制样件计划,如果需要,应编制样件控制计划
《样件制造计划》
《样件控制计划》《控制计划检查清单》
小组/技术/生产
2.6
检验计划
编制样件需测试的尺寸或性能的检验计划
资料汇总人:资料汇总日期:
《供应商新产品开发协议》
《供应商PPAP提交要求》
技术/采购
1.10
初始特殊特性清单
如顾客有指定时,应纳为公司的特殊特性,如无指定时,项目小线应定义特殊特性并初步识别特殊特性。
《特殊特性确定准则》
《特殊特性清单》(初始)
小组/技术
1.11
初始过程流程图
确定初始过程流程图
《过程流程流程》(样件)
技术
1.12
(如顾客有要求时,必须按顾客要求实施)
全尺寸检验记录/材料、性能试验记录
质检/实验室
2.9
送样确认
按顾客要求的进度和数量,将合格样件送交顾客确认,获得顾客认可。
《样件确认记录》(顾客提供)
技术
2.10
设备/工装/模具配置计划
对新增设备/工装/模具编制相应的配置计划
《设备配置计划》
《工装/模具配置计划》
3.1
包装标准
识别顾客要求,制定包装标准
《包装标准》
小组
3.2
过程流程图
编制过程流程图
《过程流程图》《过程流程图检查清单》
小组
3.3
车间平面布置图
绘制厂区平面布置图及物流图
APQP资料查核对照表
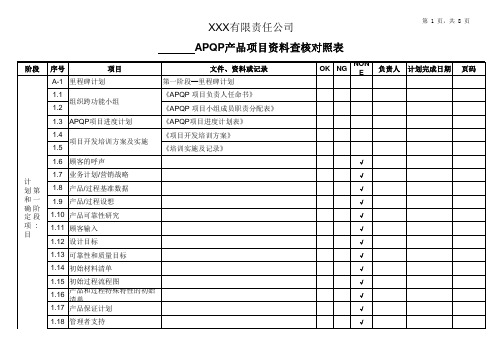
产 品 和第 过四 程阶 确阶段段 认: 阶 段
产 品 和第 过四 程阶 确段 认: 阶 段
反
馈 、
评 定 和
第 五
XXX有限责任公司
APQP产品项目资料查核对照表
序号
项目
文件、资料或记录
4.8 测量系统评价
《装置线性分析报告》
4.9
《偏移独立样本法分析报告》
4.10
《装置稳定性分析报告》
4.11 初始过程能力研究
1.4 项目开发培训方案及实施
1.5
《项目开发培训方案》 《培训实施及记录》
1.6 顾客的呼声
1.7 业务计划/营销战略
1.8 产品/过程基准数据
1.9 产品/过程设想
1.10 产品可靠性研究
1.11 顾客输入
1.12 设计目标
1.13 可靠性和质量目标
1.14 初始材料清单
1.15 初始过程流程图
《测量系统分析计划》
OK
NG
NON E
负责人 计划完成日期
页码
《初始过程能力研究计划》
《包装作业指导书》
《管理者支持》
第三阶段—里程碑审核表 第四阶段—里程碑计划 《试生产作业计划》 《首件检验报告》 《制作过程检验报告》-生产和巡检记录 《工作时间测定表》 《试生产总结报告》 《量具重复性和再现性(均值极差法)》 《计数型量具小样法(短程法)》
1.16
产品和过程特殊特性的初始 清单
1.17 产品保证计划
1.18 管理者支持
OK
NG
NON E
负责人 计划完成日期
页码
√ √ √ √ √ √ √ √ √ √ √ √ √
阶段
产 品 设第 计二 和阶 开段 发: 阶 段
新产品OTS认可流程规范及文件模板汇总

研究院在与供应商确定提交的内容时,可参考表1。
表1
序号
交付物清单
提交单位
接收单位
备注
1
工装样件提交保证书
供应商
研究院
2
尺寸检测报告
3
材料检测报告并附原始试验报告
4
性能检测报告并附原始试验报告
5
外观批准报告
供应商
研究院
6
法规件标识检验报告
7
禁用物质批准报告
8
工装样件
9
子零部件供应商清单
5.4 工装样件认可条件
5.4.1供应商应在规定的开发节点提供用于认可的工装样件,提供规定的样条、样块、检查辅具、文件规范、试验和检验记录、材料自检报告等,样件应确保按规定进行标识,否则接收部门应予拒收。
5.4.2认可时,产品图纸必须为“TG2”阶段,相关标准或规范必须制订完毕,DVP必须得到确认,相关产品检具、夹具必须已经验收合格,其组成系统满足整车目标设计要求(如果适合)。其样件状态确定为全工装、全序的样件,才能作为性能台架试验、搭载路试和尺寸认可的样件。
6.4.5专业部门工程师在接到外观工装样件1 个工作日内提交给造型部,造型部在1个工作日内完成确认;如果外观合格,造型部批准《外观批准报告》,如果外观不合格,要求供应商限期整改。
6.5 油漆件的认可
6.5.1外饰和内饰油漆件OTS认可由各专业主控
6.5.2外饰和内饰油漆件的色板由造型部联系供应商发放
6.5.3工程技术部负责工艺标准色板复制与色板管理,下发工艺标准色板
6.5.4制造品控部负责整车外观色差匹配等相关工作
6.6法规件的认可
6.6.1专业部门工程师负责法规件(法规件清单见附件四)的认可;
产品质量先期策划控制程序

1目的本程序确定产品开发全过程的各个步骤,促进与所涉及的每个职能部门的联系,保证开发进程;尽早发现所需更改,确保产品使顾客满意。
2范围本程序适用于本公司所有新产品开发和顾客工程更改后须按PPAP规定重新送样的产品〔如果客户有特殊要求,依照客户的特殊要求规定的流程进行新产品的开发〕。
3术语和定义3.1APQP:产品质量先期筹划3.2PPAP:生产件批准程序3.3DFMEA:设计失效模式及后果分析3.4PFMEA:过程潜在的失效模式及后果分析3.5MSA:测量系统分析3.6OTS:工装样件,采用生产用模具、夹具模拟生产工艺,可不用生产用的设备,不按生产节拍生产,用来评价产品和过程试验筹划。
3.7SOP:批量生产件4作业流程工程部工程部财务部工程部顾客代表总经理工程小组组长工程小组组长工程部工程小组工程小组组长总经理工程小组组长工程小组组长1第一阶段:方案和确定工程根据公司开展方向、经营方案及顾客要求编写顾客访谈报告,部门评议后将访谈的新产品背景信息、技术和质量要求及开发周期、费用预期价格等形成?产品建议书?附带产品图纸、样件、标准、特殊要求等提交给工艺工程部;组织成立工程小组(包括:生产部及工程部、品质部、财务部、资材部、业务部、管理部等部门〕根据:产品开发建议书、图纸/样件/数模/技术标准,在考虑工艺、工装、设施、材料、人员等要求,并与同类产品进行比拟后进行:组织进行本钱核算工作,本钱核算包含商务及技术本钱并提供报价单;组织各职能部门对产品建议书、技术可行性分析、本钱分析及产品其他的信息进行评审。
评审意见记录在“立项评审表〃中,评审通过经总经理批准后立项。
1组织成立工程小组并确立工程负责人,小组成员应来自以下部门:工程部、品质部、生产部及资材部、业务部、财务部、管理部,必要时,可有供方或顾客代表参加。
2明确小组成员及职责、开发周期、费用和关键时间节点:小组全体成员须按公司保密性承诺对客户工程所有信息予以保密。
IATF 16949 受控文件清单

受控文件清单BX/QR8201 顾客满意度调查计划(24)BX-QP-13顾客满意度调查管理程BX/QD8201BX/QR8202 顾客满意度调查表(C5 顾客满意)BX/QR8203 顾客满意度调查分析报告BX/QR8204 年度内部审核计划(25)BX-QP-04内部审核控制程序BX/QR8205内部质量审核实施计划(M4 内部审核)BX/QR8236 内审检查表BX/QR8207 不符合项报告BX/QR8208 不符合项分布表BX/QR8209 质量体系审核报告BX/QR8210 内审首末次会议签到表BX/QR8211过程审核计划BX/QD8202BX/QR8212 过程审核表BX/QR8213 过程审核评价报告BX/QR8214 产品审核计划BX/QD8203BX/QR8215 产品质量审核记录表BX/QR8216 产品质量审核评价报告BX/QD8204 外购外协件检验/试验指导书BX/QR8217 外购外协件产品入库检验记录(26)BX-QP-21检验和试验控制程序BX/QD8205 半成品检验/试验指导书BX/QR8218 过程检验记录(S9 检验和试验)BX/QD8206 成品检验/试验指导书BX/QR8219 成品检验记录BX/QR8220出货检验报告BX/QR8301 不合格品评审及处置单(27)BX-QP-20不合格品控制程序BX/QR8302 退货单(S10 不合格品控制)BX/QR8303让步接收申请单BX/QD8301BX/QR7538退料单BX/QR8304 返工单BX/QR8305 产品特采放行单BX/QR8306 报废申请单BX/QR8307不合格品统计表BX/QR8501年度持续改进项目计划表(28)BX-QP-18数据分析和持续改进程BX/QR8502 持续改进项目实施验证报告(M5 持续改进)BX/QR8301 不合格品评审及处置单(29)BX-QP-19纠正和预防措施管理程BX/QR8503 纠正预防措施通知单(S11 纠正和预防措BX/QD8501BX/QR7545 顾客反馈意见处理书BX/QR8504 纠正预防措施一览表BX/QR85058D报告编制/日期: 批准/日期: 3.2010年返工(返修)作业指导书3年无5年过程审核指导书 VDA6.33年产品审核指导书 VDA6.5 8D编写指导书3年3年顾客满意度统计分析方法长期无3年。