变速器壳体立式加工中心技术要求
VMC850B立式加工中心技术协议

VMC850B立式加工中心技术协议1.引言本技术协议旨在明确双方对于VMC850B立式加工中心(硬轨)的技术要求、质量标准、售后服务、价格及交付方式等方面的达成一致。
2.技术要求2.1加工范围- X轴行程应不小于800mm;- Y轴行程应不小于500mm;- Z轴行程应不小于550mm;- 主轴鼻端到工作台面的最小距离应不大于650mm;- 工作台面到滑板面的最大距离应不小于1050mm。
2.2主要技术参数- 主轴转速范围应在60-8000rpm之间;-主轴最大输出扭矩应不小于95N.m;- 快速移动速度应不小于15m/min;- 切削进给速度应不小于10m/min;3.质量标准3.1外观要求-表面应无明显划痕、麻点、色差等缺陷;-安装的各个部件应紧固牢固,无松动、脱落现象。
3.2电气性能要求-各电气元器件的安装应符合国家标准,接线应牢固可靠;-控制柜内的接线排列应整齐,标识清晰,易于维修和更换元器件;-控制系统应能够准确、稳定地控制加工中心的各项运动。
3.3加工精度要求-加工表面光洁度应达到国家标准GB/T6060-1996中第8级的要求;4.售后服务4.1装置和调试卖方应负责VMC850B立式加工中心(硬轨)的装置和调试工作,确保设备正常运行并达到产品规定的技术参数。
4.2培训卖方应提供对买方操作人员的培训,包括设备操作、常见故障排除和日常维护保养等方面的知识。
4.3售后服务期限卖方提供的售后服务期限为设备装置和调试结束后的12个月内,如果设备出现质量问题,卖方负责免费维修或更换。
5.价格及交付方式5.1价格5.2付款方式买方需要以XX%的百分比作为定金,在合同签署后的7天内支付。
剩余款项则在设备装置和调试完工后的15天内一次性支付。
5.3交付方式买方需要指定所需设备的交付地址,卖方负责将设备运送到指定地点,并承担相应的运输费用。
6.其他约定事项本技术协议独立于其他协议,任何与之相关的争议应通过友好协商解决。
立式加工中心的操作规程

立式加工中心的操作规程一、引言立式加工中心是一种高精度的数控机床,广泛应用于金属加工领域。
为了确保操作的安全性和加工的质量,制定本操作规程以指导操作人员正确操作立式加工中心。
二、安全操作规定1. 操作人员应经过专业培训,熟悉立式加工中心的结构和主要部件。
2. 在操作前,必须佩戴合适的个人防护装备,包括安全帽、护目镜、耳塞等。
3. 在加工过程中,严禁戴手套、长袖衣物或长发,以免发生危险事故。
4. 在操作中心时,操作人员应保持专注,禁止喧哗和嬉戏。
5. 加工过程中,切勿随意触摸运动中的零件,防止受伤。
6. 操作人员应严格按照操作规程操作,不得擅自更改程序或参数设置。
7. 加工结束后,关闭加工中心电源,并做好现场整理和清洁工作。
三、操作流程1. 开机准备- 检查润滑油、冷却液、切削工具等供应是否充足。
- 打开电源总开关,启动加工中心。
- 进入操作界面,确认系统正常运行。
2. 工件装夹- 检查工件和夹具的表面是否干净,及装夹是否牢固。
- 将工件放置在夹具上,调整位置和角度,确保不与切削工具发生碰撞。
3. 选择程序- 在操作界面上选择需要的加工程序。
- 确认程序所需的切削工具和刀具尺寸是否正确。
4. 设置工艺参数- 根据工艺要求,设置合适的工艺参数,如进给速度、转速等。
- 设置好刀具的补偿值,以保证加工精度。
5. 示教操作- 在示教模式下,通过操纵手柄控制加工中心进行手动运动,调整刀具起点、终点和路径。
- 确认示教路径和参数设置的正确性。
6. 开始加工- 手动将刀具移至离工件一定距离的起点位置。
- 启动自动运行,加工中心按照预设程序进行加工操作。
- 监视加工过程,保证加工品质。
7. 加工结束- 加工完成后,关闭自动运行开关。
- 清理加工现场,清除废屑和切削液。
- 关闭加工中心电源,保持设备整洁。
四、常见故障处理1. 切削声音突然变大或异响:立即停止加工,检查切削工具是否磨损或松动。
2. 加工速度变慢或暂停:检查加工程序和参数设置是否正确,排除故障后重新启动。
立式加工中心技术参数指标

联轴器
KTR或R+W公司
空气开关
优质品牌
行程开关
优质品牌
拖链
优质品牌
电器接触器
优质品牌
水泵电机
优质品牌
刀库
优质品牌
自动排屑功能
机外链板式自动排屑器
机床重量
KG
≥6000
CNC控制系统采用FANUC Oi-MC,数控系统配备标准RS-232接口、CF卡及通讯线缆。机床床身铸件由制造商自行生产。
伺服电机最大扭矩
N.m
≥12
精度
定位精度(全程)
mm
≤X/Y/Z:±0.006
重复定位精度(全程)
mm
≤X/Y/Z:±0.004
刀库
换刀方式
机械手
刀具数
pcs
≥20
刀具最大长度
mm
≥350
刀具最大直径
mm
≥180
刀具最大重量
kg
≥8
其它
冷泵电机
kw
≥0.5
滚珠丝杆轴承
NSK
线性导轨
宽度≥45mm
润滑系统
rpm
≥8000
主轴孔锥度
-
BT-40
主轴电机功率
kw
≥5.5/7.5
FANUCα电机
主轴组
优质品牌
主轴轴承
NSK(前4后2形式)
X/Y/Z轴快速位移
m/min
≥30/30/30
最大切削进给率
m/min
10
X、Y、Z滚珠丝杠
≥Φ40mm
预拉伸技术
X、Y、Z丝杠支撑形式
双端定位
X、Y、Z电机功率
kw
≥3FANUCα电机
汽车变速箱壳体机械加工工艺规程及夹具设计

编号20171352113本科生毕业设计汽车变速箱壳体机械加工工艺规程及夹具设计Processing Technology and Fixture Design of Automobile Gearbox学生姓名专业机械电子工程学号指导教师分院机电工程分院2017年6月摘要本设计是汽车变速箱箱体零件的加工工艺规程及一些工序的专用夹具设计。
汽车变速箱箱体零件的主要加工表面是平面及孔系。
一般来说,保证平面的加工精度要比保证孔系的加工精度容易。
因此,本设计遵循先面后孔的原则。
并将孔与平面的加工明确划分成粗加工和精加工阶段以保证孔系加工精度。
基准选择以变速箱箱体的输入轴和输出轴的支承孔作为粗基准,以顶面与两个工艺孔作为精基准。
主要加工工序安排是先以支承孔系定位加工出顶平面,再以顶平面与支承孔系定位加工出工艺孔。
在后续工序中除个别工序外均用顶平面和工艺孔定位加工其他孔系与平面。
支承孔系的加工采用的是坐标法镗孔。
整个加工过程均选用组合机床。
夹具选用专用夹具,夹紧方式多选用气动夹紧,夹紧可靠,机构可以不必自锁。
因此生产效率较高。
适用于大批量、流水线上加工。
能够满足设计要求。
关键词:变速箱加工工艺专用夹具ABSTRACTThe design is about the special-purpose clamping apparatus of the machining technology process and some working procedures of the car gearbox parts. The main machining surface of the car gearbox parts is the plane and a series of hole. Generally speaking, to guarantee the working accuracy of the plane is easier than to guarantee the hole’s. So the design follows the principle of plane first and hole s econd. And in order to guarantee the working accuracy of the series of hole, the machining of the hole and the plane is clearly divided into rough machining stage and finish machining stage. The supporting hole of the input bearing and output bearing is as the rough datum. And the top area and two technological holes are as the finish datum. The main process of machining technology is that first, the series of supporting hole fix and machine the top plane, and then the top plane and the series of supporting hole fix and machine technological hole. In the follow-up working procedure, all working procedures except several special ones fix and machine other series of hole and plane by using the top plane and technological hole. The machining way of the series of supporting hole is to bore hole by coordinate. The combination machine tool and special-purpose clamping apparatus are used in the whole machining process. The clamping way is to clamp by pneumatic and is very helpful. The instruction does not have to lock by itself. So the product efficiency is high. It is applicable for mass working and machining in assembly line. It can meet the design requirements.Keywords: Gearbox machining-technology special-purpose clamping apparatus目录绪论 (1)第一章汽车变速箱加工工艺规程设计 (2)1.1 零件的分析 (2)1.1.1零件的作用 (2)1.1.2零件的工艺分析 (2)1.2 箱体加工的主要问题和工艺过程设计所应采取的相应措施 (2)1.2.1孔和平面的加工顺序 (3)1.2.2孔系加工方案选择 (3)1.3 变速箱箱体加工定位基准的选择 (5)1.3.1粗基准的选择 (5)1.3.2精基准的选择 (5)1.4变速箱箱体加工主要工序安排 (6)1.5机械加工余量、工序尺寸及毛坯尺寸的确定 (7)第二章专用夹具设计 (12)2.1加工工艺孔夹具设计 (12)2.1.1定位基准的选择 (12)2.1.2切削力的计算与夹紧力分析 (12)2.1.3夹紧元件及动力装置确定 (13)2.1.4钻套、衬套、钻模板及夹具体设计 (14)2.1.5夹具精度分析 (15)2.1.6夹具设计及操作的简要说明 (16)2.2粗铣前后端面夹具设计 (17)2.2.1定位基准的选择 (17)2.2.2定位元件的设计 (17)2.2.3定位误差分析 (18)2.2.4铣削力与夹紧力计算 (19)2.2.5定向键与对刀装置设计 (20)2.2.6夹紧装置及夹具体设计 (21)2.2.7夹具设计及操作的简要说明 (23)结论 (25)参考文献 (26)致谢 (27)绪论夹具设计作为高等工科院校教学的基本训练科目,在毕业设计中占极其重要的位置。
立式加工中心操作规程全部
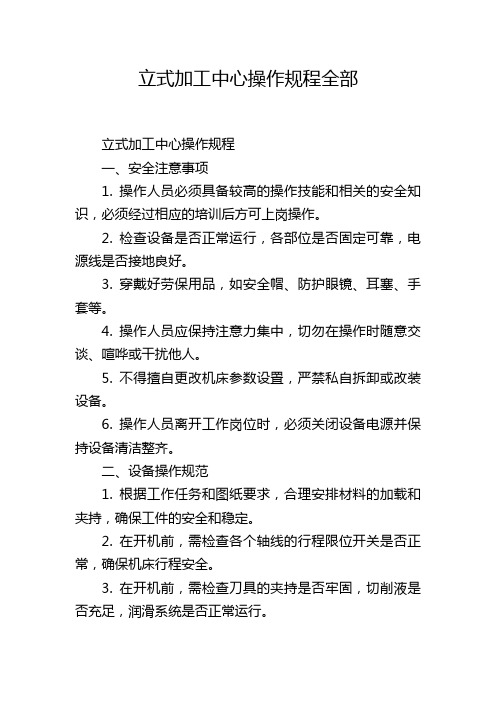
立式加工中心操作规程全部立式加工中心操作规程一、安全注意事项1. 操作人员必须具备较高的操作技能和相关的安全知识,必须经过相应的培训后方可上岗操作。
2. 检查设备是否正常运行,各部位是否固定可靠,电源线是否接地良好。
3. 穿戴好劳保用品,如安全帽、防护眼镜、耳塞、手套等。
4. 操作人员应保持注意力集中,切勿在操作时随意交谈、喧哗或干扰他人。
5. 不得擅自更改机床参数设置,严禁私自拆卸或改装设备。
6. 操作人员离开工作岗位时,必须关闭设备电源并保持设备清洁整齐。
二、设备操作规范1. 根据工作任务和图纸要求,合理安排材料的加载和夹持,确保工件的安全和稳定。
2. 在开机前,需检查各个轴线的行程限位开关是否正常,确保机床行程安全。
3. 在开机前,需检查刀具的夹持是否牢固,切削液是否充足,润滑系统是否正常运行。
4. 开机前,需将设备切换至手动模式,进行坐标轴、刀具的试动,确认无异常情况后方可切换至自动模式。
5. 调整加工参数时需谨慎操作,严禁超过设备的额定工作负荷,以免损坏设备或造成工件质量不合格。
6. 操作过程中,应随时观察加工状态,确保切削过程中切屑的排出畅通,防止切屑带入工件内部。
7. 当切削过程产生异常响声或其他异常情况时,应立即停机检查并采取相应措施解决问题,并记录异常情况及处理过程。
8. 完成加工后,及时停机并关闭设备电源,待设备彻底停止运行后方可关离合器。
三、设备维护保养1. 每天开机前和停机后,需进行设备的清洁工作,清理切削屑和润滑油,确保设备的清洁整洁。
2. 检查润滑系统的润滑油和冷却液的供给是否正常,及时补充或更换润滑油和冷却液。
3. 定期检查易损件的磨损情况,如刀具、夹具等,及时更换损坏的部件。
4. 定期对设备进行维护保养,包括清洁、润滑、紧固、调整等工作,确保设备的正常运行。
5. 设备故障时,应及时报修,确保设备的及时维修和保养。
四、操作记录1. 对每次加工操作进行详细的记录,包括工作日期、设备运行时间、加工工件及数量、使用的刀具和夹具等。
立式加工中心操作规程
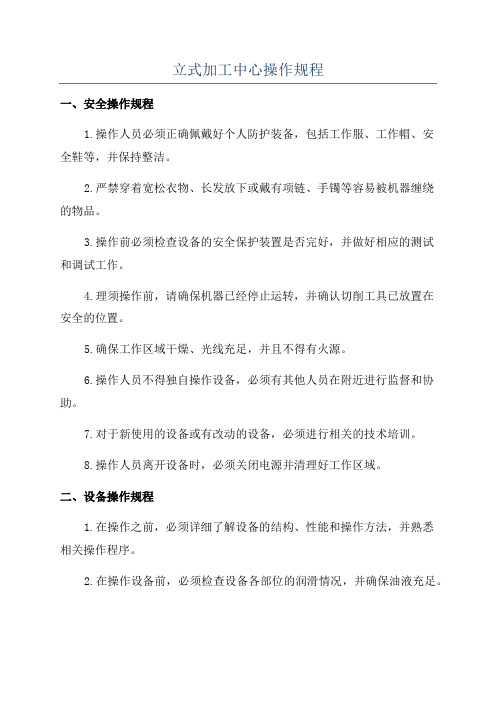
立式加工中心操作规程一、安全操作规程1.操作人员必须正确佩戴好个人防护装备,包括工作服、工作帽、安全鞋等,并保持整洁。
2.严禁穿着宽松衣物、长发放下或戴有项链、手镯等容易被机器缠绕的物品。
3.操作前必须检查设备的安全保护装置是否完好,并做好相应的测试和调试工作。
4.理须操作前,请确保机器已经停止运转,并确认切削工具已放置在安全的位置。
5.确保工作区域干燥、光线充足,并且不得有火源。
6.操作人员不得独自操作设备,必须有其他人员在附近进行监督和协助。
7.对于新使用的设备或有改动的设备,必须进行相关的技术培训。
8.操作人员离开设备时,必须关闭电源并清理好工作区域。
二、设备操作规程1.在操作之前,必须详细了解设备的结构、性能和操作方法,并熟悉相关操作程序。
2.在操作设备前,必须检查设备各部位的润滑情况,并确保油液充足。
3.操作人员应按照规定的加工工序和工艺参数进行操作,不得随意更改。
4.加工对象必须与操作人员通信,做好配合工作,并确保工件固定牢靠。
5.在加工中,严禁用手触摸旋转和运动的部件,必须使用相应的工具。
6.在紧急情况下,应迅速按下停机按钮,并通知相关人员进行紧急处理。
7.在设备异常时,不得擅自进行维修和调整,必须请专业人员进行处理。
8.加工完成后,必须及时清理设备和工作区域,保持整洁。
三、刀具操作规程1.刀具的安装和调整必须由专业人员进行,不得擅自操作。
2.在操作刀具前,必须检查刀具的磨损情况,并按照操作手册进行更换。
3.调整刀具时,首先必须切断电源,并使用专用工具进行操作。
4.禁止用手直接接触刀具,必须使用专用工具进行调整和更换。
5.刀具更换完成后,必须进行试运转,确保刀具安装正确并且没有松动。
6.刀具的存放和保养必须按照相关要求进行,严防损坏和丢失。
7.使用过的刀具必须及时清洗干净,保存在专用的刀具柜中。
四、维护保养规程1.设备的日常维护保养工作必须定期进行,并建立相关记录。
2.在设备运行中,必须定期检查各部位的润滑情况,及时添加润滑油。
立式加工中心技术要求
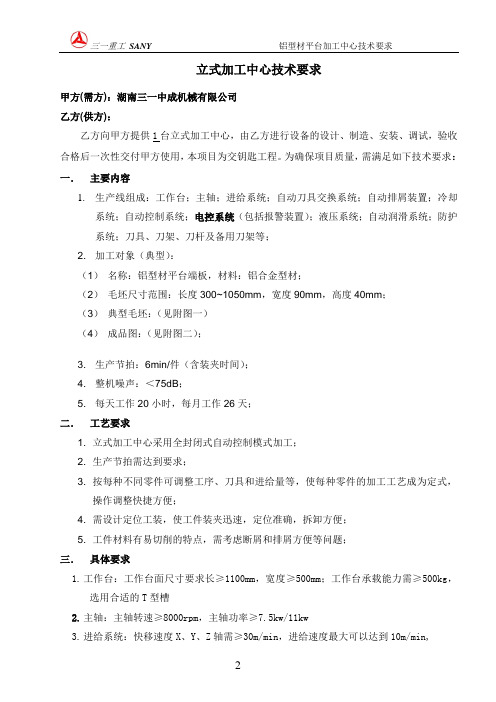
7.每月工作26天,每天使用20小时,无功能性故障;
8.人机交互部分(如:控制手柄、按钮、负载指示器等装置),均以人机工程学规律正常工作舒适布局,易于紧急情况下辩认及动作。且所有外置件均有铭牌标志,易于紧急情况下辨认及操作;
9.设备颜色按甲方要求;
10.配置5套易损件;
11.环保与安全:生得制造商所在地检验合格证,检验费用由供方承担;
七.验收标准
1.电气符合GB-5226.1电气标准;
2.机床精度按检验通则GB/T17421.2—2000执行;
3.设备制造完成后需在乙方进行试切试验和预验收;
4.连续运行15天,设备质量均符合本技术要求的各项指标;
5.培训:经乙方培训的人员必须达到甲方的上岗要求;
6.加工过程中出现撞刀、刀具损坏等非人为异常现象均视为未达到验收条件。
2.加工对象(典型):
(1)名称:铝型材平台端板,材料:铝合金型材;
(2)毛坯尺寸范围:长度300~1050mm,宽度90mm,高度40mm;
(3)典型毛坯:(见附图一)
(4)成品图:(见附图二);
3.生产节拍:6min/件(含装夹时间);
4.整机噪声:<75dB;
20寸加工中心技术参数及要求

立式加工中心技术参数及要求
(20寸)
1、工作台尺寸≥1100mm×500mm
2、X/Y/Z轴行程≥850/510/560MM
3、X/Y/Z轴交流伺服电机 2.1/2.1/3.8KW
4、X轴快速移动速度≥20MM/min
5、Y轴快速移动速度≥20MM/min
6、z轴快速移动速度≥20MM/min
7、切削进给率最大值≥8000MM/min
8、主轴鼻端至工作台面距离最大值≥775MM
9、主轴中心至立柱距离≥520MM
10、主轴马达≥9KW(11KW)
11、主轴最大转速≥8000rpm
12、主轴锥度BT40
13、刀库容量≥24把
14、选刀方式双向任意式(转臂式)
15、换刀时间≤2.5秒
16、主轴数单轴
17、功能钻孔(刚性、柔性)攻牙、铣削
18、控制系统FANUC0i-M或SIEMENS等同档次先进数控系统
19、拉钉角度90度
20、刀具最大直径≥90MM(相邻有刀)
21、刀具最大长度250MM
22、系统分辨率0.001mm
23、重复定位精度±0.002(JIS标准)
24、定位精度±0.005(JIS标准)
25、主轴径向/端面跳动0.01mm
26、气压要求≤4.5KG
27、排屑装置排屑装置(侧排式)+螺旋排屑
28、电控柜除湿制冷装置
等同档次先进数控系统。
变速器外壳机械加工工艺说明书

目录摘要 (3)引言 (5)1.工艺规程的制定 (6)1.1确定生产类型 (6)1.2 零件分析 (6)1.3 工艺规程设计 (12)1.3.1基准选择 (12)1.3.2 表面加工方方案的选择 (13)1.3.3加工阶段的划分 (14)1.3.4 机械加工顺序的安排 (14)1.3.5 工序集中与分散 (16)1.3.6 加工余量及工序尺寸的确定 (17)1.3.7 工序的确定和比较 (17)1.4 工序内容设计 (19)1.4.1 加工设备选择 (19)1.4.2 刀具的选择........................................................ 错误!未定义书签。
1.4.3 确定各工序切削用量...................................... 错误!未定义书签。
2 钻床夹具设计............................................................................ 错误!未定义书签。
2.1钻床夹具的加工方案分析............................................. 错误!未定义书签。
2.2钻床夹具的定位方案分析和夹紧方案分析................. 错误!未定义书签。
2.2.1钻床夹具的定位分析........................................... 错误!未定义书签。
2.2.2 钻床夹具的定位误差分析与计算...................... 错误!未定义书签。
2.2.3夹紧力的计算和气缸的选择............................... 错误!未定义书签。
3 铣床夹具设计 (39)3.1铣床夹具的加工方案分析 (39)3.2铣床夹具的定位方案分析和夹紧方案的分析............. 错误!未定义书签。
立式加工中心安全技术操作规程
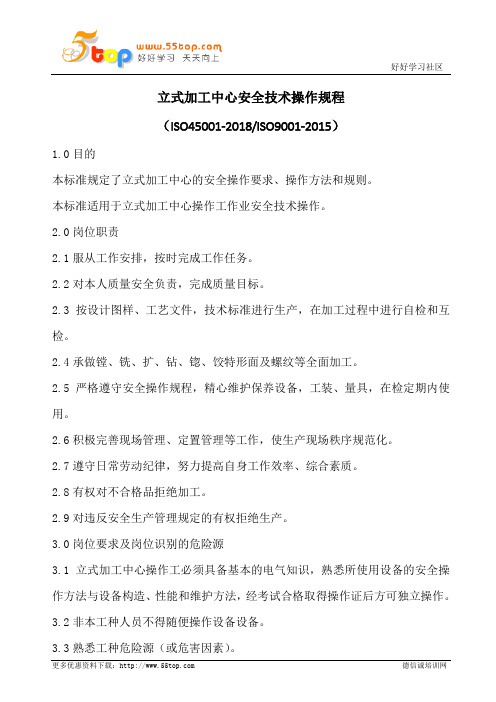
立式加工中心安全技术操作规程(ISO45001-2018/ISO9001-2015)1.0目的本标准规定了立式加工中心的安全操作要求、操作方法和规则。
本标准适用于立式加工中心操作工作业安全技术操作。
2.0岗位职责2.1服从工作安排,按时完成工作任务。
2.2对本人质量安全负责,完成质量目标。
2.3按设计图样、工艺文件,技术标准进行生产,在加工过程中进行自检和互检。
2.4承做镗、铣、扩、钻、锪、饺特形面及螺纹等全面加工。
2.5严格遵守安全操作规程,精心维护保养设备,工装、量具,在检定期内使用。
2.6积极完善现场管理、定置管理等工作,使生产现场秩序规范化。
2.7遵守日常劳动纪律,努力提高自身工作效率、综合素质。
2.8有权对不合格品拒绝加工。
2.9对违反安全生产管理规定的有权拒绝生产。
3.0岗位要求及岗位识别的危险源3.1立式加工中心操作工必须具备基本的电气知识,熟悉所使用设备的安全操作方法与设备构造、性能和维护方法,经考试合格取得操作证后方可独立操作。
3.2非本工种人员不得随便操作设备设备。
3.3熟悉工种危险源(或危害因素)。
3.4危险源(或危害因素)分析3.4.1物体打击吊装零件时,起吊不稳至零件掉落伤人。
3.4.2触电3.4.2.1人体直接接触到设备带电部位、电源等造成触电。
3.4.2.2设备漏电、设备因过载、短路、绝缘老化等引起电气火灾、触电等。
3.4.3其他伤害违章作业造成人员伤害等。
4.0操作方法4.1工作服必须经常保持清洁和完好,禁止围围巾,切削时要戴好防护眼镜等劳保用品,加工过程中禁止戴手套,超过颈根的长发应挽在帽子里。
4.2 经常整理自己的工作区域,搬走工作中不需要的东西,所有现场物品定置摆放。
4.3工作前检查。
4.3.1检查各部位的保护盖是否安装良好。
4.3.2当电源输入后请注意一些准备完成指示灯是否亮着。
4.3.3确定没有任何马达或其他部位产生异声。
4.3.4当机器第一次操作或长时间停止后,每个滑轨面均须先加润滑油,故让机器开机但不运转约过30分钟,便于润滑油泵将油打至滑轨面后再运转. 4.3.5当第一次使用机器时,请注意排屑机马达,切削液马达的旋转方向是否正确。
立式加工中心的几何精度检验要求(出口用技术要求)
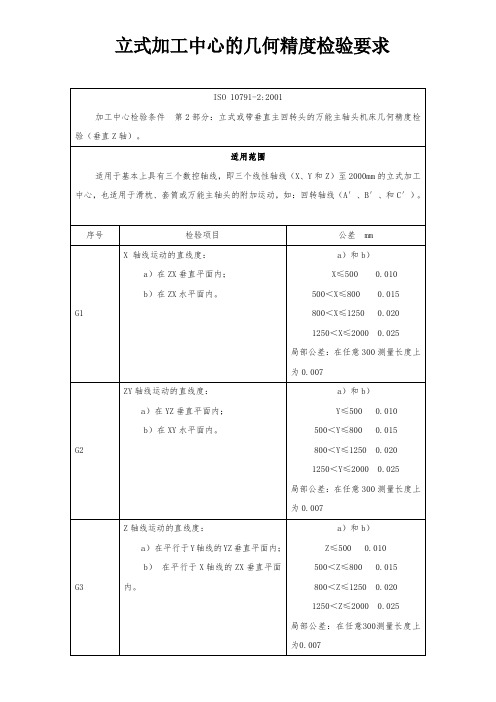
立式加工中心的几何精度检验要求G4X轴线运动的角度偏差:a)在平行于移动方向的ZX垂直平面内(俯仰);b)在XY水平面内(偏摆);c)在垂直于移动方向的YZ垂直平面内(倾斜)。
a)、b)和c)0.060/1000(或60微弧度或12角秒)G5Y轴线运动的角度偏差:a)在平行于移动方向的YZ垂直平面内(俯仰);b)在XY水平面内(偏摆);c)在垂直于移动方向的ZX垂直平面内(倾斜)。
a)、b)和c)0.060/1000(或60微弧度或12角秒)G6Z轴线运动的角度偏差:a)在YZ垂直平面内;b)在ZX垂直平面内;c)在XY水平面内。
a)、b)和c)0.060/1000(或60微弧度或12角秒)G7Z轴线运动和X轴线运动间的垂直度在500测量长度上为0.020。
G8Z轴线运动和Y轴线运动间的垂直度在500测量长度上为0.020。
G9Y轴线运动和X轴线运动间的垂直度在500测量长度上为0.020。
G10a)主轴的周期性轴向窜动;b)主轴端面跳动。
a)0.005 b)0.010G11主轴锥孔的径向跳动:a)靠近主轴端部;b)距主轴端部300处。
a)0.010b)0.020G12主轴轴线和Z轴线运动间的平行度:a)在YZ垂直平面内;b)在ZX水平面内。
a)及b)在300测量长度上为0.015G13主轴轴线和X轴线运动间的垂直度0.020/300 G14主轴轴线和Y轴线运动间的垂直度0.020/300G15工作台面的平面度L≤5000.020500<L≤8000.025800<L≤12500.0301250<L≤≤20000.040L为工作台或托板的较短边。
局部公差:在任意300测量长度上为0.012G16工作台面和X轴线运动间的平行度X≤5000.020500<X≤8000.025800<X≤12500.0301250<X≤20000.040G17工作台面和Y轴线运动间的平行度Z≤5000.020500<Z≤000.025800<Z≤12500.0301250<Z≤20000.040G180º位置时工作台ª的:a)纵向中央或基准T形槽;或b)纵向定位孔的中心线(如果有);或c)纵向侧面定位器和X轴线运动间的平行度。
变速器加工工艺知识-壳体、轴、齿轮
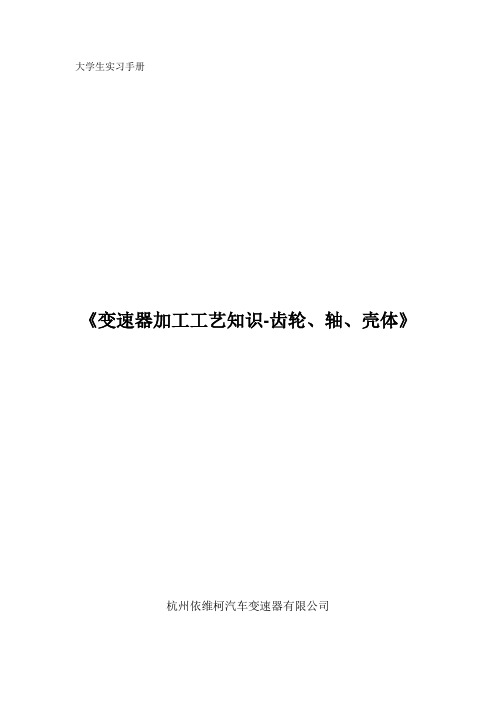
大学生实习手册《变速器加工工艺知识-齿轮、轴、壳体》杭州依维柯汽车变速器有限公司现状描述:目前,我公司生产的汽车变速器主要是采用手动换挡型式,匹配发动机排量为0.8-1.8L,搭载于经济型轿车上。
随着近今年的发展,逐步往自动换档型发展。
变速器主要涉及核心零件轴及齿轮、壳体的生产、总成装配、试验检测等过程在公司内进行。
第一部分:齿轮、轴类零件1.齿轮工艺流程简介:齿轮一般有两种结构:根据不同结构要求.齿轮零件加工主要工艺流程采用的是锻造制坯→正火→精车加工→插齿→倒尖角→滚齿→剃齿→(焊接)→热处理→磨加工→对啮修整。
热后齿部一般不再加工,除了主减从齿或顾客要求磨齿的零件。
2.轴类工艺流程简介:输入轴:锻造制坯→正火→精车加工→搓齿→钻孔→插齿→倒尖角→滚齿→剃齿→热处理→磨加工→对啮修整。
输出轴:锻造制坯→正火→精车加工→搓齿滚齿→剃齿→热处理→磨加工→对啮修整。
3.具体工艺流程简介:详细介绍如下:(1)锻造制坯:热模锻是汽车齿轮件广泛使用的毛坯锻造工艺。
以前较广泛采用的是热锻和冷挤压的毛坯,近年来,楔横轧技术在轴类加工上得到了大量推广。
这项技术特别适合为比较复杂的阶梯轴类制坯,它不仅精度较高、后序加工余量小而且生产效率高。
比如我公司生产的H331.6A及H319.5A的轴类毛坯就是采用楔横轧,现在已逐步实现了批量生产。
(2)正火:这一工艺的目的是获得适合后序齿轮切削加工的硬度和为最终热处理做组织准备,以有效地减少热处理变形。
公司所用齿轮钢的材料通常为20CrMnTi(H)及20MnCr5,一般的正火由于受人员、设备和环境的影响比较大,使得工件冷却速度和冷却的均匀性难以控制,造成硬度散差大,金相组织不均匀,直接影响机加工和最终热处理;使得热变形大而无规律,零件质量无法控制,对刀具的磨损也较大,尤其对搓齿这种受力大的工序更是明显。
为此,采用等温正火工艺。
实践证明,采用这种等温正火有效地改变了一般正火的弊端,产品质量稳定可靠。
立式加工中心技术要求立式加工中心技术要求

立式加工中心技术要求立式加工中心技术要求
标准标准机床规格机床规格
主 轴 主轴电机
15/11/7.5KW(10分钟/30分钟/连续)
主轴锥孔规格 BT-40
主轴转速 40--10000rpm 行 程 X 轴行程 1120mm Y 轴行程 510mm Z 轴行程
510mm
主轴端面至工作台面 180-690mm
主轴中心至立柱前面 510mm
工 作 台 工作台面积
1460×510mm
T 型槽(宽×数目×距离) 18mm×5×100mm 进 给 快速移动 X/Y/Z 轴30m/min 进给速度 1-8000mm/min ATC 刀库容量 24把 刀具重量
8kgf
有相邻刀具时最大刀具尺寸
Φ80×350mm 无相邻刀具时最大刀具尺
寸
Φ110×350mm
换刀方式 机械手换刀方式 选刀方式 最短路径 换刀时间(刀对刀) 1.5秒 容 量 槽 切削液槽 250L
其 它 气源 5.0—9.0kg/cm2 220 L/min 动力源 33.0KVA/21.7KVA
占地面积 2972(L)×2925(W)×2664(H)mm 机床净重 6100Kg
电源要求 3∅380V +10% ∼ -15%,50Hz 气源要求
采用标准T13277-91, 质量等级采用3-3-3, (最大粒子尺寸:5μm 最大浓度:5mg/m 3, 最高压力露点-20℃; 最大含油量1mg/m 3) 环境温度 0~40℃
环境相对湿度 85%
精 度 定位精度(JIS) ±0.005mm /全行程 重复定位精度(JIS)
±0.0015mm。
变速器壳体加工工艺设计及组合钻床的设计说明书DOC

目录摘要 (IV)ABSTRACT (IV)1前言 (1)1.1背景和意义: (1)2加工工艺的设计 (2)2.1变速器壳体的结构分析 (3)2.2零件的技术要求 (4)2.3变速器壳体的设计要求 (4)3工艺规程的制定 (5)3.1变速器壳体材料及毛坯 (5)3.2定位基准的选择 (6)4工艺路线的拟定 (6)4.1毛坯加工余量的确定及工序尺寸的确定 (8)5 专用机床的设计 (8)5.1组合机床结构方案的确定 (8)5.2组合机床配置的选择 (9)5.3被加工零件的工序图 (10)5.4零件的加工示意图 (12)6 合机床联系尺寸图的绘制 (20)6.1机床装料高度的确定 (21)6.2选用动力部件 (21)6.2.1滑台的选用 (21)6.2.2动力箱的选用 (22)6.2.3确定导向装置的尺寸 (23)6.3中间轮廓尺寸的确定 (24)7结论 (25)参考文献 (26)谢辞 (27)摘要本次设计的主要内容是变速器壳体加工工艺及组合钻床的设计,加工工艺对机械产品的质量好坏起着举足轻重的作用,如果在加工一个产品的时候工艺编的不够合理直接会影响产品的质量,同时也会使产品的生产率受到很大的限制,所以加工工艺对于机械产品的影响是不言而喻的,特别是对于加工精度很高的零件而言,设备的先进与否和工艺都是非常重要的。
组合机床是由一些通用部件和专用部件组成的为了使设计的组合机床既能满足预期的性能要求,又要做到配置上的均匀合理,符合多快好省的精神,所以必须对所设计的组合机床各个部件之间的关系进行全面的分析研究,特别是其中重要的几步:机床装料高度的确定;机床通用部件的选择。
最后对自己做的设计进行了进行了全面的总结,使自己的知识得到了融会贯通,受益匪浅。
关键字:钻削;工艺;性能;部件;精确度ABSTRACTThe design of transmission are the main contents of the shell processing technology design and composition of the drilling machine. Processing on the quality of the product quality of machinery play a decisive role. If a product in the processing time for the lack of reasonable directly affect the quality of the products. At the same time the productivity of products will also be greatly restricted, so processing technology for the impact of mechanical products is self-evident, Especially for high precision machining of parts, equipment and advanced technology are not very important Machine tools by some combination of common parts and components for the design in order to make the combination of machine tools meet the expected performance requirements. Have to be configured on the uniform and reasonable, in line with the spirit of commerical and convenience, it must be designed by a combination of various machine components of the relationship between a comprehensive analysis and study.In particular the important steps are the determination of a high degree of loading machine , universal machine parts choice. Finally, do their own design for a comprehensive summary, so that their knowledge has been comprehensively and benefited from.Key words: drilling; processing; components; precision1前言1背景和意义:制造业是国民经济的支柱,而机械制造业是其中最大的一个产业,被称为永远不落的太阳。
立式加工中心技术规格
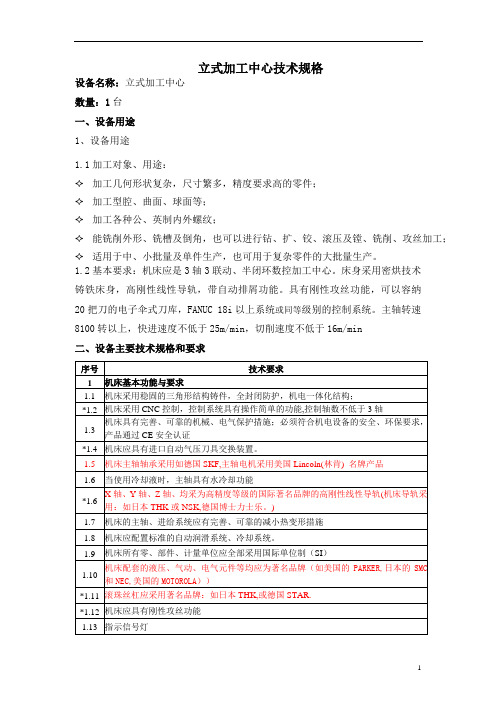
立式加工中心技术规格设备名称:立式加工中心数量:1台一、设备用途1、设备用途1.1加工对象、用途:✧加工几何形状复杂,尺寸繁多,精度要求高的零件;✧加工型腔、曲面、球面等;✧加工各种公、英制内外螺纹;✧能铣削外形、铣槽及倒角,也可以进行钻、扩、铰、滚压及镗、铣削、攻丝加工;✧适用于中、小批量及单件生产,也可用于复杂零件的大批量生产。
1.2基本要求:机床应是3轴3联动、半闭环数控加工中心。
床身采用密烘技术铸铁床身,高刚性线性导轨,带自动排屑功能。
具有刚性攻丝功能,可以容纳20把刀的电子伞式刀库,FANUC 18i以上系统或同等级别的控制系统。
主轴转速8100转以上,快进速度不低于25m/min,切削速度不低于16m/min二、设备主要技术规格和要求序号技术要求1 机床基本功能与要求1.1机床采用稳固的三角形结构铸件,全封闭防护,机电一体化结构;*1.2机床采用CNC控制,控制系统具有操作简单的功能,控制轴数不低于3轴1.3机床具有完善、可靠的机械、电气保护措施;必须符合机电设备的安全、环保要求,产品通过CE安全认证*1.4机床应具有进口自动气压刀具交换装置。
1.5机床主轴轴承采用如德国SKF,主轴电机采用美国Lincoln(林肯) 名牌产品1.6 当使用冷却液时,主轴具有水冷却功能*1.6X轴、Y轴、Z轴、均采为高精度等级的国际著名品牌的高刚性线性导轨(机床导轨采用:如日本THK或NSK,德国博士力士乐。
)1.7机床的主轴、进给系统应有完善、可靠的减小热变形措施1.8机床应配置标准的自动润滑系统、冷却系统。
1.9机床所有零、部件、计量单位应全部采用国际单位制(SI)1.10机床配套的液压、气动、电气元件等均应为著名品牌(如美国的PARKER,日本的SMC 和NEC,美国的MOTOROLA))*1.11滚珠丝杠应采用著名品牌:如日本THK,或德国STAR. *1.12 机床应具有刚性攻丝功能1.13指示信号灯2 机床主要技术参数*2.1各轴行程:X/Y/Z轴X≥508mm,Y≥400mm,Z≥500mm 2.2 主轴端面到工作台尺寸≥102-6102.3 工作台尺寸:长*宽≥660*350mm2.4 工作台承重≥1300KG2.5主轴电机功率:≥14.9KW(20HP)2.6 主轴最高转速:≥8100r/min2.7 主轴最大扭矩:≥102Nm2.8X轴快速移动速度:≥25m/min2.9 Y/Z轴快速移动速度:≥25m/min2.10 X/Y/Z轴最大进给速度:≥16m/min2.11自动换刀装置,刀库容量:≥20把2.12 刀具类型/锥度:BT/402.13 刀具最大直径(全装):≥89mm2.14 最大刀具直径:≥5.4KG2.15 刀对刀换刀时间:≤4.2秒2.16 切削对切削换刀时间:≤4.5秒3 机床精度要求3.1X/Y/Z轴位置精度:定位精度:X:≤0.010 mm全行程;Y/Z:≤0.010 mm/全行程重复定位精度:X:≤0.005mm全行程;Y/Z:≤0.005 mm全行程4 数控系统(CNC)要求4.1数控系统必须采用FANUC 18i以上系统或同等级别的控制系统,且满足机床的功能要求;系统联动轴数必须大于等于3轴,并具有铣削、钻孔、攻丝加工功能4.2系统采用15″及以上的彩色液晶显示器;4.3控制系统必须是中文操作界面4.4系统应带有标准输入/输出接口与USB接口4.5 控制轴数5 驱动系统要求5.1伺服驱动系统必须采用高可靠性的国际著名品牌,驱动电机:如采用日本安川YASKAWA5.2驱动系统应采用交流伺服驱动控制技术6 工作环境要求6.1电源:AC 380V ±10% ,50Hz±2% 6.2温度:5℃~40℃6.3相对湿度:≤90%7 随机附件7.1主机应包括机床正常使用所必需的附件(如:冷却与过滤系统、润滑系统、液压或气动系统等)7. 2提供机床其他配套附件清单7. 3提供机床其他选件清单及报价8 随机工具8.1机床专用安装、维修工具9 备件及易损件9.1提供机床备件和易损件清单10 技术资料10.1随机提供完整的中文(或英文)机床技术资料——操作使用说明书,如:机床操作使用手册、编程手册,等;——机床安装调试说明书,如:机床安装手册、调试说明书,等;三、技术服务要求1.安装和调试:机床的安装和调试,买卖双方签署购货合同后一周内卖方向买方提供合同产品地基图。
立式加工中心机对所使用的工件有哪些要求-

立式加工中心机对所使用的工件有哪些要求?立式加工中心机是指主轴轴线与工作台垂直设置的加工中心,能完成铣、镗削、钻削、攻螺纹和用切削螺纹等工序,重要适用于加工板类、盘类、模具及小型壳体类多而杂零件。
立式加工中心拥有更高效的加工速度,同时具备自动换刀的功能,是使用泛的金属切削机床之一。
问:立式加工中心机所使用的工件有哪些要求?答:第一,球头铣刀铣削曲面时,球头铣刀刀尖的切削速度很低。
假如用球头铣刀垂直于加工面铣削平曲面,球头铣刀刀尖切削的表面质量相对较差,应适当提高主轴转速,也应避开用刀尖切削。
第二,避开垂直切割。
平底圆柱铣刀有两种,一种是端面有中心孔,端边不在中心上方。
另一种是端面没有中心孔,端刃连接过心。
铣削曲面时,带有中心孔的端铣刀决不能像钻头一样垂直向下进给,除非事先钻好加工孔。
否则,铣刀会损坏。
假如使用不带中心孔的端刀,可以垂直向下进给,但由于刀片角度太小,轴向力很大,应尽量避开。
好的方法是斜向下进给,达到肯定深度后用侧刃横向切割。
铣槽面时,可以预钻工艺孔进行切削。
虽然球头铣刀垂直进给的效果比平底铣刀好,但由于轴向力过大,影响切削效果,最好不要使用这种切削方法。
第三,在铣削曲面零件时,假如发觉零件材料热处理不好,有裂纹、组织不均匀等现象,应适时停止加工,以免挥霍工时。
第四、铣削模具型腔多而杂曲面时,通常需要较长的周期。
因此,每次启动铣削前,应适当检查机床、夹具和刀具,以避开中心故障,这会影响加工精度,甚至造成废品。
第五、在模具型腔铣削时,应依据加工表面的粗糙度适当把握其余的锉修。
对于难以铣削的零件,假如加工表面粗糙度较差,应适当留多一些锉刀;对于平面、直角槽等易于加工的零件,应尽可能降低加工表面的粗糙度值,以削减锉削工作量,避开大面积锉削对型腔表面精度的影响。
- 1、下载文档前请自行甄别文档内容的完整性,平台不提供额外的编辑、内容补充、找答案等附加服务。
- 2、"仅部分预览"的文档,不可在线预览部分如存在完整性等问题,可反馈申请退款(可完整预览的文档不适用该条件!)。
- 3、如文档侵犯您的权益,请联系客服反馈,我们会尽快为您处理(人工客服工作时间:9:00-18:30)。
汽车股份有限公司变速器生产线变速器壳体立式加工中心机订货任务书(技术部分)项目:变速器项目联系人:电话:传真:地址:邮编:电子邮件:编制:校对:审核:批准:日期:立式加工中心招标规格及要求一、设备名称立式加工中心二、设备台数3台三、投标语言中文四、概述设备要有较强的通用性。
卖方可根据买方技术规格要求用本公司的相近设备进行投标。
该立式加工中心用于我公司变速器壳体(详见下表)的机加工,用于加工变速器壳体与离合器壳体连接面上各连接孔和内部一些平面、孔,与后盖连接面及各连接孔、叉轴孔、倒档锁轴孔等的粗、精加工内容及放油孔全部加工内容;年生产纲领:10万件/年;生产节拍:1.78分钟/件,含上、下料时间;零件装料高度:900-1100mm(脚踏板高度300mm)。
五、招标范围1、立式加工中心三台及相应的培训、安装、调试等技术服务;2、相应的夹具、刀具、辅具、专用装置等;3、投标厂商投标时应提供投标设备的主要配置及附件等的明细、数量、原产地及生产厂商、规格型号、精度等级、技术参数、功能等描述。
提供各部分分项报价,包括各主要配置分项报价清单、附件分项报价清单等;4、投标厂商投标时应提供工艺方案及刀具选配方案、夹具方案图,提供夹具部件分项报价清单、刀具分项报价清单等;5、投标厂商投标时,投标的设备若不采用本要求规定的几何精度检测标准,应提供其相应几何精度检测标准清单;6、如有招标文件未提及的事项,投标方应自行列明。
六、设备通用要求1、设备符合中国的劳动保护、环境保护、安全法规等法规要求;2、使用环境:温度5-45℃,相对湿度30-95%(无冷凝水);3、电源:三相交流电,380V±10%,50Hz;4、投标设备必须是全新设备(包括所有零部件、元器件、附件);5、操作面板侧面配有RS232接口及220V传输线接口,且带传输线及传输软件;6、操作面板上所有指示灯,要求有指示灯工作正常检测按钮,可以随时检测;7、操作面板可转到机床侧面或不能超过机床前面200mm;8、电器柜内安装照明灯,门开灯亮,门关灯灭;9、电器柜安装空调,带接水盒;10、电器柜要求密封、防尘;11、电器柜内有放机床说明书的装置;12、机床配备三色指示灯,正常工作时绿灯亮,正常停机时黄灯亮,异常停机时红灯亮,预报警时红灯闪烁。
生产厂家:(性能不低于以下参考厂家及型号,以下仅供参考)13、机床线路、管路布局要求合理、美观;14、所有的配管要求走直角弯,不能放置在地面上,同时考虑维修方便,不能贴紧机床,距机床外表面15mm;15、所有压缩空气用软管采用内径8mm,外径12mm的PU软管,所有压缩空气管路应配有快换接头;16、设备的气动元件在0.3-0.6MPa之间能够正常工作,如不能满足要求增加增压装置或储压装置;17、为保证维修安全,气、液回路需要带手动卸压装置。
液压回路加在泵与阀之间;18、润滑单元应有液面检测及报警装置,如在循环加工中出现润滑报警,则在循环结束后机床不能工作,润滑单元放置在机床外部,方便维修、加油,润滑单元下方应有接油盘(接油盘方便装卸);19、机床要有独立的液压站,液压站放在机床外部;20、各种阀、表、三联件等的位置要求便于维修;21、油缸、汽缸等件要求有导向装置;22、机床具备节电功能,机床在5分钟(可在5-100分钟内任意可调)后无任何动作发生,要求各种电机停电,但是CNC系统不能停电且该项功能有关闭、打开的开关;23、机床配备风枪;24、机床颜色:长城公司指定且提供色板;25、外观喷涂标记A、辅助设备(液压站、排屑器、冷却箱等)——在易于观测的位置喷涂重量(单位:公斤),字体——宋体,字高——50毫米,字宽——30毫米,喷涂颜色——长城公司指定且提供色板;B、机床的润滑、液压、冷却装置,在易于观测的位置标明容量(单位:升),字体——宋体,字高——50毫米,字宽——30毫米,喷涂颜色——长城公司指定且提供色板;C、有三角带、齿形带、链条传动的部位,标记规格、数量、型号等,可喷涂或做标牌;D、重要拧紧部位要有拧紧标识,以确认有无松动现象或松开后拧紧到位;26、其它标识A、液压站有表示液面位置的上下限标志,如果凸出在外,应该增加防护,防护与标志等高;B、限位开关、接近开关带标签型标牌,电磁阀旁做标牌标明各阀的型号及作用;C、压力表各档位及不同档位压力工作范围做标牌标明;D、与维修、操作人员安全有关的部位有警示标牌;E、液压和润滑的加油处用用标牌标明该处用油型号。
七、设备的总体要求1、机械部分1.1、机床符合GB9061《金属切削机床通用技术条件》、GB/T13574《金属切削机床静刚度检验通则》、GB/T16768《金属切削机床振动测量方法》、GB /T16769《金属切削机床噪声声压级测量方法》、GB18568《加工中心安全防护技术条件》要求规定;1.2、机床采用整体铸造床身,床身结构便于切削液顺利排出及冲屑,必要时可考虑采用压缩空气吹屑、切削液冲屑和刮板刮屑;1.3、主轴结构便于维修,主轴轴承采用由SKF、FAG、NSK、INA等知名厂家生产,不低于P4级的产品,主轴轴承工作寿命不低于20000小时;1.4、采用空气轴承结构的要设置压缩空气干燥装置;1.5、机床具备主轴刀具夹紧实时监控及主轴过载保护功能;1.6、机床具备主轴油温冷却功能,温控机采用不低于西安雷博的品牌产品;;1.7、机床具备X、Y、Z三个直线运动数控轴,且能够实现三个直线数控轴联动;1.8、X、Y、Z三个直线运动轴的滚珠丝杠和螺母采用由STAR、THK、NSK、INA或台湾上银生产,不低于3C级的产品;1.9、X、Y、Z三个直线运动轴的滚珠丝杠用轴承采用由SKF、FAG、NSK、INA等国际知名厂家生产,不低于P4级的产品;1.10、X、Y、Z三个直线运动轴的直线运动导轨采用STAR、THK、INA或台湾上银生产,不低于P3级,且保证运行2000Km无故障的产品;1.11、机床具备自动排屑装置;1.12、机床具备不设地脚、直接安放在水泥地面即可正常生产的能力;1.13、直径小于φ10的钻头设断刀检测装置进行检测并报警;1.14、机床运动部件要用永久标牌标明运动方向及易损件型号、数量等;1.15、机床采用全封闭、全防护装置,防护门由一个人可以拆下,便于维修;1.16、机床主轴具备自动换刀吹气清洁功能;1.17、若加工中产生油雾,要配有吸雾装置;1.18、零件加工采用湿式加工;2、电气及CNC数字控制系统2.1、机床电气系统符合GB5226《机床电器设备通用技术条件》要求规定;2.2、所有电器元器件均选用国际知名品牌产品;2.3、数控系统采用不低于西门子810或法那克0i系列产品,且数控系统符合JB/T8832-2001《机床数控系统通用技术条件》要求规定;2.4、具备刚性攻丝功能;2.5、配备电子手轮,与数控系统选用同厂家产品;2.6、程序存储容量不低于640m纸带;2.7、具备中、英文显示功能;2.8、刀具补正记忆数不低于200组;2.9、具备刀具寿命管理功能;2.10、具备刀具长度自动测量功能;2.11、具备英制/米制转换;2.12、具备工件计数功能;2.13、工件坐标系不低于50组;2.14、具备线外编程功能接口(RS232和DNC接口);2.15、机床采用8.4寸TFT彩色显示器;2.16、机床三个直线运动轴配备绝对位置编码器;2.17、机床主电机采用与所采用数控系统相同厂家生产、相配套的交流伺服主轴电机,符合JB/T10273-2001《数控机床交流主轴电动机通用技术条件》要求规定;机床主轴电机功率不小于7.5KW,30Min功率不小于11 KW;2.18、机床交流主轴驱动单元采用与所采用数控系统相同厂家生产、相配套的交流主轴驱动单元,符合JB/T10275-2001《数控机床交流主轴驱动单元通用技术条件》要求规定;2.19、机床三个直线运动轴所用电机采用与所采用数控系统相同厂家生产、相配套的交流伺服电机,符合JB/T10274-2001《数控机床交流伺服电动机通用技术条件》要求规定;X/Y/Z轴伺服电机功率不小于2/2/3KW;2.20、机床三个直线运动轴所用交流伺服驱动单元采用与所采用数控系统相同厂家生产、相配套的交流伺服驱动单元,符合JB/T10276-2001《数控机床交流伺服驱动单元通用技术条件》要求规定;2.21、机床电箱配备恒温控制系统,温控机采用不低于西安雷博的品牌产品;3、自动润滑系统3.1、采用全自动工作集中润滑系统,符合GB6576《机床润滑系统》及JB/T7452《机床润滑系统供油装置技术条件》要求规定;3.2、润滑油箱容量至少要能满足设备运行500小时的用量;3.3、集中自动润滑单元采用不低于南京贝奇尔的品牌产品;4、冷却液及过滤装置:4.1、机床冷却系统设计符合国标或ISO标准规定,具备油水分离、收集铁屑功能;4.2、机床配备大流量冷却系统,冷却系统具备冷却液恒温控制功能;4.3、机床具备主轴中心出水系统,内冷压力不低于1.5MPa,外冷压力不低于0.35 MP;4.4、机床配备冷却液枪;4.5、机床配备冷却液过滤装置,外冷过滤精度≤50um,内冷过滤精度≤25um;4.6、温控机采用不低于西安雷博的品牌产品;5、液压系统:5.1、机床液压系统符合GB3766及JB/T10051《机床液压系统通用技术条件》要求规定;5.2、液压泵站符合JB/T6105《数控机床液压泵站技术条件》要求规定;5.3、液压单元可选用台湾朝田、力士乐(许可证)或日本油研产品;6、气动系统:6.1、气动部分的设计符合GB/T7932或ISO有关标准要求规定;6.2、所有气源接口必须接有空气过滤器、水分离器、调压器三联件,均采用金属外壳自动排水式;6.3、气动系统具有压力报警功能,主管路上设置压力表,压力表的设定压力用标牌表示;6.4、经常拆卸的压缩空气软管连接处采用快换式接头;6.5、气动元件及系统采用“SMC”或“FESTO”的产品,选用的气动元件须经订货方认可,配有水分离装置,气动系统与机床布置合理;7、夹具:方案经买方确认后方可投入制造;7.1、每台机床配备能满足本零件加工精度要求的液压夹具一套,夹具采用若干点辅助支撑,辅助支撑采用液压锁死结构;并提供足够易损备件;7.2、夹具采用工件定位气检装置,以保证工件可靠定位;7.3、液压夹具制造参考厂家:台湾晋奕、台湾盛钰、无锡贝斯特;7.4、气动元件采用SMC或FESTO产品;7.5、液压元件采用台湾朝田、力士乐(许可证)或日本油研产品;8、刀具:方案经买方确认后方可投入制造;8.1、刀柄采用BT40,拉钉角度:45°;8.2、刀柄:采用整体式结构弹簧夹头式刀柄:重要加工部位采用AA级,跳动精度:夹套口0.001mm、4d处0.003mm;一般加工部位,跳动精度:夹套口0.003mm、4d处0.005mm;强力铣刀柄,跳动精度:4d处不大于0.008mm;面铣刀刀柄,跳动精度:不大于0.005mm;侧固式刀柄,旋转180度内跳动精度:4d处不大于0.008mm;镗刀部分:粗镗刀采用双刃镗刀;精镗刀最小调整精度不大于0.001mm;模块式镗刀重复安装精度不大于0.002mm;8.3、刀柄生产厂家优先选用日本BIG,可选用山特、肯那或台湾广杰、大连富士等厂家产品;8.4、镗刀生产厂家优先选用日本BIG,可选用山特、肯那等厂家产品;8.5、所有钻头采用直柄硬质合金内冷结构,柄部采用DIN6537标准;8.6、铰刀采用HSS直柄铰刀;8.7、丝锥采用HSS涂层丝锥;8.8、整体立铣刀直径小于φ20mm采用硬质合金涂层立铣刀,直径大于φ20mm采用HSS涂层立铣刀;8.9、刃具部分生产厂家:钻头、铰刀优先选用德国钴领、日本住友产品,可选山特、肯那、伊斯卡等产品;机夹铣刀选用住友、三菱、山特、肯那、伊斯卡等产品;U钻选用山特、肯那、BIG、三菱的产品;整体立铣刀选用住友、OSG、肯那产品;丝锥选用OSG、EMUG、BASS产品;8.10、配备刀具数量:辅具部分(含机夹刀盘、刀体、拉钉、刀柄等):每台机床配备一套,耐用辅具另备一套(3台机床共用),易损辅具另备两套(3台机床共用);刃具部分:保证提供终验收后,加工零件的数量不低于5000件,并考虑到可能发生的意外情况;其中每种机夹刀片数量不少于一整盒,钻头、铰刀、丝锥等整体刀具每种不少于5支;9、机床附件及易损件:9.1、提供设备总价1%的易损件备件;9.2、每台机床提供自动排屑装置及集屑小车一台;9.3、每台机床配备刀具破损检测装置一个;9.4、每台机床配备全套可调垫铁;9.5、40把刀移动式刀架一台;八、机床的主要技术参数1、各轴行程:机床提供三个可联动线性运动轴;X轴行程不小于1020mm,Y 轴行程不小于550mm,Z轴行程不小于550mm;2、X/Y/Z三轴快移速度不低于30m/min, 工进速度1—8000mm/min;3、X/Y/Z三轴加速度不低于0.6G;4、主轴部分:4.1、主轴最大扭矩不小于100N·m;4.2、主轴最高转速:不低于10000rPm ;4.3、主轴内锥;不小于7:24锥度 NO.40;5、工作台部分:5.1、工作台面积不小于1000*550(能满足同时安装两个工件);5.2、工作台最大承重不低于700kg;6、刀库部分6.1、刀库容量:刀位数不低于24把,备用空刀位不低于刀具总使用数量的20%;6.2、刀具交换时间不大于5秒( 切削—切削),6.3、、最大刀重不少于 6 kg;6.4、、最大刀具直径×长度(φmax×Lmax)≥φ80×250mm;6.5、选刀方式:随机存储方式;6.6、、刀具锥柄:BT40,拉钉角度:45°;7、机床位置精度:检测方法执行ISO230.2或GB17421.2标准规定;7.1、X/Y/Z三轴定位精度:A≤0.01mm(全程范围内双向检测);7.2、X/Y/Z轴重复定位精度:R≤0.006mm(全程范围内双向检测);7.3、X/Y/Z轴反向差值:B≤0.0035mm(全程范围内检测);7.4、机床采用立铣刀插补铣圆精度:铣φ60圆,圆度≤0.02mm。