立式加工中心移动工作台设计
立式加工中心工作台Z轴进给传动系统设计
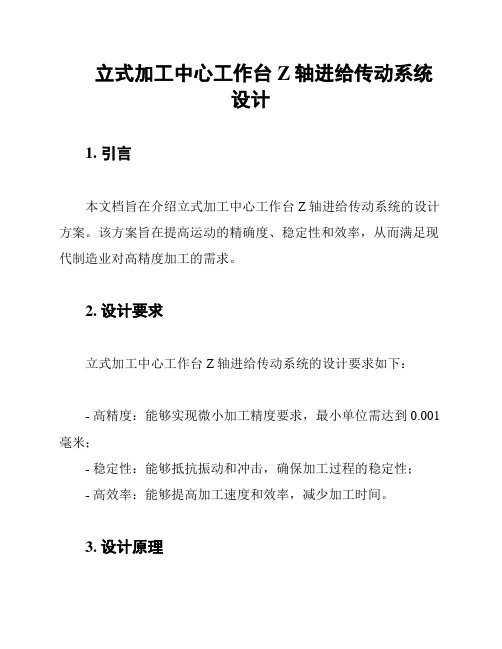
立式加工中心工作台Z轴进给传动系统设计1. 引言本文档旨在介绍立式加工中心工作台Z轴进给传动系统的设计方案。
该方案旨在提高运动的精确度、稳定性和效率,从而满足现代制造业对高精度加工的需求。
2. 设计要求立式加工中心工作台Z轴进给传动系统的设计要求如下:- 高精度:能够实现微小加工精度要求,最小单位需达到0.001毫米;- 稳定性:能够抵抗振动和冲击,确保加工过程的稳定性;- 高效率:能够提高加工速度和效率,减少加工时间。
3. 设计原理立式加工中心工作台Z轴进给传动系统设计方案基于以下原理:- 采用精密滚珠丝杠传动:使用高精度、低摩擦的滚珠丝杠传动机构,实现Z轴的精确移动;- 应用伺服电机控制:通过伺服电机控制滚珠丝杠传动系统,实现精确的位置控制和速度控制;- 配备位置传感器:在滚珠丝杠传动系统中安装位置传感器,实时检测工作台Z轴的位置,以实现闭环控制。
4. 设计方案基于上述设计原理,立式加工中心工作台Z轴进给传动系统的设计方案如下:4.1 滚珠丝杠传动机构- 选择高精度的滚珠丝杠,确保传动精度;- 采用预加载技术,提高传动系统的刚性和精密度;- 选择适当的滚珠丝杠螺距,以满足加工的需求。
4.2 伺服电机控制系统- 选择适合的伺服电机,具有高转矩和高响应速度;- 配备精密的位置检测装置,以实现精确的位置控制;- 使用先进的控制算法,实现平稳的速度控制。
4.3 位置传感器- 安装高精度的位置传感器,实时检测工作台Z轴的位置;- 将位置传感器的信号反馈给伺服电机控制系统,实现闭环控制;- 通过闭环控制,实现对工作台Z轴位置的精确控制。
5. 结论通过采用精密滚珠丝杠传动、伺服电机控制和位置传感器反馈的设计方案,现代立式加工中心工作台Z轴进给传动系统可以实现高精度、稳定性和高效率的加工。
该设计方案能够满足制造业对精确加工的要求,提高产品质量和加工效率。
高速立式加工中心工作台的有限元分析和拓扑优化

摘 要 : S l Wo k 在 oi d r s中分 别对 高速 立式加 工 中心工作 台的 4种方 案 ( 即普 筋工作 台 、 筋加 普
强 筋 工 作 台 、 筋 工 作 台 、 筋 加 强 筋 工 作 台) 行 实 体 建 模 . 模 以后 , 先 对 4种 方 案 做 有 斜 斜 进 建 首
曲 线 图 ( 1 )3 图 0 ¨. ]
象进行 下 面的研 究工作 .
2 2 模 态 分 析 .
对 高 速 立式 加 工 中心 工作 台系 统进 行 自 由模 态求解 分 析 , 时 工作 台系 统 的模 态 为 约 束模 态 , 此 提取其 前 1 5阶模 态 数 据 , 据 振 型 图查 看 工作 台 根 系统 的振 动特征 和受 力 的薄弱 区域 , 为高速 立式加 工 中心抗 振特性 研究 提供 了必要 的依 据. 工作 台系统 的模 态频 率与振 型描 述见表 4 .
q e y,do m o la l ss Fi ly,t u nc da na y i . na l he wor be h ha b e o ol g c l o tm ia i n. Be k nc s e n t p o i a p i z to —
c us her s l ft o l gia p i ia i n i otob i us。S ho ew or be c Sve — a eoft e u to het po o c lo tm z to Sn v o O c os k n h i r ii d by r a o a e s r t e fe e s n bl t uc ur . K e r : g — p e a hi i g c nt r;w o kt b e; t o og c lop i i a i n y wo ds hi h s e d m c n n e e r al op l ia tm z to
双交换工作台数控立式加工中心设计

双交换工作台数控立式加工中心设计简介工作机械将交换多个托盘来进行加工的托盘和较长工作台分别设为专用状,在使用其中一个时另一个处于无法使用状态,出现浪费现象。
并且,交换用托盘和较长工作台均配置在机械内部,没有考虑到有关准备的操作性。
并且,串联配置交换用托盘和较长工作台,从而增大机械宽度。
而且分别固定性配置较长工件的加工区域和通常的托盘加工区域,移动并驱动三个主轴 X、Y、Z 轴,因此移动并驱动主轴的机构中需要考虑刚性的同时还要考虑控制线、动力线的布线或液压、气压的配管等,机械变为复杂且大型化。
双交换工作台数控立式加工中心加工中心 1 包括床 10,床 10 的中央部安装有 Y 轴线性滑轨 20。
Y 轴线性滑轨 20 上装载有滑板 30,滑板 30 在 Y 轴方向受控移动。
滑板 30 上安装有 X 轴线性滑轨 40,X 轴线性滑轨 40 上装载有工作台单元 50。
工作台单元 50 沿 X 轴线性滑轨 40 在 X 轴方向受控移动。
工作台单元 50 上沿 Y 轴方向设有两组的线性导轨 51、线性导轨52。
床 10 上与滑板 30 相对安装有立柱 60。
立柱 60 的前表面安装有Z 轴线性导轨 70,装载主轴头 80。
主轴头 80 沿 Z 轴线性滑轨 70 在Z 轴方向受控移动。
主轴头 80 从工具库 90 接受恰当的工具,对工件进行加工。
面向床 10 的前表面的正面,左侧配置第一准备站 110。
第一准备站 110 包括平行于 Y 轴的线性滑轨 112,第一准备站 110 的侧部安装有伺服电动机 114。
伺服电动机 114 用于驱动滚珠丝杠 115。
滚珠丝杠 115 的螺母配备有托盘交换用钩子 116。
面向床 10 的前表面的正面,右侧配置第二准备站 120。
第二准备站 120 包括平行于 Y 轴的线性滑轨 122,第二准备站 120 的侧部安装有伺服电动机 124。
伺服电动机 124 用于驱动滚珠丝杠 125,滚珠丝杠 125 的螺母配备有托盘交换用钩子 126。
FANUC 0i-MB立式加工中心增加旋转工作台

l 机 转 l l
川
4 1 0 ̄ ) )
5 0 00 2) ( 盘嫂 2 0 3) ) (l 【 (
轴帕 『} 坏埘 Jj fj JI { 轴的 f 赴心 再轴 l 逊 的 I
f 数 参
L f 丸 f 似侈, }J J J%j \
0 j MB 内 存 改定 值
2 2安装 .
l l 88
l2 80 Biblioteka 2 00参 芍汁数 器 容 |及 榆 }竹 率 设定 恤 { 1 I
指 令 杆牢 备轴 的 编 f 称
0 0 00 0 l0 l
2 6 5
2 . 硬件连接 .I 2
根 据现 有加 工 中心工 作 台尺 寸和 产 品加工 要 求 ,选择
( )启 动第 四轴功能 。设定参数 :9 0 = # 0 0 4 C C 1 #9 0 4;1 1= ( N
受控轴数 ) 83 = ( ; 10 4 总控制轴数 )# 9 3 = ( # ;9 4 . 1控制轴扩张 )重 3 ,
新启动电源。
图 I
() 2其他参数设定见表 l 。 表一其他 系统参数的设定
1 引 言 、
对箱体 的四个面进行加工 ,现在的加工方式是利用不同的工装
对箱体的不同的四个面进行加工 ; 操作人员需要频繁更换工装 ,
加工 四个面需要 四次装夹定位 , 影响工件定位精度 , 而且效率低 下。为了提高工作效率 和加工精度 , 提高机床的加工柔性 , 而 从 降低工装成本 ,为此 决定在现有立式加工 中心的基础上添加旋
C PO O! A
D),c ( DP c
1
首先确认 目前正在使用 的加工中心是否有第 四轴控制功能 以及选择相关 的硬件。
立式加工中心工作台的设计与特性分析 PPT

目录
1 课题综述 2 国内外研究现状与发展趋势 3 研究目标、内容及拟解决的问题 4 实现方法、预期的目标 计5划 进度安排 6 主要参考文献
2
1 课题综述
1.1 五轴联动立式加工中心工作台介绍
五轴机床(5 Axis Machining),顾名思义, 是指在X、Y、Z,三根常见的直线轴上加上两根旋 转轴。A、B、C三轴中的两个旋转轴具有不同的运 动方式,以满足各类产品的技术需求。而在5轴加 工中心的机械设计上,机床制造商始终坚持不懈地 致力于开发出新的运动模式,以满足各种要求。综 合目前市场上各类五轴机床,其机械结构形式多种 多样。
3研究目标、内容及拟解决的问题
3.2拟解决的问题
1. 对工作台的可能出现的问先是结构形式的确定,选择合理的形式和尺寸。工作台的设计重要的是在满 足设计要求的前提下实现结构的最简化、重量的最轻巧,因此设计的刚度、强 度和稳定性计算是设计研究的主要问题。
1.12五轴联动立式加工中心工作台的特点
3. 减少装夹次数,一次装夹完成五面加工 如右图可以看出五轴加工中心还可以减
少基准转换,提高加工精度。在实际加工 中,只需一次装夹,加工精度更容易得到 保证。同时五轴加工中心由于过程链的缩 短和设备数量的减少,工装夹具数量、车 间占地面积和设备维护费用也随之减少。 这意味着您可以用更少的夹具,更少的厂 房面积和维护费用,来完成更高效更高质 量的加工!
1 课题综述
1.12五轴联动立式加工中心工作台的分类
五轴联动立式加工中心的分类:五轴联动加工中心有摇篮式、立式、卧式、NC工作台 +NC分度头、NC工作台+90°B轴、NC工作台+45°B轴、NC工作台+通用卧式五轴联动数 控机床 A轴、二轴NC 主轴等。 (1)双摆头形式(+A ,+C) (2)俯垂型摆头式(+B ,+C 刀具) (3)双转台形式(NC工作台) (4)俯垂型工作台式(+B ,+CNC工作台) (5)一摆一转形式(+A ,NC工作台)
立式加工中心VDF-850

VDF850立式加工中心售前技术资料目录第一部分VDF-850立式加工中心简介 (3)一、VDF-850主体构成 (3)二、VDF-850主要性能和特点 (3)三、VDF-850立式加工中心主要技术参数 (5)四、VDF-850机床标准配置 (5)五、VDF-850机床选择配置 (6)六、VDF-850立式加工中心主要配套件一览表 (6)七、VDF-850立式加工中心随机附件清单 (7)八、VDF-850立式加工中心随机工具清单 (7)九、VDF-850立式加工中心随机资料清单 (8)十、VDF-850机床工作条件 (8)第二部分机床外观图 (9)第三部分机床安装图 (10)第四部分精度检验标准 (12)第五部分部分标准配置图表 (12)第六部分部分选择配置图表 (13)第一部分VDF-850立式加工中心简介一、VDF-850主体构成二、VDF-850主要性能和特点VDF-850立式加工中心是大连机床集团公司引进先进技术生产的新一代数控机床,该机床独特坚稳持久的刚性结构,经由工程力学的反复仿真与计算,设计坚稳的床身结构,达到刚性倍增而质量精简的工程需求。
全面硬化处理的移动滑轨,搭配精密的研磨加工,组合出令人满意的精度品质。
不仅适用于板类、盘类、壳体类、精密零件的加工,而且适用于模具加工。
机床带有自动刀具交换系统,全封闭式防护罩,自动润滑系统、冷却系统、自动排屑装置、手动喷枪及便携式手动操作装置(MPG)。
零件一次装夹后可完成铣、镗、钻、扩、铰、攻丝等多工序加工,具有自动化程度高、可靠性强、操作简单、方便、宜人,整体造型美观大方、机电一体化程度高等优点。
1、机床底座、立柱、主轴箱体、十字滑台、工作台等基础件全部采用高强度铸铁,组织稳定,永久确保品质。
铸件结构均经过机床动力学分析和有限元分析,合理的结构程度与加强筋的搭配,保证了基础件的高刚性。
宽实的机床底座,箱形腔立柱、负荷全支撑的十字滑台可确保加工时的重负载能力。
动柱式交换工作台加工中心设计

动柱式交换工作台加工中心设计简介整机采用工作台位置固定立柱移动结构,三轴均采用直线滚珠导轨,结构设计先进新颖,精度可靠持续稳定,床身结构布局合理,整机具有足够的强度、刚性和稳定性,维修工艺性好。
立柱移动结构可获得极高的动静态精度和良好的排屑效率。
XYZ轴配置滚柱直线导轨保证高速度的同时保证高负荷和高刚性。
配置机器人或桁架机械手实现生产自动化,解决C型立加生产线配置困难等问题。
主轴及X/Y/Z三轴在立柱上移动,使用双交换工作台。
克服了C型立加的主轴悬伸太长的问题;使用高刚性的滚柱直线导轨,保证高速的同时,体现了机床的高刚性。
运动坐标与切削分离的方式更加有效的隔离切削热带来的热变形,保证了机床的高精度和稳定性。
三个坐标轴高置于床身上且使用刀具运动的方式使运动轴的重量不受工件重量的影响,保证加工的高动态响应和精度。
采用交换工作台:省了工件装夹时间,配上工业机器人可以管多台机器组成FMS省人力,好管理同时降低了用工成本,并且占地面积小:省空间。
交换工作台和自动上下料的配置可以保证不间断生产,从而达到最大产量。
提供最高的质量和效率的解决方案拨叉加工工艺方案阀体加工工艺方案往期爆文镜面滚压技术对滚压前工件的技术要求立加工中心+卧式加工中心一种新颖机床诞生了数控机床导轨是机床的根本,硬轨的精度保证工艺——注胶工艺桥式(也称天车式)龙门5轴机床DIY龙门加工中心加工镜面(Ra<0.8)孔的操作应用机械公社——为机械而生往期爆文镜面滚压技术对滚压前工件的技术要求立加工中心+卧式加工中心一种新颖机床诞生了数控机床导轨是机床的根本,硬轨的精度保证工艺——注胶工艺桥式(也称天车式)龙门5轴机床DIY龙门加工中心加工镜面(Ra<0.8)孔的操作应用。
立式加工中心移动工作台设计-开题报告

毕业设计(论文)开题报告一、课题的意义目的加工中心是一种在计算机控制下带有自动换刀系统的能完成多工序复合加工的自动化机床,并正向高速高效、高精度、模块化、网络化和复合化方向发展。
由于加工中心是典型的集高新技术于一体的机械加工设备,其生产效率高、柔性好、一机多用和易于加工复杂的曲线、曲面零件等特点,早已成为工业发达国家军民机械工业的主力加工设备。
一个国家的加工中心拥有量、消费量及总体技术水平与这个国家机械工业的加工制造技术水平息息相关。
我国的加工中心从70年代开始,已有很大发展,但技术、品种和数量上都还远远不能适应我国的经济、技术发展的需要。
进入21世纪以后,中国加工中心的消费量随着军民机械工业的大规模技术改造而迅速增长,如2001年中国加工中心的消费量仅为2662台(其中进口2290台),而同年美国、日本和德国的加工中心消费量分别为11505、6090和5291台。
到了2005年,中国加工中心的消费量猛增至约13200台(估计值,加工中心的产量数据未公布),其中进口10343台。
2005年加工中心的消费量是2001年的4.96倍,年均增幅达49.2%,一举超过美、日、德诸国,成为世界上消费加工中心最多的国家。
根据《机械工人》杂志社等单位的调查,从近600份重点用户的有效问卷中得出的结果是,加工中心机床的应用已遍及全国26个行业,其中汽车、摩托车及其零部件制造业占24%,航空航天和军工行业占18%,机床工具业占11%,模具行业占8%,轻工机械行业占4%。
在这些企业拥有的加工中心中,虽然普及型的立式和卧式加工中心仍占多数,但多轴联动、高速、大型精密等高档加工中心也占有一定比重,如在所调查的近600户用户中,拥有5轴联动加工中心的占24%。
说明中国市场消费的加工中心虽然以普及型的中档机为主,但高档机在消费量中所占比重估计已达15%至20%。
中国消费的加工中心大部分依靠进口(2005年进口量占消费量的七成多),进口金额12.97亿美元,居各类机床进口额之首,主要从日本、中国台湾、德国和韩国等地进口。
五轴立式加工中心VC630-5ax
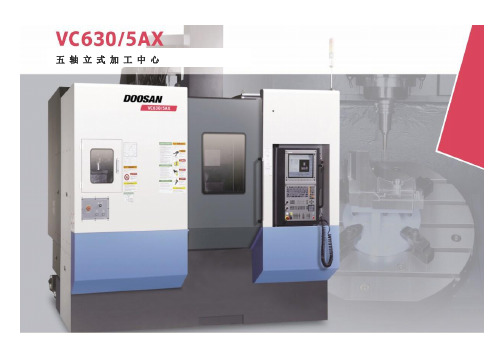
五轴立式加工中心高速主轴VC630/5AX配备了高刚性、高速度的内置主轴。
(输出:32kW ;最大扭矩:119N.m;主轴锥度:No.40)得到广泛的应用,包括进行重切削材料加工,如钛及铬镍铁合金,高速切削铝合金及其他有色金属材料加工。
作为一个标准的特征该主轴是一种双面接触式类型。
内置电机驱动主轴加工能力通过内置电机驱动主轴、高品质的平衡技术,消除任何振动带来的表面质量影响。
在高速状态主轴通过4级精密陶瓷轴承支撑的最佳设计、低离心力和最小产生热量等优点,实现了高生产力,加速时间的缩短保证了最小的主轴转动惯量同时保持其刚性。
双面接触式主轴Big plus双面接触系统是指机床主轴端面和刀柄法兰面之间,主轴锥孔和刀具锥柄之间的同步双重接触。
精度加工范围由于设计先进的机器具有严密的结构和灵敏的驱动系统,VC630/5AX机器可以提供长时间的高精度加工作业。
热位移控制:斗山热控制装置采用先进的实时补偿算法,将其应用到Z轴以此来抵消因主轴受热而引起的热位移影响。
DBB 举例:通过先进机械结构设计和斗山控制系统,实现更高精度的圆度。
DBB设置直径:200mm (7.9 inch)进给:1000mm/min (39.4 ipm) 行程规格工件最大尺寸/载重方便装夹和设备操作,适用于不同领域的加工。
机械结构VC630/5AX机床通过三维仿真分析和高精度的测量分析技术的应用,进行严格的基本结构设计和验证,确保长期高精度运行。
一体化构造床身采用细粒密烘铸铁,减震性能优良,确保了重负荷切削时候的稳定性。
VC630/5AX机床具备优越的设计,确保工件被牢固的固定在加工过程中。
自动换刀系统刀库可装40把刀,自动换刀系统可携带BT40锥度的刀具。
其可靠的系统保证了1.0秒的刀对刀换刀时间和7秒的切削对切削时间。
双向刀库遵循最短路径固定地址法选择。
更换手臂卸刀器刀具库凸轮箱刀对刀时间: 1 S40把刀库ATC,选项(60,80把)静态刚性VC630/5AX通过有限元分析已经提高了30%静态刚性。
XK714D立式加工中心
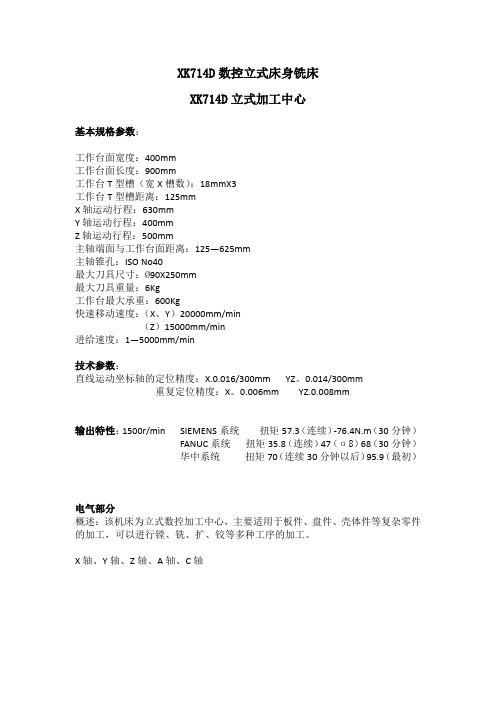
XK714D数控立式床身铣床XK714D立式加工中心基本规格参数:工作台面宽度:400mm工作台面长度:900mm工作台T型槽(宽X槽数):18mmX3工作台T型槽距离:125mmX轴运动行程:630mmY轴运动行程:400mmZ轴运动行程:500mm主轴端面与工作台面距离:125—625mm主轴锥孔:ISO No40最大刀具尺寸:Ø90X250mm最大刀具重量:6Kg工作台最大承重:600Kg快速移动速度:(X、Y)20000mm/min(Z)15000mm/min进给速度:1—5000mm/min技术参数:直线运动坐标轴的定位精度:X.0.016/300mm YZ。
0.014/300mm重复定位精度:X。
0.006mm YZ.0.008mm输出特性:1500r/min SIEMENS系统扭矩57.3(连续)-76.4N.m(30分钟)FANUC系统扭矩35.8(连续)47(α8)68(30分钟)华中系统扭矩70(连续30分钟以后)95.9(最初)电气部分概述:该机床为立式数控加工中心,主要适用于板件、盘件、壳体件等复杂零件的加工,可以进行镗、铣、扩、铰等多种工序的加工。
X轴、Y轴、Z轴、A轴、C轴编程功能:M00程序停止M01选择停止M02程序结束M03主轴正转M04主轴反转M05主轴停止M06换刀M07气冷开M08液冷开M09气、液冷停止M18解除准停M19准停M29刚性攻丝M31程序结束M45排屑器启动M46排屑器停止为安全起见,首次换刀必须对换刀动作进行单程序段操作。
必要时可将进给倍率尽可能小,确保所有动作安全无误后方可进行自动换刀。
为了进一步确保安全,对主轴旋转指令、刀库相关指令和坐标运动指令尽量不要遍在同一个程序段中,请分开编程。
使用T0;M6可将主轴上的刀具换回刀库。
操作面板。
XH716立式加工中心总体设计及主轴系统设计

XH716立式加工中心总体设计及主轴系统设计机械设计制造及其自动化摘要加工中心是典型的集高技术于一体的机械加工设备,它大大提高了劳动生产率,降低了劳动成本,改善了工人的工作环境,降低了工人的劳动强度。
本文经过对不同运动方案和各部件的设计方案的定性分析比较确定该立式加工中心的进给传动方案为:采用固定倒T型床身,电动机轴通过安装座安装在立柱导轨的滑座上,立柱导轨采用滚动直线导轨,可以实现Z方向的进给运动。
由X、Y向精密数控装置分别控制工作台和立柱完成X, Y两个方向的进给运动;X, Y, Z三个方向的进给运动均滚珠丝杠,并由交流伺服电机驱动。
导轨、滚珠丝杠采用多种润滑方式。
关键词:立式加工中心;伺服电机;精度;主轴箱;进给运动。
AbstractMachining center is a typical set of high-tech machining equipment in one, its greatly increased the labor productivity, reduce labor costs, improved working environment and reduce the labor of workers strength. This movement through the different programs and the design of various components of qualitative analysis and comparison of vertical machining centers to determine the progress of education to drive the program are: fixed inverted T-type bed, spindle seat installed by installing the sliding seat rail bed , use linear rolling guide rail bed can be achieved to the movement into the Z direction. By X, Y, precision CNC device to control the feed motion of the table and column X, Y two directions; X, Y, Z three directions of movement are ball screw feed, driven by AC servo motor. Guides, ball screws using a variety of lubrication.Key words: Vertical machining center; Servo motor; Accuracy;spindle box;Feed motion。
立式加工中心工作台设计

目录1.概述 (1)1.1技术要求 (1)1.2总体设计方案 (1)2.滚珠丝杠螺母副的选型和计算 (1)2.1主切削力及其切削分力计算 (1)2.2导轨摩擦力的计算 (2)2.3计算滚珠丝杠螺母副的轴向负载力 (2)2.4滚珠丝杠的动载荷计算与直径估算 (3)3.工作台部件的装配图设计 (7)4.滚珠丝杠螺母副的承载能力校验 (7)4.1滚珠丝杆螺母副临界压缩载荷的校验 (7)4.2滚珠丝杆螺母副临界转速的校验 (7)4.3滚珠丝杆螺母副额定寿命的校验 (8)5.计算机械传动系统的刚度 (8)5.1机械传动系统的刚度计算 (8)5.2滚珠丝杠螺母副扭转刚度的计算 (9)6.驱动电动机的选型与计算 (10)6.1计算折算到电动机轴上的负载惯量。
(10)6.2计算折算到电动机轴上的负载力矩 (10)6.3 计算坐标轴折算到电动机轴上的各种所需力矩 (11)6.4选择驱动电动机的型号 (12)7.确定滚珠丝杠螺母副的精度等级和规格型号 (14)7.1确定滚珠丝杠螺母副的精度等级 (14)7.2滚珠丝杠螺母副的规格型号 (14)7.3机械转动系统的误差计算与分析 (14)8.机械传动系统的动态分析 (15)9.课程设计总结 (15)10.参考文献 (15)立式加工中心工作台设计1.概述1.1技术要求工作台、工件和夹具总质量m=833kg(重力W=8500N),工作台行程900mm,工作台快进速度20000mm/min,工作台采用滚动摩擦导轨,动摩擦系数为0.01,静摩擦系数为0.01,工作台定位精度为0.04mm,重复定位精度为0.01mm,机床的工作寿命为20000h。
采用伺服电机,额定功率7.5kw,强力切削时铣刀直径125mm,主轴转速300r/min1.2总体设计方案为了满足以上技术要求,采取以下技术方案:(1)工作台工作面尺寸(宽度×长度)确定为400mm×1200mm。
立式加工中心直线、回转工作台设计

摘要本文主要设计立式加工中心直线、回转工作台,工作台承担纵向X 和横向Y轴两个方向的移动及一个绕Z轴的转动。
设计内容包括:1.总体结构方案的拟定。
确定了工作台结构,方案拟定为纵向、横向两个方向移动的直线工作台,在直线移动工作台的T型槽中固定一个可拆卸夹具式数控回转工作台。
2.部件概述。
这一部分详细描述了在工作台设计过程中所用到的几个典型部件,如伺服进给系统、工作台、导轨,陈述选用这几个部件的原因和对它们的基本要求。
3.结构力学的设计计算。
结合给定的主要参数对伺服进给系统和回转工作台进行选择计算,得到必需的几何参数,基本确定工作台的结构尺寸。
4.工作台装配图与零件图的绘制。
清楚地表示工作台及其组成部分的连接、装配关系和其中主要零件结构、大小及技术要求。
关键词:加工中心,工作台,伺服进给系统,回转工作台。
AbstractIn this paper,It mainly designs the moving working table and NC rotary table of vertical machining centre.The tables can move along X-axis and Y-axis also can rotate around Z-axis. what's this pater content is as follows:1.Draft the overall scheme of the structure of the tables.the moving working table moves along X-axis and Y-axis is drawn up,of which in the T-typle groove the NC rotary table is fixed which can be removed and fixed easily like a jig.2.Descripe the typical components of vertical machining center.In this part, the components used in the design, such as servo feed system、tables and guide rails,are descriped respectively why choose them,and the require-ments for them.3.Design and calculate structural e the given main parameters to select and compute the components to get other indispensable parameters,then identify the physical demension of the tables4.Draw assembly drawings and part drawings.Express the connection the tables and their components、assembly relations,also the structures and the sizes of the main components、technical requirements, clearly.Key words: Machining Center, Working Table, Servo Feed System,Rotary Working Table目录摘要 (I)Abstract II目录 (III)第一章引言 ........................................................................ 错误!未定义书签。
DMU65monoBLOCK五轴加工中心(立式主轴,摇篮式工作台)
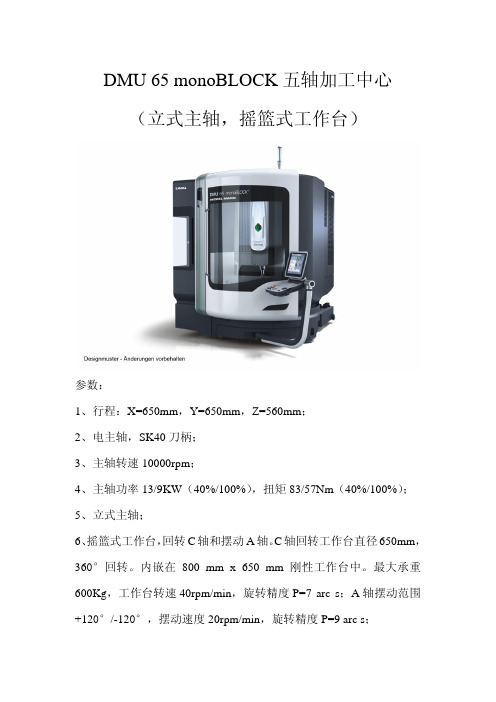
DMU 65 monoBLOCK五轴加工中心(立式主轴,摇篮式工作台)参数:1、行程:X=650mm,Y=650mm,Z=560mm;2、电主轴,SK40刀柄;3、主轴转速10000rpm;4、主轴功率13/9KW(40%/100%),扭矩83/57Nm(40%/100%);5、立式主轴;6、摇篮式工作台,回转C轴和摆动A轴。
C轴回转工作台直径650mm,360°回转。
内嵌在800 mm x 650 mm刚性工作台中。
最大承重600Kg,工作台转速40rpm/min,旋转精度P=7 arc s;A轴摆动范围+120°/-120°,摆动速度20rpm/min,旋转精度P=9 arc s;7、最大刀具长度315mm,最大刀具直径160mm,最大刀具重量8Kg;8、最大可加工的工件尺寸:直径=650mm,高度=500mm;9、直线轴(X、Y、Z)快移速度:40m/min;10、直线轴(X、Y、Z)最大进给速度:40,000m/min;11、定位精度:Pmax.=0.006mm,重复定位精度:Ps max.=0.004mm。
精度依据ISO230-2标准;12、三维海德汉iTNC530控制系统,19″TFT彩色显示器,带Smartkey 智能钥匙,处理器Pentium M, 1.8 G,硬盘80G,具有电子手轮;13、具有红外测头,具有3D快速调整包以便快速恢复精度设置,具有刀具破损检测功能;14、具有ATC功能,即加工任务快速编程参数选择。
可根据实际加工阶段需要在精度、表面质量和加工速度之间快速切换;15、30刀位刀库;16、具有冷却喷枪,可通过M功能实现气吹转换;17、具有电压安全包。
最低价:EUR230,000.00(CIF青岛港,不含税)。
立式加工中心简介

5.技术参数
项目
XH716
工作台台面尺寸(宽X长) 590*1450 mm 工作台T型槽(槽数X数量X间距) 18*5*125 mm 工作台最大承重 1350 kg X/Y/Z向行程 1270/610/760 mm X/Y/Z导轨形式 滑轨 X/Y/Z快速移动速度 20 m/min 切削进给速度范围 1~8000 mm 主轴中心线至主柱导轨面距离 635 mm 主轴端面至工作台面距离 150~910 mm 主轴锥孔 ISO50 主轴电机功率 11/15 kw 主轴转速范围 20~6000 rpm 主轴最大输出扭距 95.4 N.m 刀库容量/形式 16/斗笠式24/圆盘式(选配) 刀具最大重量 15 kg 刀具最大直径/长度 147 / 350 mm 换刀时间(刀对刀) 8s 定位精度 +0.010 mm 重复定位精度 +0.005 mm 机床总功率 35 kw 机床外形尺寸(长X宽X高) 3200X2650X3320 mm
3.分类
依据导轨分类 依据立式加工中心各轴导轨的形式可分硬轨及线轨。 硬轨适合重切削,线轨运动更灵敏。 依据转速分类 立式加工中心主轴转速6000-15000rpm为低速型, 18000rpm以上为高速型。 依据结构分类 依据立式加工中心的床身结构可分为C型及龙门型。
4.区别
卧式 卧式加工中心指主轴为水平状态的加工中心,通常都带 有自动分度的回转工作台,它一般具有3~5个运动坐 标,常见的是三个直线运动坐标加一个回转运动坐标, 工件在一次装卡后,完成除安装面和顶面以外的其余四 个表面的加工,它最适合加上箱体类零件。与立式加工 中心相比较,卧式加工中心加工时排屑容易,对加工有 利,但结构复杂.价格较高。
FM6324立式加工中心工作台组件的ANSYS模态分析及优化
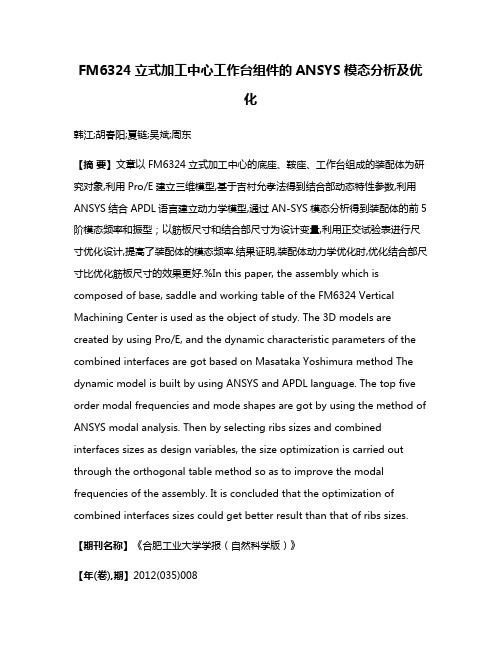
FM6324立式加工中心工作台组件的ANSYS模态分析及优化韩江;胡春阳;夏链;吴斌;周东【摘要】文章以FM6324立式加工中心的底座、鞍座、工作台组成的装配体为研究对象,利用Pro/E建立三维模型,基于吉村允孝法得到结合部动态特性参数,利用ANSYS结合APDL语言建立动力学模型,通过AN-SYS模态分析得到装配体的前5阶模态频率和振型;以筋板尺寸和结合部尺寸为设计变量,利用正交试验表进行尺寸优化设计,提高了装配体的模态频率.结果证明,装配体动力学优化时,优化结合部尺寸比优化筋板尺寸的效果更好.%In this paper, the assembly which is composed of base, saddle and working table of the FM6324 Vertical Machining Center is used as the object of study. The 3D models are created by using Pro/E, and the dynamic characteristic parameters of the combined interfaces are got based on Masataka Yoshimura method The dynamic model is built by using ANSYS and APDL language. The top five order modal frequencies and mode shapes are got by using the method of ANSYS modal analysis. Then by selecting ribs sizes and combined interfaces sizes as design variables, the size optimization is carried out through the orthogonal table method so as to improve the modal frequencies of the assembly. It is concluded that the optimization of combined interfaces sizes could get better result than that of ribs sizes.【期刊名称】《合肥工业大学学报(自然科学版)》【年(卷),期】2012(035)008【总页数】4页(P1039-1042)【关键词】装配体;吉村允孝法;结合部;ANSYS模态分析;尺寸优化【作者】韩江;胡春阳;夏链;吴斌;周东【作者单位】合肥工业大学机械与汽车工程学院,安徽合肥230009;合肥工业大学机械与汽车工程学院,安徽合肥230009;合肥工业大学机械与汽车工程学院,安徽合肥230009;合肥工业大学机械与汽车工程学院,安徽合肥230009;安徽省鸿庆精机有限公司,安徽安庆246005【正文语种】中文【中图分类】TH122CAE可以为设计提供理论依据和指导,对装配体整体的CAE分析可以获得单个零件分析中难以获得的信息;机床的动态特性会影响机床加工精度,降低生产效率[1],通过对机床装配体的模态分析可以得到多个零部件作为一个整体时所表现出来的动态特性。
任务书_立式加工中心移动工作台设计

学院机械工程学院专业班级学号学生指导教师题目立式加工中心移动工作台设计任务规定进行日期自2012 年月日起,至年月日止一、题目来源、目的、意义题目来源:本课题来源于同济现代制造技术研究所,是立式加工中心机床设计项目下的子课题之一。
目的:课题的目的是设计一个用于立式加工中心的移动工作台,该工作台可进行X 和Y 方向直线运动, 另外工作台上面可固定夹具式回转工作台( Z向转动),并满足相关的技术指标要求。
意义:直线移动工作台可以实现数控机床的X、Y直线进给运动,电气进给传动的机械结构简单,可在工作中无级调速,便于实现自动化控制。
二、主要工作内容(1)熟悉现有的各种移动式直线工作台的要求和特点;(2)完成纵、横向移动工作台的设计总图;(3)设计分析计算工作;(4)部件中主要零件的零件图绘制;(5)纵、横向移动工作台各部分的综合分析。
三、主要技术指标(或主要论点)立式加工中心的特点是结构简单,占地面积小。
总体结构方案为工作台是纵向(X)轴、横向(Y)轴两个方向的移动直线工作台,上面叠加一个可拆卸夹具式数控回转工作台。
直线工作台面尺寸(长×宽×高):900mm×500mm×50 mm;纵向(X向)工作行程为750mm,横向(Y向)工作行程为500mm;铣削刀具最大直径为Φ100mm;工作进给速度为1~1500mm/min,快速进给速度为15m/min。
四、进度计划第1周~第3周:查阅资料,翻译要求字数的英文资料,调研目前市场上数控机床的纵、横向移动工作台几种主要的结构形式,并进行方案论证,写出开题报告。
第4周~第6周:通过查阅资料和参考一些机床的结构,进行纵、横向移动工作台的结构设计。
第7周~第9周:结构分析与验算,满足技术性能指标和使用要求。
第10周~第14周:计算机绘制结构设计图纸,包括总图和一些零件图。
第15周~第16周:编写毕业设计说明书。
第17周~第18周:评审、准备答辩。
VMC850E(FANUC 三轴)

供货方案产品型号:VMC850E 产品名称:立式加工中心沈阳机床股份有限公司概述立式加工中心主要用于加工板类、盘类件、壳体件、模具等精度高、工序多、形状复杂的零件,可在一次装夹中连续完成铣、钻、扩、铰、镗、攻丝及二维三维曲面,斜面的精确加工,加工实现程序化,缩短了生产周期,从而使用户获得良好的经济效益。
一.功能及特点说明1机床总体布局VMC850E型立式加工中心采用立式框架布局,立柱固定在床身上,主轴箱沿立柱上下移动(Z向)、滑座沿床身纵向移动(Y向)、工作台沿滑座横向移动(X 向)的结构。
床身、工作台、滑座、立柱、主轴箱等大件均采用高强度铸铁材料,造型为树脂砂工艺,两次时效处理消除应力。
这些大件均采用Pro/E和Ansys优化设计,提高大件和整机的刚度和稳定性,有效抑制了切削力引起的机床变形和振动。
2拖动系统X、Y、Z轴导轨副采用滚动直线导轨,动静摩擦力小,灵敏度高,高速振动小,低速无爬行,定位精度高,伺服驱动性能优,提高机床的精度和精度稳定性。
X、Y、Z轴伺服电机经弹性联轴节与高精度滚珠丝杠直联,减少中间环节,实现无间隙传动,进给灵活、定位准确,传动精度高。
Z轴伺服电机带有自动抱闸功能,在断电的情况下,能够自动抱闸将电机轴抱紧,使之不能转动,起到安全保护的作用。
3主轴组主轴组采用台湾专业厂家生产,具有高精度,高刚性。
轴承采用P4级主轴专用轴承,整套主轴在恒温条件下组装完成后,均通过动平衡校正及跑合测试,提高了整套主轴的使用寿命及可靠性。
主轴在其转速范围内可实现无级调速,主轴采用电机内置编码器控制,可实现主轴定向和刚性攻丝功能。
4刀库采用斗笠式刀库,安装在立柱侧面,换刀时刀盘由气缸推动左右移动,气缸配有接近开关保证换刀位置准确,刀盘到达换刀位置后,主轴上下运动实现还刀和抓刀,换刀过程简单可靠。
5切削冷却系统配备大流量冷却泵及大容量水箱,充分保证循环冷却,冷却泵功率:0.4Kw,压力:1.2bar。
- 1、下载文档前请自行甄别文档内容的完整性,平台不提供额外的编辑、内容补充、找答案等附加服务。
- 2、"仅部分预览"的文档,不可在线预览部分如存在完整性等问题,可反馈申请退款(可完整预览的文档不适用该条件!)。
- 3、如文档侵犯您的权益,请联系客服反馈,我们会尽快为您处理(人工客服工作时间:9:00-18:30)。
1 前言数控机床是一种装有计算机数字控制系统的机床,数控系统能够处理加工程序,控制机床完成各种动作。
与普通机床相比,数控机床能够完成平面曲线和空间曲面的加工,加工精度和生产效率都比较高,因而应用日益广泛。
1.1 数控机床的组成一般来说,数控机床由机械部分、数字控制计算机、伺服系统、PC控制部分、液压气压传动系统、冷却润滑和排泄装置组成。
数控机床是由程序控制的,零件的编程工作是数控机床加工的重要组成部分。
伺服系统是数控机床的驱动部分,计算机输出的控制命令是通过伺服系统产生坐标移动的。
普通的立式加工中心有三个伺服电机,分别驱动纵向工作台、横向工作台、主轴箱沿X向、Y向、Z向运动。
X、Y、Z是互相垂直的坐标轴,因而当机床三坐标联动时可以加工空间曲面。
而对于五轴联动的数控机床来说,则多出了B轴和C轴。
Y轴的旋转轴为B轴,Z轴的旋转轴为C轴。
1.2 数控机床的加工运动机械加工是由切削的主运动和进给运动完成的,控制主运动可以得到合理的切削速度,控制进给可得到各种不同的加工表面。
数控机床的坐标运动是进给运动,对于三坐标的数控机床,各坐标的运动方向通常是相互垂直的,即各自沿笛卡尔坐标系的X、Y、Z轴的正负方向移动。
如何控制这些坐标移动来完成各种不同的空间曲面加工是数字控制的主要任务。
大家知道,在三维空间笛卡尔坐标系中,空间任何一点都可以用X、Y、Z坐标值来表示,对一条空间曲线也可以用三维坐标函数来表示。
怎样控制各坐标轴的运动才能完成曲面加工呢?现在来介绍一下吧。
曲面加工时刀具的移动轨迹与理论上的曲线不吻合,而是一条逼近线。
由于各种插补的计算公式不同,使逼近的折线也不同,通常有下面几种计算方法:逐点比较法,积分法和时间分割法。
1.3 数控机床的优、缺点数控机床有许多优点,因而发展很快,逐渐成为机械加工的主导机床。
(1)用数控机床加工可以获得很好的加工精度,加工质量稳定数控机床的传动件,特别是滚珠丝杠精度很高。
装配时消除了传动间隙,并采用了提高刚度的措施,因而传动精度很高。
机床导轨采用滚动导轨或粘接有摩擦系数很小的合成塑料,因而减小了摩擦阻力,消除了低速爬行。
闭环、半闭环伺服系统,装有精度很高的位置检测装置元件,并随时把位置误差反馈给计算机,使之能够及时进行误差校正。
因而使数控机床获得很高的加工精度。
数控机床的一切操作都是由程序支配的,若电控系统稳定可靠,它的工作是很可靠的,与手工操作相比,数控机床没有人为干扰,因而加工质量稳定。
(2)具有较高的生产效率在数控机床上使用的刀具通常是不重磨装夹式道具,具有很硬的表面涂层,因而切削速度较高。
采用对刀仪进行对刀,加工中心的刀库有足够数量的刀具,自动换刀的速度很快,空行程的速度在15m/min以上,有些达到了240m/min,因而辅助时间很短。
与普通机床相比,数控机床的生产效率可提高2~3倍,有些可达到几十倍。
(3)功能多许多数控机床具有很多加工功能,在一台机床上可以进行钻孔、镗孔、铣平面、铣槽、铣凸轮曲线及各种轮廓线,甚至刻字。
除装卡面可对六面体的五个面进行加工,有时还能对与坐标平面成一定角度的平面加工。
在一次装卡下完成各种加工,可以消除因重复装卡带来的误差。
也减少了测量和装卡的辅助时间。
(4)对不同零件的适应性强在同一台数控机床上可适应不同品种及尺寸规格的零件进行加工,只要更换加工程序,就可改变加工零件的品种。
(5)能够完成普通机床不能完成的复杂表面加工有些空间曲面,例如螺旋浆表面,五坐标联动数控机床加工,使之性能大为改进;数控仿形应用范围更广,具有重复应用、镜像加工功能。
(6)数控机床可大大减轻工人的劳动强度,并有较高的经济效益。
任何事物都有其二重性,数控机床也不是没有缺点,主要是有以下几方面:1)价格昂贵,一次投资较大。
2)维修和操作比较复杂要求具有较高技术水平和文化程度的工人和维修人员进行操作和维修。
数控机床是科学技术发展的结果。
高技术产品,一定要求有较高技术水平的人才操作和维修,因而如果说这是一条缺点的话,还不如说它对人们文化技术水平的提高的一种促进。
数控机床适用于多品种中、小批量生产;形状比较复杂、精度要求较高的零件加工;产品更新频繁、生产周期要求短的加工;用数控机床可以组成自动化车间和自动化工厂(FA),目前应用较多的是组成柔性自动化生产线(FML)、柔性制造单元(FMC)和柔性制造系统(FMS)。
1.4 数控机床的分类目前,数控机床品种齐全,规格繁多,可从不同角度和按照多种原则进行分类。
1.4.1. 按工艺用途分类(1)金属切削类数控机床这类机床和传统的通用机床品种一样,有数控车床、数控铣床、数控钻床、数控磨床、数控镗床以及加工中心等。
加工中心是带有自动换刀装置,在一次装卡后可以进行多种工序加工的数控机床。
(2)金属成型类数控机床如数控折弯机、数控弯管机、数控回转头压力机等。
(3)数控特种加工及其他类型数控机床如数控线切割机床、数控电火花加工机床、数控激光切割机床、数控火焰切割机床等。
1.4.2. 按控制运动的方式分类(1)点位控制数控机床点位控制(Positioning Control)又称点到点控制(Point to Point Control)。
这类数控机床的数控装置只要求精确地控制一个坐标点到另一坐标点的定位精度,见图(1.1):图1.1 点位控制切削示意图而不管一点到另一点是按照什么轨迹运动。
在移动过程中不进行任何加工。
为了精确定位和提高生产率,首先系统高速运行,然后进行1 级~3 级减速,使之慢速趋近定位点,减小定位误差。
这类数控机床主要有数控钻床、数控坐标镗床、数控冲剪床和数控测量机等。
使用数控钻镗加工零件可以省去钻模、镗模等工装,又能保证加工精度。
(2)直线控制数控机床直线切削控制(Straight Cut Control)又称平行切削控制(ParalklCutControl)。
这类数控机床不仅要求具有准确的定位功能,而且还要保证从一点到另一点之间移动的轨迹是一条直线。
其路线和移动速度是可以控制的。
对于不同的刀具和工件,可以选择不同的切削用量。
这一类数控机床包括:数控车床、数控镗铣床、加工中心等,如图1.2所示。
图1.2 直线控制切削示意图(3)轮廓控制数控机床" 轮廓控制(Contouring Control)又称为连续轨迹控制(Contou-OUS PathControl)。
这类数控机床的数控装置能同时控制两个或两个以上坐标轴,并具有插补功能。
对位移和速度进行严格的不间断的控制,即可以加工曲线或者曲面零件,如凸轮及叶片等。
轮廓控制数控机床有两坐标及两坐标以上的数控铣床、可加工曲面的数控车床、加工中心等(见图1.3)。
图1.3 轮廓控制切削示意图1.4.3 按有无检测装置分类(1)开环系统开环系统没有检测装置。
因此加工精度比较低,通常由步进电机驱动。
这种系统结构简单,价格便宜。
但步进电机转矩比较低。
(2)闭环系统闭环系统的位置检测装置装在床身和移动部件上,可以把坐标移动的准确位置检测出来并反馈给计算机,因此装有闭环系统的数控机床加工精度很高。
(3)半闭环系统这种系统与闭环系统相比不同之处是检测装置装在伺服电机的尾部,用测量电机测量位置坐标位置。
由于电动机到工作台之间的传动间隙和弹性变形、热变形等因素,因而检测的数据与实际的坐标值有误差。
但由于半闭环结构简单,安装调试放便。
检测元件不容易受损害等优点,目前应用较多。
(4)按可联动的坐标数分类按照联动(同时控制)轴数分,可以分为2 轴联动、2.5 轴联动、3 轴联动、4 轴联动、5轴联动等数控机床。
2.5轴联动是三个坐标轴(X、Y、Z)中任意两轴联动,另一个是点位或直线控制。
1.5 数控机床的发展1952年美国PARSONS公司和麻省理工学院合作试制了世界上第一台三坐标数控立式铣床。
54年美国Bendix-Cooperation公司生产出第一台工业数控机床。
先是由电子管控制,随后经历了晶体管控制、集成电路控制(NC),计算机控制(CNC),直到现在的微处理器控制(MNC)。
我国从1958年开始研制数控机床,70年代初得到广泛发展,数控技术在车床、铣床、钻床、磨床、齿轮加工机床、电加工机床等得到应用,并制出加工中心。
80年代,我国从日本发那科公司引进了3、5、6、7 等系列的数控系统和直流伺服电机,直流主轴电机等制造技术,以及引进美国GE公司的MCR系统和交流伺服系统,德国西门子VS系列可控硅调速装置,并进行了商品化生产。
这些系统可靠性高,功能齐全。
与此同时,还自行开发了3、4、5轴联动的数控系统以及双电机驱动的同步数控系统(用于火焰切割机)和新品种的伺服电机,推动了我国数控机床稳定发展,使我国数控机床在性能和质量上产生了一个质的飞跃。
它的发展趋势:1)具有先进的自检能力,使之能长期可靠的工作。
2)向高速、高精度发展。
3)更高的生产率和利用率。
4)单元模块化。
5)更强的通讯能力、图像编辑和显示能力。
2 进给伺服系统设计2.1 进给伺服系统的设计要求2.1.1、对进给伺服系统的基本要求带有数字调节的进给驱动系统都属于伺服系统。
进给伺服系统不仅是数控机床的一个重要组成部分,也是数控机床区别于一般机床的一个特殊部分。
数控机床对进给伺服系统的性能指标可归纳为:定位精度要高;跟踪指令信号的响应要快;系统的稳定性要好。
1.稳定性所谓稳定的系统,即系统在输入量改变、启动状态或外界干扰作用下,其输出量经过几次衰减振荡后,能迅速地稳定在新的或原有的平衡状态下。
它是进给伺服系统能够正常工作的基本条件。
它包含绝对稳定性和相对稳定性(稳定裕度)进给伺服系统的稳定性和系统的惯性、刚度、阻尼以及系统增益都有关系。
适当选择系统的机械参数(主要有阻尼、刚度、谐振频率和失动量等)和电气参数,并使它们达到最佳匹配,是进给伺服系统设计的目标之一。
2.精度所谓进给伺服系统的精度是指系统的输出量复现输入量的精确程度(偏差),即准确性。
它包含动态误差,即瞬态过程出现的偏差;稳态误差,即瞬态过程结束后,系统存在的偏差;静态误差,即元件误差及干扰误差。
常用的精度指标有定位精度、重复定位精度和轮廓跟随精度。
精度用误差来表示,定位误差是指工作台由一点移动到另一点时,指令值与实际移动距离的最大差值。
重复定位误差是指工作台进行一次循环动作之后,回到初始位置的偏差值。
轮廓跟随误差是指多坐标联动时,实际运动轨迹与给定运动轨迹之间的最大偏差值。
影响精度的参数很多,关系也很复杂。
采用数字调节技术可以提高伺服驱动系统的精度。
3.快速响应特性所谓快速响应特性是指系统对指令输入信号的响应速度及瞬态过程结束的迅速程度。
它包含系统的响应时间,传动装置的加速能力。
它直接影响机床的加工精度和生产率。
系统的响应速度越快,则加工效率越高,轨迹跟随精度也越高。