元器件成形工艺设计规范(A0)
作业指导书编写规范精选全文

5.4。7.4 测试完毕后,良品需在指定位置做记号,不良品需放置不良品区域并由班长送修.
6. SOP的变更和管控
6。1文件修订记录:记录SOP作业变更的事项与原因
6。1。1.需注明变更的日期及变更的人姓名.
5.3。11。2.需标明使用的耗材,如锡丝、签字笔、防静电毛刷。
5.3。12.作业内容:标示此工作站的工作项目及顺序.
5。3.12。1。标明对前一工作站的作业确认(优先作业).
5。3.12。2.作业顺序的排定及作业注意事项。
5.3。12.3.对有方向零件须标明。
5.3.12。4. 作业完成自检无误后方可将产品放于流水线上。
5。3。3。作业段别:标明此作业位于那一工程段。如:HA415EU1预加工、HA415EU1插件、HA415EU1补焊。.。。
5.3。4.工程名: 标明此工作站的作业名称.如:点胶,锡面检视…。
5。3。5 标准工时:标明该工作站作业的标准时间。
5。3。6 单页版本:标明此页SOP的版本情况。
5。3。7 文件编号:标明该页SOP对应机型、段别、单板(如HA415EU1插件文件编号为WI—AA003-01:其中AA0为机型对应编码,03对应插件段,01对应单板EU1。其中机型编码参照《机种代码一览表》,(01)预加工、(02)隧道炉、(03)插件、(04)补焊、(05)喷漆、(06)组装、(07)整机测试、(08)包装。
6。2。2如整段SOP全变更,版本用大写的英文字母标示,如:A、B….,若26个字母用完,则改使用两个英文字,如:”AA”、”AB”…。。
6.3SOP制作完成后,须经由品保QE确认,IE主管审核,工程经理批准后发文控标准化。(除制作者以外,签名部分不可使用计算机打印)。
元件封装库设计规范
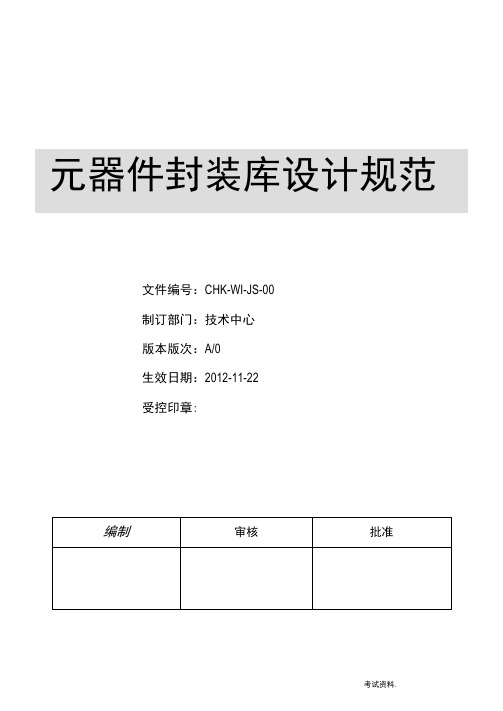
文件编号:CHK-WI-JS-00制订部门:技术中心版本版次:A/0生效日期:2012-11-22受控印章:文件修ffiBt目录一、库文件管理41•目的42. 适用范围43. 引用标准44. 术语说明45.库管理方氏56.库元件添加逍程5二、原理图元件建库规范6 1•原理图元件库分类及命名62.原理图图形耍求73.原理图中元件値标注规剧8三、PCB对装建際规范81. PCBM装库分类及命名92. PCB封装图形8*11四、PCBS装焊盘设廿规范111 •通用要求112. AI元件的封装gtm3. DIP元件的封装Sit 124. SMT元件的封装设it 125. 特殊元件的封装设it 131.目的《元件器討芸库设it 规范》(以卞简祢《规范》)力电路元件库、对装库设it 规范文甘。
本文档规 定设it 中需要注恿的一些事坝,目的是便设廿规范化,并通过垢经验固化力规范的方式,为企业内所 有设itiSIO 整、规范、统一的电子元器件图形符号相封装库,U 而实现节省设计时间,编现严品 研发周期,I?低设计差缁率,提高电路设廿水平的目的。
2•埴用范围适用于公司内部研发、生严等各环节中绘制的电子电路原理图、电路板图。
3・引用标准3.1•采用国际电气制图林旌和国家军用规范 3.2. GB/T4728-2007《电气简图用图形符号》 3.3. GB/T7092-1993《半导体集成电路外形尺寸》 3.4. GB7581-1987《半导U 分立器件外形尺寸》3.5. GB/T 15138-1994《膜集成电路和視合集成电路外形尺寸》 3.6. GJB3243-1998《电子元器件表面安装要求》3.7. JESD30-B-2006《半导体器件計装的描述性指定系统》 38 IPC-7351A-2005《表面安装设计和焊盘图形标准的通用要求》4.4. description 简要描述4.5. Component Tpye 器件类璽 4.6. Footprint 真正库封装名称4.7. SorM Footprint 标准或厂家用对装名称 4.8. Footprint path 封芸库路径 4.9. Value 标注4.10. PCB3D 3D 图形名称 4.11. PCB3D path 3D 库路径 4.12. Availability 库存量 4.13. LT 供货期 4.14. Supplier 生产商 4.15. Distributer 舗售商 4.16. Order Information ij 货号 4.17. ManufacturerP/N 物 fl 编码 4.18. RoHS 是否无舟4.19. UL 是否U LUli (尽量加人UL 号) 4.20. Note 备注4.21. SMD: Surface Mount Devices/表面貼装元件° 4.22. RA : Resistor Arrays/排田 °4.23. MELF : Metal electrode face components/金属电机无引找端面元件. 4.24. SOT: Small outline transistor/小外形晶U 管。
电子元器件安装焊接工艺设计规范
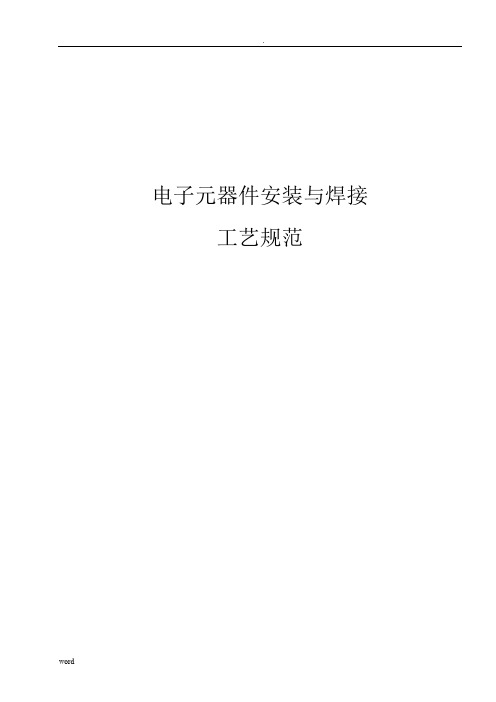
电子元器件安装与焊接工艺规范电子元器件安装与焊接工艺规范1范围本规范规定了设备电气盒制作过程中手工焊接技术要求、工艺方法和质量检验要求。
2引用标准下列文件中的有关条款通过引用而成为本规范的条款。
凡注日期或版次的引用文件,其后的任何修改单(不包括勘误的内容)或修订版本都不适用于本规范,但提倡使用本规范的各方探讨试用其最新版本的可能性。
凡未注日期或版次引用文件,其最新版本适用于本规范。
HB 7262.1-1995 航空产品电装工艺电子元器的安装HB 7262.2-1995 航空产品电装工艺电子元器的焊接QJ 3117-1999 航天电子电气产品手工焊接工艺技术要求IPC-A-610E-2010 电子组件的可接收性3技术要求与质量保证3.1一般要求3.1.1参加产品安装和检验的人员必须是经过培训合格的人员。
3.1.2环境温度要求:20℃-30℃。
3.1.3相对湿度要求:30%-75%。
3.1.4照明光照度要求:工作台面不低于500lx。
3.1.5工作场地应无灰尘,及时清除杂物(如污、油脂、导线头、绝缘体碎屑等)工作区域不得洒水。
3.2安装前准备3.2.1把安装所用的器材备齐,并放在适当位置,以便使用;3.2.2所有工具可正常使用,无油脂,按下列要求检查工具:切割工具刃口锋利,能切出整齐的切口;绝缘层和屏蔽剥离工具功能良好。
3.2.3按配套明细表检查和清点元器件、印制板、紧固件、零件等的型号规格及数量。
3.2.4凡油封的零件或部件,在安装前均应进行清洗除油,并防止已除过的零件再次糟受污染。
4元器件在印制板上安装4.1元器件准备4.1.1安装前操作人员应按产品工艺文件检查待装的各种元器件、零件及印制板的外观质量。
4.1.2元器件引线按下列要求进行了清洁处理:a、用织物清线器轻轻地擦拭引线,除去引线上的氧化层。
有镀层的引线不用织物清线器处理;b、清洁后的引线不能用裸手触摸;c、用照明(CDD)放大镜检验元器件引线清洁质量。
PCB-结构工艺设计规范(1)

PCB-结构工艺设计规范(1)PCB是现代电子装备必不可少的组成部分,而PCB的结构工艺设计规范是确保其一致性和高质量的关键所在。
下面我们就结合PCB的结构工艺,讨论一下相关的设计规范。
1. PCB元器件布局规范PCB元器件布局很重要,这不仅决定了电路板的稳定性、可靠性,还影响到PCB的尺寸、成本等。
因此,必须对PCB元器件布局进行规范化设计。
具体要求如下:1.1 元器件分组分布布局将不同的元器件分组分布布局,根据不同的性质,在不同的位置放置元器件。
通常把容易产生干扰的电源电路、模拟电路,与容易受到干扰的数字电路相分离。
1.2 元器件密度规范元器件密度要求适当。
密度过大会导致元器件之间无法分清,也不利于PCB维护和调试;密度过小会导致PCB元器件布局空间的浪费。
1.3 尺寸和位置规范PCB元器件的尺寸和位置也需要规范。
同种元器件尺寸应相同,位置也应相对固定,不同元器件的位置也应遵循规范,并确保之间的距离合适,不会因为太靠近而影响到彼此的工作。
2. PCB走线规范PCB走线是通过元器件排布设计,将各个元器件连接在一起形成电路的过程。
良好的走线规范可以提高PCB电路的可靠性、稳定性、抗干扰能力以及抗干扰能力。
具体要求如下:2.1 走线合理性规范PCB走线合理性是指走线数量,走线长度以及走线形状等都要符合规范。
PCB设计时应合理选择走线长度,把走线平行且平均分布。
PCB走线中断处的焊盘应有足够的面积,确保可靠焊接。
2.2 走线宽度规范PCB走线宽度应遵循工程设计标准。
如果走线较长,建议采用多层布线,同时应考虑到走线的接触面积,以减小接触电阻。
3. PCB焊盘规范PCB焊盘在电路板的制作过程中也是非常重要的一环,其作用是连接各个元器件。
焊盘规范要求如下:3.1 焊盘大小规范焊盘大小要合理,不同元器件的焊盘大小应依据元器件的体积、重量和固定位置来设计。
同种元器件的焊盘直径应趋于相近,长度也应相近。
3.2 焊盘间距规范焊盘间距要合理,并考虑PCB制造工艺的限制,一般而言,焊盘间距不应过小,不应小于0.3mm;也不应过大,应不超过2mm。
研发PCB工艺设计规范

研发PCB工艺设计规范PCB工艺设计规范是指在PCB(Printed Circuit Board,印刷电路板)的研发过程中,对于工艺设计方面的规定和要求。
下面是一些PCB工艺设计规范的主要内容。
一、PCB基本要求:1.PCB尺寸要求:根据产品的要求确定PCB板的尺寸,确保适配产品的安装空间。
2. 板厚要求:根据工作环境和产品需求,选择合适的PCB板厚度,一般常见的有1.6mm、1.2mm等。
3.线宽线距要求:线宽线距的设计应根据当前工艺的可制作能力来确定,以确保良好的导电性和线路稳定性。
4.成品层数要求:根据电路复杂度和成本预算,确定合适的PCB成品层数,一般有单层、双层、四层和六层等多种选择。
5.焊盘要求:焊盘的设计应符合电子组件的封装规范,确保焊接质量和可靠性。
6.阻抗控制要求:对于需要控制阻抗的高速电路,需要进行相应的设计,包括不同层之间的层间间距和层间阻抗的控制等。
二、布局要求:1.分区布局:将PCB板按不同功能区域进行分割,并合理安排各个功能模块之间的布局,以减少干扰和噪声。
2.电源分布:合理规划电源的布局,避免不同模块之间的电源干扰。
3.外围组件布局:将与外界接口相关的元器件(如插座、开关等)布置在PCB板的边缘位置,方便与外部连接。
4.散热设计:应根据电路功耗和特殊需求,设计适当的散热结构,保证电路工作的稳定性和可靠性。
5.丝印标识:在PCB板上设置必要的丝印标识,包括元器件的标记和位置,方便装配和维修。
三、走线要求:B走线:根据USB接口的设计规范,确保信号走线的绝对长度尽量短,并避免过量的串扰和信号损耗。
2.高速信号走线:对于高速信号线,应根据特定的信号完整性和阻抗控制需求进行布线,使用差分对布线和控制串扰。
3.电源线走线:为了避免电源噪声和电压降,应将电源线尽量走短,减少电流回路的阻抗。
四、焊接要求:1. DRC检查:在PCB设计完成后,进行DRC(Design Rule Check)检查,确保焊盘和元器件之间的间距和尺寸符合要求。
单板工艺查检表
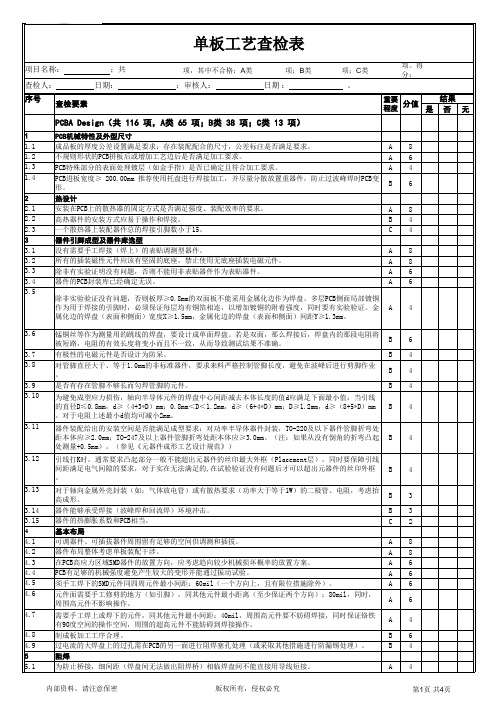
项,其中不合格:A 类项;B 类项;C 类是否无11.1A 81.2A 61.3A 41.4B622.1A 82.2B 42.3C 433.1A 83.2A 83.3A 63.4A63.5A 43.6B 63.7B 43.8B 43.9B 43.10B43.11B 43.12B 43.13B 33.14B 33.15C 244.1A 84.2A 84.3A 64.4A 64.5A 64.6A 64.7A 44.8B 64.9B 455.1A4制成板加工工序合理。
过电流的大焊盘上的过孔需在PCB的另一面进行阻焊塞孔处理(或采取其他措施进行防漏锡处理)。
阻焊为防止桥接,细间距(焊盘间无法做出阻焊桥)相临焊盘间不能直接用导线短接。
PCB有足够的机械强度避免产生较大的变形并能通过振动试验。
须手工焊下的SMD元件同四周元件最小间距:60mil(一个方向上,且有限位措施除外)。
元件面需要手工修剪的地方(如引脚),同其他元件最小距离(至少保证两个方向):80mil,同时,周围高元件不影响操作。
需要手工焊上或焊下的元件,同其他元件最小间距:40mil,周围高元件要不妨碍焊接,同时保证铬铁有90度空间的操作空间,周围的超高元件不能妨碍到焊接操作。
基本布局可调器件、可插拔器件周围留有足够的空间供调测和插拔。
器件布局整体考虑单板装配干涉。
在PCB高应力区域SMD器件的放置方向,应考虑趋向较少机械损坏概率的放置方案。
引线打K时,通常要求凸起部分一般不能超出元器件的丝印最大外框(Placement层),同时要保障引线间距满足电气间隙的要求,对于实在无法满足的,在试验验证没有问题后才可以超出元器件的丝印外框。
对于轴向金属外壳封装(如:气体放电管)或有散热要求(功率大于等于1W)的二极管、电阻,考虑抬高成形。
器件能够承受焊接(波峰焊和回流焊)环境冲击。
器件的热膨胀系数和PCB相当。
对管脚直径大于、等于1.0mm的非标准器件,要求来料严格控制管脚长度,避免在波峰后进行剪脚作业。
ISO9001-2021工装设计规范A0

ISO9001-2021工装设计规范A0工艺装备设计规范(iso9001:2021)为了规范工装设计的流程,满足用户机械加装加工建议。
2.适用范围本规范适用于于公司中试部工装设计部门。
3.引用/参考标准或资料4.术语及其定义工装,即工艺装备:指制造过程中所用的各种工具的总称。
包括刀具/夹具/模具/量具/检具/辅具/钳工工具/工位器具等。
工装为其通用简称。
工装分为专用工装/通用工装/标准工装(类似于标准件)。
5.规范建议5.1工装制作需求在装配研发样机阶段,整机工艺研发组的项目成员根据机器加装的须要明确提出制作工装的市场需求,并得出设计工装方案,经过工艺研发组审查通过后,在oa上公布工装市场需求流程,提供更多零件实物给装备研发组做为工装设计的参照物,在没实物的情况下,装备研发五美零件宣称书做为参照物设计工装。
5.2工装制作5.2.1装备研发组是接到工装制作的市场需求后,根据设计方案和零件实物或零件宣称书画出来工装3d图纸,交予工艺研发组证实;5.2.2工艺开发组确认图纸是否符合设计方案的要求,如符合,则装备开发组就将工装设计图纸和相关要求发给供应商。
5.2.3供应商根据工装设计图纸和其他有关建议报价至订货。
5.2.4采购下订单到供应商。
5.2.5供应商接到订单后,按建议制作工装。
5.3工装验收供应商搞好工装后,交货至装备研发组。
装备研发组将工装交予工艺研发组展开工装环评。
工装环评合格后,则可以收货,并搞好有关工装铭牌标签,如下图1;例如检验不合格,则回到给供应商展开修正,直至环评合格后才可以收货。
工装设计制作流程图图2工装设计制作流程图。
PCBA工艺设计规范

PCBA工艺设计规范PCBA(Printed Circuit Board Assembly,印刷电路板组装)是指将已经印制好的电路板上的元器件进行焊接和组装的过程。
PCBA工艺设计规范是制定PCBA工艺流程的一套规范文件,它包括了PCBA设计、焊接、组装、质量控制等方面的要求。
1.PCBA设计规范:-确定电路板尺寸和布局,保证安装的器件数量和尺寸的兼容性。
-设计适当的敷铜和敷焊膏区域,确保焊接质量和连接可靠性。
-合理选择元器件的布局,确保信号线和电源线的有效隔离,降低EMI(电磁干扰)。
-设计保护电路,如电源过压、过流、过热保护等,提高电路的可靠性和稳定性。
2.PCBA焊接规范:-选择适当的焊接技术,如表面贴装技术(SMT)和插件技术(THT)的结合。
-确定焊接方法,如波峰焊、回流焊等,并设置合适的焊接温度和时间。
-控制焊接过程的湿度和灰尘,使用防静电设备,避免静电引起的组装问题。
-做好元器件和焊点的对位和定位,确保焊接准确和稳定。
3.PCBA组装规范:-安装元器件时要遵循正确的顺序和位置,避免错误的插件和短路。
-严格控制焊锡量和焊接质量,避免过量或不足的焊锡引起的问题。
-设置适当的温度和时间,确保焊锡的熔化和固化,保证焊点的牢固性。
-接线、连接和固定要牢固可靠,避免松动和断连导致的电路故障。
4.PCBA质量控制规范:-制定合适的测试方法和测试标准,检测PCBA的性能和质量。
-进行严格的电气测试,包括电阻、电容、电感、短路、开路等参数测试。
-进行功能性测试,测试PCBA连接和元器件的工作状态和可靠性。
-进行环境适应性测试,模拟各种工作环境和应力条件,测试PCBA的稳定性和可靠性。
总之,PCBA工艺设计规范是指导PCBA工艺流程的一套规范文件,它包括了PCBA设计、焊接、组装、质量控制等方面的要求。
通过遵循PCBA 工艺设计规范,可以确保PCBA的焊接和组装质量,提高产品的可靠性和稳定性,降低故障率,满足客户的需求。
SMT无铅锡膏制程工艺设计规范

有限公司支持性程序文件页 码:1/5标题:SMT无铅锡膏制程工艺设计规范版 本:A01 目的为落实预防失误,不断改进的质量方针,规范公司无铅锡膏制程产品的设计工艺,规范公司无铅锡膏制程产品的制造工艺。
2范围适用于有限公司(以下简称:)无铅锡膏制程(以下简称:无铅制程)产品的设计控制与制造工艺设置。
3 职责工程部:依照研发部提供文件和设计样机,完成生产工艺的设计、选定相关使用耗材。
完成炉温曲线的设计,钢板的开设及钢板开设文件的受控。
对产品治具的评估,完成产品贴装程式的制作和校正。
完成工程样机的制作,生产过程的作业指导书,并完成SMT新机种试产报告。
完成产品贴装程式。
质量部:对样机的零件和耗材进行RoHS测试,完成测试报告。
对无铅耗材及零件管控进行稽核,完成QC工程图。
对产品无铅制程的流程符合RoHS进行稽核,完成产品的检验规范并根据EBOM进行及时更新。
制造部:按照工程部提供之产品无铅制程作业指导书进行作业,维护生产车间日常5S。
研发部:提供产品的输出文件和样机。
样机的产品规格书和零件规格承认书,并对不符合无铅锡膏制程技术要求的零件是否可用给出结论。
零件耐温清单,可推荐使用之耗材。
规定该产品的IPC610D接受等级。
按照此设计规范进行样机设计,并按照工程部给出的评审结果进行进行必要修改,修改后的样机须在进行评审。
4 规范4.1研发部无铅制程设计规范4.1.1 根据研发部设计开发计划,在设计样机完成定型时,由研发部项目组向工程部和质量部提交样机,产品规格书(包括客户规格书与规格书),主要零件规格承认书(包括PCB、IC、BGA、QFP及其他对热冲击敏感之零件),EBOM(EXCEL格式)、PCB(PROTEL的PCB格式)、零件耐温清单(EXCEL格式)、制程种类确定对推荐耗材资料(耗材详细资料,应包括所含成分,推荐炉温曲线等参数资料)等电子档文件和工程交接注意事项。
4.1.2研发部选用无铅制程产品的所有零件需符合RoHS。
电子行业电路板生产工艺规范

电子行业电路板生产工艺规范引言近年来,随着信息技术的迅猛发展,电子行业成为了现代社会中不可或缺的一部分。
而在电子产品的制造过程中,电路板起着关键性作用。
为了确保电子产品的质量和可靠性,制定一套标准的电路板生产工艺规范势在必行。
本文将以电子行业电路板生产工艺规范为主题,探讨电路板生产的各个环节和相关标准规范。
一、设计与布局电路板的设计与布局是电路板生产的重要环节,它直接关系到电路板的性能和可靠性。
设计与布局过程中需要遵循以下几个方面的规范:1.电路板尺寸规范:需要根据电路板所需功能和电子产品的尺寸要求,合理确定电路板的尺寸,保证其能够容纳所有所需元器件和线路。
2.元器件布局规范:在电路板上合理布局元器件,使得元器件之间的连接线尽可能短,降低线路阻抗和串扰的影响,从而提高电路板的信号传输效果。
3.射频干扰(EMI)设计规范:在设计过程中应考虑到电磁干扰的问题,采取合理的设计措施,如使用屏蔽罩、地平面和绕线等,以减少干扰并提升电路板的抗干扰能力。
二、生产工艺电路板的生产过程中需要遵循一系列规范的生产工艺,以保证电路板的质量和可靠性。
1.材料选择:在电路板生产中,需要选择符合要求的基材、覆铜、焊盘等材料。
这些材料应具有良好的导电性、绝缘性和热稳定性,以确保电路板的正常工作和长寿命。
2.电路板成型:电路板生产中的成型工艺需要遵循一定的规范。
包括成型温度、压力、速度等参数的设定,确保电路板成型过程中不会产生冷焊、焊盘变形等缺陷。
3.线路制作:线路制作是电路板生产的核心环节,需要遵循精确的工艺规范。
包括蚀刻、铺铜、光刻等工艺的正确操作,确保线路制作精度和均匀性。
4.焊接工艺:焊接是电路板生产中的关键环节,需要遵循一系列标准规范。
如焊锡温度、焊盘与焊垫之间的间隙、焊锡的铺开面积等。
同时,应使用可靠的焊接设备和方法,以确保焊接质量和可靠性。
5.防静电处理:静电对电子产品具有严重的影响,因此需要对电路板进行防静电处理。
PCBA-工艺设计规范

PCBA-工艺设计规范1. 引言本文档旨在规范PCBA(Printed Circuit Board Assembly,印刷电路板组装)的工艺设计,确保生产过程中的高质量和稳定性。
PCBA是电子产品制造中重要的环节之一,正确的工艺设计可以确保产品的可靠性、功能性和性能稳定性。
2. 设计要求在进行PCBA工艺设计时,需要满足以下要求:2.1 设计规范•PCB布线符合设计规范,遵循最佳布局原则,最短路径和最小电流回路原则;•PCB设计必须考虑信号完整性和抗干扰能力;•需要保留适当的物理空间,方便组装和维修。
2.2 硬件要求•PCB材料应符合相关标准要求,具有良好的导电性和绝缘性能;•PCB层数应根据实际需求来确定,同时考虑信号层和电源层的布局;•组件的选择要符合相关标准和规定,能够满足产品的功能需求。
2.3 工艺要求•PCBA整个生产过程应遵守相关工艺标准和规范,确保产品质量;•SMT(Surface Mount Technology,表面贴装技术)组装必须符合IPC(Association Connecting Electronics Industries)相关标准;•焊接工艺应确保焊点质量,防止焊接缺陷和冷焊等问题。
3. 设计流程PCBA的工艺设计流程如下:3.1 PCB设计•根据产品需求,制定PCB的尺寸、层数和布局;•完成原理图设计、布线和走线规划;•使用专业的PCB设计软件进行PCB布局和布线。
3.2 元器件选型•根据产品要求和性能需求,选取合适的元器件;•选择符合规范的供应商,确保元器件的可靠性和稳定性。
3.3 SMT组装•进行SMT贴片工艺流程,包括钢网制作、贴片、回焊等;•严格控制贴片工艺参数,确保元器件正确、牢固地焊接。
3.4 机械组装•将PCB组装到产品中,包括固定和连接电路板;•在组装过程中要注意防止静电、引脚弯曲等问题。
3.5 焊接和测试•进行焊接工艺,包括手工焊接和波峰焊接;•对焊接后的PCBA进行功能测试和质量检验,确保产品符合设计要求。
PCB工艺设计规范
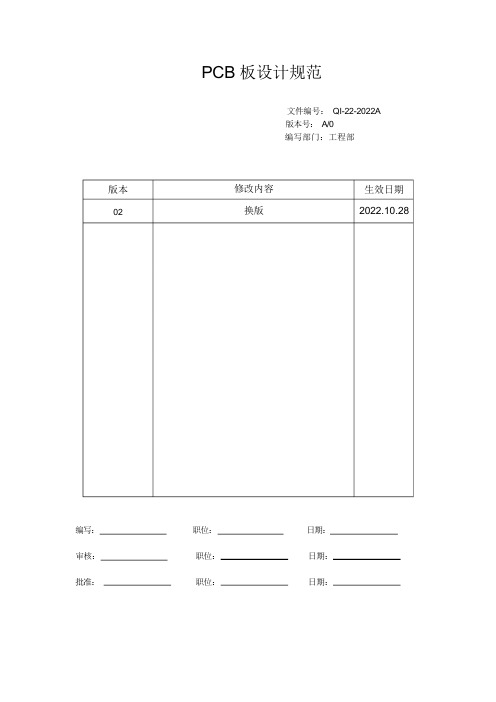
PCB 板设计规范文件编号: QI-22-2022A 版本号: A/0 编写部门:工程部编写:职位: 日期:审核:职位: 日期:批准:职位:日期:生效日期2022.10.28修改内容换版版本02.................................................................................................................................1.PCB 板设计需要有产品名称,版本号,设计日期及商标。
2.产品名称,需要通过标准化室拟定,如果是工厂的品牌,那末可以采用红光厂注册商标( )商标需要统一字符大小,或者同比例缩放字符。
不能标注商标的,HG 或者HGP 冠于产品名称前。
3.版本的序列号,可以用以下标识REV0 ,0~9, 以及0.0 ,1.0,等,弱小改动用.A 、.B 、.C 等区分。
具体要求如下:① 如果PCB 板中线条、元件器结构进行更换,一定要变更主序号,即从1.0 向2.0 等跃迁。
②如果仅仅极小改动,例如,部份焊盘大小;线条粗细、走向挪移;插件孔径,插件位置不变则主级次数可以不改,升级版只需在后一位数加之A 、B 、C 和D,五次以上改动,直接升级进主位。
③考虑国人的需要,常规用法,不使用4.0 序号。
④如果改变控制IC,原来的IC 引脚不通用,请改变型号或者名称。
⑤PCB 版本定型,技术确认BOM 单下发之后,工艺再改文件,请在原技术责任工程师确认的版本号后加入字符( -G)。
工艺部门多次改动也可参照技术部门数字序号命名,例如,G1 ,G2 向上升级…等。
4.PCB 板日期,可以用以下方案标明。
XX-YY-ZZ,或者,XX/YY/ZZ。
XX 表示年,YY 表示月,ZZ 表示日。
例如:11-08-08,也可以11-8-8,或者,11/8/8。
PCB 板设计一定要放日期标记。
TP设计规范-A0
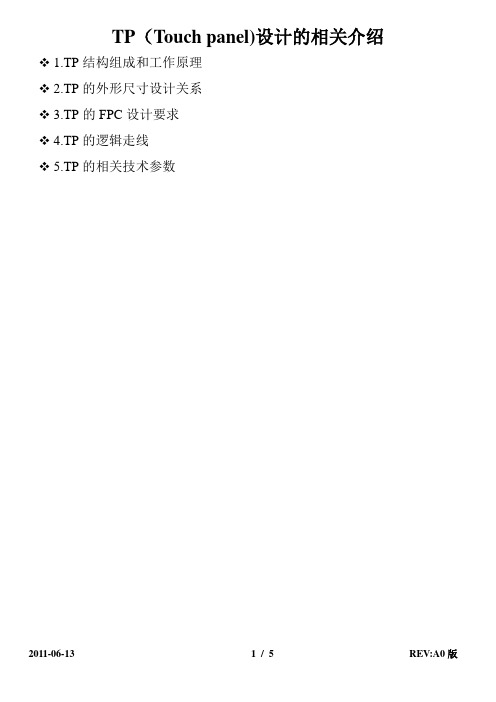
TP(Touch panel)设计的相关介绍1.TP结构组成和工作原理2.TP的外形尺寸设计关系3.TP的FPC设计要求4.TP的逻辑走线5.TP的相关技术参数一、TP的结构组成和工作原理我们常见的TP分为五种:矢量压力传感技术、电阻技术、电容技术、红外线技术及表面声波技术。
我司常用的电阻式触摸屏。
如以下说明:电阻式触摸屏主要由上部电极,下部电极,接插件等3 个基本结构组成(见上图)。
上部电极:有ITO膜的PET胶片。
下部电极:有ITO膜的PET胶片、玻璃或塑料,上面印刷有规则的绝缘小突起。
插接件:插入上部和下部电极之间热熔接于TP与装置之间的连接。
双面胶层:用胶粘力固定上,下部电极并且使上、下部电极保持一定间隔。
ITO(氧化铟)膜:透明导电膜。
非常薄,即透明又导电。
工作原理:当手指触摸屏幕时,平常相互绝缘的两层ITO导电层就在触摸点位置有了一个接触,产生电流导通作用,从而达到触摸效果.。
二、TP外形尺寸设计根据1.A、A1一般是依据模组的外形来设计。
各边比模组图的外形单边小0.2mm,公差为±0.2mm。
(以下单位均为mm)。
2.C、C1比LCD的AA区单边大0.5以上为佳。
3.B、B1比C、C1单边大1.0以上为佳,B、B1到A、A1的距离不得小于1.6,以保证有足够的空间走线,提高TP的可靠性。
4. E~E3双面胶在宽度设计时,应尽量做宽,但不得超出TP的B、B1,E、E2一般比A、A1小0.1~0.2最佳,E1、E3比B、B1大0.5左右,公差为±0.2,其厚度不得小于0.15,否则难以保证其粘性及防止在POL面片为亮片时出现水印等不良现象。
5.我们常见的TP厚度有1.0、1.1、1.4, 公差为±0.1。
6.TP的图标根据客户的需求来设计,不得善自改变其形状及大小,且图标不得进入TP的C、C1。
三、FPC设计要求1. D~D4,我们可以按照客户提供的图纸,根据一个参照物或提示的数据来设计,画出与客户图纸大致的形状。
元器件封装库设计规范
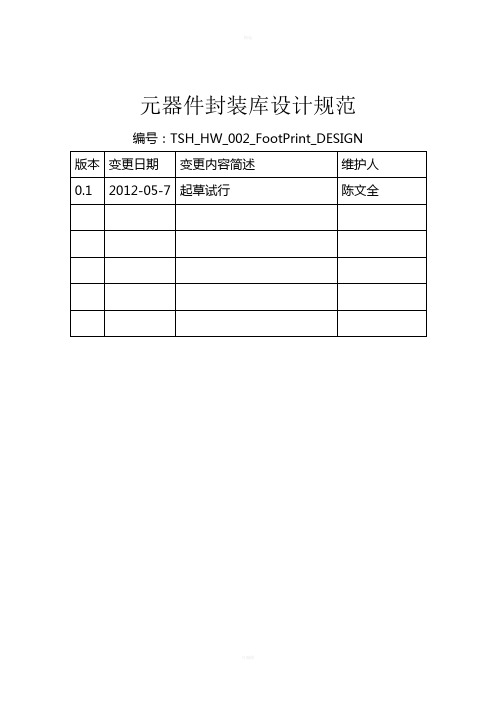
元器件封装库设计规范编号:TSH_HW_002_FootPrint_DESIGN1 概述闪龙公司《元器件封装库设计规范》(以下简称《规范》)为电路元器件PCB封装库设计规范文档。
本文档规定元器件封装库设计中需要注意的一些事项,目的是使设计规范化,并通过将经验固化为规范的方式,避免设计过程中错误的发生,最终提高产品质量。
本文中的所有信息归闪龙公司所有,未经允许,不得外传。
2 相关说明本规范作为电路设计中的指导文档,并会由其中抽取相应要点形成“元器件封装检查规范”。
3 设计规范3.1 通用规范单位尺寸使用mil(千分之一英寸)和mm(毫米)两种,以取整为使用前提。
比如:常用的100mil间距插座(2.54mm),50mil 间距芯片引脚;一些特殊的2mm间距插座,1mm间距芯片引脚,0.8mm间距BGA焊球。
因为单位换算有精度损失,在设计中不要随意切换单位!3.2 焊盘设计相关要求焊盘的命名方法参见表1注:PAD单位为mil。
焊盘类型简称标准图示命名表面贴装矩形焊盘SMD SMD + 宽(Y) x 长(X)命名举例:SMD21X20,SMD32X30。
表面贴装圆焊盘SMDC SMDC + 焊盘直径(C)命名举例:SMDC40表面贴装手指焊盘SMDF SMDF + 宽(Y) x 长(X)命名举例:SMDF57X10通孔圆焊盘THC THC + 焊盘外径(C)+ D +孔径(D)命名举例:THC25D10注:非金属化孔按通孔圆焊盘标注,焊盘外径标为0。
通孔矩形焊盘THR THR + 宽(Y)x 长(X)+ D +孔径命名举例:THR80X37D37。
4 SMD 元器件封装库的命名方法4.1 S MD分立元件的命名方法SMD 分立元件的命名方法见表2。
表2 SMD 分立元件的命名方法元件类型简称标准图示命名SMD电阻R命名方法:元件类型简称+元件尺寸命名举例:R0402,R0603,R0805 SMD排阻RA命名方法:元件类型简称+元件尺寸+个数命名举例:RA0402X4P。
电子元器件安装及焊接工艺设计规范方案精选全文

可编辑修改精选全文完整版电子元器件安装与焊接工艺规范电子元器件安装与焊接工艺规范1范围本规范规定了设备电气盒制作过程中手工焊接技术要求、工艺方法和质量检验要求. 2引用标准以下文件中的有关条款通过引用而成为本规范的条款.凡注日期或版次的引用文件,其后的任何修改单<不包括勘误的内容>或修订版本都不适用于本规范,但提倡使用本规范的各方探讨试用其最新版本的可能性.凡未注日期或版次引用文件,其最新版本适用于本规范.HB 7262.1-1995 航空产品电装工艺电子元器的安装HB 7262.2-1995 航空产品电装工艺电子元器的焊接QJ 3117-1999 航天电子电气产品手工焊接工艺技术要求IPC-A-610E-2010 电子组件的可接收性3技术要求与质量保证3.1一般要求3.1.1参加产品安装和检验的人员必须是经过培训合格的人员.环境温度要求:20℃-30℃.相对湿度要求:30%-75%.照明光照度要求:工作台面不低于500lx.工作场地应无灰尘,及时清除杂物<如污、油脂、导线头、绝缘体碎屑等>工作区域不得洒水.3.2安装前准备把安装所用的器材备齐,并放在适当位置,以便使用;所有工具可正常使用,无油脂,按以下要求检查工具:切割工具刃口锋利,能切出整齐的切口;绝缘层和屏蔽剥离工具功能良好.按配套明细表检查和清点元器件、印制板、紧固件、零件等的型号规格及数量.凡油封的零件或部件,在安装前均应进行清洗除油,并防止已除过的零件再次糟受污染.4元器件在印制板上安装4.1元器件准备4.1.1安装前操作人员应按产品工艺文件检查待装的各种元器件、零件及印制板的外观质量.4.1.2元器件引线按以下要求进行了清洁处理:a、用织物清线器轻轻地擦拭引线,除去引线上的氧化层.有镀层的引线不用织物清线器处理;b、清洁后的引线不能用裸手触摸;c、用照明<CDD>放大镜检验元器件引线清洁质量.4.2元器件成型须知a、成型工具必须表面光滑,夹口平整圆滑,以免损伤元器件;b、成型时,不应使元器件本体产生破裂,密封损坏或开裂,也不应使引线与元器件内部连接断开;c、当弯曲或切割引线时,应固定住元器件引线根部,防止产生轴向应力,损坏引线根部或元器件内部连接;d、应尽量对称成型,在同一点上只能弯曲一次;e、元器件成型方向应使元器件装在印制板上后标记明显可见;f、不允许用接长元器件引线的办法进行成型;g、不得弯曲继电器、插头座等元器件的引线.4.3元器件成型要求4.3.1轴向引线元器件引线弯曲部分不能延长到元器件本体或引线根部,弯曲半径应大于引线厚度或引线直径;见图1:图1 轴向引线元器件引脚折弯要求水平安装的元器件应有应力释放措施,每个释放弯头半径R至少为0.75mm,但不得小于引线直径.图2 元器件应力释放弯头处理要求4.3.2径向引线元器件反向安装径向引线元器件成型要求见图3:图3 径向引线元器件弯角要求4.3.3扁平封装元器件引线成型时就有防震或防应力的专门工具保护引线和壳体封接;用工具挪动扁平组件时,只允许金属工具与外壳接触;装配扁平组件时,工作台面上应垫有弹性材料.4.3.4用圆嘴钳弯曲元器件引线的方法如下:a、将成型工具夹持住元器件终端封接处到弯曲起点之间的一点上;b、逐渐弯曲元器件引线.图44.4元器件在印制板上安装的一般要求4.4.1按装配工序,将盛开好的元器件由小到大依次安装,先安装一般元器件最后再安装电敏感元器件.4.4.2当具有金属外壳的元器件需要跨接印制导线安装时,必须采取良好的绝缘措施.4.4.3安装元器件时,不应使元器件阻挡金属化孔.4.4.4质量较重的元器件应平贴在印制板上,并加套箍或用胶粘接.4.5元器件在印制板上的安装形式4.5.1贴板安装元器件与印制板安装间隙小于1mm,当元器件为金属外壳面安装面又有印制导线时,应加绝缘衬垫或绝缘管套,如图5:图5 贴板安装要求4.5.2悬空安装元器件与印制安装距离一般为3~5mm,如图6.该形式适用发热元器件的安装.图6 悬空安装要求4.5.3垂直安装元器件轴线相对于印制板平面的夹角为90°±10°,见图7.该形式适用于安装密度高的印制板俣不适用于较重的细引线的元器件.图7 元器件垂直安装要求4.5.4支架固定安装用金属支架将元器件固定在印制板上见图8:图8 元器件支架安装要求4.5.5粘接和绑扎安装对防震要求较高的元器件,巾板安装后,可用粘合剂将元器件与印制板粘接在一起,也可以用绵丝绑扎在印制板上,见图9:图9 元器件绑线安装要求4.5.6反向埋头安装反向埋头安装形式见图10:图10 元器件反向埋头安装要求4.5.7接线端子和空心铆钉的安装4.5.7.1接线端子和空心铆钉的安装要求如下:a、安装接线端子和空心铆钉时应满足正常指力下,既不转动,也不轴向移动,没有缺损或印制板基材脱落现象;b、接线端子杆不得打孔、切口、切缝和其它间断点,以免焊料和焊剂漏入孔内;c、铆接后的接线端子或空心铆钉不得有切口、切缝和其它间断点,铆接事,铆接面周围的豁口或裂缝小于90角分开,且延伸不超过铆接面时,允许有三个弧状豁口或裂缝;d、接线端子应垂直安装于印制板,倾斜角应不大于5°.4.5.7.2按以下步骤安装接线端子和空心铆钉:a、将印制板置于夹具上,将清洁的接线端子或空心铆钉从印制板的元件面插入相应的孔内,将印制板翻转,翻转时,接线端子或空心铆钉应紧靠住底板;b、用铆接器<铆压工装>接线端子或空心铆钉铆接到印制板上,应控制好压力.4.6焊接面上元器件引线处理4.6.1弯曲元器件引线焊接面上元器件引线可采用全弯曲、部分弯曲和直插式.a、全弯曲引线:引线弯曲后,引线端与印制板垂线的夹角在75°~90°之间;b、部分弯曲:引线弯曲后,引线端与印制板垂线的夹角在15°~75°之间,见下图,引线伸出长度为0.5mm~1.5mm;c、直插引线:引线端与印制板垂线的夹角在0°~15°之间,见图11,引线伸出长度为0.5mm~1.5mm.图11 焊接面元器件引脚处理要求全弯曲引线一般要求:a、引线弯曲部分的长底不得短于焊盘最大尺寸的一半或0.8mm,但不大于焊盘的直径<或长度>;b、向印制导线方向弯曲引线;c、引线全弯曲后与印制板平面允许的最大回弹角为15°;d、引线弯曲后相邻元器件的间隙不小于0.4mm;e、不许弯曲硬引线继电器、电连接器插针或工艺文件规定的其它元器件引线.4.6.2切割引线用切割器切除引线,不许损坏印制制导线;不许切割直插式集成电路、硬引线继电器插针或工艺文件规定的其它元器件引线.4.6.3固定引线用玻璃纤维焊接工具压倒已切割过的引线.4.7各类元器件在印制板上的安装4.7.1轴向引线元器件安装a、轴向引线元器件应按工艺文件规定进行近似平行安装;b、将引线穿过通孔,弯曲并焊到印制板的焊盘上.弯曲部分应满足要求.4.7.2径向引线元器件安装4.7.2.1金属壳封装的元器件反向埋头安装要求见条的要求.4.7.2.2伸出引线的基面应平行于印制板的表面,且有一定的间隙.4.7.2.3引线应从元器件的基点平直地延长,引线的弯头不应延伸到元件的本体或焊点处.4.7.2.4当元器件每根引线承重小于3.5g时,元器件可不加支撑面独立安装,此时,元器件的基面和印制板表面间距为1.3mm~2.5mm.基准面应平行印制板表面,倾斜角在10度以内.4.7.2.5当元器件每根引线承重大于3.5g时,元器件基面将平行于印制板表面安装,元器件应以以下方式加支撑:a、元器件本身所具备的弱性支脚或支座,与元器件形成一个整体与底板相接;b、采用弹性或非弹性带脚支架装置,支座不堵塞金属化孔,也不与印制板上的元器件内连;c、当弹性支座或非弹性带脚支座的元器件安装到印制板时,元器件每个支脚都应与印制板相连,支脚的最小高度为0.25mm,当使用一个分离式弹性支座或分离式弹性无脚支座时,元器件基面与印制板表面平行安装的要求, 使用非弹性支座连接元器件基面并平行安装于印制板表面时,则基面应与支座完全接触,支脚应与印制板完全接触.4.7.2.6侧面或端部安装的元器件应与印制板粘接或固定住,以防因冲击或震动而松动.4.7.2.7引线带有金属涂层的元器件安装,涂层与印制板表面焊盘处距离不得小于0.25mm.禁止修整引线涂层.4.7.3双引线元器件安装要求:距印制板表面最近的元器件本体边缘与印制板表的平行角度在10度以内,且与印制板间距在1.0mm~2.3mm以内,元器件与印制板垂线成最大角度为±15°.4.7.4扁平封装元器件安装扁平封装元器件的安装要求见条.4.7.5双列直插式集成电路的安装双列直插式元器件基面应与印制板表面隔开,其间距为0.5mm~1mm或引线的凸台高度.4.8焊接方法4.8.1单面印制板的焊接图12 单面印制板的焊接4.8.2金属化孔双面印制板的焊接金属化孔双面印制板的焊接应符合图要求.对有引线或导线插入的金属孔,通孔就充填焊料,焊料应从印制电路板一侧连续流到另一侧的元器件面,并覆盖焊盘面积90%以上,焊料允许凹缩进孔内,凹缩量如图13:图13 元器件在金属化孔双面印制板上的焊接4.8.3多层印制板的焊接多层印制板的焊接应符合图14要求.严禁两面焊接以防金属化孔内出现焊接不良.图14 元器件在多层印制板上的焊接4.8.4扁平封装集成电路的焊接采用对角线焊接方法,并符合以下规定:扁平应沿印制导线平直焊接,元器件引线与印制板的焊盘应匹配;引线最小焊接长度为1.5mm且引线在焊盘中间;元器件的型号规格标识必须在正面,严禁反装;扁平封装集成电路未使用的引线应焊接在相应的印制导线上;焊点处引线轮廓可见.图15 扁平封装元器件的焊接4.8.5断电器的焊接焊接时非密封继电器应防止焊济、焊料渗入继电器内部,在接线端子之间应塞满条形吸水纸带,焊接时继电器焊接面倾斜不大于90°.焊接密封继电器时,要防止接线端子根部绝缘子受热破裂,可用蘸乙醇的棉球在绝缘子周围帮助散热.4.8.6开关元器件的焊接焊接时可采用接点交叉焊接的方法,使加热温度分散,减少损坏.5元器件焊接判定标准元器件焊接质量判定可根据附表1~附表16内的图示.附表 2 有引脚的支撑孔-焊接主面目标 可接受不可接受和孔壁润湿角=360° 焊锡润湿覆盖率=100%•引脚和孔壁润湿角≥270° •焊盘焊锡润湿覆盖率≥0•引脚和孔壁润湿角<270°附表3 有引脚的支撑孔-焊接辅面目标可接受不可接受和孔壁润湿角=360° 焊锡润湿覆盖率=100%•引脚和孔壁润湿角≥330° •焊盘焊锡润湿覆盖率≥75%•引脚和孔壁润湿角<330° •焊盘焊锡润湿覆盖率<75%附表4 焊点状况目标可接受不可接受附表1 焊点润湿目标可接受不可接受1焊点表层总体呈现光滑和与焊接零件由良好润湿;部件的轮廓容易分辨;焊接部件的焊点有顺畅连接的边缘;2表层形状呈凹面状.可接受的焊点必须是焊接与待焊接表面,形成一个小于或等于90度的连接角时能明确表现出浸润和粘附,当焊锡量过多导致蔓延出焊盘或阻焊层的轮廓时除外.1不润湿,导致焊点形成表面的球状或珠粒状物,颇似蜡层面上的水珠;表面凸状,无顺畅连接的边缘;2移位焊点; 3虚焊点.洞区域或表面瑕疵;和焊盘润湿良好;形状可辨识;周围100%有焊锡覆盖;覆盖引脚,在焊盘或导薄而顺畅的边缘. •焊点表层是凹面的、润湿良好的焊点内引脚形状可以辨识.•焊点表面凸面,焊锡过多导致引脚形状不可辨识,但从主面可以确认引脚位于通孔中;•由于引脚弯曲导致引脚形状不可辨识.附表5 有引脚的支撑孔-垂直填充目标可接受不可接受润湿角度=360°焊锡润湿覆盖率=100% •周边润湿角度≥330°•焊盘焊锡润湿覆盖率≥75%•周边润湿角度<330°•焊盘焊锡润湿覆盖率<75% 附表6 焊接异常-暴露基底金属目标可接受不可接受露基底金属·基底金属暴露于:a〔导体的垂直面b〔元件引脚或导线的剪切端c〔有机可焊保护剂覆盖的盘·不要求焊料填充的区域露出表面涂敷层·元件引脚/导体或盘表面由于刻痕、划伤或其它情况形成的基底金属暴露不能超过对导体和焊盘的要求附表7 焊接异常-针孔/吹孔目标可接受不可接受良好、无吹孔·润湿良好、无吹孔·针孔/吹孔/空洞等使焊接特性降低到最低要求以下附表8 焊接异常-焊锡过量-锡桥目标可接受不可接受·**桥·横跨在不应相连的两导体上的焊料连接·焊料跨接到非毗邻的非共接导体或元件上附表9 焊接异常-焊锡过量-锡球目标可接受不可接受现象·锡球被裹挟/包封,不违反最小电气间隙注:锡球被裹挟/包封连接意指产品的正常工作环境不会引起锡球移动·锡球未被裹挟/包封·锡球违反最小电气间隙附表10 引脚折弯处的焊锡目标可接受不可接受折弯处无焊锡·引脚折弯处的焊锡不接触元件体·引脚折弯处的焊锡接触元件体或密封端附表11 焊接异常-反润湿目标可接受不可接受良好、无反润湿现象·润湿良好、无反润湿现象·反润湿现象导致焊接不满足表面贴装或通孔插装的焊料填充要求附表12 焊接异常-焊料受拢目标可接受不可接受料受拢·无焊料受拢·因连接产生移动而形成的受拢焊点,其特征表力纹附表13 焊接异常-焊料破裂目标可接受不可接受料破裂·无焊料破裂·焊料破裂或有裂纹附表14 焊接异常-锡尖目标可接受不可接受圆润饱满没有锡尖·焊锡圆润饱满没有锡尖·锡尖违反组装的最大高度要求或引脚凸出要求1.5毫米·锡尖违反最小电气间隙附表15 镀金插头目标可接受不可接受插头上无焊锡·镀金插头上无焊锡·在镀金插头的实际连接区域有焊锡、合金以外其它金属附表16 焊接后的引脚剪切目标可接受不可接受·引脚和焊点无破裂·引脚凸出符合规范要求·引脚和焊点无破裂·引脚凸出符合规范要求·引脚与焊点间破裂。
元件封装库设计规范
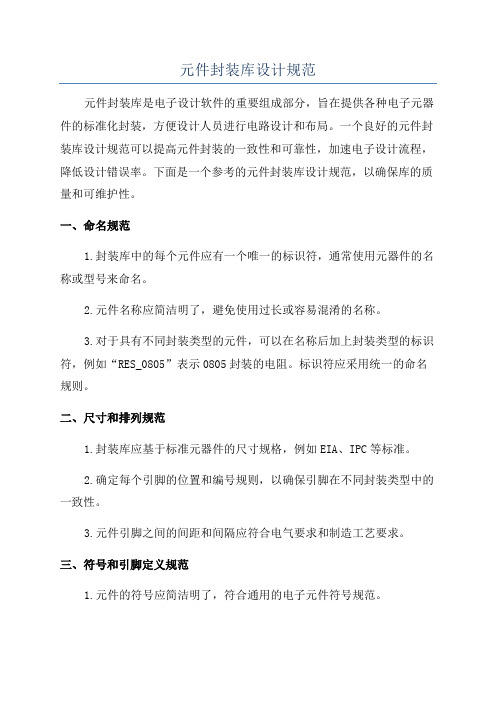
元件封装库设计规范元件封装库是电子设计软件的重要组成部分,旨在提供各种电子元器件的标准化封装,方便设计人员进行电路设计和布局。
一个良好的元件封装库设计规范可以提高元件封装的一致性和可靠性,加速电子设计流程,降低设计错误率。
下面是一个参考的元件封装库设计规范,以确保库的质量和可维护性。
一、命名规范1.封装库中的每个元件应有一个唯一的标识符,通常使用元器件的名称或型号来命名。
2.元件名称应简洁明了,避免使用过长或容易混淆的名称。
3.对于具有不同封装类型的元件,可以在名称后加上封装类型的标识符,例如“RES_0805”表示0805封装的电阻。
标识符应采用统一的命名规则。
二、尺寸和排列规范1.封装库应基于标准元器件的尺寸规格,例如EIA、IPC等标准。
2.确定每个引脚的位置和编号规则,以确保引脚在不同封装类型中的一致性。
3.元件引脚之间的间距和间隔应符合电气要求和制造工艺要求。
三、符号和引脚定义规范1.元件的符号应简洁明了,符合通用的电子元件符号规范。
2.符号应具有与元器件功能相关的形状和属性,以便于用户理解和识别。
3.确定每个引脚的编号和类型,对于一些特殊引脚(如供电引脚、地引脚等)应有特殊的标记。
四、属性和参数规范1.确定元件的关键属性和参数,如电阻值、电容值、工作电压等。
2.对于不同封装类型的元件,需要提供相应的封装尺寸和引脚数目等信息。
3.元件的参数应具有一定的准确性和可靠性,可以参考电子元器件的规格书或厂商提供的数据。
五、标注和备注规范1.对于特殊的元件要求或使用注意事项,可以通过标注和备注来说明。
2.标注和备注应清晰明了,提供足够的信息以便于用户正确理解和使用元件。
六、检查和验证规范1.在设计封装库时,需要进行严格的检查和验证工作,以确保库中元件的质量和正确性。
2.检查和验证应包括封装尺寸、引脚定义、符号、参数等方面的核对,以及元件封装的综合性测试。
七、版本控制和文档维护规范1.封装库应使用版本控制工具进行管理,以确保每个库的版本可追溯和可控。
研发工艺的设计规范标准

图37 :非金属化定位孔阻焊开窗示意图7.2.4 过孔塞孔设计[56]需要塞孔的孔在正反面阻焊都不开窗。
[57]需要过波峰焊的PCB,或者Pitch<1.0mm的BGA/CSP,其BGA过孔都采用阻焊塞孔的方法。
[58]如果要在BGA下加ICT测试点,推荐用狗骨头形状从过孔引出测试焊盘。
测试焊盘直径32mil,阻焊开窗40mil。
图38 :BGA测试焊盘示意图[59]如果PCB没有波峰焊工序,且BGA的Pitch≥1.0mm,不进行塞孔。
BGA下的测试点,也可以采用一下方法:直接BGA 过孔做测试孔,不塞孔,T面按比孔径大5mil阻焊开窗,B面测试孔焊盘为32mil,阻焊开窗40mil。
7.3 焊盘的阻焊设计[60]推荐使用非阻焊定义的焊盘(Non Solder Mask Defined)。
图39 :焊盘的阻焊设计[61]由于PCB厂家有阻焊对位精度和最小阻焊宽度的限制,阻焊开窗应比焊盘尺寸大6mil 以上阻焊非阻焊定义的焊盘Non Solder Mask Defined阻焊定义的焊盘Solder Mask DefinedDD+10mil 阻焊9.1 丝印设计通用要求[77]通用要求●丝印的线宽应大于5mil,丝印字符高度确保裸眼可见(推荐大于50mil)。
●丝印间的距离建议最小为8mil。
●丝印不允许与焊盘、基准点重叠,两者之间应保持6mil的间距。
●白色是默认的丝印油墨颜色,如有特殊需求,需要在PCB钻孔图文中说明。
●在高密度的PCB设计中,可根据需要选择丝印的内容。
丝印字符串的排列应遵循正视时代号的排序从左至右、从下往上的原则。
9.2 丝印的内容[78]丝印的内容包括:“PCB名称”、“PCB版本”、元器件序号”、“元器件极性和方向标志”、“条形码框”、“安装孔位置代号”、“元器件、连接器第一脚位置代号”、“过板方向标志”、“防静电标志”、“散热器丝印”、等。
[79]PCB板名、版本号:板名、版本应放置在PCB的Top面上,板名、版本丝印在PCB上优先水平放置。
元件成型的规范要求
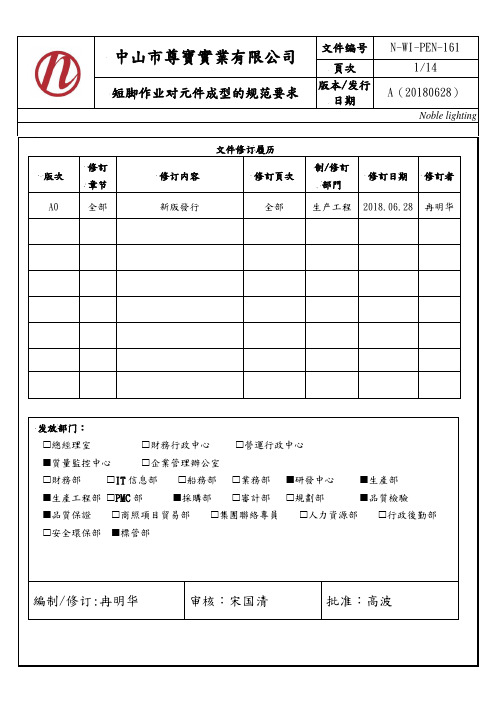
5.4未注公差均按±0.5mm。
5.5成型时不允许从元器件引线的根部直接弯折。规定弯折处距离元器件主体≥1.0mm。
5.6成型后的引线
5.6.1不得有扭曲现象,引线上不得有明显压坏和其他伤痕。
5.6.2折弯处的痕迹规定不超过0.25d的凹陷(d为引线直径)。
文件修订履历
版次
修訂章节
修订内容
修訂頁次
制/修訂部門
修訂日期
修訂者
A0
全部
新版發行
全部
生产工程
2018.06.28
冉明华
发放部门:
總經理室財務行政中心營運行政中心
質量監控中心企業管理辦公室
財務部IT信息部船務部業務部研發中心生產部
生產工程部PMC部採購部審計部規劃部品質檢驗
品質保證商照項目貿易部集團聯絡專員人力資源部行政後勤部安全環保部標管部
适用元器件
径向型(电容、发光二极管、三极管、红外接收器)
应用环境
元器件表面温升≤40℃
元器件的外形尺寸
备注
*为成型三极管类、无极性电容字符面或红外接收器类的工作面定向
6.6 ZR型
ZR型
成型代号
电容类CZR-s×h
径向二极管类VZR-s×h
三极管类VZR-s×h
电感类LZR-s×h
标定成型跨距/参数(s)
編制/修订:冉明华
审核:宋国清
批准:高波
1.0目的
规范元器件来料成型操作的方法和流程,消除元器件成型时应力造成的损伤,提高产品可靠性,提高产品质量,防止出现批次质量事故。
2.0适用范围
本规范规定了元器件引线成型生产中人、机、料、法、环的工艺要求和质量检测中的管理要求、质量控制方法、元器件引线成型方式和技术要求。本规范适用于印制板厚度为1.0~1.6mm,用手工插件的元器件(包括电阻器、电容器、电感器、二极管、三极管、集成电路、振荡器、保险丝管保险管)引线成型。适用于本公司所有产品,包括内、外发产品。
- 1、下载文档前请自行甄别文档内容的完整性,平台不提供额外的编辑、内容补充、找答案等附加服务。
- 2、"仅部分预览"的文档,不可在线预览部分如存在完整性等问题,可反馈申请退款(可完整预览的文档不适用该条件!)。
- 3、如文档侵犯您的权益,请联系客服反馈,我们会尽快为您处理(人工客服工作时间:9:00-18:30)。
元器件成形工艺设计规范Rev.: A0文件编号:发行日期:版权属于麦格米特, 禁止任何未经授权的使用。
The copyright belongs to Megmeet. Any unauthorized use is prohibited.6. 规范内容6.1 引线折弯按照元器件的引线截面图形划分,通常有圆形(直径D)和矩形(厚度T)两种引线。
阻容组件一般为圆柱形引线,而半导体元器件一般为四棱柱形引线。
6.1.1 变向折弯下ET-1a图描述了变向折弯的引线的特征参数。
折弯内径R,折弯角度ω。
ET-1a6.1.2 无变向折弯6.1.2.1 打Z折弯图ET-1b描述了无变向折弯的引线的特征参数。
折弯内径R,折弯角度ω,偏心距V。
在本规范中叫做打Z成形。
有2个折弯内径R及折弯角度ω。
ET-1b6.1.2.2 打K折弯在图ET-1c中,描述了一种特殊的折弯方式,即偏心距V=0。
通常是为了保障引线插装到装配孔后,元器件可以抬高以消除应力,或起支撑作用,或满足散热要求的一种折弯方式。
这种折弯方式就是我们常说的“打K”或“Ω折弯”。
K值的大小一般与引线的直径D和厚度T 有关,同时还与折弯的模具有关,在表EE-1中给出了常见的K值。
ET-1c注意:引线打K时,通常要求凸起部分一般不能超出元器件的丝印最大外框(Placement 层),同时要保障引线间距满足电气间隙的要求,对于实在无法满足的在试验验证没有问题后才可以超出元器件的丝印外框。
6.2 引线折弯的参数6.2.1 封装保护距离d“安装在镀通孔中的组件,从器件的本体、球状连接部分或引线焊接部分到器件引线折弯处的距离,至少d>1mm(可依器件各项要求适当调整)。
通常出于保护元器件的内部结构与方便机械加工。
需要注意的是,元器件“本体、球状连接部分或引线焊接部分”一定要参考元器件供应商提供的几何尺寸的最大外形,包括涂层在内。
同时,封装保护距离范围内的引线其延伸方向禁止被改变。
下图ET-2a~c展示了3种典型元器件的封装保护距离的具体测量方式。
图ET-2a图ET-2b图ET-2c下表EE-1列出了普通轴向和径向元器件,功率半导体元器件的封装保护距离的最小值。
表EE-1:引线的直径D 或者厚度T封装保护距离最小值d电阻玻璃二极管,塑封二极管,陶瓷封装电阻、电容, 金属膜电容电解电容功率半导体器件封装类型TO-220及以下TO-247及以上D(T)≤0.8mm 1.0mm 1.5mm 2.0mm 3.0mm 3.0mm0.8mm<D(T)<1.2mm2.0mm 2.0mm3.0mm / /1.2mm≤D(T)3mm 3mm / / /6.2.2 折弯内径R根据引线直径D(圆柱形引线)和厚度T(四棱柱形引线)的不同,元器件引线内侧的折弯半径R的值参考下表EE-2。
表EE-2:引线的直径D或者厚度T 引线内侧的折弯半径R(优选值)D(T)<0.8mm 不小于D或者T(优选值1.0mm)0.8mm≤D(T)<1.2mm 不小于1.5×直径D或者厚度T(优选值1.5mm,2.0mm)1.2mm≤D(T)不小于2.0×直径D或者厚度T(优选值2.5mm,3.0mm)由于是内径,那么元器件引线的相对外径就是R+D(T)。
6.2.3 折弯角度ω折弯角度是本次引线折弯后折弯部分的引线与原来未折弯部分引线的夹角,通常该角度大于等于90°小于180°。
折弯角度ω的优选值参考下表EE-3。
表EE-3:折弯类型折弯角度ω(公差+3°)优选值变向折弯90°非变向折弯120°,135°,150°6.2.4 偏心距V对于存在特殊装配关系或者电气绝缘的元器件,例如某些功率元器件装配了散热器,通常使用非变向折弯引线以消除应力,根据引线的直径D或者厚度T的不同,偏心距的选择也有不同的要求。
表EE-4:引线的直径D或者厚度T 偏心距V优选值D(T)<0.8mm 不小于D或者T(优选值1.0,2.0,3.0mm)0.8mm≤D(T)<1.2mm 2.0mm,3.0mm1.2mm≤D(T) 3.0mm,4.0mm6.2.5 K值需要明确的是,K是一个高度值,它不仅跟引线直径D或厚度T有关,还受到折弯内径R 和模具的影响,这里提供的是一个经验数据。
手工打K和自动化打K的尺寸有较大的差异,设计时应该考虑其差异。
表EE-5:引线的直径D或者厚度T K值(MAX)优选值D(T)<0.8mm 3mm0.8mm≤D(T)<1.2mm 3mm1.2mm≤D(T) 4.0mm其它折弯还包括环形折弯、驼峰折弯等,由于其折弯方式复杂,本规范不推荐选择。
6.2.6 关于元器件引线材质及反复折弯原则上只有纯铜(99.99%铜)及铜合金材质的引线允许折弯,对于其它材质的引线需要通过试验验证满足相关要求后才明确是否可以折弯。
由于元器件引线材质及几何外形的差异,元器件引线一般不应该反复折弯。
对于小批量验证或者制成板返修的项目,个别元器件可以以反复折弯。
对于电阻,二极管等圆柱形引线最多反复折弯次数不超过3次,对于四棱柱形引线的功率半导体器件等最多反复折弯次数不能超过2次。
对于四棱柱形引线,其折弯面必须是其四个围成四棱柱中较大的两个面。
绝对禁止折弯面是较小的两个面。
ET-2d 折弯面的选择7 元器件成形7.1 轴向元器件的成形通常按照在板面的装配方式不同,可以分为卧装成形、立装成形两种;如果没有特殊说明,以卧式水平安装在电路板上的具有轴向引线的元件的主体(包括末端的铅封或焊接)必须大体上处于两个安装孔的中间位置。
如下图所示,尽量满足X-Y≤±0.5mm。
ET-3a X≈Y7.2 卧装成形类型通常有2种形式的卧装成形,它包括卧装贴板(图ET-3b),卧装抬高(图ET-3d)如下图所示,尽量满足d≥1mm。
ET-3b 卧装贴板成形,引线变向折弯角度90°ET-3d 变向折弯及打K引线的卧装抬高成形成形关键点:R,K,d,ω,h(抬高距离);明确贴板成形的(图ET-3b),最大抬高距离不大于0.5mm;明确需要抬高成形的,最小抬高距离不小于1.5mm;通过控制打K(或者辅助支撑材料)的位置,可以控制元器件本体距离板面的距离h。
适用元器件:对于非金属外壳封装且无散热要求(功率小于1W)的二极管、电阻等可以采用ET-3b的卧装贴板成形方式;对于金属外壳封装或有散热要求(功率大于等于1W)的二极管、电阻,必须抬高成形。
应用特点:适合板面上2维空间(板面X/Y方向)较大,而且还有一定的空间高度;抬高成形的元器件,如果单个引线承受重量大于5.0g,必须使用其它固定材料固定或支撑元器件,以防止元器件受震动冲击而损坏;7.3 立装成形类型按照元器件本体下部引线的成形方式不同,可以划分为不折弯、打K成形和打Z成形。
ET-3f 本体下引线不折弯ET-3g 本体下引线打Z折弯ET-3h 本体下引线打K折弯成形关键点:R,d,K,Z,ω,h;对于无极性的元器件,要求其标识从上至下读取。
有极性的元器件,要求其可见的极性标识在顶部,以便于查检;通过控制打K或Z的位置可以控制元器件本体距离板面的距离;可以通过组件顶部2个折弯位置的距离来控制引线插件的距离。
适用元器件:二极管、电阻、保险管等等。
应用特点:如果单个引线承受重量大于5.0g,必须使用其它固定材料固定或支撑元器件,以防止元器件受震动冲击而损坏;除非使用或者借助辅助材料保障抬高和支撑(例如:瓷柱或磁珠),否则不推荐图片ET-3f 所示的本体下部引线不折弯。
如果不折弯本体下部引线,则要求元器件必须垂直板面(或倾斜角度满足相关要求);对于功率大于2W以上的电阻,由于打K成形而造成引线长度不足的,在设计时需要注意本体顶部的伸出引线需要勾焊加长,以满足插件要求;对于有引线的保险管,要注意引线与本体底部的金属部分不能短路,可以使用辅料,如直径1.5mm的套管,保护引线不与本体的下端的端子短路;在板面上2维空间(板面X/Y方向)占用空间较小,高度有要求;7.4 径向元器件的成形通常按照在板面的装配方式不同,可以分为卧装成形、立装成形两种。
7.4.1 立装成形为了防止元器件的封装材料插入焊孔而影响透锡,立装元器件的引线一般需要打K成形。
通常我公司来料的电容已经预成形引线了,对于没有成形的,参考以下成形方式,禁止打Z成形。
ET-3i 径向元器件立装成形关键点:R,K,d,ω;通过控制打K的位置可以控制元器件本体距离板面的距离;组件本体抬高距离板面h不小于1.5mm。
适用元器件:陶瓷封装的压敏电阻,热敏电阻,电容等等。
应用特点:如果单个引线承受重量大于5.0g,必须使用其它固定材料固定或支撑元器件,以防止元器件受震动冲击而损坏;在板面上2维空间(板面X/Y方向)占用空间较小,高度有要求;7.4.2 卧装成形在装配条件复杂,而且高度空间不足时,可以选用卧装成形,引线需要变向成形。
ET-3j 径向元器件卧装成形关键点:R,d,ω。
适用元器件:陶瓷封装的压敏电阻,热敏电阻,电容、电解电容等等。
应用特点:元器件至少有一边或一面与印制板接触,推荐点胶固定元器件;PCB设计安规要考虑本体下走线,同时注意绿油非有效绝缘;在板面上2维空间(板面X/Y方向)占用空间较大,应用于高度空间有限制的制成板。
7.5 功率半导体元器件的成形本规范所描述的功率半导体器件适用于TO-126,TO-220(AC/AB),ISOWATT220(AC/AB),TO-247,SOD93,SOT93,TOP31,ISOTOP,TO264,TO-3P等类型封装的IGBT管,场效应管,二极管,可控硅,三极管,整流桥等。
7.5.1 立装成形功率半导体器件引线推荐打Z折弯以更好的消除应力。
如果制成板空间非常紧张可以不成形,但是必须保障有消除装配或焊接过程的应力的措施,例如,焊接定位工装,或者后补焊等。
根据引线台阶所在Z形折弯位置的不同,可以分为台阶下折弯和台阶上下折弯(仅适用于TO-220封装)。
ET-3k ET-3l 台阶以下的引线部分折弯,其它引线位置无折弯d dET-3m ET-3n 台阶位于Z形折弯的两折弯处的中间成形关键点:R,V,ω,H(装配高度);为防止引线台阶开裂,Z形折弯到引线的台阶的距离必须保证大于等于0.5mm,即没倒角前的卡具凸起距离台阶的最小距离不小于1.0mm(即在引线台阶上下各0.5mm范围内无引线折弯形变)。
右侧的ET-3n明确的指示了具体的Z形折弯到引线台阶的测量方法,它是没有倒角的折弯凸起到台阶的最短距离。
由于在实际的成形卡具上,并没有凸起,取代的是倒角R,同时卡具加工倒角前是有凸起的,所以可以更加准确的设计卡具;注意偏心距V的尺寸,要求满足实际引线与散热器之间的间距;由于实际尺寸及安全间距的计算,图ET-3m的成形方式仅适用于TO-220封装的功率半导体器件。