轴承套圈超精研技术漫谈
轴承精密冷辗扩及磨削超精技术的发展状

轴承精密冷辗扩及磨削超精技术的发展状一、精密辗扩技术轴承套圈是作为大批量生产的零件。
采用传统的加工方法,材料利用低,工作条件差,且难以满足现在产品的要求。
近年来迅速发展的精密冷辗扩加工工艺是一种少、无切削的新工艺,由于精密冷辗扩能最大限度地使工件形状和精度接近于成品零件的形状和精度,并可显著改善工件的内在质量,大幅度地节省原材料,具有很好的经济和社会意义,所以该加工方法引起国内外轴承企业界的普遍重视。
(一)应用冷辗扩技术制造轴承套圈的优点1、可以降低原材料的消耗。
如果采用通常的切削加工方法来制造,材料的利用率通常为40~50%,而用冷辗压方法制造,材料利用率则可达60~75%。
例如:6308常规工艺下料0.918Kg,冷辗工艺下料0.68 Kg,两者相差0.23 Kg。
2、可以大幅度提高劳动生产率。
冷辗压是在辗扩机上进行的,机床的一次行程就可以完成所有形面的加工。
3、可以提高零件的机械性能。
冷辗压变形后,金属材料的晶粒组织更加致密,金属流线不变,没有切断,所以材料的抗疲劳强度提高。
采用冷辗工艺其寿命可稳定提高一倍。
洛阳轴承研究所1984年对冷辗6204轴承进行寿命实验结果表明,实际寿命与计算寿命之比达到22倍以上,可靠性达99.93%。
1990年洛阳轴承厂将冷辗工艺应用于6206轴承,实验结果为6206轴承的实验寿命与计算寿命之比达到20多倍,1998年洛阳轴承研究所与温州摩托车轴承有限公司合作,把冷辗工艺应用于摩托车曲柄连杆轴承6304,实验结果为轴承寿命1000小时,可靠性99.99%,而采用钢管车削轴承寿命为300小时,可靠性98%。
4、可以降低零件的制造成本。
冷辗压可以减少材料消耗和缩短加工时间,降低了生产成本。
减少材料消耗和缩短加工时间,机床的一次行程就可以完成多个形面加工,大幅度提高劳动生产率,节省能耗等。
5、具有很好经济效益和社会效益。
以6308为例:节材0.23 Kg,如钢材按3.6元/ Kg,节省0.828元;节约锻造加退火费达2.5元/ Kg,节能效益为2.5×0.23=0.58元;机加工减少25%,常规车加工套圈加工费为0.8元/套,那么冷辗节约加工费为0.8×25%=0.2元。
高精度轴承关键部件精密超精密加工技术

精密·制造
三、高精度轴承的精密超精密加工技术
1 磨削加工技术
加工工艺:
磨削是指用磨料,磨具切除工件上多余材料 的加工方法。磨削加工是应用较为广泛的切削加 工方法之一。
根据工艺目的和要求不同,磨削加工工艺方法有多种形式,为了适应发展需要, 磨削技术朝着精密,低粗糙度,高效,高速和自动磨削方向发展。磨削加工方法的形
2 3 6
深沟球轴承
5
圆锥滚子轴承
推力球轴承
精密·制造
二、高精度轴承各部件加工工序概述
2 轴承的结构(深沟球轴承)
精密·制造
二、高精度轴承各部件加工工序概述
3 轴承加工工艺流程
洛阳汇普轴承加工流程图
精密·制造
二、高精度轴承各部件加工工序概述
保持架
体用 并以 将隔 其离 保滚 持动 在体 轴︐ 承通 内常 ︒还 引 导 滚 动 原材料——剪料——裁环——光整——成形——整形——冲铆钉孔
实际切削路程比普通磨削路程要长;
实际的切削宽度增加,增大金属去除率,提高生产效率; 单颗磨粒的运动轨迹为正弦曲线,一个砂轮上拥有多颗磨粒,相邻的磨粒运动 轨迹便会重叠,使被加工工件表面成网状结构,有利于提高工件的表面质量。
磨削力比普通磨削要小,这样便可以提高加工的稳定性,减小磨削热的产生,
精密·制造
三、高精度轴承的精密超精密加工技术
4 油石超精研加工技术
目前轴承超精密加工中广泛采用的是油石超精研 加工,简称超精加工,一般是指用低压弹性地将细粒 度磨料的油石压在工件加工表面上,工件做旋转运动, 油石在垂直于工件旋转方向上按一定规律做快速往复 摆动,并提供良好的润滑与冷却条件,降低加工表面 粗糙度,提高几何精度。
轴承超精基础知识

目录
• 轴承超精概述 • 轴承超精加工原理 • 轴承超精加工设备 • 轴承超精加工工艺 • 轴承超精加工实践案例 • 轴承超精加工技术挑战与解决方案
01
轴承超精概述
轴承超精定义与分类
轴承超精定义
轴承超精是一种利用磨粒切削和 研磨作用,对轴承零件进行微量 切削和光整加工的技术,以提高 轴承的精度、表面质量和性能。
轴承超精分类
根据加工方式和目的的不同,轴 承超精可分为研磨超精、抛光超 精和珩磨超精等。
轴承超精应用领域
01
02
03
汽车工业
轴承是汽车关键零部件之 一,轴承超精技术对于提 高汽车的性能和降低噪音 具有重要作用。
机械工业
各类机械装备中的轴承都 需要较高的精度和性能, 轴承超精技术可以满足这 些要求。
程,包括粗磨、半精磨、超精磨等工序。
设备选型与配置
02
选择适合的超精加工设备,如超精磨床、研磨机等,并合理配
置辅助设备和工具。
工艺参数设定
03
根据工艺流程和设备特性,设定合理的工艺参数,如磨削速度、
进给量、切削深度等。
关键工艺参数控制
磨削力控制
通过调整磨削参数和砂轮特性,控制磨削力在合适范围内,避免轴 承表面烧伤和裂纹等缺陷。
汽车变速器轴承超精加工
针对变速器高速、重载的工作环境,采用特殊的热处理工艺和表面 处理技术,提高轴承的耐磨性和疲劳寿命。
汽车转向系统轴承超精加工
转向系统轴承要求具有高精度、低摩擦和低噪音等特点,通过优化 磨削参数和采用高性能磨料,实现轴承的高精度加工。
机床主轴轴承超精加工案例
高速机床主轴轴承超精加工
根据轴承材料和表面质量要求,选择 合适的抛光轮或抛光布。
滚锥轴承套圈滚道超精研工艺参数的选择

o u i ih g o a -olr b ai g r l wa e t n d r s a c n o ls o e f s p r f s i f tpe r l e n ol y n s ,a e e h o i t n ,we s lc h e o a l e n n r e r a r ee t t e r a n b e s
O 、 言 前
随着 我 国铁 路 客货 车全 面提 速 , 铁 路轴 承 ( 对 圆锥
滚子轴 承 , 称 滚 锥 轴 承 ) 使 用 性 能 提 出 了新 的 要 简 的 求 。即如何 使轴 承在 转 速 提 高 的前 提 下 , 能保 证 足 仍 够 的寿命 和 良好 的 工 作 性 能 。这 需 从 轴 承设 计 、 造 制 精度 和工作 表 面质量 等方 面 进行 改 进 。在 轴 承 的生 产 中 , 承套 圈滚 道 的 超精 研 加 工 是 决定 轴 承 套 圈 零件 轴 乃 至整 套轴 承精 度 的主 要 环 节 , 道 表 面 的超 精 研 加 滚 工直接影 响滚锥轴 承寿命 、 降低 轴 承振 动和 噪声 。 超精 研加 工始 创 于美 国 , 目前 在欧 洲 、 日本得 到 了
动设 定 , 精研 加 工过 程工 艺参 数 可 自动 变 换 , 超 以及 异 常情况 可 自动停 机 和显 示报 警 。 我 国在轴 承套 圈滚 道超 精 加 工方 面 起 步 较 晚 。2 0 世纪 6 0年代 中期 以前 , 本 采 用 砂 布 抛 光 工艺 ,0世 基 2
纪6 0年代后 期 , 引进 日本 、 国 的超 精 设 备 , 发 超 精 德 研
维普资讯
20 年第1 期 07 0
文章 编 号 : 0 —2 6 ( 0 7 1 0 7 0 1 1 2 5 20 ) 0— 0 9— 4 0
如何正确的操作外球面轴承的超精加工

超精完成的外球面轴承在逐个退磁,送往装 配车间进行装配。注意事项
细光加工时,油石的振幅一定要调小,其振 幅不要调的太大,虽然轴承的生产效率上去了,
8
顺着琴声 轻声走 去,声 音是从 一片礁 石后面 传来的 ,我慢 慢靠拢 礁石, 爬上去 伸长脖 子往下 看
但是表面的粗糙度值下降了,质量也就跟着下降 了。
其次为细光加工,在细光加工时,钝化的磨 粒不易脱落,切削作用降低,磨粒的切削深度小,
6
顺着琴声 轻声走 去,声 音是从 一片礁 石后面 传来的 ,我慢 慢靠拢 礁石, 爬上去 伸长脖 子往下 看
有利于降低工件表面的粗糙度。油石的振幅一定 要调小,其振幅不要调的太大,虽然轴承的生产 效率上去了,但是表面的粗糙度值下降了,质量 也就跟着下降了。
2
ቤተ መጻሕፍቲ ባይዱ
顺着琴声 轻声走 去,声 音是从 一片礁 石后面 传来的 ,我慢 慢靠拢 礁石, 爬上去 伸长脖 子往下 看
面积增加,便于轴承更好增加精度和质量。下面 我就讲讲轴承在超精过程中的流程,以及注意的 事项:
通过轴承磨加工机械的外球面轴承套圈
3
超精机 退磁机 首先我们要把外球面轴承退磁,其原理是让
4
顺着琴声 轻声走 去,声 音是从 一片礁 石后面 传来的 ,我慢 慢靠拢 礁石, 爬上去 伸长脖 子往下 看
轴承在超精过程中,避免有铁削粘在轴承内圈, 使轴承的精度下降。
进行粗光加工,控制油石的震动频率,其原 理为去除磨削变质层和加工余量为主。油石的振
5
幅要强,其目的就是去除轴承套圈的最层粗糙 度。
外球面轴承的超精,是将轴承磨加工之后的 一道工序,其重要作用为纳米级加工轴承套圈的 内滚道和外滚道,在外球面轴承的套圈生产过程 中是必不可少的。由于轴承在磨加工中,由于轴
高精度轴承套圈超精密加工技术的分析与展望

高精度轴承套圈超精密加工技术的分析与展望
孟鑫
【期刊名称】《军民两用技术与产品》
【年(卷),期】2018(000)022
【摘要】随着经济的发展,社会生活开始进入大机器时代.在工厂中一些大机器的使用,使得人们的工作效率相比小机器时代大大增加,人们在大机器的主轴上安装轴承套圈,用来避免大机器在长时间运作中出现磨损现象导致失效,并且轴套的位置一般装填料密封或机械密封,通过磨损轴套来保护轴.同时在航空航天领域的型号研制过程中,航空发动机、直升机和固定翼飞机、卫星飞轮、航天发动机等结构对轴承的重量、结构、强度以及耐久性的要求也越来越高,轴承套圈的加工具备很高的技术含量,轴承已经成为当代基础元件发展的瓶颈.随着科学技术的飞速发展,为满足国防建设的急迫需求,人们对于高精度轴承套圈超精密加工技术又有了新的展望.
【总页数】1页(P131)
【作者】孟鑫
【作者单位】航天精工股份有限公司,天津 300000
【正文语种】中文
【相关文献】
1.汽车圆锥滚子轴承套圈自动化联线加工技术 [J], 田世玲;于晓岩;王江山
2.超精密级球轴承套圈沟道超精研机床及工艺探讨 [J], 陈阿龙;周有华
3.高精度轴承座类零件的超精密加工技术研究 [J], 蔡文波
4.高精度轴承套圈超精密加工技术的现状与发展 [J], 关佳亮;胡志远;张妤;戚泽海;
孙晓楠;路文文
5.高精度轴承套圈超精密加工技术发展分析 [J], 程胜
因版权原因,仅展示原文概要,查看原文内容请购买。
我国轴承套圈超精研技术的改进要点

我国轴承套圈超精研技术的改进要点我曾经在《怎么样提高高精度轴承的超精质量?》一文中写到:“超精加工主要要提高和改善被加工工件表面的微观质量,这些微观质量包括粗糙度、沟形、圆度和金属条纹的走向。
”轴承套圈沟道超精研工序主要是为了降低被加工沟道的粗糙度,这是最基本的要求,无论是最原始的棍棒超精机还是采用无心支撑结构的自动化超精机,原理大同小异,都是如此。
高水平的和低档的轴承套圈超精研设备的主要区别是轴承套圈沟道形状精度的改善程度和被加工工件表面应力状态的差异。
轴承套圈沟道形状精度的改善主要取决于三个方面:首先,要约束超精前的轴承沟道磨加工形状的基础精度,轴承沟道的基准精度和位置精度在磨削工序也要精确地控制,因为这些需要约束的被加工工件的磨削工序的精度及其对超精加工的结果的影响是不容忽视的;其次,超精研设备的制造精度也会对被超精工件沟道表面形状的变化起到很大的影响,品质较差的超精机非但不能够改善磨削工序形成的形状精度,反而会破坏磨削工序形成的形状精度;第三,超精余量的大小不仅与超精加工的节拍有关,而且也与轴承沟道超精后的表面质量有关系。
假如我们的轴承产品没有对轴承的噪音和轴承的寿命提出特殊的要求,假如我们的轴承产品仅仅满足于参与国内外市场的低价格竞争,假如我们的轴承产品不想走出国门或者不想替代进口产品,那么,使用低价位的超精研设备是可以的。
因为,在中低档产品的轴承市场上,中国的轴承企业打了很多顽强的战役,在空调类家电市场和电机市场,我们的微型和小型轴承取得了不俗的销售业绩,这些成绩的取得也部分得益于我国轴承加工设备的发展和进步。
而在我国高精尖产品领域,大量的高附加值高利润轴承还是依靠进口。
我国生产的最好的轴承设备,即使出口到国外,也只是应用在普通轴承生产线上;部分大陆境内的外资和合资的轴承加工企业采购国内的轴承设备,也主要用在中低档轴承的生产线上。
迄今为止,我国高水平的进口轴承设备所占的比率很小,部分原因是由于高水平的进口轴承设备的价格普遍高于国产的轴承设备,其主要原因还是国内大部分企业生产的轴承精度和效率要求偏低,在引进更好水平的进口轴承设备方面的要求还不是特别强烈。
高精密轴承套圈锻造关键技术集成与应用

近年来,随着工业制造技术的不断发展,高精密轴承套圈锻造技术在机械制造领域中扮演着越来越重要的角色。
高精密轴承套圈锻造技术的应用,不仅可以提高产品的精密度和稳定性,还可以大幅降低生产成本,提高工业制造的效率和质量。
一、高精密轴承套圈锻造技术的定义和概述高精密轴承套圈锻造技术是指利用特定设备和工艺,将金属材料在一定的温度和压力下进行塑性变形,使得轴承套圈的尺寸精确、几何形状复杂、尺寸精度高、表面质量好的一种成形工艺。
在实际应用中,高精密轴承套圈锻造技术已经被广泛应用于航空、汽车、机械等领域。
二、高精密轴承套圈锻造技术的关键技术1.材料选用:高精密轴承套圈的锻造材料通常为高强度合金钢或不锈钢,具有优异的热加工性和机械性能。
2.模具设计:模具是高精密轴承套圈锻造过程中的关键设备,其设计需要考虑到产品的尺寸精度、几何形状和表面质量等因素。
3.加热控制:在轴承套圈的锻造过程中,加热温度和保温时间的控制对产品的质量起着至关重要的作用。
4.锻造工艺:通过控制锻造力和锻造速度,保证轴承套圈在锻造过程中不产生过多的内部应力和缺陷。
三、高精密轴承套圈锻造技术的应用1.航空航天领域:在航空航天领域,要求轴承套圈具有高精密度和高强度,以满足飞行器在高速飞行和复杂工作环境下的要求。
2.汽车制造领域:在汽车制造领域,高精密轴承套圈锻造技术可以大幅提高汽车轴承的使用寿命和性能稳定性,提高汽车的安全性和经济性。
3.机械制造领域:在机械制造领域,高精密轴承套圈锻造技术可以提高机械零部件的精密度和稳定性,降低生产成本,提高产品的市场竞争力。
四、高精密轴承套圈锻造技术的发展趋势随着材料科学、模具设计和加热控制技术的不断创新,高精密轴承套圈锻造技术将会在未来得到进一步的优化和提升。
随着全球工业制造的迅速发展,高精密轴承套圈锻造技术的应用领域将会越来越广泛。
五、结语高精密轴承套圈锻造技术是当前工业制造领域中一项非常重要的技术,其应用可以提高产品的制造精度和稳定性,降低生产成本,提高市场竞争力。
超精油石对轴承套圈的加工技术

超精油⽯对轴承套圈的加⼯技术轴承套圈磨超加⼯新技术及其国内外发展状况-->1.前⾔作为整个⼯业基础的机械制造业,正在朝着⾼精度、⾼效率、智能化和柔性化的⽅向发展。
磨削、超精研加⼯(简称“磨超加⼯”)往往是机械产品的终极加⼯环节,其机械加⼯的好坏直接影响到产品的质量和性能。
作为机械⼯业基础件之⼀轴承的⽣产中,套圈的磨超加⼯是决定套圈零件乃⾄整个轴承精度的主要环节,其中滚动表⾯的磨超加⼯,则⼜是影响轴承寿命以及轴承减振降噪的主要环节。
因此,历来磨超加⼯都是轴承制造技术领域的关键技术和核⼼技术。
国外轴承⼯业,60年代已形成⼀个稳定的套圈磨超加⼯⼯艺流程及基本⽅法,即:双端⾯磨削——⽆⼼外圆磨削——滚道切⼊⽆⼼磨削——滚道超精研加⼯。
除了结构特殊的轴承,需要附加若⼲⼯序外,⼤量⽣产的套圈均是按这⼀流程加⼯的。
⼏⼗年来,⼯艺流程未出现根本性的变化,但是这并不意味着轴承制造技术没有发展。
简要地说,60年代只是建⽴和发展“双端⾯——⽆⼼外圆——切⼊磨——超精研”这⼀⼯艺流程,并相应诞⽣了成系列的切⼊⽆⼼磨床和超精研机床,零件加⼯精度达到3~5um,单件加⼯时间13~18s(中⼩型尺⼨)。
70年代则主要是以应⽤60m/s⾼速磨削、控制⼒磨削技术及控制⼒磨床⼤量采⽤,以集成电路为特征的电⼦控制技术的数字控制技术被⼤量采⽤,从⽽提⾼了磨床及⼯艺的稳定性,零件加⼯精度达到1~3um,零件加⼯时间10~12s。
80年代以来,⼯艺及设备的加⼯精度已不是问题,主要发展⽅向是在稳定质量的前提下,追求更⾼的效率,调整更⽅便以及制造系统的数控化和⾃动化。
2.轴承套圈的磨削加⼯在轴承⽣产中,磨削加⼯劳动量约占总劳动量的60%,所⽤磨床数量也占全部⾦属切削机床的60%左右,磨削加⼯的成本占整个轴承成本的15%以上。
对于⾼精度轴承,磨削加⼯的这些⽐例更⼤。
另外,磨削加⼯⼜是整个加⼯过程中最复杂,对其了解⾄今仍是最不充分的⼀个环节。
滚子轴承套圈滚道凸度超精加工方法介绍
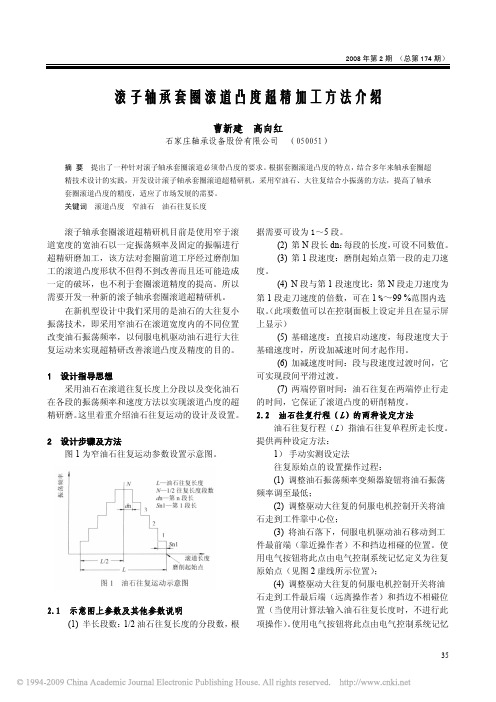
滚子轴承套圈滚道凸度超精加工方法介绍曹新建 高向红石家庄轴承设备股份有限公司 (050051)摘 要 提出了一种针对滚子轴承套圈滚道必须带凸度的要求。
根据套圈滚道凸度的特点,结合多年来轴承套圈超精技术设计的实践,开发设计滚子轴承套圈滚道超精研机,采用窄油石、大往复结合小振荡的方法,提高了轴承套圈滚道凸度的精度,适应了市场发展的需要。
关键词 滚道凸度 窄油石 油石往复长度滚子轴承套圈滚道超精研机目前是使用窄于滚道宽度的宽油石以一定振荡频率及固定的振幅进行超精研磨加工,该方法对套圈前道工序经过磨削加工的滚道凸度形状不但得不到改善而且还可能造成一定的破坏,也不利于套圈滚道精度的提高。
所以需要开发一种新的滚子轴承套圈滚道超精研机。
在新机型设计中我们采用的是油石的大往复小振荡技术,即采用窄油石在滚道宽度内的不同位置改变油石振荡频率,以伺服电机驱动油石进行大往复运动来实现超精研改善滚道凸度及精度的目的。
1 设计指导思想采用油石在滚道往复长度上分段以及变化油石在各段的振荡频率和速度方法以实现滚道凸度的超精研磨。
这里着重介绍油石往复运动的设计及设置。
2 设计步骤及方法图1为窄油石往复运动参数设置示意图。
图1 油石往复运动示意图2.1 示意图上参数及其他参数说明(1) 半长段数:1/2油石往复长度的分段数,根据需要可设为1~5段。
(2) 第段长dn :每段的长度,可设不同数值。
(3)N 第1段速度:磨削起始点第一段的走刀速度。
段与第1段速度比:第N 段走刀速度为第1速度:直接启动速度,每段速度大于基础,它可实平石往复在两端停止行走的时保长度。
提供法程:钮将油石振荡频率大往复的伺服电机控制开关将油石走服电机驱动油石移动到工件最控制开关将油石走(4) N 段走刀度的倍数,可在1 %~99 %范围内选取。
(此项数值可以在控制面板上设定并且在显示屏上显示)(5) 基础速速度时所设加减速时间才起作用。
(6) 加减速度时间:段与段速度过渡时间,现段间滑过渡。
关于深沟球轴承超精方法的探讨.doc

关于深沟球轴承超精方法的探讨浙江五洲新春集团有限公司汪燮民轴承套圈沟道的超精加工是轴承套圈加工的最后一道工序,其加工后对套圈沟道质量的改善和提高的程度将直接影响到成品轴承的最终质量,尤其是要求低噪音(甚至静音)、长寿命的轴承来说尤为重要。
深沟球轴承套圈沟道的超精目的之一,可以认为是为了使套圈沟道获得一个近乎理论上的圆环面,它包括对沟形、圆度、波纹度以及粗糙度等方面的要求。
深沟球轴承套圈沟道的超精加工方法,目前主要在用的是油石摆动的方法,国内、外各设备制造企业或轴承公司自行研发,基本都是采用这一方法。
随着科技的不断进步,设备在零件加工、装配,元器件和新技术的采用都有了突破性的更新,为轴承事业的发展做出了很大的贡献。
但无论设备怎么变化、更新,各方面技术含量的不断提高,作为最基本的工具与被加工件之间的成圆的加工运动—油石摆动成形的方法并没有改变。
本文仅想对深沟球轴承沟道超精加工设备的沟道表面成形方法进行一些探讨,在这种加工方法中,油石的摆动和沟道旋转过程中的相互作用关系,是否能使沟道表面在加工中趋近于理论上的圆环面的一部分。
一.对目前普遍使用的超精加工方法的探讨以外圈为例,如图1中的左图所示,油石绕摆头的摆动中心线摆动,CB是油石边侧的摆动面,端部截面应是圆弧线。
油石有一定的宽度,沟道在CB位置上是平行于轴平面的剖面上的交线,是非圆弧线,因此油石会在沟道中受到限制而发生干涉(见图1的右图,详见放大的图2)。
此时,不是油石研去套圈表面,就是套圈刮去油石。
因此,仅在中心剖面上,沟道与油石之间的相对运动,存在着成圆的关系(尤如车床的车刀围绕中心摆动,零件自身回转一样)。
油石在离开中心轴平面的各部分,离中心越远,干涉越大,油石边缘四角处为最大,所以从理论上讲,相互之间并不能成圆,只是在油石工作面与沟道表面互相的“谦让”中得以完成一个加工循环。
我们从几个典型的使用后的油石实样中也能很明显的看到由于干涉造成的油石表面的塌陷和缺损情况,外圈和内圈分别见图3和图4。
滚动轴承工作表面超精密加工技术研究现状
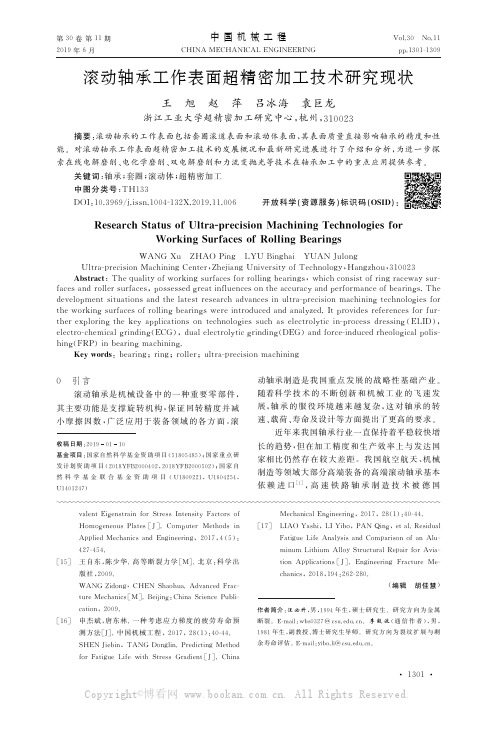
承套圈滚道的超 精 密 磨 削 技 术 来 说,目 前 最 具 有
1 套圈滚道的超精密加工技术研究现状
对于高性能滚 动 轴 承 而 言,套 圈 滚 道 在 具 有
高形状精度的同时,必须具有抗磨损、低摩擦因数
和高疲劳强度等 特 性,因 此 对 套 圈 滚 道 的 表 面 完
整性也有着极高的要求.轴承套圈滚道的传统加
y
1.
1 在线电解修整磨削方法及应用
金属结合剂超 硬 磨 料 (金 刚 石、
CBN)砂 轮 具
工工序见图 1.在套圈滚道(特别 是 内 套 圈 滚 道)
有很 高 的 强 度、硬 度 和 导 热 性,耐 磨 性 好,精 度 保
磨削加工时,砂轮易变钝及磨损,从而导致套圈滚
持性好,使用超硬 磨 料 砂 轮 磨 削 是 实 现 难 加 工 材
断裂.EGma
i
l:wbs
0327@c
su.
edu.
cn. 李 毅 波 (通 信 作 者 ),男,
1981 年生,副教授、博士研究生导 师. 研 究 方 向 为 裂 纹 扩 展 与 剩
余寿命评估.EGma
i
l:
i
bol
.
i@c
su.
edu.
cn.
y
1301
Copyright©博看网 . All Rights Reserved.
c
t
r
o
l
t
i
cg
r
i
nd
i
ng(
DEG)andf
o
r
c
e
G
i
nduc
edrheo
l
og
i
超精工艺

轴承套圈的超精加工技术简介一、概述轴承套圈经过下料、初期热处理、车削加工、中期热处理、磨削加工以后。
经过一系列严格检验后,就进入了超精加工工序。
轴承套圈超精加工主要是为了降低轴承套圈沟道或滚道的表面粗糙度,改善轴承套圈沟道或滚道的表面的应力状态。
除非上道工序对应的沟道或滚道磨削后的表面形状精度较低,轴承套圈超精加工一般不会改变加工面的形状精度和位置精度。
轴承套圈超精加工“是一种用细粒度的磨具对工件施加很小的压力,并作往复振动和慢速纵向进给运动,以实现微量磨削的一种加工方法”。
超精加工一种说法是由美国哥赖斯拉公司的维拉斯发明的,当时由于汽车车轮的滚子轴承经常产生异常的振动和噪声,问题出于轴承滚子在轴承套圈表面形成压痕所致。
经过采用软材料研磨轴承滚道表面之后,不但可以避免使轴承套圈工作表面产生压痕,而且还使得振动和噪声显著降低了。
维拉斯把这一加工方法实现了机械化,这就是最早的轴承套圈超精机。
轴承超精加工虽然发明在美国,但是现在在欧洲和日本得到进一步发展。
尤其是德国Thielenhaus公司,在轴承超精加工领域的研发技术居世界领先水平。
二、超精研加工工艺参数的选择超精研的工件旋转速度、施加于油石上的单位面积的压力、油石的振荡频率和振幅是超精研加工的主要工艺参数,这些参数的选择直接影响超精机加工工件的加工表面质量。
就加工方式来讲,一般分为采用一种油石和采用多种油石两种。
前者是采用一块油石把工作条件分为两段,称为一序两段法。
初超时,选择大的切削角,加大油石压力,就会使磨粒大量的破碎和脱落,尽可能地把前道工序的加工痕迹去掉。
前道工序的痕迹去掉后,加工表面呈梨皮形状,就得到人们称之为的超精加工的磨纹,这时就把切削角减小,降低油石压力,于是磨粒的切削作用也就降低,继续加工是把粗超时的痕迹除掉,逐渐得到平滑的加工表面,这时磨粒与加工表面的接触面积增加,进一步增加接触面积,油石就会气孔堵塞,最后致使切削完全停止,只作光超。
滚子轴承套圈滚道凸度超精加工方法介绍
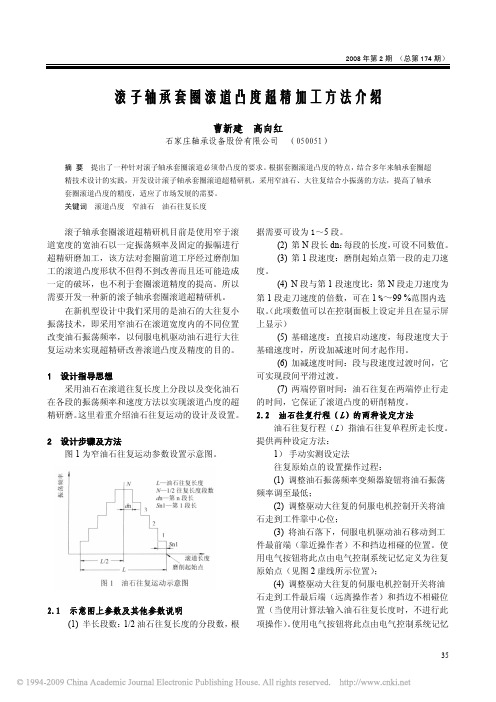
滚子轴承套圈滚道凸度超精加工方法介绍曹新建 高向红石家庄轴承设备股份有限公司 (050051)摘 要 提出了一种针对滚子轴承套圈滚道必须带凸度的要求。
根据套圈滚道凸度的特点,结合多年来轴承套圈超精技术设计的实践,开发设计滚子轴承套圈滚道超精研机,采用窄油石、大往复结合小振荡的方法,提高了轴承套圈滚道凸度的精度,适应了市场发展的需要。
关键词 滚道凸度 窄油石 油石往复长度滚子轴承套圈滚道超精研机目前是使用窄于滚道宽度的宽油石以一定振荡频率及固定的振幅进行超精研磨加工,该方法对套圈前道工序经过磨削加工的滚道凸度形状不但得不到改善而且还可能造成一定的破坏,也不利于套圈滚道精度的提高。
所以需要开发一种新的滚子轴承套圈滚道超精研机。
在新机型设计中我们采用的是油石的大往复小振荡技术,即采用窄油石在滚道宽度内的不同位置改变油石振荡频率,以伺服电机驱动油石进行大往复运动来实现超精研改善滚道凸度及精度的目的。
1 设计指导思想采用油石在滚道往复长度上分段以及变化油石在各段的振荡频率和速度方法以实现滚道凸度的超精研磨。
这里着重介绍油石往复运动的设计及设置。
2 设计步骤及方法图1为窄油石往复运动参数设置示意图。
图1 油石往复运动示意图2.1 示意图上参数及其他参数说明(1) 半长段数:1/2油石往复长度的分段数,根据需要可设为1~5段。
(2) 第段长dn :每段的长度,可设不同数值。
(3)N 第1段速度:磨削起始点第一段的走刀速度。
段与第1段速度比:第N 段走刀速度为第1速度:直接启动速度,每段速度大于基础,它可实平石往复在两端停止行走的时保长度。
提供法程:钮将油石振荡频率大往复的伺服电机控制开关将油石走服电机驱动油石移动到工件最控制开关将油石走(4) N 段走刀度的倍数,可在1 %~99 %范围内选取。
(此项数值可以在控制面板上设定并且在显示屏上显示)(5) 基础速速度时所设加减速时间才起作用。
(6) 加减速度时间:段与段速度过渡时间,现段间滑过渡。
提高滚动轴承套圈滚道和滚子精度的有序超精法

讨 和经验 ,分析 选择一种 科学获取 超精参 数的方 法—— 有序超精法进行超精加工 ,以改善超精后 的 轴承套圈滚道 ,特别是大型轴承套圈滚道 、滚子精 度 ,从而满足高精度轴承的精度和低噪声要求。
这 里 所 说 的 轴 承 套 圈 滚道 是 广 义 的 ,而 滚 子 则
圈在装配后的回转精度就不高 ,且在 高速运转时会
套 圈
有 较 大 噪 声 。而 形 成 轴承 的滚 道 、滚 子 沿 轴 线剖 面
内轮廓度在 不同圆周角度上不一致 ,以及滚道、滚
子 的 圆度值 在 轴 向各 不 同 圆截 面 上不 一 致 且形 状 不 同的 原 因 ,就 是 传 统 的 习惯 性 对轴 承 套 圈滚 道 、滚
明工 件 主轴 的 调 速范 围 、油石 振 荡 架 的往 复 频 率 范
套圈的超精转速就越小 ,越容易超坏滚道轮 廓度 。 那么 ,传统的超精方法问题 出在哪里呢?
假 如 油 石 架 的往 复 频 率 等于 工件 转 速 ,比 如 工
围和往复幅度范围 ,有的超精机是将往复和振荡分 开控制的 ,结构较复杂 ,即往 复是大幅度小频次机
生 。 因为超 精 的 线速 度相 对 是要 恒 定 在 一个 合 适 范
围内,线速度太慢会影响表面粗糙度和效率 ,但太 快又会出现表面烧伤或粘铁 ,因此 ,线速度过慢和
过 快 都 影 响超 精 质 量 。而 且 ,所超 套 圈直 径越 大 ,
超精机极其罕见。即使是数控控制 ,一般会针对振 荡头的往复运动速度和幅度进行控制 ,但超精机 的 工件主轴转速通常被认为没必要进行数控控制。国 产超精机的使用说 明书 中通常都会在规格参数栏标
目前 ,国内外生产的超精机的主轴转动通常是 采用直流或交流变频调速的 ,振 荡架的振 荡频率也
轴承套圈超精研的正交试验

白色 颗 粒 , 称 “ 精 切 削 瘤 ” 以 下 简 称 “ 削 俗 超 ( 切 瘤 ” 。经光 谱 和 电子 显 微镜 分 析 , 们 是金 属 切 ) 它 屑微 粒或 金 刚砂微粒 的烧 结物 。 由于切削瘤 的存
图 9 剥 皮状 断 口(o 5o×)
可优先选 用陶 瓷球 , 同时在耐 腐蚀 、 高温 和无磁 耐 等方面 , 陶瓷球 具有 明显优势 。
( 收稿 日期 : O —l— I 2 l I O) O
( 辑 编 张 葵)
示 为疲 劳断 I剥 落坑 一 般形 貌 , 断 V疲 劳 源 与 Z l 该 I
M a时 可获得 较好 的效果 ; P) 较差是 w C ( , W5 硬 C
4 试 验 结果
试验结 果 列 于 表 2和表 3 试验 中, 石 振 。 油
荡频率 : 超 40次/ i, 粗 5 rn 精超 30次/ i; a 5 rn 超精 研 a
时间 : 粗超 2s精超 1 。 , s
302 ) 刘 寿祥 102
原因是油 石切 削 刃钝 化 加快 , 油石 切 削 刃 与 工 件 表面摩擦 加剧 , 使切 削热 和切削 区温 度上升 , 而 进 使切 削瘤加速 形成 。因此 , 降低 油石 硬度 、 降低 油 石工作 压力 和降低 工件转速 是 消除切 削瘤 的三 大 关键 因素 。选定 油石 压力 P、 件转 速 n及油 石 工
4 结 论
通过接 触疲 劳寿 命 对 比试验 及 失 效 分 析 表 明 , 同等 接 触应 力 条 件 下 ,i d 瓷 球接 触 疲 在 s 陶 1 N 劳 寿命优 于 C r5钢球 , ,l C 且接 触 疲劳 寿命 的离 散 性与 G r5 球 接 近 , 劳 剥 落 形式 与 C r CI 钢 疲 ,l C 5钢 球相 同 , 具有 剥落 坑 , 其承载 能 力不 如 C r5 均 但 , l C 钢球 。因此在 高速 、 轻载和 冲击 载荷小 的情 况下 ,
- 1、下载文档前请自行甄别文档内容的完整性,平台不提供额外的编辑、内容补充、找答案等附加服务。
- 2、"仅部分预览"的文档,不可在线预览部分如存在完整性等问题,可反馈申请退款(可完整预览的文档不适用该条件!)。
- 3、如文档侵犯您的权益,请联系客服反馈,我们会尽快为您处理(人工客服工作时间:9:00-18:30)。
如果一个工厂只制造普通品质的轴承,比如P0级的轴承,对寿命和噪音要求不是太苛刻,用棍棒超精研是可以的,如果需要自动化程度高一些,也可以选用一些10万左右的超精研设备。假如制造P6级以上比Z3V3组更严格的轴承,选用国内高水平的超精机也是可以的。最低限度的标准是,超精研工序不能够破坏前序的磨削形状和尺寸精度。一台档次很低的超精研设备,先不要提形状的改善,先要保证不破坏前序的形状和尺寸精度。
我相信,发达国家的先进的风电轴承加工设备会逐渐走进中国风电轴承加工市场的。梯伦豪斯公司的工程师们新近研发的硬车和超精研复合车削和超精设备,是专门用于大型风电轴承加工的专用设备,计划明年推向全球市场。这种设备如果在今后的中国风电轴承生产线上应用,势必会优化中国现有的风电轴承生产工艺,同时还会给我国的风电轴承制造企业用户带来福音。购买这样一台复合硬车超精研设备大致和采购同样加工水平的一台硬车一台立磨的成本相当,由于可以在一台机床完成车削和超精工序,减少了重复安装定位误差,去掉了磨加工的热加工过程,而得到的加工表面可以达到很好的粗糙度和形状精度,发电效率最大限度的提高,轴承的长寿命的要求也可以得到保证。
前几天,有个国内很有规模的轴承集团的老板还在问我,“我们用国产超精机加工轴承套圈也能够达到要求,为什么要选用比国内超精机价格贵很多的进口产品呢?”我想,他不仅是在问我,同时他也在问他自己。这位老板还告诉我,他们建成了一个毛坯加工基地,力图在毛坯这方面技术有所突破,毛坯的问题解决了,轴承加工的其它工艺问题也大多会迎刃而解的。
轴承套圈超精研技术漫谈
那我们就从风电轴承开始谈起吧。我国是风电资源丰富的国家,在北部和西部,我们有充沛的风电潜在资源,据有关部门信息披露,我国东海,南海也有大量的风电能量资源,甚至比我国其他地区还要丰富。可能很多人还不知道,我国的风电机组的生产工艺水平还是比较落后的,表现在能源转换的效率低下,在相同资源条件下,我们要比欧美的风电机组少发很多电。相当一些业内人士都不知道,替换能源和有效的替换能源的成本上的差距,五年前开始实施的欧共体的有效的替换能源的项目现在已经付诸实施,由于采用了更先进的风电轴承生产工艺,每年多输出的电能可以供全部瑞典家庭使用一年。
最近在国内各个招标类网站经常会看到一些企业技改招标的信息。这种现象,和国家宏观调控,扩大技改资金的投放不无关系。加快企业的技术改造,积极地应对经济危机,的确是一个利国利民的好事。可是,在大量的引进国外先进技术的同时,我们应该冷静的分析一个事实,就是这些引进的设备的售后服务的问题。假如我们不充分考虑这些问题,我们的引进工作就有可能造成被动,甚至有可能失败。
还有一个问题,我们现在检测轴承的振动和噪音的方法和现在欧美的检测方法是不是一样的?如果不一样,那么,欧美的轴承是怎么样来评价轴承噪声的?有一个结论是肯定的,无论是振动的检测还是噪声的检测,最科学的数据应该是和轴承的工作状态最接近的数据。
最后一个问题,轴承在工作时,因为一般深沟球轴承都是有间隙的,所以理论上的纯滚动状态是不存在的,钢球在套圈里一定不是沿着理想的圆轨迹旋转的,而是会沿着特定的偏离角扰动的。最新的研究成果表明,轴承套圈的超精后的纹路的偏角应该尽可能的接近钢球在套圈里扰动的角度,这个结果出来的轴承的噪音和寿命的数据是最科学的。我们可以推断,只有在0间隙情况下,钢球沿着理想的圆形轨迹旋转时,直丝路的轴承的噪音和寿命的数据才是最好的。
我国在合理的有效的使用清洁能源方面的工作,还没有排上议事日程,这个从我国大上风电设备的热潮之中就可以窥见一斑。落后的风电机组生产工艺决定了落后的对相关零部件的技术要求,风电轴承采用诸如硬车,采用精细加工,采用新的超精研技术,几乎没有动作。大量的低档次的热处理设备,低档的龙门铣床、刨床和车床充斥着我国的风电机组零件加工现场,我国的大型风电轴承基本上没有采用超精研工艺。我们的相当一部分风电设备和风电轴承专家还在认为,风电轴承转速很低,采用大型超精研设备会过多的增加生产成本,在现阶段,那种国外的加工工艺不适合中国国情。
上一篇我们讲到,为了提高轴承的寿命,降低轴承的噪音,轴承套圈沟道表面超精研是必须的。很多轴承产品现在不超精,二次世界大战前的轴承套圈大多也不超精,轴承零件超精研工艺起源于二次世界大战中期,有了军方对机械系统的可靠性、稳定性和安全性的更高的要求,才有了超精技术的进步和发展。
曾几何时,我原来工作过的工厂也生产过那种最原始的棍棒超精机,当时我们的认识非常肤浅,认为有了超精研设备,会使轴承表面的光洁度增加,减少摩擦系数,进而可以提高轴承寿命。经过十多年的研究和学习,我们才认识到,当时设计棍棒超精机的时候,从研发超精研设备伊始,对超精研原理的认识就有局限性。有了这种局限性,就不可能研制出高品质的超精研设备来。几年前,我到过浙江慈溪一个轴承工厂,那个老板就亲口跟我讲,他就是喜欢用棍棒超精机,不单单是因为棍棒超精机价格便宜,而且还是因为他看到的那些自动轴承超精机无论效率还是粗糙度都没有棍棒超精机的效果好,他没有找到买自动轴承超精机的理由。
无论是大型轴承还是小型轴承的生产,对轴承品质的要求都是大同小异的。一个是降低噪音,一个是提高轴承寿命。轴承精度寿命的不稳定会造成大量的维护费用,这种维护和更换大型轴承的费用要比购买这些轴承的费用高几倍。我们是发展中国家,在生产风电轴承方面,很多人还是发展中国家的意识,这种落后的设计思维造成了我国新能源领域的大面积的资源浪费。前一阶段,我一直在沿海地区出差,看到很多风电机组形同虚设,在渤海东海岸,某个地区风电机组开机率还不足50%,这是需要有关部门反省和深思的。发达国家的风电轴承加工工艺,我们还是要静下心来学习的,要从最基层的制造工艺开始学起。
如果,我们的轴承加工企业,要生产出更高水平的产品,在安全性、可靠性和批量加工的工艺能力方面有效地替代进口产品,假如我们立志要走出国门,参与国际市场高品质轴承的竞争,就一定要学习世界上最先进的轴承加工工艺。最先进的轴承加工工艺,就是最稳定的最可靠的最安全的工艺。学习最先进的轴承加工工艺就一定要选用世界上最先进的设备。在进行企业的技术改造方面,采购进口设备至今仍然是不二的选择,因为我国现阶段生产的轴承设备,特别是轴承超精研设备和国外的制造水平差距很大,在批量稳定的加工P5级以上精密轴承的工艺能力方面很弱。如果说,我们可以用中低档次的超精研设备,用传统的轴承生产线,可以加工出替代进口的高精度轴承产品,在现阶段,这只是一个美好的愿望而已。
我们曾经不止一次的讨论过,“轴承套圈为什么要进行超精研?”实际上,在二次世界大战以前,世界上的大多数滚动轴承生产线是没有超精工序的。后来,军队在实战中发现,滚动轴承沟道经过抛光之后,会显著的提高寿命,会满足更安全、更可靠的战术要求。经过五六十年的轴承加工工艺实践,轴承工艺专家们发现,轴承沟道经过超精加工,不仅可以显著的提高轴承产品的寿命,而且还会降低工作噪音,大幅度的提高轴承的承载能力,增加机械系统的运转效率。超精加工首先会降低轴承滚道的粗糙度,会去掉磨削工序热加工形成的变质层,会把磨削工序形成的拉应力变成压应力,会有条件的改善轴承沟道的形状。如果,一套轴承不需要提高寿命,不需要降低噪音,不需要有很高的精度,可以不采用超精研工序,也可以采用棍棒超精研,可以选用价格比较低的超精机,这样成本会更低。
以引进国外的超精机为例,我们需要提醒大家的是,正是因为我们国内的超精研设备水平很低,所以需要引进这些技术,可是国内引进超精研设备不成功的先例还是有的。我曾经在国内一个大型轴承企业看到日本的几台超精研设备闲置在车间,据一个四十岁左右的车间基层人员反映,从他参加工作到现在,这几台设备从新到旧,一直没有正常使用过。我曾经在宁波地区看到一家企业,也引进了这家日本企业的超精机,经过一段时间的试加工,基本上没有达到合同要求,造成了退货的现象。另一家使用过这家日本企业的超精机的老板也在经常和我抱怨,在大多国内轴承企业的传统工艺条件下,进口的超精研设备不一定使用的非常理想。
下一篇,我们会详细分析我国的超精研设备和国外最先进的超精研设备的差距在哪里。请大家继续看《轴承套圈超精研技术漫谈 4》。
超精加工后的沟道表面的纹路什么角度最好?
这是很多低噪音轴承研究人员经常询问的一个问题。经过长期的振动和噪声仪器检测实践,我们现在已经得出了结论,直丝路的沟道获得的数据比较好。我们剖分过很多日本的轴承,在显微镜下看出的也都是直丝路。但是,欧美的轴承却是各种丝路的都有,比较纷杂。德国工程师对我国轴承企业过于强调超精的直丝路很不以为然。有一个理论应该引起我们的重视,沟道表面的丝路夹角偏角和轴承的寿命有关,直丝路肯定不是寿命最高的微观形态。
那么,现在我们可以清楚的告诉这个浙江轴承厂的老板,选用什么档次的超精研设备取决与你制造什么品质的轴承产品,当你生产的品质还能够被市场忍受的时候,的确不需要花那么多钱买高水平的超精机,甚至你根本用不着超精研设备,你还可以用更便宜的材料,不需要热处理,不需要很好的检测设备,也可以制造出轴承来。理由是,轴承产品是由市场需要决定的。
后一种情况是理想状态,我们现在轴承生产检测的测试方法也基于理想状态,而在工业生产过程中,任何理想状态获得的数据只有参考价值。假如没有更先进的符合工作状态数据的检测方法,那我们只有采用具有参考价值的数据来间接地评定轴承零件的超精加工结果。而干扰是客观存在的,很多噪声是需要经过分析一些有规律的干扰和偶然性的干扰来处理的,这就给高水平的超精机超精实验提供了更加符合现场实践的分析依据。
一般来说,欧美企业的超精研设备出现的问题相对少一些,主要还是因为,在售前,欧美企业一般会详细的了解用户的使用工况和工艺条件,对一些不合理的工艺问题会针对性的提出整改意见,以至于避免发生设备和加工工艺不配套的矛盾。