影响电镀镀层质量的因素——镀液的性能
电镀质量六大影响因素

电镀质量六大影响因素影响电镀质量的因素很多,包括镀液的各种成分以及各种电镀工艺参数,下面讨论其中的主要因素。
(l) pH值的影响镀液中的pH值影响氢的放电电位、碱性夹杂物的沉淀,还影响络合物或水化物的组成以及添加剂的吸附程度。
但是,对各种因素的影响程度一般不可预见。
最佳的pH值往往要通过试验决定。
在含有络合剂离子的镀液中,pH值可能影响存在的各种络合物的平衡,因而必须根据浓度来考虑。
电镀过程中,若pH值增大,则阴极效率比阳极效率高,pH值减小则反之。
通过加入适当的缓冲剂可以将pH值稳定在一定的范围。
(2)添加剂的影响镀液中的光亮剂、整平剂、润湿剂等添加剂能明显改善镀层组织。
这些添加剂有无机和有机之分,无机添加剂在电解液中形成高分散度的氢氧化物或硫化物胶体,吸附在阴极表面阻碍金属析出,提高阴极极化作用。
有机添加剂多为表面活性物质,它们会吸附在阴极表面形成一层吸附膜,阻碍金属析出,因而提高阴极极化作用。
另外,某些有机添加剂在电解液中形成胶体,会与金属离子络合形成胶体一金属离子型络合物,阻碍金属离子放电而提高阴极极化作用。
(3)电流密度的影响任何电镀液都必须有一个能产生正常镀层的电流密度范围。
当电流密度过低时,阴极极化作用较小,镀层结晶粗大,甚至没有镀层。
随着电流密度的增加,阴极极化作用也随着增加,镀层晶粒越来越细。
当电流密度过高,超过极限电流密度时,镀层质量开始恶化,甚至出现海绵体、枝晶状、“烧焦”及发黑等。
电流密度的上限和下限是由电镀液的本性、浓度、温度和搅拌等因素决定的。
一般情况下,主盐浓度增大,镀液温度升高,以及有搅拌的条件下,可以允许采用较大的电流密度。
(4)电流波形的影响电流波形的影响是通过阴极电位和电流密度的变化来影响阴极沉积过程的,它进而影响镀层的组织结构甚至成分,使镀层性能和外观发生变化。
实践证明,三相全波整流和稳压直流相当,对镀层组织几乎没有什么影响,而其他波形则影响较大。
例如,单相半波会使镀铬层产生无光泽的黑灰色;单相全波会使焦磷酸盐镀铜及铜锡合金镀层光亮。
年度电镀质量异常总结(3篇)

第1篇一、前言随着我国电子产业的快速发展,电镀工艺在电子产品制造中的应用越来越广泛。
然而,在电镀过程中,由于各种原因,质量异常问题时有发生,给企业带来了巨大的经济损失和信誉风险。
为了提高电镀质量,降低质量异常发生率,本文对2021年度电镀质量异常情况进行总结,分析原因,并提出改进措施。
二、2021年度电镀质量异常情况概述1. 异常类型2021年度电镀质量异常主要包括以下几种类型:(1)外观缺陷:如氧化、腐蚀、起泡、脱皮、露底等。
(2)电镀层厚度不足:导致防护性能降低,易受腐蚀。
(3)电镀层结合力差:导致涂层脱落,影响产品使用寿命。
(4)电镀液稳定性差:导致电镀层质量不稳定,影响产品一致性。
2. 异常原因(1)原辅材料质量:原辅材料质量不合格是导致电镀质量异常的主要原因之一。
如:电镀液成分不稳定、添加剂含量不足等。
(2)设备故障:设备老化、维护不当或操作失误等原因导致设备故障,进而影响电镀质量。
(3)工艺参数控制:工艺参数设置不合理、温度、电流、时间等参数控制不准确,导致电镀层质量不稳定。
(4)环境因素:温度、湿度、灰尘等环境因素对电镀质量有较大影响。
三、2021年度电镀质量异常原因分析及改进措施1. 原辅材料质量(1)原因分析:原辅材料质量不稳定,如电镀液成分波动、添加剂含量不足等。
(2)改进措施:加强原辅材料供应商的管理,严格检验标准,确保原辅材料质量。
2. 设备故障(1)原因分析:设备老化、维护不当或操作失误等原因导致设备故障。
(2)改进措施:加强设备维护保养,定期进行设备检查,提高操作人员技能水平。
3. 工艺参数控制(1)原因分析:工艺参数设置不合理、温度、电流、时间等参数控制不准确。
(2)改进措施:优化工艺参数,制定详细的操作规程,加强工艺参数的监控。
4. 环境因素(1)原因分析:温度、湿度、灰尘等环境因素对电镀质量有较大影响。
(2)改进措施:加强车间环境管理,保持车间温度、湿度稳定,控制灰尘等污染源。
{品质管理品质培训}镀液性能与镀层质量检验培训
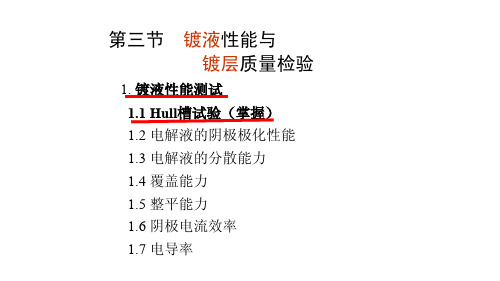
第三节 镀液性能与镀层质量检验1. 镀液性能测试1.1 Hull槽试验(掌握)1.2 电解液的阴极极化性能1.3 电解液的分散能力1.4 覆盖能力1.5 整平能力1.6 阴极电流效率1.7 电导率什么是Hull 槽ABCDab cd ABCD e-+267mL 槽的几何尺寸:a = 48mm ,b = 64mm ,c = 102mm , d = 127mm ,e = 65mm横截面Hull 槽是一种小型电镀试验装置,简便而又迅速地进行多种电镀试验。
Hull 槽的横截面为梯形,故又称为梯形槽。
Hull 槽的容积有两种:267mL 和1000mL ,前者应用较广泛。
国内应用时在 267mL 容积中盛 250mL 电解液。
Hull 槽的特点Hull 槽最大特点:阴极上各部位到阳极的距离不相同(逐渐变化的)。
造成阴极上各部位的电流密度不相等,同时是逐渐变化的。
在阴极上离阳极最远的一端(远端,图中D )电流密度最小, 最近的一端(近端,图中B )电流密度最大。
阴极上电流密度分布公式:i c = I(C 1 - C 2log 10l )式中: l ----阴极上某点到近端的距离(单位:cm),i c ----该点的电流密度(单位:A/dm 2)。
I----通过Hull 槽的试验电流 (单位:A),阴极ABD阳极C对267mL槽(250mL电解液),用4 种常用电解液(酸性镀铜,酸性镀镍,氰化镀镉,氰化镀锌)实验并取平均结果,得出C1 = 5.1019 C2 = 5.2401应用上面公式时,还乘267/250因子,才能得出正确i c。
另外,l 适用范围0.635~8.255 cm。
为使用方便,可将计算值列成表。
250mL Hull槽阴极上的电流密度分布(A/dm2)文献中关于常数C1、C2的测量值互有差异用267mL Hull槽,对11种镀液(4种镀锌、2种镀镍、3种镀铜、2种镀仿金) 测量。
使用线性回归法,得平均值Hull 槽试验中阴极上的电流密度变化范围很宽,近端和远端的电流密度相差50多倍。
电镀铜实验报告
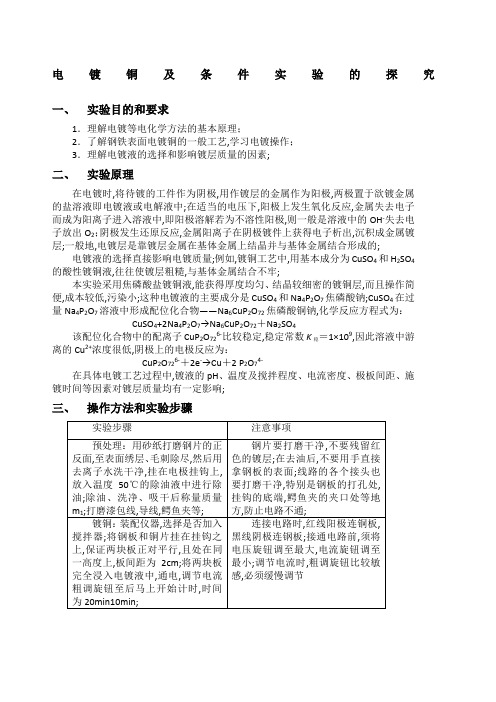
电镀铜及条件实验的探究一、实验目的和要求1.理解电镀等电化学方法的基本原理;2.了解钢铁表面电镀铜的一般工艺,学习电镀操作;3.理解电镀液的选择和影响镀层质量的因素;二、实验原理在电镀时,将待镀的工件作为阴极,用作镀层的金属作为阳极,两极置于欲镀金属的盐溶液即电镀液或电解液中;在适当的电压下,阳极上发生氧化反应,金属失去电子而成为阳离子进入溶液中,即阳极溶解若为不溶性阳极,则一般是溶液中的OH-失去电子放出O2;阴极发生还原反应,金属阳离子在阴极镀件上获得电子析出,沉积成金属镀层;一般地,电镀层是靠镀层金属在基体金属上结晶并与基体金属结合形成的;电镀液的选择直接影响电镀质量;例如,镀铜工艺中,用基本成分为CuSO4和H2SO4的酸性镀铜液,往往使镀层粗糙,与基体金属结合不牢;本实验采用焦磷酸盐镀铜液,能获得厚度均匀、结晶较细密的镀铜层,而且操作简便,成本较低,污染小;这种电镀液的主要成分是CuSO4和Na4P2O7焦磷酸钠;CuSO4在过量Na4P2O7溶液中形成配位化合物——Na6CuP2O72焦磷酸铜钠,化学反应方程式为:CuSO4+2Na4P2O7→Na6CuP2O72+Na2SO4该配位化合物中的配离子CuP2O726-比较稳定,稳定常数K稳=1×109,因此溶液中游离的Cu2+浓度很低,阴极上的电极反应为:CuP2O726-+2e-→Cu+2 P2O74-在具体电镀工艺过程中,镀液的pH、温度及搅拌程度、电流密度、极板间距、施镀时间等因素对镀层质量均有一定影响;三、操作方法和实验步骤四、数据记录与处理五、实验结果分析先分析是否搅拌这个自变量,在20min情况下,是否搅拌对镀层厚度的影响不大;估计是长时间电镀后,镀层覆盖到一定程度,不再覆盖,从镀层均匀度来看,搅拌的镀层更均匀;10min 的情况下,不搅拌的镀层厚度搅拌的镀层更厚,估计是4号钢片表面积更大,易于镀铜的关系;4组数据也说明了搅拌对镀层厚度影响不大,但是从镀层观察结果来看,搅拌后的镀层更均匀光亮;再来看时间这个自变量,4组实验总库伦量相等,20min的镀层厚度明显比10min的大,而且镀层也更均匀;六、心得顾佳辉:通过这次试验,我理解了电镀等电化学方法的基本原理,了解了钢铁表面电镀铜的一般工艺,学习电镀操作,明白了电镀液的选择和影响镀层质量的因素;准备阶段方面,对碳钢片的预处理很重要,用砂纸打磨钢片的正反面,至表面绣层、毛刺除尽,然后用去离子水洗干净,这几步我们做的很仔细;在板间距的控制上,我们在搅拌过程中很难保持每个部位都是相距2cm,只能保证中线相距2cm;另外镀层结束后对镀层观察方面,对于均匀度这样的特性,我们只能通过肉眼观察,难免有较大误差,最好可以用专门的仪器来判定;此实验通过控制变量的方法,研究单一变量对电镀效果的影响;在实验过程中,我认为有两点需要改进的地方;其一是该实验作为分析实验,需要数据的精确性,但是因为本实验中质量差最大为,只精确到的数据不足以显示出其变量改变后对镀层厚度的影响,应该使用更高精度的测重仪器;同时镀铜过程实际镀层覆盖六个表面积,但是计算过程只考虑了两个,也会造成误差;其二是四次实验分两组由不同的操作者在不同的仪器上完成,尽管电镀液混合过,但是仪器本身有所差别,操作者也有差别,会导致实验数据不准;综上,本次试验结论有待考究,结合以上两点改进后实验数据会更加精确;万舜:这次“电镀铜及条件实验的探究”实验;实验的原理我们在化学课程中早已学习过,但是在实际的电镀工业中,考虑到镀层的光滑程度以及牢固度,所以我们选用的不是基本成分为CuSO4和H2SO4的酸性镀铜液,而是焦磷酸盐镀铜液,这样能获得厚度均匀、结晶较细密的镀铜层;在实验操作方面,预处理阶段非常关键,直接关乎到整个实验的成功与否;所以打磨,清洗,去油等处理都需要很细心的去做;由于我们是要探讨不同条件下电镀的效果差异,所以我们需要与另一个小组保持其余条件的一致,所以电镀液需要实现进行混合平分;在电镀过程中,由于需要将钢板和铜片完全浸没在电镀液中,所以我们无法观察到电镀过程中的每一个变化;而且我们的比较的变量中有一个是是否搅拌,所以为了让数据更我说服力,我们最好是和另一个组同步搅拌速率;最后称重,计算镀层厚度时,我们所做的两个数据结果非常接近,而另一组的结果相差则比较大;我觉的最终的原因应该是空气天平的灵敏度不够,达不到实验的精度要求,这一点在我们称量镀铜后的钢板质量时就可以发现了,两次质量差仅有或,质量产生的误差可能就达到了50%;再就是我们计算钢板表面积时,只计算了上下两个表面,没有加上侧面积,也没有减去打孔的面积,但是表面积引起的相对误差较小;最后观察镀层时,虽然正反两面差距都不大,但是仍可以观察到,搅拌过的那组两面的镀层均匀程度更接近;这个实验不但让我直接了解并操作了电镀铜的工序,也让我重温了电路的连接,更重要的是可以探究不同条件下对镀层质量的影响;。
应用电化学习题复习及答案
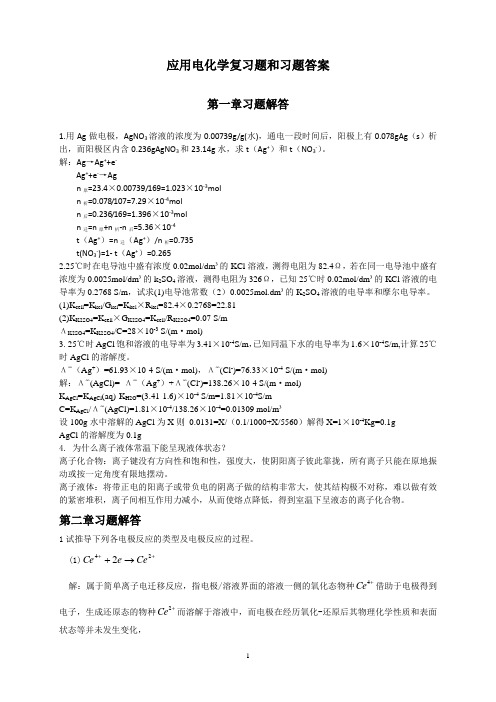
应用电化学复习题和习题答案第一章习题解答1.用Ag 做电极,AgNO 3溶液的浓度为0.00739g/g(水),通电一段时间后,阳极上有0.078gAg (s )析出,而阳极区内含0.236gAgNO 3和23.14g 水,求t (Ag +)和t (NO 3-)。
解:Ag →Ag ++e -Ag ++e -→Agn 原=23.4×0.00739/169=1.023×10-3mol n 析=0.078/107=7.29×10-4mol n 后=0.236/169=1.396×10-3mol n 迁=n 原+n 析-n 后=5.36×10-4t (Ag +)=n 迁(Ag +)/n 析=0.735 t(NO 3-)=1- t (Ag +)=0.2652.25℃时在电导池中盛有浓度0.02mol/dm ³的KCl 溶液,测得电阻为82.4Ω,若在同一电导池中盛有浓度为0.0025mol/dm ³的k 2SO 4溶液,测得电阻为326Ω,已知25℃时0.02mol/dm ³的KCl 溶液的电导率为0.2768 S/m ,试求(1)电导池常数(2)0.0025mol.dm ³的K 2SO 4溶液的电导率和摩尔电导率。
(1)K cell =K kcl /G kcl =K kcl ×R kcl =82.4×0.2768=22.81 (2)K K2SO4=K cell ×G K2SO4=K cell /R K2SO4=0.07 S/m ΛK2SO4=K K2SO4/C=28×10-3 S/(m ·mol)3. 25℃时AgCl 饱和溶液的电导率为3.41×10-4S/m ,已知同温下水的电导率为1.6×10-4S/m,计算25℃时AgCl 的溶解度。
影响电镀层质量的因素及生产中注意事项

影响电镀层质量的因素及生产中注意事项摘要:介绍了影响电镀层质量的物理、化学及人为三大影响因素,物理因素主要为镀件材料、形状及表面状态等;化学因素主要为化工材料及配液用水等。
论述了电镀工艺中挂具、阳极、设备及包装对镀房质量的影响,并针对这些质量影响因素在生产过程中应注意的事项进行了详细阐述。
关键词:镀层质量;影响因素;注意事项引言电镀过程中影响电镀层质量的因素较多且复杂,但总的可以归结为物理的、化学的和人为的三种影响因素,在生产过程中,对这三种影响因素加以控制和注意,就会获得满意的、稳定的镀层质量。
一、物理因素影响电镀层质量的物理因素主要有受镀零件、挂具、装挂方式、阳极、设备、包装及贮存环境等。
1受镀零件受镀零件基体材料、形状大小、表面质量对电镀层的影响非常大,这是不容忽视的。
1.1基体材料在设计产品零件时,如该零件需要镀覆,设计者应充分考虑零件材料的镀覆性,当合金中非主成分的铜、铝及镁等金属总含量超过指标时,其表面就很难获得合格的镀覆层;另外,有些采用不符合标准或劣质原材料加工零部件,当加工零部件材料中的铅、锡或镉等金属杂质含量超过一定量时,也难以在零部件表面获得优质的镀覆层。
针对基体材料影响因素应注意以下几点:1〉设计者在选择零部件材料时,除考虑材料在产品中的性能外,还应考虑表面处理对材料的选择性。
2〉应选择符合标准要求的材料加工零部件。
1.2形状对于电镀来说,产品零件的几何形状是不确定的,是变动量最大的物理因素,也是决定电镀加工难易程度的重要因素。
零件形状越复杂,电镀难度系数就越大,对于外形复杂的零件,在进行电镀加工时,突起的部位会因电流过大而烧焦,而低凹部位又因电流过小而镀层很薄或根本镀不上镀层,即便是简单的平板零件,如不采取保护措施,也会使平板四周镀层较厚,而中心部位镀层厚度较薄。
针对形状大小影响因素应注意以下几点:1〉镀覆形状复杂的零件时,应尽可能选取分散能力好的镀液。
2〉根据零件形状选择合适的挂具及装挂方式,避免窝气、尖端放电或深孔无镀层等疵病的产生。
《应用电化学》复习思考题参考答案
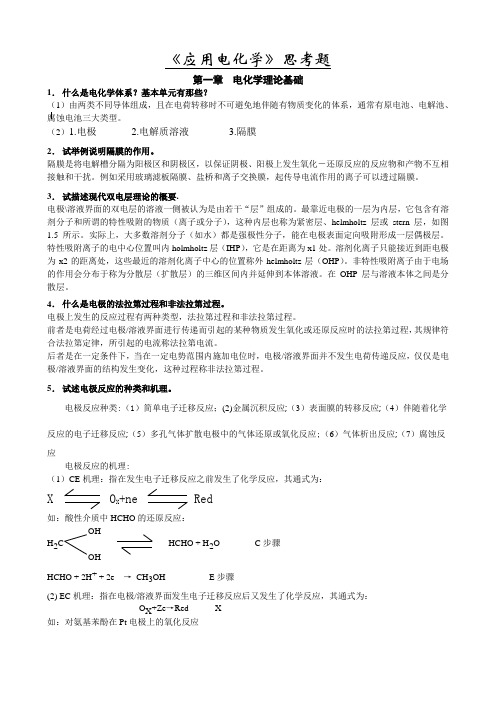
《应用电化学》思考题第一章电化学理论基础1.什么是电化学体系?基本单元有那些?(1)由两类不同导体组成,且在电荷转移时不可避免地伴随有物质变化的体系,通常有原电池、电解池、腐蚀电池三大类型。
(2)1.电极 2.电解质溶液 3.隔膜2.试举例说明隔膜的作用。
隔膜是将电解槽分隔为阳极区和阴极区,以保证阴极、阳极上发生氧化-还原反应的反应物和产物不互相接触和干扰。
例如采用玻璃滤板隔膜、盐桥和离子交换膜,起传导电流作用的离子可以透过隔膜。
3.试描述现代双电层理论的概要.电极\溶液界面的双电层的溶液一侧被认为是由若干“层”组成的。
最靠近电极的一层为内层,它包含有溶剂分子和所谓的特性吸附的物质(离子或分子),这种内层也称为紧密层、helmholtz层或stern层,如图1.5所示。
实际上,大多数溶剂分子(如水)都是强极性分子,能在电极表面定向吸附形成一层偶极层。
特性吸附离子的电中心位置叫内holmholtz层(IHP),它是在距离为x1处。
溶剂化离子只能接近到距电极为x2的距离处,这些最近的溶剂化离子中心的位置称外helmholtz层(OHP)。
非特性吸附离子由于电场的作用会分布于称为分散层(扩散层)的三维区间内并延伸到本体溶液。
在OHP层与溶液本体之间是分散层。
4.什么是电极的法拉第过程和非法拉第过程。
电极上发生的反应过程有两种类型,法拉第过程和非法拉第过程。
前者是电荷经过电极/溶液界面进行传递而引起的某种物质发生氧化或还原反应时的法拉第过程,其规律符合法拉第定律,所引起的电流称法拉第电流。
后者是在一定条件下,当在一定电势范围内施加电位时,电极/溶液界面并不发生电荷传递反应,仅仅是电极/溶液界面的结构发生变化,这种过程称非法拉第过程。
5.试述电极反应的种类和机理。
电极反应种类:(1)简单电子迁移反应;(2)金属沉积反应;(3)表面膜的转移反应;(4)伴随着化学反应的电子迁移反应;(5)多孔气体扩散电极中的气体还原或氧化反应;(6)气体析出反应;(7)腐蚀反应电极反应的机理:(1)CE机理:指在发生电子迁移反应之前发生了化学反应,其通式为:X O X+ne RedH2HCHO + H2O C步骤HCHO + 2H+ + 2e →CH3OH E步骤(2) EC机理:指在电极/溶液界面发生电子迁移反应后又发生了化学反应,其通式为:O X+Ze→Red X如:对氨基苯酚在Pt电极上的氧化反应(3)催化机理a、“外壳层”催化:EC机理中的一种,指在电极和溶液之间的电子传递反应,通过电极表面物种氧化—还原的媒介作用,使反应在比裸电极低的超电势下发生,其通式可表示如下:X + ne Red E步骤X + Y C步骤如:Fe3+/Fe2+电对催化H2O2的还原反应:1/2H2O2+e→OH-3+2+Fe+ 1/2H2O2→Fe3++ OH-b、“内壳层”催化:也称为化学氧化—还原催化,即当反应物的总电化学反应中包括旧键的断裂和新键的形成时,发生在电子转移步骤的前、后或其中而产生了某种化学加成物或某些其它的电活性中间体,总的活化能会被某些“化学的”氧化—还原催化剂所降低。
化学镀镍镀层质量影响因素的分析
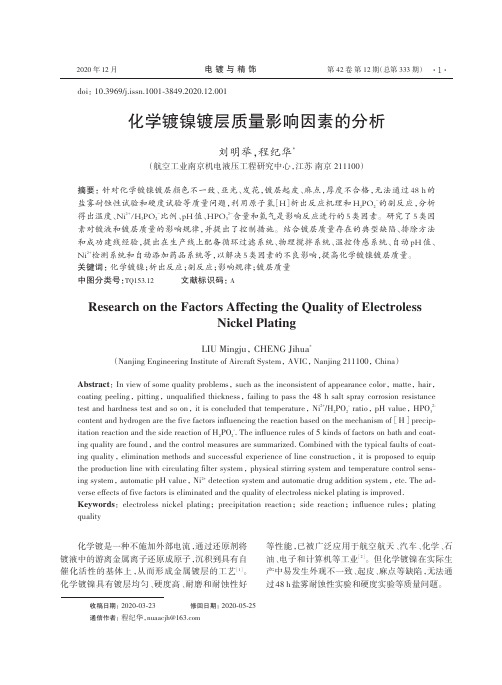
化学镀镍镀层质量影响因素的分析刘明举,程纪华*(航空工业南京机电液压工程研究中心,江苏南京211100)摘要:针对化学镀镍镀层颜色不一致、亚光、发花,镀层起皮、麻点,厚度不合格,无法通过48h的盐雾耐蚀性试验和硬度试验等质量问题,利用原子氢[H]析出反应机理和H2PO2-的副反应,分析得出温度、Ni2+/H2PO2-比例、pH值、HPO32-含量和氢气是影响反应进行的5类因素。
研究了5类因素对镀液和镀层质量的影响规律,并提出了控制措施。
结合镀层质量存在的典型缺陷、排除方法和成功建线经验,提出在生产线上配备循环过滤系统、物理搅拌系统、温控传感系统、自动pH值、Ni2+检测系统和自动添加药品系统等,以解决5类因素的不良影响,提高化学镀镍镀层质量。
关键词:化学镀镍;析出反应;副反应;影响规律;镀层质量中图分类号:TQ153.12文献标识码:AResearch on the Factors Affecting the Quality of ElectrolessNickel PlatingLIU Mingju,CHENG Jihua*(Nanjing Engineering Institute of Aircraft System,AVIC,Nanjing211100,China)Abstract:In view of some quality problems,such as the inconsistent of appearance color,matte,hair,coating peeling,pitting,unqualified thickness,failing to pass the48h salt spray corrosion resistance test and hardness test and so on,it is concluded that temperature,Ni2+/H2PO2-ratio,pH value,HPO32-content and hydrogen are the five factors influencing the reaction based on the mechanism of[H]precip⁃itation reaction and the side reaction of H2PO2-.The influence rules of5kinds of factors on bath and coat⁃ing quality are found,and the control measures are bined with the typical faults of coat⁃ing quality,elimination methods and successful experience of line construction,it is proposed to equip the production line with circulating filter system,physical stirring system and temperature control sens⁃ing system,automatic pH value,Ni2+detection system and automatic drug addition system,etc.The ad⁃verse effects of five factors is eliminated and the quality of electroless nickel plating is improved. Keywords:electroless nickel plating;precipitation reaction;side reaction;influence rules;plating quality化学镀是一种不施加外部电流,通过还原剂将镀液中的游离金属离子还原成原子,沉积到具有自催化活性的基体上,从而形成金属镀层的工艺[1]。
影响镀层厚度分布均匀性的因素:镀液性能因素-阴极上的电流分布

影响镀层厚度分布均匀性的因素:镀液性能因素-阴极上的电流分布当只考虑几何因素对阴极电流分布的影响时,称为“一次电流分布”;若同时考虑电化学因素的影响,则称为“二次电流分布”。
电流分布不等于金属分布,因为后者还与不同阴极电流密度时的电流效率有关。
在此,先讨论二次电流分布的影响因素,即不考虑阴极电流效率影响的问题。
显然,此时工件上的阴极电流密度分布越均匀,则镀层厚度分布越均匀。
2.2.1 几个概念2.2.1.1 远阴极与近阴极将一个工件装挂于阴极杆上,同一个阴极工件的不同部位到阳极的距离不可能完全相同(与工件装挂方式及其本身形状和复杂程度有关)。
离阳极最近的一点(或线、面)称为“近阴极”,其与阳极的距离以k表示;离阳极最远的一点(或线、面)称为“远阴极”,其与阳极的距离用,抚表示。
2.2.1.2 远近阴极距离差远、近阴极与阳极距离之差,称为远近阴极距离差,以△l表示,则△l=l 远—l近。
2.2.1.3 镀液的电导率镀液为正负离子导电,是第二类导体,它也存在电阻。
镀液单位体积(边长为 1 cm的正方体,即l cm3)的电阻称为镀液的电阻率,以p表示。
电阻的倒数称为电导,电阻率的倒数二则为电导率,单位为“西门子/厘米”(S/cm)。
电流通过电阻时会产生电压降。
平时所说的“槽电压”就是电流通过镀液、阴极杆与挂具、挂具与工件及阳极相关部分总串联电阻的电压降。
镀液的电导率越高,则槽电压越低。
整流器的输出电压要高于槽电压,其差值则为汇流排、汇流排与阴阳极杆接触电阻、汇流排与整流器输出板接触电阻等“外电阻”的电压降。
若汇流排(或软线)面积过小、接头太多或接头接触不良,外电路上发热量大,直流损耗也就大。
当阴阳极杆的截面积过小时,也有压降损失,两个端头测得的槽电压会有差别。
将直流回路上的电压损失尽量降低,是必要的节能措施。
滚镀时,浸入镀液中滚筒孔眼的总表面积为镀液的导电面积。
若滚桶孔眼过小、开孔率过低,该值则很小,槽电压很高,槽液发热快,甚至整流器开至最大,电流也上不去。
2023-2024学年高二化学人教版2019选择性必修1试题实验07简单的电镀实验
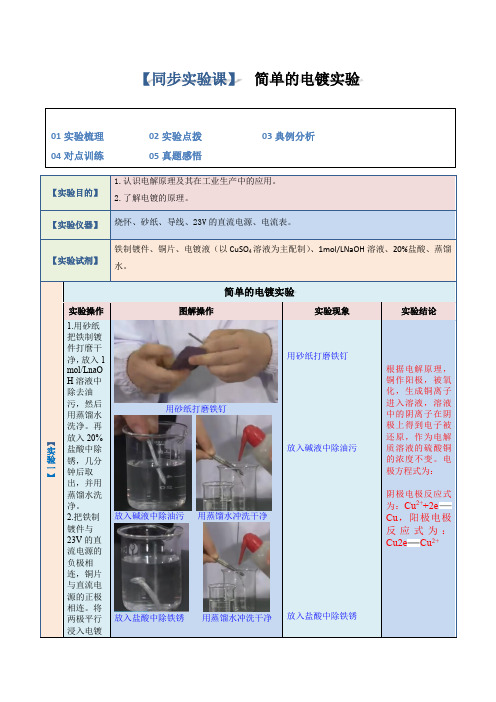
【同步实验课】简单的电镀实验【实验目的】1.认识电解原理及其在工业生产中的应用。
2.了解电镀的原理。
【实验仪器】烧怀、砂纸、导线、23V的直流电源、电流表。
【实验试剂】铁制镀件、铜片、电镀液(以CuSO4溶液为主配制)、1mol/LNaOH溶液、20%盐酸、蒸馏水。
【实验一】简单的电镀实验实验操作图解操作实验现象实验结论1.用砂纸把铁制镀件打麿干净,放入1mol/LnaOH溶液中除去油污,然后用蒸馏水洗净。
再放入20%盐酸中除锈,几分钟后取出,并用蒸馏水洗净。
2.把铁制镀件与23V的直流电源的负极相连,铜片与直流电源的正极相连。
将两极平行浸入电镀用砂纸打磨铁钉放入碱液中除油污用蒸馏水冲洗干净放入盐酸中除铁锈用蒸馏水冲洗干净用砂纸打磨铁钉放入碱液中除油污放入盐酸中除铁锈根据电解原理,铜作阳极,被氧化,生成铜离子进入溶液,溶液中的阴离子在阴极上得到电子被还原,作为电解质溶液的硫酸铜的浓度不变。
电极方程式为:阴极电极反应式为:Cu2++2eCu,阳极电极反应式为:Cu2e Cu2+01实验梳理02实验点拨03典例分析04对点训练05真题感悟连接好装置,进行电镀铁钉上附着了红色的铜(一)问题与讨论:1.若用如图所示装置,模拟铁制品上镀铜,则电解质溶液c、电极a、电极b的电极材料分别是什么?电镀过程中电解质溶液的浓度如何变化?【解析】若用如图所示装置,模拟铁制品上镀铜,则电极a是Cu,电极b是铁制品,电解质溶液c是CuSO4溶液。
电镀过程中电解质溶液的浓度不变。
2.电镀前,如果将铜片与直流电源的负极相连,铁制镀件与直流电源的正极相连。
通电后观察到的现象是什么?阴极和阳极发生的反应分别是什么?【解析】电镀前,如果将铜片与直流电源的负极相连,则铜片为阴极,硫酸铜溶液中的铜离子得到电子转化为铜,铁制镀件与直流电源的正极相连,则铁为阳极,铁失去电子,转化为亚铁离子。
阴极电极反应式为:Cu2++2e Cu,阳极电极反应式为:Fe2e Fe2+3.查阅资料,了解工业生产中提高电镀质量的方法。
机械零件表面保护
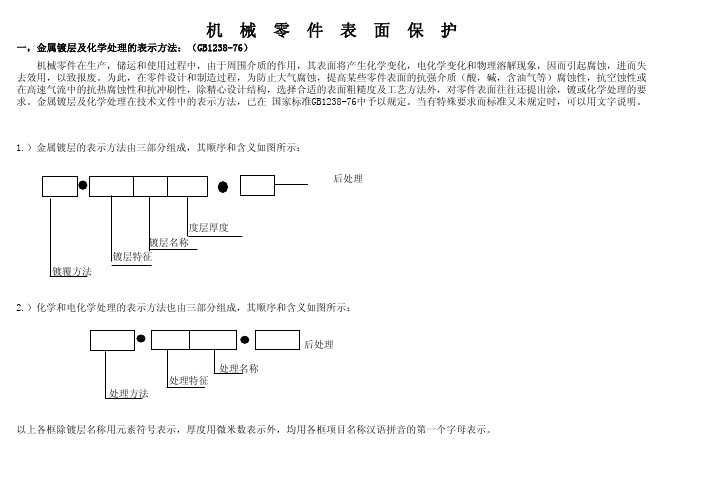
1.)金属镀层的表示方法由三部分组成,其顺序和含义如图所示:
后处理
镀覆方法
度层厚度 镀层名称 镀层特征
2.)化学和电化学处理的表示方法也由三部分组成,其顺序和含义如图所示:
处理方法
处理名称 处理特征
后处理
以上各框除镀层名称用元素符号表示,厚度用微米数表示外,均用各框项目名称汉语拼音的第一个字母表示。
10,)铬酸盐封闭:铝和铝合金制件电化学后,在铬酸盐溶液中进行处理,以提高氧化膜在大气中的稳定性。
以上6,7和8各项可以作为处理或后处理的过程,而9和100两项则为后处理过程。 三,镀层和化学覆盖层的选择原则
选择镀层和化学覆盖层时应考虑下列因素。 1.零件的材料,热处理状态,结构,形状和配合公差:不同材料和镀覆层相互接触时,可能发生接触腐蚀。一般把这种腐蚀分为三个等级。 0级—不引起接触腐蚀,可安全使用,如铝和铅的接触;经过镀镉和钝化处理后的钢制件之间的接触;钛合金与不锈钢的接触等。 1级—引起接触腐蚀,但影响不严重,除热带海洋条件外,一般可使用。如果在活动零件的接触部分涂油,或在不活动零件的接触部分涂油漆,
(Cr)25
注:1.在紧固件的标记中,电镀或电化学处理的符号D及彩虹符号C可以省略。 2.镀层厚度不便表示时,可不注。
二,关于表面防护主要名词术语的说明:
1,)电镀:在电流通过电解质溶液的条件下,与作为阴极的金属制件或具有表面导电层的非金属制件表面上形成与基本牢固结合的金属覆盖的过程
2,)化学镀:在没有外电流作用下,依靠溶液中各物质或金属与溶液中物质间的氧化还没有反应,于金属或非金属制件表面上形成与基本牢固 的金属覆盖层面的过程。
4.析氢对镀层的影响:在电解溶液中,由于水分子的离解,总会有氢离子析出,除逸出液面外,同时也会向金属内部渗入,从下列几方面,影响镀层质量:
铜电镀液密度

铜电镀液密度铜电镀液密度一、简介铜电镀液是一种用于在金属表面镀上一层铜的化学液体。
铜电镀液密度是指单位体积铜电镀液中所含有的铜离子的量。
在铜电镀工艺中,密度的控制是非常重要的,它直接影响着镀层的质量和性能。
二、密度与铜电镀质量的关系1. 密度与镀层均匀性铜电镀液的密度高低决定了铜离子在镀液中的浓度。
当镀液密度较高时,铜离子的浓度也较高,有利于均匀地镀上一层厚度均匀的铜层。
相反,密度较低的镀液在铜离子浓度不足时容易出现镀层不均匀的问题。
2. 密度与镀层结构镀层的结构对其性能有重要影响,而密度是控制镀层结构的一个关键因素。
较高密度的铜电镀液可形成结构致密的镀层,具有更强的抗氧化性能;而较低密度的镀液往往会导致孔隙较多的镀层,容易受到氧化的侵蚀。
三、密度的控制方法1. 控制镀液成分首先,通过调整镀液的配方来控制密度。
铜电镀液通常包含铜盐、酸、添加剂等成分。
通过改变这些成分的浓度,可以改变铜离子的浓度,从而影响密度。
2. 控制镀液工艺参数其次,合理控制镀液的工艺参数也是控制密度的关键。
镀液的温度、电流密度、搅拌速度等因素都会影响铜离子的释放速率,进而影响密度。
3. 密度检测与调整密度的检测是保证电镀质量的重要环节。
一般可以使用密度计进行测量,通过与设定值进行比较,来判断是否需要进行调整。
如果发现密度偏高,则可以适量添加稀释剂;如果发现密度偏低,则可以适当添加铜盐。
四、结语铜电镀液密度的控制直接关系着铜镀层的质量。
通过合理调整镀液成分和控制工艺参数,以及定期进行密度检测与调整,我们可以获得均匀、致密的铜镀层。
只有不断提高密度控制的精确度和稳定性,才能满足不同工业领域对镀层质量的要求,保持铜电镀工艺的可靠性和可持续性发展。
影响电镀层质量的内因与外因剖析

影响电镀层质量的内因与外因剖析电镀件质量的好坏直接影响着设备的整体质量。
影响电镀质量的因素包括内部因素和外部因素。
因此,不仅要对影响电镀质量的内部因素应有一个全面的认识,而且对影响电镀质量的外部因素也不容忽视,严格控制每一个环节,才能确保电镀质量。
影响电镀质量的因素包括内部因素和外部因素两个方面:一、内部因素电镀车间内部严格的质量管理是电镀零件质量的有力保障。
为了从根本上提高电镀质量,并获得优质镀层的目的,对影响电镀质量的每一个内部环节都应有一个全面的认识。
(一)前处理因素镀层与基体之间的结合力、防腐性能和外观质量的好坏,与零部件镀前表面处理的优劣有着直接关系。
附着于零件表面的油、锈、氧化皮等污物,就是妨碍电镀液与金属基体充分接触的中间障碍物,在这种表面上不可能形成合格的电镀层。
当镀件上附着极薄的甚至肉眼看不见的油膜和氧化膜时,虽然得到外观正常、结晶细致的镀层,但是结合强度大为降低。
因此,做好零件的前处理,是整个电镀工序获得良好结果的先决条件。
首先,必须保证除油和酸洗溶液的浓度和纯度,溶液中漂浮的油污要及时清理干净;其次,除锈液杂质达到一定量时,将会影响镀层质量,所以要定期更换。
(二)电镀药液因素在电镀生产中,由于各种原因,导致各种有害杂质进入电镀液。
杂质的种类繁多,大致有金属杂质、金属氧化物、非金属杂质和种种不溶性悬浮物、有机杂质等。
各种镀液所含杂质的种类不尽相同,对同一种杂质的容忍程度也不相同。
当一种或几种有害杂质积累到一定程度时,就会影响镀液性能和镀层质量,因此,不能等到杂质积累到造成危害时,才处理电镀液。
另外,电镀药液各成分含量有一个最佳工艺范围,应对槽子药液定期进行化验分析,保证各成份在工艺范围内;同时,根据生产任务量、实际经验和化验结果,在杂质积累到有可能影响电镀层质量之前,净化处理电镀液,以保证电镀药液的稳定性。
(三)工艺条件控制因素工艺条件的控制直接影响着电镀层的质量。
只有掌握和控制好每个镀种的各工艺条件,才能获得优质镀层。
电镀的主要工艺参数

电镀的主要工艺参数电镀是一种常见的表面处理工艺,通过在物体表面上镀上一层金属薄膜,以改善物体的外观、耐腐蚀性和导电性能。
在进行电镀过程中,有许多关键的工艺参数需要控制和调整,以确保镀层的质量和性能达到要求。
电镀液的成分是决定电镀效果的关键因素之一。
电镀液主要包括金属盐、添加剂和溶剂等组分。
金属盐通常是金属阳离子的盐酸或硫酸盐,而添加剂则包括控制镀层均匀性、增加附着力和改善电镀速度的化学物质。
溶剂的选择要考虑到溶解性、挥发性和安全性等因素。
电镀液的温度是影响电镀过程的重要参数。
一般来说,液体温度越高,电镀速度越快,但过高的温度可能导致电镀液的挥发和分解,影响镀层的质量。
因此,需要根据金属的性质和电镀液的成分来确定合适的温度范围。
电镀液的酸碱度(pH值)也是一个关键的工艺参数。
不同金属的电镀液对pH值的要求不同,一般建议在合适的酸碱度范围内进行电镀。
酸碱度的调整可以通过添加酸或碱来实现,但要注意避免过高或过低的pH值对电镀液和镀层的影响。
电流密度是控制电镀速度和镀层均匀性的重要参数。
电流密度过高会导致局部电流过大,造成镀层厚度不均匀或甚至出现气孔和裂纹等缺陷。
而电流密度过低则会导致镀层速度过慢,影响生产效率。
因此,需要根据工件的形状、大小和电镀液的性质来选择合适的电流密度。
电镀时间是影响镀层厚度和质量的关键因素。
电镀时间过长可能导致镀层厚度过厚或出现过量金属沉积,而电镀时间过短则可能导致镀层厚度不足。
因此,需要根据要求的镀层厚度和电镀液的特性来确定适当的电镀时间。
还需要注意电极的选择和放置位置。
电极应与工件接触良好,以确保电流的传导和镀层的均匀性。
放置位置的选择要考虑到工件的形状和尺寸,以避免电流过于集中或过于分散。
电镀的主要工艺参数包括电镀液的成分、温度、酸碱度,以及电流密度、电镀时间和电极的选择和放置位置等。
合理控制和调整这些参数,可以获得满足要求的电镀镀层,提高产品的质量和性能。
化学镀液 电镀液
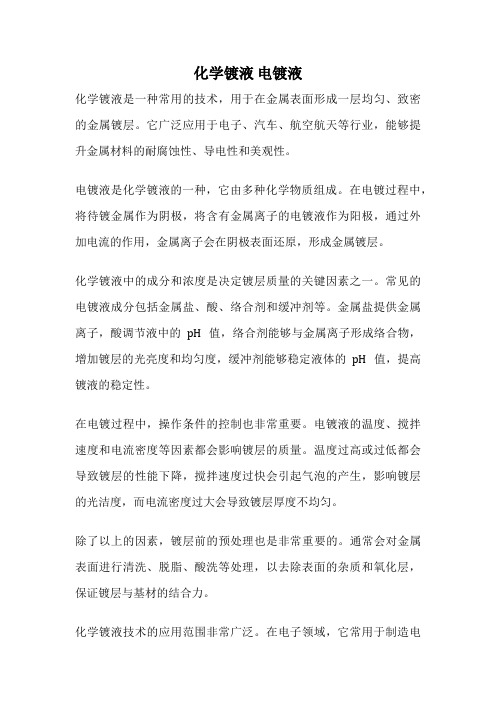
化学镀液电镀液化学镀液是一种常用的技术,用于在金属表面形成一层均匀、致密的金属镀层。
它广泛应用于电子、汽车、航空航天等行业,能够提升金属材料的耐腐蚀性、导电性和美观性。
电镀液是化学镀液的一种,它由多种化学物质组成。
在电镀过程中,将待镀金属作为阴极,将含有金属离子的电镀液作为阳极,通过外加电流的作用,金属离子会在阴极表面还原,形成金属镀层。
化学镀液中的成分和浓度是决定镀层质量的关键因素之一。
常见的电镀液成分包括金属盐、酸、络合剂和缓冲剂等。
金属盐提供金属离子,酸调节液中的pH值,络合剂能够与金属离子形成络合物,增加镀层的光亮度和均匀度,缓冲剂能够稳定液体的pH值,提高镀液的稳定性。
在电镀过程中,操作条件的控制也非常重要。
电镀液的温度、搅拌速度和电流密度等因素都会影响镀层的质量。
温度过高或过低都会导致镀层的性能下降,搅拌速度过快会引起气泡的产生,影响镀层的光洁度,而电流密度过大会导致镀层厚度不均匀。
除了以上的因素,镀层前的预处理也是非常重要的。
通常会对金属表面进行清洗、脱脂、酸洗等处理,以去除表面的杂质和氧化层,保证镀层与基材的结合力。
化学镀液技术的应用范围非常广泛。
在电子领域,它常用于制造电子元器件,如印制电路板、连接器等。
在汽车行业,它可以用于改善汽车零部件的耐腐蚀性和外观质量。
在航空航天领域,化学镀液被广泛应用于制造飞机零部件,以提高其耐蚀性和抗疲劳性能。
化学镀液技术的发展已经取得了很大的进展,但仍然面临一些挑战。
例如,一些电镀液中使用的物质对环境和人体健康具有潜在的危害,因此需要合理管理和处理废液。
此外,随着新材料和新工艺的不断涌现,化学镀液技术也需要不断创新和改进,以满足不断变化的需求。
化学镀液是一种重要的技术,具有广泛的应用前景。
随着科学技术的不断发展,化学镀液技术将继续进步,为各个行业提供更高质量的金属镀层。
我们相信,通过不断的研究和创新,化学镀液技术将为人类创造更美好的未来。
电镀中内孔不上镀的原因
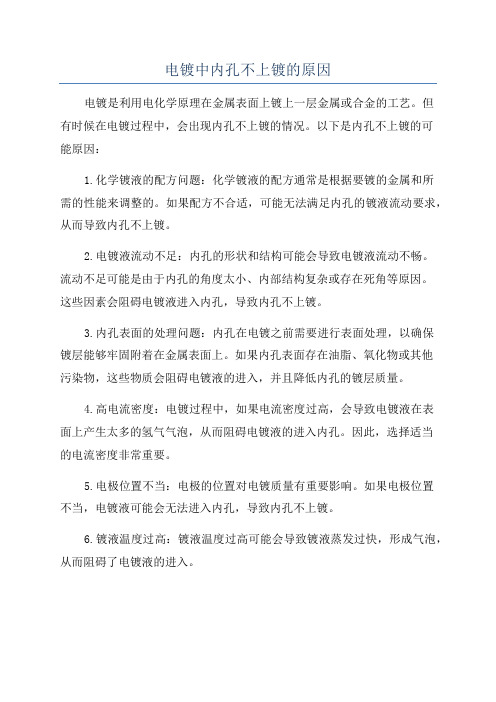
电镀中内孔不上镀的原因电镀是利用电化学原理在金属表面上镀上一层金属或合金的工艺。
但有时候在电镀过程中,会出现内孔不上镀的情况。
以下是内孔不上镀的可能原因:1.化学镀液的配方问题:化学镀液的配方通常是根据要镀的金属和所需的性能来调整的。
如果配方不合适,可能无法满足内孔的镀液流动要求,从而导致内孔不上镀。
2.电镀液流动不足:内孔的形状和结构可能会导致电镀液流动不畅。
流动不足可能是由于内孔的角度太小、内部结构复杂或存在死角等原因。
这些因素会阻碍电镀液进入内孔,导致内孔不上镀。
3.内孔表面的处理问题:内孔在电镀之前需要进行表面处理,以确保镀层能够牢固附着在金属表面上。
如果内孔表面存在油脂、氧化物或其他污染物,这些物质会阻碍电镀液的进入,并且降低内孔的镀层质量。
4.高电流密度:电镀过程中,如果电流密度过高,会导致电镀液在表面上产生太多的氢气气泡,从而阻碍电镀液的进入内孔。
因此,选择适当的电流密度非常重要。
5.电极位置不当:电极的位置对电镀质量有重要影响。
如果电极位置不当,电镀液可能会无法进入内孔,导致内孔不上镀。
6.镀液温度过高:镀液温度过高可能会导致镀液蒸发过快,形成气泡,从而阻碍了电镀液的进入。
7.电极效率问题:电极效率是指在电镀过程中,电极上实际发生的电化学反应与理论上应发生的反应之比。
如果电极效率低,电镀液的金属离子生成率较低,镀层的质量就会受到影响,导致内孔不上镀。
防止内孔不上镀的方法包括优化镀液配方、改进内孔结构、进行彻底的表面处理、选择适当的电流密度和电极位置、控制镀液温度等。
此外,定期检查和维护设备,确保镀液的质量和性能也是非常重要的。
真空电镀中镀液的pH值及对镀层性能的影响研究
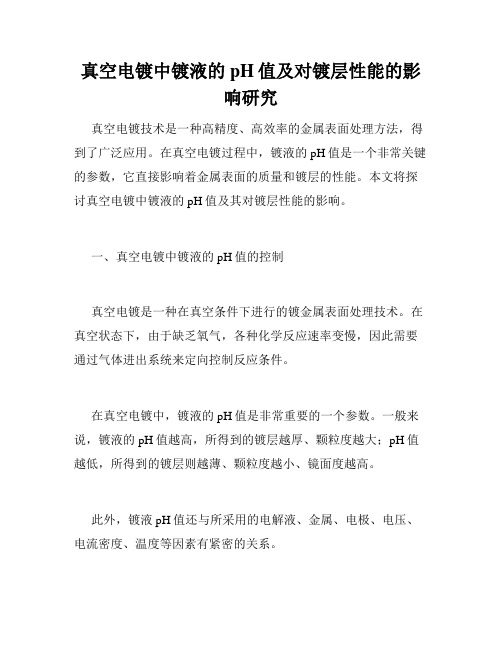
真空电镀中镀液的pH值及对镀层性能的影响研究真空电镀技术是一种高精度、高效率的金属表面处理方法,得到了广泛应用。
在真空电镀过程中,镀液的pH值是一个非常关键的参数,它直接影响着金属表面的质量和镀层的性能。
本文将探讨真空电镀中镀液的pH值及其对镀层性能的影响。
一、真空电镀中镀液的pH值的控制真空电镀是一种在真空条件下进行的镀金属表面处理技术。
在真空状态下,由于缺乏氧气,各种化学反应速率变慢,因此需要通过气体进出系统来定向控制反应条件。
在真空电镀中,镀液的pH值是非常重要的一个参数。
一般来说,镀液的pH值越高,所得到的镀层越厚、颗粒度越大;pH值越低,所得到的镀层则越薄、颗粒度越小、镜面度越高。
此外,镀液pH值还与所采用的电解液、金属、电极、电压、电流密度、温度等因素有紧密的关系。
众所周知,金属表面的化学性质会影响到电化学反应的进行,从而影响到镀层的形成。
因此,在真空电镀中,不同金属或合金的镀层形成机理与反应动力学是不尽相同的,因而也需要采用不同的pH值进行处理。
在实际操作中,可以通过改变电解液成分、电流密度、电源电压等多种方法来调节镀液的pH值,从而达到较好的镀层质量。
二、镀液pH值对镀层质量的影响在真空电镀过程中,镀液的pH值是一个非常关键的因素,它直接影响着金属表面的质量和镀层的性能。
下面将详细探讨镀液pH值对镀层性能的影响。
1. 镀层的外观质量镀液的pH值影响着镀层表面的光滑度和亮度。
一般来说,当镀液的pH控制在7.5以下,所得到的镀层表面光滑度更好、更有亮度,亮度呈现明显的白色金属过渡层。
当镀液pH值继续降低到6.5以下时,镀层的表面光滑度会越来越差,表面开始出现裂纹和毛刺,并且表面色泽也变暗。
2. 镀层的机械性能镀液的pH值还有助于调节金属表面的硬度和抗腐蚀性。
实验表明,当镀液的pH值在7.5~8.0之间时,所得到的镀层具有较好的硬度和抗腐蚀性;而当pH值过高或过低时,镀层的硬度会降低,抗腐蚀性也会明显下降。
影响电镀层质量的因素及生产中注意事项

1 物 理 因素
影 响 电镀 层 质量 的物 理 因素 主要 有 受镀 零 件 、 挂 具 、 挂 方式 、 装 阳极 、 设备 、 包装 及贮 存环 境等 。
1 1 受镀零 件 .
凹部 位又 因 电流过 小 而镀 层 很 薄 或 根 本 镀 不 上 镀
种影 响 因素 , 生 产 过 程 中 , 这 三 种 影 响 因素 加 在 对
以控 制 和注 意 , 就会 获得 满意 的 、 定 的镀层 质量 。 稳
针 对基 体材 料影 响 因素应 注 意 以下 几 点 :) 1 设
计 者在 选择 零部 件材 料 时 , 考 虑材 料 在 产 品 中 的 除
性 能外 , 应考 虑表 面处 理对 材 料 的选 择 性 。2 应 还 ) 选 择符 合标 准要 求 的材料 加工 零部 件 。
1 12 形 .. 状
对 于 电镀 来 说 , 品零 件 的几 何 形 状 是 不 确 产 定 的 , 变动 量 最 大 的物 理 因素 , 是 决 定 电镀 加 是 也 工 难 易程 度 的 重 要 因 素 。零 件 形 状 越 复 杂 , 电镀 难 度 系数 就越 大 , 于外 形 复 杂 的零 件 , 进 行 电 对 在
中的铅 、 或 镉 等 金 属 杂 质 含 量 超 过 一 定 量 时 , 锡 也 难 以在零 部 件表 面获得 优质 的镀 覆层 。
收 稿 日期 : 0 10 —2 2 1—42
21年 1 月 01 1
电 镀 与 精 饰
第 3 卷第 1 期( 2 期) ・ 3・ 3 1 总24 2
El c r p a i g Pr d c i n e t 0 l tn o u t o
电镀铜的性能分析和影响因素
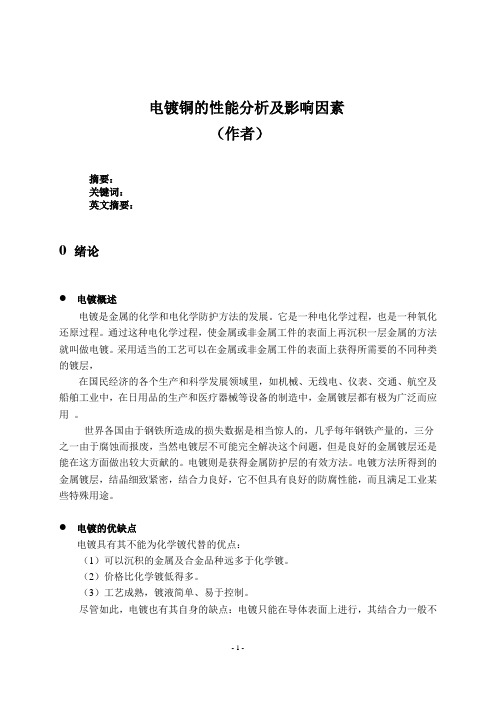
电镀铜的性能分析及影响因素(作者)摘要:关键词:英文摘要:0 绪论●电镀概述电镀是金属的化学和电化学防护方法的发展。
它是一种电化学过程,也是一种氧化还原过程。
通过这种电化学过程,使金属或非金属工件的表面上再沉积一层金属的方法就叫做电镀。
采用适当的工艺可以在金属或非金属工件的表面上获得所需要的不同种类的镀层,在国民经济的各个生产和科学发展领域里,如机械、无线电、仪表、交通、航空及船舶工业中,在日用品的生产和医疗器械等设备的制造中,金属镀层都有极为广泛而应用。
世界各国由于钢铁所造成的损失数据是相当惊人的,几乎每年钢铁产量的,三分之一由于腐蚀而报废,当然电镀层不可能完全解决这个问题,但是良好的金属镀层还是能在这方面做出较大贡献的。
电镀则是获得金属防护层的有效方法。
电镀方法所得到的金属镀层,结晶细致紧密,结合力良好,它不但具有良好的防腐性能,而且满足工业某些特殊用途。
●电镀的优缺点电镀具有其不能为化学镀代替的优点:(1)可以沉积的金属及合金品种远多于化学镀。
(2)价格比化学镀低得多。
(3)工艺成熟,镀液简单、易于控制。
尽管如此,电镀也有其自身的缺点:电镀只能在导体表面上进行,其结合力一般不及化学镀电镀铜的应用领域铜具有良好的导电、导热性能,质软而韧,有良好的压延性和抛光性能。
为了提高表面镀层和基体金属的结合力,铜镀层常用作防护、装饰性镀层的底层,对局部渗碳工件,常用镀铜来保护不需要渗碳的部位。
1)铜箔粗化处理铜箔是制造印制板的关键导电材料,但是印制板外层铜箔毛面在与绝缘基板压合制造覆铜板之前必须经过电镀铜粗化处理,使之具有一定的表面粗糙度,才能保证与基板有足够的粘合力。
铜箔的粗化处理通常分 2 步:一是在较低铜离子浓度高电流密度下的粗化处理,二是在高铜离子浓度低电流密度下的固化处理。
粗化处理过程中必须使用特殊的添加剂,否则铜箔在高温层压制造覆铜板时会出现“铜粉转移”现象,影响与基板的结合力,严重时会使线路从基板上脱落。
真空电镀中镀液的循环和搅拌对镀层性能的影响研究

真空电镀中镀液的循环和搅拌对镀层性能的影响研究随着现代工业的发展,电镀技术在各个领域中得到广泛应用,电镀中的环保问题也已成为业内关注的问题之一。
而真空电镀技术因其高品质的镀层、低环境污染等优点,在各个领域的应用越来越广泛。
对于真空电镀技术来说,镀液的循环和搅拌是影响镀层质量的关键环节之一。
本文将就真空电镀中镀液的循环和搅拌对镀层性能的影响进行探讨。
一、真空电镀的工艺过程真空电镀技术是利用蒸化器将金属加热至蒸发状态后,将其沉积在基材表面来形成一层金属膜的过程。
该技术广泛应用于光学、电子、化工、航空航天、汽车等领域中,特别是在高精度的光学镜片和微电子器件制造过程中,其应用已经达到令人惊叹的高水平。
在真空电镀过程中,镀材和基材被放入真空镀膜机中,通过控制蒸发器的加热程度将镀材加热至蒸发状态,镀材蒸发的高温气体沉积在基材上形成金属膜。
在这个过程中,我们需要通过控制镀液的循环和搅拌来保证金属蒸汽的均匀沉积以及增加不同的反应流体之间的接触面积。
二、镀液循环的影响镀液的循环可以使沉积于基材表面的金属粒子大小和形状分布更为均匀,从而得到更加优良的镀层。
循环对沉积速度的影响主要与镀液中携带的溶质成分有关。
通常情况下,循环速率越快,溶质的浓度越均匀,金属颗粒尺寸分布也将变得更加均匀。
反之,当液体静止或循环速率过慢时,会使得不溶质成分在镀液中逐渐聚集,超过饱和状态而形成固溶体,镀层的质量也会下降。
此外,循环速率的影响还表现在沉积速率上,如当循环速率过慢时,由于液体的对流强度比较小,沉积速度会逐渐降低,增加薄膜旋涡的形成,使得沉积的材料本身质量也会受到影响。
三、镀液搅拌的影响工艺过程中,镀液的搅拌也是非常关键的环节。
由于金属的沉积和水平(或基材表面)的甚至程度有关,在镀膜的表面上失控的状态可能会导致不均匀的表面,并差异性的镀膜结果。
在循环的同时,对于镀液的搅拌也很关键。
在镀液中加入适当的机械搅拌还能进一步提高镀层的质量。
- 1、下载文档前请自行甄别文档内容的完整性,平台不提供额外的编辑、内容补充、找答案等附加服务。
- 2、"仅部分预览"的文档,不可在线预览部分如存在完整性等问题,可反馈申请退款(可完整预览的文档不适用该条件!)。
- 3、如文档侵犯您的权益,请联系客服反馈,我们会尽快为您处理(人工客服工作时间:9:00-18:30)。
影响电镀镀层质量的因素——镀液的性能镀层种类繁多,同时,沉积某种金属用的镀液也可有不同类型,因此,各类镀种的镀液组成千差万别,但较理想的镀液应具有如下的性能:
(1)沉积金属离子阴极还原极化较大,以获得晶粒度小、致密,有良好附着力的镀层。
(2)稳定且导电性好。
(3)金属电沉积的速度较大,装载容量也较大。
(4)成本低,毒性小。
镀液配方千差万别,但一般都是由主盐、导电盐(支持电解质〕、络合剂和一些添加剂等组成。
主盐是指进行沉积的金属离子盐,主盐对镀层的影响体现在:主盐浓度高,镀层较粗糙,但允许的电流密度大;主盐浓度低,允许通过的电流密度小,影响沉积速度。
一般电镀过程要求在高的主盐浓度下进行,考虑到溶解度等因素,常用的主盐是硫酸盐或氯化物。
导电盐(支持电解质〉的作用是增加电镀液的导电能力,调节?只值,这样不仅可降低槽压、提高镀液的分散能力,更重要的是某些导电盐的添加有助于改善镀液的物理化学性能和阳极性能。
在单盐电解液中,镀层的结晶较为粗糙,但价廉、允许的电流密度大。
而加人络合剂的复盐电解液使金属离子的阴极还原极化得到了提高,可得到的镀层细致、紧密、质量好,但成本较高。
对于Zn、Cu、Cd、Ag、Au等的电镀,常见的络合剂是氰化物;但对于沖、等金
属的电镀,因这些元素的水合离子电沉积时极化较大,因而可不必添加络合剂。
在复盐电解液的电镀过程中,因氰化物的毒性较大,无氰电镀成为发展方向。
添加剂在镀液中不能改变溶液性质,但却能显著地改善镀层的性能。
添加剂对镀层的影响体现在添加剂能吸附于电极表面,可改变电极一溶液界面双电层的结构,达到提高阴极还原过程过电位、改变丁曲线斜率等目的。
添加剂的选择是经验性的,添加剂可以是无机物或有机物,通常指的添加剂有光亮剂、整平剂、润湿剂和活化剂等。
镀液的性能可以影响镀层的质量,而镀液是由溶质和溶剂组成的,溶剂对镀层质量也应有一定影响。
电镀液溶剂必须具有下列性质:①电解质在其中是可溶的;②具有较高的介电常数,使溶解的电解质完全或大部分电离成离子。
电镀中用的溶剂有水、有机溶剂和熔盐体系等。
1.电镀工艺因素对镀层影响
电流密度对镀层的影响主要体现在电流密度大,电镀同样厚度的镀层所需时间短,可提高生产效率,同时,电流密度大,形成的晶核数增加,镀层结晶细而紧密,但电流密度太大会出现枝状晶体和针孔等。
对于电镀过程,电流密度存在一个最适宜范围。
电解液温度对镀层的影响体现在温度升髙,能提高阴极和阳极电流效率,消除阳极钝化,增加盐的溶解度和溶液导电能力,降低浓差极化和电化学极化。
但温度太高,结晶生长的速度超过了形成结晶活性的生长点,因而导致形成粗晶和孔隙较多的镀层。
电解液的搅拌有利于减少浓差极化,利于得到致密的镀层,同时
减少氢脆。
此外,电解液的值、冲击电流和换向电流等的使用对镀层质量也有一定影响。
2.阳极
电镀时阳极对镀层质量也有影响。
阳极氧化一般经历活化区(金属溶解区\钝化区(表面生成钝化膜)和过钝化区(表面产生高价金属离子或析出氧气)三个步骤。
电镀中阳极的选择应是与阴极沉积物种相同,镀液中的电解质应选择不使阳极发生钝化的物质,电镀过程中可调节电流密度保持阳极在活化区域。
如果某些阳极(如Cr)能发生剧烈钝化则可用惰性阳极。