催化裂化催化剂再生反应
催化剂的失活与再生
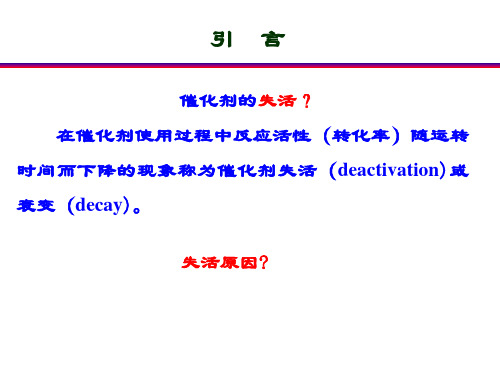
H H NH H
无孤对电子(无毒)
说明:当有孤对电子时呈 毒性 ,没有孤对电 子时,无毒
防治办法:选择适当物 质将毒物转化为不带孤 对电子的无毒物质。
金属催化剂的三类毒物
2)金属离子:具有已占用 的d轨道,并且d轨道上有 与金属催化剂的空轨键合 的电子(不可逆)。 例如:对Pt催化剂 金属离子没有d轨 无毒 d轨全空 d轨半充满以前 有毒:金属离子的d轨从半 充满到全充满 防治办法:进入反应工段之 前除去毒物。
Li , Be 2 没有d轨 无毒(对Pt催化剂) Na , Mg 2 , Al 3 K , Ca 2 3d 0 4s 0 Rb , Sr 2 , Zr 4 4d 0 5s 0 Cs , Ba 2 , La 3 , Ce3 5d 0 6s 0 Th 4 6s 0 7 s 0 Cu 2 3d 9 4 s 0 有毒 Cu , Zn 2 3d 10 4s 0 Ag , Cd 2 , In3 4d 10 5s 0 Sn 2 4d 10 5s 2 Au , Hg 2 5d 10 6s 0 Hg 5d 10 6s1 Tl , Pb 2 , Bi 3 5d 10 6s 2 Cr 3 3d 3 4s 0 无毒 Cr 2 3d 4 4s 0 Mn 2 3d 5 4 s 0 有毒 Fe 2 3d 6 4s 0 Co 2 3d 7 4 s 0 Ni 2 3d 8 4s 0
5、选择性中毒
选择性中毒:利用毒物分子对某些活性部位的选择性吸 附来抑制或中毒不希望的催化活性,提高催化选择性。 例子1:Pt-Re/Al2O3重整催化剂,利用少量硫化剂对氢解 活性中心的选择性中毒(预硫化)提高芳构化选择性。 例子2:FCC汽油选择性加氢脱硫的催化剂,利用碱性物 质或结焦对强加氢活性中心的选择性中毒,提高加氢脱 硫选择性。 例子3:正己烷异构化的Ni/八面沸石催化剂,利用少量 H2S对氢解活性中心的选择性中毒抑制裂解反应,提高异 构化选择性。
催化裂化
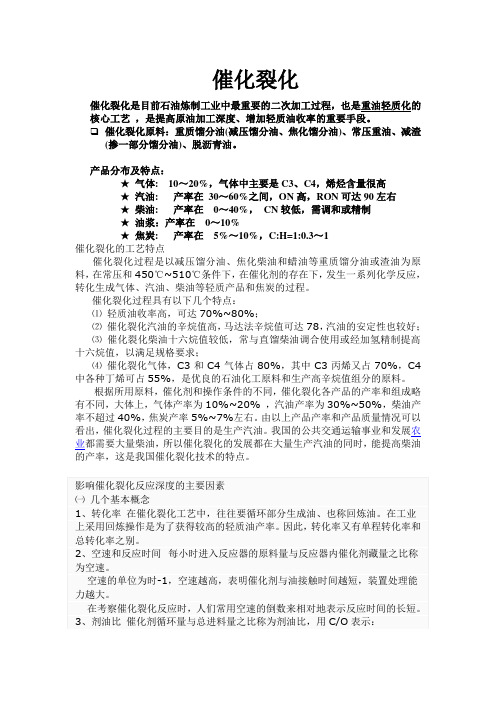
催化裂化催化裂化是目前石油炼制工业中最重要的二次加工过程,也是重油轻质化的核心工艺,是提高原油加工深度、增加轻质油收率的重要手段。
催化裂化原料:重质馏分油(减压馏分油、焦化馏分油)、常压重油、减渣(掺一部分馏分油)、脱沥青油。
产品分布及特点:★气体: 10~20%,气体中主要是C3、C4,烯烃含量很高★汽油: 产率在30~60%之间,ON高,RON可达90左右★柴油: 产率在0~40%,CN较低,需调和或精制★油浆:产率在0~10%★焦炭: 产率在5%~10%,C:H=1:0.3~1催化裂化的工艺特点催化裂化过程是以减压馏分油、焦化柴油和蜡油等重质馏分油或渣油为原料,在常压和450℃~510℃条件下,在催化剂的存在下,发生一系列化学反应,转化生成气体、汽油、柴油等轻质产品和焦炭的过程。
催化裂化过程具有以下几个特点:⑴轻质油收率高,可达70%~80%;⑵催化裂化汽油的辛烷值高,马达法辛烷值可达78,汽油的安定性也较好;⑶催化裂化柴油十六烷值较低,常与直馏柴油调合使用或经加氢精制提高十六烷值,以满足规格要求;⑷催化裂化气体,C3和C4气体占80%,其中C3丙烯又占70%,C4中各种丁烯可占55%,是优良的石油化工原料和生产高辛烷值组分的原料。
根据所用原料,催化剂和操作条件的不同,催化裂化各产品的产率和组成略有不同,大体上,气体产率为10%~20% ,汽油产率为30%~50%,柴油产率不超过40%,焦炭产率5%~7%左右。
由以上产品产率和产品质量情况可以看出,催化裂化过程的主要目的是生产汽油。
我国的公共交通运输事业和发展农业都需要大量柴油,所以催化裂化的发展都在大量生产汽油的同时,能提高柴油的产率,这是我国催化裂化技术的特点。
在同一条件下,剂油比大,表明原料油能与更多的催化剂接触。
㈡影响催化裂化反应深度的主要因素影响催化裂化反应转化率的主要因素有:原料性质、反应温度、反应压力、反应时间。
1、原料油的性质原料油性质主要是其化学组成。
催化裂化装置反应再生系统工艺流程
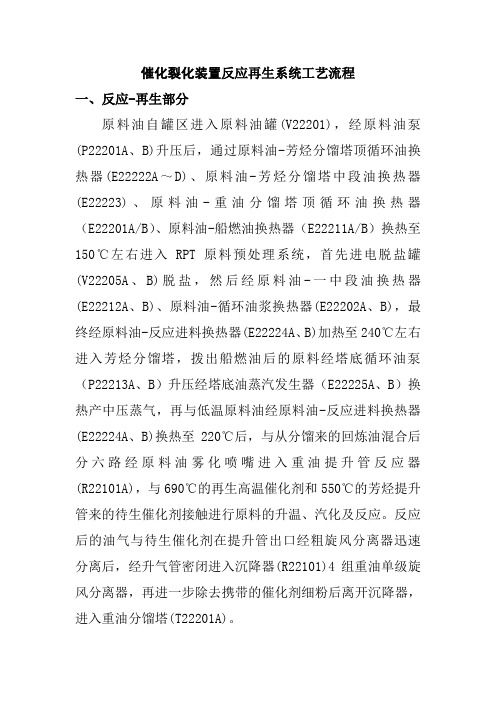
催化裂化装置反应再生系统工艺流程一、反应-再生部分原料油自罐区进入原料油罐(V22201),经原料油泵(P22201A、B)升压后,通过原料油-芳烃分馏塔顶循环油换热器(E22222A~D)、原料油-芳烃分馏塔中段油换热器(E22223)、原料油-重油分馏塔顶循环油换热器(E22201A/B)、原料油-船燃油换热器(E22211A/B)换热至150℃左右进入RPT原料预处理系统,首先进电脱盐罐(V22205A、B)脱盐,然后经原料油-一中段油换热器(E22212A、B)、原料油-循环油浆换热器(E22202A、B),最终经原料油-反应进料换热器(E22224A、B)加热至240℃左右进入芳烃分馏塔,拨出船燃油后的原料经塔底循环油泵(P22213A、B)升压经塔底油蒸汽发生器(E22225A、B)换热产中压蒸气,再与低温原料油经原料油-反应进料换热器(E22224A、B)换热至220℃后,与从分馏来的回炼油混合后分六路经原料油雾化喷嘴进入重油提升管反应器(R22101A),与690℃的再生高温催化剂和550℃的芳烃提升管来的待生催化剂接触进行原料的升温、汽化及反应。
反应后的油气与待生催化剂在提升管出口经粗旋风分离器迅速分离后,经升气管密闭进入沉降器(R22101)4组重油单级旋风分离器,再进一步除去携带的催化剂细粉后离开沉降器,进入重油分馏塔(T22201A)。
重油分馏塔分馏后的塔顶油气经冷凝冷却后进入油气分离器(V22203A),分离出的粗轻燃油分四路经雾化喷嘴进入芳烃提升管反应器(R22101B),与690℃催化剂接触进行原料的升温、汽化及反应。
反应后的油气与待生催化剂在提升管出口经粗旋风分离器迅速分离后,经升气管密闭进入沉降器内轻燃油单级旋风分离器,再进一步除去携带的催化剂细粉后离开沉降器,进入芳烃分馏塔(T22201B)。
油气分离出来的待生催化剂与重油部分的待生催化剂一起进入反应沉降器的汽提段。
催化裂化高级工问答题大全
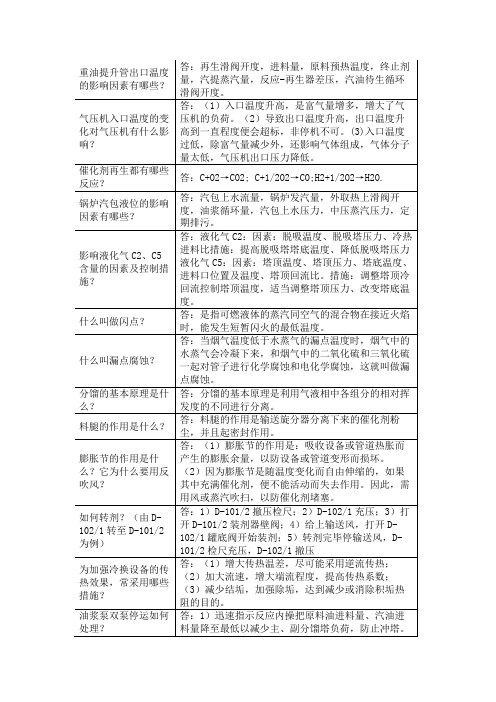
传热的三种基本形式是传导传热、对流传热、辐射传热。传导传热:热量从一个物体的高温部位传送至其低温部位,或者两个直接接触的物体之间,热量从高温物体传送至低温物体,这种传热过程将连续地进行,直到整个物体或直接接触的两个物体的各部分的温度完全相等为止,这种传热叫热传导。对流传热:由于流体(液体和气体)质点的移动,将热量向它所占空气的一部分带至另一部分,这种传热方式叫做对流传导。辐射传热:物体的热不需要任何传递介质,而以辐射能的形式传递的过程,称为辐射传热。
简述蒸汽发生器的正常停用?
答:(1)打开汽包的蒸汽放空阀,逐渐关闭汽包蒸汽出口阀;(2)缓慢关闭蒸汽发生器的进出口阀门,使热油逐渐走旁路,控制好汽包的液位,待蒸汽发生器冷却下来后(蜡油蒸汽发生器在切出来后就要进行退油,不要等发生器冷下来),停止进水,但暂时还应保留发生器内存水;(3)管线按吹扫要求进行退油吹扫,扫好后将壳程内存水全部排入地漏(排净后,蒸汽放空阀和低点排凝阀不关闭)。
四机组油冷器的切换步骤?
答:(1)缓慢打开备用油冷器入口阀,充满油(油冷器顶部放空见油)。(2)缓慢打开备用油冷器出口阀。(3)缓慢关闭在用油冷器出入口阀。
外取热爆管现象?
答:1)再生压力升高,再生器稀相和再生外集气室温度下降,烟气轮机入口温度下降,外取热器温度下降。2)外取热器料位下降或回0,二密床料位稍有上升,烧焦罐料位基本不变。3)因大量水汽进入再生旋分器,旋分器负荷增大,烟气携带催化剂量增大,烟机振动有上升现象。4)锅炉蒸汽压力下降,FIQ6580上升。5)给水流量不正常地大于蒸汽流量,汽包水位下降。6)烟囱有大量蒸汽和催化剂冒出。
蒸汽发生器发生液空的处理方法?
答:(1)首先将热源切出蒸汽发生器,让其降温; (2)将蒸汽放空阀打开,将蒸汽切出管网放空;(3)等蒸汽发生器温度降低后,再向汽包补水至正常液位,按正常启动程序重新投用;(4)注意液面空时,千万不要立即向汽包补水,以免突沸发生事故。
催化裂化催化剂
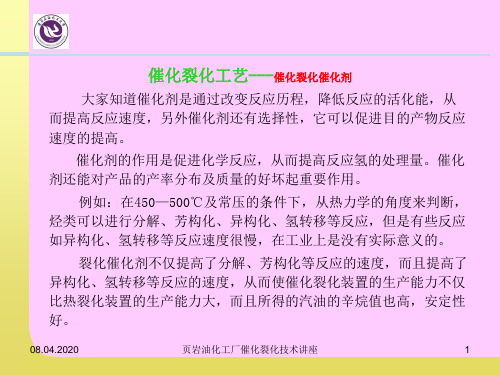
08.04.2020
页岩油化工厂催化裂化技术讲座
3
2、无定型硅酸铝催化剂 1958年我国开始生产小球状93-5毫米 合成硅酸铝催化剂,用于
移动床。 1965年开始生产微球状920-100微米 合成硅酸铝。 ①高铝低铝催化剂和合成方法 硅酸铝的主要成分是氧化硅和氧化铝,依铝含量的不同,合成硅
酸铝又分为低铝和高铝。 低铝硅酸铝含Al2O3 10-13% 高铝硅酸铝含Al2O3 25% 合成的方法是:由Na2SiO3 俗称水玻璃 Al2 (SO4)3,溶液按一定比例配 合生成凝胶,再经过水洗,过滤,成型,干燥,活化等步骤制成。
08.04.2020
页岩油化工厂催化裂化技术讲座
10
⑶分子筛催化剂的结构
每个单元晶胞结构,每个单元晶胞由八个削角八面体构成,削角八面体 的每个顶端是Si或Al原子,其间由氧原子相连接。由八个削角八面体围成的 空洞称为“八面沸石笼”。它是催化反应进行的主要场所。其体积为820埃。
进入八面沸石笼的主要通道是由十二员环组成,其平均直径为0.8— 0.9nm。钠离子的位置有多处。
项目 新鲜催化剂 平衡催化剂
松动 0.40 0.63
沉降 0.44 0.69
密实 0.53 0.79
催化剂的堆积密度常用于计量催化剂的体积重量,催化剂的颗 粒密度对催化剂的流化性能有重要的影响。
08.04.、活性、稳定性
(1)活性:是指催化剂促进化学反应的能力。
由于AL:O键趋向正电荷较强 Si,使Al带有正电性,即为非质 子酸。
在有少量的水存在在时,由 于AL原子带正电性使水分子离解 为H+与OH-,其中OH-与带正电的 性的Al结合,而则H+在Al原子附 近呈游离状态,此即质子酸。 (如a)
第六节催化裂化反应再生系统资料
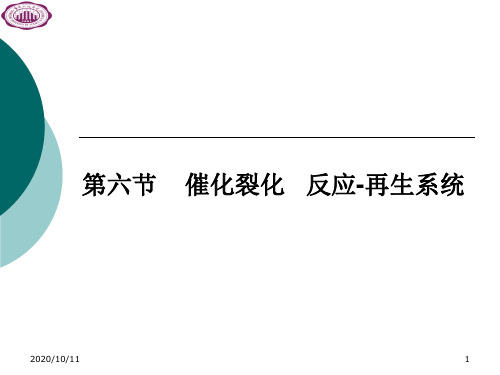
2020/10/11
19
c.快速床(循环流化床)再生 ➢气相转化成连续相,催化剂颗粒变为分散相,从而强化 了烧碳过程 ➢随着气速的提高,返混程度减小,中、上部接近于平推 流,也有利于烧碳强度的提高 ➢在快速流化床区域,必须有较大的固体循环量才能保持 较高的床层密度 ➢催化裂化装置的烧焦罐再生就是属于循环流化床的一种 再生方式
➢再生温度对烧碳反应速率的影响十分显著,提高再生温 度是提高烧碳速率的有效手段,在单段再生时,密相创层 的温度一般不超过730℃
➢工业上一般采用的空气线速为0.6~0.7m/s ➢工业装置采用的再生器压力在0.25~0.4MPa(绝)之间 ➢单段再生的主要问题是再生温度的提高受到限制和密相 床层的有效催化剂含炭量低
9
分段反应
➢不同的馏分需要不同的反应条件,理想选择是不同的 馏分在不同的场所和条件下进行反应 ➢两段提升管(Ⅰ型)催化裂化:
★第一段提升管只进新鲜原料,段间抽出柴油出装置 ★第二段提升管单独进循环油,显著改善产品分布 ★第二段提升管底部回炼汽油,降低汽油烯烃含量 ➢分段进料避免了新鲜原料和油浆的相互干扰
2020/10/11
18
b.两段再生 ➢两段再生是把烧碳过程分为两个阶段进行 ➢与单段相比,两段再生的主要优点是:
①对于全混床反应器,第一段出口的半再生剂的含碳量 高于再生剂的含碳量,从而提高了烧碳速率;
②在第二段再生时可以用新鲜空气和更高的温度,提高 了烧碳速率;
③第二段内的水气分压可以很低,减轻了催化剂的水热 老化;且第二段的催化剂藏量比单段再生器的催化剂藏量低, 停留时间较短。因此,第二段可采用较高的再生温度。
2020/10/11
20
2020/10/11
21
重油催化裂化反应再生单元操作法

重油催化裂化反应再生单元操作法一、正常操作1.提升管出口温度(8TIC101)的控制反应温度对反应速度、产品分布和质量、再生烧焦率和设备结焦都有很大影响,它是日常生产中调节反应转化率和改变生产方案的最主要的调节参数之一。
提升管出口温度的设计值为510~538℃。
该温度的确定:1)用于改变生产方案:液化气方案(510~515℃)汽油方案(503~510℃)柴油方案(497~503℃)2)控制设备结焦:a.反应终了温度偏高,热裂化反应严重,热裂化缩合结焦--“硬焦”。
b.反应终了温度偏低,油气中重沸物冷凝、聚合结焦--“软焦”。
3) 降低再生烧焦率:减少非反应焦--可汽提炭,温度在汽提影响因素中起很大作用。
4) 对产品质量的影响:提高温度可以提高汽油辛烷值,但随着温度的升高汽油烯烃含量增加。
主要影响因素:1)催化剂循环量增加,反应温度上升。
2)原料油预热温度(8TIC201)上升,反应温度上升。
3)进料量及回炼比的变化。
4)进料性质改变影响反应转化率,反应温度变化。
5)原料带水,反应温度下降。
6)二再温度(8TI154)升高,反应温度上升。
7)反应沉降器压力(8PI108)升高,反应温度下降。
8)提升管注汽量的变化。
9)预提升介质及介质量的变化。
10)终止剂注入量增大,反应温度下降。
11)再生斜管流化不好,反应温度变化。
12)新鲜催化剂补充量的变化。
13)再生剂定炭高低的变化。
14)钝化剂是否加注及注入量多少的影响。
15)反应助剂是否加入及加入量多少的影响。
16)仪表或滑阀失灵。
调节方法:1)正常情况下,通过8TIC101调节再生滑阀开度改变催化剂循环量来自动控制提升管出口温度。
2)注入终止剂后,可视转化率和产品分布情况适当调整反应温度。
3)适当调整外取热器取热量,保证相对平稳的再生温度。
4)再生斜管流化不好时应尽快查明原因进行处理,以建立良好的催化剂循环量。
5)滑阀失灵引起自锁时(除跟踪失调外),应相对平稳各操作参数,尽量减少波动。
催化裂化再生系统

1再生动力学1.1催化剂上的焦炭1)焦炭的化学组成催化剂上的焦炭来源于四个方面:⑴在酸性中心上由催化裂化反应生成的焦炭;⑵由原料中高沸点、高碱性化合物在催化剂表面吸附,经过缩合反应生成的焦炭;⑶因汽提段汽提不完全而残留在催化剂上的重质烃类,是一种富氢焦炭;⑷由于镍、钒等重金属沉积在催化剂表面上造成催化剂中毒,促使脱氢和缩合反应的加剧,而产生的次生焦炭;或者是由于催化剂的活性中心被堵塞和中和,所导致的过度热裂化反应所生成的焦炭。
上述四种来源的焦炭通常被分别称为催化焦、附加焦(也称为原料焦)、剂油比焦(也称为可汽提焦)和污染焦。
实际上,这四种来源的焦炭在催化剂上是无法辩认的。
所谓“焦炭”并不是具有严格的固定组成和结构的物质。
它不是纯碳,一般主要由碳和氢组成,是高度缩合的碳氢化合物,但碳和氢的比例受多种因素的影响,有相当大的变化范围。
影响H/C的因素主要有:催化剂、原料、反应温度、反应时间及汽提条件等。
对一定的催化剂和原料,影响焦炭H/C的主要因素是反应温度和反应时间(或结焦量)。
普遍认为,反应温度越高,焦炭的H/C越小,即焦炭中氢含量越低。
反应时间加长也有同样的影响。
在硅酸铝催化剂上用多种单体烃和轻瓦斯油进行催化裂化反应试验,结果表明所得焦炭的H/C不相同,而在0.4~0.9之间变化。
除碳和氢外,焦炭中还可能含有硫、氮、氧等杂原子,这主要决定于原料的杂原子化合物的含量。
应该指出,焦炭的化学组成,是焦炭的一个重要性质,尤其是C/H,对再生器的操作,特别是对装置的热平衡具有重要意义。
但很遗憾,焦炭的C/H很难测定准确,主要是氢含量很难测准,因为一般用燃烧法测定生成的水量,而水量难以测准,而且在燃烧过程中催化剂结构本身也可能放出一部分水,因而造成实验误差。
在生产装置上,一般还是以测定烟气中CO、CO2和O2的组成,利用焦炭在空气中燃烧时的元素平衡等计算焦炭中的C/H比。
2)焦炭的结构前面谈到焦炭的化学组成是不均匀的,而焦炭的结构与其组成密切相关,可以想象,焦炭的结构也是不均匀的,实际研究结果也证明了这一点,而且结构问题比组成更为复杂。
催化裂化的装置简介及工艺流程
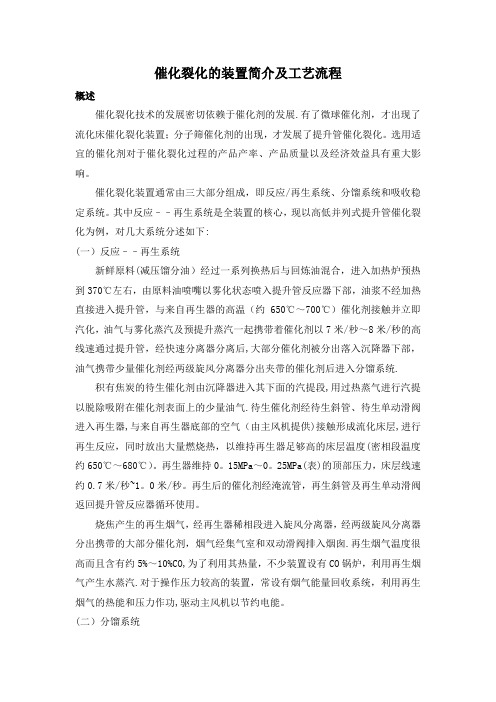
催化裂化的装置简介及工艺流程概述催化裂化技术的发展密切依赖于催化剂的发展.有了微球催化剂,才出现了流化床催化裂化装置;分子筛催化剂的出现,才发展了提升管催化裂化。
选用适宜的催化剂对于催化裂化过程的产品产率、产品质量以及经济效益具有重大影响。
催化裂化装置通常由三大部分组成,即反应/再生系统、分馏系统和吸收稳定系统。
其中反应––再生系统是全装置的核心,现以高低并列式提升管催化裂化为例,对几大系统分述如下:(一)反应––再生系统新鲜原料(减压馏分油)经过一系列换热后与回炼油混合,进入加热炉预热到370℃左右,由原料油喷嘴以雾化状态喷入提升管反应器下部,油浆不经加热直接进入提升管,与来自再生器的高温(约650℃~700℃)催化剂接触并立即汽化,油气与雾化蒸汽及预提升蒸汽一起携带着催化剂以7米/秒~8米/秒的高线速通过提升管,经快速分离器分离后,大部分催化剂被分出落入沉降器下部,油气携带少量催化剂经两级旋风分离器分出夹带的催化剂后进入分馏系统.积有焦炭的待生催化剂由沉降器进入其下面的汽提段,用过热蒸气进行汽提以脱除吸附在催化剂表面上的少量油气.待生催化剂经待生斜管、待生单动滑阀进入再生器,与来自再生器底部的空气(由主风机提供)接触形成流化床层,进行再生反应,同时放出大量燃烧热,以维持再生器足够高的床层温度(密相段温度约650℃~680℃)。
再生器维持0。
15MPa~0。
25MPa(表)的顶部压力,床层线速约0.7米/秒~1。
0米/秒。
再生后的催化剂经淹流管,再生斜管及再生单动滑阀返回提升管反应器循环使用。
烧焦产生的再生烟气,经再生器稀相段进入旋风分离器,经两级旋风分离器分出携带的大部分催化剂,烟气经集气室和双动滑阀排入烟囱.再生烟气温度很高而且含有约5%~10%CO,为了利用其热量,不少装置设有CO锅炉,利用再生烟气产生水蒸汽.对于操作压力较高的装置,常设有烟气能量回收系统,利用再生烟气的热能和压力作功,驱动主风机以节约电能。
第六节 催化裂化反应-再生系统概述

2018/11/5
21
催化裂化主要设备
1、预提升段 2、裂化反应段 3、汽提段
2018/11/5
22
催化裂化主要设备
预提升段:加速催化剂,使催化剂形成活塞流向
上流动,使催化剂上的重金属钝化,有利于油雾
的快速混合,一般为3-6m。
裂化反应段:提供裂化反应的场所。
中止反应技术(MTC)
2018/11/5 11
两段与单段实验室结果对比:
轻油收率可提高 2-3 个百分点 原料转化深度提高 5 个百分点
汽油烯烃含量下降12-13个百分点
液收率提高2.5个百分点以上 干气产率大幅度降低 可显著提高柴汽比
2018/11/5
12
两段与单段工业试验结果对比:
轻油收率提高4个百分点以上
第六节
催化裂化 反应-再生系统
2018/11/5
1
催化裂化装置一般有四部分构成:反应-再生系统,分
馏系统,吸收-稳定系统和能量回收系统
装置形式主要有高低并列式、同轴式等
2018/11/5
2
一:提升管反应器
提升管反应器主要有提升管、沉降器、汽提段、旋分 器、待生斜管等部分组成
2018/11/5
2018/11/5
6
两段提升管 FCC技术的思想及特点
两段FCC技术的基本思想:
★提高催化裂化催化剂的有效活性和选择性,从而改
善目的产品分布;
★分段反应,提高调整生产方案的灵活性
因此,两段提升管FCC技术打破原来的提升管反应器型 式和反-再系统流程: ★两段提升管反应器取代单一反应器 ★构成拥有两路循环的反应-再生系统
5.催化裂化

29 0.569 51
(2)汽油、轻柴油单程产率、总产率,及轻质油收率
26.4 汽油单程产率= 100 %=33% 80
23
4.3 烃类的催化裂化反应
15.1 轻柴油单程产率= 100 %=18.88% 80
汽油总产率= 26.4 100 %=51.76% 51
轻柴油总产率=
15.1 100 %=29.61% 51
V0,V Voil, 20,m 3 /h Vcat,m 3 h 1
式中,Mcat——催化剂的质量藏量,t; Vcat——催化剂的体积藏量,m3。 藏量:在反应器和再生器内经常保持的催化剂的量,对流 化床指分布板(管)以上的催化剂量。 (2)假反应时间 若空速↗,则单位Cat.上通过的原料油↗,原料油分 子停留在Cat.上的时间就↙。
↗Cat.的活性有利于↗反应速度,可↗转化率,从而↗反应
器处理能力。
↗Cat.的活性有利于促进氢转移和异构化反应。 Cat.的活性取决于组成和结构。
29
4.3 烃类的催化裂化反应
2、反应温度
反应温度对反应速度、产品产率分布及产品质量影响 显著。 (1)反应速度常数与温度的变化关系:
d ln K E dT RT 2
柴油
C10- C20
0-40%
油浆 焦炭
以稠环芳烃为主 缩合产物
5-7%不等 5-10%掺渣油高
13
4.3 烃类的催化裂化反应
H CH3 C CH3 + 思考1:为什么催化裂化产物中少C1、C2,多C3、C4? H+(Cat.) + CH3 CH CH3
正碳离子分解时不生成<C3、C4的更小正碳离子。 思考2:为什么催化裂化产物中多异构烃? 伯、仲正碳离子稳定性差,易转化为叔正碳离子。 思考3:为什么催化裂化产物中多β烯烃(2-烯烃)?
催化裂化装置吸收稳定系统的原理是什么

催化裂化装置吸收稳定系统的原理是什么?催化裂化生产过程的主要产品是气体、汽油和柴油,其中气体产品包括干气和液化石油气,干气作为本装置燃料气烧掉,液化石油气是宝贵的石油化工原料和民用燃料。
所谓吸收稳定,目的在于将来自分馏部分的催化富气中C2以下组分与C3以上组分分离以便分别利用,同时将混入汽油中的少量气体烃分出,以降低汽油的蒸气压,保证符合商品规格。
吸收-稳定系统包括吸收塔、解吸塔、再吸收塔、稳定塔以及相应的冷换设备。
由分馏系统油气分离器出来的富气经气体压缩机升压后,冷却并分出凝缩油,压缩富气进入吸收塔底部,粗汽油和稳定汽油作为吸收剂由塔顶进入,吸收了C3、C4(及部分C2)的富吸收油由塔底抽出送至解吸塔顶部。
吸收塔设有一个中段回流以维持塔内较低的温度,吸收塔顶出来的贫气中尚夹带少量汽油,经再吸收塔用轻柴油回收其中的汽油组分后成为干气送燃料气管网。
吸收了汽油的轻柴油由再吸收塔底抽出返回分馏塔。
解吸塔的作用是通过加热将富吸收油中C2组分解吸出来,由塔顶引出进入中间平衡罐,塔底为脱乙烷汽油被送至稳定塔。
稳定塔的目的是将汽油中C4以下的轻烃脱除,在塔顶得到液化石油气〈简称液化气〉,塔底得到合格的汽油——稳定汽油。
吸收解吸系统有两种流程,上面介绍的是吸收塔和解吸塔分开的所谓双塔流程;还有一种单塔流程,即一个塔同时完成吸收和解吸的任务。
双塔流程优于单塔流程,它能同时满足高吸收率和高解吸率的要求。
催化裂化反应装置基本原理一、催化裂化工艺过程的特点催化裂化过程是使原料在有催化剂存在下,在470~530度和0.1~0.3兆帕的压力条件下,发生一系列化学反应,转化成气体,汽油、柴油等轻质产品和焦炭的过程。
催化裂化的原料一般是重质馏分油,例如减压馏分油(减压蜻油)和焦化馏分油等,随着催化裂化技术和催化剂工艺的不断发展,进一步扩大了催化裂化原料范围,部分或全部渣油也可作催化原料。
催化裂化过程具有以下几个特点: 1335920680(1)轻质油收率高,可达70~80%,而原油初馏的轻质油收率仅为10~40%。
催化裂化再生器稀相密度异常分析与处置
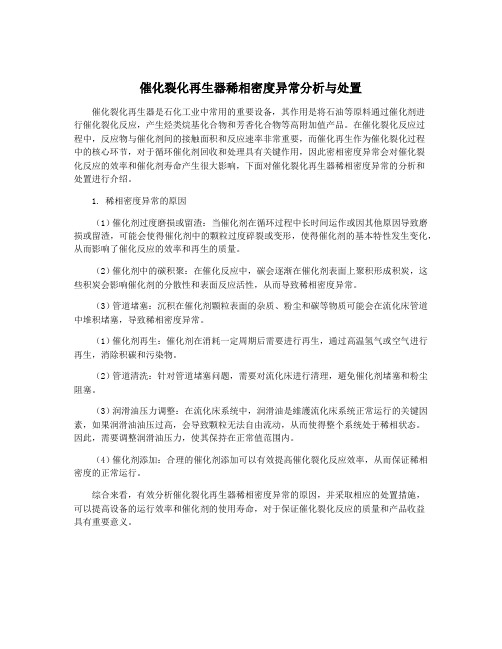
催化裂化再生器稀相密度异常分析与处置催化裂化再生器是石化工业中常用的重要设备,其作用是将石油等原料通过催化剂进行催化裂化反应,产生烃类烷基化合物和芳香化合物等高附加值产品。
在催化裂化反应过程中,反应物与催化剂间的接触面积和反应速率非常重要,而催化再生作为催化裂化过程中的核心环节,对于循环催化剂回收和处理具有关键作用,因此密相密度异常会对催化裂化反应的效率和催化剂寿命产生很大影响,下面对催化裂化再生器稀相密度异常的分析和处置进行介绍。
1. 稀相密度异常的原因(1)催化剂过度磨损或留渣:当催化剂在循环过程中长时间运作或因其他原因导致磨损或留渣,可能会使得催化剂中的颗粒过度碎裂或变形,使得催化剂的基本特性发生变化,从而影响了催化反应的效率和再生的质量。
(2)催化剂中的碳积聚:在催化反应中,碳会逐渐在催化剂表面上聚积形成积炭,这些积炭会影响催化剂的分散性和表面反应活性,从而导致稀相密度异常。
(3)管道堵塞:沉积在催化剂颗粒表面的杂质、粉尘和碳等物质可能会在流化床管道中堆积堵塞,导致稀相密度异常。
(1)催化剂再生:催化剂在消耗一定周期后需要进行再生,通过高温氢气或空气进行再生,消除积碳和污染物。
(2)管道清洗:针对管道堵塞问题,需要对流化床进行清理,避免催化剂堵塞和粉尘阻塞。
(3)润滑油压力调整:在流化床系统中,润滑油是維護流化床系统正常运行的关键因素,如果润滑油油压过高,会导致颗粒无法自由流动,从而使得整个系统处于稀相状态。
因此,需要调整润滑油压力,使其保持在正常值范围内。
(4)催化剂添加:合理的催化剂添加可以有效提高催化裂化反应效率,从而保证稀相密度的正常运行。
综合来看,有效分析催化裂化再生器稀相密度异常的原因,并采取相应的处置措施,可以提高设备的运行效率和催化剂的使用寿命,对于保证催化裂化反应的质量和产品收益具有重要意义。
催化裂化(分析的很全面)
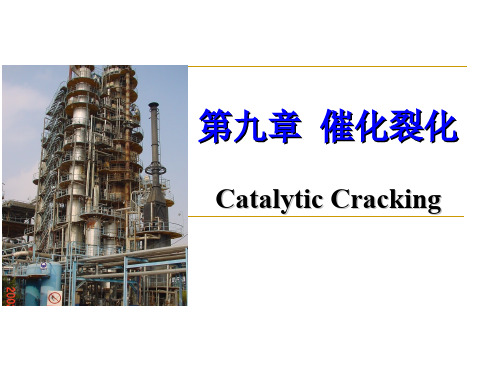
第九章 催化裂化
Catalytic Cracking
第一节 概述
燃料生产中一个重要的问题
如何将原油中的重质馏分油甚至渣油转化成轻
质燃料产品
重质油轻质化
从大分子分解为较小的分子
主要依靠分解反应(热反应和催化反应)
从低 H/C 的组成转化成较高 H/C 的组成
脱 碳(溶剂脱沥青、催化裂化、焦炭化等) 加 氢(加氢裂化)
变)
提高催化剂的活性还有利于促进氢转移反应和异
构化反应,对提高产品质量有利。
催化剂的活性取决于它的结构和组成。
② 活性和催化剂表面上的积炭有关
催化剂表面积炭量↗,活性↙ 。 单位催化剂上焦炭沉积量主要与催化剂在反应器内
的停留时间有关。
催化剂上的焦炭含量还与剂油比有关
③ 剂油比, C/O
一、催化裂化的原料和产品
催化裂化是目前石油炼制工业中最重要的二次加工过
程,也是重油轻质化的核心工艺 ,是提高原油加工深 度、增加轻质油收率的重要手段。
催化裂化原料:重质馏分油 ( 减压馏分油、焦化馏分
油 ) 、常压重油、减渣 ( 掺一部分馏分油 ) 、脱沥青 油。 主要控制指标:金属含量和残碳值
催化裂化技术今后的发展方向: ① 加工重质原料 ② 降低能耗 ③ 减少环境污染 ④ 适应多种生产需要的催化剂和工艺 ⑤ 过程模拟和计算机应用
第二节 石油烃类的催化裂化反应
一、单体烃的催化裂化反应
1 .各类单体烃的裂化反应
(1). 烷 烃
烷烃主要发生分解反应,例如 :
C16H34
+ C8H16 C8H18
催化裂化催化剂的再利用

催化裂化催化剂的再利用摘要:催化裂化催化剂不仅生成量大,而且重金属含量高,具有较强的污染性,处理起来特别困难。
如果其NiO质量分数大于0.1%或V的质量分数大于3%,该废催化剂就属于危险固体废物。
传统的掩埋法会造成资源的浪费,也会导致土壤、地下水和大气的严重污染,许多国家已明令禁止FCC废催化剂的直接排放,我国为落实生态文明建设战略目标也出台了相应的限制措施。
如果将废FCC催化剂加以综合回收利用,不仅可以节约大量的La、Ce等稀土金属,而且可以避免废催化剂带来的环境问题。
回收利用FCC 废催化剂的途径有磁分离回收、化学法复活、制备加氢催化剂、制备分子筛和吸附剂以及生产橡胶填充剂等。
鉴于长岭分公司紧邻催化剂制造厂,FCC废催化剂可送至催化剂厂,采用化学法复活回用,或生产分子筛、吸附剂或橡胶填充剂等产品。
关键词:催化裂化催化剂粉尘分子筛吸附剂1 前言流化催化裂化(FCC)工艺是在高温和催化剂的作用下,使重质油裂化为C1~C4气体、汽油和柴油等产品的过程,是石油炼制过程中最重要的原油二次加工过程。
在此过程中,副产的焦炭会沉积在催化剂表面,引起催化剂暂时失活,在再生器中烧去催化剂表面的焦炭可恢复其活性;同时,原料油所含的金属离子镍(Ni)、铁(Fe)和钒(V)等也会沉积在催化剂表面上,导致催化剂中毒而永久失活,此外,由于催化剂在使用过程中处于高温流化状态,机械磨损冲击和水热变形也会严重影响其使用性能。
因此,流化催化裂化装置一般需要定期卸出部分性能下降的平衡催化剂,用新鲜催化剂进行置换,这是FCC废催化剂的来源之一。
而FCC废催化剂的另一个来源是,FCC烟气中所含的催化剂细粉在进入烟气轮机和余热回收系统之前被旋风分离器收集下来,这部分催化剂颗粒很细(<20μm),不能再加入反应再生系统中使用,只能作为废催化剂处理。
FCC催化剂失活(废催化剂)后主要成分为SiO2和Al2O3,还含有少量的Ni、Fe、V 和Na等元素,具有多孔性分子筛结构,比表面积和孔体积较大,具有很好的吸附性能。
催化裂化反应再生系统流程

催化裂化反应再生系统流程
1. 新鲜原料油经换热后与回炼油浆混合,经加热炉加热至180-320℃后至催化裂化提升管反应器下部的喷嘴。
2. 原料油由蒸气雾化并喷入提升管内,在其中与来自再生器的高温催化剂(600-750℃)接触,随即汽化并进行反应。
3. 油气在提升管内的停留时间很短,一般只有几秒钟。
反应产物经旋风分离器分离出夹带的催化剂后离开沉降器去分馏塔。
4. 积有焦炭的催化剂(称待生催化剂)由沉降器落入下面的汽提段。
汽提段内装有多层人字形挡板并在底部通入过热水蒸气,待生催化剂上吸附的油气和颗粒之间的空间内的油气被水蒸气置换出而返回上部。
5. 经汽提后的待生催化剂通过待生斜管进人再生器。
再生器的主要作用是烧去催化剂上因反应而生成的积炭,使催化剂的活性得以恢复。
6. 再生后的催化剂(称再生催化剂)落人淹流管,经再生斜管送回反应器循环使用。
再生烟气经旋风分离器分离出夹带的催化剂后,经双动滑阀排人大气。
第五节催化裂化催化剂再生反应

2019/10/12
页岩油化工厂催化裂化技术讲座
3
(1)硅酸铝的失活速率方程水热失活是个缓慢的过程。对 于无定型硅酸铝,则可认为失活速率可用一级反应动力学方程 来描述。
dA/dt=kdA 积分后得:
Aτ =A0 exp(-kdτ ) 式中A0和Aτ 为初始和停留时间为τ 的活性,kd为失活 速率常数。
物料参数
基
准
+Ni(265μ
g/g)
+V (830μ g/g)
微反活性指数 77.5
73.5
74.2
焦炭产率
4.05
5.62
5.48
焦炭产率中污染碳 0
2.26
2.01
氢气产率
0.20
0.76
0.64
氢气产率中污染氢 0
0.56
0.44
2019/10/12
页岩油化工厂催化裂化技术讲座
11
(2)金属污染的程度与其老化的程度有关 实验表明:已经老化的重金属要比新沉积的金属的作用弱的多。 因此,仅用催化剂上沉积的重金属量还不能确切地反映催化剂的
一般 再生的供热量小于反应系统的耗热为热不足,等于为热 平衡,大于为热过剩。
2019/10/12
页岩油化工厂催化裂化技术讲座
19
五、再生反应动力学 再生反应速度决定再生器的效率,它对催化剂的活性、
选择的燃烧速度。因此,许多研
究工作都 集中于烧碳反应动力学,而对氢的燃烧研究的较 少。
8
(2)结焦失活的动力学方程
voorhis通过对大量数据分析认为尽管焦炭产率与催化剂的类 型、原料组成及操作条件有关。但是沉积在催化剂上的焦炭与反 应时间的关系基本上是相同的。
第四章_催化裂化

焦炭总产率= 2.64 100%=5.18% 51
焦炭单程产率= 2.64 100%=3.3% 80
轻质油收率是汽油和轻柴油总产率之和: 轻质油收率=(51.76+29.61)%=81.37%
1
2.影响催化裂化反应速度的主要因素 催化裂化反应过程包括以下七个步骤: ① 反应物从主气流扩散到催化剂表面 ② 反应物沿催化剂微孔向催化剂内部扩散
1
催化裂化速率的影响因素: (1).催化剂活性 ① 提高催化剂活性,反应速度提高 ② 活性和催化剂表面上的积炭有关 ③ 剂油比,C/O
催化剂循环量 t / h) ( 剂油比C / O 总进料量(t / h)
1
(2).反应温度
① 反应温度提高,在其他条件不变的情况下,转化率提高 ② 反应温度的改变可改变热裂化和催化裂化反应的比例
1
二、裂化催化剂的再生 (regeneration)
催化剂上沉积的焦炭是一种缩合产物,它的主要成分是碳 和氢,其经验分子式可写成(CHn)m,n=0.5~1.0
通常离开反应器时的催化剂(待生剂)上含炭约1%,对分 子筛催化剂一般要求再生剂上的碳含量降到0.1%甚至 0.05%以下
通过再生只能恢复催化剂由于结焦而丧失的活性,但不 能恢复由于结构变化及金属污染而引起的失活 催化剂的再生过程决定着整个装置的热平衡和生产能力
1
使用性能
活性、稳定性:测微反活性 选择性:主要目的产物是汽油 密度:影响流化性能 筛分组成、机械强度:保证良好的流化性能
1
国产分子筛种类:
REY(稀土Y型) USY(超稳Y型) REHY(稀土氢Y型) Y型分子筛:人工合成的是含钠离子分子筛, 用其它阳离子置换后,得到很高活性的Y型分 子筛。 助剂:辛烷值助剂、金属钝化剂、CO助燃剂。
催化裂化催化剂的发展历程及研究进展

及研究进展2023-10-28CATALOGUE 目录•催化裂化催化剂概述•催化裂化催化剂的发展历程•催化裂化催化剂的研究进展•催化裂化催化剂的未来发展及挑战•结论与展望01催化裂化催化剂概述催化裂化催化剂是一种固体酸催化剂,用于促进石油烃类的大分子裂解成小分子,同时增加低沸点、高价值产品的产率。
催化裂化催化剂定义催化裂化催化剂可以提供活性位点,促进烃类分子的裂解、异构化和氢转移等反应,同时具有高选择性和高转化率的特点。
催化裂化催化剂作用催化裂化催化剂的定义与作用不同类型催化裂化催化剂酸性催化剂(如Y型、X型、ZSM-5等)、基性催化剂(如钙型、钠型等)、金属氧化物催化剂(如V2O5-WO3/TiO2等)。
不同类型催化裂化催化剂特点不同类型的催化裂化催化剂具有不同的酸性和活性特点,可以根据不同原料和产品需求进行选择。
催化裂化催化剂的种类与特点催化裂化催化剂发展历程从20世纪50年代开始,催化裂化技术逐渐发展并应用于工业生产,随着技术的进步,新型的催化裂化催化剂不断涌现。
催化裂化催化剂现状目前的催化裂化催化剂已经实现了高度专业化和精细化,不仅提高了产品的质量和产量,还降低了能耗和环境污染。
催化裂化催化剂的历史与现状02催化裂化催化剂的发展历程总结词第一代催化裂化催化剂主要基于氧化铝和氧化硅为载体,使用稀土元素和碱金属作为活性组分,具有较高的裂化活性和稳定性。
详细描述第一代催化裂化催化剂在上世纪60年代开始商业应用,主要基于氧化铝和氧化硅为载体,通过添加稀土元素和碱金属进行改性,提高了催化剂的活性和稳定性。
该催化剂在当时具有较高的裂化选择性,能够有效地将大分子烃类裂解成小分子烃类。
总结词第二代催化裂化催化剂在第一代催化剂的基础上,使用了新型载体材料和活性组分,进一步提高了裂化活性和选择性,同时降低了压力和温度要求。
详细描述第二代催化裂化催化剂在上世纪80年代开始商业应用,在第一代催化剂的基础上,使用了新型载体材料如分子筛等,并优化了活性组分的组成,进一步提高了催化剂的活化和选择性。
- 1、下载文档前请自行甄别文档内容的完整性,平台不提供额外的编辑、内容补充、找答案等附加服务。
- 2、"仅部分预览"的文档,不可在线预览部分如存在完整性等问题,可反馈申请退款(可完整预览的文档不适用该条件!)。
- 3、如文档侵犯您的权益,请联系客服反馈,我们会尽快为您处理(人工客服工作时间:9:00-18:30)。
? 分子筛的结构不同失活的情况也不同,温度对催化剂的失活有 重要的影响。
2020/2/2
页岩油化工厂催化裂化技术讲座
1
无定型硅铝催化剂 温度高于650℃ 失活很快
REY分子筛晶体崩塌温度 870-880℃ USY分子筛晶体崩塌温度 950-980℃ 对于分子筛催化剂
<650℃ 失活很慢 <720℃ 失活并不严重 >720℃ 失活问题比较突出
n— 常数,对分子筛催化剂约为0.12-0.30 ,平均为0.21, 对无定型硅铝剂高得多。
2020/2/2
页岩油化工厂催化裂化技术讲座
9
3、毒物引起的失活
(1) 催化裂化催化剂的主要毒物是(Fe、Ni、V、Gu )等重金 属与金属钠和碱性氮化物,前面我们已经做了简单的讨论。
镍的脱氢作用导致催化剂的选择性变差 结果是:焦炭产率上升,液体产率下降,产品不饱合度下降。 钒是使催化剂的活性下降。
③可汽提焦—也称剂油比焦 因为在汽提段汽提不完全而残留在催化剂上的重质烃类,其氢碳比 较高,可汽提焦的量与汽提段的汽提效果,催化剂的空结构状况等因素 有关。 ④污染焦—由于重金属沉积在催化剂上促进脱氢和缩合反应产生的 焦。污染焦的量与催化剂上的金属沉积量、沉积金属的类型有关
2020/2/2
页岩油化工厂催化裂化技术讲座
当催化剂上金属含量低于3000μ g/g时,镍比钒的影响大4-5 倍,而在高含量(15000-20000μ g/g)钒对选择性的影响与镍达 到相同的水平。
2020/2/2
页岩油化工厂催化裂化技术讲座
10
表9-9 镍钒对催化剂影响的比较
物料参数
基
准
+Ni (265μ
g/g)
+V (830μ g/g)
2020/2/2
页岩油化工厂催化裂化技术讲座
7
(1) 工业催化裂化所产生的焦炭可认为包括四类焦炭:
① 催化焦—烃类在催化剂活性中心上反应时,生成的焦炭。H/C约 为0.4。随转化率的增大而增大。
②附加焦—原料中的焦炭前身物(主要是稠环基烃)在催化剂表面 上吸附,经缩合反应产生焦炭。通常认为在全回炼时附加焦的量与康氏 残碳值大体上相当。
污染程度。此外,重金属污染的影响的大小还与催化剂的抗金属污 染能力有关。 (3)催化剂上重金属的来源
金属来源于原料油。对于重油来说重金属的污染是一个严重的 问题。
例如:大庆原油减压渣油的重金属含量,镍含量约5μ g/g。如 果催化剂的单耗为1kg/t 计算平衡催化剂上的镍也在5000μ g/g。
2020/2/2
8
(2)结焦失活的动力学方程
voorhis通过对大量数据分析认为尽管焦炭产率与催化剂的类 型、原料组成及操作条件有关。但是沉积在催化剂上的焦炭与反 应时间的关系基本上是相同的。
CC=Atcn CC—催化剂上积碳的质量分数 tc— 催化剂停留时间 A— 随原料油和催化剂性质以及操作条件而
变的系数,A值约为0.2-0.8
2020/2/2
页岩油化工厂催化裂化技术讲座
13
(5)碱性氮化物
它使催化剂的活性和选择性降低。碱性氮化物的毒害作用的大小除 了与总碱氮有关外,还与其分子结构有关。例如分子大小、 分子类 型、 分子的饱和度。
4、催化剂的平衡活性 由于新鲜催化剂在使用中会受到各种因素的影响而逐渐发生变化, 因此新鲜催化剂的活性并不能反应工业装置中实际的催化剂活性。实 际通常用平衡活性来表示装置中实际的相对稳定的催化剂活性。 影响活性的因素 (1)催化剂的水热失活速度 催化剂的水热失活主要发生在再生剂,因为它是温度最高和水汽 多的场合。 催化剂颗粒在再生器内的停留时间分布是计算催化剂失活的重要 基础。
微反活性指数 77.5
73.5
74.2
焦炭产率
4.05
5.62
5.48
焦炭产率中污染碳 0
2.26
2.01
氢气产率
0.20
0.76
0.64
氢气产率中污染氢 0
0.56
0.44
2020/2/2
页岩油化工厂催化裂化技术讲座
11
(2)金属污染的程度与其老化的程度有关 实验表明:已经老化的重金属要比新沉积的金属的作用弱的多。 因此,仅用催化剂上沉积的重金属量还不能确切地反映催化剂的
页岩油化工厂催化裂化技术讲座
4
(2)分子筛催化剂的一级失活动力学方程 chester等在研究分子筛催化剂的失活动力学时得到如图9-13的结果
2020/2/2
页岩油化工厂催化裂化技术讲座
5
根据此结果,作者提出了以下的假设。
分子筛催化剂Байду номын сангаас活性可以分为两个温度区,在低温的活性以无定 形基质的活性为主,而在高温区的失活则以分子筛活性为主。因此, 分子筛催化剂的活性速率常数kd可以用式(9-20)表示:
2020/2/2
页岩油化工厂催化裂化技术讲座
2
表9-8新鲜剂与水热减活平衡剂的物性比较
物性参数
表面积
孔体积
堆积密度 g/ml
大密度 小密度
微反活性:MA
新鲜剂 200-600 0.17-0.71 0.79-0.88 0.48-0.53 70-83
平衡剂 60-130 0.16-0.45 0.90-1.03 0.70-0.82 56-70
催化裂化工艺 第五节 裂化催化剂的再生反应
一、裂化催化剂的失活
裂化催化剂失活的三个原因:
a、高温或高温水蒸汽的作用;
b、裂化反应生焦;
c、毒物的毒害
?1、水热失活
? 高温,特别是水蒸气存在的条件下,裂化催化剂的表面结构发 生变化,比表面减小,孔容减小,分子筛的晶体破坏,导致催化 剂的活性和选择性下降。
式中,AM EM AZ EZ分别是无定形基质和分子筛的指前因子和活化
能。由图Am可, E见m,, 在Az高, E温z 区的活化能明显增大。
2020/2/2
页岩油化工厂催化裂化技术讲座
6
2、结焦失活
催化裂化反应生成的焦炭沉积在催化剂的表面上覆盖催化 剂的活性中心,使催化剂的活性和选择性下降。随着反应的进 行,催化剂上沉积的焦炭增多,失活程度加大。
页岩油化工厂催化裂化技术讲座
12
(4)碱金属和碱土金属
它们以离子形态存在时,可以吸附在催化剂的酸性中心上。 并使之中和,从而降低催化剂的活性。
在实际生产中,钠对催化裂化催化剂的中毒是需要注意的。 金属钠和V具有一样的作用 ,而且会降低催化剂结构的熔点,使 之在再生温度条件下发生熔化现象,把分子筛和基质一同破坏。
2020/2/2
页岩油化工厂催化裂化技术讲座
3
(1)硅酸铝的失活速率方程水热失活是个缓慢的过程。对
于无定型硅酸铝,则可认为失活速率可用一级反应动力学方程 来描述。
dA/dt=kdA 积分后得:
Aτ =A0 exp(-kdτ ) 式中A0和Aτ 为初始和停留时间为τ 的活性,kd为失活 速率常数。
2020/2/2