孔类零件编程方法
数控加工程序编制铣削编程4孔类零件的程序编制
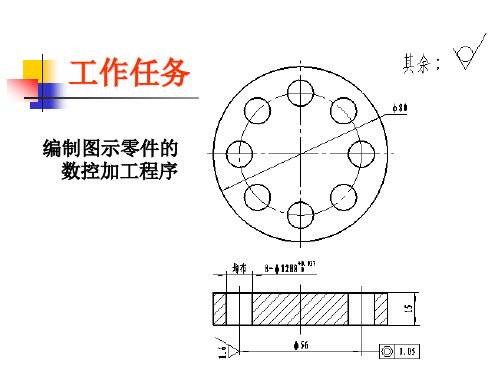
二、相关知识
(四)孔加工循环指令
举例:如图所示,用此程序加 工xy平面上在z轴方向排列的螺 纹孔M12x1。在此,出发点定 为x30y20,第一个孔与此参考 点的距离为20mm,其他的钻 孔相互间的距离也是20mm。 首先执行循环LCYC83加工孔, 然后运行循环LCYC84进行螺 纹切削。钻孔深度为80mm, 攻70mm。
LCYC60循环指令应用
二、相关知识
(四)孔加工循环指令
N10 G0 G54 G71 G17 G90 Tl Dl ;确定工艺参数 N20 S500 M3 y30 x20 z110 ;回到出发点(任意的) N30 R10l=75 R102=2 R103=72 R104=22 ;定义钻孔循环参数 N40 R105=l R107=82 R108=20 R109=10 ;定义钻孔循环参数 N50 R110=30 R111=10 R127=1 ;定义钻孔循环参数 N60 Rl15=83 R116=30 R117=20 R118=20 Rl19=5 R120=90 R121=20 N70 LCYC60 ;调用线性孔循环 N71 M05;
刀具,从而保孔的尺寸精度和表面粗糙度值。
二、相关知识
(三)孔加工刀具的选用
3)钻削速度V、进给量F的选择 F(mm/min)=S(r/min)×f(mm/r) S(r/min)=1000×V/(π×D) (r/min)
钻削进给量F参考值
加工材料
深 径 切削用
刀具直径do(mm)
比
量
灰铸铁
可锻铁、锰铸 铁
l/do
8 10 12 16 20 25 30 35 40
163~229HB (HT100、
HT150)
可锻铸铁 (≤229HB)
加工中心29个孔打孔编程格式

加工中心29个孔打孔编程格式摘要:1.加工中心29个孔的基本信息2.打孔编程的步骤与方法3.编程格式的规范与应用4.实际操作中的注意事项正文:加工中心29个孔打孔编程格式是在制造业中广泛应用的一种工艺方法。
在进行打孔编程时,需要遵循一定的步骤与方法,以确保孔位的精确度和加工效率。
本文将详细介绍加工中心29个孔的打孔编程格式,并提供实用的操作指南。
一、加工中心29个孔的基本信息加工中心29个孔是指在加工过程中,需要在工件上打29个孔。
这些孔的位置、直径、深度和分布应根据零件图纸和加工要求来确定。
在实际操作中,加工中心29个孔可分为两类:一类是通孔,另一类是盲孔。
通孔是指孔底与孔口在同一平面上,而盲孔则是指孔底与孔口不在同一平面上。
二、打孔编程的步骤与方法1.读取零件图纸,了解孔的位置、直径、深度等信息,为编程做好准备。
2.选择合适的编程软件,如CAM软件、UG软件等,根据零件图纸和加工要求进行编程。
3.编写程序,包括以下内容:(1)设定加工中心的工作坐标系,使编程坐标系与工件坐标系一致。
(2)编写孔的加工循环,包括孔的直径、深度、进给速度、切削速度等参数。
(3)编写移位指令,使加工中心在打孔过程中能够自动移位。
(4)编写刀具补偿指令,以保证孔径的精度。
(5)编写安全区域指令,避免加工过程中发生碰撞。
4.模拟加工,检查程序的正确性,调整参数以优化加工过程。
5.实现在线加工,监控加工过程,确保孔的加工质量。
三、编程格式的规范与应用1.编程格式应遵循加工中心的编程规范,如ISO代码、G代码等。
2.编程格式应清晰、简洁,便于阅读和理解。
3.编程格式中的指令应准确无误,确保加工中心能够按照要求进行加工。
4.编程格式中的参数应合理设置,以提高加工效率和加工质量。
四、实际操作中的注意事项1.严格按照零件图纸和加工要求进行编程,确保孔位的精确度。
2.合理选择刀具,根据孔的直径、深度和材料特性选择合适的切削参数。
3.加工过程中注意监控刀具的磨损情况,及时更换刀具以保证孔的加工质量。
任务五孔类零件加工

二、知识讲解
4.钻孔循环指令(G81、G82) (1)钻孔循环(G81) 格式:
G 98 G 81X __ Y __ Z __ R __ F __ L __; G 99
G81指令用于正常钻孔,切削进给执行到孔底, 然后刀具从孔底快速移动退回。G81孔加工动作 如左图所示。 (2)钻孔循环(G82) 格式:
二、知识讲解
(一)孔的技术要求 孔在机械加工中,所占的比例很大,几乎所有的机械 G 43 G 00 产品都有孔,例如,轴类零件、盘类零件、壳体类零 G 44 G 01 件和箱体类零件等。孔按形状可以分为圆柱形孔、圆 锥孔、螺纹孔等。其中圆柱孔又可以分为通孔、台阶 孔和盲孔。但是,由于钻削的精度较低,表面较粗糙, 一般加工精度在IT10以下,表面粗糙度Ra值大于 12.5μm ,生产效率也比较低。因此,钻孔主要用于粗 加工,例如,精度和粗糙度要求不高的螺钉孔、油孔 和螺纹底孔等。但精度和粗糙度要求较高的孔,也要 以钻孔作为预加工工序。
5.高速深孔钻(G73、G83) 格式: G73指令用于深孔钻削,Z轴方向的间断进给有利于深孔加工过程中断屑与排 屑,减少退刀量可以进行高效率的加工。指令Q为每一次进给的加工深度; G73孔加工动作如图所示,图中k为每一次退刀距离,此值由系统确定,无需 用户指定。注意:Z、Q移动量为零时,该指令不执行。
项目四 数控铣床及加工中心 编程基础
任务五 孔类零件加工
一、任务导入
已知图示工件毛坯为 100*80*30mm ,材料为 45# , 编写孔加工程序,进行仿真加工。
二、知识讲解
钻孔知识
1.钻削加工是用钻头在工件上加工孔的一种方法。数控 铣床钻孔时,工件固定不动,刀具做旋转运动(主运 动)的同时沿轴向移动(进给运动)。 2.要编制其加工程序,首先,编程人员应了解孔类零 件刀具的选择与使用方法;其次,根据孔的形状和加 工特点选择合适的固定循环指令;最后,按照数控系 统所规定的加工程序格式进行编程。
数控加工中心典型零件编程实例

X30. Y-30.; 点出C孔位。
X60. Y-30.; 点出D孔位。
G80 G28 G91 Z0; 返回换刀点。
N2 M06 T02; 换2号刀(φ6mm钻头)。
M03 S8越平面,同时执行刀具长度补偿。
X15. Y-45.; 铣削沉孔B。
G80 G28 G91 Z0;
N6 M06 T06; 换6号刀(可调粗镗刀)。
M03 S800;
G43 G90 G0 Z20. H06;
G86 X60. Y-30. R3. Z -17. F100; 镗φ32孔留0.02mm余量。
G80 G28 G91 Z0;
C(X = 30.00 Y = -30.00) D(X = 60.00 Y = -30.00)
4、参考程序
程序段号 O100 程序名
G40 G80 G49; 安全设定。
G28 G91 Z0; 经当前点,返回换刀点。
G28 X0 Y0; 返回机床原点。
G54; 坐标系设定。
G80 G28 G91 Z0;
M5;
M9;
M1; 选择性暂停,控制尺寸。(试件时使用)
N8 M06 T08; 换8号刀(φ8H7铰刀)。
M03 S200;
M8; 冷却液设定。
G43 G90 G0 Z20. H08;
G85 X30. Y-30. R3. Z -19. F50; 铰φ8H7孔。
(1)为保证孔间距精度,先采用中心钻点孔。
(2)采用φ6的钻头钻削两个φ6孔。
(3)采用φ7.8钻头钻削φ8孔留余量0.2mm。
(4)采用φ30钻头钻留余量2mm。
阶梯孔编程及加工

阶梯孔编程及加工【任务引入】本节任务为阶梯孔的加工,数控编程指令在之前的章节已经学习过,重点是掌握孔的加工工艺。
【任务描述】按照给定的程序和要求完成下图5-1所示工件的加工。
图5-1【任务准备】1.内孔车削刀具选择钻孔时,对于精度要求不高的内孔,可用麻花直接钻出;对于精度要求较高的内孔,钻孔后还需要进一步加工才能完成,应留出下道工序的加工余量。
选择麻花钻长度时,一般应使麻花钻加工部分的长度大于孔深,直径以所车削的最小孔来确定。
内孔车刀的种类及用途见表5-1。
表5-1图例用途车削通孔类零件车削盲孔或台阶孔类零件2.内孔车削刀具的安装(1)刀杆伸出刀架的长度应尽可能短,以增加刚度,避免因刀杆弯曲变形,而使孔产生锥形误差,一般比被加工孔长5~6mm。
(2)刀尖应等高或略高于工件旋转中心,以减小振动和扎刀现象,防止车刀下部碰坏孔壁而影响加工精度。
(3)刀杆要装正,应平行于工件轴线,不能歪斜,以防止刀杆后半部分碰到工件孔口。
(4)盲孔车刀装夹时,内偏刀的主切削刃应与孔底成30°~5O°,并且在车削时要求横向有足够的退刀余量。
3.内孔车削刀具的刃磨方法(1)磨主后面,同时磨出主偏角及主后角。
(2)磨副后面,同时磨出副偏角及副后角。
(3)磨前面,同时磨出前角。
(4)修磨各刀面及刀尖。
4.麻花钻安装与找正(1)麻花钻的安装一般情况下,直柄麻花钻安装在钻夹头或钻夹套上,再将钻夹头的锥柄插入尾座锥孔内。
(2)麻花钻找正使钻头的中心与工件的旋转中心对准,否则可能导致孔径钻大、钻偏,甚至折断钻头。
5.钻孔方法钻孔前,应将工件端面车平,以利于钻头定心,即用钻尖略钻人工件,然后摇动尾座手轮,钻出一定的孔深。
也可先在工件的端面上钻出中心孔,然后再用钻头钻削。
6.工步安排原则工步是指在加工表面(或装配时的连接面)和加工(或装配)工具、主轴转速及进给量不变的情况下,所连续完成的那一部分作业。
数控加工划分工步一般应遵循以下原则:(1)先粗后精原则应先切除整个零件的大部分余量,再将其表面精加工一遍,以保证加工精度和表面粗糙度的要求。
孔加工编程与仿真加工介绍课件
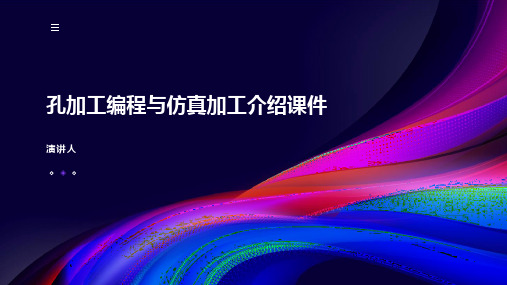
提高加工质量:通过编程和仿真, 提高加工质量,减少质量问题
降低加工成本
01 02 03 04
01
优化加工工艺:通过仿真加工,优 化加工工艺,提高加工效率
02
减少废品率:通过仿真加工,提前 发现并解决加工问题,减少废品率
03
降低设备损耗:通过仿真加工,优 化设备参数,降低设备损耗
自动编程:利用自动编程系统进行孔加工编程, 如FANUC、SIEMENS等 混合编程:结合手工编程和CAM编程,提高编 程效率和精度
编程实例
01
编程步骤:选择孔 加工类型、设定加 工参数、生成加工
程序
02
实例一:钻孔加工, 设定钻头直径、进 给速度、切削深度
等参数
03
实例二:镗孔加工, 设定镗刀直径、进 给速度、切削深度
谢谢
04
提高生产效率:通过仿真加工,缩 短生产周期,提高生产效率
优化加工工艺
1
提高加工效率:通过优化加工工艺, 提高生产效率,降低生产成本。
2
减少废品率:优化加工工艺,减少 废品率,提高产品质量。
3
提高加工精度:优化加工工艺,提 高加工精度,满足产品精度要求。
4
降低能耗:优化加工工艺,降低能 耗,实现绿色生产。
计算机辅助工程(CAE): 利用计算机技术进行工程分
析和优化
4
仿真加工:利用计算机技术 进行加工过程的模拟和优化, 以提高生产效率和产品质量
仿真软件介绍
Mastercam:功能强大, 支持多种数控系统,操作简
单,适合初学者
Cimatron:集成 CAD/CAM/CAE功能,支 持多种数控系统,适合复杂
阶梯孔类零件的工艺分析及数控编程举例(附数控加工工序卡)
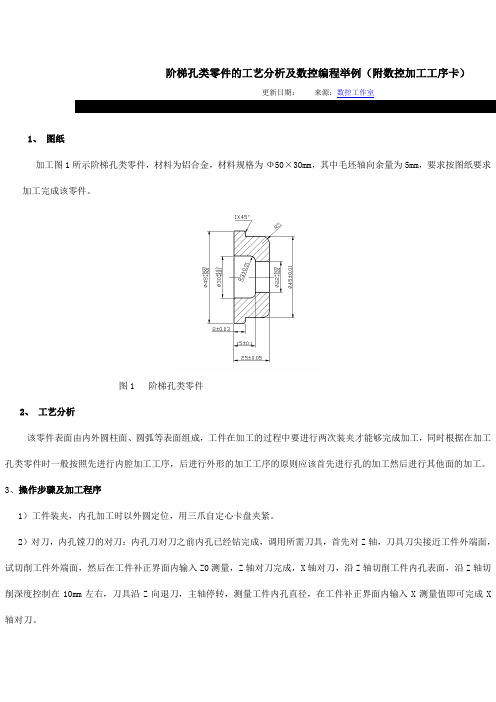
阶梯孔类零件的工艺分析及数控编程举例(附数控加工工序卡)更新日期:来源:数控工作室1、图纸加工图1所示阶梯孔类零件,材料为铝合金,材料规格为Ф50×30mm,其中毛坯轴向余量为5mm,要求按图纸要求加工完成该零件。
图1 阶梯孔类零件2、工艺分析该零件表面由内外圆柱面、圆弧等表面组成,工件在加工的过程中要进行两次装夹才能够完成加工,同时根据在加工孔类零件时一般按照先进行内腔加工工序,后进行外形的加工工序的原则应该首先进行孔的加工然后进行其他面的加工。
3、操作步骤及加工程序1)工件装夹,内孔加工时以外圆定位,用三爪自定心卡盘夹紧。
2)对刀,内孔镗刀的对刀:内孔刀对刀之前内孔已经钻完成,调用所需刀具,首先对Z轴,刀具刀尖接近工件外端面,试切削工件外端面,然后在工件补正界面内输入Z0测量,Z轴对刀完成,X轴对刀,沿Z轴切削工件内孔表面,沿Z轴切削深度控制在10mm左右,刀具沿Z向退刀,主轴停转,测量工件内孔直径,在工件补正界面内输入X测量值即可完成X 轴对刀。
数控加工工序卡3)编写程序1、应用G71内外径粗车复合循环指令进行编程:O0013;G90;(绝对坐标编程)G95;(转化为每转进给)M03S400;(主轴正转400r/min)T0101;(调用一号刀具90°外圆车刀粗加工用)G00X52;Z2;(刀具定位)G71U1R1X0.5Z0.1P10Q11F0.3;(外圆粗车复合循环指令,单边切深为2mm,退刀量为1mm,轴向留量为0.5mm,径向留量为0.1mm)M00;(程序停止)M05;(主轴停转)T0202;(调用二号刀具90°外圆车刀精加工用)G95;(转化为每转进给)G00X50;Z2;(刀具定位)P10G00X35;(刀具快速进给至精加工位置,精加工开始行)G01G42Z0F0.1;(刀具精进给至Z0位置进给量为0.1mm/r)G03X45Z-5R5F0.1;(精加工R5圆弧)G01Z-17;(精加工Ф45尺寸)G00G40X50;(取消刀补)Z100;(刀具退刀至安全位置)M05;(主轴停转)G95;(转化为每转进给)M03S400;(主轴正转400r/min)T0303;(调用三号刀具通孔镗刀粗加工内孔用)G00X18;Z2;(刀具定位)G71U1R1X-0.5Z0.1P12Q13F0.3;(内孔粗车复合循环指令,单边切深为2mm,退刀量为1mm,轴向留量为0.5mm,径向留量为0.1mm)M00;(程序停止)M05;(主轴停转)M03S800;(主轴正转800r/min)T0404;(调用四号刀具通孔镗刀精加工内孔用)G95;(转化为每转进给)G00X18;Z2;(刀具定位)N12G00X30;(刀具快速进给至加工位置)G01G41Z-12F0.1;(精加工Ф30建立刀补进给量为0.1mm/r)G01X22;N13Z-27;(精加工Ф22内孔进给量为0.1mm/r)G00G40X18;(取消刀补)Z100;(刀具退刀至安全位置)M05;(主轴停转)G95;(转化为每转进给)M03S400;(主轴正转400r/min)T0101;(调用一号刀具90°外圆车刀粗加工外圆用)G00X52;Z2;(刀具定位)G71U1R1X0.5Z0.1P14Q15F0.3;(外圆粗车复合循环指令,单边切深为2mm,退刀量为1mm,轴向留量为0.5mm,径向留量为0.1mm)M00;(程序停止)M05;(主轴停转)M03S800;(主轴正转800r/min)G95;(转化为每转进给)T0202;(调用二号刀具90°外圆车刀精加工外圆用)G00X52;Z2;(刀具定位)P14G00X48;(刀具快速进给至加工位置)P15G01G42Z-10F0.1;(精加工Ф48外圆进给量为0.1mm/r)Z100;(刀具退刀至安全位置)M05;(主轴停转)M30;(程序结束返回至程序头)4)试运行5)切削加工。
UG NX6 数控编程教程2(孔加工)

第二章点位加工本章要点1.点位加工概述2.点位加工几何体设置3.点位加工循环参数设置4.点位加工一般参数设置2.1 点位加工概述点位加工是一种相当常见的机械加工方法,如图2-1所示的工件。
点位加工包括钻孔、镗孔、扩孔、铰孔、点焊和铆接等,UG NX6可为各种点位加工操作创建刀具路径,如图2-2所示。
点位加工的刀具运动由3部分组成:首先刀具快速定位在加工位置上,然后切入零件,完成切削后退回。
图2-1 点位加工工件图2-2 点位加工刀轨2.1.1 操作安全点在点位加工中,操作安全点是每个切削运动的起点和终点,也是进刀、退刀、避让、快速移刀等辅助运动的起点和终点。
通常,刀具将以快速或进刀进给率向操作安全点运动,刀具从操作安全点向部件表面上的刀位点运动时,以及切削至指定深度的过程将使用切削进给率,如图2-3所示。
但是,如果一个循环处于活动状态,系统将使用“循环参数”菜单中指定的循环进给率。
图2-3 最小安全距离及刀具运动速率2.1.2 加工循环数控系统对典型加工中几个固定或连续动作用同一个指令来指定,完成本来要用多个程序段指令完成的加工动作,这个指令就是加工循环指令。
为了满足不同类型孔的加工要求,UG在点位加工中提供了多种循环类型,控制刀具的切削运动过程。
点位加工操作就是选择合理的加工循环并进行合理的参数设定的过程。
点位加工操作循环也称作固定循环,通常包括的基本动作如下:1.精确定位。
2.以快进或进刀速度移动至操作安全点。
3.以切削速度运动至零件表面上的加工位置点。
4.以切削速度或循环进给率加工至孔最深处。
5.孔底动作(暂停、让刀等)。
6.以退刀速度或快进速度退回操作安全点。
7.快速运行至安全平面(安全平面被激活)。
2.2 点位加工几何体设置为了创建点位加工刀轨,需要定义点位加工几何体。
点位加工几何的设置包括指定孔、部件表面和底面3种加工几何,其中孔为必选项,而部件表面和底面为可选项,如图2-4所示。
图2-4 点位加工几何体2.2.1 指定加工位置在“钻”对话框几何体组中单击“指定孔”图标,系统弹出“点到点几何体”对话框,其中“选择”选项用于选择孔加工的点位几何对象(这些几何对象可以是一般点、圆弧、圆、椭圆以及实心体或片体上的孔),其余选项用于编辑已指定的点位,如图2-5所示。
数控车床的孔加工编程方法举例
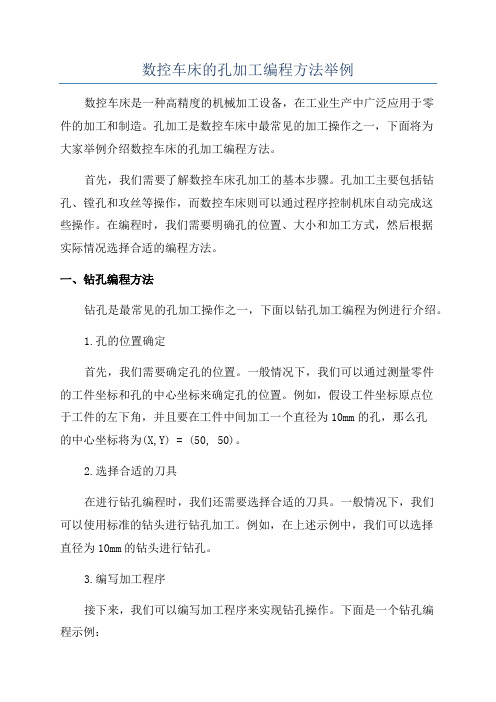
数控车床的孔加工编程方法举例数控车床是一种高精度的机械加工设备,在工业生产中广泛应用于零件的加工和制造。
孔加工是数控车床中最常见的加工操作之一,下面将为大家举例介绍数控车床的孔加工编程方法。
首先,我们需要了解数控车床孔加工的基本步骤。
孔加工主要包括钻孔、镗孔和攻丝等操作,而数控车床则可以通过程序控制机床自动完成这些操作。
在编程时,我们需要明确孔的位置、大小和加工方式,然后根据实际情况选择合适的编程方法。
一、钻孔编程方法钻孔是最常见的孔加工操作之一,下面以钻孔加工编程为例进行介绍。
1.孔的位置确定首先,我们需要确定孔的位置。
一般情况下,我们可以通过测量零件的工件坐标和孔的中心坐标来确定孔的位置。
例如,假设工件坐标原点位于工件的左下角,并且要在工件中间加工一个直径为10mm的孔,那么孔的中心坐标将为(X,Y) = (50, 50)。
2.选择合适的刀具在进行钻孔编程时,我们还需要选择合适的刀具。
一般情况下,我们可以使用标准的钻头进行钻孔加工。
例如,在上述示例中,我们可以选择直径为10mm的钻头进行钻孔。
3.编写加工程序接下来,我们可以编写加工程序来实现钻孔操作。
下面是一个钻孔编程示例:O0001(程序号)N1G90G54G64G80(绝对坐标系,工件坐标系,等距插补模式,取消固定循环)N2S500M3(设置主轴转速为500转/分钟,开启主轴)N3G0X50Y50(快速定位到孔的中心坐标)N4 G81 Z-10 R2 F100 (启动钻孔循环,Z轴下降10mm,每次进刀2mm,进给速度为100mm/分钟)N5G80(取消固定循环)N6M5(关闭主轴)N7M30(程序结束)在上述示例中,首先通过G90指令设置绝对坐标系和工件坐标系。
然后通过G64指令设置等距插补模式,取消固定循环。
接着,通过G0指令进行快速定位,将刀具移动到孔的中心坐标处。
然后通过G81指令启动钻孔循环,设置Z轴下降10mm,每次进刀2mm,进给速度为100mm/分钟。
数控加工程序编制-加工中心-孔类零件程序编制全解

G88循环
二、相关知识
(二)固定循环功能
(5)精镗循环(G76) 指令格式: G76 X_ Y_ Z_ R_ Q_ F_
精镗时,主轴在孔底定向停止后,向刀尖反方向移 动,然后快速退刀。
这种带有让刀的退刀不会划伤已加工平面,保证了 镗孔精度。
程序格式中,Q 表示刀尖的偏移量,一般为正数, 移动方向由机床参数设定。
1
钻中心孔
2
钻φ5mm通孔
3
攻丝
螺纹孔加工工序卡
刀具规格
类型
材料
A4中心钻
高速钢
Φ4.2mm麻花钻 高速钢
M5mm细牙丝锥 高速钢
主轴转速 (r/min)
1200 600 80
进给速度 (mm/min)
20 30 64
(6)编制零件螺纹孔钻中心孔加工程序
四、拓展知识
用西门子802D孔及螺纹加工循环指令加工图零件。
(二)固定循环功能
(2)带停顿的钻孔循环(G82) 指令格式:
G82 X_Y_Z_P_R_F_
G82循环
该指令除了要在孔底暂停外,其它动作与G81相同。暂 停时间由地址P给出。此指令主要用于加工盲孔,以提 高孔深精度。
二、相关知识
(二)固定循环功能
(3)断屑式深孔加工循环(G73)
指令格式: G73 X_Y_Z_Q_R_F_
三、工作任务的完成
(一)数控加工工艺的制订
4.刀具准备,填写刀具卡
序号
1 2 3
4
5 6 7
刀具号
T05 T06 T07
名称 麻花钻 麻花钻 镗刀
T08 镗刀
T09 中心钻 T10 机用铰刀 T11 麻花钻
刀具规格 直径
加工中心的孔加工编程及技巧

《加工中心的孔加工编程及技巧》2005年5月25日加工中心的孔加工编程及技巧摘要:孔加工在数控加工中一直占有重要的地位,如何在加工过程中按照合理的工艺编制出正确的加工程序是非常关键的因素。
关键词:孔加工固定循环子程序极坐标一、引言孔加工在数控加工中一直占有重要的地位。
在合理的加工工艺编制好以后如何编制出正确的程序将直接影响到工件是否加工合格。
复杂的孔加工将用到数控系统中的许多功能。
诸如:孔加工固定循环、子程序、极坐标、坐标旋转等。
因此,如何将这些指令灵活应用在加工的程序中将直接关系到程序的合理性。
二、应用实例下面就以一个定位连接板(图1)作为实例,介绍该类程序的编制及技巧。
1、技术要求:1)零件材料:灰铸铁HT2002)加工部位:加粗部分(φ110,2-φ70H7),8-M12深15,18-φ13深20。
3)加工说明:φ70H7预孔为铸造,余量5mm。
基准面A、B、C、D前工序已完成。
夹具形式不用考虑,φ110孔用铣削方式。
4)数控机床:立式加工中心VMC800;数控系统:FANUC 0iM5)按数控工序卡片编制加工中心程序。
6)程序编制方法:固定循环、子程序、坐标系旋转、极坐标指令等图1 定位连接板2、加工工艺3、加工程序主程序O0001;第0001号程序,加工主程序;建立工件坐标系,并运动到φ70H7孔的中心位置N10T02M6;调用02号刀具(粗镗φ);刀具长度正补偿,并运动到安全高度M03S380;主轴正转M08;打开冷却液;调用粗加工固定循环加工φ70H7孔至φ;在位置继续加工G80;取消固定循环N20T03M6;调用03号刀具(φ40立铣刀铣φ110孔);快速定位到φ110孔的中心位置;刀具长度正补偿,并运动到安全高度M3S420;主轴正转;下刀至第一次的深度位置(粗加工)M98P0501;调用0501号子程序S560;下刀至第二次的深度位置(半精加工)M98P0501;调用0501号子程序M01;检查尺寸。
数控铣床加工中心加工工艺编程与操作孔槽类工件加工
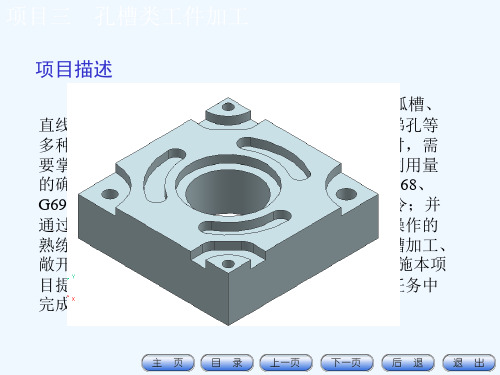
任务1 钻孔加工
4)固定循环的两种返回方式
注意: G98返回初始平面。 G99返回安全平面。
任务1 钻孔加工
固定循环的两种返回方式动画演示
任务1 钻孔加工
G98、G99两种返回方式的应用区别
任务1 钻孔加工
(2)G81、G82钻孔循环指令详解 1)G81、G82指令格式: G81 X Y Z R F K ; G82 X Y Z R P F K ;
任务1 钻孔加工
2、孔加工路线及余量的确定
(3)孔加工时各工序间余量确定
加工工序
加工直径 (毫米)
工序特点
扩孔
10~20 20~50
钻孔后扩孔 粗扩后精扩 钻孔后扩孔 粗扩后精扩
10~20
铰孔
20~30 30~50
50~80
80~100
半精镗
20~80 80~150
精镗
<30 30~130
>130
任务1 钻孔加工 相关知识:
1、孔加工方法选择及常见孔加工刀具 2、孔加工路线及余量的确定 3、钻孔加工固定循环指令
任务1 钻孔加工
1、孔加工方法选择及常见孔加工刀具
序号 1 2 3 4 5 6 7
8
9
加工方案
钻 钻—铰 钻—粗铰(扩)—精铰
钻—扩 钻—扩—铰 钻—扩—粗铰—精铰
粗镗(扩孔) 粗镗(扩孔) —半精镗
暂停、主轴正转 主轴准停 — — 暂停 —
暂停、主轴正转 —
主轴停 主轴正转 暂停、主轴停
暂停
退刀动作 快速进给 快速进给 快速进给
— 快速进给 快速进给 快速进给 切削进给 切削进给 快速进给 快速进给 手动进给 切削进给
用途 高速深孔加工 攻左旋螺纹
数控车(铣)床编程与操作课题1 通孔类零件加工
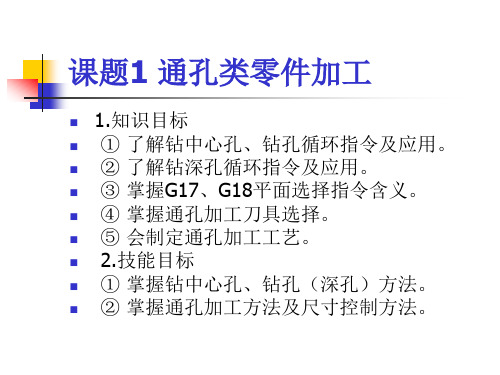
两种方案加工路线差不多。具体步骤见加工工 艺(表3-5)。
3.选择合理切削用量
工步号
1 2 3 4 5 6
7 8
表3-5通孔零件加工工艺
工步内容
刀具号
车右端面
T01
粗、精车φ34、φ30外圆至尺寸
程序段号
程序内容 (法那克系统)
N10 G40 G99 G80 G18
N20 T0505
N30 M3 S600
N40 G00 X17.6 Z3
N50 G01 Z-43 F0.15
N60 X17
N70 G00 Z3
程序内容 (西门子系统) G40 G90 G95 G18 T05 D1 M3 S600 G00 X17.6 Z3 G01 Z-43 F0.15 X17 G00 Z3
3.钻深孔循环指令
(1)指令功能 通过分步钻入直至达到给定的钻削深度, 在每步钻削时通过刀具退回且停顿一定 时间达到断屑或排屑目的,最后刀具以 快速移动速度退回。
(2)指令格式 法那克系统与西门子系统深孔钻削循环 指令见表3-3。
(3)指令使用说明
1)调用钻孔循环G83(LCYC83)前应先指定主轴转速和方向。 2)调用西门子钻孔循环(LCYC83)前,刀具应处于钻孔位置;
刀具沿-X方向进刀,转速为 800r/min 精车φ30外圆 精车台阶面 精车φ34外圆 刀具沿+X方向退出 刀具退回至换刀点 程序停、主轴停、测量 换中心钻 设置钻中心孔转速 刀具移动至循环起点
设置循环参数,调用钻孔循环钻 中心孔
刀具退回至换刀点 换麻花钻 设置钻孔速度 钻头移动至循环起点
阶梯孔编程及加工

阶梯孔编程及加工【任务引入】本节任务为阶梯孔的加工,数控编程指令在之前的章节已经学习过,重点是掌握孔的加工工艺。
【任务描述】按照给定的程序和要求完成下图5-1所示工件的加工。
图5-1【任务准备】1.内孔车削刀具选择钻孔时,对于精度要求不高的内孔,可用麻花直接钻出;对于精度要求较高的内孔,钻孔后还需要进一步加工才能完成,应留出下道工序的加工余量。
选择麻花钻长度时,一般应使麻花钻加工部分的长度大于孔深,直径以所车削的最小孔来确定。
内孔车刀的种类及用途见表5-1。
表5-1图例用途车削通孔类零件车削盲孔或台阶孔类零件2.内孔车削刀具的安装(1)刀杆伸出刀架的长度应尽可能短,以增加刚度,避免因刀杆弯曲变形,而使孔产生锥形误差,一般比被加工孔长5~6mm。
(2)刀尖应等高或略高于工件旋转中心,以减小振动和扎刀现象,防止车刀下部碰坏孔壁而影响加工精度。
(3)刀杆要装正,应平行于工件轴线,不能歪斜,以防止刀杆后半部分碰到工件孔口。
(4)盲孔车刀装夹时,内偏刀的主切削刃应与孔底成30°~5O°,并且在车削时要求横向有足够的退刀余量。
3.内孔车削刀具的刃磨方法(1)磨主后面,同时磨出主偏角及主后角。
(2)磨副后面,同时磨出副偏角及副后角。
(3)磨前面,同时磨出前角。
(4)修磨各刀面及刀尖。
4.麻花钻安装与找正(1)麻花钻的安装一般情况下,直柄麻花钻安装在钻夹头或钻夹套上,再将钻夹头的锥柄插入尾座锥孔内。
(2)麻花钻找正使钻头的中心与工件的旋转中心对准,否则可能导致孔径钻大、钻偏,甚至折断钻头。
5.钻孔方法钻孔前,应将工件端面车平,以利于钻头定心,即用钻尖略钻人工件,然后摇动尾座手轮,钻出一定的孔深。
也可先在工件的端面上钻出中心孔,然后再用钻头钻削。
6.工步安排原则工步是指在加工表面(或装配时的连接面)和加工(或装配)工具、主轴转速及进给量不变的情况下,所连续完成的那一部分作业。
数控加工划分工步一般应遵循以下原则:(1)先粗后精原则应先切除整个零件的大部分余量,再将其表面精加工一遍,以保证加工精度和表面粗糙度的要求。
- 1、下载文档前请自行甄别文档内容的完整性,平台不提供额外的编辑、内容补充、找答案等附加服务。
- 2、"仅部分预览"的文档,不可在线预览部分如存在完整性等问题,可反馈申请退款(可完整预览的文档不适用该条件!)。
- 3、如文档侵犯您的权益,请联系客服反馈,我们会尽快为您处理(人工客服工作时间:9:00-18:30)。
项目四孔类零件编程方法
2008年10月13日
(总第13、14课时)
教学目的:能正确制定孔加工的加工工艺
掌握阶梯孔工件的编程方法
熟练运用仿真软件加工孔类零件
教学重点:孔加工的方法确定
教学难点:孔的编成方法
教学方法:多媒体教学
课型:新授
课时安排:2课时
教学过程:
导入:在数控车床上加工工件时往往会遇到各种各样的孔,通过钻、铰、镗、扩等可以加
新授:
45钢φ65×80 棒料
三、装夹方式:
以工件的左端面及φ50外圆为安装基准,夹于车床卡盘上。
四、工艺分析:
可用钻孔、粗镗孔、精镗孔方式加工内孔,然后外圆加工,一次装夹完成各表面的加工。
五、加工过程:
车端面;
对刀;
用φ38钻头手动钻内孔;
换镗刀,镗内孔各表面;
粗精车60外圆、右倒角。
六、刀具选择:
Φ38钻头置于尾座
硬质合金不通孔镗刀,置于T02刀位
硬质合金90度偏刀,加工倒角及外圆,置于T01刀位
七、确定切削用量:
八、编写加工程序:
o1245;
T0101(外圆)
M3S700
G0X65.Z2.
G71U2.R1.
G71P10Q20U0.5W0.1F0.25 N10G0X57.983
G1Z0F0.1
X59.983Z-1.
Z-60.
N20G0X65.
X100.Z100.M5M0
T0101
M3S1000
G0X65.Z2.
G70P10Q20
G0X100.Z100.M5M0
T0202(镗孔)
M3S500
G0X38.Z2.
G71U1.5R1.
G71P30Q40U-0.3W0.05F0.15 N30G0X50.018
G1Z0F0.1
Z-40.
X40.018
Z-60.
N40G0X38.
X100.Z100.M5M0
T0202
M3S1000
G0X38.Z2.
G70P30Q40
G0X100.Z100.
M30
课堂练习:
知识小结:本节课主要讲了阶梯孔的加工工艺及编程示例,为下节课
作业:
教学后记和反馈:
个别学生没有注意到用G71复合循环指令编程中在孔加工时应U的值应取负值。