套筒类零件的加工工艺
套筒类零件加工工艺处理与分析
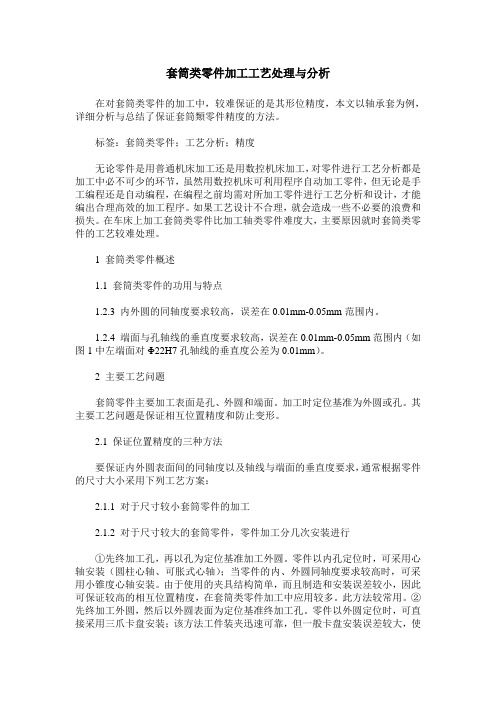
套筒类零件加工工艺处理与分析在对套筒类零件的加工中,较难保证的是其形位精度,本文以轴承套为例,详细分析与总结了保证套筒類零件精度的方法。
标签:套筒类零件;工艺分析;精度无论零件是用普通机床加工还是用数控机床加工,对零件进行工艺分析都是加工中必不可少的环节,虽然用数控机床可利用程序自动加工零件,但无论是手工编程还是自动编程,在编程之前均需对所加工零件进行工艺分析和设计,才能编出合理高效的加工程序。
如果工艺设计不合理,就会造成一些不必要的浪费和损失。
在车床上加工套筒类零件比加工轴类零件难度大,主要原因就时套筒类零件的工艺较难处理。
1 套筒类零件概述1.1 套筒类零件的功用与特点1.2.3 内外圆的同轴度要求较高,误差在0.01mm-0.05mm范围内。
1.2.4 端面与孔轴线的垂直度要求较高,误差在0.01mm-0.05mm范围内(如图1中左端面对Φ22H7孔轴线的垂直度公差为0.01mm)。
2 主要工艺问题套筒零件主要加工表面是孔、外圆和端面。
加工时定位基准为外圆或孔。
其主要工艺问题是保证相互位置精度和防止变形。
2.1 保证位置精度的三种方法要保证内外圆表面间的同轴度以及轴线与端面的垂直度要求,通常根据零件的尺寸大小采用下列工艺方案:2.1.1 对于尺寸较小套筒零件的加工2.1.2 对于尺寸较大的套筒零件,零件加工分几次安装进行①先终加工孔,再以孔为定位基准加工外圆。
零件以内孔定位时,可采用心轴安装(圆柱心轴、可胀式心轴);当零件的内、外圆同轴度要求较高时,可采用小锥度心轴安装。
由于使用的夹具结构简单,而且制造和安装误差较小,因此可保证较高的相互位置精度,在套筒类零件加工中应用较多。
此方法较常用。
②先终加工外圆,然后以外圆表面为定位基准终加工孔。
零件以外圆定位时,可直接采用三爪卡盘安装;该方法工件装夹迅速可靠,但一般卡盘安装误差较大,使得加工后工件的相互位置精度较低。
如果欲使同轴度误差较小,则须采用定心精度较高的夹具,如弹性膜片卡盘,液性塑料夹头、经过修磨的三爪自定心卡盘和软爪等。
套筒类零件加工

3.保证相互位置精度的方法 (1)在一次装夹中完成所有内孔与外圆表面及端面的加工。一般
在卧式车床或立式车床上进行,精加工也可以在磨床上进行。此时, 常用三爪卡盘或四爪卡盘装夹工件,分别如图(a)、(b)所示。这 种安装方法可消除由于多次安装而带来的安装误差,保证零件内孔与 外圆的同轴度及端面与内孔轴线的垂直度。但是这种安装方法由于工 序比较集中,对尺寸较大(尤其是长径比较大)的套筒安装不方便, 故多用于尺寸较小的套筒的车削加工。对于凸缘的短套筒,可先车凸 缘端,然后掉头夹压凸缘端,这种安装方法可防止因套筒刚度降低而 产生的变形,如图(c)所示。
(1)液压缸体的材料。液压缸体的材料一般有铸铁和无缝钢管
两种。本例采用无缝钢管。
(2)液压缸体表面加工方法。82h6 mm外圆加工精度为IT6,
加工方法采用粗车、精车。内孔加工精度较高,粗加工采用半精镗,
半精加工采用精镗,精加工采用浮动镗,光整加工采用滚压。
(3
82h6 mm外圆作为定位基准
加工内孔。
短套筒的安装
(2)全部加工分在几次装夹中进行,先加工孔,然后以孔作为定位 基准加工外圆表面。用这种方法加工套筒,以精加工好的内孔作为精基 准最终加工外圆。当以内孔为精基准加工外圆时,常用锥度心轴装夹工 件,并用两顶尖支承心轴。由于锥度心轴结构简单,制造、安装误差较 小,因而可以保证比较高的同轴度要求,是套筒加工中常见的装夹方法。
4.防止套筒变形的措施
1)减小切削力和切削热对套筒变形的 影响
减小切削力和切削热对套筒变形影响的 措施如下:
(1)粗、精加工应分开进行,并应严格 控制精加工的切削用量,以减小零件加工时 的变形。
(2)内、外表面同时加工,使径向力相ቤተ መጻሕፍቲ ባይዱ互抵消,如图所示。
套筒零件的加工工艺分析及编程
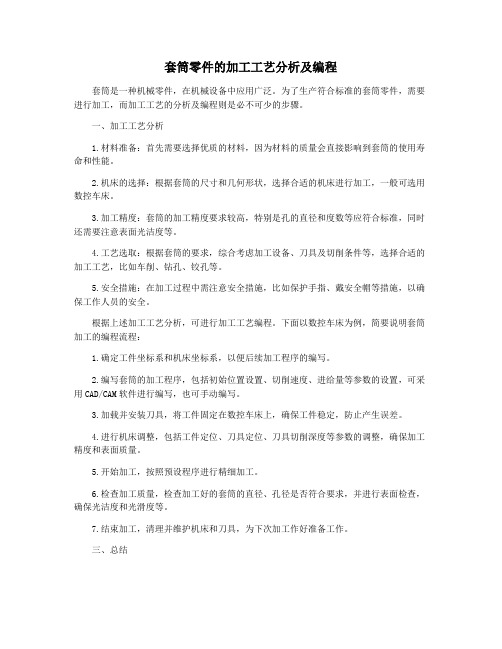
套筒零件的加工工艺分析及编程
套筒是一种机械零件,在机械设备中应用广泛。
为了生产符合标准的套筒零件,需要进行加工,而加工工艺的分析及编程则是必不可少的步骤。
一、加工工艺分析
1.材料准备:首先需要选择优质的材料,因为材料的质量会直接影响到套筒的使用寿命和性能。
2.机床的选择:根据套筒的尺寸和几何形状,选择合适的机床进行加工,一般可选用数控车床。
3.加工精度:套筒的加工精度要求较高,特别是孔的直径和度数等应符合标准,同时还需要注意表面光洁度等。
4.工艺选取:根据套筒的要求,综合考虑加工设备、刀具及切削条件等,选择合适的加工工艺,比如车削、钻孔、铰孔等。
5.安全措施:在加工过程中需注意安全措施,比如保护手指、戴安全帽等措施,以确保工作人员的安全。
根据上述加工工艺分析,可进行加工工艺编程。
下面以数控车床为例,简要说明套筒加工的编程流程:
1.确定工件坐标系和机床坐标系,以便后续加工程序的编写。
2.编写套筒的加工程序,包括初始位置设置、切削速度、进给量等参数的设置,可采用CAD/CAM软件进行编写,也可手动编写。
3.加载并安装刀具,将工件固定在数控车床上,确保工件稳定,防止产生误差。
4.进行机床调整,包括工件定位、刀具定位、刀具切削深度等参数的调整,确保加工精度和表面质量。
5.开始加工,按照预设程序进行精细加工。
6.检查加工质量,检查加工好的套筒的直径、孔径是否符合要求,并进行表面检查,确保光洁度和光滑度等。
7.结束加工,清理并维护机床和刀具,为下次加工作好准备工作。
三、总结。
薄壁套筒零件加工工艺
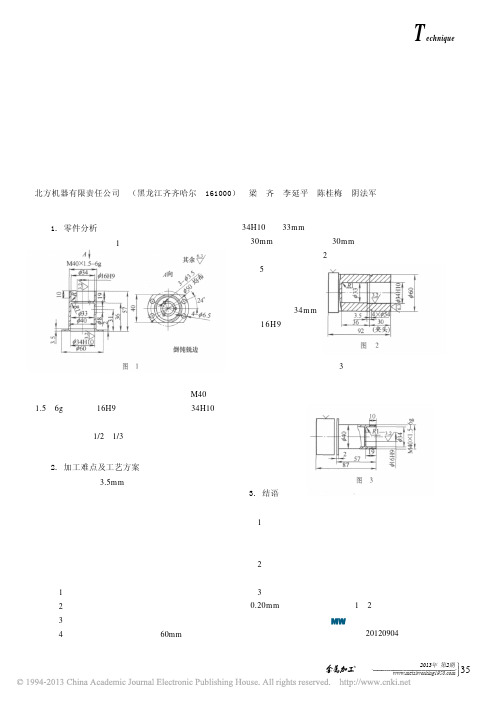
35echniqueT工 艺1. 零件分析典型薄壁套筒如图1所示。
图 1此零件属于薄壁套筒类零件,从图样上看,工艺没有难点。
但是从装配图面上看,外螺纹M40×1.5-6g 与内孔φ16H9及另一端面内止口φ34H10都有同轴度要求,在图样上不给出同轴度要求,加工中可取公差的1/2或1/3。
按正常加工方法很难保证产品图样要求。
2. 加工难点及工艺方案此零件壁厚为3.5mm ,按正常加工方法一次装夹中完成外圆及内孔并切断,设计夹具装夹,车另一端面及内孔。
但是外圆要求不严,壁又薄,用夹具装夹必须提高外圆精度,才能保证产品要求。
这样无形中增加工艺成本,所以说,此零件加工难点就是装夹加工方面。
为避免加工中的变形,特制定加工工艺方案如下:(1)毛坯选择单件下料,包括夹头尺寸。
(2)粗加工内孔,单边留量。
(3)调质处理。
(4)车端面,车外圆到尺寸φ60mm ,车内孔φ34H10及φ33mm 到尺寸,保持深度尺寸(加上夹头30mm ),距端面尺寸30mm 内车外空刀(空刀为夹头切断处),如图2所示。
(5)按外圆找正,装夹(夹头)零件,车端面,保持全长尺寸,车内孔φ34m m 及孔φ16H9定寸,保持深度尺寸,车外圆及外螺纹定寸,按空刀槽切断保证产品质量要求,如图3所示。
此方法加工套筒,增加夹头,可以保证产品质量,加工中没有变形,但是此方法适用于小批量生产零件,不适用大批量生产。
大批量生产最好设计车用夹具,零件定寸基准必须加严才能适用于夹具定位。
3. 结语加工薄壁套筒应注意以下几点:(1)多次装夹完成的套筒,如内孔精度高,可设计车用心轴,定心精度高,可保证较高的形位公差要求。
(2)多次装夹完成的套筒,如外圆精度高,可设计弹性夹具,零件装夹可靠。
(3)如果套筒壁薄,精度高还可以精加工后再留0.20mm ,卸下零件自然时效1~2天后,再从新装夹加工防止加工变形。
(收稿日期:20120904)北方机器有限责任公司 (黑龙江齐齐哈尔 161000) 梁 齐 李延平 陈桂梅 阴法军薄壁套筒零件加工工艺图 2图 3。
套筒类零件的加工工艺及夹具设计

套筒类零件的加工工艺及夹具设计套筒是一种常用的机械零件,广泛应用于汽车、机械设备等领域。
套筒的加工工艺及夹具设计对于产品质量和生产效率有着重要影响。
下面将从套筒类零件的加工工艺和夹具设计两个方面进行详细介绍。
一、套筒类零件的加工工艺1.材料选择:套筒常用的材料有铸铁、合金钢等。
根据产品的要求和使用环境选择合适的材料。
2.工艺规划:在确定套筒的形状和尺寸后,进行工艺规划。
包括确定加工顺序、加工方法、工艺参数等。
3.车削:套筒类零件的加工通常采用车削加工。
首先是粗车削,将套筒的外径、内径和长度粗略加工到指定尺寸。
然后进行精车削,将尺寸加工到精度要求的范围内。
4.放电加工:对于一些工艺要求高、难以进行车削的套筒类零件,可以采用放电加工。
通过电火花的烧蚀和溶解作用,使套筒的表面精度得到提高。
5.热处理:对于一些要求硬度和耐磨性的套筒类零件,可以进行热处理。
热处理方法包括淬火、调质等,可以提高套筒的使用寿命和性能。
6.光洁处理:对于一些外观要求高的套筒类零件,可以进行光洁处理。
包括抛光、喷砂等方法,使套筒表面变得光滑。
二、套筒类零件的夹具设计1.夹具类型选择:根据工件的形状和加工要求选择合适的夹具类型。
常用的夹具类型有卡盘夹具、槽铣夹具等。
2.夹紧力设计:根据套筒的材料和形状,设计夹具的夹紧力。
夹紧力要足够大,保证工件的刚性和位置精度。
3.夹具定位设计:设计夹具的定位方式,保证工件在加工过程中的位置精度。
常用的定位方式有销针定位、销楔定位等。
4.夹具结构设计:根据套筒的特点和工艺要求,设计夹具的结构。
包括夹具机构、夹具部件的尺寸和材料等。
5.夹具刀具设计:根据加工工艺的要求,设计夹具的刀具。
包括车刀、铣刀等。
刀具要具备良好的切削性能和耐磨性。
6.夹具的安装和调试:根据设计要求,进行夹具的安装和调试。
确保夹具能够正常工作并满足加工要求。
以上是关于套筒类零件的加工工艺及夹具设计的详细介绍。
加工工艺的合理选择和夹具的设计可以有效提高套筒类零件的加工效率和产品质量。
车床尾座套筒加工工艺及夹具设计

车床尾座套筒加工工艺及夹具设计一、车床尾座套筒加工工艺1.材料准备:选用合适的材料进行加工,一般选择高强度、耐磨损的材料。
2.车削工序:先将材料锯成适当的长度,然后进入车床车削工序。
先进行外圆车削,保证材料的尺寸和精度;然后进行内圆车削,加工套筒的内孔。
3.铣削工序:根据套筒的设计要求,进行铣削工序,加工套筒的平面和各种形状的凹陷部分。
4.螺纹加工:如果套筒需要有螺纹的部分,则进行螺纹加工,一般使用车床进行内和外螺纹的切削。
5.电火花加工:如果套筒需要有精密的小孔或者细长的槽,可以选择电火花加工进行加工。
6.整体校对:最后对加工好的尺寸进行校对,确保加工精度和尺寸要求。
二、夹具设计夹具是加工过程中用于固定工件、定位加工刀具的装置。
为了保证车床尾座套筒的加工质量和效率,需要设计合理的夹具。
以下是夹具设计的一般步骤:1.夹具功能要求:确定夹具的基本功能要求,如固定工件、定位刀具、方便加工等。
2.工件定位:根据尺寸和形状要求,确定工件在夹具中的定位方式,如使用止削装置、夹紧块等。
3.工件固定:确定工件在夹具中的固定方式,如使用螺栓、夹紧块、弹性夹具等。
4.夹具切削力分析:根据加工过程中的切削力分析,确定夹具的刚性和耐力要求,避免因切削力导致夹具变形或破坏。
5.夹具结构设计:根据以上要求,设计夹具的结构和形状,包括夹具底座、定位装置、夹紧装置等。
6.夹具制造和安装:根据设计图纸制作夹具零部件,然后进行组装和安装。
以上是车床尾座套筒加工工艺及夹具设计的基本介绍,具体的加工工艺和夹具设计需要根据实际情况进行详细分析和设计。
合理的加工工艺和夹具设计可以提高加工效率和产品质量。
套筒类零件加工工艺规程
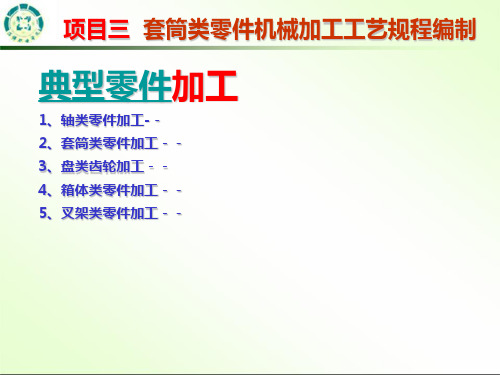
分类
项目三 套筒类零件机械加工工艺规程编制
图6-1 各类套筒零件 a )、 b )滑动轴承 c )钻套 d ) 轴承衬套 e )气缸套 f )液压缸
项目三 套筒类零件机械加工工艺规程编制
套筒类零件 套筒类零件的结构
套筒类零件在机械中应用十分广泛。 其加工表面主要有端面、外圆表面、内圆(孔)表面。 端面和外圆加工,通常在车床上进行。 套筒类零件的内孔,作为支承或导向的主要表面,其加 工方法根据使用的刀具不同,通常采用车孔、钻孔(包 括扩孔、锪孔)、铰孔、镗孔、拉孔、磨孔以及各种孔 的光整加工和特种加工等。
复习: 机床夹具设计基础 1、机床夹具设计基础
夹具的组成:
机床夹具
定位装置
夹紧装置
其他装置 或元件
夹具体
Text
项目三
套筒类零件机械加工工艺规程编制
钻床夹具设计特点
1)钻床夹具的主要类型
◆在钻床上进行孔的钻、扩、铰、 锪、攻螺纹等加工所用的夹具称 为钻床夹具,也称钻模。
项目三
套筒类零件机械加工工艺规程编制
项目三 套筒类零件机械加工工艺规程编制 相关知识:
一、车孔 2.车孔的关键技术是解决内孔车刀的刚性和排屑问题。 1)尽量增加刀杆的截面积,使内孔车刀的刀尖位于刀杆的中心 线上。 2)刀杆的伸出长度尽可能缩短,使刀杆伸出长度略大于孔深即 可。 3)为了使内孔车刀的后面既不和工件孔面发生干涉和摩擦,也 不使内孔车刀的后角磨得过大时削弱刀尖强度,内孔车刀的后 面一般磨成两个后角的形式。 4)为了使已加工表面不致于被切屑划伤,通孔的内孔车刀最好 磨成正刃倾角,切屑流向待加工表面(前排屑)。不通孔的内 孔车刀当然无法从前端排屑,只能从后端排屑,所以刃倾角一 般取-2°~0°。
套筒生产工艺
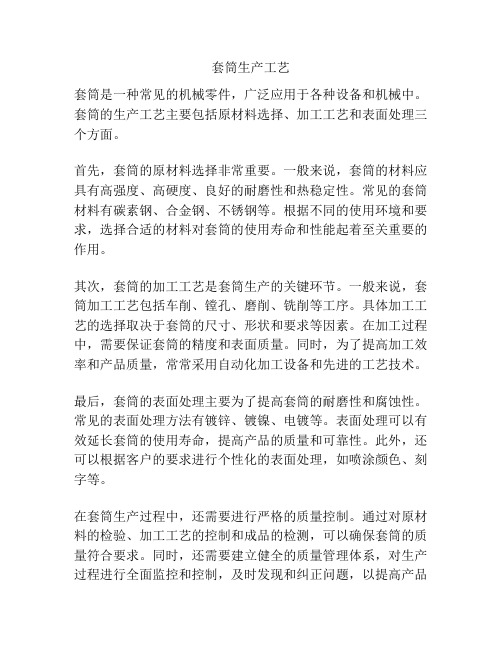
套筒生产工艺
套筒是一种常见的机械零件,广泛应用于各种设备和机械中。
套筒的生产工艺主要包括原材料选择、加工工艺和表面处理三个方面。
首先,套筒的原材料选择非常重要。
一般来说,套筒的材料应具有高强度、高硬度、良好的耐磨性和热稳定性。
常见的套筒材料有碳素钢、合金钢、不锈钢等。
根据不同的使用环境和要求,选择合适的材料对套筒的使用寿命和性能起着至关重要的作用。
其次,套筒的加工工艺是套筒生产的关键环节。
一般来说,套筒加工工艺包括车削、镗孔、磨削、铣削等工序。
具体加工工艺的选择取决于套筒的尺寸、形状和要求等因素。
在加工过程中,需要保证套筒的精度和表面质量。
同时,为了提高加工效率和产品质量,常常采用自动化加工设备和先进的工艺技术。
最后,套筒的表面处理主要为了提高套筒的耐磨性和腐蚀性。
常见的表面处理方法有镀锌、镀镍、电镀等。
表面处理可以有效延长套筒的使用寿命,提高产品的质量和可靠性。
此外,还可以根据客户的要求进行个性化的表面处理,如喷涂颜色、刻字等。
在套筒生产过程中,还需要进行严格的质量控制。
通过对原材料的检验、加工工艺的控制和成品的检测,可以确保套筒的质量符合要求。
同时,还需要建立健全的质量管理体系,对生产过程进行全面监控和控制,及时发现和纠正问题,以提高产品
的一致性和可靠性。
综上所述,套筒的生产工艺涵盖了原材料选择、加工工艺和表面处理等多个环节。
通过科学合理的工艺流程和质量控制措施,可以生产出符合要求的套筒产品。
提高套筒的生产效率和质量水平对于提升企业竞争力和满足客户需求具有重要意义。
定位套筒零件的机械加工工艺设计

定位套筒是一种常见的机械零件,用于实现零件的定位和固定。
以下是定位套筒零件的机械加工工艺设计的一般步骤:
1.确定零件的材料:根据定位套筒的使用环境和要求,选择合适的材料,如钢、铝合
金等。
2.设计零件的几何形状:根据零件的功能和装配要求,确定定位套筒的几何形状,包
括外径、内径、长度等参数。
3.绘制工艺图纸:根据零件的几何形状和尺寸要求,绘制详细的工艺图纸,包括三视
图、剖视图和加工标记等。
4.确定加工工艺:根据零件的几何形状和工艺要求,确定合适的加工工艺,包括车
削、铣削、钻孔、磨削等。
5.制定刀具选择和切削参数:根据加工工艺和零件材料,选择适当的刀具类型和规
格,并确定合适的切削参数,如切削速度、进给速度和切削深度等。
6.加工零件:按照工艺图纸和加工工艺要求,使用相应的加工设备和刀具进行零件的
加工,包括外径加工、内径加工、面加工等。
7.检验与调整:对加工完成的定位套筒进行尺寸检验和质量检验,如使用测量工具测
量尺寸精度、表面粗糙度等,并根据检验结果进行必要的调整和修正。
8.表面处理:根据需求,对定位套筒进行表面处理,如镀锌、镀铬等,以提高其耐腐
蚀性和美观度。
9.清洗和包装:对加工完成的定位套筒进行清洗,去除切削液和金属屑,并进行适当
的包装,以保护零件免受损坏。
以上是定位套筒零件的一般机械加工工艺设计的步骤,具体的工艺设计还需根据零件的具体要求和加工设备的特点进行调整和优化。
在加工过程中,需要注意安全操作,保证零件的加工质量和精度。
加工套筒的工艺

加工套筒的工艺加工套筒是一种常见的加工零件,广泛应用于机械设备、汽车工业、航空航天等领域。
下面我们将详细介绍加工套筒的工艺过程。
首先,加工套筒的工艺流程可以分为材料准备、下料、车削、钻孔、车外圆、车内圆、镗内孔、磨削、检验和包装等步骤。
下面我们将逐一进行介绍。
1. 材料准备:选择适当的材料是加工套筒的第一步。
常见的材料有铁、铜、铝、不锈钢等。
根据零件的具体要求,选择合适的材料进行加工。
2. 下料:将原材料根据设计要求切割成适当大小的工件。
常见的下料方法有剪切、火花切割等。
3. 车削:使用车床进行车削加工。
首先进行外圆车削,将工件的外表面精确加工成所需的直径和长度。
车削时应注意控制刀具的进给速度、切削速度和切削深度,以保证车削质量。
4. 钻孔:对套筒进行钻孔加工。
根据设计要求,在套筒的端面或侧面进行钻孔. 钻孔时应注意选择合适的钻头、钻孔方式和钻孔深度,以保证钻孔的准确度和表面质量。
5. 车外圆:对套筒进行外圆车削。
通过车床的工作台和刀架的协调动作,将套筒的外表面加工成所需的直径、长度和形状。
车外圆时应注意控制车刀的切削力、进给速度和切削速度,以确保外圆的精度和表面质量。
6. 车内圆:对套筒进行内圆车削。
通过车床的进给装置、工作台和刀架的联动,将套筒的内表面加工成所需的直径、长度和形状。
车内圆时应注意选择合适的车刀、进给速度和切削速度,以确保内圆的精度和表面质量。
7. 镗内孔:对套筒进行镗孔加工。
使用镗铣床或镗床进行加工,将套筒的内孔加工成所需的直径和深度。
镗孔时应注意选择合适的刀具、进给速度和切削速度,以保证孔的精度和表面质量。
8. 磨削:对套筒进行磨削加工。
通过磨床的砂轮和工件的旋转运动,进一步提高套筒的精度和表面质量。
磨削时应注意选择合适的砂轮、进给速度和磨削时间,以确保磨削的精度和表面质量。
9. 检验:对加工完成的套筒进行检验。
采用各种测量工具和仪器,如千分尺、游标卡尺、量具等对套筒的尺寸、形状、表面质量进行检测,以确保套筒满足设计要求。
机械制造及工艺——套筒类零件加工工艺

套筒类零件加工工艺第一节概述一、套筒类零件的功用和结构特点套筒类零件是机械中常见的一种零件,它的应用范围很广。
如支承旋转轴的各种形式的滑动轴承、夹具上引导刀具的导向套、内燃机气缸套、液压系统中的液压缸以及一般用途的套筒,如图7-1所示。
由于其功用不同,套筒类零件的结构和尺寸有着很大的差别,但其结构上仍有共同点:零件的主要表面为同轴度要求较高的内外圆表面;零件壁的厚度较薄且易变形;零件长度一般大于直径等。
二、套筒类零件的技术要求、材料和毛坯1.套筒类零件的技术要求套筒类零件的主要表面是孔和外圆,其主要技术要求如下。
(1)孔的技术要求。
孔是套筒类零件起支承或导向作用的最主要表面,通常与运动的轴、刀具或活塞相配合。
孔的直径尺寸公差等级一般为IT7,精密轴套可取工IT6 ,气缸和液压缸由于与其配合的活塞上有密封圈,要求较低,通常取IT9 。
孔的形状精度,应控制在孔径公差以内,一些精密套筒控制在孔径公差的土1/2~1/3,甚至更严。
对于长的套筒,除了圆度要求以外还应注意孔的圆柱度。
为了保证零件的功用和提高其耐磨性,孔的表面粗糙度Ra 值为1.6~0.16μm ,要求高的精密套筒Ra可达0.04 μm 。
(2)外圆表面的技术要求。
外圆是套筒类零件的支承面,常以过盈配合或过渡配合与箱体或机架上的孔相连接。
外径尺寸公差等级通常取IT7~IT6 ,其形状精度控制在外径公差以内,表面粗糙度Ra 值为 3.2~0.63 μm 。
(3)孔与外圆的同轴度要求。
当孔的最终加工是将套筒装人箱体或机架后进行时,套筒内外圆间的同轴度要求较低;若最终加工是在装配前完成的,则同轴度要求较高,一般为Φ0.05~0.01 mm 。
(4)孔轴线与端面的垂直度要求。
套筒的端面(包括凸缘端面)若在工作中承受载荷,或在装配和加工时作为定位基准,则端面与孔轴线垂直度要求较高,一般为0.05~0.01 mm 。
2.套筒类零件的材料与毛坯套筒类零件一般用钢、铸铁、青铜或黄铜制成。
套筒零件的加工

序号 工序 名称
01 下料 02 车
03 热 04 磨 05 磨 06 检
工序内容
定位
夹紧
Φ48×130mm(五件合一)
车端面,Ra10μm,钻、镗孔300,0.033 mm 外圆 留磨余量0.3mm,车外圆45,00..100790 mm 端面
留磨余量0.3mm,倒角,切断;
调头,车端面,确保尺寸20mm, Ra10μm,倒角;
1.确保短套零件各表面位置精度旳措施
从短套零件旳技术要求可知,其主要位置精度是 内、外圆表面旳同轴度及端面与轴线之间旳垂直 度要求。在加工过程中一般常采用下述措施。
1)在一次装夹过程中完毕内外表面及端面旳全 方面加工,这种加工措施消除了工件旳装夹误差, 可取得很高旳相对位置精度。但是,这种加工措 施旳工序比较集中,对于尺寸较大旳套筒零件也 不便于装夹。
(1)如图4-3(a)所示,缸筒以一端止口定位,用 弹性夹头夹紧;另一端以架窝支承在中心架上。这 种措施装卸工件比较麻烦,定位精度低,但不需要专 用设备,合用于单件小批生产;
(2)如图4-3(b)所示,缸筒以一端止口定位,用 弹性夹头夹紧;另一端以30º-60º外圆锥面与压力 头上旳专用内锥套定位和夹紧。这种措施装卸工 件比较以便,定位精度高,须有压力头,合用于中、 小批生产。
对于一般精度旳套筒,假如需径向夹紧时,也尽量 使径向夹紧力均匀,使用过渡套或弹簧套夹紧工件。 或者作出工艺凸台及工艺螺纹,以降低夹紧变形。
套筒类零件加工工艺

套筒类零件加工工艺套筒是一种常见的机械零件,广泛应用于各种机械设备中。
套筒类零件的加工工艺是指对套筒进行加工的过程和方法。
在加工套筒类零件时,需要根据产品的要求和工艺要求,选择合适的加工方法和工艺流程,以确保零件的质量和精度。
套筒类零件的加工工艺主要包括以下几个方面:材料准备、工艺设计、机械加工和表面处理。
首先是材料准备。
套筒类零件一般使用金属材料进行加工,常见的有钢材、铸铁材料等。
在进行材料准备时,需要对材料进行检验和筛选,确保材料的质量和性能符合要求。
同时,还需要对材料进行切割和锻造等工艺处理,以获得适合加工的材料。
接下来是工艺设计。
工艺设计是指根据产品的要求和工艺要求,确定套筒类零件的加工方法和工艺流程。
在进行工艺设计时,需要考虑到零件的形状、尺寸、精度要求等因素,选择合适的加工方法,如车削、铣削、钻削等。
同时,还需要确定加工的顺序和工艺参数,如切削速度、进给量、切削深度等,以确保零件的加工质量和精度。
然后是机械加工。
机械加工是指使用机床进行零件的切削、成形和加工的过程。
在进行机械加工时,需要根据工艺设计的要求,选取合适的机床和刀具,进行加工操作。
常见的机械加工方法包括车削、铣削、钻削、磨削等。
在进行机械加工时,需要注意调整机床和刀具的参数,控制加工的速度和精度,以确保零件的加工质量和精度。
最后是表面处理。
表面处理是指对套筒类零件的表面进行处理,以改善其外观和性能。
常见的表面处理方法包括热处理、电镀、喷涂等。
在进行表面处理时,需要根据产品的要求和工艺要求,选择合适的处理方法和工艺流程,以获得符合要求的表面效果和性能。
总结起来,套筒类零件的加工工艺是一个复杂的过程,需要综合考虑材料、工艺设计、机械加工和表面处理等因素。
只有在严格按照工艺要求进行加工,才能获得质量和精度达标的套筒类零件。
在实际生产中,要根据具体情况选择合适的加工方法和工艺流程,以提高生产效率和产品质量。
通过不断改进和优化加工工艺,可以进一步提高套筒类零件的加工精度和质量,满足不同客户的需求。
套筒零件加工工艺分析
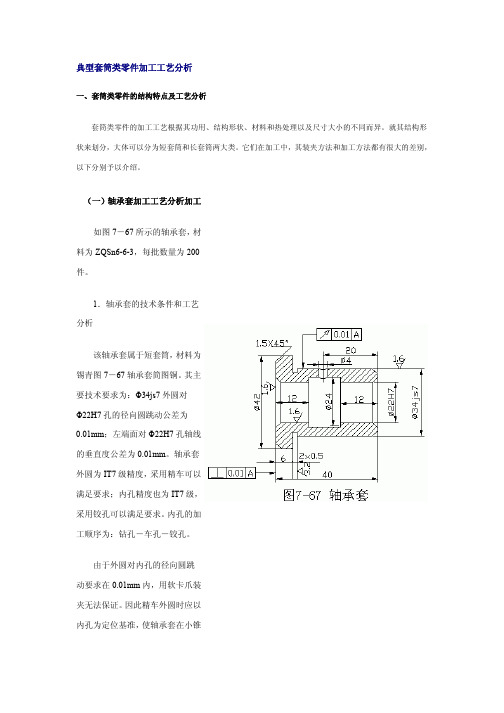
3
粗车 空刀槽 2×0.5mm,取总长 40.5mm,车分割槽 Ф20×3mm, 中心孔
两端倒角 1.5×45°,5 件同加工,尺寸均相同
钻孔 Ф22H7 至 Ф22mm 成单件
4
钻
软爪夹 Ф42mm 外圆
• 车端面,取总长 40mm 至尺寸
5 车、铰
• 车内孔 Ф22H7 为 Ф22 mm • 车内槽 Ф24×16mm 至尺寸 • 铰孔 Ф22H7 至尺寸 • 孔两端倒角
由于外圆对内孔的径向圆跳 动要求在 0.01mm 内,用软卡爪装 夹无法保证。因此精车外圆时应以 内孔为定位基准,使轴承套在小锥
度心轴上定位,用两顶尖装夹。这 样可使加工基准和测量基准一致, 容易达到图纸要求。
车铰内孔时,应与端面在一次 装夹中加工出,以保证端面与内孔 轴线的垂直度在 0.01mm 以内。
3.精铰(浮动镗刀镗孔)到 Ф70±0.02mm,
表面粗糙度值 Ra 为 2.5µm
4
滚压孔 用滚压头滚压孔至 Ф70
mm,表面粗糙 一端用螺纹固定在夹具中, 另一
度值 Ra 为 0.32µm
端搭中心架
1.车去工艺螺纹,车 Ф82h6 到尺寸,割 R7 槽
软爪夹一端,以孔定位顶另一端
2.镗内锥孔 1°30′及车端面
5
车
软爪夹一端,中心架托另一端(百 分表找正孔)
3.调头,车 Ф82h6 到尺寸,割 R7 槽
软爪夹一端,顶另一端
4.镗内锥孔 1°30′及车端面
软爪夹一端,顶另一端
二、套筒类零件加工中的主要工艺问题
一般套筒类零件在机械加工中的主要工艺问题是保证内外圆的相互位置精度(即保证内、外圆表面的 同轴度以及轴线与端面的垂直度要求)和防止变形。
典型套筒类零件的加工工艺分析

典型套筒类零件的加工工艺分析引言:套筒类零件是机械零件中常见的一种,广泛应用于各种机械设备中。
其加工工艺分析对于提高零件的加工质量和降低成本具有重要意义。
本文将从设计、材料选择、工艺规划以及加工工艺等方面对典型套筒类零件的加工工艺进行详细分析。
一、设计:二、材料选择:三、工艺规划:1.工艺路线规划:根据零件的形状、材料和加工要求,确定合适的工艺路线。
典型的工艺路线包括铣削、车削、钻孔、镗孔、磨削等工序。
2.切削参数选择:根据零件的材料和加工要求,选择合适的切削参数,包括切削速度、进给速度、切削深度等。
通过试切试验和经验总结,不断优化和调整切削参数。
3.夹具设计:根据零件的形状和加工要求,设计合适的夹具,以保证零件在加工过程中的稳定性和精度。
四、加工工艺:1.车削工艺:车削是加工套筒类零件常用的工艺之一、根据零件的形状和加工要求,选择合适的切削工具和切削参数进行车削。
2.镗削工艺:镗削用于加工孔的精度要求较高的套筒类零件。
根据零件的尺寸和加工要求,选择合适的镗削刀具和切削参数进行镗削。
3.铣削工艺:铣削常用于加工套筒类零件的外形轮廓。
根据零件的形状和加工要求,选择合适的铣削刀具和切削参数进行铣削。
4.钻孔工艺:钻孔通常用于套筒类零件的孔加工。
根据零件的尺寸和加工要求,选择合适的钻孔刀具和切削参数进行钻孔。
5.磨削工艺:磨削常用于加工套筒类零件的表面精加工。
根据零件的表面粗糙度要求,选择合适的磨削工具和切削参数进行磨削。
五、加工装备和工具选择:根据零件的工艺要求,选择合适的加工装备和工具。
常用的加工设备包括车床、铣床、钻床、磨床等。
根据工艺要求和经济性考虑,选择合适的设备和工具。
六、检验和质量控制:在加工过程中,需要进行适当的检验和质量控制,以确保零件的加工质量。
常用的检验方法包括尺寸检验、形状检验、表面粗糙度检验等。
结论:典型套筒类零件的加工工艺分析对于提高零件的加工质量和降低成本具有重要意义。
通过合理的设计、材料选择、工艺规划和加工工艺,可以实现零件的精确加工和高效生产。
典型的套类零件加工工艺PPT课件
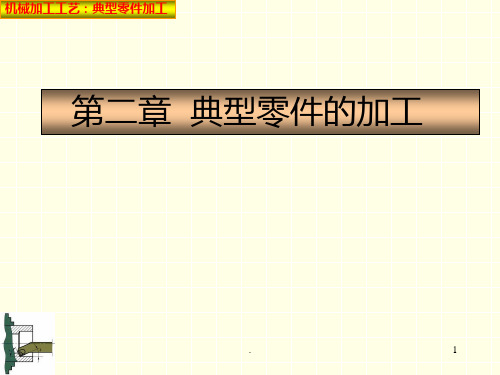
由于其装夹后不能自动定心,所以装夹效率较低,装夹时必
须用划线盘或百分表找正,使工件回转中心与车床主轴中心对齐,
如图b为用百分表找正外圆的示意图。
.
9
典型零件加工:套筒件加工
2)用四爪卡盘安装工件 找正方法 有非加工表面的,要按最大的非加工表面找正; 所有表面都需加工的,要根据加工余量最小的表面找正。
机械加工工艺:典型零件加工
第二章 典型零件的加工
.
1
典型零件加工:套筒件加工
二、套筒类零件的加工
.
2
典型零件加工:套筒件加工
二、套筒类零件的加工
(一)工艺分析 1.功用及结构特点 套类零件在各类机器中应用很广,如滑动
轴承、钻套、导向套、汽缸、油缸等。
⑴功用 支撑 (如滑动轴承),导向作用(如钻套、油缸)
(与材料、结构、尺寸有关,)常用棒料、锻件、铸件。 当孔径d<20mm,一般用棒料、无缝管; 较长较大的套,常用无缝管、带孔的铸锻件;
某些油缸常用35焊接缸头、耳轴、法兰盘等;不需焊时 用45钢。
.
4
典型零件加工:套筒件加工
二、套筒类零件的加工 (一)工艺分析
1.功用及结构特点
2.材料与毛坯 3.主要技术要求:
.
8
典型零件加工:套筒件加工
2.定位与装夹方法 (1)一次装夹完成各主要表面全部加工
1)三爪自定心卡盘安装工件 2)用四爪卡盘安装工件
当四重爪量卡较盘重的的外工形件进行装夹时,宜用四爪单动卡盘或其它 如专图用a夹所具示。。它的四个 爪通过4个螺杆独立移 动。它的特点是能装 夹形状比较复杂的非 回转体如方形、长方 形等,而且夹紧力大。
在花盘上安装零件
.
13
- 1、下载文档前请自行甄别文档内容的完整性,平台不提供额外的编辑、内容补充、找答案等附加服务。
- 2、"仅部分预览"的文档,不可在线预览部分如存在完整性等问题,可反馈申请退款(可完整预览的文档不适用该条件!)。
- 3、如文档侵犯您的权益,请联系客服反馈,我们会尽快为您处理(人工客服工作时间:9:00-18:30)。
课题:套筒类零件的加工工艺一、十四、教学目的:熟悉零件的功用、结构特点和主要技术要求。
掌握套筒类零件内孔一般加工方法的工艺特点、应用场合、了解套筒类零件内孔表面精密加工方法的加工原理、工艺特点及应用场合;掌握并能拟订长、短套筒零件的加工艺二、十五、教学重点:孔各种加工方法的工艺特点和应用范围,长、短套筒零件的加工工艺分析、工艺规程的编制。
三、十六、教学难点:套筒零件的工艺规程编制,孔的精密加工四、教学时数: 2 学时,其中实践性教学学时。
五、习题:六、教学后记:第四节套筒类零件的加工一、概述(一)、零件的功用与结构1、1、功用:支承、导向作用2、2、结构:主要表面为同轴度要求较高的内、外圆表面,零件壁厚较薄,长度大于直径。
常见的有轴承衬套、钻套、液压油缸,如图所示:(二)、技术要求1、孔的技术要求孔是套筒零件与回转轴颈,刀具或移动活塞相配合,是起支承或导向作用,孔的直径尺寸一般IT7,精密轴套IT6,气缸液压缸为IT9形状精度在尺寸公差内,精密轴套控制在1/2-1/3T,长套筒要圆柱度要求,表面粗糙度Ra1.6~0.16um,高的可达Ra0.4。
2、2、外圆表面要求外圆一般以过盈或过渡配合与机座或箱体上的孔相连接,它是套筒零件的支承表面。
外圆的尺寸精度一般为IT6~IT7,形状尺寸精度控制在外径公差范围内表面粗糙度Ra3.2~0.63。
3、孔与外圆的同轴度当孔的终加工是在套筒装入机座后加工的,要求较低,最终加工是在装配前完成的,一般同轴度为0.01~0.054、轴线与端面的垂直度要求端面(包括凸缘端面)若在工作中受轴向或作定位基准(装配基准)时,其垂直度为0.01~0.05。
(三)、材料与毛坯1、1、材料:钢、铸铁、青铜或黄铜,或双金属结构如滑动轴承以离心铸造法浇注巴氏合金。
2、2、毛坯:孔径小的用热轧或冷拉棒料,也可用实心铸件,孔径大的用无缝钢管或带孔铸件,锻件大量生产时采用冷挤压或粉末冶金。
(四)、加工工艺套筒类零件加工的主要工艺问题是如何保证其主要加工表面(内孔和外圆)之间的相互位置精度,以及内孔本身的加工精度和表面粗糙度要求。
尤其是薄壁、深孔的套筒零件,由于受力后容易变形,加上深孔刀具的刚性及排屑与散热条件差,故其深孔加工经常成为套筒零件加工的技术关键。
套筒类零件的加工顺序一般有两种情况:第一种情况为:粗加工外圆——粗、精加工内孔——最终精加工外圆。
这种方案适用于外圆表面是最重要表面的套筒类零件加工第二种情况为:粗加工内孔——粗、精加工外圆——最终精加工内孔。
这种方案适用于内孔表面是最重要表面的套筒类零件加工。
套筒类零件的外圆表面加工方法,根据精度要求可选择车削和磨削。
内表面加工方法的选择则需考虑零件的结构特点、孔径大小、长径比、材料、技术要求及生产类型等多种因素。
二、套筒类零件的内孔加工内孔是套筒类零件的主要加工表面,加工方法选择的原则具体根据孔的大小,深度,精度,结构形状等面定。
①①当孔径较小时(〈Φ50mm〉宜采用钻扩,较方案②②孔较大时采用钻孔后镗或直接镗孔③③箱体上孔多采用精镗,浮动镗,缸筒件用精镗,珩磨,滚压④④淬硬套筒,宜采用磨孔⑤⑤精密孔用高精度磨削,研磨,珩磨或抛光等常见孔的加工方法:钻孔扩孔铰孔孔的加工方法镗孔拉孔磨孔、珩孔,研磨孔(一)、钻孔滚压加工钻孔是在实心材料上加工孔的第一道工序。
它主要用于精度要求较高孔的预加工或精度低于IT11级的孔的终加工。
钻孔刀具常用麻花钻。
由于麻花钻具有宽而深的容屑槽、钻头顶部有横刃及钻头只有两条很窄的螺旋棱带与孔壁接触等结构特点,因而钻头的刚性差、导向性能差,钻孔时容易引偏,易出现孔径扩大现象,孔壁加工质量较差。
措施:加工前先加工孔的端面,采用工件回转方式或先钻引导锥等使用范围:孔径≤φ75mm,当孔径≥φ35mm时分两次钻,第一次钻孔的直径为所需孔径的1/2-7/10。
第二次钻到所需孔径,这时横刃不参加切削,轴向抗力小,切削较轻小。
(二)、扩孔扩孔是用扩孔钻对工件上已钻出、铸出或锻出孔作进一步加工的方法。
扩孔加工有如下特点:1、加工精度比钻孔高:切深小,钻头无横刃,刀体刚度大,导向作用好IT11~10,Ra6.3~3.22、扩孔能纠正原孔轴线的歪斜3、生产率高,由于余量小(1/8φ)扩孔齿数较多,f=0.4-2mm/r4、孔径>φ100的孔,多用镗孔而不用扩孔(三)、铰孔铰孔是未淬硬的中小尺寸孔进行精加工的一种方法,加工的孔径范围一般为φ3~φ80mm.铰孔的工艺特点:1、1、铰孔精度主要取决于铰刀精度。
2、2、铰孔比镗孔容易保证尺寸精度和形状精度,且生产率较高。
一般IT7~IT8,手铰达IT6。
Ra1.6~0.2。
3、3、适应性差,一种铰刀只能加工一种尺寸和一种精度的孔。
4、4、不能校正原孔轴线的偏斜。
(四)、镗孔镗孔是常用的孔的加工方法,可作为粗加工,也可以作精加工。
其主要工艺特点:1、1、加工范围广,非标孔、大直径孔、短孔以及盲孔、有色金属孔及孔系等加工。
2、2、获得较高的精度与低表面粗糙度,IT8~IT6,Ra1.6~0.4用金刚镗则更低3、3、修正前道工序的孔轴线的偏斜和不直,生产率较低4、4、可在车,铣,镗及数控机床上进行(五)、磨孔磨孔是单件小批生间中常用的孔精加工方法,它特别适宜于加工淬硬的孔,表面精度断续的孔和长度很短的精密孔。
对于中小型回转零件,磨孔在内圆磨床或万能磨床上进行对于大型薄零件,可采用无心内圆磨削。
内圆磨削的工艺特点:1、1、轮直径D受到工件孔径刀的限制(D=0.5~0.9D),砂轮尺寸小,损耗快,经常要更换影响效益2、磨削速度低因此,磨削精度较难控制3、砂轮轴受孔径与长度限制,刚性差,易弯曲,振动,影响加工精度与表面粗糙度4、砂轮与工件内切,接触面积大,散热条件差,易烧伤,宜用较砂轮5、切削液不易进入磨削区,排屑困难。
内孔磨削方法:中心圆磨:用于中小型工件,在万能磨,内圆磨床上进行磨削方法行星式内圆磨:用于重量大,形状不对称的内孔,用行星或磨床无心内圆磨:用于直径短套孔。
(五)、拉孔:拉孔是拉刀在拉床上对已预加工的孔进行半精加工或精加工的方法拉孔方法的特点:1、尺寸精度高,表面质量好IT7~9,Ra1.6~0.12、不能纠正轴线的偏斜3、拉刀结构复杂,成本高,制造周期长4、一把拉刀只拉一种规格尺寸的孔,要求工件材质均匀。
薄壁孔,盲孔,阶梯孔,深孔,大直径孔和很小的孔及淬硬孔不宜拉。
拉削范围为φ10~100三、孔的精密加工当套筒类零件内孔的加工精度和表面粗糙度要求很高时,则精加工后还需进行精密加工。
金刚镗(精细镗)孔的精密加工方法研磨,珩磨(一)、精细镗滚压精细镗是由于最初使用金刚石作镗刀材料而得名。
精细镗的工艺特点:1、1、用精度高,刚度大,高转速的金刚镗床(转速高达500r/min)切铸铁100m/min,钢200 m/min,铝300 m/min2、2、削用量小,切削刀热小,加工精度高3、3、生产率高加工范围广(二)、珩磨珩磨是用若干细粒度磨条组成的珩磨头进行内孔光整加工的方法,通常在磨削或精镗后进行。
1、1、珩磨工作原理2、2、珩磨孔的工艺特点:(1)(1)加工范围广(2)(2)磨头与主轴浮动联接(3)(3)精度高,IT6,Ra0.8~0.025能修正几何误差交叉网纹有利于油膜形成。
3、3、影响珩磨质量和生产率的因素(1)珩磨的圆周速度V P和往复速度V w的因素V P ↑、V w↑质量好效率高,但磨损↑、热↑、易堵塞V P/ V w的比值影响网纹交叉角αα=40~60°(2)珩磨头行程L与越程量aL=L k+2a-Ls式中L k:被加工表面长度Ls:磨条长度但磨条不宜过长(3)珩磨压力。
F↑η↑F↑磨损↑切削能力↓(4)冷却与润滑。
(三)研磨略(四)滚压四、套筒类零件加工工艺分析套筒类零件由于其功用、结构形状、尺寸、材料及热处理等的不同,其工艺差别很大。
就结构形状而言,可分为短套筒与长套筒两类,这两类套筒在装夹与加工方法上有很大的差别。
下面分别分析其工艺特点。
(一)、短套筒零件的加工——气缸套零件加工工艺如图为A110型柴油机气缸零件图,由于L/D≈3,属短套。
内孔G是重要表面,其加工工艺过程如下:气缸套零件加工工艺工序工序名称工序内容定位夹紧号010 铸造毛坯020 人工时效030 粗镗内孔 镗内孔至Φ10820.0+mm 和一端台阶Φ135mm 。
外圆040 粗车外圆 粗车各级外圆 内孔 气压胀胎夹具050 热处理正火 060 半精车 半精车法兰凸台端面及外国内孔气压胀胎夹具 070 半精镗 半精镗内孔Φ1091.0+mm 及总长2695.05.0+-mm 。
外圆法兰凸台端面及外圆 080 精 车精车法兰凸台端面,外圆割槽 内孔气压胀胎夹具 090 去氧化皮用圆弧车刀R10车外圆并用靠模样板 100 半精车半精车密封槽 外圆法兰凸台端面及外圆 110 精 镗镗精内孔Φ110065.010.0--mm 外圆法兰凸台端面及外圆 120 精 车精车外圆Φ129043.0065.0--mm ,Φ132085.0148.0--mm 内孔气压胀胎夹具 130 粗 珩粗珩磨内孔Φ110025.006.0-- 外圆法兰凸台端面及外圆 140 精珩 精珩磨内孔Φ110035.00+ 外圆法兰凸台端面及外圆 (二)、长套加工——油缸零件的加工工艺图所示为液压油缸零件。
该零件的孔长与直径之比L/D=24,属典型的长套筒零件.:图中主要技术要求为:(1)内孔必须光滑无纵向划痕;(2)内孔圆柱度误差不大于0.04mm;(3)内孔轴线的直线度误差不大于0。
1/1000mm;(4)内孔轴线与端面的垂直度误差不大于0。
03mm;(5)内孔对两端支承外圆(Φ82h6))的同轴度允差为Φ0.04mm.对于油缸这类长套筒零件,为保证内外圆同轴度,加工外圆时,其装夹方式常采用下面两种:用顶尖顶住两端孔口的倒角;一头夹紧外圆另一头用中心架支承(一夹一托)或一头夹紧外圆另一头用后顶尖顶住(一夹一顶)。
加工内孔时,一般采用夹一头、另一头用中心架支承外圆。
粗加工孔采用镗削,半精加工和精加工孔多用浮动铰孔方式。
若内孔表面要求粗糙度很低时,还须选用折磨或滚压加工。
本例采用一夹一托或一夹一顶方式来加工外圆;采用工艺螺纹固夹一头、中心架托另一头外圆的方式来加工内孔。
内孔经推镗、浮动精铰后再进行冷压加工,以保证达到图纸规定的要求。
其加工工艺如下:油缸零件的加工工艺。